DOI:
10.1039/C6QI00246C
(Research Article)
Inorg. Chem. Front., 2016,
3, 1332-1340
Efficient and chemoselective hydrogenation of nitroarenes by γ-Fe2O3 modified hollow mesoporous carbon microspheres
Received
13th July 2016
, Accepted 27th August 2016
First published on 29th August 2016
Abstract
Recently, it has become imperative to design non-precious-metal-based nanocatalysts with high catalytic efficiency for the hydrogenation of nitroarenes to the corresponding aromatic amines under mild reaction conditions. In this study, γ-Fe2O3-nanoparticle-supported hollow mesoporous carbon microsphere (h-MCM) nanocatalysts (γ-Fe2O3/h-MCM) were prepared, and their catalytic performance for the hydrogenation of nitroarenes was investigated. Here, h-MCM prepared by the co-sol–emulsion-gel method exhibited a mesoporous hollow structure, high surface area, and accessible interior space as well as a graphitic carbon framework; thus, aromatic compounds can sufficiently come into contact with the active sites, as well as enhance the mass transfer effect. N2H4·H2O used herein as the reducing agent only generated N2 and H2O as harmless by-products. γ-Fe2O3/h-MCM was obtained by the calcination of Fe(NO3)3-absorbed h-MCM under an inert atmosphere. From transmission electron microscopy results, the annealing temperature significantly affected the γ-Fe2O3 particle size, and in turn catalytic activity: the γ-Fe2O3/h-MCM nanocatalyst annealed at 500 °C for 15 min (20%-γ-Fe2O3/h-MCM-500-15) exhibited high catalytic activity. By the use of 20%-γ-Fe2O3/h-MCM-500-15 as the optimal catalyst, all nitroarenes investigated for hydrogenation exhibited high conversion, with a 100% selectivity for aniline, indicating the excellent selectivity of γ-Fe2O3-based catalysts. In addition, the catalyst can be easily recovered with an external magnetic field and reused at least five times without obvious decrease in catalytic activity. This study provides a useful platform based on a cost-effective, magnetically recyclable γ-Fe2O3-based nanocatalyst for the highly efficient hydrogenation of nitroarenes.
Introduction
Aromatic amines are important intermediates in the synthesis of various industrially valuable products, such as agrochemicals, dyes, polymers, herbicides, pigments, and pharmaceuticals.1,2 Traditionally, aromatic amines can be synthesized by the reduction of the corresponding nitroarenes using Fe/Sn–HCl or hydride reagents as reductants.3–5 Nevertheless, these methods are not environment friendly, due to the generation of harmful chemical waste and other metal salts during reduction. With respect to environmental concerns, the hydrogenation of nitroarenes to the corresponding amines using H2 as the reductant is an emerging topic in organic synthesis, affording H2O as the only byproduct. During the past few years, researchers have investigated transition-metal-based catalysts for the catalytic hydrogenation of nitro compounds.6,7 Noble-metal-based supported catalysts, such as Pd and Pt, exhibit high catalytic activity for the hydrogenation of nitroarenes under ambient reaction conditions, i.e., room temperature and atmospheric H2 pressure.8–10 Nevertheless, as noble metals are extremely scarce, noble-metal catalysts are very expensive, which in turn increases the production cost of amines. On the other hand, non-precious metal catalysts, such as Co and Ni-based heterogeneous catalysts have also been investigated for the catalytic hydrogenation of nitroarenes. However, the use of such catalysts stipulates the use of harsh conditions, such as high H2 pressure and relatively high temperatures.11,12 Although the well-known RANEY® nickel catalyst is used for the catalytic hydrogenation of nitroarenes, drawbacks, such as its pyrophoric nature and moisture sensitivity, significantly limit its application.13 Thus, it is imperative to develop non-precious metal catalysts with high catalytic efficiency for the hydrogenation of nitroarenes under mild reaction conditions.
Nowadays, metal nanoparticles (NPs) that can be used as catalytic activity centers are supported on mesostructured materials for preventing their aggregation, decreasing metal usage, and enhancing catalytic activities. Mesoporous materials, such as hollow mesoporous phosphosilicate, mesoporous silica, N-doped mesoporous carbon, Al2O3, and MOFs, have been used as supports for preparing noble-metal or non-precious metal-based nanocatalysts.14–21 These catalysts exhibit excellent catalytic activities for some reactions. On the other hand, these catalysts also exhibit some drawbacks, such as insufficient contact between the active site and reactants. Recently, hollow mesoporous carbon microspheres (h-MCM) have been reported to exhibit excellent physicochemical properties as compared to those of microporous or nonporous materials; thus, h-MCM can be ideal candidates for fabricating supported nanocatalysts.22–24 Notably, h-MCM exhibits a mesoporous hollow structure, low density, high surface area, as well as accessible interior space and a graphitic carbon framework; thus, h-MCM facilitates not only adsorption to aromatic compounds and permits sufficient contact with active sites, but also enhances the mass transfer effect; thus, h-MCM-based nanocatalysts exhibit high catalytic efficiency. Typically, h-MCM is prepared via hard- and soft-templating approaches, and both strategies are well accepted.23,25 However, both hard- and soft-templating methods involve multiple steps for synthesizing h-MCM. As compared to the two commonly accepted methods, the recently reported co-sol–emulsion-gel method is a facile method for preparing h-MCM with ultrahigh surface area and large pore volume.26
With the abovementioned information, and according to the reported studies that utilize γ-Fe2O3 for catalyzing the hydrogenation of nitroarenes with hydrazine hydrate (N2H4·H2O),27,28 h-MCM materials with high surface area were prepared in this study by the co-sol–emulsion-gel method and modified with γ-Fe2O3 NPs by the calcination of Fe(NO3)3-modified h-MCM under an inert atmosphere, affording the γ-Fe2O3/h-MCM nanocatalyst. Using N2H4·H2O as the reductant, γ-Fe2O3/h-MCM can catalyze the hydrogenation of nitroarenes at atmospheric pressure with high conversion and yield, generating N2 and H2O as byproducts; the production of nontoxic byproducts is in agreement with the national environmental policy. Furthermore, the eco-friendly γ-Fe2O3/h-MCM nanocatalyst is not only inexpensive but also magnetically recyclable. The catalyst can be recovered in a facile manner and can be reused at least five times without obvious decrease in catalytic activity.
Experimental
Materials
Resorcinol, cetyltrimethylammonium bromide (CTAB), tetraethyl orthosilicate (TEOS), and N2H4·H2O were supplied by Tianjin Heowns Biochemical Technology Co., Ltd. Aromatic nitro compounds, ferric nitrate, and other reagents were of analytical grade and were purchased from Sinopharm Chemical Reagent Co. Ltd (China); they were used without further purification.
Preparation of h-MCM
h-MCM was prepared according to a similar co-sol–emulsion-gel procedure reported previously.26 Typically, 0.2 g of resorcinol and 0.6 g of CTAB were first dissolved under vigorous stirring in a 100 mL round-bottom flask containing 25 mL of deionized water and 5 mL of ethanol at room temperature. Second, after all reagents were completely dissolved, 0.2 mL of 25 wt% NH3·H2O was added dropwise. Third, 0.28 mL of a formaldehyde solution was added dropwise, followed by the immediate addition of TEOS to the transparent solution. Next, the prepared mixture was stirred at room temperature for 24 h and then transferred to a Teflon-lined autoclave and heated at 80 °C for one day. Then, the solid materials were obtained by centrifugation and vacuum-dried overnight. Finally, the solid materials thus obtained were annealed from 25 °C to 850 °C at a ramp rate of 1 °C min−1 and maintained at 850 °C for 3 h under N2. The obtained hollow mesoporous carbon/silica microspheres were etched with a 15% HF aqueous solution for 24 h, followed by centrifugation and subsequently washed with H2O, affording h-MCM.
Fabrication of the γ-Fe2O3/h-MCM catalyst
First, h-MCM and Fe(NO3)3·9H2O were dissolved in 30 mL of H2O. Second, after complete adsorption and rotary drying, the obtained composite was annealed from room temperature to a certain high temperature at a ramp rate of 5 °C min−1 and maintained for 15 min under an inert atmosphere. Then, the m-γ-Fe2O3/h-MCM-x-y catalyst was obtained, where m represents the γ-Fe2O3 weight percentage, x represents the annealing temperature, and y represents the annealing time.
Hydrogenation of nitroarenes using the γ-Fe2O3/h-MCM catalyst
Typically, 10 mg of 20%-γ-Fe2O3/h-MCM-500-15 and 1 mmol of an aromatic nitro compound were ultrasonically dispersed in 5 mL of ethanol, followed by the addition of 4 mmol of N2H4·H2O, and then the mixture was heated to 80 °C and refluxed for several hours. The reaction process was monitored on an Agilent gas chromatography-mass spectrometry (GC-MS 5977E) system.
Characterization
The morphology of the h-MCM and γ-Fe2O3/h-MCM catalyst was characterized by transmission electron microscopy (TEM, Tecnai G2 F30) and scanning electron microscopy (SEM, JSM-6701F). Powder X-ray diffraction (PXRD, Rigaku D/max-2400) equipped with Cu-K radiation was employed for investigating the physical properties of the samples. X-ray photoelectron spectroscopy (XPS, Perkin-Elmer PHI-5702) was employed for measuring the electronic states of the surface of the γ-Fe2O3/h-MCM catalyst. N2 adsorption–desorption isotherms of the h-MCM and γ-Fe2O3/h-MCM catalyst were recorded at 77 K using a Micromeritics ASAP 2010 analyzer (USA). The magnetic measurement of γ-Fe2O3/h-MCM was performed using a Quantum Design vibrating sample magnetometer (VSM) at room temperature under an applied magnetic field sweeping from −15 to 15 kOe. Inductively coupled plasma atomic emission spectroscopy (ICP-AES) was employed for testing the γ-Fe2O3 content of the γ-Fe2O3/h-MCM nanocatalyst. GC-MS was applied for estimating the conversion and selectivity from the hydrogenation of nitroarene.
Results and discussion
Material characterization
In this study, Fe(NO)3 was absorbed into the mesopores and hollow core of h-MCM. When annealed at high temperatures under N2, Fe(NO)3 was converted to γ-Fe2O3, which was attributed to the reducibility of the carbon framework of h-MCM (Scheme 1).29 For investigating the crystalline phase of iron oxide, the PXRD of the samples annealed at 400 °C, 500 °C, 600 °C, and 700 °C was measured, and Fig. 1 shows the results. In all samples, a peak was centered at 26.4°, corresponding to the graphitic interlayer of h-MCM. In the 20%-γ-Fe2O3/h-MCM-400-15 sample, very weak peaks were observed, corresponding to iron oxide, which was probably due to the fact that a low annealing temperature just converted a part of Fe(NO)3 to γ-Fe2O3. However, in the 20%-γ-Fe2O3/h-MCM-500-15, 20%-γ-Fe2O3/h-MCM-600-15, and 20%-γ-Fe2O3/h-MCM-700-15 samples, very clear diffraction peaks were observed for γ-Fe2O3, centered at 2θ = 30.2°, 35.6°, 43.3°, 57.1°, and 62.9°, corresponding to (220), (311), (400), (511), and (440) of γ-Fe2O3 (JCPDS no. 39-1346), respectively.30
 |
| Scheme 1 The fabrication procedure of the γ-Fe2O3/h-MCM nanocatalyst and its catalytic hydrogenation of nitrobenzene. | |
 |
| Fig. 1 XRD spectra of the h-MCM and the prepared γ-Fe2O3/h-MCM nanocatalysts. | |
Fig. 2 shows the morphology of the samples. From the SEM image of h-MCM in Fig. 2a, h-MCM exhibited a spherical shape with an average diameter of approximately 150 nm. Fig. 2b shows the TEM image of h-MCM, in which h-MCM exhibited a hollow core with a shell thickness of approximately 20 nm. The mesopores on the shell were clearly visible. When h-MCM was absorbed with Fe(NO)3 and annealed under N2, γ-Fe2O3 was successfully supported on the mesopores and in the hollow core of h-MCM. Fig. 2c shows the image of 20%-γ-Fe2O3/h-MCM-500-15 annealed at 500 °C; γ-Fe2O3 tiny particles were clearly grafted on h-MCM with an average diameter of approximately 3 nm (Fig. 2c, inset). However, for the 20%-γ-Fe2O3/h-MCM-600-15 and 20%-γ-Fe2O3/h-MCM-700-15 catalysts annealed at 600 °C and 700 °C, larger γ-Fe2O3 NPs with average diameters of approximately 5 nm and 7 nm were observed, respectively (Fig. 2d and e, insets). The reason that the calcination temperature affects the particle size of the γ-Fe2O3 NPs was that at higher annealing temperature, the γ-Fe2O3 NPs tend to aggregate and form lager particles. As shown in the TEM images in Fig. 2d and e, at high annealing temperature, the h-MCM support was slightly damaged. The diameters of the γ-Fe2O3 NPs measured from TEM images were consistent with the results calculated from the Scherrer equation. The different γ-Fe2O3 NP sizes possibly affected the performance of the prepared catalyst. As can be observed in the EDS result in Fig. 2f, the prepared catalysts were composed of Fe, O, and C elements.
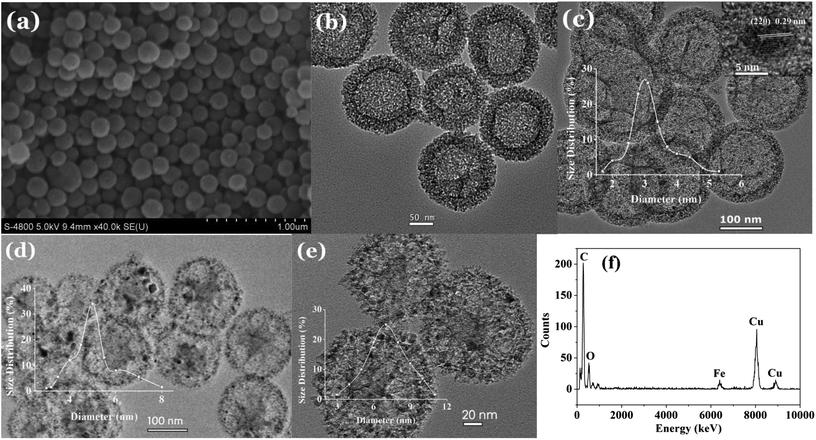 |
| Fig. 2 SEM (a) and TEM (b) images of the h-MCM, TEM images of the 20%-γ-Fe2O3/h-MCM-500-15 (c), 20%-γ-Fe2O3/h-MCM-600-15 (d) and 20%-γ-Fe2O3/h-MCM-700-15 (e) (inset image of c, the lattice fringe of the γ-Fe2O3; inset curves of c, d and e, size distribution of γ-Fe2O3 NPs), and EDS spectrum of the 20%-γ-Fe2O3/h-MCM-500-15 (f). | |
For investigating the composition and surface valence states of the prepared γ-Fe2O3/h-MCM nanocatalysts, XPS analysis was employed. Fig. 3a shows a wide-range XPS spectrum of 20%-γ-Fe2O3/h-MCM-500-15: the obtained catalyst was mainly composed of Fe, O, and C elements, which is consistent with the result obtained from EDS (Fig. 2f). Using the reference C 1s peak at 284.6 eV, the Fe 2p spectrum is shown in Fig. 3b. Two broad peaks were observed in the Fe 2p spectrum, attributed to Fe 2p1/2 and Fe 2p3/2, respectively. More importantly, a characteristic peak was clearly observed at 719.8 eV between Fe 2p1/2 and Fe 2p3/2, attributed to γ-Fe2O3.29
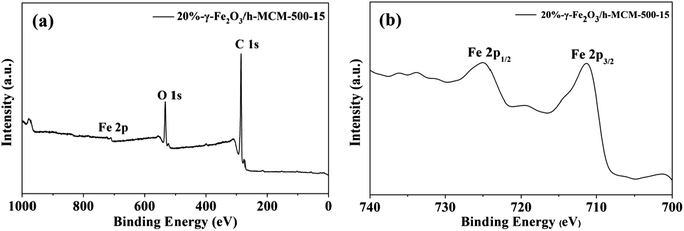 |
| Fig. 3 XPS wide-scan spectrum of the 20%-γ-Fe2O3/h-MCM-500-15 (a), and XPS spectrum of Fe 2p (b). | |
Fig. 4a shows the N2 adsorption/desorption isotherms of the h-MCM and 20%-γ-Fe2O3/h-MCM-500-15 nanocatalyst. As can be observed, both materials exhibited type IV isotherms, implying that both of the prepared samples exhibit mesostructures. Fig. 4b shows the pore size distribution curves of both samples. h-MCM exhibited a pore size distribution between 4 and 20 nm, while the 20%-γ-Fe2O3/h-MCM-500-15 catalyst exhibited a decreased pore size distribution between 4 and 10 nm, probably due to the grafting of the γ-Fe2O3 NPs in the mesopores of h-MCM. Furthermore, Table 1 summarizes the textual properties of h-MCM and the 20%-γ-Fe2O3/h-MCM-500-15 nanocatalyst. The surface area, pore volume, and average pore size of h-MCM were 1058.9 m2 g−1, 1.8 cm3 g−1, and 6.7 nm, respectively. When h-MCM was modified with γ-Fe2O3 NPs, these textual properties decreased to 948 m2 g−1, 1.01 cm3 g−1, and 4.8 nm, respectively, for 20%-γ-Fe2O3/h-MCM-500-15. The ultrahigh surface area and mesoporous structure of the prepared nanocatalyst are beneficial for catalytic reactions.31,32
 |
| Fig. 4 The N2 sorption isotherms of h-MCM and 20%-γ-Fe2O3/h-MCM-500-15 (a), the pore size distribution of h-MCM and 20%-γ-Fe2O3/h-MCM-500-15 (b). | |
Table 1 Textual properties of h-MCM and 20%-γ-Fe2O3/h-MCM-500-15
Entry |
Sample |
S
BET (m2 g−1) |
Pore volume (cm3 g−1) |
Pore size (nm) |
1 |
h-MCM |
1058.9 |
1.8 |
6.7 |
2 |
20%-γ-Fe2O3/h-MCM-500-15 |
948 |
1.01 |
4.8 |
As shown in Fig. 5, the magnetic hysteresis loop of the 20%-γ-Fe2O3/h-MCM-500-15 nanocatalyst was obtained at room temperature. It can be seen that the nanocatalyst exhibited superparamagnetic properties,33 and the saturation magnetization was approximately 9.8 emu g−1; this value is essential because the catalyst could be easily recovered from the reaction mixture by an external magnetic field, thus avoiding complex separation. The inset in Fig. 5 shows the simple recovery process of a catalyst using a magnet. In addition, the collected catalysts also can be re-dispersed with a slight shake. The excellent magnetic properties of the 20%-γ-Fe2O3/h-MCM-500-15 nanocatalyst make it promising in magnetic recyclable catalysis.
 |
| Fig. 5 Room-temperature magnetization curve of the 20%-γ-Fe2O3/h-MCM-500-15 nanocatalyst. Inset is the magnetic manipulation of the 20%-γ-Fe2O3/h-MCM-500-15 nanocatalyst. | |
Hydrogenation of nitroarenes
The prepared γ-Fe2O3/h-MCM catalyst exhibited a high surface area, easily accessible internal and external surfaces, and highly dispersed γ-Fe2O3 NPs, which encouraged us to investigate its catalytic activity for the hydrogenation of nitroarenes using N2H4·H2O as the reducing agent (Scheme 1). Nitrobenzene was chosen as the model substrate for screening the optimal reaction conditions, and Table 2 summarizes the results. Initially, we chose ethanol as the solvent and a refluxing temperature of 80 °C as the reaction temperature for optimizing the catalyst. As described in TEM analysis, 20%-γ-Fe2O3/h-MCM-15 annealed at 700 °C, 600 °C, and 500 °C exhibited a γ-Fe2O3 NP size of 3 nm, 5 nm, and 7 nm, respectively. At the same loading of γ-Fe2O3, the smaller the size of the γ-Fe2O3 NP, the greater is the surface area of the active sites. Hence, the 20%-γ-Fe2O3/h-MCM-500-15 catalyst should exhibit high catalytic activity, and Table 2 lists the results; entries 2–4 confirm this inference. From entry 2 in Table 2, with the use of the 20%-γ-Fe2O3/h-MCM-500-15 catalyst, the conversion and selectivity for the hydrogenation of nitrobenzene were both 100%. Because ferric salts were not completely converted to γ-Fe2O3, the 20%-γ-Fe2O3/h-MCM-400-15 catalyst only exhibited a conversion of 72.40% for the hydrogenation of nitrobenzene (Table 2, entry 1). When the annealing time was prolonged to 30 min or 60 min, the conversion for hydrogenation slightly decreased (Table 2, entries 5 and 6). Thus, a long pyrolysis time is apparently not beneficial for the γ-Fe2O3/h-MCM activity. On the other hand, upon decreasing γ-Fe2O3 loading in γ-Fe2O3/h-MCM-500-15 to 12% and 6%, the conversion of hydrogenation decreased to 58.66% and 34%, respectively (Table 2, entries 7 and 8). When H2 (1 atm) was selected instead of N2H4·H2O as the reductant, almost no reaction occurred (Table 2, entry 9). Using the unsupported h-MCM and commercial α-Fe2O3 as the catalysts, just no greater than 1% nitrobenzene was converted (Table 2, entries 10 and 11), indicating that magnetic γ-Fe2O3 is the active site. The Fe3O4 NPs fabricated according to Zhao's study also exhibited a low catalytic activity for the hydrogenation of nitrobenzene (Table 2, entry 12).34 When the optimal catalyst was selected as 20%-γ-Fe2O3/h-MCM-500-15, the effect of the reaction solvent was studied next. As can be observed from entries 13–15 in Table 2, the use of H2O, ethyl acetate, and cyclohexane exhibited catalytic activity less than that observed with the use of ethanol, probably due to the poor solubility of nitrobenzene in H2O and poor dispersibility of the investigated catalyst in ethyl acetate and cyclohexane. Furthermore, the reaction temperatures of 20 °C, 40 °C, and 60 °C were also investigated (Table 2, entries 16–18), and the results indicated that a low reaction temperature results in low catalytic activity for the 20%-γ-Fe2O3/h-MCM-500-15 catalyst. When the nitrobenzene was hydrogenated without a catalyst, and only used the reductant of hydrazine, the reaction almost did not occur with only 0.48% conversion of the nitrobenzene (Table 2, entry 19). From the above investigation of the reaction conditions, under all conditions catalyzed by γ-Fe2O3-based catalysts, the selectivity of aniline was near 100%, indicative of the excellent selectivity of γ-Fe2O3-based catalysts.
Table 2 Screening of the reaction conditions using the catalytic hydrogenation of nitrobenzene to aniline as the probe reactiona

|
Entry |
Catalyst |
Solvent |
Reaction temperature |
Conv. (%) |
Sel. (%) |
Reaction conditions: nitrobenzene (1 mmol), catalyst (10 mg), 4 mmol of hydrazine hydrate, solvent (5 mL), reactions were allowed to run for 2 h at 80 °C.
Using H2 as the reductant.
3 mg catalyst.
|
1 |
20%-γ-Fe2O3/h-MCM-400-15 |
Ethanol |
80 |
72.40 |
100 |
2 |
20%-γ-Fe2O3/h-MCM-500-15 |
Ethanol |
80 |
100 |
100 |
3 |
20%-γ-Fe2O3/h-MCM-600-15 |
Ethanol |
80 |
90.36 |
100 |
4 |
20%-γ-Fe2O3/h-MCM-700-15 |
Ethanol |
80 |
36.42 |
99.9 |
5 |
20%-γ-Fe2O3/h-MCM-500-30 |
Ethanol |
80 |
97.21 |
100 |
6 |
20%-γ-Fe2O3/h-MCM-500-60 |
Ethanol |
80 |
99.97 |
100 |
7 |
12%-γ-Fe2O3/h-MCM-500-15 |
Ethanol |
80 |
58.66 |
100 |
8 |
6%-γ-Fe2O3/h-MCM-500-15 |
Ethanol |
80 |
34 |
100 |
9b |
20%-γ-Fe2O3/h-MCM-500-15 |
Ethanol |
80 |
0 |
0 |
10 |
h-MCM |
Ethanol |
80 |
0.42 |
100 |
11c |
α-Fe2O3 |
Ethanol |
80 |
0.18 |
100 |
12c |
Fe3O4 |
Ethanol |
80 |
11.40 |
99.6 |
13 |
20%-γ-Fe2O3/h-MCM-500-15 |
H2O |
80 |
95.19 |
100 |
14 |
20%-γ-Fe2O3/h-MCM-500-15 |
Ethyl acetate |
80 |
24.77 |
100 |
15 |
20%-γ-Fe2O3/h-MCM-500-15 |
Cyclohexane |
80 |
99.9 |
100 |
16 |
20%-γ-Fe2O3/h-MCM-500-15 |
Ethanol |
20 |
1.54 |
100 |
17 |
20%-γ-Fe2O3/h-MCM-500-15 |
Ethanol |
40 |
3.12 |
100 |
18 |
20%-γ-Fe2O3/h-MCM-500-15 |
Ethanol |
60 |
40.74 |
100 |
19 |
None |
Ethanol |
80 |
0.48 |
100 |
The reaction mechanism for the reduction of nitrobenzene is described as follows: first, the reactant nitrobenzene and N2H4·H2O were absorbed into the mesopores of h-MCM and then attached on the surface of γ-Fe2O3 NPs. As N2H4·H2O is a two-electron reducing agent, when it comes into contact with γ-Fe2O3 NPs, it rapidly reduces Fe3+ to Fe2+, subsequently transferring the electron to nitrobenzene. Then, nitrobenzene is hydrogenated to nitrosobenzene, followed by rapid conversion to phenylhydroxylamine. These two reaction processes are rapid; thus, the intermediates cannot be detected. Finally, the intermediates are directly transformed to the final aniline product, which is considered to be the rate-determining step.28,35,36
With the optimized reaction conditions (1 mmol of nitroarene, 10 mg of the 20%-γ-Fe2O3/h-MCM-500-15 catalyst, 4 mmol of hydrazine hydrate, refluxed at 80 °C), the general applicability for the γ-Fe2O3/h-MCM catalytic reduction of nitroarenes was further investigated. Table 3 summarizes the results obtained from the catalytic reduction of the substituted nitroarenes; most of the corresponding substituted aromatic amines were obtained with high conversion and almost 100% selectivity. Methyl-substituted nitrobenzenes (Table 3, entries 2 and 3) afforded a conversion of greater than 92% and a quantitative selectivity of 100%. Other functional groups, such as phenolic hydroxyl and amino (Table 3, entries 4–9), almost did not affect the reduction of the nitro group, affording the corresponding aryl amines with high yields. However, as can be observed in entry 8, a yield of 93.7% was observed in 10 h, probably attributed to the ortho-position effect of the amino group. As shown in entries 10 and 11 of Table 3, Cl- and Br-substituted nitroarenes were effectively reduced to the corresponding chloroaniline and bromoaniline without obvious dehalogenation; this is very interesting because haloaromatic amines are very important chemical intermediates widely used in the synthesis of herbicides, dyes, drugs, and pesticides.37–39 Although noble-metal-based catalysts, such as Pd catalysts, exhibit high activity, dehalogenation always accompanies catalytic reduction.39,40 In entry 12, the nitroarene with the reducible functional ketone group exhibited a high selectivity of 100%, affording the only product without the reduction of the ketone group. Therefore, the results listed in entries 10–12 further highlight the chemoselectivity of the 20%-γ-Fe2O3/h-MCM-500-15 nanocatalyst, which exhibits remarkable advantages as compared to those of noble metal-based catalysts. The hydrogenation of nitroindoline (Table 3, entry 14) only afforded a conversion of 77.61%, probably attributed to the electronic effect of the pyrryl group. Nitrobenzene containing a sulfanilamide group was completely hydrogenated in 2 h (Table 3, entry 15). From the above results, the hydrogenation of nitroarenes using the γ-Fe2O3/h-MCM catalyst affords the corresponding anilines with high conversion and excellent selectivity near 100%, demonstrating the industrial application of γ-Fe2O3-based catalysts for the chemoselective reduction of nitroarenes.
Table 3 Hydrogenation of various nitroarenes using 20%-γ-Fe2O3/h-MCM-500-15 nanocatalyst
The reusability of the prepared catalyst is also a very important factor for an industrial catalyst. Thus, the recyclability of the nanocatalyst 20%-γ-Fe2O3/h-MCM-500-15 that was detailedly investigated in this work was further evaluated. Because the 20%-γ-Fe2O3/h-MCM-500-15 exhibits superparamagnetic properties, it can be easily separated from the reaction mixture using an external magnet and after being thoroughly washed with water and ethanol, the recovered catalyst was reused in the next catalytic cycle. As displayed in Fig. 6a, the 20%-γ-Fe2O3/h-MCM-500-15 nanocatalyst can be reused for at least five cycles in the catalytic hydrogenation of nitrobenzene to aniline with the conversion almost not decreased and the selectivity maintained at 100%. In addition, the morphology of the 20%-γ-Fe2O3/h-MCM-500-15 nanocatalyst used five runs almost unchanged and the γ-Fe2O3 NPs were still highly dispersed on the h-MCM support as shown in Fig. 6b. The above results indicated the excellent catalytic activity and stability of the 20%-γ-Fe2O3/h-MCM-500-15 nanocatalyst upon reuse.
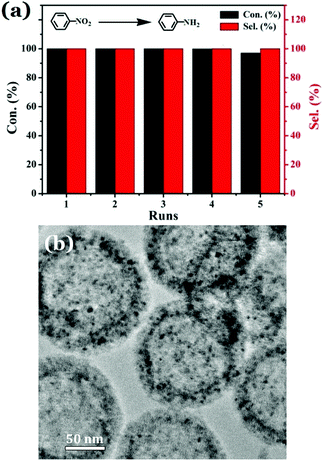 |
| Fig. 6 The reusability of the 20%-γ-Fe2O3/h-MCM-500-15 for catalytic hydrogenation of nitrobenzene to aniline (a), and the TEM image of the 20%-γ-Fe2O3/h-MCM-500-15 used after five cycles (b). | |
Conclusions
In summary, a γ-Fe2O3 NP-modified h-MCM nanocatalyst was prepared by the calcination of Fe(NO3)3-absorbed h-MCM under N2, and its catalytic performance for the hydrogenation of aromatic nitro compounds was investigated. The nanocatalyst annealed at 500 °C for 15 min (20%-γ-Fe2O3/h-MCM-500-15) exhibited high catalytic activity, attributed to the highly dispersed γ-Fe2O3 extremely tiny particles and the specific mesostructured h-MCM support. The 20%-γ-Fe2O3/h-MCM-500-15 nanocatalyst used for the hydrogenation of nitroarenes exhibited high conversion as well as 100% selectivity for aniline; in addition, this catalyst could be easily recovered and reused for at least five cycles, thereby demonstrating promise and significant potential for the use of non-precious metal catalysts in green chemistry.
Acknowledgements
We acknowledge the financial support from the Fundamental Research Funds for the Central Universities (lzujbky-2015-14 and lzujbky-2015-21) and the NSFC (Grant 21301082).
Notes and references
- M. N. Pahalagedara, L. R. Pahalagedara, J. He, R. Miao, B. Gottlieb, D. Rathnayake and S. L. Suib, J. Catal., 2016, 336, 41–48 CrossRef CAS.
- W.-J. Liu, K. Tian and H. Jiang, Green Chem., 2015, 17, 821–826 RSC.
- M. Tumma and R. Srivastava, Catal. Commun., 2013, 37, 64–68 CrossRef CAS.
- N. V. Sidgwick and H. E. Rubie, J. Chem. Soc. Trans., 1921, 119, 1013–1024 RSC.
- H. H. Hodgson, J. Soc. Dyers Colour., 1926, 42, 76–80 CrossRef CAS.
- S. Byun, Y. Song and B. M. Kim, ACS Appl. Mater. Interfaces, 2016, 8, 14637–14647 CAS.
- O. Beswick, D. Lamey, F. Muriset, T. LaGrange, L. Oberson, S. Yoon, E. Sulman, P. J. Dyson and L. Kiwi-Minsker, Catal. Today, 2016, 273, 244–251 CrossRef CAS.
- O. Verho, K. P. J. Gustafson, A. Nagendiran, C.-W. Tai and J.-E. Bäckvall, ChemCatChem, 2014, 6, 3153–3159 CrossRef CAS.
- S. Zhang, C.-R. Chang, Z.-Q. Huang, J. Li, Z. Wu, Y. Ma, Z. Zhang, Y. Wang and Y. Qu, J. Am. Chem. Soc., 2016, 138, 2629–2637 CrossRef CAS PubMed.
- G. Fan and Y. Wang, Synth. React. Inorg. Met.-Org. Chem., 2014, 44, 967–973 CrossRef CAS.
- Z. Wei, J. Wang, S. Mao, D. Su, H. Jin, Y. Wang, F. Xu, H. Li and Y. Wang, ACS Catal., 2015, 5, 4783–4789 CrossRef CAS.
- T. Wang, Z. Dong, T. Fu, Y. Zhao, T. Wang, Y. Wang, Y. Chen, B. Han and W. Ding, Chem. Commun., 2015, 51, 17712–17715 RSC.
- H. D. Burge, D. J. Collins and B. H. Davis, Ind. Eng. Chem. Prod. Res. Dev., 1980, 19, 389–391 CrossRef CAS.
- S. K. Das, M. K. Bhunia, D. Chakraborty, A. R. Khuda-Bukhsh and A. Bhaumik, Chem. Commun., 2012, 48, 2891–2893 RSC.
- Y. Chen, H.-R. Chen and J.-L. Shi, Acc. Chem. Res., 2014, 47, 125–137 CrossRef CAS PubMed.
- Q. Liang, H. Su, J. Yan, C. Leung, S. Cao and D. Yuan, Chin. J. Catal., 2014, 35, 1078–1083 CrossRef CAS.
- W. Zuo, G. Yu and Z. Dong, RSC Adv., 2016, 6, 11749–11753 RSC.
- H. N. Pham, J. J. Sattler, B. M. Weckhuysen and A. K. Datye, ACS Catal., 2016, 6, 2257–2264 CrossRef CAS PubMed.
- W. Zhang, X.-J. Lin, Y.-G. Sun, D.-S. Bin, A.-M. Cao and L.-J. Wan, ACS Appl. Mater. Interfaces, 2015, 7, 27031–27034 CAS.
- D. Munz, D. Wang, M. M. Moyer, M. S. Webster-Gardiner, P. Kunal, D. Watts, B. G. Trewyn, A. N. Vedernikov and T. B. Gunnoe, ACS Catal., 2016, 6, 4584–4593 CrossRef CAS.
- S. Guo, Y. Yang, N. Liu, S. Qiao, H. Huang, Y. Liu and Z. Kang, Sci. Bull., 2016, 61, 68–77 CrossRef CAS.
- S. Yang, L. Peng, P. Huang, X. Wang, Y. Sun, C. Cao and W. Song, Angew. Chem., Int. Ed., 2016, 55, 4016–4020 CrossRef CAS PubMed.
- T. Liu, L. Qu, K. Qian, J. Liu, Q. Zhang, L. Liu and S. Liu, Chem. Commun., 2016, 52, 1709–1712 RSC.
- Q. Huang, S. Wang, Y. Zhang, B. Yu, L. Hou, G. Su, S. Ma, J. Zou and H. Huang, J. Phys. Chem. C, 2016, 120, 3139–3144 CAS.
- H. Zhang, M. Yu, H. Song, O. Noonan, J. Zhang, Y. Yang, L. Zhou and C. Yu, Chem. Mater., 2015, 27, 6297–6304 CrossRef CAS.
- J. Hou, T. Cao, F. Idrees and C. Cao, Nanoscale, 2016, 8, 451–457 RSC.
- R. V. Jagadeesh, A.-E. Surkus, H. Junge, M.-M. Pohl, J. Radnik, J. Rabeah, H. Huan, V. Schuenemann, A. Brueckner and M. Beller, Science, 2013, 342, 1073–1076 CrossRef CAS PubMed.
- I. T. Papadas, S. Fountoulaki, I. N. Lykakis and G. S. Armatas, Chem. – Eur. J., 2016, 22, 4600–4607 CrossRef CAS PubMed.
- Z. Dong, X. Le, Y. Liu, C. Dong and J. Ma, J. Mater. Chem. A, 2014, 2, 18775–18785 CAS.
- R. Liu, J.-F. Liu, L.-Q. Zhang, J.-F. Sun and G.-B. Jiang, J. Mater. Chem. A, 2016, 4, 7606–7614 CAS.
- Z. Zhao, Y. Dai, J. Lin and G. Wang, Chem. Mater., 2014, 26, 3151–3161 CrossRef CAS.
- Z. X. Yan, G. Q. He, G. H. Zhang, H. Meng and P. K. Shen, Int. J. Hydrogen Energy, 2010, 35, 3263–3269 CrossRef CAS.
- Z. Sun, Q. Yue, Y. Liu, J. Wei, B. Li, S. Kaliaguine, Y. Deng, Z. Wu and D. Zhao, J. Mater. Chem. A, 2014, 2, 18322–18328 CAS.
- Y. Deng, D. Qi, C. Deng, X. Zhang and D. Zhao, J. Am. Chem. Soc., 2008, 130, 28–29 CrossRef CAS PubMed.
- O. Beswick, I. Yuranov, D. T. L. Alexander and L. Kiwi-Minsker, Catal. Today, 2015, 249, 45–51 CrossRef CAS.
- Y. Li, Y.-X. Zhou, X. Ma and H.-L. Jiang, Chem. Commun., 2016, 52, 4199–4202 RSC.
- T. Fu, P. Hu, T. Wang, Z. Dong, N. Xue, L. Peng, X. Guo and W. Ding, Chin. J. Catal., 2015, 36, 2030–2035 CrossRef CAS.
- Y. Wang, Y. Yang, Y. Li, J. Lai and K. Sun, Catal. Commun., 2012, 19, 110–114 CrossRef CAS.
- Q. Wei, Y.-S. Shi, K.-Q. Sun and B.-Q. Xu, Chem. Commun., 2016, 52, 3026–3029 RSC.
- A. H. Pizarro, C. B. Molina, J. A. Casas and J. J. Rodriguez, Appl. Catal., B, 2014, 158–159, 175–181 CrossRef CAS.
|
This journal is © the Partner Organisations 2016 |
Click here to see how this site uses Cookies. View our privacy policy here.