DOI:
10.1039/C5NJ01717C
(Paper)
New J. Chem., 2016,
40, 320-324
One-step hydrothermal synthesis of photoluminescent carbon nitride dots derived from ionic liquids†
Received
(in Montpellier, France)
2nd July 2015
, Accepted 21st October 2015
First published on 23rd October 2015
Abstract
We present an economical and facile hydrothermal approach to synthesize fluorescent carbon nitride dots (CNDs) derived from ionic liquids. The results suggest that the CNDs thus obtained are highly water-soluble and exhibit a strong fluorescence. The one-step preparation process is simple and effective, neither a strong acid solvent nor surface modification reagent is needed, which makes this approach very suitable for industrial production.
Introduction
Since fluorescent semiconductor quantum dots (QDs) have some unique optical and biochemical properties and several magnificent applications in optoelectronic devices, biological labelling, etc.,1–6 they are considered a popular subject in academic research and various industrial areas. However, the use of heavy metals, which are essential elements in these conventional semiconductors, is restricted because of concerns about their toxicity, stability and environmental hazard.7–9 Therefore, the search for benign nanomaterials with similar optical properties is a critical issue.
Recently a new type of visible emitter, exclusively based on carbon dots (CDs), was reported which had a great impact in health and environmental applications. Also, they were proven to be a kind of promising building block for future nanodevices due to their fascinating photoluminescence and potential as non-toxic replacements for traditional heavy-metal-based quantum dots.10–13 On the other hand, carbon nitride dots (CNDs) have received attention from materials researchers because of their unique characteristics and wide performances in catalysis, sensors, corrosion protection, etc.14,15 Several methods to prepare CDs or CNDs have been reported, such as chemical oxidation of arc-discharge single-walled carbon nanotubes,16 electrochemical oxidation of graphite and multiwalled carbon nanotubes,17,18 laser ablation of graphite,10 separation of combusted carbon soot,19,20 and carbonizing polymerized resols on silica spheres.21 However, most of these synthesis methods involve intricate processes, surface modification, expensive starting materials or large energy-consuming devices, consequently leading to limited yield quantities of the CDs or CNDs. Therefore, it is still critical to build an economical, facile, effective and green synthetic route to produce strongly fluorescent CDs or CNDs on a large scale for practical applications.
Nowadays, ionic liquids (ILs) have been gaining great attention for their potential use in chemical syntheses because of their “green” characteristics, such as negligible volatility and non-flammability under ambient conditions, large liquid range, high thermal and chemical stability, strong solubility power and a number of possible variations in cation and anion features, which allow fine-tuning of the IL properties.22–25 However, to the best of our knowledge, a one-step preparation of CNDs derived from ionic liquids through the hydrothermal approach has not been reported so far. In the last decade, the hydrothermal technique has offered several advantages, such as in the decomposition of hazardous and/or refractory chemical substances, homogeneous precipitation using metal chelates under hydrothermal conditions, and a host of other chemical engineering and environmental engineering issues dealing with the recycling of rubbers and plastics, and so on. Recently Zhao et al. reported the hydrothermal carbonization of chitosan under mild aqueous conditions for the production of N-doped carbonaceous materials26 and Tian et al. exploited a hydrothermal synthesis route for the enhanced photoluminescence of carbon nanoparticles.27
In this work, we report an economical and facile hydrothermal approach to synthesize CNDs derived from ionic liquids. It is found that the CNDs formed through the heat-treatment-based strategy are highly water-soluble and exhibit a strong fluorescence. The one-step preparation process is simple and effective, neither a strong acid solvent nor surface modification reagent is needed, which makes this approach very suitable for industrial production.
Experimental
Reagents
1-Butyl-3-methylimidazolium tetrafluoroborate ([Bmim]BF4), 1-butylpyridinium tetrafluoroborate ([BPy]BF4), 1-hexyl-3-methylimidazolium tetrafluoroborate ([Hmim]BF4), 1-dodecyl-3-methylimidazolium tetrafluoroborate ([C12mim]BF4), and 1-hexadecyl-3-methylimidazolium bromide ([C16mim]Br) were purchased from Lanzhou Greenchem ILS, LICP, CAS, China. All the chemicals were used as received without further purification.
Apparatus
UV-vis absorption was characterized using a UV1800 UV-vis spectrophotometer (Shimadzu Corporation, Japan). Photoluminescence (PL) emission measurements were performed using a RF-5301PC fluorescence spectrophotometer (Shimadzu Corporation, Japan). The morphology of the as-synthesized nanoparticles was studied using a FEI Tecnai G2 F20 transmission electron microscope (TEM) and an IX71 inverted research microscope (Olympus, Japan). The surface groups on the CNDs were measured with a 8400s FTIR spectrometer (Shimadzu Corporation, Japan). X-ray photoelectron spectroscopy (XPS) analysis was measured on an ESCALAB MK-II X-ray photoelectron spectrometer. Raman spectra were recorded using a DXR Raman microscope (Thermo Fisher Scientific, America).
Synthesis of CNDs
As shown in Scheme 1, the photoluminescent CNDs were prepared by polymerization of an ionic liquid and distilled water. In a typical procedure, 0.5 g of 1-butyl-3-methylimidazolium tetrafluoroborate ([Bmim]BF4) was added to 20 mL of distilled water, which was then transferred to a Teflon-lined stainless-steel autoclave and sealed to heat at 200 °C. After reaction for 12 h, a dark brown solution was obtained, which implied the formation of the CNDs.
 |
| Scheme 1 Hydrothermal approach to prepare CNDs. | |
Quantum yield
The quantum yield (Φ) of the CNDs was measured by comparing the integrated photoluminescence intensities and the absorbance values with reference quinine sulfate (QS). The quinine sulfate (literature Φ = 0.54) was dissolved in 0.1 M H2SO4 (refractive index (η) of 1.33) and the CNDs were dissolved in distilled water (η = 1.33).
where Φ is the quantum yield, I is the measured integrated emission intensity, η is the refractive index, and A is the optical density. The subscript R refers to the reference fluorophore of the known quantum yield.
Results and discussion
Optimization of preparation
In order to acquire a high quantum yield, the synthesis conditions of the CNDs, including the amount of ionic liquid, the volume of water, reaction temperature and time, were optimized. As shown in Table S1 (ESI†), the optimal result (No. 9) demonstrated that to obtain a high quantum yield the reaction needed a higher temperature, longer time, higher gas pressure and an appropriate proportion of reactants.
Characterization of CNDs
Fig. 1 depicts the UV-vis absorption and photoluminescence (PL) spectra for the sample. The first absorption band at 240 nm was observed for both samples. When it was excited at 355 nm, the PL spectra showed a peak position at 458 nm. A 218 nm red shift from the first absorption peak was observed. In addition, the fluorescence intensity gradually decreases with increasing excitation wavelength. Such an observation is similar to other carbon nitride dots,24 which may be attributed to an optical selection of differently sized nanoparticles (quantum effect) or different emissive traps on the CND surface or another mechanism altogether. The fluorescence quantum yield of the CNDs is about 8.34% with quinine sulfate as a standard reference (Table S2, ESI†).
 |
| Fig. 1 UV-vis absorption spectra and PL spectra for CNDs. | |
The transmission electron microscope (TEM) images (Fig. 2) and FL images of CNDs (Fig. S1, ESI†) showed that the nanoparticles were uniform with a spherical shape, and that the as-prepared CNDs were well dispersed in narrow distributions of 4.15 ± 1.95 nm diameter. The chemical composition of these nanoparticles was further determined by collecting the corresponding energy-dispersed spectroscopy (EDS) results, as shown in Fig. S2 (ESI†). Peaks of C, N and O elements are observed, indicating that these nanoparticles are formed by [Bmim]BF4 and H2O. Furthermore, peaks of F, S, Si and Cu elements are also observed, which originate from [Bmim]BF4 adsorbed on the surface of CNDs and the glass substrate used for EDS analysis. The elemental analysis indicated that the composition of the CNDs was C 48.97 wt%, N 8.56 wt% and H 5.72 wt% (Table S3, ESI†). It was found that after hydrothermal carbonization the carbon content of the CNDs obviously increased, which was mainly due to the loss of nitrogen and hydrogen in the hydrothermal process. The surface composition and elemental analysis for the overall composition of the resultant nanoparticles were characterized by XPS techniques. The XPS spectrum of the nanoparticles shown in Fig. S3–S6 (ESI†) exhibits three peaks at 285, 401 and 532 eV, which are attributed to C1s, N1s, and O1s, respectively. Another two peaks at 193 and 685 eV associated with B1s and F1s are also observed, which may come from [Bmim]BF4 adsorbed on the surface of the particles. All these results indicate that the nanoparticles thus obtained are mainly composed of C, N, O, H and limited amounts of B and F elements.
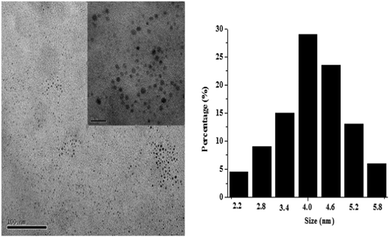 |
| Fig. 2 TEM images (left) and the size distributions (right) for CNDs. The inset scale bar is 20 nm. | |
As shown in Fig. 3, the Fourier Transform Infrared (FT-IR) spectrum of CNDs exhibited peaks at 3446 cm−1 and 1635 cm−1, which were attributed to the stretching vibrations and in-plane bending vibration of –OH, respectively. The peaks at 2964 cm−1, 2874 cm−1 and 1302 cm−1 corresponded to the asymmetric and symmetric stretching vibrations of C–H bonds. There were typical peaks around 1060 cm−1, which were ascribed to the stretching vibrations of B–F. The characteristic absorption bands of the aromatic C–N heterocycles at 1465 cm−1 and 1572 cm−1 were observed, revealing that the local structure of the nanoparticles thus obtained is composed of CN units.28,29 Compared to [Bmim]BF4, the CNDs showed a decrease in the absorption of the C–H unsaturated stretching vibrations at 3095 cm−1 and 3156 cm−1, which can be interpreted as the decomposition of the imidazole ring through the hydrothermal process.
 |
| Fig. 3 FT-IR spectrum of (a) [Bmim]BF4 and (b) CNDs. | |
Influence of pH and ionic strengths
The typical Raman spectrum in Fig. S7 (ESI†) shows a strong D band at 1100 cm−1, a very weak G band at 1419 cm−1 and a peak at 2436 cm−1, ascribed to the disordered carbon and sp2 clusters, indicating an amorphous nature.30
As shown in Fig. S8 (ESI†), the CNDs showed excellent photostability as the fluorescence intensity did not change obviously, even after continuous excitation with a 150 W Xe lamp for 11 hours.
The impact of pH and ionic strengths on the fluorescence intensity of the CNDs was investigated (Fig. 4). The results indicated that even in an aqueous solution with a high ionic strength, the fluorescence intensity of the CNDs was stable. However, the fluorescence intensity of the CNDs increased when the solution pH varied from 1.0 to 5.8. On the contrary, the fluorescence intensity decreased significantly when the pH value varied from 5.8 to 13. These phenomena show the potential of these fluorescent CNDs as good candidates for biological applications and pH sensors. It is found that such observations are similar to those of modified carbon nanoparticles passivated by an N-containing polymer, which are attributed to the presence of N-containing groups on the surface,24 but our one-step “green” process is absolutely more economical and facile, and does not require strong acid treatment or surface modification.
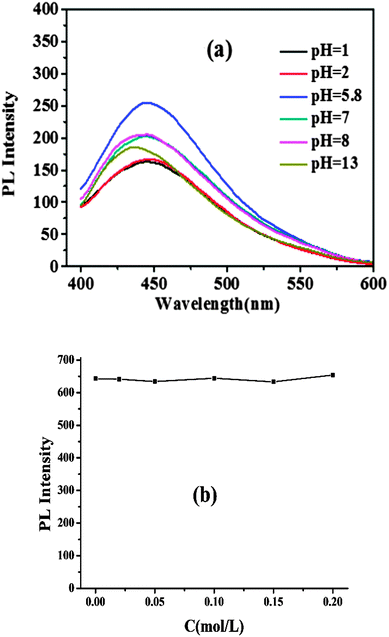 |
| Fig. 4 The influence of pH and ionic strengths on the fluorescence intensity of the CNDs. | |
Method practicability
In addition, it was also found that other ionic liquids may serve as the carbon precursor for the synthesis of fluorescent CNDs. Different types of nitrogenous ionic liquids ([Bmim]BF4, [BPy]BF4, [Hmim]BF4, [C12mim]BF4, [C16mim]Br) were applied to test the possibility of producing fluorescent CNDs. As shown in Fig. 5, the quantum yield of the carbon nitride dots derived from different types of ionic liquids ranged from 7.65% to 8.34%, suggesting that this simple method can be widely applied in the synthesis of different CNDs, originating from ionic liquids, for specific demands.
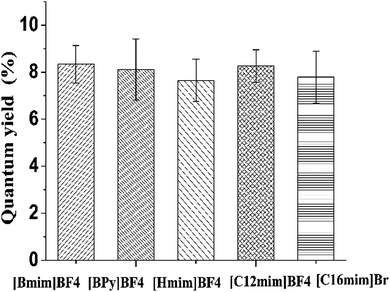 |
| Fig. 5 Quantum yields of carbon nitride dots derived from different types of ionic liquid. | |
Comparison with other methods
Table 1 compares the present method with other methods for the synthesis of CNDs. As can be seen, the present method exhibited a higher quantum yield than most of the previously reported methods.29,31–33 What's more, this method bears several unique merits, such as being clean, cheap, convenient and having a potential to advance large-scale industrialization.
Table 1 Comparison of fluorescent carbon nanoparticles with different methods
Method |
Source |
Color of products |
Excitation and emission wavelength (nm) |
Composition |
Quantum yield (%) |
Ref. |
Hydrothermal treatment |
L-Ascorbic acid |
Dark brown |
340, 420 |
— |
6.79 |
26
|
Microwave |
Poly(ethylene glycol) and saccharide |
Dark brown |
330, 425 |
C, O |
6.3 |
27
|
Hydrothermal treatment |
Pomelo peel |
— |
365, 444 |
C, N, O |
6.9 |
28
|
Reflux or microwave |
CCl4 and 1,2-ethylenediamine |
— |
360, 440 |
C, N, O |
11 |
29
|
Hydrothermal treatment |
Ionic liquids |
Dark brown |
355, 458 |
C, N, O, H |
8.34 |
This method |
Conclusions
In conclusion, fluorescent carbon nitride dots derived from ionic liquids have been prepared by a hydrothermal reaction. The synthesized carbon nitride dots showed some benign properties such as higher photoluminescence efficiencies (8.34%), monodispersity and a small diameter (4.15 ± 1.95 nm). In comparison with previous methods, this method bears several unique merits, such as being clean, cheap, convenient and having a potential to advance large-scale industrialization. This one-step “green” process has no need for strong acid treatment or surface modification. In particular, the as-prepared carbon nitride dots exhibit excellent stability in biological media, and their luminescence intensity is also stable with the ionic strength or pH in the physiological and pathological range of pH 4.5–8.8. The strong fluorescence and excellent water dispersion is attributed to the abundant surface traps and functional groups. We believe that the as-prepared carbon nitride dots can be one of the most promising candidates for a new type of fluorescent marker for use in biomedical imaging, bio-sensors and drug delivery.
Acknowledgements
This work was supported by the National Natural Science Foundation of China (Grant No. 81402899).
References
- S. T. Selvan, P. K. Patra, C. Y. Ang and J. Y. Ying, Angew. Chem., Int. Ed., 2007, 46(14), 2448–2452, DOI:10.1002/anie.200604245.
- P. M. A. Farias, B. S. Santos, A. A. de Thomaz, R. Ferreira, F. D. Menezes, C. L. Cesar and A. Fontes, J. Phys. Chem. B, 2008, 112(9), 2734–2737, DOI:10.1021/jp0758465.
- K. Boeneman, J. B. Delehanty, K. Susumu, M. H. Stewart and I. L. Medintz, J. Am. Chem. Soc., 2010, 132(17), 5975–5977, DOI:10.1021/ja100201w.
- J. R. Petta, A. C. Johnson, J. M. Taylor, E. A. Laird, A. Yacoby, M. D. Lukin, C. M. Marcus, M. P. Hanson and A. C. Gossard, Science, 2005, 309(5744), 2180–2184, DOI:10.1126/science.1116955.
- J. P. Reithmaier, G. Sek, A. Loffler, C. Hofmann, S. Kuhn, S. Reitzenstein, L. V. Keldysh, V. D. Kulakovskii, T. L. Reinecke and A. Forchel, Nature, 2004, 432(7014), 197–200, DOI:10.1038/nature02969.
- M. Kroutvar, Y. Ducommun, D. Heiss, M. Bichler, D. Schuh, G. Abstreiter and J. J. Finley, Nature, 2004, 432(7013), 81–84, DOI:10.1038/nature03008.
- A. M. Derfus, W. C. W. Chan and S. N. Bhatia, Nano Lett., 2004, 4(1), 11–18, DOI:10.1021/nl0347334.
- N. Lewinski, V. Colvin and R. Drezek, Small, 2008, 4(1), 26–49, DOI:10.1002/smll.200700595.
- A. M. Derfus, W. C. W. Chan and S. N. Bhatia, Nano Lett., 2003, 4(1), 11–18, DOI:10.1021/nl0347334.
- Y.-P. Sun, B. Zhou, Y. Lin, W. Wang, K. A. S. Fernando, P. Pathak, M. J. Meziani, B. A. Harruff, X. Wang, H. Wang, P. G. Luo, H. Yang, M. E. Kose, B. Chen, L. M. Veca and S.-Y. Xie, J. Am. Chem. Soc., 2006, 128(24), 7756–7757, DOI:10.1021/ja062677d.
- H. Li, X. He, Z. Kang, H. Huang, Y. Liu, J. Liu, S. Lian, C. H. A. Tsang, X. Yang and S.-T. Lee, Angew. Chem., Int. Ed., 2010, 49(26), 4430–4434, DOI:10.1002/anie.200906154.
- J. Zong, Y. Zhu, X. Yang, J. Shen and C. Li, Chem. Commun., 2011, 47(2), 764–766, 10.1039/c0cc03092a.
- H. Liu, T. Ye and C. Mao, Angew. Chem., Int. Ed., 2007, 46(34), 6473–6475, DOI:10.1002/anie.200701271.
- L. Yang, P. W. May, Y. Huang and L. Yin, J. Mater. Chem., 2007, 17(13), 1255–1257 RSC.
- L. Liu, D. Ma, H. Zheng, X. Li, M. Cheng and X. Bao, Microporous Mesoporous Mater., 2008, 110(2–3), 216–222, DOI:10.1016/j.micromeso.2007.06.012.
- X. Xu, R. Ray, Y. Gu, H. J. Ploehn, L. Gearheart, K. Raker and W. A. Scrivens, J. Am. Chem. Soc., 2004, 126(40), 12736–12737, DOI:10.1021/ja040082h.
- Q.-L. Zhao, Z.-L. Zhang, B.-H. Huang, J. Peng, M. Zhang and D.-W. Pang, Chem. Commun., 2008, 5116, 10.1039/b812420e.
- J. Zhou, C. Booker, R. Li, X. Zhou, T.-K. Sham, X. Sun and Z. Ding, J. Am. Chem. Soc., 2007, 129(4), 744–745, DOI:10.1021/ja0669070.
- S. C. Ray, A. Saha, N. R. Jana and R. Sarkar, J. Phys. Chem. C, 2009, 113(43), 18546–18551, DOI:10.1021/jp905912n.
- L. Tian, D. Ghosh, W. Chen, S. Pradhan, X. Chang and S. Chen, Chem. Mater., 2009, 21(13), 2803–2809, DOI:10.1021/cm900709w.
- A. B. Bourlinos, A. Stassinopoulos, D. Anglos, R. Zboril, V. Georgakilas and E. P. Giannelis, Chem. Mater., 2008, 20(14), 4539–4541, DOI:10.1021/cm800506r.
- X. Han and D. W. Armstrong, Acc. Chem. Res., 2007, 40(11), 1079–1086, DOI:10.1021/ar700044y.
- Y. Pei, J. Wang, K. Wu, X. Xuan and X. Lu, Sep. Purif. Technol., 2009, 64(3), 288–295, DOI:10.1016/j.seppur.2008.10.010.
- Y. Zhang, Y. Shen, J. Yuan, D. Han, Z. Wang, Q. Zhang and L. Niu, Angew. Chem., 2006, 45(35), 5867–5870, DOI:10.1002/anie.200600120.
- Y. Zhang and M. Antonietti, Chem. – Asian J., 2010, 5(6), 1307–1311, DOI:10.1002/asia.200900685.
- L. Zhao, N. Baccile, S. Gross, Y. Zhang, W. Wei, Y. Sun, M. Antonietti and M.-M. Titirici, Carbon, 2010, 48(13), 3778–3787, DOI:10.1016/j.carbon.2010.06.040.
- L. Tian, Y. Song, X. Chang and S. Chen, Scr. Mater., 2010, 62(11), 883–886, DOI:10.1016/j.scriptamat.2010.02.035.
- M. J. Bojdys, J.-O. Müller, M. Antonietti and A. Thomas, Chem. – Eur. J., 2008, 14(27), 8177–8182, DOI:10.1002/chem.200800190.
- S. Liu, J. Tian, L. Wang, Y. Luo, J. Zhai and X. Sun, J. Mater. Chem., 2011, 21(32), 11726, 10.1039/c1jm12149a.
- Y. H. Yang, J. H. Cui, M. T. Zheng, C. F. Hu, S. Z. Tan, Y. Xiao, Q. Yang and Y. L. Liu, Chem. Commun., 2012, 48(3), 380–382, 10.1039/c1cc15678k.
- B. Zhang, C.-y. Liu and Y. Liu, Eur. J. Inorg. Chem., 2010, 4411–4414, DOI:10.1002/ejic.201000622.
- H. Zhu, X. Wang, Y. Li, Z. Wang, F. Yang and X. Yang, Chem. Commun., 2009, 5118, 10.1039/b907612c.
- W. Lu, X. Qin, S. Liu, G. Chang, Y. Zhang, Y. Luo, A. M. Asiri, A. O. Al-Youbi and X. Sun, Anal. Chem., 2012, 84(12), 5351–5357, DOI:10.1021/ac3007939.
Footnote |
† Electronic supplementary information (ESI) available. See DOI: 10.1039/c5nj01717c |
|
This journal is © The Royal Society of Chemistry and the Centre National de la Recherche Scientifique 2016 |
Click here to see how this site uses Cookies. View our privacy policy here.