DOI:
10.1039/C6RA02929A
(Paper)
RSC Adv., 2016,
6, 25185-25190
Insight into composition evolution in the synthesis of high-performance Cu/SiO2 catalysts for CO2 hydrogenation†
Received
1st February 2016
, Accepted 26th February 2016
First published on 29th February 2016
Abstract
High-performance catalysts are the key factor for CO2 activation and conversion. In this paper, we systematically investigate the whole composition evolution process of Cu/SiO2 catalysts for CO2 hydrogenation. The precursor gradually evolved from amorphous Cu species to copper phyllosilicate, then to CuO with the increase of calcination temperature from ambient temperature to 700 °C. With the evolution of the precursor, the corresponding species after reduction were gradually evolved from Cu0 to Cu+, then to Cu0 again. The ratios of Cu+/(Cu+ + Cu0) are positively correlated with the catalytic activities. The Cu+ species derived from copper phyllosilicate were demonstrated to be crucial in achieving high-performance Cu/SiO2 catalysts for CO2 hydrogenation. The composition evolution has been demonstrated to be an efficient strategy to synthesize high-performance catalysts. This strategy of composition evolution can be applied to the synthesis of other high-performance Cu-based heterogeneous catalysts.
1. Introduction
CO2 is one of the major “greenhouse gases”.1 Recently, CO2 emission along with urbanization has become one of the most important issues around the world, because the rapidly increasing CO2 concentration in the atmosphere leads to global climate changes (e.g., ocean acidification, global warming and so on).2–5 Although natural photosynthesis can convert CO2 to organic carbon, it is far from enough to consume so much CO2 in a short period with its increasing concentration.6 Hence, finding a new way to achieve resource utilization of CO2 is quite necessary and urgent.
Catalytic conversion of CO2 to high value-added chemicals, such as methanol, formic acid, dimethyl carbonate, cyclic carbonates and so on, was demonstrated to be an efficient way to achieve resource utilization of CO2.7–15 CO2 hydrogenation reaction is one of the most important CO2 catalytic conversion reactions.16–21 Cu-based catalysts have been widely used for CO2 hydrogenation.22–24 However, the catalytic performance of Cu-based catalysts are still relatively low. Thus, it is essential to develop high-performance Cu-based catalysts for CO2 hydrogenation.
It is well-known that the synthesis processes of heterogeneous catalysts contain multi steps, and the compositions would undergo complicated changes.25–30 The composition evolution will be a efficient strategy to synthesize high-performance catalysts.
In this paper, we systematically investigate the whole composition evolution processes of Cu/SiO2 catalysts for CO2 hydrogenation. The whole synthesis processes were composed of three steps: ammonia-evaporation, calcination and reduction. Combining the powder XRD, quasi-in situ XPS and XAES, the whole composition evolution processes were tracked in the three steps. Moreover, according to the catalytic performance, calcination step was found to be the key step in the whole synthesis process. In the calcination step, the precursor gradually evolved from amorphous Cu species, to copper phyllosilicate, then to CuO with the increase of calcination temperature from ambient temperature to 700 °C, which leads to the different ratios of Cu+/(Cu+ + Cu0) in the final catalysts after reduction. The ratios of Cu+/(Cu+ + Cu0) are positively correlated with the catalytic activities. The Cu+ species derived from copper phyllosilicate were demonstrated to be the crucial role to achieve high-performance Cu/SiO2 catalysts for CO2 hydrogenation.
2. Experimental
2.1 Materials
The following materials were used for this experiment: Cu(NO3)2·3H2O (AR, Aladdin Reagent Co., Ltd, China), 28% ammonia aqueous solution (Sinopharm Chemical Reagent Co., Ltd, China), silica gel (AR, Aladdin Reagent Co., Ltd, China), and ultrapure water (18 MΩ cm). All chemicals were used as received without further purification. Glove box filled with high-pure argon was used for protecting the as-synthesized samples and catalysts.
2.2 Catalyst preparation
Four Cu/SiO2 catalysts treated with different prepared conditions were synthesized by ammonia-evaporation method,31,32 and described as follows. 7.5 g of Cu(NO3)2·3H2O was dissolved in 100 mL of ultrapure water, and 28% ammonia aqueous solution was then dropped to form a copper ammonia complex solution with pH value of 10–11. 15 g of silica gel was subsequently added into the copper ammonia complex solution and stirred for about 10 h. Then, the suspension was heated at 70 °C to evaporate ammonia. The evaporation process was not stopped until the pH value of the suspension decreased to 6–7. The precipitate was washed with deionized water and dried at 100 °C for 8 h. Then, the catalyst precursors were calcined in air at 300 °C, 500 °C, and 700 °C for 5 h, respectively, and denoted as Cu–Si–O-T, where T represents the calcination temperature. The calcined precursors were reduced at 300 °C for 2 h under pure H2 atmosphere and the reduced Cu/SiO2 catalysts were denoted as Cu–Si-T, where T represents the calcination temperature. Moreover, the precursor without calcination was as a reference, and denoted as Cu–Si–O-no calcination (Cu–Si–O-no cal.). After reduction at 300 °C under pure H2 atmosphere, the corresponding reduced catalyst was denoted as Cu–Si-no calcination (Cu–Si-no cal.).
2.3 Catalyst characterization
The Cu loading was analyzed by inductively coupled plasma (ICP), which was carried out on Ultima2 plasma emission spectrometer from Jobin Yvon.
The BET surface area was determined by N2 adsorption–desorption at liquid nitrogen temperature (77 K), which performed on Micromeritics ASAP 2020. The specific surface area was calculated from the isotherms using the Brunauere–Emmette–Teller (BET) method. Average pore size was calculated by Barrett–Joyner–Halenda (BJH) equation in desorption branch.
The Fourier translation infrared (FT-IR) spectrum was measured using a Perkin-Elmer Spectrum One FT-IR spectrophotometer in the range of 1600–400 cm−1. The sample were finely grounded, dispersed in KBr and pelletized.
The powder X-ray diffraction (PXRD) patterns were collected with a Rigaku Miniflex 600 diffractometer at 40 kV and 15 mA for Cu-Kα radiation (λ = 1.5406 Å) with a scan speed of 1° min−1 in the 2θ range of 15–75°.
Temperature-programmed reduction (TPR) was carried out on Altamira Instruments (AMI-300) at atmospheric pressure. Thermal conductivity detector (TCD) current was 75 mA, and the detector temperature was 100 °C. The calcined Cu–Si–O-T precursor was outgassed at 120 °C under Ar for 30 min. After cooling to room temperature under Ar, the gas was switched to a 10% H2/Ar mixture gas flowing at 30 mL min−1, and then the sample was heated up to 300 °C at a ramping rate of 10 °C min−1. The amount of H2 consumed was monitored by TCD.
Transmission electron microscopy (TEM) was performed on Titan F20 field-emission transmission electron microscopy at low temperature (105 K) by liquid-nitrogen cooling.
Quasi-in situ X-ray photoelectron spectroscopy (XPS) and X-ray auger electron spectroscopy (XAES) measurements were performed with a Thermo Fisher ESCALAB 250Xi spectrometer equipped with an Al anode (Al-Kα = 1486.6 eV). For the Cu/SiO2 precursors, the measurements were performed directly. For the reduced Cu–Si-T catalysts, a quasi-in situ reduction reactor installed in the Thermo Fisher ESCALAB 250Xi spectrometer chamber was used to reduce the Cu/SiO2 precursors. After reduction, the reduced Cu–Si-T catalysts were directly transferred to analytical chamber to avoid exposure to air. All samples were pressed into wafer for measurement.
2.4 Activity evaluation
The catalytic performance measurements of the reduced Cu–Si-T catalysts for CO2 hydrogenation were carried out in a continuous-flow, high-pressure and fixed-bed reactor. Before reaction, the calcined Cu–Si–O-T precursors were reduced under pure H2 at a flow rate of 20 mL min−1 under atmospheric pressure. The reduction temperature was programmed to increase from room temperature to 300 °C and maintained at 300 °C for 2 h. The reactor was then cooled to room temperature. After reduction, the catalytic reaction was carried out under the conditions of 3.0 MPa, V(CO2)
:
V(H2) = 1
:
4, 5% N2 as internal standard gas, and weight hour space velocity of CO2 (WHSV) = 16 L gcat.−1 h−1. The composition of the raw gases and products was monitored using an on-line Shimadzu GC-2014 gas chromatograph equipped with a thermal conductivity detector and a flame ionization detector.
The conversion of CO2, the selectivity to CO and CH3OH, and the weight-time yield (WTY) of CH3OH were calculated using the following formulas:
Conversion of CO2 (%) = ([CO2]in/[N2]in − [CO2]out/[N2]out)/([CO2]in/[N2]in) × 100% |
Selectivity to CO (%) = [(R-FCO × ACO)/(R-FCO2 × ACO2)] × [(1 − CCO2)/CCO2] |
Selectivity to CH3OH (%) = (R-FCH3OH × ACH3OH)/(R-FCH3OH × ACH3OH + R-FCH4 × ACH4) × (1 − SCO) |
Selectivity to CH4 (%) = 1 − SCO − SCH3OH |
where [N
2]
in and [N
2]
out are the concentrations of N
2 at the inlet and outlet, [CO
2]
in and [CO
2]
out are the concentrations of the CO
2 at the inlet and outlet, respectively.
A: the chromatographic peak area; R-F: the relative correction factor;
SCO: selectivity to CO;
SCH3OH: selectivity to CH
3OH.
3. Results and discussion
3.1 Catalytic activity
The performance of CO2 hydrogenation reaction over series of the reduced Cu–Si-T catalysts with different calcination condition were performed at different reaction temperature at 3.0 MPa and 16 L gcat.−1 h−1. Products of CO2 hydrogenation reaction over the reduced Cu–Si-T catalysts include CO, CH3OH and CH4. The corresponding selectivities to CO, CH3OH and CH4 are presented in Fig. S1 (details shown in ESI†). The conversions of CO2 over the reduced Cu–Si-T catalysts with different reaction temperatures are shown in Fig. 1. When the reaction temperature at 320 °C, the conversion of CO2 over the Cu–Si-no cal. catalyst is 12.6%. Along with the increasing of calcination temperature from 300 to 500 °C, the conversions of CO2 raise from 19.3% to 24.9%. When the calcination temperature is further improved to 700 °C, the conversion of CO2 over the reduced Cu–Si-700 catalyst obviously decreases, suggesting that the conversion of CO2 over the reduced Cu–Si-500 catalyst reaches the maximum value. Reaction temperature at 280, 300 and 340 °C, there are similar trends. The conversions of CO2 firstly climb up and then decline with the increasing of calcination temperature. The trend of catalytic activities is volcanic type at each reaction temperature, which suggests that calcination temperature would greatly affect the catalytic activities of Cu/SiO2 catalysts synthesized by ammonia-evaporation method for CO2 hydrogenation. To explore the original effect of composition evolution on the catalytic activity, a series of characterization experiments were firstly performed on the reduced Cu–Si-T catalysts.
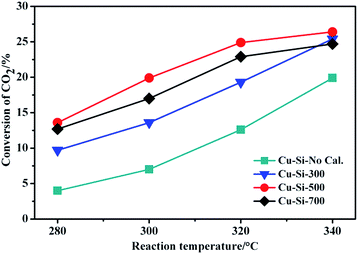 |
| Fig. 1 Conversions of CO2 over the reduced Cu–Si-T catalysts. Reaction condition: 0.3 g catalyst, 3.0 MPa and WHSV of 16 L gcat.−1 h−1. | |
3.2 Characterizations of the reduced Cu–Si-T catalysts
The physicochemical properties of the reduced Cu–Si-T catalysts are shown in Table 1, respectively. Cu loadings determined by ICP for the reduced catalysts are close to (11.0 ± 0.1) wt%, which eliminates the influence of Cu loading on the catalytic activity. N2 adsorption–desorption isotherms of the reduced Cu–Si-T catalysts are presented in Fig. S2.† The BET surface area plots (Fig. S3†) of the reduced Cu–Si-T catalysts were determined by N2 adsorption–desorption isotherms. And corresponding average pore sizes were calculated by BJH equation in desorption branch.33 In Table 1, the BET surface area of the reduced Cu–Si-T catalysts firstly increases from 421.2 to 432.0 m2 g−1, and then decreases to 397.7 m2 g−1 along with the increasing of calcination temperature from ambient temperature to 700 °C. The BET surface area of the Cu–Si-500 catalyst is higher than those of other reduced Cu–Si-T catalysts, and the average pore size of the Cu–Si-500 catalyst is smaller than those of other reduced Cu–Si-T catalysts, indicating that calcination temperature affects the BET surface area and average pore size, and the suitable calcination temperature (500 °C) is of benefit to obtain catalyst with higher BET surface area and smaller average pore size.
Table 1 Physicochemical properties of the reduced Cu–Si-T catalysts
Catalysts |
Cu loading (%) |
BET surface area (m2 g−1) |
Average pore size (nm) |
Cu–Si-no cal. |
11.1 |
421.2 |
5.2 |
Cu–Si-300 |
11.0 |
428.4 |
5.0 |
Cu–Si-500 |
10.9 |
432.0 |
4.9 |
Cu–Si-700 |
11.1 |
397.7 |
5.0 |
TEM images and the corresponding particle size distribution diagrams of the reduced Cu–Si-T catalysts are displayed in Fig. 2, respectively. The Cu nanoparticles are well dispersed on the surface of SiO2 support for the four reduced Cu–Si-T catalysts. And the average size of Cu nanoparticles for the four reduced Cu–Si-T catalysts is close to each other (2–3 nm), which can exclude that the effect of particle size on the difference of catalytic activities of the reduced Cu–Si-T catalysts for CO2 hydrogenation.
 |
| Fig. 2 TEM images of the reduced Cu–Si-T catalysts: (a) Cu–Si-no cal., (b) Cu–Si-300, (c) Cu–Si-500, (d) Cu–Si-700. The insets show the corresponding size distribution diagrams. | |
The PXRD patterns (Fig. 3a and d) of the reduced Cu–Si-no cal. and Cu–Si-700 catalysts show obvious Cu phases (2θ = 43.30, 50.44, and 74.10°, PDF#70-3039). In Fig. 3b–d, the diffraction peak centered at 37.0° is indexed to Cu2O phase (PDF#34-1354). Actually, the Cu and Cu2O phases co-exist in all the reduced Cu–Si-T catalysts. Because of the relative less content of Cu or Cu2O in the corresponding catalysts, their corresponding diffraction peaks are invisible. Quasi-in situ XPS and XAES were further carried out to quantify the ratio of Cu+ and Cu0.
 |
| Fig. 3 PXRD patterns of the reduced Cu–Si-T catalysts: (a) Cu–Si-no cal., (b) Cu–Si-300, (c) Cu–Si-500, (d) Cu–Si-700. | |
The calcined Cu–Si–O-T precursors were reduced in a quasi-in situ reduction reactor installed in the Thermo Fisher ESCALAB 250Xi spectrometer chamber. After reduction, the reduced Cu–Si-T catalysts were directly transferred the analytical chamber to avoid exposure to air. The Cu2+ satellite peaks in the Cu 2p XPS spectra (Fig. S4†) of the reduced Cu–Si-T catalysts are invisible, implying that the Cu2+ species have been completely reduced to Cu+ or Cu0 species. Cu LMM XAES spectra (Fig. 4) of the reduced Cu–Si-T catalysts were further carried out to distinguish and quantify the ratio of Cu+ and Cu0. The ratios of Cu+/(Cu+ + Cu0) in the reduced Cu–Si-T catalysts are 0.55, 0.70, 0.93, 0.74, respectively. The ratio of Cu+/(Cu+ + Cu0) firstly increases and then decreases along with the changing of calcination condition.
 |
| Fig. 4 Quasi-in situ Cu LMM XAES spectra of the reduced Cu–Si-T catalysts: (a) Cu–Si-no cal., (b) Cu–Si-300, (c) Cu–Si-500, (d) Cu–Si-700. | |
Based on the above results, it can be concluded that calcination temperature may obviously affect the catalytic activities of the reduced Cu–Si-T catalysts by adjusting the ratios of Cu+/(Cu+ + Cu0). However, how could calcination temperature control the ratios of Cu+/(Cu+ + Cu0)? The calcined Cu–Si–O-T precursors were further characterized in details below.
3.3 Characterizations of the Cu–Si–O-T precursors
Firstly, the compositions of the calcined and without calcined Cu–Si–O-T precursors are identified by PXRD patterns (Fig. 5). The board diffraction peak centered at 22° belongs to the amorphous SiO2 support.34 In Fig. 5a, there is no other obvious diffraction peak, indicating that the Cu species existed in the amorphous form in the Cu–Si–O-no cal. precursor. In Fig. 5b–d, the diffraction peaks centered around at 30.8, 35.0, 57.5, and 62.4° are indexed to the phase of copper phyllosilicate (PDF#27-0188), indicating that calcination is of benefit to form copper phyllosilicate. Compared with the standard peaks, the actual diffraction peaks of copper phyllosilicate in the calcined Cu–Si–O-T precursors shift slightly to higher degrees with the increasing of calcination temperature, suggesting that the higher temperature calcination treatment can decrease the cell volume of copper phyllosilicate due to the loss of crystalliferous water or coordinated OH group.35 Furthermore, the phase of CuO (2θ = 35.2, 38.4, 48.4°) (PDF#44-0706) appeared in the calcined Cu–Si–O-700 precursor (Fig. 5d), indicating that partial copper phyllosilicate has been destroyed and converted to CuO after calcination at 700 °C. In addition, FT-IR spectra of the calcined and without calcined Cu–Si–O-T precursors (Fig. S5†) were also measured. The δOH band at 670 cm−1 and the νSiO shoulder peak at 1042 cm−1 suggest the presence of copper phyllosilicate in the calcined Cu–Si–O-T precursors.34 However, considering the similar PXRD patterns of the calcined Cu–Si–O-300 and Cu–Si–O-500 precursors, why do the corresponding catalytic activities show apparent difference?
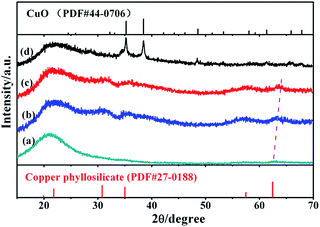 |
| Fig. 5 PXRD patterns of the calcined Cu–Si–O-T precursors: (a) Cu–Si-no cal., (b) Cu–Si–O-300, (c) Cu–Si–O-500 and (d) Cu–Si–O-700. | |
The Cu 2p XPS spectra of the calcined Cu–Si–O-T precursors were further measured to analysis of the valence of copper species in the calcined Cu–Si–O-T precursors (Fig. 6). The Cu 2p3/2 peaks at 933.0–936.0 eV and the corresponding satellite peaks suggest that the oxidation state of Cu is +2 in all the calcined Cu–Si–O-T precursors. After deconvolution processing of Cu 2p3/2 peaks, it is obvious that binding energies (BE) of Cu 2p3/2 are at 935.9 and 934.5 eV, respectively, indicating that there are two kinds of Cu2+ species in the calcined Cu–Si–O-T precursors. And the Cu 2p3/2 peak at 935.9 eV should be attributed to copper phyllosilicate, while that at 934.5 eV should be ascribed to CuO or other Cu2+ species.33 Moreover, based on the results of PXRD in Fig. 5a, Cu2+ species in the Cu–Si-no cal. precursor should be all amorphous state. Notably, it is important to emphasize that the proportion of copper phyllosilicate increases as the calcination temperature rising from ambient temperature to 500 °C, while it decreases as the calcination temperature increasing from 500 to 700 °C, indicating that 500 °C is quite suitable for forming abundant copper phyllosilicate, which is responsible for the high percentage of Cu+ demonstrated by quasi-in situ Cu LMM XAES spectra in Fig. 4. The above results of PXRD and Cu 2p XPS show that the calcined Cu–Si–O-T precursors were composed with copper phyllosilicate and/or CuO/Cu2+ species. The reduction temperature of copper phyllosilicate to Cu+ is lower than that of CuO to Cu0.31 Furthermore, H2-TPR profiles of the calcined Cu–Si–O-T precursors presented the reduction peaks of the calcined Cu–Si–O-T precursors firstly shift to lower temperature before 500 °C calcination and then to higher temperature after 700 °C calcination (Fig. S6†). Therefore, the amount of copper phyllosilicate in the calcined Cu–Si–O-T precursors firstly increases and then decreases with the calcination temperature increasing from ambient temperature to 700 °C can be proved by the results of PXRD, Cu 2p XPS and H2-TPR characterizations.
 |
| Fig. 6 Cu 2p XPS spectra of the calcined Cu–Si–O-T precursors: (a) Cu–Si-no cal., (b) Cu–Si–O-300, (c) Cu–Si–O-500, (d) Cu–Si–O-700. | |
Based on the results and discussion, the influence of Cu loading and particle size on the catalytic activities has been excluded. Remarkably, the relationships between conversion of CO2 and Cu+/(Cu+ + Cu0) over the reduced Cu–Si-T catalysts at different reaction temperature are presented in Fig. 7. It is obvious that there is a directly positively proportional relationship between conversion of CO2 and Cu+/(Cu+ + Cu0), indicating that the high performance of Cu/SiO2 catalysts is due to the high ratio of Cu+/(Cu+ + Cu0). The proportion of copper phyllosilicate in the calcined Cu–Si–O-T precursors, which is determined by calcination temperature, greatly affects the ratios of Cu+/(Cu+ + Cu0) after reduction. It is clear that calcination temperature would control the ratios of Cu+/(Cu+ + Cu0) by adjusting the proportion of copper phyllosilicate in the calcined Cu–Si–O-T precursors, while the ratios of Cu+/(Cu+ + Cu0) further determine the catalytic activities of the reduced Cu–Si-T catalysts for CO2 hydrogenation.
 |
| Fig. 7 The relationships between conversion of CO2 and Cu+/(Cu+ + Cu0) over the reduced Cu–Si-T catalysts at different reaction temperatures: (a) 340 °C, (b) 320 °C, (c) 300 °C and (d) 280 °C. | |
4. Conclusion
In summary, the composition evolution from amorphous Cu species to copper phyllosilicate and then to CuO driven by the calcination temperature in the Cu–Si–O-T precursors was elaborated in details. This composition evolution directly results in different ratios of Cu+/(Cu+ + Cu0). Moreover, the positive correlation between the ratios of Cu+/(Cu+ + Cu0) and the catalytic activities of the reduced Cu–Si-T catalysts was well established. Therefore, the whole correlation from the composition evolution in the precursors and catalysts to the catalytic performance was clearly demonstrated. The Cu+ species derived from copper phyllosilicate were demonstrated to be the crucial role to achieve high-performance Cu/SiO2 catalysts for CO2 hydrogenation. This work not only provides a strategy of composition evolution to synthesize high-performance Cu/SiO2 catalysts, but also gives some inspiration for the synthesis of other high-performance Cu-based heterogeneous catalysts.
Acknowledgements
We gratefully acknowledge financial support from the NSF of China (91545201, 21403237, 21303202, 21303203), the 973 Program (2013CB933200), and the NSF of Fujian Province (2014J05025).
Notes and references
- T. V. Ramachandra, B. H. Aithal and K. Sreejith, Renewable Sustainable Energy Rev., 2015, 44, 473–495 CrossRef.
- X. Ouyang and B. Lin, Renewable Sustainable Energy Rev., 2015, 45, 838–849 CrossRef CAS.
- A. S. Alshehry and M. Belloumi, Renewable Sustainable Energy Rev., 2015, 41, 237–247 CrossRef.
- X. Zhou, J. Zhang and J. Li, Energy Policy, 2013, 57, 43–51 CrossRef CAS.
- S. C. Doney, V. J. Fabry, R. A. Feely and J. A. Kleypas, Annual Review of Marine Science, 2009, 1, 169–192 CrossRef PubMed.
- P. Falkowski, R. J. Scholes, E. Boyle, J. Canadell, D. Canfield, J. Elser, J. Elser, N. Gruber, K. Hibbard, P. Högberg, S. Linder, F. T. Mackenzie, B. Moore III, T. Pedersen, Y. Rosenthal, S. Seitzinger, V. Smetacek and W. Steffen, Science, 2000, 290, 291–296 CrossRef CAS PubMed.
- J. Albo, M. Alvarez-Guerra, P. Castaño and A. Irabien, Green Chem., 2015, 17, 2304–2324 RSC.
- M. A. A. Aziz, A. A. Jalil, S. Triwahyono and A. Ahmad, Green Chem., 2015, 17, 2647–2663 RSC.
- F. Frusteri, M. Cordaro, C. Cannilla and G. Bonura, Appl. Catal., B, 2015, 162, 57–65 CrossRef CAS.
- Y. Chen, S. Choi and L. T. Thompson, ACS Catal., 2015, 5, 1717–1725 CrossRef CAS.
- C. Maeda, Y. Miyazaki and T. Ema, Catal. Sci. Technol., 2014, 4, 1482–1497 CAS.
- A. Bansode and A. Urakawa, J. Catal., 2014, 309, 66–70 CrossRef CAS.
- J. Liu, C. Li, F. Wang, S. He, H. Chen, Y. Zhao, M. Wei, D. G. Evans and X. Duan, Catal. Sci. Technol., 2013, 3, 2627–2633 CAS.
- D. Preti, C. Resta, S. Squarcialupi and G. Fachinetti, Angew. Chem., Int. Ed., 2011, 50, 12551–12554 CrossRef CAS PubMed.
- N. Keller, G. Rebmann and V. Keller, J. Mol. Catal. A: Chem., 2010, 317, 1–18 CrossRef CAS.
- X. Yang, S. Kattel, S. D. Senanayake, J. A. Boscoboinik, X. Nie, J. Graciani, J. A. Rodriguez, P. Liu, D. J. Stacchiola and J. G. Chen, J. Am. Chem. Soc., 2015, 137, 10104–10107 CrossRef CAS PubMed.
- C. Liu, B. Yang, E. Tyo, S. Seifert, J. DeBartolo, B. von Issendorff, P. Zapol, S. Vajda and L. A. Curtiss, J. Am. Chem. Soc., 2015, 137, 8676–8679 CrossRef CAS PubMed.
- J. Graciani, K. Mudiyanselage, F. Xu, A. E. Baber, J. Evans, S. D. Senanayake, D. J. Stacchiola, P. Liu, J. Hrbek, J. F. Sanz and J. A. Rodriguez, Science, 2014, 345, 546–550 CrossRef CAS PubMed.
- O. Martin and J. Pérez-Ramírez, Catal. Sci. Technol., 2013, 3, 3343–3352 CAS.
- Y.-N. Li, R. Ma, L.-N. He and Z.-F. Diao, Catal. Sci. Technol., 2014, 4, 1498–1512 CAS.
- I. Ganesh, Renewable Sustainable Energy Rev., 2014, 31, 221–257 CrossRef CAS.
- M. Behrens, F. Studt, I. Kasatkin, S. Kühl, M. Hävecker, F. Abild-Pedersen, S. Zander, F. Girgsdies, P. Kurr, B.-L. Kniep, M. Tovar, R. W. Fischer, J. K. Nørskov and R. Schlögl, Science, 2012, 336, 893–897 CrossRef CAS PubMed.
- E. L. Kunkes, F. Studt, F. Abild-Pedersen, R. Schlögl and M. Behrens, J. Catal., 2015, 328, 43–48 CrossRef CAS.
- P. Gao, L. Zhong, L. Zhang, H. Wang, N. Zhao, W. Wei and Y. Sun, Catal. Sci. Technol., 2015, 5, 4365–4377 CAS.
- R. Schlögl, Angew. Chem., Int. Ed., 2015, 54, 3465–3520 CrossRef PubMed.
- M. Behrens and R. Schlögl, Z. Anorg. Allg. Chem., 2013, 639, 2683–2695 CrossRef CAS.
- C. Xie, Q. Yang, Z. Xu and Y. Du, J. Mol. Catal. A: Chem., 2014, 381, 107–113 CrossRef CAS.
- Q. Chen, H. Liu, Y. Xin and X. Cheng, Electrochim. Acta, 2013, 111, 284–291 CrossRef CAS.
- W. Zhou, F. Sun, K. Pan, G. Tian, B. Jiang, Z. Ren, C. Tian and H. Fu, Adv. Funct. Mater., 2011, 21, 1922–1930 CrossRef CAS.
- P. Djinović, J. Batista and A. Pintar, Appl. Catal., A, 2008, 347, 23–33 CrossRef.
- Z.-Q. Wang, Z.-N. Xu, S.-Y. Peng, M.-J. Zhang, G. Lu, Q.-S. Chen, Y. Chen and G.-C. Guo, ACS Catal., 2015, 5, 4255–4259 CrossRef CAS.
- J. Lin, X. Zhao, Y. Cui, H. Zhang and D. Liao, Chem. Commun., 2012, 48, 1177–1179 RSC.
- L. F. Chen, P. J. Guo, M. H. Qiao, S. R. Yan, H. X. Li, W. Shen, H. L. Xu and K. N. Fan, J. Catal., 2008, 257, 172–180 CrossRef CAS.
- X. Zheng, H. Lin, J. Zheng, X. Duan and Y. Yuan, ACS Catal., 2013, 3, 2738–2749 CrossRef CAS.
- C. H. Yang, H. T. Wu, F. Yang and G. D. Hu, Ceram. Int., 2014, 40, 4753–4757 CrossRef CAS.
Footnote |
† Electronic supplementary information (ESI) available: Selectivity, BET, FT-IR, XPS, H2-TPR. See DOI: 10.1039/c6ra02929a |
|
This journal is © The Royal Society of Chemistry 2016 |
Click here to see how this site uses Cookies. View our privacy policy here.