DOI:
10.1039/C6RA19877E
(Review Article)
RSC Adv., 2016,
6, 95449-95468
Tin-based nanomaterials for electrochemical energy storage
Received
6th August 2016
, Accepted 15th September 2016
First published on 16th September 2016
Abstract
Electrochemical energy storage has received a lot of attention due to the common recognition of sustainable development. Nanomaterials are ideal candidates as electrode materials in different fields of energy storage devices, offering favorable transport features, high surface to volume ratio and excellent physicochemical properties. This review is focused on the recent progress in nanostructured Sn-based electrode materials, including Sn, Sn alloys, Sn oxides (SnOx, x = 1, 2), dichalcogenides (SnSx, x = 1, 2) and oxysalts for lithium/sodium-ion batteries and supercapacitors. Sn-based compounds, including SnO, SnO2, MSnxOy (M = Co, Ca, Zn, Mo; x = 1, y = 3), SnS, SnS2, Sn3P4, SnC2O4, SnP2O7, etc., and their composites, possess various valence states and exhibit rich chemistry. They are very attractive candidates for efficient electrochemical energy storage systems because of their unique physicochemical properties, such as conductivity, mechanical and thermal stability, and cyclability. In this review, we aim to provide a systematic summary of the synthesis, modification, and electrochemical performance of nanostructured Sn-based compounds, as well as their energy storage applications in lithium/sodium-ion batteries (LIB/SIB), and supercapacitors. The relationship between nanoarchitectures and electrochemical performances, as well as the related charge-storage mechanism is discussed. Moreover, remarks on the challenges and perspectives of Sn-containing compounds for further development in electrochemical energy storage applications are proposed. This review sheds light on the sustainable development of advanced rechargeable batteries and supercapacitors, with a focus on Sn-based nanomaterials.
 Mingming Zhao | Mingming Zhao is a student at Yangzhou University, under supervision by Professor Huan Pang. She focuses on nanomaterials for energy storage, like supercapacitors. |
 Qunxing Zhao | Qunxing Zhao is currently a graduate student under supervision by Professor Huan Pang at Yangzhou University, and Professor Wen-Yong Lai at the Institute of Advanced Materials (IAM), Nanjing University of Posts and Telecommunications. His current research focuses on one dimensional silver nanomaterials and their composite and flexible thin film electrodes for energy-storage devices, like supercapacitors. |
 Jiaqing Qiu | Jiaqing Qiu is a student at Yangzhou University under supervision by Professor Huan Pang. She focuses on nanomaterials for energy storage, like supercapacitors. |
 Huaiguo Xue | Huaiguo Xue received his Ph.D. degree in polymer chemistry from Zhejiang University in 2002. He is currently a professor of physical chemistry and the dean of the College of Chemistry and Chemical Engineering at Yangzhou University. His research interests focus on electrochemistry, functional polymers and biosensors. |
 Huan Pang | Huan Pang received his Ph.D. degree from Nanjing University in 2011. He then founded his research group in Anyang Normal University, where he was appointed as a distinguished professor in 2013. He has now joined Yangzhou University as a university distinguished professor. He has published more than 90 papers in peer-reviewed journals, including Chemical Society Reviews, Advanced Materials, Energy Environ. Sci., with 3500 citations (H-index = 31). His research interests include the development of inorganic nanostructures and their applications in flexible electronics, with a focus on energy devices. |
1. Introduction
Nowadays, the increasing environmental problems, such as global warming and pollution, provide great impetus for the reduction of the society's dependence on fossil fuels; it is preferable to produce energy from renewable and sustainable resources. The utilization of electricity generated from intermittent renewable sources requires efficient energy storage systems (ESSs). Among clean energy technologies, electrochemical ESSs are considered the most feasible, environmentally friendly, and sustainable. Electrochemical ESSs such as rechargeable batteries (LIB/SIB) and supercapacitors have been widely used in portable electronics, electric vehicles, and smart electrical grids.
Nanomaterials, with attractive chemical and physical properties, are being explored for their potential in energy storage applications. The design and creation of new materials and substances that are chemically modified from the molecular and atomic level, to sizes on the nanoscale, would offer significantly enhanced functions for energy storage applications. During the past decades, much effort has been particularly devoted to fabricating a great number of nanostructured materials as electrodes in a range of LIBs, SIBs and supercapacitors. This research trend has been evidenced by many important pioneering studies published during the past decades. As expected, a notable improvement in performance has been achieved through recent advances in the development of advanced nanostructured materials and understanding of charge storage mechanisms. In batteries and supercapacitors, the nanostructuring of electrode materials may reduce diffusion/transport lengths for both ions and electrons, increase active sites, and relieve the volume expansion/contraction, thus leading to improved capacity, and higher power/energy density, and a longer cycle life. In some cases, new thermodynamics and/or kinetics allow enhanced phase transitions and rate capabilities during Li+ intercalation–deintercalation. It is believed that new developments in the field of nanomaterial chemistry hold the key to further breakthroughs in ESSs.155,254
Recent progress has demonstrated that Sn-based nanomaterials are very promising candidates for ESSs because of their unique physical and chemical properties, such as conductivity, mechanical and thermal stability. Sn is also inexpensive (roughly 20 dollars per kilogram), relatively safe to work with as a powder (not extremely pyrophoric), nontoxic, and highly abundant. The use of Sn@C, SnO2@C nanocomposites has been primarily investigated as an effective strategy. The carbonaceous materials are used not only as effective buffer zones to minimize the volume changes, but also as conductive phases to alleviate the low electrical conductivity and poor electrochemical stabilities of pure Sn based materials, resulting in enhanced cycle stability and rate capability. In this review, we present a summary on the synthesis, modification, and electrochemical performance of Sn-based nanomaterials. Also, their energy storage applications in the fields of LIBs, SIBs and supercapacitors are emphasized. The relationship between nanoarchitectures and electrochemical performances, as well as related charge-storage mechanisms is discussed. This review ends with an outlook on Sn-containing compounds for further progress in electrochemical energy storage applications.
2. Li-ion batteries
2.1 Sn
2.1.1 Pure Sn. New anode materials with higher theoretical capacities have been exploited, such as Sn-based materials (∼992 mA h g−1), Si-based materials (∼4200 mA h g−1), Co3O4 (890 mA h g−1), and Fe3O4 (928 mA h g−1). Among them, metallic tin (Sn) receives considerable attention for its advantageous properties, such as high theoretical capacity, high tap density, and safe thermodynamic potential. Sn is a promising option for high-capacity anode materials upon undergoing the Li-alloying/de-alloying reaction, due to its high theoretical gravimetric and volumetric capacities, according to the Li4.4Sn stoichiometry in the fully lithiated state.1 To date, various Sn nanostructures, such as nanoparticles, nanowires and nanosheets have been developed.2–4 Nevertheless, the practical application of Sn anode materials in Li-ion batteries (LIBs) is still restricted because of the low intrinsic electrical conductivity of Sn and the huge volumetric expansion and aggregation of Sn nanoparticles (NPs) during lithium alloying and dealloying processes, which lead to severe degradation of the electrodes upon cycling and dramatically shorten the cycle life of the Sn electrode. Besides, the mechanical stress induced by the severe volume variation (>300%) that occurs upon full lithiation and de-lithiation of Sn ultimately leads to a loss of Sn as a malleable, ductile, and highly crystalline metal.5,6 Generally, lithiation and de-lithiation occur reversibly, according to the following eqn (1): |
xLi + xe− + ySn ↔ LixSn
| (1) |
2.1.2 Sn@C. Sn undergoes large volume changes upon lithium alloying and de-alloying.7 This well-known phenomenon leads to pulverization of the active material and loss of contact with the current collector, eventually resulting in rapid capacity fading upon cycling. In order to address this challenge, there are several approaches involving the generation of not only porous nanostructures of Sn, but also Sn@C, such as Sn@CNFs, Sn@graphene, Sn@C/graphene, Sn/CNTs/graphene.8–15Among the various structures of Sn/C nanocomposites, the most attention is paid to one dimensional (1D) core–shell nanomaterials consisting of Sn nanomaterials as core and carbon layers as shell.16–19 The roles of carbon in the unique core–shell structure have been proposed as follows: (1) limiting the volume expansion and stabilizing the structure; (2) increasing the electrical conductivity; (3) protecting the nanomaterials from damage in various working environments. These core–shell nanomaterials can be produced via in situ methods. Li et al. reported the in situ synthesis of Sn nanowires encapsulated in amorphous carbon nanotubes. Deng and Lee also presented the fabrication of rambutan-like tin–carbon nanocomposites, via an ex situ method. The optimized thickness of carbon layers can help to approach the better performance of the anodes. Therefore, combining Sn that has a high capacity, with carbon having a good cycling behavior, can yield synergetic results. Another effective way to enhance the performance is by decorating Sn nanoparticles in the 2D or 3D nanomaterials using various methods, such as electroless plating, ball milling, fluidized-bed chemical vapor deposition (CVD), spray pyrolysis, solid-state reaction, and microwave-plasma CVD (MPCVD). These composite nanostructures suppress the volume expansion of the Sn nanoparticles during the charge/discharge cycles with the unique property of the 2D network of favoring both the electronic and ionic charge transport during the cell operation. The composite anode has shown outstanding electrochemical performance in terms of reversible capacity (and of a relatively low irreversible capacity), rate capability and cycle life, which have been evaluated in very demanding charge/discharge conditions.20–27
2.1.3 Sn@others. Sn can composite with other materials, including titanium dioxide and conducting polymers, not only to prevent the aggregation of Sn but to also serve as a buffer scaffold.28–36 TiO2 has a small volume expansion ratio (3%) upon intercalation/extraction of Li-ions, exhibiting good cyclic stability.28,245,248 Li et al. scrupulously designed a robust, porous 1D TiO2−x–carbon (TiO2−x–C) substrate to encapsulate Sn nanoparticles, as shown in Fig. 1a, in which the firm TiO2−x–C substrate can fully absorb the volume expansion of the Sn nanoparticles in the TiO2−x–C substrate during the charging–discharging processes, as shown in Fig. 1a. The porous TiO2−x–C–Sn nanofibers exhibit a high capacity of 957 mA h g−1 after 200 cycles at 0.1 A g−1 and can cycle over 10
000 times at 3 A g−1 while retaining 82.3% of their capacity, which represents the longest cycling life of Sn-based anodes for LIBs so far.29
 |
| Fig. 1 (a) Schematic illustration of the formation of highly stable porous TiO2−x–C–Sn composite nanofibers and insertion of Sn nanoparticles. (b) SEM images of 3D Sn/PPy composite network. (c) TEM images of Sn nanoparticles highly dispersed and embedded in PPy nanosheets. (d) Electrochemical cycling performance and (e) coulombic efficiency of the 3D Sn/PPy electrode, Sn@PPy/PVDF electrode, and Sn/PVDF electrode at a charge–discharge current of 200 mA g−1. Reproduced with permission ref. 29. Copyright 2014 American Chemical Society (a). Reproduced with permission ref. 37. Copyright 2014 Springer (b–e). | |
In order to optimize the electrode system of lithium-ion batteries for problems such as lithium ion diffusion, electron transportation, and large volume changes during cycling processes, judicious combinations of conducting polymers, such as polyaniline,154 polypyrrole (PPy), with selected metals with tailored structures as anode materials are fascinating, due to their underlying synergistic effects and simple fabrication procedures.30–34 Fan et al. designed and synthesized a novel anode material composed of ultrafine Sn nanoparticles (5 nm) anchored inside a well-connected three-dimensional (3D) PPy nanosheet network through a simple microemulsion-based preparation of tin nanoparticles with organic crystal surface-induced PPy polymerization, as shown in Fig. 1b–e. The PPy network acts as both binder and conductive matrix for the dispersion of Sn nanoparticles. It is capable of forming a conformal coating that tightly binds Sn nanoparticles with the current collector, and can serve as a geometrical coating to insure the structural and interfacial stability of tin nanoparticles during cycling. Furthermore, the distinct 3D ultrathin PPy nanosheet network with large surface area can provide a stable support for the high dispersion of Sn nanoparticles, as well as the highway for electron/Li+ transport. Using the designed 3D Sn/PPy electrode, outstanding electrochemical performance has been achieved, such as stable reversible capacity, high coulomb efficiency, and superior rate capacities upon increased currents, as shown in Fig. 1b–e.35–37
2.2 Sn–M (M = Co, Ni, Cd, Zn, Fe)
Sn-alloys possess high theoretical capacities and fast charge/discharge rates, making them very promising, high specific energy anode materials for LIBs. Advanced alloy anodes have been developed with a long cycle life of over 300 cycles and a reversible capacity of 500–700 mA h g−1. The capacity fade rates of these alloy materials are as low as 0.07% per cycle. Simultaneously, the first-cycle irreversible capacity loss of alloy anodes can be reduced to 50–100 mA h g−1, corresponding to a high initial coulombic efficiency of ∼90%. The cause of first cycle capacity loss has been attributed to (a) a loss of active material, (b) SEI formation, (c) Li trapping in the host alloy, (d) reaction with oxide impurities and (e) the aggregation of active particles. The approaches used for improving the cycling performance of alloy anodes include (a) multiphase composites, (b) porous anode structures, (c) reducing active particle size, (d) intermetallic phases, (e) thin-film and amorphous alloys, (f) hollow nanoparticles.38–48 Qin synthesized a 3D hybrid Sn–Ni@PEO nanotube array as a high performance anode for a lithium-ion battery, through a simple one-step electrodeposition method, for the first time. As shown in Fig. 2a, the electrode morphology is well preserved after repeated Li+ insertion and extraction, indicating that the positive synergistic effect of the alloy nanotube array and 3D ultrathin PEO coating could authentically optimize the current volume-expansion electrode system. As shown in Fig. 2c, the electrochemistry results confirm that the superiority of the Sn–Ni@PEO nanotube array electrode could largely boost durable high reversible capacities and superior rate performances, compared to the Sn–Ni nanowire array.49,50 Hou embedded Sn@Ni3Sn4 into nanocable-like carbon hybrids through a novel gas-phase route. The introduced Ni3Sn4 layer not only suppresses the tin-induced volume expansion, but also provides more voids and vacancies in the interior of the nanocables. The hybrids exhibit a long cycle life (360 mA h g−1 at 1 A g−1 after 1500 cycles).51–54 Leibowitz synthesized FeSn2–TiC nanocomposite alloy anodes by a mechanochemical process. The FeSn2–TiC alloy shows an initial gravimetric capacity of 511 mA h g−1 (1073 mA h cm−3) with a first-cycle coulombic efficiency of 77%, as shown in Fig. 2b. The TiC buffer matrix in the nanocomposite anode accommodates the large volume change occurring during the charge–discharge process and leads to good cyclability, compared to similar Sn-based anodes.55–58
 |
| Fig. 2 (a) Schematic illustration of the formation of the Sn–Ni@PEO nanotube array. (b) HRTEM images of the as-synthesized FeSn2–TiC electrode powder, showing a lower magnification image of a ∼100 nm agglomerate, with the inset showing the diffraction pattern. (c) Cycle performance of the Sn–Ni@PEO nanotube array and Sn–Ni nanowire array in the electrode potential range of 0.01–2.0 V (vs. Li/Li+) at 0.2 A g−1. Reproduced with permission ref. 50. Copyright 2014 Royal Society of Chemistry (a and c). Reproduced with permission ref. 55. Copyright 2015 Elsevier (b). | |
2.3 SnO2
2.3.1 Pure SnO2. Nanostructured SnO2 with a high theoretical gravimetric lithium storage capacity of 782 mA h g−1 and low potential of Li-ion intercalation has been considered as an attractive replacement for the graphite anodes. However, the SnO2 anode electrode suffers severe mechanical disintegration, due to the drastic volumetric changes during lithium ion insertion and extraction, and therefore leads to the rapid deterioration in capacity. Large improvement attempts have been focused on controlling the volumetric change by using nano-sized SnO2 particles with various morphologies, such as hollow nanospheres, nanowires, nanocolloids, mesoporous structures and nanobelts. These materials have been proven to exhibit better electrochemical performance, suggesting that structure modification could be an effective solution to enhance the electrochemical performance.59–70
2.3.2 MSnO3 (M = Co, Ca, Cd, Na, Zn). MSnO3 are synthesized with different structures, such as nanoboxes, yolk–shell hollow microcubes and nanotubes.71–77 Lou developed a new type of hybrid nanostructure, a carbon coated hollow nanostructure of amorphous complex metal oxides, for highly reversible lithium storage, as shown in Fig. 3a and b. This unique structure well integrates three main design principles and is anticipated to manifest excellent lithium storage performance because of the superior structural advantages, as shown in Fig. 3c and d.71,72 Amorphous ZnSnO3 double-shell and yolk–shell hollow microcubes were synthesized by the calcination of their corresponding ZnSn(OH)6 precursors, pre-prepared through a facile chemical solution method in argon. The as-prepared amorphous ZnSnO3 double-shell hollow microcubes have an average edge length of 1.6 μm.73–77
 |
| Fig. 3 (a) FESEM images of CoSnO3@C nanoboxes; (b) a uniform carbon coating layer on the surface of CoSnO3 nanoboxes; (c) comparative cycling performance of CoSnO3 nanoboxes with and without carbon coating, CoSnO3 nanocubes, crystalline Co–Sn–O nanoboxes and commercial SnO2 particles; (d) rate capability of CoSnO3 nanoboxes, with and without carbon coating, obtained between 0.01 and 1.5 V at various current densities. Reproduced with permission ref. 71. Copyright 2013 Royal Society of Chemistry (a–d). | |
2.3.3 M-doped SnO2 (M = Mo, Fe, Cu). Dopants favor the reversible formation of lithium oxide, thus, enabling the beneficial combination of lithium storage by alloying and conversion. This value is slightly higher than that obtainable by the alloying process of Sn present in the material. Compared to SnO2, Mo-doped SnO2 showed a lower first cycle reversible capacity, but improved capacity retention when cycled in a rather narrow voltage range (0.0–1.0 V), which was assigned to decreased crystallite growth upon synthesis and a favored dispersion of the electrochemically active metallic Sn, formed upon the first lithiation.83 Doping SnO2 with Fe leads to a significantly enhanced specific capacity, cycling stability, and coulombic efficiency. After ten cycles, SFO-C exhibits a reversible specific capacity of 1519 mA h g−1, which is about twice that of pure SnO2.84
2.3.4 SnO2@M (Ni, Mo, Fe). The SnO2/metal composites exhibit a high reversible capacity, stable cycling performance and superior rate capability, benefiting from high electron transport and fast ion diffusion. Jiang developed a porous Ni/SnO2 composite electrode composed of homogeneously distributed SnO2 and Ni nanoparticles; the reaction kinetics of SnO2 is greatly enhanced, leading to a full conversion reaction, superior cycling stability and improved rate capability. The uniformly distributed Ni nanoparticles provide a fast charge transport pathway for electrochemical reactions, and restrict the direct contact and aggregation of SnO2 nanoparticles during cycling. In the meantime, the void space among the nanoclusters increases the contact area between the electrolyte and active materials, and accommodates the huge volume change during cycling as well. The Ni/SnO2 composite electrode possesses a high reversible capacity of 820.5 mA h g−1 at 1 A g−1 up to 100 cycles.84,85 Tin titanate nanowires, coupled with SnO2 nanoparticles have been prepared by combining the hydrolysis of the Sn(II) precursor with tin-to-hydrogen ion exchange using layered hydrogen titanate nanowires as conformal templates under hydrothermal conditions. This synthetic strategy allows for the incorporation of electrochemically active Sn into the layered titanate and simultaneous deposition of SnO2 nanoparticles on the as-prepared tin titanate nanowires. The tin titanate nanowires coupled with SnO2 nanoparticles showed improved cycle performance and increased lithium storage capacity, as compared to mesoporous SnO2 nanoparticle aggregates and hydrogen titanate nanowires. The SnO2 nanoparticles supported on tin titanate can buffer the large volume changes during the Li–Sn alloying and dealloying process in flexible layered titanate nanostructures with large interlayer distances.86
2.3.5 SnO2@MxOy (Fe, Ni, Mn). Hybridizing tin oxide with transition metal oxide can effectively activate the irreversible capacity because the transition metal nanoparticles in the composites can reversibly convert extra Li2O to Li+.87,88 Yu et al. prepared SnO2–CuO–Li2O film with multideck-cage porous morphology, which showed a high reversible capacity (1158.5 mA h g−1) and only an initial capacity loss of 17.6% at 0.5C. Du et al. demonstrated that Fe2O3 (ref. 255 and 256) @SnO2@C porous core–shell nanorods showed high initial coulombic efficiency (73%), high reversible capacity (995.4 mA h g−1 at 0.2 A g−1), and good cycling performance.89 Yuan designed and synthesized a quaternary hierarchical nanocomposite (rGO-Fe3O4–SnO2–C); Fe3O4 and SnO2 nanoparticles were uniformly dispersed on the rGO nanosheets and fully encapsulated by the outmost carbon layers, forming a sandwich-like buffering structure for excellent dimensional integrity. It exhibited a reversible capacity of 868.6 mA h g−1 after 100 cycles at a current density of 200 mA g−1.90 For CoO-in-CoSnO3, Co2(OH)2CO3 nanowires were first obtained by a hydrothermal method and then deposited with ALD SnO2. The CoO wire-void-CoSnO3 tube was formed with the decomposition of Co2(OH)2CO3 and its simultaneous reaction with the outer SnO2 layer. In this unique wire-in-tube structure, both CoO and CoSnO3 are promising materials for lithium ion battery anodes with high theoretical capacities, and the porous and hollow feature is essential for better electrode/electrolyte contact, shorter ion diffusion path and better structure stability. Enhanced rate capability and cycling stability have been demonstrated with the structure, showing its promising application for the anode material of lithium ion battery.78–82
2.3.6 SnO2@non-metal. A variety of nanostructured tin oxides/carbon composites with peculiar morphologies, such as yolk–shell, nanochains, nanorods/GS and NSs/graphene structures have been synthesized.73,74,78–81 They all exhibited better lithium storage and cycling performance as anode materials for LIBs, which can be attributed to the fully synergistic effects of nanostructured tin oxides and the highly flexible and good conductive carbon. The carbon component of tin oxides/carbon composites can partly accommodate the volume change of tin oxides, prevent tin oxides from aggregation and pulverization, prevent continual formation of the SEI film, ensure the electrode integrity during prolonged cycling processes, enhance the electronic conductivity of the overall electrode and further facilitate electron and ion transport throughout the electrode.93–100 For example, Zhang et al. reported that chemically anchored SnO2 nanoparticles on both sides of rGO, retained a specific capacity of 558 mA h g−1 after 50 cycles at a current density of 264 mA g−1, indicating a capacity loss of 0.6% per C–D cycle.101–103 The SnO2/CNTs hybrid has been prepared by several groups with different kinds of methods.104–107 Fairly scattered tin dioxide nanocrystals serve as highly active sites for lithiation and delithiation, while the CNTs provide a flexible support for loading tin dioxide nanocrystals and highways for lithium ion and electron transport. These composites exhibit similarly decreasing cycling performance, with no more than 200 cycles. Although Lee et al., Zhang et al., and Kim et al. accomplished stable cycling by complex electrode design, those so-called elaborate nanostructures still exhibit deficiencies in achieving recoverable initial reversible capacity, suffering from large rates.99,108–110 Conducting polymers have been introduced to improve the anode performance in LIBs.111–113 In addition to improving electron conductivity, the soft polymer matrix can also relax the internal stress of solid particle anodes that suffer from severe volume change during charge–discharge cycles.114–116 SnO2 particles covered by PPy demonstrated improved cycling performance, compared to the standalone SnO2 nanoparticles.116–118 The SnO2-PPy hybrid nanowires were synthesized in a one-step process by a simple electrochemical method. Over 200 cycles, the hybrid nanowires showed superior cyclic performance and a charge capacity higher than 0.307 mA h cm−2, because the polypyrrole matrix effectively prevented agglomeration of the SnO2 nanoparticles and acted as an elastic buffer to mitigate volumetric changes in the nanoparticles.117,118To improve the cycling characteristics of the pure SnOx (such as SnO2) thin film anodes, an efficient method was carried out by adding P2O5 to increase the number of spectator atoms to constitute the matrix. The high specific capacity of 136 mA h cm−2 was maintained after 300 cycles, and they showed cycle stability for 300 cycles with a very high current. In the case of Sn2P2O7, the amorphous solid had better performance than the crystalloids. It showed lower initial irreversible discharge capacity and higher reversible capacity.91,92 Zhang synthesized core–shell nanostructured composite material consisting of nano-Si as the core and SnO2 as the shell by a sol–gel method. The partial reversible reaction between Li and SnO2 during the first cycle was identified, and the reactivity of the Si core was investigated by ex situ analyses. The nano-Si/SnO2 core–shell nanostructured electrode showed a reversible capacity of 1000 mA h g−1 and good cycle retention, close to 80% of the first charge capacity over 50 cycles.119,120
2.4 SnS2
2.4.1 Pure SnS2. SnS2 is a promising material, due to a high surface area (which can increase ion uptake and lead to higher capacities) and a crystal structure conducive to repeated Li-ion insertion and de-insertion, without a significant loss of capacity. In the crystal structure, octahedral coordinated Sn atoms are sandwiched between two layers of sulfur atoms, hexagonally close packed through strong Sn–S covalent bonds to form triple layers. The adjacent triple layers of SnS2 are attached via weak van der Waals interactions. During charge/discharge, Li-ions can easily undergo insertion/deinsertion between these layers, which are stacked together through the van der Waals gap. Thus, the layered material can minimize the volume change during the charge/discharge process and facilitate the transport of lithium ions. The electrochemical reactions of SnS2 with lithium are expressed in the following two step reactions (2) and (3). |
SnS2 + 4Li+ + 4e− → Sn + 2Li2S
| (2) |
|
Sn + xLi+ + xe− ↔ LixSn (0 ≦ x ≦ 4.4)
| (3) |
During the initial discharge process, SnS2 reacts with Li+ ions and converts to active Sn and Li2S, and metallic Sn is embedded within the inert matrix of Li2S. In the subsequent step, metallic Sn further reacts with Li+ ions to form the Li4.4Sn alloy, which can be reversibly converted into Sn and Li+ during charging (dealloying). It is the second step that involves a large volume expansion of about 300%. At the same time, it is stipulated that Li2S serves as the buffering domain during Li–Sn alloying/dealloying, thereby reducing the volume variation and capacity fading by maintaining electrode integrity. It provides an ion-conducting medium for Li-ion migration and prevents the aggregation of the nanosized Sn metal particles formed in the first step. However, during repetitive cycling, the buffering effect of Li2S becomes inefficient, due to the enormous volume variation, and therefore the Sn particle aggregation is no longer contained and this manifests in fast capacity fading. Different strategies have been employed to minimize this volume variation. One strategy involves controlling the morphology of the compound by forming porous structures; so far, various nanostructured morphologies, such as nanorods, nanobelts, nanosheets and 3D nanoflowers have been reported.121–139 The main advantages of porous nanostructured materials are large surface area and large pore sizes, which can easily accommodate the volume expansion. Further, short diffusion path lengths and large contact areas between the electrode and the electrolyte can increase the rate capability of the active material.
Among the various nanostructured morphologies, the 3D hierarchical structures formed by self-assembly offer a large surface area and high porosity and are ideal for minimizing the pulverization of the electrode. Jana et al. reported an ionothermal synthesis method, where hierarchical flower-like assemblies composed of 2D nanosheets of SnS2 were obtained;140,142 the nanostructure showed an average discharge capacity of 458 mA h g−1 after 50 cycles. Wu et al. prepared layer-stacked hexagonal tin disulfide (SnS2) nanorods by using tetragonal tin (Sn) nanorods as sacrificial templates and silica (SiO2) as nano-reactors.141 The SnS2–SiO2 nanorod electrode retained a capacity of 536 mA h g−1 after 25 cycles in the potential range of 0.01–1.15 V at a current density of 200 mA g−1. Zhai et al. prepared ultrathin hexagonal SnS2 nanosheets by a hydrothermal method using tin(IV) chloride and thioacetamide.143 The SnS2 nanosheets exhibited a high discharge capacity of 513 mA h g−1 after 50 cycles at a current density of 100 mA g−1. A solvothermal synthesis of 1D layered SnS2 ultralong nanobelts was carried out by Wang et al., using SnCl4, CS2 and ammonia reagents; the nanobelts showed a capacity of 560 mA h g−1 at a 0.1C rate between 0.01 to 2 V.144 Sun et al. prepared 2D SnS2 nanoplates and this material showed a very high capacity and even after 30 cycles, it retained a capacity of 583 mA h g−1 at a current density of 323 mA g−1 between 0.001 to 1.1 V.145 Jiao et al. synthesized a 3D flower-like SnS2 hierarchical architecture by a simple solvothermal method using SnCl4 and CS2 in ethanol.146 The electrode exhibited a specific capacity of 549.5 mA h g−1 at a current density of 100 mA g−1 after 100 cycles. The above-described literature survey on some notable research outcomes in SnS2 nanostructures and their application to LIBs, shows that a variety of methods, such as ionic liquid assisted, templating and thermal decomposition have been used in the past for preparing these nanostructures.
2.4.2 SnS2@C. These SnS2-based anodes suffer from rapid capacity decay caused by pulverization of the electrode materials, due to the large volume changes during extended discharge/charge processes. The same vacillations, which reduce cyclability in SnS2, plague other anode materials such as silicon and numerous metal oxides. Two effective strategies have been developed to solve this problem. The first strategy is to reduce the size of the electrode materials in order to relax the strain during the volume expansion and contraction. The other is to prepare them as composites using a carbon matrix, such as mesoporous carbon, N-doped microporous carbon nanospheres, graphene, and carbon nanotubes (CNTs).147,148,244 These matrices can buffer the volume variation and accelerate ion and electron transport during the discharge/charge processes. The combination of these two approaches could potentially offer a viable way to mitigate the volume changes and further improve the electrochemical performance of LIBs. Gao developed a kind of nanocomposite material made of layered SnS2 nanoplates vertically grown on reduced graphene oxide nanoribbons (rGONRs) as an anode in lithium ion batteries. At a rate of 0.4 A g−1, the material exhibits a high discharge capacity of 823 mA h g−1, even after 800 cycles. It shows a high capacity of 642 mA h g−1 at 0.2 A g−1, superior rate and cycling stability after long-term cycling. Moreover, the full cell has a high output working voltage of 3.4 V. These excellent lithium storage performances can be mainly attributed to the synergistic effect between the highly conductive network of rGONRs and the high lithium-ion storage capability of layered SnS2 nanoplates.149 Tang developed a three-dimensional (3D) interconnected graphene network embedded with uniformly distributed SnS2 nanoplates by a facile two-step method. The as-prepared SSG exhibits excellent cycling performance with a capacity of 1060 mA h g−1, retained after 200 charge/discharge cycles at a current density of 100 mA g−1, and also a superior rate capability of 670 mA h g−1, even at such a high current density of 2000 mA g−1. This favorable performance can be attributed to the unique 3D interconnected architecture with great electro-conductivity and its intimate contact with SnS2.150
2.5 Sn4P3, SnF2
Tin phosphide (Sn4P3) has a high theoretical capacity and forms Li3P with Li ion conductivity in the initial lithium insertion. Li3P acts as a matrix, suppressing the volume change and giving lithium ion conduction paths.151 Liu synthesized Sn4P3 nanoparticles with different sizes via a facile solvothermal method at 180 °C for 10 h. The as-prepared Sn4P3 nanoparticles have an average size of about 15 nm. Sn4P3 nanoparticles with the smallest size give the best cycling and rate performances. They deliver a discharge capacity of 612 mA h g−1 after 10 cycles and could still maintain 442 mA h g−1 after 320 cycles at the current density of 100 mA g−1 within a voltage limit of 0.01–3.0 V. Even after 200 cycles at a current density of 200 mA g−1, the specific capacity could still remain at 315 mA h g−1.152 Tin(II) fluoride (SnF2) has a high Li-storage capacity because it stores lithium first by a conversion reaction and then by a Li/Sn alloying/dealloying reaction. A polyacrylonitrile (PAN)-bound SnF2 electrode was heat-treated to enhance the integral electrical contact and the mechanical strength through its cross-linked framework. The heat-treated SnF2 electrode showed reversible capacities of 1047 mA h g−1 in the first cycle and 902 mA h g−1 after 100 cycles. Part of the excess capacity is due to lithium storage at the Sn/LiF interface, and the other part is assumed to correspond to the presence of reduced SnF2 with protons released during the thermal cross-linking of PAN.153
3. Na-ion batteries
3.1 Sn
3.1.1 Pure Sn. Tin can be used as an efficient negative electrode material for Na-ion batteries.156–163 Similar to Li, it was reported that Na can also alloy with a number of metals, such as Sn, Sb, Pb, and Ge, and that these alloys have relatively high theoretical capacities by forming Na-rich intermetallic compounds, such as Na15Sn4, Na3Sb, Na15Pb4, and Na3Ge, respectively. Among these metals, Sn is one of the most attractive anode materials because of its high theoretical capacity and low reaction potential.162–165 To understand and improve the electrochemical properties of the Sn anode for Na-ion batteries, the alloying/dealloying of Sn with Na has been investigated. Chevrier et al. investigated a voltage profile for the electrochemical reaction of Sn with Na, based on density functional theory (DFT) calculations of the Na–Sn binary phases with crystal structures. According to their calculations, the voltage curve has four plateaus corresponding to NaSn5, NaSn, Na9Sn4, and Na15Sn4, which is almost identical to the experimental results of Huggins, with the exception of the NaSn5 phase. On the basis of these studies, Ellis et al. examined the electrochemical insertion of Na into Sn using in situ X-ray diffraction at ambient temperatures. XRD analysis clearly confirmed the formation of four different Na–Sn alloy phases in two-phase regions. Nevertheless, only the Na15Sn4 phase formed at full sodiation was identically matched with the reference data, and the three other intermediate Na–Sn phases did not correspond to any of the reported Na–Sn phases. Baggetto et al. investigated the Na-ion reaction mechanism of Sn using various analyses and reported a new metastable phase of Na5Sn2 in the Na–Sn system, which remained an unknown phase in the work of Ellis et al. In addition, they suggested that at least two more plateaus are present during charging above 0.7 V, which had not been reported in previous studies. According to their mechanism, the insertion of Na into Sn progressed via a series of four steps: an unidentified phase (Na0.6Sn), an amorphous phase (Na1.2Sn), a hexagonal R
m phase (Na5Sn2), and a fully sodiated I
3d phase (Na15Sn4). This mechanism was confirmed by the theoretical voltages calculated from existing crystal structures using DFT calculations and constant current and quasiequilibrium measurements (GITT). However, Wang et al. proposed a different mechanism for the reaction of Sn with Na based on in situ transmission electron microscopy (TEM) studies. In their mechanism, the sodiation of Sn nanoparticles proceeded via a two-step reaction: the first step is the phase transition of Sn to amorphous NaSn2, and amorphous Na9Sn4, Na3Sn and crystalline Na15Sn4 are formed sequentially in the second step. They suggested that the first step is a two-phase reaction with a migrating phase boundary to form an amorphous NaxSn alloy (x = 0.5) and that the second step is a single-phase reaction without the formation of a phase boundary. These single-phase sodiation reactions are not consistent with the two-phase mechanism proposed by other groups. Because the phase behaviors are significantly affected by kinetic factors, such as the experimental configuration and sample conditions, the Sn nanoparticles may take a different reaction pathway compared with the Sn electrode prepared by magnetron sputtering. Nam et al. found that two Sn electrodes having completely different morphologies and crystallographic orientations prepared by electrodeposition, and their electrochemical properties for Na-ion battery applications were examined, with an emphasis on the effects of the morphology and the phase structure of Sn on the cyclability of the electrodes. Finally, the feasibility of the pure Sn electrode, which is prepared by a binder- and conductive agent-free process, would be verified.170Hou et al. reported Sn hollow nanospheres, which maintained much better reversible capacity than solid Sn nanospheres, indicating a close connection between this alloy anode nanostructure and its electrochemical properties. However, similar works with reported precise structural control in NIBs are still in rapid expansion when further exploring the performance of Sn anodes.166–170 Liu et al. developed Sn nanoparticle-coated, viral nanoforests to achieve long cycling stability with high performance in a Na-ion battery.166 However, the use of vapor deposition (CVD and PVD) and electrodeposition techniques during the preparation may also increase the processing cost of the Na-ion battery, hindering its development in industrial applications.166,167,169,171,172 Nam demonstrated a novel electrochemical approach to synthesize single-crystalline 1D Sn nanofibers using an organic compound as a growth modifier. This process is low-cost, one-step, extremely fast and performed at room temperature using a nontoxic bath preparation. Specifically, no additional processes are needed for preparing and removing the templates. Moreover, this process is suitable for mass production on large-area substrates because of the high uniformity of the nanofibers over the entire substrate.173
3.1.2 Sn@C. Sodium can reversibly alloy with tin at high theoretical capacities.174 However, these compounds still suffer from rapid capacity degradation as a result of large changes in volume and the resultant pulverization and loss of electrical connectivity. To address this issue, nanocomposites with different carbonaceous materials have been widely synthesized.175 Liu et al. reported the fabrication of Sn nanodots finely encapsulated in porous N-doped carbon (designated as PNC) nanofibers by an electrospinning technique and subsequent thermal treatment, as shown in Fig. 4a and b. The as-prepared Sn NDs@PNC nanofibers with flexible free-standing membranes can be directly used as binder- and current collector-free anodes, demonstrating promising electrochemical performance in Na-ion batteries.176 Xie et al. reported the preparation of core-sheath structured Sn@carbon nanotube (Sn@CNT) nanopillars, grown vertically on carbon paper (Sn@CNT-CP) through a novel and facile soaking-chemical vapour deposition (S-CVD) technique, as shown in Fig. 4c and d. The electrode achieved a reversible capacity of 887 mA h cm−2 in the first cycle and good cyclability extending to 100 cycles.177 As a high-capacity, high-rate, and long-cycle life anode for sodium ion batteries, ultra-small Sn nanoparticles (≈8 nm) homogeneously embedded in a spherical carbon network (denoted as 8-Sn@C) was prepared using an aerosol spray pyrolysis method, as shown in Fig. 4e and f. The remarkable electrochemical performance of 8-Sn@C is due to the synergetic effects between the well-dispersed ultra-small Sn nanoparticles and the conductive carbon network. This unique structure of very-fine Sn nanoparticles embedded in the porous carbon network can effectively suppress the volume fluctuation and particle aggregation of tin during the prolonged sodiation/desodiation process, thus solving the major problems of pulverization, loss of electrical contact and low utilization rate facing the Sn anode.178
 |
| Fig. 4 (a) SEM and (b) TEM of Sn NDs@PNC nanofibers. (c) Medium-magnification SEM images of Sn@CNT-CP. (d) TEM image of a single Sn@CNT nanopillar. (e and f) SEM and TEM images of 8-Sn@C. Reproduced with permission ref. 176. Copyright 2015 Wiley (a and b). Reproduced with permission ref. 177. Copyright 2015 Elsevier (c and d). Reproduced with permission ref. 178. Copyright 2015 Wiley (e and f). | |
3.1.3 Sn@others. Apart from the above materials, other well-functioning materials have been synthesized for this application, such as polymers, natural wood fiber, and Sn4+xP3@(Sn–P). A pure Sn nanoparticle electrode with conductive binder was prepared showing higher specific capacity and higher cycling stability without any carbon black, compared to Sn/CMC (carboxymethylated cellulose) and Sn/PVDF (polyvinylidene fluoride) electrodes. The Sn in the Sn/PFM electrode delivered 806 mA h g−1 at C/50 and 610 mA h g−1 at C/10. After 10 cycles at C/10, the capacity of Sn had no decay.179 Zhu et al. reported an electrodeposited Sn film on conductive wood fiber to achieve 339 mA h g−1 for a stable cycling performance of 400 cycles. The soft nature of the wood fibers effectively releases the mechanical stresses associated with the sodiation process, and the mesoporous structure functions as an electrolyte reservoir that allows for ion transport through the outer and inner surfaces of the fiber.180 Li et al. prepared a novel tin phosphide and amorphous Sn and P (Sn4+xP3@(Sn–P)) composite in large amounts by a simple low-energy ball-milling method that can meet the demand for large-scale applications. The as-obtained Sn4+xP3@(Sn–P) composite was investigated as the anode for SIBs in half-cells and showed high capacity and high rate capability.181
3.2 Sn–M (M = Sb, Co, Cu, Ge)
3.2.1 Sn–M. Amorphous bimetallic nanoalloys with good conductivity, strain tolerance, and large sites for the insertion of Na+ ions are desirable electrode materials for superior SIBs.182–186 The bare Sn electrode suffers from a severe pulverization issue, due to volumetric expansion and disintegration, leading to poor cycling performance. The benefits of amorphous bimetallic nanoalloys are that the uniform distribution of the electrically conducting M1 (e.g., Co) nanoparticles in close proximity to the high-capacity M2 (e.g., Sn) storage compound could contribute to electrical integration in the electrodes.186 Tin-based alloys are considered as necessary electrode materials for sodium ion batteries (Sn–Sb, Sn–Ni, Sn–Co, Sn–Cu, Sn–Ge, Sn–Ge–Sb). The mechanism of Sn alloys is not a simple combination of Sn and other transition metal reactions. To easily explain the process, we take the Sn and SnSb anode with Na as an example. The reversible reaction occurs during the majority of the charge process. A large proportion of Na exists at the charge anode material, showing that the crystalline Sb is lacking in the process of recrystallization. The reaction of SnSb yields Na3Sb at full discharge at higher temperatures, while the RT reaction yields amorphous compounds, indicating that the Na reaction with SnSb may not be simply written as SnSb + Na → Na3Sb + Sn.186 Liu et al. synthesized highly porous Ni3Sn2 microcages, composed of tiny nanoparticles, by a facile, template-free, solvothermal method for use as anode materials for high capacity and high-rate-capability Na-ion batteries. A reversible capacity of approximately 270 mA h g−1 was stably maintained at 1C during the first 300 cycles.185 Farbod et al. reported the electrochemical charge/discharge cycling behavior of Sn–Ge–Sb, Sn–Ge, and Sb–Ge alloy thin films for use as sodium ion battery anodes. Sn50Ge25Sb25 demonstrates the best overall cycling performance, with 662 mA h g−1 of capacity remaining after 50 cycles. The alloy also offers an exquisite rate capability, delivering a stable cycling capacity of 658 and 381 mA h g−1 at 850 and 8500 mA g−1, respectively.186
3.2.2 Sn–M@C. Sn alloys suffer from poor electrochemical properties, mainly attributed to the large volume change during cycling, the relatively low conductivity and aggregation of the alloy particles. To circumvent these obstacles and achieve improved electrochemical properties, a variety of nanostructures or carbon-based nanocomposites have been investigated. At present, carbon-based@Sn alloys nanocomposites are mainly carbon and graphene; Sn–Cu–C, SnSe/C, Cu6Sn5–TiC–C, SnSb–TiC–C, SnSb–CNF, and C/Sn/Ni/TMV have been widely synthesized.187–191 Kim et al. studied porous CNF-supported SnSb nanocomposites as anodes for rechargeable NIBs, using electrospinning and a subsequent thermal treatment processes to get good performance, high rate capability, high reversibility, and long-term stability.192 Ji synthesized rGO-SnSb nanocomposites where SnSb alloy particles can tightly combine with the surfaces of rGO sheets, which can not only effectively suppress the agglomeration of SnSb particles, but also maintain excellent electronic conduction, as shown in Fig. 5a and b. Furthermore, the mechanical flexibility of the rGO phase can accommodate the volume expansion and contraction of SnSb particles during the prolonged cycling and therefore improve the electrode integrity mechanically and electronically, as shown in Fig. 5c.193 Yang et al. prepared SnSe/rGO by a facile ball milling method, and its electrochemical performance was significantly enhanced, as reflected by a high specific capacity of 590 mA h g−1 at 0.050 A g−1, a rate capability of 260 mA h g−1 at 10 A g−1, and long-term stability over 120 cycles. This improvement may be attributed to the high electronic conductivity of rGO, which also serves as a matrix to buffer changes in volume and maintain the mechanical integrity of the electrode during (de)sodiation processes.194
 |
| Fig. 5 (a) Schematic illustration of the fabrication processes of rGO-SnSb nanocomposites for rechargeable Na-ion batteries, (b) TEM images of rGO-SnSb nanocomposites, (c) the cycling performance of rGO-SnSb electrodes in the voltage window of 0.001–2.5 V at a cycling rate of 0.2C. Reproduced with permission ref. 193. Copyright 2014 Wiley (a–c). | |
3.3 SnO2
3.3.1 Pure SnO2. SnO2 can exhibit a theoretical capacity of 667 mA h g−1 based on the reaction of 3.75 Na and one Sn (Na15Sn4), except for Na2O formation. Park et al. investigated the electrochemical properties of the SnO2 electrode for sodium-ion batteries, as shown in Fig. 6a. The Na/SnO2 cell delivered initial discharge and charge capacities of 747 and 150 mA h g−1, respectively. In-plane cracks caused the loss of electrical contact of the active material and hence, the capacities decreased gradually.195 Lu et al. reported SnO, and SnO2 prepared by hydrothermal reactions, as shown in Fig. 6b and c. Although SnO had larger particles, more uneven particle size, and particle distribution, it outperformed both SnO2 and SnO2/C. The material demonstrated high reversible capacity, low polarization, and low irreversible capacity loss. Shimizu et al. prepared the SnO thick-film electrodes using a gas-deposition method. The SnO electrode showed a high-rate performance with the capacity of 200 mA h g−1 at the high current density of 500 mA g−1.196
 |
| Fig. 6 (a) Schematic drawing of SnO2 electrochemical reactions during discharge. The lightning bolt represents in-plane crack propagation. (b) Medium magnification images of flower-like SnO2. (c) Discharge and charge voltage profiles of the Na/SnO2 cell cycled at a current density of 100 mA h g−1. Reproduced with permission ref. 195. Copyright 2014 Elsevier (a). Reproduced with permission ref. 196. Copyright 2015 Elsevier (b and c). | |
3.3.2 SnO2@C. SnO2 can deliver a high theoretical sodium storage capacity of 1378 mA h g−1, but with the same volume variation problem as Sn metal; hence, further surface treatment or a matrix scaffold is needed to stabilize the SnO2 anode and improve the electronic conductivity.197,198 Zhang et al. synthesized a nanohybrid anode consisting of ultrafine SnO2 anchored on few-layered rGO by a facile hydrothermal route, as shown in Fig. 7a and b. The hybrid can sustain a stable cycling with a charge capacity of 369 mA h g−1 retained after 100 cycles at 100 mA g−1. SnO2@graphene nanocomposites have improved cycling performance, but this method lacks the process ability and rate capability because of the high cost of graphene;199,200 therefore, many other carbon materials, such as multiwalled carbon nanotubes, carbon cloth, and porous carbon nanofiber have been applied. Wang et al. Reported a SnO2@multiwalled carbon nanotubes (MWCNTs) nanocomposite, synthesized by a solvothermal method, exhibiting a high reversible sodium storage capacity and a good cycling performance.201 Liu et al. demonstrated an anode consisting of a SnO2 nanocrystal layer grown on hierarchical microfibers of carbon cloth (CC) with extra surface coating, to addresses the above challenges associated with SnO2 anodes by the hydrothermal and ALD method, as shown in Fig. 7c and d. The soft nature of CC and the nanocrystal structure of SnO2 layers can effectively accommodate the volume change associated with the sodiation process.202 Dirican et al. introduced a new amorphous carbon-coated SnO2-electrodeposited porous carbon nanofiber (PCNF@SnO2@C) composite that not only has high sodium storage capability, but also maintains its structural integrity with ongoing repetitive cycles, as shown in Fig. 7e and f.203
 |
| Fig. 7 (a and b) SEM, TEM images of SnO2/rGO. (c and d) SEM and TEM images of SnO2/CC. (e and f) SEM images and TEM images of PCNF@SnO2@C composite. Reproduced with permission ref. 200. Copyright 2015 Elsevier (a and b). Reproduced with permission ref. 202. Copyright 2015 Elsevier (c and d). Reproduced with permission ref. 203. Copyright 2015 American Chemical Society (e and f). | |
3.4 SnS2
Considering the additional capacity contribution from the conversion reaction, tin sulfides possess higher theoretical capacities compared to metallic tin. Moreover, tin sulfide appears to be more promising, due to the large interlayer spacing in its layered structure, which facilitates the insertion and extraction of sodium ions. 2D SnS2 nanosheets (34 nm in thickness) with high specific capacity, good rate capability, and cycling stability were synthesized via a facile refluxing process. The SnS2 nanosheets delivered a high reversible specific capacity of 733 and 435 mA h g−1 at 0.1 and 2 A g−1, respectively, and still exhibited a high capacity retention of 647 mA h g−1 during the 50th cycle at 0.1 A g−1.204 Dutta et al. Synthesized tin monosulphide by a simple wet chemical synthesis approach. The as-prepared tin monosulphide has been used as the anode in Na-ion batteries without any in situ conductive carbon or graphene coating, and the electrode exhibits a high reversible sodium reversible capacity of ∼500 mA h g−1 at a discharge rate of 125 mA g−1.205–208 However, because of severe pulverization due to great volume expansion (420%) and poor kinetics caused by slow electron transport, SnS2 cracks and gradually loses contact with the current collector, resulting in poor cycle ability and low rate capability.209–211 A general approach to enhancing its electrochemical performance is to fabricate SnS2 based nano-composite architectures.212–216 Qu et al. came up with a novel SnS2-rGO nanocomposite, produced by a facile hydrothermal route from a mixture of tin(IV) chloride, thioacetamide (TAA) and GO, exhibiting high-capacity, high-rate, and long-cycle life, as shown in Fig. 8.217 Wang et al. developed a simple solid–state reaction method, in which the carbon-coated SnS2 (SnS2/C) anode materials were synthesized by annealing metallic Sn, sulfur powder, and polyacrylonitrile in a sealed vacuum glass tube. The SnS2/C nanospheres with unique layered structure exhibited a high reversible capacity of 660 mA h g−1 at a current density of 50 mA g−1 and maintained 570 mA h g−1 for 100 cycles with a degradation rate of 0.14% per cycle. The superior cycling stability of the SnS2/C electrode is attributed to the stable nanosphere morphology and structural integrity during charge/discharge cycles, as evidenced by ex situ characterization.218
 |
| Fig. 8 (a) Representative FESEM image of the SnS2-rGO composite. (b) HRTEM image of the SnS2-rGO composite. (c) Cycling performance of SnS2-rGO, SnS2 and graphene electrodes at 0.2 A g−1 for 100 cycles. (d) Rate performance of SnS2-rGO and SnS2 electrodes. Reproduced with permission ref. 217. Copyright 2014 Wiley (a–d). | |
3.5 Sn4P3
The long cycle stability and rate performance of the as-obtained Sn4P3 nanoparticles have been tested as anode material for lithium ion batteries for the first time. Sn4P3 nanoparticles, with the smallest size give the best cycling and rate performances. The improved electrochemical performances of the Sn4P3 electrode might be largely attributed to their small-size. Liu et al. developed a facile approach to the synthesis of Sn4P3 nanoparticles by a solvothermal reaction.219 An intermetallic compound of Sn4P3 was obtained by facile high-energy mechanical ball milling in an Ar atmosphere for an hour. Sn4P3 delivered a high reversible capacity of 718 mA h g−1, and showed very stable cycle performance with negligible capacity fading over 100 cycles; the cycle performance of Sn4P3 was better than those of previously reported Sn-based materials and phosphorus/carbon composites.220 Phosphorus/carbon composite materials have shown excellent electrochemical performance, including the highest specific capacity (1890 mA h g−1) among all reported anode materials.221,222 However, phosphorus has poor electrical conductivity, and thus, a large amount of carbon (30 wt%) has to be used in the phosphorus/carbon composites to enhance their electrical conductivity, which decreases their gravimetric and volumetric energy densities.223 Uniform yolk–shell Sn4P3@C nanospheres were facilely synthesized via a top-down phosphorized route with yolk–shell Sn@C nanospheres as the precursor. As anode materials for Na-ion batteries, they exhibit a very high reversible capacity (790 mA h g−1), superior rate capability and stable cycling performance (a high capacity of 360 mA h g−1 at 1.5C after long 400 cycles). Qian et al. described a green approach to the synthesis of the Sn4P3/C nanocomposite and demonstrated its excellent Na-storage performance as a novel anode of Na-ion batteries. This Sn4P3/C anode can deliver a very high reversible capacity of 850 mA h g−1 with a remarkable rate capability with 50% capacity output at 500 mA g−1 and can also be cycled with 86% capacity retention over 150 cycles.224
3.6 Others
Other tin based materials like tin–phosphate glass, multiphase tin and tin sulfide@other transition metal sulfide also exhibit high performance. The tin–phosphate glass is a promising candidate for new anode active material that realizes high energy density sodium ion batteries. During the first charge process, sodium ions diffused into the tin–phosphate glass matrix and due to the reduction of Sn2+ to the SnO state, sodiated tin metal nano-sized particles were formed in the oxide glass matrix. After the second cycle, Honma et al. confirmed the steady reversible reaction of ∼320 mA h g−1 at 0–1 V cutoff voltage conditions, by the alloying process in NaxSn4.225 Kim et al. successfully synthesized multiphase SnSb nanoparticles-on SnO2/Sn/C nanofibers by electrospinning, followed by heat treatment under Ar atmosphere. The nanocomposite fibers were observed to be multiphase single crystalline SnSb particles on SnO2/Sn/C nanofibers. These fiber electrodes exhibited high capacity in both lithium and sodium tests, due to the synergistic effects of 1D and 0D hybrid nanostructures, offering large surface area, good electric conductivity, and buffer volume variation.226 Tin-molybdenum oxide yolk–shell microspheres prepared by a one-pot spray pyrolysis process transformed into yolk–shell SnS–MoS2 composite microspheres. The yolk–shell SnS–MoS2 composite microspheres with high structural stability during repeated sodium insertion and desertion processes have low charge-transfer resistance, even after long-term cycling, as shown in Fig. 9. This resulted from the synergetic effect of the yolk–shell structure and uniform mixing of the SnS and MoS2 nanocrystals.227
 |
| Fig. 9 (a and b) FE-SEM image, TEM image of the yolk–shell SnS–MoS2 composite microspheres, (c) initial charge/discharge curves at a constant current density of 0.5 A g−1, (d) cycling performances of all samples at a constant current density of 0.5 A g−1. Reproduced with permission ref. 227. Copyright 2014 American Chemical Society (a–d). | |
4. Supercapacitors
4.1 SnO2
4.1.1 Pure SnO2. The hydrous RuO2 electrode with its extraordinary capacitance properties is the most suitable electrode material for supercapacitors. However, due to its rarity and high cost, wide usage of RuO2 in supercapacitor applications is limited. Therefore, efforts have been made to find inexpensive materials, such as MnO2, NiO, SnO2 and Co3O4 for supercapacitor applications. Due to the non-toxic nature and low cost, SnO2 is attracting much attention in the field of supercapacitors. SnO2 is noted as co-material for RuO2, due to its chemical stability and high electrical conductivity. Generally, two different mechanisms have been proposed for the charge storage mechanisms.230 For the pseudocapacitors, it is the intercalation/deintercalation of protons or alkaline metal cations that leads to the full utilization of the electrode material. This may be the reason for obtaining a higher specific capacitance at a lower scan rate. There are redox peaks in the cyclic voltammetric (CV) curves of pseudocapacitors. For electric double-layer capacitors (EDLC), the explanation of mechanism relates to the surface adsorption process for a higher scan rate. This is based on the diffusion effect of the proton within the electrode materials. Hence, it is believed that part of the surface of electrode materials contributed at a high charging/discharging rate, which decreased the specific capacitance. EDLC depends mainly on the accumulation of charges at the interface of the electrode/electrolyte. Moreover, supercapacitor performance is morphology dependent and improved performance is observed with porous morphology, due to better insertion of the electrolyte within the pores of the electrode material. As a result, Sn based materials with porous morphology have been widely studied. The shapes of the CV curves of EDLC are rectangular (more or less). The excellent performances of the supercapacitor were attributed to the morphology and structure of the materials. Several examples of Sn-based nanomaterials and their electrochemical properties are given in Table 1. Meng et al. have synthesized 3D SnO2 nanoflowers on Ti substrate by a one-step and surfactant-free hydrothermal method. This is a very simple and cost-effective technique for the industrial production of SnO2 nanostructures. 3D SnO2 nanoflowers grown on Ti substrate not only offer a direct path for electrons toward the current collector, but can also alleviate the volume change during the charge/discharge process, due to the unique hierarchical structure. Moreover, it has an accessible surface for electrochemical reactions. Ni nanoparticles on SnO2 nanoflowers have also been developed.228 SnO2 aggregation nanostructures with uniform pores were synthesized through a gas–liquid interfacial reaction driven by solvothermal means. This architecture exhibits excellent cycling stability as an electrode for supercapacitors (97% capacity retention over 1000 cycles at 1 A g−1 after the first 80 cycles decay).229 Nanocrystalline SnO2 thin films were deposited by a simple and inexpensive chemical route. The deposited films were nanocrystalline with the tetragonal rutile structure of SnO2. The SnO2 showed a maximum specific capacitance of 66 F g−1 in 0.5 Na2SO4 electrolyte at 10 mV s−1 scan rate. The enhanced specific capacitance observed in our case may be due to its highly porous morphology.230
Table 1 Summary of the state-of-the-art Sn and Sn compound based electrode materials for supercapacitor applications
Category |
Selected examples |
Electrochemical properties |
Ref. |
Sn |
Sn@graphene |
320 F g−1 at 10 mV s−1, 96%, 800 cycles |
261 |
SnO2 |
Ni–SnO2 |
410 mF cm−2, ∼93.6%, 2500 cycles |
228 |
SnO2 thin films |
66 F g−1 at 10 mV s−1 |
230 |
SnO2 aggregations |
50.3 F g−1, 1 A g−1, 1000 cycles |
229 |
SnO2@C |
SnO2@C |
37.8 F g−1 at 5 mV s−1 |
243 |
SnO2/rGO |
347.3 F g−1 at 5 mV s−1, 90%, 3000 cycles |
239 |
PtRu/SnO2 on G |
99.7 F g−1 at 50 mV s−1 |
242 |
PANI/SnO2 |
173 F g−1 at 25 mV s−1 |
247 |
G-SnO2-PANI |
913.4 F g−1 at 5 mV s−1, 90.8%, 1000 cycles |
249 |
SnO2/carbon aerogel |
62.5–66.6 F g−1 |
241 |
Others |
Ru–Sn oxides |
714 F g−1 at 25 mV s−1 |
256 |
Sb–SnO2–MnO2 |
319.0 F g−1 at 0.2 A g−1 |
259 |
SnO2@MoO3 |
295 F g−1 at 5 mV s−1, 97%, 1000 cycles |
258 |
Ni/Co/SnOx |
328 F g−1 at 1 mV s−1, 86%, 600 cycles |
244 |
Sn doped PEDOT |
181.41 F g−1 at 10 mV s−1, 92%, 1000 cycles |
262 |
LiSn2(PO4)3 |
19.4 F g−1, 0.05 A g−1 |
266 |
4.1.2 SnO2@C. Materials that could be used as supercapacitor electrode materials include metal oxides, carbon materials, and conducting polymers.231 Of particular interest are carbon-based electrode materials because of their low cost and potential to realize both high specific capacitance and high power density as a result of their high surface areas. Carbon-based materials have usually been added with the active materials for improving the electrical, electrochemical, and electrocatalytic properties, especially in energy devices. This inhomogeneous mechanical dispersion reduces the performance of the active materials.232 However, the limited charge accumulation in the electrical double layer restricts the specific capacitance of EDLCs to a range of relatively small values between 90 and 250 F g−1. Meanwhile, pseudocapacitors based on metal oxides such as RuO2, CoOx, and MnO2 or conducting polymers including polypyrrole and polyaniline usually show less cycling stability than EDLCs, but have high specific capacitance values.233 Graphene, a novel and unique EDLC-based carbon material with a one-atom thick layer has been used as a supercapacitor electrode material, due to its high surface area, excellent stability, and good conductivity.234–237 Wang and co-workers reported on the microwave-assisted, one-pot synthesis of SnO2/graphene, which gave rise to the specific capacitance of 99.7 F g−1.238 Zhang adopted a simple and fast colloid electrostatic self-assembly method to prepare the SnO2/graphene nanocomposite (SGNC). As shown in Fig. 10, the SGNC has the specific capacitance of 347.3 F g−1. Furthermore, this material also showed excellent cycling stability, and the specific capacitance was 90% retained after 3000 cycles.239 Li et al. prepared SnO2/graphene using a one-pot synthesis approach, which showed a specific capacitance of 34.6 F g−1.240 SnO2/graphene nanocomposite hydrogel was synthesized using a solvothermal processing route. This one-pot synthesis strategy is facile and does not require any reducing or oxidizing agent. The in situ growth of SnO2 led to uniformly decorated nanoparticles on the surface of graphene. The SnO2/graphene nanocomposite possessed a pronounced enhancement of electrochemical properties, allowing the nanocomposite to be used as a supercapacitor.241,242 To realize a suitable pseudocapacitor nanomaterial, the recently developed technique of reaction under autogenic pressure at elevated temperature has been employed to synthesize SnO2@C nanocomposites. The synthesized SnO2@C nanomaterials are highly crystalline with hexagonal shape. The nanocomposite has a maximum specific capacitance of 37.8 F g−1 at a scan rate of 5 mV s−1.243
 |
| Fig. 10 (a) Schematic illustration of the preparation of SGNC, (b) capacitance values of SGNC, rGO, and SnO2 against scan rates calculated by CV curves, (c) cycling performance of SGNC at a current density of 100 mA g−1; the inset gives the initial and the last 10 cycles of SGNC. Reproduced with permission ref. 239. Copyright 2015 Springer (a–c). | |
Polyaniline (PANI) has attracted significant attention, due to its environmental stability and controllable electrical conductivity. However, the conductance of these polymers is low in the dedoped state, which would result in high ohmic polarization of supercapacitors, reducing their reversibility and stability.246 To solve these problems and explore any potential synergistic effects, Hu et al. proposed polyaniline–tin oxide composites (PANI/SnO2) as electrode materials for supercapacitors. The results indicate that the PANI/SnO2 has a synergistic effect on the complementary properties of both components.247 Jin synthesized a nanostructured graphene–SnO2–polyaniline (GSP) ternary composite via a one-pot method, including the reduction of GO by Sn2+, and tiny SnO2 nanoparticles were homogeneously distributed on the graphene sheets. PANI was synthesized in situ on the surface of the graphene–SnO2 composite in order to obtain the GSP ternary composite. The GSP ternary composite achieved a maximum capacitance of 913.4 F g−1 after 1000 cycles.249
4.1.3 SnO2@MxOy (M = Ru, Ti, Ta, Mo). Due to the high cost of ruthenium precursors and the possible synergistic effects occurring among RuO2, SnO2, TiO2, and Ta2O5, binary (Ru–Sn, Ru–Ti, Ru–Ta) and ternary (Ru–Sn–Ti, Ru–Sn–Ta) mixed oxides have been developed. For example, the utilization of RuO2 was promoted by introducing Sn into RuO2·xH2O via a modified sol–gel method.250–253 Since the total specific capacitance of mixed Ru–Sn oxides is highly composition-dependent and a precise composition control for this series of oxides is complicated, a simple process for preparing Ru–Sn mixed oxides with very high-power characteristics, acceptable specific capacitance, and long service-life is practically desirable.256,257 Tin oxide coated molybdenum oxide nanowires (SnO2/MoO3) were synthesized by a combination of hydrothermal and wet chemical routes. The specific capacitance of SnO2/MoO3 core–shell composite nanowires is 295 F g−1, which is much higher than the specific capacitance of pure individual MoO3 (69 F g−1) and SnO2 (96.6 F g−1), as shown in Fig. 11. Moreover, the synthesized core shell composite nanowires have also exhibited excellent long-term cycling stability.258 To enhance the specific capacity and cycling stability of manganese oxides (MnO2) for supercapacitors, Sb doped SnO2 (SS) were coated on MnO2 through a sol–gel method to prepare MnO2 electrodes. SS-MnO2 electrodes hold the porous structure, displaying superior cycling stability at large current work conditions in charge–discharge tests and good capacity performance at high scanning rates in CV tests.259 Ferreira synthesized ternary oxides by the Pechini method, with subsequent deposition onto a titanium substrate in a thin-film form. It exhibited a maximum specific capacitance of 328 F g−1. Specific power and specific energy were 345.7 W kg−1 and 18.92 W h kg−1, respectively, and the capacitance retention was kept at 86% of its initial value after 600 cycles.260
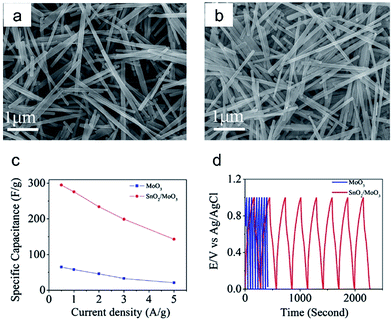 |
| Fig. 11 (a) FE-SEM image of MoO3 nanowires synthesized at 180 °C for 10 h. (b) FE-SEM image of 5 nm SnO2 deposited MoO3 nanowires. (c) Specific capacitance variation of MoO3 and 5 nm SnO2 coated MoO3 nanowires at different current densities. (d) Galvanostatic charge–discharge curves of MoO3 and 5 nm SnO2 coated MoO3 nanowires at a charge discharge current density of 0.5 A g−1. Reproduced with permission ref. 258. Copyright 2012 Elsevier (a–d). | |
4.2 Others
Other tin based nanomaterials have been widely researched in recent years. Sn nanoparticle decorated graphene (Sn–Gr) materials were prepared by adding tin powder to the reaction of graphite oxide during thermal reduction. The Sn nanoparticles were uniformly distributed on the surface of Gr sheets, in which Sn nanoparticles acted as a spacer to effectively to prevent the restacking of Gr sheets. The Sn–Gr electrodes exhibited a high specific capacitance of 320 F g−1 at a scan rate of 10 mV s−1 in 2 M KNO3 aqueous solution.261 Electrochemically synthesized tin ion (Sn2+) doped poly(3-methylthiophene) and poly(3,4-ethylenedioxythiophene) on pencil graphite electrode (PGE) were prepared to be utilized as the electrode materials for supercapacitor applications.262 In contrast to carbon-based materials and metal oxides, conducting polymers have good electrical conductivity and large capacitance.263–265 Among conducting polymers, polythiophene and its derivatives have received much interest, due to their several advantages: (i) compatibility in both aqueous and organic electrolytes, (ii) ability to work in a wide potential range, (iii) environmental stability, (iv) high electrical conductivity, (v) large pseudocapacitance, (vi) fast electrochemical charge/discharge process.266–268
5. Conclusion and outlook
In this review, we have attempted to chart the significant progress in nanostructured Sn, Sn oxides, dichalcogenides (SnSx, x = 1, 2), Sn alloys, oxysalts and their nanocomposites for rechargeable LIBs/SIBs and supercapacitors. The rational and creative design of unique nanoarchitectures helps to address the significant issues encountered during the electrochemical reactions, thus dramatically enhancing the capacity, rate capability, and cycle life of Sn-based electrodes. These developments greatly enrich Sn based chemistry and represent promising steps towards viable energy storage devices. Compared to other new anode materials with higher theoretical capacities, such as Si-based materials, Ge-based materials and transition metal oxides like Co3O4 and Fe3O4, the Sn-based materials have received considerable attention for their advantageous properties, such as high theoretical capacity, high tap density, and safe thermodynamic potential in LIBs and SIBs. In supercapacitors, different oxide materials such as RuO2, MnO2, CoO, NiO, Bi2O3, Fe3O4, SnO2, SnO have been studied widely, however, Sn based nanomaterials have attracted more attention because of their low cost, chemical stability and high electrical conductivity.
Despite the various structural forms, based on our comprehensive study, the Sn-based anode materials must enable the relief of the Sn volume variation during cycling, promotion of the ion/electron transfer and inhibition of the SEI formation. In addition to these three design principles, the Sn-based anodes should afford high tap/packing density to increase the areal/volumetric capacities for their viable applications in next-generation batteries. Future research should be focused on developing novel processes capable of preparing high tap/packing density Sn-based anodes, which is also the key to removing the threat from Si-based materials to their potential implementation in future LIBs and SIBs. What is more, by virtue of the modern analytical techniques on the atomic or molecular level, the investigation on increasing the initial coulombic efficiency of nanostructured electrode materials needs to be emphasized, since it is important for the commercialization of nanostructured materials for rechargeable LIBs/SIBs and supercapacitors. Although the road to viable energy storage devices based on nanostructured Sn-based materials is still significantly challenging, great strides have been achieved over the past decade. For the realization of wide industrial applications of nanostructured Sn-based electrode materials in the energy-storage fields, more work is required to achieve large-scale preparation, improve volumetric energy density (i.e., increase the tap density), and maintain high compatibility between electrodes with electrolytes, as well as device systems.
Acknowledgements
This work was supported by the Program for New Century Excellent Talents of the University in China (grant no. NCET-13-0645) and the National Natural Science Foundation of China (NSFC-21201010, 21673203, 21671170, 21673203, 21505118 and 51202106), Innovation Scientists and Technicians Troop Construction Projects of Henan Province-164200150018, Plan for Scientific Innovation Talent of Henan Province, Program for Innovative Research Team (in Science and Technology) in University of Henan Province (14IRTSTHN004, 16IRTSTHN003), the Science & Technology Foundation of Henan Province (122102210253 and 13A150019), the Science & Technology Foundation of Jiangsu Province (BK20150438), the Six Talent Plan (2015-XCL-030), Innovation and Entrepreneurship Training Program for College Students in Jiangsu province (No. 201611117047Y) and the China Postdoctoral Science Foundation (2012M521115). We also acknowledge the Priority Academic Program Development of Jiangsu Higher Education Institutions.
References
- Y. Yu, L. Gu, P. A. V. Aken and J. Maier, J. Am. Chem. Soc., 2009, 131, 15984–15987 CrossRef CAS PubMed.
- B. C. Duan, W. K. Wang and Y. S. Yang, Rare Met. Mater. Eng., 2012, 41, 93–100 Search PubMed.
- Y. J. Hsu and S. Y. Lu, J. Phys. Chem. B, 2005, 109, 4398–4403 CrossRef CAS PubMed.
- T. L. Tan, O. I. Malyi and S. Manzhos, Solid State Ionics, 2014, 268, 273–276 CrossRef CAS.
- Y. Zou and Y. Wang, ACS Nano, 2011, 5, 8108–8114 CrossRef CAS PubMed.
- H. S. Im, Y. J. Cho, C. S. Jung, D. M. Jang, J. Park, F. Shojaei and H. S. Kang, ACS Nano, 2013, 7, 11103–11105 CrossRef CAS PubMed.
- N. Li, H. W. Song, G. W. Yang and C. X. Wang, J. Mater. Chem. A, 2014, 2, 2526–2529 CAS.
- F. Nobili, I. Meschini, F. Croce, R. Tossici and R. Marassi, Electrochim. Acta, 2013, 107, 85–92 CrossRef CAS.
- I. Meschini, F. Nobili, R. Marassi, R. Tossici, A. Savoini, M. L. Focarete and F. Croce, J. Power Sources, 2013, 226, 241–248 CrossRef CAS.
- Y. J. Hong and Y. C. Kang, Small, 2015, 11, 2157–2163 CrossRef CAS PubMed.
- K. Shiva, K. Jayaramulu and A. J. Bhattacharyya, Z. Anorg. Allg. Chem., 2014, 5, 1115–1118 CrossRef.
- J. Z. Chen, L. Yang, Z. X. Zhang, A. Deb and S.-I. Hirano, Electrochim. Acta, 2014, 127, 390–396 CrossRef CAS.
- G. H. Zhang, J. Zhu, S. C. Hou, F. L. Gong, F. Li, C. C. Li and H. G. Duan, Nano Energy, 2014, 9, 61–70 CrossRef CAS.
- F. Cheng, W.-C. Li, W.-P. Zhang and A.-H. Lu, Nano Energy, 2016, 19, 486–494 CrossRef CAS.
- Z. Q. Zhu, S. W. Wang, Q. Jin, T. R. Zhang, F. Y. Cheng and J. Chen, Nano Lett., 2014, 14, 153–157 CrossRef CAS PubMed.
- Y. Zhong, X. F. Li, R. Y. Li, M. Cai and X. L. Sun, Appl. Surf. Sci., 2015, 332, 192–197 CrossRef CAS.
- K.-C. Hsu, C.-E. Liu, C.-Y. Lee and H.-T. Chiu, J. Mater. Chem., 2012, 22, 21533–21535 RSC.
- M.-J. Deng, D.-C. Tsai, C.-F. Li and F.-S. Shieu, Appl. Surf. Sci., 2013, 285P, 180–184 CrossRef.
- W. Ni, J. L. Cheng, X. D. Li, B. Wang, Q. Guan, L. Huang, G. F. Gu and H. Li, J. Mater. Chem. A, 2014, 2, 19122–19124 CAS.
- D.-H. Nam, J. W. Kim, S.-Y. Lee, H.-A.-S. Shin, S.-H. Lee and Y.-C. Joo, J. Mater. Chem. A, 2015, 3, 11021–11023 CAS.
- H. Y. Wang, H. Q. Huang, C. G. Wang, B. Yan, Y. T. Yu, Y. Yang and G. Yang, ACS Sustainable Chem. Eng., 2014, 2, 2310–2317 CrossRef CAS.
- F. R. Beck, R. Epur, A. Manivannan and P. N. Kumta, Electrochim. Acta, 2014, 127, 299–306 CrossRef CAS.
- X. Y. Zhou, Y. L. Zou and J. Yang, J. Power Sources, 2014, 253, 287–293 CrossRef CAS.
- C. D. Wang, Y. Li, Q.-H. Wu, X. F. Chen and W. J. Zhang, Nanoscale, 2013, 5, 10599–10602 RSC.
- X. S. Zhou, J. C. Bao, Z. H. Dai and Y.-G. Guo, J. Phys. Chem. C, 2013, 117, 25367–25373 CAS.
- P. C. Lian, J. Y. Wang, G. X. Liu, Y. Y. Wang and H. H. Wang, J. Alloys Compd., 2014, 604, 188–195 CrossRef CAS.
- J. C. Guo, Z. C. Yang and L. A. Archer, J. Mater. Chem. A, 2013, 1, 8710–8713 CAS.
- X. Y. Li, Y. M. Chen, H. T. Wang, H. M. Yao, H. T. Huang, Y. W. Mai, N. Hu and L. M. Zhou, Adv. Funct. Mater., 2016, 26, 376–383 CrossRef CAS.
- Z. F. Li, H. Y. Zhang, Q. Liu, Y. D. Liu, L. Stanciu and J. Xie, ACS Appl. Mater. Interfaces, 2014, 6, 5996–6001 CAS.
- D. L. Ma, Z. Y. Cao, H. G. Wang, X. L. Huang, L. M. Wang and X. B. Zhang, Energy Environ. Sci., 2012, 5, 8538–8542 CAS.
- F. Han, D. Li, W. C. Li, C. Lei, Q. Sun and A. H. Lu, Adv. Funct. Mater., 2013, 23, 1692 CrossRef CAS.
- H. J. Ding, B. Yao, J. K. Feng and J. X. Zhang, J. Mater. Chem. A, 2013, 1, 11200–11203 Search PubMed.
- P. J. Zhang, L. B. Wang, J. Xie, L. W. Su and C. A. Ma, J. Mater. Chem. A, 2014, 2, 3776–3781 CAS.
- H. Yu, L. J. Pan, N. Liu, M. T. McDowell, Z. N. Bao and Y. Cui, Nat. Commun., 2013, 4, 1943–1947 Search PubMed.
- M. Sindoro, Y. H. Feng, S. X. Xing, H. Li, J. Xu, H. L. Hu, C. C. Liu, Y. W. Wang, H. Zhang, Z. X. Shen and H. Y. Chen, Angew. Chem., Int. Ed., 2011, 50, 9898–9901 CrossRef CAS PubMed.
- J. X. Zhu, D. Yang, X. H. Rui, D. Sim, H. Yu, H. H. Hng, H. E. Hoster, P. M. Ajayan and Q. Y. Yan, Small, 2013, 9, 3390–3393 CrossRef CAS PubMed.
- X. Fan, X. N. Tang, D. Q. Ma, D. Q. Maa and X. H. Xu, J. Solid State Electrochem., 2014, 18, 1137–1145 CrossRef CAS.
- D. B. Polat, J. Lu and K. Amine, ACS Appl. Mater. Interfaces, 2014, 6, 10877–10885 CAS.
- M. Uysal, T. Cetinkaya, A. Alp and H. Akbulut, Thin Solid Films, 2014, 572, 216–223 CrossRef CAS.
- H. X. Dang, K. C. Klavetter, M. L. Meyerson, A. Hellera and C. B. Mullins, J. Mater. Chem. A, 2015, 3, 13500 CAS.
- H. Gul, M. Uysal, T. C. Etinkaya, M. O. Guler, A. Alp and H. Akbulut, Int. J. Hydrogen Energy, 2014, 39, 21414–21419 CrossRef CAS.
- X. Liu, J. Y. Xie, P. P. Lv, K. Wang, Z. H. Feng and K. Swierczek, Solid State Ionics, 2015, 269, 86–92 CrossRef CAS.
- H. G. Zhang, T. Shi, D. J. Wetzel, R. G. Nuzzo and P. V. Braun, Adv. Mater., 2016, 28, 742–747 CrossRef CAS PubMed.
- J. Liu, Y. R. Wen, P. A. V. Aken, J. Maier and Y. Yu, Nano Lett., 2014, 14, 6387–6392 CrossRef CAS PubMed.
- M. Uysal, H. Gul, A. Alp and H. Akbulut, Int. J. Hydrogen Energy, 2014, 39, 21391–21398 CrossRef CAS.
- D. S. Guan, J. Y. Li, X. F. Gao and C. Yuan, J. Alloys Compd., 2014, 617, 464–471 CrossRef CAS.
- Z. Edfouf, M. T. Sougrati and F. Cuevas, J. Power Sources, 2013, 238, 210–217 CrossRef CAS.
- K. Zhuo, M. G. Jeong and C. H. Chung, J. Power Sources, 2013, 244, 601–605 CrossRef CAS.
- X. Fan, P. Dou, D. Q. Ma, P. Bi, A. N. Jiang, J. Zhu and X. H. Xu, ACS Appl. Mater. Interfaces, 2014, 6, 22282–22288 CAS.
- J. Qin, X. Zhang, N. Q. Zhao, C. S. Shi, E. Z. Liu, J. J. Lia and C. N. He, RSC Adv., 2014, 4, 49247–49251 RSC.
- X. Y. Hou, Y. J. Hu, H. Jiang, Y. F. Li, X. F. Niu and C. Z. Li, Chem. Commun., 2015, 51, 16373–16376 RSC.
- Q. L. Jiang, D. Z. Hu, M. Q. Jia and R. S. Xue, Appl. Surf. Sci., 2014, 321, 109–115 CrossRef CAS.
- A. Birrozzi, F. Maroni and R. Raccichini, J. Power Sources, 2015, 294, 248–253 CrossRef CAS.
- P. X. Zhang, Y. Y. Wang and J. W. Wang, Electrochim. Acta, 2014, 137, 121–130 CrossRef CAS.
- J. Leibowitz, E. Allcorn and A. Manthiram, J. Power Sources, 2015, 295, 125–130 CrossRef CAS.
- B. Liu, A. Abouimrane, D. E. Brown, X. F. Zhang, Y. Ren, Z. Z. Fang and K. Amine, J. Mater. Chem. A, 2013, 1, 4376–4380 CAS.
- Y. Ye, P. Wu, X. Zhang, T. Zhou, Y. W. Tang, Y. M. Zhou and T. H. Lu, RSC Adv., 2014, 4, 17401–17405 RSC.
- B. Liu, A. Abouimrane, Y. Ren, M. Balasubramanian, D. P. Wang, Z. gang, Z. Fang and K. Amine, Chem. Mater., 2012, 24, 4653–4661 CrossRef CAS.
- J. P. Liu, Y. Y. Li, X. T. Huang, R. M. Ding, Y. Y. Hu, J. Jiang and L. Liao, J. Mater. Chem., 2009, 19, 1859–1862 RSC.
- P. Meduri, C. Pendyala, V. Kumar, G. U. Sumanasekera and M. K. Sunkara, Nano Lett., 2009, 9, 612–617 CrossRef CAS PubMed.
- M. S. Park, Y. M. Kang, G. X. Wang, S. X. Dou and H. K. Liu, Adv. Funct. Mater., 2008, 18, 455–460 CrossRef CAS.
- J. Z. Wang, N. Du, H. Zhang, J. X. Yu and D. R. Yang, J. Phys. Chem. C, 2011, 115, 11302–11307 CAS.
- Y. Wang, J. Y. Lee and H. C. Zeng, Chem. Mater., 2005, 17, 3899–3903 CrossRef CAS.
- Z. X. Yang, G. D. Du, C. Q. Feng, S. A. Li, Z. X. Chen, P. Zhang, Z. P. Guo, X. B. Yu, G. N. Chen, S. Z. Huang and H. K. Liu, Electrochim. Acta, 2010, 55, 5485–5488 CrossRef CAS.
- J. F. Ye, H. J. Zhang, R. Yang, X. G. Li and L. M. Qi, Small, 2010, 6, 296–302 CrossRef CAS PubMed.
- F. Cheng, Z. Tao, J. Liang and J. Chen, Chem. Mater., 2008, 20, 667–671 CrossRef CAS.
- C. Wang, G. H. Du, K. Stahl, H. X. Huang, Y. J. Zhong and J. Z. Jiang, J. Phys. Chem. C, 2012, 116, 4000–4007 CAS.
- C. Wang, Q. Wu, H. L. Ge, T. Shang and J. Z. Jiang, Nanotechnology, 2012, 23, 075704 CrossRef PubMed.
- R. Yang, Y. G. Gu, Y. Q. Li, J. Zheng and X. G. Li, Acta Mater., 2010, 58, 866–869 CrossRef CAS.
- S. J. Ding and X. W. Lou, Nanoscale, 2011, 3, 3586–3589 RSC.
- Z. Y. Wang, Z. C. Wang, W. T. Liu, W. Xiao and X. W. Lou, Energy Environ. Sci., 2013, 6, 87–91 CAS.
- X. F. Chen, Y. Huang and H. J. Huang, Mater. Lett., 2015, 149, 33–36 CrossRef CAS.
- Y. K. Wang, D. Li and J. M. Zhang, Mater. Lett., 2016, 167, 222–225 CrossRef CAS.
- Q. S. Xie, Y. T. Ma, X. Q. Zhang, H. Z. Guo, A. L. Lu, L. S. Wang, G. H. Yue and D. L. Peng, Electrochim. Acta, 2014, 141, 374–383 CrossRef CAS.
- Y. T. Ma, Q. S. Xie, X. Liu, Y. C. Zhao, D. Q. Zeng, L. S. Wang, Y. Zheng and D. L. Peng, Electrochim. Acta, 2015, 182, 327–333 CrossRef CAS.
- S. Zhao, Y. Bai and W.-F. Zhang, Electrochim. Acta, 2010, 55, 3891–3896 CrossRef CAS.
- Y. Sharma, N. Sharma, G. V. S. Rao and B. V. R. Chowdari, J. Power Sources, 2009, 192, 627–635 CrossRef CAS.
- K. Wang, Y. Huang, T. Z. Han, Y. Zhao, H. J. Huang and L. L. Xue, Ceram. Int., 2014, 40, 2359–2364 CrossRef CAS.
- Y. Q. Cao, L. Zhang and K. P. Su, Electrochim. Acta, 2014, 132, 483–489 CrossRef CAS.
- G. Q. Fang, S. Kaneko, W. W. Liu, B. B. Xia, H. D. Sun, R. X. Zhang, J. W. Zheng and D. C. Li, Appl. Surf. Sci., 2013, 283, 963–967 CrossRef CAS.
- F. Q. Fan, G. Q. Fang, R. X. Zhang, Y. H. Xu, J. W. Zheng and D. C. Li, Appl. Surf. Sci., 2014, 311, 484–489 CrossRef CAS.
- C. Guan, X. L. Li, H. Yu, L. Mao, L. H. Wong, Q. Y. Yanc and J. Wang, Nanoscale, 2014, 6, 13824–13830 RSC.
- L. L. Li, S. J. Peng, J. Wang, Y. L. Cheah, P. F. Teh, Y. Ko, C. L. Wong and M. Srinivasan, ACS Appl. Mater. Interfaces, 2012, 4, 6005–6012 CAS.
- Y. Z. Jiang, Y. Li, P. Zhou, S. L. Yu, W. P. Sun and S. X. Dou, ACS Appl. Mater. Interfaces, 2015, 7, 26367–26373 CAS.
- Y. Hwa, W.-S. Kim, B.-C. Yu, H. S. Kim, S.-H. Honga and H.-J. Sohn, J. Mater. Chem. A, 2013, 1, 3733–3736 CAS.
- H. K. Wang, M. Wang, B. B. Li, X. Yang, K. Safarova, R. Zboril, A. L. Rogachc and M. K. H. Leung, CrystEngComm, 2014, 16, 7529–7534 RSC.
- C. X. Hua, X. P. Fang, Z. X. Wang and L. Q. Chen, Chem.–Eur. J., 2014, 20, 5487–5491 CrossRef CAS PubMed.
- M. Chen, P. P. Liu, C. J. Wang, W. J. Ren and G. W. Diao, New J. Chem., 2014, 38, 4566–4573 RSC.
- G. E. Luo, Y. H. Lu, S. S. Zeng, S. B. Zhong, X. Y. Yua, Y. P. Fang and L. Y. Sun, Electrochim. Acta, 2015, 182, 715–722 CrossRef CAS.
- T. Z. Yuan, Y. Z. Jiang and M. Yan, Electrochim. Acta, 2014, 136, 27–32 CrossRef CAS.
- S. H. Lee, S. H. Jee and Y. S. Yoon, Electrochim. Acta, 2013, 87, 905–911 CrossRef CAS.
- W.-J. Cui, J. Yi, L. Chen, C.-X. Wang and Y.-Y. Xia, J. Power Sources, 2012, 217, 77–84 CrossRef CAS.
- J. X. Wang, W. Li and F. Wang, Nanoscale, 2014, 6, 3217–3222 RSC.
- X. Y. Yu, S. Y. Yang, B. H. Zhang, D. Shao, X. M. Dong and Y. P. Fang, J. Mater. Chem., 2011, 21, 12295–12302 RSC.
- P. Wu, N. Du, H. Zhang, J. X. Yu and D. R. Yang, J. Phys. Chem. C, 2010, 114, 22535–22538 CAS.
- Y. Zhao, J. Li, N. Wang, C. X. Wu, G. F. Dong and L. H. Guan, J. Phys. Chem. C, 2012, 116, 18612–18617 CAS.
- C. H. Xu, J. Sun and L. Gao, J. Mater. Chem., 2012, 22, 975–979 RSC.
- J. F. Liang, W. Wei, D. Zhong, Q. L. Yang, L. D. Li and L. Guo, ACS Appl. Mater. Interfaces, 2012, 4, 454–459 CAS.
- Z.-S. Wu, G. Zhou, L.-C. Yin, W. Ren, F. Li and H.-M. Cheng, Nano Energy, 2012, 1, 107–131 CrossRef CAS.
- X. Wang, X. Cao, L. Bourgeois, H. Guan, S. Chen, Y. Zhong, D.-M. Tang, H. Li, T. Zhai, L. Li, Y. Bando and D. Golberg, Adv. Funct. Mater., 2012, 22, 2682–2690 CrossRef CAS.
- J. Yao, X. Shen, B. Wang, H. Liu and G. Wang, Electrochem.
Commun., 2009, 11, 1849–1852 CrossRef CAS.
- S.-M. Paek, E. Yoo and I. Honma, Nano Lett., 2009, 9, 72–75 CrossRef CAS PubMed.
- L.-S. Zhang, L.-Y. Jiang, H.-J. Yan, W. D. Wang, W. Wang, W.-G. Song, Y.-G. Guo and L.-J. Wan, J. Mater. Chem., 2010, 20, 5462–5467 RSC.
- G. Chen, Z. Wang and D. Xia, Chem. Mater., 2008, 20, 6951–6956 CrossRef CAS.
- P. Wu, N. Du, H. Zhang, J. Yu and D. Yang, J. Phys. Chem. C, 2010, 114, 22535–22538 CAS.
- D. Ahn, X. Xiao, Y. Li, A. K. Sachdev, H. W. Park, A. Yu and Z. Chen, J. Power Sources, 2012, 212, 66–72 CrossRef CAS.
- L. Noerochim, J. Z. Wang, S. L. Chou, D. Wexler and H. K. Liu, Carbon, 2012, 50, 1289–1297 CrossRef CAS.
- H. X. Zhang, C. Feng, Y. C. Zhai, K. L. Jiang, Q. Q. Li and S. S. Fan, Adv. Mater., 2009, 21, 2299–2304 CrossRef CAS.
- K. J. Chan, H. I. Sung, S. S. Deok, L. G. Hee, S. H. Woo, P. K. Soo and K. D. Wan, Nanotechnology, 2012, 23, 465402 CrossRef PubMed.
- H. W. Song, N. Li and C. X. Wang, Electrochim. Acta, 2014, 120, 46–51 CrossRef CAS.
- I. Boyano, M. Bengoechea, I. Meatza, O. Miguel, I. Cantero, E. Ochoteco and J. Rodriguez, J. Power Sources, 2007, 166, 471–477 CrossRef CAS.
- S. Y. Chew, C. Feng and H. Liu, J. Electrochem. Soc., 2007, 154, A633–A637 CrossRef CAS.
- M. Sun, S. Zhang, T. Jiang and J. Yu, Electrochem. Commun., 2008, 10, 1819–1822 CrossRef CAS.
- B. Veeraraghavan, J. Paul and B. Popov, J. Power Sources, 2002, 109, 377–387 CrossRef CAS.
- G. X. Wang, L. Yang, Y. Chen, J. Z. Wang, S. Bewlay and H. K. Liu, Electrochim. Acta, 2005, 50, 4649–4654 CrossRef CAS.
- L. Cui, J. Shen, F. Cheng, Z. Tao and J. Chen, J. Power Sources, 2011, 196, 2195–2201 CrossRef CAS.
- L. Yuan, J. Wang, S. Y. Chew, J. Chen, Z. P. Guo, L. Zhao and H. K. Liu, J. Power Sources, 2007, 174, 1183–1187 CrossRef CAS.
- D.-H. Nam, S.-J. Lim, M.-J. Kim and H.-S. Kwon, RSC Adv., 2013, 3, 16102–16108 RSC.
- L. P. Zhang, Y. F. Wang, S. Q. Gou and J. H. Zeng, J. Phys. Chem. C, 2015, 119, 28721–28727 CAS.
- Y. Hwa, W.-S. Kim, B.-C. Yu, H. S. Kim, S.-H. Honga and H.-J. Sohn, J. Mater. Chem. A, 2013, 1, 3733–3737 CAS.
- S. Liu, X. Yin, Q. Hao, M. Zhang, L. Li, L. Chen, Q. Li, Y. Wang and T. Wang, Mater. Lett., 2010, 64, 2350–2353 CrossRef CAS.
- P. Wu, N. Du, H. Zhang, J. Liu, L. Chang, L. Wang, D. Yang and J. Z. Jiang, Nanoscale, 2012, 4, 4002–4006 RSC.
- J. Lu, C. Nan, L. Li, Q. Peng and Y. Li, Nano Res., 2013, 6, 55–64 CrossRef CAS.
- H. Mukaibo, A. Yoshizawa, T. Momma and T. Osakaa, J. Power Sources, 2003, 12, 119–121 Search PubMed.
- S. Liu, X. Yin, L. Chen, Q. Li and T. Wang, Solid State Sci., 2010, 12, 712–718 CrossRef CAS.
- C. Zhai, N. Du and H. Z. D. Yang, Chem. Commun., 2011, 47, 1270–1272 RSC.
- J. Wang, J. Liu, H. Xu, S. Ji, J. Wang, Y. Zhou, P. Hodgson and Y. Li, J. Mater. Chem. A, 2013, 1, 1117–1122 CAS.
- J. Ma, D. Lei, L. Mei, X. Duan, Q. Li, T. Wang and W. Zheng, CrystEngComm, 2012, 14, 832–836 RSC.
- J. W. Seo, J. T. Jang, S. W. Park, C. Kim, B. Park and J. Cheon, Adv. Mater., 2008, 20, 4269–4273 CrossRef CAS.
- H. Zhong, G. Yang, H. Song, Q. Liao, H. Cui, P. Shen and C. X. Wang, J. Phys. Chem. C, 2012, 116, 9319–9326 CAS.
- T. J. Kim, C. Kim, D. Son, M. Choi and B. Park, J. Power Sources, 2007, 167, 529–535 CrossRef CAS.
- J. Ma, D. Lei, X. Duan, Q. Li, T. Wang, A. Cao, Y. Maod and W. Zheng, RSC Adv., 2012, 2, 3615–3617 RSC.
- J. Zai, K. Wang, Y. Su, X. Qian and J. Chen, J. Power Sources, 2011, 196, 3650–3654 CrossRef CAS.
- J. Zai, X. Qian, K. Wang, C. Yu, L. Tao, Y. Xiao and J. Chen, CrystEngComm, 2012, 14, 1364–1375 RSC.
- Y. Du, Z. Yin, X. Rui, Z. Zeng, X. J. Wu, J. Liu, Y. Zhu, J. Zhu, X. Huang, Q. Yan and H. Zhang, Nanoscale, 2013, 5, 1456–1459 RSC.
- X. Y. Yu, H. Hu, Y. Wang, H. Chen and X. W. Lou, Angew. Chem., Int. Ed., 2015, 54, 7395–7398 CrossRef CAS PubMed.
- Q. Wu, L. Jiao, J. Du, J. Yang, L. Guo, Y. Liu, Y. Wang and H. Yuan, J. Power Sources, 2013, 239, 89–93 CrossRef CAS.
- Y. Liu, H. Kang, L. Jiao, C. Chen, K. Cao, Y. Wang and H. Yuan, Nanoscale, 2015, 7, 1325–1332 RSC.
- L. Zhang, H. B. Wu, Y. Yan, X. Wang and X. W. Lou, Energy Environ. Sci., 2014, 7, 3302–3306 CAS.
- C. K. Chan, H. Peng, G. Liu, X. F. Zhang, R. A. Huggins and Y. Cui, Nat. Nanotechnol., 2008, 3, 31–35 CrossRef CAS PubMed.
- X. Su and J. Li, Adv. Energy Mater., 2014, 4, 31–35 Search PubMed.
- J. Cai, Z. Li and P. K. Shen, ACS Appl. Mater. Interfaces, 2012, 4, 4093–4098 CAS.
- M. Sathish, S. Mitani and I. Honma, J. Phys. Chem. C, 2012, 116, 12475–12481 CAS.
- Z.-Y. Sui, C. Wang, K. Shu, Q.-S. Yang, Y. Ge, G. G. Wallace and B.-H. Han, J. Mater. Chem. A, 2015, 3, 10403–10412 CAS.
- C. Sun, Y. Deng, L. Wan, X. Qin and G. Chen, ACS Appl. Mater. Interfaces, 2014, 6, 11277–11285 CAS.
- M. Zheng, D. Qiu, B. Zhao, L. Ma, X. Wang, Z. Lin, L. Pan, Y. Zheng and Y. Shi, RSC Adv., 2013, 3, 699–703 RSC.
- S. Liu, X. Lu, J. Xie, G. Cao, T. Zhu and X. Zhao, ACS Appl. Mater. Interfaces, 2013, 5, 1588–1595 CAS.
- J.-G. Kang and G.-H. Lee, J. Mater. Chem., 2012, 22, 9330 RSC.
- C. T. Gao and L. Li, ACS Appl. Mater. Interfaces, 2015, 7, 26549–26556 CAS.
- H. L. Tang, X. Qi, W. J. Han, L. Ren, Y. D. Liu, X. Y. Wang and J. X. Zhong, Appl. Surf. Sci., 2015, 355, 7–13 CrossRef CAS.
- A. Ueda, M. Nagao, A. Inoue, A. Hayashi, Y. Seino, T. Ota and M. Tatsumisago, J. Power Sources, 2013, 244, 597–600 CrossRef CAS.
- S. L. Liu, H. Z. Zhang, L. Q. Xu, L. B. Ma and X. X. Chen, J. Power Sources, 2016, 304, 346–353 CrossRef CAS.
- L. Shen, L. Shen, Z. Wang and L. Q. Chen, Chem.–Eur. J., 2015, 21, 8491–8496 CrossRef CAS PubMed.
- H. Tang, J. Wang, H. Yin, H. Zhao, D. Wan and Z. Tang, Adv. Mater., 2015, 27, 1117–1123 CrossRef CAS PubMed.
- X. H. Zhang, H. Y. Xu, L. L. Ge and R. Guo, Acta Phys-Chim Sin, 2016, 32, 356–364 CAS.
- S. Komaba, Y. Matsuura, T. Ishikawa, N. Yabuuchi, W. Murata and S. Kuze, Electrochem. Commun., 2012, 21, 65–71 CrossRef CAS.
- L. D. Ellis, T. D. Hatchard and M. N. Obrovac, J. Electrochem. Soc., 2012, 159, A1801–A1806 CrossRef CAS.
- J. W. Wang, X. H. Liu, S. X. Mao and J. Y. Huang, Nano Lett., 2012, 12, 5897–5902 CrossRef CAS PubMed.
- M.-F. Ng, J. Zheng and P. Wu, J. Phys. Chem. C, 2010, 114, 8542–8547 CAS.
- Y. Wang, M. Wu, Z. Jiao and J. Y. Lee, Chem. Mater., 2009, 21, 3210–3214 CrossRef CAS.
- J. W. Zheng, S. M. L. Nai, M. Gupta, P. Saha, K. Kadakia, S. K. Park and P. N. Kumta, J. Phys. Chem. C, 2009, 113, 14015–14019 CAS.
- W.-J. Zhang, M. F. Ng, P. Wu, J. Wei and M. Gupta, J. Power Sources, 2011, 196, 13–17 CrossRef CAS.
- M. K. Datta, R. Epur, P. Saha, K. Kadakia, S. K. Park and P. N. Kumta, J. Power Sources, 2013, 225, 316–321 CrossRef CAS.
- M. N. Obrovac, L. Christensen, D. B. Le and J. R. Dahnb, J. Electrochem. Soc., 2007, 154, A849–A853 CrossRef CAS.
- V. L. Chevrier and G. Ceder, J. Electrochem. Soc., 2011, 158, A1011 CrossRef CAS.
- Y. H. Liu, Y. H. Xu, Y. J. Zhu, J. N. Culver, C. A. Lundgren, K. Xu and C. S. Wang, ACS Nano, 2013, 7, 3627–3634 CrossRef CAS PubMed.
- X. Q. Xie, K. Kretschmer and J. Zhang, Nano Energy, 2015, 13, 208–217 CrossRef CAS.
- H. S. Hou, X. N. Tang and M. Q. Guo, Mater. Lett., 2014, 128, 408–411 CrossRef CAS.
- P. R. Abel, Y.-M. Lin and T. D. Souza, J. Phys. Chem. C, 2013, 117, 18885–18890 CAS.
- D.-H. Nam, K.-S. Hong, S.-J. Lim, T.-H. Kim and H.-S. Kwon, J. Phys. Chem. C, 2014, 118, 20086–20093 CAS.
- Y. Y. Cheng, J. F. Huang, R. Z. Li, Z. W. Xu, L. Y. Cao, H. B. Ouyang, J. Y. Li, H. Qi and C. W. Wang, Electrochim. Acta, 2015, 180, 227–233 CrossRef CAS.
- W. Chen, Z. L. Fan and C. L. Wang, Chem. Commun., 2010, 46, 3905–3911 RSC.
- D.-H. Nam, T.-H. Kim and H.-S. Kwon, ACS Nano, 2014, 8, 11824–11835 CrossRef CAS PubMed.
- Y. Kim, K.-H. Ha and K. T. Lee, Chem.–Eur. J., 2014, 20, 11980–11992 CrossRef CAS PubMed.
- X. Yang, R. Y. Zhang and N. Chen, Chem.–Eur. J., 2016, 22, 1445–1451 CrossRef CAS PubMed.
- Y. C. Liu, N. Zhang and J. Chen, Adv. Mater., 2015, 27, 6702–6707 CrossRef CAS PubMed.
- X. Q. Xie, K. Kretschmer and B. Sun, Nano Energy, 2015, 13, 208–217 CrossRef CAS.
- Y. C. Liu, N. Zhang and J. Chen, Adv. Funct. Mater., 2015, 25, 214–220 CrossRef CAS.
- K. H. Dai, H. Zhao, Z. H. Wang, X. Y. Song, V. Battaglia and G. Liu, J. Power Sources, 2014, 263, 276–279 CrossRef CAS.
- H. L. Zhu, Z. Jia, Y. C. Chen, N. Weadock, J. Y. Wan, O. Vaaland, X. G. Han, T. Li and L. B. Hu, Nano Lett., 2013, 13, 3093–3100 CrossRef CAS PubMed.
- W. J. Li, S.-L. Chou, J.-Z. Wang, J. H. Kim, H.-K. Liu and S.-X. Dou, Adv. Mater., 2014, 26, 4037–4042 CrossRef CAS PubMed.
- J. Zhu and D. Deng, J. Phys. Chem. C, 2015, 119, 21323–21328 CAS.
- P. R. Abel, M. G. Fields, A. Heller and C. B. Mullins, ACS Appl. Mater. Interfaces, 2014, 6, 15860–15867 CAS.
- M. G. Wang, J. Han, H. X. Xiong and R. Guo, Langmuir, 2015, 31, 6220–6228 CrossRef CAS PubMed.
- J. Liu, Y. R. Wen, J. Maier and Y. Yu, Nano Lett., 2014, 14, 6387–6392 CrossRef CAS PubMed.
- M. Dahbi, N. Yabuuchi, K. Kubota, K. Tokiwa and S. Komaba, Phys. Chem. Chem. Phys., 2014, 16, 15007–15028 RSC.
- A. Darwiche, M. T. Sougrati, B. Fraisse, L. Stievano and L. Monconduit, J. Am. Chem. Soc., 2012, 134, 20805–20811 CrossRef CAS PubMed.
- M. He, K. Kravchyk and M. Walter, Nano Lett., 2014, 14, 1255–1262 CrossRef CAS PubMed.
- Y. Zhu, X. Han, Y. Xu, Y. Liu and S. Zheng, ACS Nano, 2013, 7, 6378–6386 CrossRef CAS PubMed.
- Z. A. Zhang, X. X. Zhao and J. Li, Electrochim. Acta, 2015, 176, 1296–1301 CrossRef CAS.
- I. T. Kim, E. Allcorn and A. Manthiram, J. Power Sources, 2015, 281, 11–17 CrossRef CAS.
- I. T. Kim, S.-O. Kim and A. Manthiram, J. Power Sources, 2014, 269, 848–854 CrossRef CAS.
- L. W. Ji, M. Gu, Y. Y. Shao, X. L. Li, M. H. Engelhard, B. W. Arey, W. Wang, Z. M. Nie, J. Xiao, C. M. Wang, J.-G. Zhang and J. Liu, Adv. Mater., 2014, 26, 2901–2908 CrossRef CAS PubMed.
- L. W. Ji, W. D. Zhou, V. Chabot, A. P. Yu and X. C. Xiao, ACS Appl. Mater. Interfaces, 2015, 7, 24895–24901 CAS.
- J. Park, J.-W. Park, J.-H. Han, S.-W. Lee, K.-Y. Lee, H.-S. Ryu, K.-W. Kim, G. X. Wang and J.-H. Ahn, Mater. Res. Bull., 2014, 58, 186–189 CrossRef CAS.
- Y. C. Lu, C. Ma, T. Kidera, J. Alvarado, T. Kidera, N. Dimov, Y. S. Meng and S. Okada, J. Power Sources, 2015, 284, 287–295 CrossRef CAS.
- M. D. Slater, D. Kim, E. Lee and C. S. Johnson, Adv. Funct. Mater., 2012, 8, 947–958 Search PubMed.
- Y. Wang, D. Su, C. Wang and G. Wang, Electrochem. Commun., 2013, 29, 8–11 CrossRef CAS.
- D. Su, H.-J. Ahn and G. Wang, Chem. Commun., 2013, 49, 3131–3133 RSC.
- Y. D. Zhang, J. Xie, S. C. Zhang, P. Y. Zhu, G. S. Cao and X. B. Zhao, Electrochim. Acta, 2015, 151, 8–15 CrossRef CAS.
- Y. Wang, D. W. Su, C. Y. Wang and G. X. Wang, Electrochem. Commun., 2013, 29, 298–311 Search PubMed.
- Y. H. Liu, X. Fang, M. Y. Ge, J. P. Rong, C. F. Shen, A. Y. Zhang, H. A. Enaya and C. W. Zhou, Nano Energy, 2015, 16, 399–407 CrossRef CAS.
- M. Dirican, Y. Lu, Y. Q. Ge, O. Yildiz and X. W. Zhang, ACS Appl. Mater. Interfaces, 2015, 7, 18387–18396 CAS.
- W. P. Sun, X. H. Rui, D. Yang, Z. Q. Sun, B. Li, W. Y. Zhang, Y. Zong, S. Madhavi, S. X. Dou and Q. Y. Yan, ACS Nano, 2015, 4, 11371–11381 CrossRef PubMed.
- P. K. Dutta, U. K. Sen and S. Mitra, RSC Adv., 2014, 4, 43155–43159 RSC.
- Y. D. Zhang, P. Y. Zhu, L. L. Huang, J. Xie, S. C. Zhang, G. S. Cao and X. B. Zhao, Adv. Funct. Mater., 2014, 25, 481–489 CrossRef.
- B. H. Qu, C. Z. Ma, G. Ji, C. H. Xu, J. Xu, Y. S. Meng, T. H. Wang and J. Y. Lee, Adv. Mater., 2014, 26, 3854–3859 CrossRef CAS PubMed.
- T. F. Zhou, W. K. Pang, C. F. Zhang, J. P. Yang, Z. X. Chen, H. K. Liu and Z. P. Guo, ACS Nano, 2014, 8, 8323–8333 CrossRef CAS PubMed.
- Z. F. Jiang, C. Wang, G. H. Du, Y. J. Zhong and J. Z. Jiang, J. Mater. Chem., 2012, 22, 9494–9496 RSC.
- X. Q. Xie, D. W. Su, S. Q. Chen, J. Q. Zhang, S. X. Dou and G. X. Wang, Chem.–Asian J., 2014, 9, 1611–1619 CrossRef CAS PubMed.
- J. W. Wang, X. H. Liu, S. X. Mao and J. Y. Huang, Nano Lett., 2012, 12, 5897–5902 CrossRef CAS PubMed.
- Y. J. Hong, J. W. Yoon, J. H. Lee and Y. C. Kang, Chem.–Eur. J., 2015, 21, 371–376 CrossRef CAS PubMed.
- Y. C. Liu, H. Y. Kang, L. F. Jiao, C. C. Chen, K. Z. Cao, Y. J. Wang and H. T. Yuan, Nanoscale, 2015, 7, 1325–1332 RSC.
- W. W. Xu, K. N. Zhao, L. Zhang, Z. Q. Xie, Z. Y. Cai and Y. Wang, J. Alloys Compd., 2016, 654, 357–362 CrossRef CAS.
- C. Ma, J. Xu, J. Alvarado, B. H. Qu, J. Somerville, J. Y. Lee and Y. S. Meng, Chem. Mater., 2015, 27, 5633–5640 CrossRef CAS.
- Y. D. Zhang, P. Y. Zhu, L. L. Huang, J. Xie, S. C. Zhang, G. S. Cao and X. B. Zhao, Adv. Funct. Mater., 2015, 25, 481–489 CrossRef CAS.
- B. H. Qu, C. Ma, G. Ji, C. H. Xu, J. Xu, Y. S. Meng, T. H. Wang and J. Y. Lee, Adv. Mater., 2014, 26, 3854–3859 CrossRef CAS PubMed.
- J. J. Wang, C. Luo, J. F. Mao, Y. J. Zhu, X. L. Fan, A. C. Mignerey and C. S. Wang, ACS Appl. Mater. Interfaces, 2015, 7, 11476–11481 CAS.
- S. L. Liu, H. Z. Zhang, L. Q. Xu, L. B. Ma and X. X. Chen, J. Power Sources, 2016, 304, 346–353 CrossRef CAS.
- Y. J. Kim, Y. Kim, A. Choi, S. Woo, D. Mok, N.-S. Choi, Y. S. Jung, J. H. Ryu, S. M. Oh and K. T. Lee, Adv. Mater., 2014, 26, 4139–4144 CrossRef CAS PubMed.
- Y. Kim, Y. Park, A. Choi, N.-S. Choi, J. Kim, J. Lee, J. H. Ryu, S. M. Oh and K. T. Lee, Adv. Mater., 2013, 25, 3045–3050 CrossRef CAS PubMed.
- J. Qian, X. Wu, Y. Cao, X. Ai and H. Yang, Angew. Chem., Int. Ed., 2013, 52, 4633–4638 CrossRef CAS PubMed.
- Y. J. Kim, Y. Kim, A. Choi, S. Woo, D. Mok, N.-S. Choi, Y. S. Jung, J. H. Ryu, S. M. Oh and K. T. Lee, Adv. Mater., 2014, 26, 4139–4144 CrossRef CAS PubMed.
- J. F. Qian, Y. Xiong, Y. L. Cao, X. P. Ai and H. X. Yang, Nano Lett., 2014, 14, 1865–1869 CrossRef CAS PubMed.
- T. Honma, T. Togashi, H. Kondo, T. Komatsu, H. Yamauchi, A. Sakamoto and T. Sakai, APL Mater., 2013, 052101–052103 CrossRef.
- J.-C. Kim and D.-W. Kim, Electrochem. Commun., 2014, 46, 124–127 CrossRef CAS.
- J. F. Qian, Y. Xiong and Y. L. Cao, Nano Lett., 2014, 14, 1865–1869 CrossRef CAS PubMed.
- X. Q. Meng, M. Zhou, X. L. Li, J. Y. Yao, F. L. Liu, H. C. He, P. Xiao and Y. H. Zhang, Electrochim. Acta, 2013, 109, 20–26 CrossRef CAS.
- X. Q. Meng, M. Zhou and X. L. Li, Electrochim. Acta, 2013, 109, 20–26 CrossRef CAS.
- S. N. Pusawale, P. R. Deshmukh and C. D. Lokhande, Appl. Surf. Sci., 2011, 257, 9498–9502 CrossRef CAS.
- S. Y. Wang, S. P. Jiang and X. Wang, Electrochim. Acta, 2011, 56, 3338–3344 CrossRef CAS.
- R. K. Selvan, I. Perelshtein, N. Perkas and A. Gedanken, J. Phys. Chem. C, 2008, 112, 1825–1830 CAS.
- S. P. Lim, N. M. Huang and H. N. Limb, Ceram. Int., 2013, 39, 6647–6655 CrossRef CAS.
- Y. Wang, Z. Shi, Y. Huang, Y. Ma, C. Wang, M. Chen and Y. Chen, J. Phy. Chem. C, 2009, 113, 13103–13107 CrossRef CAS.
- C. Liu, Z. Yu, D. Neff, A. Zhamu and B. Z. Jang, Nano Lett., 2010, 10, 4863–4868 CrossRef CAS PubMed.
- T. Y. Kim, H. W. Lee, M. Stoller, D. R. Dreyer, C. W. Bielawski, R. S. Ruoff and K. S. Suh, ACS Nano, 2011, 5, 436–442 CrossRef CAS PubMed.
- M. D. Stoller, S. Park, Y. Zhu, J. An and R. S. Ruoff, Nano Lett., 2008, 8, 3498–3502 CrossRef CAS PubMed.
- S. Wang, S. P. Jiang and X. Wang, Electrochim. Acta, 2011, 56, 3338–3344 CrossRef CAS.
- Y. K. Wang, Y. S. Liu and J. M. Zhang, J. Nanopart. Res., 2015, 17, 420–424 CrossRef.
- F. Li, J. Song, S. Gan, S. Gan, Q. Zhang, D. Han and L. N. A. Ivaska, Nanotechnology, 2009, 20, 455602 CrossRef PubMed.
- S. P. Lim, N. M. Huang and H. N. Limb, Ceram. Int., 2013, 39, 6647–6655 CrossRef CAS.
- S. Y. Wang, S. P. Jiang and X. Wang, Electrochim. Acta, 2011, 56, 3338–3344 CrossRef CAS.
- R. K. Selvan, I. Perelshtein and A. Gedanken, J. Phys. Chem. C, 2008, 112, 1825–1830 CAS.
- F. Su, C. K. Poh, J. S. Chen, G. Xu, D. Wang, Q. Li, J. y. Lin and X. W. Lou, Energy Environ. Sci., 2011, 4, 717–724 CAS.
- H. Ren, J. j. Sun, R. b. Yu, M. Yang, L. Gu, P. Liu, H. j. Zhao, D. Kisailuse and D. Wang, Chem. Sci., 2016, 7, 793–798 RSC.
- P. Manivel, S. Ramakrishnan, N. K. Kothurkar, A. Balamurugan, N. Ponpandian, D. Mangalaraj and C. Viswanathan, Mater. Res. Bull., 2013, 48, 640–645 CrossRef CAS.
- Z.-A. Hu, Y.-L. Xie, Y.-X. Wang, L.-P. Mo, Y.-Y. Yang and Z.-Y. Zhang, Mater. Chem. Phys., 2009, 114, 990–995 CrossRef CAS.
- J. Du, X. y. Lai, N. l. Yang, J. Zhai, D. Kisailus, F. B. Su, D. Wang and L. Jiang, ACS Nano, 2011, 5, 590–596 CrossRef CAS PubMed.
- Y. H. Jin and M. Q. Jia, Colloids Surf., A, 2015, 464, 17–25 CrossRef CAS.
- S. Trasatti, Parts A & B, Elsevier, 1980 Search PubMed.
- S.-M. Lin and T.-C. Wen, J. Appl. Electrochem., 1993, 23, 487–492 CAS.
- S. Ferro and A. D. Battisti, J. Phys. Chem. B, 2002, 106, 2249–2252 CrossRef CAS.
- C.-C. Wang and C.-C. Hu, J. Electrochem. Soc., 2005, 152, A370–A375 CrossRef CAS.
- J. Han, M. G. Wang, R. Chen, N. Han and R. Guo, Chem Commun, 2014, 50, 8295–8298 RSC.
- X. Y. Lai, J. Li, B. A. Korgel, Z. H. Dong, Z. m. Li, F. b. Su, J. Du and D. Wang, Angew. Chem., Int. Ed., 2011, 50, 2738–2741 CrossRef CAS PubMed.
- D. Mao, J. Yao, X. Y. Lai, M. Yang, J. Du and D. Wang, Small, 2011, 5, 578–582 CrossRef PubMed.
- C.-C. Wang and C.-C. Hu, Electrochim. Acta, 2005, 50, 2573–2581 CrossRef CAS.
- I. Shakir, M. Shahid and D. J. Kang, Electrochim. Acta, 2012, 72, 134–137 CrossRef CAS.
- Y. Q. Zhang and Y. Mo, Electrochim. Acta, 2014, 142, 76–83 CrossRef CAS.
- C. S. Ferreira, R. R. Passos and L. A. Pocrifka, J. Power Sources, 2014, 271, 104–107 CrossRef CAS.
- Z. Qin, Z. J. Li and R. A. Outlaw, J. Power Sources, 2012, 3, 303–308 CrossRef.
- D. P. Dubal, S. V. Patil and C. D. Lokhande, J. Alloys Compd., 2012, 552, 240–247 CrossRef.
- F. Cao, Y. Liu and J. Yuan, Electrochim. Acta, 2012, 81, 1–7 CrossRef CAS.
- H. Liu, Y. Wang and Y. Ding, Mater. Sci. Eng., B, 2013, 178, 293–298 CrossRef CAS.
- C. Fu, H. Zhou and Y. Kuang, Mater. Chem. Phys., 2012, 132, 596–600 CrossRef CAS.
- F. C. Cebeci, E. Sezer and A. S. Sarac, Electrochim. Acta, 2009, 54, 6354–6360 CrossRef CAS.
- J. E. Benedetti, S. C. Canobre and S. Neves, Electrochim. Acta, 2007, 52, 4734–4741 CrossRef CAS.
- G. P. Pandey and A. C. Rastogi, Electrochim. Acta, 2013, 87, 158–168 CrossRef CAS.
|
This journal is © The Royal Society of Chemistry 2016 |
Click here to see how this site uses Cookies. View our privacy policy here.