DOI:
10.1039/C6RA16030A
(Paper)
RSC Adv., 2016,
6, 80924-80933
Preparation of high encapsulation efficiency fragrance microcapsules and their application in textiles†
Received
21st June 2016
, Accepted 10th August 2016
First published on 11th August 2016
Abstract
Poly(1,4-butanediol dimethacrylate) microcapsules containing dementholized peppermint oil (DPO) were prepared by interfacial free-radical polymerization. The influence of the composition of the core material on the morphology of the fragrance microcapsules was investigated by scanning electron microscopy (SEM). Response surface methodology (RSM) was applied to optimize the effects of curing temperature, homogenization time, ratio of core/shell and homogenization rate on the encapsulation efficiency. The thermal stability of the fragrance microcapsules was studied by thermogravimetric analysis (TGA). The prepared fragrance microcapsule, under optimal conditions, possessed spherical shape, good thermal stability below 100 °C and high encapsulation efficiency of 91%. In addition, the fragrance microcapsules coated onto cotton fabric displayed good washing durability after 15 cycles, which will be beneficial for their future application in textiles, daily necessities and so on.
1. Introduction
Fragrance has numerous fantastic properties, such as hypnose, relieving anxiety, alleviating suffering, uplifting spirit, and improving work efficiency and has been widely used in our daily life.1–3 Fragrance is particularly useful as aromatic finishing agents for textile, such as aromatic therapy,4 antibacterial textiles5 and insecticide textile.6,7 In earlier days, physical absorption was a commonly used method for textile aromatic finishing, which involved the physical diffusion of fragrance molecules into the gaps between the fibers, impregnation with a solution containing fragrance and then coating by mixing the fragrance with the binder. However, these methods fail to survive one or two washing cycles. Microencapsulation is one of the latest technologies used in the fragrance field, which can embed the volatile fragrance inside a polymer membrane.8 In this way, the fragrance is physically isolated from the external environment, thus protecting the active agents against rapid evaporation, oxidization and contamination, and the isolation also allows controlled release. Numerous encapsulation techniques have been used to synthesize fragrance microcapsules, including spray drying,9 layer-by-layer deposition,10 phase separation11 and interface polymerization.12 The interfacial free-radical polymerization (IFRP) is a type of interface polymerization, which is considered to be an advantageous method to enable polymerization at the interface of oil/water.13 There are several reports about fragrance microcapsules synthesized by interface polymerization with two reactive monomers.14–16 However studies investigating fragrance microcapsules prepared by IFRP are rare, in which only one monomer is required. The advantage of having only one monomer is that the process is more economic and environmentally friendly, as cross-linking agents are not required.17,18 During the preparation process, the reactive monomer and initiator are in two different phases. The initiator triggers the polymerization of the monomer at the interface, which leads to a high loading capacity and high encapsulation efficiency. Microencapsulation techniques promote the wide use of fragrance microcapsules in aromatic finishing agents in textiles.19 Brisa Peña20 proposed microencapsulation of vanillin into a polysulfone (PSF) shell by phase inversion precipitation in textile, with a low encapsulation efficiency of 45%. During the preparation, they used N,N-dimethylformamide (DMF) to dissolve PSF, which introduced a toxic substance into the system. An Rye Lee21 used melamine-formaldehyde as a shell material to prepare microcapsules for textile applications, in which the residue monomer was toxic and the microcapsules had a low encapsulation efficiency of 80%. It is thus important to develop nontoxic and novel shell materials to fabricate fragrance microcapsules with a high encapsulation efficiency.
Additionally, in textile applications, the encapsulation efficiency of the core material is a major factor that should be taken into consideration.22,23 It is well-known that many factors affect the encapsulation efficiency during the preparation, such as the curing temperature, homogenization time, the ratio of shell/core and homogenization rate.24–26 However, it is expensive to obtain optimal conditions through conventional single factor experiments because various factors interact with each other. Response surface methodology (RSM) is widely used for studying the effects of several factors at different levels and their influences on each other, which can overcome the shortcomings of the traditional orthogonal method.27,28 Adane Tilahun Getachew et al.29 encapsulated coffee oil using polyethyleneglycol. And process parameters that affect the encapsulation efficiency such as temperature, pressure and polymer–oil ratios were optimized by RSM. Soheyla Honary et al.30 prepared nanoparticles by an ionotropic gelation method and optimized the encapsulation efficiency and particle size at different combinations of chitosan concentration, chitosan/tripolyphosphate mass and vancomycin/chitosan mass using RSM. Therefore, RSM could comprehensively reflect the relationships between encapsulation efficiency and those factors. The methodology gathers results more precisely and reduces the number of assays to optimize the process.31,32
In this paper, with excellent properties of refreshing aroma, anti-inflammatory behavior, and its use as an analgesic and spasmolysis applications, dementholized peppermint oil (DPO) was selected as a model fragrance. 1,4-Butanediol dimethacrylate (BDDMA), a commonly used crosslinker,33,34 was used individually to synthesize the shell of fragrance microcapsules. Poly(1,4-butanediol dimethacrylate) (PBDDMA) fragrance microcapsules with a high encapsulation efficiency and low toxicity were synthesized through the IFRP method. The paper offers a novel nontoxic shell material to synthesize fragrance microcapsules. The optimal condition to synthesize fragrance microcapsules with high encapsulation efficiency has been obtained by investigating the interactions between various factors in this experiment. Additionally, the as prepared fragrance microcapsules have been applied successfully in textiles, and show good laundering durability, which indicates that the fragrance microcapsules have a huge potential value.
2. Experimental
2.1 Materials
1,4-Butanediol dimethacrylate (BDDMA, Aldrich, 95%, 200–300 ppm MEHQ as an inhibitor) was used to form the shell. Gum arabic power (GA, Sinopharm Chemical Reagent Co., Ltd, 100%) was used as dispersant. Dementholized peppermint oil (DPO, Anhui Fengle Perfume Co., Ltd, 100%) and caprylic/capric triglyceride (GTCC, LinYi LvSen Chemical Co., Ltd, 99%) were employed as the core material. Ammonium pyrosulfite (APS, Aldrich, 98%) was selected as the initiator. Sodium metabisulfite (Na2S2O5, Adamas, 99%) was used as the catalyst. Toluene (Shanghai Lingfeng Chemical Reagent Co., Ltd, 99.5%) was used as solvent. Ethanol (Aldrich, 99.8%) was used as extracting agent. The fabric was scoured and bleached 100%, cotton knit (0.1 × 0.1 m−2), with areal density of 214 g m−2 and had a thickness of 1.53 mm. Polyurethane binder (PU, Bayer Material Science, 99%) was used to bond the fabric with microcapsules. Fatty alcohol–polyoxyethylene ether (Sinopharm Chemical Reagent Co., Ltd, 99%) was selected as penetrant. All the materials were used as received without further purification.
2.2 Preparation of PBDDMA microcapsules
The core material (15 g) comprised of DPO and GTCC. The BDDMA monomer was added into the core material in a 50 ml glass beaker to form the oil phase. APS (0.1 g, 4.4 × 10−4 mol) was dissolved into deionized water (3 g, 0.2 mol) in a 10 ml vial at room temperature to obtain the initiator solution. The catalyst solution was prepared by adding Na2S2O5 (0.13 g, 6.8 × 10−4 mol) into deionized water (2 g, 0.1 mol) in a 10 ml vial. 15 g of the GA emulsifier (10%) was diluted by deionized water (12.5 g, 0.7 mol) in a 50 ml glass beaker, forming the aqueous phase. The oil-in-water (O/W) emulsion was prepared by mixing the oil phase and aqueous phase, which was followed by high-speed shearing for several minutes using a homogenizer (ULTRA-TURRAX, T25, IKA). After the emulsion was deoxygenated by bubbling N2 for 30 minutes in a 100 ml conical flask, the initiator solution was added into the emulsion rapidly. After another 10 minutes, the catalyst solution was added into the emulsion rapidly to start the polymerization, forming microcapsules at room temperature with magnetic stirring for 2 h. Subsequently, the microcapsule slurry was placed into a water bath at a certain temperature to cure the shell of microcapsules with magnetic stirring for 1 h. The entire process was purged with N2. After that, the microcapsules were collected by filtration with triple washes at room temperature.
2.3 Morphology
The morphologies of microcapsules were characterized by scanning electron microscope (SEM, TM-1000, Hitachi Limited) under dry conditions.
2.4 Encapsulation efficiency
The method to measure the encapsulation efficiency was the same as our previous work.14,17,18 First, a linear relationship between the concentrations of core material and their UV absorbances was created according to the calibration curve of the spectrophotometry. Then, the unencapsulated core material (free oil) was extracted from the microcapsule suspension into toluene. The concentrations of free oil were determined according to the UV absorbance, which was used to calculate the encapsulation efficiency (see ESI†).
2.5 Experimental design for RSM and optimization
RSM is a mathematical and statistical method for optimizing the process parameters, which can be used to obtain desired results: microcapsules with a high encapsulation efficiency produced by fewer experimental trials than in other methods such as orthogonal experimental design and uniform design.35 There is a variety of experiment design methods in RSM, of which Central Composite Design (CCD) and Box–Behnken Design (BBD) are the two most widely used methods. Generally, the CCD consists of two-level fractional factorial runs, center runs and two-level axial runs. The BBD is a three-level design without any points at the vertices of a cubic region created by the upper and lower limits for each variable. This could be advantageous when the points on the corners of the cube represent factor-level combinations that are prohibitively expensive or impossible to test because of physical process constraints.36 Therefore, BBD was employed to explore the optimal conditions of synthesizing fragrance microcapsules, in which curing temperature (X1), homogenization time (X2), the ratio of core/shell (X3) and homogenization rate (X4) were selected as independent variables (factors). The encapsulation efficiency of the core material was used as a dependent variable (response). A good level of the four independent variables was determined in a single factor variable experiment in which the encapsulation efficiency improved to its maximum value and subsequently decreased from the highest value. Therefore, the curing temperature, homogenization time, the ratio of core/shell and homogenization rate were 30–60 °C, 3–5 min, 2–10 and 5000–9000 rpm, respectively. The optimal process condition was obtained by maximizing the response variables. According to composition of the four variables, 30 experiments were generated as showed in Table 1. The polynomial models described the correlation between the four variables and encapsulation efficiency. One-way ANOVA in RSM was applied to the experimental data corresponding to the design of Table 1 and the significance of the model (p < 0.05) was estimated. Regression analysis and response surfaces were analyzed by Design Export software.
Table 1 Design and results of Box–Behnken experimentsa
Run no. |
X1 (°C) |
X2 (min) |
X3 |
X4 (rpm) |
Encapsulation efficiency (%) |
X1, temperature; X2, homogenization time; X3, ratio of core/shell; X4, homogenization rate. |
1 |
40 |
4.5 |
4 |
6000 |
83.0 |
2 |
45 |
5.0 |
6 |
7000 |
83.8 |
3 |
45 |
4.0 |
6 |
7000 |
90.2 |
4 |
45 |
4.0 |
6 |
7000 |
90.7 |
5 |
45 |
4.0 |
6 |
7000 |
90.0 |
6 |
45 |
3.0 |
6 |
7000 |
85.9 |
7 |
50 |
3.5 |
4 |
8000 |
83.0 |
8 |
45 |
4.0 |
2 |
7000 |
63.3 |
9 |
50 |
4.5 |
8 |
6000 |
79.9 |
10 |
45 |
4.0 |
6 |
7000 |
90.0 |
11 |
30 |
4.0 |
6 |
7000 |
78.1 |
12 |
40 |
4.5 |
8 |
6000 |
78.3 |
13 |
50 |
4.5 |
4 |
8000 |
76.7 |
14 |
40 |
3.5 |
4 |
6000 |
80.4 |
15 |
40 |
3.5 |
8 |
6000 |
70.3 |
16 |
45 |
4.0 |
6 |
7000 |
91.0 |
17 |
45 |
4.0 |
10 |
7000 |
60.5 |
18 |
40 |
3.5 |
4 |
8000 |
77.5 |
19 |
50 |
3.5 |
8 |
8000 |
72.6 |
20 |
40 |
4.5 |
4 |
8000 |
77.7 |
21 |
60 |
4.0 |
6 |
7000 |
79.7 |
22 |
50 |
4.5 |
4 |
6000 |
77.2 |
23 |
40 |
4.5 |
8 |
8000 |
73.8 |
24 |
50 |
4.5 |
8 |
8000 |
76.1 |
25 |
45 |
4.0 |
6 |
9000 |
76.4 |
26 |
45 |
4.0 |
6 |
7000 |
90.8 |
27 |
50 |
3.5 |
4 |
6000 |
76.2 |
28 |
40 |
3.5 |
8 |
8000 |
72.6 |
29 |
50 |
3.5 |
8 |
6000 |
69.5 |
30 |
45 |
4.0 |
6 |
5000 |
72.6 |
2.6 Chemical structure and core–shell structure analysis
The chemical structures of PBDDMA film, core material (liquid) and microcapsules powder were characterized by Fourier transform infrared-attenuated total reflection (FTIR-ATR, Nicolet 6700, Thermo Fisher Scientific Inc., USA). The chemical structure of the fragrance microcapsules indicated the compositions. The microcapsules powder was milled and added to toluene to dissolve the core material. Then, the pure shell material (PBDDMA) was obtained by filtration with triple washes at room temperature. The core–shell structure of the fragrance microcapsules was characterized by transmission electron microscopy (TEM, JEM-2100, JEOL) under dry conditions.
2.7 Release behavior
The encapsulated DPO can diffuse from the microcapsules into air while GTCC cannot. The release behavior of the DPO was studied using a Mettler-Toledo analytical balance (AL204, METTLER TOLEDO) and oven (DHG-9145A, Shanghai Lengpu Instrument Co., Ltd.). 5.0 g of dry microcapsules and pure core material were put into the oven at 50 °C. And 4.2 g of pure core material was put into oven at 50 °C, in which the value of pure core materials should be equal to the core material of dry microcapsules (5.0 g). Then, the samples were weighed every 2 h, and the weight of the remaining microcapsules was used to calculate the weight of the released DPO.
2.8 Thermal stability analysis of microcapsules
The thermal stabilities of the core material, microcapsules and PBDDMA shell material were evaluated by the thermal gravimetric analysis (TGA, TG209F1, German resistance instrument Co., Ltd) under an atmosphere of N2 from 30 °C to 600 °C at a heating rate of 5 °C min−1.
2.9 Treatment of microcapsules on fabric
The cotton fabric samples were treated with fragrance microcapsules. The fabric samples were impregnated with an aqueous solution (200 g) composed of microcapsules, penetrant and PU binder at 40 °C for 30 min. The concentration of microcapsules, penetrant and PU binder were 5 wt%, 2 wt% and 5 wt%, respectively. The impregnated fabric was padded up to 90% pickup by the two-dips with a padder (P-B1, Xiamen rapid precision machinery Co., Ltd), preliminarily dried at 50 °C for 1 min, and baked at 150, 160 and 170 °C for 1 and 2 min by electricity using a heat drum wind drying oven (101C-48, Shanghai experiment factory Co., Ltd), respectively.
2.10 Washing durability and oil loading capacity
The washing durability of the fragrance microcapsules on textile substrates was evaluated. The fabric samples treated with the fragrance microcapsules were washed by a domestic laundry machine (3XGSC9455JQ, Hewlett Packard co., Ltd) with 5, 10 and 15 cycles. The fabric samples were soaked in ethanol to extract the fragrance oil from the microcapsules coated onto the fabric. The amount of fragrance oil was determined by UV-visible spectroscopy. The mass of DPO in the initial fabric sample was attained (see ESI†).
3. Results and discussion
3.1 Mechanism and morphology
The mechanism of the PBDDMA shell formation is shown in Fig. 1. By high speed shearing, the O/W microemulsion was formed. Then, the initiator APS was split into free radicals in the continuous phase under the protection of N2. Afterwards, the free radicals triggered the carbon–carbon double bond of BDDMA monomer to polymerize at the interface of the droplets. Once the free radical polymerization began, more monomers dissolving in the core material migrated to the interface to participate in the polymerization, leading to the growth of polymer chains. Finally, the polymer chains aggregated with each other thus forming the PBDDMA network with the core material encapsulated inside.
 |
| Fig. 1 The schematic process of encapsulation. | |
The morphologies of the fragrance microcapsules were influenced by the composition of the core material, as shown in Fig. 2. For Fig. 2a, when the core material was pure fragrance (DPO, 100 wt%), the surface of the dry fragrance microcapsules was found to collapse and rupture. As the content of DPO decreased to 75 wt% in the core material, the morphologies of microcapsules were irregular spheres with dimpled surfaces, as illustrated in Fig. 2b. If the content of DPO was further decreased to 50 wt%, the morphologies of dry fragrance microcapsules were smooth spheres, which demonstrated that 50 wt% of DPO was appropriate for the formation of microcapsules (Fig. 2c). Accordingly, the optimal ratio of DPO/GTCC in the core material was 1
:
1, which enabled the microcapsules to hold a spherical morphology.
 |
| Fig. 2 SEM images of microcapsules with the content of DPO in the core material: (a) 100 wt%; (b) 75 wt%; (c) 50 wt%. | |
3.2 Chemical structure analysis and structure of PBDDMA shell
In this study, the chemical structures of core material (liquid), the microcapsules powder and the PBDDMA film were characterized using FTIR spectroscopy as shown in Fig. 3. Fig. 3a illustrates that the carbonyl-stretching (C
O) absorption (1728 cm−1) and a C–O stretching vibration (1152 cm−1) of the ester group of PBDDMA were observed. The two absorption peaks of 1730 cm−1 and 1156 cm−1 of the fragrance microcapsules indicated that the microcapsule shell is PBDDMA in Fig. 3b. The visible peak at 3383 cm−1 for the stretching vibration of hydroxyl groups of the core material shown in Fig. 3c was also observed in the spectrum of the microcapsules (Fig. 3b). This proved that the microcapsules contained the core material and PBDDMA shell material. The visible peak around 1600 cm−1 indicated that there were residual double bonds present after the polymerization, possibly due to steric interference.17 Moreover, TEM image (Fig. 4) below proved the core–shell structures of fragrance microcapsules with PBDDMA as shell material and DPO/GTCC as core material.
 |
| Fig. 3 Infrared spectra of (a) PBDDMA shell, (b) microcapsules and (c) core material DPO/GTCC. | |
 |
| Fig. 4 Transmission electron micrograph of microcapsules. | |
3.3 Encapsulation efficiency
To obtain the fragrance microcapsules with high encapsulation efficiency,37 curing temperature (X1), and homogenization time (X2), the ratio of core/shell (X3) and homogenization rate (X4) were selected as the independent variables (factors) while the encapsulation efficiency of the core material was the dependent variable (response). Then, a systematic optimization was carried out by using RSM to estimate the extended effect of the formulation variables (X1, X2, X3 and X4) on the encapsulation efficiency. A Box–Behnken design consisted of 30 experiment formulas as shown in Table 1. The values of the investigated responses measured for all experiments were fitted in Box–Behnken design to get a model equation for the response variable analysis. The relationship between the four independent variables and encapsulation efficiency was given by the following regression equation from RSM analysis: |
Encapsulation efficiency (%) = 90.42 + 0.07X1 + 0.69X2 − 1.84X3 + 0.12X4 − 0.2X1X2 + 0.53X1X3 + X1X4 + 1.6X2X3 − 1.45X2X4 − 0.07X3X4 − 1.28X12 − 1.41X22 − 7.14X32 − 4X42
| (1) |
Fig. 5 shows the actual values of the encapsulation efficiency and the predicted values of the encapsulation efficiency, obtained from the regression equation above. The ANOVA analysis for quadratic regression model is summarized in Table 2. The P value was less than 0.0001 indicating the model was significant and adequate. The results of model summary demonstrated R2 value, the adjusted R2 (Radj2) value and the coefficient of variation (CV) value were 0.9626, 0.9277 and 2.71, respectively, indicating a good precision and reliability of the experiments.31 It was found that encapsulation efficiency was significantly influenced by the linear of X3 and the quadratic of X1, X2, X3 and X4 (P < 0.05). Meanwhile, it demonstrated that X2X3 and X2X4 had significant effects on encapsulation efficiency (P < 0.05). The data revealed that the significant factors that affected encapsulation efficiency were the synergistic effects of linear contributions of X1, X2, and X4, and interaction effects of X1X2, X1X3, X1X4, and X2X3.
 |
| Fig. 5 Plots of predicted encapsulation efficiency compared with the actual response of encapsulation efficiency. | |
Table 2 Summary of ANOVA for quadratic modelsa
Source |
Sum of squares |
d.f.* |
Mean square |
F-Value |
p-Value prob > F |
Significant |
d.f.*, degree of freedom; p < 0.0001, extremely significant (**); p < 0.05, significant (*); p > 0.05, not significant (—). |
Model |
1762.81 |
14 |
125.92 |
27.60 |
<0.0001 |
** |
X1(T) |
0.17 |
1 |
0.17 |
0.04 |
0.8479 |
— |
X2(t) |
11.47 |
1 |
11.47 |
2.51 |
0.1337 |
— |
X3(core/shell) |
81.36 |
1 |
81.36 |
17.83 |
0.0007 |
* |
X4(speed) |
0.35 |
1 |
0.35 |
0.08 |
0.7862 |
— |
X1X2 |
0.65 |
1 |
0.65 |
0.14 |
0.7107 |
— |
X1X3 |
4.55 |
1 |
4.55 |
0.10 |
0.3340 |
— |
X1X4 |
16.06 |
1 |
16.06 |
3.52 |
0.0802 |
— |
X2X3 |
40.80 |
1 |
40.80 |
8.94 |
0.0092 |
* |
X2X4 |
33.61 |
1 |
33.61 |
7.37 |
0.0160 |
* |
X3X4 |
0.08 |
1 |
0.08 |
0.02 |
0.8984 |
— |
X12 |
201.19 |
1 |
201.19 |
44.09 |
<0.0001 |
** |
X22 |
52.47 |
1 |
52.47 |
11.50 |
0.0040 |
* |
X32 |
1351.75 |
1 |
1351.75 |
296.25 |
<0.0001 |
** |
X42 |
424.85 |
1 |
424.85 |
93.11 |
<0.0001 |
** |
Residual |
68.44 |
15 |
4.56 |
|
|
|
Pure error |
0.94 |
5 |
0.19 |
|
|
|
Cor total |
1831.26 |
29 |
|
|
|
|
R2 |
0.96 |
Radj2 |
0.9277 |
|
CV% |
2.71 |
|
|
|
|
|
The three-dimensional response surface graphs in Fig. 6 were very useful in investigating the main effects and interaction effects of the four factors, which gave a visual representation. The contour plots in the Fig. 6a and f were rounder than other contour plots indicating that the symmetric influence of temperature and homogenization time on encapsulation efficiency was minimal as well as the symmetric influence of the interactions between homogenization rate and the ratio of core/shell (c/s). The response surfaces in Fig. 6b and d show that encapsulation efficiencies were improved to their maximum values and subsequently decreased from the highest values. Additionally, the encapsulation efficiency did not change significantly as the cure temperature and homogenization time improved during preparation, which indicated that the effect of c/s on encapsulation efficiency was more significant than the temperature and the homogenization time. The results agreed with the conclusion of ANOVA test, which indicated that the ratio of core and shell had significant effects on encapsulation efficiency. Encapsulation efficiency improved to the maximum value and subsequently decreased from the highest value due to the decrease in the thickness of wall membranes leading to the loss of oil.35,38–40 From Fig. 6c and e, it was observed that the effect of homogenization rate on encapsulation efficiency was more significant than the curing temperature and homogenization time. The reason was that the increasing homogenization rate resulted in a smaller particle size, and subsequently a higher homogenization rate led to an increase in the size. The phenomenon of the influence of homogenous rate on the microcapsule diameter and the encapsulation efficiency was due to the balanced relation of the three kinds of forces that existed in the procedure of emulsification. The three kinds of forces were the shear stress, surface tension and viscous stress. The shear stress contributed to the droplets dispersed with smaller diameter, while the surface tension and viscous stress contributed to the droplets aggregating into bigger droplets preventing dispersed droplets. When the shear stress was greater than the sum of the viscous stress and the surface tension, the emulsion droplets divided into smaller droplets. On the contrary, the small droplets aggregated to bigger droplets when the viscous stress and the surface tension were greater than the shear stress under the condition that the homogenization rate was too high leading to the very small size of the emulsion droplets. The shear stress depended on the homogenization rate and homogenization time, and the viscous stress and the surface tension depended on the property of the core materials. When the other factors were constant, the diameter of the capsules decreased first and then increased as the homogenization rate increased.17,41 Fig. 6 reveals that c/s and homogenous rate were the main factors affecting encapsulation efficiency. The optimal parameters were obtained as follows: the temperature was 44.78 °C, the homogenization time was 3.95 min, the ratio of core/shell was 5.94 and the homogenization rate was 7123.98 rpm. The theoretical highest encapsulation efficiency was 90.4% calculated by RSM. Then, fragrance microcapsules synthesized by the optimal conditions above had a high encapsulation efficiency of 91.0%, which was the average value from five repeated experiments. The encapsulation efficiency of five repeated experiments with optimal conditions were 90.8%, 90.9%, 90.9%, 91.0% and 91.2%, respectively. The standard deviation was 0.15. The particle size and particle size distribution of the fragrance microcapsules are shown in Fig. 7. The parameters of the five repeated experiments are based on the optimal conditions from RSM, which were as follows: the temperature was 45 °C, the homogenization time was 4 min, the ratio of core/shell was 6 and the homogenization rate was 7124 rpm. Therefore, it indicated that the RSM model can predict the highest encapsulation efficiency precisely.
 |
| Fig. 6 Response surface plots showing the effect of (a) homogenization time and temperature, (b) core/shell and temperature, (c) homogenization rate and temperature, (d) core/shell and homogenization time, (e) homogenization rate and time and (f) homogenization rate and core/shell on encapsulation efficiency. | |
 |
| Fig. 7 Particle size and particle size distribution of the microcapsules. | |
3.4 Thermal stability
The thermal stability of the fragrance microcapsules prepared using the optimal parameters above was evaluated by thermogravimetric analysis (TGA) as shown in Fig. 8. The loss in the mass of the fragrance microcapsules occurred in three stages from 30 °C to 600 °C. The first stage was due to the evaporation of the fragrance oil DPO from 100 °C to 208 °C. The second stage ranged from 240 °C to 320 °C due to the weight loss of GTCC and partial loss of the shell material. The third stage was from 320 °C to 600 °C, which indicated the full degradation of the shell material. The onset evaporation of DPO inside the microcapsules was about 100 °C (b) while onset evaporation of DPO without encapsulation was 50 °C (a), which demonstrated that fragrance microcapsules can improve the onset evaporation temperature of fragrance oil and increase the applicable temperature region of the fragrance oil. Accordingly, microcapsules had a good thermal stability and could protect the leakage of DPO below 100 °C.
 |
| Fig. 8 TGA curve of the pure core material, microcapsules and PBDDMA shell material. | |
3.5 Release behavior
The release curves of the pure DPO and fragrance microcapsules powder at 50 °C are shown in Fig. 9. According to the curve of fragrance microcapsules, DPO was released from the inside of the microcapsules quickly during the initial 20 h, and then the release rate slowed down during the next 30 h. After releasing for 50 h, the release rate of DPO changed more slowly. The release curve of the pure DPO indicated that DPO completely evaporated after 5 h at 50 °C. However, as the DPO was encapsulated by PBDDMA, there was 70 wt% DPO inside the PBDDMA microcapsules after 5 h at 50 °C. It was concluded that the encapsulated DPO at 50 °C was durable.
 |
| Fig. 9 Release curves of the pure core material and the microcapsules at 50 °C. | |
3.6 Laundering durability of the microcapsules-treated fabrics
The fragrance microcapsules prepared under the optimal parameters were applied in textile. First, the fabric samples were impregnated with fragrance microcapsules in a solution at 40 °C for 30 min, and then they were padded up to 90% pickup by the two-dips with a padder. Then, one part of the fabric samples was baked at 150, 160 and 170 °C for 1 min. Furthermore, another part of fabric samples was baked at 150, 160 and 170 °C for 2 min. The residual fragrance on the fabric was evaluated, as shown in Fig. 10. It was found that the retention of fragrance in the textile substrate after 5 washing cycles evidently decreased. Moreover, the fragrance contents on the fabric slowly decreased with further increasing washing cycles. The reason was due to the low adhesion force between the microcapsules and the textile substrate, which resulted in a rapid decrease of the retention of the fragrance in the textile substrate. With an increase in the number of washing cycles, the fragrance microcapsules that fastened on knits and located between the fibers began to detach from the textile, and the contents of fragrance microcapsules decreased again. Additionally, the laundering durability of the microcapsules-treated fabrics was significantly influenced by the baking temperature and time. When the baking temperature was set to 160 °C for 2 min, the retention of fragrance in the textile substrate was the highest. In general, higher baking temperatures and longer times contributed to a higher adhesive stress between the microcapsules and the textile substrate, which protected fragrance microcapsules from being washed off and led to a high retention of fragrance in the textile substrate. However, the fragrance was likely to diffuse from the inside of microcapsules when the baking temperature was above 160 °C, which resulted in low fragrance contents on the textile substrate.
 |
| Fig. 10 Objective evaluation of the washing durability of fragrance microcapsule-treated fabrics. | |
Fig. 11 showed SEM photographs of the textile substrate coated by fragrance microcapsules that were baked at 160 °C for 2 min. The SEM images of the textile substrate washed after 0, 5, 10 and 15 cycles are shown in Fig. 11. As can be seen from Fig. 11a, microcapsules were clearly observed on the fiber surface and the interstices between the fibers before washing. Most of the microcapsules possessed good shapes without leakage. After 5 washing cycles, many fragrance microcapsules absorbed on the surface of fiber disappeared as shown in Fig. 11b. And part of the fragrance microcapsules were still located at the interstices on the fabric after 10 washing cycles (Fig. 11c) and 15 washing cycles (Fig. 11d), which also demonstrated that the fragrance microcapsules coated on textile had a certain resistance to washing.
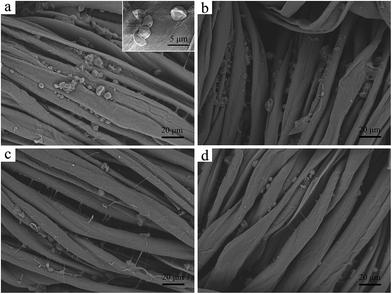 |
| Fig. 11 SEM morphologies of textile after several washing cycles: (a) 0, (b) 5, (c) 10 and (d) 15. | |
4. Conclusion
In this study, poly(1,4-butanediol dimethacrylate) microcapsules were synthesized by interfacial free-radical polymerization, in which a BDDMA monomer was self-crosslinked to form a polymer shell. It was found that the polarity of the core material was correlative to the shape of the microcapsules and that the microcapsules possessed spherical shape as the content of DPO and GTCC was 50%, respectively, in the core material. According to the RSM, the highest yield of encapsulation efficiency of 90.4% was achieved. The TGA results indicated that the fragrance microcapsules had good thermal stability and the fragrance microcapsules can prevent leakage of the fragrance oil DPO below 100 °C. It was found that the fragrance contents on the fabric decreased slowly with an increasing number of washing cycles. As the fabric was baked at 160 °C for 2 min, the fragrance microcapsules had the best laundry durability, which is encouraging for applications in textile.
Acknowledgements
The authors thank for financial support by National Nature Science Foundation of China (51473032, 51503034), Fundamental Research Funds for the Central Universities (CUSF-DH-D-2016024, 2232015D3-12) and Science and Technology Commission of Shanghai Municipality for Yangfan Program (15YF1400700).
References
- L. Jeong Yun, O. Sung Jin, L. Min Suk, P. Jong Yun, R. Jung Yun and L. Ki Hoon, Fibers Polym., 2012, 13, 1209–1213 CrossRef.
- C. X. Wang and S. L. Chen, Fibres Text. East. Eur., 2005, 13, 41–44 CAS.
- M. E. Hyland, B. Whalley and A. W. A. Geraghty, J. Psychosom. Res., 2007, 62, 331–340 CrossRef PubMed.
- G. Buchbauer, L. Jirovetz, W. Jager, H. Dietrich, C. Plank and E. Karamat, Z. Naturforsch., C: Biosci., 1991, 46, 1067–1072 CAS.
- Z. Yang, G. Liang, L. ly, W.-m. Au, H. Zhong, T. K. S. Wong and Z. Yang, in Advanced Polymer Science and Engineering, ed. C. H. Wang, L. X. Ma and W. Yang, 2011, vol. 221, pp. 308–315 Search PubMed.
- T. K. Maji and M. R. Hussain, J. Appl. Polym. Sci., 2009, 111, 779–785 CAS.
- B. Pena, L.-C. de Menorval, R. Garcia-Valls and T. Gumi, ACS Appl. Mater. Interfaces, 2011, 3, 4420–4430 CAS.
- A. V. Sadovoy, M. V. Lomova, M. N. Antipina, N. A. Braun, G. B. Sukhorukov and M. V. Kiryukhin, ACS Appl. Mater. Interfaces, 2013, 5, 8948–8954 CAS.
- G. Tian, Y. Li, Q. Yuan, L. Cheng, P. Kuang and P. Tang, Carbohydr. Polym., 2015, 122, 5–10 CrossRef CAS PubMed.
- J. Shi, X. Zhang, S. Zhang, X. Wang and Z. Jiang, ACS Appl. Mater. Interfaces, 2013, 5, 10433–10436 CAS.
- B. Kim, T. Y. Lee, A. Abbaspourrad and S.-H. Kim, Chem. Mater., 2014, 26, 7166–7171 CrossRef CAS.
- D. Li, Z. Guan, W. Zhang, X. Zhou, W. Y. Zhang, Z. Zhuang, X. Wang and C. J. Yang, ACS Appl. Mater. Interfaces, 2010, 2, 2711–2714 CAS.
- S. Lone, G. S. Ghodake, D. S. Lee and I. W. Cheong, New J. Chem., 2013, 37, 877–881 RSC.
- Y. Zhang, D. Zhao, X. Jiao, K. Ye, X.-h. Lu and G. Qiu, Acta Polym. Sin., 2016, 1, 46–52 Search PubMed.
- Q. Wu, D. Zhao, X. Jiao, Y. Zhang, K. J. Shea, X. Lu and G. Qiu, Ind. Eng. Chem. Res., 2015, 54, 8130–8136 CrossRef CAS.
- H. Ichiura, M. Takayama, N. Nishida and Y. Otani, J. Appl. Polym. Sci., 2012, 124, 242–247 CrossRef CAS.
- X. Jiao, D. Zhao, Y. Zhang, Q. Wu, G. Qiu, X. Lu and X. Shi, Colloid Polym. Sci., 2016, 294, 639–646 CAS.
- D. Zhao, X. Jiao, Y. Zhang, D. An, X. D. Shi, X. H. Lu, G. Qiu and K. J. Shea, RSC Adv., 2015, 5, 96067–96073 RSC.
- T. Feczko, V. Kokol and B. Voncina, Macromol. Res., 2010, 18, 636–640 CrossRef CAS.
- B. Peña, C. Panisello, G. Areste, R. Garcia-Valls and T. Gumi, Chem. Eng. J., 2012, 179, 394–403 CrossRef.
- A. R. Lee, C. H. Han and E. Yi, Fibers Polym., 2014, 15, 35–40 CrossRef CAS.
- A. Sansukcharearnpon, S. Wanichwecharungruang, N. Leepipatpaiboon, T. Kerdcharoen and S. Arayachukeat, Int. J. Pharm., 2010, 391, 267–273 CrossRef CAS PubMed.
- A. K. Nayak, D. Pal and K. Santra, Carbohydr. Polym., 2014, 107, 41–50 CrossRef CAS PubMed.
- C. Wu, T. Wu, Z. Fang, J. Zheng, S. Xu, S. Chen, Y. Hu and X. Ye, RSC Adv., 2016, 6, 46686–46695 RSC.
- A. A. de Camara Jr, S. Dupont, L. Beney, P. Gervais, A. Rosenthal, R. T. Pinto Correia and M. R. da Silva Pedrini, Appl. Microbiol. Biotechnol., 2016, 100, 5547–5558 CrossRef PubMed.
- S. Takeungwongtrakul, S. Benjakul and A. H-kittikun, Eur. J. Lipid Sci. Technol., 2015, 117, 450–459 CrossRef CAS.
- S. Senanayake and F. Shahidi, Food Chem., 2002, 77, 115–123 CrossRef.
- R. Minjares-Fuentes, A. Femenia, M. C. Garau, M. G. Candelas-Cadillo, S. Simal and C. Rossello, Carbohydr. Polym., 2016, 138, 180–191 CrossRef CAS PubMed.
- A. T. Getachew and B. S. Chun, LWT--Food Sci. Technol., 2016, 70, 126–134 CrossRef CAS.
- S. Honary, P. Ebrahimi and R. Hadianamrei, Pharm. Dev. Technol., 2014, 19, 987–998 CrossRef CAS PubMed.
- Y. Ma, Y. Zhang, S. Zhao, Y. Wang, S. Wang, Y. Zhou, N. Li, H. Xie, W. Yu, Y. Liu, W. Wang and X. Ma, J. Biomed. Mater. Res., Part A, 2012, 100, 989–998 CrossRef PubMed.
- A. K. Nayak, D. Pal and S. Das, Carbohydr. Polym., 2013, 96, 349–357 CrossRef CAS PubMed.
- M. Jonsson, O. Nordin and E. Malmstrom, J. Appl. Polym. Sci., 2011, 121, 369–375 CrossRef CAS.
- I. Hofmeister, K. Landfester and A. Taden, Macromolecules, 2014, 47, 5768–5773 CrossRef CAS.
- Z. Xiao, W. Li and G. Zhu, Colloid Polym. Sci., 2015, 293, 1339–1348 CAS.
- W. C. Chuan, L. Y. Tsai and L. C. Juan, Int. J. Heat Mass Transfer, 2000, 43, 1869–1872 CrossRef.
- T. S. Shim, S. H. Kim and S. M. Yang, Part. Part. Syst. Charact., 2013, 30, 9–45 CrossRef CAS.
- F. Tatar and T. Kahyaoglu, J. Food Process. Preserv., 2015, 39, 624–633 CrossRef CAS.
- Y. Xia and D. W. Pack, Pharm. Res., 2014, 31, 3201–3210 CrossRef CAS PubMed.
- L. Jing and X. Zhao, Trans. CSAE, 2008, vol. 24, pp. 303–306 Search PubMed.
- L. Sanchez, P. Sanchez, M. Carmona, A. de Lucas and J. F. Rodriguez, Colloid Polym. Sci., 2008, 286, 1019–1027 CAS.
Footnote |
† Electronic supplementary information (ESI) available. See DOI: 10.1039/c6ra16030a |
|
This journal is © The Royal Society of Chemistry 2016 |
Click here to see how this site uses Cookies. View our privacy policy here.