DOI:
10.1039/C5RA18829F
(Paper)
RSC Adv., 2016,
6, 2512-2519
Fire retardant and charring effect of cyclic phenolphthalein (phenylene phosphonate) oligomer on polybutylene terephthalate
Received
14th September 2015
, Accepted 22nd December 2015
First published on 23rd December 2015
Abstract
A novel solid flame retardant cyclic phenolphthalein (phenylene phosphonate) (CPPA) oligomer was synthesized in high yields through the reaction of phenylphosphonic dichloride with phenolphthalein under pseudo-high dilution conditions via polycondensation. Detailed structural characterizations of this oligomer were conducted using matrix-assisted laser desorption/ionization time-of-flight mass spectrometry, 1H NMR, 31P NMR, and FTIR. Furthermore, the flame-retardant efficiency of this oligomer in polybutylene terephthalate (PBT) was investigated using limiting oxygen index (LOI), UL-94 tests and Microscale combustion colorimetry (MCC). After adding 20 wt% CPPA, the LOI increased from 20.2% to 26.2% and the UL-94 V-0 rating was achieved. The PHRR and THR values of PBT/CPPA25% were decreased. Thermogravimetric analysis, FTIR, and pyrolysis/GC/MS were employed to elucidate the pyrolysis behavior of CPPA and PBT/CPPA. The residual morphologies of the residue of the PBT/CPPA25% system were investigated through scanning electron microscopy. Results showed that the CPPA oligomer could change the degradation path of PBT and improved the char formation of the PBT/CPPA system.
Introduction
Fire safety has gained considerable attention because of the severe damage, injuries, and deaths caused by fire. Although halogen-containing flame retardants are widely used, toxic and harmful substances are released during the combustion process. Thus, discovering environmentally friendly phosphorus-containing flame retardants has become an important research topic.1–3 To date, phosphine oxides,4 phosphinates,5 phosphonates,6–9 phosphates,10,11 and phosphorus–nitrogen compounds12,13 have been successfully used as flame retardants in polymeric materials. Aromatic phosphates, such as resorcinol bis(diphenyl phosphate), poly(sulfonyldiphenylene phenylphosphonate), and bisphenol A bis(diphenyl phosphate), are effective polymers that produce phenolic functionalities upon pyrolysis, including bisphenol A polycarbonate, PC/ABS, and polybutylene terephthalate (PBT).14–19 Phosphorus-containing flame retardants are effective in polymers that produce polyarylate functionalities upon pyrolysis.20–25 Cyclic oligomers possess a unique combination of low melt viscosity and the possibility of undergoing controlled polymerization in the melt without the liberation of volatile byproducts. These properties render the oligomers good candidates in advanced thermoplastic compositions.26,27 Cyclic oligomers can also be well dispersed in the polymer matrix and offer good compatibility with polymer materials.
In this research, we introduce a cyclic phenolphthalein (phenylene phosphonate) oligomer. This oligomer was developed through the cyclization reaction of phenylphosphonic dichloride (PPD) with phenolphthalein under pseudo-high dilution conditions. The synthesis of the cyclic (arylene phosphonate) oligomer is shown in Fig. 1. The synthesis conditions are mild and convenient. Notably, the cyclic phenolphthalein (phenylene phosphonate) oligomer is used as an additive agent to improve the flame-retardant property. We selected PBT as the matrix resin for studying the flame retardant effect of the cyclic (arylene phosphonate) oligomer. The application of cyclic (arylene phosphonate) oligomer as a flame retardant additive in PBT was investigated.
 |
| Fig. 1 Synthesis scheme of cyclic phenolphthalein (phenylene phosphonate) oligomer. | |
Experimental
Materials
Phenylphosphonic dichloride, phenolphthalein was purchased from Alfa and used as received. PBT (PBT1084, density 1.31 ± 0.02 g cm−3, intrinsic viscosity 0.84 ± 0.02 cm3 g−1) used in this study was obtained as pellets from Nantong Xingchen Synthetic Material Co. Ltd., China. PBT pellets were dried for 24 h in a vacuum oven at 120 °C before use, whereas other reagents and solvents were obtained commercially and used without further purification.
Synthetic procedures
The cyclization reaction of phenylphosphonic dichloride and phenolphthalein was conducted in a 500 mL four-neck round-bottom flask equipped with a nitrogen inlet, thermometer, injection port and stirrer. The flask was charged with 200 mL of dichloromethane, 40 mL of distilled water and 0.2 g PTC (phase transfer catalyst, hexadecyltrimethylammonium bromide) at 10 °C. Disodium salt solution of phenolphthalein (7 mmol) in 50 mL distilled water and a methylene dichloride solution of phenylphosphonic dichloride (PPD) (7 mmol) were added dropwise to the mixture in the mechanically stirred flask in an equimolar fashion over a period of 8 h. After the addition, the mixture was stirred for another 2 h. The organic phase was separated and washed thrice with 15 mL of distilled water and then evaporated to dry. The yield of CPPA was 2.22 g (yield: 72%). FTIR (KBr, cm−1): 1132, 1287, 1169 (P
O), 1770 (C
O), 1202 and 1017 (P–O–C) cm−1. 1H NMR (DMSO-d6, ppm): δ 6.76 (d, 4H), 7.08 (d, 4H), 7.55–7.72 (m, 4H), 7.76 (d, 1H), 7.80 (m, 1H), 7.89–7.98 (m, 3H) ppm. 31P NMR (DMSO-d6, ppm): 12.02 (d, 1P).
Methods
Matrix-assisted laser desorption/ionization-time of flight mass spectra (MALDI-TOF-MS) were recorded on a LDI-1700 instrument at a wavelength of 337 nm (N2 laser light) using 1,8,9-dithranol as the matrix. The instrument was operated in a positive linear mode. NMR proton spectra were recorded on a Varian Unity-400 NMR spectrometer at 400 MHz in DMSO-d6 using tetramethylsilane (TMS) as the standard. Thermogravimetry analysis (TGA) was performed with a Mettler Toledo TGA851 thermal gravimetric analyzer using a continuous nitrogen flow (50 mL min−1) and a heating rate of 10 °C min−1 from 30 to 700 °C. The sample was approximately 10–20 mg. Different Scanning calorimetry (DSC) was carried out on a Mettler Toledo DSC1 Stare under continuous nitrogen flow (200 mL min−1). The samples were first heated from 25 to 250 °C at a rate of 10 °C min−1 to remove thermal history, and cooled at a rate of 10 °C min−1 25 °C, and then reheated to 250 °C at a rate of 10 °C min−1, to obtain the melting temperature (Tm) and crystallization temperature (Tc). The chemical structures of combustion residue were characterized using a VERTEX 70 FTIR (Bruker Optics) spectroscope in KBr pellets. It was collected in the region of 4000–400 cm−1 with a spectral resolution of 2 cm−1 and 64 scans. The residues for infrared analysis were obtained after thermal treatment by TGA equipment. Field emission scanning electron microscope (FESEM, XL30 ESEM FEG) was used for the observation of morphology. First the sample was heated in a temperature-programmable microfurnace pyrolyser (CDS5000-1500) under continuous helium flow (1 mL min−1). The gas thermal degradation products were identified by GC/MS (Agilent 5975). In gas chromatogram, a HB-1 nonpolar column was temperature-programmed from 80 °C (3 min) to 280 °C (20 min) at a heating rate of 10 °C min−1. For the MS measurement, ionization was carried out by electron impact (EI) at 70 eV, and a mass range between 20 and 600 amu was scanned at a rate of 2 s per scan. Mass spectrometric identification was carried out using NIST2008 standard spectral library. In the few cases, when compounds were not included in the libraries, they were identified on the basis of both the molecular ion m/z value and of the ion decomposition pattern constructed for the best fit with the mass spectrum.
Preparation of composites
PBT pellets with different contents of CPPA (15 wt%, 20 wt%, and 25 wt%) were mixed. Subsequently, melt blends were performed using a Haake Rheocord 90 internal mixer at 230 °C for 5 min with a rotation speed of 60 rpm. Samples were then molded by compression for the standard test. The neat PBT used as a standard was treated in the same manner. All blends included 1 wt% of polytetrafluorethylene (PTFE).
Combustion test
The combustion performance was studied by the limited oxygen index (LOI) test and the vertical burning ratings (UL-94) test standard on 3.0 mm specimens in the vertical configuration. LOI was measured using an LOI instrument (HC-2 Analytical Instrument Factory, China) on sheets (130 × 6.5 × 3 mm) according to the standard oxygen index test (GB2406-82, China). The test was based on the determination of the percentage of oxygen in a gas mixture (O2 and N2), which will just sustain the burning of 50 mm length of a sample for 180 s. According to the UL-94 test, the sample rod (130 × 13.0 × 3.0 mm) was placed in a holder in a vertical position and the lower end of the rod is contacted by a flame for 10 s thus initiating burning. Microscale combustion colorimeter (MCC) was used to investigate the flammability characteristics of PBT and PBT/CPPA25% composites according to ASTM D7309-07. About 20 mg samples were heated in nitrogen atmosphere (80 mL min−1) at a constant heating rate of 60 °C min−1 from room temperature to 750 °C. The decomposition products were mixed with oxygen (20 mL min−1) and then combusted in the combustion furnace (900 °C).
Results and discussion
Characterization of oligomer CPPA
Matrix-assisted laser desorption/ionization-time of flight mass spectrometry (MALDI-TOF-MS) was performed to confirm the cyclic nature of the oligomer. A relatively clean positive spectrum with a reasonable signal-to-noise ratio was obtained. The MALDI-TOF-MS spectrum revealed that the products include cyclic oligomers that range from dimers (n = 2, m/z = 881.2) to hexamers (n = 6, m/z = 2642.3) and minimal linear components. In addition to the molecular ion peaks for [Mn + H]+, the MALDI-TOF-MS spectra of CPPA (Fig. 2) showed the molecular ion peaks for the isotope adducts [Mn + D]+ and [Mn + T]+. Traces of linear oligomers were observed, and the signal was located at 759.2 Da.
 |
| Fig. 2 MALDI-TOF-MS spectrum of CPPA oligomer. | |
Scanning electron microscopy (SEM) image of the matrix
As shown in Fig. 3, an unclear phase separation of CPPA and PBT occurs. It showed the good process compatibility between PBT and CPPA.
 |
| Fig. 3 SEM image of the fractured surface of PBT/CPPA25% matrix. | |
Flammability properties
The flammability of flame-retardant materials was evaluated using the limiting oxygen index (LOI) value and the UL-94 test results (Table 1). The LOI value increased to 26.8% when the amount of CPPA was 20 wt%. Given the UL-94 test results, the sample can reach the UL-94 V-0 rating when the CPPA content was 20 wt%. Although adding CPPA cannot eliminate the melt dripping of PBT, the dripping of blends without flame cannot ignite the cotton during the test compared with the pure PBT. Thus, this dripping can reduce the loss from burning caused by dripping. Notably, the addition of CPPA was beneficial for improving the flame retardancy of PBT.
Table 1 LOI (%) values and UL-94 of different PBT samples
Samples |
Ignition the cotton |
Observed dripping |
LOI (%) |
UL-94 |
PBT |
Yes |
Drip |
20.2 |
— |
PBT/CPPA15% |
Yes |
Drip |
23.2 |
V-2 |
PBT/CPPA20% |
No |
Drip |
26.2 |
V-0 |
PBT/CPPA25% |
No |
Drip |
29.6 |
V-0 |
The heat release properties of PBT and PBT/CPPA25% were studied by a microscale combustion calorimetry technique (MCC), and the obtained heat release rate (HRR) curves are shown in Fig. 4. The peak of heat release rate (PHRR) is the maximum value of the specific heat release rate divided by the heating rate. The total heat release (THR) is the time integral of the specific heat release rate over the whole testing time. The lower THR indicate it maybe has better flame retardant performance. In this study, a reduction of both PHRR and THR is observed for PBT/CPPA25%. The PHRR values decrease from 416 W g−1 for neat PBT to 396 W g−1 for PBT/CPPA25%. The THR decreases from 24.8 kJ g−1 for neat PBT to 19.7 kJ g−1 for PBT/CPPA25%. This may be attributed to that CPPA accelerates the dehydration of PBT and releases water. CPPA promotes the formation of char layer which decreases the release amount of decomposition products.
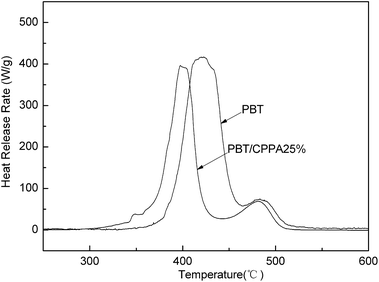 |
| Fig. 4 MCC curves of PBT and PBT/CPPA25% matrix. | |
Thermal stability analysis
The effect of fire retardants (CPPA) on the thermal property of PBT was investigated using DSC. The sample was treated in liquid nitrogen and fractured. Fig. 5 presents the DSC heating and cooling thermogram curves of neat PBT and PBT/CPPA25%. Multiple melting peaks were observed in the two samples upon heating, whereas a single peak was observed upon cooling. Adding CPPA resulted in decreased melting and crystallization temperature levels. The Tm1, Tm2, and Tc in pure PBT were 217, 225, and 196 °C, respectively, and those in PBT/CPPA25% mixture were 212, 222, and 190 °C, respectively.
 |
| Fig. 5 DSC thermograms recorded during the heating (a and b) and cooling (c and d) steps (10 °C min−1, N2) for PBT and PBT/CPFP25%. | |
Fig. 6 shows the thermogravimetric curves of PBT, CPPA, and the PBT/CPPA25% mixture (experimental and calculated) under nitrogen atmosphere. The thermogravimetric data of PBT, CPPA, and their mixtures are summarized in Table 2.
 |
| Fig. 6 Thermogravimetry of PBT, CPPA and PBT/CPPA25% mixture (experimental and calculated). | |
Table 2 Thermal property of different samples in nitrogena
Sample |
Tonset (°C) |
Tmax and weight loss at this stage |
Char yield/% (700 °C) (by experimental) |
Char yield/% (700 °C) (by calculated) |
Tmax,1 (°C) |
Weight loss (%) |
Tmax,2 (°C) |
Weight loss (%) |
Tonset is the onset decomposition temperature at which the weight loss is 5%. Tmax is the maximum-rate degradation temperature. Tmax,1 is the maximum-rate degradation temperature of first stage. Tmax,2 is the maximum-rate degradation temperature of second stage. |
CPPA |
312 |
385 |
20 |
— |
— |
54 |
— |
PBT |
372 |
403 |
51 |
469 |
93.6 |
0 |
— |
PBT/CPPA15% |
365 |
393 |
59 |
474 |
82 |
12 |
7 |
PBT/CPPA20% |
357 |
386 |
46 |
467 |
77 |
15 |
10 |
PBT/CPPA25% |
345 |
384 |
51 |
459 |
77 |
16 |
12 |
The thermal degradation of pure CPPA started at 312 °C. This degradation involved a one-step decomposition and obtained a large amount of charred residue (54%) at 700 °C under nitrogen atmosphere (Table 2). By contrast, the thermal degradation of pure PBT, which involved a two-step decomposition, started at 372 °C and showed no residue under the same condition. The Tonset of PBT/CPPA composites at the first step was slightly lower than that of pure PBT. Moreover, the onset decomposition temperature decreased as the amount of CPBA increased.
Thermogravimetry provides evidence that CPPA interacts with PBT upon pyrolysis because of the increase in solid residue and the decrease in the onset decomposition temperature of the formulation containing CPPA (Fig. 7). This phenomenon is well demonstrated by the comparison of experimental and calculated thermograms. The calculated curve is a linear combination of the thermograms of the single components of the mixture. Therefore, the curve represents a non-interacting behavior. At the end of the first step, weight loss was lower than that of pure PBT, and CPPA restrained the decomposition of PBT. The addition of CPPA improved the char formation of PBT. A final solid residue percentage of approximately 16% was obtained at 700 °C under inert atmosphere. This result also shows that CPPA is a good char former. The amount of solid residue obtained at 700 °C increased by more than 30%, which is expected from their independent thermal decomposition behavior. A similar effect was observed in previous studies.15,16,28–30
 |
| Fig. 7 Gas chromatogram of the gaseous pyrolysis products of CPPA obtained on heating at 600 °C (50 °C min−1) for 1 min, for peak assignment see Table 3. | |
Pyrolysis/GC/MS study
Pyrolysis/GC/MS measurement was conducted to evaluate the influence of CPPA on the thermal decomposition behavior of PBT. CPPA, PBT, and PBT/CPPA25% were pyrolyzed at 600 °C by pyrolysis/GC/MS to obtain a more precise insight into the products of thermal decomposition. We inferred the structures of the products according to the NIST2008 standard spectral library.
Table 3 shows the main pyrolysis products of CPPA obtained through pyrolysis/GC/MS analysis. A typical chromatogram is shown in Fig. 7 and reports the formation of benzene, phenol, phenyl diphenyl phosphinate, and triphenyl phosphite.
Table 3 The pyrolysis products of CPPA at 600 °C
Peak no. |
Molecular mass (m/z) |
Compound |
m/z: 310, 217, 199, 170, 153, 112, 94, 77, 65, 51. m/z: 294, 201, 170, 95, 77, 65, 51, 39. |
1 |
44 |
CO2 |
2 |
78 |
 |
3 |
94 |
 |
4 |
224 |
Olefin from PTC |
5a |
310 |
 |
6b |
294 |
 |
Neat PBT and PBT/CPPA25% were heated at 600 °C for 1 min. The corresponding gas chromatograms are shown in Fig. 7(a) and (b). The chemical structures of the components are provided in Table 4.
Table 4 The pyrolysis products of PBT and PBT/CPPA25% at 600 °C
Peak no. |
Molecular mass (m/z) |
Compound |
1 |
44, 54 |
CO2, H2C CHCH CH2 |
2 |
72 |
 |
3 |
78 |
 |
4 |
94 |
 |
5 |
122 |
 |
6 |
176 |
 |
7, 9 |
224, 212 |
Olefin from PTC |
8 |
234 |
 |
10 |
220 |
 |
11 |
274 |
 |
12 |
310 |
 |
13 |
298 |
 |
14 |
310 |
 |
15 |
396 |
 |
In both cases, compounds 10 and 11 (terephthalic acid mono-3-butenyl ester and terephthalic acid di-3-butenyl ester, respectively) were the main thermolysis products. The main pyrolysis products of neat PBT were basically the same as previously reported.11 The new evolved products, namely, phenol, resulted from CPPA (Fig. 8). The formation of benzene on the pyrolysis of PBT modified by CPPA was shown in the Fig. 9. The presence of CPPA increased the amount of generated tetrahydrofuran, probably at the expense of butadiene,31 and products 8 and 15 increased with the decrease in products 13 and 14.
 |
| Fig. 8 Gas chromatogram of the gaseous pyrolysis products of PBT (a) and PBT/CPPA25% (b) obtained on heating at 600 °C (50 °C min−1) for 1 min. For peak assignment see Table 4. | |
 |
| Fig. 9 Formation of benzene on the pyrolysis of PBT modified by CPPA. | |
In conclusion, the pyrolysis/GC/MS data support the thermogravimetric evidence that CPPA changes the degradation path of PBT as new products are formed.
Infrared study of residues
Fig. 10 shows the IR spectra of the initial CPPA (spectrum (a)) and the solid residue obtained at 20% weight loss (b) and after the main stage of weight loss (c). In spectrum (a), the main absorption bands were associated with the vibrations of aromatic ring (1600 and 1503 cm−1), aromatic C–H (3057 and 743 cm−1), C
O (1770 cm−1), phosphine oxide phosphoryl P
O (1287, 1169, and 1132 cm−1), and P–O–C (1017 cm−1). Further heating to a weight loss of 20% and after the main stage of weight loss resulted in decreased absorption of C
O and increased absorption band at 1000 cm−1 (P–OH).32 The phosphoryl absorption band at 1287 cm−1 reduced in frequency and broadened as a result of hydrogen bonding. Moreover, the band was superimposed with the aromatic C–O vibration (1210 cm−1).
 |
| Fig. 10 Infrared spectra of initial CPPA (a) and its solid product of the thermal decomposition collected at 20% weight loss (b), and after the main stage of weight loss (c). KBr pellets. | |
Fig. 11 shows the IR spectra of initial PBT/CPPA25% and solid residues from the PBT/CPPA25% formulation. In spectrum (a), the absorption bands at 1170, 1016, and 935 cm−1 were attributed to CPPA. At 20% weight loss (Fig. 11, spectrum (b)), new absorption bands at 2664, 2544, and 1695 cm−1 (aromatic acid) appeared. This thermal decomposition behavior resembles that of pure PBT.28 The residue that remained after 25% weight loss exhibited new bands, indicating the formation of anhydride groups (1781 and 1204 cm−1).
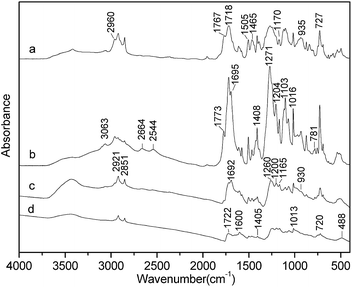 |
| Fig. 11 Infrared spectra of initial PBT/CPPA25% (a) and solid products of the thermal decomposition of the mixture collected during thermogravimetry at different steps of weight loss in inert atmosphere: 20% weight loss (b), 50% weight loss (c), and after the main stage of weight loss (d). KBr pellets. | |
Further degradation led to an increase in the characteristic absorption bands of O–Cring at 1200 cm−1.
At 50% weight loss, the amount of CPPA in the polymer appeared to decline, as shown by the low relative intensity of absorption at 930 cm−1. Further heating to the main stage of weight loss and beyond resulted in different IR absorption changes depending on the existence of additives. In the presence of CPPA, a broad absorption band appeared at 1600 cm−1, which is due to aromatic C
C stretching vibrations.6 As this band grew with increasing weight loss, we inferred that the charring processes involving aromatization occurred.31,32 Bonding to the methylene group at 2920 and 2850 cm−1 and the aromatic C–H (720 cm−1) were still detected in the solid residue after the main stage of weight loss.28
Based on the FTIR investigations reported above, CPPA promotes the aromatization of PBT during thermal degradation. This degradation is speculated to be caused by an active participation of CPPA in the ongoing chemical processes.
Morphology of residues
The PBT/CPPA25% composite was burnt during the UL-94 test, and its residue was collected for testing. As shown in Fig. 12, the PBT/CPPA25% outer char residue presents a compact and continuous char layer that provides a considerably superior barrier to heat transfer and combustible gases. This layer then interferes with the combustion of the materials. Interior char residue with abundant holes was formed by gaseous products during burning. Stable and integrated char structures improve flame retardancy. Moreover, char structures cannot be destroyed even at high temperature, and the morphologies of residual chars can explain the efficient flame retardancy of CPPA. Thus, flame retardancy was improved.
 |
| Fig. 12 SEM images of PBT/CPPA25% composite char: the outer surface (a), the inner surface (b). | |
Energy-dispersive spectrometry (EDS) measurements showed the enrichment of P, C, and O elements on the surface of PBT/CPPA25% char composite. EDS revealed that the residual chars contained polyphosphoric or phosphoric acid, which has a function in carbonization. During burning, phosphorus in polymers is converted to phosphoric acid, and further thermal decomposition leads to polyphosphoric acid formation. Polyphosphoric acid esterifies and dehydrates the pyrolyzing polymer, and a simultaneously forming phosphorus-rich carbonaceous layer further inhibits the pyrolytic reactions. These data agree with those obtained from infrared study of residues.
Conclusions
A novel solid flame retardant cyclic phenolphthalein (phenylene phosphonate) oligomer was synthesized in high yields through the reaction of PPD with phenolphthalein under pseudo-high dilution conditions. FTIR, 1H NMR, 31P NMR, and MALDI-TOF-MS were performed to confirm the cyclic structure of the CPPA oligomer. CPPA was added as flame retardant to PBT via melt blending. TGA, FTIR, and pyrolysis/GC/MS studies showed that CPPA improved the residual char formations of composites. Moreover, results indicated that the addition of CPPA apparently changed the pyrolysis pathways of PBT through the formation of thermally stable polyarylates and phenolic groups. CPPA addition resulted in the increase of LOI and achievement of UL-94 test V-0 rating. The PHRR and THR values of PBT/CPPA25% were decreased. SEM images showed that the residue, which contains a continuous outer surface and porous internal structure, provided a good barrier for improving the thermal behavior and flammability properties of the composites during burning.
In addition, the cyclic oligomer flame retardant possesses good material compatibility and thermal stability, as well as shows potential difficulty in migration. Therefore, the cyclic oligomer flame retardant presents broad application prospects.
Notes and references
- S. V. Levchik and E. D. Weil, Polym. Int., 2005, 54, 11–35 CrossRef CAS
. - S. Bernhard, Materials, 2010, 3, 4710–4745 CrossRef
. - S. V. Levchik and E. D. A. Weil, J. Fire Sci., 2006, 24, 345–364 CrossRef CAS
. - W. Aufmuth, S. V. Levchik, G. F. Levchik and M. Klatt, Fire Mater., 1999, 23, 1–6 CrossRef CAS
. - W. Yang, N. N. Hong, L. Song, Y. Hu, R. K. K. Yuen and X. L. Gong, Ind. Eng. Chem. Res., 2012, 51, 8253–8261 CrossRef CAS
. - A. I. Balabanovich and E. Engelmann, Polym. Degrad. Stab., 2003, 79, 85–92 CrossRef CAS
. - L. Chen and Z. W. Yu, Materials, 2010, 3, 4746–4760 CrossRef CAS
. - H. Q. Peng, Q. Zhou and D. Y. Wang, J. Ind. Eng. Chem., 2008, 14, 589–595 CrossRef CAS
. - D. Price, K. Pyrah, T. R. Hull, G. J. Milnes and J. R. Ebdon, Polym. Degrad. Stab., 2002, 77, 227–233 CrossRef CAS
. - E. Gallo, B. Schartel, U. Braun and D. Acierno, Polym. Adv. Technol., 2011, 22, 2382–2391 CrossRef CAS
. - J. F. Xiao, Y. Hu, L. Yang and Y. B. Cai, Polym. Degrad. Stab., 2006, 91, 2093–2100 CrossRef CAS
. - X. Zhang, Y. Zhong and Z. P. Mao, Polym. Degrad. Stab., 2012, 97, 1504–1510 CrossRef CAS
. - C. Nguyen and S. Jinhwan Kim, Macromol. Res., 2008, 16, 620–625 CrossRef CAS
. - G. F. Levchik, Y. V. Grigoriev, A. I. Balabanovich, S. V. Levchik and M. Klatt, Polym. Int., 2000, 49, 1095–1100 CrossRef CAS
. - A. I. Balabanovich, A. M. Balabanovich and J. Engelmann, Polym. Int., 2003, 52, 1309–1314 CrossRef CAS
. - A. I. Balabanovich, G. F. Levchik, S. V. Levchik and J. Engelmann, J. Fire Sci., 2002, 20, 71–83 CrossRef CAS
. - A. I. Balabanovich, J. Anal. Appl. Pyrolysis, 2004, 72, 229–233 CrossRef CAS
. - M. C. Despinasse and B. Schartel, Polym. Degrad. Stab., 2012, 97, 2571–2580 CrossRef CAS
. - E. A. Murashko, G. F. Levchik, S. V. Levchik, D. A. Bright and S. Dashevsky, J. Appl. Polym. Sci., 1999, 71, 1863–1872 CrossRef CAS
. - D. Hoang and J. Kim, Macromol. Res., 2015, 23, 579–591 CrossRef CAS
. - Y. H. Guan, J. Q. Huang, J. C. Yang and Z. B. Shao, Ind. Eng. Chem. Res., 2015, 54, 3524–3531 CrossRef CAS
. - X. J. Lai, S. Tang, H. Q. Li and X. R. Zeng, Polym. Degrad. Stab., 2015, 113, 22–31 CrossRef CAS
. - C. M. Feng, Z. W. Li, M. Y. Liang, J. G. Huang and H. B. Liu, J. Anal. Appl. Pyrolysis, 2015, 111, 238–246 CrossRef CAS
. - A. Ramani and A. E. Dahoe, Polym. Degrad. Stab., 2014, 104, 71–86 CrossRef CAS
. - Y. Wei, S. Lei and H. Yuan, J. Appl. Polym. Sci., 2011, 122, 1480–1488 CrossRef
. - Q. Z. Guo and T. L. Chen, Chem. J. Chin. Univ., 2003, 24, 909–912 CAS
. - H. M. Zhang, Q. Z. Guo and T. L. Chen, Chin. J. Polym. Sci., 2004, 22, 83–89 Search PubMed
. - A. I. Balabanovich, T. A. Zevaco and W. S. Macromol, Mater Eng., 2004, 289, 181–190 CAS
. - A. I. Balabanovich, Polym. Degrad. Stab., 2007, 84, 451–458 CrossRef
. - A. I. Balabanovich, J. Fire Sci., 2003, 21, 285–298 CrossRef CAS
. - I. C. McNeill and M. Bounekhel, Polym. Degrad. Stab., 1991, 34, 187–204 CrossRef CAS
. - L. Costa, M. Avataneo, P. Bracco and V. Brunella, Polym. Degrad. Stab., 2002, 77, 503–510 CrossRef CAS
.
|
This journal is © The Royal Society of Chemistry 2016 |
Click here to see how this site uses Cookies. View our privacy policy here.