DOI:
10.1039/C7PY00047B
(Paper)
Polym. Chem., 2017,
8, 2010-2015
Facile conversion of plant oil (anethole) to a high-performance material†
Received
10th January 2017
, Accepted 20th February 2017
First published on 20th February 2017
Abstract
Anethole, a naturally occurring aromatic compound which can be extracted abundantly from plants like star anise, fennel and basil, has been conveniently transformed to a functional monomer in an overall yield of 81% via a two-step procedure. The obtained monomer combines reactive benzocyclobutene and propylene groups, thus it can undergo thermo-polymerization to form a crosslinking network, showing a low dielectric constant (<2.64 in a range of frequencies varying from 0.1 to 30 MHz) and low water uptake (<0.20% in boiling water for 144 h). TGA and DSC data exhibit that the cross-linked network has a 5 wt% loss temperature of 455 °C in N2 and a Tg of 160 °C, respectively. These results indicate that the new polymer based on biorenewable anethole is comparable to the materials derived from petroleum. On the basis of the wide application of low dielectric constant materials in the microelectronic industry, this work would offer a new sustainable feedstock to organic low k materials. Moreover, this contribution also provides a new route to convert other aromatic natural products.
Introduction
Recently, approaches to make the best use of renewable biomass resources rather than traditional petrochemical raw materials have attracted much attention,1–5 as a result of the rapidly decreasing store of fossil oil. Among those approaches, many efforts have been made in the investigations of polymeric materials derived from biomass. It is expected that the polymers from bio-resources could possess the same or even better performance than the traditional petroleum-based materials.6–8 Of various biomasses, those having aromatic skeletons9–13 are particularly gathering interest from industry because they can be converted to materials with excellent thermo-mechanical properties. A typical example is the conversion of lignin, a kind of branched macromolecule with a polyphenolic network structure.14,15 Until now, it has been well researched and transformed to many useful polymeric materials.16–20 Nevertheless, most natural biomasses with aromatic units are still difficult to convert to polymerizable monomers. Hence, investigation on the handy conversion of biomasses with aryl units is desirable.
It is to be noted that anethole, a naturally existing aromatic compound, has a very simple and interesting chemical structure (see Scheme 1), which is extracted abundantly from star anise, tarragon, fennel and basil.21 Because of its fragrance and high volatility, anethole has been widely used as a perfume in cosmetics, and a flavoring agent in foods and non-alcoholic beverages.22 Moreover, this plant oil has been also used as a feedstock for the synthesis of many fine chemicals such as p-methoxybenzaldehyde23 and p-anisic acid.24 In recent years, the investigation on the application of anethole in polymeric materials has received much attention.25–27 However, most of the investigations employ complicated procedures for the synthesis of suitable monomers based on anethole. Thus, developing a simple and convenient route for the conversion of anethole to valuable polymers is very necessary.
 |
| Scheme 1 The procedure for the conversion of anethole. | |
It is well known that polymers based on benzocyclobutene possess good thermo-stability and good mechanical properties,28–30 and they have been recognized as one of the best candidates for high performance materials in microelectronic applications. Considering that benzocyclobutene has a tendency to form a highly reactive o-quinodimethane at high temperature which can react with vinyl groups, we thus designed a new monomer having both an anethole moiety and a benzocyclobutene unit (see Scheme 1). For the synthesis of the monomer, a two-step procedure was employed. Firstly, the methoxy group in anethole was transformed to hydroxyl in the presence of sodium dodecyl mercaptan,31 and secondly the produced propylene phenol was then reacted with bromobenzocyclobutene to give a functional monomer.32 Upon heating, the monomer was easily converted to an infusible and insoluble resin through a ring-opening reaction of the benzocyclobutene unit. The obtained resin showed a low dielectric constant (Dk) and high thermostability. These results indicate that the resin is comparable to petroleum-based materials and has potential application in the microelectronic industry. Here, we report the details.
Experimental
Materials
All solvents and reagents were commercially available and used as received. Anethole was purchased from Nanjing Chemlin Chemical Industry Co., China. 4-Bromo-benzocyclobutene was purchased from Chemtarget Technologies Co., China. Other reagents were purchased either from Sigma Aldrich or TCI.
Measurements
1H NMR and 13C NMR spectra were recorded on a JEOL ECZ400 NMR spectrometer. High resolution mass spectra (HRMS) were recorded on a DARTSVP mass spectrometer. Fourier transform infrared spectra (FT-IR) were obtained on a Nicolet spectrometer with KBr pellets. Differential scanning calorimetry (DSC) curves were collected with a TA Instrument of DSC Q200 at a heating rate of 10 °C min−1 under a nitrogen flow. Dynamic mechanical analysis (DMA) was performed with a heating rate of 3 °C min−1 in air on the Mettler Toledo DMA/SDTA861e instruments. Thermo-gravimetric analysis (TGA) was performed under a nitrogen atmosphere on a NETZSCH TG 209 apparatus at a heating rate of 10 °C min−1 from room temperature to 1000 °C. Dielectric properties of cured samples with an average diameter of 10.0 mm and an average thickness of 4.2 mm were characterized by using a 4294A Precision Impedance Analyzer (Agilent) at room temperature.
Synthesis of (E)-4-propenyl phenol (B)
To a mixture of C12H25SNa (113.50 g, 506 mmol) and NMP (300 mL), anethole (50.00 g, 337 mmol) was added dropwise with vigorous stirring at room temperature. Then the mixture was allowed to heat to 130 °C and kept at that temperature for 18 h. The solvent was removed in a vacuum. The residue was neutralized to pH < 7 by using a diluted hydrochloric acid solution and extracted with ethyl acetate (3 × 100 mL). The combined organic layer was washed with brine, dried over anhydrous Na2SO4 and filtered. The filtrate was concentrated, and the obtained residue was purified by column chromatography using a mixture of ethyl acetate and petroleum ether (1
:
20, v/v) as the eluent. (E)-4-Propenyl phenol was obtained as a white solid in a yield of 96%. 1H NMR (400 MHz, CDCl3): δ = 7.20 (d, J = 7.7 Hz, 2H), 6.75 (d, J = 7.4 Hz, 2H), 6.32 (d, J = 15.7 Hz, 1H), 6.15–6.01 (m, 1H), 4.97 (s, 1H), 1.85 (d, J = 6.6 Hz, 3H). 13C NMR (101 MHz, CDCl3): δ = 154.5, 131.1, 130.3, 127.2 (2C), 123.7, 115.5 (2C), 18.5. HRMS-EI (m/z): Calcd C9H10O [M]+ 134.0732; Found 134.0730. Anal. Calcd C9H10O: C, 80.56; H, 7.51; Found: C, 80.28; H, 7.52.
Synthesis of monomer M-BCB
A mixture of (E)-4-propenyl phenol (5.00 g, 37 mmol), KOH (3.14 g, 56 mmol), DMF (80 mL) and toluene (20 mL) was heated to reflux and maintained at that temperature for 5 h. In that case, the water generated during the reaction was removed using Dean–Stark apparatus via an azeotropic toluene–water mixture. After being cooled to room temperature, CuI (0.71 mg, 3.7 mmol), 1-butyl imidazole (0.49 mL, 3.7 mmol) and 4-bromobenzocyclobutene (8.87 g, 48 mmol) were added to the flask under an argon atmosphere. The mixture was heated to 140 °C and kept at that temperature for 24 h in argon. After cooling to room temperature, the mixture was poured into 100 mL of water and extracted with ethyl acetate (3 × 100 mL). The organic layer was combined, washed with saturated aq. NaCl solution, dried over anhydrous Na2SO4, and filtered. The crude product was concentrated and purified by column chromatography using petroleum ether as the eluent. The target product was obtained as a colorless liquid with a yield of 84%. 1H NMR (400 MHz, CDCl3): δ = 7.27 (dd, J = 11.6, 9.0 Hz, 2H), 6.99 (d, J = 7.9 Hz, 1H), 6.93–6.87 (m, 2H), 6.85 (dd, J = 8.0, 2.1 Hz, 1H), 6.74 (d, J = 1.7 Hz, 1H), 6.35 (dd, J = 15.7, 1.3 Hz, 1H), 6.21–6.05 (m, 1H), 3.13 (s, 4H), 1.86 (dd, J = 6.6, 1.5 Hz, 3H). 13C NMR (101 MHz, CDCl3): δ = 157.1, 156.5, 146.8, 140.5, 132.8, 130.3, 127.1 (2C), 124.6, 123.9, 118.6, 118.4 (2C), 114.5, 29.2, 29.0, 18.6. HRMS-EI (m/z): Calcd C17H16O [M]+ 236.1201; Found 236.1205. Anal. Calcd C17H16O: C, 86.40; H, 6.82; Found: C, 86.27; H, 6.70.
Preparation of cured sample
Approximately one gram of monomer was placed in a flat-bottom glass tube, which was kept at 70 °C in a vacuum for 0.5 h to remove residual solvent. Then the tube was filled with argon and slowly heated to 200 °C and kept at that temperature for 6 h. After cooling to room temperature, the tube was moved to a quartz tube furnace. The furnace was then maintained at 200 °C for 1 h, 220 °C for 2 h, and 250 °C for 4 h, respectively. A fully cured cylinder sample thus was prepared, which was then used for the measurements of dielectric properties and water uptake.
Measurement of water uptake
A cured sample (PM-BCB) with an average diameter of 10.0 mm and an average thickness of about 1.0 mm was dried in vacuo until a constant weight (0.0001 g) was achieved. The sample was then immersed in boiling water and kept at the boiling temperature for an appropriate time. After being taken out of the water, the water residue on the surface of the sample was removed with filter paper. The sample was weighed, and its water uptake was calculated based on the increase of its weight after immersion in the boiling water. The final data were obtained from the average results of measurements of 5 samples.
Results and discussion
Synthesis and characterization of the new monomer based on anethole
The procedure for the synthesis of the new monomer M-BCB is shown in Scheme 1. As can be seen in Scheme 1, M-BCB is prepared by a two-step route. Firstly, anethole is converted to the intermediate (E)-4-propylenephenol (B) by removing the methyl group, and then the intermediate B is treated with bromobenzo-cyclobutene to yield the target monomer. For the conversion of anethole into the intermediate, most of the Lewis or Brønsted acids can be used to remove the methyl group.27 However, in our case, both CF3SO3H and a solution of BF3 in ether gave a polymer accompanying the removal of the methyl group. Even the use of a solution of HBr in acetic acid also made anethole form a polymer. Such results indicate that the propylene group in anethole is sensitive to both Lewis and Brønsted acids. Fortunately, when sodium dodecyl mercaptan was used, anethole was transformed to 4-propylenephenol in an almost quantitative yield. The obtained phenol was further incorporated into 4-bromocyclobutene by means of the Ullmann coupling reaction (see Scheme 1). In the presence of a ligand (1-butyl imidazole), M-BCB was obtained in a yield of 84%. Interestingly, in the absence of the ligand, M-BCB was prepared with a low yield (about 60%), suggesting that the ligand was necessary for the etherification reaction between phenols and halogenated aromatic compounds.
The obtained M-BCB is a colorless liquid with low viscosity and soluble in most of the common organic solvents, implying its good processability. The chemical structure of M-BCB was confirmed by its 1H NMR, 13C NMR spectra, HR-MS and elemental analysis. The detailed data are depicted in the Experimental section, and shown in the ESI.† As an example, Fig. 1 shows the 1H NMR spectrum of M-BCB. Typically, the peak at 3.1 ppm is attributed to the H at the cyclobutene group of benzocyclobutene,33 and the peaks in a range of chemical shifts from 6.1 to 6.4 ppm are derived from the H at the vinyl group in M-BCB.31 Hence, all data are in accordance with the proposed structure of M-BCB.
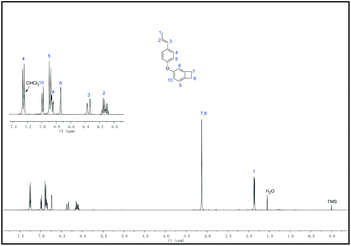 |
| Fig. 1
1H NMR spectrum of M-BCB (400 MHz, CDCl3). | |
Thermo-crosslinking reaction of M-BCB
At high temperature, the four-membered-ring on benzocyclobutene has a tendency to produce a highly reactive o-quinodimethane intermediate. This intermediate then reacts with the vinyl groups or itself to form copolymers.34 In our case, such a thermo-crosslinking reaction of M-BCB was monitored by DSC, and the results are shown in Fig. 2. As depicted in Fig. 2, M-BCB shows an onset temperature of 193 °C and gives a maximum exothermic peak temperature at 257 °C. Such a curing behavior of M-BCB is similar to that of the benzocyclobutene-based polymers or monomers, suggesting that the thermo-crosslinking of M-BCB is caused by the ring-opening reaction of benzocyclobutene. In the second scan, no obvious exothermic peak can be observed, indicating that the thermo-crosslinking reaction of M-BCB has completed. The cross-linked M-BCB (PM-BCB) is pale yellow and transparent (see Fig. 3), as well as hard but not brittle. It is also observed from Fig. 2 that the PM-BCB exhibits a glass transition temperature (Tg) at near 160 °C. Dynamic mechanical analysis (DMA) shows that PM-BCB has a Tg of about 189 °C (see Fig. S8 in the ESI†). Such a Tg of PM-BCB is higher than that of PMMA (105 °C),35 and poly-carbonates (150 °C),36 implying good heat resistance of the polymer obtained.
 |
| Fig. 2 DSC traces of M-BCB in N2 with a heating rate of 10 °C min−1. | |
 |
| Fig. 3 An image of the PM-BCB sample. | |
It was found in our previous work that the propylene group in anethole was much more inert,27 which made anethole unable to be thermally polymerized. It inspires us to investigate whether the propylene group in M-BCB reacts with the o-quinodimethane intermediate or not. For this purpose, a comparable 4-propyl substituted substance M1 was synthesized (Scheme 2, the synthesis is described in the ESI†).
 |
| Scheme 2 Chemical structure of the comparable compound. | |
By using the same procedure as that of treating M-BCB, M1 was heated to 250 °C and kept at that temperature for 4 h to give a sticky yellow liquid PM1, which was easily dissoluble in common organic solvents such as toluene, hexane and ethyl acetate. In contrast, thermally treated M-BCB turned out to be a pale yellow solid (Fig. 3), which was insoluble and infusible. In fact, there is only one functional group of benzocyclobutene in M1, thus heating it only gives the products that are derived from the reaction of the o-quinodimethane intermediate with itself. DSC analysis of M1 shows that the exothermic enthalpy is 106.2 kJ mol−1 (Fig. S9†), which is much lower than that of M-BCB (169.5 kJ mol−1, see Fig. 2). Consequently, the propylene group in M-BCB does participate in the thermo-crosslinking reaction.
The thermo-crosslinking reaction of M-BCB was monitored by FT-IR spectroscopy. Fig. 4 shows the difference in FT-IR spectra between M-BCB and thermo-crosslinked M-BCB (PM-BCB). As seen from Fig. 4, the characteristic peaks at 965 cm−1 and 1657 cm−1, attributed to the trans di-substituted alkene,37 disappeared after thermo-crosslinking. Moreover, the peaks at 924 and 1467 cm−1, ascribed to the four-member ring of the benzocyclobutene group,33 vanished in PM-BCB, suggesting the complete cross-linking of the monomer.
 |
| Fig. 4 FT-IR spectra of M-BCB and PM-BCB. | |
Thermostability of PM-BCB
The thermostability of PM-BCB was evaluated by thermogravimetric analysis, and the results are depicted in Fig. 5. PM-BCB has a 5 wt% loss temperature of about 455 °C, and exhibits a maximum weight loss temperature at 503 °C. These data are comparable to commonly used high-performance materials, such as epoxy and Novolac resins.38,39
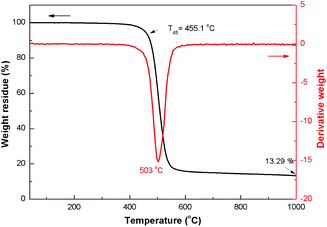 |
| Fig. 5 TGA curves of PM-BCB in N2 with a heating rate of 10 °C min−1. | |
Dielectric properties and water uptake of the thermo-crosslinked M-BCB
Benzocyclobutene-based polymers have been widely used as low Dk materials in the microelectronic industry. In our case, Dk of PM-BCB, which contains a biomass content of 56%, was measured via the standard capacitance method.40 As illustrated in Fig. 6, an average Dk of PM-BCB remains below 2.64 with an average dissipation factor (Df) of less than 2 × 10−3 in a range of frequencies from 0.1 to 30 MHz. These data are comparable to that of mostly used low-k materials, such as SiLK resins (k = 2.65),41 and polybenzoxazoles (k = 2.81).42
 |
| Fig. 6 Dielectric properties of PM-BCB. | |
The water uptake of PM-BCB was carried out by immersing it into boiling water and keeping it at the boiling temperature for an appropriate time. The results of the water uptake of PM-BCB samples at a certain period time are summarized in Table 1. As can be seen from Table 1, PM-BCB has a water uptake of below 0.20 wt% (kept in boiling water for 144 h), which is better than that of Kapton, a famous commercial polyimide used as the insulating coating in industry, which shows water absorption of 0.74%.43 The contact angle of water on PM-BCB sample was measured. The average contact angle of water is 94° (Fig. S11†), suggesting the good hydrophobic properties of PM-BCB. Such good hydrophobicity leads to a low water uptake of PM-BCB, which can enhance the endurance of the material for utilization under moist conditions.
Table 1 Water uptake of P1 measured in boiling water
Time (h) |
6 |
12 |
24 |
48 |
120 |
144 |
Water uptake (%) |
0.19 |
0.19 |
0.19 |
0.19 |
0.19 |
0.19 |
The above-mentioned results demonstrate that PM-BCB mainly derived from biomass has a similar performance to the full petroleum-based materials in the terms of high thermo-stability, good dielectric properties and low water uptake, implying that the polymer has potential application in the microelectronic industry.
Conclusions
In summary, we have successfully transformed anethole to a functional monomer in high yield through a two-step procedure. The obtained monomer contains active benzocyclobutene and propylene groups, thus it can thermally polymerize to form a crosslinking network, showing low Dk, high thermostability and low water uptake. These data exhibit that the new polymer based on biorenewable anethole is comparable to the petroleum-based materials. Thanks to the wide application of low k materials in the microelectronic industry, this work may provide a new sustainable feedstock supply of organic low k materials. Furthermore, our facile method is also suitable for the conversion of other naturally occurring β-methylstyrenes such as isosafrole, methyl isoeugenol, and acetyl isoeugenol.
Acknowledgements
This work is carried out under financial support from the National Natural Science Foundation of China (NSFC No. 21374131, 21574146, and 21504103), the Ministry of Science and Technology of China (2011ZX02703 and 2015CB931900), the Strategic Priority Research Program of the Chinese Academy of Sciences (Grant XDB 20020000) and the Science and Technology Commission of Shanghai Municipality (15ZR1449200 and 16JC1403800).
Notes and references
- A. Gandini, Macromolecules, 2008, 41, 9491–9504 CrossRef CAS.
- R. T. Mathers, J. Polym. Sci., Part A: Polym. Chem., 2012, 50, 1–15 CrossRef CAS.
- S. A. Miller, ACS Macro Lett., 2013, 2, 550–554 CrossRef CAS.
- C. Vilela, A. F. Sousa, A. C. Fonseca, A. C. Serra, J. F. J. Coelho, C. S. R. Freire and A. J. D. Silvestre, Polym. Chem., 2014, 5, 3119–3141 RSC.
- T. Iwata, Angew. Chem., Int. Ed., 2015, 54, 3210–3215 CrossRef CAS PubMed.
- M. A. R. Meier, J. O. Metzger and U. S. Schubert, Chem. Soc. Rev., 2007, 36, 1788 RSC.
- P. Gallezot, Catal. Today, 2011, 167, 31–36 CrossRef CAS.
- A. Llevot, P. K. Dannecker, M. von Czapiewski, L. C. Over, Z. Soyler and M. A. Meier, Green Chem., 2016, 22, 11510–11521 CAS.
- P. Buono, A. Duval, P. Verge, L. Averous and Y. Habibi, ACS Sustainable Chem. Eng., 2016, 4, 5212–5222 CrossRef CAS.
- K. Ranathunge, L. Schreiber and R. Franke, Plant Sci., 2011, 180, 399–413 CrossRef CAS PubMed.
- J. Zhang, J. Li, Y. Tang, L. Lin and M. Long, Carbohydr. Polym., 2015, 130, 420–428 CrossRef CAS PubMed.
- S. Hong, K.-D. Min, B.-U. Nam and O. O. Park, Green Chem., 2016, 18, 5142–5150 RSC.
- A. Maneffa, P. Priecel and J. A. Lopez-Sanchez, ChemSusChem, 2016, 9, 2736–2748 CrossRef CAS PubMed.
- C. Xu, R. A. Arancon, J. Labidi and R. Luque, Chem. Soc. Rev., 2014, 43, 7485–7500 RSC.
- M. Fache, E. Darroman, V. Besse, R. Auvergne, S. Caillol and B. Boutevin, Green Chem., 2014, 16, 1987–1998 RSC.
- F. G. Calvo-Flores and J. A. Dobado, ChemSusChem, 2010, 3, 1227–1235 CrossRef CAS PubMed.
- A. L. Holmberg, N. A. Nguyen, M. G. Karavolias, K. H. Reno, R. P. Wool and T. H. Epps III, Macromolecules, 2016, 49, 1286–1295 CrossRef CAS.
- A. L. Holmberg, K. H. Reno, N. A. Nguyen, R. P. Wool and T. H. Epps III, ACS Macro Lett., 2016, 5, 574–578 CrossRef CAS PubMed.
- A. L. Holmberg, J. F. Stanzione, R. P. Wool and T. H. Epps, ACS Sustainable Chem. Eng., 2014, 2, 569–573 CrossRef CAS.
- T. Yoshida, R. Lu, S. Han, K. Hattori, T. Katsuta, K.-I. Takeda, K. Sugimoto and M. Funaoka, J. Polym. Sci., Part A: Polym. Chem., 2009, 47, 824–832 CrossRef CAS.
- H. Ullah and B. Honermeier, Ind. Crops Prod., 2013, 42, 489–499 CrossRef CAS.
- A. Zeller, K. Horst and M. Rychlik, Chem. Res. Toxicol., 2009, 22, 1929–1937 CrossRef CAS PubMed.
- S. Lai and D. G. Lee, Synthesis, 2001, 1645–1648 CrossRef CAS.
- S.-i. Hirashima, Y. Kudo, T. Nobuta, N. Tada and A. Itoh, Tetrahedron Lett., 2009, 50, 4328–4330 CrossRef CAS.
- M. C. Davis, A. J. Guenthner, T. J. Groshens, J. T. Reams and J. M. Mabry, J. Polym. Sci., Part A: Polym. Chem., 2012, 50, 4127–4136 CrossRef CAS.
- M. C. Davis, A. J. Guenthner, C. M. Sahagun, K. R. Lamison, J. T. Reams and J. M. Mabry, Polymer, 2013, 54, 6902–6909 CrossRef CAS.
- F. He, Y. Gao, K. Jin, J. Wang, J. Sun and Q. Fang, ACS Sustainable Chem. Eng., 2016, 4, 4451–4456 CrossRef CAS.
- S. Tian, J. Sun, K. Jin, J. Wang, F. He, S. Zheng and Q. Fang, ACS Appl. Mater. Interfaces, 2014, 6, 20437–20443 CAS.
- F. He, J. Wang, Y. Luo, J. Sun and Q. Fang, Macromol. Chem. Phys., 2015, 216, 2302–2308 CrossRef CAS.
- J. Wang, I. Piskun and S. L. Craig, ACS Macro Lett., 2015, 4, 834–837 CrossRef CAS.
- J. A. Dodge, M. G. Stocksdale, K. J. Fahey and C. D. Jones, J. Org. Chem., 1995, 60, 739–741 CrossRef CAS.
- H. Rao, Y. Jin, H. Fu, Y. Jiang and Y. Zhao, Chem. – Eur. J., 2006, 12, 3636–3646 CrossRef CAS PubMed.
- J. Tong, S. Diao, K. Jin, C. Yuan, J. Wang, J. Sun and Q. Fang, Polymer, 2014, 55, 3628–3633 CrossRef CAS.
- J. Wang, Y. Luo, K. Jin, C. Yuan, J. Sun, F. He and Q. Fang, Polym. Chem., 2015, 6, 5984–5988 RSC.
- H. Wang, T. Chang, X. Li, W. Zhang, Z. Hu and A. M. Jonas, Nanoscale, 2016, 8, 14950–14955 RSC.
- F. Hacıoğlu, T. Özdemir, K. G. Kinalır and A. Usanmaz, Prog. Nucl. Energy, 2016, 90, 98–104 CrossRef.
- S. B. Halligudi, N. K. Kala Raj, R. Rajani, I. R. Unni and S. Gopinathan, Appl. Catal., A, 2000, 204, L1–L5 CrossRef CAS.
- W. Liu, Z. Wang, L. Xiong and L. Zhao, Polymer, 2010, 51, 4776–4783 CrossRef CAS.
- S. Ghosh and M. Acharyya, RSC Adv., 2016, 6, 28781–28786 RSC.
- Y. Luo, K. Jin, C. He, J. Wang, J. Sun, F. He, J. Zhou, Y. Wang and Q. Fang, Macromolecules, 2016, 49, 7314–7321 CrossRef CAS.
- S. J. Martin, J. P. Godschalx, M. E. Mills, E. O. Shaffer and P. H. Townsend, Adv. Mater., 2000, 12, 1769–1778 CrossRef CAS.
- J. Wu, Y. Xi, G. T. McCandless, Y. Xie, R. Menon, Y. Patel, D. J. Yang, S. T. Iacono and B. M. Novak, Macromolecules, 2015, 48, 6087–6095 CrossRef CAS.
- F. Bellucci and L. Nicodemo, Corrosion, 1993, 49, 235–247 CrossRef CAS.
Footnote |
† Electronic supplementary information (ESI) available. See DOI: 10.1039/c7py00047b |
|
This journal is © The Royal Society of Chemistry 2017 |
Click here to see how this site uses Cookies. View our privacy policy here.