DOI:
10.1039/C6RA21704D
(Paper)
RSC Adv., 2016,
6, 104104-104111
Removal of toluene in adsorption–discharge plasma systems over a nickel modified SBA-15 catalyst
Received
30th August 2016
, Accepted 19th October 2016
First published on 26th October 2016
Abstract
An atmospheric-pressure dielectric barrier discharge (DBD) has been used to investigate the destruction of low concentrations of toluene with nickel loaded SBA-15 (Ni–SBA) catalyst in adsorption–discharge plasma system. The adsorption capacity and catalytic activity of SBA and Ni–SBA were studied. The experimental results showed that the incorporation of Ni into the ordered hexagonal mesopores of SBA afforded a remarkable enhancement in the catalytic activity and CO2 selectivity. However, the presence of the metal oxide lowered the specific surface area and decreased the adsorbed amount of toluene. In situ FTIR was used to explore catalysts adsorption process, and revealed that incorporation of Ni resulted in partial oxidation of toluene over Ni–SBA. The catalysts, after several adsorption-plasma process cycles, were characterized by XRD and TEM techniques. The results indicated that the plasma treatment tended to decrease the size of the metal oxides and increase their dispersion in the support surface and influence the adsorption and catalytic performance. In addition, GC-MS spectra were used to analyze the by-products and speculate the reason of catalysts deactivation.
1. Introduction
Toluene is extensively used as an industrial solvent and reagent (paints and coatings, gums, medicines, dyes etc.) and it is also one of important components in gasoline.1 Its emission is harmful to ecological system and human health, therefore, reducing its emission is required in accordance with regulations in many countries.2 Furthermore, several conventional techniques have been applied to control toluene emission including adsorption,3 membrane separation4 and catalytic oxidation.5 However, these methods are not cost-effective for the abatement of low concentration volatile organic compounds (VOCs) in high volume waste gas streams.
In the last two decades, extensive research has been devoted to utilizing non-thermal plasma (NTP) technology because of its capability of eliminating various low concentration VOCs simultaneously under ambient conditions.6 Unfortunately, the NTP technology is accompanied with some hazardous by-products (such as ozone) which resulting in low carbon dioxide selectivity. Recently, NTP assisted catalysis has been regarded as one of the emerging technologies and has attracted increasing interests.7 The combination of NTP and catalysis has great potential to enhance the removal efficiency of the gas pollutant, increase the selectivity of the desired final products through deep oxidation and reduce the generation of undesirable by-products.
Catalysts which possess sufficient VOC adsorption capacity and excellent catalytic performance for oxidation of the adsorbed VOCs were essential in plasma-catalysis system. In recent years, various catalysts including NaNO2, HZSM-5, γ-Al2O3 and TiO2 have been developed to improve the performance of plasma-catalytic oxidation of VOCs.8–11 Wang et al.9 had compared Ag/HZSM-5, Mn/HZSM-5 and Ce/HZSM-5 catalysts for plasma-catalytic oxidation of adsorbed toluene and found that Ag–Mn/HZSM-5 displayed the best catalytic performance. Zhao et al.12 reported that the presence of Ag and Cu in the AgCu/HZSM-5 significantly improved the removal efficiency of formaldehyde in a cycled storage–discharge system. The main reasons were attributed to the plasma-enhanced catalytic redox cycles between Ag and Cu species. However, high costs of noble metals limited their wide industrial applications. Therefore, the development of highly ozone decomposable and stable metal oxide catalysts will be desirable for application in plasma-catalytic oxidation of VOCs.
Ni-based catalysts, highly actively in ozone decomposition and effective inhibition of carbon deposition,13,14 were extensively used as catalysts for the oxidation of VOCs. Wu et al.11 combined non-thermal plasma with nickel oxide loaded on different supports to eliminate toluene, and found that the presence of water vapor significantly reduced the removal efficiency of toluene over Ni-based catalysts. In addition, the adsorption–discharge plasma system has also attracted more and more attention as a promising method to dispose VOCs.8,10 Xu et al.15 compared the toluene decomposition efficiencies on AgMn/SBA-15 in the plasma-catalysis system with continuous and cyclic plasma systems. It was found that the adsorption–discharge plasma system significantly improved the carbon balance. In adsorption–discharge plasma system, toluene was firstly adsorbed on the catalysts and then the pollutant was cut down, and the adsorbed toluene was degraded by plasma with air.
In this work, impregnation method was used to prepare Ni–SBA catalyst which was applied to investigate the catalytic decomposition performance of toluene in adsorption–discharge non-thermal plasma system. The adsorption process of toluene on the surface of the catalysts was monitored by in situ FTIR spectroscopy. Secondary products were analyzed by gas chromatogram-mass spectrum (GC-MS). Besides, a cyclic experiment was conducted and the as-prepared catalysts were characterized by XRD and TEM after several adsorption-plasma process cycles.
2. Experimental
2.1. Catalyst preparation
The supports (SBA-15, purchased from XFANO, INC) were dried in an oven at 110 °C for 12 h and cooled to room temperature. Ni–SBA catalysts were prepared by impregnation method using Ni(NO3)2 aqueous solutions, followed by ultrasound for 1 h and the precipitates of Ni–SBA with 5% wt of Ni to initial SBA-15 were collected and drying in air at room temperature for 24 h. The well-impregnated catalyst were then heated to 110 °C for 24 h and calcined with air at a heating rate of 2 °C min−1 from 30 °C to 400 °C, then held 5 h at 400 °C. The resulted catalyst contained 5 wt% nickel loadings and was named as Ni–SBA.
2.2. Catalyst characterization
Small-angle X-ray powder diffraction (XRD) was recorded with a Bruker D8-ADVANCE X-ray diffractometer using Cu Kα radiation (k = 0.154 nm, 40 kV, 40 mA). The N2 adsorption–desorption isotherms were carried out at 77 K on a Micromeritics ASAP 2020 instrument.
The shapes, morphologies and sizes of as-prepared catalysts were characterized by transmission electron microscopy (TEM) on a JEM-2100HR (JEOL, Japan) electron microscope at 200 kV. Hydrogen temperature programmed reduction (H2-TPR) was performed on ASAP 2920 (Micromeritics, USA) in order to determine the redox activity of the impregnated catalyst. Before measurement, 50 mg of catalyst was degassed at 300 °C for 1 h in argon gas flow, then the temperature declined to 30 °C. The carrier gas was changed to a mixture of 10 vol% H2/Ar at a flow rate of 30 ml min−1 and heated from 30 °C to 800 °C at a heating rate of 10 °C min−1.
Toluene temperature programmed desorption (toluene-TPD) was carried out in a quartz cylindrical fixed-bed microreactor. The catalyst was first activated in situ in a N2 atmosphere (20 ml min−1) at 350 °C for 0.5 h, then cooled to room temperature and exposed to 50 ppm toluene in microreactor at a flow rate of 40 ml min−1 for 1 h. After flushing with N2 at room temperature for 30 min, the catalyst was heated to 500 °C at different heating rates from 2 to 10 °C min−1 in flowing N2 (20 ml min−1). The desorbed toluene (m/z = 92) was continuously monitored by on-line mass spectrometry (Hiden Analytical Ltd. HPR20).
2.3. Catalytic evaluation and analyses
Toluene adsorption was carried out in a quartz tube (internal diameter of 6 mm) containing 150 mg of catalyst at room temperature (25 °C). A certain concentration of toluene (50 ppm) was passed through the reactor at a flow rate of 100 ml min−1. The outlet gas was analyzed by an on-line gas chromatography (GC-2014C, SHIMADZU), equipped with a flame ionization detector (FID) and a 30 m TG-WAXMS capillary column. The high voltage power, applied to the discharge reactor, was supplied by a booster (0–220 V) coupled with a high voltage impulse-generator (50 Hz, 0–15 kV) in series.
The specific input energy (SIE), toluene adsorption amount (na, mmol) and toluene mineralization rate (RC7H8) were defined as follows:
|
 | (1) |
|
 | (2) |
|
 | (3) |
|
 | (4) |
|
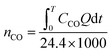 | (5) |
where
P (W) and
Q were the discharge power and gas flow rate;
Tb was the breakthrough time (min), corresponded to
Cinad/
Coutad = 0.1;
Cinad and
Coutad were the inlet and outlet concentration of toluene (ppm). The flow rates of adsorption and plasma catalysis process were the same, and
Q represented the flow rate (L min
−1);
T and
CCO2 were the discharge time (min) and the concentrations of CO
2 in the outlet gas stream during non-thermal plasma catalysis (ppm).
In situ FTIR were recorded at room temperature using a Nicolet 6700 FTIR spectrometer (16 scans, 4.0 cm−1 resolution) equipped with an MCT detector and cooled by liquid nitrogen. The remaining byproducts formed in the surface of the spent catalysts were qualitatively analyzed by a gas chromatography/mass spectrometry (GCMS-QP2010 Ultra, Shimadzu Corporation, Japan).
3. Results and discussion
3.1. Catalytic evaluation
The adsorption characteristics of SBA and Ni–SBA are shown in Fig. 1a. Pure SBA has longer breakthrough time than Ni–SBA sample, and their adsorption capacities are 15.1 μmol and 13.5 μmol, respectively. This can be attributed to the surface area decrease of the loading sample. The pure SBA-15 and Ni–SBA had a BET surface area of 499 m2 g−1 and 460 m2 g−1, respectively. Nickel loading on SBA-15 decreased its surface area, pore volume and pore size, as listed in Table 1, the changes of BET surface areas, pore volume and pore size for pure SBA-15 and Ni–SBA were small, which can be deduced that metal loaded SBA-15 retained a mesoporous structure of SBA-15. Fig. 1b displays the mineralization rates of toluene. After 60 min plasma treatment, Ni–SBA catalyst showed much higher toluene mineralization rate (∼71.8%) than pure SBA (∼53.6%), suggesting that toluene was probably completely converted to CO2 and CO over Ni–SBA than that of SBA. It can be attributed to the addition of nickel that accelerates the decomposition of ozone to form free radicals at ambient temperatures, and promotes the cleavage of C–C bond.16
 |
| Fig. 1 Adsorption and catalytic characteristics of SBA and Ni–SBA for toluene: (a) breakthrough curves and adsorption amount (insert), (b) toluene mineralization rate. | |
Table 1 Surface area, pore volume and pore diameter of pure SBA-15 and Ni–SBA catalysts
Samples |
Specific surface area (m2 g−1) |
Pore volume (cm3 g−1) |
Pore size (Å) |
SBA-15 |
499 |
0.90 |
68.0 |
Ni–SBA |
460 |
0.83 |
64.3 |
Fig. 2a and b display the yields of CO2 and CO over SBA and Ni–SBA catalysts in plasma catalysis process. As seen from the figure, both CO2 and CO concentrations first increased and then declined slowly over both SBA and Ni–SBA. It can be attributed to the decreasing amounts of toluene adsorbed on the catalysts. Furthermore, it can be found that CO2 amounts are higher over Ni–SBA, suggesting that toluene was probably completely converted to CO2 over Ni–SBA than that of SBA. Meanwhile, Fig. 2c shows the outlet ozone concentration as the discharge time extended. The outlet ozone concentration increased in plasma catalysis process in both catalysts, and Ni–SBA sample shows good ozone decomposition ability. The reason that outlet ozone concentration increased as the discharge time extended may be ascribed to (i) the reaction of excess molecular oxygen and atomic oxygen or the accumulation of organic intermediates over the active sites,17,18 (ii) the decreasing amounts of toluene adsorbed on the catalysts.
 |
| Fig. 2 As-prepared catalysts of (a) CO2 concentration, (b) CO concentration, (c) O3 emissions as functions of regeneration time. | |
To achieve the information about toluene adsorption over SBA and Ni–SBA catalysts, in situ FT-IR spectra with different adsorption time were recorded at 25 °C and displayed in Fig. 3. Noticeably, the intensity of the band assigned to phenyl ring vibrations at 1495 cm−1 is increased gradually as the adsorption time extended, suggesting the increasing amount of toluene adsorption on the as-prepared catalysts. The peaks at 1383 and 1453 cm−1, appeared over both SBA and Ni–SBA catalysts after adsorption for 60 min, were attributed to the bending vibrations of methylene group.19,20 Interestingly, some new bands were appeared in Ni–SBA sample after the adsorption of toluene. The bands at 1749 cm−1, 1735 cm−1, 1717 cm−1 and 1540 cm−1 were observed and attributed to the stretching modes of C
O, and C
C stretching modes of benzenoid rings was found at a band of 1473 cm−1.21–23 This result pointed out that some chemical reactions occurred in the methyl group over Ni–SBA catalyst which indicated that the incorporation of Ni led to a partial oxidation of toluene after adsorption.
 |
| Fig. 3 The in situ FT-IR spectra of toluene adsorbed on the surface of (a) SBA, (b) Ni–SBA. | |
3.2. Characterization of the catalysts
3.2.1. XRD and TEM analysis. As seen from the low-angle XRD patterns (shown in Fig. 4a), three peaks can be detected between 2θ = 0.5–5.0° with the strongest one corresponding to (100) diffraction followed by two weak diffraction from (110) and (200) planes. No significant changes were found after metal introduction, except the slight shift towards higher angles. This demonstrates a slight framework compaction for Ni–SBA and loading nickel did not destroy the mesoporous structure of SBA. For the wide angle XRD patterns of SBA and Ni–SBA samples as shown in Fig. 4b, the diffraction peaks of nickel oxide were detected, suggesting that the active component of Ni has been loaded onto SBA successfully. Fig. 4c and d display the TEM images of SBA and Ni–SBA, respectively. The images clearly demonstrated the uniform pores formed even after incorporation of the metal nickel, and the estimated diameter of the pores is around 7 nm. The mean particle sizes of NiO nanoparticles are nearly 15 nm and located on the surfaces of SBA as shown in Fig. 4d. The size of the dispersed metal oxides can strongly influence the catalytic activity for toluene oxidation.24
 |
| Fig. 4 XRD patterns of Ni–SBA (a) small angle region, (b) wide angle region, TEM images of (c) SBA, (d) Ni–SBA. | |
3.2.2. H2-TPR analysis. Fig. 5 presents the H2-TPR profiles of the loaded mesoporous SBA materials and bulk NiO sample. For pure NiO sample, a sharp reduction peak centered at 342 °C, which is ascribed to the reduction of Ni species from Ni2+ to Ni. Compared with NiO, Ni–SBA sample showed two broad peaks at 308 and 442 °C, and the hydrogen consumption of Ni–SBA sample is 1.36 mmol g−1. This suggests that there are two kinds of NiO species in the Ni–SBA sample. The first peak can be ascribed to the reduction of bulk NiO, and the second peak is attributable to the surface nickel silicate that complex NiO strongly interacting with support.25
 |
| Fig. 5 H2-TPR profiles of NiO and Ni–SBA catalysts. | |
3.2.3. Desorption activation energies of toluene vapor on the catalysts. Fig. 6 shows the toluene-TPD curves of toluene desorption on catalysts at different heating rates. Toluene-TPD experiments were carried out to evaluate the binding energy between toluene and the surfaces of SBA and Ni–SBA. Fig. 6 exhibits a single big asymmetric hump and the peak temperature (Tp) increased as the heating rate was increased from 2 to 10 °C (see Table 2). For SBA, the maximum toluene-TPD peaks can be observed at 78, 95, 105, 112 and 116 °C with heating rates from 2, 4, 6, 8 and 10 °C min−1, respectively. However, the maximum toluene-TPD peak shifted to a lower temperature with a maximum at 114 °C with a heating rate of 2 °C min−1 in the case of Ni–SBA. The TPD peak at a higher temperature indicated the presence of a stronger interaction between catalysts and toluene. The desorption activation energy (Ed) can be calculated from a series of Tp achieved at different heating rates.26 The Ed value of SBA-15 was bigger than that of Ni–SBA catalyst, suggesting that there is much stronger interaction between toluene and SBA surface compared to Ni–SBA. However, the higher toluene adsorption energy means higher activation barrier for the total oxidation to CO2 and are disadvantageous for the total oxidation of toluene.27 This result is in accordance with our observation that metal Ni doped SBA can improve the CO2 selectivity and toluene catalytic performance.
 |
| Fig. 6 Toluene-TPD profiles over the synthesized samples. | |
Table 2 Desorption activation energy of toluene vapor on SBA and Ni–SBA catalysts
Samples |
Maximum peak temperature Tm (K) at different heating rate |
Desorption activation energy Ed (kJ mol−1) |
2 K min−1 |
4 K min−1 |
6 K min−1 |
8 K min−1 |
10 K min−1 |
SBA-15 (toluene) |
78 |
95 |
105 |
112 |
116 |
41.149 |
Ni/SBA-15 (toluene) |
73 |
93 |
99 |
109 |
114 |
37.771 |
3.3. Cyclic operation experiments
3.3.1. Cyclic operation performance of Ni–SBA catalyst. Fig. 7a shows the toluene adsorption amount over SBA and Ni–SBA catalysts in several consecutive adsorption–catalysis processes. Interestingly, the adsorption amounts of toluene over pure SBA are almost identical, while the adsorption capacity of Ni–SBA increases gradually in the second cycle experiment. This can be attributed to the increase of metal oxide dispersion and the decrease of particle size which may be beneficial to the toluene adsorption and catalytic performance after plasma treatment,28 and it can be demonstrated confirmed by the following XRD and TEM results (shows in Fig. 8). Meanwhile, with the increase of adsorption–catalysis cycling times, the adsorption amount over SBA and Ni–SBA declined gradually. It may be ascribed to the accumulation of organic by-products which adsorbs on the surface of the spent catalyst, and cause the catalyst deactivation.29 Moreover, Fig. 7b gives the profiles of toluene mineralization rates of Ni–SBA sample in different adsorption–catalysis cycles. Similarly, Ni–SBA sample showed the highest toluene mineralization rates in the second adsorption–catalysis processes and then decreased gradually due to the accumulation of by-products.
 |
| Fig. 7 (a) Toluene adsorption cycle on SBA and Ni–SBA catalysts, (b) toluene mineralization rates in different cycles on Ni–SBA sample. | |
 |
| Fig. 8 XRD images of adsorption/regeneration cycles Ni–SBA catalyst (a) wide angle region, (b) small angle region, TEM images of (c) fresh Ni–SBA catalyst (d) Ni–SBA catalyst for several cycles of adsorption/regeneration process. | |
3.3.2. XRD and TEM analysis of cyclic operation catalysts. The low and wide angle XRD patterns of fresh and spent Ni–SBA catalyst were shown in Fig. 8a and b. No significant changes were observed after several adsorption/regeneration cycles. This result indicates that the structure of catalyst kept unchanged although the adsorption amount of toluene decreased slightly during several cycles of adsorption–catalysis processes. Fig. 8c displays the TEM images of fresh Ni–SBA catalysts (the same as Fig. 4d). Fig. 8d shows the TEM result of Ni–SBA sample that after several adsorption–catalysis circulation treatment. It can be seen that the size of the metal oxides became smaller and their dispersion increased. This result can certify the conclusion of Fig. 7 that the toluene adsorption amount and mineralization rates of Ni–SBA catalyst increased after plasma catalysis.
3.4. Byproducts analysis
Fig. 9 shows the GC-MS spectra of by-products over SBA and Ni–SBA catalysts after five cycles adsorption/regeneration process. More long-chained alkanes (2,4-dimethylheptane, 3,7-dimethyldecane, hexadecane and eicosane, etc.) were detected over pure SBA catalyst, while oxygen-containing organic compound (such as benzaldehyde, benzyl alcohol, methyl benzoate, etc.) were found in the loading sample. This result can be attributed to the fact that nickel can accelerate C–C, O–H, and C–H bond cleavage,30 leading to the formation of oxygen-containing organic compounds. Most of these compounds can be decomposed easily and at last the toluene decomposition efficiency was improved in this adsorption–discharge plasma system. From these GC-MS results, it can be speculated that oxygen-containing by-products may deactivate Ni–SBA. In addition, some nitrogen-containing organic compounds (o-nitrotoluene and p-nitrotoluene) were detected by GC-MS. Nitrotoluene appeared due to the reaction of toluene with excited NO2˙ radicals.31
 |
| Fig. 9 GC-MS spectra of by-products on the catalyst surface after adsorption/regeneration for fifth cycle (a) SBA, (b) Ni–SBA. | |
4. Conclusions
In this study, nickel modified SBA-15 was successfully prepared by impregnation method and applied to toluene removal in adsorption–discharge plasma system. The adsorption–regeneration performance of as-prepared catalyst was also studied. The main results showed that pure SBA had longer breakthrough time and higher adsorption capacity than Ni–SBA, while Ni–SBA catalyst exhibited eminent properties in toluene mineralization rate and CO2 yield. And the GC-MS results showed that more alkanes by-products and oxygen-containing organic compounds were found over SBA and Ni–SBA after several cycles of adsorption/regeneration reaction, respectively. This can be ascribed to the addition of nickel that accelerated the decomposition of ozone, formed more active species, and accelerated C–C, O–H, and C–H bond cleavage. Moreover, the adsorption amount of toluene over Ni–SBA increased after plasma treatment due to the decrease of metal oxide particle size and enhancement of dispersion that may be beneficial for toluene adsorption and catalytic stability.
Acknowledgements
This work was financially supported by National Natural Science Foundation of China (No. U1201231, No. 51378218, No. B5151050, No. 5110818, No. 51578245), Science and Technology Program of Guangzhou (No. 201510010164, 201607010095) and Fundamental Research Funds for the Central Universities (No. 2015zz052, D215086w, D2154140).
References
- H. T. Znad, K. Katoh and Y. Kawase, J. Hazard. Mater., 2007, 141, 745–752 CrossRef CAS PubMed.
- R. Huang, M. J. Lu, P. T. Wang, Y. D. Chen, J. L. Wu, M. L. Fu, L. M. Chen and D. Q. Ye, RSC Adv., 2015, 5, 72113–72120 RSC.
- S. Bhatia, A. Z. Abdullah and C. T. Wong, J. Hazard. Mater., 2009, 163, 73–81 CrossRef CAS PubMed.
- M. Zilli, C. Guarino, D. Daffonchio, S. Borin and A. Converti, Process Biochem., 2005, 40, 2035–2043 CrossRef CAS.
- Y. Dai, X. Y. Wang, Q. G. Dai and D. Li, Appl. Catal., B, 2012, 111–112, 141–149 CrossRef CAS.
- X. B. Zhu, X. Gao, R. Qin, Y. X. Zeng, R. Y. Qu, C. H. Zheng and X. Tu, Appl. Catal., B, 2015, 170–171, 293–300 CrossRef CAS.
- A. M. Vandenbroucke, R. Morent, N. De Geyter and C. Leys, J. Adv. Oxid. Technol., 2012, 15, 232–241 CAS.
- W. J. Liang, J. Li, J. X. Li, T. Zhu and Y. Q. Jin, J. Hazard. Mater., 2010, 175, 1090–1095 CrossRef CAS PubMed.
- W. Z. Wang, H. L. Wang, T. L. Zhu and X. J. Fan, J. Hazard. Mater., 2015, 292, 70–78 CrossRef CAS PubMed.
- W. C. Xu, N. Wang, Y. D. Chen, J. D. Chen, X. X. Xu, L. Yu, L. M. Chen and D. Q. Ye, Catal. Commun., 2016, 84, 61–66 CrossRef CAS.
- J. Wu, Q. Xia, H. Wang and Z. Li, Appl. Catal., B, 2014, 156–157, 265–272 CrossRef CAS.
- D. Z. Zhao, X. S. Li, C. Shi, H. Y. Fan and A. M. Zhu, Chem. Eng. Sci., 2011, 66, 3922–3929 CrossRef CAS.
- J. R. Rostrupnielsen and J. H. B. Hansen, J. Catal., 1993, 144, 38–49 CrossRef CAS.
- R. Yang, C. Xing, C. Lv, L. Shi and N. Tsubaki, Appl. Catal., A, 2010, 385, 92–100 CrossRef CAS.
- X. X. Xu, P. T. Wang, W. C. Xu, J. L. Wu, L. M. Chen, M. L. Fu and D. Ye, Chem. Eng. J., 2016, 283, 276–284 CrossRef CAS.
- S. Pattanaik, F. E. Huggins and G. P. Huffman, J. Hazard. Mater., 2010, 178, 804–813 CrossRef CAS PubMed.
- X. Fan, T. Zhu, Y. Wan and X. Yan, J. Hazard. Mater., 2010, 180, 616–621 CrossRef CAS PubMed.
- H.-H. Kim, A. Ogata and S. Futamura, Appl. Catal., B, 2008, 79, 356–367 CrossRef CAS.
- X. Liu, J. K. Lambert, D. A. Arendarskiia and R. J. Farrauto, Appl. Catal., B, 2001, 35, 125–136 CrossRef CAS.
- J. M. Joskowska, I. Kopczynska, B. Debski, D. H. Kedzia, R. Aranowski and J. Hupka, Physicochem. Probl. Miner. Process., 2012, 48, 129–140 Search PubMed.
- W. F. Chen and L. F. Yan, Nanoscale, 2010, 2, 559–563 RSC.
- L. He, J. Li and J. H. Xin, Biosens. Bioelectron., 2015, 70, 69–73 CrossRef CAS PubMed.
- W. Gamrad, A. Dreier, R. Goddard and K. R. Pörschke, Angew. Chem., Int. Ed., 2015, 54, 4482–4487 CrossRef CAS PubMed.
- H. Li, Y. B. She and T. Wang, Front. Chem. Sci. Eng., 2012, 6, 356–368 CrossRef CAS.
- Q. H. Trinh, S. B. Lee and Y. S. Mok, J. Hazard. Mater., 2015, 285, 525–534 CrossRef CAS PubMed.
- Z. J. Zhang, S. K. Xian, H. X. Xi, H. H. Wang and Z. Li, Chem. Eng. Sci., 2011, 66, 4878–4888 CrossRef CAS.
- E. J. Park, J. H. Lee, K. D. Kim, D. H. Kim, M. G. Jeong and Y. D. Kim, Catal. Today, 2016, 260, 100–106 CrossRef CAS.
- Z. H. Li, S. X. Tian, H. T. Wang and H. B. Tian, J. Mol. Catal. A: Chem., 2004, 211, 149–153 CrossRef CAS.
- D. Torres and P. Liu, Catal. Lett., 2012, 142, 1211–1217 CrossRef CAS.
- M. Zhao, T. L. Church and A. T. Harris, Appl. Catal., B, 2011, 101, 522–530 CrossRef CAS.
- C. M. Du, J. H. Yan and B. Cheron, Plasma Sources Sci. Technol., 2007, 16, 791–797 CrossRef CAS.
|
This journal is © The Royal Society of Chemistry 2016 |
Click here to see how this site uses Cookies. View our privacy policy here.