DOI:
10.1039/C6RA25196J
(Paper)
RSC Adv., 2017,
7, 2513-2519
Study of structure–performance relationships of polymeric dispersants on particle dispersion and stabilisation†
Received
13th October 2016
, Accepted 31st October 2016
First published on 12th January 2017
Abstract
A series of polymeric dispersants in three different structural types, namely AB diblock, ABA triblock and comb, were synthesised via reversible addition–fragmentation chain transfer (RAFT) polymerisation. They were systematically designed and optimised with varying molecular weights, compositions, anchoring and stabilising chain lengths, then investigated and compared over the dispersion performance of SiO2 particles in organic media. The comparisons indicated that the optimised AB diblock poly(2-(dimethylamino)ethyl methacrylate)30-b-poly(ethyl methacrylate)40 (PD30-b-PE40) and ABA triblock (PD30-b-PE60-b-PD30) dispersants enabled homogeneous SiO2 particle dispersion, which were more effective in reducing particle size and system viscosity than the comb dispersant poly((2-(dimethylamino)ethyl methacrylate)30-co-(poly(propylene glycol) acrylate)15) (P(D30-co-PPGA15)). In particular, it was found that AB diblock copolymer dispersants are generally at least as effective as or better than their ABA triblock equivalents in particle dispersion and stabilisation. Thus, the dispersion effectiveness of the three structural types can be ordered as: AB ≥ ABA > comb. Furthermore, structure–performance relationships were developed between dispersants' molecular structures and dispersion performances, in order to provide constructive guidance for the structural design and selection of polymeric dispersants for effective particle dispersion and stabilisation in organic media for various applications.
1. Introduction
Physical surface modification through noncovalent bonding is one of the most commonly used methods for dispersing and stabilising solid particles (such as SiO2, TiO2, carbon black, pigment particles and others) in liquid media, due to its convenience, wide applicability and processability particularly in industrial applications.1–4 It is usually implemented by utilising surfactants or macromolecules to adsorb onto the particle surface, in order to minimise the high surface energy and physical attractive forces between the particles, and to prevent their agglomeration.4–7 Such surfactants have traditionally been small molecular surfactants, but recent advancement in polymer chemistry has made the more effective polymeric dispersants available. This is especially supported by the development of controlled/living radical polymerisation (CLRP) techniques, such as atom transfer radical polymerisation (ATRP),8–12 reversible addition–fragmentation chain transfer (RAFT) polymerisation,13–16 nitroxide-mediated polymerisation (NMP)17,18 and others,19,20 which have overcome the limitations of conventional polymerisation methods in polymeric structure design and synthesis. Through CLRP, polymeric dispersants with controlled molecular weight, narrow molecular weight distribution and well-defined structures can be prepared, including block copolymers (AB, ABA, BAB),21–26 graft copolymers (comb, dendrimer, hyperbranched)27–30 and others,31–36 which are more effective in particle dispersion than homopolymers or random copolymers synthesised by conventional polymerisation methods. These structurally well-defined copolymers' anchoring chains can robustly adsorb onto the particle surface through multi-point noncovalent interactions, such as hydrogen bonding, dipole–dipole, zwitterionic, acid–base interaction and others.24,37,38 Simultaneously, their stabilising chains can form steric stabilisation barriers around the particles in solvent media, enabling homogeneous dispersion and stabilisation while preventing them from aggregating. Hence, copolymers with properly designed molecular structures and compositions can provide effective dispersion stability to solid particles.
For instance, Auschra et al.23 used ATRP to prepare AB diblock copolymer dispersants with poly(2-(dimethylamino)ethyl acrylate) (PDMAEA) as the anchoring chain and poly(butyl acrylate) (PBA) as the stabilising chain, which could effectively prohibit two types of pigment particles from agglomerating in solvents. Similarly, Chen et al.38 also used ATRP and synthesised poly(butyl methacrylate-co-glycidyl methacrylate) (P(BMA-co-GMA)) copolymer dispersants with different polar pendants (tertiary amino, hydroxyl or carboxylic acid groups) grafted onto the GMA oxirane side groups. Specifically, the copolymer with tertiary amino pendants resulted in homogeneous dispersion of a representative yellow pigment in solvent medium, achieving fine particle size, low viscosity and long-term stability. Meanwhile, Kuo et al.24 prepared an AB diblock copolymer dispersant poly(styrene-EHA-HEMA)-b-poly(styrene-EHA-HEMA-DMAEMA) (P(SEH)-b-P(SEHD)) via NMP, where tertiary amino groups of DMAEMA on the P(SEHD) anchoring chain could strongly adsorb onto carbon black particle surface, while the P(SEH) stabilising chain could contribute sufficient steric repulsion force to avoid particle flocculation and could stabilise carbon black dispersion in organic solvent.
Although the recent applications of CLRP techniques to prepare polymeric dispersants have achieved some promising results in particle dispersion, the related research mostly focused on relatively simple structures such as AB diblock copolymers, with limited studies on other molecular architectures. More importantly, there is a general lack of systematic investigation on the “structure–effect” or “structure–performance” relationships between different polymeric dispersants' molecular structures and dispersion performances.
Hence in this work, we utilised the CLRP technique of RAFT polymerisation to synthesise a series of polymeric dispersants in three well-defined structural types, namely AB diblock, ABA triblock and comb, with different molecular weights, compositions, anchoring and stabilising chain lengths. Then, we systematically examined and compared these dispersants' dispersion on SiO2 particles in xylene and a solvent-based resin as model organic media, in order to develop structure–performance relationships between polymeric dispersants' molecular architectures, structural compositions and dispersion performances. These can provide future guidelines for the design and selection of polymeric dispersants' molecular architectures and structural characteristic features for effective particle dispersion and stabilisation in organic media.
2. Experimental
2.1 Materials
2-(Dimethylamino)ethyl methacrylate (DMA, 99%, J&K Chemical), ethyl methacrylate (EMA, 99%, J&K Chemical) and poly(propylene glycol) acrylate (PPGA, Mn ≈ 475, 99%, Sigma-Aldrich) were passed through basic alumina column before use. 2,2′-Azoisobutyronitrile (AIBN, 99%, J&K Chemical) was recrystallized from ethanol before use. Solvent-based acrylic resin ETERAC 7331-1-XS-70 (70% solid content, Eternal Materials), ACEMATT OK-412 silica (SiO2, ∼6 μm, Evonik Industries), commercial polymeric dispersant Efka-PX-4310 (EFKA-4310, acrylic block copolymer, Mn ≈ 9000, BASF) and commercial polymeric dispersant DISPERBYK-2008 (BYK-2008, acrylic copolymer, Mn ≈ 7000, BYK Chemie) were used as received. 1,4-Dioxane, n-hexane, xylene and other solvents were purchased from Beijing Chemical Reagent Co., Ltd. (China) and purified before usage. The RAFT chain transfer agent (CTA) S-1-dodecyl-S′-(α,α′-dimethyl-α′′-acetic acid)trithiocarbonate (DDMAT) was prepared according to literature.39
2.2 Instruments
Proton nuclear magnetic resonance (1H NMR) spectra were obtained using 300 MHz JEOL JNM-ECA300 and 400 MHz JEOL JNM-ECA400 spectrometers. All the copolymers' number averaged molecular weight (Mn) and molecular weight distribution or polydispersity index (PDI = Mw/Mn) were determined by Waters 1515 gel permeation chromatography (GPC) system equipped with a 2414 refractive index detector, a Waters 1515 Isocratic HPLC pump and three Styragel columns. The GPC system was calibrated by monodispersed polystyrene standards, and its eluent was tetrahydrofuran (THF) with 2% triethylamine at a flowrate of 1 mL min−1 at 35 °C. The SiO2 samples were dispersed by a high-speed disperser (SFJ-400, 550 W, 0–7500 rpm). The dispersed samples' viscosities were measured by a Brookfield RVT rotational viscometer (Spindle No. 4) at 30 rpm and 25 °C, and their average particle sizes were measured by a Zehntner ZGR 2021 grindometer (0–50 μm). Morphology images of dispersed SiO2 particles were recorded by using a high-resolution field emission JEOL JSM-7401 scanning electron microscope (SEM) operated at 15 kV after samples had been initially coated with gold for 30 s.
2.3 Synthesis of AB diblock copolymers
AB diblock copolymers were synthesised by a two-step RAFT polymerisation (Scheme S1†). The typical reaction is as follows (PDMA30-b-PEMA40 (denoted as PD30-b-PE40)): the first step used RAFT CTA DDMAT (72.8 mg, 0.2 mmol), DMA (0.942 g, 6 mmol), AIBN (3.28 mg, 0.02 mmol) and 1,4-dioxane (1.5 mL), which were added into a Schlenk tube. The mixture was carefully degassed by purging with N2 gas for 30 min, and then reacted at 70 °C with stirring for 8 h. After the reaction, the Schlenk tube was quenched in liquid N2 and diluted with 1,4-dioxane (2 mL), before being precipitated in cold n-hexane twice. The purified product was vacuum dried overnight at room temperature, obtaining a yellow solid as the RAFT macromolecular CTA (PDMA-CTA). The second step used PDMA-CTA (1.016 g, 0.2 mmol), EMA (0.912 g, 8 mmol), AIBN (3.28 mg, 0.02 mmol) and 1,4-dioxane (3 mL), which were added into a Schlenk tube. The mixture was carefully degassed by purging with N2 gas for 30 min, and then reacted at 70 °C with stirring for 8 h. After the reaction, the Schlenk tube was quenched in liquid N2 and diluted with 1,4-dioxane (3 mL), before being precipitated in cold n-hexane twice. The purified product was vacuum dried overnight at room temperature, obtaining a yellow solid as the final product PD30-b-PE40. 1H NMR (300 MHz, CDCl3, (CH3)4Si, Fig. S1†), δ/ppm: 0.78–1.12 (3H, m, C(CH3)), 1.20–1.33 (3H, m, OCH2CH3), 1.74–2.04 (2H, m, C(CH3)CH2), 2.26–2.35 (6H, m, N(CH3)2), 2.52–2.66 (2H, m, OCH2CH2N) and 3.95–4.17 (2H, m, COOCH2 of PDMA and PEMA blocks).
The synthesis of ABA triblock and comb copolymers followed similar procedures as the AB diblock copolymers above (see ESI†).
2.4 Preparation and measurement of SiO2 particle dispersion
SiO2 particle dispersion was prepared by a high-speed dispersion process. Solvent-based resin ETERAC 7331-1-XS-70 (185.72 g, 100 wt%), synthesised polymeric dispersant (0.52 g, 0.28 wt% (or 5 wt% of SiO2)) and xylene (6.87 g, 3.7 wt%) were added into a 250 mL stainless steel can, where the mixture was first slowly stirred by a high-speed disperser at a speed below 1000 rpm (500–800 rpm). Then SiO2 (10.4 g, 5.6 wt%) was slowly added into the mixture, before raising the high-speed disperser's speed to 2800 rpm to disperse the mixture for 20 min with lids covering the can to avoid solvent evaporation. Afterwards, the dispersed mixture was transferred to a thermostatic water bath at a constant temperature of 25 °C for 4 h. The mixture's viscosity was measured three times by a Brookfield RVT rotational viscometer immediately after being removed from the thermostatic water bath, using Spindle No. 4 at a rotational speed of 30 rpm under 25 °C. Then, the mixture was diluted with extra xylene (59.92 g, 32.3 wt%), before being dispersed by the high-speed disperser at a speed of 2800 rpm for 10 min with lids covering the can. After all the bubbles inside the diluted mixture resulted from the high-speed dispersion had disappeared in 2 h, its average particle size was measured three times by a Zehntner ZGR 2021 grindometer.
3. Results and discussion
The three polymeric dispersant structural types of AB diblock, ABA triblock and comb copolymers were designed and synthesised, which are shown with SiO2 particle dispersion in a schematic representation in Scheme 1.
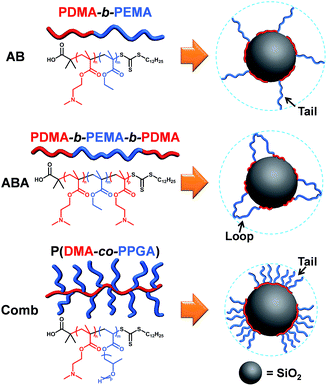 |
| Scheme 1 Schematic representation of SiO2 particle dispersion by AB diblock, ABA triblock and comb copolymer dispersants. | |
The general synthetic strategies of these three dispersant structural types are depicted in ESI.† The number averaged molecular weight (Mn) and polydispersity index (PDI) of all the prepared polymeric dispersants were estimated from 1H NMR and GPC measurements, which were used to determine their molecular structures and compositions (see Table S1†).
3.1 Structural optimisation of AB diblock copolymer dispersants
AB diblock copolymers were designed and optimised first, in order to determine the most effective anchoring and stabilising chain compositions, which were used as the basis for preparing ABA triblock and comb copolymers. Previous studies demonstrated that PDMA as an anchoring chain was effective in dispersing different kinds of organic and inorganic particles such as SiO2, iron oxide, carbon black, organic pigments and others.1,22–24 Thus, PDMA was selected as the anchoring chain (A block) for the three structural types, as its multiple tertiary amino anchoring groups can simultaneously interact with the predominant silanol functional groups on the SiO2 particle surface mainly through hydrogen bonding in organic media.40–43 Meanwhile, PEMA was chosen as the AB diblock copolymer's stabilising chain (B block), due to its low particle surface affinity and compatible solvation in the model organic media (xylene and solvent-based resin). Due to the anchoring chains' multi-point interactions with the SiO2 particle surface, they can form a robust foundation to support the stabilising chains in protruding into the bulk solution and creating steric stabilisation barriers around the particles, in order to provide sufficient steric repulsion force to avoid particle aggregation (see Scheme 1).4,37
Then, the structural compositions of AB diblock dispersants PDMA-b-PEMA (denoted as PD-b-PE) were optimised by adjusting their anchoring and stabilising chains' lengths or degrees of polymerisation (see Table S1†). After synthesis and purification, these dispersants were prepared for rheological and particle size tests, which are two of the key dispersion performance measurements. Generally speaking, after the addition of dispersants, the lower the viscosity and the smaller the particle size, the more stable the dispersion system.24,27,35 A control sample with no dispersant added was used as the basis for comparison, which has an absolute averaged viscosity of 8000 mPa s and averaged particle size of 35 μm. Fig. 1 reveals the structure–performance relationship between different PDMA degrees of polymerisation and viscosity/particle size reduction. The results initially indicated a trend with the enhancement of viscosity and particle size reduction as the polymerisation degree of PDMA increased, while keeping the stabilising chain unchanged as PEMA40. This is because as the PDMA chain grew longer, its concentration of tertiary amino groups became higher, making it easier and more tightly adsorbed onto the SiO2 surface due to stronger multi-point anchoring effect. This made the dispersants more difficult to desorb from the SiO2 surface, resulting in more stable particle dispersion, which was reflected in further reduced system viscosity and smaller particle size. However, this trend only continued until an optimal length of around 30 monomer units of PDMA was reached, before the viscosity and particle size began to increase again and became less effective with longer PDMA chain of 40 monomer units. Such phenomenon has been reported by past researchers, who found that longer anchoring chains were not necessarily more effective in particle dispersion than shorter counterparts, because shorter anchoring chains would result in higher surface density of adsorbed dispersants, which would form a denser polymeric layer on the particle surface to enhance steric stabilisation.23,24
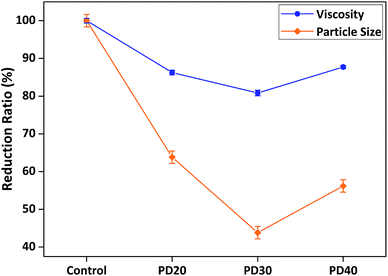 |
| Fig. 1 Structure–performance relationship between different PDMA degrees of polymerisation and viscosity/particle size reduction (all dispersants' stabilising chain fixed as PEMA40). | |
The optimisation of the AB diblock type's stabilising chain length was similar to that of its anchoring chain. Fig. 2 reveals the structure–performance relationship between different PEMA degrees of polymerisation and viscosity/particle size reduction. The results initially showed that when the dispersant's optimised anchoring chain remained unchanged as PDMA30, the longer the PEMA stabilising chain, the greater the viscosity and particle size reduction. This is because as the PEMA chains became longer, they could create thicker steric stabilisation barriers around SiO2 particles enhancing dispersion stability, which was reflected in further reduced system viscosity and finer particle size. However, this trend only continued until an optimal length of around 40 monomer units of PEMA was reached, before the viscosity and particle size started to rise again and became less effective with longer PEMA chain of 60 monomer units. This can be explained by possible “bridging flocculation”, as when the stabilising chains become too long, their tail conformations formed might tangle with each other and cause particle aggregation instead of dispersion.3,4 Hence, PD30-b-PE40 is the optimal AB diblock copolymer dispersant with optimised anchoring and stabilising chain length, which exhibited the most effective dispersion performance in reducing system viscosity and particle size.
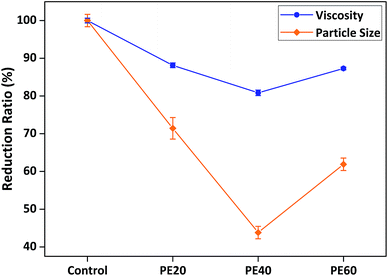 |
| Fig. 2 Structure–performance relationship between different PEMA degrees of polymerisation and viscosity/particle size reduction (all dispersants' anchoring chain fixed as PDMA30). | |
3.2 Structural optimisation of ABA triblock copolymer dispersants
ABA triblock copolymer is an extension from the AB diblock structure, where the main difference is the extra anchoring chain (A block) attached to the AB type stabilising chain's free-end (B block) (see Scheme 1). This structure allows the ABA type to form two possible adsorption conformations: when the two outer anchoring chains (A blocks) simultaneously adsorb on the same particle, loop conformation will occur with the bending of the middle stabilising chain (B block); and when one anchoring chain adsorb on one particle while the other anchoring chain adsorb on another particle, bridging conformation will occur and cause particle flocculation.3,4 Due to possible bridging conformation, the ABA type in general is not as effective as the AB type, which will predominantly exhibit tail conformation adsorption on particle surface to create steric stabilisation barrier. Nevertheless, based on the optimised results of AB type dispersants, we synthesised and characterised a series of ABA type dispersants with different anchoring and stabilising chain lengths and molecular weights (see Table S1†), before being prepared for rheological and particle size measurements.
Alike AB type dispersants, the results in Fig. 3 indicated that when the ABA type dispersants' stabilising chain remained unchanged as PEMA40, the longer the two PDMA anchoring chains on both ends, the greater the viscosity and particle size reduction until an optimal length of around 30 monomer units was reached. Similarly, when the ABA type dispersants' two anchoring chains remained unchanged as PDMA30, the longer the PEMA stabilising chain, the greater the viscosity and particle size reduction until an optimal length of around 60 monomer units was reached, before the viscosity and particle size began to increase again and became less effective with longer PEMA chain of 80 monomer units. Hence, PD30-b-PE60-b-PD30 is the optimised ABA triblock copolymer dispersant, which displayed the most effective dispersion performance in lowering particle size and system viscosity.
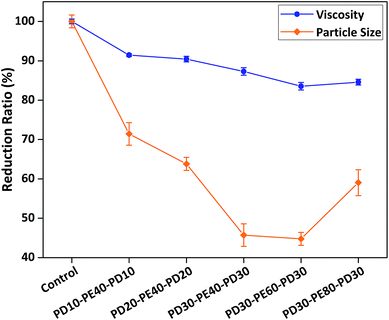 |
| Fig. 3 Structure–performance relationships between different PDMA and PEMA degrees of polymerisation and viscosity/particle size reduction. | |
3.3 Structural optimisation of comb copolymer dispersants
Different to the AB diblock and ABA triblock copolymers, comb copolymers have multiple anchoring groups along their backbone with pendant side branches acting as stabilising chains (see Scheme 1). This unique structure allows comb copolymers to predominantly exhibit multiple tail conformation adsorptions on particle surface forming steric stabilisation barriers.3,4 Based on the optimised results of AB and ABA type dispersants, we further synthesised and characterised a series of comb copolymer dispersants with different chain lengths and degrees of polymerisation (see Table S1†), before being prepared for rheological and particle size measurements.
For comparison reasons, the comb copolymers' anchoring backbone chain was fixed as PDMA30, the same as the optimised AB and ABA type dispersants. With this, the results in Fig. 4 indicated that the higher the polymerisation degree of PPGA stabilising side chains, the greater the viscosity and particle size reduction, due to denser steric stabilisation barriers formed resulting in more stable particle dispersion. However, this trend only continued until an optimal polymerisation degree of around 15 PPGA monomers was reached, before the viscosity and particle size started to increase and became less effective with higher amount of 20 PPGA monomer units. Hence, P(D30-co-PPGA15) is the optimised comb copolymer dispersant, exhibiting the most effective dispersion performance in reducing system viscosity and particle size.
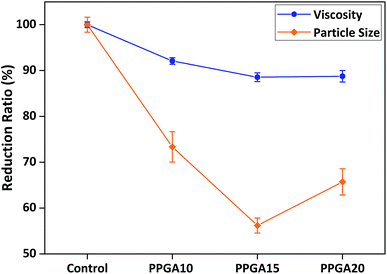 |
| Fig. 4 Structure–performance relationship between different PPGA degrees of polymerisation and viscosity/particle size reduction (all dispersants' anchoring chain fixed as PDMA30). | |
3.4 Structure–performance comparisons between AB, ABA and comb copolymer dispersants
After the systematic structural optimisation of AB diblock, ABA triblock and comb copolymer dispersants, we compared the optimised dispersants of each structural type and also with two commercial acrylic block copolymer dispersants (EFKA-4310 and BYK-2008) in dispersion performance. Fig. 5 reveals that all three types of optimised dispersants performed better than the two commercial dispersants in lowering system viscosity, yielding smaller particle size and producing more stable SiO2 particle dispersion. Meanwhile, the optimised AB type (PD30-b-PE40) and ABA type (PD30-b-PE60-b-PD30) dispersants were more effective in viscosity and particle size reduction than the optimised comb dispersant (P(D30-co-PPGA15)).
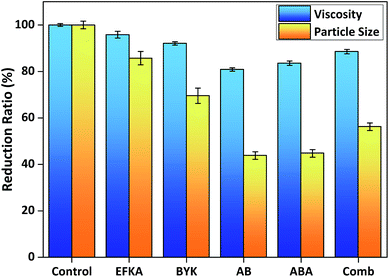 |
| Fig. 5 Dispersion performance comparison between AB diblock, ABA triblock, comb and commercial polymeric dispersants (EFKA: EFKA-4310; BYK: BYK-2008; AB: PD30-b-PE40; ABA: PD30-b-PE60-b-PD30; comb: P(D30-co-PPGA15)). | |
This is further demonstrated by SEM characterisation in Fig. 6, which displays the morphology of dispersed SiO2 particles in xylene. It is evident that the SiO2 particles agglomerated together without any dispersion in the control sample with no added dispersant (Fig. 6(a)). In comparison, after the optimised AB, ABA and comb copolymer dispersants were added into the system, the aggregated SiO2 particles were effectively dispersed (Fig. 6(b)–(d)). More specifically, the AB and ABA type dispersants resulted in almost monodispersed particle dispersion, which were more homogeneous than the comb dispersant. These were further supported by examining another particle type – mesoporous silica nanoparticles (MSNs),44,45 which showed similar results in dispersion performance (see Fig. S4†). Although the comb dispersant would form tail conformation adsorption on particle surface similar to the AB type dispersant, it is more entropically unfavourable to expose the anchoring groups along its backbone facing the particle surface while rearranging its pendant stabilising side chains pointing outwards. Hence, steric stabilisation barriers created by the comb copolymer were less stable than those formed by the block copolymers, thus weaker in dispersion stability.
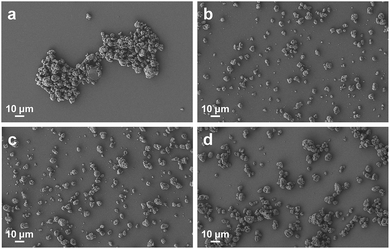 |
| Fig. 6 SEM images of dispersed SiO2 particles in xylene: (a) control sample without dispersant; (b) AB diblock: PD30-b-PE40; (c) ABA triblock: PD30-b-PE60-b-PD30; (d) comb: P(D30-co-PPGA15). | |
Additionally, the difference in the three dispersant types' dispersion effectiveness may also be explained by the structure–performance relationship between the “blockiness” of their comonomer distribution and their dispersion performance. In fact, previous studies found that copolymers were more effective dispersants if their comonomer distributions were more “blocky”.3,4 The comb copolymer lacked “blockiness” in its random comonomer distribution, where the anchoring DMA monomer units were distributed randomly along its backbone with some gaps between successive units, which weakened the anchoring groups' multi-point interactions with the particle surface compared to the uniform anchoring chains of AB and ABA type copolymers. Hence, as the AB and ABA type copolymer dispersants are more “blocky”, they are generally more effective in particle dispersion than the analogous comb copolymer dispersants.
Meanwhile, an interesting observation from Fig. 5 and 6 reveals that the optimised AB diblock (PD30-b-PE40) and ABA triblock (PD30-b-PE60-b-PD30) dispersants have rather similar effectiveness in viscosity and particle size reduction, perhaps with the AB diblock being slightly better in viscosity reduction. This implies that although the risk of the ABA type dispersant's possible bridging conformation in causing particle agglomeration could not be precluded, the dispersion stability from its predominant loop conformation was comparable in effectiveness to the AB type dispersant's tail conformation, as both loop and tail conformations are effective in producing steric stabilisation barriers.4,35,38 Thus if the ABA triblock structure is carefully designed and optimised according to the dispersion system, it can be as effective as the AB diblock structure in particle dispersion. However, the bending of ABA type's middle stabilising chain when forming loop conformation will result in an extra entropic penalty that must be compensated by the adsorption energy provided by the two outer anchoring chains, which must supply sufficient anchoring strength to prevent desorption from the particle surface. The bending of the middle stabilising chain will also result in thinner steric stabilisation barrier, thus reduced dispersion stability, compared to that of AB type with the same stabilising chain length, which can fully extend into the solvent medium. Hence as a general guideline, AB diblock copolymer dispersants are at least as effective as or better than their ABA triblock equivalents in particle dispersion and stabilisation. Therefore, the structure–performance relationship between the three dispersant types' molecular structure and dispersion effectiveness can be ordered as: AB ≥ ABA > comb.
Furthermore, there are also similarities in structure–performance relationships between the three dispersant types' anchoring and stabilising chain length, composition and dispersion performance. As demonstrated before, under the same stabilising chain, as their anchoring chain lengthened, there were more anchoring groups simultaneously interacting with the particle surface, allowing dispersants to adsorb more rigidly on the particles and resulting in enhanced dispersion stability, which was reflected in finer particle size and reduced system viscosity. However, this trend only continued until an optimal length of anchoring chain was reached, before the dispersion performance became less effective with longer chains. Similarly, under the same anchoring chain, as the dispersants' stabilising chain length increased, they could provide thicker steric stabilisation barriers around the particles, which were more effective in preventing aggregation, thus forming more stable particle dispersion. However, this trend also only continued until an optimal length of stabilising chain was reached, before the dispersion effectiveness weakened with longer chains, due to possible bridging flocculation.
4. Conclusions
Overall, through RAFT polymerisation, a series of AB diblock, ABA triblock and comb copolymer dispersants with different anchoring and stabilising chain lengths and compositions were synthesised and characterised. These three structural types were systematically optimised and compared in dispersion performance, in order to develop structure–performance relationships. It was found that the dispersion effectiveness of the three structural types can be ordered as: AB ≥ ABA > comb. Specifically, the optimised AB diblock (PD30-b-PE40) and ABA triblock (PD30-b-PE60-b-PD30) dispersants were more effective in reducing system viscosity and particle size of SiO2 than the comb dispersant (P(D30-co-PPGA15)) and two commercial polymeric dispersants (EFKA-4310 and BYK-2008). Moreover, AB diblock copolymer dispersants are generally at least as effective as or better than their ABA triblock equivalents in particle dispersion. These results can provide constructive guidelines for the design and selection of polymeric dispersants' molecular architectures and structural compositions for effective particle dispersion and stabilisation in organic media.
Acknowledgements
This study was financially supported by the National Natural Science Foundation of China (Project No. 51573086) and the special fund of State Key Joint Laboratory of Environment Simulation and Pollution Control (No. 15K07ESPCT).
References
- H. Zou, S. Wu and J. Shen, Chem. Rev., 2008, 108, 3893–3957 CrossRef CAS PubMed.
- B. I. Kharisov, R. Dias, O. V. Kharissova, A. Vazquez, Y. Peña and I. Gómez, RSC Adv., 2014, 4, 45354–45381 RSC.
- T. Tadros, Adv. Colloid Interface Sci., 2009, 147–148, 281–299 CrossRef CAS PubMed.
- T. F. Tadros, Applied Surfactants: Principles and Applications, WILEY-VCH Verlag GmbH & Co. KGaA, Weinheim, 2005 Search PubMed.
- C. Dai, S. Wang, Y. Li, M. Gao, Y. Liu, Y. Sun and M. Zhao, RSC Adv., 2015, 5, 61838–61845 RSC.
- Y. H. Lai, M. C. Kuo, J. C. Huang and M. Chen, Mater. Sci. Eng., A, 2007, 458, 158–169 CrossRef.
- X. K. Ma, N. H. Lee, H. J. Oh, J. W. Kim, C. K. Rhee, K. S. Park and S. J. Kim, Colloids Surf., A, 2010, 358, 172–176 CrossRef CAS.
- J. S. Wang and K. Matyjaszewski, J. Am. Chem. Soc., 1995, 117, 5614–5615 CrossRef CAS.
- T. E. Patten, J. Xia, T. Abernathy and K. Matyjaszewski, Science, 1996, 272, 866–868 CAS.
- K. Matyjaszewski and J. Xia, Chem. Rev., 2001, 101, 2921–2990 CrossRef CAS PubMed.
- K. Matyjaszewski, Macromolecules, 2012, 45, 4015–4039 CrossRef CAS.
- Y. Yang, J. Wang, J. Zhang, J. Liu, X. Yang and H. Zhao, Langmuir, 2009, 25, 11808–11814 CrossRef CAS PubMed.
- J. Chiefari, Y. K. Chong, F. Ercole, J. Krstina, J. Jeffery, T. P. T. Le, R. T. A. Mayadunne, G. F. Meijs, C. L. Moad, G. Moad, E. Rizzardo and S. H. Thang, Macromolecules, 1998, 31, 5559–5562 CrossRef CAS.
- G. Moad, E. Rizzardo and S. H. Thang, Polymer, 2008, 49, 1079–1131 CrossRef CAS.
- G. Moad, E. Rizzardo and S. H. Thang, Aust. J. Chem., 2012, 65, 985–1076 CrossRef CAS.
- Y. Guo, H. Liu, D. Tang, C. Li and Y. Zhao, Polym. Chem., 2015, 6, 2647–2658 RSC.
- V. Sciannamea, R. Jérôme and C. Detrembleur, Chem. Rev., 2008, 108, 1104–1126 CrossRef CAS PubMed.
- J. Nicolas, Y. Guillaneuf, C. Lefay, D. Bertin, D. Gigmes and B. Charleux, Prog. Polym. Sci., 2013, 38, 63–235 CrossRef CAS.
- M. Vamvakaki, G. F. Unali, V. Bütün, S. Boucher, K. L. Robinson, N. C. Billingham and S. P. Armes, Macromolecules, 2001, 34, 6839–6841 CrossRef CAS.
- N. H. Raduan, T. S. Horozov and T. K. Georgiou, Soft Matter, 2010, 6, 2321–2329 RSC.
- C. J. Chang, S. J. Chang, K. C. Shih and F. L. Pan, J. Polym. Sci., Part B: Polym. Phys., 2005, 43, 3337–3353 CrossRef CAS.
- Z. Wang, Q. Liu, H. Zhu, H. Liu, Y. Chen and M. Yang, Carbon, 2007, 45, 285–292 CrossRef CAS.
- C. Auschra, E. Eckstein, A. Mühlebach, M. O. Zink and F. Rime, Prog. Org. Coat., 2002, 45, 83–93 CrossRef CAS.
- K. H. Kuo, Y. H. Peng, W. Y. Chiu and T. M. Don, J. Polym. Sci., Part A: Polym. Chem., 2008, 46, 6185–6197 CrossRef CAS.
- H. Yin and Y. Feng, RSC Adv., 2016, 6, 79943–79951 RSC.
- Y. Yang, L. Liu, J. Zhang, C. Li and H. Zhao, Langmuir, 2007, 23, 2867–2873 CrossRef CAS PubMed.
- R. Vestberg, A. M. Piekarski, E. D. Pressly, K. Y. Van Berkel, M. Malkoch, J. Gerbac, N. Ueno and C. J. Hawker, J. Polym. Sci., Part A: Polym. Chem., 2009, 47, 1237–1258 CrossRef CAS.
- D. Astruc, E. Boisselier and C. Ornelas, Chem. Rev., 2010, 110, 1857–1959 CrossRef CAS PubMed.
- Z. Deng, L. Wang, H. Yu, X. Zhai and Y. Chen, RSC Adv., 2016, 6, 27682–27689 RSC.
- W. Yuan, Z. Zhao, J. Yuan, S. Gu, F. Zhang, X. Xie and J. Ren, Polym. Int., 2011, 60, 194–201 CrossRef CAS.
- J. Loiseau, N. Doerr, J. M. Suau, J. B. Egraz, M. F. Llauro and C. Ladaviere, Macromolecules, 2003, 36, 3066–3077 CrossRef CAS.
- P. L. Golas, S. Louie, G. V. Lowry, K. Matyjaszewski and R. D. Tilton, Langmuir, 2010, 26, 16890–16900 CrossRef CAS PubMed.
- T. Lee, B. Kim, S. Kim, J. H. Han, H. B. Jeon, Y. S. Lee and H. J. Paik, Nanoscale, 2015, 7, 6745–6753 RSC.
- T. Lee, J. Park, K. Kim, A. K. Mohanty, B. Kim, J. H. Han, H. B. Jeon, Y. S. Lee and H. J. Paik, RSC Adv., 2015, 5, 69410–69417 RSC.
- F. Touaiti, P. Alam, R. Nilsson, M. Pahlevan, M. P. Ansell, C. E. Wilén and M. Toivakka, Prog. Org. Coat., 2013, 76, 439–446 CrossRef CAS.
- L. Zheng, M. Zhou, Q. Yan and J. Yuan, Prog. Chem., 2009, 21, 1389–1397 CAS.
- B. Faure, G. Salazaralvarez, A. Ahniyaz, I. Villaluenga, G. Berriozabal, Y. R. D. Miguel and L. Bergström, Sci. Technol. Adv. Mater., 2013, 14, 301–304 CrossRef PubMed.
- Y. M. Chen, R. S. Hsu, H. C. Lin, S. J. Chang, S. C. Chen and J. J. Lin, J. Colloid Interface Sci., 2009, 334, 42–49 CrossRef CAS PubMed.
- J. T. Lai, D. Filla and R. Shea, Macromolecules, 2002, 35, 6754–6756 CrossRef CAS.
- L. Zhou, W. Yuan, J. Yuan and X. Hong, Mater. Lett., 2008, 62, 1372–1375 CrossRef CAS.
- S. C. Jana and S. Jain, Polymer, 2001, 42, 6897–6905 CrossRef CAS.
- X. Yang, T. Dai and Y. Lu, Polymer, 2006, 47, 441–447 CrossRef CAS.
- A. Perro, S. Reculusa, E. Bourgeat-Lami, E. Duguet and S. Ravaine, Colloids Surf., A, 2006, 284–285, 78–83 CrossRef.
- T. Wang, M. Wang, C. Ding and J. Fu, Chem. Commun., 2014, 50, 12469–12472 RSC.
- C. Y. Hong, X. Li and C. Y. Pan, J. Mater. Chem., 2009, 19, 5155–5160 RSC.
Footnote |
† Electronic supplementary information (ESI) available: Synthetic procedures and schemes of ABA triblock and comb copolymers, 1H NMR spectra and GPC characterisation of all synthesised polymers. See DOI: 10.1039/c6ra25196j |
|
This journal is © The Royal Society of Chemistry 2017 |
Click here to see how this site uses Cookies. View our privacy policy here.