DOI:
10.1039/C5RA15399A
(Paper)
RSC Adv., 2015,
5, 97231-97238
Synthesis of a cationic fluorinated polyacrylate emulsifier-free emulsion via ab initio RAFT emulsion polymerization and its hydrophobic properties of coating films
Received
2nd August 2015
, Accepted 26th October 2015
First published on 26th October 2015
Abstract
A cationic fluorinated polyacrylate emulsifier-free emulsion was successfully synthesized via ab initio RAFT emulsion polymerization mediated by the poly(2-(dimethylamino)ethyl methacrylate)-b-poly(hexafluorobutyl acrylate) (PDMAEMA-b-PHFBA)trithiocarbonate macro-RAFT agent. The influence of the amount of PDMAEMA-b-PHFBA on emulsion polymerization and finished fabric properties was investigated. The monomer conversion increased as the amount of PDMAEMA-b-PHFBA increased from 1 wt% to 5 wt%, and decreased slightly afterwards. The water contact angle of the finished fabric increased with the increase of the amount of PDMAEMA-b-PHFBA. The latex particles, presented as spherical particles with diameters of 44–56 nm, were characterized by TEM. FT-IR and 1H-NMR results demonstrated that all the monomers had effectively participated in the emulsion polymerization. The surface morphology of the fabrics was characterized by scanning electron microscopy (SEM), which revealed that the cationic fluorinated polyacrylate emulsifier-free emulsion was deposited on the surface of the fabric, and the treated fabrics showed good water repellency.
1. Introduction
Fluorinated polyacrylate polymers have received considerable attention because of their excellent properties such as low surface energies, high resistances to thermal, chemical, and weather attack, low dielectric constants, good film-forming properties, and good mechanical properties.1–5 Therefore, numerous researches on fluorinated polyacrylate polymers have been conducted for their wide applications in leather,6 paper making,7 textile,8,9 and coating industries.10–12 Emulsion polymerization is an effective method to obtain fluorinated polyacrylate polymers due to some major advantages, including the use of an environmentally friendly solvent, efficient heat transfer, fast polymerization ratios, and easy processing abilities.13,14 Emulsifiers are needed in traditional emulsion polymerization to stabilize and nucleate the emulsion particle. However, small molecule emulsifiers in an emulsion might pollute the environment and damage the electric, optic, surface, and water resistance properties of fluorinated polyacrylate polymers.15
To eliminate the drawbacks resulting from small molecule emulsifiers in emulsion polymerization, emulsifier-free emulsion polymerization is used to solve this problem. In general, fluorinated polyacrylate emulsifier-free emulsions can be synthesized in the presence of the reactive emulsifier,3,16–18 which can be bonded with latex particles by a covalent bond. However, when the reactivity of the reactive emulsifier is too low, the unreacted reactive emulsifiers in the final latex will migrate toward the film surface during the film formation process, resulting in the deleterious effects on film properties.19 Compared with emulsifier-free emulsion with reactive emulsifier, the emulsifier-free emulsion with fluorine-containing amphiphilic block copolymers exhibit dramatically different properties20–23 such as narrow particle size distributions and better emulsion stabilities. In previous studies, fluorine-containing amphiphilic block copolymers have been synthesized via RAFT polymerization, and micelle formation behaviors in aqueous solutions have been extensively studied.24–27 For example, Yao et al.28 synthesized a series of fluorine-containing amphiphilic di-block copolymers comprising hydrophobic poly(p-(2-(p-tolyloxy)perfluorocyclobutoxy)phenyl methacrylate) and hydrophilic poly(2-(diethylamino)ethyl methacrylate) segments via successive RAFT polymerizations, and the spherical micelles can be obtained by self-assembly in deionized water. Skrabania et al.29 synthesized linear amphiphilic tri-block copolymers of poly(ethylene oxide)-b-poly(butyl acrylate)-b-b-poly(tetrahydroperfluorodecyl acrylate) (PEO-b-PBA-b-PFA) and poly(ethylene oxide)-b-poly(2-ethylhexyl acrylate)-b-poly(tetrahydroperfluorodecyl acrylate) (PEO-b-PEHA-b-PFA) tri-block copolymers by a RAFT approach in two successive steps using a PEO macro-CTA, and the PEO-b-PBA-b-PFA and PEO-b-PEHA-b-PFA tri-block copolymers could self-assemble in water into spherical micellar aggregates. However, very few papers, to the best of our knowledge, have been published to date on the use of fluorine-containing amphiphilic block copolymer as a stabilizer for fluorinated polyacrylate emulsifier-free emulsion. In our previous research, an anionic fluorinated polyacrylate emulsifier-free emulsion was synthesized by a poly(acrylic acid)-b-poly(hexaflurobutyl acrylate) (PAA-b-PHFBA)trithiocarbonate macro-RAFT agent.30 However, there is no report on using cationic fluorine-containing amphiphilic block copolymers as a stabilizer in the synthesis of cationic fluorinated polyacrylate emulsifier-free emulsions, which shows very high adhesion to anionic substrates such as textiles, paper, leather, and glass.
The purpose of this study is to synthesize a cationic fluorinated polyacrylate emulsifier-free emulsion using poly(2-(dimethylamino)ethyl methacrylate)-b-poly(hexafluorobutyl acrylate) (PDMAEMA-b-PHFBA) both as a stabilizer and a RAFT agent. In addition, the cationic fluorinated polyacrylate emulsifier-free emulsion is used as a fabric finishing agent. The influence of the amount of PDMAEMA-b-PHFBA on emulsion polymerization and finished fabric properties was studied. The resulting amphiphilic block copolymer was characterized by Fourier transform infrared spectroscopy (FT-IR), nuclear magnetic resonance (1H-NMR) spectroscopy, and gel permeation chromatography (GPC). The cationic fluorinated polyacrylate was characterized by transmission electron microscopy (TEM) and dynamic laser scattering (DLS), while the finished fabric was measured by scanning electron microscopy (SEM) and contact angle (CA) analysis.
2. Experimental section
2.1 Materials
2-(Dimethylamino)ethyl methacrylate (DMAEMA) was purchased from the Feixiang Group of Companies and passed through an alumina column to remove any inhibitors prior to use. Hexafluorobutyl acrylate (HFBA) and hexafluorobutyl methacrylate (HFBMA) supplied by the XEOGIA Fluorine-Silicon Chemical Company went through an alkaline alumina chromatographic column to remove any inhibitors before use. Butyl acrylate (BA) and styrene (St) were purchased from the Tianjin Kemiou Chemical Co. Ltd. and used as received. Stearyl acrylate (SA) was purchased from the Tianjin Tianjiao Chemical Co., Ltd. and used as received. (2-(Acryloyloxy)ethyl)trimethylammonium chloride (DMC) was purchased from the Adamas Reagent Co., Ltd. 4,4′-Azobis(4-cyanopentanoic acid) (AIBN) was supplied by the Fluka Company. 2,2′-Azobis(2-methylpropionamidine)dihydrochloride (AIBA) was purchased from the Shanghai Eybridge Chemical Technology Co., Ltd. 2-{[(Dodecylsulfanyl)-carbonothioyl]sulfanyl}succinic acid (DCTSS) was synthesized and purified as described in ref. 31.
2.2 Synthesis of the poly(2-(dimethylamino)ethyl methacrylate)-b-poly(hexafluorobutyl acrylate)trithiocarbonate macro-RAFT agent
Poly(2-(dimethylamino)ethyl methacrylate)-b-poly(hexafluorobutyl acrylate) (PDMAEMA-b-PHFBA) macro-RAFT agent was synthesized by a two-step solution polymerization. First, 0.25 g (5.00 × 10−4 mol) of DCTSS, 0.0209 g (1.00 × 10−4 mol) of AIBN, 4.01 g (2.55 × 10−2 mol) of DMAEMA and 11.89 mL of dioxane were mixed in a three-necked flask equipped with a reflux condenser. The mixture was deoxygenated with argon gas for 30 min, and then immersed in a heated water bath at 80 °C for 6 h. After the flask was cooled to room temperature, 0.03 g (1.00 × 10−4 mol) of AIBN, 2.41 g (1.02 × 10−2 mol) of HFBA and 7.93 mL of dioxane were added. The mixture was deoxygenated with argon gas for 30 min and reacted for another 6 h at 70 °C. A yellow powder was obtained after precipitation of the mixture in hexane and dried at 50 °C under vacuum for 48 h.
2.3 Synthesis of cationic fluorinated polyacrylate emulsifier-free emulsion
Table 1 describes the recipes for cationic fluorinated polyacrylate emulsifier-free emulsion. For a typical reaction procedure, 0.65 g (3.00 × 10−4 mol) of PDMAEMA-b-PHFBA was dissolved in 5.50 mL 0.1 mol L−1 HCl to form a PDMAEMA-b-PHFBA solution that was divided into two parts. One part of the PDMAEMA-b-PHFBA solution was added in the flask, and the other part of the PDMAEMA-b-PHFBA solution with St, BA, HFBMA, DMC, SA monomers was homogenized under continuous stirring in the aqueous phase to form the monomer pre-emulsion. 4.80 g (4.61 × 10−2 mol) of St, 7.20 g (5.62 × 10−2 mol) of BA, 1.2 g (4.80 × 10−3 mol) of HFBMA, 0.24 g (1.24 × 10−3 mol) of DMC, 0.6 g (1.85 × 10−3 mol) of SA, 5.42 g of PDMAEMA-b-PHFBA solution, and 9.52 mL of deionized water were mixed in the beaker and then intensively homogenized to form the pre-emulsion.
Table 1 Recipes for cationic fluorinated polyacrylate emulsifier-free emulsion
Sample |
P1 |
P2 |
P3 |
P4 |
P5 |
PDMAEMA-b-PHFBA/g |
0.13 |
0.26 |
0.52 |
0.65 |
0.78 |
BA/g |
7.20 |
7.20 |
7.20 |
7.20 |
7.20 |
St/g |
4.80 |
4.80 |
4.80 |
4.80 |
4.80 |
HFBMA/g |
1.20 |
1.20 |
1.20 |
1.20 |
1.20 |
DMC/g |
0.24 |
0.24 |
0.24 |
0.24 |
0.24 |
SA/g |
0.60 |
0.60 |
0.60 |
0.60 |
0.60 |
AIBA/g |
0.1287 |
0.1287 |
0.1287 |
0.1287 |
0.1287 |
0.1 mol L−1 HCl/mL |
15.48 |
15.48 |
15.48 |
15.48 |
15.48 |
DI water/mL |
16.70 |
16.70 |
16.70 |
16.70 |
16.70 |
A 100 mL three-neck round-bottom flask equipped with a reflux condenser, a thermometer and a mechanical stirrer was charged with 0.73 g of the PDMAEMA-b-PHFBA solution, 9.98 mL 0.1 mol L−1 HCl and 1.18 mL deionized water, and the mixture was deoxygenated with argon gas for 30 min at room temperature. One quarter of the pre-emulsion and AIBA aqueous solution (0.0429 g (1.58 × 10−4 mol) of AIBA in 2.00 mL deionized water) were added dropwise into the reacting mixture and the mixture was kept at 80 °C for 30 min. Then, the polymerization continued with a slow addition of the remaining pre-emulsion and AIBA aqueous solutions (0.0858 g (3.16 × 10−4 mol) of AIBA in 4.00 mL deionized water) over 90 min. After the addition was complete, the reaction went on for another 2 h.
2.4 Fabric treatment
The cotton fabrics were padded with two dips and nips (70%–80% wet pick up) in a solution containing cationic fluorinated polyacrylate emulsifier-free emulsion at a concentration of 70 g L−1. After the treatment, the cotton fabrics were dried at 80 °C for 3 min and cured at 160 °C for 3 min.
2.5 Characterizations
Monomer conversion was measured by gravimetric analysis. Two grams of emulsion was cast onto a weighing disk, quenched with hydroquinone, and dried to a constant weight at 120 °C. The latex particle size and distribution of the synthesized emulsion were measured with a Malvern Nano ZS instrument (Malvern Instruments, UK) at a fixed scattering angle of 90° at room temperature. The Fourier transform infrared (FT-IR) spectra were obtained on a BRUKER Advance VECTOR-22 spectrometer. Nuclear magnetic resonance (1H-NMR) spectra were obtained on a 400 MHz ADVANCE III spectrometer in dimethylsulfoxide-d6 as the solvent. Molecular weights and molecular weight distributions were determined on a Waters 201 gel permeation chromatograph (GPC). The eluent was N,N-dimethylformamide (DMF) at a flow rate of 1.0 mL min−1. The column system was calibrated by monodisperse linear poly(methyl methacrylate) standards. Transmission electron microscopy (TEM) of the cationic fluorinated polyacrylate emulsifier-free emulsion particles was performed on a FEI Tecnai G2 F20 S-TWIN (FEI Ltd., America) at a voltage of 75 kV. The sample was stained with 1.5% phosphotungstic acid solution. Contact angle (CA) measurements were performed on a contact angle goniometer (OCA 20, Dataphysics Company, Germany) by the sessile drop method with a microsyringe at room temperature. Static contact angles were obtained from the injection volume of 5 μL water droplets on the surface of the finished fabrics. The average value obtained from nine contact angle readings at different locations on the same sample was used as the final value for each sample. The morphology of the fabrics was determined by field emission scanning electron microscopy (FE-SEM) (Hitachi S-4800 Japan).
3. Results and discussion
3.1 Structure and characterization of PDMAEMA-b-PHFBA
Poly(2-(dimethylamino)ethyl methacrylate)-b-poly(hexafluorobutyl acrylate) (PDMAEMA-b-PHFBA) was first synthesized via a two-step RAFT solution polymerization of 2-(dimethylamino)ethyl methacrylate (DMAEMA) and hexafluorobutyl acrylate (HFBA). The structure and composition of PDMAEMA-b-PHFBA were characterized by FT-IR, 1H-NMR and GPC. As shown in Fig. 1, the bonds at 2950 cm−1 and 2875 cm−1 can be assigned to characteristic stretching vibration peaks of methyl groups (–CH3) and methylene groups (–CH2–). The characteristic stretching vibration peak of C–H in –N(CH3)2 appears at 2772 cm−1. The peak at 1456 cm−1 is assigned to the bending vibration of –CH2– groups. The characteristic stretching vibration peak of C
O appears at 1726 cm−1. The peak at 1150 cm−1 is the stretching vibration absorption peak of C–O. The absorption located at 1301 cm−1 is characteristic of the C–F bond stretching vibration and the peak at 671 cm−1 is caused by the wagging vibration of CF2 groups.32 The peak at 1189 cm−1 and 690 cm−1 can be ascribed to the characteristic absorption of –CF2 and –CF3 groups, respectively.32,33 Therefore, FT-IR results demonstrate that DMAEMA and HFBA have effectively participated in the polymerization process and PDMAEMA-b-PHFBA was obtained.
 |
| Fig. 1 FT-IR spectrum of PDMAEMA-b-PHFBA. | |
The 1H-NMR spectrum of PDMAEMA-b-PHFBA dissolved in dimethylsulfoxide-d6 is illustrated in Fig. 2. Feature signals of the PDMAEMA segment (δ = 2.64 ppm ((CH3)2NCH2CH2–) (e H), δ = 4.01 ppm ((CH3)2NCH2CH2–) (f H), δ = 2.22 ppm ((CH3)2NCH2CH2–) (d H)), and PHFBA segment (δ = 5.97 ppm (CF3CHFCF2CH2–) (h H), δ = 4.55 ppm (CF3CHFCF2CH2–) (g H)) appear in the spectrum. The signals at 0.86 ppm and 1.23 ppm are attributed to the methyl protons and methylene protons of the RAFT agent, respectively, and they provide good evidence that the polymer chains have ends that are derived from the original RAFT agent. This indicates that PDMAEMA-b-PHFBA is able to act as a macro-RAFT agent and to be extended through further polymerization. Furthermore, the molecular weight and its distribution of PDMAEMA-b-PHFBA were characterized by GPC. The GPC chromatogram of PDMAEMA-b-PHFBA is exhibited in Fig. 3 as a function of elution time, in which only one single peak could be observed, indicating that the product is composed of amphiphilic block copolymers of PDMAEMA-b-PHFBA, rather than a mixture containing the homopolymer of PHFBA and PDMAEMA. The Mn of PDMAEMA-b-PHFBA is 8.51 × 103 g mol−1 and the polydispersity index is 1.59. Narrowly distributed PDMAEMA-b-PHFBA is obtained, indicating good control of the RAFT polymerization technique.
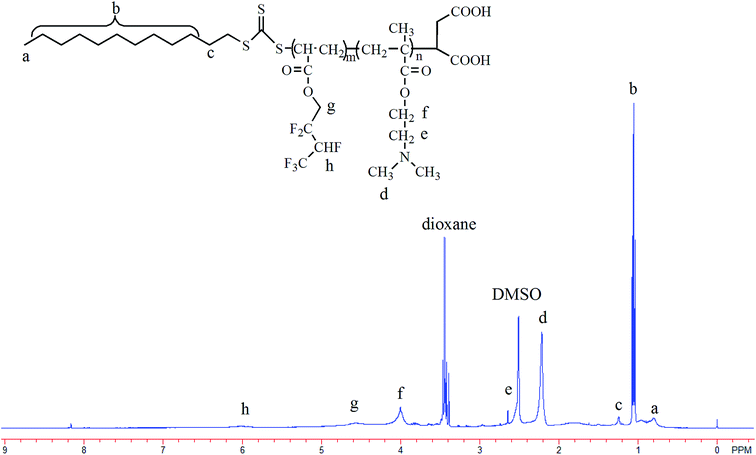 |
| Fig. 2 1H-NMR spectrum of PDMAEMA-b-PHFBA. | |
 |
| Fig. 3 GPC trace of PDMAEMA-b-PHFBA. | |
3.2 Synthesis and characterization of cationic fluorinated polyacrylate emulsifier-free emulsion
PDMAEMA-b-PHFBA containing both a hydrophobic PHFBA segment and a hydrophilic PDMAEMA segment is amphiphilic and expected to self-assemble into micelles, in which the polymerization of St/BA/SA/DMC/HFBMA continues to produce cationic fluorinated polyacrylate emulsifier-free emulsion particles under RAFT control due to the active RAFT end located in the micelle interior, as shown in Scheme 1. The resulting latex particles were stabilized by the anchor of the hydrophobic PHFBA blocks to the latex particle surface via a covalent bond, while the hydrophilic PDMAEMA blocks extended into the water phase and created a well-defined hydrophilic shell surrounding the particles. Fig. 4 shows the effect of the PDMAEMA-b-PHFBA amount on monomer conversion. The monomer conversion increases from 75% to 97% as the amount of PDMAEMA-b-PHFBA increases from 1 wt% to 5 wt%, then the monomer conversion decreases slightly with further increases in the PDMAEMA-b-PHFBA amount.
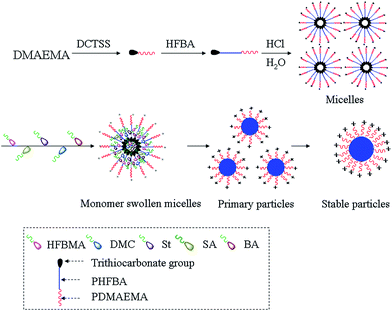 |
| Scheme 1 Schematic for the synthesis of cationic fluorinated polyacrylate emulsifier-free emulsion with poly(2-(dimethylamino)ethyl methacrylate)-b-poly(hexafluorobutyl acrylate)trithiocarbonate as the stabilizer. | |
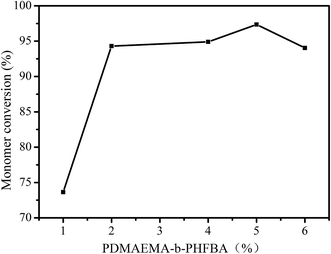 |
| Fig. 4 Effect of the dosage of PDMAEMA-b-PHFBA on the monomer conversion. | |
A series of experiments using different amounts of PDMAEMA-b-PHFBA were carried out. Fig. 5 illustrates the effect of the amount of PDMAEMA-b-PHFBA on latex particle size. Latex particle size decreases from 209 nm to 185 nm as the amount of PDMAEMA-b-PHFBA increases from 1 wt% to 2 wt%, and then the latex particle size increases with further increase in the PDMAEMA-b-PHFBA amount. This phenomenon can be explained by the fact that the number of micelles and latex particles increases with increasing amounts of PDMAEMA-b-PHFBA, resulting in a decrease of latex particle size. However, the probability of particle collision increases with further increases in the number of latex particles. The conglomeration of particles results in the increase of the latex particle size.
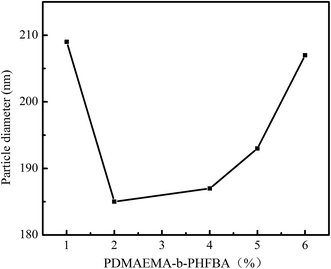 |
| Fig. 5 Effect of dosage of PDMAEMA-b-PHFBA on latex particle size. | |
Fig. 6(A) shows the TEM image of cationic fluorinated polyacrylate emulsifier-free emulsion particles using 5 wt% PDMAEMA-b-PHFBA block copolymer as a stabilizer. The cationic fluorinated polyacrylate emulsifier-free emulsion particles are uniform spheres with diameters of about 44–56 nm. The average particle diameter size and distribution measured by means of DLS are presented in Fig. 6(B). The Z-average hydrodynamic diameter of the latex particle is 193 nm and the size distribution is 0.126. The diameter of latex particles measured by DLS is much larger than that measured by TEM owing to the fact that the hydrodynamic diameter is measured by the particle size analyzer based on dynamic light scattering in the aqueous solution. The latex particles are swollen in the aqueous solution during the DLS measurements; on the contrary, TEM shows the diameter of the dried latex particles. Based on the results of TEM and DLS, it is can be concluded that the cationic fluorinated polyacrylate emulsifier-free emulsion particles have been successfully obtained by the emulsifier-free emulsion polymerization method.
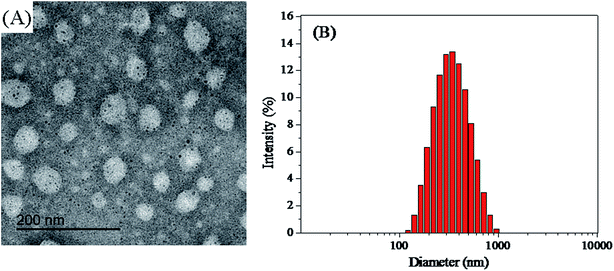 |
| Fig. 6 (A) TEM image and (B) size distribution measured using DLS of cationic fluorinated polyacrylate emulsifier-free emulsion. | |
The structure of cationic fluorinated polyacrylate was characterized by FT-IR and 1H-NMR. As shown in Fig. 7, the bands at 2929 cm−1 and 2851 cm−1 can be assigned to characteristic stretching vibration peaks of methyl groups (–CH3) and methylene groups (–CH2), respectively. The characteristic stretching vibration peak of C
O appears at 1728 cm−1. The bands at 1493 cm−1 and can be assigned to stretching vibration peaks of unsaturated C
C in the benzene ring. The characteristic stretching vibration absorption peak occurring at 1453 cm−1 is attributed to the framework vibration peaks of the benzene ring. The peaks 760 cm−1 and 699 cm−1 are ascribed to the bending vibration of C–H in the benzene ring. The characteristic stretching vibration absorption peak occurring at 1158 cm−1 is attributed to –C–O– of esters. The peaks at 1189 cm−1 and 690 cm−1 are ascribed to the characteristic absorbance of –CF2 and CF3, respectively. The characteristic peak of a quaternary ammonium salt (–N+(CH3)3Cl−) appears at 960 cm−1. Fig. 8 shows the 1H-NMR spectrum of cationic fluorinated polyacrylate. It can be seen that the typical δH of –CHF2 in the PHFBMA segment and the PHBA segment are both found at 5.97 ppm (p1 H, p2 H). Peaks at 0.92 ppm (h H), 1.42 ppm (g H, f H), and 4.12 ppm (e H) belong to the δH of –O–CH2CH2CH2CH3 in the PBA segment. The δH of the benzene ring in the PSt segment is found at 6.4–7.2 ppm (d H). Peak at 3.52 ppm (j H) belongs to the δH of –N+–(CH3)3 in the PDMC segment. The typical δH of –N–CH2 in the PDMAEMA segment is found at 2.82 ppm (u H). Therefore, FT-IR and 1H-NMR results demonstrate that all the monomers effectively participated in the emulsion polymerization and a cationic fluorinated polyacrylate copolymer is obtained.
 |
| Fig. 7 FT-IR spectrum of cationic fluorinated polyacrylate. | |
 |
| Fig. 8 1H-NMR spectrum of cationic fluorinated polyacrylate. | |
3.3 Contact angle analysis
The water contact angle is commonly used as a criterion for the evaluation of the hydrophobicity of a solid surface.34 The surface is hydrophobic when θ is higher than 90° and the surface is hydrophilic when θ is lower than 90°.35 In order to investigate the water repellency of cationic fluorinated polyacrylate, we tested the water contact angle of fabrics treated with cationic fluorinated polyacrylate emulsifier-free emulsion. As shown in Fig. 9, the water contact angle of finished fabrics increased from 122° to 141° with the increase of the amount of PDMAEMA-b-PHFBA from 1 wt% to 6 wt%. This phenomenon can be explained by the fact that the number of micelles increased with increasing amounts of PDMAEMA-b-PHFBA, so the HFBMA monomers are much easier to diffuse into the interior of the micelles and then react with acrylate monomers to form cationic fluorinated polyacrylate, resulting in the increase of fluorinated segment length in the polymer with increasing amounts of PDMAEMA-b-PHFBA. In the curing process, the fluorinated segments can enrich and occupy the finished fabric's surface, resulting in the increase of the water contact angle of the finished fabrics. When the PDMAEMA-b-PHFBA amount is more than 4%, the incremental tendency of the water contact angle begins to weaken, indicating that the enrichment of fluorinated groups reached a maximum value, and further enhancing of PDMAEMA-b-PHFBA content has only little influence on the surface property of the finished fabrics.
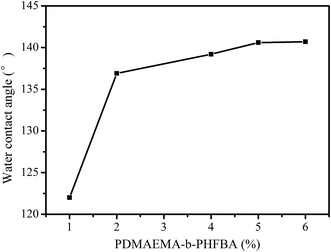 |
| Fig. 9 Effect of dosage of PDMAEMA-b-PHFBA on water contact angle of finished fabrics. | |
3.4 Surface morphology of the finished fabrics
As is well known, the properties or application performances of a polymer depend significantly on its structure or morphology on substrates. Therefore, an exploration of its morphology on substrates is crucial. Fig. 10 shows the scanning electron microscopy (SEM) image of the fabric before and after treatment with cationic fluorinated polyacrylate emulsifier-free emulsion. From Fig. 10(a and b), it can be clearly seen that the unfinished fabric surface is uneven. There are many deep grooves or slender concave grooves on its surface. On the contrary, the surface of the finished fabric with cationic fluorinated polyacrylate emulsifier-free emulsion is smooth, and the concave grooves disappear. These results indicate that cationic fluorinated polyacrylate polymers have low surface tension, which makes them spread out easily. On the other hand, cationic fluorinated polyacrylate emulsifier-free emulsion preferably adsorbs on negatively charged fiber surfaces. Therefore, the smooth polymer film is formed on the fiber surface during the finishing process. In our experiment, we found that the water molecules were quickly absorbed when water droplets were placed on surface of the unfinished fabric. However, the water contact angle of the finished fabrics was up to 141°, indicating that the finished fabrics have excellent water repelling abilities. This is owing to the extremely low surface free energy and self-aggregated property of the fluorine atoms, causing the fluorinated segments to be preferentially oriented to the fabric surface during the film formation so as to decrease the surface energy of the finished fabrics.
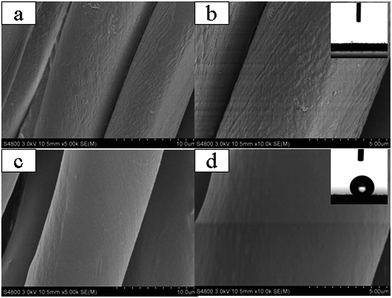 |
| Fig. 10 SEM images of the surface of the unfinished fabric (a and b) and the finished fabric (c and d) with cationic fluorinated polyacrylate emulsifier-free emulsion. | |
4. Conclusions
Cationic fluorinated polyacrylate emulsifier-free emulsion was successfully synthesized using fluorine-containing amphiphilic block copolymer PDMAEMA-b-PHFBA as a stabilizer via ab initio RAFT emulsion polymerization. The monomer conversion increased from 75% to 97% as the amount of PDMAEMA-b-PHFBA increased from 1 wt% to 5 wt%, and then the monomer conversion decreased slightly with further increasing the PDMAEMA-b-PHFBA amount. Spherical-like particles of about 44–56 nm in diameter were observed using TEM analysis. 1H-NMR and FT-IR analysis confirmed that all the monomers were successfully introduced into the cationic fluorinated polyacrylate. The water contact angle of the finished fabrics increased as the amount of PDMAEMA-b-PHFBA increased from 1 wt% to 6 wt%, and the treated fabrics showed good water repelling tendencies. SEM analysis revealed that the cationic fluorinated polyacrylate emulsifier-free emulsion successfully adhered to the fiber surface.
Acknowledgements
This study was supported by the National Natural Science Fund of China (No. 21206088), the Academic Backbone Cultivation Program of Shaanxi University of Science and Technology (No. XSGP201205), and the Key Scientific Research Group of Shaanxi Province (No. 2013KCT-08).
References
- G. Li, H. T. Zheng, Y. X. Wang, W. Hu, Q. B. Dong and R. K. Bai, Polymer, 2010, 51, 1940–1946 CrossRef CAS.
- W. Zhang, L. He, J. Y. Liang, G. Chang, N. Wang and J. Appl, Polym. Sci., 2011, 120, 1152–1161 Search PubMed.
- F. C. Zhao, X. R. Zeng, H. Q. Li and J. Zhang, Colloids Surf., A, 2012, 396, 328–335 CrossRef CAS.
- A. L. Qu, X. F. Wen, P. H. Pi, J. Cheng and Z. R. Yang, Polym. Int., 2008, 57, 1287–1294 CrossRef CAS.
- S. Salima, G. Frédéric, G. Claude and G. Serge, Eur. Polym. J., 2006, 42, 702–710 CrossRef.
- J. Hu, J. Z. Ma and W. J. Deng, Mater. Lett., 2008, 62, 2931–2934 CrossRef CAS.
- Y. Su, Y. D. Shen, L. Wang, X. R. Wang, X. J. Lai, F. S. Zhang and G. J. Liu, Appl. Mech. Mater., 2013, 316, 923–926 CrossRef.
- W. Xu, Q. An, L. Hao, D. Zhang and M. Zhang, Fibers Polym., 2014, 15, 457–464 CrossRef CAS.
- A. Abou-Okeil, S. M. El-Sawy and F. A. Abdel-Mohdy, Carbohydr. Polym., 2013, 92, 2293–2298 CrossRef CAS PubMed.
- J. Wang, X. R. Zeng and H. Q. Li, J. Coat. Technol. Res., 2010, 7, 469–476 CrossRef CAS.
- O. Yilmaz, Prog. Org. Coat., 2014, 77, 110–117 CrossRef CAS.
- S. F. Zhang, Y. E. He, R. M. Wang, Z. M. Wu and P. F. Song, Iran. Polym. J., 2013, 22, 447–456 CrossRef CAS.
- K. Schmidtke, G. Lieser, M. Klapper and K. Müllen, Colloid Polym. Sci., 2010, 288, 333–339 CAS.
- A. R. Mahdavian, M. Ashjari and A. B. Makoo, Eur. Polym. J., 2007, 43, 336–344 CrossRef CAS.
- L. Chen, L. L. Yan, Q. H. Li, C. F. Wang and S. Chen, Langmuir, 2009, 26, 1724–1733 CrossRef PubMed.
- G. H. Li, N. Li, C. Wang, Y. H. Niu and X. M. Gong, Colloid Polym. Sci., 2014, 292, 123–131 CAS.
- R. Q. Bai, T. Qiu, C. Xu, L. F. He and X. Y. Li, Colloid Polym. Sci., 2012, 290, 769–776 CAS.
- L. J. Chen and F. Q. Wu, Surf. Eng., 2012, 28, 220–224 CrossRef CAS.
- L. Chen, L. Yan, Q. Li, C. Wang and S. Chen, Langmuir, 2010, 26, 1724–1733 CrossRef CAS PubMed.
- S. Garnier and A. Laschewsky, Langmuir, 2006, 22, 4044–4053 CrossRef CAS PubMed.
- M. Save, M. Manguian, C. Chassenieux and B. Charleux, Macromolecules, 2005, 38, 280–289 CrossRef CAS.
- J. Rieger, F. Stoffelbach, C. Bui, D. Alaimo, C. JérÔme and B. Charleux, Macromolecules, 2008, 41, 4065–4068 CrossRef CAS.
- D. E. Ganeva, E. Sprong, H. de Bruyn, G. G. Warr, C. H. Such and B. S. Hawkett, Macromolecules, 2007, 40, 6181–6189 CrossRef CAS.
- K. Y. Mya, E. M. J. Lin, C. S. Gudipati, H. B. A. S. Gose and C. He, J. Phys. Chem. B, 2010, 114, 9128–9134 CrossRef CAS PubMed.
- B. Tan, C. Gudipati, H. Hussain, C. He, Y. Liu and T. Davis, Macromol. Rapid Commun., 2009, 30, 1002–1008 CrossRef CAS PubMed.
- S. Xu and W. Liu, J. Polym. Sci., Part B: Polym. Phys., 2008, 46, 1000–1006 CrossRef CAS.
- S. Xu and W. Liu, J. Fluorine Chem., 2008, 129, 125–130 CrossRef CAS.
- W. Q. Yao, Y. J. Li, S. Zhang, H. Liu and X. Y. Huang, J. Polym. Sci., Part A: Polym. Chem., 2011, 49, 4433–4440 CrossRef CAS.
- K. Skrabania, A. Laschewsky, H. Berlepsch and C. Böttcher, Langmuir, 2009, 25, 7594–7601 CrossRef CAS PubMed.
- J. H. Zhou, L. Zhang and J. Z. Ma, Chem. Eng. J., 2013, 223, 8–17 CrossRef CAS.
- C. H. Such, E. Rizzardo, A. K. Serelis, B. S. Hawkett, R. G. Gilbert, C. J. Ferguson and R. J. Hughes, Patent Number US 20060223936A1, 2006.
- Z. J. Wei, W. L. Liu, D. Tian, C. L. Xiao and X. Q. Wang, Appl. Surf. Sci., 2010, 256, 3972–3976 CrossRef CAS.
- S. P. Xu and W. Q. Liu, J. Fluorine Chem., 2008, 129, 125–130 CrossRef CAS.
- J. W. Ha, I. J. Park and S. B. Lee, Macromolecules, 2006, 383, 736–744 Search PubMed.
- B. T. Zhang, B. L. Liu, X. B. Deng, S. S. Cao, X. H. Hou and H. L. Chen, Appl. Surf. Sci., 2007, 254, 452–458 CrossRef CAS.
|
This journal is © The Royal Society of Chemistry 2015 |
Click here to see how this site uses Cookies. View our privacy policy here.