DOI:
10.1039/C6RA10689G
(Paper)
RSC Adv., 2016,
6, 78252-78256
Three-dimensional carbon boron nitrides with a broken, hollow, spherical shell for water treatment†
Received
25th April 2016
, Accepted 30th June 2016
First published on 21st July 2016
Abstract
Three-dimensional carbon boron nitrides (3D C-BN) with a unique morphology were fabricated by a simple method, which are composed of broken, hollow, spherical shells. The 3D C-BN possesses abundant surface adsorption sites, exhibiting excellent adsorption rates for methylene blue (MB) in aqueous solution. The best advantages are that the absorption rate of the MB becomes faster when it was used for the second time. Moreover, the excellent reusability of the 3D C-BN was confirmed; it can be reused eight times at least, and the adsorption capacity still preserves a high level of up to 95%. Our findings indicate that the 3D C-BN is a promising adsorption material for water purification.
1. Introduction
Low-dimensional nanomaterials such as zero-dimensional (0D) particles, one-dimensional (1D) fibres, wires or tubes, and two-dimensional (2D) membranes or nanosheets, have been widely applied to construct nanodevices and functional nanomaterials.1–3 Nowadays, three-dimensional (3D) nanostructured materials, including 3D metals/hydroxides,4 3D polymers5 and 3D ceramics,6 have received much attention due to their interesting properties and advanced potential applications.7,8 For example, 3D carbon as a practical 3D nanostructured material, has been extensively applied in the adsorption, catalysis, energy and biomedical fields.9,10 Especially, because of the urgent need to solve daily worsening environment problems, much attention has been focused on 3D carbon, which has an excellent adsorption ability for environmental pollutants.11
As an isostructure of carbon, hexagonal boron nitride (hBN) has been called “white graphite”.12–15 Porous boron nitride exhibits preeminent physical and chemical properties.16–21 These characteristics make porous boron nitride a promising candidate.22 Numerous researches have been conducted on BN to study its performance for the removal of organic solvents23 organic dyes24 and metallic ions25 from air or drinking water. It have been noted that the studies on 3D boron nitride (3D BN) are developing very fast. Lian et al. presented a facile solid phase method for preparing unique 3D hBN nanoflowers, which showed good thermal stability and high specific surface area.26 Liu et al. reported a 3D BN architecture consisting of an interconnected flexible network of nanosheets. This 3D BN architecture showed high specific surface area, excellent adsorption properties for organic dyes in aqueous solution as well as good reusability (88% of the starting adsorption capacity is maintained after 15 cycles).27 In a very recent work, Zhao et al. developed a kind of 3D BN foam fabricated by a vesicant-assisted gas-foaming process. The product had a vesicular structure with hierarchical pores ranging from the nm to μm scale and with ultrathin walls consisting of mono- or few-layered BN membranes with planar sizes as large as 100 μm. Their studies showed that the 3D BN foam exhibits a superstrong adsorbent ability up to 190 times its own weight toward a wide range of environmental contaminations, including several kind of oils and dyes.28
Herein, we report a method to synthesize a novel 3D nanostructure with a hollow-sphere shell morphology. The as-synthesized sample has high carbon content, which we named as 3D carbon boron nitride (3D C-BN). Our studies show that the prepared 3D C-BN sample displays excellent adsorption performance for dye (methylene blue, MB) in wastewater treatment, including a high adsorption rate, large capacity and excellent reusability. More interestingly, the adsorption rate becomes higher when the 3D C-BN sample was used for the second time after the desorption process. Our results indicate that 3D C-BN can be regarded as a promising adsorbent material for water cleaning.
2. Experimental
Material synthesis
The synthesis process of 3D C-BN is described as follows: firstly, NH4BF4 and NaBH4 in a 1
:
1 molar ratio were dissolved in neat 1,4-diethylene dioxide at 40 °C under stirring, to obtain the filter liquor; secondly, the mixed solvent was dried to obtain a white gel (polymeric aminoborane, PAB)29 at a related high temperature. After that, an identical amount of melamine diborate (M2B, the preparation process has been described in another paper24) powder and the prepared white gel were dissolved in 1,4-diethylene dioxide solution under strong stirring at 40 °C, and then dried at 60 °C for 6 h. Finally, the mixed white powder was heated to 1050 °C at a rate of 5 °C min−1 and kept for 4 h in tube furnace. All reactions were carried out in a flow of N2.
Characterization
The morphology of 3D C-BN was investigated by scanning electron microscopy (SEM, S-4800, HITACHI) and transmission electron microscopy (TEM, Tecnai F20, Philips). The structure of the sample was examined by X-ray powder diffraction analysis (XRD, D8 FOCUS, BRUKER). Fourier transforme infrared spectra (FTIR) were recorded on a Nicolet 7100 spectrophotometer between 400 and 4000 cm−1. A double beam UV/vis spectrophotometer (U-3900H, HITACHI) was used to determine the concentration of dye in water samples. Conventional elemental analyzers (TC500 and CS230, Leco) were applied to analyse the detailed N, O, and C contents. X-Ray photoelectron spectroscopy (XPS) was examined by a VGESCALAB 210 electron spectrometer. The nitrogen physisorption isotherms were measured at −196 °C on an AutoSorb iQ-C TCD analyzer. Prior to measurement, the samples were activated in a vacuum at 300 °C for 3 h. The Brunauer–Emmett–Teller (BET) specific surface area was calculated from the nitrogen adsorption data in a relative pressure ranging from 0.01 to 0.3.
3. Results and discussion
Characterization
3D C-BN is white, even when the carbon content measured by conventional elemental analyzers reaches 3.0 w% (Table 1). The measured composition for O is 18.7 w% and for N is 40.1 w%. Meanwhile, we also get a corresponding compound composition of B 0.373, C 0.039, N 0.398 and O 0.190 by XPS analysis. Fig. 1(a) shows the SEM image of the 3D C-BN. The sample has a three dimensional morphology of many broken hollow spherical shells, which can be confirmed by the enlarged SEM image shown in Fig. 1(b). An individual microsphere with a diameter of ∼4 μm and a thickness of ∼40 nm can be clearly observed. A TEM image is given in Fig. 1(c), indicating the same result obtained by SEM. The inset picture is the SAED pattern taken from the edge of the broken hollow spherical shell, which reveals the hexagonally structured characteristics of the sample. Rings can be indexed to the (002), (100), (110) diffractions of hBN, respectively. The 3D C-BN’s layer interspacing is ∼0.35 nm. Fig. 1(e) shows the XRD pattern of the white powder, in which all the diffraction peaks can be indexed to planes of hBN (card no. 34-0421).30 The peaks look very broad with a large full width at half maximum (FWHM). The pattern is handled by peak fitting and calculating with Scherrer equation. The crystallinity is 62.6%, and the crystallite size is about 1.8 nm, which matches well with the HRTEM image. The FTIR spectrum of the 3D C-BN is shown in Fig. 1(f).31 The surface bonds indexed by the absorbance peaks are listed as follows: B–OH/B–NH2 (∼3421 and ∼3257 cm−1); C
O (∼1630 cm−1); B–N (∼1400 cm−1); B–N–O (∼1160 cm−1); C–O (∼1080 cm−1); B–N–O (∼930 cm−1); and BN–B (∼800 cm−1).32,33
Table 1 C, N and O concentration of the original 3D C-BN sample and recycled samples
Sample |
C (w%) |
N (w%) |
O (w%) |
Raw |
3.0 |
40.1 |
18.7 |
1st-recycled |
9.2 |
35.9 |
18.9 |
2nd-recycled |
9.9 |
32.8 |
24.3 |
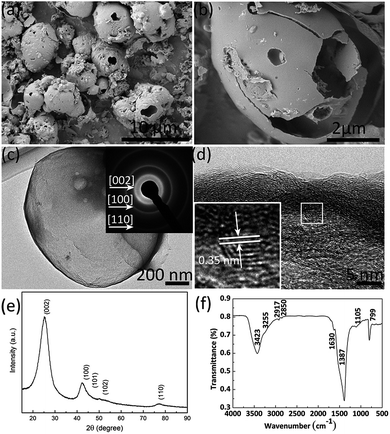 |
| Fig. 1 (a) SEM image of 3D C-BN. (b) High magnification SEM image showing an individual hollow spherical shell. (c) Typical TEM images of the 3D C-BN. Inset is the corresponding SAED pattern. (d) HRTEM image of the shell. The layer distance is about 0.35 nm. (e) XRD pattern of 3D C-BN. (f) FTIR spectra of 3D C-BN. | |
Adsorption properties
Organic dyes are recognized as one of the main industrial pollution sources in the world and can cause great harm to people’s daily life and natural environment by polluting drinking water.34 Wastewater treatment has become the focus of environmental protection. In order to study the adsorption properties of 3D C-BN, 100 mg of 3D C-BN were added into 100 ml of MB solution with an initial concentration of 50 mg L−1. The UV-vis spectra data were collected at different time intervals, which are showed in Fig. 2(a). Fig. 3(b) gives the corresponding adsorption rate curve. After 90 min, the MB had been completely absorbed by 3D C-BN at room temperature. Corresponding photographic images of MB solution collected at different times after adding 3D C-BN were given in the inset of Fig. 2(c), showing the water becoming clean. The adsorption isotherm was applied to the Langmuir model35 which fits well to the experimental data; a correlation coefficient of 0.99 is shown in Fig. 2(e). The Langmuir model is used to represent the relationship between the equilibrium solute concentration and the equilibrium adsorption capacity:where the Qm is the maximum adsorption capacity corresponding to complete monolayer coverage (mg L−1), K is the equilibrium constant (L mg−1), Ce is the equilibrium solute concentration (mg L−1), and Qe is the adsorbed amount of dye at equilibrium concentration (mg L−1).
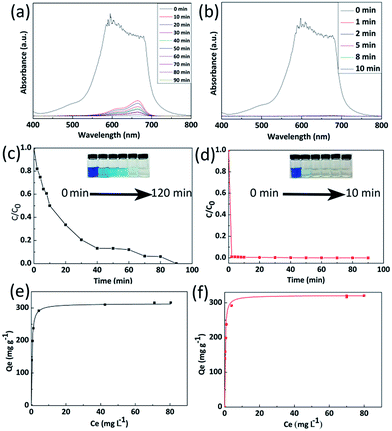 |
| Fig. 2 adsorption performance of dyes (MB) on the 3D C-BN sample. (a) UV-vis absorption spectra of the aqueous MB solution (50 mg L−1, 100 mL) in the presence of 3D C-BN at different time intervals, respectively. (b) UV-vis absorption spectra of MB solution using the 1st-recycled 3D C-BN sample as adsorbent. (c) Corresponding adsorption rates of MB, insert is the visual variation of MB solution with time. (d) Corresponding adsorption rate and visual variation of MB solution on the 1st-recycled 3D C-BN with time. (e) Adsorption isotherms of MB. (f) Adsorption isotherms of MB on the 1st-recycled 3D C-BN sample. | |
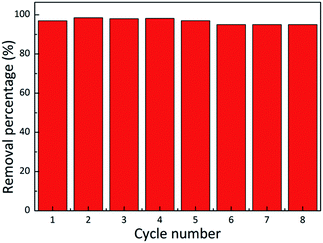 |
| Fig. 3 Adsorption ability of MB on 3D C-BN in 8 successive cycles of desorption–adsorption (initial MB concentration: 50 mg L−1). | |
The maximum adsorption capacity of 3D C-BN for MB is 313.15 mg g−1, higher than that of BN nanocarpets,36 carbon fibre,37 and graphene38 that have been reported before. The prominent adsorption capacity of 3D C-BN is responsible for the abundant surface functional species,25 such as –OH, resulting from our specially designed synthesis procedure. After adsorption, the 3D C-BN was recycled by heating up to 400 °C in the air for one hour.39 Interestingly, we found that after the first regeneration cycle, the newly generated 3D C-BN, named as 1st-recycled 3D C-BN, displays highly enhanced adsorption performance. Fig. 2(b) shows the recycled sample’s UV-visible sorption spectra, indicating a dramatic change compared with Fig. 2(b). The adsorption rate of the 1st-recycled 3D C-BN is obviously faster than the raw one. The MB is removed from the water in less than two minutes (Fig. 2(d)). Fig. 2(f) shows the adsorption isotherm applied to the Langmuir model. The maximum adsorption capacity Qm of the 1st-recycled 3D C-BN is 321.43 mg g−1 and fits well to experimental data with a correlation coefficient > 0.99. Fig. 3 gives the cycle number of the 3D C-BN. The recycled materials could almost maintain the same adsorption capacity within 5 runs. After eight cycles, the capacity of C-BN remains more than 95%. The morphology of the raw sample and the 8th-recycled one were compared by SEM imaging (Fig. S2†). The hollow spherical shells in the raw sample were broken into pieces after several times of reuse, and this is suggested to be the reason for their decreased capacity. Obviously, the high stability and reusability make the 3D C-BN extremely appropriate to be used as an efficient dye adsorption material.
It is interesting that the adsorption rate of the 1st-recycled 3D C-BN sample is obviously higher than the raw one. The reason for the enhanced adsorption rate is attributed to the increased C content and the elimination of undesired ester molecules. Conventional elemental analyzers were applied to analyse the detailed N, O, and C content of the raw sample, the 1st-recycled one and the 2nd-recycled one (Table 1). It is clear that the C content is increased after the adsorption–desorption cycles, because of the incomplete combustion of MB. The XRD pattern of the 1st-recycled sample shows very little difference to the raw one in terms of phase and crystallinity, so the increased C is suggested to be graphite and activated carbon, which would contribute to adsorption rate and capacity. Fig. 4 shows the FTIR spectra of the raw sample and the 1st-recycled one. The peaks located at 2920 cm−1 and 2854 cm−1 in the raw 3D C-BN sample’s spectra, corresponding to the C–H antisymmetric and symmetric stretching vibration, almost disappeared in the 1st-recycled one. Meanwhile the peak at 1630 cm−1 of C
O stretching and the double peaks at 1170 cm−1 and 1110 cm−1 of C–O–C stretching also disappeared. It is suggested that there are some ester molecules attached to the raw 3D C-BN grains, which decrease the adsorption activity of the surface functional species. These undesired ester molecules are eliminated after the desorption process, which lead to a sharp rise in the adsorption rate. The HRTEM images (Fig. 5) of these two samples coincide with this inference. We can see a definite fringe corresponding to the (002) plane in the image of the 1st-recycled sample. In vivid contrast, only fuzzy fringes can be observed in the raw sample, suggesting the existence of undesired ester molecules.
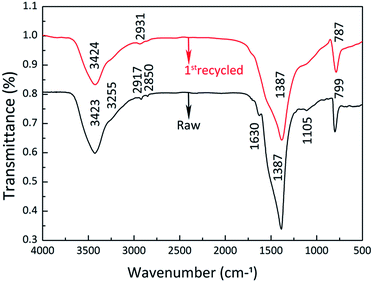 |
| Fig. 4 Comparison of FTIR spectra between the original sample and the 1st-recycled sample. | |
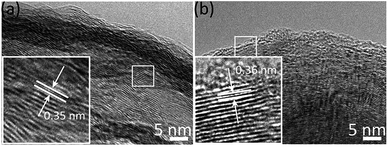 |
| Fig. 5 (a) The corresponding HRTEM image of the original sample. (b) The corresponding HRTEM image of the recycled sample. | |
Based on the above-mentioned experimental results and analysis, the synthesis method of 3D C-BN including high-temperature pyrolysis and self-bubbling is illustrated in Fig. 6. The precursor powders change gradually into a series of B–N–H polymeric forms such as polymeric aminoborane (PAB), (H2BNH2)n, polyiminoborane (PIB), (HBNH)n, and a BN matrix with a small quantity of hydrogen when the heat treatment started.29 It is very easy for these B–N–H polymeric forms and M2B precursors to release H2 or other gases, which can blow the precursor into bubbles (Fig. 6(b)). Hexagonal carbon and BN nanosheets are generated in the bubble walls during the high-temperature pyrolysis process, which then fabricates C-BN shells. Since the released gas accumulates, the C-BN bubbles are blasted from the inside and final result in the broken hollow sphere shell like morphology (Fig. 6(f)).40 Additionally, the introduction of M2B into the precursor can increase the C content of 3D C-BN, which promotes surface functional groups for the removal of MB.41 Further investigation is underway.
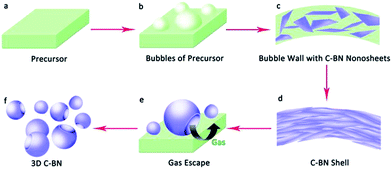 |
| Fig. 6 Experimental scheme of the synthesis method of 3D C-BN. | |
4. Conclusions
In summary, we have successfully synthesized a new kind of 3D C-BN nanomaterial with the morphology of broken, hollow, spherical shells via a high-temperature pyrolysis and self-bubbling method. The 3D C-BN sample presents significant adsorption performance for organic dyes. The maximum adsorption capacity of MB on the 3D C-BN reaches 313.15 mg g−1, and the removal efficiency of 95% is maintained even after recycling 8 times. The adsorption rate becomes much higher after one adsorption–desorption cycle. More importantly, MB can be totally removed in less than 2 minutes. Therefore, it will be very convenient as well as saving more resources in practice.
Acknowledgements
This work was supported by the National Natural Science Foundation of China (Grants No. 51372066 and No. 51172060), the Program for Changjiang Scholars and Innovative Research Team in University (PCSIRT: Grant No. IRT13060), the Innovation Fund for Excellent Graduate Student of Hebei Province (Grant No. 220056) and the Natural Science Foundation of Hebei Province (Grant No. B2015202079).
References
- B. Weng, S. Liu, Z. Tang and Y. Xu, RSC Adv., 2014, 4, 12685–12700 RSC.
- Y. Chen, C. Tan, H. Zhang and L. Wang, Chem. Soc. Rev., 2015, 44, 2681–2701 RSC.
- Z. Yu, H. Yuan, K. Lu, Y. Zhang and Z. Wei, RSC Adv., 2012, 2, 338–343 RSC.
- X. Xia, J. Tu, Y. Zhang, Y. Mai, X. Wang, C. Gu and X. Zhao, J. Phys. Chem. C, 2011, 115, 22662–22668 CAS.
- H. Minamimoto, H. Irie, T. Uematsu, T. Tsuda, A. Imanishi, S. Seki and S. Kuwabata, Langmuir, 2015, 31, 4281–4289 CrossRef CAS PubMed.
- J. Lewis, J. Smay, J. Stuecker and J. Cesarano, J. Am. Ceram. Soc., 2006, 89(12), 3599–3609 CrossRef CAS.
- H. Ng, J. Li, M. Smith, P. Nguyen, A. Casse, J. Han and M. Meyyappan, Science, 2003, 300, 1249 CrossRef CAS PubMed.
- International Technology Roadmap for Semiconductors 2001, Semiconductor Industry Association, San Jose, CA, 2001 Search PubMed.
- M. Serrano, M. Gutiérrez and F. Monte, Prog. Polym. Sci., 2014, 39, 1448–1471 CrossRef CAS.
- G. Gruner, Anal. Bioanal. Chem., 2006, 38(4), 322–335 Search PubMed.
- T. Wu, M. Chen, L. Zhang, X. Xu, Y. Liu, J. Yan, W. Wang and J. Gao, J. Mater. Chem. A, 2013, 1, 7612–7621 CAS.
- H. Zeng, C. Zhi, Z. Zhang, X. Wei, X. Wang, W. Guo, Y. Bando and D. Golberg, Nano Lett., 2010, 10, 5049–5055 CrossRef CAS PubMed.
- J. Li, H. Luo, J. Lin, Y. Xue, Z. Liu, P. Jin, X. Xu, Y. Huang, D. Liu, J. Zhang and C. Tang, Mater. Res. Express, 2014, 1, 035035 CrossRef.
- W. Lei, V. Mochalin, D. Liu, S. Qin, Y. Gogotsi and Y. Chen, Nat. Commun., 2015, 6, 8849 CrossRef CAS PubMed.
- W. Lei, D. Liu and Y. Chen, Adv. Mater. Interfaces, 2015, 2, 1400529 CrossRef.
- H. Wada, K. Nojima, K. Kuroda and C. Kato, J. Ceram. Soc. Jpn., 1987, 95, 130–134 CAS.
- C. Zhi, Y. Bando, C. Tang, H. Kuwahara and D. Golberg, Adv. Mater., 2009, 21, 2889 CrossRef CAS.
- R. Gao, L. Yin, C. Wang, Y. Qi, N. Lun, L. Zhang, Y. Liu, L. Kang and X. Wang, J. Phys. Chem. C, 2009, 113, 15160–15165 CAS.
- J. Pattanayak, T. Kar and S. J. Scheiner, J. Phys. Chem. A, 2002, 106, 2970–2978 CrossRef CAS.
- D. Liu, L. He, W. Lei, K. D. Klika, L. Kong and Y. Chen, Adv. Mater. Interfaces, 2015, 2, 1500228 CrossRef.
- D. Liu, W. Lei, S. Qin, K. D. Klika and Y. Chen, Phys. Chem. Chem. Phys., 2016, 18, 84–88 RSC.
- J. Li, J. Lin, X. Xu, X. Zhang, Y. Mi, Z. Mo, Y. Fan, L. Hu, X. Yang, J. Zhang, F. Meng, S. Yuan and C. Tang, Nanotechnology, 2013, 24, 155603 CrossRef PubMed.
- G. Postole, A. Gervasini, C. Guimon, A. Auroux and B. Bonnetot, J. Phys. Chem. B, 2006, 110, 12572–12580 CrossRef CAS PubMed.
- J. Li, H. Jia, Y. Ding, H. Luo, A. Saleem, Z. Liu, L. Hu and C. Tang, Nanotechnology, 2015, 26, 47 Search PubMed.
- J. Li, X. Xiao, X. Xu, J. Lin, Y. Huang, Y. Xue, P. Jin, J. Zou and C. Tang, Sci. Rep., 2013, 3, 3208 Search PubMed.
- G. Lian, X. Zhang, M. Tan, S. Zhang, D. Cui and Q. Wang, J. Mater. Chem., 2011, 21, 9201 RSC.
- D. Liu, W. Lei, S. Qin and Y. Chen, Physical Chemistry Two-Dimensional Materials, 2013, vol. 4, p. 4453 Search PubMed.
- H. Zhao, X. Song and H. Zeng, NPG Asia Mater., 2015, 7, e168 CrossRef CAS.
- X. Wang, C. Zhi and L. Li, Adv. Mater., 2011, 23(35), 4072–4076 CrossRef CAS PubMed.
- W. Lei, D. Portehault, D. Liu, S. Qin and Y. Chen, Nat. Commun., 2013, 4, 1777 CrossRef PubMed.
- R. Nemanich, S. Solin and R. Martin, Phys. Rev. B, 1981, 23, 6348 CrossRef CAS.
- C. Tang, Y. Bando, Y. Huang, C. Y. Zhi and D. Golberg, Adv. Funct. Mater., 2008, 18, 3653–3661 CrossRef CAS.
- C. Zhi, Y. Bando, C. Tang and D. Golberg, Appl. Phys. Lett., 2005, 86, 213110 CrossRef.
- E. Forgacs, T. Cserháti and G. Oros, Environ. Int., 2004, 30, 953–971 CrossRef CAS PubMed.
- X. Wang, Y. Zhong, T. Zhai, Y. Guo, S. Chen, Y. Ma, J. Yao, Y. Bando and D. Golberg, J. Mater. Chem., 2011, 21, 17680–17687 RSC.
- X. Zhang, G. Lian, S. Zhang, D. Cui and Q. Wang, CrystEngComm, 2012, 14, 4670–4676 RSC.
- S. Senthilkumaar, P. Varadarajan, K. Porkodi and C. Subbhuraam, J. Colloid Interface Sci., 2005, 284, 78–82 CrossRef CAS PubMed.
- T. Liu, Y. Li, Q. Du, J. Sun, Y. Jiao, G. Yang, Z. Wang, Y. Xia, W. Zhang, K. Wang, H. Zhu and D. Wu, Colloids Surf., B, 2012, 90, 197–203 CrossRef CAS PubMed.
- J. Li, Y. Huang, Z. Liu, J. Zhang, X. Liu, H. Luo, Y. Ma, X. Xu, Y. Lu, J. Lin, J. Zou and C. Tang, J. Mater. Chem. A, 2015, 3, 8185 CAS.
- X. Wang, A. Pakdel, C. Zhi, K. Watanabe, T. Sekiguchi, D. Golberg and Y. Bando, J. Phys.: Condens. Matter, 2012, 24, 314205 CrossRef PubMed.
- X. Zhang, Z. Lu, J. Lin, Y. Fan, L. Li, X. Xu, L. Hu, F. Meng, J. Zhao and C. Tang, ECS J. Solid State Sci. Technol., 2012, 2(3), R39–R43 CrossRef.
Footnote |
† Electronic supplementary information (ESI) available. See DOI: 10.1039/c6ra10689g |
|
This journal is © The Royal Society of Chemistry 2016 |
Click here to see how this site uses Cookies. View our privacy policy here.