DOI:
10.1039/C6CC07094A
(Feature Article)
Chem. Commun., 2017,
53, 72-81
Alternative synthetic approaches for metal–organic frameworks: transformation from solid matters†
Received
30th August 2016
, Accepted 3rd October 2016
First published on 3rd October 2016
Abstract
Developing economic and sustainable synthetic strategies for metal–organic frameworks (MOFs) is imperative for promoting MOF materials into large scale industrial use. Very recently, an alternative strategy for MOF synthesis by using solvent-insoluble “solid matters” as cation reservoirs and/or templates has been developed to accomplish this goal, in which the solid matters often refer to metals, metal oxides, hydroxides, carbonates, and so forth, but excluding the soluble metal salts which have been prevailingly used in MOF synthesis. Although most of the pioneering activities in this field have just started in the past 5 years, remarkable achievements have been made covering the synthesis, functionalization, positioning, and applications. A great number of MOFs in powder form, thin-films, or membranes, have been prepared through such solid-to-MOF transformations. This field is rapidly developing and expanding, and the number of related scientific publications has strikingly increased over the last few years. The aim of this review is to summarise the latest developments, highlight the present state-of-the-art, and also provide an overview for future research directions.
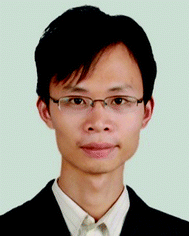
Guowu Zhan
| Guowu Zhan received his BEng and MEng in Chemical Engineering from Xiamen University (China) in 2009 and 2012, respectively. He is currently pursuing his PhD degree at the National University of Singapore under the supervision of Professor Hua Chun Zeng. He is currently working on design, fabrication, and application of integrated nanocatalysts with mesoporous silica/silicate and microporous MOF materials. |
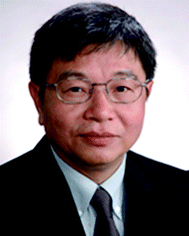
Hua Chun Zeng
| Professor Hua Chun Zeng obtained his BSc in Chemistry from Xiamen University in 1982, and PhD in Physical Chemistry from the University of British Columbia in 1989. Following postdoctoral work at the University of Toronto, he joined the faculty at the National University of Singapore in 1991. His research interests are, at present, focused on the exploratory design and synthesis of inorganic nanostructures with an emphasis on catalytic applications. |
1 Introduction
Metal–organic frameworks (MOFs), as an emerging class of porous materials, show enormous application potential in a wide array of technological fields such as gas storage, membrane separation, chemical sensing, controlled release, and heterogeneous catalysis.1–8 From the view point of a supramolecular architecture, in particular, MOF solids are built by chemical coordination between metal ions (or clusters) and polytopic organic linkers into periodic porous frameworks.1 Regarding their general synthetic methods, most MOFs are obtained prevailingly from homogeneous solution reactions between soluble metal salts and organic ingredients in one or mixed polar solvents (e.g., water, alcohol, or other organic solvents).9 Alternatively, in recent years, metal salt-free procedures have also been developed for the MOF synthesis using solid matters or electrodes as new sources of metal components.5,10 In a typical electrochemical synthesis, for example, metal ions needed for the formation of MOFs are supplied continuously by the dissolution of anodic metals in an electrochemical cell containing desired organic linkers and electrolytes. Several archetypical ZnII, CuII, and AlIII based MOFs have been synthesised successfully.11 Only a handful of MOFs have been prepared with this redox method so far, although the commercial production of HKUST-1 (Basolite® C 300) from sacrificial copper electrodes as a CuII ion source has been achieved by BASF.
In contrast, a wealth of MOFs have been successfully produced from solid matters (e.g., metals, metal oxides, hydroxides, carbonates, etc.), which appears to be a more general and powerful strategy. What is more, solid matters could provide a template role for directing the growth of MOFs. Therefore, in this review, we mainly focus on the recent progress in the use of solvent-insoluble solid matters for the synthesis of MOFs. Herein, we define the solid matters rather broadly as the solvent-insoluble metal precursors and the insolubility means the solid matters hardly release metal cations in the solvents without additional chemical reactions.
Different from common soluble metal salts in homogeneous solution, metal ions within solvent-insoluble solid matters are constrained and would be released in a more controllable way from spatiotemporal views. The released cations would further coordinate with nearby organic ligands available and self-assemble to MOFs. At a fundamental level, MOF products are thermodynamically more stable than solid matters in the presence of ligands (minimization of the Gibbs free energy of the system12), which contributes to the main driving force for the metal liberation and the subsequent chemical conversion. Based on the most current processes reported in the literature, the following eight salient features could be summarised to describe this alternative route for MOF synthesis. In particular, the first three points highlight the green chemistry and sustainability of this strategy, and the last five emphasise the technical advantages of this type of synthesis. (i) Economy of raw materials: solid matters are usually inexpensive feedstocks from large-scale industrial production, ceramic materials, or even natural minerals which are more readily available than metal salts (which are commonly produced from immersing metals in an acid bath (HCl, HNO3, etc.)). (ii) Free of anion impurity: since no exotic metal salt source is used, undesired salt anions such as NO3−, CH3COO−, and Cl− are avoided during the synthesis that minimises unwanted waste, whereas acidic side-products are inherently present in the conventional MOFs. In addition, the nitrate metal salts are potentially explosive and the chloride metal salts are corrosive. (iii) Ecological advantage: environmentally more benign processes of solid into MOF transformation are realised, due to their fast kinetics and free or minimal use of problematic solvents (e.g., N-methylpyrrolidine (NMP), dimethyl sulfoxide (DMSO), and dimethylformamide (DMF), which are commonly used in conventional MOF synthesis). For instance, copper hydroxide can be rapidly converted to HKUST-1 just within 5 min at room-temperature in aqueous ethanolic solution.13 Helms et al. have reported a series of minute-MOFs prepared from divalent metal oxides as precursors.14 And it was reported that only one second of reaction time is required for the full conversion of V2O5 to a vanadium-based MOF.15 Importantly, the extremely fast transformation at room temperature did not compromise the high crystallinity. (iv) Morphological architectures (Fig. 1c): under sophisticated control, the morphology of the precursor phase (viz., solid matters) can be replicated to the derived MOF. Because metal-based solid precursors can be pre-shaped into desirable structures facilely via well-established synthetic techniques of nanomaterials, morphological architectures of MOF materials can also be engineered accordingly. (v) Tuning the size and shape of MOFs (Fig. 1f): controlled release of metal ions from solid matters actually exerts additional influence on the crystallisation of MOFs. By employing solid precursors, metal ions in the solution become significantly scarce and relatively localised in the early stage of the reaction, which enables the kinetic control over the nucleation and growth of MOFs, yielding them with unusual properties and structures that are sought after. (vi) Pattern formation (Fig. 1h): MOF positioning is essential for device fabrication.16 By applying self-templating solid matters (Fig. 1g), the location, crystal size, orientation, and overall patterns of MOFs can be controlled precisely. Moreover, such site-designation or assembly can lead to higher order architectures (e.g., 3-dimensional (3D) superstructures) of MOFs. (vii) Fabrication of MOF films (Fig. 1j): solid matters can be easily fixed on a specific substrate. With the assistance of solid matters as both nucleation seeds and metal ion sources, resultant films or membranes of MOFs can be generated on various substrates, which is particularly useful for sensing and membrane applications. (viii) Fabrication of multifunctional composites: basically, so far there have been two major ways for integration of MOFs with other component phases: (a) partial conversion of solid matters results in well-defined core@shell or yolk@shell heterostructures (Fig. 1e), and (b) solid matters, as metal sources for MOFs, can be preinstalled in host matrixes or blended with other versatile components before their transformation into MOFs (Fig. 1l).
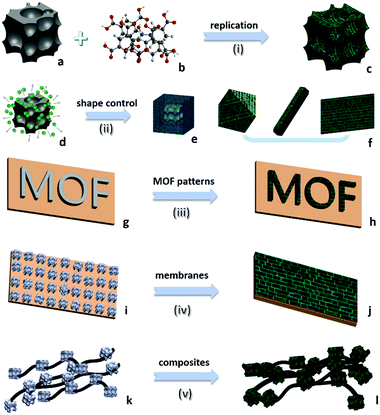 |
| Fig. 1 Conceptual illustrations summarising various approaches used in conversion of solid matters to MOFs: (a) solid matters, (b) organic ligands, (c) replicated MOFs, (d) solid matters with releasing metal ions (small green spheres), (e) core–shell structured solid@MOF, (f) shape-controlled MOFs, (g) solid matter patterns on substrates, (h) MOF assembly on substrates, (i) pre-allocation of solid matters on substrates, (j) MOF membranes or films on the substrate, (k) pristine solid matter composites, and (l) MOF-containing composites. | |
To the best of our knowledge, currently, there are no review papers available introducing the aforementioned solid-to-MOF transformation in the scientific literature. Therefore, the aim of this review is to explain the basic concepts and highlight recent developments in this emerging subfield of MOF research, noting that all the studies exemplified herein were just published in the last few years (from 2009 to 2016). In addition to the Introduction (Section 1), the remaining contents in this review are organised into the following topics: different types of solid matters used in synthesis are categorised (Section 2); presently available synthetic techniques are showcased (Section 3); several milestones of key developments are highlighted, together with a comparison among the representative methods and their process merits (Sections 4 to 8); and conclusions and perspectives are given in the end (Section 9) based on our personal views.
2 Solid matters as metal sources
In the novel protocol described in the review, the insoluble solid matters mainly act as metal ion (or atom) reservoirs, but the diffusion rate of ions (or atoms) in solids is generally very slow. The lattice enthalpy (or energy), representing the strength of the forces among the ions, is a dominant factor controlling the release of metal ions and thus determining whether a solid matter could be used for this type of MOF synthesis. For example, in contrast to their carbonates, the oxides of rare-earth metals are less reactive for MOF synthesis due to higher lattice enthalpies in these oxides, which often results in unreacted oxide residues in the products.17 Additionally, the following reactivity order ZnO > Co(OH)2 > CoO was observed when the studied oxides/hydroxides were mixed with a fixed imidazole ligand for the syntheses of their corresponding MOFs.18 A summary of the solid matters used in this type of MOF synthesis is presented in Table S1 for easy reference, ESI.† According to their chemical nature, these solid precursors can be broadly classified into the following categories.
2.1 Metals
Oxidative dissolution has long been used for shape alteration of metal nanoparticles through preferential removal of atoms at vertices and edges.19 Therefore, the released metal ions could be captured by adjacent organic ligands to form MOFs. Nevertheless, there are only a few examples available for such transformations. For instance, pure Cu nanoparticles with 8 nm in diameter can be converted to Cu@Cu-MOF-74 or Cu@HKUST-1 as the naked Cu was mixed with H4dobdc or H3BTC in a solvent mixture of DMF and ethanol.20 In another study, as shown in Fig. 2, the Pt–Ni alloy can be converted into PtNi@Ni-MOF-74, where the dealloying process of particles and the forming process of MOFs were simultaneously conducted due to different chemical reactivity of the two metallic species (only the Ni metal ions were etched out).21 Similarly, MOF films can also be prepared from the direct conversion of metal plates. For instance, Qiu et al. have grown Zn3(BTC)2 films on zinc slices by directly immersing the zinc slices (pretreated with H2O2) in a H3BTC solution at 140 °C for 24 h.22 Likewise, HKUST-1 thin layers can be densely packed on different Cu substrates (e.g., Cu grids, wires or meshes) by in situ oxidative dissolution of the surface Cu atoms of these substrates.23,24
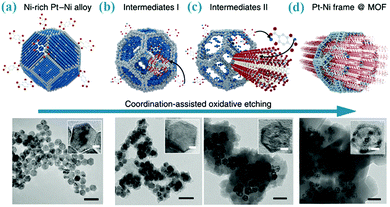 |
| Fig. 2 Schematic illustration of the conversion of the Pt–Ni alloy to Ni based MOF via a coordination-assisted oxidative dissolution process. The scale bars in the TEM images are 50 nm (the scale bars in insets, 5 nm). Reprinted from ref. 21 with permission from Nature Publishing Group. | |
2.2 Metal oxides
Generally speaking, metal oxides are basic in nature and they are thermodynamically stable because of high lattice energies (typically 4–6 MJ mol−1).25 Therefore, introducing acid would initiate the controllable release of metal ions (viz., acidic etching), which can be used as metal sources for the synthesis of MOFs. More specifically, the reaction between metal oxide and organic ligands (e.g., polytopic acids or imidazoles) involves simple acid–base neutralisations which result in the formation of MOFs. Existing examples of this type of synthesis include: ZnO, CuO, Cu2O, Al2O3, MgO, MnO, CoO, NiO, V2O5, and the like (see Table S1, ESI†). To date, ZnO has been among the most studied solid matters for a popular class of ZIFs (ZIFs = zeolitic imidazolate frameworks). In solution-based synthesis, the solvent system used is an important parameter that affects the rates of dissolution of metal oxides, and thus of nucleation and growth of MOFs.26,27 Using a cosolvent made from octanol and ethanol, for example, it was found that the addition of ethanol would enhance the dissolution of ZnO in octanol (containing 2-methylimidazole) and thus accelerate the conversion of ZnO to ZIF-8, whereas no ZIF-8 was formed if ethanol was absent.28 Besides the composition, it was found that shape, size, surface roughness, and surface charge of metal oxides might also affect the reaction rate of metal-oxide to MOF conversion.14,29 For example, Peng et al. reported that CuO nanosheets could be easily converted to HKUST-1 crystals, whilst CuO microcrystals were kept unchanged under the identical conditions.29
2.3 Metal hydroxides
Metal hydroxides, which are ubiquitous in nature, have also been utilised for the MOF synthesis. Such solid compounds include layered double hydroxides (LDHs, M1−x2+Mx3+(OH)yAzn−), hydroxy double salts (HDSs, M1−x2+(M′)x2+(OH)yAzn−), and layered simple hydroxides (LSHs, M2+(OH)yAzn−) in which certain anions (An−, e.g., CO32− and NO3−) are also intercalated within their lamellar structures or gallery spaces. Generally, the reaction path for the MOF synthesis follows: (i) the charge-balancing anions located in the interlayer space would exchange with the ligand anions after deprotonation, (ii) the positively charged sheets also promote the transportation of the ligands of a targeted MOF, and (iii) the mobility of the ligand anions within the layers is very high, yielding fast coordination with the available cationic ions from dissolution. For instance, green rust is a FeII–FeIII LDH (Fe42+Fe23+(OH)12·SO4) which could be converted to Fe-based MOFs at room temperature within a time as short as 5 min.30 As also exemplified by Caro et al., ZnII–AlIII LDH could partially convert to ZIF-8, leading to the formation of ZIF-8/LDH composite membranes with enhanced gas separation performance.31 Parsons et al. have designed a fast (<1 min) and mild (room temperature) synthetic route for HKUST-1, Cu-BDC, ZIF-8, and IRMOF-3 by using (Zn, Cu) HDSs as intermediates (originally from ZnO).32 Furthermore, the space-time-yield for HKUST-1 reaches 3.6 × 104 kg m−3 day−1, which is at least one order of magnitude greater than those in previous reports, and is suitable for industrial commercialisation. In analogy to LDHs, the cobalt carbonate hydroxide LSH (Co(CO3)0.5(OH)) has a layered crystal structure in which CO32− ions are intercalated between cobalt hydroxide sheets which could deprotonate the 2-methylimidazole ligand, and initiate the crystallisation process of ZIF-67.33 Similarly, Cu2(OH)3(OAc) LSH can also be used to prepare Cu–Fe based Prussian Blue analogues (PBAs) at room temperature.34 In these cases, Coulomb force can be used for enhancing the interaction between solid matters and ligands. Since they are positively charged, the surfaces of hydroxide host layers easily adsorb the negatively charged organic ligands (e.g., carboxylate anions from deprotonation of carboxylic acids).35 Nevertheless, it should be pointed out that the LSHs with charge-neutral layers (i.e., brucite-like Mx+(OH)x which does not have charge-balancing anions in its interlayer space) can also be used for the MOF synthesis.36–40
2.4 Metal carbonates and other insoluble salts
It has been anticipated that the conversion of metal carbonates to MOFs is nearly waste-free, because this reaction just produces CO2 and H2O as byproducts (MCO3 + H2L → [ML]n + CO2 + H2O, assuming the L of polytopic acids (H2L) as ligands). James et al. have explored seven different kinds of rare-earth carbonates RE2(CO3)3 (rare-earth metal ions (RE) = Y, Sm, Gd, Tb, Dy, Er and Yb) to prepare the corresponding rare-earth metal(III) based MOFs.17 Along the similar line, Kitagawa et al. have also provided a demonstration of conversion of CaCO3 to CaII based MOFs, considering that CaCO3 is one of the most abundant biominerals in nature.41 Additionally, biomineralised CaCO3 with a hierarchically porous structure allows the fabrication of MOFs with superstructures. Similar to these metal carbonates, in principle, other insoluble or less soluble metal salts can also be adopted for this kind of synthesis; of course, further verification of their synthetic feasibility is certainly needed.
2.5 Mixed solid matters
Besides a single solid precursor, mixed solid matters can also be used as multi-precursors for making MOFs. Very recently, three different aluminium-containing minerals, Al2O3, Al(OH)3 and AlO(OH), were used for the synthesis of MIL-53(Al) at 200 °C for 72 h.42 Importantly, the derived MIL-53(Al) has higher thermal stability and water-vapour resistance than its counterparts attained by conventional methods, which implies that natural minerals on Earth's crusts are potential raw materials for the industrial scale production of MOFs. It is noteworthy that dual metal sources from both solid matter and metal salts have been reported in some cases.43 In this regard, it is anticipated that multiple types or components of solid precursors could be further employed if even more complicated MOF materials are targeted in future.
3 Synthetic methods
Similar to common synthetic routines of using soluble metal salts as metal ion sources, formation of MOFs from solid matters can take place in both solvent-based and solvent-free procedures. The central role for solvents is that they provide necessary mobility for the reactants (particularly the organic ligands) in desired coordination reactions, though most of the solid matters discussed in this review have extremely low solubility. In the solvent-based process, normally, water or some non-aggressive organic solvents (e.g., ethanol and methanol) are used at room temperature or under hydrothermal or solvothermal conditions. Although they are mostly conducted at room-temperature, conversions at elevated temperatures are also seen in order to accelerate the reactions involved. In many solution-based processes, “dissolution-then-regrowth” mechanism is anticipated as solid matters mixed with ligand solutions.44 The colour change of a solid suspension is usually visualised along the evolution from solid matters to MOFs in many reports, which is particularly true for copper based MOFs which have a vivid blue colour.45,46
When the metal cations from solid matter dissolution might not be the desired active species for the synthetic construction of MOFs, reducing or oxidising agents could also be added in order to tune their oxidation states. For instance, ascorbic acid not only enhances the dissolution of the sacrificial V2O5 phase but also helps to reduce the VV to VIII oxidation state required for the fabrication of vanadium-based MOFs. Similarly, dissolved oxygen in solution converts the monovalent CuI to divalent CuII state after the dissolution of Cu2O (viz., 2Cu2O + O2 + 8H+ → 4Cu2+ + 4H2O), and promotes the formation of HKUST-1.44,47–49
On the other hand, solvent-free synthesis (i.e., dry conversion) is another common approach using solid state precursors, which mainly refers to the mechanochemistry (e.g., mortar grinding or high-energy ball milling), solvent-free oven heating and solvent-free microwave heating (see Fig. 3). Normally, these types of reactions cannot occur spontaneously via simple physical mixing of solid matters and ligands, and therefore, additional energies (e.g., mechanical force and heating, etc.) or processes (e.g., mineral neogenesis) must be applied in order to trigger the reactions.
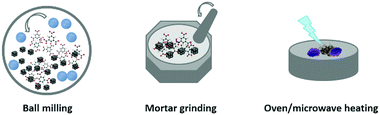 |
| Fig. 3 Schematic diagrams illustrating the solvent-free synthesis of MOFs from solid matters. | |
First of all, mechanochemistry with solid–solid reactions by mechanical action is a clean and industrially applicable method featuring a short reaction time, low temperature, and nearly a solventless or solvent-free process. This approach is frequently used in the synthesis of pharmaceutical materials with coordination bonds,50 and now it has been developed for the synthesis of several types of MOFs.17,51–53 For example, ZIF-8 can be produced by grinding ZnO and 2-methylimidazole together by a ball mill at a rotation rate of 100 rpm under a truly solvent-free condition.52 Mixing different solid matters with one type of ligands allows for the preparation of MOFs with hetero-metals.17 In addition to the neat grinding, in some cases, a small amount of liquid or ions could also be added into the ball mill to improve the synthetic efficiency, which are called liquid-assisted grinding and ion-assisted grinding, respectively.17,51,53 Recently, James et al. have explored an extrusion technique (using twin screw or single screw extrusion) for scaling of the mechanochemical synthesis of MOFs in a continuous process.54
Apart from the aid of external mechanical force, secondly, solvent-free synthesis can also be realised by physical mixing of solid metal matters with organic ligands under heating conditions (e.g., oven heating or microwave heating).18,55,56 The ligands with a low melting point might melt upon heating, and the reactions between the solid matter and melted ligands involve a simple acid–base neutralisation that provides the metal cations and ligand anions. Apparently, such a heating eases the coordination reactions involved. Oven heating solvent-free synthesis can also lead to the formation of otherwise not accessible new MOFs.37 Usually, the chemical transformation of ZnO into ZIF-8 via solvent-free routes requires a long reaction time, but if the process is carried out under microwave heating conditions, the reaction can be completed in less than 30 min.26 In addition, volumetric expansion has been observed due to the density difference between solid matters and product MOFs. Therefore, shaped MOFs can be fabricated if the solvent-free reaction system is proceeded in a closed vessel.55
Thirdly, biomimetic alternatives are another approach for the transformation of solid matters into MOFs in terms of solvent-free synthesis, in which the conversion takes place in the presence of moisture or vapours under surprisingly mild conditions (without agitation and mechanical forces) based on the inherent mobility of reactants under this condition.57 For example, an “accelerated ageing” (akin to mineral neogenesis) mechanism has been demonstrated by Friščić et al. to synthesize MOFs from minerals at high humidity with temperature up to 45 °C.25,58,59 The scalability of the reactivity has also been investigated, and multi-gram amounts of ZIF-8 and ZIF-67 have been produced from the solid precursors of ZnO and CoO, respectively.25,58 Although it can be accelerated in the presence of salt additives, the ageing process normally needs several days to complete the reaction. Nevertheless, this type of process is very effective for the synthesis of a variety of one-dimensional (1D) coordination polymers and 2D, 3D MOFs from their corresponding parent metal constituents (e.g., MgO, MnO, CoO, NiO, ZnO, CdO, PbO, and Bi2O3) through the ageing transformation.25,60
4 Morphological replication
Different from freely mobile metal ion sources in the solution phase, solid matters provide the metal cations in spatially and temporally controlled ways where the nucleation sites are not homogeneously distributed across the entire solution but occur more locally surrounding their parent solids.44 And the homogeneous nucleation in the solution is inherently inhibited since most of the metal ions are constrained within the solid matters. Therefore, the sacrificial solid matters not only provide the metal ions but also serve as architecture-directing agents, and thus it is possible for copying the morphology or patterns of such solid precursors to the derived MOFs. This self-template preparative methodology is named as “coordination replication” or “pseudomorphic replication” by Kitagawa et al.15,45,46,61,62 As illustrated in Fig. 4a, Kitagawa et al. for the first time reported this replication method for converting alumina to an aluminium naphthalene dicarboxylate framework (Al(OH)(ndc)).61 In this way, the morphology of the parent solids (e.g., a 2D honeycomb pattern or a 3D inverse opal structure) can be totally replicated to the resultant aluminium-based MOFs in a reliable and extremely fast way. Inspired by this work, macro- and mesoporous Cu(OH)2–polyacrylamide composite can be employed as a parent solid for the synthesis of mesoscopic superstructures of Cu2(bdc)2(bpy) frameworks (Fig. 4b),45 in which the polymer not only maintains the shape replication but also enhances the mechanical robustness required for processability.
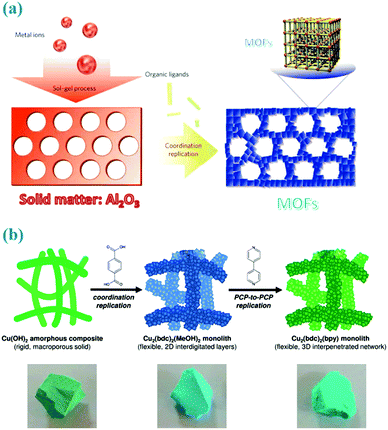 |
| Fig. 4 (a) Coordination replication of Al2O3 with honeycomb patterns to a more stable aluminium naphthalene dicarboxylate framework. Reprinted from ref. 61 with permission from Nature Publishing Group. (b) Two step coordination replication of the Cu(OH)2–polyacrylamide composite to 2D layered frameworks and 3D networks. Reprinted from ref. 45 with permission from the Royal Society of Chemistry. | |
Three-dimensional (3D) monoliths of MOFs are difficult to prepare because the crystalline MOFs are usually in bulk powder or particle form and thus lack of inter-particulate linkages. Recently, Kanamori et al. have reported a direct conversion of Cu(OH)2-based monoliths to HKUST-1 monoliths, in which the macropores in the original gels were preserved.46 Importantly, the authors also found that the derived HKUST-1 monoliths have good mechanical properties comparable to periodic mesoporous SiO2 monoliths, traits vital for industrial prospects. Sometimes, organic or inorganic binders could also be added to help shaping MOFs into technically relevant extrudates. For example, Cu(OH)2 extrudates with 20 wt% kaolinite as a binder underwent transformation into HKUST-1 in the presence of an ethanolic H3BTC solution.13
Overall, there are several factors that should be taken care in order to guarantee the perfect replication. The most important factor is the spatiotemporal synchronisation of the precursor dissolution and the MOF crystallisation. If the dissolution kinetics of the sacrificial phase is higher than the kinetics of MOF crystallisation, it is necessary to either apply polymer coating layers (as a barrier) on the solid matters or use solvent with high viscosity (e.g., octanol28) to slow down the out-diffusion of metal cations at solid–liquid interfaces. Secondly, it should be noted that the parent solid matter phase is required to possess huge porosity (e.g., containing mesopores or macropores) in order to facilitate the diffusion and transportation of organic ligands in the entire solid and fulfil the coordination replication.45 Or else, only partial replication would be obtained, producing core–shell structures. Thirdly, the parent solid matters for coordination replication are generally micro-sized particles, and the daughter MOF phases in meso-structures usually comprise numerous polycrystalline grains (<100 nm) due to the heterogeneous nucleation. This is the reason why the surfaces of the generated MOFs are rather rough. On the other hand, it is difficult for nanoscale solid matters to maintain their original morphology owing to relatively easy release of metal ions. However, they could be used as solid precursors for the domain growth of 3D-networks of MOFs. In our recent study (Fig. 5), for example, uniform Cu2O nanocubes (edge length of 60 nm) were used as a point source of copper ions to prepare 3D-networks of HKUST-1 with hierarchically arranged pore structures (e.g., micro-, meso-, and macropores).44
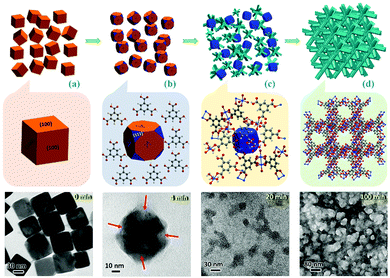 |
| Fig. 5 Synthetic approach for HKUST-1 3D-nets prepared from Cu2O nanocubes. (a) Synthesis of Cu2O; (b) oxidative dissolution of CuI to CuII ions (illustrated as blue colour) with the assistance of H3BTC; (c) nucleation-growth of HKUST-1 in growing domains and domain integration; and (d) total consumption of the Cu2O phase and the formation of HKUST-1 3D-nets. Reprinted from ref. 44 with permission from the Royal Society of Chemistry. | |
5 Shape and dimensional controls
To date, it remains difficult to control geometric shapes of MOF products by adjusting coordination behaviours of metals and ligands. In particular, low dimensional MOF morphologies (e.g., 1D fibres and 2D nanosheets) are difficult to prepare and thus they are seldom reported. The usage of solid matter as a metal ion source actually plays a kinetic role in adjusting the coordination behaviours of targeted MOFs. As shown in Fig. 6, recently, our group has reported a facile route at room temperature and ambient pressure for the preparation of copper-containing nanostructured MOFs with low dimensional shapes (i.e., fibres, rods, sheets and cuboids) using Cu2O nanoparticles in spherical or cubic shape to provide required copper ions.47 Interestingly, when the monovalent Cu2O was replaced by divalent CuO, the product HKUST-1 only has an irregular shape which is totally different from Cu(HBTC)-1 by using Cu2O as a parent solid (Fig. 6). It is inferred that the starting CuI solution is essential to promote the slow growth of low-dimensional MOFs. In this regard, the growth process is somewhat similar to the shape-controlled synthesis of gold nanoplates achieved by using a syringe pump to slowly deliver the precursor to the reaction system.63
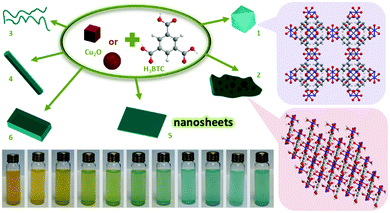 |
| Fig. 6 Shape controlled synthesis of MOFs by using cubic or spherical Cu2O particles as metal source: (1) octahedral HKUST-1, (2) shape-uncontrolled Cu(HBTC)-1, (3–6) oriented Cu(HBTC)-1 with defined shapes. Ball and sticks models of HKUST-1 (purple background) and Cu(HBTC)-1 (pink background). Bottom colour photographs illustrate the evolution of Cu2O to HKUST-1 at room temperature (reaction time increasing from left to right). Reprinted from ref. 47 with permission from John Wiley and Sons. | |
6 Synthetic positioning and patterning
Currently, the grown MOFs are difficult to be positioned in a designated region with traditional methods due to the lack of spatial control over MOF nucleation. Nevertheless, it becomes possible to obtain patterned MOFs for device application if the solid matters are pre-allocated (or pre-patterned) onto desired positions in order to initiate localised heterogeneous nucleation and growth.28,40,56,64 Briefly, this protocol involves two steps: first, the solvent-insoluble metal containing matters are positioned on a substrate via some established techniques (e.g., sol–gel process),64 then their transformation into MOFs is conducted under both solution and solvent-free conditions. For instance, positioned metal oxides can serve as heterogeneous seeds for the growth of MOFs, which not only reduces the nucleation time and temperature required for MOF synthesis but is capable of designating the resultant crystals to various substrates even within glass and polydimethylsiloxane channels (by using microfluidic techniques).65 In another report, the Co(CO3)0.5(OH) nanowires were firstly grown onto a Ni foam substrate, then, they could be converted to ZIF-67, leading to the formation of a ZIF-67-based nanotube array on Ni foam substrates.33 Similarly, as shown in Fig. 7, ZnO@ZIF-8 nanorod arrays could be obtained by using the ZnO arrays grown on a fluorine-doped tin oxide (FTO) coated glass as a template.27 Excitingly, such MOF composite arrays have promising applications for H2O2 sensing. Therefore, in this way, the building MOF patterns can be achieved at will.
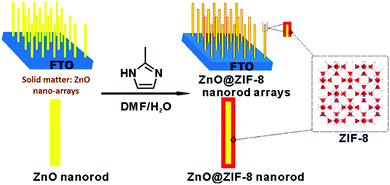 |
| Fig. 7 Schematic illustration of ZnO@ZIF-8 patterns fabricated from the solid to MOF transformation. Reprinted from ref. 27 with permission from the American Chemical Society. | |
7 Making thin films and membranes
MOFs with permanent porosity are ideal candidates for membrane materials in gas separation or liquid separation via pervaporation.66,67 High quality MOF membranes comprise a thin layer of continuously grown MOF films on top of a porous substrate (e.g., inorganic or polymeric substrates), where how to avoid grain boundary defects and improve film–substrate interactions are two key factors influencing their ultimate separation performance. As a simple but powerful technique, solid matter transformation has now been used to fabricate efficient MOF membranes.
Unlike MOFs, other solid materials can be more easily attached to versatile substrates via methods such as solution growth, microcontact printing, dip-pen lithography, photolithography, and chemical vapour deposition and so on. Therefore, converting solid matters to their corresponding MOFs allows the in situ growth of MOF films on various substrates. For instance, MOF films and membranes prepared from such solid-to-MOF transformations can now be adhered on glass, plastic, polymer, silicon wafer, or electrode.64,68,69 Helms et al. have found that ZIF-7 grown on polymers from the ZnO precursor can be changed from isolated crystallites to continuous films by varying the solvent composition.26 Obviously, only the composites with a continuous films of MOFs can be used as effective membranes for gas separation.36 Ameloot et al. have recently proposed the supplying organic linker (2-methylimidazole) as a vapour instead of a solution to react with ZnO at 100 °C for 30 min, which enables the formation of ultrathin and homogeneous ZIF-8 membranes under the solvent-free conditions.70
Recently, well-grown and defect-free ZIF-8 membranes (a thickness of 800 nm) supported on anodic aluminium oxide (AAO) were prepared from Zn(OH)2/AAO nanofilms, as displayed in Fig. 8a and b.38 The Zn(OH)2/AAO template can be obtained by vacuum suction filtering the Zn(OH)2 suspensions on AAO. In addition, the authors found that thicker ZIF-8 membranes (2.5 μm) exhibited higher selectivity and faster H2 permeability than other ZIF-8 membranes that have ever been reported. Similarly, Fig. 8c–f illustrates two examples of ZIF-8 films coated on carbon steel or Si wafer translated from their corresponding supported ZnO films.56,68 This procedure can also be applied to the fabrication of HKUST-1/polymer hollow fibre membranes towards gas separation.71
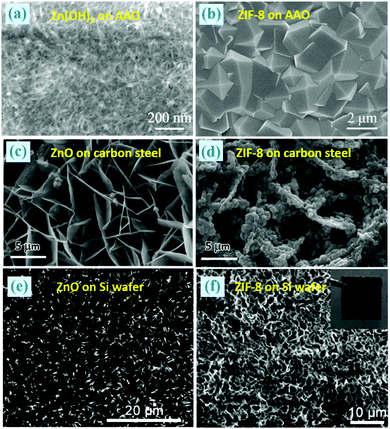 |
| Fig. 8 (a–f) SEM images of ZIF-8 films coated on versatile substrates through the transformation of the corresponding ZnO films. Inset in (f): a photograph of the ZIF-8 film. Reprinted from ref. 38 and 56 with permission from the Royal Society of Chemistry and ref. 68 with permission from the American Chemical Society. | |
Substrate materials can also serve as feedstock materials to grow MOF films at the interface if the substrate shares the same metal element with the target MOF to be deposited. Usually, no surface modification is required under this condition. For example, a metallic copper net can provide the copper source to prepare the copper net supported HKUST-1 membranes.43 Importantly, the resultant membrane possesses high permeability and selectivity for H2 over CO2, N2, and CH4, promising for recycling H2 from steam reforming. Similarly, MIL-110 supported on an AAO membrane can be fabricated with the aluminium source from the solid AAO under hydrothermal conditions.72
8 Synthesising nanocomposites
Integration of MOFs with functional nanoparticles facilitates their wider applications, which can be realised by using solid matter/nanoparticle (NP) composites as the precursors. Compared with MOFs, metal oxides can more easily be deposited on metal NPs. For example, Cu2O can be coated on various metal NPs (e.g., Au and Pd).73 Then, the transformation of Cu2O into Cu-based MOFs leads to the formation of well-defined yolk–shell structured NPs@Cu-MOFs.48 An alumina coated gold nanorod can be used as a precursor to prepare a core–shell composite with an aluminium-based MOF coated on the surface of gold nanorods.74 The oriented growth of Al-MOF on Ag NPs can be achieved by atomic layer deposition of alumina thin films (thickness from 0.1 to 3 nm) on Ag NPs and the subsequent transformation.75 Similarly, binary metal oxide (ZnSnO3) can be translated to ZIF-8/SnO2 composites, since the ligands would preferentially react with ZnII rather than SnIV.76 Recently, Ni-rich Pt–Ni alloy nanoparticles were used to produce a (Pt–Ni)@(Ni-MOF-74) composite.21 The MOF coating layer on the surface of Pt endows the hybrid with molecular sieve effects in several catalytic reactions.
Multifunctional (metal-oxide)@MOFs with core–shell or yolk–shell structures can be synthesised by using metal oxides as a template, in which if the diffusion rate of metal ions is larger than that of organic ligands, a yolk@shell product was obtained, whereas, core@shell one was obtained if the opposite happens.77 The growth of MOFs was confined on the core surface because metal ions for constructing MOFs were provided solely through sacrificing the core material. A ZnO@ZIF-8 core–shell heterostructure could be prepared by partial conversion of ZnO on the surface region.27,28 In another report, ZnO nanoparticles could be adsorbed on the surface of carbon nanotubes (CNTs), then the transformation of ZnO into ZIF-8 proceeded on the surface of CNTs, leading to the formation of a ZIF-8/CNT composite.78 Likewise, MOF/polymer composites can be prepared by firstly mixing the solid matters and polymers followed by the conversion. For example, ZnO-to-ZIF chemical transformation can help to fabricate the ZIF/polymer composites with layered architectures.26 Moreover, the included polymer in the MOF/polymer composites would increase their mechanical robustness, so the resultant MOFs are easily handled.45
Besides the fabrication of MOF films on substrates (Section 7), the solid-matter assisted method enables incorporation of other functional materials within the MOF thin films. As illustrated in Fig. 9, Peng et al. have explored a general Cu(OH)2 assisted technique to confine diverse components (such as small ions, micrometre-sized particles, inorganic nanoparticles and bioactive proteins) in HKUST-1 thin films at room temperature.79 Therefore, the resultant composite MOF films have dual merits from both the size-sieving effect of HKUST-1 and the original property of the encapsulated materials. For example, Au/HKUST-1 composite thin films can be explored as catalytic membrane reactors, which show the selective hydrogenation of n-hexene (26.3% conversion) and cis-stilbene (0%). Along these lines, the approach would provide virtually unlimited possibility for hybridisation of MOFs with any nanomaterials if their parent solid matters can be hybridised both chemically and structurally.
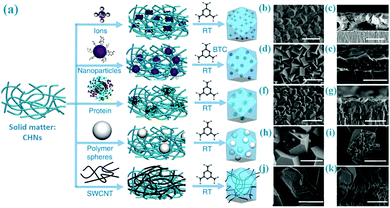 |
| Fig. 9 (a) Functionalization of HKUST-1 membranes by using copper hydroxide nanostrands (CHNs) as a copper ion source; (b–k) SEM images of the resultant products combining HKUST-1 with various different components (e.g., small ions, polymer spheres, CNTs, inorganic nanoparticles and bioactive proteins, etc.). The scale bars are (b) 3 μm; (c) 4 μm; (d and e) 3 μm; (f) 5 μm; (g and h) 3 μm; (i) 5 μm; (j) 3 μm; (k) 2 μm, respectively. Reprinted from ref. 79 with permission from Nature Publishing Group. | |
9 Conclusions and perspectives
As introduced in the foregoing examples of solid-to-MOF transformation, this methodology could be considered as one of the most versatile strategies in controlled synthesis and functionalization of MOFs with special architectures. Below are some urgent issues and technical challenges which should be addressed in order to further develop this topical research.
(1) At the moment, solid precursors used in this strategy have been limited to less soluble solids, and they have so far been focused only on a few groups of inorganic substances, as discussed above. In fact, many others are still largely unexplored, especially those of mineral materials. Associated with this issue, furthermore, general criteria to efficiently distinguish and rapidly screen potential precursor matters for such MOF synthesis have not been established yet.
(2) Although our knowledge on the general synthesis of this strategy has been accumulated rapidly, our understanding of mechanistic aspects such as nucleation and crystal-growth processes of MOFs is still unclear. In principle, many in situ and operando evaluation tools established in nanoscience and nanotechnology research studies over the past few decades can be readily applied into these types of time-resolved dynamic investigations.
(3) The concentration gradient of metal ions caused by the solid matters in the solution phase could be used for adjusting the crystal growth rate of MOFs. Therefore, more effort should be made to understand the fundamental mechanism of solid-to-MOF transformation in order to grow MOFs into predesigned shape and architectures.
(4) The main kinetic issue involved in these transformative syntheses is the rate of solid matter dissolution and the rate of MOF formation. Thus, how to create a predictable and reproducible kinetics for the solid matter dissolution is critically important. However, most of the current investigations have mainly focused on MOF formation, but the fine control over the solid matter dissolution has not been achieved, particularly over complicated transformations involving multiple types of metal precursors and variable valence metal ions when additional redox reactions are involved.
(5) The solvent-free approach is generally considered “greener”. Unlike the solution approach, however, solid form of reactants limits intra- and inter-particle diffusions. Therefore, thorough mixing of solid reactants becomes a crucial synthetic parameter to such transformative reactions. Nevertheless, it should be noted that mixing of raw materials by hand-grinding in a mortar is less manageable, though it has been commonly adopted. Due to variations in experimental conditions (e.g., the size of mortar and the force applied), such processes are insufficiently reproducible among the researchers.
(6) It remains a great challenge to confine the growth of MOFs inside a pore or a cavity (e.g., with porous silica or carbon nanoshells). Since they can provide constraining metal ion sources, solid state metal sources can also be used for the confined construction of MOFs inside spaces of porous structures. Nonetheless, so far no such attempts have been reported in the literature.
With more research endeavours devoted, we believe that the above urgent issues and technical challenges could be addressed at both macroscopic and microscopic (molecular) levels in near future, not only to pursue fundamental interest in advanced synthesis but also to make this strategy more suitable for sustainable large scale production and industrial applications of MOFs.
Acknowledgements
This project is funded by the National Research Foundation (NRF), Prime Minister's Office, Singapore under its Campus for Research Excellence and Technological Enterprise (CREATE) program.
Notes and references
- H. Furukawa, K. E. Cordova, M. O'Keeffe and O. M. Yaghi, Science, 2013, 341, 1230444 CrossRef PubMed.
- A. U. Czaja, N. Trukhan and U. Muller, Chem. Soc. Rev., 2009, 38, 1284–1293 RSC.
- B. Liu, J. Mater. Chem., 2012, 22, 10094–10101 RSC.
- J. Lee, O. K. Farha, J. Roberts, K. A. Scheidt, S. T. Nguyen and J. T. Hupp, Chem. Soc. Rev., 2009, 38, 1450–1459 RSC.
- B. Chen, Z. Yang, Y. Zhu and Y. Xia, J. Mater. Chem. A, 2014, 2, 16811–16831 CAS.
- Q. Yang, Q. Xu, S.-H. Yu and H.-L. Jiang, Angew. Chem., Int. Ed., 2016, 55, 3685–3689 CrossRef CAS PubMed.
- J.-D. Xiao, Q. Shang, Y. Xiong, Q. Zhang, Y. Luo, S.-H. Yu and H.-L. Jiang, Angew. Chem., Int. Ed., 2016, 55, 9389–9393 CrossRef CAS PubMed.
- C. Y. Huang Gang and J. Hailong, Acta Chim. Sin., 2016, 74, 113–129 CrossRef.
- N. Stock and S. Biswas, Chem. Rev., 2012, 112, 933–969 CrossRef CAS PubMed.
- Y. Yue, N. Mehio, A. J. Binder and S. Dai, CrystEngComm, 2015, 17, 1728–1735 RSC.
- A. Martinez Joaristi, J. Juan-Alcañiz, P. Serra-Crespo, F. Kapteijn and J. Gascon, Cryst. Growth Des., 2012, 12, 3489–3498 CAS.
- A. Altree-Williams, A. Pring, Y. Ngothai and J. Brugger, Earth-Sci. Rev., 2015, 150, 628–651 CrossRef CAS.
- G. Majano and J. Pérez-Ramírez, Adv. Mater., 2013, 25, 1052–1057 CrossRef CAS PubMed.
- L. Maserati, S. M. Meckler, C. Li and B. A. Helms, Chem. Mater., 2016, 28, 1581–1588 CrossRef CAS.
- J. Reboul, K. Yoshida, S. Furukawa and S. Kitagawa, CrystEngComm, 2015, 17, 323–330 RSC.
- P. Falcaro, D. Buso, A. J. Hill and C. M. Doherty, Adv. Mater., 2012, 24, 3153–3168 CrossRef CAS PubMed.
- W. Yuan, J. O'Connor and S. L. James, CrystEngComm, 2010, 12, 3515–3517 RSC.
- M. Lanchas, D. Vallejo-Sanchez, G. Beobide, O. Castillo, A. T. Aguayo, A. Luque and P. Roman, Chem. Commun., 2012, 48, 9930–9932 RSC.
- M. N. O'Brien, M. R. Jones, K. A. Brown and C. A. Mirkin, J. Am. Chem. Soc., 2014, 136, 7603–7606 CrossRef PubMed.
- I. Luz, A. Loiudice, D. T. Sun, W. L. Queen and R. Buonsanti, Chem. Mater., 2016, 28, 3839–3849 CrossRef.
- Z. Li, R. Yu, J. Huang, Y. Shi, D. Zhang, X. Zhong, D. Wang, Y. Wu and Y. Li, Nat. Commun., 2015, 6, 8248 CrossRef CAS PubMed.
- X. Zou, G. Zhu, I. J. Hewitt, F. Sun and S. Qiu, Dalton Trans., 2009, 3009–3013 RSC.
- Y. Tanihara, A. Nozaki, Y. Kuwahara, K. Mori and H. Yamashita, Bull. Chem. Soc. Jpn., 2016, 89, 1048 CrossRef.
- A. Nozaki, Y. Tanihara, Y. Kuwahara, K. Mori and H. Yamashita, Chem. Lett., 2016, 45, 976–978 CrossRef CAS.
- F. Qi, R. S. Stein and T. Friscic, Green Chem., 2014, 16, 121–132 RSC.
- S. M. Meckler, C. Li, W. L. Queen, T. E. Williams, J. R. Long, R. Buonsanti, D. J. Milliron and B. A. Helms, Chem. Mater., 2015, 27, 7673–7679 CrossRef CAS.
- W. Zhan, Q. Kuang, J. Zhou, X. Kong, Z. Xie and L. Zheng, J. Am. Chem. Soc., 2013, 135, 1926–1933 CrossRef CAS PubMed.
- S. Li, W. Zhang, Y. Zhu, Q. Zhao and F. Huo, Cryst. Growth Des., 2015, 15, 1017–1021 CAS.
- Y. Guo, Y. Mao, P. Hu, Y. Ying and X. Peng, ChemistrySelect, 2016, 1, 108–113 CrossRef CAS.
- G. Majano, O. Ingold, M. Yulikov, G. Jeschke and J. Perez-Ramirez, CrystEngComm, 2013, 15, 9885–9892 RSC.
- Y. Liu, J. H. Pan, N. Wang, F. Steinbach, X. Liu and J. Caro, Angew. Chem., 2015, 127, 3071–3075 CrossRef.
- J. Zhao, W. T. Nunn, P. C. Lemaire, Y. Lin, M. D. Dickey, C. J. Oldham, H. J. Walls, G. W. Peterson, M. D. Losego and G. N. Parsons, J. Am. Chem. Soc., 2015, 137, 13756–13759 CrossRef CAS PubMed.
- D. Yu, L. Ge, B. Wu, L. Wu, H. Wang and T. Xu, J. Mater. Chem. A, 2015, 3, 16688–16694 CAS.
- M. Lang, E. Delahaye, D. Foix, D. Ihiawakrim, O. Ersen, C. Leuvrey, J.-M. Grenèche, G. Rogez and P. Rabu, Eur. J. Inorg. Chem., 2016, 2030–2038 CrossRef CAS.
- Y. Mao, L. Shi, H. Huang, Q. Yu, Z. Ye and X. Peng, CrystEngComm, 2013, 15, 265–270 RSC.
- P. Hu, Y. Yang, Y. Mao, J. Li, W. Cao, Y. Ying, Y. Liu, J. Lei and X. Peng, CrystEngComm, 2015, 17, 1576–1582 RSC.
- M. Lanchas, S. Arcediano, G. Beobide, O. Castillo, A. Luque and S. Perez-Yanez, Inorg. Chem. Front., 2015, 2, 425–433 RSC.
- J. Li, W. Cao, Y. Mao, Y. Ying, L. Sun and X. Peng, CrystEngComm, 2014, 16, 9788–9791 RSC.
- Y. Mao, L. shi, H. Huang, W. Cao, J. Li, L. Sun, X. Jin and X. Peng, Chem. Commun., 2013, 49, 5666–5668 RSC.
- K. Okada, R. Ricco, Y. Tokudome, M. J. Styles, A. J. Hill, M. Takahashi and P. Falcaro, Adv. Funct. Mater., 2014, 24, 1969–1977 CrossRef CAS.
- K. Sumida, M. Hu, S. Furukawa and S. Kitagawa, Inorg. Chem., 2016, 55, 3700–3705 CrossRef CAS PubMed.
- Z. Li, Y. Wu, J. Li, Y. Zhang, X. Zou and F. Li, Chem. – Eur. J., 2015, 21, 6913–6920 CrossRef CAS PubMed.
- H. Guo, G. Zhu, I. J. Hewitt and S. Qiu, J. Am. Chem. Soc., 2009, 131, 1646–1647 CrossRef CAS PubMed.
- G. Zhan and H. C. Zeng, Chem. Commun., 2016, 52, 8432–8435 RSC.
- K. Sumida, N. Moitra, J. Reboul, S. Fukumoto, K. Nakanishi, K. Kanamori, S. Furukawa and S. Kitagawa, Chem. Sci., 2015, 6, 5938–5946 RSC.
- N. Moitra, S. Fukumoto, J. Reboul, K. Sumida, Y. Zhu, K. Nakanishi, S. Furukawa, S. Kitagawa and K. Kanamori, Chem. Commun., 2015, 51, 3511–3514 RSC.
- G. Zhan and H. C. Zeng, Adv. Funct. Mater., 2016, 26, 3268–3281 CrossRef CAS.
- Y. Liu, W. Zhang, S. Li, C. Cui, J. Wu, H. Chen and F. Huo, Chem. Mater., 2014, 26, 1119–1125 CrossRef CAS.
- Y. Liu, J. Zhang, L. Song, W. Xu, Z. Guo, X. Yang, X. Wu and X. Chen, ACS Appl. Mater. Interfaces, 2016, 8, 22745–22750 CAS.
- A. Delori, T. Friscic and W. Jones, CrystEngComm, 2012, 14, 2350–2362 RSC.
- T. Friscic and L. Fabian, CrystEngComm, 2009, 11, 743–745 RSC.
- S. Tanaka, K. Kida, T. Nagaoka, T. Ota and Y. Miyake, Chem. Commun., 2013, 49, 7884–7886 RSC.
- P. J. Beldon, L. Fábián, R. S. Stein, A. Thirumurugan, A. K. Cheetham and T. Friščić, Angew. Chem., Int. Ed., 2010, 49, 9640–9643 CrossRef CAS PubMed.
- D. Crawford, J. Casaban, R. Haydon, N. Giri, T. McNally and S. L. James, Chem. Sci., 2015, 6, 1645–1649 RSC.
- J.-B. Lin, R.-B. Lin, X.-N. Cheng, J.-P. Zhang and X.-M. Chen, Chem. Commun., 2011, 47, 9185–9187 RSC.
- I. Stassen, N. Campagnol, J. Fransaer, P. Vereecken, D. De Vos and R. Ameloot, CrystEngComm, 2013, 15, 9308–9311 RSC.
- X. Feng, C. Jia, J. Wang, X. Cao, P. Tang and W. Yuan, Green Chem., 2015, 17, 3740–3745 RSC.
- C. Mottillo, Y. Lu, M.-H. Pham, M. J. Cliffe, T.-O. Do and T. Friscic, Green Chem., 2013, 15, 2121–2131 RSC.
- M. J. Cliffe, C. Mottillo, R. S. Stein, D.-K. Bucar and T. Friscic, Chem. Sci., 2012, 3, 2495–2500 RSC.
- V. André, A. Hardeman, I. Halasz, R. S. Stein, G. J. Jackson, D. G. Reid, M. J. Duer, C. Curfs, M. T. Duarte and T. Friščić, Angew.
Chem., Int. Ed., 2011, 50, 7858–7861 CrossRef PubMed.
- J. Reboul, S. Furukawa, N. Horike, M. Tsotsalas, K. Hirai, H. Uehara, M. Kondo, N. Louvain, O. Sakata and S. Kitagawa, Nat. Mater., 2012, 11, 717–723 CrossRef CAS PubMed.
- M. Nakahama, J. Reboul, K.-i. Kamei, S. Kitagawa and S. Furukawa, Chem. Lett., 2014, 43, 1052–1054 CrossRef CAS.
- G. Zhan, L. Ke, Q. Li, J. Huang, D. Hua, A.-R. Ibrahim and D. Sun, Ind. Eng. Chem. Res., 2012, 51, 15753–15762 CrossRef CAS.
- T. Toyao, K. Liang, K. Okada, R. Ricco, M. J. Styles, Y. Tokudome, Y. Horiuchi, A. J. Hill, M. Takahashi, M. Matsuoka and P. Falcaro, Inorg. Chem. Front., 2015, 2, 434–441 RSC.
- E. Zanchetta, L. Malfatti, R. Ricco, M. J. Styles, F. Lisi, C. J. Coghlan, C. J. Doonan, A. J. Hill, G. Brusatin and P. Falcaro, Chem. Mater., 2015, 27, 690–699 CrossRef CAS.
- S. Qiu, M. Xue and G. Zhu, Chem. Soc. Rev., 2014, 43, 6116–6140 RSC.
- J. Yao and H. Wang, Chem. Soc. Rev., 2014, 43, 4470–4493 RSC.
- Y. Yue, Z.-A. Qiao, X. Li, A. J. Binder, E. Formo, Z. Pan, C. Tian, Z. Bi and S. Dai, Cryst. Growth Des., 2013, 13, 1002–1005 CAS.
- N. Kornienko, Y. Zhao, C. S. Kley, C. Zhu, D. Kim, S. Lin, C. J. Chang, O. M. Yaghi and P. Yang, J. Am. Chem. Soc., 2015, 137, 14129–14135 CrossRef CAS PubMed.
- I. Stassen, M. Styles, G. Grenci, H. V. Gorp, W. Vanderlinden, S. D. Feyter, P. Falcaro, D. D. Vos, P. Vereecken and R. Ameloot, Nat. Mater., 2016, 15, 304–310 CrossRef CAS PubMed.
- Y. Mao, J. Li, W. Cao, Y. Ying, L. Sun and X. Peng, ACS Appl. Mater. Interfaces, 2014, 6, 4473–4479 CAS.
- Y. Mao, H. Huang, Y. Liu, L. Shi, W. Cao, J. Li, L. Sun and X. Peng, CrystEngComm, 2013, 15, 5591–5593 RSC.
- C. Kuo, Y. Tang, L. Chou, B. T. Sneed, C. N. Brodsky, Z. Zhao and C. Tsung, J. Am. Chem. Soc., 2012, 134, 14345–14348 CrossRef CAS PubMed.
- K. Khaletskaya, J. Reboul, M. Meilikhov, M. Nakahama, S. Diring, M. Tsujimoto, S. Isoda, F. Kim, K.-i. Kamei, R. A. Fischer, S. Kitagawa and S. Furukawa, J. Am. Chem. Soc., 2013, 135, 10998–11005 CrossRef CAS PubMed.
- Y. Zhao, N. Kornienko, Z. Liu, C. Zhu, S. Asahina, T.-R. Kuo, W. Bao, C. Xie, A. Hexemer, O. Terasaki, P. Yang and O. M. Yaghi, J. Am. Chem. Soc., 2015, 137, 2199–2202 CrossRef CAS PubMed.
- F. Cheng, W.-C. Li, J.-N. Zhu, W.-P. Zhang and A.-H. Lu, Nano Energy, 2016, 19, 486–494 CrossRef CAS.
- F. Bu, L. Xu, W. Zhang, C. Jin, R. Qi, R. Huang and J. Jiang, Chem. Commun., 2015, 51, 6198–6201 RSC.
- Y. Yue, B. Guo, Z.-A. Qiao, P. F. Fulvio, J. Chen, A. J. Binder, C. Tian and S. Dai, Microporous Mesoporous Mater., 2014, 198, 139–143 CrossRef CAS.
- Y. Mao, J. Li, W. Cao, Y. Ying, P. Hu, Y. Liu, L. Sun, H. Wang, C. Jin and X. Peng, Nat. Commun., 2014, 5, 5532 CrossRef PubMed.
Footnote |
† Electronic supplementary information (ESI) available: A list of solid matters reported in the literature for MOF synthesis. See DOI: 10.1039/c6cc07094a |
|
This journal is © The Royal Society of Chemistry 2017 |
Click here to see how this site uses Cookies. View our privacy policy here.