DOI:
10.1039/C6RA20634D
(Paper)
RSC Adv., 2016,
6, 109083-109090
FESEM and XPS studies of ZrO2 modified electrodeposited NiCoCrAlY nanocomposite coating subjected to hot corrosion environment
Received
16th August 2016
, Accepted 7th November 2016
First published on 7th November 2016
Abstract
The aim of this study is to investigate the influence of Co and reactive element oxide, i.e. ZrO2, addition on the hot corrosion behavior of NiCrAlY electrodeposited nanocomposite coatings. The hot corrosion behavior of the coatings was investigated in a medium comprising 75% Na2SO4 and 25% NaCl and expressed as weight change. The addition of ZrO2 resulted in a reduction of Co content from 40 wt% to 20 wt%, as shown by EDX. The hot corrosion studies revealed that the addition of cobalt and yttrium to the NiCrAl coating enhanced its corrosion resistance. However, the effect of Y was more pronounced in the case of NiCrAl compared to NiCoCrAl coatings. The introduction of small amounts of ZrO2 further resulted in a reduction in weight gain. The formation of oxide of Ni on the surface of NiCrAlY and that of Co on the surface of NiCoCrAlY coatings was confirmed by FESEM and XPS analysis. XPS analysis revealed the presence of oxide of Al as well as small amounts of oxide of Cr on the surface and near surface of NiCrAlY and NiCrAlY(Z) coatings, while only oxide of Cr was observed in NiCoCrAlY and NiCoCrAlY(Z) coatings and this was responsible for their improved hot corrosion resistance.
1. Introduction
Hot corrosion is a rapid form of attack that occurs on metals and alloys from their interaction with alkali metal contaminants, such as sodium/potassium, and with sulfur in fuel to form molten sulfates.1 The damage is accelerated when the surfaces are covered with a thin film of fused salt in an oxidizing atmosphere at elevated temperatures. Such an attack results in the formation of a porous, non-protective oxide scale at the surface.1 The combination of high temperature with environmental contaminants and low-grade fuels, such as sodium, vanadium and chlorine, has attracted special attention to the phenomenon of hot corrosion.2 Hot corrosion processes are generally of two types, namely, high temperature hot corrosion (HTHC) or Type I and low temperature hot corrosion (LTHC) or Type II.3 Type I hot corrosion is observed mainly within the temperature range of 800–950 °C.4 It initiates with the condensation of fused alkali metal salts on the surface of the components. A cycle of chemical reactions take place, initially attacking the protective oxide film and subsequently progressing into the coating/substrate material. The depletion of elements like Al and Cr leads to the accelerated oxidation of base material, resulting in porous scale formation. The macroscopic appearance of HTHC is characterized by severe peeling of the metal and by significant color change. For example, a greenish color appears on the surface of metals and alloys due to the formation of NiO in the area of accelerated attack.5 On the other hand, LTHC is observed mainly in the temperature range of 670–750 °C.6 In this form of hot corrosion, low melting point eutectic mixtures like Na2SO4 and CoSO4 (the melting temperature is 540 °C) result in pitting corrosion in localized areas. This localized attack can be related to the localized failure of the scale due to either thermal cycling, erosion or chemical reactions.6
Advances in materials development and coating technology have increased the operating temperatures of gas turbines, boilers and industrial waste incinerators.7 Composite coatings are able to meet the spectrum of requirements like oxidation and corrosion resistance while the base material provides the necessary mechanical properties. MCrAlY, where M is Ni, Co, Fe or their combination, type coatings are adopted to combat the effects of hot corrosion to a greater extent. This type of coating is conventionally obtained from methods like plasma spraying, high velocity oxy fuel spraying and electron beam physical vapor deposition.6 Electrodeposition method is being widely used for the development of wear and corrosion resistant coatings. However, scarce reports are available on the development of high temperature coatings like MCrAlY by electrodeposition method.8,9 Saremi et al. explored the feasibility of electrodepositing NiCrAlY coating from the individual elemental particles on the superalloy IN-738 and investigated its oxidation and hot corrosion behaviour. They successfully deposited the coating on a superalloy substrate and observed an improvement in the hot corrosion and cyclic oxidation behaviour.8 Bahamirian et al. deposited NiCrAlY coating by electroplating and atmospheric plasma spray methods on an IN738LC substrate followed by atmospheric plasma spraying of yttria stabilized zirconia (YSZ).9 They observed that the transformation of zirconia from tetragonal to monoclinic phase is much lower in the electroplated NiCrAlY and YSZ plasma sprayed system. This was required for hot corrosion and thermal shock resistance.9 Yang et al.10,11 compared the hot corrosion and oxidation behaviour of an electrodeposited Ni–Cr–Al nanocomposite coating with an arc melted NiCrAl alloy. They observed that the hot corrosion behaviour of the nanocomposite coating was better due to the formation of a continuous and compact oxide scale.10 They also reported that the oxidation properties of the nanocomposite coating could be improved by optimizing the composition, incorporating more nanoparticles and the addition of a reactive element oxide.11
Thus, it can be seen that explicit reports are available on electrodeposited NiCrAlY coating. However, scarce reports are available on the development and hot corrosion behaviour of the NiCoCrAlY coating. The presence of cobalt in the NiCrAlY coating helps to enhance the high temperature performance of the coating. In the present study, an attempt has been made to develop the NiCoCrAlY coating and understand its hot corrosion behaviour. Furthermore, the effect of addition a reactive oxide, namely zirconia, on the hot corrosion behaviour of NiCoCrAlY coatings has also been studied. The hot corrosion studies were performed in 75% Na2SO4 + 25% NaCl mixture at 800 °C. X-ray photoelectron spectroscopy was specifically adopted to identify the products formed on the surface during the exposure of these coatings to the hot corrosive environment.
2. Experimental details
The NiCrAlY and NiCoCrAlY nanocomposite coatings were developed by conventional electrodeposition method using additive free sulfamate electrolyte. The composition of the electrolyte is as follows: nickel sulfamate 250 g L−1, nickel chloride 6 g L−1 and boric acid 30 g L−1. The development of the nanocomposite coating comprises two steps: the first step consisted of suspending the chromium (Cr) and aluminium (Al) nanoparticles in the electrolyte for nearly 16 h followed by electrodeposition of NiCrAl and NiCoCrAl nanocomposite coatings. The second step comprised yttrium (Y) incorporation by immersing the composite coating in 10% yttrium nitrate solution followed by homogenization. The detailed procedure has been discussed elsewhere.8 Cobalt was introduced in the electrolyte as cobalt sulfamate and the content was optimized so as to obtain 40 wt% in the coating. A cobalt content of 40 wt% was chosen as Ni–Co alloys with less than 50 wt% Co exhibit good mechanical properties while those above 50 wt% Co are suitable for magnetic applications.12 The zirconia (ZrO2) modified coatings were prepared by dispersing nano ZrO2 particles along with Cr and Al particles in the electrolyte and the obtained coatings were designated as NiCrAlY(Z) and NiCoCrAlY(Z). All the coatings were deposited on a Ni sheet (cathode) with a plating area of 3.75 cm × 3.75 cm and a nickel plate with a dimension of 3.75 cm × 5.0 cm was employed as the anode. The pH of the electrolyte was maintained at 4.00 and the deposition was performed galvanostatically at 0.016 A cm−2 to obtain a coating thickness of 45 ± 5 μm. The nanoparticles were kept in suspension during electrodeposition by subjecting to magnetic stirring at a speed of 350 ± 20 rpm. Prior to electrodeposition, the nickel sheet was subjected to a pretreatment sequence to obtain an adherent coating. The pretreatment consisted of immersion in 10% nitric acid for 15 s followed by cathodic activation in 20% sodium hydroxide by applying a current density of 0.16 A cm−2 for 1 min. The activated nickel substrate was then neutralized by immersion in 20% sulfuric acid for 30 s followed by thorough rinsing in deionized water. The electrodeposited Ni/NiCoCrAlY and Ni/NiCoCrAlY(Z) nanocomposite coatings were homogenized at 1000 °C for 2 h.
The hot corrosion properties of the unmodified and ZrO2 modified NiCrAlY and NiCoCrAlY nanocomposite coatings were studied by initially preheating the coatings on a hot plate for 30 min followed by applying a paste of 75% Na2SO4 and 25% NaCl mixture using a brush so as to obtain a salt deposit of 4–6 mg cm−2. The salt-coated coatings were allowed to dry and were then heat-treated by placing in a muffle furnace preheated to 800 °C for duration of 6 h. The heat-treated coatings were taken out, cooled to ambient conditions, washed with boiling distilled water for 30 min and ultimately dried and weighed. The hot corrosion resistance is expressed in terms of mass gain.
The surface morphology and composition of Ni/NiCoCrAlY and Ni/NiCoCrAlY(Z) composite coatings after subjected to hot corrosion environment were characterized using field emission scanning electron microscope (FESEM) and energy dispersive X-ray analysis (EDX) affixed with FESEM. X-ray photoelectron spectroscopy (XPS) of these nanocomposite coatings were recorded with a SPECS spectrometer using non-monochromatic Al Kα radiation (1486.6 eV) as an X-ray source operated at 150 W (12 kV, 12.5 mA). All binding energies reported here were referenced with C1s peak at 284.6 eV. For XPS analysis, the coatings were mounted on the sample holders after cutting into small pieces and kept in the load-lock chamber at ultrahigh vacuum (UHV) of 10−9 Torr for 5 h in order to desorb any volatile species present on the surface. After 5 h, the coatings were placed into analyzer chamber with UHV at 10−9 Torr. Survey and individual core level spectra were recorded with pass energies of 70 and 40 eV, respectively. Sputtering of the coating samples was carried out by defocused Ar+ ion beam using IQE11/35 ion gun by applying energy of 1 keV with Ar gas pressure of 1 × 10−6 Torr for 3 min. In estimating the atomic percentages, the entire peak area under the core level spectra of respective element with the spin–orbit doublet was considered.
3. Results and discussion
3.1 Composition
The cobalt, aluminium, chromium, zirconium and oxygen contents in the as-deposited coatings and that after exposure to hot corrosive environment at 800 °C were determined by EDX analysis and are summarized in Table 1. The Cr and Al content in the NiCrAlY composite coating were observed to be 0.5 wt% and 1.3 wt%, respectively. The modification of the coating with small amounts of ZrO2 (<0.5 wt%) resulted in a marginal increase in the Cr (1.0 wt%) and Al (2.0 wt%) contents. It can also be seen from the table that alloying of Ni with 40 wt% Co increases the Cr and Al contents in the NiCoCrAlY coating. The increase in Cr and Al contents can be related to the increase in their solubility in the γ phase present primarily in the NiCrAl system.13 The detailed characterization of the Ni/NiCo–Cr–Al composite coating has been discussed by the authors elsewhere.14 However, modification of the coatings with small amounts of ZrO2 resulted in a reduction in cobalt content from 40 wt% to 20 wt%. The reduction in Co content in the ZrO2 modified coating led to marginally lower Cr and Al contents in the NiCoCrAlY(Z) composite coating. Such a reduction in Cr and Al contents was not seen in the NiCrAlY coatings. This suggests that the ZrO2 particles affect the cobalt reduction on the cathode. Alternatively, the anomalous co-deposition of Co in the presence of Ni is affected by the addition of ZrO2. A similar effect of ZrO2 on Ni–Co alloys has been reported elsewhere by one of the co-authors.15 The Y content in all the coatings is about 0.2 wt%.
Table 1 Elemental analysis of Ni/NiCoCrAlY and Ni/NiCoCrAlY(Z) by EDX (concentration in at% is given in brackets)
Coatings |
Co, wt% |
Cr, wt% |
Al, wt% |
Zr, wt% |
As-deposited |
Hot corroded |
As-deposited |
Hot corroded |
As-deposited |
Hot corroded |
As-deposited |
Hot corroded |
NiCrAlY |
— |
— |
0.5 (0.6) |
0.04 (0.05) |
1.3 (2.8) |
0.11 (0.2) |
— |
— |
NiCrAlY(Z) |
— |
— |
1.0 (1.2) |
0.6 (0.8) |
2.0 (3) |
0.5 (0.6) |
0.3 (0.2) |
— |
NiCoCrAlY |
40 (38.9) |
70 (43) |
2.0 (1.8) |
— |
3.0 (5.6) |
0.4 (0.5) |
— |
— |
NiCoCrAlY(Z) |
20 (18.7) |
71 (44) |
1.0 (1) |
— |
2.0 (3) |
— |
0.4 (0.25) |
— |
3.2 Hot corrosion behaviour
The hot corrosion behaviour expressed in terms of weight gain is shown in Fig. 1. A correlation between the weight gain and corrosion resistance has been reported by Stearns et al.16 They reported that the onset of hot corrosion is preceded by an induction period i.e. a period of little or no weight gain. The induction period is followed by a period of rapidly accelerating weight gain that may either consume the entire sample or transform into a period of decelerating weight gain. It can be seen from Fig. 1 that the weight gain of the NiCoCrAl coating is significantly less compared to that of the NiCrAl coating. In other words, the addition of Co in NiCrAl coating assisted in enhancing the hot corrosion resistance. This can be attributed to the fact that addition of Co reduces the diffusion velocity of sulfur (obtained from the corrosive medium) by two orders of magnitude as compared to Ni.17 Hence, the presence of Co in the NiCrAl coating reduces the internal diffusion of sulfur during the hot corrosion and, consequently, the sulfuration/oxidation cyclic reaction during the corrosion process could be alleviated effectively. The incorporation of yttrium resulted in a substantial decrease in the weight gain of the NiCrAl coating while the effect was negligible in the case of the NiCoCrAl coating. Yttrium, in addition to increasing the adhesion strength of the oxide scale, also decreases the detrimental effect of sulfur.18 While Y and Co individually improve the hot corrosion resistance, their addition together did not reveal any additional increase in the hot corrosion resistance. The modification of the coatings with reactive oxide, namely zirconia, further reduced the weight gain of both the coatings. The weight gain was lower in the case of NiCoCrAlY(Z) composite coating compared to NiCrAlY(Z) coating. Thus, two inferences can be drawn from the weight gain studies: firstly, alloying of nickel with cobalt imparts hot corrosion resistance and secondly the incorporation of small amounts of reactive oxide particles like zirconia enhances the resistance towards hot corrosion. The hot corrosion studies have been performed at 800 °C hence, it is Type I hot corrosion and Rapp and Goto have proposed the Type I hot corrosion as a fluxing process wherein the attack is induced via liquid Na2SO4 deposits whereby oxygen and sulfur removal from the Na2SO4 causes the Na2O activity in the Na2SO4 to be increased to levels at which oxides such as NiO and Al2O3 can be fluxed from the alloy surface and precipitated out in the Na2SO4 as discontinuous particles. This process has been shown to be unaffected by the composition of the gas phase.19
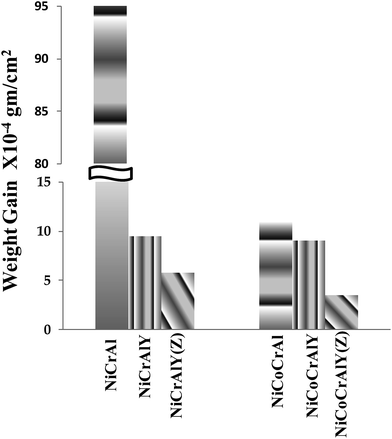 |
| Fig. 1 Comparative oxidation behavior of Ni/NiCoCrAlY and ZrO2 modified Ni/NiCoCrAlY coatings. | |
3.3 Surface morphology
The morphologies of the products formed on the surface of Ni/NiCoCrAlY and Ni/NiCoCrAlY(Z) coatings exposed to hot corrosion environment are presented in Fig. 2. Sharp edged facet like morphology is observed on the surface of NiCrAlY coating. EDX analysis revealed that the facet consists essentially of Ni and O corresponding to NiO. A fine crystalline matrix with a continuous oxide network that comprises cobalt and oxygen is seen on the surface of the NiCoCrAlY composite coating (Fig. 2). A smooth round edged facet morphology of NiO is observed on the surface of the NiCrAlY(Z) composite coating while a fine matrix morphology with bright discontinuous cobalt based oxide dispersed throughout the coating is observed on the surface of the NiCoCrAlY(Z) coating. The presence of the dispersed oxide can be associated with the reduced Co content in the latter coating, thereby resulting in reduced amounts of cobalt based oxide in the ZrO2 modified coating.
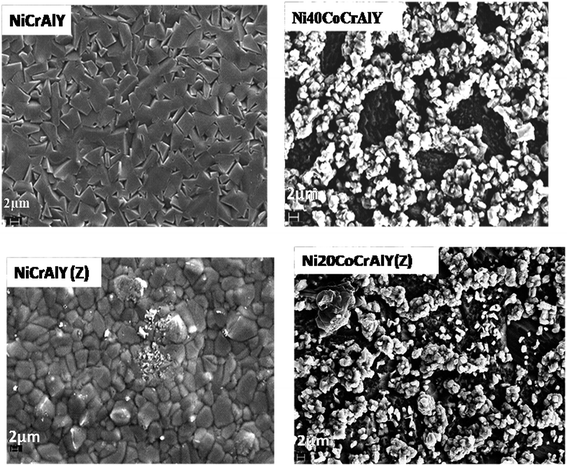 |
| Fig. 2 Surface morphologies of Ni/NiCoCrAlY and ZrO2 modified Ni/NiCoCrAlY coatings. | |
3.4 XPS studies
Typical survey spectra of NiCrAlY based alloy coatings are shown in Fig. 3. They clearly show the presence of Ni, Cr and Al in the NiCrAlY coatings and Ni, Cr, Co in the NiCoCrAlY coatings. The survey scan shows the absence of both zirconium and yttrium on the surface and sub-surface. Typical XP spectra of Ni 2p core levels of hot-corroded and sputtered NiCrAlY and NiCrAlYZrO2 coatings are shown in Fig. 4. A Ni 2p3/2 peak at 854.3 eV along with a characteristic satellite peak at 861 eV is observed, which are assigned to NiO species.20 After sputtering, the peak intensities increased in both the coatings. A similar Ni 2p3/2 core level spectra were also observed for NiCoCrAlY and NiCoCrAlYZrO2 coatings. An Al 2p binding energy peak is observed around 73.3 eV in both Ni–Cr–Al–Y and Ni–Cr–Al–Y–ZrO2 coatings, as displayed in Fig. 5. This corresponds to a suboxide of Al.21,22 After sputtering, the binding energy is shifted to 72.5 eV, which can be assigned to the intermetallic aluminide phase.23 The presence of Al was not observed in the NiCoCrAlY type coatings. The Cr 2p core level spectra obtained for NiCoCrAlY and NiCoCrAlYZrO2 coatings are shown in Fig. 6 and a peak related to Cr 2p3/2 was observed at 576.5 eV in both the coatings, which corresponds to Cr3+ species i.e. Cr2O3.24 The intensity of oxidized Cr species increases after sputtering in both coatings. Similar Cr 2p core level spectra were also obtained for hot-corroded and sputtered NiCrAlY and NiCrAlYZrO2 coatings. Typical Co 2p core level spectra of the hot-corroded and sputtered NiCoCrAlY and NiCoCrAlYZrO2 coatings are shown in Fig. 7. The Co 2p3/2 core level peak at 780.4 eV with a characteristic satellite peak in both NiCoCrAlY and NiCoCrAlYZrO2 coatings is attributed to the Co2+ state.25 After sputtering, the intensity of oxidized Co increases. The XP spectra of O 1s core levels of NiCrAlY and NiCoCrAlY based coatings are observed to be broad in nature and they can be curve-fitted into several component peaks. Accordingly, the hot-corroded coatings show a main peak around 530.0 eV that corresponds to oxygen associated to metal oxides like NiO and CoO, whereas peaks at 531.8 and 533.4 eV are attributed to OH− and H2O species, respectively, present in the coatings.26 A typical O 1s core level spectrum of NiCoCrAlY coating is displayed in Fig. 8. The presence of adsorbed OH− and water molecules can be attributed to the fact that coatings were washed with water after hot corrosion studies. These are reduced after sputtering and, consequently, there is an increase in the oxide related peak upon sputtering. The absence of sulfur related peaks in the XPS survey scan after sputtering shows the absence of sulfide formation in the sub-surface of the coatings. This shows the stability of coating against sulfur attack at high temperature.
 |
| Fig. 3 Survey spectra of hot-corroded (top panel) and sputtered (bottom panel) coatings: (a) Ni–Cr–Al–Y, (b) Ni–Cr–Al–Y–ZrO2, (c) Ni–Co–Cr–Al–Y and (d) Ni–Co–Cr–Al–Y–ZrO2. | |
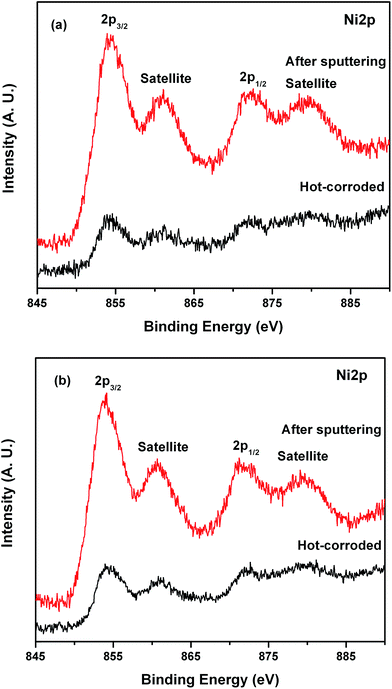 |
| Fig. 4 XPS of Ni 2p core levels of hot-corroded and sputtered (a) Ni–Cr–Al–Y and (b) Ni–Cr–Al–Y–ZrO2 coatings. | |
 |
| Fig. 5 XPS of Al 2p core levels of (a) hot-corroded and (b) sputtered Ni–Cr–Al–Y coating. | |
 |
| Fig. 6 XPS of Cr 2p core levels of hot-corroded and sputtered (a) Ni–Co–Cr–Al–Y and (b) Ni–Co–Cr–Al–Y–ZrO2 coatings. | |
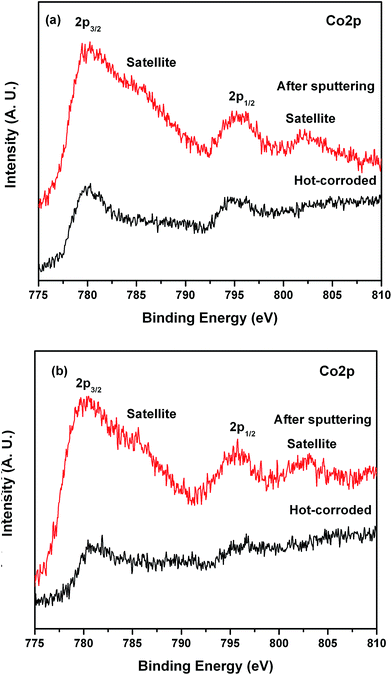 |
| Fig. 7 XPS of Co 2p core levels of hot-corroded and sputtered (a) Ni–Co–Cr–Al–Y and (b) Ni–Co–Cr–Al–Y–ZrO2 coatings. | |
 |
| Fig. 8 XPS of O 1s core level of (a) hot-corroded and (b) sputtered Ni–Co–Cr–Al–Y coating. | |
Relative surface concentrations of different elements in different conditions can be evaluated from XPS spectra using atomic sensitivity factors. Atomic percentages of different elements in hot-corroded as well as sputtered nanocomposite coatings are summarized in Table 2. The intensities of these elements were enhanced after sputtering. Addition of Co to the NiCrAl coating results in lower Al or no Al and lower Cr and Ni contents on the surface. The amount of Ni on the surface slightly increases after addition of ZrO2 in the NiCrAlY coating. On the other hand, the amount of Ni decreases when Co is added to the nanocomposite coating. It further decreases in the ZrO2 modified NiCoCrAlY coating. Again, the concentration of Co decreases after addition of ZrO2 in the coating. All these findings are consistent with the EDX results. As can be seen in the Table 2, the concentrations of Cr and Al are higher in the near surface region in the NiCrAlY coating with ZrO2. This shows that both the elements segregate on the coating surface, which is beneficial for corrosion resistance as they can form protective oxide layers on the surface. In addition, the amounts of Al and Ni are similar in the NiCrAlY based coatings. In the case of the Co containing coatings, XPS shows the absence of Al and the enrichment of Cr in the subsurface region. Addition of ZrO2 helps to increase the amount of Cr in the near surface region of the NiCrAlY coatings while a reduction is seen in the NiCoCrAlY coatings. Thus, the hot corrosion resistance of the NiCoCrAlY composite coatings is better than that of the NiCrAlY coatings owing to the presence of cobalt oxide and increased amounts of chromium oxide in the sub-surface region.
Table 2 Relative surface concentrations (at%) of different elemental species in Ni and Ni–Co based coatings after hot corrosion studies evaluated from XPS (concentrations after sputtering are given in brackets)
Coatings |
Ni |
Cr |
Al |
Y |
Co |
Zr |
O |
NiCrAlY |
10.3 (20.4) |
2.5 (0.4) |
10.7 (22.3) |
— (—) |
— (—) |
— (—) |
76.5 (56.9) |
NiCrAlY(Z) |
13.1 (23.9) |
3.3 (2.6) |
12.3 (26.2) |
— (—) |
— (—) |
— (—) |
71.3 (47.3) |
NiCoCrAlY |
5.0 (4.9) |
0.6 (13.1) |
— (—) |
— (—) |
10.9 (19.6) |
— (—) |
83.5 (62.4) |
NiCoCrAlY(Z) |
1.4 (4.3) |
3.2 (7.4) |
— (—) |
— (—) |
6.8 (11.7) |
— (—) |
88.6 (76.6) |
4. Conclusions
The Ni/Ni–CoCrAlY and their ZrO2 modified nanocomposite coatings were electrodeposited and their hot corrosion behavior evaluated in 75% Na2SO4 + 25% NaCl medium. Addition of Co to the NiCrAlY coating marginally enhanced the Cr and Al contents in the coating. Furthermore, addition of ZrO2 to the NiCoCrAlY coating resulted in a reduction in Co content in the coating. The hot corrosion resistance studies expressed in terms of weight gain revealed that the lowest gain was observed in the NiCoCrAlYZrO2 nanocomposite coating among all the coatings studied here. Distinct nickel and cobalt oxides were observed on the surface of the NiCrAlY and NiCoCrAlY coatings. This observation was obtained from both FESEM and XPS analysis. XPS studies showed the presence of intermetallic nickel aluminide in the NiCrAlY coatings. XPS analysis also demonstrated that both Al and Cr oxides are present in the NiCrAlY based coatings while the NiCoCrAlYZrO2 coatings are enriched with Cr responsible for their better hot corrosion resistance.
Acknowledgements
The authors would like to thank Director, CSIR-NAL, for the permission to publish this work. They also acknowledge Mr Siju for his assistance in performing the FESEM analysis. The financial assistance to perform this study was obtained from the Council of Scientific and Industrial Research, India.
References
- T. S. Sidhu, S. Prakash and R. D. Agrawal, Curr. Sci., 2006, 90, 41–47 CAS.
- N. Eliaz, G. Shemesh and R. M. Latanision, Eng. Failure Anal., 2002, 9, 31–43 CrossRef CAS.
- N. S. Bornstein, M. A. De Crescente and H. A. Roth, Metall. Trans., 1973, 4, 1799–1810 CrossRef CAS.
- G. Y. Lai, High Temperature Corrosion and Materials Applications, ASM International, 2007, pp. 249–258 Search PubMed.
- R. A. Rapp, Corrosion, 1986, 42, 568–577 CrossRef CAS.
- J. R. Nicholls, JOM, 2000, 52, 28–35 CrossRef CAS.
- M. H. Li, X. F. Sun, J. G. Li and Z. Y. Zhang, et al., Oxid. Met., 2003, 59, 591–605 CrossRef CAS.
- M. Saremi and M. Bahraini, Trans. Inst. Met. Finish., 2003, 81, 24–27 CAS.
- M. Bahamirian and S. Khameneh Asi, Iran. J. Mater. Sci. Eng., 2013, 10, 12–21 CAS.
- X. Yang, X. Peng and F. Wang, Scr. Mater., 2007, 56, 891–894 CrossRef CAS.
- X. Yang, X. Peng, C. Xu and F. Wang, J. Electrochem. Soc., 2009, 156, 167–175 CrossRef.
- B. Bakhit and A. Akbari, J. Coat. Technol. Res., 2013, 10, 285 CrossRef CAS.
- U. Tack, Ph.D. thesis, Freiberg University of Technology, 2004.
- M. Srivastava, Siju, J. N. Balaraju and B. Ravisankar, J. Mater. Eng. Perform., 2015, 24, 1937–1944 CrossRef CAS.
- M. Srivastava, A. Srinivasan and V. K. W. Grips, Am. J. Mater. Sci., 2011, 1, 113–122 CrossRef.
- C. A. Stearns, F. J. Kohl and G. C. Fryburg, NASA Technical Report 1977, NASA-TRW VIA, B-1900, 713 C, and IN-738.
- M. Qiao and C. Zhou, Corros. Sci., 2012, 63, 239–245 CrossRef CAS.
- H. Lan, Z. G. Yang, Z. X. Xia, Y. D. Zhang and C. Zhang, Corros. Sci., 2011, 53, 1476–1483 CrossRef CAS.
- F. Pettit, Oxid. Met., 2011, 76, 1–21 CrossRef CAS.
- I. Hotovy, J. Huran and L. Spiess, et al., Sens. Actuators, B, 1999, 57, 147–152 CrossRef CAS.
- G. Faraci, S. La Rosa, A. R. Pennisi, Y. Hwu and G. Margaritondo, Phys. Rev. B: Condens. Matter Mater. Phys., 1993, 47, 4052–4055 CrossRef CAS.
- S. Popinciuc, H. T. Jonkman and B. J. V. Wees, J. Appl. Phys., 2007, 101, 93701–93705 CrossRef.
- T. J. S. Anand and A. H. W. Ngan, J. Mech. Eng. Tech., 2010, 2, 25–39 Search PubMed.
- C. Anandan, V. K. W. Grips, K. S. Rajam, V. Jayaram and P. Bera, Appl. Surf. Sci., 2002, 191, 254–260 CrossRef CAS.
- C. D. Wagner, W. M. Riggs, L. E. Davis and J. F. Moulder, Handbook of X-ray Photoelectron Spectroscopy, Perkin-Elmer Corporation, 1979 Search PubMed.
- T. Choudhury, S. O. Saied, J. L. Sullivan and A. M. Abbot, J. Phys. D: Appl. Phys., 1989, 22, 1185–1195 CrossRef CAS.
|
This journal is © The Royal Society of Chemistry 2016 |
Click here to see how this site uses Cookies. View our privacy policy here.