DOI:
10.1039/C5RA14153B
(Paper)
RSC Adv., 2015,
5, 74075-74083
A general electrodeposition-based method for in situ construction of resistive-type semiconductor film gas-sensor with excellent sensing performance
Received
17th July 2015
, Accepted 25th August 2015
First published on 25th August 2015
Abstract
For the construction of a resistive-type gas-sensor, it is usually required for a sensing film to be fabricated on a non-conductive substrate. The in situ construction of a sensor by subjecting the substrate to an electrodeposition method is impossible and there have been no related reports on this. Herein, taking the in situ construction of a SnO2 film sensor as an example, a novel electrodeposition-based method was introduced. A conductive graphite coating was firstly fabricated on the non-conductive substrate for the implementation of the electrodeposition, and then a calcining process was employed. The conductive pristine graphite coating was found to become non-conductive after being calcined for more than 70 min at 500 °C, resulting in the final electrodeposited film being able to work as a sensing film. Some important parameters related to the sensing performances, including the formation, the conductivity, the electrodeposition time, the calcining time and the working temperature, were systematically studied. Under the optimal conditions, the SnO2 film sensor exhibited high sensitivity, a fast response and recovery, and long-term stability in the detection of ethanol gas with concentrations ranging between 1–100 ppm. The electrodeposition-based method is reproducible, mass-productive and general. It is therefore practical and promising for the construction of various semiconductor film sensors.
Introduction
The resistive-type gas sensor represents a kind of conventional device for the detection of flammable and noxious environmental gases. A gas sensor is composed of a non-conductive ceramic substrate, two electrodes on the ends of the substrate and a sensing film connecting the two electrodes. The coating of the sensing film onto the substrate is essential and even decisive in obtaining a sensor with excellent sensitivity, stability and/or reproducibility.
Generally, the sensor film is fabricated by three steps,1–3 i.e. synthesizing powder-like sensing materials using various methods, blending the powders with specific liquids into pastes and then coating the pastes onto substrates, which are widely employed in studies focused on the sensing property of a material. However, in addition to the fussy manipulations, the particles in the coated film usually physically contact each other and their morphologies are easily destroyed during the coating process, inherently resulting in the instability, the undefined sensitivity and the reproducibility of the final sensor. Some in situ methods, like chemical vapor deposition (CVD),4,5 physical vapor deposition (PVD),6 and electrospinning processes7,8 can be used to directly grow a sensing film on the corresponding substrates and effectively overcome the drawbacks of the three-step method, but they are restricted to the fabrication of films on a flat substrate and require sophisticated equipment, limiting their wider applications. Recently, the monolayer colloidal crystal template method developed by our groups has been used to fabricate an ordered porous sensing film directly on various substrates and because of the assistance of templates, the reproducible construction of sensors is also feasible.9–11 However, the method still presents difficulties in obtaining a large area ideal template with few or no defects, and sometimes layer-by-layer manipulations must be carried out to improve the conductivity of a film, limiting the mass-production of sensors.
Electrodeposition, a traditional method for fabricating films on conductive solid substrates, has many advantages, such as requiring simple apparatus, easy manipulation, strong controllability, low cost and mass production. Till now, electrodeposition of nearly all semiconductor materials suitable to be used in gas-sensors has been achieved. This is obviously beneficial for the construction, performance improvement and practicality of gas-sensors. However, because the substrate of a gas-sensor is non-conductive, direct electrodeposition of a sensing film on such a substrate is completely impossible. Alternatively, in several reports,12–14 sensing materials had to be electrodeposited on conductive substrates first and then peeled off, transferred on special substrates (e.g. polystyrene film) and processed with additional electrodes for the construction of specific sensors. The subsequent manipulations were difficult and not suitable for most sensing materials, in addition to the fact that they could cause more or less mechanical damage to the materials. The application of the electrodeposition method in the construction of a gas-sensor device still suffers from severe limitations and the advantages of electrodeposition cannot be fully embodied. The growth of sensing materials on available ordinary substrates directly used in gas-sensors is obviously necessary, but no one has tried to do so because of the limitation of the non-conductivity of the substrate.
Herein, a new process for construction of a gas-sensor based on electrodeposition is introduced. A ceramic tube widely used in the field of gas-sensors was chosen as the substrate. In order to make the substrate conductive, the surface of the substrate was coated with a graphite film, which was a key step. And then, the electrodeposition of the semiconductor could be favorably carried out on the substrate. After a subsequent calcination process, the graphite layer was found to have a particular character, i.e., its conductivity would be significantly decreased and finally disappear, which guaranteed that the electrodeposited film could directly work as a sensing film. Thus, the construction of a sensor by electrodeposition would be very easy, and every available inorganic semiconductor sensor could be obtained by this method. To more clearly explain the process and the sensing performance of the as-prepared sensor, SnO2, the most widely used material in gas-sensors, was chosen as an example.
Experimental
Construction of the gas-sensor
A commercially applied ceramic tube (Scheme 1a) with an outer diameter of 2 mm and a length of 5 mm was employed as the substrate. It contains two conductive gold films around the ends, electrode wires welded on the gold films and a naked non-conductive ceramic surface (Scheme 1a). Before use, it was ultrasonically cleaned sequentially in acetone and in ethanol, and then dried. An ordinary cuboid graphite block was then used to repeatedly and uniformly scrape the surface of the tube to acquire a conductive graphite coating connecting the gold films on the ends (Scheme 1b). The resistance was controlled at ∼80 Ω. Subsequently, the electrode wires on the two ends of the tube were connected with the cathode of a galvanostatic instrument (Scheme 1c). Then, the tube was immersed into 30 mL electrolytic solution in an electrolytic cell with a graphite electrode as the counter electrode. Typically, for the fabrication of the SnO2 film, the electrolytic solution was composed of 0.02 M SnSO4, 0.1 M NaNO3 and 0.075 HNO3. The electrodeposition was carried out at 0.8 mA. 90 min later, the electrodeposition was stopped. The tube was then taken out, washed with deionized water, dried at room temperature and calcined at 500 °C to increase the resistance of the graphite coating and promote the formation of the SnO2 film. After 100 min, the heat treatment was stopped and a SnO2/graphite hybrid film gas-sensor was finally obtained (Scheme 1d). Subsequently, a spring-like nickel-chrome (Ni–Cr) alloy heating wire was crossed through the tube. The heating wire and the electrodes of the ceramic tube were then welded on a specific support used in a gas-sensing test system (Scheme 1e). The as-constructed gas-sensor could work. Other semiconductor/graphite sensors could be also constructed by a similar process.
 |
| Scheme 1 Fabrication process of the semiconductor/graphite gas-sensor based on an electrodeposition method. (a) Schematic of the ceramic tube used as the substrate; (b) tube covered with the graphite coating; (c) electrodeposition of the semiconductor on the tube; (d) semiconductor film on the graphite-covered tube; (e) tube connected on a specific support. | |
Gas-sensing test
The gas sensing test was operated on a WS-30A system (Weisheng Instruments Co., Zhengzhou, China). The detection of ethanol gas was chosen as an example to evaluate the performance of the as-constructed sensors. A stationary state gas distribution method was carried out for gas response testing. The working temperature of the sensors was adjusted by varying the heating voltage of the Cr–Ni wire and monitored with a thermometer. The ethanol gas to be detected was injected into a test chamber and mixed with air. The conductivity (or resistance) of the sensor would be changed. After it was stabilized, the chamber was opened and the ethanol gas was removed. The conductivity would be recovered. The same procedure was followed for the recycling test.
Characterizations
The morphologies of the graphite coating and the SnO2/graphite hybrid film on the ceramic tubes were examined by scanning electron microscopy (SEM, Shimadzu SS-550 and Quanta 250 FEG). The compositions were characterized by X-ray powder diffraction (XRD, D/max2200, with Cu Kα radiation). Samples for the XRD measurements were prepared on frosted glass substrates under the same conditions as those for preparation on the ceramic tubes.
Results and discussion
Character of the graphite coating
Fig. 1a shows the morphology of a pure pristine graphite coating fabricated by scraping the surface of the ceramic tube with a graphite block. It uniformly covered the whole surface of the ceramic tube and was composed of closely contacted graphite sheets and indistinguishable carbon fine particles. Although there were some micro-cracks, the coating still had very high conductivity. The resistance was around 80 Ω, approximately a liminal value, which was easily obtained by controlling the scraping time. Compared to the graphite block with high thermal stability, the carbon fine particles and the edges of the graphite sheets in the coating should have a higher surface energy because of their super small sizes, according to general physicochemical theory. As a result, when this coating was calcined at a high temperature in air, these fine particles and edges had higher reactive activities with oxygen and were preferentially removed away. The thermogravimetric curve of the corresponding graphite powder in the simulate air showed that the weight loss continually increased when the temperature was increased (Fig. 1b). In the range of 200–500 °C, the loss should be attributed to the removal of fine carbon particles and the edges of the graphite sheets. Above 500 °C, all the graphite sheets would also be removed quickly. Here, the temperature of 500 °C was optimized to calcine the graphite coating. Fig. 1c shows the morphology of the graphite coating after calcination for 100 min. Due to the partial loss of carbon and the expanding–shrinking action of the graphite sheets in the heating–cooling process, the coating became very loose. The graphite sheets with irregular edges and lots of pores among the sheets could be clearly identified. The conductivity of the graphite coating was thereby drastically decreased and varied with the calcining time. As shown in Fig. 1d, as the time increased to 70 min, the resistance of the coating gradually increased from 0.1 to 1346 kΩ. After that, the resistance was too high to be measured and the coating was thought to become non-conductive. These characteristics are obviously beneficial for the electrodeposition construction of a semiconductor gas-sensor on a graphite coating. We can electrodeposit a semiconductor film on the pristine graphite coating covered substrate (without being heated) and then decrease the conductivity of the coating by a calcining process to make the final semiconductor film lie on a non-conductive support.
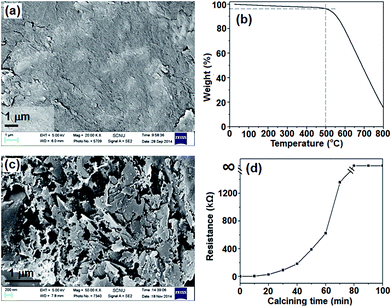 |
| Fig. 1 Characterization of the graphite coating. (a) SEM image of the pristine graphite coating; (b) thermogravimetric curve of the graphite powder; (c) SEM image of the graphite coating calcined for 100 min at 500 °C; (d) variation of the resistance of the coating with an increase in the calcining time. | |
The electrodeposited film on the graphite coating
Fig. 2a shows the morphology of the electrodeposited film on the pristine graphite coating covered on the ceramic tube after a deposition time of 90 min and before calcination. The film was composed of closely packed spherical particles with sizes of 80–200 nm. Because of the influence of the bottom graphite coating, some cracks could be generated during the growth of the film. In the XRD pattern (Fig. 2b-①) of the hybrid film (composed of the bottom graphite coating and the upper electrodeposited film), only a peak at ∼26° was found and this should be attributed to the carbon (002) plane, which explains that the electrodeposited particle film was amorphous. After being calcined for 100 min at 500 °C, the amorphous substance was transformed into crystalline SnO2. The (110), (101) and (211) planes of SnO2 were clearly displayed in the corresponding XRD pattern (JCPDS no. 41-1445) (Fig. 2b-②). The peak of graphite could be still discerned. The morphology of the calcined sample is shown in Fig. 2c. The shapes and sizes of the particles remained approximately consistent with those before calcination. However, the cracks had been multiplied and enlarged, which divided the film into patches in certain areas. Through the cracks (inset of Fig. 1c), the graphite sheets could be found and they connected the adjacent SnO2 particle film patches. Notably, during the calcining process, the resistance of the hybrid film experienced a regular variation (Fig. 2d). It first gradually increased from 0.14 kΩ (the resistance of the hybrid film before being calcined) to 680 kΩ as the calcining time increased to 100 min, and then remained almost unchanged when the calcination continued.
 |
| Fig. 2 Characterization of the electrodeposited film on the graphite coating. (a) SEM image of the film before calcination; (b) XRD pattern of the film before (①) and after (②) calcination for 100 min; (c) SEM image of the film calcined for 100 min; (d) variation of resistance of the film with calcining time. The calcination temperature was controlled at 500 °C. | |
Formation and conductive mechanism of the film on the graphite coating
During the electrodeposition process in the mixed solution of SnSO4, NaNO3 and HNO3 at room temperature, on the cathode electrode surface (graphite coating), two half reactions would occur as follows:15–17 |
NO3− + H2O + 2e− → NO2− + 2OH−
| (1) |
|
NO3− + 7H2O + 8e− → NH4+ + 10OH−
| (2) |
Once OH− ions formed on the graphite coating, they would then immediately react with Sn2+ ions to form Sn(OH)2:
|
Sn2+ + 2OH− → Sn(OH)2↓
| (3) |
In the electrolyte exposed to air, some Sn2+ ions might be oxidized into Sn4+ ions, and these ions would still react with OH− ions to produce Sn(OH)4. Because the surface of the graphite coating was nearly homogenous, plus the corresponding reactions were very quick, the as-formed tin hydroxide particles showed spherical shapes and amorphous state (Fig. 2b). In the subsequent heat treatment in air at 500 °C, tin hydroxides would be decomposed and oxidized to generate crystalline SnO2. At the same time, the graphite coating at the bottom would be partially oxidized and expanded. Because of the difference in the expansion coefficients between graphite and the tin-containing compounds (i.e. tin hydroxides and SnO2), the electrodeposited film naturally generated many cracks. Accompanying these chemical changes and physical actions, the conductivity of the heated film would decrease gradually until it reached a stable state, as shown in Fig. 2d.
The conductivity mechanism was suggested as follows: based on the electrodeposition principle, the obtained tin-containing compound film must be always closely adhered to the graphite coating even though they were heated at a high temperature and generated many cracks, as shown in Scheme 2a and b. Once a voltage was applied to the electrodes on the two ends of the ceramic tube, the bottom graphite coating and the upper tin-containing compound film could form a circuit (Scheme 2a1 and b1). Because of the difference in resistance between the two films, the intensity of the current allocated to them would be different.18 Before calcination, the electrodeposited amorphous tin hydroxides were non-conductive and had super high resistance, but the pristine graphite coating was a good conductor with very low resistance, resulting in the current only passing through the graphite coating (Scheme 2a1). As the calcining time increased, tin hydroxides were gradually transformed into crystalline SnO2 with decreased resistance and increased conductivity, while the resistance of the graphite coating was always increased (as shown in Fig. 1d). The current would be thereby allowed to pass through the SnO2 layer. After calcination for 100 min, the bottom graphite layer had been changed to be non-conductive as a whole, but in local areas composed of one or several closely overlying graphite sheets, could still have good conductivity and act as conductive wires to connect the cracks in the upper SnO2 layer (as shown in Fig. 2c). Due to the deletion of the conductivity of the graphite layer and the formation of the stable SnO2 layer, the resistance of the hybrid film remained stable and the current only passed through the SnO2 layer (Scheme 2c). This was essential for the SnO2 film to work as a resistance-type gas-sensing film.
 |
| Scheme 2 Schematic illustration of the state of the electrodeposited film and the graphite coating. (a) and (b) show the state of the hybrid film before and after calcination, respectively; (a1) and (b1) show the circuit and the current flowing in the hybrid film corresponding to (a) and (b), respectively, after a voltage was applied to the two ends of the ceramic tube. | |
Gas-sensitivity of the film sensor
The ceramic tube covered with the SnO2/graphite hybrid film (heated for 100 min at 450 °C) could be directly constructed into a kind of resistive type gas sensor (Fig. 3a) used for the detection of ethanol gas in the surroundings. A practical gas-sensor should work at a suitable temperature to quickly respond to the ethanol gas, exhibit the highest sensitivity and quickly recover. Fig. 3b shows the response of the sensor to 50 ppm ethanol gas at different working temperatures. The gas sensitivity is defined as S = Rair/Rgas, where Rair and Rgas are the resistances of the sensor in the air and the air mixed with ethanol gas, respectively.19 The response time is defined as the time required to reach 90% of the equilibrium value; the recovery time is defined as the time taken for the sensor output to decrease to 10% of its steady value after the gas was removed. When the temperature was lower than 100 °C, no signal could be detected. At 100 °C, a sensitivity of 2.0 was obtained (Fig. 3c), and the response time was calculated as 35 s (inset of Fig. 3b), but the sensor couldn’t be completely recovered. As the temperature increased to 160 °C, the sensitivity gradually increased to the maximum, 8.9; both the response and the recovery time decreased to 8 s. In the range of 160–240 °C, the sensitivity, the response time and the recovery time were almost constant. When the temperature was higher than 240 °C, the sensitivity decreased with an increase in the temperature; the response and the recovery time kept constant. Obviously, the sensor could work in a wide range of temperatures, exhibiting optimal excellent performances. For energy-saving, the working temperature was optimized as 160 °C. At this temperature, the sensor could be employed to effectively detect different concentrations of ethanol gas mixed in air (Fig. 3d). The concentration limit of the detectable ethanol gas was as low as 1 ppm. The sensitivity noticeably increased with an increase in the gas concentration (Fig. 3e). When the concentration increased from 1 to 100 ppm, the sensitivity gradually increased from 2.2 to 10.4. The response time and the corresponding recovery time were always limited to the range of 7–9 s.
 |
| Fig. 3 (a) A photo of the SnO2/graphite hybrid film sensor; (b) and (c) response and sensitivity of the sensor in detecting 50 ppm ethanol gas at different working temperatures; the inset of (b) shows the corresponding response and recovery time; (d) and (e) response and sensitivity of the sensor in detecting different concentrations of ethanol gas at 160 °C. | |
Sensing mechanism and influential facts on the sensitivity
Generally, when the n-type SnO2 semiconductor is used in a gas-sensor and exposed to air, O2 molecules will be chemisorbed and capture some electrons of SnO2 to be changed into O2−, O− and O2− on the sensing body surfaces.20,21 After the reducing gas (e.g., ethanol gas) is introduced, some of the oxygen species will be reduced and removed from the surfaces, and the captured electrons will be released to pour back to SnO2, resulting in the variation of the resistance of SnO2 and the exhibition of sensitivity. For the SnO2/graphite hybrid film reported here, because the pure graphite film (whether heated or not) had no response to ethanol gas (not shown here), the surface area of the SnO2 film exposed to the atmosphere and the ratio of the electric current passing through the SnO2 film would be decisive for the final sensitivity of the hybrid film. It was thereby easily deduced that the electrodeposition time and the calcining time in the fabrication process should have crucial impacts on the sensitivity of the final film.
Fig. 4a shows the response of the films obtained from different electrodeposition times towards 50 ppm ethanol gas. All films had been calcined for 100 min at 500 °C and the bottom graphite coating should be non-conductive. With a short electrodeposition time, for example, 15 min, the obtained film constituted by SnO2 particles with smaller sizes should be thinner and be easier to be broken to generate more and bigger cracks per unit area during the heating process, resulting in a less exposed surface area of the SnO2 film and a lower sensitivity (3.1). With an increase in the electrodeposition time, the particles became bigger and the final SnO2 film was densified, thickened and strengthened. This could reduce the number and the size of cracks in the film, increasing the exposed surface area and the sensitivity of the SnO2 film. After an electrodeposition time of 90 min, the resulting SnO2 film had the maximum surface area and the maximum sensitivity (8.9). When continually increasing the electrodeposition time, the thickness of the film may have been increased but the surface area couldn’t be changed, so the sensitivity kept constant.
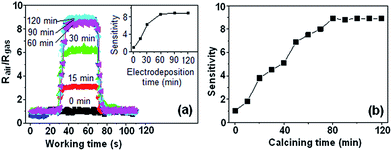 |
| Fig. 4 Effects of the electrodeposition time and calcining time in the fabrication process of the sensor on the sensing performance. (a) Response of the sensors fabricated with different electrodeposition times towards 50 ppm ethanol gas; (b) the sensitivity of the sensors fabricated with different calcining times in the detection of 50 ppm ethanol gas. | |
Taking the sample obtained from 90 min of electrodeposition as an optimal example, the effect of the calcining time on the sensitivity of the hybrid film was analyzed. Fig. 4b shows how the sensitivity of the film varied with calcining time in the detection of 50 ppm ethanol gas. Before calcination, the electric current only passed through the graphite layer and there were no SnO2 particles in the electrodeposited layer, so the hybrid film showed no response. Once the calcination at 500 °C began, the conductivity of the graphite layer gradually decreased but that of the electrodeposited layer increased because of the continuous generation of SnO2 particles, resulting in an increase of the ratio of current allocated to the electrodeposited layer when the sensor worked. The electric signal caused by the variation of the resistance of the film was more easily detected and showed higher variation, plus the total surface area of the SnO2 particles increased, leading to a gradual increase in the sensitivity until the calcining time reached 80 min. After that, the graphite layer became non-conductive, there were no new SnO2 particles generated and the sensitivity did not vary with the calcining time.
Furthermore, it should be noted that the final film was composed of spherical particles and there were many naked spherical surfaces (Fig. 2c). This increased the total surface area of the film, enhanced the adsorption for negative oxygen ions and increased the sensitivity. Besides, the grain boundaries in the film could also adsorb negative oxygen ions and have an impact on the sensing performance of the film.22 As we know, in the electrodeposition process, adjacent particles with different crystallization orientations can gradually contact and cross each other as they grow up, resulting in the formation of chemical bonding and grain boundaries between them; in the subsequent calcining processes at high temperature, the atoms are more active and it is easier for them to diffuse, and the connections between the particles is enhanced. With the increase in the electrodeposition time and the calcining time, the total number of grain boundaries would increase until the film reached a steady state. Thereby, the final SnO2 film patch here could be considered as a polycrystal with many grain boundaries. For the SnO2 gas-sensor, two different conduction mechanisms, grain boundary conduction and neck conduction, had been proposed,23,24 in addition to the surface conduction mechanism. Here, the particles had grown together and most necks were removed. Grain boundary conduction would play an essential role for the film.25 The atoms in the grain boundary had a higher activity than those in other regions and easily adsorbed more negative oxygen ions in air to build potential barriers at a lower temperature (e.g. 160 °C). After the negative oxygen ions reacted with the introduced ethanol gas, a high conductivity (/resistance) change (i.e. sensitivity) would be exhibited. Still, based on the electrodeposition mechanism, more grain boundaries should be located near the surface of the film. Meanwhile, grain boundaries buried in the bulk region were believed to be chemically inactive due to the dense morphology of the thin film.26 This could be further confirmed by the fact that the sensitivity of the film remained nearly constant with the electrodeposition time once the time was longer than 90 min (Fig. 4). The adsorption/desorption of the negative oxygen ions mainly occurred near the surface of the film, resulting in the quick response and quick recovery of the film sensor. Additionally, the close contact between the film and the substrate could allow a steady current to pass through the film and further enhance the sensing performance of the sensor. A comparison of sensor responses of some pure SnO2 gas sensors for ethanol sensing is summarized in Table 1. It was found that the present sensor exhibited better sensing properties including an optimized working temperature, sensitivity and response/recovery time.
Table 1 Comparison of the sensing characteristics of pure SnO2 gas sensors fabricated by different methods
Methods |
Working temperature (°C) |
Sensitivity (gas concentration) |
Response/recovery time (s) |
Ref. |
In situ electrodeposition |
160 |
8.9 (50 ppm) |
8/8 |
This work |
Molecular beam epitaxy |
400 |
2.8 (100 ppm) |
80/320 |
27 |
Pulsed laser deposition |
250 |
7 (60 ppm) |
8/20 |
28 |
Sputtering method |
350 |
2.5 (50 ppm) |
—/— |
29 |
Photochemical deposition |
260 |
4.6 (100 ppm) |
10/8 |
10 |
Thermal evaporation |
350 |
3.78 (50 ppm) |
—/— |
30 |
Sol–gel template method |
200 |
3.5 (50 ppm) |
—/— |
31 |
Manually coating |
300 |
7 (50 ppm) |
7/20 |
32 |
Sol–gel method |
250 |
3.2 (150 ppm) |
—/— |
33 |
Spin coating |
200 |
6.2 (400 ppm) |
170/— |
34 |
Practicality of the electrodeposition method in fabrication of gas-sensor
In the fabrication process, the electrodeposition time and the calcining time were easily controlled over a wide range to let the sensing performance of SnO2/graphite hybrid film reach a steady limit state, which was beneficial for the reproduction of sensors with uniform performance. As shown in Fig. 5a, the sensitivity of four sensors fabricated one by one under the same conditions was nearly kept consistent in the detection of 50 ppm ethanol gas. Moreover, because of the controllability of the fabrication parameters, the mass production of the sensors was also feasible. For mass production, during the electrodeposition process, several ceramic tubes could be concurrently connected (in parallel) to the cathode of the power source to obtain uniform films, and then subjected to the same heat-treatments. The different mass-produced fabricated sensors exhibited approximately the same sensing performance (Fig. 5b). More interestingly, the sensor also showed super high stability (Fig. 5c). After the sensor experienced more than 100 tests and was placed in ordinary surroundings for more than 9 months without any protection, it still exhibited nearly the same sensitivity as that when it was first used in the detection of 50 ppm ethanol gas. Thus, the sensor may be reused continuously. Humidity and CO2 gas are important factors that might affect the gas-sensing properties of a metal oxide semiconductor. The SnO2 film sensor was thus investigated for the detection of 50 ppm ethanol gas under different relative humidities and in mixed gases containing different concentrations of CO2 gas, respectively, as shown in Fig. 5d and e. As the relative humidity increased from 50% to 90%, the sensitivity exhibited a decrease of ∼6.5%; in the mixed gas containing CO2, as the concentration of the additionally introduced CO2 increased to 3 vol%, the sensitivity exhibited a decrease of ∼2.5%. These slight variations in sensitivity and the nearly unvaried response/recovery time demonstrated that humidity and the presence of CO2 gas in air had little influence on the sensor. In addition, the method was general in terms of the fabrication of semiconductor film gas-sensors on a substrate covered with a graphite coating. By this method, ZnO, Fe2O3, CuO and NiO film sensors had been also fabricated according to the reported electrodeposition process.35–39 They could response to ethanol gas too and exhibit a specific sensitivity, respectively (Fig. 5f). For the p-type CuO and NiO film, their resistances decreased with the injection of reductive ethanol gas and their sensitivity was defined as S = Rgas/Rair. Finally, it should be noted the electrodeposition method is flexible and many strategies, for example, the addition of suitable surfactants in the electrolyte, the use of templates, layer-by-layer construction and co-deposition, can be employed to control the morphology, the surface area or composition of the film, which implies that there are infinite possibilities in the construction of excellent gas-sensors. Many studies on these are in progress.
 |
| Fig. 5 Responses of (a) the reproduced sensors; (b) the mass-produced sensors; and (c) a sensor after being placed for a certain time in ordinary surroundings. (d) The effect of humidity on the response of a sensor (RH represents the relative humidity); (e) the effect of additionally introduced CO2 gas on the response of a sensor; and (f) the responses of some other typical oxide sensors in the detection of 50 ppm ethanol gas. | |
Conclusions
In summary, based on an electrodeposition method and with the assistance of a calcining process, semiconductor film gas-sensors were in situ constructed on a non-conductive substrate covered with a graphite coating. The pristine graphite coating had excellent conductivity and contributed to the implementation of the electrodeposition; after being calcined, it became non-conductive as a whole and the semiconductor film could then work as a gas-sensor. The obtained SnO2 film sensor was used in the detection of ethanol gas with concentrations as low as 1 ppm, showing fast response and recovery, high sensitivity and long-term stability. The electrodeposition time and calcining time could put impacts on the sensing performance, but once they were controlled to higher than a specific value, the sensitivity of the film would always keep nearly constant. Due to the easy controllability, the fabrication method showed extraordinary practicality and could be used in the reproduction and the mass-production of a semiconductor film sensor. The method is also general. In addition to the metallic oxide (e.g. SnO2, ZnO, Fe2O3, CuO and NiO) film sensors mentioned here, in theory, any semiconductor film (with good thermal stability) sensor could be constructed.
Acknowledgements
This work was co-supported by the Research Project of Chinese Ministry of Education (No. 213029A), the National Natural Science Foundation of China (No. 31071057), the Natural Science Foundation of Guangdong Province (No. 10351063101000001) and the Special funds for Discipline Construction in Guangdong Province (No. 2013KJCX0057).
Notes and references
- G. Neri, S. G. Leonardi, M. Latino, N. Donato, S. Baek, D. E. Conte, P. A. Russo and N. Pinna, Sens. Actuators, B, 2013, 179, 61–68 CrossRef CAS PubMed.
- L. H. Zhu, D. Z. Zhang, Y. Wang, C. H. Feng, J. R. Zhou, C. X. Liu and S. P. Ruan, RSC Adv., 2015, 5, 28105–28110 RSC.
- S. Thirumalairajan, V. R. Mastelaro and C. A. Escanhoela, ACS Appl. Mater. Interfaces, 2014, 6, 21739–21749 CAS.
- F. E. Annanouch, I. Gracia, E. Figueras, E. Llobet, C. Cane and S. Vallejos, Sens. Actuators, B, 2015, 216, 374–383 CrossRef CAS PubMed.
- Q. N. Abdullah, F. K. Yam, J. J. Hassan, C. W. Chin, Z. Hassan and M. Bououdina, Int. J. Hydrogen Energy, 2013, 38, 14085–14101 CrossRef CAS PubMed.
- K. Lizuka, M. Kambara and T. Yoshida, Sens. Actuators, B, 2012, 173, 455–461 CrossRef PubMed.
- O. Landau, A. Rothschild and E. Zussman, Chem. Mater., 2009, 21, 9–11 CrossRef CAS.
- W. Tang and J. Wang, J. Mater. Sci., 2015, 50, 4209–4220 CrossRef CAS.
- F. Q. Sun, W. P. Cai, Y. Li, L. C. Jia and F. Lu, Adv. Mater., 2005, 17, 2872–2876 CrossRef CAS PubMed.
- S. P. Xu, F. Q. Sun, F. L. Gu, Y. B. Zuo, L. H. Zhang, C. F. Fan, S. M. Yang and W. S. Li, ACS Appl. Mater. Interfaces, 2014, 6, 1251–1257 CAS.
- S. P. Xu, F. Q. Sun, S. M. Yang, Z. Z. Pan, J. F. Long and F. L. Gu, Sci. Rep., 2015, 5, 8939 CrossRef CAS PubMed.
- A. Star, V. Joshi, S. Skarupo, D. Thomas and J. P. Gabriel, J. Phys. Chem. B, 2006, 110, 21014–21020 CrossRef CAS PubMed.
- D. Jung, M. Han and G. S. Lee, Carbon, 2014, 78, 156–163 CrossRef CAS PubMed.
- M. Z. Atashbar and S. Singamaneni, Sens. Actuators, B, 2005, 111–112, 13–21 CrossRef CAS PubMed.
- S. T. Chang, I. C. Leu and M. H. Hon, J. Cryst. Growth, 2004, 273, 195–202 CrossRef CAS PubMed.
- X. P. Chen, J. Y. Liang, Z. T. Zhou, H. N. Duan, B. Q. Li and Q. M. Yang, Mater. Res. Bull., 2010, 45, 2006–2011 CrossRef CAS PubMed.
- E. Hosono, S. Fujihara, H. Imai, I. Honma and H. Zhou, Chem. Commun., 2005, 2609–2611 RSC.
- A. Tricoli and S. E. Pratsinis, Nat. Nanotechnol., 2010, 5, 54–60 CrossRef CAS PubMed.
- X. Y. Lai, J. Li, B. A. Korgel, Z. H. Dong, Z. M. Li, F. B. Su, J. A. Du and D. Wang, Angew. Chem., Int. Ed., 2011, 50, 2738–2741 CrossRef CAS PubMed.
- G. H. Lu, L. E. Ocola and J. H. Chen, Adv. Mater., 2009, 21, 2487–2491 CrossRef CAS PubMed.
- S. Mao, S. M Cui, G. H. Lu, K. H. Yu, Z. H. Wen and J. H. Chen, J. Mater. Chem., 2012, 22, 11009–11013 RSC.
- J. R. Huang, K. Yu, C. P. Gu, M. H. Zhai, Y. J. Wu, M. Yang and J. H. Liu, Sens. Actuators, B, 2010, 147, 467–474 CrossRef CAS PubMed.
- Z. H. Jin, H. J. Zhou, Z. L. Jin, R. F. Savinell and C. C. Liu, Sens. Actuators, B, 1998, 52, 188–194 CrossRef CAS.
- Y. Liu, E. Koep and M. L. Liu, Chem. Mater., 2005, 17, 3997–4000 CrossRef CAS.
- L. G. Teoh, Y. M. Hon, J. Shieh, W. H. Lai and M. H. Hon, Sens. Actuators, B, 2003, 96, 219–225 CrossRef CAS.
- S. W. Lee, P. P. Tsai and H. Chen, Sens. Actuators, B, 2000, 67, 122–127 CrossRef CAS.
- M. Kronelda, S. Novikov, S. Saukko, P. Kuivalainen, P. Kostamo and V. Lantto, Sens. Actuators, B, 2006, 118, 110–114 CrossRef PubMed.
- Y. Zhao, Z. Feng and Y. Liang, Sens. Actuators, B, 1999, 56, 224–227 CrossRef CAS.
- C. Bittencourt, E. Llobet, M. A. P. Silva, R. Landers, L. Nieto, K. O. Vicaro, J. E. Sueiras, J. Calderer and X. Correig, Sens. Actuators, B, 2003, 92, 67–72 CrossRef CAS.
- K. M. Li, Y. J. Li, M. Y. Lu, C. I. Kuo and L. J. Chen, Adv. Funct. Mater., 2009, 19, 2453–2456 CrossRef CAS PubMed.
- G. X. Wang, J. S. Park, M. S. Parkb and X. L. Gou, Sens. Actuators, B, 2008, 131, 313–317 CrossRef CAS PubMed.
- J. Zhang, J. Guo, H. Y. Xu and B. Q. Cao, ACS Appl. Mater. Interfaces, 2013, 5, 7893–7898 CAS.
- R. Rella, A. Serra, P. Siciliano, L. Vasanelli, G. de, A. Licciulli and A. Quirini, Sens. Actuators, B, 1997, 44, 462–467 CrossRef CAS.
- I. T. Weber, R. Andrade, E. R. Leite and E. Longo, Sens. Actuators, B, 2001, 72, 180–183 CrossRef CAS.
- J. Y. Zheng, S. I. Son, T. K. Van and Y. S. Kang, RSC Adv., 2015, 5, 36307–36314 RSC.
- F. Tsin, A. Venerosy, J. Vidal, S. Collin, J. Clatot, L. Lombez, M. Paire, S. Borensztajn, C. Broussillou and P. P. Grand, Sci. Rep., 2015, 5, 8961 CrossRef CAS PubMed.
- Y. Q. Wang, T. T. Jiang, D. W. Meng, J. Yang, Y. C. Li, Q. Ma and J. Han, Appl. Surf. Sci., 2014, 317, 414–421 CrossRef CAS PubMed.
- H. B. Kim, H. Kim, H. S. Sohn, I. Son and H. S. Lee, Mater. Lett., 2013, 101, 65–68 CrossRef CAS PubMed.
- X. F. Song, L. Gao and S. Mathur, J. Phys. Chem. C, 2011, 115, 21730–21735 CAS.
|
This journal is © The Royal Society of Chemistry 2015 |
Click here to see how this site uses Cookies. View our privacy policy here.