DOI:
10.1039/C5RA22886G
(Paper)
RSC Adv., 2016,
6, 94-104
Effective removal of Cr(VI) using β-cyclodextrin–chitosan modified biochars with adsorption/reduction bifuctional roles
Received
31st October 2015
, Accepted 11th December 2015
First published on 15th December 2015
Abstract
In this work, beta-cyclodextrin–chitosan modified walnut shell biochars (β-CCWB) were synthesized as a low-cost adsorbent for the removal of heavy metal Cr(VI) from aqueous solutions. Batch sorption experiments were carried out to investigate the adsorption characteristic of β-CCWB. The experimental data fitted a pseudo-second order equation and Freundlich isotherm model, and the optimum adsorption of the modified biochar was observed at pH 2.0 with an adsorption capacity of 206 mg g−1. Thermodynamic analysis showed that the adsorption process was spontaneous and endothermic. The removal efficiency of Cr(VI) by β-CCWB (about 93%) was higher than that by the pristine biochar (about 27%). Characteristic analysis indicated that amino and carboxyl groups were the major functional groups for Cr(VI) sorption, and implied that the electrostatic attraction of Cr(VI) to the positively charged biochar surface, reduction of Cr(VI) to Cr(III) ions and the complexation between Cr(III) ions and β-CCWB functional groups were responsible for Cr(VI) removal mechanism in this research. Furthermore, the environmentally friendly and low-cost β-CCWB could be applied as a potential effective adsorbent to remediate Cr(VI) contamination from aqueous solution.
1. Introduction
Due to the development of industry and economy, chromium (Cr) has been commonly used as well as released to the environment in a variety of industrial activities including electro plating, chromate manufacturing, leather tanning,1,2 electro-planting, metal polishing etc.3,4 In contrast to organic contaminants, Cr is non-biodegradable and persistent in ecosystems.5 Cr exists mainly as Cr(VI) and Cr(III), while the former is much more soluble and mobile in aqueous solutions than the latter, which has caused extensive attention due to its carcinogenic, mutagenic and teratogenic effects on biological systems.2 Therefore, it is imperative to remove Cr(VI) from wastewater prior to the discharge into water bodies.
All kinds of techniques have been applied to remove Cr(VI) from the aqueous solution, such as cyanide treatment, electro-chemical precipitation, reverse osmosis,6 adsorption,7 solvent extraction and ion exchange.1,8 Among these methods, adsorption is the most widely used because of its high efficiency and recovery of toxic and valuable metals from wastewater.9–11 Some adsorbents like activated carbon,12 zeolite,13 iron oxide, fullerene,14 graphene15 have been used for Cr(VI) removal. However, these materials mentioned above have the defects of limited adsorption ability, aggregation or high cost.
Biochar is the porous carbonaceous by-product generated from biomass through pyrolysis/carbonization under anoxic and anaerobic conditions.16 When applied to soils, biochar can not only increase soil fertility, raise agriculture productivity and enhance soil water holding capacity,17,18 but also serve as carbon storage to reduce CO2 emissions and mitigate climate change.19 Apart from soil application, recent studies have focused on biochar's potential ability on removing various contaminants (heavy metal, organic pollutants and microbial contaminants) from wastewater system, due to its accessible and abundant in feedstock materials.20,21 However, the biochar derived directly from biomass feedstock without any modification and activation usually has relatively low adsorption capacity, which is influenced by the feedstock type, production methods and processing conditions.22,23 Thus, recent researches have paid attention to modify the biochar production process or impregnate the materials with chemical agents so as to improve biochar sorption ability.24
Chitosan (beta 1,4-polyglucosamine), a renewable transformed polysaccharide and generally prepared commercially by deacetylation of chitin from crustacean shells with alkaline solution, which is one of the most abundant amino-polysaccharide exist in the environment. Chitosan and its derivatives which obtained through chemical and physical modifications of raw chitosan, including cross-linking, grafting and impregnation of the chitosan backbone25,26 have been used in treating contaminants due to its surface functionalities, biodegradability, nontoxicity and its useful tendency to dissolve in acid solution.11 Additional, this natural biopolymer and derivatives have received great attention in their application for metal ions adsorption due to the high ratio of amine groups (–NH2) and hydroxyl groups (–OH) and the insertion of active agents with functional groups into chitosan may make its adsorption capacity to a higher degree.27 Beta-cyclodextrin (β-CD) has a cylindrical structure, which ends with a hydrophilic exterior and a hydrophobic cavity, which can form inclusion complexes with a wide range of organic molecules possessing suitable shape and size in water spontaneously.28,29 Thus, the combination of chitosan, β-CD and biochar would be an innovative and effective adsorbent in the treatment of industrial wastewater and nature water.
In this study, β-cyclodextrin–chitosan (β-CC) was synthesized firstly, and then combined with walnut shell biochar produced through slow pyrolysis at different temperatures of 300, 450 and 600 °C, and this new-type materials was used to enhance the adsorption capacity for Cr(VI) removal in wastewater. The overarching targets of this study are to: (a) prepare β-cyclodextrin–chitosan walnut shell biochar materials and characterize them; (b) compare the adsorption capacity of modified biochar under different pyrolysis temperature; (c) examine the influence of pH, initial concentration, contact time and ionic strength conditions on the sorption of Cr(VI) on this materials; (d) establish and elucidate the underlying interaction mechanisms through a series of laboratory experiments and mathematical model.
2. Materials and methods
2.1 Materials
Walnut shell biomass was obtained from Changsha, Hunan Province of China. The biomass feedstock were dried and milled to fraction. β-CD with purity above 98% and chitosan with purity above 99% without any further purification were purchased from Beijing Solarbio Science & Technology Co. Ltd. All other chemicals employed in this experiments including HCl, NaOH, NaCl, K2Cr2O7, H2SO4, H3PO4, acetone, glutaraldehyde, 1-ethyl-3-(3-dimethyl)aminopropyl carbodiimide (EDC), N-hydroxyl succinimide (NHS) were of analytical reagent grade.
2.2 Preparation of adsorbent
Walnut shell biomass was rinsed with ultrapure water and oven-dried at 60 °C. Then, the dried biomass were pyrolyzed in a lab-scale tubular reactor (SK-G08123K, China) at 300 °C, 450 °C, 600 °C, respectively, in N2 environment for 2 h before cooling. The biochar samples produced from different pyrolysis temperature were referred to as WB300, WB450, WB600, respectively. The samples were then washed, dried (80 °C), and sieved through 150 mesh screen. β-CC was prepared according to the method of Fan et al.30,31 And the β-CC was held by hydrogen binding, with very large surface area and showed great improvement in the uptake properties of contaminants compared to the unmodified chitosan due to its high concentration of active sites. Firstly, WB300, WB450, WB600 biochar dispersion was prepared by sonicating 2 g biochar sample for 2 h in ultrapure water, respectively. Subsequently, the mixed solution (50 mL 0.1 mol L−1 EDC and 0.1 mol L−1 NHS) was added into the biochar dispersion with continuous stirring for 2.5 h in order to activate the functional groups of walnut shell biochar. The pH of the resulting solution was adjusted at 7.0 using dilute sodium hydroxide. After that, β-CC (4 g), the activated biochar solution and 10 mL glutaraldehyde were added into a flask and dispersed in ultrapure water by ultrasonic dispersion for 10 min. After ultrasonic dispersion, the mixed solutions were stirred at 60 °C for 2 h. The precipitate was washed with 2% (w/v) NaOH and ultrapure water in turn until pH was about 7.0. Then products were collected through filtration, oven-dried under vacuum overnight at 50 °C and sealed in a desiccator for further experiment tests. The obtained novel composites are referred to as β-CCWB300, β-CCWB450 and β-CCWB600.
2.3 Characterization of biochar
The BET and pore volume analysis was carried out with the Brunauer, Emmett, and Teller (BET) (Instruments Quadrasorb SI, USA). Scanning electron microscope (SEM) images were obtained on a field emission scanning electron microscopy (JSM-7001F, Japan). Fourier transform infrared (FTIR) spectrum was measured on a spectrophotometer (Nicolet Magna-IR 750 spectrometer, USA) using the KBr pellet technique. The X-ray photoelectron spectroscopy (XPS) measurements were performed using an ESCALAB 250Xi X-ray photoelectron spectrometer (Thermo Fisher, USA).
2.4 Batch adsorption of Cr(VI)
The adsorption of Cr(VI) was studied as a function of pH, initial concentration, contact time, adsorption temperature, and ionic strength. Potassium dichromate (K2Cr2O7) was used for preparing the stock solutions of heavy metals. The concentrations of residual Cr(VI) were analyzed by measuring the absorbance of the purple complex of Cr(VI) with 1,5-diphenylcarbohydrazide method with a UV-vis spectrophotometer (Pgeneral T6, Beijing, China) at the wavelength of 540 nm.
In order to investigate the effect of initial solution pH in this adsorption, the initial pH values of 50 mL Cr(VI) solution (100 mg L−1) were adjusted from 2.0 to 10.0 using dilute NaOH or HCl solutions. Kinetic tests were carried out by contacting 0.1 g adsorbent with 50 mL Cr(VI) solution (100 mg L−1) at 25 °C and optimum pH value of 2.0 in thermostatic water bath oscillators. The residual Cr(VI) concentration was measured after designated time period (5, 10, 30, 60, 120, 240, 360, 480, 720, 960, 1200, 1440, 1800, 2280 and 2800 min). For the adsorption isotherm study, 0.1 g of adsorbent was contacted with 50 mL of Cr(VI) solution at concentrations of 20, 50, 100, 200, 300, 400, 500, 600 and 800 mg L−1 at 25 °C with continuous shaking. For the effect of background ionic strength, the experiments were studied at pH 2.0, 25 °C and initial Cr(VI) solution (100 mg L−1) was adjusted by different concentrations of NaCl (0, 0.001, 0.005, 0.01, 0.05, 0.1, 0.5, 1.0 mol L−1). The removal percentage (p, %) and the equilibrium adsorption capacity (qe, mg g−1) of β-CCWB450 was calculated by using the following equations:
|
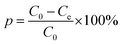 | (1) |
|
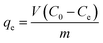 | (2) |
where
C0 (mg L
−1) and
Ce (mg L
−1) are the initial and equilibrium concentrations of Cr(
VI) ions,
m (g) is the mass of the adsorbent β-CCWB450 and
V (L) is the volume of metal solution.
All the experimental treatments were performed in duplicate and the average values were reported. The relative errors of the data were generally within 5%.
3. Results and discussion
3.1 Characteristic of β-CCWB
3.1.1 BET and pore volume. The surface area, pore volume and pore size of WB450 and β-CCWB450 were presented in Table 1. The BET surface area of β-CCWB450 (82.09 m2 g−1) was larger than that of pristine biochar (11.76 m2 g−1), and the β-CCWB450 was possessed of larger pore volume and smaller pore size than that of WB450. This phenomenon may be due to the process of introducing β-CC.
Table 1 BET characteristics of β-CCWB450 and WB450
|
Specific surface area (m2 g−1) |
Pore volume (m3 g−1) |
Average pore (nm) |
WB450 |
11.76 |
0.02589 |
8.805 |
β-CCWB450 |
82.09 |
0.08271 |
4.030 |
3.1.2 SEM. The surface morphological characteristics of the materials before and after heavy metal adsorption were compared by the scanning electron microscopy graphs. The SEM images of the carbon materials are presented in Fig. 1. As seen in Fig. 1a, a lot of carbon particles were observed from the surface of the pristine biochar (WB450), which indicated that the walnut shell were pyrolyzed and carbonized. As shown in Fig. 1b, the β-CC spheres were decorated and anchored on the surface of WB450, which provided effective adsorption sites and generated higher BET surface areas and larger pore volume. Fig. 1c showed that the pore amount decreased and some splendent crystals appeared on the surface of β-CCWB450 after the adsorption of Cr(VI). This may be that chromium ions were adsorbed on it and blocked the pore channel.
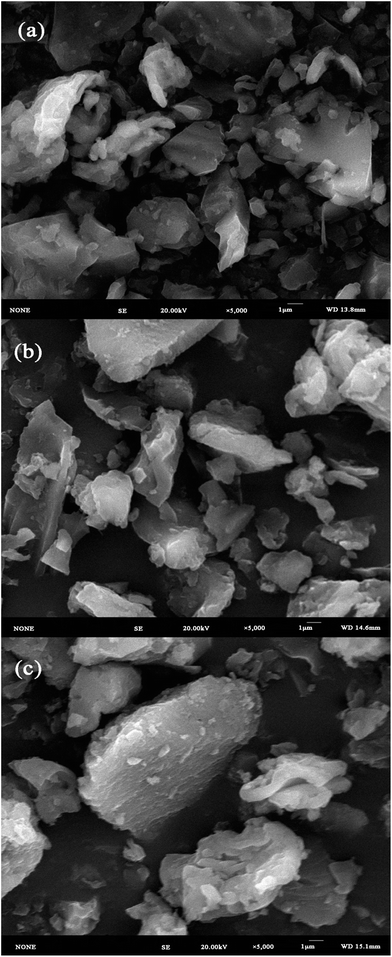 |
| Fig. 1 SEM images of (a) pristine biochar, (b) modified biochar before adsorption and (c) after adsorption. | |
3.1.4 XPS. The XPS was performed on β-CCWB450 and β-CCWB450 loaded with Cr to study the surface chemical compositions and investigate the species of the Cr bound on the β-CCWB450 to gain further information on its removal mechanism.The principal elements on the surface of the β-CCWB450 before adsorption were C 1s (77.06%), O 1s (20.69%), N 1s (2.24%), chrome (not been detected because of the extremely low content) and the modified biochar after adsorption were C 1s (66.32%), O 1s (28.46%), N 1s (1.68%) and Cr2p (3.53%) (see Fig. 3a). The N/C ratio was estimated to be 0.29 and 0.25 for β-CCWB450 before and after adsorption, respectively. The obvious increase in chrome content and the decrease in N/C ratio indicated that β-CC was introduced into biochar and amino groups may participate in removing chromium ions.
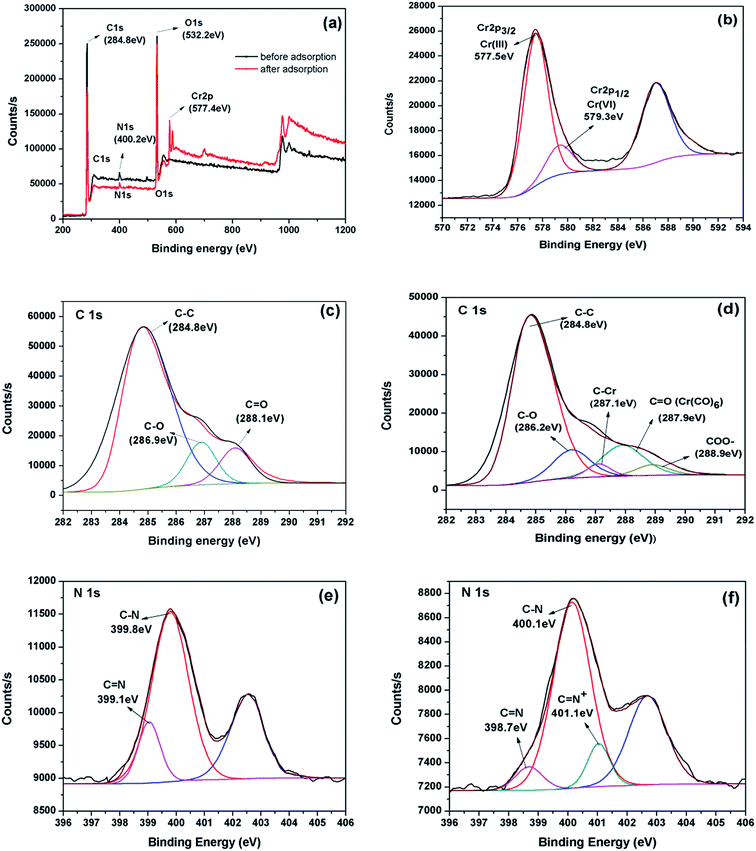 |
| Fig. 3 XPS spectra of (a) β-CCWB450 before and after adsorption, (b) Cr2p of β-CCWB450 after adsorption, (c) the C 1s XPS spectra of β-CCWB450 before and (d) after adsorption, (e) the N 1s XPS spectra of β-CCWB450 before and (f) after adsorption. | |
Detailed XPS survey of the regions for trivalent chromium and hexavalent chromium was shown in Fig. 3b. The area of Cr(III) peak at the binding energy of 577.5 eV is distinctly greater than the area of Cr(VI) peak at the binding energy of 579.3 eV. This data demonstrated that part of adsorbed Cr(VI) anions was reduced to Cr(III) after exposure to β-CCWB450.
As shown in Fig. 3c, the C 1s XPS spectrum of β-CCWB450 can be curve-fitted into three peak components at approximately 284.8 eV (C–C), 286.9 eV (C–O) and 288.1 eV (C
O).34,35 As seen from Fig. 3d, the C 1s XPS spectrum of β-CCWB450 loaded with Cr clearly indicates that five components corresponding to C–C (284.8 eV), C–O (286.2 eV), C–Cr (287.1 eV), C
O[Cr(CO)6] (287.9 eV) and COO− (288.9 eV).36,37 On the basis of the XPS results, the main difference between β-CCWB450 and β-CCWB450 loaded with Cr was the new peak of C–Cr and COO− bond. That may be attributed to the fact that carboxyl groups were successfully introduced to the modified biochar and this functional groups can enhance the ability of modified materials to remove chromium ions by chelation reaction.
The peak around 399 eV was attributed to N 1s (Fig. 3e and f). Following the modification of β-CC, the pristine biochar was functionalized with –NH2 groups, which was in agreement with FTIR results. In addition, the minor shift in bond energy of quinoid amine (C
N), benzoid amine (C–N) and new peak occurred at 401.1 eV in doped imine (C
N+) also revealed that amino groups were involved in the fixation of Cr(VI) and chelation of Cr(III) during the adsorption process.
3.2 Comparison of removal efficiency by modified biochar and pristine biochar
The comparison of removal efficiency by β-CCWB300, β-CCWB450, β-CCWB600 and WB450 was carried out at the varying Cr(VI) concentrations from 20 to 800 mg L−1 at initial pH of 2.0 and temperature of 25 °C.
As shown in Fig. 4a, the Cr(VI) adsorption capacity of the modified biochar from three different pristine biochar were almost equal at diverse Cr(VI) concentration solutions at 298.15 K, which indicating that the pyrolysis temperature has no significant effect on adsorption of Cr(VI) by β-CCWB. However, from Fig. 4b, the Cr(VI) adsorption capacity of the β-CCWB450 ranged from 9.9 mg g−1 to 136.25 mg g−1 at 298.15 K and the optimum adsorption was 206 mg g−1 at 318.15 K, which was much higher than of the pristine biochar (WB450).
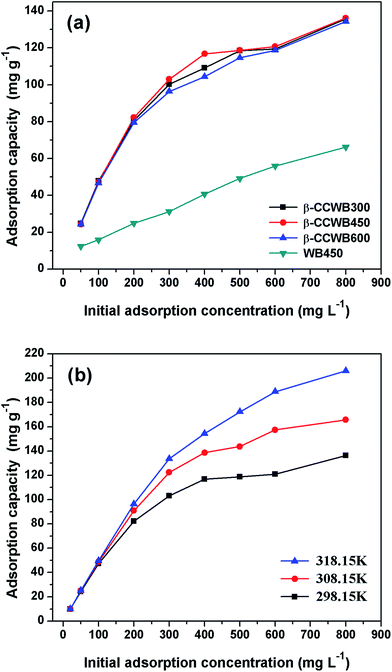 |
| Fig. 4 (a) The comparison of adsorption capacity on β-CCWB and WB450 under 298.15 K, (b) the comparison of adsorption capacity on β-CCWB450 under different adsorption temperatures (Cr(VI) solution volume: 50 mL; adsorbent dose: 0.1 g; contact time: 24 h; pH: 2.0). | |
In a word, the removal efficiency of the modified biochar was 1.1 to 3.1 times higher than that of the pristine biochar and this novel modified materials β-CCWB exhibited much higher adsorption capacity and removal efficiency than pristine biochar.
3.3 The effect of zero point charge and optimization of pH
Zero point charge (pHpzc), the potential in the sliding plane of colloidal particles, which is related to the surface charge of particles.38 The zeta potentials of the β-CCWB450 are shown in Fig. 5. It was obvious that pHpzc of the β-CCWB450 was found to be at pH 3.6. Under the solution pH < pHpzc, the surface of the β-CCWB450 was positively charged, resulted in the main adsorption mechanism of significant electrostatic attraction between the positively charged surface and the Cr(VI) anions. When the solution pH > pHpzc, β-CCWB450 surface was negatively charged, which was due to the deprotonation of functional groups of β-CCWB450 that could inhibit the Cr(VI) adsorption due to electrostatic repulsion between the negative charge of β-CCWB450 and Cr(VI) anions, suggesting that other sorption mechanism served as the main force to adsorb Cr(VI) such as surface complexation.
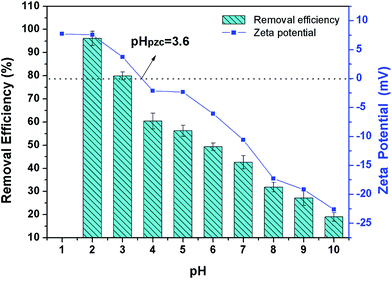 |
| Fig. 5 Effect of initial solution pH values on Cr(VI) removal by β-CCWB450 and zeta potential of β-CCWB450 at different solution pH. | |
pH is one of the most crucial factors significantly affecting the adsorption efficiency. The surface charge and the speciation of chromium depended on the solution pH. Cr(VI) exists primarily as HCrO4− and Cr2O72− (pH = 1.0–6.8) and stable CrO42− (pH > 6.8).39 Cr(III) was predominantly presented as Cr3+ under acidic condition. During the adsorption, at low pH, more HCrO4− and Cr2O72− formed and the stronger interaction between the positively charged functional groups of adsorbent and the negatively charged chromate ions caused higher adsorption.2 Meanwhile, in this process, Cr(VI) was partially reduced to Cr(III) by reductive surface functional groups like amino groups and hydroxyl groups40 on the β-CCWB. Some Cr(III) released back into the solution in the form of water-soluble Cr(III) species, others precipitated on the surface of the β-CCWB in the form of Cr2O3.
From Fig. 5, the decrease in Cr(VI) removal with the increase of pH could be attributed to the competition between higher concentration of OH− with Cr(VI) species for the sorption sites on the β-CCWB. From the above, the optimum solution pH was 2 for Cr(VI) removal.
3.4 Adsorption experiments
3.4.1 Adsorption kinetics. The kinetics of Cr(VI) removal was carried out to understand the adsorption behavior of β-CCWB450. The Cr(VI) adsorption data onto β-CCWB450 was shown in Fig. 6a and the contact time was varied between 5 min to 2880 min to establish equilibrium. The rate of Cr(VI) adsorption was fast, with 80% of the ultimate adsorption occurred in the first 5 min, and the adsorption capacity continued to raise slightly for the next 12 h, followed by a very slow approach to equilibrium.
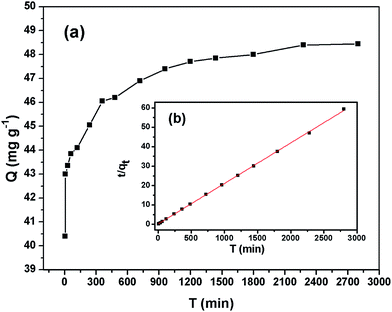 |
| Fig. 6 Kinetics of Cr(VI) adsorption onto the β-CCWB450 at 298.15 K. (a) Cr(VI) sorption kinetics data, (b) pseudo-second-order model for Cr(VI) adsorption (initial Cr(VI) concentration 100 mg L−1; pH = 2.0). | |
To investigate the mechanism of adsorption, three different kinetic models (pseudo-first-order, pseudo-second-order, and Elovich) were applied and illustrated as follows:
The pseudo-first-order model:
|
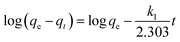 | (3) |
The pseudo-second-order model:
|
 | (4) |
The Elovich model:
|
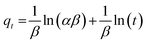 | (5) |
where
qe (mg g
−1) and
qt (mg g
−1) are the amount of metal ion adsorbed per unit mass of the adsorbent at equilibrium and time
t (min) respectively.
k1 (min
−1) and
k2 (g mg
−1 min
−1) are the pseudo-first-order and pseudo-second-order rate constant respectively.
α (mg g
−1 min
−1) and
β (g mg
−1) are the Elovich constants.
The results of the above three kinetics were presented in Table 2. The correlation coefficient values were much higher for the pseudo-second-order (R2 = 0.99) (Fig. 6b) than the pseudo-first-order (R2 = 0.65) and Elovich (R2 = 0.96) kinetics model, which suggested that experimental data fitted well with the pseudo-second-order model. So that, the chemisorption of Cr(VI) was the rate-determining step of adsorption process, which involved the chemical interaction between chromium ions and polar functional groups on the adsorbent, such as ion exchange and chelating reaction.
Table 2 Pseudo-first-order, pseudo-second-order and Elovich equation model parameters for Cr(VI) adsorption on β-CCWB450
|
Parameter 1 |
Parameter 2 |
R2 |
Pseudo-first-order |
qe = 46.60 mg g−1 |
k1 = 0.83 min−1 |
0.65 |
Pseudo-second-order |
qe = 48.50 mg g−1 |
k2 = 0.00015 g mg−1 min−1 |
0.999 |
Elovich |
α = 4.06 × 1015 mg g−1 min−1 |
β = 0.0854 g mg−1 |
0.959 |
3.4.2 Adsorption isotherm. In order to study the adsorption equilibrium of Cr(VI), Langmuir isotherm model and Freundlich isotherm model were applied to simulate the equilibrium characteristics of the adsorption.The Langmuir model assumes that the uptake of metal ions occurs on a homogeneous surface by monolayer sorption without interaction between sorbed ions. While the Freundlich isotherm model assumes that the adsorption occurs on a heterogenous surface by multilayer sorption and that the adsorption amount of adsorbate increases infinitely with increasing concentration, which suggests that binding sites are not equivalent or independent.
The Langmuir model:
|
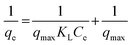 | (6) |
The Freundlich model:
where
qe (mg g
−1) and
qmax (mg g
−1) are the amount of Cr(
VI) adsorbed at equilibrium time and the maximum quantity of metal ions per unit biochar to form a complete monolayer on the surface, respectively.
Ce (mg L
−1) is the equilibrium solute concentration.
KL (L mg
−1) is Langmuir affinity, which represents enthalpy of sorption and related to temperature.
KF and
n are the Freundlich constants related to the sorption capacity and sorption intensity, respectively.
The correlation coefficient (R2) calculated from Langmuir and Freundlich isotherm models are listed in Table 3 and the sorption isotherms were shown in Fig. 7. It could be obviously observed that the relative parameters R2 (0.96, 0.98, 0.99) of Freundlich was higher than that (0.95, 0.95, 0.92) of Langmuir at all temperatures (298.15 K, 308.15 K, 318.15 K). These results indicated that the Cr(VI) ions sorption to the binding sites was heterogeneity sorption, which may be attributed to the active functional groups such as amino groups and carboxyl groups on the β-CCWB450 surface. In addition, the Freundlich model constant n at three temperature were 4.20, 4.19 and 4.29, respectively, which reflected that the adsorption between chromium ions and adsorbent was favorable (1 < n < 10). The larger value of empirical parameter n also denotes stronger interaction between adsorbent and heavy metal. Futhermore, as seen in Table 4, the comparison of the maximum Cr(VI) adsorption capacity of various adsorbents in previous study was presented. And the prepared β-CCWB450 maintained much better Cr(VI) removal performance than many other adsorbents that reported in the literature.2,39,41,42
Table 3 Constants and correlation coefficients of Freundlich and Langmuir models for Cr(VI) adsorption onto β-CCWB450
T (K) |
Langmuir model |
Freundlich model |
qm (mg g−1) |
KL (L mg−1) |
R2 |
KF (L mg−1) |
n |
R2 |
298.15 |
124.42 |
0.091 |
0.95 |
31.84 |
4.20 |
0.96 |
308.15 |
149.33 |
0.090 |
0.95 |
38.83 |
4.19 |
0.98 |
318.15 |
188.56 |
0.101 |
0.92 |
52.98 |
4.29 |
0.99 |
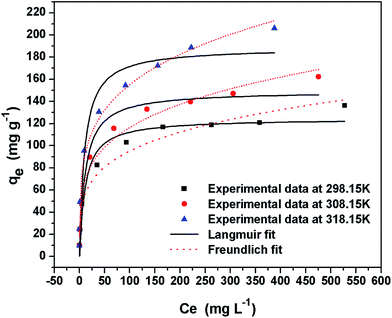 |
| Fig. 7 Freundlich and Langmuir isotherms of Cr(VI) adsorption on β-CCWB450 (Cr(VI) solution volume: 50 mL; adsorbent dose: 0.1 g; contact time: 24 h; pH: 2.0). | |
Table 4 Comparison of the maximum Cr(VI) adsorption capacity of various adsorbents
Adsorbents |
Adsorption capacity (mg g−1) |
References |
Activated charcoal |
12.87 |
40 |
Activated carbon |
36.34 |
41 |
Zinc–biochar nanocomposites |
102.66 |
38 |
Sugar beet tailing biochar |
123 |
2 |
β-CCWB450 |
206 |
This study |
3.4.3 Adsorption thermodynamic studies. The effect of temperature on the adsorption process was investigated at three different temperatures (298.15 K, 308.15 K and 318.15 K). The thermodynamic parameters such as changes in enthalpy (ΔH0), entropy (ΔS0) and Gibbs free energy (ΔG0) of sorption are essential in defining whether sorption is endothermic or exothermic. Three thermodynamic parameters are estimated by following relationship: |
ΔG0 = −RT ln K
| (8) |
|
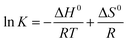 | (9) |
where K is the adsorption equilibrium constant. T (K) is the absolute temperature, and R (8.314 J mol−1 K−1) is the gas constant. ΔH0 (kJ mol−1) and ΔS0 (kJ mol−1 K−1) are the enthalpy change and entropy change, respectively. The values of ΔH0 and ΔS0 can be obtained from the slope and intercept of a plot of ln
K against T−1 (R2 > 0.98) from the Fig. 8. The results of the thermodynamic parameters were shown in Table 5.
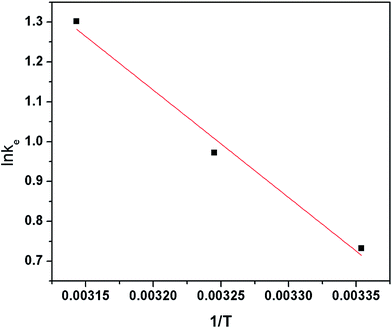 |
| Fig. 8 Plot of ln k0 versus T−1 for estimation of thermodynamic parameters for the adsorption of Cr(VI) on β-CCWB450 (Cr(VI) solution volume: 50 mL; adsorbent dose: 0.1 g; initial Cr(VI) concentration: 20, 50, 100, 200, 300, 400, 500, 600, 800 mg L−1; contact time: 24 h; pH: 2.0). | |
Table 5 Thermodynamic parameters for Cr(VI) adsorption on β-CCWB450
|
298.15 K |
308.15 K |
318.15 K |
ΔH0 (kJ mol−1) |
ΔS0 (kJ mol−1 K−1) |
R2 |
ln k0 |
0.732 |
0.972 |
1.301 |
21.91 |
81.02 |
0.98 |
ΔG0 (kJ mol−1) |
−5.155 |
−6.774 |
−9.716 |
The negative values of ΔG0 at all different temperatures indicated that the process of the adsorption was spontaneous in nature. What's more, the apparent decrease in negative values of ΔG0 with increasing temperature implied that the adsorption became more favorable at higher temperature. The standard enthalpy and entropy changes of adsorption were determined to be 21.91 kJ mol−1 and 81.02 J K−1 mol−1, respectively. The positive value of ΔH0 proved that the adsorption was an endothermic process. The value of ΔS0 was also positive, which suggested that the increase of randomness at the solution interface during the sorption of Cr(VI) metal ions. All the parameters may also implied that the increased temperatures provided heavy metals ions sufficient energy to overcome the diffuse layer and to be adsorbed onto biochar's interface structure.
3.5 The effect of ionic strength
The presence of salinity had been testified to reduce the sorption of Cr(VI) onto modified biochar.39 In this study, the background ionic strength of the solutions was adjusted by NaCl. As shown in Fig. 9, the amount of Cr(VI) ions absorbed was decreased slightly with the increase of the ionic strength from 0.001 to 0.005 M. However, the removal efficiency declined to 70.5% at the higher Na+ concentration of 1.0 mol L−1. The observed inverse relationship between the adsorption amount of Cr(VI) and ionic concentration suggested that salinity might have competed with Cr(VI) for sorption sites. On the other hand, the relative adsorption at higher ionic strength was not tremendously affected may also indicates that specific interactions and the formation of Cr complexation were existed besides electrostatic adsorption.
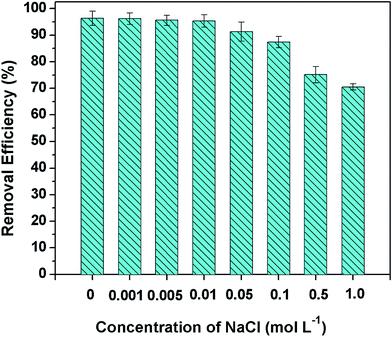 |
| Fig. 9 Effect of different concentrations of NaCl on Cr(VI) removal by β-CCWB450 (Cr(VI) solution volume: 50 mL; adsorbent dose: 0.1 g; initial Cr(VI) concentration: 100 mg L−1; contact time: 24 h; pH: 2.0). | |
3.6 Desorption and regeneration analysis
Desorption is a vital process in adsorption study in order to access the economic value of the β-CCWB composites. Desorption study will help to regenerate the spent adsorbent so that it can be reused to adsorb Cr ions. In this experiment, desorption efficiency of the spent β-CCWB450 was surveyed by using 0.5 mol L−1 sodium hydroxide. The adsorption–desorption cycle was repeated 5 times with same adsorbent. It was clear from Fig. 10 that the removal efficiency decreased gradually with the increasing regeneration cycles, but above 54.6% in fifth cycle, which may be a result of the decrease of specific surface area and the weakness of functional groups on β-CCWB. In brief, the β-CCWB after Cr adsorption could be regenerated with 0.5 mol L−1 sodium hydroxide.
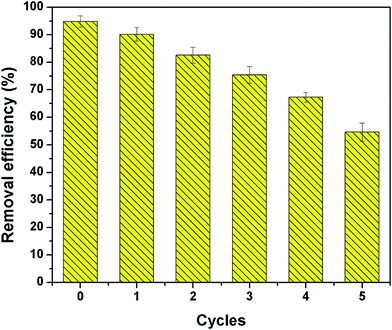 |
| Fig. 10 Fifth consecutive adsorption–desorption cycles of β-CCWB450 for Cr(VI) removal (Cr(VI) solution volume: 50 mL; adsorbent dose: 0.1 g; initial Cr(VI) concentration: 100 mg L−1; contact time: 24 h; pH: 2.0). | |
3.7 Reduction of Cr(VI) to Cr(III) by β-CCWB
The concentration of Cr(VI), Cr(III) and total Cr in the solution after adsorption were measured (Fig. 11a). Cr(III), which did not exist initially, increased dramatically at the beginning of adsorption, with final Cr(III) concentration of 13.8 mg L−1 and Cr(VI) concentration of 3.2 mg L−1. These results indicated that large amount of Cr(VI) was reduced to Cr(III) when contacted with β-CCWB, and part of the converted Cr(III) was retained by β-CCWB (Fig. 3b) and the other part was released into solution.
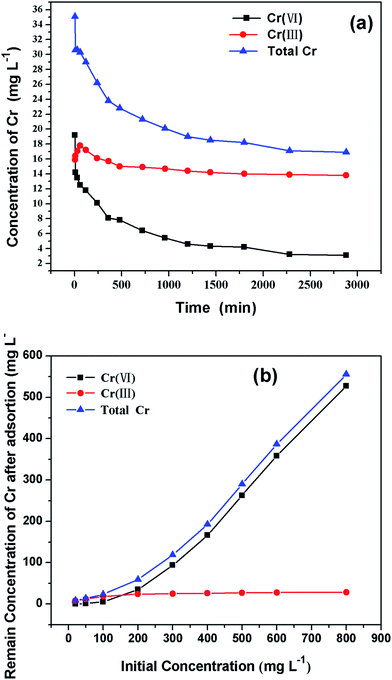 |
| Fig. 11 (a) Time variation of Cr(III), Cr(VI) and total Cr concentration (initial Cr(VI) concentration: 100 mg L−1; Cr(VI) solution volume: 50 mL; adsorbent dose: 0.1 g; pH: 2.0), (b) initial concentration variation of Cr(III), Cr(VI) and total Cr concentration after adsorption (Cr(VI) solution volume: 50 mL; contact time: 24 h; adsorbent dose: 0.1 g; pH: 2.0). | |
As shown in the Fig. 11b, the removal of Cr(VI) increased with the increase of initial concentration. Interestingly, the concentration of Cr(III) after adsorption, however, remained 28.2 mg L−1, which did not raise followed the increase of initial Cr(VI) concentration. The amount of proton that disappeared in the solution was proportional to the amount of removed Cr(VI). And this results were consistent with the research of Park et al.43 that Cr(VI) could be easily reduced to Cr(III) by positively charged functional groups. Dong et al.2 reported that Cr(VI) was largely reduced to Cr(III) by contact with the biochar from sugar beet tailing. The reduction of Cr(VI) by organic substances is accompanied by proton consumption (eqn (10) and (11)). And this study obtained the same conclusion as the reported studies, that most of the Cr bound on the β-CCWB was in the Cr(III) state (Fig. 3b).
|
HCrO4− + 7H+ + 3e− (from organic substances) → Cr3+ + 4H2O
| (10) |
|
Cr2O72− + 14H+ + 6e− (from organic substances) → 2Cr3+ + 7H2O
| (11) |
3.8 Removal mechanism
From the FTIR spectral data, it was observed that the predominant functional groups on the β-CCWB were the amino groups and carboxyl groups. After metal ion adsorption, it was found that there was a significant shift in this two functional groups peak. This revealed the possible mechanism of the coordination of metal ions onto amino and carboxyl groups of β-CCWB. Furthermore, the XPS analysis of modified biochar (before and after adsorption) showed that chrome was successfully adsorbed to the surface of modified biochar mainly in the form of trivalent chromium. Theoretically, the –NH2 and –COOH groups on β-CCWB could be easily protonated and form positively charged –NH3+ and –COOH+ groups. By the electrostatic interaction, the protonated groups on the β-CCWB sufficiently attracted the negatively charged Cr2O72− ions, resulting in the enrichment of Cr2O72− ions onto the surface of the β-CCWB.
We hypothesized that β-CCWB effectively removed Cr(VI) via electrostatic attraction of Cr(VI) coupled with Cr(VI) reduction to Cr(III) and Cr(III) complexation.2,3,43,44 And it can be speculated that three steps were involved in the adsorption process (Fig. 12). Firstly, under strongly acidic conditions, the amino and carboxyl groups on β-CCWB surface could be easily protonated to form –NH3+ and –COOH+ groups, the negatively charged Cr2O72− and HCrO4− species were migrated to the positively charged surface of β-CCWB (protonated amino and carboxyl groups) by electrostatic interaction. Secondly, with the participation of π electrons donors from biochar, Cr(VI) was reduced to Cr(III) (Fig. 3b), and Cr(VI) is also reduced to Cr(III) by glutaraldehyde molecules (cross linker).44 Finally, part of the converted Cr(III) was bound into β-CCWB surface to form stable complexed Cr(III) with functional groups, with the rest being released to the medium. Generally speaking, during the process, this new material not only acted as an adsorbent to sorb chromium but also assisted the reduction of hexavalent chromium via a redox reaction.
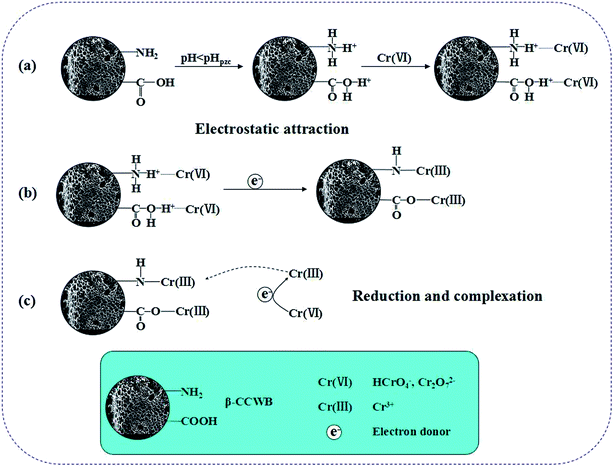 |
| Fig. 12 Proposed removal mechanism of Cr(VI) by β-CCWB. | |
4. Conclusion
In this study, the walnut shell biochar modified by β-CC with high active surface area was successfully synthesized, the advantages of using this synthetic material as an alternative adsorbent to remove Cr(VI) from aqueous mainly based on its high removal efficiency, low cost and simple synthesis method. Characterization of β-CCWB indicated that the physiochemical properties (e.g., surface area, porosity and thermal stability) of the biochars were significantly enhanced by the additions of β-CC. It is noteworthy that β-CCWB have an excellent adsorption and reduction capacity of Cr(VI), and the maximum adsorption capacity obtained from the optimum conditions was 206 mg g−1. The Cr(VI) removal mechanisms involved with electrostatic attraction coupled with Cr(VI) reduction and complexation. In a word, results obtained from this study demonstrated that these novel β-CCWB adsorbents exhibit a new opportunities for their applications in the removal of Cr(VI) ions from aqueous solution for its efficiency and both β-CC and biochar are low-cost and environmental friendly materials.
Acknowledgements
This study was financially supported by the National Natural Science Foundation of China (Grant No. 41271332 and 51521006 and 51478470) and the Hunan Provincial Innovation Foundation for Postgraduate (Grant No. CX2015B090 and CX2015B095).
References
- X. J. Tong, J. Y. Li, J. H. Yuan and R. K. Xu, Chem. Eng. J., 2011, 172, 828–834 CrossRef CAS.
- X. Dong, L. Q. Ma and Y. Li, J. Hazard. Mater., 2011, 190, 909–915 CrossRef CAS PubMed.
- L. Li, L. Fan, M. Sun, H. Qiu, X. Li, H. Duan and C. Luo, Colloids Surf., B, 2013, 107, 76–83 CrossRef CAS PubMed.
- Y. Zhou, B. Gao, A. R. Zimmerman, J. Fang, Y. Sun and X. Cao, Chem. Eng. J., 2013, 231, 512–518 CrossRef CAS.
- E. Agrafioti, D. Kalderis and E. Diamadopoulos, J. Environ. Manage., 2014, 133, 309–314 CrossRef CAS PubMed.
- Z. B. Zhang, X. H. Cao, P. Liang and Y. H. Liu, J. Radioanal. Nucl. Chem., 2012, 295, 1201–1208 CrossRef.
- D. Mohan, C. U. Pittman and P. H. Steele, Energy Fuels, 2006, 20, 848–889 CrossRef CAS.
- B. Chen, Z. Chen and S. Lv, Bioresour. Technol., 2011, 102, 716–723 CrossRef CAS.
- R. K. Xu, S. C. Xiao, J. H. Yuan and A. Z. Zhao, Bioresour. Technol., 2011, 102, 10293–10298 CrossRef CAS PubMed.
- P. Regmi, J. L. Garcia Moscoso, S. Kumar, X. Cao, J. Mao and G. Schafran, J. Environ. Manage., 2012, 109, 61–69 CrossRef CAS.
- M. K. Kim, K. Shanmuga Sundaram, G. Anantha Iyengar and K. P. Lee, Chem. Eng. J., 2015, 267, 51–64 CrossRef CAS.
- X. Sun and U. Ghosh, Environ. Toxicol. Chem., 2008, 27, 2287–2295 CAS.
- E. Kantarelis, W. Yang and W. Blasiak, Fuel, 2014, 122, 119–125 CrossRef CAS.
- X. Cao, L. Ma, B. Gao and W. Harris, Environ. Sci. Technol., 2009, 43, 3285–3291 CrossRef CAS PubMed.
- J. Zhu, S. Wei, H. Gu, S. B. Rapole, Q. Wang, Z. Luo, N. Haldolaarachchige, D. P. Young and Z. Guo, Environ. Sci. Technol., 2012, 46, 977–985 CrossRef CAS PubMed.
- M. Ahmad, A. U. Rajapaksha, J. E. Lim, M. Zhang, N. Bolan, D. Mohan, M. Vithanage, S. S. Lee and Y. S. Ok, Chemosphere, 2014, 99, 19–33 CrossRef CAS.
- M. Zhang, B. Gao, S. Varnoosfaderani, A. Hebard, Y. Yao and M. Inyang, Bioresour. Technol., 2013, 130, 457–462 CrossRef CAS.
- A. Janus, A. Pelfrene, S. Heymans, C. Deboffe, F. Douay and C. Waterlot, J. Environ. Manage., 2015, 162, 275–289 CrossRef CAS.
- M. Zhang, B. Gao, Y. Yao, Y. Xue and M. Inyang, Chem. Eng. J., 2012, 210, 26–32 CrossRef CAS.
- M. Inyang and E. Dickenson, Chemosphere, 2015, 134, 232–240 CrossRef CAS PubMed.
- X. F. Tan, Y. G. Liu, G. M. Zeng, X. Wang, X. J. Hu, Y. L. Gu and Z. Z. Yang, Chemosphere, 2015, 125, 70–85 CrossRef CAS PubMed.
- M. Zhang, B. Gao, Y. Yao, Y. Xue and M. Inyang, Sci. Total Environ., 2012, 435–436, 567–572 CrossRef CAS.
- Z. Song, F. Lian, Z. Yu, L. Zhu, B. Xing and W. Qiu, Chem. Eng. J., 2014, 242, 36–42 CrossRef CAS.
- E. Agrafioti, D. Kalderis and E. Diamadopoulos, J. Environ. Manage., 2014, 146, 444–450 CrossRef CAS.
- P. O. Boamah, Y. Huang, M. Hua, Q. Zhang, J. Wu, J. Onumah, L. K. Sam-Amoah and P. O. Boamah, Ecotoxicol. Environ. Saf., 2015, 116, 113–120 CrossRef CAS.
- M. Vakili, M. Rafatullah, B. Salamatinia, A. Z. Abdullah, M. H. Ibrahim, K. B. Tan, Z. Gholami and P. Amouzgar, Carbohydr. Polym., 2014, 113, 115–130 CrossRef CAS.
- B. Liu, X. Lv, X. Meng, G. Yu and D. Wang, Chem. Eng. J., 2013, 220, 412–419 CrossRef CAS.
- W. Li, X. Liu, Q. Yang, N. Zhang, Y. Du and H. Zhu, Food Chem., 2015, 184, 99–104 CrossRef CAS PubMed.
- H. Wu, J. Kong, X. Yao, C. Zhao, Y. Dong and X. Lu, Chem. Eng. J., 2015, 270, 101–109 CrossRef CAS.
- L. Fan, M. Li, Z. Lv, M. Sun, C. Luo, F. Lu and H. Qiu, Colloids Surf., B, 2012, 95, 42–49 CrossRef CAS.
- A. Binello, G. Cravotto, G. M. Nano and P. Spagliardi, Flavour Fragrance J., 2004, 19, 394–400 CrossRef CAS.
- J. B. Dima, C. Sequeiros and N. E. Zaritzky, Chemosphere, 2015, 141, 100–111 CrossRef CAS PubMed.
- M. M. Zhang, Y. G. Liu, T. T. Li, W. H. Xu, B. H. Zheng, X. F. Tan, H. Wang, Y. M. Guo, F. Y. Guo and S. F. Wang, RSC Adv., 2015, 5, 46955–46964 RSC.
- W. H. Xu, S. F. Wang, Y. G. Liu, G. M. Zeng, B. H. Zheng, X. F. Tan, T. T. Li, H. Wang, F. Y. Guo and M. M. Zhang, RSC Adv., 2015, 5, 24009–24015 RSC.
- S. Stankovich, D. A. Dikin, R. D. Piner, K. A. Kohlhaas, A. Kleinhammes, Y. Jia, Y. Wu, S. T. Nguyen and R. S. Ruoff, Carbon, 2007, 45, 1558–1565 CrossRef CAS.
- L. Q. Xu, D. Wan, H. F. Gong, K. G. Neoh, E. T. Kang and G. D. Fu, Langmuir, 2010, 26, 15376–15382 CrossRef CAS PubMed.
- V. Datsyuk, M. Kalyva, K. Papagelis, J. Parthenios, D. Tasis, A. Siokou, I. Kallitsis and C. Galiotis, Carbon, 2008, 46, 833–840 CrossRef CAS.
- T. Y. Jiang, J. Jiang, R. K. Xu and Z. Li, Chemosphere, 2012, 89, 249–256 CrossRef CAS PubMed.
- C. Gan, Y. G. Liu, X. F. Tan, S. F. Wang, G. M. Zeng, B. H. Zheng, T. T. Li, Z. J. Jiang and W. Liu, RSC Adv., 2015, 5, 35107–35115 RSC.
- L. L. Wei, R. Gu and J. M. Lee, Appl. Catal., B, 2015, 176–177, 325–330 CrossRef CAS.
- S. Mor, K. Ravindra and N. R. Bishnoi, Bioresour. Technol., 2007, 98, 954–957 CrossRef CAS.
- A. K. Giri, R. Patel and S. Mandal, Chem. Eng. J., 2012, 185–186, 71–81 CrossRef CAS.
- D. Park, Y. S. Yun, J. H. Jo and J. M. Park, Water Res., 2005, 39, 533–540 CrossRef CAS.
- G. N. Kousalya, M. Rajiv Gandhi and S. Meenakshi, Int. J. Biol. Macromol., 2010, 47, 308–315 CrossRef CAS.
|
This journal is © The Royal Society of Chemistry 2016 |
Click here to see how this site uses Cookies. View our privacy policy here.