DOI:
10.1039/C6RA18228C
(Paper)
RSC Adv., 2016,
6, 80262-80267
Preparation of AlN microspheres/UHMWPE composites for insulating thermal conductors
Received
18th July 2016
, Accepted 18th August 2016
First published on 18th August 2016
Abstract
AlN microspheres were prepared by applying both sol–gel technique and gas reduction nitridation, and then modified by 3-aminopropyltriethoxysilane (KH550) to increase the affinity with the polymer. The KH550 modified AlN microspheres/UHMWPE composites were fabricated by solution mixing and hot pressing technique. Their microstructure, thermal stability, thermal conductivity and dielectric properties were investigated. The AlN microspheres/UHMWPE composite demonstrated much higher thermal conductivity in comparison with the commercial AlN particles/UHMWPE composite. The dielectric constant and dielectric loss of the KH550 modified AlN microspheres/UHMWPE composites increased slightly with increasing AlN content. The KH550 modified AlN microspheres/UHMWPE composites still had a high surface resistivity (>1014 Ω m) and volume resistivity (>1015 Ω m).
1. Introduction
In the past decade, polymeric matrixes have drawn much interest because of their low cost, low density, ease of processing, electrical insulating properties and chemical inertia.1,2 With the miniaturization of microelectronics in modern information industry, it is necessary to develop new generation polymer composites with high thermal conductivity, low dielectric constant and dielectric loss, and excellent electrical insulation when they are used in circuit boards, heat exchangers, substrates, and electronic packaging.3–6 Traditional polymers such as polyethylene (PE), polypropylene (PP) and polyamide (PA) are excellent electrical insulators with low thermal conductivity of only about 0.2 W mK−1, which is far from the needs to effectively dissipate heat. It is therefore highly desirable to increase the thermal conductivity of the traditional polymer.7
The most commonly method applied to develop high thermal conductive polymer composites is to introduce a highly thermally conductive component, such as oxides (Al2O3,8 SiO2,9 ZnO10 and MgO11), carbides (SiC12,13), nitrides (AlN,14,15 BN16,17 and SiN18).19 However, a high loading of fillers (>60 wt%) is required to achieve a high thermal conductivity, which in return deteriorates the mechanical and processing properties of the composites.12 It has been found that a segregated structure is beneficial to lower the thermally conductive percolation threshold which plays a significant role in the enhancement of thermal conductivity. In a segregated conductive network, thermally conductive fillers are located on the interface of the polymer matrix particles instead of being randomly distributed in the whole system, which results in the thermally conductive network and pathway formed at low loading.20,21 Hu et al. found that PP/AlN composites with segregated structure showed more than 20% higher thermal conductivity than composites with random distribution.22
According to the heat transfer mechanism of lattice vibration, a highly crystalline polymer is beneficial to increase the thermal conductivity of composites such as liquid crystal polymer (LCP), high-density polyethylene (HDPE), ultra-high molecular weight polyethylene (UHMWPE).3,23,24 UHMWPE is one of the promising matrix due to its high wear resistance, low friction coefficient, high chemical stability, non-toxic and self-lubricating properties, which has great applications in the fields of medical, mining, oil, textile chemical, the aerospace industry.5,25 Aluminium nitride (AlN) has evoked considerable interest owing to its high thermal conductivity, low dielectric constant, high electrical resistance, chemical inertness.15,19,23,26,27 So far, various low-dimensional AlN materials such as nanowires, nanorods, nanoplates and nanowhiskers used as thermally conductive fillers have been reported.28 However, there are very few reports on spherical AlN particles applied to the conductive fillers. Generally, spherical AlN particles exhibit brilliant dispersity and packing density in polymer matrix, which can aid in the formation of particle networks and pathways.29,30 Moreover, thermally conductive polymer composites filled with spherical AlN particles will show isotropy in space domain. In this study, we proposed a method for synthesis of AlN microspheres by applying both sol–gel technique and gas reduction nitridation, and constructed UHMWPE composites filled with the KH550 modified AlN microspheres.31–33 The KH550 modified AlN microspheres/UHMWPE composites demonstrated a much higher thermal conductivity than that of the commercial AlN particles/UHMWPE composites. The thermal stability, thermal conductivity, dielectric properties and electrical insulation of AlN microspheres/UHMWPE composites were also described.
2. Experimental
2.1. Reagents
Poly(ethylene glycol)-block-poly(propylene glycol)-block-poly(ethylene glycol) (F127, Mn ∼ 14
600), 3-aminopropyltriethoxysilane (KH550, 98%) and commercial aluminium nitride (AlN 99.5%) were purchased from Aladdin. Aluminum chloride hexahydrate (AlCl3·6H2O, AR), ethanol (AR), propylene oxide (PO, AR) and acetone (AR) were purchased from Sinopharm Chemical Reagent Co., Ltd. Ultra-high molecular weight polyethylene (UHMWPE) powder (0.97 g cm−3, mean particle size of 60 μm) was supplied by Nanjing Deyuan Science and Technology Co. Ltd. All reagents were used for the synthesis without further purification.
2.2. Synthesis of AlN microspheres
In a typical procedure for the synthesis of AlN microspheres, the aluminum chloride hexahydrate (500 g) was dissolved in a mixed solvent which consist of distilled water (460 ml), ethanol (635 ml) and F127 (80 g) in a large beaker with mechanical stirring. When aluminum chloride hexahydrate is completely dissolved, propylene oxide (900 ml) was poured into the solution quickly to initiate the condensation reaction and followed by continuing vigorous stirring for 15 seconds. After 32 seconds' standing, the transparent solution turned into a white cream-like gel quite rapidly. Subsequently, the wet gel was dried at 80 °C to get a white fine and smooth powders. The powders were heat treated at 500 °C for 2 h in air to wipe off carbon and then heat treated at 1300 °C for 2 h under flowing NH3 (5000 sccm) in a tube furnace to obtain AlN microspheres.
2.3. Surface modification of AlN microspheres
The surface modification of the AlN microspheres with the silane coupling agent involved the following steps:34,35 (a) dissolving 53 μl 3-aminopropyltriethoxysilane (KH550, 1 wt% of the AlN microspheres) in 15 ml acetone; (b) 5 g AlN microspheres and 0.2 g water was added to the solution and stirring for 10 min; (c) heating the mixture to 70 °C, refluxing it for 4 h while stirring; (d) rinsing the mixture with ethanol by filtration at least three times; (e) drying the mixture at 100 °C to remove the solvent to obtain the KH550 modified AlN microspheres.
2.4. Preparation of AlN microspheres/UHMWPE composites
The AlN microspheres were fed into the acetone to form a suspension, and then the intense dispersion process was achieved using ultrasonication for 60 min and followed by magnetic stirring for 60 min before the UHMWPE was added into the suspension. After mixing with UHMWPE powders under ultrasonication and stirring for 2 h, the acetone was completely evaporated. The mixtures of UHMWPE powders and AlN microspheres are obtained. Subsequently, the mixtures were compression-molded into a stainless steel die at 200 °C and 12.7 MPa after preheating for 4 min. The resulting AlN microspheres/UHMWPE composites were cooled to room temperature by cold compression molding for 3 min.
2.5. Characterization
FE-SEM (S-4800, Hitachi, Japan) was used to observe the morphology of the samples. XRD analysis was carried out on PANalytical B.V. Empyrean 200895 X-ray diffractometer with Cu Kα radiation (λ = 1.54 Å), and scan speed was 2.00 deg per min. Thermo gravimetric analysis (TG) was used to evaluate the weight loss of composites and surface treated AlN microspheres, using TA Q500 thermal analyzer. Differential scanning calorimetry analysis (DSC) was carried out under N2 atmosphere, using TA Q200 thermal analyzer. 5–7 mg samples were first heated up to 100 °C to remove water and then cooled to 30 °C. The samples were reheated from 30 to 170 °C at 10 °C min−1 and held isotherm at 170 °C for 3 min. Fourier-transform infrared spectrometry (FTIR) was conducted on a Nicolet iS5 FTIR spectrometer over the range of 4000–400 cm−1. The analysis to the change in the environment of N atom was performed by X-ray photoelectron spectroscopy (XPS, ESCALAB). The thermal conductivity λ was calculated by using λ = ρ × δ × CP, where ρ is the sample density estimated by drainage method using Mettler Toledo AL/AB-N Balance, δ the thermal diffusivity and CP the specific heat of the sample which was determined with Netzsch LFA-427 on cylindrical samples (1 mm thickness, 12.7 mm in diameter) according to ASTM E1461. The measurement of dielectric properties were performed using a broadband dielectric spectrometer (Turnkey Concept 50, Novocontrol Technologies GmbH & Co. KG, Hundsangen, Germany) in a frequency range of 101 to 106 Hz. All of the samples have a layer of gold evaporated on both surfaces to serve as electrodes. The volume resistivity and surface resistivity were measured on ultrahigh electric resistor (ZC36, Shanghai Anbiao Electronic Co., LTD, China), and the applied voltage to the test samples was 250 V.
3. Results and discussion
Fig. 1a shows the XRD patterns of the AlN microspheres. The diffraction peaks could be indexed in accord with wurtzite-structured phase AlN (JCPDS files number 70-2545). The AlN microspheres illustrated higher degree of crystallinity, and no Al2O3 impurity peak can be observed. Fig. 1b shows the SEM images of the AlN precursors with regular spherical morphology. After nitridation, the regular spherical morphology still remained and the diameter of the microspheres decreased to about 2 μm (Fig. 1c). Moreover, the synthesized AlN microspheres have the more regular shape than the commercial AlN particles (Fig. 1d).
 |
| Fig. 1 (a) XRD patterns of the synthesized AlN microspheres and commercial AlN particles. SEM images of (b) AlN precursor, (c) synthesized AlN microspheres, (d) commercial AlN particles. | |
It is important for the composites to enhance the dispersion and integration between the inorganic particles and the polymer matrix, and the surface modification of the particles by silane coupling agents is a useful method to improve the dispersion of particles in matrix.36 Fig. 2 shows the FTIR spectra and TGA curves of the AlN microspheres and the KH550 modified AlN microspheres. The KH550 modified AlN microspheres presents additional absorption at 1100 cm−1, 1460 cm−1, 2852 cm−1 and 2920 cm−1, which could be attributed to the Si–O stretching, –NH shear vibration, symmetric and asymmetric –CH2– stretching vibrations respectively. Thermal gravimetric analysis (TGA) was further used to demonstrate the modification of AlN microspheres.37 From Fig. 2b it can be found that the KH550 modified AlN microspheres had a higher weight loss than the AlN microspheres at 300–800 °C, which could be attributed to the decomposition of the silane agent. To obtain more evidence about the modification of AlN, XPS was applied to analyze the change in the environment of N atom. As shown in Fig. 2c, the N 1s spectrum of the KH550 modified AlN can be divided to two peaks (397.5 eV and 400.1 eV). The binding energy peak at 397.5 eV corresponding to N–Al bonds is stronger than that at 400.1 eV corresponding to –CH2–NH2 bonds.38 Fig. 3 shows the SEM images of the AlN microspheres/UHMWPE composites and the KH550 modified AlN microspheres/UHMWPE composites. It is obvious that the surface modification of the AlN microspheres can improve the compatibility and interfacial adhesion between the AlN microspheres and polymer matrix.35
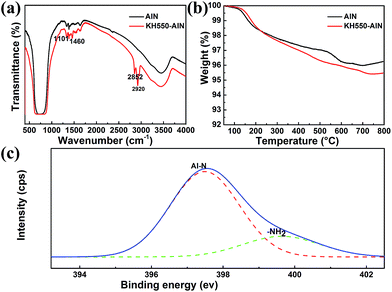 |
| Fig. 2 (a) FTIR spectra and (b) TGA curves of AlN microspheres and KH550 modified AlN microspheres. (c) XPS (N 1s) spectrum of KH550 modified AlN microspheres. | |
 |
| Fig. 3 SEM images of (a) AlN microspheres/UHMWPE and (b) KH550 modified AlN microspheres/UHMWPE composites (AlN/UHMWPE = 40/60, weight percentage ratio). | |
Fig. 4 shows DSC analyses of the pure UHMWPE and the KH550 modified AlN microspheres/UHMWPE composites. Corresponding data obtained from the DSC curves are summarized in Table 1. Herein, Tm is the temperature of peak point (melting temperature). The crystallinity (Xc) of the UHMWPE was calculated according to eqn (1)
|
 | (1) |
where
x is volume fraction of filler, Δ
Hm specific melting enthalpy of UHMWPE and Δ
Hm100 specific melting enthalpy for 100% crystalline polyethylene, which is set as 289.3 J g
−1 for this calculation.
39 The AlN content had slightly influence on the melting temperature of the UHMWPE, and the melting temperature is decreased from 137.04 °C (pure UHMWP) to 133.05 °C (60 wt% AlN).
 |
| Fig. 4 DSC analyses of UHMWPE and KH550 modified AlN microspheres/UHMWPE composites. (a) Melting process, and (b) crystallizing process. | |
Table 1 DSC data of UHMWPE and KH550 modified AlN microspheres/UHMWPE composites
AlN/UHMWPE (w/w) |
ΔHm (J g−1) |
Tm (°C) |
Xc (%) |
0/100 |
157.83 |
137.04 |
54.55 |
10/90 |
142.28 |
136.73 |
50.75 |
20/80 |
129.07 |
136.08 |
47.83 |
30/70 |
119.37 |
134.45 |
46.36 |
40/60 |
104.13 |
135.17 |
42.91 |
50/50 |
100.26 |
134.02 |
44.65 |
60/40 |
95.58 |
133.05 |
47.33 |
From Table 1 it can be found that the incorporation of the AlN microspheres affected the crystallinity (Xc) of the UHMWPE. The crystallinity of the UHMWPE decreased with increasing AlN microspheres, which indicated that the AlN microspheres could inhibit the formation of large crystalline domains of UHMWPE because AlN microspheres were filled in the interlamellar space of UHMWPE.40
Thermal stability of the composites is one of the critical properties for the composites in processing and practical application.1,41 Fig. 5 shows the TGA and DTG results of the KH550 modified AlN microspheres/UHMWPE composites. The thermal stability of the KH550 modified AlN microspheres/UHMWPE composites slightly shifted to higher temperature with increasing content of the AlN microspheres, which can be ascribed to the higher heat capacity and thermal conductivity of the AlN microspheres. Herein AlN microspheres acted as barriers to delay the formation and escape of volatile byproducts during the pyrolysis.
 |
| Fig. 5 (a) TGA and (b) DTG curves of UHMWPE and KH550 modified AlN microspheres/UHMWPE composites. | |
Fig. 6a and b show the dependence of the thermal conductivity and thermal conductivity enhancement on the AlN contents for the KH550 modified AlN microspheres/UHMWPE composites and the commercial AlN particles/UHMWPE composites. Similar to the commercial AlN particles/UHMWPE composites, the thermal conductivity of the KH550 modified AlN microspheres/UHMWPE composites gradually increased with an increase of AlN content. When the AlN contents was more than 30 wt%, however, the thermal conductivity of the KH550 modified AlN microspheres/UHMWPE composites demonstrated a significant enhancement, which could be attributed to the dispersion state of AlN microspheres in UHMWPE matrix. When AlN contents were lower, the AlN microspheres were distributed separately (light grey regions in Fig. 6c) and wrapped by polymer without direct contact, thus the thermal resistance between AlN microspheres was very large. With increase of the AlN contents, the AlN microspheres would contact each other and thermally conductive AlN networks were formed at the interfaces among the UHMWPE particles in the AlN/UHMWPE composites (light grey regions in Fig. 6d and e), which would result in significant increase of the thermal conductivity. It is obvious that the AlN microspheres were much more effective in enhancing the thermal conductive of the composites than that of the commercial AlN particles. Therefore, the AlN microspheres were beneficial to pack and form a compact three-dimensional thermally conductive channels and networks in the matrix compared with commercial AlN particles.
 |
| Fig. 6 Dependence of (a) thermal conductivity and (b) thermal conductivity enhancement on AlN contents for KH550 modified AlN microspheres/UHMWPE composites and commercial AlN particles/UHMWPE composites. SEM images of KH550 modified AlN microspheres/UHMWPE composites, (c) 10 wt% AlN microspheres; (d) 30 wt% AlN microspheres; (e) 60 wt% AlN microspheres. | |
The dielectric constant and dielectric loss are also the crucial properties to insulating thermal conductive composites. Fig. 7a shows the frequency dependence of the dielectric constants of the KH550 modified AlN microspheres/UHMWPE composites. The dielectric constant of the composites decreased slightly with increasing frequency and AlN contents. The former indicated that the interfacial dipoles have less time to orient themselves in the direction of the alternating field at high frequency, and the latter, dielectric constant enhancement, can be ascribed to the interfacial polarization effect because of the space charge accumulation at the interface.42,43 Fig. 7b shows the frequency dependence of the dielectric loss of the KH550 modified AlN microspheres/UHMWPE composites. It can be found that the dielectric loss decreased with the frequency at low frequencies and increased with the frequency at high frequencies. This is because the interfacial polarization effect plays a crucial role at low frequencies and the dipolar relaxation of the UHMWPE exerts main influence at high frequency.1,44 It is obvious that the KH550 modified AlN microspheres/UHMWPE composites possessed a very low dielectric constant and dielectric loss in the measured frequency range from 10 to 106 Hz, which is very important for the application as plastic packaging and electronic substrate.
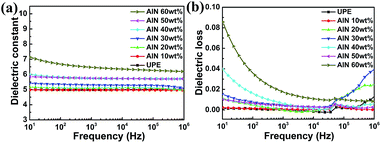 |
| Fig. 7 Frequency dependence of (a) dielectric constant and (b) dielectric loss of KH550 modified AlN microspheres/UHMWPE composites. | |
Fig. 8 shows dependence of the surface resistivity and volume resistivity on the AlN contents for the KH550 modified AlN microspheres/UHMWPE composites. Both surface resistivity and volume resistivity decreased with the increase of the AlN content. The surface resistivity were in the range from 6.41 × 1016 to 8.97 × 1014 Ω m, and the volume resistivity were in the range from 3.5 × 1016 to 1.13 × 1015 Ω m. The decrease of the surface resistivity and volume resistivity with increasing AlN content may be attributed to lower electric resistivity of the AlN in comparison with the UHMWPE. However, it is obvious that the KH550 modified AlN microspheres/UHMWPE composites still demonstrated excellent electrical insulation properties which contributed to the application of electrical insulating field.
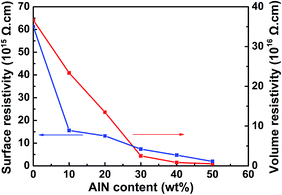 |
| Fig. 8 Dependence of surface resistivity and volume resistivity on AlN contents for KH550 modified AlN microspheres/UHMWPE composites. | |
4. Conclusions
AlN microspheres were successfully prepared by applying both sol–gel technique and gas reduction nitridation and then the KH550 modified AlN microspheres/UHMWPE composites were fabricated by solution mixing and hot pressing technique. The AlN microspheres/UHMWPE composites demonstrated much higher thermal conductivity in comparison with the commercial AlN particles/UHMWPE composites. The introduction of the AlN microspheres results in slightly decrease in melting temperature and degree of crystallinity of UHMWPE, which indicated an improved thermal stability. The dielectric constant and dielectric loss of the KH550 modified AlN microspheres/UHMWPE composites increased slightly with increasing AlN contents, but it still remained at a low level in the frequency range from 101 to 106 Hz. Moreover, the KH550 modified AlN microspheres/UHMWPE composites still remained higher surface resistivity (>1014 Ω m) and volume resistivity (>1015 Ω m).
Acknowledgements
The authors gratefully acknowledge support for this research from the Program for Innovative Research Team in University of Ministry of Education of China (IRT13R54) and the Fundamental Research Funds for the Central Universities (+2016FZA4007).
Notes and references
- W. Zhou, Thermochim. Acta, 2011, 512, 183–188 CrossRef CAS.
- Z. Gao and L. Zhao, Mater. Des., 2015, 66, 176–182 CrossRef CAS.
- J. Gu, N. Li, L. Tian, Z. Lv and Q. Zhang, RSC Adv., 2015, 5, 36334–36339 RSC.
- Y. Zhou, H. Wang, L. Wang, K. Yu, Z. Lin, L. He and Y. Bai, Mater. Sci. Eng., B, 2012, 177, 892–896 CrossRef CAS.
- J. Gu, Y. Guo, Z. Lv, W. Geng and Q. Zhang, Composites, Part A, 2015, 78, 95–101 CrossRef CAS.
- W. Zhou, S. Qi, H. Li and S. Shao, Thermochim. Acta, 2007, 452, 36–42 CrossRef CAS.
- T. Liu, J. Li, X. Wang, Z. Deng, X. Yu, A. Lu, F. Yu and J. He, J. Thermoplast. Compos. Mater., 2013, 28, 32–45 CrossRef.
- Y. Hu, G. Du and N. Chen, Compos. Sci. Technol., 2016, 124, 36–43 CrossRef CAS.
- J. Zeng, R. L. Fu, Y. Shen, H. He and X. F. Song, J. Appl. Polym. Sci., 2009, 113, 2117–2125 CrossRef CAS.
- M. M. Hossain, H. Shima, M. A. Islam, M. Hasan and M. Lee, RSC Adv., 2016, 6, 4683–4694 RSC.
- F. P. Du, W. Yang, F. Zhang, C. Y. Tang, S. P. Liu, L. Yin and W. C. Law, ACS Appl. Mater. Interfaces, 2015, 7, 14397–14403 CAS.
- Y. Hwang, M. Kim and J. Kim, Chem. Eng. J., 2014, 246, 229–237 CrossRef CAS.
- M. Parchovianský, D. Galusek, P. Švančárek, J. Sedláček and P. Šajgalík, Ceram. Int., 2014, 40, 14421–14429 CrossRef.
- N.-k. Gao, X. Yu, H.-y. Jin, B. He, P. Dong and C. Gao, IOP Conf. Ser.: Mater. Sci. Eng., 2011, 18, 82017–82020 CrossRef.
- Y. Zhou, Y. Yao, C. Y. Chen, K. Moon, H. Wang and C. P. Wong, Sci. Rep., 2014, 4, 4779 Search PubMed.
- X. Zhang, L. Shen, H. Wu and S. Guo, Compos. Sci. Technol., 2013, 89, 24–28 CrossRef CAS.
- Y. Wu, F. Li, J. Huyan, X. Zou and Y. Li, J. Appl. Polym. Sci., 2015, 132, 41951–41955 Search PubMed.
- G. Hou, B. Cheng, F. Ding, M. Yao, P. Hu and F. Yuan, ACS Appl. Mater. Interfaces, 2015, 7, 2873–2881 CAS.
- V. Onbattuvelli and S. Atre, Mater. Manuf. Processes, 2011, 26, 832–845 CrossRef CAS.
- H. Pang, L. Xu, D.-X. Yan and Z.-M. Li, Prog. Polym. Sci., 2014, 39, 1908–1933 CrossRef CAS.
- H. Deng, L. Lin, M. Ji, S. Zhang, M. Yang and Q. Fu, Prog. Polym. Sci., 2014, 39, 627–655 CrossRef CAS.
- M. Hu, J. Feng and K. M. Ng, Compos. Sci. Technol., 2015, 110, 26–34 CrossRef CAS.
- L. H. Sinh, J.-M. Hong, B. T. Son, N. N. Trung and J.-Y. Bae, Polym. Compos., 2012, 33, 2140–2146 CrossRef CAS.
- J. Jung, J. Kim, Y. R. Uhm, J.-K. Jeon, S. Lee, H. M. Lee and C. K. Rhee, Thermochim. Acta, 2010, 499, 8–14 CrossRef CAS.
- X. Wu, P. Jiang, Y. Zhou, J. Yu, F. Zhang, L. Dong and Y. Yin, J. Appl. Polym. Sci., 2014, 131, 40528–40538 Search PubMed.
- J. Wan, X. Qiao, L.-a. Wu, Y. Wu and X. Fan, J. Sol-Gel Sci. Technol., 2015, 76, 658–665 CrossRef CAS.
- Y. Chen, W. He, G. Zhou, Y. Hu, S. Wang and Z. Tao, Polym. Int., 2014, 63, 546–551 CrossRef CAS.
- H. M. Lee, K. Bharathi and D. K. Kim, Adv. Eng. Mater., 2014, 16, 655–669 CrossRef CAS.
- M. Kida, L. Weber, C. Monachon and A. Mortensen, J. Appl. Phys., 2011, 109, 064907 CrossRef.
- J.-P. Hong, S.-W. Yoon, T. Hwang, J.-S. Oh, S.-C. Hong, Y. Lee and J.-D. Nam, Thermochim. Acta, 2012, 537, 70–75 CrossRef CAS.
- Y. Xu and D. D. L. Chung, Compos. Interfaces, 2000, 7, 243–256 CrossRef CAS.
- H. Yu, L. Li, T. Kido, G. Xi, G. Xu and F. Guo, J. Appl. Polym. Sci., 2012, 124, 669–677 CrossRef CAS.
- C.-Y. Hsieh and S.-L. Chung, J. Appl. Polym. Sci., 2006, 102, 4734–4740 CrossRef CAS.
- S.-Y. Wu, Y.-L. Huang, C.-C. M. Ma, S.-M. Yuen, C.-C. Teng and S.-Y. Yang, Composites, Part A, 2011, 42, 1573–1583 CrossRef.
- S. Kango, S. Kalia, A. Celli, J. Njuguna, Y. Habibi and R. Kumar, Prog. Polym. Sci., 2013, 38, 1232–1261 CrossRef CAS.
- X. Huang, T. Iizuka, P. Jiang, Y. Ohki and T. Tanaka, J. Phys. Chem. C, 2012, 116, 13629–13639 CAS.
- J. Hou, G. Li, N. Yang, L. Qin, M. E. Grami, Q. Zhang, N. Wang and X. Qu, RSC Adv., 2014, 4, 44282–44290 RSC.
- Y.-N. Mi, G. Liang, A. Gu, F. Zhao and L. Yuan, Ind. Eng. Chem. Res., 2013, 52, 3342–3353 CrossRef CAS.
- W. Zhou, D. Yu, C. Min, Y. Fu and X. Guo, J. Appl. Polym. Sci., 2009, 112, 1695–1703 CrossRef CAS.
- S. Zhou, W. Luo, H. Zou, M. Liang and S. Li, J. Compos. Mater., 2015, 50, 327–337 CrossRef.
- X. Wu, Y. Wang, L. Xie, J. Yu, F. Liu and P. Jiang, Iran. Polym. J., 2012, 22, 61–73 CrossRef.
- Y. Li, X. Huang, Z. Hu, P. Jiang, S. Li and T. Tanaka, ACS Appl. Mater. Interfaces, 2011, 3, 4396–4403 CAS.
- L. Fang, W. Wu, X. Huang, J. He and P. Jiang, Compos. Sci. Technol., 2015, 107, 67–74 CrossRef CAS.
- W. Zhou and J. Cai, J. Appl. Polym. Sci., 2012, 124, 4346–4351 CrossRef CAS.
|
This journal is © The Royal Society of Chemistry 2016 |
Click here to see how this site uses Cookies. View our privacy policy here.