DOI:
10.1039/C6RA05379C
(Paper)
RSC Adv., 2016,
6, 49091-49100
Novel aluminium exchanged dodecatungstophosphoric acid supported on K-10 clay as catalyst: benzoylation of diphenyloxide with benzoic anhydride†
Received
29th February 2016
, Accepted 10th May 2016
First published on 11th May 2016
Abstract
A series of (20% w/w) aluminium exchanged dodeca-tungstophosphoric acids (DTP) (Alx-DTP, x = 0.33–1) supported on montmorillonite K-10 clay were synthesized and completely characterized by sophisticated techniques. These catalysts were used for the selective benzoylation of diphenyl oxide with benzoic anhydride to a mono acylated product. Al0.66-DTP/K-10 catalyst showed the best activity amongst other aluminium substituted catalysts and Cs2.5H0.5PW12O40 (Cs-DTP)/K-10. Different supports such as ZrO2, SnO2 and K-10 were used to study the effect of support on the acidic property and activity of Al0.66-DTP supported catalysts in the benzoylation reaction. The order of activity was Al0.66-DTP/K-10 > Al0.66-DTP/SnO2 > Al0.66-DTP/ZrO2. The effect of benzoylating agents such as benzoic anhydride, benzoyl chloride and benzoic acid on the conversion and rate was also studied. Benzoic anhydride showed the highest reactivity. Eley–Rideal mechanism was found to be consistent with the data. The activation energy for benzoylation of DPO was calculated as 22 kcal mol−1, which further supports that the reaction is kinetically controlled. Al0.66-DTP/K-10 was an active and robust catalyst.
Introduction
Heteropoly acids (HPA) and their salts, either in a supported or an unsupported form, are frequently used as solid acid catalysts for various industrially significant reactions.1–3 Dodeca-tungstophosphoric acid (DTP) having the Keggin structure is reported to have the highest acidity and best thermal stability amongst all the HPAs in several acid catalysed reactions.1–4 Unsupported HPAs have some basic drawbacks like very high solubility in polar media and low surface area of salts of HPAs. The problems associated with bulk HPAs can be overcome by the use of an appropriate support and/or substituting the H+ ions with metal ions.2,5–9 Various supports used to prepare a heterogeneous catalyst for bulk heteropoly acid or substituted heteropoly acids include, metal oxides (ZrO2, TiO2, SnO2 and Nb2O5),10–13 mesoporous materials (silica, HMS, MCM-41, SBA-15),3,14–17 alumina,18 active carbon,19 graphene20 and montmorillonite K-10.3,21–24 Various metals ions have been reported to make the exchanged HPA and classified accordingly in two groups.25 Different metal ions such as Na+, Al3+, Cu2+, Cs+, Ag+, Y3+, Fe3+, Bi3+, Ru3+, Al3+, Sm3+, Ti4+, Zr4+, Ti4+, Hf4+ and Sn4+ have been studied in detail for several reactions.6,8,26–30 Some metal ions act as electron pair acceptor and hence generate Lewis acidic sites in substituted heteropoly acid.7 Cs substituted DTP either supported or unsupported have been explored extensively in reactions because of higher acidity content as compared to the parent acid.3,30 The synergistic effect of supporting DTP and its Cs substituted salts on K-10 has been reported and used in several reactions.3,21–24 Aluminium exchanged DTP supported on titania was employed in the reaction of anisole with benzyl alcohol which showed that Al exchanged DTP are very active for the reaction.25 Therefore it was planned to investigate the effect of support as well as content of aluminium in exchanged DTP on acidity and activity in Friedel–Crafts acylation reaction. Benzophenones are very important class of fine chemicals which can be produced from acylation of different aromatic ethers (such as anisole, veratrole, diphenyl oxide) with benzoyl chlorides, alcohols and olefins having numerous applications in industries like fragrance, pharmaceuticals, dyes and as heat transfer fluids.31–34 However, the use benzoyl chloride causes corrosion of process equipment because of HCl generated during reaction and makes the process uneconomical. Further these reactions are catalyzed by different homogenous Lewis and Brønsted acid catalysts which require neutralization of the acidic medium and presents several environmental and economic issues.10,23
Benzoylation of diphenyl oxide with benzoyl chloride produces 4-phenoxybenzophenone which is used as intermediate and as a heat transfer fluid. Sawant et al.34 have reported the benzoylation of diphenyl oxide with benzoyl chloride over DTP/ZrO2, which gives 97% selectivity of 4-phenoxybenzophenone along with only 39.3% conversion of benzoyl chloride after 3 h under optimum conditions. Overall yield of product is still very low. Further the use of acid chloride has disadvantage in terms of economic and environmental issues as discussed above.
Benzoic anhydride as a benzoylating agent has been used in various benzoylation reactions of alkyl benzenes, aromatic ethers, etc.35 The activity of benzoic anhydride was compared with benzoyl chloride and found to be better in case of benzoylation of veratrole to 3,4-dimethoxybenzophenoene over H–Y zeolite.35 The better activity of benzoic anhydride was explained on the basis of its strong adsorption on the catalytic surface due to higher molecular weight of benzoic anhydride as compared to benzoyl chloride.36 The co-product formed with use of benzoic anhydride is benzoic acid, which can be easily recovered and used for other purposes. Benzoylation of diphenyl oxide using benzoic anhydride is so far not reported in literature and advantages discussed above makes it an alternative for the green synthesis of the acylated product. For the first time we are reporting the use of benzoic anhydride as acylating agent for acylation of diphenyl oxide.
The primary aim of the present work was the synthesis of different aluminium salts of dodeca-tungstophosphoric acid (DTP) supported metal oxides including montmorillonite K-10 clay as catalysts with varying aluminium content and to characterize them by different methods such as FT-IR, NH3-TPD, XRD, surface area analysis, TGA and SEM. The activity of the prepared catalysts was investigated in selective benzoylation of diphenyl oxide with benzoic anhydride under solvent free condition to monoacylated product. Different reaction parameters were optimized to derive suitable mechanism and kinetics.
Experimental section
Chemicals and catalysts
The list of chemicals procured was as follows: diphenyl oxide, dodeca-tungstophosphoric acid hexahydrate, benzoic anhydride, benzoic acid, n-dodecane, aluminium nitrate (AR grade; S. D. Fine Chem. Ltd, Mumbai, India), cesium chloride, K-10 clay (Aldrich, USA).
Catalyst synthesis
Preparation of 20% w/w Alx-DTP/K-10. Supported aluminium exchanged heteropoly acid catalyst, 20% w/w Alx-DTP over K-10 montmorillonite (Alx-DTP/K-10) was synthesized by wet impregnation method as reported for Cs-DTP/K-10 in our laboratory.21–24,37The preparation involves two steps of impregnation. Firstly, aluminium with varying amount was loaded on K-10. Around 5 g of support (K-10) was dried for 3 h in oven at 120 °C to remove moisture. The required quantity of aluminium nitrate was dissolved in methanol (5 ml) and then added in small amount (approximately 1 ml) each time as an aluminium source to 4 g of K-10, kneaded and dried in air to get free flowing solid. The obtained solid material was again dried at 120 °C for 4 h to remove the entire methanol.
In second step, the desired amount of DTP was dissolved in methanol and added to dry powder of aluminium loaded K-10 clay descried before resulting in formation of slurry which was dried as stated above to get a nearly dry solid material. The resultant material was dried at 120 °C for 12 h followed by calcination at 300 °C for 3 h to get active 20% w/w Alx-DTP/K-10, where x represents the number of aluminium ions, which was varied from 0.33 to 1. A series of 20% (w/w) Cs2.5-DTP/K-10 was synthesized by the same method as described by us for cesium chloride as a source of Cs. Al-DTP supported on different supports (ZrO2 and SnO2) were prepared by similar procedure as described above.
Characterization of catalysts. Different characterization techniques were employed to characterize the fresh and used catalyst. The detail methodology is given in ESI.†
Reaction procedure. Experiments were conducted in a glass reactor (volume 50 cm3) having 6-bladed pitched-turbine impeller. The setup was kept in a thermostatic oil bath provided with PID controller. The reaction was started by taking the appropriate quantities of reactants and internal standard n-dodecane (usually 3% v/v) and the temperature was set to a known value and agitated. The control experiment consisted of benzoic anhydride 0.0057 mol, diphenyl oxide 0.057 mol, catalyst loading 0.03 g cm−3, temperature 130 °C, speed of agitation 800 rpm. The zero hour sample was taken once the mixture reached the desired temperature, the catalyst added and the stirring started again. Clear samples were taken at regular time interval for analysis. The samples were centrifuged and analyzed by using BP-1 column in GC 6810 having FID detector. Samples were quantified by using internal standard method.
Results and discussion
BET surface area analysis
The textural characteristics of the catalysts are given in Table 1. The adsorption–desorption isotherms of different aluminium substituted and supported catalyst are shown in Fig. 1. Surface area of K-10 support decreases after loading of DTP which suggests the filling of pores by DTP particles. However on aluminium substitution, the salt formation of aluminium with DTP results in increase in surface area which is due to the dense porous network formed by the salts of DTP with aluminium as has been explained by Moffat et al.38 Pore sizes of all catalyst are in the range of 5 nm to 7.5 nm and show a type IV hysteresis loop, representative of mesoporous material. Also all samples show a negligible amount of micropore volume which further confirms the mesoporous nature of samples. The amount of N2 adsorbed at the highest P/P0 is also tabulated in Table 1. K-10 has maximum nitrogen adsorption capacity which decreases when DTP and Al-DTP are loaded. Decrease in the surface area supports that long range pores are hindered or blocked making N2 adsorption possible only in most accessible pores and hence the surface area decreases.39 The closure point of hysteresis loops of K-10 and DTP/K-10 took place when the value of P/P0 reached 0.5, while in the case of Al substituted catalyst it shifted towards high P/P0 value which indicates the presence of more macrospores as compared to K-10 and DTP/K-10.
Table 1 Surface area pore volume and pore diameter analysis
Sr. No |
Catalyst |
Total amount of N2 adsorbed (cm3 g−1 STP) |
Surface area (m2 g−1) |
Pore diameter (nm) |
Pore volume (cm3 g−1) |
1 |
Montmorillonite K-10 |
245.7 |
227.1 |
6.4 |
0.36 |
2 |
20% (w/w) DTP/K-10 |
139.6 |
110.6 |
7.1 |
0.31 |
3 |
20% (w/w) Al0.33-DTP/K-10 |
183.3 |
168.9 |
6.4 |
0.29 |
4 |
20% (w/w) Al0.66-DTP/K-10 |
188.5 |
180.2 |
6.0 |
0.27 |
5 |
20% (w/w) Al1-DTP/K-10 |
196.3 |
183.6 |
6.1 |
0.28 |
6 |
20% (w/w) Cs-DTP/K-10 |
232.1 |
205.8 |
5.9 |
0.29 |
7 |
Reused 20% (w/w) Al0.66-DTP/K-10 |
183.3 |
176.4 |
6.1 |
0.27 |
 |
| Fig. 1 N2 adsorption–desorption isotherms of (a) K-10 clay, (b) DTP/K-10, (c) Al0.33-DTP/K-10 (d) Al0.66-DTP/K-10 (e) Al1-DTP/K-10 (f) reused Al0.66-DTP/K-10. | |
The surface area analysis of used and fresh catalyst was also compared in order to see any changes in surface area of the reused catalyst (Fig. 1 and Table 1). There is a marginal decrease in the overall surface are of the reused catalyst; however, other properties remain the same which indicate the reusability of catalyst.
X-ray powder diffraction (XRD)
The XRD diffraction patterns of all catalysts are shown in Fig. 2. The observed sharp peaks in the diffractogram of K-10 are due to quartz and other impurities.40 Despite sharp peaks shown by these impurities two broad 2θ peaks at 20° (due to 110 diffraction) and 35° (due to 105 diffraction) of montmorillonite K-10 can be easily found in the XRD pattern. DTP is crystalline in nature as reported earlier;23 hence the loading of DTP on K-10 may result in change in overall XRD patterns shown by K-10. The loading of DTP and aluminium exchanged DTP on K-10 results in decrease in the intensity shown by K-10 and there are no distinct peaks shown by DTP related to its crystalline nature. This indicates high dispersion of these materials on the surface and their interaction with the support.40 The XRD pattern of used and fresh catalyst was also compared to see the fidelity of catalyst composition after the use. There is no difference in the XRD pattern which confirms the stability of catalyst after 4th reuse.
 |
| Fig. 2 XRD of different catalysts (a) K-10 clay, (b) DTP/K-10, (c) Al0.66-DTP/K-10 (d) reused Al0.66-DTP/K-10. | |
Fourier transforms infrared spectroscopy (FT-IR)
Keggin structure of supported dodeca-tungstophosphoric acid and aluminium exchanged catalysts were confirmed by comparing their FT-IR spectra (Fig. 3). The characteristic peaks (between 700 and 1100 cm−1) related to Keggin structure of DTP i.e. at 1081 cm−1, 984 cm−1, 897 and 812 cm−1 were assignable respectively to the vibration of ν (P–O), terminal ν (W
O), corner ν (W–O–W) and edge-sharing ν (W–O–W).5,37 Overall spectra of the supported catalysts are quite similar to that shown by K-10. The peaks related to DTP and metal exchanged DTP have got superimposed on those of support suggesting that the structure remains unaltered even after interaction with K-10.23,40 The FT-IR of spent catalyst was compared with the fresh catalyst to confirm the stability of exchanged DTP after the reaction. Fig. 3 shows all characteristic peaks related to Keggin structure in the spent catalyst as shown by the fresh catalyst, once again supporting the stability of catalyst and its activity was not affected during reaction.
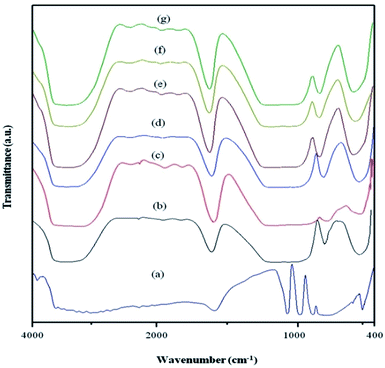 |
| Fig. 3 FT-IR spectra of catalysts (a) DTP, (b) K-10 clay, (c) DTP/K-10, (d) Al0.33-DTP/K-10 (e) Al0.66-DTP/K-10 (f) Al1-DTP/K-10 (g) reused Al0.66-DTP/K-10. | |
NH3-TPD
The NH3-TPD of K-10, DTP and Al-DTP/K-10 was conducted in the range of 50 °C to 650 °C (Fig. 4 and Table 2). All supported catalysts showed two different desorption peak of ammonia in the range of 100–300 °C and from 450 to 600 °C. The montmorillonite K-10 also shows theses peaks as it is an acid treated clay and hence possesses not only weak but also strong acidic sites (Fig. 4). Strength of moderate and strong acidic sites varies with the change in the content of aluminium (Table 2); however, the total replacement of protons of heteropoly results in increase in weak acidic site but the strong site concentration decreases. The overall acidity possessed by the aluminium exchanged supported catalyst were more as compared to DTP/K-10 and Cs-DTP/K-10 which may be due to Lewis acidity possessed by aluminium.
 |
| Fig. 4 NH3-TPD patterns of different catalysts (a) K-10 clay, (b) DTP/K-10, (c) Al0.33-DTP/K-10 (d) Al0.66-DTP/K-10 (e) Al1-DTP/K-10 (f) reused Al0.66-DTP/K-10. | |
Table 2 Acid strength distribution of K-10 supported catalyst
No. |
Catalyst |
Acidity (mmol of NH3 g−1) |
Weak |
Moderate/strong |
Total |
1 |
K-10 |
0.53 |
0.46 |
0.99 |
2 |
20% (w/w) DTP/K-10 |
0.75 |
1.12 |
1.87 |
3 |
20% (w/w) Al0.33-DTP/K-10 |
0.82 |
1.14 |
1.96 |
4 |
20% (w/w) Al0.66-DTP/K-10 |
0.80 |
1.33 |
2.13 |
5 |
20% (w/w) Al1-DTP/K-10 |
0.88 |
1.27 |
2.16 |
6 |
20% (w/w) Cs-DTP/K-10 |
0.36 |
1.15 |
1.51 |
7 |
Reused 20% (w/w) Al0.66-DTP/K-10 |
0.79 |
1.30 |
2.09 |
TGA analysis
TGA analysis of different samples, i.e. montmorillonite K-10, DTP/K-10 and Al0.66-DTP/K-10 was done to study the thermal stability (Fig. 5). DTP is supposed to decompose around 465 °C;1 hence, supporting DTP on proper support and/or replacement of protons will further increase its thermal stability.5 TGA profile reveals that supporting DTP on K-10 increases it thermal stability as there is only marginal loss of 3% after 300 °C. The weight loss of total 12% of support is due to the loss water which is physically adsorbed and present in interlayer and also due to –OH group destruction of the montmorillonite K-10.41 Further its substitution with Al results in increase in thermal stability and is in good agreement with different literature which reported increase in thermal stability of metal ion exchanged heteropoly acid.7–9,23
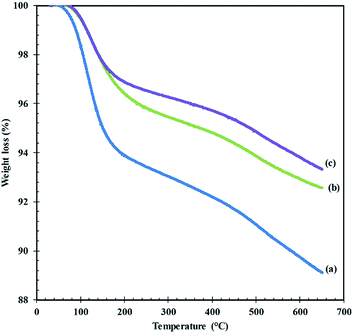 |
| Fig. 5 TGA analysis of (a) K-10 clay, (b) DTP/K-10, (c) Al0.66-DTP/K-10. | |
SEM
The surface morphology of the sample was evaluated from SEM analysis. Fig. 6 shows formation of agglomerates after loading of Al exchanged DTP on supports. The morphology of Al exchanged catalyst shows a smooth surface as reported for Cs-DTP/K-10.37 The fresh and reused catalyst shows no difference in the morphology which confirms the reusable nature of catalyst.
 |
| Fig. 6 SEM images of (a) fresh Al0.66-DTP/K-10, (b) reused Al0.66-DTP/K-10. | |
Efficacy of various solid acid catalysts
The activity of different catalysts, namely, K-10, 20% w/w DTP/K-10, 20% w/w Cs-DTP/K-10 and 20% w/w Alx-DTP/K-10 in solvent free benzoylation of diphenyl oxide was studied with benzoic anhydride (Scheme 1 and Fig. 7). The result shows highest activity of Al0.66-DTP/K-10 catalyst as compared to others due to its highest acidity (Table 2). The aluminium exchanged catalysts were found to be more active in comparison of Cs-DTP/K-10, DTP/K-10 and K-10. The acidity of the catalysts determined by ammonia TPD is in the following order: Al1-DTP/K-10 ≅ Al0.66-DTP/K-10 > Al0.33-DTP/K-10 > DTP/K-10 > Cs-DTP/K-10 > K-10. The activity of these catalysts towards conversion of benzoic anhydride under solvent less condition was also in the same order as mentioned above as: Al1-DTP/K-10 ≅ Al0.66-DTP/K-10 > Al0.33-DTP/K-10 > DTP/K-10 > Cs-DTP/K-10 > K-10. Change in the amount of aluminium substitution in catalyst increases the concentration of acidic sites from week to strong sites as shown in Fig. 4. The activity shown by the Al substituted catalysts supported on K-10 is greater as compared to that shown by Cs-DTP/K-10 and DTP/K-10, which is due to the high acidity of the Al-exchanged catalyst. This also indicates that aluminium helps to enhance the overall acidity of these catalysts because of the Lewis acidity of Al. However, in comparison with Al0.66-DTP/K-10; there is no distinct difference in conversion with Al1-DTP/K-10 (Fig. 7). This is due to marginal difference in the acidity possessed by these catalysts. Hence all further experiments and studies were carried out with Al0.66-DTP/K-10 catalyst.
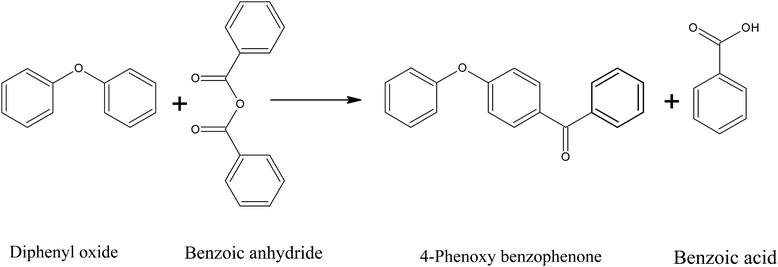 |
| Scheme 1 Benzoylation of diphenyl oxide with benzoic anhydride. | |
 |
| Fig. 7 Effect of various catalysts on conversion of benzoic anhydride. Benzoic anhydride 0.0057 mol, diphenyl oxide 0.057 mol, catalyst loading 0.03 g cm−3, temperature 130 °C, speed of agitation 800 rpm, total volume 10.1 cm3, reaction time 120 min. | |
Effect of different supports on benzoylation activity
The activities of Al0.66-DTP supported on three different supports i.e. ZrO2, SnO2 and K-10 prepared by the same method as described above were evaluated to understand the role of support. The conversion of benzoic anhydride was found to be in the following order for these catalyst as Al-DTP/K-10 > Al-DTP/SnO2 > Al-DTP/ZrO2 (Fig. 8). The acidity of these catalysts was evaluated by using ammonia TPD in the range of 50 °C to 650 °C (Fig. 9) and the calculated acid site strengths are given in Table 3. The acidity possessed by these catalyst were found in following order Al0.66-DTP/K-10 > Al0.66-DTP/SnO2 > Al0.66-DTP/ZrO2 which is in the same order as obtained for the conversion of benzoic anhydride. The SnO2 supported catalyst shows mainly a strong acidic site and very few weak acidic sites; however, the total acidity is still very low as compared to that of K-10 supported catalyst which has both strong and weak sites (Table 3). The high acidity of K-10 as compared to other metal oxide is the most probable reason behind the high activity and acidity shown by the Al0.66-DTP/K-10 catalyst. Further surface area may be another reason as we can see from Table 3, the surface area of different catalysts are in following order, Al0.66-DTP/K-10 > Al0.66-DTP/SnO2 > Al0.66-DTP/ZrO2. Large surface area results in better dispersion of active catalyst surface. High acidity of K-10 supported catalyst along with better dispersion could be the reason for its high activity in benzoylation reaction. Hence for further reaction, K-10 was selected as the support in order to get the maximum yield of product.
 |
| Fig. 8 Benzoylation activity of Al0.66-DTP supported on different supports. Benzoic anhydride 0.0057 mol, diphenyl oxide 0.057 mol, catalyst loading 0.03 g cm−3, temperature 130 °C, speed of agitation 800 rpm, total volume 10.1 cm3, reaction time 120 min. | |
 |
| Fig. 9 NH3-TPD patterns of different supported catalysts (a) Al0.66-DTP/ZrO2, (b) Al0.66-DTP/SnO2, (c) Al0.66-DTP/K-10. | |
Table 3 Acid strength distribution and surface property of Al0.66-DTP supported on different supports
No. |
Catalyst |
Acidity (mmol of NH3 g−1) |
Surface area (m2 g−1) |
1 |
20% (w/w) Al0.66-DTP/K-10 |
2.13 |
205.8 |
2 |
20% (w/w) Al0.66-DTP/ZrO2 |
1.22 |
49.6 |
3 |
20% (w/w) Al0.66-DTP/SnO2 |
1.33 |
102.6 |
Effect of different benzoylating agent
Benzoylation of diphenyl oxide was carried out using three different benzoylating agents, i.e. benzoic acid, benzoic anhydride and benzoyl chloride (Table 4); the benzoylation reaction with benzoic acid shows no conversion at 130 °C which supports the fact that there is no reaction of benzoic acid towards formation of benzoylated product formed during reaction with benzoic anhydride. The reaction with benzoyl chloride gives 56.6% conversion and 96% selectivity towards 4-phenoxybenzophenone. Hence, overall yield of desired product is found to be 54.5%, while reaction with benzoic anhydride gives the 72.1% conversion and 100% selectivity of desired product resulting in overall yield of 72% which is considerably high as compared to the yield obtained from benzoyl chloride after 2 h. The strong adsorption of benzoic anhydride due to its higher molecular weight as in the case of zeolite and other solid acid catalysts23,35 can be applied here as the most probable reason for the superior activity shown by benzoic anhydride amongst the different benzoylating agents used for reaction. Apart from reactivity, the green part of synthesis using benzoic anhydride is the formation of benzoic acid (co-product) as compared to HCl generated during use of benzoyl chloride, makes the benzoic anhydride more preferable benzoylating agent not only in terms of reactivity but also in terms of green synthesis process.
Table 4 Reactivity of different benzoylating agenta
No. |
Acylating agent |
Conversion (%) |
Selectivity of 4-phenoxybenzophenone (%) |
Conditions: diphenyl oxide/benzoylating agent (mole ratio) = 10, catalyst loading = 0.03 g cm−3, temperature = 130 °C, speed of agitation 800 rpm, reaction time = 120 min. |
1 |
Benzoyl chloride |
56.6 |
96 |
2 |
Benzoic anhydride |
72.1 |
100 |
3 |
Benzoic acid |
No conversion |
— |
Stability of catalyst
The heterogeneity of catalyst in a reaction system was investigated to confirm the stability of prepared catalyst. The catalyst was removed by simple filtration after 1 h of initial reaction time and reaction was started again without addition of catalyst in the same reactor (reactor was washed to get rid of trace of catalyst attached to glass surface) with the same reaction condition. After 2 h the reaction was stopped and the analysis of the reaction sample showed no more conversion of benzoic anhydride indicating the heterogeneous nature and stability of catalyst without any leaching of active sites.
Effect of different reaction parameters
Various reaction parameters were studied in detail to optimize the conversion of benzoic anhydride and rate of formation of benzoylated product.
Speed of agitation
Fig. 10 shows that with increase in agitation speed from 400 to 800 rpm the conversion seems to increase and thereafter remains constant which indicates the negligible effect of mass transfer resistance on rate of benzoylation. Hence 800 rpm was selected as the optimum speed of agitation for further reaction. The details about the theoretical calculation of mass transfer resistance effect on reaction rate have been explored and detailed in some of our literature.21–23 Only calculation part is reported in ESI† to confirm the absence mass transfer resistance on reaction rate.
 |
| Fig. 10 Effect of speed of agitation on conversion of benzoic anhydride. Benzoic anhydride 0.0057 mol, diphenyl oxide 0.057 mol, catalyst loading 0.03 g cm−3, temperature 130 °C, total volume 10.1 cm3. ( ) 400 rpm, ( ) 600 rpm, ( ) 800 rpm, ( ) 1000 rpm. | |
Effect of the catalyst loading
The catalyst loading was changed from 0.01 g cm−3 to 0.04 g cm−3 (Fig. 11(a)). The plots were made for different catalyst loading vs. initial rate to see a linear relationship (Fig. 11(b)). It is due to the increase in vacant sites for the benzoylation reaction with increase in catalyst loading which results in the initial reaction rate enhancement. We also did the theoretical calculation and found that Wietz–Prater modulus (Cwp) was far less than unity (Cwp = 0.0026), and hence the reaction was kinetically controlled42 which was further confirmed by the activation energy calculation.
 |
| Fig. 11 Effect of catalyst loading on (a) conversion of benzoic anhydride. (b) Initial rate of benzoylation of DPO. Benzoic anhydride 0.0057 mol, diphenyl oxide 0.057 mol, temperature 130 °C, speed of agitation 800 rpm, total volume 10.1 cm3. ( ) 0.01 g cm−3, ( ) 0.02 g cm−3, ( ) 0.03 g cm−3, ( ) 0.04 g cm−3, (-------) predicted values. | |
Effect of mole ratio
The mole ratio of two reactants was varied in range of 1
:
2 to 1
:
15 (benzoic anhydride to diphenyl oxide) maintaining the other variables constant (Fig. 12). The reaction was found to be greatly dependent on the change in mole ratio of the benzoic anhydride with diphenyl oxide. The increase in number of moles of diphenyl oxide by keeping constant moles of benzoic anhydride provides a better and enhanced conversion and rate. The most probable reason is attributed to the solubility of the formed products (desired along with benzoic acid) in the diphenyl oxide. The increase in the mole ratio, results in excess moles of diphenyl oxide which helps to solubilise the product formed and helps to free the catalytic site for further reaction. At 1
:
10 mole ratio good conversion was obtained and hence it was selected as optimum mole ratio for further study.
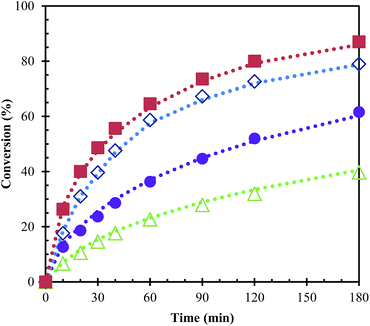 |
| Fig. 12 Effect of mole ratio on conversion of benzoic anhydride. Catalyst loading 0.03 g cm−3, temperature 130 °C, speed of agitation 800 rpm, total volume 10.1 cm3. ( ) 1 : 2, ( ) 1 : 5, ( ) 1 : 10, ( ) 1 : 15, (-------) predicted values. | |
Effect of temperature
The temperature of the reaction was changed from 110–140 °C to see its effect and to prove that the reaction is only kinetically controlled and all other resistance have been successfully avoided. The final conversion of limiting reactant (i.e. benzoic anhydride) increased with change in temperature (Fig. 13), which supports that the reaction was kinetically controlled.
 |
| Fig. 13 Effect of temperature on conversion of benzoic anhydride. Benzoic anhydride 0.0057 mol, diphenyl oxide 0.057 mol, catalyst loading 0.03 g cm−3, speed of agitation 800 rpm, total volume 10.1 cm3, reaction time 120 min. ( ) 110 °C, ( ) 120 °C, ( ) 130 °C, ( ) 140 °C, (-------) predicted values. | |
Catalyst reusability studies
The catalyst robustness was studied through reusability four times. The separated catalyst was mixed with 30 ml of methanol and acetone mixture (50
:
50 v/v) at reflux condition for 1 h, separated by using filter paper and dried at 120 °C for 4 h. Makeup of catalyst loss during the regeneration was done to reach the optimized catalyst loading value. There was a very negligible decrease in the final conversion of benzoic anhydride (Fig. 14). Recovered catalyst after the 4th reuse was characterized by different techniques and found to be the same in the nature as the fresh one. Hence catalyst is reusable.
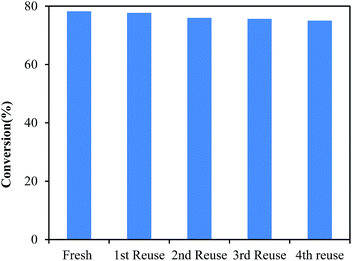 |
| Fig. 14 Reusability of catalyst. Benzoic anhydride 0.0057 mol, diphenyl oxide 0.057 mol, catalyst loading 0.03 g cm−3, temperature 130 °C, speed of agitation 800 rpm, total volume 10.1 cm3, reaction time 180 min. | |
Development of theoretical model
A detailed kinetic model was developed by using above results. The Eley–Rideal mechanism was supposed to be the best suited model based on the preliminary analysis. Consider D (diphenyl oxide), B (benzoic anhydride), product E (4-phenoxybenzophenone) and F (co-product benzoic acid). The detail of derivation of the model is reported in some of our work23,42 and hence the derivation part is given in ESI.†
Considering, the surface reaction between the chemisorbed BS and reactant D as the rate limiting step. The rate of benzoylation of diphenyl oxide based on the conversion of benzoic anhydride B is given as:
|
 | (1) |
We know that,
|
CD = CD0 − CB0XB = CB0(M − XB)
| (1b) |
Substituting in terms of XB and integrating the eqn (1), we have,
|
 | (2) |
The experimental data obtained at optimized conditions were used to validate the predicated model. Using Polymath 6.0 Software constants were calculated and the results are presented in Table 5. The Arrhenius plot was also made (Fig. 15) to get apparent activation energy as 22 kcal mol−1. It further supports the fact of kinetically controlled benzoylation of diphenyl oxide.
Table 5 Kinetics parameters of benzoylation of DPO at different temperature
No. |
T (K) |
k (cm6 mol−1 g−1 s−1) |
KB (cm3 mol−1) |
Activation energy (E) (kcal mol−1) |
1 |
383 |
0.038 |
0.14 |
22 |
2 |
393 |
0.079 |
0.11 |
3 |
403 |
0.166 |
0.09 |
4 |
413 |
0.302 |
0.07 |
 |
| Fig. 15 Arrhenius plot for benzoylation of diphenyl oxide. | |
For the validation of derived mathematical model (eqn (2)), we have calculated the theoretical or predicted conversion by using the obtained rate constant and adsorption constant for different reaction condition. These conversion values are then plotted in the Fig. 11 (catalyst loading effect), 12 (mole ratio effect) and 13 (temperature effect) as dotted line along with the experimental value of conversion. The plot shows the best fitting of the theoretical value and the experimentally obtained value, hence validates the model very well.
Conclusion
Aluminium exchanged DTP supported on montmorillonite K-10 with varying amount of Al content (0.33 to 1) was prepared and characterized by different techniques. The catalysts were tested for the selective preparation of 4-phenoxybenzophenoen using benzoic anhydride as benzoylation agent. Al0.66-DTP/K-10 was the most active catalyst among the prepared catalysts. Effect of different supports on the activity of Al0.66-DTP for benzoylation of diphenyl oxide was studied and its activity was found in the following order Al0.66-DTP/K-10 > Al0.66-DTP/SnO2 > Al0.66-DTP/ZrO2. The surface area and acidity of the supports plays an important role for their activity in benzoylation reaction. A detailed investigation of various reaction parameters was done and optimized to get the maximum yield of the product vis-a-vis that reported so far. The catalyst stability was also investigated and found to be heterogeneous in nature without any leaching of the active sites. Using benzoic anhydride as benzoylating agent not only results in better yield of product but also helps to avoid the use of acid chloride, thus making process green and economical. The kinetic modelling was done based on the Eley–Rideal mechanism and the apparent activation energy was found to be 22 kcal mol−1.
Conflict of interest
The authors declare no conflict of interest.
Nomenclature
B | Reactant species B, benzoic anhydride |
BS | Chemisorbed B |
D | Reactant species D, diphenyl oxide |
E | 4-Phenoxybenzophenone |
F | Benzoic acid |
B0 | Concentration of B in bulk liquid phase, (mol cm−3) |
CB | Concentration of B, (mol cm−3) |
CD | Concentration of D, (mol cm−3) |
CF | Concentration of F in, (mol cm−3) |
k | Reaction rate constant (cm6 mol−1 g−1 s−1) |
KB | Adsorption equilibrium constant for B (cm3 mol−1) |
M | Mole ratio of A to B |
w | Catalyst loading (g cm−3) |
XB | Fractional conversion of B |
Acronyms
K-10 | Montmorillonite clay |
Cs-DTP/K10 | Cs2.5H0.5PW12O40 supported on montmorillonite acid treated clay K-10 |
Al-DTP/K10 | AlxH(3−x) PW12O40 supported on montmorillonite acid treated clay K-10 |
Acknowledgements
M. S. Tiwari acknowledges University Grants Commission (UGC) for the award of BSR Senior Research Fellowship under its SAP program in Centre for Advanced Studies in Chemical Engineering. G. D. Yadav acknowledges support from R. T. Mody Distinguished Professor Endowment and J. C. Bose National Fellowship of Department of Science and Technology, Govt. of India.
References
- I. V. Kozhevnikov, Chem. Rev., 1998, 98, 171–198 CrossRef CAS PubMed
. - G. D. Yadav, N. S. Asthana and V. S. Kamble, Appl. Catal., A, 2003, 240(1), 53–69 CrossRef CAS
. - G. D. Yadav, Catal. Surv. Asia, 2005, 9(2), 117–137 CrossRef CAS
. - G. D. Yadav and H. G. Manyar, Microporous Mesoporous Mater., 2003, 63, 85–96 CrossRef CAS
. - F. Su, L. Ma, D. Song, X. Zhang and Y. Guo, Green Chem., 2013, 15, 885–890 RSC
. - K.-I. Shimizu, H. Furukawa, N. Kobayashi, Y. Itaya and A. Satsuma, Green Chem., 2009, 11, 1627–1632 RSC
. - K. Shimizu, K. Niimi and A. Satsuma, Catal. Commun., 2008, 9, 980–983 CrossRef CAS
. - G. D. Yadav and M. S. Krishnan, Ind. Eng. Chem. Res., 1998, 37(8), 3358–3365 CrossRef CAS
. - G. D. Yadav, P. K. Goel and A. V. Joshi, Green Chem., 2001, 3(2), 92–99 RSC
. - B. M. Devassy, F. Lefebvre and S. B. Halligudi, J. Catal., 2005, 231, 1–10 CrossRef CAS
. - R. M. Ladera, M. Ojeda, J. L. G. Fierro and S. Rojas, Catal. Sci. Technol., 2015, 5, 484–491 CAS
. - M. Srinivas, G. Raveendra, G. Parameswaram, P. S. Sai Prasad and N. Lingaiah, J. Mol. Catal. A: Chem., 2016, 413, 7–14 CrossRef CAS
. - K. Srilatha, N. Lingaiah, B. L. A. Prabhavathi Devi, R. B. N. Prasad, S. Venkateswar and P. S. Sai Prasad, Appl. Catal., A, 2009, 365, 28–33 CrossRef CAS
. - E. Rafiee, M. Khodayari, S. Shahebrahimi and M. Joshaghani, J. Mol. Catal. A: Chem., 2011, 351, 204–209 CrossRef CAS
. - K. You, R. Deng, J. Jian, P. Liu, Q. Ai and H. A. Luo, RSC Adv., 2015, 5, 73083–73090 RSC
. - G. Karthikeyan and A. Pandurangan, J. Mol. Catal. A: Chem., 2009, 311, 36–45 CrossRef CAS
. - T. Pinto, V. Dufaud and F. Lefebvre, Appl. Catal., A, 2014, 483, 103 CrossRef CAS
. - P. Sharma, S. Vyas and A. Patel, J. Mol. Catal. A: Chem., 2004, 214, 281–286 CrossRef CAS
. - P. Ferreira, I. M. Fonseca, A. M. Ramos, J. Vital and J. E. Castanheiro, Catal. Commun., 2011, 12, 573–576 CrossRef CAS
. - E. Rafiee and M. Khodayari, RSC Adv., 2016, 6, 36433–36440 RSC
. - G. D. Yadav and N. Kirthivasan, J. Chem. Soc., Chem. Commun., 1995, 203–204 RSC
. - G. D. Yadav and N. S. Doshi, Catal. Today, 2000, 60, 263–273 CrossRef CAS
. - M. S. Tiwari and G. D. Yadav, Chem. Eng. J., 2015, 266, 64–73 CrossRef CAS
. - G. D. Yadav and G. George, J. Mol. Catal. A: Chem., 2008, 292, 54–61 CrossRef CAS
. - C. Ramesh Kumar, P. S. Sai Prasad and N. Lingaiah, J. Mol. Catal. A: Chem., 2011, 350, 83–90 CrossRef CAS
. - C. R. Kumar, K. Jagadeeswaraiah, P. S. Sai Prasad and N. Lingaiah, ChemCatChem, 2012, 4, 1360–1367 CrossRef CAS
. - T. Baba, H. Watanabe and Y. Ono, J. Phys. Chem., 1983, 87, 2406–2411 CrossRef CAS
. - T. Baba, J. Sakai and Y. Ono, Bull. Chem. Soc. Jpn., 1982, 55, 2657–2658 CrossRef CAS
. - A. K. Gosh and J. B. Moffat, J. Catal., 1986, 101, 238–245 CrossRef
. - G. D. Yadav and S. B. Kamble, Ind. Eng. Chem. Res., 2008, 48(21), 9383–9393 CrossRef
. - G. D. Yadav and S. Sengupta, Org. Process Res. Dev., 2002, 6, 256–262 CrossRef CAS
. - G. Gliozzi, S. Passeri, F. Bortolani, M. Ardizzi, P. Mangifesta and F. Cavani, Catalysts, 2015, 5, 2223–2243 CrossRef CAS
. - M. S. Tiwari, G. D. Yadav and F. T. T. Ng, Can. J. Chem. Eng., 2014, 92, 2157–2165 CrossRef CAS
. - D. P. Sawant, B. M. Devassy and S. B. Halligudi, J. Mol. Catal. A: Chem., 2007, 217, 211–217 CrossRef
. - T. Raja, A. P. Singh, A. V. Ramaswamy, A. Finiels and P. Moreau, Appl. Catal., A, 2001, 211, 31–39 CrossRef CAS
. - E. G. Derouane, J. Mol. Catal. A: Chem., 1998, 134, 29–45 CrossRef CAS
. - G. D. Yadav and P. S. Surve, Appl. Catal., A, 2013, 468, 112–119 CrossRef CAS
. - J. B. Highfield, B. K. Hodnett, J. B. McMonagle and J. B. Moffat, Proc. 8th Int. Congr. Catalysis, ed. IUPAC, Verlag Chemie, Frankfurt am Main, 1984, vol. 5, p. 611 Search PubMed
. - W. Zhang, P. Jiang, Y. Wang, J. Zhang and P. Zhang, Catal. Sci. Technol., 2015, 5, 101 CAS
. - G. Varadwaj, S. Rana and K. Parida, Chem. Eng. J., 2013, 215–216, 849–858 CrossRef CAS
. - O. S. Ahmed and D. K. Dutta, Thermochim. Acta, 2003, 395, 209–216 CrossRef CAS
. - G. D. Yadav and J. J. Nair, Langmuir, 2000, 16(9), 4072–4079 CrossRef CAS
.
Footnote |
† Electronic supplementary information (ESI) available. See DOI: 10.1039/c6ra05379c |
|
This journal is © The Royal Society of Chemistry 2016 |
Click here to see how this site uses Cookies. View our privacy policy here.