DOI:
10.1039/C6RA10711G
(Paper)
RSC Adv., 2016,
6, 65072-65080
Sulfonated nanocrystal cellulose/sulfophenylated poly(ether ether ketone ketone) composites for proton exchange membranes
Received
25th April 2016
, Accepted 1st July 2016
First published on 4th July 2016
Abstract
Nanocomposites were prepared with sulfonated nanocrystal cellulose (sNCC) and sulfophenylated poly(ether ether ketone ketone) (Ph-SPEEKK) for studying proton exchange membranes. The properties, including proton conductivity, mechanical properties, water uptake and swelling ratio were thoroughly investigated. The proton conductivity of the sNCC/Ph-SPEEKK composite membrane was much higher than that of pure Ph-SPEEKK in the range of 30–90 °C when the sNCC ratio was less than 10%. The presence of the hydroxyl and sulfonic acid groups on the sNCC was supposed to benefit the network formation via hydrogen bonds for the proton conduction. In addition, the mechanical properties of the composite membranes were much improved compared with those of the pure Ph-SPEEKK membrane. And the swelling ratio of the composite membranes was acceptable for the application. It was proved that the incorporation of sNCC into the sulfonated polymer matrix as a component to enhance the performance of the proton exchange membrane is one of the promising preparation strategies.
Introduction
Proton exchange membrane fuel cells (PEMFCs) have gained much interest in recent years because of their certain potential advantages, such as low operating temperatures, portable applications, power generation, high efficiency, etc.1,2 The key component of PEMFC is a dense proton-exchange membrane (PEM), which determines the efficiency of PEMFCs.3,4 As a representative of the most promising proton-conducting polymers, Nafion® showed excellent performances, such as high ionic conductivity and excellent chemical stability.5 However, their high cost, low proton conductivity over 80 °C and high methanol permeability hinder their widespread application.6–8 Thus, sulfonated aromatic main chain polymers including sulfonated polyimides, sulfonated polybenzimidazoles, and sulfonated poly(arylene ether ketone)s, has become promising alternatives owning to their good thermal stability, appropriate mechanical properties and high proton conductivity.9–12
Sulfonated poly(arylene ether ketone)s (SPAEKs) have been widely investigated for the using as PEMs because of several groups.13–16 It was found the high proton conductivity was maintained by the high sulfonic acid group amount on the PAEK molecular chains. However, the increasing number of sulfonic acid groups would lead to the loss of the mechanical strength and dimensional stability under the circumstances of high temperature and high humidity.17 Extensive efforts to well get the balance between proton conductivity and dimensional stability are required. Some strategies, such as incorporation of inorganic nano-size particles and construction of crosslinking networks, were applied to modify the overall performance of SPAEK-type PEMs.18
Cellulose, one of the most abundant natural biopolymers,19 is a polysaccharide consisting of a linear chain of several hundred to many thousands of β(1–4) linked D-glucose units. As a biobased reinforcing nanofiller, nanocrystal cellulose (NCC) has been gained increasing interest due to its excellent mechanical properties, high surface area, high crystallinity and unique optical properties.20,21 It could be produced by a mechanical treatment or acid hydrolysis of cellulosic biomass such as ramie, cotton, jute and microcrystalline cellulose (MCC).22,23 It can be typically a rigid rod-shaped nanocrystalline cellulose domain (whisker) with 1–100 nm in diameter and tens to hundreds of nanometers in length.23,24 There are rich amount of hydroxyl groups (–OH) on the NCC surface.25 When NCC was produced by sulfonic acid hydrolysis from MCC, it could be sulfonated simultaneously, and thus sulfonated nanocrystal cellulose (sNCC) can be prepared.23 The composite PEMs incorporated with sNCC could be expected to present excellent mechanical properties and proton conductivity resulted by the stronger hydrogen bond with water, which is helpful to the proton transfer.
As a member of SPAEKs, sulfophenylated poly(ether ether ketone ketone) (Ph-SPEEKK) have some attractive properties, including simple preparation process, high proton conductivity and good mechanical properties.2,13 In this work, sNCC was introduced to prepare the composite PEMs as an attempt to further enhance the performance of Ph-SPEEKK. The presence of the hydroxyl groups and sulfonic acid groups on sNCC was supposed to benefit the formation of “pathway” between sNCC and Ph-SPEEKK for proton transportation. Additionally, the introduction of the sNCC was expected to improve the mechanical properties and the dimensional stability of the membranes.
Experimental
Materials
Cellulose microcrystalline (25 μm, powder) was purchased from Admas Company. K2CO3 (Beijing Chemical Reagent, China) was dried at 120 °C for 24 h and ground into fine powder before use. Sulfuric acid (95–98%) and toluene were obtained from Beijing Chemical Reagent, China. Potassium carbonate was supplied by Beijing Chemical Reagent, and dried at 120 °C in vacuum for 12 h prior to use. Dimethyl sulfoxide (DMSO) and tetramethylene sulfone (TMS) were purchased from Tianjin Chemical Reagent, China. 2-Phenylhydroquinone was purchased from Aldrich. 1,4-Bis(4-fluorobenzoyl)benzene was offered by Changchun Jilin University Special Plastic Engineering Research Co., Ltd. All other organic solvents were obtained from commercial sources and purified by conventional methods.
The sNCC was prepared by sulfuric acid treatment of microcrystalline cellulose.23 The 20 g of cellulose microcrystalline powder was put into 350 ml of 64% sulfuric acid to get a solution. After stirring at 45 °C for 3 h, 5 times amount of water was added to terminate the reaction. The excess acid was removed by centrifugation, and the residual acid was further removed by dialysis with deionized water. The suspensions were freeze-dried for 48 h to get sulfonated NCC.
Synthesis of Ph-SPEEKK
2-Phenylhydroquinone (0.015 mol, 2.8795 g), potassium carbonate (2.2770 g), sulfolane (24 ml), and toluene (12 ml) were introduced into a 100 ml three-neck round-bottom flask with a Dean–Stark trap and a condenser under nitrogen protection. The reaction mixture was kept stirring at 140 °C for 3 h. After the toluene was drained from the system, the reaction temperature was increased to 180 °C. Then 2 ml of sulfolane was added to the reaction solution after 5 h. An hour later, the viscous solution was slowly poured into 800 ml of distilled water with stirring to precipitate the produced polymer. The product was shattered and then washed in deionized water and ethanol for three times to remove the inorganic salts, solvents and monomer residues. The obtained polymer was dried at 120 °C in a vacuum oven overnight. The synthetic scheme and the structure of Ph-SPEEKK are shown in Scheme 1.
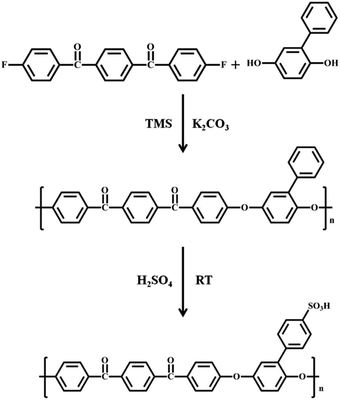 |
| Scheme 1 Synthesis of the sulfophenylated poly(ether ether ketone ketone) (Ph-SPEEKK). | |
Dried product (6.8 g) and 100 ml of sulfuric acid were added into a three-neck bottle and stirred at room temperature for 12 h. The viscous solution was cooled and precipitated into ice/water. The product was washed with distilled water several times until the PH value of drained water reached a value of 7.0. The obtained sample was dried at 80 °C under vacuum for 24 h.
Preparation of sNCC/Ph-SPEEKK composite membranes
sNCC/DMSO suspension was prepared by stirring, and then various amount of Ph-SPEEKK powder was added into sNCC/DMSO suspension. A mixture solution of sNCC/Ph-SPEEKK in DMSO was formed after stirring at 50 °C for 8 h. The prepared solution was cast onto a horizontal glass plate, and carefully dried at 80 °C for 24 h. After drying at 100 °C under vacuum for another 24 h, flexible membranes were obtained by immersing the membranes on the glass in hot water.
The sNCC/Ph-SPEEKK composite membranes were named as sNCC10 (sNCC weight ratio was 10%), sNCC8 (sNCC weight ratio was 8%), sNCC6 (sNCC weight ratio was 6%), sNCC4 (sNCC weight ratio was 4%) and sNCC2 (sNCC weight ratio was 2%), respectively.
Characterization
Chemical structure analysis. Fourier transform infrared spectroscopy (FTIR, Nicolet iS10, USA) was used to characterize their chemical structure and compositions of the thin films. The measurements were taken in the wavenumber range of 4000–550 cm−1 at a resolution of 32 cm−1.1H NMR spectrum was obtained on a Bruker 510 spectrometer (500 MHz) using DMSO-d6 as solvent. DMSO signal at 2.51 ppm was used as chemical shift reference. 13C NMR spectrum was acquired on a Bruker AVANCE III HD 500 with the frequency of 300 MHz also using DMSO-d6 as solvent. DMSO signal at 39.85 ppm were used as chemical shift reference. The 1H and 13C NMR result of Ph-SPEEKK were in well agreement with its expected structure, as shown in Fig. 1.
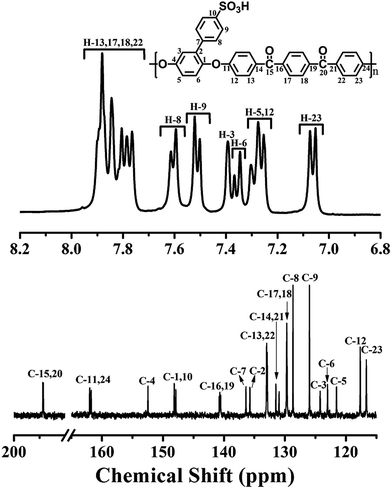 |
| Fig. 1 1H NMR and 13C spectrum of the prepared Ph-SPEEKK. | |
1H NMR (DMSO-d6, ppm): δ 7.97–7.70 (m, 4H), 7.60 (d, J = 7.8 Hz, 1H), 7.51 (d, J = 7.9 Hz, 1H), 7.43–7.16 (m, 3H), 7.06 (d, J = 8.5 Hz, 1H).
X-ray Photoelectron Spectroscopy (XPS) characterization was performed with an ESCALABMKLL instrument from VG. SCIENTIFIC. LTD of England to measure the sulfonic group amount on the obtained sNCC. The X-ray source type was A1 K, and the analysis mode was CAE (pass energy 100.0 eV).
Water uptake and swelling ratio measurements. All membranes used were vacuum dried at 120 °C for 24 h until a constant weight was obtained before measurement. Weights and lengths of dry and wet membranes were measured. The polymer membranes were immersed in deionized water at various temperatures for 2 h before the weights and the lengths of dry membranes were measured. The lengths and weights of the swollen membranes after the water immersion were also measured. The water on the membrane surface was quickly removed by wiping with tissue paper. The water uptake in weight ratio was calculated from the weight variation against the initial weight, and the equation is shown as following:
Water uptake (%) = (Wwet − Wdry)/Wdry × 100% |
where Wwet and Wdry are the weights of wet and dry membrane, respectively.The swelling ratio (%) was calculated from:
Swelling ratio (%) = (Lwet − Ldry)/Ldry × 100% |
where
Lwet and
Ldry are the lengths of wet and dry membrane samples, respectively.
Ion-exchange capacity (IEC) of membranes. The ion-exchange capacity (IEC) of membrane was determined by acid–base titration. The membranes with similar weight and size were immersed in 1 M NaCl solution for 24 h at room temperature to permit the complete exchange of H+ ions with Na+ ions. The released protons in the solution were titrated with a 0.05 M NaOH aqueous solution using phenolphthalein as an indicator. The IEC values were calculated by the following formula:
IEC (mequiv. g−1) = VNaOH × CNaOH/Wmembrane |
where VNaOH and CNaOH were volume and molarity of NaOH solution, respectively, and Wmembrane was the weight of dry membrane.
Oxidative stability. Small pieces of the membrane samples were soaked in Fenton's reagent (3% H2O2 containing 2 ppm FeSO4) at 80 °C. The oxidative stability is measured by recording the dissolution time when the membrane samples disappear and the retained weights of membranes after treating in Fenton's reagent for 1 h.
Mechanical properties. The mechanical properties of the polymer membranes were evaluated at room temperature by using a SHIMADZU AG-I 1 KN instrument at a tensile speed of 2 mm min−1. The size of samples was 50 mm × 5 mm. Each membrane was measured both at dry and wet state. Five specimens were measured for every membrane.
Proton conductivity. The proton conductivity of membranes was measured under various conditions of temperature by a four-electrode ac impedance method and the frequency range was between 10 Hz and 106 Hz using a Princeton Applied Research/EG&G Model 273 Potentiostat/Galvanostat. The samples were soaked in distilled water for at least 24 h after cutting into desired size (45 mm × 10 mm). The conductivity measurement as function of temperature between 30 and 100 °C was performed with the cell immersed in distilled water. The proton conductivity was calculated by the following formula:
where L is the distance between the two electrodes, R is the measured resistance and A is the cross-sectional area of the membrane, respectively.
Thermal analysis. Thermal gravimetric analysis (TGA) was carried out to evaluate the thermal stability of the membranes using a PerkinElmer Pyris-1 thermal analyzer system. Before analysis, the films were kept in the TGA furnace at 90 °C under nitrogen atmosphere for 30 min in order to remove the water of the samples. The samples were cooled to 70 °C at the rate of 20 °C min−1, and then reheated to 700 °C at 10 °C min−1 in nitrogen atmosphere.
Morphology characterization. A JEOL JEM-1011 transmission electron microscope (TEM) with an accelerating voltage of 100 kV was used to study the morphology of prepared sNCC and composite membrane. The sNCC suspension and mixed liquor containing 10 ml of DMSO, 0.1 g of Ph-SPEEKK and 0.0008 g of sNCC were ultrasonic processed, respectively. Then, one drop of solution were dropped on the carbon coated TEM copper grid and blotted. Staining was not applied.The morphology of the membranes was studied using a scanning electron microscope (SEM), Shimadzu SSX-550 super scan SEM with 15 kV acceleration voltages. The samples were fractured in liquid nitrogen, and the fresh fractured surfaces were vacuum coated with Au to avoid charging prior to SEM examination.
X-ray diffraction measurement (XRD). The X-ray diffraction of the dry membranes and sNCC was measured on a RINT2000 vertical goniometer diffractometer with Cu Kα tube at 40 kV and 100 mA. The measurement temperature was 30 °C. Diffraction profiles were acquired in the 2θ range of 5–40° with the rate of 2° min−1.
Results and discussion
Morphology of sNCC
The TEM image of the prepared sNCC is shown in Fig. 2. The shape of the sNCC was rod. Its length was around 200 nm and diameter was less than 100 nm.
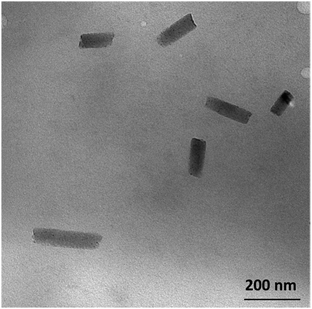 |
| Fig. 2 TEM image of sNCC. | |
FTIR spectroscopy for sNCC and membranes
Fig. 3 shows FTIR spectra of sNCC, Ph-SPEEKK and sNCC/Ph-SPEEKK membranes. The peaks observed in the region around 3124–3527 cm−1 were assigned to be the stretching vibrations of OH groups. The band around 2902 cm−1, was associated with aliphatic C–H stretches. The peak observed in the spectra of all samples at 1025 cm−1 was due to the C–O–C pyranose ring stretching vibration. The bands at ∼1155 and 1105 cm−1 were ascribed to be the C–C band and C–O–C glycosidic ether linkages, respectively.26 All these are the characteristic absorption peaks of sNCC from FTIR spectroscopy. Additionally, at 1162 cm−1 and 675 cm−1, there were bands that corresponded to the stretching of the sulfonic groups, which proved the NCC was sulfonated successfully.
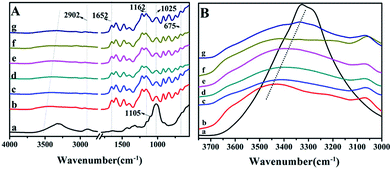 |
| Fig. 3 FTIR spectra of sNCC, Ph-SPEEKK and the composites (A). The enlarged parts in the range of 3000–3750 cm−1 (B): sNCC (a), Ph-SPEEKK (b), sNCC2 (c), sNCC4 (d), sNCC6 (e), sNCC8 (f) and sNCC10 (g). | |
In the FTIR spectra of Ph-SPEEKK and the composite membranes, the characteristic absorption of carbonyl groups at 1652 cm−1, and the characteristic absorption of sulfonic group at 1162 cm−1 and 675 cm−1 could be clearly observed. Compare to Ph-SPEEKK, the peak around 3432 cm−1 moved to lower wavenumbers with the sNCC insertion content, which proved the stronger intermolecular hydrogen bond between Ph-SPEEKK and sNCC happened. The formed hydrogen bond averaged the density of electron cloud, and thus decreased the stretching vibration frequency. Furthermore, the intermolecular hydrogen bond could be affected by the sNCC content. Therefore, the higher sNCC content, the lower hydrogen bond peak wavenumbers of the composite membrane presented.
Fig. 4 shows the XPS profile of the sNCC. The S2p peak presented on the XPS profile also proved the presence of –SO3H on the sNCC prepared by sulfuric acid hydrolysis of microcrystalline cellulose (MCC). And the content of –SO3H (0.202 mmol g−1) could be obtained by calculation using the following equation:
where
nS and
M represents the amount of substance of S in a repeating unit (C
6H
10O
5),
M represents the quality of a repeating unit.
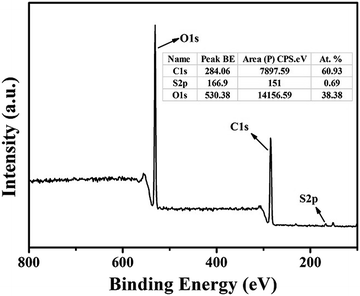 |
| Fig. 4 XPS profile of sNCC. | |
Water sorption and swelling ratio of membranes
Water uptake of the membrane is a critical factor for the performance of PEM materials. Water is the main vehicle by which protons are transported across the membranes.27 Fig. 5(a) presents the water uptake values of the membranes at different temperature. It can be obviously observed that the water uptake increased with elevated temperature, which should be attributed to the increased water molecule mobility.
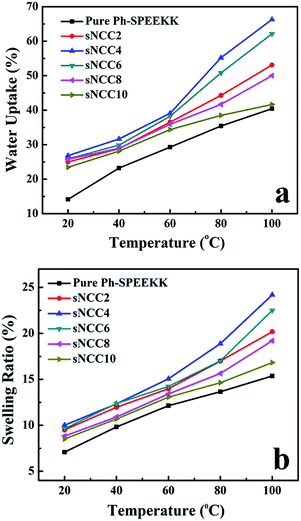 |
| Fig. 5 Water uptake (a) and swelling ratio (b) of the membranes at different temperature. | |
On the other hand, the composite membranes always exhibited higher level of water uptake than pure membrane. For example, the water uptake of sNCC4 was 55% at 80 °C, which was much higher than that of the pure Ph-SPEEKK membrane (35%). This should be associated with the introduction of sNCC which has abundant hydroxyl groups and sulfonic acid groups on its surface. Both hydroxyl groups and sulfonic acid groups can form hydrogen bond with the water molecules. In addition, the strong hydrogen bond network between sNCC and Ph-SPEEKK could bound more water molecules, too. Thus, the composite membrane water uptake ratio was apparently increased with the sNCC insertion.
Furthermore, the water uptake of the composite membrane increased with the sNCC ratio when the ratio was less than 4%, and then began to decrease with the sNCC ratio, as shown in Fig. 5(a). It seemed that sNCC began to aggregate together when its ratio reached 6%, which resulted in the lower specific surface area of sNCC, and thus the water absorption was also affected.
Dimensional stability is one of important parameters and crucial for the PEMs to operate under hot and humid circumstances. One of the study aims is to prepare the PEMs with high proton conductivity but low-swelling. The volume swelling ratios were also studied and displayed in Fig. 5(b). It is shown the sNCC introduction could have influence on the swelling ratio of the composite membranes when the water absorption of the composite membrane was higher than that of the pristine membrane, as shown in Fig. 5(a). Satisfactorily, the swelling ratio of all the membranes was less than 20% even at 80 °C, though sNCC/Ph-SPEEKK composite membranes had higher swelling ratio than pristine Ph-SPEEKK. This proved that the sulfonated NCC could form network with the Ph-SPEEKK matrix by the hydrogen bond between hydroxyl groups on sNCC surface and the sulfonic acid groups on Ph-SPEEKK, which could restrict the matrix motion and impede the swelling of the membranes.
Oxidative stability and ion-exchange capacity (IEC) of membranes
To evaluate the capability of withstanding stronger oxidizing environment during the fuel cell operation of the polymer membranes, the oxidative stability of the membrane samples were evaluated by the weight loss after treatment in Fenton's reagent at 80 °C for 60 min. The time that the membranes started to disintegrate into pieces in Fenton's reagent at 80 °C was also recorded. The testing results are summarized in Table 1. The mass-lose rate of these composite membranes was still retained above 91% after treatment in Fenton's reagent at 80 °C for 1 h, and they were not dissolved within 5 h. The result showed that the oxidative stability of sNCC/Ph-SPEEKK was acceptable compared with the formal results in the other reports.28
Table 1 IEC, thermal property and oxidative stability of the membranes
Membrane |
IEC mmol g−1a |
Td5b °C |
Td10c °C |
Oxidative stability |
RWd (%) |
Te (h) |
Experimental values of ion-exchange capacity. Temperature at 5% weight loss. Temperature at 10% weight loss. Retained weights of membranes after treating in Fenton's reagent for 1 h at 80 °C. The dissolved time of polymer membranes in Fenton's reagent. |
Ph-SPEEKK |
1.979 |
359 |
404 |
98 |
>5 |
sNCC2 |
2.034 |
354 |
403 |
94 |
>5 |
sNCC4 |
2.161 |
347 |
402 |
94 |
>5 |
sNCC6 |
2.145 |
338 |
389 |
92 |
>5 |
sNCC8 |
2.131 |
319 |
378 |
93 |
>5 |
sNCC10 |
2.122 |
311 |
376 |
91 |
>5 |
Ion-exchange capacity (IEC) plays an important role in determining the proton conductivity of the polymer electrolyte membranes.12 The values of IEC are compiled in Table 1. The experimental IEC values of the membranes were in a range of 1.979 to 2.161. It was found that the nanocomposite membranes exhibited higher IEC values than pure Ph-SPEEKK membrane, and the sNCC4 presented the highest IEC value of 2.161. This should be caused by the –OH and –SO3H groups on the sulfonic acid modified sNCC.
Proton conductivity of pure and composite membranes
The proton conductivity of the polymer membranes is closely related to several parameters such as position and number of ionic groups, acidity, molecular structures and membrane morphology.29 The proton conductivity of the membranes measured at different temperatures is shown in Fig. 6. The conductivities increased with the increasing of the temperature for each sample, which was attributed to the enhanced charge transport at higher temperatures.24 It was also noteworthy that the proton conductivity of the composite membranes except sNCC10 was much higher than that of Ph-SPEEKK in the range of 30–90 °C. In particular, the proton conductivity of composite membrane with 4% sNCC could reach 0.115 S cm−1 at 80 °C, which was 47% higher than that of pure membrane (0.078 S cm−1).
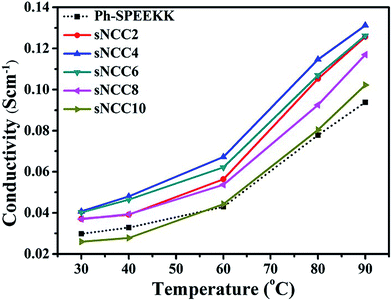 |
| Fig. 6 Proton conductivity of the membranes at different temperature. | |
This result was agreed with the IEC value result, and might be associated with two factors. One is that the addition of the sulfonated sNCC to Ph-SPEEKK can further enhance its proton conductivity with the introduction of additional sulfonic acid group and hydroxyl group. Another reason was the abundant hydroxyl groups on sNCC surface can increase composite membranes' water absorption capacity, as shown in Fig. 5(a). The water molecules are the carriers of the proton transfer to form hydrated ions according to “Vehicle” mechanism.30 In the “vehicle" mechanism, the proton diffuses together with a vehicle, e.g., as H3O+, where the counter-diffusion of non-protonated vehicle, e.g., H2O, promotes the net transportation of protons. The more water molecules exist in the membrane, the higher proton conductivity could be achieved. Furthermore, hydrogen bonding formed by the sulfonic groups and hydroxyl groups from SPAEKs and sNCC could produce more continuous proton transport channel, and would be advantageous to the proton transfer following “Grotthuss” mechanism, too.31,32 “Grotthuss” mechanism explicated that the proton diffused throughout the entire hydrogen bond network of water at a rate considerably greater than that of conventional diffusion. In our case, the proton jumped from one hydrogen bond system formed by –SO3H, –OH and water to another.33 The more –SO3H and –OH amounts, the higher temperature, the faster diffusing rate of proton. Accordingly, a suggested mechanism of proton conducting is illustrated in Fig. 7.
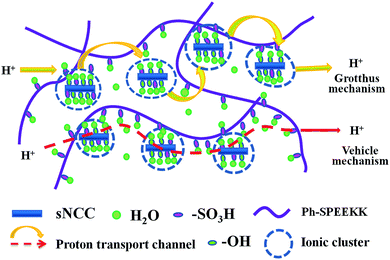 |
| Fig. 7 The suggested proton transport path in the composite membranes. | |
On the other hand, when the sNCC content was too high, the possible sNCC aggregation resulted by the rich hydroxyl groups on sNCC would happen and affect the proton transportation, which led to a proton conductivity decrease. It seemed that 4% sNCC could afford a uniformly distributed sNCC in the composite membrane which could bring forth a efficient network between sNCC and Ph-SPEEKK with high proton conductivity. When sNCC ratio was higher than 4%, conductivity began to decrease, and it became comparable with pristine membrane when sNCC ratio increased to 10%.
Thermal properties of sNCC and membranes
Thermal properties of the membranes and sNCC were studied by TGA measurements. TGA measurements indicated that there are three dramatic weight loss ranges with increasing temperature in Fig. 8. The first weight loss of composite membranes appears at 195 °C, which may be attributed to the thermal degradation of the sNCC in the membranes. This first weight loss temperature was higher than that of pure sNCC (180 °C). The increased thermal stability of sNCC may be due to the strong hydrogen bonding between sNCC and Ph-SPEEKK.
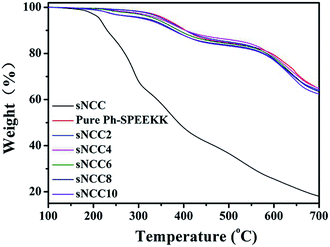 |
| Fig. 8 TGA curves of sNCC and membranes. | |
The second weight loss appears at 330 °C caused by the splitting-off of the sulfonic acid groups,34 and the other one appeared at 540–675 °C, which was attributed to the decomposition of the main chain. An increase in sNCC content resulted in a decrease of thermal stability, and the composite membranes exhibited lower thermal stability than the pure Ph-SPEEKK membrane. Table 1 shows that the temperature at 5% mass loss of the composite membranes decreased from 359 to 311 °C with the increase of sNCC content from 0 to 10%, due to the low thermal stability of the sNCC. This also proved that the interaction between sNCC and Ph-SPEEKK was strong. The temperature of the nanocomposite membranes degraded at 5% and 10% weight loss were all above 300 °C. No obvious degradation below 200 °C was observed, which could satisfy the practical application.
Mechanical properties of the membranes
Table 2 summarizes the mechanical properties of pure and composite membranes in their dry and wet state. In the dry state, the membranes possessed high tensile strength in the range of 41.9–50.1 MPa and Young's modulus of 0.85–1.20 GPa, with elongations at break of 64.6–179.7%. The moduli always increased with the sNCC ratio. The strength of the composite membranes was higher than that of pristine Ph-SPEEKK when the sNCC content was lower than 6%. With 4% of sNCC, the composite membrane strength could be as high as 50.1 MPa, and the elongation at break was 179.7%, which was 19.6% and 25.8% higher than that of Ph-SPEEKK, respectively. For the wet membranes, similar improvements tendency in strength were observed. Therefore, addition of appropriate content of sNCC with high mechanical performance and surface area could lead to better mechanical properties of membranes.35 It might also be ascribed to the formation of the hydrogen bonding network between the –OH groups of sNCC and the –SO3H groups of Ph-SPEEKK which could transfer the stress. While the composite membrane sNCC8 and sNCC10 presented worse strength and flexibility. This should be resulted by the sNCC aggregation and the stress concentration produced in the membrane, which could depress the membrane performance.
Table 2 Mechanical properties of the membranes
Membrane |
Tensile strength (MPa) |
Young's modulus (MPa) |
Elongation at break (%) |
Dry |
Wet |
Dry |
Wet |
Dry |
Wet |
Ph-SPEEKK |
41.9 |
29.9 |
853 |
497 |
142.8 |
70.3 |
sNCC2 |
46.4 |
31.9 |
901 |
637 |
154.8 |
71.9 |
sNCC4 |
50.1 |
32.3 |
914 |
626 |
179.7 |
76.6 |
sNCC6 |
44.2 |
35.9 |
921 |
630 |
136.7 |
63.0 |
sNCC8 |
41.8 |
27.2 |
950 |
697 |
99.3 |
51.1 |
sNCC10 |
33.6 |
19.7 |
1200 |
726 |
64.6 |
35.4 |
Morphology of the membranes
Since microstructure of the composite membranes has a close relationship with the performance of the composite films,36 the morphology of sNCC/Ph-SPEEKK membranes was studied by SEM. The cross sections of pure Ph-SPEEKK film and composite films: sNCC2, sNCC4, sNCC6, and sNCC10 fractured in liquid nitrogen were measured, and the morphologies are shown in Fig. 9. It is shown the morphology of Ph-SPEEKK and composite films with various sNCC ratios was different. Pristine Ph-SPEEKK membrane was flat and smooth. For the composite membranes of sNCC2, sNCC4 and sNCC6, there were many dimples appeared on the fractured section, which suggested their higher strengths and flexibility. While the morphology of sNCC8 and sNCC10 shows the brittle characteristics of the membranes, which may be caused by the aggregation of sNCC. These morphology results were agreed with the results of tensile test. Fig. 10 presents the TEM image of the sNCC/Ph-SPEEKK composite membranes with 4% of sNCC as an example. The images revealed that rod-like cellulose nanocrystals maintained diameters less than 100 nm and lengths ranging from 100 to 300 nm, and dispersed in the Ph-SPEEKK matrix uniformly.
 |
| Fig. 9 SEM images of pure Ph-SPEEKK (a), sNCC2 (b), sNCC4 (c), sNCC6 (d), sNCC8 (e), sNCC10 (f). | |
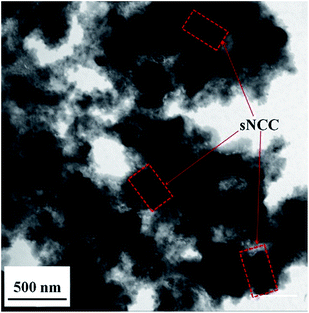 |
| Fig. 10 TEM image of sNCC4. | |
X-ray diffraction analysis
The WAXD patterns of the sNCC and membranes are shown in Fig. 11. sNCC exhibited three main reflection peaks at 2θ = 15.8°, 22.4°, and 34.4° relative to the cellulose I crystalline structure.37 While the broad diffraction peaks confirmed the amorphous nature of Ph-SPEEKK membrane. Even with the addition of sNCC, there was no obvious change on the diffraction peaks. It seemed that the sNCC insertion did not give rise to the ordered structure of Ph-SPEEKK apparently.
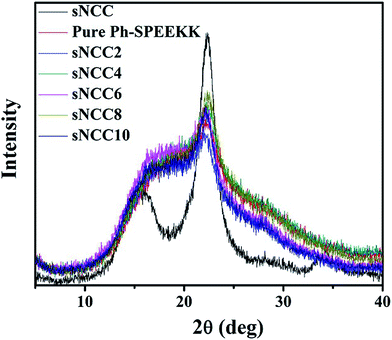 |
| Fig. 11 XRD patterns of the sNCC and membranes. | |
Conclusions
Sulfonated nanocrystal cellulose/sulfophenylated poly(ether ether ketone ketone) composites were successfully prepared via a solution casting method for the proton exchange membrane application. The property evaluation results showed the sNCC was a good component to enhance the performance of the composite membranes. With the introduction of sNCC, an obvious improvement in proton conductivity and mechanical properties could be observed. The composite membrane with 4% sNCC content presented a proton conductivity of 0.115 S cm−1 at 80 °C, which was much higher than that of Ph-SPEEKK. Furthermore, its strength and elongation at break was 19.6% and 25.8% higher than that of Ph-SPEEKK, respectively. The hydroxyl and sulfonic acid groups on the sNCC was supposed to benefit the hydrogen bond network formation for proton conduction and mechanical performance. The morphology studies obviously revealed the enhanced effects of the sNCC on the membrane strength, which was agreed with the results of tensile test. Thus, incorporation of appropriate ratio of sNCC into the sulfonated polymer matrix was proved to be a good choice for producing high performance proton exchange membranes.
Acknowledgements
The authors acknowledge the financial support for this project from the National Natural Science Foundation of China (No. 21404013), the Science and Technology Development Plan of Jilin Province, China (No. 20140204039GX, 20140204016GX, 20160101323JC and 20130521003JH), Changchun Science and Technology Plan Project, China (No. 14KG105, 14GH003 and 13KG36), and the Research Project of Science and Technology of the Education Department of Jilin Province during the 12th Five-year Plan Period (No. 2015-78).
References
- B. C. Steele and A. Heinzel, Nature, 2001, 414, 345–352 CrossRef CAS PubMed.
- B. J. Liu, G. P. Robertson, D. S. Kim, M. D. Guiver, W. Hu and Z. H. Jiang, Macromolecules, 2007, 40, 1934–1944 CrossRef CAS.
- J. W. Rhim, H. B. Park, C. S. Lee, J. H. Jun, D. S. Kim and Y. M. Lee, J. Membr. Sci., 2004, 238, 143–151 CrossRef CAS.
- R. Lei, L. X. Gao, R. Z. Jin and X. P. Qiu, Chin. J. Polym. Sci., 2014, 32, 941–952 CrossRef CAS.
- J. Roziere and D. J. Jones, Annu. Rev. Mater. Res., 2003, 33, 503–555 CrossRef CAS.
- T. D. Gierke, G. E. Munn and F. C. Wilson, J. Polym. Sci., Polym. Phys. Ed., 1981, 19, 1687–1704 CrossRef CAS.
- Y. Yang and S. Holdcroft, Fuel Cells, 2005, 5, 171–186 CrossRef CAS.
- M. A. Hickner, C. H. Fujimoto and C. J. Cornelius, Polymer, 2006, 47, 4238–4244 CrossRef CAS.
- B. J. Liu, W. Hu, Y. S. Kim, H. F. Zou, G. P. Robertson, Z. H. Jiang and M. D. Guiver, Electrochim. Acta, 2010, 55, 3817–3823 CrossRef CAS.
- B. J. Liu, W. Hu, C. H. Chen, Z. H. Jiang, W. J. Zhang, Z. W. Wu and T. Matsumoto, Polymer, 2004, 45, 3241–3247 CrossRef CAS.
- J. Jouanneau, R. Mercier, L. Gonon and G. Gebel, Macromolecules, 2007, 40, 983–990 CrossRef CAS.
- Y. Yin, J. Fang, H. Kita and K. I. Okamoto, Chem. Lett., 2003, 32, 328–329 CrossRef CAS.
- P. Salarizadeha, M. Javanbakhta and S. Pourmahdianc, Solid State Ionics, 2015, 281, 12–20 CrossRef.
- V. S. Rangasamy, S. Thayumanasundaram, N. D. Greefb, J. Seob and J. W. Locquet, Solid State Ionics, 2012, 216, 83–89 CrossRef CAS.
- E. Drioli and E. Fontananova, Annu. Rev. Chem. Biomol. Eng., 2012, 3, 395–420 CrossRef CAS PubMed.
- T. Higashihara, K. Matsumoto and M. Ueda, Polymer, 2009, 3, 5341–5357 CrossRef.
- B. Smitha, S. Sridhar and A. A. Khan, J. Membr. Sci., 2003, 225, 63–76 CrossRef CAS.
- B. P. Tripathi and V. K. Shahi, Prog. Polym. Sci., 2011, 36, 945–979 CrossRef CAS.
- D. Dai and M. Fan, RSC Adv., 2015, 5, 7713–7719 RSC.
- J. F. Revol, L. Godbout and D. G. Gray, J. Pulp Pap. Sci., 1998, 24, 146–149 CAS.
- Y. Habibi, L. A. Lucia and O. J. Rojas, Chem. Rev., 2010, 110, 3479–3500 CrossRef CAS PubMed.
- R. A. Khan, S. Salmieri, D. Dussault, J. U. Calderon, M. R. Kamal, A. Safrany and M. Lacroix, J. Agric. Food Chem., 2010, 58, 7878–7885 CrossRef CAS PubMed.
- D. Bondeson, A. Mathew and K. Okaman, Cellulose, 2006, 13, 171–180 CrossRef CAS.
- W. Bai, J. Holbery and K. Li, Cellulose, 2009, 16, 455–465 CrossRef CAS.
- G. Siqueira, J. Bras and A. Dufresne, Biomacromolecules, 2009, 10, 425–432 CrossRef CAS PubMed.
- A. Mandal and D. Chakrabarty, Carbohydr. Polym., 2011, 86, 1291–1299 CrossRef CAS.
- M. Rikukawa and K. Sanui, Prog. Polym. Sci., 2000, 25, 1463–1502 CrossRef CAS.
- H. X. Xie, D. Tao, X. Z. Xiang, Y. X. Ou, X. J. Bai and L. Wang, J. Membr. Sci., 2015, 473, 226–236 CrossRef CAS.
- N. Li, D. S. Hwang, S. Y. Lee, Y. L. Liu, Y. M. Lee and M. D. Guiver, Macromolecules, 2011, 44, 4901–4910 CrossRef CAS.
- K. D. Kreuer, A. Rabenau and W. Weppner, Angew. Chem., Int. Ed. Engl., 1982, 21, 208–209 CrossRef.
- L. A. Guillermo, D. K. Thomas and S. Daniel, Chem. Mater., 2011, 23, 1424–1429 CrossRef.
- T. J. F. Day, U. W. Schmitt and G. A. Voth, J. Am. Chem. Soc., 2000, 122, 12027–12028 CrossRef CAS.
- P. B. Palani, R. Kannan, S. Rajashabala, S. Rajendran and G. Velraj, Ionics, 2015, 21, 507–513 CrossRef.
- B. L. Wang, Z. Z. Cai, N. Zhang, B. Zhang, D. Qi, C. J. Zhao and H. Na, RSC Adv., 2015, 5, 536–544 RSC.
- Y. Nevo, N. Peer, S. Yochelis, M. Igbaria, S. Meirovitch, O. Shoseyov and Y. Paltiel, RSC Adv., 2015, 5, 7713–7719 RSC.
- X. L. Xu, L. Li, H. Wang, X. J. Li and X. P. Zhuang, RSC Adv., 2015, 5, 4934–4940 RSC.
- E. Fortunatia, M. Peltzerc, I. Armentanoa, L. Torrea, A. Jiménezc and J. M. Kennya, Carbohydr. Polym., 2012, 90, 948–956 CrossRef PubMed.
|
This journal is © The Royal Society of Chemistry 2016 |
Click here to see how this site uses Cookies. View our privacy policy here.