DOI:
10.1039/C6RA10902K
(Paper)
RSC Adv., 2016,
6, 63365-63372
Adsorption characteristics of graphene oxide nanosheets on cement†
Received
27th April 2016
, Accepted 21st June 2016
First published on
23rd June 2016
Abstract
Modifying cement with graphene oxide (GO) nanosheets tremendously improves its mechanical properties but decreases its fluidity. The adsorption characteristics between GO and cement play a pivotal role in the influence on fluidity. In this paper, the adsorption characteristics of graphene oxide nanosheets on cement were investigated using scanning electron microscopy (SEM), total organic carbon (TOC), Fourier transform infrared spectra (FTIR) and XPS analyses. The results show that GO nanosheets have a strong adsorption ability on the cement surface. The adsorption data was best fitted with the Freundlich adsorption isotherm model and described by a pseudo-second order kinetics model. The adsorption process includes a chemical reaction where the –COOH groups on the edge of the GO nanosheets react with metal cations. The adsorption layer thickness of the GO nanosheets on the cement was about 10.16 nm.
1 Introduction
Cement is the key component of concrete and mortar, which is one of the most important and widely used building materials. However, its inherent cracks due to lesser tensile strength and strain capacity constitute a main drawback.1–6 As we know, graphene oxide (GO) has many unique properties, such as excellent mechanical properties, high surface functionalization, high surface area and good dispersibility in aqueous solvents. Also, there can be many active groups added to GO sheets, such as carboxyl groups (–COOH) on the edges of GO sheets, and epoxy groups (–CH(O)CH–) and hydroxyl groups (–OH) on the basal planes.7,8 Hence, GO has been widely used as a chemical admixture for cement; the addition of small amounts of GO could improve most properties of cement composites.9–12
Based on existing research, the introduction of GO could increase the flexural strength, tensile strength, compressive strength and transport properties of cement.13–17 Meanwhile, GO has a negative influence on the fluidity of cement.18,19 Certainly, fluidity is an important property of cement; good fluidity was the premise of its workability and pumpability in actual usage processes. A decrease in fluidity would lead to lower durability of the cement. The significance of sustainability in the construction industry has been recognized in recent years, especially with respect to the consumption of energy and natural resources. Thus, the key issue of GO as an admixture is the decrease in cement fluidity. The adsorption characteristics between the admixture and the cement have a strong influence on the cement’s fluidity. For example, water-reducing agents, as one of the most important chemical admixtures, could adsorb onto the cement particles and deflocculate and separate to release trapped water, thereby producing pastes with greater fluidity.20 Therefore, it is important to understand how GO nanosheets are adsorbed onto cement for controlling the fluidity of the cement. Research into the adsorption characteristics of GO nanosheets on cement could explore the reasons for the decrease in fluidity, and give guidance on the modification of GO nanosheets in the cement field.
On account of the above considerations, this study aimed to investigate the adsorption characteristics of graphene oxide nanosheets on cement. The saturated adsorption amount, adsorption isotherm and adsorption layer thickness of cement adsorption by GO nanosheets were studied. The microstructures of cement adsorption by GO nanosheets were also observed.
2 Experimental section
2.1 Materials
The chemicals used in this research were graphite (size <15 nm), potassium permanganate (KMnO4), concentrated sulfuric acid (H2SO4, 98%), sodium nitrate (NaNO3) and hydrogen peroxide (H2O2, 30%), which were all analytically pure. The materials used in this research were Portland cement type 52.5R, and the Blaine surface area of the cement is 3550 ± 100 cm2 g−1. The chemical composition of the cement is shown in Table 1.
Table 1 Chemical composition of the cement (%)
Component |
CaO |
SiO2 |
Al2O3 |
Fe2O3 |
MgO |
SO3 |
K2O |
Na2O |
LOI |
Content |
65.1 |
21.3 |
5.1 |
2.9 |
1.1 |
1.8 |
0.7 |
0.3 |
1.7 |
2.2 Preparation of GO
GO was synthesized from natural graphite powder using a modified Hummers’ method. 2 g of graphite powder was stirred with 0.5 g of NaNO3 into 96 mL of H2SO4 (98%) in a 500 mL three-necked round-bottomed flask. The mixture was cooled in an ice-bath (<5 °C). Under continuous stirring, 12 g of KMnO4 was added slowly three times (4 g) after each 15 minutes. After the addition, the ice-bath was removed and the mixture was stirred for 2 h at 35 °C. When the mixture was transformed into a paste (brownish grey colored), 80 mL of distilled water was added to it. After 30 minutes, the reaction was terminated by the addition of excess water (200 mL) and 10 mL of 30% H2O2 resulting in a bright yellow color of the mixture. The solution was purified by vacuum suction filtration and washed with deionized water repeatedly until the pH of the washing water was nearly 7. At last, the GO was dried for 36 h in a freeze-dryer.
2.3 Characterization
A series of GO aqueous dispersions with different concentrations (250–650 mg L−1) were prepared. Then, cement (0.09 g) was mixed with a GO aqueous dispersion (60 g) in a beaker flask. After 10, 20, 30, 60, 90, 120, 150 and 180 min in an oven controlled crystal oscillator (25 °C), the mixture was vacuum filtered.
2.3.1 Adsorption amount measurement.
The extracted solution of GO nanosheets was measured by total organic carbon (TOC) to calculate the residual concentration of the GO nanosheets. Measurements were generally repeated three times and the average was taken as the result. The adsorption amount of GO nanosheets on the surface of the cement was calculated as follows:21–23 | 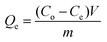 | (1) |
where Qe is the adsorption amount (mg g−1), C0 and Ce represent the initial and equilibrium concentration of the GO aqueous dispersion (mg L−1), and V (L) and m (g) are the initial volume of the GO aqueous dispersion and the mass of the adsorbent used, respectively.
2.3.2 Morphological observation.
The obtained lower filter cake dried in a vacuum could also be used for JSM-6700F scanning electron microscope (SEM) measurements. The surfaces were sputter-coated with a thin layer (1 nm) of gold for good conductivity prior to SEM imaging.
2.3.3 Chemical analyses.
Fourier transform infrared spectra (FTIR) measurements were performed on a Nicolet 380 infrared spectrometer (Thermo electron corporation, United States). After filtration, the obtained lower filter cake dried in a vacuum was used for FTIR measurement; 1 mg powder samples were mixed with 100 mg of KBr to make slices.
2.3.4 Adsorption layer thickness calculation.
The thickness of the adsorbed GO nanosheets on the cement surface was measured using X-ray photoelectron spectroscopy (XPS), using an Ultra Axis DLD, XPS (Kratos Analytical Ltd, UK) with a Kα radiation source of aluminium and a photoelectron energy of 1489.0 eV. Before the XPS measurement, a GO aqueous dispersion with a concentration of a saturated adsorption amount was prepared. After adsorption and filtration, the obtained lower filter cake dried in a vacuum was used for the XPS measurement.
3 Results and discussion
3.1 Characterization of GO
Fig. 1(a) shows that the GO sheets were basically transparent and the folding nature was clearly visible from the TEM images. From the XPS fitted result of C 1s in GO shown in Fig. 1(b), three strong peaks at 284.8, 286.8 and 288.1 eV corresponding to the C–C, C–O (hydroxyl and epoxide) and C
O (carboxyl) groups of GO are noticed. This indicates that oxygen functional groups exist in the GO. Fig. 1(c) shows the Raman spectra of the GO; peaks at 1340 cm−1 (D band) and 1580 cm−1 (G band) indicate the lowering of the numbers of the sp2 domains by the introduction of oxygen-containing functional groups during extensive oxidation. These results are also supported by FTIR spectra (Fig. S1†). Fig. 1(d) displays an AFM image of the GO nanosheets after ultrasonication. The results show that the irregular lamellae of the GO can be observed with a thickness of about 0.83 nm. These results mean that aqueous dispersion of the GO nanosheets was obtained and the GO nanosheets were dispersed in the water by ultra-sonication. Also, the surface area of the GO nanosheets is 376.53 m2 g−1 according to BTE calculation.
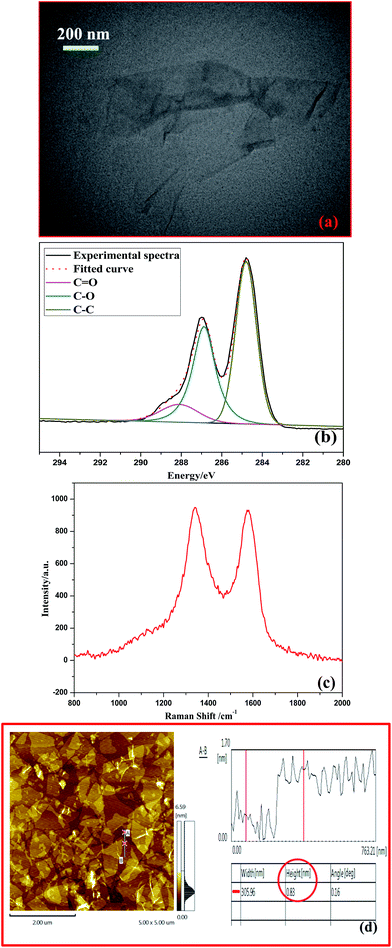 |
| Fig. 1 (a) TEM image of GO. (b) Fitted XPS spectra of C1s in GO. (c) Raman spectra of GO. (d) AFM image of GO nanosheets. | |
3.2 Adsorption phenomena and morphological analysis
Fig. 2(a) shows that the concentration of GO in the adsorption system gradually decreased with the increase of contact time at different initial concentrations. Fig. 2(a) is considered to be a classical example of an adsorption plot, in which the GO adsorbed on the cement is very fast in the first contact minutes, followed by gradual removal before reaching an equilibrium. And the adsorption equilibrium of all concentrations was reached at 120 min. Fig. 2(b) shows the variation of GO concentration (C0) with the adsorption amount (Qe) at 120 min. It can be seen from Fig. 2(b) that the Qe increased with the increase in C0. When C0 was 250 mg L−1, the corresponding Qe was estimated to be 176.93 mg g−1; the same value increased to 232.56 mg g−1 when C0 was 450 mg L−1. These results were consistent with the microscopic observation results. Also, the Qe was nearly unchanged when C0 was higher than 550 mg L−1. The Qe stayed at around 300.00 mg g−1 at the higher concentrations.
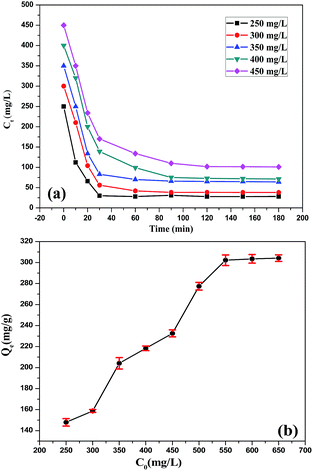 |
| Fig. 2 (a) Decrease in GO concentration (Ct) with time for different initial concentrations. (b) Increase in adsorption amount (Qe) with GO concentration (C0). | |
As shown in Fig. 3, cement was mixed with GO aqueous dispersions in a beaker flask at different concentrations. After 120 min in the oven controlled crystal oscillator at 25 °C, the color of the GO aqueous dispersion changed from yellow to transparent, and the system divided into two layers. The supernatant was the water in the GO aqueous dispersion; the subnatant was the precipitate of GO adsorbed on the surface of the cement. And the amount of the subnatant decreased with the decrease in GO concentration. This means that the adsorption amount of GO increased with the augmentation of GO concentration. The results are consistent with the TOC measurement.
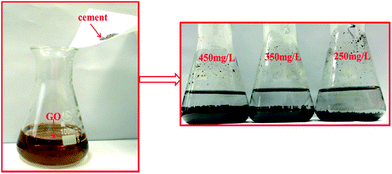 |
| Fig. 3 The adsorption results of GO treated cement at different concentrations. | |
Fig. 4 shows the microstructure of pristine cement and cement adsorption by GO nanosheets (120 min) at 250 mg L−1, 350 mg L−1 and 450 mg L−1. The SEM image of pure GO nanosheets is shown in Fig. S2.† From Fig. 4(a), we can observe the hydration products (gel and crystal) of the cement. As demonstrated in Fig. 4(b), the GO sheets covered the surface of the hydration products, forming a thin coating. We discovered some hydration crystals under the GO sheets coating when the concentration was 250 mg L−1. But hydration crystals could not be observed when the concentration was 350 mg L−1 (Fig. 4(c)). And the aggregation of GO sheets appeared at the surface of the hydration products when the concentration was 450 mg L−1 (Fig. 4(d)). The amount of GO sheets on the surface of the hydration products increased with the increase in GO concentration.
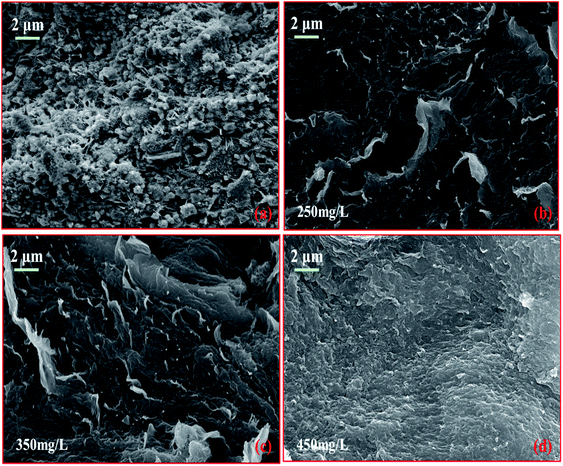 |
| Fig. 4 The microstructure of pristine cement and cement adsorption by GO nanosheets at different concentrations. | |
3.3 Adsorption kinetics and isotherms
In order to examine the mechanism and rate-controlling steps of the adsorption process, we applied a pseudo-first-order Lagergren equation (eqn (2)) and a pseudo-second-order rate equation (eqn (3)) to the adsorption data to understand the time dependent adsorption process. The pseudo-first-order model is expressed as | 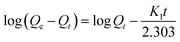 | (2) |
and the pseudo-second-order model can be expressed as | 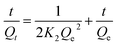 | (3) |
where K1 and K2 are the pseudo-first-order Lagergren rate constant (min−1) and pseudo-second-order rate constant (g mg−1 min−1) of adsorption, and Qe and Qt are the amounts of GO adsorbed (mg g−1) at equilibrium and at time t (min).
Pseudo-first-order and pseudo-second-order kinetic models of GO adsorption onto cement were fitted and are shown in Fig. 5 and the simulation results are also listed in Table 2. The results show that the linear correlation coefficients (R2) for the pseudo-second-order kinetic model were closer to 1 than for the pseudo-first-order model. The results suggest that the adsorption kinetics of GO on cement are fitted well with the pseudo-second-order model. From Table 3, it is seen that the experimental and calculated values of the adsorption capacities are in close agreement. These results indicate that the nature of adsorption is a chemical-controlled process.24
 |
| Fig. 5 The pseudo-first-order kinetics (a) and pseudo-second-order kinetics (b) for GO adsorption onto cement. | |
Table 2 The coefficients of associations of pseudo-first-order (eqn (2)) and pseudo-second-order (eqn (3)) models
C
0 (mg L−1) |
250 |
300 |
350 |
400 |
450 |
Eqn (2)
|
0.926 |
0.883 |
0.914 |
0.963 |
0.976 |
Eqn (3)
|
0.998 |
0.978 |
0.980 |
0.979 |
0.978 |
Table 3 Summary of the kinetic parameters as obtained from the pseudo-second-order rate equation
C
0 (mg L−1) |
Q
exp (mg g−1) |
Q
cal (mg g−1) |
K
2 (g mg−1 min−1) |
250 |
147.96 |
148.23 |
6.53 × 10−4 |
300 |
179.71 |
182.02 |
2.09 × 10−4 |
350 |
196.40 |
198.91 |
1.94 × 10−4 |
400 |
218.46 |
221.03 |
9.20 × 10−5 |
450 |
250.08 |
253.71 |
9.86 × 10−5 |
To study the mode of interaction between GO and cement, the adsorption equilibrium was studied with the help of the Langmuir and Freundlich isotherm models. The Langmuir adsorption formula is:
| 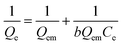 | (4) |
where
Qe is the adsorption amount (mg g
−1),
Qem is the saturated adsorption amount (mg g
−1),
b is the constant depending upon the nature of the adsorbate and adsorbent, and
Ce represents the equilibrium concentration (mg L
−1).
The Freundlich adsorption formula is:
| 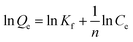 | (5) |
where
Qe is the adsorption amount (mg g
−1),
Ce represents the equilibrium concentration (mg L
−1), and
Kf and
n are the constants depending upon the adsorption capacity.
The adsorption isotherms of GO on cement following the linearized Langmuir and Freundlich models are shown in Fig. 6, and the simulation results are all listed in Table 4. And we have also fitted the experimental result with Langmuir–Freundlich models (Fig. S3†). The experimental results were fitted better with the Freundlich model (R2 = 0.991) than the Langmuir model (R2 = 0.950). This result implied that the adsorption of GO on cement is mainly a multilayer type. It also indicated that GO adsorption was not just physical adsorption on the adsorbent but chemical reactions were also very much involved in this process.25,26
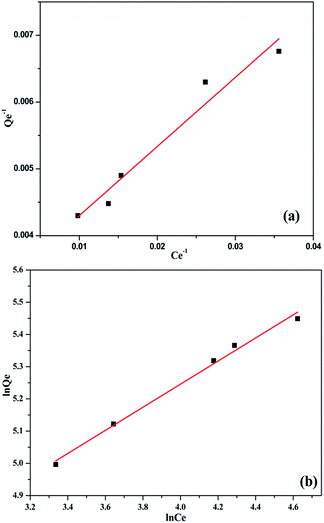 |
| Fig. 6 The Langmuir (a) and Freundlich (b) isotherm models for the adsorption of the GO nanosheets on cement. | |
Table 4 Parameters of Langmuir and Freundlich models for adsorption of the GO on cement
Langmuir |
Freundlich |
B
|
Q
em (mg g−1) |
R
2
|
K
f
|
n
|
R
2
|
0.03 |
305.81 |
0.950 |
45.24 |
2.79 |
0.991 |
3.4 FTIR analysis
In order to research the chemical reactions between GO and cement, FTIR analysis was conducted. The FTIR spectra of the pristine GO and cement adsorption by GO nanosheets are shown in Fig. 7. The absorption band at ∼1740 cm−1 could be attributed to the C
O stretching of –COOH. The bands at ∼1580 cm−1 and ∼1420 cm−1 resulted from –COO− (carboxylate), and the weak absorption band at ∼694 cm−1 could be explained by the out of plane deviational vibration of –COO−.27–30 As noted in Fig. 7, the C
O stretching of –COOH in GO was absent in the GO treated cement. The peak from 1450 cm−1 to 1575 cm−1 of cement adsorption by GO nanosheets was also nonexistent in GO at the same time. This is because the H+ in the carboxyl groups were substituted by metal cations, generating –COO−. The FTIR results indicated that the chemical reactions of –COOH in GO produced a new product containing –COO− in the cement adsorption by GO nanosheets system.
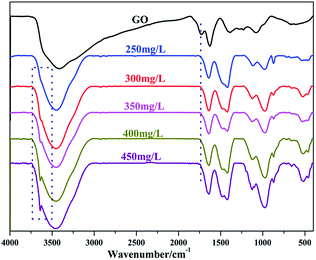 |
| Fig. 7 FTIR analyses of pristine GO and cement adsorption by GO nanosheets at different concentrations. | |
3.5 Adsorption layer thickness
As the Si and Ca elements are contained in the mineral matter of cement but are not contained in GO nanosheets, Si and Ca can be used as marker elements for the measurement of the thickness of GO nanosheets. The weakening degree of Si 2p and Ca 2p photoelectrons that pass through the GO nanosheets on the cement surface is used to approximately calculate the thickness of the GO nanosheets. The adsorption layer thickness of the GO nanosheets on the surface of the cement was calculated as follows:31,32 | I(b) = I0 exp[−b/λ(Ek)] | (6) |
where I0 is the initial photoelectron intensity, b is the adsorption layer thickness (nm), I(b) is the photoelectron intensity through the adsorption layer with thickness b, and Ek is a constant related to the electron kinetic energy, λ(Ek), which is called the photoelectron inelastic scattering free path, calculated by | λ(Ek) = 2170Ek−2 + 0.72(aEk)−1/2 | (7) |
where Ek is the photoelectron kinetic energy (eV), and a is the monoatomic layer thickness (nm), which is calculated bywhere M is the relative atomic mass or relative molecular mass, n is the number of atoms in the molecule, N is Avogadro’s constant, and ρ is the material density (kg m−3).
The Si 2p and Ca 2p XPS spectra of the cement surface with or without GO nanosheets are shown in Fig. 8. These spectra show that the Si 2p and Ca 2p photoelectron intensities of the cement decreased to varying degrees after adsorption of GO nanosheets. It is possible to calculate I(0) and I(t) by measuring the attenuation of the Si 2p and Ca 2p photoelectron intensities and thus to calculate the adsorption layer thickness via eqn (6)–(8). Table 5 shows the adsorption layer thickness of GO nanosheets on the cement. As can be seen in Table 5, the adsorption layer thickness of the GO nanosheets on the cement was 11.35 nm when Si was used as the marker element; when Ca was used as the marker element the adsorption layer thickness of the GO nanosheets on the cement was 8.97 nm. From these calculations, we can reach the conclusion that the adsorption layer thickness of the GO nanosheets on the cement was about 10.16 nm. The AFM result in Fig. 1(b) shows that the thickness of the GO nanosheets was about 0.83 nm. Therefore, there are around 9 layers of GO nanosheets adsorbed on the cement surface.
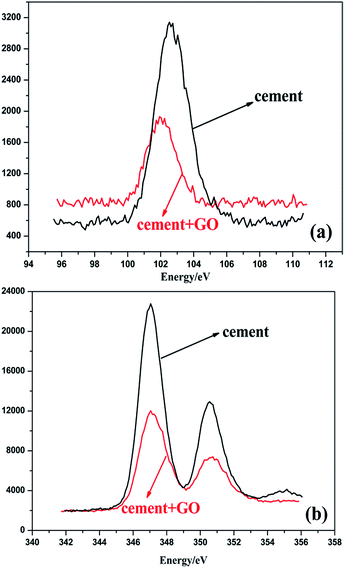 |
| Fig. 8 The Si 2p (a) and Ca 2p (b) XPS spectra of the cement surface with or without GO nanosheets. | |
Table 5 Adsorption layer thickness of GO nanosheets on cement surface
Marker element |
Thickness of adsorbed film (nm) |
Average thickness (nm) |
Si |
11.35 |
10.16 |
Ca |
8.97 |
4 The adsorption process of the GO nanosheets on cement
As shown in Fig. 9(a), the GO nanosheets adsorbed onto the surface of the cement; the van der Waals force between the GO layers made the cement particles come close to each other, which was the main reason for the negative influence on the fluidity of the cement. Also, as represented in Fig. 9(b), the chemical process (substitution reaction) was present in the adsorption system which occurred between –COOH in the GO nanosheets and metal ions in the hydration product, producing –COO−.
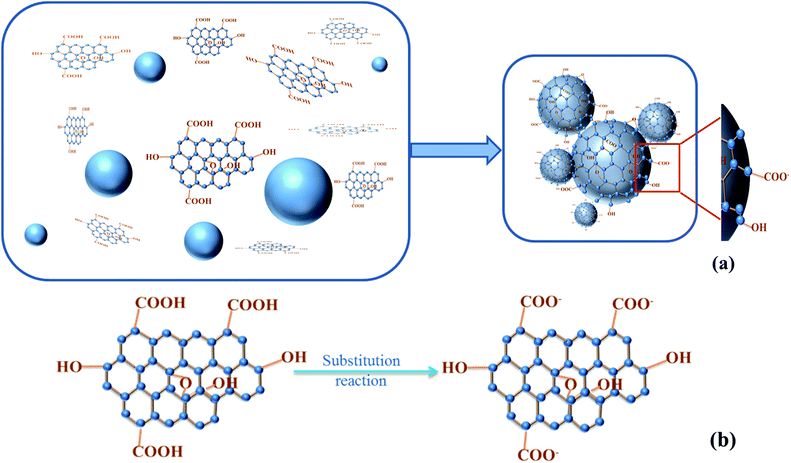 |
| Fig. 9 (a) Adsorption schematic of GO nanosheets on the cement surface. (b) The substitution reaction of GO in the adsorption system. | |
5 Conclusion
GO nanosheets have a strong adsorption ability on the cement surface. The adsorption amount increased with the concentration of the GO nanosheets. And the experimental data of the equilibrium of the adsorption amount matched well with the Freundlich isotherms. The adsorption mechanism of GO on the cement included chemical processes. The –COOH on the edge of the GO nanosheets reacted with the metal cations in the cement hydration system, generating –COO−. In addition, the adsorption layer thickness of the GO nanosheets on the cement was about 10.16 nm, and there were around 9 layers of GO nanosheets adsorbed on the cement surface.
Notes and references
- L. K. Aggarwal, P. C. Thapliyal and S. R. Karade, Construct. Build. Mater., 2007, 21, 379–383 CrossRef.
- Z. Y. Lu, D. S. Hou, L. S. Meng, G. X. Sun, C. Lu and Z. J. Li, RSC Adv., 2015, 5, 100598–100605 RSC.
- D. Carnelli, R. Libanori, B. Feichtenschlager, L. Nicoleau, G. Albrecht and A. R. Studart, Cem. Concr. Res., 2015, 78, 245–251 CrossRef CAS.
- S. Biswas, S. Vinnakota and S. Roy, RSC Adv., 2016, 6, 7933–7940 RSC.
- S. J. Chen, F. G. Collins, A. J. N. Macleod, Z. Pan, W. H. Duan and C. M. Wang, IES Journal Part A: Civil and Structural Engineering, 2011, 4, 254–265 CrossRef.
- A. Sedaghat, M. K. Ram, A. Zayed, R. Kamal and N. Shanahan, Open J. Compos. Mater., 2014, 4, 10 Search PubMed.
- Y. W. Zhu, S. Murali, W. W. Cai, X. S. Li, J. W. Suk, J. R. Potts and R. S. Ruoff, Adv. Mater., 2010, 22, 3906–3924 CrossRef CAS PubMed.
- S. Stankovich, D. A. Dikin, R. D. Piner, K. A. Kohlhaas, A. Kleinhammes, Y. Y. Jia, Y. Wu, S. T. Nguyen and R. S. Ruoff, Carbon, 2007, 45, 1558–1565 CrossRef CAS.
- S. Chuah, Z. Pan, J. G. Sanjayan, C. M. Wang and W. H. Duan, Construct. Build. Mater., 2014, 73, 113–124 CrossRef.
- Z. Pan, L. He, L. Qiu, A. H. Korayem, G. Li, J. W. Zhu, F. Collins, D. Li, W. H. Duan and M. C. Wang, Cem. Concr. Compos., 2015, 58, 140–147 CrossRef CAS.
- S. H. Lv, Y. Y. Ma, C. C. Qiu, T. Sun, J. J. Liu and Q. F. Zhou, Construct. Build. Mater., 2013, 49, 121–127 CrossRef.
- M. Saafi, L. Tang, J. Fung, M. Rahman and J. Liggat, Cem. Concr. Res., 2015, 67, 292–299 CrossRef CAS.
- X. G. Li, W. Wei, H. Qin and Y. H. Hu, J. Phys. Chem. Solids, 2015, 85, 39–43 CrossRef CAS.
- S. Sharma and N. C. Kothiyal, RSC Adv., 2015, 5, 52642–52657 RSC.
- J. Chen, D. Zhao, H. Y. Ge and J. Wang, Construct. Build. Mater., 2015, 84, 66–72 CrossRef.
- K. Gong, Z. Pan, A. H. Korayem, L. Qiu, D. Li, F. Collins, C. M. Wang and W. H. Duan, J. Mater. Civ. Eng., 2014, 27, A4014010 CrossRef.
- A. P. Singh, M. Mishra, A. Chandra and S. K. Dhawan, Nanotechnology, 2011, 22, 465701 CrossRef PubMed.
- Y. Shang, D. Zhang, C. Yang, Y. Y. Liu and Y. Liu, Construct. Build. Mater., 2015, 96, 20–28 CrossRef.
- A. Mohammed, J. G. Sanjayan, W. H. Duan and A. Nazari, Construct. Build. Mater., 2015, 84, 341–347 CrossRef.
- D. Ji, Z. Y. Luo, M. He, Y. J. Shi and X. L. Gu, Cem. Concr. Res., 2012, 42, 1199–1206 CrossRef CAS.
- S. Kundu, S. S. Kavalakatt, A. Pal, S. K. Ghosh, M. Mandal and T. Pal, Water Res., 2004, 38, 3780–3790 CrossRef CAS PubMed.
- Q. P. Ran, P. Somasundaran, C. W. Miao, J. P. Liu, S. S. Wu and J. Shen, J. Dispersion Sci. Technol., 2010, 31, 790–798 CrossRef CAS.
- K. Yoshioka, E. Tazawa, K. Kawai and T. Enohata, Cem. Concr. Res., 2002, 32, 1507–1513 CrossRef CAS.
- B. C. Yang, Y. Z. Guo, S. R Zhang, T. Wen and C. Zhao, RSC Adv., 2014, 4, 64771–64780 RSC.
- D. Dinda, A. Gupta and S. K. Saha, J. Mater. Chem. A, 2013, 1, 11221–11228 CAS.
-
R. E. Treybal, Mass transfer operations, McGraw-Hill Book Company, Singapore, 3rd edn, 1981, p. 35 Search PubMed.
- K. V. P. M. Shafi, A. Ulman, X. Z. Yan, N. L. Yang, C. Estournès, H. White and M. Rafailovich, Langmuir, 2001, 17, 5093–5097 CrossRef CAS.
- C. Santhosh, P. Kollu, S. Doshi, M. Sharma, D. Bahadur, M. T. Vanchinathan, P. Saravanand, B. S. Kime and A. N. Grace, RSC Adv., 2014, 4, 28300–28308 RSC.
- M. Wang, R. M. Wang, S. R. Zheng, S. Farhan, H. Yao and H. Jiang, Cem. Concr. Res., 2015, 76, 62–69 CrossRef CAS.
- M. Wang, R. M. Wang, H. Yao, S. Farhan, S. R. Zheng, Z. J. Wang, C. C. Du and H. Jiang, Construct. Build. Mater., 2016, 111, 710–718 CrossRef.
- H. M. Lou, K. Ji, H. K. Lin, Y. X. Pang, Y. H. Deng, X. Q. Qiu, H. B. Zhang and Z. G. Xie, Cem. Concr. Res., 2012, 42, 1043–1048 CrossRef CAS.
- M. T. Brumbach and J. C. Woicik, Surf. Interface Anal., 2012, 44, 1379–1384 CrossRef CAS.
Footnote |
† Electronic supplementary information (ESI) available. See DOI: 10.1039/c6ra10902k |
|
This journal is © The Royal Society of Chemistry 2016 |
Click here to see how this site uses Cookies. View our privacy policy here.