DOI:
10.1039/C6FD00054A
(Paper)
Faraday Discuss., 2016,
192, 283-301
A novel methodology for assessing the environmental sustainability of ionic liquids used for CO2 capture†
Received
15th March 2016
, Accepted 20th April 2016
First published on 28th April 2016
Abstract
Ionic liquids (ILs) have been proposed as suitable sorbents for CO2 capture because of their high CO2 absorption capacity, thermal stability, negligible vapour pressure and physico-chemical tunability. However, the environmental implications of ILs are currently largely unknown because of a lack of data. The issue is further complicated by their complex chemical structures and numerous precursors for which environmental data are scarce or non-existent. In an attempt to address this issue, this paper presents a new methodology for estimating life cycle environmental impacts of novel ILs, with the aim of aiding synthesis and selection of more sustainable CO2 sorbents. The methodology consists of four main steps: (1) selection of an appropriate IL and synthesis route; (2) construction of a life cycle tree; (3) life cycle assessment; and (4) recommendations for improvements. The application of the methodology is illustrated using trihexyltetradecylphosphonium 1,2,4-triazolide ([P66614][124Triz]), a promising IL for CO2 capture currently under development. Following the above steps, the paper demonstrates how the data obtained from laboratory synthesis of the IL can be scaled up to industrial production to estimate life cycle impacts and identify environmental hotspots. In this particular case, the main hotspots are the precursors used in the synthesis of the IL. Comparison of impacts with monoethanolamine (MEA), currently the most widely-used CO2 sorbent, suggests that [P66614][124Triz] has much higher impacts than MEA, including global warming potential. However, human toxicity potential is significantly higher for MEA. Therefore, the proposed methodology can be used to optimise the design of ILs and to guide selection of more sustainable CO2 sorbents. Although the focus is on ILs, the methodology is generic and can be applied to other chemicals under development.
1. Introduction
Reducing greenhouse gas (GHG) emissions has become a major global challenge, with many countries seeking to implement appropriate solutions to mitigate climate change. Carbon capture and storage (CCS) and carbon capture and utilisation (CCU) are considered as promising options that could help towards addressing this challenge.1–3 However, they are both constrained by the efficiency of CO2 capture, which can significantly influence their economic and environmental sustainability. Thus, further development of CO2 capture processes aiming to reduce costs and environmental impacts is important for successful deployment of CCS and CCU at a large scale.
Currently, the most mature and widely-used method for CO2 capture is post-combustion absorption in monoethanolamine (MEA).4–6 The advantages of MEA are its high CO2 absorption capacity and relatively low cost. However, MEA is toxic, corrosive at elevated temperatures and expensive to regenerate because of the large enthalpy of CO2 absorption (−85 kJ mol−1 at 40 °C)7 and heat losses through vaporization.6,8,9 Therefore, development of more sustainable sorbents is one of the main challenges for CCS and CCU.
In recent years, various alternatives to MEA have been suggested, including KS-1 solvent, Econamine FG+SM, amidoxime, metal–organic frameworks, microporous organic polymers, zeolitic imidazolate frameworks and membranes, and ionic liquids (ILs).10 The latter are considered an attractive alternative to amine-based solvents because of their high CO2 solubility and related absorption capacity, extremely low vapour pressure and low corrosivity.8,9,11 Furthermore, the vast number of possible combinations of cations and anions allow the solvent to be custom-made for specific applications.10 A recent study which tested tetraalkylphosphonium superbase ILs reported that, at room temperature and atmospheric pressure, trihexyltetradecylphosphonium 1,2,4-triazolide ([P66614][124Triz]) (C34H71PN3) had equimolar CO2 uptake under dry conditions and slightly below that under wet conditions.7 Thus, these results suggest that [P66614][124Triz] is a promising sorbent for CO2 capture.
However, before novel ILs such as [P66614][124Triz] can be used as alternatives to conventional sorbents, it is necessary to understand their environmental implications, to avoid solving one environmental problem – climate change – at the expense of other impacts. It is also important that the environmental evaluation be carried out on a life cycle basis, to ensure that the impacts are not shifted from one life cycle stage to another, a problem known as ‘leakage’ of environmental impacts. This is not a trivial task, as life cycle impacts of novel ILs are as yet unknown because they are still being developed, and data for their manufacture and use at an industrial scale are limited. This is further complicated by their complex synthesis routes involving numerous precursors for which life cycle data are scarce or non-existent.
In an attempt to address this issue, this paper presents a novel methodology for estimating life cycle environmental impacts of ILs under development, with the aim of identifying hotspots and aiding synthesis and selection of more sustainable sorbents. Although the focus here is on ILs, the methodology is generic enough to be applicable to other chemicals. The example of [P66614][124Triz] is used to illustrate the application of the methodology by estimating its life cycle environmental impacts in comparison to MEA. The next section describes the proposed methodology, followed by its application in Section 3. The conclusions and recommendations for future work are given in Section 4.
2. Methodology
The proposed methodology for estimating the life cycle environmental impacts of novel ILs, outlined in Fig. 1, comprises four main steps:
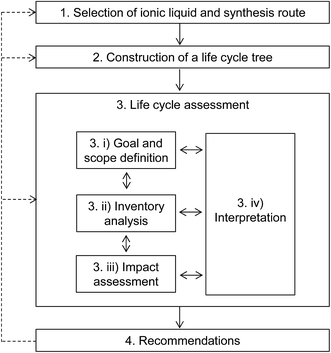 |
| Fig. 1 Proposed methodology for assessing life cycle environmental sustainability of ionic liquids. | |
(1) selection of an IL and its preparation method;
(2) construction of a life cycle tree for the selected IL;
(3) life cycle assessment (LCA); and
(4) recommendations for improvements.
These steps are described in more detail in the following sections.
2.1. Step 1: selection of ionic liquid and synthesis route
As shown in Fig. 1, the first step involves selecting an IL and identifying the synthesis route(s) available for its production. In the case of commercially available ILs, it is possible that more than one route will exist. In that case, the most prevalent commercial process should be selected to ensure representative results. For ILs under development, i.e. synthesised only at a laboratory scale, the preparation method known or used at the time of the assessment should be considered.
2.2. Step 2: construction of a life cycle tree
ILs usually have a complex structure involving numerous precursors for which life cycle data are scarce or not available. To address this issue, a life cycle tree of the IL under study is constructed in the second step (Fig. 1), tracing back to the basic precursors for which life cycle data are available (e.g. hydrogen, ammonia, benzene, methanol, etc.).
Similarly to ILs, it is likely that more than one synthesis route will be available for the precursors, so the most prevalent commercial route should be selected whenever possible. This information can be sourced from scientific journals, patents, chemical handbooks, technology encyclopedias and industry.
Following the completion of the life cycle tree, an LCA of the selected IL can be carried out as outlined below.
2.3. Step 3: life cycle assessment
As indicated in Fig. 1, LCA involves four phases:12,13
(i) goal and scope of the study: definition of the goal of the study, system boundaries, functional unit (unit of analysis) and assumptions;
(ii) inventory analysis: collection of data on materials and energy used in the system and emissions to air, water and soil;
(iii) environmental impact assessment: estimation of environmental impacts based on the inventory data; and
(iv) interpretation: analysis of the results and comparison of impacts with alternative sorbents to identify hotspots and opportunities for improvements.
For LCA of ILs, the most challenging phase will be the inventory analysis, because of a lack of life cycle inventory data for most novel ILs and their precursors. Furthermore, the data that are available for IL synthesis will be at the laboratory scale, so scaling up to a possible industrial production will be necessary to reflect the actual manufacturing conditions as closely as possible. Different methods can be used for filling data gaps, including stoichiometric, thermodynamics, empirical scale-up and other relevant relationships. The robustness of the results should be tested through sensitivity and uncertainty analyses.
2.4. Step 4: recommendations for improvement
In the fourth and final step of the proposed methodology, recommendations for improvements are made based on the findings of the LCA study. For example, these could include a change of the synthesis route, substitution of raw materials, improvements in the energy and atom efficiency or selection of a different ionic liquid. As shown in Fig. 1, this process is iterative, with the recommendations fed back to the preceding steps, as needed.
The next section illustrates how the proposed methodology can be applied, using the IL [P66614][124Triz] as an example.
3. Application of the methodology: the case of [P66614][124Triz]
3.1. Step 1: selection of ionic liquid and synthesis route
As mentioned earlier, [P66614][124Triz] represents a promising sorbent for CO2 capture based on its high (equimolar) CO2 uptake at room temperature and atmospheric pressure, under both dry and wet conditions.7 In comparison to amino-acid based ILs, which can also achieve equimolar absorption, superbase ILs are not subject to large viscosity increases after CO2 absorption and are thus more suitable for practical applications.7 Phosphonium-based ILs are also much cheaper than other classes of ILs. Moreover, [P66614][124Triz] has recently been used successfully for CO2 conversion to formate via electrochemical reduction,14 which suggests that it could also be used for carbon utilisation, in addition to capture.
[P66614][124Triz] was synthesised by reacting trihexyl(tetradecyl)phosphonium hydroxide ([P66614][OH]) and 1,2,4-triazole in ethanol (Fig. 2). The reactants were mixed in a 1
:
1 mol ratio and stirred for 16 hours at room temperature to produce a solution containing [P66614][124Triz], ethanol and water. Ethanol was removed in a rotary evaporator at 50 °C for one hour. Finally, the IL solution was dried in a rotary evaporator at 50 °C and under high-vacuum conditions for 48 hours. The overall production yield was in excess of 90%. Further details on the production process are provided in the next section.
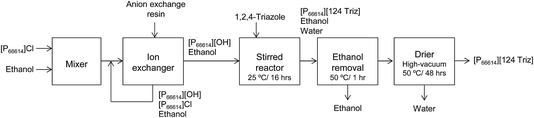 |
| Fig. 2 Synthesis of [P66614][124Triz] (adapted from Taylor et al.7). | |
3.2. Step 2: construction of the life cycle tree
Neither of the two compounds used in the synthesis of [P66614][124Triz] ([P66614][OH] and 1,2,4-triazole) are available in LCA databases, so they had to be traced back to their basic precursors through the construction of a life cycle tree, as shown in Fig. 3. These precursors were identified based on the prevalent commercial production routes found in the literature (see Table 1). A brief description of the synthesis of each precursor is given below and summarised in Table 2; for further details, see Section 1 in ESI.†
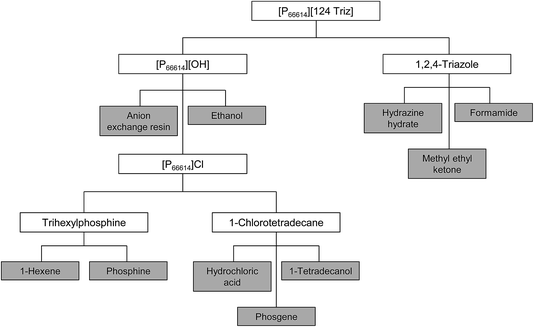 |
| Fig. 3 The life cycle tree for the production of [P66614][124Triz] (the shaded boxes indicate the compounds for which data are available in LCA databases. Data for the compounds shown in clear boxes are not available). | |
Table 1 Precursors for commercial production of [P66614][124Triz]
Compound |
Precursors |
Source |
[P66614][OH] |
[P66614]Cl |
Taylor et al.7 |
[P66614]Cl |
Trihexylphosphine |
Bradaric et al.15 |
1-Chlorotetradecane |
Trihexylphosphine |
Phosphine |
Rauhut et al.16 |
1-Hexene |
1-Chlorotetradecane |
Hydrochloric acid |
Demail et al.17 |
1-Tetradecanol |
Phosgene |
1,2,4-Triazole |
Formamide |
Petree et al.18 |
Hydrazine hydrate |
Table 2 Chemical reactions involved in the production of [P66614][124Triz] and its precursors
Compound |
Chemical reactionsa |
The bold font in the column “Chemical reactions” indicates the main compounds produced, corresponding to the respective compounds in the column “Compound”.
|
[P66614][124Triz] |
[P(CH2(CH2)4CH3)3(CH2(CH2)12CH3)][OH] + HNNCHNCH→[P(CH2(CH2)4CH3)3(CH2(CH2)12CH3)][NNCHNCH] + H2O |
[P66614]OH |
[P(CH2(CH2)4CH3)3(CH2(CH2)12CH3)][Cl] + OH → [P(CH2(CH2)4CH3)3(CH2(CH2)12CH3)][OH] + Cl |
[P66614]Cl |
P(CH2(CH2)4CH3)3 + CH3(CH2)13Cl → [P(CH2(CH2)4CH3)3(CH2(CH2)12CH3)][Cl] + HCl |
Trihexylphosphine |
PH3 + CH2CH(CH2)3CH3 → P(CH2(CH2)4CH3)3 + PH3 + CH2CH(CH2)3CH3 |
1-Chlorotetradecane |
Reaction (i) |
CH3(CH2)13OH + HCl → CH3(CH2)13Cl + CH3(CH2)13OH + CH3(CH2)13O(CH2)13CH3 + H2O |
Reaction (ii) |
CH3(CH2)13OH + COCl2 → CH3(CH2)12Cl + CH3(CH2)13O(CH2)13CH3 + CH3(CH2)13OCOO(CH2)13CH3 + HCl + COCl2 |
1,2,4-Triazole |
CH3 NO + N2H4·H2O → HNNCHNCH + CH3NO + N2H4 + NH3 + HCOOH + H2O + [NH4][HCO2] |
3.2.1. Trihexyl(tetradecyl)phosphonium hydroxide ([P66614][OH]).
As shown in Fig. 2, this IL can be synthesised from trihexyl(tetradecyl)phosphonium chloride ([P66614]Cl) using an anion exchange resin such as Amberlite IRN-78 (OH-form) and ethanol at ambient temperature and atmospheric pressure.7 As indicated in Fig. 3, the latter two are available in LCA databases but [P66614]Cl is not, so its precursors need to be identified to enable estimation of its life cycle impacts.
3.2.2. Trihexyl(tetradecyl)phosphonium chloride ([P66614]Cl).
Cytec, a leading commercial manufacturer of ILs, synthesises this IL by reacting trihexylphosphine and 1-chlorotetradecane at 140 °C and atmospheric pressure, followed by a separation step; the overall yield is 93.9%.15 Neither of these chemicals is available in LCA databases; hence, it is necessary to identify their precursors.
3.2.3. Trihexylphosphine.
Tertiary organophosphines, such as trihexylphosphine, are commonly synthesised from the free-radical addition of phosphine to unsaturated compounds such as 1-hexene in the presence of a free radical promoter.16 Under specific temperature and pressure conditions (e.g. 70 °C and 3.4 bar), this reaction can produce tertiary organophosphines as the predominant product with a yield of >80% with respect to the unsaturated compound.16 As indicated in Fig. 3, life cycle inventory data for both phosphine and hexane are available in LCA databases, which will allow estimation of the LCA impacts of trihexylphosphine in the next step of the methodology.
3.2.4. 1-Chlorotetradecane.
The second precursor for [P66614]Cl can be synthesised through a nucleophilic substitution reaction between an alcohol and a halogen acid.17 This is a two-step process, starting with a reaction between 1-tetradecanol and hydrochloric acid and followed by the addition of phosgene, with separation steps between the reactions. The first step takes place at 140 °C and 4 bar and the second at 120 °C and atmospheric pressure. The two reactions can achieve conversions of 60–95% on a mole basis. As shown in Fig. 3, life cycle inventory data for 1-tetradecanol, hydrochloric acid and phosgene are available in LCA databases, allowing estimation of the LCA impacts of 1-chlorotetradecane. Together with the LCA estimates for trihexylphosphine, it is now possible to determine the LCA impacts of [P66614]Cl and ultimately, the impacts of [P66614][OH].
3.2.5. 1,2,4-Triazole.
This precursor for [P66614][124Triz] can be synthesised from hydrazine hydrate and formamide in a single-step reaction, followed by multiple purification steps using organic solvents, such as methyl ethyl ketone.18 The reaction takes place at 170 °C and atmospheric pressure with yields of 84–90%. Life cycle inventory data are available in LCA databases for all the precursors.
With all the precursors traced back to the point where all the life cycle inventory data are available, LCA of the target IL ([P66614][124Triz]) can now be performed in the next step.
3.3. Step 3: Life cycle assessment
As indicated in Fig. 1, the LCA methodology follows the guidelines in the ISO 14040/44 LCA standards.12,13 The LCA modelling has been carried out in GaBi V6.4 (ref. 19) and the following impacts have been estimated applying the CML 2001 impact assessment method:20 global warming potential (GWP), abiotic depletion potentials for elements and fossil resources (ADP elements and ADP fossil), acidification potential (AP), eutrophication potential (EP), human toxicity potential (HTP), ozone layer depletion potential (ODP), photochemical oxidants creation potential (POCP), fresh water and marine aquatic ecotoxicity potentials (FAETP and MAETP) and terrestrial ecotoxicity potential (TETP).
3.3.1. Goal and scope definition.
The goal of the study is to estimate the life cycle environmental impacts of the target IL with the aim of identifying the hotspots and improvement opportunities at an early stage of its development. The functional unit is defined as the ‘production of 1 kg of [P66614][124Triz]’ and the system boundaries are from ‘cradle to gate’ (Fig. 4), including the production of the target IL and all its precursors. In accordance with the goal of the study, the impacts from the use and end-of-life of the IL are excluded from the system boundary.
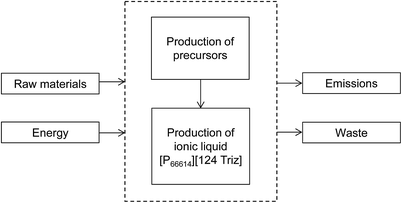 |
| Fig. 4 The system boundary for the production of [P66614][124Triz]. | |
3.3.2. Inventory analysis.
In this step of the methodology, material and energy requirements for the production of [P66614][124Triz] and its precursors are estimated, as described below.
3.3.2.1 Estimation of material requirements.
The raw materials required for the production of each precursor have been estimated using the stoichiometric relationships for the chemical reactions shown in Table 2. The estimations take into account the yields or conversions reported in the literature for each chemical reaction (see Section 3.2 for details). These estimates are given in Table 3. For example, the reaction for the production of [P66614][124Triz] shown in Table 2 has been balanced for the production of 1 kg of the IL as follows:
Table 3 Estimation of material requirements for the production of 1 kg of [P66614][124Triz] and its precursorsa,b
Compound |
Quantity (mol kg−1) |
Quantity (g kg−1) |
Reactants |
Quantity (mol kg−1) |
Quantity (g kg−1) |
By-products and waste |
Quantity (mol kg−1) |
Quantity (g kg−1) |
All quantities are expressed per kg of [P66614][124Triz].
The mass flows do not balance for the production of [P66614][OH] because of the use of the resin which is not considered in the mass balances. This is also the case for the solvents (ethanol in the production of [P66614][OH] and methyl ethyl ketone in the production of 1,2,4-triazole).
Estimated according to the preparation method reported in Taylor et al.7 The resin is assumed to be Amberlite IRN-78 (OH− form).
Estimated according to the preparation method reported in Petree et al.18
|
[P66614][124Triz] |
1.81 |
1000 |
[P66614][OH] |
1.81 |
905 |
OH− |
— |
30 |
1,2,4-Triazole |
1.81 |
125 |
|
|
|
[P66614][OH] |
1.81 |
905 |
[P66614]Cl |
1.81 |
940 |
Cl− |
1.81 |
64 |
Anion exchange resinc |
— |
34.5 |
|
|
|
Ethanolc |
— |
122 |
|
|
|
[P66614]Cl |
1.81 |
940 |
Trihexylphosphine |
2 |
574 |
Hydrochloric acid |
0.083 |
3 |
1-Chlorotetradecane |
2 |
466 |
Organic waste |
— |
97 |
Trihexylphosphine |
2 |
574 |
Phosphine |
2.4 |
84 |
Phosphine |
0.4 |
14 |
1-Hexene |
7.2 |
605 |
1-Hexene |
1.2 |
101 |
1-Chlorotetradecane |
2 |
466 |
Phosgene |
1.1 |
109 |
Waste water |
1.71 |
31 |
Hydrochloric acid |
1.5 |
54 |
Ditetradecyl ether |
0.04 |
16 |
1-Tetradecanol |
2.2 |
471 |
Ditetradecyl carbonate |
0.07 |
32 |
Catalyst |
— |
0.3 |
Hydrochloric acid |
0.73 |
26 |
|
|
Phosgene |
0.64 |
63 |
1,2,4-Triazole |
1.81 |
125 |
Formamide |
8.3 |
374 |
Ammonia |
2.35 |
40 |
Hydrazine hydrate |
3.24 |
162 |
Formic acid |
1.9 |
87 |
Methyl ethyl ketoned |
— |
557 |
Waste water |
5 |
90 |
|
|
Ammonium formate |
0.74 |
47 |
|
|
Formamide |
0.86 |
39 |
|
|
Hydrazine |
1.25 |
40 |
|
|
Organic waste |
— |
68 |
Thus:
The mass of the reactants is then equal to (see Table S1 in ESI† for the molecular weights):
1.81 moles [P66614][OH] × 500 g mol−1 = 905 g [P66614][OH] |
1.81 moles 1,2,4-triazole × 69 g mol−1 = 125 g 1,2,4-triazole |
Therefore, 905 g of [P66614][OH] and 125 g of 1,2,4-triazole are required to produce 1 kg of [P66614][124Triz], also generating 30 g waste (OH− from the anion exchange resin); see Table 3. The calculations for the rest of the raw materials can be found in Section 1 in ESI.†
3.3.2.2 Estimation of energy requirements.
As manufacturing data at the industrial scale are not available, a series of assumptions had to be made to estimate energy requirements. First, the theoretical energy consumption for the production of [P66614][124Triz] and the precursors has been estimated using the heat of formation of reactants and products based on the methods in Felder and Rousseau21 and described in Section 2 in ESI.† Secondly, only the energy requirements of reactors (heating and cooling) have been considered as it is not known what other unit operations may be needed in a future commercial production process and what their configuration and capacity might be. Therefore, energy consumption for separation, pumping and other operations is excluded from the estimation; however, the effect of this assumption is tested in the sensitivity and uncertainty analyses later in the paper. Finally, the theoretical energy consumption of reactors has been scaled-up to industrial scale using empirical factors that take into account energy losses.22 Thus, the estimated theoretical heat requirements for endothermic reactions have been multiplied by a factor of 4.2, assuming the heat is supplied by natural gas. Similarly, the theoretical amount of heat generated by exothermic reactions has been converted to actual cooling electricity requirements using a factor of 3.2. The results are summarised in Table 4; for further details, see Section 2 in ESI.†
Table 4 Estimation of energy requirements of reactors for the production of 1 kg of [P66614][124Triz] and its precursorsa
Compound |
Theoretical energy consumptionb (MJ kg−1) |
Scaled-up energy consumptionc (MJ kg−1) |
Assumptions |
All energy values expressed per kg of [P66614][124Triz].
Estimated using the heat of formation of reactants and products. Negative values represent an exothermic reaction and it has been assumed that the reactor is cooled using electricity.
Estimated using the theoretical energy values and the empirical factors in Mehrkesh and Karunanithi:22 a factor of 4.2 has been applied for the heat assuming the use of natural gas and a factor of 3.2 for electricity for cooling.
|
[P66614][124Triz] |
0.36 |
1.16 |
Electricity for cooling |
[P66614]Cl |
1.71 |
7.21 |
Natural gas for heating |
Trihexylphosphine |
0.31 |
1.30 |
Natural gas for heating |
1-Chlorotetradecane (1st reactor) |
0.44 |
1.43 |
Electricity for cooling |
1-Chlorotetradecane (2nd reactor) |
0.042 |
0.175 |
Natural gas for heating |
1,2,4-Triazole (1st reactor) |
1.57 |
6.59 |
Natural gas for heating |
1,2,4-Triazole (2nd reactor) |
0.03 |
0.12 |
Natural gas for heating |
Total heat (natural gas)
|
|
15.40
|
|
Total electricity
|
|
2.59
|
|
3.3.2.3 Life cycle modelling.
The material and energy data estimated in the previous two steps and given in Tables 3 and 4 have then been used as the inputs into the LCA model to estimate the impacts of [P66614][124Triz] production from ‘cradle to gate’. The background life cycle inventory data for the materials and energy have largely been sourced from the Ecoinvent database.23 The exceptions are 1-hexene, 1-tetradecanol, formamide and hydrazine hydrate, for which inventory data are not available and alternative chemicals have been assumed instead. For 1-hexene and 1-tetradecanol, LCA data for n-olefins and fatty alcohols have been used, respectively. This is a reasonable approximation because 1-hexene is an olefin or alkene compound24 and 1-tetradecanol is a type of fatty alcohol.25 Formamide data have been approximated with the data for formic acid because the former is derived from the latter;26 however, this means that the impacts from the conversion of formic acid to formamide are not considered. Finally, data for generic inorganic chemicals have been used to represent hydrazine hydrate as more specific data are not available.
All the raw materials are assumed to be transported to the respective production plants over a distance of 100 km. For energy, it has been assumed that the heat is supplied to the reactors by steam generated from UK natural gas and that electricity is sourced from the UK electricity mix. The waste streams shown in Table 3 are assumed to be treated as industrial wastewater. The system has also been credited for producing the by-products (see Table 3) and so avoiding the impacts which would have otherwise been generated if these products were produced in dedicated commercial plants. The avoided impacts have been estimated by subtracting the LCA impacts of the by-products produced in dedicated facilities (sourced from Ecoinvent) from the total impacts of producing [P66614][124Triz].
3.3.3. Impact assessment.
The LCA impacts of [P66614][124Triz], estimated using the inventory data detailed in the previous section, are presented in Fig. 5. For example, GWP is estimated at 6.3 kg CO2 eq. per kg [P66614][124Triz], after the avoided impact from the by-products (−1.1 kg CO2 eq. per kg) has been taken into account. Thus, the by-products save 15% of GHG emissions from the production of [P66614][124Triz]. Similarly to GWP, the credits for the by-products lead to a reduction in all other impacts, most significantly for HTP (28%), ADP elements (25%), ADP fossil (20%) and POCP (16%). The main contributors to the impacts and the opportunities for improvements are discussed in the next section.
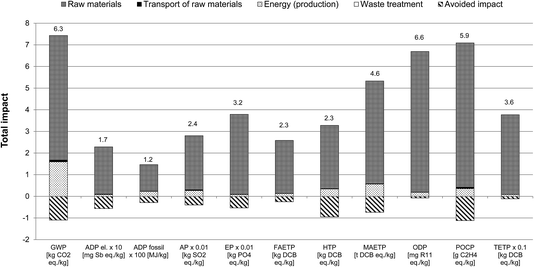 |
| Fig. 5 Environmental impacts of [P66614][124Triz] from cradle to gate (all impacts expressed per kg of [P66614][124Triz]. The values shown on top of each bar represent the total impact after the credits for by-products have been taken into account. The values for some impacts have been scaled to fit on the scale. The original values can be obtained by multiplying the value shown on the y-axis by the scaling factor given on the x-axis. Impact categories: GWP: global warming potential; ADP elements: abiotic depletion potential of elements; ADP fossil: abiotic depletion potential of fossil resources; AP: acidification potential; EP: eutrophication potential; FAETP: fresh water aquatic ecotoxicity potential; HTP: human toxicity potential; MAETP: marine aquatic ecotoxicity potential; ODP: ozone depletion potential; POCP: photochemical oxidants creation potential; TETP: terrestrial ecotoxicity potential. DCB: dichlorobenzene). | |
3.3.4. Interpretation of results.
3.3.4.1 Identification of hotspots and opportunities for improvements.
As indicated in Fig. 5, the raw materials used in the production of the precursors are the main environmental hotspot. In the case of GWP, they contribute 77% to the total impact, particularly phosphine, 1-hexene, methyl ethyl ketone, formamide and 1-tetradecanol (Fig. 6). The former two, used in the synthesis of trihexylphosphine, the precursor for [P66614]Cl, contribute around 23% each to the GWP of the raw materials. These, together with the other precursors used for [P66614]Cl production, contribute 47% to the total GWP.
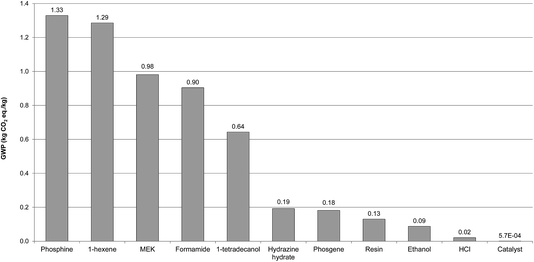 |
| Fig. 6 Contribution of different raw materials to the GWP of [P66614][124Triz] (GWP expressed per kg of [P66614][124Triz]. MEK: methyl ethyl ketone; resin: anion exchange). | |
Although only 84 g of phosphine is required for the production of 1 kg of [P66614][124Triz] (see Table 3), its GWP is eight times higher than the average GWP of inorganic chemicals (15.8 kg CO2 eq. per kg phosphine vs. 1.86 kg CO2 eq. per kg inorganic chemical). This is due to the energy-intensive production of white elemental phosphorus which is used to produce phosphine.27
By comparison, 1-hexene has a relatively low GWP (2 kg CO2 eq. per kg) but, since 605 g is needed to produce 1 kg of [P66614][124Triz], its overall contribution to the GWP is relatively high. Similarly, methyl ethyl ketone, formamide and 1-tetradecanol have a relatively low GWP (1.76, 2 and 1.4 kg CO2 eq. per kg, respectively), but are used in larger quantities (see Table 3), thus contributing 14–17% to the GWP of the raw materials.
Energy consumption is the second largest contributor to the GWP of [P66614][124Triz], causing 22% of this impact, mainly because of the highly endothermic reactions in the synthesis of [P66614]Cl and 1,2,4-triazole, as well as the cooling requirements in the synthesis of 1-chlorotetradecane (see Section 2 in ESI†).
The raw materials are also the main contributors to the other impact categories (Fig. 5). However, their average contribution is higher than for GWP (93%, with the highest single contribution from phosphine at 30%). The contribution of energy is relatively small (6.7% on average) and that of transport and waste treatment negligible.
Therefore, these results suggest that the main opportunities for improvements lie in reducing the impacts associated with the raw materials, either through their substitution or improvements in their respective production processes. Furthermore, energy integration and use of low-carbon options would help to reduce GHG emissions from the production of [P66614][124Triz].
3.3.4.2 Comparison of impacts with MEA.
To find out if [P66614][124Triz] is an environmentally sustainable alternative to MEA, commercially the most-widely used sorbent for CO2 capture, their impacts are compared in Fig. 7. The results suggest that [P66614][124Triz] has higher environmental impacts than MEA for 10 out of the 11 categories, ranging from 55% higher ADP fossil to 20 times higher ODP, with GWP nearly twice as high. The reason for a particularly high ODP is the trichloromethane used in preparation of the anionic resin, which contributes 90% to the total impact. As indicated in Fig. 7, the only impact for which MEA is an environmentally worse option than [P66614][124Triz] is HTP, which is 18 times higher for MEA – this is due to its high toxicity.28
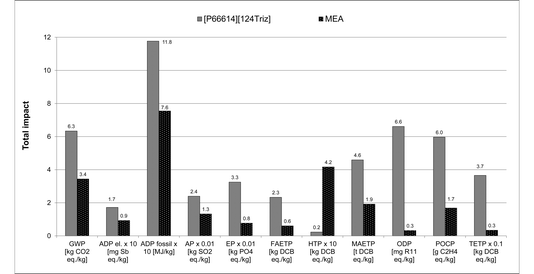 |
| Fig. 7 Comparison of environmental impacts of [P66614][124Triz] and MEA per kg of substance (data for MEA production sourced from Ecoinvent. The values for some impacts have been scaled to fit on the scale. The original values can be obtained by multiplying the value shown on the y-axis by the scaling factor given on the x-axis. For impacts nomenclature, see Fig. 5). | |
Therefore, these results suggest that [P66614][124Triz] is environmentally less sustainable than MEA and would not be a viable replacement alternative. However, given the goal of the study, this comparison has been carried out per kg of each substance produced, which may be misleading. Instead, they should be compared on the basis of their performance in a CO2 capture process. Since these data are not available for either of the substances, we consider their respective sorption capacities as the best proxy parameter available at present. The sorption capacity of [P66614][124Triz] is reportedly equal to 1.01 mol IL per mol CO2.7 For MEA, both the theoretical (estimated) and actual (pilot plant) absorption capacities are considered, equal to 2 (ref. 29) and 2.44 mol MEA per mol CO2,30 respectively. Therefore, on a mole-ratio basis, [P66614][124Triz] captures more CO2 than MEA. It has also been assumed that both sorbents are reused at a rate of 99.997%, based on the reported reuse of MEA.6,31
As shown in Fig. 8, the environmental impacts of the IL are now significantly higher than those of MEA, ranging from two times higher ADP fossil to 23–28 higher ODP for both the theoretical and actual MEA absorption capacities; global warming potential is eight times greater. The exception to this is HTP, which is on average 13 times higher for MEA. This is due to much more IL being required than MEA to capture the same amount of CO2 (557.5 g vs. 122 g or 149 g of MEA per kg of CO2). However, these results should be interpreted with care as they are based purely on the sorption capacities and, owing to a lack of data, they do not take into account other aspects, such as process operating conditions, regeneration and degradation of the sorbents, etc. Furthermore, given the lack of real industrial data, many assumptions had to be made to estimate the impacts of the IL, which could lead to uncertainties. Therefore, to test the robustness of the results, sensitivity and uncertainty analyses have been carried out as discussed next.
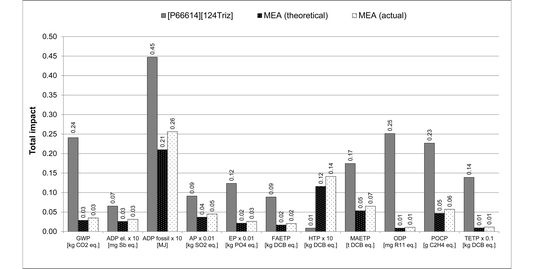 |
| Fig. 8 Comparison of environmental impacts of [P66614][124Triz] and MEA per kg of CO2 captured [The rate of reuse of 99.997% assumed for both [P66614][124Triz] and MEA. Data for CO2 absorption capacities sourced from literature: [P66614][124Triz]7 and MEA.7,29,30 For MEA, “theoretical” represents an estimated (Xie et al. 2010) and “actual” an average sorption capacity achieved in a pilot plant (Sønderby et al. 2013). The values for some impacts have been scaled to fit on the scale. The original values can be obtained by multiplying the value shown on the y-axis by the scaling factor given on the x-axis. For impacts nomenclature, see Fig. 5]. | |
3.3.4.3 Sensitivity and uncertainty analyses.
Sensitivity analysis.
The LCA findings presented in Section 3.3.4.1 suggest that the raw materials are the main hotspots in the production of [P66614][124Triz] across all the impacts. Energy is also a hotspot for GWP and ADP fossil. Thus, the assumptions for these two life cycle stages have been examined through the sensitivity analysis to understand how they may affect the impacts. For the raw materials for which proxy data were used (1-hexene, 1-tetradecanol, formamide and hydrazine hydrate), the effect of using these data has been considered by varying the impacts of these materials (arbitrarily) by ±50%. For energy, the validity of the theoretical estimates has also been tested by changing the consumption by ±50%.
Fig. 9 shows that the results are much more sensitive to the assumptions for the raw materials than for energy; this is to be expected since the former are the main hotspot. However, in both cases, the lowest values for the impacts of the IL are still significantly higher than for MEA. For example, if energy consumption is 50% lower than estimated, GWP is still 80% higher than for MEA. If the impacts of the above-mentioned four raw materials are 50% smaller than assumed originally, GWP is 50% higher than for MEA. Therefore, these findings suggest that the estimates for energy consumption and the assumptions for the missing raw materials data are robust.
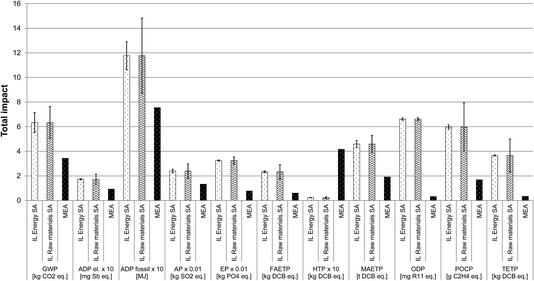 |
| Fig. 9 Sensitivity analysis for the assumptions on the raw materials and energy used in the production of [P66614][124Triz] and comparison of impacts with MEA (all impacts expressed per kg of substance. IL energy SA: ionic liquid energy sensitivity analysis. IL raw materials SA: ionic liquid raw materials sensitivity analysis. The values for some impacts have been scaled to fit on the scale. The original values can be obtained by multiplying the value shown on the y-axis by the scaling factor given on the x-axis. For impacts nomenclature, see Fig. 5). | |
Uncertainty analysis.
To test the level of confidence in the results, a Monte Carlo simulation with 10
000 iterations has been performed, generating the probabilistic results for the impacts. The simulation has been carried out using GaBi which enables the uncertainty to be estimated with respect to the quantities of materials and energy used in the system. As the quantities of the raw materials are quite robust, the focus of the uncertainty analysis has been on energy consumption, since these values were estimated rather than measured. Both the consumption of heat and electricity have been varied, again assuming an arbitrary range of ±50%.
The results of the Monte Carlo simulation are given in Fig. 10, with the horizontal lines representing the mean (expected) values and the error bars the spread of results between the 10th and 90th percentiles, indicating that we can expect impacts to fall between this range with a 90% confidence level. As can be seen, there is little variation in the impacts, with all categories still being much higher for the IL than MEA (except for HTP, as before). These results suggest a high confidence in the original findings that [P66614][124Triz] has significantly higher impacts than MEA. Therefore, in the next and final step of the methodology, recommendations can be made on how its impacts could be reduced.
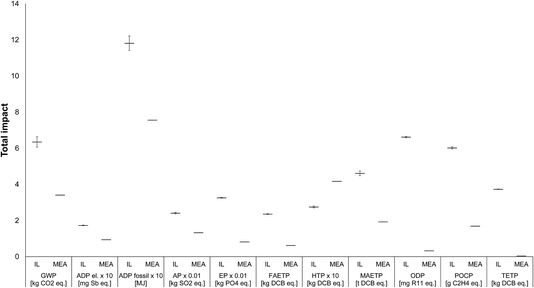 |
| Fig. 10 Uncertainty analysis related to the estimates of energy used in the production of [P66614][124Triz] and comparison of impacts with MEA [all impacts expressed per kg of substance. For the IL, the horizontal bars represent the expected (mean) values and the error bars the range between the 10th and 90th percentile. The values for some impacts have been scaled to fit on the scale. The original values can be obtained by multiplying the value shown on the y-axis by the scaling factor given on the x-axis. For impacts nomenclature, see Fig. 5]. | |
3.4. Step 4: Recommendations
As discussed in Section 3.3.4.1, the main hotspot in the life cycle of [P66614][124Triz] is the production of [P66614]Cl, which is a precursor for [P66614][OH], which in turn is one of the main raw materials used in the synthesis of [P66614][124Triz] (see Fig. 3). The synthesis route for [P66614]Cl considered in this study is based on Cytec's synthesis route for phosphonium-based ionic liquids, which uses trihexylphosphine as the main reactant. Trihexylphosphine is commonly synthesised from phosphine gas, which is highly toxic to humans when inhaled. For example, acute exposure to phosphine can cause respiratory and cardiovascular damage and liver or renal failure, which in some cases can lead to death.32 Furthermore, phosphine gas has a significantly higher GWP (15.8 kg CO2 eq. per kg) than the average inorganic chemical compound (1.86 kg CO2 eq. per kg) owing to the use of white phosphorus.
Alternatively, it is possible to synthesise [P66614]Cl from aluminium trialkyl and phosphorus trichloride, as suggested by Hall et al.33 and Umeno and Takita.34 The proposed synthesis route consists of a phosphine-free multi-step process for preparing quaternary phosphonium salts. However, a full LCA study should be conducted to evaluate the potential environmental advantages of producing [P66614]Cl via this alternative route. Furthermore, a significant reduction in ODP could be achieved by substituting trichloromethane, used for preparation of the anionic resin, with another non-ozone depleting substance. However, care should be taken in choosing the substance to avoid increasing other impacts, such as GWP or HTP.
4. Conclusions
This paper has proposed a novel methodology for estimating life cycle environmental impacts of ILs under development, with the aim of identifying hotspots and aiding synthesis and selection of more sustainable sorbents for CO2 capture. The example of [P66614][124Triz] was used to illustrate the application of the methodology by estimating the impacts of its production from cradle to gate and comparing it to MEA, currently the most-widely used sorbent for CO2 capture. The case study also shows how to deal with real-life situations in the early development stages of chemicals when scant data are available.
The results suggest that 10 out of 11 environmental impacts considered are higher for [P66614][124Triz] than for MEA. This includes GWP, which is estimated at 6.3 kg CO2 eq. per kg of [P66614][124Triz], compared to 3.4 kg CO2 eq. per kg of MEA. The only exception is human toxicity potential which is 18 times higher for MEA than for [P66614][124Triz]. When the sorption capacities of the two substances are taken into account, the difference in the impacts is even higher in favour of MEA. This is largely due to the many precursors and energy used in the synthesis of the IL.
Nevertheless, owing to a lack of data, it is not possible to determine at this stage whether the use of this (or any other) IL would lead to a more sustainable CO2 capturing process overall, when operating conditions are taken into account, including sorbent regeneration, reuse and degradation. For that reason, further research will be required to examine fully the environmental sustainability of using ILs as CO2 sorbents. However, one of the main limitations is that, unlike other established processes, the industrial production of ILs cannot be simulated using simulation software such as Aspen Plus, because ILs are not supported in the existing component databanks. This is a similar problem to that experienced with LCA databases which will need to be addressed in the near future to ensure more sustainable production of ILs.
It should also be noted that, although the focus here has been on ILs, the proposed methodology is applicable to other chemicals. Further research is recommended to demonstrate how it can be used to help improve the environmental sustainability of other chemicals at an early design stage.
Acknowledgements
This work was carried out as part of the “4CU” Programme Grant, aimed at sustainable conversion of carbon dioxide into fuels, led by The University of Sheffield and carried out in collaboration with The University of Manchester, Queen's University Belfast and University College London. The authors acknowledge gratefully the UK Engineering and Physical Sciences Research Council (EPSRC) for supporting this work financially (Grant No. EP/K001329/1).
References
- J. D. Figueroa, T. Fout, S. Plasynski, H. McIlvried and R. D. Srivastava, Advances in CO2 capture technology—The U.S. Department of Energy's Carbon Sequestration Program, Int. J. Greenhouse Gas Control, 2008, 2(1), 9–20 CrossRef CAS.
-
EASAC, Carbon capture and storage in Europe, European Academies Science Advisory Council, ISBN: 978-3-8047-3180-6. Available in: http://www.easac.eu/fileadmin/Reports/Easac_13_CCS_Web_Complete.pdf, 2013 Search PubMed.
-
P. Styring, D. Jansen, H. de Coninck, H. Reith and K. Armstrong, Carbon Capture and Utilisation in the Green Economy. Centre for Low Carbon Futures, Available at: http://co2chem.co.uk/wp-content/uploads/2012/06/CCU%20in%20the%20green%20economy%20report.pdf, 2011 Search PubMed.
- R. Notz, H. P. Mangalapally and H. Hasse, Post combustion CO2 capture by reactive absorption: Pilot plant description and results of systematic studies with MEA, Int. J. Greenhouse Gas Control, 2012, 6, 84–112 CrossRef CAS.
- E. S. Rubin, H. Mantripragada, A. Marks, P. Versteeg and J. Kitchin, The outlook for improved carbon capture technology, Prog. Energy Combust. Sci., 2012, 38(5), 630–671 CrossRef CAS.
- L. Zhu, G. W. Schade and C. J. Nielsen, Real-Time Monitoring of Emissions from Monoethanolamine-Based Industrial Scale Carbon Capture Facilities, Environ. Sci. Technol., 2013, 47(24), 14306–14314 CrossRef CAS PubMed.
- S. F. R. Taylor, C. McCrellis, C. McStay, J. Jacquemin, C. Hardacre and M. Mercy,
et al., CO2 Capture in Wet and Dry Superbase Ionic Liquids, J. Solution Chem., 2015, 1–17 Search PubMed.
- X. Zhang, X. Zhang, H. Dong, Z. Zhao, S. Zhang and Y. Huang, Carbon capture with ionic liquids: overview and progress, Energy Environ. Sci., 2012, 5(5), 6668–6681 CAS.
- J. F. Brennecke and B. E. Gurkan, Ionic Liquids for CO2 Capture and Emission Reduction, J. Phys. Chem. Lett., 2010, 1(24), 3459–3464 CrossRef CAS.
- B.-S. Lee and S.-T. Lin, Screening of ionic liquids for CO2 capture using the COSMO-SAC model, Chem. Eng. Sci., 2015, 121, 157–168 CrossRef CAS.
- R. G. Reddy, Novel applications of ionic liquids in materials processing, J. Phys.: Conf. Ser., 2009, 165(1), 012076 CrossRef.
- ISO, ISO 14040-Environmental Management – Life Cycle Assessment – Principles and Framework. Available at: http://www.iso.org/iso/catalogue_detail?csnumber=37456; 2006.
- ISO. ISO 14044-Environmental Management – Life Cycle Assessment – Requirements and Guidelines. Available at:http://www.iso.org/iso/catalogue_detail?csnumber=38498, 2006.
- N. Hollingsworth, S. F. R. Taylor, M. T. Galante, J. Jacquemin, C. Longo and K. B. Holt,
et al., Reduction of Carbon Dioxide to Formate at Low Overpotential Using a Superbase Ionic Liquid, Angew. Chem., Int. Ed., 2015, 54(47), 14164–14168 CrossRef CAS PubMed.
- C. J. Bradaric, A. Downard, C. Kennedy, A. J. Robertson and Y. Zhou, Industrial preparation of phosphonium ionic liquids, Green Chem., 2003, 5(2), 143–152 RSC.
- M. M. Rauhut, H. A. Currier, A. M. Semsel and V. P. Wystrach, The Free Radical Addition of Phosphines to Unsaturated Compounds, J. Org. Chem., 1961, 26(12), 5138–5145 CrossRef CAS.
-
H. Demail, J. C. Schweickert and P. Le Gars, Process for the preparation of alkyl chlorides, US Pat. US 5723704 A. Available at: http://www.google.co.uk/patents/US5723704. 1998.
-
H. E. Petree, J. R. Pociask and G. Jt. Method for direct preparation for 1,2,4-triazole from hydrazine and formamide, US Pat. US 4267347 A. Available at: http://www.google.co.uk/patents/US4267347, 1981.
-
Thinkstep, Gabi V6.4. Thinkstep, https://www.thinkstep.com/software/gabi-lca/, 2014 Search PubMed.
-
J. B. Guinée, M. Gorrée, R. Heijungs, G. Huppes, R. Kleijn and A. de Koning, Life cycle assessment: an operational guide to the ISO standards, Available at: http://media.leidenuniv.nl/legacy/new-dutch-lca-guide-part-1.pdf. 2001 Search PubMed.
-
R. M. Felder and R. W. Rousseau, Elementary Principles of Chemical Processes, ed. N. J. Hoboken, John Wiley & Sons, 2005 Search PubMed.
- A. Mehrkesh and A. T. Karunanithi, Energetic Ionic Materials: How Green Are They? A Comparative Life Cycle Assessment Study, ACS Sustainable Chem. Eng., 2013, 1(4), 448–455 CrossRef CAS.
-
Ecoinvent, Ecoinvent database 2.1., Ecoinvent Centre, http://www.ecoinvent.org/home.html, 2013 Search PubMed.
-
NCBI. 1-Hexene, National Center for Biotechnology Information. Available at: https://pubchem.ncbi.nlm.nih.gov/compound/1-hexene#section=Top, 2016.
- H. Hasturk, E. Goguet-Surmenian, A. Blackwood, C. Andry and A. Kantarci, 1-Tetradecanol Complex: Therapeutic Actions in Experimental Periodontitis, J. Periodontol., 2009, 80(7), 1103–1113 CrossRef CAS PubMed.
- R. W. Gora, S. J. Grabowski and J. Leszczynski, Dimers of Formic Acid, Acetic Acid, Formamide and Pyrrole-2-carboxylic Acid: an Ab Initio Study, J. Phys. Chem. A, 2005, 109(29), 6397–6405 CrossRef CAS PubMed.
-
W. A. Rickelton, Phosphine and Its Derivatives, Kirk-Othmer Encyclopedia of Chemical Technology, John Wiley & Sons, Inc., 2000 Search PubMed.
-
DOW, Material safety data sheet for Monoethanolamine, The DOW Chemical Company, Available at: http://msdssearch.dow.com/PublishedLiteratureDOWCOM/dh_0044/0901b80380044789.pdf?filepath=amines/pdfs/noreg/111-01388.pdf%26fromPage=GetDoc, 2003 Search PubMed.
- H.-B. Xie, Y. Zhou, Y. Zhang and J. K. Johnson, Reaction Mechanism of Monoethanolamine with CO2 in Aqueous Solution from Molecular Modeling, J. Phys. Chem. A, 2010, 114(43), 11844–11852 CrossRef CAS PubMed.
- T. L. Sønderby, K. B. Carlsen, P. L. Fosbøl, L. G. Kiørboe and N. von Solms, A new pilot absorber for CO2 capture from flue gases: Measuring and modelling capture with MEA solution, Int. J. Greenhouse Gas Control, 2013, 12, 181–192 CrossRef.
- M. R. M. Abu-Zahra, L. H. J. Schneiders, J. P. M. Niederer, P. H. M. Feron and G. F. Versteeg, CO2 capture from power plants: Part I. A parametric study of the technical performance based on monoethanolamine, Int. J. Greenhouse Gas Control, 2007, 1(1), 37–46 CrossRef CAS.
-
L. Assem and M. Takamiya, Phosphine: Toxicological overview, Health Protection Agency and Institute of Environment and Health, Cranfield Univeristy, Available at: https://www.gov.uk/government/uploads/system/uploads/attachment_data/file/338253/HPA_Phosphine_toxicological_overview_v1.pdf, 2007 Search PubMed.
-
R. E. Hall, A. Kessler and A. R. Mclain, Process for the preparation of phosphonium salts and phosphine oxides starting with aluminum trialkyl, US Pat. US 3459808 A. Available at: http://www.google.co.uk/patents/US3459808, 1969.
-
M. Umeno and S. Takita, Preparation process of quaternary phosphonium hydroxide, US Pat. US 4761493 A, Available at: http://www.google.ch/patents/US4761493, 1988.
Footnote |
† Electronic supplementary information (ESI) available. See DOI: 10.1039/c6fd00054a |
|
This journal is © The Royal Society of Chemistry 2016 |
Click here to see how this site uses Cookies. View our privacy policy here.