DOI:
10.1039/C5RA20356B
(Paper)
RSC Adv., 2015,
5, 103625-103635
Synthesis and characterization of castor oil based hybrid polymers and their polyurethane–urea/silica coatings
Received
6th October 2015
, Accepted 24th November 2015
First published on 25th November 2015
Abstract
Novel acrylated alkoxysilane castor oil (AASCO) with hydrolysable –Si–OCH3 was synthesized from castor oil, maleic anhydride and different weight percentages of 3-(trimethoxysilyl)propyl methacrylate (TMSPMA), via free radical copolymerization. The AASCO was characterized by 1H, 13C Nuclear Magnetic Resonance (NMR), Fourier transform infrared (FTIR) spectroscopy, gel permeation chromatography (GPC) and differential scanning calorimetry (DSC) techniques. This AASCO was further reacted with isophorone diisocyanate at NCO
:
OH ratio of 1.6
:
1 to get the isocyanate terminated silica hybrid polyurethane prepolymers. This work provides an effective and promising way to modify the castor oil backbone for high-performance coating application. The present work deals with the structural modifications of castor oil (CO), a renewable resource, to develop functional organic–inorganic hybrid polymers and their polyurethane–urea/silica (PU–urea/Si) coatings. For this purpose, a new acrylated alkoxysilane castor oil (AASCO) with hydrolysable –Si–OCH3 was synthesized from CO, maleic anhydride and different weight percentages of 3-(trimethoxysilyl)propyl methacrylate (TMSPMA), via free radical copolymerization. The AASCO was characterized by 1H, 13C Nuclear Magnetic Resonance (NMR), Fourier transform infrared (FTIR) spectroscopy, gel permeation chromatography (GPC) and differential scanning calorimetry (DSC) techniques. This AASCO was further reacted with isophorone diisocyanate at NCO
:
OH ratio of 1.6
:
1 to get the isocyanate terminated silica hybrid polyurethane prepolymers. The thermo-mechanical properties of the coating films were studied using Dynamic Mechanical Analysis (DMA), Thermogravimetric Analysis (TGA) and Universal Testing Machine (UTM). The coating films were evaluated for their salt spray resistance, swelling and contact angle (CA) properties. The CO modified silane based hybrid coatings have shown better mechanical, viscoelastic and CA properties when compared to control (CO based PU–urea) coatings. Similarly, the hybrid coating films with higher TMSPMA content have shown better thermal stability, less swelling and enhanced CA properties [water CA (102°), diiodomethane CA (72.75°)] and also exhibited excellent corrosion resistance properties.
1. Introduction
Renewable resources are emerging as interesting sustainable platform to design and develop eco-friendly functional polymers which can compete or even surpass the existing petroleum-based polymers on a cost and performance basis.1,2 Amongst renewable resources, plant oils are being used for the development of polyols and polyurethanes (PUs) for coatings and other applications.3,4 Vegetable oils such as soybean, cotton seed, linseed, castor, etc. are important sources for the development of polymers with excellent properties, however, the unique backbone chemistry of castor oil makes it the material of choice for the development of PUs. CO serves as a natural polyol for the preparation of PU due to its inherent hydroxyl functionality. The long fatty acid chain in CO backbone provides flexibility and water resistant properties to the resultant PUs.5–7 However, oil based PUs possess relatively low thermal stability, rigidity and strength required for structural applications by themselves.8–10 The suitable structural modifications of CO backbone and/or development of organic–inorganic hybrid polyurethane network are being implied to improve these properties for which a wide array of materials and techniques are available to develop organic–inorganic hybrid materials. However, the utilization of silane and sol–gel chemistry offers versatility to design and develop PU hybrids with improved properties for coating applications.
There are several routes to improve the properties of plant oil based PU. Several methods have been explored, such as the introduction of nano particles,11–19 sol–gel/alkoxy silane monomers as end capping reagent for PU coatings.20–25 Raju et al.2 developed hybrid coating from castor oil, modified through Si–OCH3 groups in the backbone chain with IPDI and were used to prepare PU/urea–silica based hybrid coatings. Improved mechanical and viscoelastic properties were claimed by the authors. Liang Shen et al.26 developed new silanized castor oil (MSCO) composed of castor oil and 3-mercaptopropyl trimethoxysilane via thiol–ene coupling. This MSCO was used as a functional polyol in the preparation of a series of bio-based PU/siloxane hybrid coatings through reactions with different castor oil and IPDI ratios. In all these materials silicon chemistry has played an important role in improving the properties or attains some unusual characteristics. Even addition of a very small amount of silica causes a crucial improvement of properties of modified materials. In the quest of eco-friendly hybrid materials, the reactive silanes and plant oils chemistry have to play a definitive role in coming years especially for functional coatings and composite development.
As described above most of the approaches developed hybrid materials by adding external organo silane coupling groups, in our an attempt to find new hybrid materials and use of the CO as renewable resources, synthesis of new renewable alkoxy silane functional material (AASCO) using CO, MA through TMSPMA has been investigated. The above synthesized AASCO has been used as functional polyol and IPDI to get moisture cured PU–urea/silica hybrid coating films. The effect of the TMSPMA on coating properties of the cross linked silica hybrid polyurethane–urea coating films was also evaluated. Thermal, mechanical and CA properties of these hybrid films were investigated by using DMTA, TGA, UTM and CA.
2. Experimental section
2.1. Materials
Castor oil (CO) was obtained from the local market with characteristic properties such as hydroxyl value 162 mg per KOH per g and acid value 2 mg per KOH per g. Isophorone diisocyanate (IPDI) was supplied by Evonik industries, Germany. 3-(Trimethoxysilyl)propyl methacrylate (TMSPMA) was obtained from Aldrich (Milwaukee, WI). Maleic anhydride (MA), dibutyltin dilaurate (DBTDL), azobisisobutyronitrile (AIBN), and other chemicals were of analytical grade and were used without further purification.
2.2. Synthesis of CO and MA adduct
CO and MA adduct was synthesized in a four necked reaction flask equipped with a mechanical stirrer and a thermometer by charging castor oil (100 grams) and maleic anhydride (4 grams) and the reaction was maintained at 90 °C. The reaction was stopped when the anhydride peak at 1850 cm−1 disappears in the FT-IR spectra. The modified oil was named as COMA. The acid value (AV) and hydroxyl value (OHV) of COMA were measured according to the ASTM standards D 1639-89 and D 4274-94, respectively. Their characteristics are summarized in Table 1. The reaction scheme for the synthesis of the COMA is shown in Scheme 1.
Table 1 The Characteristics of CO, COMA and AASCO
Sample code |
Mw |
Mn |
Mz |
Polydispersity |
HV (mg KOH per g) |
AV (mg KOH per g) |
Viscosity (mPa s) at 25 °C |
Tg (°C) |
(Mw/Mn) |
(Mz/Mn) |
CO |
1582 |
1316 |
1782 |
1.2 |
1.35 |
162 |
2 |
640 |
−30.68 |
COMA |
1878 |
1415 |
2181 |
1.32 |
1.54 |
138 |
26 |
890 |
−28.3 |
AASCO-0.05 |
2065 |
1553 |
2724 |
1.32 |
1.75 |
138 |
26 |
920 |
−28.1 |
AASCO-0.15 |
2108 |
1552 |
2774 |
1.35 |
1.78 |
138 |
26 |
980 |
−27.7 |
AASCO-0.3 |
2249 |
1692 |
2794 |
1.32 |
1.65 |
138 |
26 |
1000 |
−26.8 |
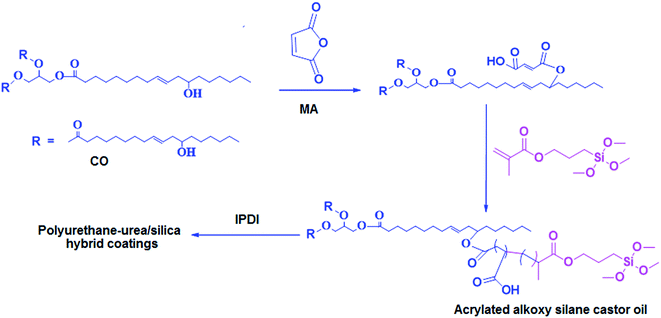 |
| Scheme 1 Schematic & synthetic route for hybrid polymers and their coatings. | |
FTIR (KBr): cm−1: 3462 (–OH), 3008 (
CH–), 1746 (–C
O), 1658 (–C
C–).
1H NMR (CDCl3, 300 MHz): δ (ppm) = 6.25–6.4 (HOOC–C![[H with combining low line]](https://www.rsc.org/images/entities/char_0048_0332.gif)
C
–OCO–), 5.3–5.56 (C![[H with combining low line]](https://www.rsc.org/images/entities/char_0048_0332.gif)
C
), 5.28–5.31 (R–O–CH2–C
(–OR)–CH2–O–R), 4.11–4.32 (R–O–C
2–CH(–OR)–C
2–O–R), 3.86 (H2C–C
(–OCO–CH
CH–COOH)–CH2–), 3.59–3.61 (–CH
CH–CH2–CH(O
)–CH2–), 2.74–2.78 (–CH
CH–CH2–C
(OH)–CH2–), 2.2–2.32 (–OCO–C
2–CH2), 1.22–1.3 (CH2 chain), 0.85–0.89 (CH3); 13C NMR(CDCl3, 125 MHz): δ (ppm) = 172–173.6 (R–(O
O)–R), 165–166.6 (HOO
–CH
CH–COO–CH–), 123–133 (–CH
CH–), 73.5 (HOOC–CH
CH–COO–
H–), 71.3 (CH
CH–CH2–
H(OH)CH2–CH2–), 68.7 (R–O–CH2–
H(–OR)–CH2–O–R), 61.9 (R–O–
H2–CH(–OR)–
H2–O–R).
2.3. Synthesis of acrylated alkoxysilane castor oil (AASCO)
AASCO was synthesized by charging COMA with various mole ratios of TMSPMA and AIBN (0.1%) catalyst into a two-necked flask placed over an isothermal bath equipped with mechanical stirrer and nitrogen inlet. The reactant mixture was slowly heated up to 75 °C and maintained at 75–80 °C under nitrogen atmosphere for 5 h. The modified oil was named as AASCO. The characteristics of the obtained oils are summarized in Table 1. The compositions of the different hybrid polymers and mole ratios are shown in Table 2.
Table 2 Various weight ratios used to prepare the different hybrid polymers and their coatings
Sample code |
CO (grams) |
MA (grams) |
TMSPMA (grams) |
OH/NCO |
VOC content in % weight |
COMA |
100 |
4 |
— |
— |
— |
AASCO-0.05 |
100 |
4 |
0.05 |
— |
|
AASCO-0.15 |
100 |
4 |
0.15 |
— |
— |
AASCO-0.3 |
100 |
4 |
0.3 |
— |
— |
COPU |
|
— |
— |
1/1.6 |
5 |
AASCOPU-0.05 |
|
— |
— |
1/1.6 |
5 |
AASCOPU-0.15 |
|
— |
— |
1/1.6 |
5 |
AASCOPU-0.3 |
|
— |
— |
1/1.6 |
5 |
The products were further characterized by FTIR and 1H & 13C NMR.
FTIR (KBr): cm−1: 3462 (–OH), 3008 (
CH–), 1746 (–C
O), 1658 (–C
C–), 1083 (Si–OCH3), 1188 (–Si–CH2–).
1H NMR (CDCl3, 300 MHz): δ (ppm) = 3.81 (–H2C(–CH3)–OCO–C
2–CH2–CH2–Si–OCH3), 3.59–3.61 (–CH
CH–CH2–CH(O
)–CH2–), 3.41 (–H2C(–CH3)–OCO–CH2–CH2–CH2–Si–OC
3), 1.92 (–H2C(–C
3)–OCO–CH2–CH2–CH2–Si–OCH3); 13C NMR (CDCl3, 125 MHz):δ (ppm) = 73.6 (H
–OCO–CH
CH–),67.8 ((3HC)–CH–COO–
H2–CH2–CH2–Si–OCH3), 51.3 (COO–
H2–CH2–CH2–Si–OCH3), 18.1 ((3H
)–CH–COO–
H2–CH2–CH2–Si–OCH3).
2.4. Synthesis of polyurethane/urea–silica hybrid films
The hybrid coating films were prepared using the formulation as summarised in Table 2. AASCO was further reacted with IPDI in presence of 0.01 wt% of DBTL as catalyst at NCO/OH eq. ratios of 1.6
:
1 at around 75–80 °C to get different –NCO terminated hybrid prepolymers. The above prepared –NCO terminated hybrid prepolymers (AASCOPU) were used further for the preparation of final coatings. The hybrid –NCO terminated prepolymer films were cast on releasing paper using manual driven square applicator. The films were kept at atmospheric moisture and laboratory humidity condition for 40 days for moisture cure and also to carry out the hydrolysis reactions of alkoxy silane groups of AASCO. The disappearance of –NCO peak at 2270 cm−1 from FT-IR spectroscopy was taken as a measure of complete cure. The compositions of the different hybrid PUs, mole ratios and their volatile organic compounds (VOC) in % weight are shown in Table 2.
3. Characterization
Characterization of CO and modified oils was done by gel permeation chromatography (GPC: Varian prostar chromatography model-210, USA). Samples were dissolved in THF by taking 0.1 g/10 mL and experiments were carried out at a flow rate of 1.0 mL min−1 using THF as the mobile phase. Columns were calibrated with Aldrich polystyrene standards. The chemical structures of oil, hybrid prepolymers and their PU–urea films were elucidated by using Fourier-Transform Infrared Spectroscopy (FT-IR) (Perkin-Elmer Spectrum one). The 1H & 13C Nuclear Magnetic Resonance spectroscopy (NMR) spectra were recorded in CDCl3 solvent using a Varian-Inova-300 MHz spectrometer. Thermal analysis was done by a Dynamic Mechanical Analysis (DMA) TAQ800 instrument (TA Instruments, USA) in tensile mode at a frequency of 1 Hz with a heating rate of 3 °C min−1 by scanning the films from −60 °C to 150 °C. Thermogravimetric analysis (Mettler Toledo TGA 1/SDTAe) was carried out with a heating rate of 10 °C min−1 under a N2 atmosphere. Differential scanning calorimetry (DSC) analysis was recorded on a TAQ 2000 (TA Instruments, USA). Samples were heated from −70 °C to 150 °C at a heating rate of 10 °C min−1 under nitrogen atmosphere at a flow rate of 30 mL min−1. The viscosity of oil and their hybrid prepolymers were determined by using ICI cone & plate viscometer VR-4410 with 900 rpm motor speed. Contact angle was measured by DSA 100 (KRUSS) instrument through sessile drop method. The tensile properties films were measured by Universal Testing Machine using Instron 3367 according to ASTM D2370-98. Pull-off adhesion strength of the coatings on the mild steel (MS) was measured following ASTM D4541-02 using the PosiTest AT-A Automatic Adhesion Tester (Defelsko corporation, USA). The scratch hardness of coating was determined by using a Sheen automatic scratch tester-REF 705 (Komal scientific, India). Salt spray test of coated panels as such was performed according to ASTM B117 using 5% NaCl solution with an exposure time of 600 h.
4. Results and discussion
4.1. Structural analysis of CO, COMA and AASCO
The structural elucidation of prepolymers can be characterized using both FTIR and NMR spectroscopic techniques. The polymerization products of the oil with acrylic siloxane carry the characteristic features of MA, TMSPMA and the glyceride structures. FT-IR spectra of CO, COSA and AASCO prepolymers are compared in Fig. 1. For CO, the broad peak at 3434 cm−1 can be ascribed to the –OH functional group absorption, while that at 1640 cm−1 can be assigned to the –HC
CH– double bond stretching frequency. When CO reacts with MA, the –OH peak was evidently decreased, while the double bond peak was enhanced. No peaks corresponding to cyclic anhydride at 1779 cm−1 and 1849 cm−1 were found, indicating that almost all of the maleic anhydride was consumed in the reaction with CO. On the other hand the AASCO samples shows the bands in the region between 1100 and 1000 cm−1 are attributed to Si–OCH3.27 In fact the absorptions due to silanol and C–O groups cannot be confidently assigned due to several medium and weak intensity bands in the range 1090–1040 cm−1. However, as per analysis reports28,29 strong peak near 1090 cm−1 is commonly present in the IR spectrum of compounds with a Si–O–C linkages, whereas an 1190 cm−1 band is typical for Si–O–CH3 compounds. 1H and 13C NMR spectra of CO, COMA and AASCO were shown in the Fig. 2 and 3 respectively. The exact resonance signal positions have been reported from the expanded spectrum for each resonance area. 1H-NMR spectra of CO, COMA and AASCO are comparable. However, considerable variation in peak intensity of signals of protons attached to double bonds was observed owing to varying extent of unsaturation and hydrolysable methoxy silane groups (–Si–OCH3). Fig. 2 shows 1H NMR of the AASCO in which the peaks appearing at 3.4 (peak, n) ppm (–Si–OC
3); 3.81 (peak, l) (–H2C(–CH3)–OCO–C
2–CH2–CH2–Si–OCH3), 3.59–3.61 (peak, d) (–CH
CH–CH2–CH(O
)–CH2–), 1.92 (peak, o) (–H2C(–C
3)–OCO–CH2–CH2–CH2–Si–OCH3), and 6.2–6.4 ppm (peak, k) (HOOC–C![[H with combining low line]](https://www.rsc.org/images/entities/char_0048_0332.gif)
C
–OCO–) indicate the presence of unreacted acrylate double bond in the polymer. Several multiplets at δ 1.2 to 1.8 ppm correspond to protons of various groups bound to the linear carbon chain (–CH2–CH2–).30,31 Similar conclusions can be drawn for the assignment of peaks in the 13C NMR spectrum (Fig. 3) of the same sample showing the similar feature,2,32 except additional peaks at 165–167 (peak, 9), (–
OOH), 73.6 (peak, 10) (H
–OCO–CH
CH–), 67.8 (peak, 12) ((3HC)–CH–COO–
H2–CH2–CH2–Si–OCH3), 51.3 (COO–CH2–CH2–CH2–Si–O
H3), 18.1 (peak, 13) ((3H
)–CH–COO–CH2–CH2–CH2–Si–OCH3) in AASCO spectrum. The FT-IR spectra of the hybrid coating films are shown in Fig. 4 with their characteristic bands appearing in the range of 3000–3400 cm−1, a combination of urethane carbonyl –NH–CO–O with secondary amide peaks and ester carbonyl –CO–O at 1740 cm−1, and a combination of –N–H out-of-plane bending and –C–N stretching at 1526 cm−1. All of the absorbance present in the spectrums of the hybrid coating films is a characteristic of CO based coating films displaying symmetric and asymmetric stretching vibration of the aliphatic –CH2 group absorptions at 2925 and 2855 cm−1, together with –CH2 bending vibrations at 1364 cm−1. All hybrid coating films shows the condensation results in the formation of silica network (Si–O–Si linkages) as compared to the control PU–urea (COPU) coating films.
 |
| Fig. 1 FTIR spectra of the CO, COMA and AASCO. | |
 |
| Fig. 2 1H NMR spectrum of CO, COMA and AASCO. | |
 |
| Fig. 3 13C NMR spectrum of CO, COMA and AASCO. | |
 |
| Fig. 4 FTIR spectra of coating films. | |
The molecular weight and molecular weight distribution of oil based polymers were monitored by GPC technique using tetrahydrofuran solvent. The number (Mn), average (Mw) molecular weights, viscosity and DSC data of CO along with prepolymers are presented in Table 1. It is found that the molar mass average values of AASCO is slightly higher (Mn: 1692; Mw: 2249) in comparison to the molar mass average values of COMA and CO (Mn: 1415 & 1316; Mw: 1878 & 1582, respectively). The change in TMSPMA mole ratio content induces change in viscosity, molecular weight and glass transition temperature (Tg) of the polymer.
4.2. DMA analysis
The DMA technique is used to detect the viscoelastic behavior of coating films and provides quantitative results for the tensile storage modulus E′ and the corresponding loss modulus E′′. E′ and E′′ characterize the elastic and viscous component of a material under deformation and E′ is a measure of the mechanical energy stored under load. The tan
δ compares the amounts of dissipated and stored energy. The loss factor tan
δ can then be expressed as the quotient of loss and storage, E′′/E′. The Tg values of hybrid coating films are obtained from the peaks of tan
δ curves. The crosslink density (υe) of hybrid coting films was calculated by using eqn (1)where R is the universal gas constant, and T the temperature in K. E′ values in the rubbery region at T > Tg were taken to calculate υe by using eqn (1).
To observe the effect of TMSPMA weight percent on dynamic mechanical properties, Fig. 5 and 6, show the storage modulus, loss modulus and loss tangent as a function of temperature and the dynamical properties of coating films summarized in Table 3. As shown in the figures, hybrid PU–urea films behave similar homogeneous polymeric networks with respect to E′ curves. In the glassy region, the E′ follow the expected trends. The Tg values of COPU, AASCOPU-0.05, AASCOPU-0.15, and AASCOPU-0.3 are 23.58, 24.79, 26.14, and 27.29 °C, respectively. The E′ values of COPU, AASCOPU-0.05, AASCOPU-0.15, and AASCOPU-0.3 hybrid coating films are 5.31 × 107, 6.312 × 107, 7.554 × 107, and 7.864 × 107, respectively at 20 °C, which indicates that good mechanical integrity of the hybrid coating films. The increase in E′ and Tg with increasing TMSPMA weight percent suggest that the hybrid films became harder due to increase in crosslink density. The addition of TMSPMA leads to a moderate increase in Tg and storage modulus due to Si–O–Si network and cross linked structures, which retard segmental motion of the polymer23,33 and increases the Tg and E′.
 |
| Fig. 5 log E′, tan δ vs. temperature DMA curves of coating films. | |
 |
| Fig. 6 log E′′ vs. temperature DMA curves of coating films. | |
Table 3 DMA data of coating films
Sample code |
Tg (°C) |
tan δmax |
E′ at 20 °C [Pa] |
E′ at Tg + 5 °C [Pa] |
υc (Tg + 5 °C) (mol cm−3) |
COPU |
23.58 |
0.79 |
5.31 × 107 |
1.606 × 107 |
2.06 × 10−3 |
AASCOPU-0.05 |
24.79 |
0.82 |
6.312 × 107 |
1.689 × 107 |
2.235 × 10−3 |
AASCOPU-0.15 |
26.14 |
0.82 |
7.554 × 107 |
1.694 × 107 |
2.232 × 10−3 |
AASCOPU-0.3 |
27.29 |
0.88 |
7.864 × 107 |
1.953 × 107 |
2.564 × 10−3 |
4.3. Contact angle and swelling properties
The contact angle (CA) measurement was carried out on the hybrid PU–urea films and the control PU (COPU) using water and diiodomethane. Their corresponding CA and surface free energies (SFE) data summarized in Table 4. The control PU–urea film shows the wettability properties with water CA of about 63.8° (COPU), when the CO were modified with TMSPMA, the hybrid film surfaces showed water CA of about 102° (AASCOPU-0.05, 75.12°; AASCOPU-0.15, 85.9°; AASCOPU-0.3, 102.4°). The improvement of the hydrophobic capacity of hybrid films can be confirmed that the improvement of the hydrophobic capacity of hybrid films by increasing TMSPMA weight ratio due to the formation of Si–O–Si linkage by moisture curing process while oleophobic properties were achieved in a similar manner with diiodomethane. Therefore, it can be concluded that the hydrophobicity and oleophobicity of the hybrid coating films can be effectively turned by varying the feed ratio of TMSPMA.
Table 4 Contact angle & swelling properties data of coating films
Sample code |
Contact angle (θ) |
Wt (%) |
WL (%) |
Q (%) |
Water |
DIM |
SFEa (mN m−1) |
Values determined by KRUSS advance software. |
COPU |
63.8 |
45.6 |
48.13 |
132.03 |
2.5 |
0.76 |
AASCOPU-0.05 |
75.12 |
49.1 |
41.27 |
127.4 |
1.74 |
0.61 |
AASCOPU-0.15 |
85.9 |
58.5 |
33.08 |
123.6 |
1.59 |
0.42 |
AASCOPU-0.3 |
102.4 |
72.75 |
22.22 |
113.4 |
1.08 |
0.33 |
Table 4 also shows the water & toluene swelling as a function of immersion time (72 h) of the coating films. The swelling ratio measurements of the cured films can be used to observe water resistance and hydrophobicity. The swelling ratio (Q%) in water is calculated using following equation.2,23
Swelling ratio (Q), % = [(Ws − Wd)/Wd] × 100 |
where
Wd is the weight of the dry sample and
Ws is the weight of the swollen sample.
In toluene, calculation was done according to the following equations.
Wt (%) = [(W1 − W2)/W2] × 100 |
Wt: amounts of toluene absorption by hybrid film.
WL (%) = [(W0 − W2)/W0] × 100 |
WL: amounts of hybrid films dissolved into the toluene solution. where known weight (
W0) of coating films, the towel down dry sample weight (
W1) and the oven-dried sample weight (
W2) were obtained.
All of the films exhibited significant swelling in toluene at various TMSPMA ratio, as shown in Table 4. Based on overall swelling studies, the addition of TMSPMA typically decreased the degree of swelling indicating the formation of cross linked networks. This is expected because the concentration of Si–O–Si network increases drastically with the addition of TMSPMA. This was also supplemented by contact angle measurement wherein contact angle was found to increase with increasing content of silica in the coating films in comparison to control.
4.4. Tensile, adhesion, hardness and MEK rub of coatings
The tensile, adhesion, hardness and MEK rub of coatings data of hybrid coating films are summarized in Table 5. The data suggest that the elongation decreases as the weight percent of TMSPMA increases. In the case of PU–urea obtained with only CO shows more elongation. The maximum displacement values continuously decreased with the addition of TMSPMA which is an expected outcome due to the increase in the amount of the silica content. The adhesion strength and scratch hardness values of hybrid coating films follow the order COPU > AASCOPU-0.05 > AASCOPU-0.15 > AASCOPU-0.3. All these properties were found to depends on TMSPMA weight percent as shown in Table 5. All these coating were found to pass >200 MEK rubs (ASTM D4752 standard test method) indicating a good film properties. The overall mechanical behavior of the cross linked PU–urea hybrids is dependent on the TMSPMA weight percent, hard segment content, cross linking density and intermolecular interactions between their hard segments.
Table 5 Tensile, adhesion strength, scratch and MEK rub properties of coating films
Sample code |
Tensile strength (MPa) |
Max. displacement (mm) |
Adhesion strength (MPa) |
Scratch hardness (kg) |
MEK rub |
COPU |
5.9 |
133.12 |
2.79 |
2.4 |
>200 |
AASCOPU-0.05 |
6.76 |
126.27 |
2.89 |
2.4 |
>200 |
AASCOPU-0.15 |
6.89 |
116.84 |
3.19 |
2.6 |
>200 |
AASCOPU-0.3 |
6.93 |
108.15 |
3.54 |
2.8 |
>200 |
4.5. Salt spray test
This test gives an estimate of corrosion resistance ability of the coating material when coated on the MS panels. The most conversant corrosion of this type is the rusting of iron exposed to moist atmosphere. Salt spray test results of coating panels were observed periodically and the images for 600 h of exposure are shown in Fig. 7. The hybrid coating formulations were found to provide substantial improvement over the control COPU formulation with respect to blister resistance as well as adhesion to metal substrate. However, the hybrid PU–urea films surface is covered with the Si–O–Si linkages collectively providing barrier to water and corrosive agents leading to enhance the corrosion protection efficiently of the hybrid PU–urea coatings.12
 |
| Fig. 7 Salt spray images of coating films: (a) COPU; (b) AASCOPU-0.05; (c) AASCOPU-0.15 and (d) AASCOPU-0.3. | |
4.6. TGA analysis
The thermal degradation studies of coating films was done in a N2 environment at a heating rate of 10 °C min−1 and are shown in Fig. 8. It was noticed from the TGA profile that the thermal stability of the hybrid coating films is higher than the control coating film (COPU). The initial decomposition around 100–150 °C was due to the volatilization of the residual solvent as well as the entrapped moisture present in the coating films. As found in the previous study,34,35 all oil based PU–urea reveals three distinct stages of decomposition in the curves. In the first stage, polyurethane decomposed slowly until 335 °C which accounted for the first 20–25% of the weight loss. Weight loss was very rapid in the temperature range of 300–500 °C. The main degradation process can be observed at temperatures around 350 °C to 380 °C. The comparative thermal stability of various coating films was evaluated from TGA data. The values of Ton (initial decomposition temperature for degradation step), Tend (final decomposition temperature for degradation step), Tmax (maximum decomposition temperature for degradation step), % weight remaining (at 300 and 400 °C) and Td (90%) (decomposition temperature at 90% weight loss) are summarized in Table 6. All the hybrid samples show three steps of degradation profile. The data in table show that the thermal stability of the coating films increased with increasing the TMSPMA mole ratio. The above behavior might be depending on the network structure and other chemical structural factors such as steric strain and conformational arrangements of the groups. The addition of cross linker leads to a significant increase in thermal stability due to the presence of Si–O–Si linkages. All these factors complicated the understanding of the relationship between crosslinking density and thermal stability of the coating films.
 |
| Fig. 8 TGA & DTG curves of coating films. | |
Table 6 Thermal analysis data of coating films
Sample code |
Ton (°C) |
Tmax (°C) |
Td (50%) (°C) |
Tend (°C) |
% weight remaining at |
Td (90%) (°C) |
Tmax1 |
Tmax2 |
300 (°C) |
400 (°C) |
COPU |
274 |
320 |
360 |
363 |
472 |
89.29 |
31.69 |
441 |
AASCOPU-0.05 |
283 |
328 |
366 |
374 |
478 |
93.52 |
38.27 |
449 |
AASCOPU-0.15 |
288 |
331 |
371 |
378 |
480 |
94 |
39.01 |
450 |
AASCOPU-0.3 |
290 |
334 |
374 |
381 |
481 |
94.2 |
40.25 |
451 |
5. Conclusions
A series of renewable resource based hybrid polymers and their PU–urea/silica hybrid coatings l have been prepared using CO, MA and different mole ratios of TMSPMA. The synthesized acrylated alkoxysilane functional castor oil was further reacted with IPDI to get isocyanate terminated silica hybrid PU prepolymer. The excess isocyanate of the prepolymers was cured under atmospheric moisture to get PU–urea/silica hybrids coating films. Hybrid coating films were studied for its thermal, tensile, and viscoelastic properties using different techniques. The swelling properties, contact angle and other coating properties were directly dependent on the mole ratio of TMSPMA. The hydrophobic and oleophobic character of the hybrid coating films was found to increase with an increasing TMSPMA mole ratio. The CO based PU–urea/silica hybrid coatings show better thermal, mechanical and viscoelastic properties in comparison to the control (castor oil based PU–urea COPU) coatings. This may be due to the reinforcement effect and covalent attachment of silica in castor based PU–urea backbone. The crosslink density were also found to increase with increasing TMSPMA mole ratio content in the hybrid coating films resulting in higher modulus as measured by DMTA and thermal stability as measured by TGA. Therefore, the judicious modification of CO with TMSPMA monomer and control over the crosslinking are critical criterion for the design of high performance coating applications. Based on the overall property analysis, this type of hybrid coatings is expected to be a good candidate as protective coating in moist environment. In this study, we have been able to show a new strategy to design castor oils based PU–urea/silica hybrid coatings films with improved thermal, mechanical and corrosion resistance which is expected to reduce the use of petroleum based raw materials for the development of coatings.
Acknowledgements
Author would like to thank Asian Paints staffs for their support in characterization and the authors also thank V. P. Technology and Asian Paints Management for their permission to publish this work.
References
- D. L. Kaplan, Biopolymers from renewable resources, Springer, New York, 1998 Search PubMed.
- S. Allauddin, R. Narayan and K. V. S. N. Raju, ACS Sustainable Chem. Eng., 2013, 1, 910–918 CrossRef.
- D. P. Pfister, Y. Xia and R. C. Larock, ChemSusChem, 2011, 4, 703–717 CrossRef CAS PubMed.
- G. Lligadas, J. C. Ronda, M. Galià and V. Cádiz, Biomacromolecules, 2010, 11, 2825–2835 CrossRef PubMed.
- D. S. Ogunniyi, Bioresour. Technol., 2006, 97, 1086–1091 CrossRef CAS PubMed.
- Z. S. Petrovic, Polym. Rev., 2008, 48, 109–155 CrossRef CAS.
- K. T. Achaya, J. Am. Oil Chem. Soc., 1971, 48, 758–763 CrossRef.
- N. Teramoto, Y. Saitoh, A. Takahashi and M. Shibata, J. Appl. Polym. Sci., 2010, 115, 3199–3204 CrossRef CAS.
- M. J. John and S. Thomas, Carbohydr. Polym., 2008, 71, 343–364 CrossRef CAS.
- I. Ganetri, L. Tighzert, P. Dony and A. Challioui, J. Mater. Environ. Sci., 2013, 4, 571–582 CAS.
- K. M. S. Meer, R. M. Sankar, J. Paul, S. N. Jaisankara and A. B. Mandal, Phys. Chem. Chem. Phys., 2014, 16, 9276–9288 RSC.
- S. Ahmad, F. Zafar, E. Sharmin, N. Garg and M. Kashif, Prog. Org. Coat., 2012, 73, 112–117 CrossRef CAS.
- G. I. Williams and R. P. Wool, Appl. Compos. Mater., 2000, 7, 421–432 CrossRef CAS.
- G. Lligadas, J. C. Ronda, G. Marina and V. Cadiz, Biomacromolecules, 2006, 7, 3521–3535 CrossRef CAS.
- U. Hiroshi, K. Mai, T. Takashi, N. Mitsuru, U. Arimitsu and K. Shiro, Chem. Mater., 2003, 15, 2492–2494 CrossRef.
- T. O. Siyanbola, K. Sasidhar, B. Anjaneyulu, K. P. Kumar, B. V. S. K. Rao, R. Narayan, O. Olaofe, E. T. Akintayo and K. V. S. N. Raju, J. Mater. Sci., 2013, 48, 8215–8227 CrossRef CAS.
- G. Lligadas, L. Callau, J. C. Ronda, M. Galia and V. Cadiz, J. Polym. Sci., Part A: Polym. Chem., 2005, 43, 6295–6307 CrossRef CAS.
- C. R. Wold and M. D. Soucek, Macromol. Chem. Phys., 2000, 201, 382–392 CrossRef CAS.
- D. Deffar, G. Teng and M. D. Soucek, Macromol. Mater. Eng., 2001, 286, 204–215 CrossRef CAS.
- G. Lligadas, J. C. Ronda, G. Marina and V. Cadiz, Biomacromolecules, 2006, 7, 2420–2426 CrossRef CAS PubMed.
- K. M. S. Meera, R. M. Sankar, S. N. Jaisankara and A. B. Mandal, J. Phys. Chem. B, 2013, 117, 2682–2694 CrossRef PubMed.
- I. S. Ristića, J. B. Simendića, I. Krakovskyb, H. Valentovab, R. Radičevića, S. Cakićc and N. Nikolićc, Mater. Chem. Phys., 2012, 1, 74–81 CrossRef.
- S. Allauddin, R. Narayan and K. V. S. N. Raju, J. Coat. Technol. Res., 2014, 11, 397–407 CrossRef.
- A. A. Cumurcu and T. Erciyes, Prog. Org. Coat., 2010, 67, 317–323 CrossRef CAS.
- D. Akrama, E. Sharmina and S. Ahmada, Prog. Org. Coat., 2014, 77, 957–964 CrossRef.
- C. Fu, Z. Yang, Z. Zheng and L. Shen, Prog. Org. Coat., 2014, 77, 1241–1248 CrossRef CAS.
- O. S. Rodríguez and M. Gilbert, J. Appl. Polym. Sci., 1998, 66, 2111–2119 CrossRef.
- B. Riegel, S. Blittersdorf, W. Kiefer, S. Hofacker and M. Muller, J. Non-Cryst. Solids, 1998, 226, 76–84 CrossRef CAS.
- H. Hussain, H. U. Rehman and Z. Ahmad, J. Sol-Gel Sci. Technol., 2005, 36, 239–248 CrossRef CAS.
- S. Çolak and S. H. Küsefoğlu, J. Appl. Polym. Sci., 2007, 104, 2244–2253 CrossRef.
- E. Can, R. P. Wool and S. Küsefoğlu, J. Appl. Polym. Sci., 2006, 102, 2433–2447 CrossRef CAS.
- H. S. Zhang and T. E. Hogen-Esch, Langmuir, 1998, 14, 4972–4977 CrossRef CAS.
- P. Florian, K. K. Jena, S. Allauddin, R. Narayan and K. V. S. N. Raju, Ind. Eng. Chem. Res., 2010, 49, 4517–4527 CrossRef CAS.
- I. Javni, Z. S. Petrović, A. Guo and R. Fuller, J. Appl. Polym. Sci., 2000, 8, 1723–1734 CrossRef.
- E. Hablot, D. Zheng, M. Bouquey and L. Avérous, Macromol. Mater. Eng., 2008, 293, 922–929 CrossRef.
|
This journal is © The Royal Society of Chemistry 2015 |
Click here to see how this site uses Cookies. View our privacy policy here.