DOI:
10.1039/C5GC90070K
(Editorial)
Green Chem., 2016,
18, 590-593
Catalytic versus stoichiometric reagents as a key concept for Green Chemistry
Abstract
25 years ago catalysis was highlighted as a main principle of Green Chemistry. Selective catalysis enables an efficient utilisation of resources and the design of benign processes. Waste formation caused by stoichiometric reagents, for instance in reduction or oxidation reactions, can be overcome using suitable catalysts and benign reductants and oxidants, respectively. Solid acidic and basic catalysts prevent prevalent salt formation associated with the use of molecular acids and bases. Catalysts allow us to decrease the activation energy of chemical transformations, enhance the reaction rate, facilitate high selectivity and are crucial to reduce the number of process steps.
The year 2016 marks the 25th anniversary of the field of Green Chemistry. Green Chemistry was put forward as a knowledge-based approach for environmental protection with 12 principles characterising safe and environmentally benign processes.1 This editorial contributes to a series featuring the 12 Principles of Green Chemistry. It is not surprising that catalysis was included in the list of the principles as ‘catalytic reagents (as selective as possible) are superior to stoichiometric reagents’ (Fig. 1).
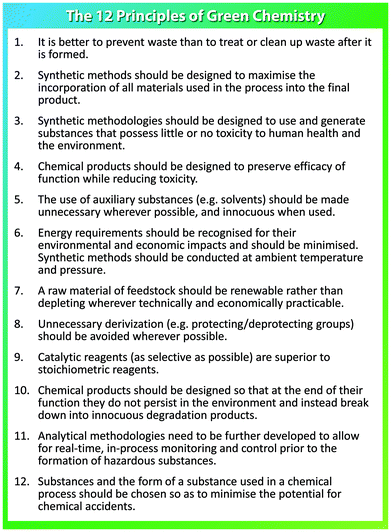 |
| Fig. 1 The 12 Principles of Green Chemistry.1c | |
Long before the definition of the principles of Green Chemistry, several industrial processes in oil refining, polymer production, and many others successfully used catalysis. Especially for industrial fuel and bulk chemical production, catalytic processes are indispensable. Technologies such as large-scale ammonia or methanol synthesis would hardly be possible without active and selective catalysts. Catalysis presents a key technology to enable energy and resource efficient chemical transformations.
The concept of Green Chemistry highlights the outstanding potential of catalysis to contribute to the guiding principle of benign by design. In particular the use of stoichiometric reagents often applied in organic synthesis is inevitably associated with waste formation. Apparent examples include stoichiometric reductions or oxidations using e.g. NaBH4 or chromium(VI) reagents, respectively. Comparable challenges arise in various other transformations, here only reactions employing stoichiometric amounts of molecular acids and bases as major sources of waste are mentioned.2
In addition to waste prevention, catalysis also decreases the activation energy required for a chemical transformation, enhances the rate of reaction, allows high selectivity and is potentially able to reduce the number of process steps. Importantly, re-usability of catalysts provides economic feasibility facilitating industrial application of new green processes. In what follows we present examples demonstrating the opportunities offered by catalysis to design green(er) chemical processes.
1. Green(er) chemical processes
Roger Sheldon defined the E(nvironmental) factor as an excellent metric to estimate waste generation of chemical processes.2,3 The E factor relates the mass of waste to the mass of product formed. Of course, other measures such as atom efficiency exist and other factors have to be taken into account when assessing the sustainability of a process, i.e. toxicity of waste. Nevertheless, the E factor remains a convenient means to estimate process efficiency from an environmental viewpoint. The E factor combines yield, stoichiometry and solvent/additive usage in a simple measure applicable to lab-scale experiments as well as industrial production facilities. The most efficient processes possess E = 0, whereas high E values indicate large amounts of by-products (for all shown E values 100% yields are assumed).
Solid acids in Friedel–Crafts acylations
Friedel–Crafts acylations are widely applied in fine chemical synthesis. These processes clearly emphasise the distinct advantages of solid acids compared to homogeneous Lewis acids such as AlCl3. Using an aromatic substrate, a greater than stoichiometric amount of AlCl3 is required due to complex formation with the ketone. A water quench releases the organic product as well as ca. 3 equivalents of HCl forming salt upon neutralisation.4 In recent years, several studies emphasised the potential of solid acids such as zeolite H-BEA for acetylation of substrates such as anisole, eliminating salt formation and enabling a facilitated product work-up (Scheme 1).5
 |
| Scheme 1 Friedel–Crafts acylation of anisole. | |
Solid acids in Beckmann rearrangements
The Beckmann rearrangement of cyclohexanone oxime into caprolactam, a monomer for the synthesis of nylon-6, presents another excellent example for the potential of solid acid catalysts in waste prevention (Scheme 2). As highlighted by Sheldon, industrial manufacture of organic compounds often suffers from inorganic wastes such as salts.2 Conventionally, caprolactam is produced in oleum associated with the need for subsequent neutralization with ammonia. This brings about co-producing equimolar amounts of ammonium sulphate and the product. Recently, Sumitomo commercialized an alternative catalytic process. Carrying out the Beckmann rearrangement in the vapour-phase over a high Si MFI zeolite as a solid catalyst enables an E factor of zero as opposed to 1.2 for the conventional process.2
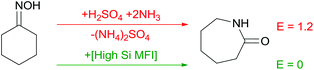 |
| Scheme 2 Beckmann rearrangement. | |
Efficient oxidation catalysis – phenol
Benign oxidation processes in particular remain a major challenge for catalysis, with the ultimate goal to use air oxygen as oxidant. Phenol is widely used e.g. for production of polymers (via bisphenol A) and resins. In the classic approach, benzene is transformed into phenol in three steps, including (i) production of cumene (isopropylbenzene), (ii) oxidation of cumene with molecular oxygen into cumene hydroperoxide, and (iii) acidic hydrolysis of the latter yielding phenol and acetone as coproduct (Scheme 3). Consequently, the price of phenol strongly depends on marketability of acetone. Transforming toluene to phenol via benzoic acid presents an attractive alternative, however, it suffers from a clearly higher energy demand compared to the conventional process. The Boreskov Institute of Catalysis developed a new technology utilising N2O as oxidant and forming molecular nitrogen as sole by-product.6 However, availability of N2O hinders broad application of this concept and suitable catalysts for a direct oxidation of phenol with air oxygen remains as future challenge and opportunity.
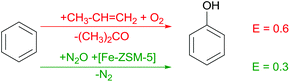 |
| Scheme 3 Phenol synthesis. | |
Efficient oxidation catalysis – propylene oxide
Also, for the oxidation of propylene to propylene oxide, an important monomer for polymer production, a direct pathway presents a major challenge (Scheme 4). On an industrial scale, propylene oxide production via the chlorohydrin process includes two steps, namely (i) chlorohydrin synthesis and (ii) dehydrochlorination and neutralization. Consequently, propylene oxide production is inevitably connected to utilization of environmentally dangerous Cl2 and the formation of an aqueous CaCl2 containing waste stream. An alternative process proceeds via oxidation of isobutane or ethylbenzene with oxygen to form the peroxide sources for subsequent oxidation of propylene. Dependent on the peroxide source, equimolar amounts of isobutene or styrene accompany propylene oxide production as coproduct. The more environmentally benign Degussa–Uhde process utilises H2O2 as oxidant and TS-1 as solid catalyst. This one-step process avoids waste generation or the formation of coproducts and has been recently commercialised2,3 in spite of the higher price of H2O2 as oxidant compared to oxygen. Additionally, production of hydrogen peroxide based on molecular H2 and O2 represents the productivity vs. safety dilemma.7
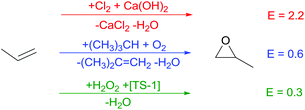 |
| Scheme 4 Production of propylene oxide. | |
Avoiding toxic waste
Disodium iminoacetate (DSIDA) presents a key intermediate for production of glyphosate (N-(phosphonomethyl)glycine), a widely utilized herbicide. Despite a low E factor of 0.2 for the conventional process, the applied non-catalytic Strecker synthesis utilises hazardous compounds such as hydrogen cyanide, formaldehyde and HCl, respectively. In contrast, a catalytic process relying on copper-catalysed dehydrogenation of diethanolamine (E = 0.05) was awarded the Green Chemistry award in 1996. A comparative study by Tian et al. highlighted – albeit with minor reduction of the E factor – major advantages of this alternative glyphosate production (Scheme 5).8
 |
| Scheme 5 Production of disodium iminoacetate (DSIDA). | |
Energy efficiency – renewable feedstocks
Efficient energy use presents a major global challenge. Catalysts decrease the activation energy of chemical transformations contributing to energy efficient processes. Cellulose is a sustainable renewable feedstock, which can be transformed into value-added products after hydrolysis into glucose, a key transformation in future biorefineries.9 However, cellulose is insoluble in water and very resistant against hydrolysis. Without catalyst, hydrolysis is possible in sub- and supercritical water at 250–400 °C.10 Under these conditions, glucose decomposes quickly. Applying molecular acids decreases the required temperature for hydrolysis to 110–240 °C.11 Solid acids or enzymes such as cellulase enable an even lower reaction temperature.10,12 As expected, glucose is more stable under milder reaction conditions; therefore, the product yield in the presence of cellulase is maximal. Using catalysts, EA decreases from 150–215 kJ mol−1 to 40–125 kJ mol−1, respectively (Table 1).
Table 1 Activation energy of cellulose hydrolysis to glucose in the presence of different catalysts
Entry |
Catalyst |
Temperature, °C |
E
a, kJ mol−1 a |
Yield of glucose, % |
Ref. |
E
A not only depends on catalyst but also on degree of crystallinity and polymerisation of cellulose.
Yield of soluble glucans.
|
1 |
No catalyst |
250–400 |
150–215 |
<40 |
10
|
2 |
H2SO4 |
110–240 |
100–180 |
65 |
10,11
|
3 |
Sulfonated carbon |
70–100 |
110 |
64b |
14
|
4 |
Cellulase enzyme |
40–70 |
40–125 |
75–95 |
10,12
|
2. Future opportunities
Applied for many years in refinery technology and bulk chemical synthesis, catalysis as a main principle of Green Chemistry has found its way into the production of fine chemicals and pharmaceuticals. Technologies such as flexible continuous processes and modular reactor concepts will without doubt facilitate expansion of the scope of catalysis in the latter fields.13 In particular, the development of novel highly active and selective base metal catalysts is of pivotal importance and a focus point of intense research.
Considering the major target of CO2-neutral products and processes as well as the challenges related to closed carbon cycles, catalysis presents a key element. In recent years, chemo- and biocatalysts have proven their potential to integrate renewable feedstocks such as biomass and CO2 into chemical value chains. Biofuels based on waste streams and bulk chemicals such as methanol produced from CO2 and green H2 accessible via photo- and/or electro-catalytic water splitting become feasible. Chemical energy storage can address challenges and opportunities related to fluctuating supply of renewable energy creating a strong link between the energy sector and chemical industry.
We are convinced that catalysis together with other principles of Green Chemistry and green engineering are indispensable on the way to sustainable processes and future circular economy.
3. Conclusion remarks
During the last 25 years, catalysis has proven to be an essential tool for Green Chemistry. Catalysis enables the design of resource and energy efficient processes according to the mission statement benign by design.
Acknowledgements
We thank the Alexander von Humboldt Foundation and the Bayer Foundation for the financial support. This work was performed as part of the Cluster of Excellence “Tailor-Made Fuels from Biomass” funded by the Excellence Initiative of the German federal and state governments to promote science and research at German universities.
Notes and references
-
(a) P. T. Anastas, L. B. Bartlett, M. M. Kirchhoff and T. C. Williamson, Catal. Today, 2000, 55, 11 CrossRef CAS;
(b) S. L. Y. Tang, R. L. Smith and M. Poliakoff, Green Chem., 2005, 7, 761 RSC;
(c)
P. T. Anastas and J. C. Warner, Green Chemistry: Theory and Practice, Oxford University Press, 1998 Search PubMed.
-
R. A. Sheldon, Catalysis, the atom utilization concept and waste minimization, in Indust. Environ. Chem. Proc, ed. D. T. Sawyer and A. E. Martell, Plenum Press, NY, USA, 1992, p. 99 Search PubMed.
- R. A. Sheldon, Green Chem., 2007, 9, 1273 RSC; R. A. Sheldon, Chem. Soc. Rev., 2012, 41, 1437 RSC.
- J. H. Clark, Green Chem., 1999, 1, 1 RSC;
Handbook of Green Chemistry and Technology, ed. J. Clark and D. Macquarries, Blackwell Science Ltd., 2002 Search PubMed.
- K. Smith, Z. Zhenhua and P. K. G. Hodgson, J. Mol. Catal. A: Chem., 1998, 134, 121 CrossRef CAS.
- G. I. Panov, G. A. Sheveleva, A. S. Kharitonov, V. N. Romannikov and L. A. Vostrikova, Appl. Catal., A, 1992, 82, 31 CrossRef CAS.
- E. J. Beckman, Green Chem., 2003, 5, 332 RSC.
- J. Tian, H. Shi, X. Li, Y. Yin and L. Chen, Green Chem., 2012, 14, 1990 RSC.
- A. Corma, S. Iborra and A. Velty, Chem. Rev., 2007, 107, 2411 CrossRef CAS.
- Y. Yu, X. Lou and H. Wu, Energy Fuels, 2008, 22, 46 CrossRef CAS.
- L. Negahdar, I. Delidovich and R. Palkovits, Appl. Catal., B Environ., 2016, 184, 285 CrossRef CAS.
- S. Zhang, D. E. Wolfgang and D. B. Wilson, Biotechnol. Bioeng., 1999, 66, 35 CrossRef CAS.
-
http://www2.epa.gov/greenchemistry/presidential-green-chemistry-challenge-winners
.
- S. Suganuma, K. Nakajima, M. Kitano, D. Yamaguchi, H. Kato, S. Hayashi and M. Hara, J. Am. Chem. Soc., 2008, 130, 12787 CrossRef CAS.
|
This journal is © The Royal Society of Chemistry 2016 |