DOI:
10.1039/C5QI00215J
(Research Article)
Inorg. Chem. Front., 2016,
3, 645-650
Flattening sol–gel nanospheres into a carbon sheet-intercalated cobalt/carbon/cobalt sandwich-nanostructure †
Received
26th October 2015
, Accepted 1st February 2016
First published on 3rd February 2016
Abstract
It is known that carbon layer intercalation can reduce and even avoid the breakdown of matrix material induced by expansion in hydrogen storage processes. Herein, we provide a general strategy to synthesize a uniform cobalt/carbon/cobalt sandwich-like nanosheet stack (denoted as Co/C/Co), which is difficult to achieve using conventional one-pot synthetic methods. In this strategy, sol–gel nanospheres covered with cobaltII–cobaltIII layered double hydroxide (CoII–CoIII–LDH) were firstly constructed and used as a precursor. After a simple post-treatment the sandwich-nanostructures were successfully obtained, which display an extra high capacity, excellent high-rate capability, and long cycle life. Distinct from the most common structures of carbon-based composites (mixed, wrapped, or anchored models), the resultant materials display a uniform sandwich-like configuration: few-layer carbon sheets conformably intercalate cobalt nanoparticles. This facile strategy can be easily extended to design other metal/carbon/metal sandwich-like nanomaterials.
Introduction
Since the first report in 2004 about an isolated two-dimensional (2D) carbon crystal or graphene (GR) with a single atom thickness,1 an avalanche of research has followed due to its outstanding optical, electronic, and mechanical properties.2 Along with this, attempts to functionalize, decorate, and dope 2D carbon have also led to an increased interest in a large number of modification techniques.3 More specifically, the preparation of 2D carbon-intercalated structures is a topic of great interest to those in catalysis and energy research areas, which has prompted the development of advanced graphene based materials for energy applications, including supercapacitors, batteries, and fuel cells.4 However due to their large lattice mismatch and lack of chemical interactions, there is a substantial interfacial energy between them. Thus, when depositing a selected object on the surface of a carbon sheet, it often tends to grow only at defect sites and prefers to form a discontinuous island-like domain to minimize the unfavorable interfaces.5 Therefore, the formation of a continuous and conformable layer-by-layer structure based on carbon nanosheets remains a great challenge and is highly desirable. Recently, a “2D chemistry” concept has been presented as a new aspect for the fabrication of layer-by-layer carbon structures. For example, easily treatable liquid exfoliated GR and reduced graphene oxide (rGO) are used to support the deposition of noble metals at an organic–water interface, which has been investigated to prepare graphene-based catalysts and electrode materials.6 However, this method also does not resolve the above problem about their interfaces. Enlightened by the “2D chemistry” method, a new suggestion for the preparation of decorated carbon nanosheets with a continuous and conformable coverage shell is provided by us in this work: flattening sol–gel hollow nanospheres into carbon sheet-intercalated sandwich-nanostructures. This avoids the collapsing effect often induced by thermal pyrolysis and carbonization processes if a lamellar sol–gel precursor is directly heat treated, which will only result in the formation of a layered composite, not a sandwich structure. Fortunately, the above suggestion is realized by us through a detailed chemical design, in which cobalt/carbon/cobalt (Co/C/Co) sandwich nanostructures are obtained and display satisfactory electrochemical hydrogen storage properties. Firstly, an oil/water sol–gel system containing sphere-like droplets is constructed using cyclohexane as an oil component, Triton X-100 (TX-100, polyoxyethylene octylphenyl ether) as a hydroxyl surfactant and n-butyl alcohol as a co-surfactant. After that, layered double hydroxide (LDH) cobalt compounds are introduced, which assemble onto the droplets through interactions between its own hydroxyl groups and the surfactant. The above two steps are from the previous literature.7 Later, the oil component of cyclohexane in the droplets is removed through forceful centrifugation treatment, resulting in the formation of a carbonaceous sandwich precursor. Finally, through a controlled annealing process a carbon sheet-intercalated cobalt sandwich-structure is obtained, assisted by the deoxidizing effect of carbon.
We report here a general strategy to synthesize uniform cobalt/carbon/cobalt sandwich-like nanosheets (denoted as Co/C/Co). The process for the fabrication of superposed CoII–CoIII–LDH precursor with a hierarchical structure is schematically illustrated in Scheme 1.
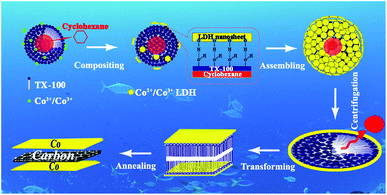 |
| Scheme 1 Schematic illustration of the fabrication procedure of the carbon nanosheet-intercalated metal sandwich-structure. | |
Results and discussion
Structure, morphology and composition of the precursor
Firstly, cyclohexane oil droplets were well dispersed in a continuous aqueous phase containing Triton X-100 (TX-100, polyoxyethylene octylphenyl ether) surfactant. Later, cobalt nitrate and hydrogen peroxide were dissolved in the aqueous phase. It is found that its zeta potential value is around +28.2 mV (Fig. S1†), confirming that Co2+ is well-distributed on the surfaces of the surfactant. After ammonia solution was added, LDH nanosheets formed and were deposited and adsorbed on the surfaces of the oil droplets through hydrogen bonding interactions between the hydroxyl groups in TX-100 and those in CoII–CoIII–LDH (Fig. S2a† inset). On increasing the amount of ammonia solution, more and more LDH crystallites are adsorbed onto the oil droplet surfaces and assemble as an outer shell, which is hydrogen bonded to the inner shell. At the same time, our dynamic light scattering (DLS) measurements confirmed that the diameter of the spheres changed from 163 nm to 346 nm, as shown in Fig. S2a,† which means that the thicknesses of the CoII–CoIII–LDH layers are variable. This phenomenon was also observed in the literature.7 The composition of the LDH is also confirmed by its corresponding XRD measurements (Fig. S2b†), which agree well with the reported literature.7
Next, by high speed centrifugation, the oil phase (cyclohexane) is divided by means of its different density compared with that of LDH. As shown in Fig. 1a, a large number of superposed lamellar nano-architectures with a diameter of about 450 nm are obtained. Its typical cross-section scanning electron microscopy (SEM) image (Fig. 1a inset) shows that a nanoplate is composed of three layers (sandwich-like structure) and the thickness of a single layer is around 10 nm. This special sandwich-like structure is very different from that reported in the literature7 due to the distinct post-treatment of the collected composite precursor in the experiment, in which the composite precursor is only centrifuged, without being washed with any reagent. The above post-treatment avoids the destruction of the layered composite and ensures the formation of the lamellar sandwich structure from the previous sphere-like structure. Transmission electron microscopy (TEM) examination further demonstrates the above result. As shown in Fig. 1b, it is clearly observed that a nanoplate contains different layers. Its related high-resolution transmission electron microscopy (HRTEM) image (Fig. 1b inset) displays the (110) plane of CoII–CoIII–LDH, as is expected if its (001) planes are parallel to the nanoplate surface. The Fourier transform infrared (FT-IR) spectrum of the CoII–CoIII–LDH precursors (Fig. 1c) shows a very intense absorption band at 1384 cm−1, corresponding to the absorption peak of intercalated nitrate anions. A broad absorption peak centered at ca. 3380 cm−1 can be assigned to the stretching mode of hydrogen-bonded hydroxyl groups, demonstrating the strong stability of the composite. In addition, the Brunauer–Emmett–Teller (BET) area of the precursors is 40.8 m2 g−1, as shown in Fig. 1d.
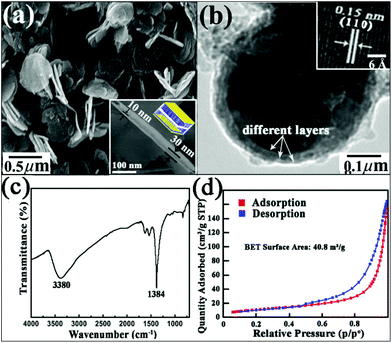 |
| Fig. 1 (a) SEM image of the resulting sample after high speed centrifugation, the inset is the sample's high-resolution cross-section view; (b) TEM image of the resulting sample, the inset is its corresponding HRTEM image. (c) FT-IR spectrum and (d) N2 adsorption/desorption isotherm of the superposed CoII–CoIII–LDH precursors. | |
Structure, morphology and composition of the Co/C/Co sandwich-nanostructure
Using the residual surfactant as a carbon source, the sandwich-nanostructured precursor was reduced to its Co/C/Co counterpart. Through a series of detailed comparison experiments, it is found that in order to avoid the formation of cobalt oxides, a vacuum atmosphere is critical. As shown in Fig. S3 and Table S1,† under an Ar gas atmosphere cobalt oxide always exists. In contrast, under a vacuum atmosphere the precursor is transformed into pure face-centered cubic (fcc) cobalt and amorphous carbon at 700 °C, as shown in Fig. S4 and Table S1.† The carbon content in the product is about 9.2 wt%, as indicated by its ICP-AES result. The change from the surfactant to carbon sheets has been proved by FT-IR analysis. As shown in Fig. S5,† the FT-IR spectrum of the resultant Co/C/Co displays a peak at 1370 cm−1 due to the plane vibrations of CH and two peaks at 1570 and 3425 cm−1 deriving from the hydroxyl groups. Compared with that of the superposed CoII–CoIII–LDH precursors, it is obvious that the surfactant TX-100 has been transformed into carbon-based material. The changes of its composition and structure have also been confirmed by X-ray photoelectron spectroscopy (XPS) and Raman measurements. As shown in Fig. S6a and b,† a C 1s peak at 284.6 eV originates from the sp2-hybridized carbon bond and the Co 2p peaks at 779.2 and 795.5 eV assigned to metallic cobalt8,9 are observed. The state of carbon in the product was further studied by Raman examinations. As shown in Fig. S6c,† three prominent peaks located at 1344 cm−1 (D-band), 1570 cm−1 (G-band) and 2688 cm−1 (2D-band) are observed, which correspond to the breathing modes of rings and the E2g phonon of sp2-bonded carbon atoms in a two-dimensional hexagonal lattice, respectively.10 Both XPS and Raman results again confirm the process of carbon sheet formation from the surfactant. Furthermore, it is generally accepted that the character of a hierarchical porous structure has a great influence on its performance in energy storage. Thus, the hierarchically structured Co/C/Co was collected for N2 adsorption/desorption isotherm measurement. The corresponding result (Fig. S6d†) displays a desorption hysteresis loop (H3 type). According to the International Union of Pure and Applied Chemistry (IUPAC) classification, this is often observed for aggregates of plate-like particles giving rise to slit-shaped pores.11 By the calculation of single point surface area at p/p° = 0.30, a relatively high BET specific surface area (SSA) of 160.4 m2 g−1 is also obtained. The Barrett–Joyner–Halenda (BJH) pore size distribution plot calculated from desorption branch is shown in the inset of Fig. S6d,† which indicates that the Co/C/Co sandwich-nanostructure has both micropores and mesopores, which are attributed to the porous carbon nanosheets intercalated and slit-shaped pores between the multiple Co/C/Co architecture, respectively. The large surface area and rich porosity of the hierarchical porous Co/C/Co sandwich-nanostructure should make it a good candidate as an electrochemical hydrogen storage material, considering metal cobalt to be a potential hydrogen storage material.
The hierarchical nanostructures have been further confirmed using TEM, HRTEM, SAED, SEM and EELS examinations. The TEM results (Fig. 2a and b) and the high-power SEM microscopy images (Fig. 2c and d) of the nanostructures confirm that the hierarchical structure is a sandwich-like one. Now, all the above results prove that the design for a Co/C/Co sandwich-nanostructure in Scheme 1 has been realized. As shown in Fig. 2b, the (111) lattice plane of fcc-Co and (002) lattice plane of carbon intercalated are clearly observed. In addition, it is found that the carbon layer is about 1.5 nm thick and composed of 5 carbon layers. SAED measurements indicate that the cobalt counterpart in a Co/C/Co nanoparticle is polycrystalline, as shown in the inset of Fig. 2b. Its SEM image (Fig. 2c) also exhibits a sandwich-structure with a 25 nm diameter, in which the EELS curve demonstrates the composition of the sandwich-structure and that Co and C elements take up its whole region. The presence of carbon nanosheet intercalation not only strengthens the hierarchical structure, but also prevents the nanoparticles from complete agglomeration, leaving large interspaces between them, which provide abundant diffusion channels for guest molecules.
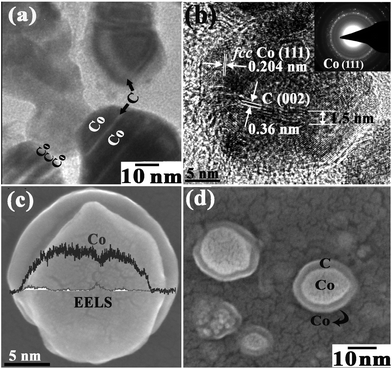 |
| Fig. 2 (a) and (b) Typical TEM and HRTEM images of the Co/C/Co sandwich nanostructure, the inset in (b) is its corresponding SAED image. (c) and (d) SEM images of the as-obtained nanoparticles, the inset curve in (c) is the EELS results for Co and C elements. | |
Electrochemical hydrogen storage properties
To further investigate the hydrogen storage ability of the Co/C/Co sandwich-nanostructure, its electrochemical hydrogen storage capacity at 30 mA g−1 current density was firstly tested, as shown in Fig. 3a. In the charging process, one charge plateau appears at about 1.36 V, which can be ascribed to the reaction of Co/C/Co → Co/C/Co − Hx, similar to that reported in the literature.12,13 At the same time, a mass of gas bubbles were also observed in our experiments. All of the above phenomena prove the production of hydrogen in the electrochemical process. In the discharge curve, two obvious plateaus are observed at 1.20 V and 0.43 V, which suggests that different hydrogen desorption sites exist in the product. Lower discharge plateaus that appear at about 0.43 V should be attributed to the desorption of hydrogen adsorbed on the surface of the nanocomposite, which has been pointed out in the literature.14,15 The discharge plateau that appears at about 1.20 V is comparable to that of other Co based alloys,16 which is due to the reaction of Co/C/Co − Hx → Co/C/Co. It is also noted that the balanced lengths of both charge and discharge plateaus indicate the excellent reversibility and columbic efficiency of the electrode. Furthermore, the cycling performance demonstrates that the as-prepared Co/C/Co sandwich-nanostructure has satisfactory stability as an electrochemical hydrogen storage material. Fig. 3b shows the cycling stability of the product at a discharge current density of 30 mA g−1. It is clear that the composite achieves a maximum discharge capacity as high as 786 mA h g−1 (2.88 wt% hydrogen), which is about 1.82 times that of pure Co nanoparticles17 and close to the theoretical hydrogen storage capacity of individual metal Co.17 Importantly, even after 50 cycles, the discharge capacity still remains at 667 mA h g−1 (2.44 wt% hydrogen). Compared with traditional AB5 type,18,19 AB2 type,20 AB type21 and Mg-based alloy22,23 hydrogen storage materials, the as-prepared Co/C/Co sandwich-nanostructure displays a much higher discharge capacity and cycling stability, which is due to the fact that the intercalated carbon sheets tightly envelop the Co nanoparticles to protect and restrict them just like a three-layered sandwich. Also, the carbon sheets act as a buffer layer to conveniently allow bypassing of nanostructure collapse that would inevitably arise in the hydrogen absorption/desorption process. Our observation of the maintained nanostructure after hydrogen absorption/desorption cycles demonstrates the above point. Additionally, the Co/C/Co sandwich-nanostructure also exhibits good electrochemical hydrogen storage performance at high current densities. To further test its cyclability under various high rates, discharge capacities versus current densities from 30 to 1000 mA g−1 are examined. As shown in Fig. 3b, the discharging capacity varies from 786 to 636.7 mA h g−1. The discharging capacity curves still maintain satisfactory kinetic features at high rates, indicating a facile charge transport process. Notably, the retention of the as-obtained nanocomposites is up to 95% at a hydrogen discharge density of 200 mA g−1, which is much higher than the previous results.24
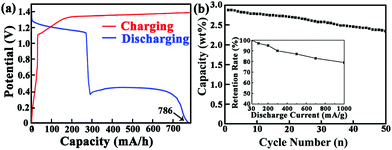 |
| Fig. 3 (a) Electrochemical hydrogen storage charge–discharge curves of the as-obtained product at a current density of 30 mA g−1; (b) cycling performance and retention rate at various hydrogen discharge densities of the Co/C/Co sandwich-nanostructure. | |
We attribute the excellent hydrogen storage performance of the product to its unique hierarchical architecture. Firstly, in the as-obtained open hierarchical structure, the interlayer spacing between the layers can be easily filled with electrolyte, ensuring that a high amount of the surface area comes into effective contact with the electrolyte, facilitating transportation of a large flux of hydrogen storage. Secondly, the porous sandwich-nanostructure offers a very short effective diffusion distance for hydrogen, resulting in an enhanced rate performance. Thirdly, the thin carbon layers, as a conducting coating on cobalt nanoparticles, not only significantly enhance the electrical conductivity of the material, but also supply continuous conductive paths between Co particles and carbon sheets. Last but not least, each of the spaces between the carbon sheets, provide elastic buffer spaces to accommodate the volume changes during hydrogen insertion and extraction, which contribute to excellent cyclability and high rate retention ability.
Finally, a cyclic voltammogram curve (CV) was recorded to further investigate the electrochemical hydrogen adsorption–desorption behavior of the product, as shown in Fig. S7.† The main CV feature of the sample shows two remarkable anodic current peaks, which is different from the results of previous reports where only one pair of peaks was exhibited.25 In the reversed scan, two strong oxidation peaks are centered at −0.96 V and −0.20 V, which are far from the equilibrium potentials of pure Co and carbon materials.26,27 The potential position and features of the anodic peak at −0.96 V agree with the discharge potential at 1.2 V, which belongs to the electrochemical oxidation of hydrogen in the crystal lattice, as reported in the literature.27–29 The current peak appearing at about −0.20 V is comparable to the discharge plateau at 0.43 V in the hydrogen desorption process, which is due to the electrochemical oxidation of hydrogen adsorbed on the surface of the electrode material and frequently observed for the electrochemical hydrogen storage electrodes.30,31 So the reversible CV peaks observed here are ascribed to the quasi-reversible electrochemical reaction:
Co/C/Co + xH2O + xe− ↔ Co/C/Co − Hx + xOH− |
Conclusions
In summary, we demonstrate a general strategy for the synthesis of metal/carbon/metal sandwich-like nanoparticles, which can avoid the substantial interfacial tensions that would be inevitably engendered by the direct growth of metal nanoparticles on carbon sheet. The as-prepared Co/C/Co sandwich-nanostructures show a high capacity, an excellent rate capability and good cycling stability as anticipated by us.
Experimental section
Synthesis of the CoII–CoIII–LDH precursor
The O/W emulsion consisted of cyclohexane (5 mL), TX-100 surfactant (20 mL) and n-butyl alcohol co-surfactant (10 mL) as the oil phase, and water (250 mL). The mixture was vigorously stirred and 0.01 mol of Co(NO3)2·6H2O and hydrogen peroxide solution (1 mL, 30%) were dissolved in the water phase. Then, with a stirring speed of 60 rpm, 10 wt% ammonia aqueous solution was added into the emulsion at a rate of 4 mL min−1 to a give a pH value of 9.5. The reaction was allowed to proceed at ambient temperature for 9 hours (h), after which the suspension was centrifuged and collected. For subsequent characterization, the product was washed with double distilled water and ethanol and then dried at 60 °C for 10 h.
Synthesis of the Co/C/Co sandwich-structure
The unwashed composite precursor (containing residual surfactant) was collected and calcinated at 700 °C for 4 h in a vacuum atmosphere. This treatment ensured that the surfactant was decomposed and carbonized to amorphous carbon.
Characterization
The crystallographic structures of the materials were determined using a powder XRD system (TTR-III, Japan) equipped with Cu Kα radiation (λ = 0.15406 nm). A scan rate of 10° min−1 was used to record the patterns in the range of 10–70°. The products were observed under a SU8000 cold emission field scanning electron microanalyser (Hitachi, Japan) operated at 10 kV to examine their microstructures. Transmission electron microscope (TEM) images and high-resolution transmission electron microscopic (HRTEM) images of the nanostructures were taken using a JEOL HRTEM (JEM2010 electron microscope) at a 200 kV accelerating voltage. Fourier transform infrared (FT-IR) spectra were recorded with 2 cm−1 spectral resolution using a PerkinElmer Spotlight spectrometer. Dynamic light scattering (DLS) and zeta potential measurements were performed using a Malvern Zetasizer NS90 equipped with a He/Ne laser (633 nm wavelength). Furthermore, N2 adsorption/desorption measurements were measured at the temperature of liquid nitrogen (77 K) using a Micromeritics ASAP 3020 instrument. The specific surface area was calculated by the Brunauer–Emmett–Teller (BET) method. The X-ray photoelectron spectroscopy (XPS) measurements were performed using a PHI 5700 ESCA system with a monochromatic Al-Kα (1486.6 eV) radiation source and a hemisphere detector. Moreover, in order to determine Co and C element content in the composites, 0.1 M HNO3 was used to dissolve the composites and their dissolved solutions were filtered and analyzed using inductive coupled plasma atomic emission spectrometry (ICP-AES) measurements (Thermo Elemental, IRIS Intrepid II XSP).
Electrochemical hydrogen storage measurements
The hydrogen charge and discharge curves were measured in a two-electrode test cell using a LAND battery test instrument (CT2001A), which contains one positive electrode and one negative electrode, and the electrolyte was 6 M KOH aqueous solution. The negative electrode was composed of 85 wt% of the as-obtained powder and 10 wt% acetylene black. The positive electrode material consisted of 80 wt% nickel hydroxide and 15 wt% Co. Each of the positive and negative electrode materials were mixed with 5 wt% PTFE and coated on 1 cm2 Ni-foam. The electrode plates were pressed at a pressure of 50 kg cm−2 for 30 s. CV measurements were performed using an electrochemical workstation (CHI 660E) of a three-electrode test cell. The cell consisted of the as-obtained compound as the working electrode, a metal platinum gauze as the counter electrode and a Hg/Hg2Cl2 electrode as the reference electrode, and the electrolyte was 6 M KOH. The scan range was between −1.2 V and 0 V vs. Hg/Hg2Cl2, and the scan started from the open circuit potential and then along the negative direction at a scan rate of 10 mV s−1.
Acknowledgements
We thank the Program for NCET in University (NCET-13-0754), the Natural Science Foundation of China (Grant No. 51272050 and 51072038), the fundamental research funds for the central universities (No. HEUCF2016), Harbin Sci-tech innovation foundation (RC2012XK017012), Harbin Youth Fund (RC2014QN017004), Youth Fund of Heilongjiang Province (QC2014C006), and the Open Project Program of Key Laboratory for Photonic and Electric Bandgap Materials, Ministry of Education, Harbin Normal University (PEBM201301) for the financial support of this research.
Notes and references
- K. S. Novoselov, A. K. Geim, S. V. Morozov, D. Jiang, Y. Zhang, S. V. Dubonos, I. V. Grigorieva and A. A. Firsov, Science, 2004, 30, 666 CrossRef PubMed.
-
(a) I. Vlassiouk, S. Smirnov, I. Ivanov, P. F. Fulvio, S. Dai, H. Meyer, M. Chi, D. Hensley, P. Datskos and N. V. Lavrik, Nanotechnology, 2011, 22, 1 CrossRef PubMed;
(b) C. M. Weber, D. M. Eisele, J. P. Rabe, Y. Liang, X. Feng, L. Zhi, K. Mullen, J. L. Lyon, R. Williams, D. A. Vanden Bout and K. J. Stevenson, Small, 2010, 6, 184 CrossRef CAS PubMed;
(c) K. S. Novoselov, A. K. Geim, S. V. Morozov, D. Jiang, M. I. Katsnelson, I. V. Grigorieva, S. V. Dubono and A. A. Firsov, Nature, 2005, 438, 197 CrossRef CAS PubMed.
-
(a) J. A. Robinson, M. Hollande, M. LaBella, K. A. Trumbull, R. Cavalero and D. W. Snyder, Nano Lett., 2011, 11, 3875 CrossRef CAS PubMed;
(b) A. Mishchenko, J. S. Tu, Y. Cao, R. V. Gorbachev, J. R. Wallbank, M. T. Greenaway, V. E. Morozov, S. V. Morozov, M. J. Zhu, S. L. Wong, F. Withers, C. R. Woods, Y. J. Kim, K. Watanabe, T. Taniguchi, E. E. Vdovin, O. Makarovsky, T. M. Fromhold, V. I. Fal'ko, A. K. Geim, L. Eaves and K. S. Novoselov, Nat. Nanotechnol., 2014, 9, 808 CrossRef CAS PubMed.
-
(a) V. H. Rodrigues de Souza, M. M. Oliveira and A. J. Gorgatti Zarbin, J. Power Sources, 2014, 260, 34 CrossRef CAS;
(b) P. V. Kamat, J. Phys. Chem. Lett., 2010, 1, 520 CrossRef CAS;
(c) J. M. Yuk, K. Kim, B. N. Alemán, W. Regan, J. H. Ryu, J. Park, P. Ercius, H. M. Lee, A. P. Alivisatos, M. F. Crommie, J. Y. Lee and A. Zettl, Nano Lett., 2011, 11, 3290 CrossRef CAS PubMed.
-
(a) X. Huang, X. Y. Qi, F. Boey and H. Zhang, Chem. Soc. Rev., 2012, 41, 666 RSC;
(b) Q. J. Xiang, J. G. Yu and M. Jaroniec, Chem. Soc. Rev., 2012, 41, 782 RSC;
(c) H. L. Wang and H. J. Dai, Chem. Soc. Rev., 2013, 42, 3088 RSC;
(d) Z. S. Wu, G. M. Zhou, L. C. Yin, W. Ren, F. Li and H. M. Cheng, Nano Energy, 2012, 1, 107 CrossRef CAS;
(e) X. Li, W. Qi, D. Mei, M. L. Sushko, I. Aksay and J. Liu, Adv. Mater., 2012, 24, 5136 CrossRef CAS PubMed;
(f) D. H. Wang, R. Kou, D. Choi, Z. G. Yang, Z. M. Nie, J. Li, L. V. Saraf, D. H. Hu, J. G. Zhang, G. L. Graff, J. Liu, M. A. Pope and I. A. Aksay, ACS Nano, 2010, 4, 1587 CrossRef CAS PubMed.
-
(a) S. J. Hoseini, M. Dehghani and H. Nasrabadi, Catal. Sci. Technol., 2014, 4, 1078 RSC;
(b) K. Bramhaiah and N. S. John, RSC Adv., 2013, 3, 7765 RSC;
(c) X. Zan, Z. Fang, J. Wu, F. Xiao, F. Huo and H. Duan, Biosens. Bioelectron., 2013, 49, 71 CrossRef CAS PubMed;
(d) M. M. Gudarzi and F. Sharif, Soft Matter, 2011, 7, 3432 RSC;
(e) S. Biswas and L. T. Drzal, Nano Lett., 2009, 9, 167 CrossRef CAS PubMed;
(f) R. V. Salvatierra, S. H. Domingues, M. M. Oliveira and A. J. G. Zarbin, Carbon, 2013, 57, 410 CrossRef CAS.
- J. Sun, H. M. Liu, X. Chen, D. G. Evans and W. S. Yang, Nanoscale, 2013, 5, 7564 RSC.
- M. C. Biesinger, B. P. Payne, A. P. Grosvenor, L. M. Lau, A. R. Gerson and R. S. C. Smart, Appl. Surf. Sci., 2011, 257, 2717 CrossRef CAS.
- X. A. Li, X. J. Han, Y. C. Du and P. Xu, J. Magn. Magn. Mater., 2011, 323, 14 CrossRef CAS.
- R. J. Tseng, C. O. Baker, B. Shedd, J. X. Huang, R. B. Kaner, J. Y. Ouyang and Y. Yang, Appl. Phys. Lett., 2007, 90, 053101 CrossRef.
- K. S. W. Sing, D. H. Everett, R. A. W. Haul, L. Moscou, R. A. Pierotti and J. Rouquerol, Pure Appl. Chem., 1985, 57, 603 CrossRef CAS.
- Y. L. Cao, W. C. Zhou, X. Y. Li, X. P. Ai, X. P. Gao and H. X. Yang, Electrochim. Acta, 2006, 51, 4285 CrossRef CAS.
- Y. H. Zhang, L. F. Jiao, H. T. Yuan, Y. Y. Zhang, L. Liu and Y. J. Wang, Int. J. Hydrogen Energy, 2008, 33, 1317 CrossRef CAS.
- Z. W. Lu, S. M. Yao, G. R. Li, T. Y. Yan and X. P. Gao, Electrochim. Acta, 2008, 53, 2369 CrossRef CAS.
- G. P. Dai, C. Liu, M. Liu, M. Z. Wang and H. M. Cheng, Nano Lett., 2002, 2, 503 CrossRef CAS.
- D. W. Song, Y. J. Wang, Q. H. Wang, Y. P. Wang, L. F. Jiao and H. T. Yuan, J. Power Sources, 2010, 195, 7115 CrossRef CAS.
- S. R. Chung, K. W. Wang and T. P. Perng, J. Electrochem. Soc., 2006, 153, 1128 CrossRef.
- B. Liao, Y. Q. Lei, L. X. Chen, G. L. Lu, H. G. Pan and Q. D. Wang, J. Power Sources, 2004, 129, 358 CrossRef CAS.
- T. Kohno, H. Yosid and F. Kawashima, J. Alloys Compd., 2000, 311, 5 CrossRef.
- M. Y. Song, D. Ahn, I. H. Kwon and S. H. Chough, J. Electrochem. Soc., 2001, 148, 1041 CrossRef.
- H. Yukawa, Y. Takahashi and M. Morinaga, Mater. Sci., 1999, 14, 291 CAS.
- Q. F. Tian, Y. Zhang, L. X. Sun, F. Xu, Z. C. Tan and H. T. Yuan, J. Power Sources, 2006, 158, 1463 CrossRef CAS.
- W. Liu, Y. Lei, D. Sun, J. Wu and Q. D. Wang, J. Power Sources, 1996, 58, 243 CrossRef CAS.
-
(a) S. Q. Yang, P. Gao, D. Bao, Y. J. Chen, L. Q. Wang, P. P. Yang, G. B. Li and Y. Z. Sun, J. Mater. Chem. A, 2013, 1, 6731 RSC;
(b) D. Bao, P. Gao, X. D. Shen, C. Chang, L. Q. Wang, Y. Wang, Y. J. Chen, X. M. Zhou, S. C. Sun, G. B. Li and P. P. Yang, ACS Appl. Mater. Interfaces, 2014, 6, 2902 CrossRef CAS PubMed;
(c) C. Chang, P. Gao, D. Bao, L. Q. Wang, Y. Wang, Y. J. Chen, X. M. Zhou, S. C. Sun, G. B. Li and P. P. Yang, J. Power Sources, 2014, 255, 318 CrossRef CAS;
(d) Y. J. Chen, Q. S. Wang, C. L. Zhu, P. Gao, Q. Y. Ouyang, T. S. Wang, Y. Ma and C. W. Sun, J. Mater. Chem., 2012, 22, 5924 RSC.
- D. Wang, X. P. Ai and H. X. Yang, Chem. Mater., 2004, 16, 5194 CrossRef.
- W. T. Tan, E. B. Lim and J. K. Goh, J. Solid State Electrochem., 2005, 9, 30 CrossRef CAS.
- Y. Liu, Y. J. Wang, L. L. Xiao, D. W. Song, Y. P. Wang, L. F. Jiao and H. T. Yuan, Electrochim. Acta, 2008, 53, 2265 CrossRef CAS.
- V. Lavrentiev, H. Naramoto, K. Narumi, S. Sakai and P. Avramov, Chem. Phys. Lett., 2006, 423, 366 CrossRef CAS.
- P. Gao, Y. Wang, S. Q. Yang, Y. J. Chen, Z. Xue, L. Q. Wang, G. B. Li and Y. Z. Sun, Int. J. Hydrogen Energy, 2012, 37, 17126 CrossRef CAS.
- S. Sakai, H. Naramoto, P. V. Avramov, T. Yaita, V. Lavrentiev, K. Narumi, Y. Baba and Y. Maeda, Thin Solid Films, 2007, 515, 7758 CrossRef CAS.
- P. Gao, S. Q. Yang, Z. Xue, G. B. Liu, G. L. Zhang, L. Q. Wang, G. B. Li, Y. Z. Sun and Y. J. Chen, J. Alloys Compd., 2012, 539, 90 CrossRef CAS.
Footnote |
† Electronic supplementary information (ESI) available. See DOI: 10.1039/c5qi00215j |
|
This journal is © the Partner Organisations 2016 |
Click here to see how this site uses Cookies. View our privacy policy here.