DOI:
10.1039/C6RA02921C
(Paper)
RSC Adv., 2016,
6, 36786-36793
SrCe0.95Y0.05O3−δ–ZnO dual-phase membranes for hydrogen permeation
Received
1st February 2016
, Accepted 6th April 2016
First published on 7th April 2016
Abstract
A hydrogen permeation membrane plays a key role in membrane reactor applications for hydrogen production. To this end, a SrCe0.95Y0.05O3−δ (SCY) proton conductor has been regarded as an attractive candidate. This work aimed to increase the practical value of SCY by making its composite with ZnO. The presence of ZnO was found to increase the sinterability of SCY, resulting in a 200 °C reduction in the sintering temperature required to obtain a dense membrane as normally achieved at 1400 °C. The electrical conductivities of the composites in a hydrogen atmosphere were also enhanced by the addition of ZnO. The fact that the sintering of the composite membrane at 1200 °C leads to the formation of a dense composite body while not resulting in the formation of new phases detectable by powder X-ray diffractions highlights the chemical compatibility of SCY and ZnO. The phase stability of the composite to water was also improved relative to the pure SCY. Hydrogen permeation fluxes were increased with the ZnO content until 20% (by weight) over which, the flux degradation started to occur, most probably due to the ZnO reduction by hydrogen. As such, SCY–10% ZnO is deemed as the optimized composite. The maximum flux attained using this membrane was 0.039 mL (STP) cm−2 min−1 at 900 °C. Long term evaluation testing for over a 48 hour-period was performed where the SCY–10% ZnO membrane was subjected to alternating cycles of CO2 and N2 sweep gas flows. Despite the significant overall degradation in performance beyond the 3rd cycle, the results show substantial recovery in the performance over the 2nd and 3rd cycles. In contrast with these conventional perovskite and metal dual phase membranes, this work features an attractive concept to develop a proton conducting membrane from SCY-based composite membranes.
1. Introduction
A membrane reactor is an attractive chemical reaction engineering technique where reaction and separation can be performed simultaneously; the viability of which is determined by its reaction and separation efficiencies and membrane stability.1 Such a concept, due to its low cost and practicality, is of significant relevance to clean energy technology particularly in relation to the hydrogen (i.e., the best fuel candidate for a sustainable future) production and separation.2 Within this context, high temperature proton conducting ceramic (HTPCC) membranes which are mostly based on ABO3 perovskites from the family of BaCeO3, SrCeO3, BaZrO3 and SrZrO3, represent one of the most attractive membrane reactor technologies.3–10 Despite the highest proton conductivity observed in BaCeO3-based proton conductors, these compounds however also exhibit oxygen ionic conductivity which increases with increasing temperature.11 SrCeO3-based proton conductors on the other hand, appear to have predominant proton conductivity in hydrogen or steam containing atmosphere;12 primarily due to the suppression of oxygen ionic conduction within their distorted orthorhombic structure.13–15 To this end, to transport hydrogen, SrCeO3 compounds would be more suitable as a membrane material than BaCeO3 compounds. Still, the reported hydrogen permeability through SrCeO3-based membranes in a non-galvanic mode is quite low, i.e., in the order of magnitude of 10−2 mL cm−2 min−1 at ∼900 °C under H2/He gradients for a 1–1.5 cm-thick membrane.16 Moreover, these compounds require sintering to be performed at temperatures of at least 1400 °C to obtain dense membranes. Such high temperature sintering process is considered disadvantageous given the high energy consumption in addition to the risk of altering the metal elements distribution, i.e., re-distribution which may deteriorate the original ionic conductivity.17
The hydrogen permeation rate through the proton-based conducting perovskites is generally limited by the electronic transport given their lower electronic conductivity (relative to the proton conductivity), even in the doped perovskites.18 The electronic conductivity of these compounds therefore should be increased to enhance the hydrogen transport rate. This can be achieved by adding another percolative phase with high electronic conductivity such as metal (e.g., Ni, Ag, Pd, Au or Pt) or perovskite with prevailing electronic conductivity.19,20 Enhanced hydrogen fluxes have indeed been achieved in such dual-phase membranes, e.g., Ni–Ba(Zr0.1Ce0.7Y0.2)O3, Ni–BaCe0.95Tb0.05O3−δ, BaCe0.8Y0.2O3−δ–Ni and Ce0.8(Sm0.8Sr0.2)0.2O2−δ–SrTi0.5Fe0.5O3−δ.21–24 The future trend would be to move away from precious metals considering their high cost. Ni, a relatively cheap metal, has hitherto been widely used although it may form volatile liquid phase during sintering at very high temperature.25 This leads to possible reactions between the supposedly preserved individual phases. Furthermore, to avoid the oxidation of Ni to NiO, the sintering of Ni-containing dual-phase membranes should be performed in inert atmosphere which adds the synthesis complexity and cost.26 Accordingly, metal oxides are the more attractive alternatives as the electronic conductor phase.
In this work, zinc oxide (ZnO) was proposed as the electronic conducting phase for the main proton conductor phase of SrCe0.95Y0.05O3, together forming a dual-phase membrane for high temperature hydrogen permeation. Several hypotheses exist for choosing ZnO. Firstly, the presence of ZnO is expected to reduce the sintering temperature in accordance with its proven use as sintering aid, for example to lower the sintering temperature of gadolinium samarium zirconate and barium cerate based compounds.27 The improved sintering properties, remarkably, has not been obtained at the expense of its proton conductivity.28–31 Secondly, ZnO would contribute substantially towards improved electronic conductivity since it is an n-type electronic conductor particularly under H2-contaning atmosphere.32,33 Within this context, ZnO, for instance, has been used as a dopant to enhance the electronic conductivity of oxygen ionic conductor ceria-based compounds over a wide range of temperatures and oxygen partial pressures.34,35 Thirdly, ZnO has almost similar value of thermal expansion coefficient with (8 × 10−6 K−1) that of SrCeO3 (10.8 × 10−6 K−1) between 300 and 1273 K which minimizes the thermo-mechanical incompatibility issue between phases such as crack formation.34,36 ZnO, in addition, is widely regarded as an inexpensive, non-toxic and chemically stable material which is abundantly available in nature. Accordingly, this paper strives to systematically study the chemical and sintering compatibility, electrical conductivity and hydrogen permeation properties of dual-phase membranes of SrCe0.95Y0.05O3–ZnO. The effects of adding up to 20% (by weight) of ZnO (into SrCe0.95Y0.05O3 main phase) to these properties were discussed.
2. Experimental sections
2.1. Preparation of SrCe0.95Y0.05O3 (SCY) powders and dense SCY–ZnO dual-phase dense membranes
SrCe0.95Y0.05O3 (SCY) powder was synthesized through the citric acid/ethylene glycol complexation and ammonium nitrate combustion combined route. Sr(NO3)2, Ce(NO3)3·6H2O, Y(NO3)3·6H2O, all in analytical grade, were used as the metal ion precursors. Citric acid (CA) and ethylene glycol (EG) with at least 99.5% purities were used as the chelating agents. Ammonium nitrate (NH4NO3) was used as the combusting agent. The stoichiometric amounts of metal nitrates were dissolved into de-ionized water. CA, EG and NH4NO3 were then added into the mixture sequentially under stirring. The molar ratios of the total metal ions, CA, EG and NH4NO3 were kept at 1
:
1.2
:
1.4
:
5. The pH of the solution was adjusted using NH4OH and/or HNO3 to approximately 4 to prevent selective precipitation. The mixture was then heated to 80 °C over a hot plate under constant stirring. The water was then evaporated by heating at 100 °C; resulting in the formation of a viscous gel. This gel was transferred to a 1 L beaker and then heated inside an oven at 430 °C, during which the auto-combustion of the gel occurred; resulting in the fine SCY powder precursor. This precursor was calcined for 5 hours at temperatures between 750 and 1000 °C in an air atmosphere to form the perovskite phase. The resultant perovskite powder was then milled for 48 hours followed by sieving through a 200-mesh screen sifter to remove large-size agglomerates.
To form dual-phase (composite) structure, the final SCY powder was mixed with ZnO powder (∼30 nm particle size) at different ratios for the two powders. Here, all the ratio values (percentage) are referred as the weight ratios or weight percentage. The powder mixtures were ground using mortar and pestle and milled inside the planetary mill. The powder mixtures (SCY–ZnO) were then pressed uniaxially at 10 MPa; forming the so-called “green disks” with the diameter of 2.5 cm. For the electrical conductivity measurements, some portions of the powders mixtures were also pressed into the so-called “green bars” with the dimension of 30 mm × 8 mm × 2 mm. These green disks and bars were finally sintered at temperatures between 1100 and 1400 °C to obtain dense bodies.
2.2. Chemical compatibility and phase stability tests
The chemical compatibility of SCY and ZnO was tested by subjecting their powders mixture (1
:
1 by weight ratio) to milling and 12 hour calcination at 1200 °C. To examine the phase stability of SCY–ZnO dual-phase membrane, the membrane sintered at 1200 °C was crushed and ground into powder which was exposed to 100% flowing CO2 gas for 30 hours at various temperatures between 100 and 850 °C. The phase stability of this dual-phase powder under extreme moisture environment was also tested by immersing the SCY–ZnO powders mixture within boiling water for 6 hours. The powder mixture was then recovered by filtration and dried at 200 °C for 24 hours.
2.3. Hydrogen permeation tests
Hydrogen (H2) permeation tests were performed using a home-made permeation cell. The disk membrane was fixed on top of an alumina tube and sealed using Ag paste as detailed elsewhere.37 Feed gas containing 21% (by volume) of H2 balanced by He was exposed to the feed side of the membrane while high purity N2 was used as sweep gas in the permeate side. The feed and sweep gas flow rates were controlled using mass flow controllers (D08-8B/ZM, Shanxi Chuangwei Instrument Co. Ltd., China). The flow rate of the effluent gas stream, i.e., the permeated hydrogen and sweep gas, was measured using a soap bubble flow meter. The composition of the effluent gas stream was analyzed using a gas chromatograph (Agilent 6890, Ar as the carrier gas) with a carbon molecular sieve column (4 m × Φ 3 mm). The hydrogen permeation flux was calculated as follows: |
 | (1) |
where Vt is the flow rate of the effluent gas stream; Am is the effective membrane area; yH2 and yN2 are the hydrogen and nitrogen volume fractions in the effluent gas stream, respectively. The existence of helium in less than 1 vol% in the effluent stream indicates a slight leakage from the sealing; the hydrogen flux from leakage had been subtracted using eqn (1).
2.4. Characterizations
The phase of the powders was analyzed by an X-ray diffractometer (XRD, Bruker D8 Advance, Germany) using Cu-K radiation (λ = 0.15404 nm). A continuous scan mode was used to collect 2θ data from 20 to 80 with a 0.02 sampling increment and a 2 min−1 scan rate. X-ray tube voltage and current were set at 40 kV and 30 mA, respectively. A scanning electron microscope (SEM, FEI Sirion 200, Netherlands) was used to examine the morphology of the membranes. Elemental distribution on the membranes was probed using energy dispersive X-ray analyzer (INCA oxford) attached to the SEM instrument. Crystal structures of crushed membrane was also investigated by transmission electron microscopy (model TECNAI G2TF20 S-TWIN) at 200 kV accelerating voltage. A copper grid coated with carbon and formava film was used to disperse the powder that has been mixed with acetone and treated in ultrasonic bath. The electrical conductivity of the sintered rectangular bar was measured in hydrogen atmosphere by the four-probe direct current method from room temperature to 800 °C using a Keithley 2400 Source Meter. As the current and voltage collectors, two silver wires were attached to the opposing ends of the bar using silver paste followed by heating at 750 °C for 4 hours in air. The bar was then placed inside the quartz tube and heated within the tubular furnace so that the temperature and atmosphere can be controlled. Current–voltage data were recorded in the current range of 0–1 A. The resistance of the bar was obtained from the slope of I–V plot by the least square method. The conductivity was calculated as follows: |
 | (2) |
where L, Re, and As represent the distance between the two wires (cm), the resistance of the bar specimen (Ω) and the cross-section area (cm2), respectively.
3. Results and discussion
3.1. Chemical compatibility and phase stability
Fig. 1a shows the powder X-ray diffraction (XRD) patterns of the individual SrCe0.95Y0.05O3 (SCY) and ZnO powders calcined at 1000 °C and the dual-phase SCY–ZnO membranes containing 10, 20 and 30 wt% of ZnO sintered at 1200 °C. SCY pattern exhibits the characteristic peaks of perovskite oxide [PDF-no. 831157] while ZnO presents its own characteristic peaks [PDF-no. 800075]. All peaks on the dual-phase patterns can be attributed to the peaks of the individual powders. This, together with the absence of new peaks (within the detection limit of XRD) indicates the absence of significant reactions between the SCY and ZnO phases up to 1200 °C and therefore mirrors the chemical compatibility of SCY and ZnO. The HRTEM images of the crushed dual phase membrane with 10% ZnO content are displayed in Fig. 1b. As expected, the lattice spacing of both oxide phases (SCY and ZnO) can be detected. For example, the spacing distances of 3.04 Å and 2.47 Å can be indexed to the SCY perovskite ((1 2 1) planes) and ZnO ((101) planes).
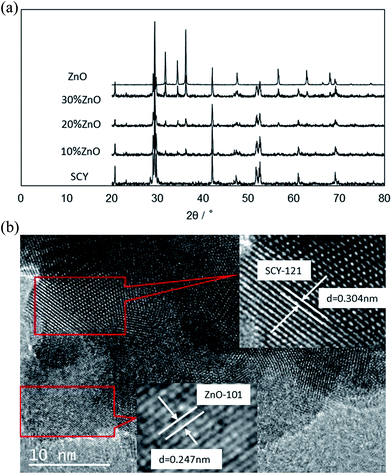 |
| Fig. 1 (a) Powder X-ray diffraction patterns of SrCe0.95Y0.05O3 and ZnO powders calcined at 1000 °C and SrCe0.95Y0.05O3–ZnO dual-phase membranes sintered at 1200 °C; (b) HRTEM images of the grounded SCY–ZnO (10 wt%) dual phase membrane sintered at 1200 °C. | |
The phase stabilities of the SCY and SCY–ZnO membranes were tested by subjecting them to boiling water for 6 hours and flowing CO2 at 850 °C for 30 hours. The practical value of H2 separation membrane lies in its application within the steam reforming reactions which involve exposure to H2O and CO2.3 Its stability in these components, therefore, is crucial. Powder X-ray diffraction patterns of these membranes after the tests are shown in Fig. 2 and 3. Upon comparing SCY/H2O pattern in Fig. 2 with the fresh SCY pattern, it is apparent that SCY has low phase stability in H2O. Its original structure was deteriorated during contact with boiling water. Likewise, the comparison between the remaining dual-phase patterns in Fig. 2 against their respective fresh patterns highlights the enhanced stability upon adding ZnO phase as implied by the retaining of all original peaks in the treated dual-phase powder patterns. This is likely due to the higher phase stability for ZnO or a small part of ZnO was dissolved into the lattice.30 Fig. 3 shows that both SCY membrane and dual-phase SCY–ZnO membrane are stable in CO2 as no other impurity phases were detected.
 |
| Fig. 2 Powder X-ray diffraction patterns of SrCe0.95Y0.05O3 and SrCe0.95Y0.05O3–ZnO dual-phase powders subjected to immersion in boiling water. | |
 |
| Fig. 3 Powder X-ray diffraction patterns of SrCe0.95Y0.05O3 and SrCe0.95Y0.05O3–ZnO dual-phase powders exposure to CO2. | |
3.2. Morphology
SCY membrane required sintering temperature of 1400 °C to form dense body. Dense SCY–ZnO dual-phase membrane, on the other hand, can be achieved by sintering at 1200 °C which signifies the reduction of sintering temperature of 200 °C. ZnO can thus be regarded as an efficient sintering aid in this particular case as is reported elsewhere.28–31 The morphology of the surface and cross sections of SCY–ZnO dual-phase membranes sintered at 1200 °C for 4 hours are displayed in Fig. 4. S and C in this figure denote the surface and cross-section area, respectively, while the number represents the weight% of ZnO. These images feature the formation of dense surface with well-defined sub-micro grains as well as some isolated pinholes across their cross-section area. Notably, the contrast between the individual phases becomes more apparent at larger ZnO content, i.e., SCY–20 wt% ZnO (S20). We used energy dispersive X-ray mapping (not shown here) to confirm that the brighter sections correspond to SCY while the darker sections correspond to ZnO. Fig. 5, in turn, displays the intensity distribution of Zn signals across the linear portion on the cross-section area of the membrane. The spreading out of the intensity implies the relatively uniform and dispersed distribution of ZnO.
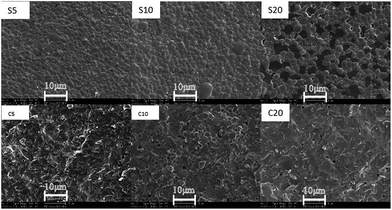 |
| Fig. 4 Scanning electron microscopy images of the surface and cross-section of SrCe0.95Y0.05O3–ZnO dual-phase membranes. | |
 |
| Fig. 5 Intensity distribution of Zn signals across linear portion on the cross-section area of SrCe0.95Y0.05O3–10 wt% ZnO dual-phase membrane. | |
3.3. Electrical conductivity
The Arrhenius plot of electrical conductivity for SCY, SCY–10 wt% ZnO and SCY–20 wt% ZnO in H2 displayed in Fig. 6 shows decreased conductivity with decreasing temperature and thus reflecting semiconducting behavior. The addition of ZnO increases the conductivity substantially (relative to SCY). Increasing ZnO content up to 20 wt% still results in minor improvement of the conductivity (relative to 10 wt% ZnO). The highest conductivity observed for SCY–20 wt% ZnO dual-phase membrane was 0.054 S cm−1 at 900 °C. The activation energy for the conductivity of this dual-phase membrane was 70.66 kJ mol−1.
 |
| Fig. 6 Arrhenius plot of electrical conductivity in hydrogen between 750 and 900 °C. | |
3.4. Hydrogen permeability
Temperature dependent hydrogen permeation fluxes through 1–1.5 mm-thick SCY and SCY–ZnO dual-phase disk membranes between 750 and 900 °C for feed gas and sweep gas flow rates of 123 and 142 mL min−1, respectively, are shown in Fig. 7. Increasing temperature boosts the fluxes due to increased surface exchange kinetics and proton bulk diffusion at higher temperatures.38 Larger ZnO content generally leads to enhanced permeation fluxes as captured by the increasing trend in the order of SCY, SCY–5% ZnO, SCY–10% ZnO and SCY–20% ZnO. It is also noted that the fluxes trend for SCY–20 wt% ZnO shows deviation to the other membranes trends (Fig. 7), i.e., reduction of fluxes starting at 850 °C, which can be understood in terms of ZnO reduction at higher temperature. This is as anticipated given the substantial content of ZnO in this dual-phase membrane. To this end, the compromise between the flux magnitude and the ZnO reduction renders SCY–10 wt% ZnO the most attractive composite. Despite the anticipated increase in hydrogen fluxes with increasing sweep gas flow rate from enlarging driving force obtained by the reduced hydrogen partial pressure in the permeate side. Fig. 8 shows that this effect becomes marginal beyond 120 mL min−1. The permeation fluxes reach its highest, 0.039 mL (STP) cm−2 min−1 for 1.09 mm-thick SCY–10% ZnO dual-phase membrane at 900 °C and feed gas and sweep gas flow rate of 90 and 138 mL min−1, respectively. This value is approximately 1.5 times higher than the flux of the same thick SCY membrane under similar conditions. Such enhancement in H2 permeation rate is attributed to the increased electronic conductivity from ZnO presence which contributes to the rise in ambipolar conductivity.30
 |
| Fig. 7 Temperature dependent hydrogen permeation fluxes through SrCe0.95Y0.05O3 and SrCe0.95Y0.05O3–ZnO dual-phase membranes between 750 and 900 °C. | |
 |
| Fig. 8 Hydrogen permeation fluxes as a function of sweep gas flow rate for SrCe0.95Y0.05O3–10 wt% ZnO dual-phase membrane. | |
3.5. Long term permeation stability
Long term evaluation was performed on 1.10 mm-thick SCY–10% ZnO membrane against alternating CO2 and N2 sweep gas flows (i.e., 100 mL min−1 CO2 flow rate and 120 mL min−1 N2 flow rate) to check its stability and recovery ability; the results of which are shown in Fig. 9. Despite the overall reduction in flux from 0.026 mL (STP) cm−2 min−1 to only 0.002 mL (STP) cm−2 min−1 over 48 hour-period, the membrane shows quite consistent performance and good recovery ability during the 2nd and 3rd alternating cycles. The original performance can be recovered in the 2nd cycle after returning the sweep gas back from CO2 to N2. In the next alternating cycle, reduction in performance however was shown, with approximately 92% of the original performance can be recovered. Marked reduction in performance then occurred during the subsequently alternating cycles, which highlights the insufficient stability of this membrane and the necessity to enhance it further to warrant its application as hydrogen permeation membrane in steam reforming reactions which involves the presence of CO2.
 |
| Fig. 9 Long term performance of SrCe0.95Y0.05O3–10 wt% ZnO dual-phase membrane subjected to alternating cycles of CO2 and N2 sweep gases. | |
3.6. Post-stability testing analysis
To understand what happens during these alternating cycles, the tested membrane was subjected to powder XRD, SEM and TEM analysis. Powder X-ray diffractions were performed on the feed and sweep sides of the membranes; the results of which are displayed in Fig. 10. Although majority of the characteristic peaks of the original perovskite and hexagonal wurtzite phases were retained, numerous new peaks appeared.
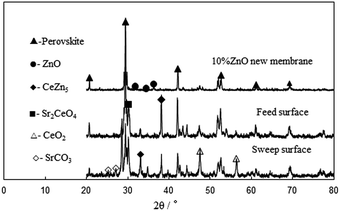 |
| Fig. 10 Powder X-ray diffraction patterns of the tested SrCe0.95Y0.05O3–10 wt% ZnO dual-phase membrane. | |
These new peaks can be assigned to the impurities phases produced, such as CeO2, CeZn5 and Sr2CeO4. In agreement with the XRD analysis (Fig. 10), the crystal planes of these impurity phases were also detected in the HRTEM images in Fig. 11. As can be seen, in addition to the (121) planes of SCY, the planes with spacing distance of 3.13 and 2.36 Å can be assigned to CeO2 (111) and CeZn5 (200), respectively. The appearance of an unusual phase of CeZn5 is sourced from the possible reactions during the hydrogen permeation test at high temperatures. Both tetravalent cerium in the SCY and ZnO can be reduced to metallic Ce and Zn, then could be further reacted to form CeZn5 at high temperatures. The distributions of these new phases are not homogenous on both membrane sides. SrCO3 and CeO2, for example, were not present on the feed side (Fig. 10) perhaps due to its subsequent reduction by H2 and formation of CeZn5. This indicates the complexity nature of the phase segregation and structure deterioration which occurred in the membranes exposed to non-uniform environment. Moreover, lower intensities for the peaks assigned to the original phases and the higher intensities for the new peaks indicated by the pattern on the sweep side (relative to the feed side). This reflects the larger deterioration rate on the sweep side as is expected upon exposing this side to CO2. SEM images on the tested membrane (Fig. 12a–c) reveal significant differences in its surface morphology with respect to the fresh membrane (S10-Fig. 4) despite the analogous cross-section morphology and the good mechanical integrity this membrane retained. The well-defined grains previously observed in the fresh membrane no longer exist in the feed side and sweep side of the tested membrane. There are instead minute-like particles distributed all over the feed side surface. Moreover, the sweep side surface also becomes very coarse and filled with dot-like pores; consistent with the large extent of reaction that took place on this side. When the content of ZnO in the composite membrane is more than 20 wt%, the membrane cannot be used for hydrogen permeation as it experienced serious leaking caused by the reduction of ZnO to Zn. Due to the low boiling point of zinc (906 °C), Zn is easily lost by evaporation during the high temperature test leaving a porous and gas-leaking ceramic membrane structure as shown in Fig. 12d.
 |
| Fig. 11 HRTEM images of the spent SCY–ZnO (10 wt%) dual phase membrane. | |
 |
| Fig. 12 Cross-section and surface morphologies of the tested SrCe0.95Y0.05O3–10 wt% ZnO dual-phase membrane (a–c) and the cross-section of the failed SrCe0.95Y0.05O3–20 wt% ZnO dual-phase membrane after the permeation test for 10 hours at 900 °C (d). | |
4. Conclusions
We have proven several points from our hypotheses. For example, the addition of ZnO as the second phase can reduce the sintering temperature of the dual-phase membrane (relative to the SrCe0.95Y0.05O3 (SCY)); the dual-phase membranes have higher electrical conductivities than the SCY membrane and SCY is chemically compatible with ZnO, at least up to 1200 °C. We also showed that the hydrogen permeation fluxes can reach 0.039 mL (STP) cm−2 min−1 for 1.09 mm-thick SCY–10% ZnO dual-phase membrane at 900 °C. Despite the insufficient stability the membrane displayed at the end of 48 hour stability testing, our study features an attractive concept towards developing improved version of SCY-based hydrogen permeation membranes.
Acknowledgements
The authors gratefully acknowledge the research funding provided by the National Natural Science Foundation of China (NSFC, No. 21476131, 21176187 and 21276147) and the Research Fund for the Doctoral Program of Higher Education of China (RFDP 20131201110007). S. Liu acknowledges the support from the Australian Research Council (ARC) through the Future Fellow Program (FT12100178).
Notes and references
- E. Kikuchi, Membrane reactor application to hydrogen production, Catal. Today, 2000, 56, 97–101 CrossRef CAS.
- M. Balat, Potential importance of hydrogen as a future solution to environmental and transportation problems, Int. J. Hydrogen Energy, 2008, 33, 4013–4029 CrossRef CAS.
- D. Medvedev, A. Murashkina, E. Pikalova, A. Demin, A. Podias and P. Tsiakaras, BaCeO3: materials development, properties and application, Prog. Mater. Sci., 2014, 60, 72–129 CrossRef CAS.
- Z. Tao, L. Yan, J. Qiao, B. Wang, L. Zhang and J. Zhang, A review of advanced proton-conducting materials for hydrogen separation, Prog. Mater. Sci., 2015, 75, 1–50 CrossRef.
- I.-M. Hung, Y.-J. Chiang, J. S. Ching Jang, J.-C. Lin, S.-W. Lee, J.-K. Chang and C.-S. Hsic, The proton conduction and hydrogen permeation characteristic of Sr(Ce0.6Zr0.4)0.85Y0.15O3−δ ceramic separation membrane, J. Eur. Ceram. Soc., 2015, 35, 163–170 CrossRef CAS.
- S. Zisekas, G. Karagiannakis, G. Marnellos and M. Stoukides, Study of ammonia decomposition in a proton conducting solid electrolyte cell, Ionics, 2002, 8, 118–122 CrossRef CAS.
- X.-Z. Fu, X.-X. Luo, J.-L. Luo, K. T. Chuang, A. R. Sanger and A. Krzywicki, Ethane dehydrogenation over nano-Cr2O3 anode catalyst in proton ceramic fuel cell reactors to co-produce ethylene and electricity, J. Power Sources, 2011, 196, 1036–1041 CrossRef CAS.
- N. Nasani, D. Ramasamy, S. Mikhalev, A. V. Kovalevsky and D. P. Fagg, Fabrication and electrochemical performance of a stable, anode supported thin BaCe0.4Zr0.4Y0.2O3–d electrolyte protonic ceramic fuel cell, J. Power Sources, 2015, 278, 582–589 CrossRef CAS.
- H. Borland, L. Llivina, S. Colominas and J. Abellà, Proton conducting ceramics for potentiometric hydrogen sensors for molten metals, Fusion Eng. Des., 2013, 88(9–10), 2431–2435 CrossRef CAS.
- J. Li, H. Yoon and E. D. Wachsman, Carbon dioxide reforming of methane in a SrCe0.7Zr0.2Eu0.1O3−δ proton conducting membrane reactor, Int. J. Hydrogen Energy, 2012, 37(24), 19125–19132 CrossRef CAS.
- H. Iwahara, Y. Asakura, K. Katahira and M. Tanaka, Prospect of hydrogen technology using proton-conducting ceramics, Solid State Ionics, 2004, 168, 299–310 CrossRef CAS.
- H. Iwahara, T. Esaka, H. Uchida and N. Maeda, Proton conduction in sintered oxides and its application to steam electrolysis for hydrogen production, Solid State Ionics, 1981, 3–4, 359–363 CrossRef CAS.
- K. S. Knight and N. Bonanos, The crystal structures of some doped and undoped alkaline earth cerate perovskites, Materials. Research. Bulletin, 1995, 30(3), 347–356 CrossRef CAS.
- N. Bonanos, K. S. Knight and B. Ellis, Perovskite solid electrolytes: structure, transport properties and fuel cell applications, Solid State Ionics, 1995, 79, 161–170 CrossRef CAS.
- J. Guan, S. E. Dorris, U. Balachandran and M. Liu, Transport properties of SrCe0.95Y0.05O3−δ and its application for hydrogen separation, Solid State Ionics, 1998, 110, 303–310 CrossRef CAS.
- X. Wei, J. Kniep and Y. S. Lin, Hydrogen permeation through terbium doped strontium cerate membranes enabled by presence of reducing gas in the downstream, J. Membr. Sci., 2009, 345, 201–206 CrossRef CAS.
- Y. Lin, S. Fang, D. Su, K. S. Brinkman and F. Chen, Enhancing grain boundary ionic conductivity in mixed ionic–electronic conductors, Nat. Commun., 2015 DOI:10.1038/ncomms7824.
- G. C. Mather, D. Poulidi, A. Thursfield, M. J. Pascual, J. R. Jurado and I. S. Metcalfe, Hydrogen-permeation
characteristics of a SrCeO3-based ceramic separation membrane: thermal, ageing and surface-modification effects, Solid State Ionics, 2010, 181, 230–235 CrossRef CAS.
- S.-Y. Jeon, D.-K. Lim, M.-B. Choi, E. D. Wachsman and S.-J. Song, Hydrogen separation by Pd–CaZr0.9Y0.1O3−δ cermet composite membranes, Sep. Purif. Technol., 2011, 79(3), 337–341 CrossRef CAS.
- U. (Balu) Balachandran, T. H. Lee, C. Y. Park, J. E. Emerson, J. J. Picciolo and S. E. Dorris, Dense cermet membranes for hydrogen separation, Sep. Purif. Technol., 2014, 121, 54–59 CrossRef.
- C. Zuo, T. H. Lee, S. E. Dorris, U. Balachandran and M. Liu, Composite Ni–Ba(Zr0.1Ce0.7Y0.2)O3 membrane for hydrogen separation, J. Power Sources, 2006, 159, 1291–1295 CrossRef CAS.
- X. Meng, J. Song, N. Yang, B. Meng, X. Tan, Z.-F. Ma and K. Li, Ni–BaCe0.95Tb0.05O3−δ cermet membranes for hydrogen permeation, J. Membr. Sci., 2012, 401–402, 300–305 CrossRef CAS.
- S. J. Song, J. H. Moon, T. H. Lee, S. E. Dorris and U. Balachandran, Thickness dependence of hydrogen permeability for Ni–BaCe0.8Y0.2O3−δ, Solid State Ionics, 2008, 179, 1854–1857 CrossRef CAS.
- A. Murashkina, E. Pikalova, D. Medvedev, A. Demin and P. Tsiakaras, Hydrogen production aided by new (1 − x)SrTi0.5Fe0.5O3−δ−xCe0.8(Sm0.8Sr0.2)0.2O2−δ (MIEC) composite membranes, Int. J. Hydrogen Energy, 2014, 39, 12472–12479 CrossRef CAS.
- R. M. German, P. Suri and S. J. Park, Review: liquid phase sintering, J. Mater. Sci., 2009, 44, 1–39 CrossRef CAS.
- T. Sekino, T. Nakajima, S. Ueda and K. Niihara, Reduction and sintering of a nickel-dispersed-alumina composite and its properties, J. Am. Ceram. Soc., 1997, 80, 1139–1148 CrossRef CAS.
- Z. Liu, J. Ouyang and Y. Zhou, Sintering and electrical conductivity of the GdSmZr2O7 ceramic with and without ZnO sintering aid, J. Power Sources, 2013, 243, 836–840 CrossRef CAS.
- P. Babilo and S. M Haile, Enhanced sintering of yttrium-doped barium zirconate by addition of ZnO, J. Am. Ceram. Soc., 2005, 88(9), 2362–2368 CrossRef CAS.
- C. Peng, J. Melnik, J.-L. Luo, A. R. Sanger and K. T. Chuang, BaZr0.8Y0.2O3−δ electrolyte with and without ZnO sintering aid: preparation and characterization, Solid State Ionic, 2010, 181(29–30), 1372–1377 CrossRef CAS.
- C. Zhang, H. Zhao, N. Xu, X. Li and N. Chen, Influence of ZnO addition on the properties of high temperature proton conductor Ba0.3Ce0.5Zr0.4Y0.1O3−δ synthesized via citrate–nitrate method, Int. J. Hydrogen Energy, 2009, 34, 2739–2746 CrossRef CAS.
- H. Wang, R. Peng, X. Wu, J. Hu and C. Xia, Sintering behavior and conductivity study of yttrium-doped BaCeO3–BaZrO3 solid solutions using ZnO additives, J. Am. Ceram. Soc., 2009, 92(11), 2623–2629 CrossRef CAS.
- S. J. Baik, J. H. Jang, C. H. Lee, W. Y. Cho and K. S. Lim, Highly textured and conductive undoped ZnO film using hydrogen post-treatment, Appl. Phys. Lett., 1997, 70, 3516–3518 CrossRef CAS.
- G. Chris Van de Walle, Defect analysis and engineering in ZnO, Phys. B, 2001, 308–310, 899–903 CrossRef.
- S. Cheng, M. Søgaard, L. Han, W. Zhang, M. Chen, A. Kaiser and P. V. Hendriksen, A novel CO2- and SO2-tolerant dual phase composite membrane for oxygen separation, Chem. Commun., 2015, 51, 7140–7143 RSC.
- K. Schmalez, M. Daniels, A. Buchheit, M. Grünebaum, L. Haase, S. Koops and H. D. Wiemhöfer, Influence of zinc oxide on the conductivity of ceria, J. Electrochem. Soc., 2013, 160(9), 1081–1087 CrossRef.
- S. Manjulat, K. Krishnan, B. K. Nagar, M. K. Saxen and D. Smruti, Heat capacity and thermal expansion coefficient of SrCeO3(s) and Sr2CeO4(s), Thermochim. Acta, 2011, 525, 167–176 CrossRef.
- J. Kniep and Y. S. Lin, Effect of zirconium doping on hydrogen permeation through strontium cerate membranes, Ind. Eng. Chem. Res., 2010, 49, 2768–2774 CrossRef CAS.
- S. Zhan, X. Zhu, B. Ji, W. Wang, X. Zhang, J. Wang, W. Yang and L. Lin, Preparation and hydrogen permeation of SrCe0.95Y0.05O3−δ symmetrical membranes, J. Membr. Sci., 2009, 340, 241–248 CrossRef CAS.
|
This journal is © The Royal Society of Chemistry 2016 |
Click here to see how this site uses Cookies. View our privacy policy here.