DOI:
10.1039/C7GC01719G
(Paper)
Green Chem., 2017,
19, 4380-4395
Environmental impact assessment of wheat straw based alkyl polyglucosides produced using novel chemical approaches†
Received
12th June 2017
, Accepted 21st July 2017
First published on 18th August 2017
Abstract
This paper evaluates and quantifies the environmental performance of alkyl polyglucosides sourced from wheat straw (WS-APG), a low-cost and low-ecological impact agricultural residue, compared to that of their commercial counterpart, which is sourced from palm kernel oil and wheat grain (PW-APG). Escalating pressure to consider the environmental sustainability of fossil derived surfactant consumption has driven biosurfactants to become the product of choice within the surfactant market, and a class of ‘plant’ based non-ionic surfactants called alkyl polyglucosides (APG) are particularly prevalent. However, the existing food based feedstock of APG such as coconut oil, palm oil, wheat and corn (in addition to being expensive) will potentially undermine the claimed ‘sustainability’ of the APG products (i.e. the ‘food vs. chemical’ issue). Here, we present the “cradle-to-gate” life cycle impact assessment of a suggested alternative, hybridised APG synthesis technique where the Fisher glycosidation method is supplemented by novel, green chemistry based techniques. This evaluation provides a quantitative insight into direct GHG intensity and other ecological impact indicators, including land use, waste generation and energy consumption. Upon evaluation, the wheat straw-derived pathway delivered GHG-emission savings in the range of 84–98%, compared to that of the palm kernel–wheat grain pathway. Waste generated from the production of unit mass of the product amounted to 0.43 kg and 10.73 kg per kg of WS-APG and PW-APG, respectively. In addition to the above mentioned facts, the ‘cradle–gate’ stages of WS-APG production were also found to consume relatively lower amounts of water and fossil-derived energy. In conclusion, of the two APG production pathways, the suggested ‘hybrid’ pathway using an agricultural residue, wheat straw, was found to be sustainable and to demonstrate better environmental performance.
Introduction
Alkyl polyglucosides (APGs) belong to the non-ionic group of surfactants which, unlike the majority of surfactants, are synthesised primarily from oleo-chemicals (plant derived feedstock chemicals). From 1960, the use of petrochemical surfactants declined in response to environmental (primarily due to their deleterious effect on the aquatic ecosystems) and aesthetic (foaming of surface water) concerns and the majority of personal care products, therefore, switched to oleo-chemical surfactants.1–3 The emulsifying, foaming and wetting capabilities of APG, at relatively lower temperatures, have enabled it to find application in detergents and hard-surface cleaners, laundry detergents, fabric softeners and personal care products like hair-conditioners and shampoos. Currently, APGs are synthesized via the Fischer glycosidation, which comprises a reaction between plant based fatty alcohols (typically sourced from palm or coconut oil) and carbohydrates (typically sourced from starch based sources such as wheat) in the presence of an acid resin catalyst. Commercial scale synthesis of APG began in the 1990s, with a current production of 80
000 tonnes per annum.4–6,8 The bio-surfactant market is currently worth £390 million and has been projected to grow by 4% per annum during the next ten years.3–5
APGs, within the overall biosurfactant market, have been realised only recently for their relatively potent nature and application in high value final products. Therefore, a very limited number of studies exist which evaluate their environmental performance.1,6,7 These studies entail the assessment of techno-economically optimised life cycle processes of APG synthesised from palm-kernel oil or coconut oil (as the fatty alcohol source) and wheat grain or corn starch (as the sugar source).1,6,7 Techno-economic studies undertaken by Hirsinger et al.6 and Stalmans et al.7 on a wide range of surfactants provided limited clarity on APGs, unlike the life cycle assessment of palm kernel and wheat grain-derived APG (PW-APG) by Guilbot et al.1 This study quantified the transnational “cradle to grave” environmental impact of APG sourced from palm kernel oil and wheat starch, focusing on impact categories appropriate for industrial biomass utilisation and conversion. According to this study, the amount of GHG emissions produced via the baseline APG production pathway is 12.3 g CO2 eq. per g of PW-APG, where land-use was determined to be the highest emission contributor, accounting for 15% to 51% of the total emissions depending on the nature of the soil type adopted. Moreover, the overall impact was determined to be influenced by the degree of APG incorporation into the final formulation.
The aim of the analysis presented is to quantify the environmental impact of the use of a low-cost agricultural residue, wheat straw, as an alternative to conventional crops, for the synthesis of APG (WS-APG), through the life cycle assessment (LCA) approach from a “cradle–gate” perspective. Life cycle assessment is a technique applied to quantify and analyse the environmental impact embedded in a process or a product from raw material acquisition to the end-of-life phase, depending on the product's functionality. This technique offers the analyst the flexibility to draw the extent of analysis via pre-conception of a system boundary. The ISO guided-life cycle assessment is a robust impact and sustainability assessment tool finding wider application in this era of circular economy. Therefore, this analysis in particular adheres to the EN 16760:2015 guidelines and requirements for life cycle assessment of bio-based products.
For the purpose of establishing the environmental sustainability of the WS-APG production pathway, a life cycle assessment of the commercial techno-economically optimised PW-APG production studied by Guilbot et al.1 has been chosen as the baseline case. From a process perspective, the novelty of the WS-APG pathway lies in the application of green techniques including low temperature microwave extraction and the use of supercritical CO2, in contrast to the baseline study. Supercritical CO2 extraction is not only environmentally benign but an economically feasible process for feedstock preparation.9 However, the Fischer glycosidation is the chosen method of APG synthesis in both cases. In comparison with other LCA studies, which compared a bio-based product with a conventional petrochemical or non-biological counterpart,11–13 this paper compares the environmental impact of two biologically-sourced surfactants. This paper, in addition to acknowledging the level of detail captured in the baseline study, also aims to bridge some gaps within the same. This paper, in addition to detailing the usage of indicators, also determines the GHG emissions related to both wheat and oil palm cultivation stemming from different land cover changes and biogenic CO2 uptake based on the product composition. This study mainly captures a key impact indicator which is of significance to the principle of green chemistry, the waste-factor (measured as kg of waste per g of the product), and allocates GHG emissions under different scenarios, in compliance with the EN 16760:2015 for bio-based products, in contrast to the baseline case.1
Methodology
For brevity, in the upcoming sections, APG synthesised from wheat straw will be referred to as WS-APG and the affiliated process will be referred to as the “analysis process”; APG synthesised from palm kernel oil and wheat grain will be referred to as “PW-APG” which will represent the comparative “baseline process” for the analysis case.
Scope
This study encompasses the “cradle (raw material acquisition) to gate (product distribution from factory gates)” stages of the two APG processes. The analysis process is assessed at the present time and is geographically restricted to the UK.
For the purpose of this study, a dedicated LCA model was developed (refer to Appendix 1.1†). The emission inventories of materials and energy in this model are populated with data sourced from publicly available databases (e.g. Ecoinvent 2.2, Biograce, 2013) and national inventories14–16 and regional life cycle assessments.1,6,7,10,12,13
Details of the full chemical process of synthesising WS-APG were established prior to conducting the LCA. A “cradle to grave” life process of the analysis and baseline APG production is mapped [as presented in Appendix 1.3†]. A “cradle–gate” process map for WS-APG and PW-APG has been provided in Fig. 1 and 2, which also gives elaborate information on the material/energy inputs, products, resulting wastes and emissions.
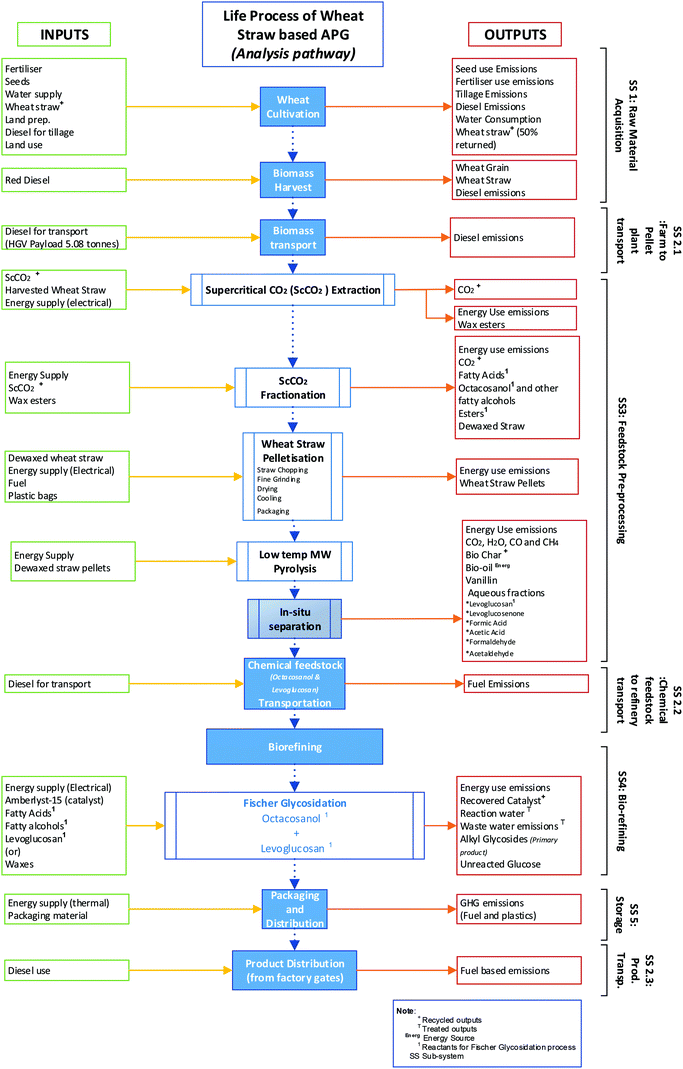 |
| Fig. 1 Cradle–gate life cycle stages for WS-APG production. | |
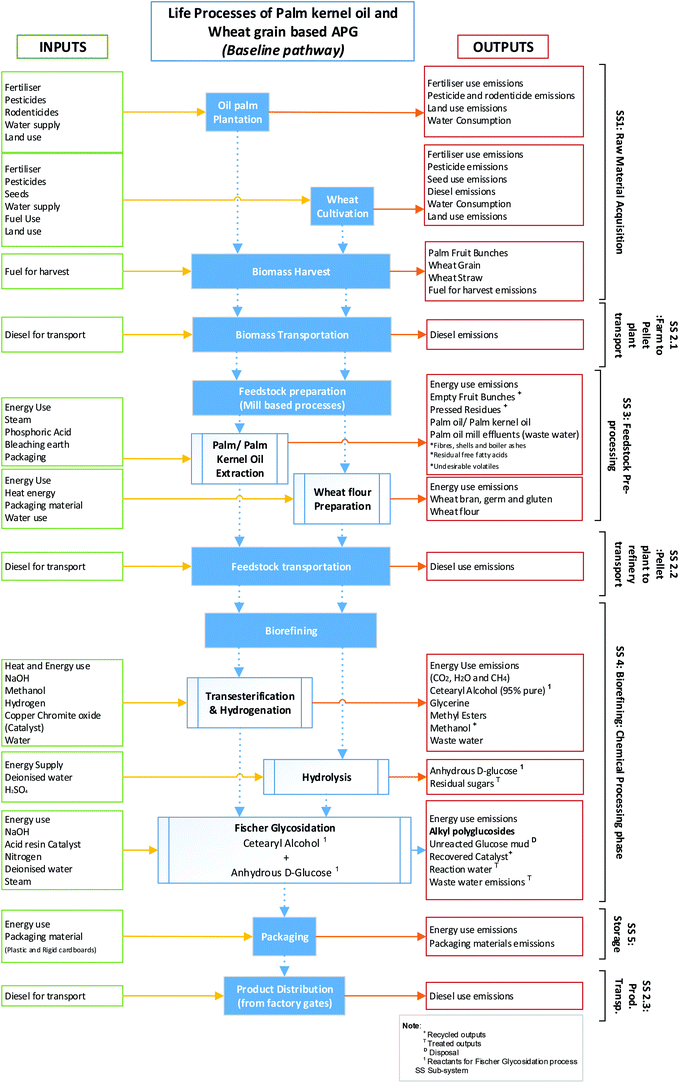 |
| Fig. 2 Life cycle system for PW-APG synthesis (source: ref. 1). | |
In addition to the environmental indicators, this study aims to quantify a key parameter which addresses one of the underpinning principles of green chemical pathways, the waste-factor [waste factor, a ratio of the mass of waste generated per functional unit (kg g−1 of APG)]. The fate of the waste generated at each of the stages of WS-APG has also been accounted, unlike the baseline study.1 To quantify and append the environmental impact to a given product, ISO 14044 standards suggest the definition of a functional unit which for this study will be 1 g of APG and will be used to quantify the impact using the following environmental indicators.
• Direct GHG emissions (g CO2 eq. per g of APG)
• Land use change & emissions (g CO2 eq. per g of APG)
• Fossil derived energy footprint (kW h g−1 of APG)
• Water consumption (m3 g−1 of APG)
• Waste-factor (kg of waste per g of APG)
To quantify the impact of the analysis and baseline processes, according to these indicators, a life cycle inventory of WS-APG17,18 and PW-APG1 was developed from the available literature and through personal communication. In the case where data availability is a constraint, appropriate assumptions have been adopted to allow indicators to be calculated and uncertainties arising from these assumptions have been dealt with in associated sensitivity analyses.
The methods of impact quantification and allocation, the relevant assumptions adopted within these models and sensitivity assessments are presented under appropriate methods. Quantities of the material, energy input, products, wastes and emissions fed and resulting from each of the life cycle stages have been captured under the respective ‘methodology’ segments. Information on the data source (life cycle inventory), and the model developed to undertake this assessment are listed in the Appendix 1.1 and 1.2.†
Wheat straw.
Straw from winter wheat is cultivated on established cropland with appropriate pesticide, fertiliser and manure application and no land use change (LUC) emission is assumed for the default scenario. Since, in the UK, water needs of winter wheat cultivation are largely fulfilled by rainfall, only limited irrigation is required. See Table 1 for a summary of the parameters used. As a waste material, a decision on how to allocate emissions to the biomass cultivation stage is non-trivial. Three possible scenarios are presented below. These scenarios involve partitioning of GHGD between wheat straw and wheat grain based on mass and economic significance.
Table 1 Biomass cultivation: material inputs and yield characteristics
Parameters |
Units |
Values |
Source |
WS – wheat straw.
Assumed based on current agronomic practices in the UK (see source).
At 85% dry matter.
|
Acreage |
ha |
1 |
|
Seeds |
kg ha−1 |
185 |
1, 23 and 24
|
Diesel |
l ha−1 |
73 |
1, 12, 23 and 24
|
Electricity |
kW h ha−1 |
6.25 |
1, 12, 23 and 24
|
Pesticides |
kg ha−1 |
2.5 |
1, 12, 23 and 24
|
Irrigation water |
m3 ha−1 |
0.38 |
1, 12, 23 and 24
|
Fertilisers |
N fertiliser |
kg ha−1 |
196 |
1, 12, 23 and 24
|
P fertiliser |
kg ha−1 |
45 |
|
K fertiliser |
kg ha−1 |
65.2 |
|
Compost |
kg ha−1 |
15 000 |
1, 12, 23 and 24
|
Grain yield21,22 |
kg ha−1 |
7920 |
12, 19 and 20
|
% WSa recovered |
% |
50b |
23 and 25
|
% WS re-incorporated into the soil |
% |
50 |
|
Straw yield |
kg ha−1 |
3500 |
23 and 26
|
Net mass of WSc |
kg ha−1 |
2975 |
— |
Scenario 1: Wheat straw as a low value “residue”
Conventionally (and as assumed in previous studies1,6,13), emissions associated with biomass (wheat straw) cultivation are solely allotted to wheat grain since the primary purpose of cultivating the crop is for obtaining the grain. Straw is considered an agricultural residue with limited value.
Scenario 2: Adding economic value to the feedstock (scenario of choice)
Rather than a true ‘waste’ material, wheat straw is demanded in various other sectors, including animal husbandry and energy generation. Since the purpose of this study is to add economic value to an “agricultural residue”, we allocate GHGD per hectare from both analysis and baseline studies, according to their economic significance. Based on the price of straw and grain, in Sept. 2015,26 17.7% of the total cultivation emissions were allocated to wheat straw and 82.3% to wheat grain.
Scenario 3: Mass of feedstock generated
Scenario 3 allocates emissions between the grain and straw based on the total harvestable mass fraction of the respective agricultural product. In the case of winter wheat, the mass of straw generated (after 50% of the straw is re-incorporated into the soil) is estimated to be 3500 kg ha−1, which amounts to 21% by mass of the total saleable mass (grain and straw).
Oil palm.
The baseline study assumes that fatty alcohols are sourced from oil palm1 and, specifically, palm kernel rather than the fruit. A hectare of oil palm plantation is assumed to yield 20–23 tonnes of fresh palm fruits, which themselves yield approximately 750–850 kg of seed kernels.
Biomass harvest
Upon maturity, wheat grain is combine-harvested and the wheat straw is left on the field for further drying before it can be harvested, baled and sold. In line with current UK agricultural practices, we assume that 50% of wheat straw is harvested and the rest is ploughed back into the soil.
Material consumption.
GHG emissions within this stage are calculated by multiplying the quantities of materials and energy used by their respective emission factors (EFs) (kg CO2 eq. per unit). Emission factors for UK-based commodities and services are adopted from the Department for the Environment, Food and Rural Affairs (DEFRA). The empirical approach to calculate these parameters have been presented in the ESI.†
Direct N2O emissions.
Direct N2O emissions, common in agricultural practices, are attributable to the use of N-fertilisers. These emissions are quantified as N2O-N, which refers to the amount of nitrous oxide bound to the nitrogen component of the fertiliser. N2O emissions are influenced by a number of factors (refer to Appendix 1.4† for further assumptions on these factors) including weather patterns, soil properties and the local agricultural practices.
Since in-depth analysis and quantification of N2O emissions fall outside the scope of analysis, potential N2O emissions from UK agricultural soils were adopted from the Home Grown Cereals Authority (HGCA).24,27–29
Energy use emissions.
Energy use contributes emissions from the consumption of power generated from fossil-derived energy sources. Electricity-related GHGD can be predicted using the emission factor (EF) for electricity attributable to the national average ‘mix’ and the empirical method used to predict this parameter has been presented in the ESI (Appendix 1.1†).
Emission factor related to the UK average energy mix was adopted from the DEFRA GHG emission inventory14 to calculate an electricity based GHGD of 36.4 g CO2 eq. per kW h. For the baseline case, the Indonesian average energy mix was independently calculated from national statistics15 to be 85.3 g CO2 eq. per kW h.
Water consumption.
Direct GHG emissions associated with irrigation in the UK were calculated directly using the associated emission factors from DEFRA.14 Since the emissions associated with irrigation of the baseline crop (oil palm) in Indonesia are unavailable, emissions were predicted using the method of Rothausen and Conway.31 According to this study, lifting of 1 kg of water (assuming a water density of 1000 kg m−3) up to 1 m at an efficiency of 98% using diesel for energy produces 0.654 g CO2 eq. Due to being known parameters, an empirical technique for the calculation of GHGD associated with material and energy consumption has been presented in the ESI† for the reader's reference.
Post-harvest activities
According to a study by Glithero et al.25 approximately 50% of the agricultural residue (wheat straw) in Yorkshire and Humber, UK, is harvested and the rest is returned back to the soil. Therefore, this study assumes 50% of the total wheat straw from the field to be harvested, baled, roughly weighing 300 kg each, and transported to the pelleting facility.
The GHGD attributable to biomass cultivation and harvest (Gross biom_cultGHG) is the sum of energy, material and water requirements attributable to a hectare of plantation. The calculated overall emissions are converted into the functional unit of this study. Please note that the emission associated with the feedstock harvest is also included within this parameter.
Bio-sequestration
Bio-sequestration is a phenomenon where plant photosynthesis or other biological processes capture atmospheric CO2 and store it in plant matter and soil. This biogenic CO2 that is sequestered by the biomass during the cultivation process will be referred to as biomass credit. Besides APG, excess quantities of industrially significant levoglucosan and a soil conditioning, high-quality biochar are produced as by-products of the analysis process. Thus, the mechanism by which WS-APG can be credited with bio-sequestration involves the assumption of utilising biochar for soil conditioning in addition to wheat straw incorporation. Biochar, the residual carbon of wheat straw that has been pyrolysed via low temperature microwave, is capable of storing carbon for at least a 1000 years.34
To precisely predict the quantity of CO2 contained within the by-product biochar, the following factors must be first defined.32 These factors have been indicated and the figures assumed for each of the factors have been presented below:
| BiocharCO2 = [WS.BioChm × CCWS-BioCh] × 3.664 | (1.1) |
where Biochar
CO2 = Carbon sequestered per unit biomass (kg CO
2.ha
−1yr
−1); WS.BioCh
m = Total mass of wheat straw-derived biochar (kg); CC
WS-BioCh = Carbon content of wheat straw derived biochar (%); 3.664 = C to CO
2 conversion factor suggested by IPCC.
40
The quantity of CO2 that could potentially be sequestered via re-incorporation of activated wheat straw (biochar) into the soil can be predicted using eqn (1.2).
|  | (1.2) |
where Biom_C is biomass credit (g CO
2 eq. per g APG); Bio-char
CO2 is carbon sequestered per unit biomass (kg CO
2 per ha per year); Harvt. bio_m is the total harvestable biomass per unit area (kg ha
−1); FU
biomass is the biomass required to synthesise 1 g of APG.
The predicted biomass credit (Biom_C) is deducted from the overall cultivation and harvest emissions (Gross biom_cultGHGD) to give the net GHGD for this stage.
| Net biom\_cultGHGD = (Gross biom\_cultGHGD) − Biom\_C | (2) |
Land use
Land use change emissions (LUE) are calculated as kg CO2 eq. per g of feedstock and then converted into the functional unit of this analysis (g CO2 eq. per g of APG). A brief description of the calculations and the associated assumptions is presented in the following sections.
Wheat straw.
Wheat straw is generated as a by-product of wheat grain production. Wheat, in the UK, is cultivated on croplands which were originally natural lands (temperate forests) converted for agriculture. Since the precise time of conversion is unknown, land use change emissions predicted are conventionally allocated to wheat grain,1,12,37 considering that the conversion occurred for food crop cultivation, potentially thousands of years ago.
Oil palm.
Oil palm cultivated in Indonesia has been adopted for LUE analysis.1 Oil palm is a perennial crop which is cut down for fresh plantation (to boost the active growth and yield of the area of land) approximately every 25 years. Though the baseline study has focused on the oil palm that is sourced from a mature plantation, a sensitivity analysis to identify the relative impact of this feedstock when established on land converted from tropical forest peatlands has not been undertaken. In this study, LUE for oil palm are economically allocated between palm oil and palm kernel oil [note: the market price of palm fruit and palm kernel, as of Sept. 2015,10 is £440.55 per tonne and £472.48 per tonne, respectively. Therefore, the fraction of allocation designated to palm fruit and kernel is 48.3% and 51.7% respectively].
The land use emissions attributable to the analysis and baseline feedstocks have been predicted using a tool called “Direct land use change assessment tool, Version 2013.1” developed by Blonk Consultants, Netherlands.35 This model predicts the land use emissions based on the difference in carbon stock between a given area (ha) of natural land and transformed land. The method to quantify the organic carbon content of soil/vegetation before and after land conversion is prescribed in PAS 2050-1.35,38
In the land use emission estimation tool, the emissions are amortised over the period of crop-cultivation. The period of amortisation is dependent on the original land cover and crop-type (emissions to the transformed land). In line with the British Standards Institute and the European Parliament recommendations, we assume an amortisation period of 20 years38,39 with a linear rate of carbon decay over 20 years. Other assumptions associated with this tool used to calculate the direct GHG emissions from natural land conversion can be found in Appendix 1.5.† For the reader's information, however, it has been briefly described below.
Estimation of land use factors.
The global regions have been classified based on their climatic conditions and soil type which have been provided in Appendix 1.5.† The land use emission tool enables the selection of variables according to the country and the crop cultivated. A weighted average of the two major top soil/climate types attributable to the chosen country is considered alongside default factors for land use, land management and input factors of the transformed land which have been prescribed for the analysis and baseline crops by Eggleston et al.40 The standard soil organic carbon stock (SOCST) of the original land belonging to the UK and Indonesia is predicted. Further information on the calculation of the various parameters leading to the quantification of CSactual and CSref.veg has been presented in the ESI Appendix 1.5.†
Land Use Change emissions attributable to the chosen crop in a chosen world region, established on a chosen natural land area, where the emissions are amortised over 20 years, are calculated as shown in eqn (3)46,47
| LUE (t CO2 per ha per year) = [CSactual − CSref.veg] − 3.664 × 1/20 | (3) |
where 3.664 refers to the C to CO
2 conversion factor suggested by IPCC.
40
Land use scenario.
A sensitivity analysis for the different land type scenarios, attributable to the candidate APGs, was undertaken. Conventionally, wheat is cultivated on established croplands and expansion of its cultivated area in the UK is highly unlikely. Oil palm, on the other hand, is cultivated on a mixture of established croplands, converted grasslands and converted tropical peat forests in Indonesia. However, to accommodate the potential demand, expansion of the two feedstock crops on three different natural-land types is considered:
• Palm oil (baseline)
■ Tropical moist peat forests
■ Fertile tropical grasslands
■ Perennial croplands (i.e. conversion from existing tropical croplands)
• Wheat (analysis)
■ Fertile temperate grasslands
■ Cold temperate forests
■ Annual croplands (i.e. conversion from existing temperate croplands)
In scenario A (grassland to plantation), potential conversion of natural grasslands (and their carbon stock) to crop lands is considered. Scenario B (forests to plantation) is primarily devoted to a potential scale-up situation, when there is an increase in demand for WS-APG. For the default scenario, however, wheat was assumed to be cultivated on previously established grasslands.
Stage 2: Commodity transportation
To calculate emissions for the transport of feedstock from the field to the pre-processing plant, GHGD from fuel combustion is calculated based on the fuel consumed, which in turn is estimated as a function of the vehicle's payload and distance. Transportation emissions (g CO2 eq. per g of APG) can be predicted using pre-determined EFs per tonne kilometre. Consideration of payload, as a parameter, has significant impacts on the estimation of transport emissions. This study assumes transportation of primary and secondary products derived from the original feedstock that is produced from one hectare of wheat or palm, as a starting point. Transportation emissions are allocated over the shipped mass of products, therefore, the higher the payload, the lower the transportation emission. This assumption facilitates the calculation of the highest possible transportation emissions for individual life stage, while we acknowledge that in ‘real-world’ production systems, the payload is likely to be economically optimised and thus is likely to reduce transportation emissions. The implications of this assumption have been discussed further in the upcoming section. Due to being known parameters, the empirical technique used to calculate the GHGD associated with transportation of commodities between the different facilities has been presented in Appendix 1.1 of the ESI.†
Sub-stage 2.1: Farm to pre-processing plant.
The harvested and baled wheat straw from a plantation is assumed to be transported to a pelleting factory located in the UK via diesel-operated trucks. This facility is assumed to be located at a distance of 150 km from the plantation. Individual UK based vehicular EFs were adopted from the DEFRA emission factor repository.14 The baseline study (APG from palm kernel and wheat grain) assumes that the fresh fruit bunches and wheat grains are transported from the plantation to the pre-processing plant using appropriate diesel-operated trucks over a distance of 50 km and 150 km, respectively. The GHG emissions associated with this parameter will be denoted Transp. (F–P)GHG.
Sub-stage 2.2: Pre-processing plant to refinery.
Within the WS-APG supply chain, products of pre-processing phase, octacosanol and levoglucosan (production details elaborated below) are assumed to be transported to a refinery located at a distance of 150 km using a low-sulphur diesel operated truck. The GHG emissions released as a part of this life stage will be denoted by Transp. (P–R)GHG for both the baseline and analysis processes.
The baseline study assumes that refined palm kernel oil from an oil mill is freighted by sea to a refinery located in Marseille (Europe) at a distance of 11
000 km and then to Germany by train (1100 km). Wheat starch from the wheat mill is transported to a refinery via rail over a distance of 100 km. The functional unit chosen for this study determines the GHG intensity of the corresponding products and if the relative yield of product from one feedstock is higher than its counterpart, the yield is likely to neutralise the emissions from transportation.
Sub-stage 2.3: Product distribution.
The final product of the analysis process, wheat straw based alkyl polyglucosides (WS-APG), is an intermediate product which is eventually incorporated into other products (e.g. cosmetics, detergents, and domestic cleaners). The destination from onward processing is assumed to be located at a distance of 150 km within the UK and transportation is assumed to be through a diesel-operated truck. The baseline study has adopted a very similar assumption. The emission released at this life stage of both the analysis and baseline APG is denoted by Transp. (R–S.i)GHG where “S.i” refers to a secondary industry where this intermediate product will be utilised. The sum of all the transportation emissions along the “cradle–gate” life cycle of WS-APG gives the total transportation based GHG emissions.
Stage 3: Pre-processing raw feedstock
Wheat straw.
Drying and milling.
Fresh wheat straw is assumed to be “blow dried” for which the energy consumed is dependent on the moisture content of the raw wheat straw (assumed to be 15%).33,42 After drying, the straw is milled to enable pelletisation.
Supercritical CO2 extraction of straw wax.
The key inputs of this process are the energy used for the conversion of CO2 into its supercritical form, supercritical CO2 as the solvent, and the matrix (dried and milled wheat straw) from which the wax esters are to be fractioned. For the preparation of feedstock required for APG synthesis, wax is extracted from the dried and milled wheat straw via supercritical CO2 (ScCO2) extraction. Supercritical CO2 for lipid extraction is considered a green solvent owing to its non-toxic, inert and non-flammable nature, unlike its conventional counterparts (e.g. toluene and hexane), and the fact that the supercritical solvent can be recovered and re-used. This preliminary step not only facilitates the separation of valuable wax esters but also provides better access to the cellulosic components which upon activation (gradually dried) will yield valuable platform chemicals, particularly levoglucosan.
The isolated wheat straw wax is primarily composed of a mixture of lipids. The lipid of interest in this study, n-octacosanol, quantified to be 1570 ± 78 mg kg−1 of dried and milled wheat straw, is fractionated from the lipid mixture. n-Octacosanol is a straight chain 28-carbon fatty alcohol which is predominantly found in plant waxes on the cuticular surface. Octacosanol contributes the hydrophobic (water-repelling) moiety to the APG synthesised via the Fischer glycosidation process. However, transforming CO2 into its supercritical form can be energy intensive and solvent losses may also be incurred from this process.
Pelletisation.
The dried de-waxed straw is milled and bound into pellets along with binding additives (e.g. glycerol or bentonite) by passing the milled straw through a heated “die”. Our study assumes 99% conversion efficiency from wheat straw to pellets.
Low temperature MW pyrolysis.
According to the information from experimental WS-APG production obtained through personal communication17 and the literature,18,41,43 we assume that a pelleted WS sample of 175 g is thermally activated at 1200 W for 7–8 min at 130–150 °C in a microwave pyrolysis chamber, during which a range of products are isolated at varying times via in situ separation
• Aqueous fractions of organic acids and aldehydes (formic acids, formaldehyde, acetic acid and acetaldehyde);
• Anhydrous sugars (levoglucosan and small amounts of levoglucosenone) with phenols;
• A gas mixture containing hydrocarbons and exhaust products – CO2, CO and CH4 and H2O;
• Biochar and bio-oil.
In comparison with conventional pyrolysis, low temperature microwave pyrolysis aids the separation and isolation of large organic molecules bound to the matrix without degrading the quality. The main product of this sub-stage is the high value chemical levoglucosan, which is a 6-carbon organic compound.
According to Budarin and Fan (2015), roughly 30 g of levoglucosan can be extracted from 1 kg of dried pelleted wheat straw.17
Levoglucosan contributes the hydrophilic (water-attracting) moiety to APG synthesis via the Fisher glycosidation in the analysis process. Process inputs, outputs and assumptions associated with the consumption of energy and other resources across the pre-processing stages are summarised in Table 2.
Table 2 Material/energy inputs and productivity related to the pre-processing phase
Parameters |
Units |
Drying |
Milling |
ScCO2 fractionation |
Straw pelletisation |
MW pyrolysis |
The phase products a, b, c, d, and e refer to dried wheat straw, milled wheat straw, wheat wax, pelletized wheat straw and levoglucosan, respectively. Process efficiencies assigned are educated assumptions. |
Energy use |
kW h kg−1 straw |
0.062 |
0.060 |
0.096 |
0.1057 |
0.084 |
ScCO2 supply |
kg kg−1 straw |
— |
— |
2.2 |
— |
— |
ScCO2 loss |
% |
— |
— |
2 |
— |
— |
Process efficiency |
% |
99 |
98 |
98 |
98 |
|
Wax yield |
kg kg−1 straw |
— |
— |
0.02 |
— |
— |
Mass of initial feed |
kg |
3500 |
2975 |
2915 |
2857.2 |
2851.5 |
Mass of phase-product+ |
kg |
2975 a |
2915 b |
58.3 c |
2851.5 d |
102.6 e |
Sources |
— |
1, 42 |
1, 42 |
18, 17, 41 |
18, 17 |
18, 17, 42 |
Palm kernel and wheat.
Refined palm kernel oil (RPKO) and wheat starch.
Fresh palm fruits are sterilised and conveyed to the digestion unit where the kernels are separated from the fruit. Kernels are sent to the kernel crushing plant where crude kernel oil is press-extracted. Crude palm kernel oil is then thermo-chemically processed using commercially optimised techniques to produce the primary feedstock for APG synthesis, namely refined palm kernel oil (RPKO). The empty fruit bunches from which the palm fruits are isolated are assumed to be sent back to the farm for mulching and for use as a substitute for fertilisers. The crushed shells and mesocarp are assumed to be used as boiler fuels. The condensates from sterilisation, gases from boiler stacks and methane from anaerobic degradation of palm oil mill effluents in addition to the manufacturing emissions of resources used in this stage contribute to the overall environmental impact. The list of materials that feed into the baseline process for the synthesis of PW-APG and further information on the pre-processing phase and materials consumed can be found in the baseline source literature.1
Harvested wheat grains are assumed to be washed, dried and ground into flour. The wheat bran and wheat germ are isolated through sifting. The wheat flour is made into a slurry when mixed with water and is enzymatically hydrolysed, refined, evaporated and crystallised to produce anhydrous D-glucose. Anhydrous-D-glucose contributes the hydrophilic moiety to the PW-APG surfactant molecule.
Stage 4: Bio-refining: thermo-chemical conversion
The Fisher glycosidation is the chosen pathway of APG synthesis in both the baseline and analysis processes. This process involves mixture of fatty alcohols and anhydrous sugars, in the presence of acid catalyst, which when approaching equilibrium, creates linkages between the two fatty chains and sugars, resulting in the formation of anomers, isomers and acyclic compounds. At completion, unreacted glucose is assumed to be isolated through decantation and centrifugation. The unreacted glucose is destined for disposal through incineration. The target APG is purified and assumed to be pelleted and packaged for transportation to the secondary industries for the final formulation. The primary feedstock, reaction specifications, and products/by-products formed within both the analysis and baseline pathways are elaborated below.
GHGD attributable to the bio-refining stage (Bio_refGHG) is the sum of energy and material intensity attributable to the preparation of a product that is obtainable with feedstock and is applied to both the analysis and baseline pathways.
Wheat straw based octacosanol and levoglucosan.
n-Octacosanol extracted from ScCO2 fractionation of wheat straw wax and levoglucosan from low temperature microwave pyrolysis of wheat straw pellets contribute to the hydrophobic (fatty) and hydrophilic (sugar) moieties of APG, respectively. The conversion efficiency of the process is assumed to be 92% (based on a similar assumption from the baseline study1) and no catalyst is recovered. Upon the completion of the reaction, the APG molecule is diluted with water and extracted with ethyl acetate. The aqueous solution is allowed to stand at room temperature to enable evaporation of water and dried under vacuum. The process inputs for WS-APG synthesis via the Fischer glycosidation has been presented in Table 3.45
Table 3 Process-material specifications for the Fischer glycosidation to produce WS-APG
Parameters |
Units |
WS-APG |
Source.45 |
Reactants |
Fatty alcohol |
kg |
0.0028 |
Levoglucosan |
kg |
0.0009 |
Catalyst |
kg |
0.00059 |
|
Reaction medium (total pumped) |
Nitrogen |
kg |
0.00014 |
Process efficiency (assumed) |
|
% |
92 |
|
Stabilising chemical |
Ethyl acetate |
kg |
0.018 |
Water |
m3 |
0.01 |
|
Stabilising chemicals recovered |
Ethyl acetate |
% |
95 |
Water |
% |
99 |
Refined palm kernel oil based cetearyl alcohol and wheat based anhydrous-D-glucose.
According to the baseline study,1 cetearyl alcohol and glucose acquired from the pre-processing phase are subjected to glycosidation at 104 °C for 4–6 hours in the presence of the acid catalyst. The process temperature is maintained through to formulation and packaging of APG as the latter solidifies at room temperature. The energy intensity of this process has been quantified by the authors of the baseline studies to be 313 kW h per tonne of PW-APG. The unreacted sugars obtained as a waste from this process are assumed to be incinerated and other liquid effluents transferred to the local waste water treatment plant.
Stage 5: Packaging and storage
Alkyl polyglucosides solidify at room temperature and therefore, within both the analysis and baseline processes, they are assumed to be “pearlized” prior to packaging. Due to a lack of information related to scale-up, packaging and storage, APG synthesised from the pathway is assumed to follow the baseline's packaging and storage process. Both WS-APG and PW-APG are assumed to be filled into low density poly ethylene packs (LDPE) and packaged in rigid cardboard boxes.
Material quantities used within this stage of the life cycle are presented in Table 4. Packaging and storage (Pac_StorGHGD) emissions are empirically predicted according to eqn (4).
| Pac\_StorGHGD = [Stage\_materialGHGD + Stage\_energyGHGD]Pac\_Stor | (4) |
Table 4 Material and energy consumed for the packaging and storage of the finished product
Parameters |
Sub-parameters |
Units |
WS-APG |
Energy use |
|
kW h kg−1 |
1.183 |
Packaging material |
LDPE |
kg kg−1 |
9.613 |
Rigid cardboard boxes |
kg kg−1 |
3.618 |
Product – GHGD
GHGD (measured as g CO2 e per g of APG) of the WS-APG and PW-APG is predicted by summing the GHG emissions predicted at every stage. Please note that the amount of carbon sequestered has been accounted under the parameter Net biom_cultGHGD. An elaborate empirical method to calculate GHGD for the various life cycle stages has been presented in Appendix 1.1.†
Fossil-derived energy consumption
The fossil-derived energy intensity of the analysis and baseline pathways associated with the synthesis of WS-APG and PW-APG, respectively, has been evaluated. This parameter is measured as kW h g−1 of APG synthesised and, in addition to the amount of electricity consumed, the amount of fuel (diesel and heavy fuel oils) used for transportation purposes has also been captured. Besides the amount of fuel which was assumed (based on the payload capacity) for the operation of the trucks, information regarding energy inputs for the pre-processing and bio-refining stages was obtained from the technical sources responsible for the process development (GCCE and University of Liverpool).17,18,41,45 |  | (5) |
where Net biom_cultf_e is the fossil-derived energy used for biomass cultivation (kg per batch of APG); Pre_Prof_e is the fossil-derived energy used within the pre-processing stage (kg per batch APG); Bio_reff_e is fossil-derived energy within the biorefining (kg per batch APG); Pac_&_Storf_e is the fossil-derived energy used for packaging/storage of the product (kg per batch APG).
Water consumption
When considering bio-based products, it is also important to quantify the amount of water consumed towards the synthesis of each of the products. This parameter considers the use of irrigation and process water, quantified at each of the life cycle stages, is measured as m3 g−1 of the respective APG. Water related inputs for the agricultural phase were assumed based on the published literature.1,10,19 However, process related water consumption (from pre-processing up to bio-refining) was sourced from information provided by the technical team and the review of the published literature.17,18,41,45 |  | (6) |
where Net biom_cultwater is water used for biomass cultivation (kg per batch of APG); Pre_Prowater is water used within the pre-processing stage (kg per batch APG); Bio_refwater is water used within the biorefining and stabilisation of the product (kg per batch APG); Pac_&_Storwater is water used for packaging/storage of the product (kg per batch APG).
Waste factor
The amount of waste generated (including wastewater, waste heat, gaseous emissions, unfractionated microwave products, unreacted glucose and undesirable fatty esters) is quantified as kg g−1 of the WS-APG and PW-APG, based on mass balance between inputs and outputs of the respective processes. Information required to undertake this analysis was obtained from the previously published literature and personal communication with the technical team of process developers (GCCE and University of Liverpool).17,18,41,45 |  | (7) |
where Net biom_cultwaste is waste produced within the biomass cultivation stage (kg per batch of APG); Pre_Prowaste is waste produced within the pre-processing phase (kg per batch APG); Bio_refwaste is waste produced during bio-refinery (kg per batch APG); Pac_&_Storwaste is waste produced during packaging of the product (kg per batch APG).
Results & discussion
Direct GHG emissions
The quantified environmental impact of a novel pathway devised to synthesise APG from wheat straw is compared with a baseline, commercially established process where the APG is synthesised from palm kernel and wheat grain (both of which are food-crops). The environmental impact indicators quantified in this analysis are direct GHG emissions, fossil-based energy consumption, water consumption and wastes produced.
Stage 1: Raw material acquisition
Biomass cultivation and harvest.
The major sources of GHGs in the biomass cultivation and harvest stage are contributed by nitrogen fertilisers via two pathways: contribution via field based N2O emissions; and via fertiliser manufacture. The direct N2O emissions attributable to both the analysis and baseline crop established over an area of 1 ha have been predicted. Due to the relatively greater precipitation in the assumed location of North Yorkshire, cropland is located in a leach/run-off prone area. The N2O emission released from N-fertiliser mineralisation was determined to be 1582.4 kg CO2 eq. per ha per year. It is essential to note that the baseline study does not account for the amount of N released as leachate or run-off and therefore only direct emissions were compared.
Bio-sequestration.
The amount of CO2 that can be potentially sequestered into WS-biochar, via plant-derived bio-sequestration followed by low temperature microwave pyrolysis, was estimated to be −1377 kg CO2 per ha, which falls within the range of sequestration rates for winter wheat ranges of −917 to −1905.2 kg CO2 per ha depending on the soil type, local weather conditions and the crop variety.12,13,36 The amount was predicted based on the amount of carbon (% by mass of carbon) locked within biochar that could be obtained from a hectare worth of WS biomass (which results in 829.1 kg of WS-biochar) after extraction of the desirable compounds including straw wax, the sugars and the aqueous fraction. The predicted CO2 savings contribute a sequestration capacity of 83 g CO2 per kg wheat straw biochar, based on the carbon content of straw biochar reported within the literature.16 With a biomass requirement of 1.094 kg of wheat straw to produce 1 g of WS-APG, the latter acquires a biomass credit of −90.7 g CO2 per g of WS-APG. A biomass credit is not considered for palm kernel and wheat grain within the production of PW-APG, since both feedstocks are food crops and there are no recyclable products that create a carbon loop within their life cycle. The CO2 sequestration rate of wheat straw was validated with the average sequestration rate recorded from the earlier literature. The percentage difference between the calculated and recorded sequestration rates was determined to be −2.3%.
Land use change – scenario analysis.
Land-cover change (incorporated into the ‘Biomass cultivation and land use’ stage) is estimated to contribute the highest GHG emissions, followed by emissions resulting from the use of fertilisers. In order to capture this threshold for each of the candidate APG, a land-use based sensitivity assessment was undertaken. Prior to the discussion of overall emissions resulting from the life cycle of the candidate APGs, the sensitivity of biomass cultivation emissions to land use (LUC) change must be understood.
Scenario 1.
In the default scenario, wheat crop is assumed to be cultivated on previously established croplands, and therefore, the emissions were determined to be 0.0 g CO2 eq. per ha per year as the change in carbon stock is constant. This scenario cannot be applied to the baseline feedstock, palm kernel, since both the palm fruit and palm kernel are key feedstocks from this food crop.
Scenario 2.
Under this scenario, the gross emission calculated for the cultivation of winter wheat was determined to be 2537 g CO2 eq. per ha per year and was in line with findings, ranging between 2106–2700 g CO2 eq. per ha per year, from similar studies.1,19,24 The emission attributable to wheat straw based on its economic significance is 64 g CO2 eq. per kg of straw, compared to 270 g CO2 eq. per kg for the baseline (wheat grain and palm kernel) feedstock, excluding land use emissions.
Scenario 3.
The emission estimated upon mass based allocation of biomass cultivation emissions, specific to wheat straw, is 68 g CO2 eq. per kg of the feedstock (excluding land use emissions), compared to 155 g CO2 eq. per kg for the baseline (wheat grain and palm kernel) feedstock. The quantified impacts from the biomass cultivation stage have been presented in Table 5.
Table 5 GHGD attributable to candidate crop cultivation and harvest
Parameters |
Sub-parameters |
Specifications |
Units |
Wheat straw |
Wheat grain |
Oil palm |
Emission allocation undertaken based on the economic value of wheat straw at 17.7%.
Default scenario – Crop cultivated on existing croplands.
Scenario 1 – Crop cultivated on original grasslands.
Scenario 2 – Crop cultivated on original temperate or tropical forests.
Biomass credit presented only for information.
Parameters contributing to the calculation of net phase emissions.
|
GHGD |
Crop establishment |
Seed use emissions |
kg CO2 eq. per ha per year |
51.8 |
51.8 |
2.84 |
Water use emissions |
kg CO2 eq. per ha per year |
0.0057 |
0.0057 |
0.53 |
Fertilisers |
N2O induced emissions |
kg CO2 eq. per ha per year |
1582.4 |
1582.4 |
579.5 |
N |
kg CO2 eq. per ha per year |
298.4 |
298.4 |
254.54 |
P |
kg CO2 eq. per ha per year |
264.6 |
264.6 |
182.28 |
K |
kg CO2 eq. per ha per year |
30.66 |
30.66 |
79.90 |
Pesticide |
|
kg CO2 eq. per ha per year |
1.475 |
0.826 |
43.2 |
Compost |
|
kg CO2 eq. per ha per year |
150 |
150 |
0 |
Energy |
Diesel |
kg CO2 eq. per ha per year |
195.64 |
195.64 |
162.7 |
Electricity use emissions |
kg CO2 eq. per ha per year |
2.25 |
2.25 |
0.05 |
Gross Ems. |
|
kg CO2 eq. per ha per year |
2276 |
2276 |
1050 |
|
Biomass credite |
Carbon offset (by target biomass) |
|
kg CO2 per kg |
−0.083 |
0.0 |
0.0 |
|
kg CO2 per g of APG |
−0.09 |
0.0 |
0.0 |
|
Emission allocation scenarios |
Scenario 1: Straw as residuef |
|
kg CO2 per kg |
0.0 |
0.30 |
0.053 |
Scenario 2: Economic allocation |
|
kg CO2 per kg |
0.064a |
0.237 |
0.033 |
Scenario 3: Mass-based allocation |
|
kg CO2 per kg |
0.07 |
0.154 |
0.002 |
|
Land use scenarios |
Default scenariob,f |
|
kg CO2 per g of APG |
0.07 |
0.016 |
0.0002 |
Scenario Ac |
|
kg CO2 per g of APG |
0.68 |
0.055 |
−0.028 |
Scenario Bd |
|
kg CO2 per g of APG |
1.29 |
0.094 |
0.149 |
|
|
Net phase emissions (Net biom_cultGHGD) |
|
kg CO2 per g of APG |
0.070 |
0.098 |
Stage 2: Commodity transportation
The highest transportation emissions were determined for WS-APG at 0.007 kg CO2 eq. per g of WS-APG, compared to 0.0001 kg CO2 eq. per g for PW-APG. Within the analysis process, wheat straw transport from ‘farm to the pre-processing plant’ was the top GHG contributor due its bulk yet lower payload. The second highest GHG emissions resulted from the assumption of WS-APG distribution to secondary industries. GHG emission resulting from the transportation of the baseline feedstock, wheat grain and palm kernel, in comparison with the wheat straw, is relatively lower. The baseline biomass, palm kernel and wheat grain are favoured because of the ‘richness’ of the embedded chemical feedstock (i.e. fatty alcohol and starch), which will be evident from Fig. 3. Applying this scheme to the commodity transportation, in the analysis process, low payload yet space-demanding wheat straw incurs higher fuel consumption, compared to the feedstock rich palm kernel oil and wheat grain.
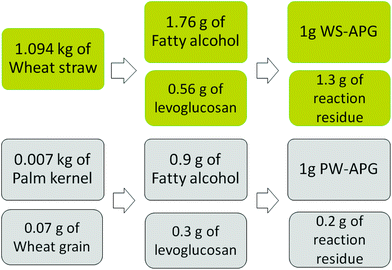 |
| Fig. 3 Quantities of feedstock (within the analysis and baseline processes) required to generate 1 g of APG. | |
Stage 3: Pre-processing raw feedstock
Pre-processing of wheat straw was found to contribute relatively higher quantities of GHG emissions via the use of energy-intensive activities, mainly straw drying, milling and pelletisation. The overall energy consumed, within the pre-processing phase, for the conversion of CO2 into its supercritical form (scCO2) for wax extraction and fractionation procedures contributed to relatively low GHG emission as the energy consumption for this process was relatively low and solvent CO2 use emissions were primarily from the process-based losses (2%) while the rest of the solvent is re-used. Refer to Table 6 for the GHGD resulting from the pre-processing phase.
Table 6 Emissions associated with the different activities of the ‘pre-processing’ phase of WS-APG, compared to that of PW-APG production
Activity |
Parameter |
Units |
WS-APG |
PW-APG |
Parameters contributing to the calculation of net phase emissions.
|
Straw drying and milling |
Energy use ems. (UK avg.) |
kg CO2 eq. per batch |
154.29 |
— |
|
ScCO2 extraction |
Net ScCO2 ems. |
kg CO2 eq. per batch |
2.65 |
— |
Process energy use ems. |
kg CO2 eq. per batch |
101.28 |
— |
|
Straw pelletisation |
Energy use ems. |
kg CO2 eq. per batch |
108.72 |
— |
|
Emissions from fatty alcohol extraction |
kg CO2 eq. per batch |
258.22 |
273.73 |
|
MW pyrolysis and in situ separation ems. |
Energy use Ems. |
kg CO2 eq. per batch |
106.35 |
— |
CO2 |
kg CO2 eq. per batch |
46.02 |
— |
H2O |
kg CO2 eq. per batch |
0.00 |
— |
CO |
kg CO2 eq. per batch |
0.04 |
— |
CH4 |
kg CO2 eq. per batch |
0.09 |
— |
Fatty alcohol |
kg per batch |
58.31 |
99.29 |
Sugars |
kg per batch |
102.6 |
4625 |
Biochar |
kg per batch |
829.06 |
— |
Aqueous fraction |
kg per batch |
179.64 |
— |
Organic acids and aldehydes |
kg per batch |
102.79 |
— |
Fatty alcohol required for 1 g of APG |
kg |
0.0017 |
0.0009 |
Sugars required for 1 g of APG |
kg |
0.00056 |
0.0001 |
|
Emissions from sugars extraction |
kg CO2 eq. per batch |
519.44 |
482.98 |
Mass based ems. allocation |
Fatty alcohola |
kg CO2 eq. per g of APG |
0.0075 |
0.0046 |
Sugarsa |
kg CO2 eq. per g of APG |
0.0000081 |
0.0002 |
|
Phase emissions (Pre_ProGHG) |
kg CO2 eq. per g of APG |
0.0075 |
0.0048 |
Stage 4: Bio-refining: thermo-chemical conversion
The bio-refining stage of WS-APG synthesis was determined to be less emission-intensive compared to that of its conventional counterpart, PW-APG. WS-APG is observed to be 15% more energy intensive than that required to carry out a similar Fisher glycosidation for PW-APG and the catalyst (sulphuric acid) losses encountered during the refining process were observed to contribute significant amounts of GHGD. However, the use of sodium hydroxide to neutralise the glycosidation reaction, in the baseline pathway, was determined to be the highest GHG emission.
Stage 5: Packaging and storage
GHG emissions attributable to packaging of APG were based on the use of packaging material which are assumed to be plastic and rigid cardboard. To be specific, the emission factors associated with packaging primarily comprise manufacturing emissions and their re-use or recyclability. Note that the packaging materials in both the cases are assumed to be recycled. Owing to a lack of equivalent information for Indonesia, DEFRA's packaging EFs were assumed for the baseline case as well. Direct GHG emissions attributable to the packaging and storage of candidate APGs were determined to be 6.2 g CO2 eq. per g of WS-APG and 6.3 g CO2 eq. per g of PW-APG, respectively. A slight difference of 0.1 g CO2 eq. per g of the product stems from the difference in the GHG emission factors accounted for the UK and European packaging.
Product life cycle GHG emission threshold
Direct GHG emissions attributable to WS-APG and PW-APG were assessed and quantified (Table 7). It is observed that overall, WS-APG was calculated to be less GHG intensive at 1.6 g CO2 eq. per g. However, the threshold of GHG intensity, contributed by factors including land use and emission allocation assumptions, needs to be determined to obtain a holistic environmental image of the candidate APGs assessed in this study.
Table 7 Direct GHG emissions from the life cycle stages of WS-APG and PW-APG (at the baseline scenario)
Life cycle stages |
GHG footprint (g CO2 eq. per g of APG) |
WS-APG |
PW-APG |
Ideally, biomass cultivation emissions attributable to wheat straw must be 0.0 g CO2 eq. per g of APG, since any GHG emissions calculated are attributable to the main product, the wheat grain.
|
Biomass cultivation |
70.2a |
16.9 |
Land use |
0.0 |
81.8 |
Transport (pre-processing) |
5.8 |
0.2 |
Pre-processing |
7.4 |
4.9 |
Transport (to refinery) |
0.4 |
0.0 |
Refining phase |
1.3 |
9.9 |
Package and storage |
6.2 |
6.3 |
Transport (from factory gates) |
1.1 |
0.0 |
Biomass credit |
−90.7 |
0.00 |
Total GHGD |
1.6 |
120.0 |
In Table 7, the GHGD of WS-APG was calculated to be 1.6 g CO2 eq. per g of the product, compared to 120 g CO2 eq. per g of PW-APG. Wheat straw derived alkyl polyglucosides were able to deliver relative GHG emission savings of up to 98.6% due to the considered biomass credit (−90.7 g CO2 eq. per g of WS-APG) from CO2 sequestration via photosynthesis.
Land use emissions attributable to wheat straw were also assumed to be 0.0 g CO2 per g of APG since no active conversion of forest land or grassland has been reported for wheat. However, GHG emissions attributable to wheat straw when cultivated on croplands converted from temperate grasslands and pristine forests would fall in the range of 68.3 and 1288 g CO2 eq. per g of WS-APG, respectively. In the baseline case (PW-APG), however, the GHGD (of 10.2 g CO2 eq. per g of PW-APG) from the lowest possible GHG emission scenario (i.e. conversion of grasslands to oil palm plantation) arises from the lack of consideration of sequestration related carbon savings. The rationale for this assumption is that the palm plantation has been established on grasslands and pristine forestland for the cultivation of palm fruits/kernel (food crops), which is also the key feedstock in the baseline process.1 The highest possible GHG emission scenario results from the assumption of oil palm cultivation on a previously pristine forest land (which is also the situation in the current ‘real-world’ production). Land use emissions attributable to the grassland and forestland conversion to oil palm fields were found to contribute −27.7 to 148 g CO2 eq. per g of PW-APG, respectively.
GHGD of WS-APG and PW-APG were quantified to fall in the ranges of 1.6–294 g CO2 eq. per g WS-APG and 10.2–264 g CO2 eq. per g of PW-APG. The source of these presented emission ranges, among the different life stages, is the biomass cultivation phase and the highest emission contributor of both WS-APG and PW-APG is land use emissions. This suggests that WS-APG is capable of delivering GHG savings by a minimum of 84%, compared to that of PW-APG. However, at the highest possible emission scenario (forest converted to plantation), wheat straw appears to produce relatively higher GHG emissions, compared to the baseline candidate (+11.36%).
Additional environmental impact indicators
Unlike conventional life cycle assessment, this paper assesses the direct environmental impact indicators including fossil-energy use, wastes generated and water consumption. The outcomes of this assessment for WS-APG and PW-APG have been presented in Table 8.
Table 8 Key environmental impact indicators for WS-APG and PW-APG production
Environmental parameter |
Units |
WS-APG |
PW-APG |
Fossil-energy use |
kW h g−1 APG |
0.269 |
18.8 |
Water consumption |
m3 g−1 APG |
0.11 |
0.33 |
Waste generated |
kg g−1 of APG |
0.43 |
10.58 |
Fossil-derived energy consumption.
PW-APG is found to be energy intensive, contributing 18.8 kW h g−1 of PW-APG, due to greater fuel consumption involving transportation of refined palm kernel oil from the pre-processing plant in Indonesia to France via a marine tanker and then to Germany via rail. Within the analysis supply chain, the biomass and chemical feedstock for WS-APG production was assumed to be locally transported via road, within the UK. The ‘refining’ stage emission, within the PW-APG production pathway, was also found to be relatively energy intensive (0.124 kW h g−1 of PW-APG) compared to 0.001 kW h g−1 of WS-APG. The stage that consumed the higher amount of energy in the WS-APG processing pathway is the biomass cultivation with fuel spent for land-preparation, fertiliser/pesticide application, harvest and electricity for irrigational purposes. The fuel and power consumption for the cultivation of biomass in the analysis case amounted to 0.127 kW h g−1 and 0.126 kW h g−1 of WS-APG, respectively. Comparatively, the fuel and power consumption for biomass cultivation for palm kernel and wheat grain amounted to 0.0067 and 0.0066 kW h g−1 of APG due to higher volumetric yield per area.
Water consumption.
As for the fossil-energy consumption results, the analysis process (WS-APG pathway) is found to be less water intensive compared to the PW-APG pathway. The most water intensive stage, within the baseline pathway, was during ‘pre-processing’ where large quantities of steam (roughly 0.31–0.32 m3 of water per g of APG) are required to deactivate the enzymes which convert the kernel oil to undesirable free fatty acids.1 Comparatively, in the analysis scenario, the pre-processing stage involved removal of water from the straw for the pelletisation and extraction of desirable compounds and does not involve water consumption. However, the WS-APG pathway utilises relatively greater amounts of water during the ‘refining’ phase (0.11 m3 g−1 of WS-APG) for the dilution and extraction of WS-APG with ethyl acetate and this water is lost via evaporation. The refining stage within the PW-APG production pathway does not involve a dilution step, and hence consumes relatively lower amounts of water (0.01 m3 g−1 of APG).
Waste generation.
Wastes generated from the baseline (PW-APG) pathway were higher than those of the analysis (WS-APG) pathway, amounting to 10.58 kg g−1 of PW-APG and 0.43 kg g−1 of WS-APG, respectively. The largest waste generating stages within the WS-APG and PW-APG production pathways were determined to be ‘pre-processing’ and ‘refining’. The most waste-intensive stage within the baseline (PW-APG) pathway was ‘pre-processing’ where a mixture of solid, gaseous and liquid wastes were generated including empty fruit bunches and kernels, palm oil mill effluents (POME) rich in fatty acid methyl esters, condensed sterilisation water, methane from POME and other gases from treatment ponds and wastewater from the palm kernel refinery.
Potential fluctuations in the calculated impacts
The pathway devised for WS-APG production is less fossil-energy, water and waste intensive for the scenario assessed in this study with the chosen set of assumptions. Since this study is evaluating a lab-scale process, it is challenging to pin-point potential scale-up strategies and, as a result, the quantified environmental parameters will fluctuate depending on any changes to the assumptions or pathways that occur during the scale-up/commercialisation, for example, inclusion of any international transportation of biomass/feedstock for refining, variation in road transportation distances, generation of a new kind of ‘non-benign’ waste from scCO2 fractionating an organic component etc. Nevertheless, it is probable that the impacts may reduce rather than increase for WS-APG via the techno-economic optimisation of this currently lab-scale production technique, considering parametric trade-offs (for example, impact of scale-up on efficiency) and other scale-up strategies. Effective utilisation of waste heat from the straw pelletisation process via a closed-loop is also a potential option.
The end-life of the biochar, the key “carbon-storing” by-product of WS-APG, determines the rate of CO2 sequestration. According to a study undertaken by the UK Biochar Research Centre, 2009, the avoided CO2 emission from burning biochar for energy was 2–3 times greater (roughly 9500 kg CO2 per ha per year for winter wheat)48 than that from burning any other raw biomass (that deliver avoided emissions of 5000 kg CO2 per ha per year), when compared with coal.30 Nevertheless, carbon that is sequestered through biomass cultivation and MW-pyrolysis can be locked only through incorporation into the soil. The fate of biochar, in this study, has not been investigated as it falls outside the boundary of analysis.
The main source of waste, within the life process of WS-APG, is in the “pre-processing” stage and is associated with losses in biomass encountered across the drying, milling and pelleting phases, the gas fraction composed of CO and other gases and the aqueous fraction composed of phenol and other high-quality organic components. The amount of associated wastes can be lowered by devising suitable separation techniques which would facilitate further fractionation of high value components.
In terms of direct GHG emissions, within the analysis (WS-APG) pathway, the use of green catalysts such as Amberlyst-15, recognised for their re-usable capability, higher degree of feedstock–product conversion efficiency per unit input, high specificity and low environmental impact relative to conventional catalysts could help lower the GHG intensity of the process.44
Conclusions
An environmental impact assessment was undertaken to quantitatively and qualitatively evaluate a process that was devised to synthesise high-value chemicals, biosurfactants (WS-APG), from a relatively low-value feedstock, wheat straw. An equivalent commercial process that synthesises APG from palm kernel and wheat grain (PW-APG) was adopted as the benchmark for the analysis process. The use of an agricultural residue for a primary feedstock and greener, alternative pre-processing pathways using benign/recyclable solvents means that the environmental performance for the WS-APG process was determined to save GHG emissions in the range of 84–98%, relative to those of PW-APG, from a ‘cradle to gate’ perspective. The GHG emission savings are valid only when treating wheat straw as an agriculture residue and not as a primary product of cultivation. In terms of the additional environmental impact indicators assessed, WS-APG was found to consume less fossil-derived energy and water and also generate lower quantities of waste compared to the commercially established PW-APG production pathway. Owing to the novel nature of the WS-APG production pathway that has been assessed in this study, a number of assumptions were required to reach this conclusion. However, it is highly likely that the estimated prices for the WS-APG pathway are on the ‘higher’ side of wheat to what would be expected after its commercialisation. This is likely to be achieved via potential optimisation through the use of an innovative ‘low-environmental impact’ catalyst, adopting benign reagents to replace non-benign materials, improvement of process efficiency and effective use of waste heat/gases to supply heat/energy for the processes will reduce energy/material based emissions within the WS-APG production stages. Boosting the conversion efficiency (e.g. from straw to primary feedstock, and from primary feedstock to the final product) to a rate similar to or better than the baseline process will also lower the overall environmental burden. A feasibility study is incomplete without a coherent economic impact analysis and this has also been undertaken for the proposed low-waste biorefinery presented here. The outcome of this analysis will be captured in a forthcoming paper.
Acknowledgements
This work was funded by the EPSRC (EP/K014773/1), and this paper is based on a project titled “Sustainable Chemical Feedstocks”. The esteemed institutions Green Chemistry Centre of Excellence, University of York and Dept. of Chemistry, University of Liverpool are thanked for their well-founded encouragement in producing this work.
References
- J. Guilbot, S. Kerverdo, A. Milius, R. Escola and F. Pomrehn, Life Cycle assessment of surfactants: the case of an alkyl polyglucosides used as a self-emulsifier in cosmetics, Green Chem., 2013, 15, 3337–3354 RSC.
-
D. Balzer and H. Luders, Nonionic Surfactants- Alkyl Polyglucosides, CRC Press, 1st edn, 2000 Search PubMed.
-
I. Pantellic, Alkyl Polyglucosides: From natural-origin surfactants to prospective delivery systems, Elsevier, 1st edn, 2014 Search PubMed.
- Biosurfactant market analysis by product (Rhamnolipids, sorolipids, MES, APG, Sorbitan esters, Sucrose esters), http://www.grandviewresearch.com/industry-analysis/biosurfactants-industry, (accessed 2015 Jul 16).
- Surfactants Market worth $42 million by 2020, http://www.marketsandmarkets.com/PressReleases/surfactants.asp, (accessed October 2015).
- F. Hirsinger and K. P. Schick, A Life Cycle Inventory for the production of alkyl polyglucosides in Europe, Tenside, Surfactants, Deterg., 1995, 32(2), 193–200 CAS.
- M. Stalmans, H. Berenbold, J. L. Berna, L. Cavalli, A. Dillarstone, M. Franke, F. Hirsinger, D. Janzen, K. Kosswig, D. Postlethwaite, T. Rappert, C. Renta, D. Scharer, K. P. Schick, W. Schul, H. Thomas and R. Vansloten, European Life-Cycle Inventory For Detergent Surfactants Production, Tenside, Surfactants, Deterg., 1995, 32 Search PubMed.
-
D. Rust and S. Wildes, Surfactants: A Market opportunity study Update, United Soybean Board, 2008 Search PubMed.
-
M. Gifford, Economic feasibility study on the supercritical fluid extraction of edible oils, College of Engineering, Rowan University, 2015, http://www.supercriticalfluids.com/wp-content/uploads/AP-105-Economic-Feasibility-on-SFE-of-Edible-Oils1.pdf, (accessed February 2016) Search PubMed.
- M. Halimah, Y. Tan, K. Nik Sasha, Z. Zuriati, A. Rawaida and Y. Choo, Determination of life cycle inventory and greenhouse gas emissions for a selected oil palm nursery in Malaysia: A case study, J. Oil Palm Res., 2013, 25(3), 343–347 CAS.
-
A. Schultze, R. Lauranson and M. Toullec, Study for a simplified LCA methodology adapted to bioproducts, The French Environment and Energy Management Agency, 2009, http://www.ademe.fr/sites/default/files/assets/documents/69583_synthese_finale_bioproduits_gb.pdf, (accessed August 2015) Search PubMed.
- L. Wang, J. Littlewood and R. Murphy, Environmental sustainability of bioethanol production from wheat straw in the UK, Renewable Sustainable Energy Rev., 2013, 28, 715–725 CrossRef CAS.
- A. Li Borrion, M. McManus and G. Hammond, Environmental life cycle assessment of bioethanol production from wheat straw, Biomass Bioenergy, 2012, 47, 9–19 CrossRef CAS.
- DEFRA: Greenhouse gas Conversion Factor Repository, http://www.ukconversionfactorscarbonsmart.co.uk/, (accessed September 2015).
-
F. Indarwati, L. Ambarsari, M. Yusuf, V. Suzanty, A. Kurnaiwan and Z. Thaib, Handbook of Energy and Economic statistics of Indonesia, Ministry of Energy and Mineral Resources, 2014, http://prokum.esdm.go.id/Publikasi/Handbook%20of%20Energy%20&%20Economic%20Statistics%20of%20Indonesia%20/HEESI%202014.pdf, (accessed September 2015) Search PubMed.
-
ISCC 205, GHG Emissions Calculation Methodology and GHG Audit, International Sustainability and Carbon Certification, 2015 Search PubMed.
-
V. Budarin and J. Fan, EPSRC- Sustainable Renewable feedstocks -SEI-Y, 2015 Search PubMed.
- V. L. Budarin, J. H. Clark, B. A. Lanigan, P. Shuttleworth, S. W. Breeden, A. J. Wilson, D. J. Macquarrie, K. Milkowski, J. Jones, T. Bridgeman and A. Ross, The preparation of high-grade bio-oils through the controlled, low temperature microwave activation of wheat straw, Bioresour. Technol., 2009, 100, 6064–6068 CrossRef CAS PubMed.
-
J. Elliot, A. Cargill and E. Boys, Understanding carbon footprinting for cereals and oilseeds, http://www.nabim.org.uk/download/document/29e5dac9fde35475dda0a77819129d86, (accessed September 2015).
-
Department of Environment, Food and Rural Affairs, Farming statistics: Provisional 2015 cereal and oilseed rape production estimates UK, 2015, https://www.gov.uk/government/uploads/system/uploads/attachment_data/file/469400/structure-june-ukcerealoilseed-statsnotice-20oct15.pdf, (accessed December 2015) Search PubMed.
-
P. Berry, S. Clarke, N. Paveley, J. Clarke and R. Sylvester-Bradley, Increasing the production of wheat in the UK- Essential actions to meet wheat's potential by 2050, Home Grown Cereals Authority (HGCA), 2012, cereals.ahdb.org.uk/media/5435/Wheat_Sub_Group_Report.doc, (accessed November 2015) Search PubMed.
-
J. Spink, P. Street, R. Sylvester-Bradley and P. Berry, The potential to increase productivity of wheat and oilseed rape in the UK, London, UK, 2009 Search PubMed.
-
Home Grown Cereals Authority (HGCA), Assessing the nutrient content of cereal straw, 2009, http://cereals.ahdb.org.uk/media/183781/is05_nutrient_content_in_cereal_straw.pdf, (accessed July 2015) Search PubMed.
-
D. Kindred, N. Mortimer, R. Sylvester-Bradley, G. Brown and J. Woods, Understanding and managing uncertainties to improve biofuel GHG emissions calculations, 2008, http://cereals.ahdb.org.uk/media/277114/pr435-final-project-report-part-ii.pdf, (accessed February 2016) Search PubMed.
- N. J. Glithero, S. J. Ramsden and P. Wilson, Barriers and incentives to the production of bioethanol from cereal straw: A farm business perspective, Energy Policy, 2013, 59, 161–171 CrossRef CAS PubMed.
-
British Hay and Straw Merchants Association, Big Baled Wheat Straw Prices, Department for Environment, Food and Rural Affairs, 2015 Search PubMed.
-
R. Sylvester-Bradley, R. E. Thorman, D. R. Kindred, S. C. Wynn, K. E. Smith, R. M. Rees, C. F. E. Topp, V. A. Pappa, N. D. Mortimer, T. H. Misselbrook, S. Gilhespy, L. M. Cardenas, M. Chauhan, G. Bennett, S. Malkin and D. G. Munro, Minimising nitrous oxide intensities of arable crops (MIN-NO) Report No. 548, ADHB Cereals and oilseeds, 2015.
- D. S. Reay, E. A. Davidson, K. A. Smith, P. Smith, J. M. Melillo, F. Dentener and P. J. Crutzen, Nat. Clim. Change, 2012, 2, 410–416 CrossRef CAS.
-
C. De Klein, S. Novoa, S. Ogle, K. Smith, P. Rochette and T. Wirth, in IPCC Guidelines for National Greenhouse Gas Inventories, Intergovernmental Panel for Climate Change, 2006, vol. 4, pp. 11.3–11.54, http://www.ipcc-nggip.iges.or.jp/public/2006gl/pdf/4_Volume4/V4_11_Ch11_N2O&CO2.pdf Search PubMed.
-
F. Nicholson, D. Kindred, A. Bhogal, S. Roques, J. Kerley, S. Twining, T. Brassington, P. Gladders, H. Balshaw, S. Cook and S. Ellis, Straw Incorporation review, Home Grown Cereals Authority (HGCA), Malton, UK, 2013 Search PubMed.
- S. G. S. A. Rothausen and D. Conway, Greenhouse-gas emissions from energy use in the water sector, Nat. Clim. Change, 2011, 1(4), 210–219 CrossRef CAS.
- K. Lokesh, V. Sethi, T. Nikolaidis, E. Goodger and D. Nalianda, Life cycle greenhouse gas analysis of biojet fuels with a technical investigation into their impact on jet engine performance, Biomass Bioenergy, 2015, 77, 26–44 CrossRef CAS.
- P. Adapa, L. Tabil and G. Schoenau, Pelleting characteristics of selected biomass with and without steam explosion pre-treatment, Int. J. Agric. Biol. Eng., 2010, 3(3), 62–79 CAS.
- D. Laird, The Charcoal Vision- A win-win-win scenario for simultaneously producing bioenergy, permanently sequestering carbon, while improving soil and water quality, Agron. J., 2007, 100(1), 178–181 CrossRef.
- Direct land use Change Assessment Tool, Blonk Consultants, 2013.
- M. Jarecki and R. Lal, Crop Management for Soil Carbon Sequestration, Crit. Rev. Plant Sci., 2003, 22(6), 471–502 CrossRef.
-
G. Punter, D. Rickeard, J. Larive, R. Edwards, N. Mortimer, R. Horne, A. Bauen and J. Woods, Evaluation for the production of Ethanol from Wheat, 2004, http://www.rms.lv/bionett/Files/BioE-2004-001%20Ethanol_WTW_final_report.pdf.Well-to-Wheel, (accessed March 2015) Search PubMed.
-
British Standards Institution, Assessment of Life Cycle greenhouse gas emissions from horticultural products, PAS 2050-1:2012, 2012, http://www.tuinbouw.nl/sites/default/files/PAS2050-1_0.pdf, (accessed June 2015) Search PubMed.
-
European Commission, Commission Decision on Guidelines for calculation of land carbon stocks for the purpose of Annex V to Directive 2009/28/EC, European Commission, 2010 Search PubMed.
-
S. Eggleston, L. Buendia, K. Miwa, T. Ngara and K. Tanabe, IPCC Guidelines for National Greenhouse Gas Inventories, Institute for Global Environmental Strategies, vol. 4, Agriculture, Forestry and other land use, 2006, http://www.ipcc-nggip.iges.or.jp/public/2006gl/vol4.html, (accessed June 2015) Search PubMed.
- V. Budarin, P. Shuttleworth, J. Dodson, A. Hunt, B. Lanigan, R. Marriott, K. J. Milkowski, A. J. Wilson, S. W. Breeden, J. Fan, E. H. K. Sin and J. H. Clark, Use of green chemical technologies in an integrated biorefinery, Energy Environ. Sci., 2011, 4, 471–479 CAS.
- X. Li and E. Mupondwa, Life Cycle Assessment of densified wheat straw pellets in the Canadian Prairies, Int. J. Life Cycle Assess., 2012, 17, 420–431 CrossRef CAS.
- O. Mašek, V. Budarin, M. Gronnow, K. Crombie, P. Brownsort, E. Fitzpatrick and P. Hurst, Microwave and slow pyrolysis biochar—Comparison of physical and functional properties, J. Anal. Appl. Pyrolysis, 2013, 100, 41–48 CrossRef.
- S. Jetti, N. Babu, G. P. Paliwal, A. Bhatewra, T. Kadre and S. Jain, Amberlyst 15DRY Resin: A green and recyclable catalyst for facile and efficient one-pot synthesis of 3,4-hihydropyrimidin-2(1H)-ones, Der Pharma Chem., 2012, 4(1), 417–427 Search PubMed.
-
P. Priecel and J. Lopez-Sanchez, EPSRC- Sustainable Renewable feedstocks -SEI-Y, 2015 Search PubMed.
-
L. Marelli, F. Ramos, R. Heider and R. Koeble, Land use change and Biodiversity Loss estimate of GHG emissions form global land use change scenarios, EU Joint research Centre, Ispra, Italy, 2011 Search PubMed.
- T. Ponsioen and T. Blonk, Calculating land use change in carbon footprints of agricultural products as an impact of current land use, J. Cleaner Prod., 2012, 28(2012), 120–126 CrossRef.
- S. Shackley, J. Hammond, J. Gaunt and R. Ibarrola, The feasibility and costs of biochar deployment in the UK, Carbon Manage., 2011, 2(3), 335–356 CrossRef.
Footnote |
† Electronic supplementary information (ESI) available. See DOI: 10.1039/c7gc01719g |
|
This journal is © The Royal Society of Chemistry 2017 |
Click here to see how this site uses Cookies. View our privacy policy here.