DOI:
10.1039/C5RA13862K
(Paper)
RSC Adv., 2015,
5, 82429-82437
Study on the catalytic prepolymerization of an acetylene-functional benzoxazine and the thermal degradation of its cured product
Received
14th July 2015
, Accepted 21st September 2015
First published on 22nd September 2015
Abstract
In this paper, the prepolymerization of acetylene-functional benzoxazine was carried out by using nickel acetylacetonate hydrate/triphenyl phosphine as a catalyst at a low temperature. By this method, the reaction heat of acetylene polymerization was partially released and no ring-opening polymerization of benzoxazine occurred. After that, the prepolymer was cured stepwise to obtain the cured product according to a traditional curing process. As a comparison, another cured product was directly obtained from acetylene-functional benzoxazine by the traditional method without prepolymerization. The curing behaviors and the thermal properties of these two polybenzoxazines were investigated and compared by FTIR, DSC, DMA, and TGA. Their thermal decomposition behaviors were further studied by TGA-FTIR, Py-GC/MS, and SEM. The results show that the catalytic prepolymeriztion makes the whole curing process milder and more controllable in a broader processing window. Furthermore, more crosslinked-polyacetylene structures and benzene from the catalytic prepolymerization improve the thermal stability of the polybenzoxazines. Additionally, less amine compounds were detected in the prepolymerization system during the thermal decomposition process and the appearance of the residue was stable and controllable after pyrolysis.
1 Introduction
Polybenzoxazines are a kind of high performance thermosetting resins with excellent molecular design flexibility, good flame retardancy, high thermal stability and char yield.1,2 In order to further improve the thermal stability of polybenzoxazines, reactive functional groups or rigid groups were introduced into the benzoxazine monomers through molecular design.3–12 Ishida et al. synthesized a series of acetylene-functional benzoxazines which had superior thermal stability and high char yields.13–15 The following thermal degradation research on these polybenzoxazines showed that the polymerization of acetylene groups could greatly improve the thermal stability of the hanging amine species and extend the chain length of the polymers, which finally led to a higher char yield.16 However, the thermally activated polymerization of acetylene groups and oxazine rings usually occurs simultaneously during the curing process, and the viscosity of the curing system increases in an extremely short time.15 Especially, the polymerization of the acetylene groups releases huge heat, which is very adverse for processing of materials.17
According to the researches of arylacetylene resins, some efforts have been made to lower the crosslinking reaction temperature and control the reaction heat of the acetylene groups in the curing process. For example, some catalysts like nickel catalysts, copper catalysts and palladium catalysts were used.18–22 By this method, the release of the reaction heat becomes mild and the polymerization is controllable.
In this article, nickel acetylacetonate hydrate/triphenyl phosphine as a catalyst was applied for the acetylene-functional benzoxazine. A prepolymer was prepared first by catalytic polymerization of the partial acetylene groups without the occurrence of ring-opening polymerization of benzoxazine. Afterwards, a traditional curing procedure was used to get the polybenzoxazine based on the polymerization of oxazine ring and residual acetylene groups. By this method, the crosslinking reaction of the acetylene groups could occur before that of the oxazine rings, and the polymerization heat of the acetylene groups released partly during prepolymerization, which made the following reaction mild. Therefore, the whole polymerization reactions became controllable. As a comparison, another polymer of acetylene-functional benzoxazine was directly prepared by the same traditional method without catalyst or prepolymerization. Both curing behaviors and thermal properties of these two polybenzoxazines were investigated. Furthermore, their thermal degradation behaviors were studied. Based on these results, we explained the reason why the prepolymerization could improve the thermal stability of cured acetylene-functional benzoxazine. Related degradation mechanisms were also illuminated.
2 Experimental
2.1 Materials
All chemicals were used as received. 3-Aminophenylacetylene (99%) was obtained from Shandong Jiaozhou Fine Chemicals Co. Nickel acetylacetonate hydrate and triphenyl phosphine were obtained from Aladdin Fine Chemicals Co. Formaldehyde, phenol, salicylaldehyde, sodium borohydride, ethanol, toluene, and butanone were bought from Chengdu Kelong Fine Chemicals Co.
2.2 Synthesis of 3-(3-ethynylphenyl)-3,4-dihydro-2H-benzo[e][1,3]oxazine
Three-step method for preparing acetylene-functional benzoxazine (Fig. 1) was used.23 The desired product is denoted as Ph-apa. 1H NMR (400 MHz, DMSO-d6, 298 K), ppm: δ: 4.14 (s, 1H,
CH), 4.67 (s, 2H, C–CH2–N–), 5.46 (s, 2H, N–CH2–O–), 6.72–7.26 (m, 8H, Ar); FTIR (KBr, cm−1): 3280 (stretching of
C–H), 2104 (stretching of C
C), 1230 (asymmetric stretching of C–O–C), 1160 (asymmetric stretching of C–N–C), 942 (out of plane C–H stretch of benzene attached to oxazine).
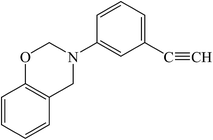 |
| Fig. 1 Chemical structure of Ph-apa. | |
2.3 Preparation of prepolymer and polybenzoxazines
Ph-apa (0.1 mol), nickel acetylacetonate hydrate (1.35 × 10−3 mol) and triphenyl phosphine (1.35 × 10−3 mol) were mixed in butanone (40 ml) at 95 °C for 5 h in a nitrogen atmosphere. Then, the mixture was dried at 50 °C under vacuum to remove the solvent. The prepolymer is denoted as Pre(Ph-apa-ca). For comparison, the mixture which wasn't prepolymerized is denoted as Ph-apa-ca.
Then, Pre(Ph-apa-ca) and Ph-apa were cured in an oven by following steps: 120 °C (1 h), 140 °C (1 h), 160 °C (1 h), 180 °C (1 h), 200 °C (1 h) and 230 °C (2 h). The polybenzoxazines are represented as Polypre(Ph-apa-ca) and Poly(Ph-apa) respectively.
Ph-apa-ca was cured at 120 °C for 10 min in the oven. The explosive polymerization happened and the sample formed char suddenly. The residual cast is represented as Poly(Ph-apa-ca).
2.4 Measurements and characterization
Fourier transform infrared (FTIR) spectra of the cured samples were obtained using a Nicolet Magna 560 spectrometer with a resolution of 4 cm−1 and a scanning mode of 32 times. The samples were ground with spectroscopy-grade KBr. 1H NMR spectra were recorded using Bruker Avance 400 Hz NMR spectrometers in DMSO-d6. Differential scanning calorimetry (DSC) was performed on a TA Instruments Q20 model using 5–10 mg of the sample at a heating rate of 10 °C min−1 from 40 to 350 °C under nitrogen atmosphere. The thermal mechanical properties of the cured casts were obtained by using TA instruments DMA Q800 dynamic mechanical analyzer (DMA) with sample dimensions of 30 mm × 10 mm × 3 mm in a three point bend mode from 20 to 400 °C with a heating rate of 5 °C min−1 and a frequency of 1 Hz. The pyrolysis samples were prepared under nitrogen atmosphere in a tubular furnace reactor. A heating rate of 10 °C min−1 was used from room temperature to desired temperatures (350 °C, 420 °C, 520 °C and 650 °C). The morphologies of polymer bulks were observed by field emission-scanning electron microscope (FESEM) FEI Inspect F. The samples were fractured in liquid nitrogen. Then the fractured surfaces were coated with gold and observed with an accelerating voltage of 20 kV. Thermogravimetric analysis (TGA) was performed using a TA Q600 thermal analyzer. Cured samples were analyzed in an open silicon pan from room temperature to 800 °C at a heating rate of 10 °C min−1 under nitrogen atmosphere. Thermogravimetry coupled with Fourier transform infrared spectroscopy (TGA-FTIR) experiments were carried out on a TA Instruments TA-Q500 thermogravimetric analyzer interfaced to a Nicolet 6700 Fourier transform infrared spectrometer. Thermal degradation of the samples was under nitrogen atmosphere from 30 to 820 °C at a heating rate of 20 °C min−1. The temperatures of the transfer line and gas cell were both set at 150 °C to prevent gas condensation. FTIR spectra were collected with 4 scans co-added at a resolution of 8 cm−1, resulting in a time resolution of 1 s. About 20 mg of cured samples were used. Pyrolysis-Gas chromatography/Mass spectrometry (Py-GC/MS) analysis was carried out using a combination of single-point pyrolyzer PY-2020i (Frontier, Japan) and chromatograph-mass spectrometer GC/MS QP2010 (Shimadzu, Japan) equipped with a pyrolysis injection system. Stepwise-temperature method was applied in Py-GC/MS test to study the transformation of chemical structures of polymer bulk during pyrolysis process at high temperatures. As shown in Fig. 2, the polymer bulk (mo) was pyrolyzed at temperature T1 to give a char (C1) and volatile products (P1). Then, the C1 (namely m1) was pyrolyzed again at T2 to gain the char (C2) and the corresponding volatile products (P2). The continuous tests were done at T3 and T4.
 |
| Fig. 2 Schematic diagram of the stepwise-temperature method applied in Py-GC/MS. | |
3 Results and discussion
3.1 DSC analysis
DSC results are shown in Fig. 3. As seen in Fig. 3(a), only one exothermic peak at 247 °C was observed for Ph-apa, suggesting that the ring-opening polymerization of benzoxazine and the crosslinking reaction of the acetylene groups occurred at the same time. A huge exothermic enthalpy of 879 J g−1 mainly due to the crosslinking reaction of the acetylene groups was seen, which is adverse for processing. In addition, this fast and high exothermic heat may affect sufficient crosslinking reaction. However, the results became different after adding the catalyst. For Ph-apa-ca without the prepolymerization in Fig. 3(b), the original one exothermic peak turned into two peaks at lower temperatures. The lower temperature at 184 °C should be mainly attributed to the crosslinking reaction of the residual acetylene groups due to the catalyzing effect. Also, we found that the total exothermic enthalpy of Ph-apa-ca was 878 J g−1 which was still very high, indicating that the catalyst accelerated the polymerization of acetylene groups without changing the total quantity of the released heat. The catalyst can induce the polymerization of the acetylene groups with releasing heat at a relative low temperature. This explained why the explosive polymerization could happen when Ph-apa-ca was cured only at 120 °C for 10 min in an oven. When the explosive polymerization occurred with releasing a lot of heat, the actual temperature in the resin would be much higher than 120 °C, which made the whole curing reaction finish rapidly.
 |
| Fig. 3 DSC curves of Ph-apa (a), Ph-apa-ca (b) and Pre(Ph-apa-ca) (c). | |
Moreover, it is interesting to observe that, for Pre(Ph-apa-ca) in Fig. 3(c), the first exothermic peak became smaller after prepolymerization, meaning that a part of the acetylene groups experienced the crosslinking reactions during the prepolymerization because of the catalysis. The total exothermic enthalpy decreased from 878 J g−1 to 555 J g−1, which made the explosive polymerization not occur during the following curing process of Pre(Ph-apa-ca). A perfect cured sample, Polypre(Ph-apa-ca), was obtained via this prepolymerization. Additionally, the peak temperature of the first exothermic peak for Pre(Ph-apa-ca) attributed to residual acetylene groups decreased from 184 °C to 152 °C after the prepolymerization. The cyclotrimerization of acetylene groups usually needs a temperature above 220 °C, but catalysts can lower the reaction temperature.24 So, the decrease of the peak temperature in Fig. 3(c) implied that the cyclotrimerization temperature of the acetylene groups may decrease after the catalytic prepolymerization, and more benzene structures may be formed.
Above all, the prepolymerization makes the acetylene groups polymerize at a relative low temperature with releasing a part of heat and further lowers the curing temperature.
3.2
1H NMR analysis
The 1H NMR spectrum of Ph-apa is shown in Fig. 4(b). The resonances of
C–H, Ar–CH2–N, and N–CH2–O protons appeared at 4.14 ppm, 4.67 ppm and 5.46 ppm, respectively, while the Ar–H protons were at 6.72–7.26 ppm. The 1H NMR spectrum of Pre(Ph-apa-ca) is shown in Fig. 4(a). Obviously, the peak area of the acetylene groups decreased from 1.0 to 0.69, and a new resonance at 6.68 ppm due to
C–H appeared. At the same time, the whole peak area of Ar–H increased correspondingly. These results indicated that a part of acetylene groups underwent the crosslinking reaction and turned into short chain polyene after prepolymerization. The calculated data showed that about 31% of acetylene groups in Ph-apa underwent the conversion. Additionally, the peak areas of methylenes in benzoxazine ring were nearly unchanged after prepolymerization, suggesting that the prepolymerization has little influence on the ring-opening reaction of benzoxazine. The curing reaction sequence of this acetylene-functional benzoxazine was successfully controlled by the prepolymerization.
 |
| Fig. 4 The 1H NMR spectra of Pre(Ph-apa-ca) (a) and Ph-apa (b). | |
3.3 FTIR analysis
FTIR spectra of the benzoxazine monomer and prepolymer are shown in Fig. 5(a) and (b). The bands at 3280 cm−1 and 942 cm−1 represent the characteristic peaks of acetylene groups and oxazine rings respectively. After the prepolymerization, the band at 942 cm−1 didn't change and the band at 3423 cm−1 assigned to the hydroxyl groups from the ring-opening reaction of oxazine ring was not observed. This result also supports the fact that the prepolymerization has little influence on the oxazine rings. Additionally, a small C
C stretching vibration at 1680 cm−1 appeared for Pre(Ph-apa-ca), indicating the formation of short chain polyene structures after the prepolymerization. In order to investigate the reaction degree of acetylene groups after catalytic prepolymerization, a change ratio of the band at 3280 cm−1 was calculated. The band at 2920 cm−1 due to the C–H stretching of methylene group was used as an internal standard. The ratios of integrated intensities of the bands at 3280 cm−1 to the internal standard band in Pre(Ph-apa-ca) and Ph-apa were 6.91 and 10.79, respectively. Their ratio was 64.0%. This meant that 36.0% of acetylene groups reacted after prepolymerization, which is similar to the NMR results.
 |
| Fig. 5 FTIR spectra of Ph-apa (a), Pre(Ph-apa-ca) (b), Poly(Ph-apa-ca) (c), Polypre(Ph-apa-ca) (d) and Poly(Ph-apa) (e). | |
The FTIR spectra of Poly(Ph-apa) and Polypre(Ph-apa-ca) are shown in Fig. 5(d) and (e). For both polymers, the band at 942 cm−1 assigned to oxazine ring disappeared after curing, while the band at 3423 cm−1 due to the hydroxyl group appeared, which meant that the polymerization of benzoxazines happened. When the cyclotrimerization of acetylene groups occurs, 1,3,5-trisubstituted benzene ring will be formed. As seen in Fig. 5(d) and (e), the band at 3280 cm−1 assigned to acetylene groups almost disappeared. At the same time, the intensity of the band at 3045 cm−1 assigned to Ar–H increased after curing, which proved the formation of new benzene rings from the cyclotrimerization of acetylene groups in Ph-apa and Pre(Ph-apa-ca).15 Meanwhile, the bands at 1680 cm−1 and 700 cm−1 assigned to short chain polyene structures from the polymerization of the acetylene groups were observed in Poly(Ph-apa), while the bands at 1668 cm−1 and 700 cm−1 assigned to C
C group were found in Polypre(Ph-apa-ca). As we know, when the chain length of polyene structures extend to form polyacetylene, a red shift of the characteristic band of C
C group in FTIR spectra will happen. So, the change from 1680 cm−1 to 1668 cm−1 on the C
C group indicated that more polyacetylene structures existed in Polypre(Ph-apa-ca) compared with Poly(Ph-apa).
The effect of the catalytic prepolymerization on the crosslinking reaction of the acetylene groups was further investigated. The ratios of integrated intensities of the bands at 3045 cm−1 to the integrated intensity of the internal standard band in Polypre(Ph-apa-ca) and Poly(Ph-apa), were 2.44 and 1.60 respectively. As mentioned above, the characteristic band at 3045 cm−1 was attributed to benzene ring structure. These ratios indicated that more benzene ring structures existed in the Polypre(Ph-apa-ca) compared with Poly(Ph-apa). The possible reason is that the reactions of acetylene groups and oxazine rings in Ph-apa are drastic with releasing a lot of heat, which makes the viscosity of the system increase quickly and forces the acetylene groups to form oligomers like short chain polyenes. However, for Pre(Ph-apa-ca), the reaction heat releases partly during the prepolymerization, so the system viscosity increases slowly during curing and the crosslinking reaction of the acetylene groups was relatively mild, which made more acetylene groups form polyacetylene and benzene structures.
Furthermore, the FTIR spectra of Poly(Ph-apa-ca) is shown in Fig. 5(c). The characteristic peaks of benzoxazine and acetylene groups disappeared after the explosive polymerization, which meant that the polymerization of benzoxazine and acetylene groups occurred in a short time. However, the band at 1680 cm−1 assigned to short chain polyene structures was not detected. These structures may undergo the thermal degradation under a great amount of heat released from the explosive polymerization.
Combined with the above results, the possible crosslinked structures of Polypre(Ph-apa-ca) and Poly(Ph-apa) are speculated in Fig. 6. Due to the polymerization of the acetylene groups, short chain polyenes, polyacetylene, and trisubstituted benzene structures formed in both polybenzoxazines.25–28 During the prepolymerization of Pre(Ph-apa-ca), some acetylene groups react and form the short chain polyenes which further transform into polyacetylene structures upon the following curing. More polyacetylene and benzene structures exist in the Polypre(Ph-apa-ca), which leads to its high thermal stability.
 |
| Fig. 6 The network structures of Polypre(Ph-apa-ca) and Poly(Ph-apa). | |
3.4 Dynamic mechanical analysis
The comparison of the thermal properties of Polypre(Ph-apa-ca) and Poly(Ph-apa) was carried out by the DMA tests. DMA result of Poly(Ph-apa-ca) wasn't obtained because we couldn't get a suitable sample due to the foam during its cure. Poly(Ph-apa) and Polypre(Ph-apa-ca) showed Tgs (E′′) of 326 °C and 348 °C, respectively, which were very high among polybenzoxazines. These results are similar to the previous report that the cured acetylene functional benzoxazines have Tgs of over 300 °C.14 As seen in Fig. 7, The E′, E′′ and tan
δ values of both polybenzoxazines were almost the same before 250 °C. After that, E′ of Poly(Ph-apa) had a fast decrease, which resulted in a lower Tg than Polypre(Ph-apa-ca). It is known that higher Tg corresponds to higher crosslinking density for polybenzoxazine.29 Although all acetylene groups for Poly(Ph-apa) and Polypre(Ph-apa-ca) are consumed during curing, the formed crosslinked structures are different. Polypre(Ph-apa-ca) contains more crosslinked polyacetylene and benzene structures than Poly(Ph-apa) because the prepolymerization promotes corresponding reactions of the acetylene groups, which leads to higher crosslinking density and network rigidity for Polypre(Ph-apa-ca).
 |
| Fig. 7 Dynamic mechanical spectra of Poly(Ph-apa) and Polypre(Ph-apa-ca). | |
3.5 TGA analysis
Thermal stability of polymers usually depends on their crosslinked structures. As shown in Fig. 8, Polypre(Ph-apa-ca) showed better thermal stability than Poly(Ph-apa). The temperatures at 5% and 10% loss weight of Polypre(Ph-apa-ca) were almost 15 °C higher than those of Poly(Ph-apa). Also, the char yield of Polypre(Ph-apa-ca) at 800 °C was 64% which was higher than 54% of Poly(Ph-apa). The higher thermal stability of Polypre(Ph-apa-ca) is because there are more thermal stable crosslinked structures restraining the degradation.
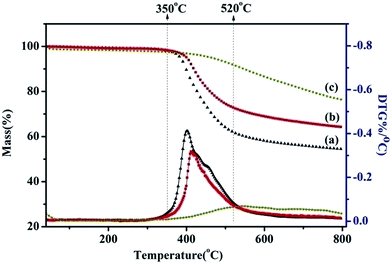 |
| Fig. 8 The TGA curves of Poly(Ph-apa) (a), Polypre(Ph-apa-ca) (b) and Poly(Ph-apa-ca) (c). | |
Furthermore, the main difference in the weight loss between Polypre(Ph-apa-ca) and Poly(Ph-apa) occurred in a temperature range from 350 °C to 520 °C. It can be seen that Polypre(Ph-apa-ca) had a low degradation rate than Poly(Ph-apa). Polypre(Ph-apa-ca) showed a maximum rate of −0.310% °C−1 at 413 °C, while Poly(Ph-apa) had a maximum rate of −0.412% °C−1 at 402 °C. After 520 °C, both polybenzoxazines showed a similar loss trend. So, it can be speculated that the difference of thermal stability between these two polybenzoxazines would be mainly attributed to the degradation between 350 °C and 520 °C.
It should be noted that Poly(Ph-apa-ca) also showed a very high char yield of 76% at 800 °C. But this meant nothing because the degradation and char forming had already occurred during its curing. It was meaningless to compare it with other two polybenzoxazines.
3.6 The morphology analysis
After heated at high temperatures, Polypre(Ph-apa-ca) and Poly(Ph-apa) showed different appearances (Fig. 9(a)). As the degradation temperature increased from 25 °C to 650 °C, Poly(Ph-apa) began to foam and deform severely while Polypre(Ph-apa-ca) just changed a little. Compared to Poly(Ph-apa), Polypre(Ph-apa-ca) showed much better shape stability under high temperatures. SEM graphs of both polybenzoxazines after heated at 420 °C are shown in Fig. 9(b) and (c). There was lots of foam morphology existing in the body of Poly(Ph-apa) attributing to the volatilization of degradation compounds. In the body of Polypre(Ph-apa-ca), the resin matrix still occupied a major part and only few foams could be found, suggesting that the crosslinked structures of Polypre(Ph-apa-ca) were more thermal stable. This result agrees well with the results from TGA.
 |
| Fig. 9 The photos of the two polymers during pyrolysis (a), the SEM graphs of Poly(Ph-apa) (b) and Polypre(Ph-apa-ca) (c) after 420 °C. | |
3.7 TGA-FTIR analysis
To study the degradation of both polybenzoxazines, two-dimensional TGA-FTIR spectra of Poly(Ph-apa) and Polypre(Ph-apa-ca) are shown in Fig. 10. The volatiles for Poly(Ph-apa) were detected at 420 °C which was lower than 450 °C of Polypre(Ph-apa-ca). Poly(Ph-apa) showed a larger amount of volatiles than Polypre(Ph-apa-ca), indicating Polypre(Ph-apa-ca) had better thermal stability.
 |
| Fig. 10 The FTIR spectra of the two polymers during degradation process: (a) Polypre(Ph-apa-ca), (b) Poly(Ph-apa). | |
As we know, phenols and amine compounds are the main volatiles during the degradation of polybenzoxazines. The release of phenols and amine compounds could be traced by the absorption bands at 3656 cm−1 and 3337 cm−1, respectively. Low et al. also studied the thermal degradation of acetylene functional polybenzoxazines by TGA-FTIR, however, ammonia was found instead of aniline species in their report.16 Usually, the release of amine compounds occurs at a lower temperature than that of phenols because of the weak C–N bond. However, it could be observed in this case that the release of the amine compounds occurred after that of phenols for both polybenzoxazines, which implied that there were more stable structures in the amine compounds. They undoubtedly came from the crosslinking reaction of the acetylene groups attached to aniline. Furthermore, it should be noticed that the amine compounds were detected mainly around 530 °C for Poly(Ph-apa). But for Polypre(Ph-apa-ca), the release of the amine species was little at 530 °C and retarded to over 700 °C. This suggested that the amine species in Polypre(Ph-apa-ca) were more stable than that in Poly(Ph-apa) because the prepolymerization made the acetylene groups form more stable structures and prevented the release of the volatiles.
3.8 Py-GC/MS analysis
To further study the different degradation processes between Poly(Ph-apa) and Polypre(Ph-apa-ca), a stepwise-temperature testing method based on Py-GC/MS was applied. Previous studies16 on degradation mechanism of the cured acetylene functional benzoxazines were focused on the classification and the content percentage (CPn) of various degradation products during the whole degradation process. However, in our studies, a stepwise-temperature testing method based on Py-GC/MS could tell us the CPn of various degradation products at different degradation temperatures. Based on the methods of the mass spectrometry and the classification used before,30–32 the decomposition products were grouped into eleven types, including small molecule gas (abbr. as Gas), phenolic compounds (–OH), amines (–NH), Mannich bases (Mannich), benzene derivatives (Ph), biphenyl compounds (Biph), bisphenol derivatives (Bi–OH), 2,3-benzofuran derivatives (Bf), naphthalene (Na), paranaphthalene (Pna), and phenanthridine derivatives (Pd). The products including –OH, –NH, Mannich, Ph, and Gas from the primary degradation products were obtained directly from the cleavage of the original networks of polybenzoxazines, and the other volatile species came from the secondary degradation products resulted from the further reactions of the polymer bulks. However, in the previous studies of the thermal degradation of cured acetylene functional benzoxazine, the secondary degradation products of Bf, Na, Pna and Pd were not discussed.16 Based on the weights of the sample at different degradation temperatures and our previous research,33,34 Δmn (losing-weight percentage), EMPn (mass percentage of each volatile type at a certain temperature), and TEMP (the total mass percentage of each degradation products during the whole thermal degradation process) were calculated by eqn (1)–(3), respectively. The results are listed in Table 1. |  | (1) |
| EMPn = Δmn × CPn (n = 1, 2, 3, 4) | (2) |
|  | (3) |
Table 1 Contents of thermal degradation volatiles at different pyrolysis temperatures
|
|
Δmn (%) |
|
Primary degradation products (%) |
Secondary degradation products (%) |
–OH |
–NH |
Mannich |
Ph |
Gas |
Bi–OH, Pd, Bf, Bi-ph, Na, Pna |
Note that this value has eliminated the proportion of the catalyst.
|
Poly(Ph-apa) |
350 °C |
11.7 |
EMP1 |
4.88 |
5.31 |
1.25 |
— |
— |
— |
420 °C |
16.4 |
EMP2 |
10.88 |
3.50 |
0.62 |
0.48 |
— |
0.71 |
520 °C |
9.3 |
EMP3 |
3.1 |
1.18 |
— |
— |
3.72 |
1 |
650 °C |
1.1 |
EMP4 |
0.1 |
0.08 |
0.06 |
0.18 |
0.54 |
0.11 |
|
|
T
EMP
|
18.96 |
10.07 |
1.93 |
0.66 |
4.26 |
1.82 |
Polypre(Ph-apa-ca) |
350 °C |
3.3a |
EMP1 |
1.71 |
0.09 |
1.53 |
— |
— |
— |
420 °C |
15.3 |
EMP2 |
12.45 |
0.92 |
1.06 |
— |
— |
0.56 |
520 °C |
10.2 |
EMP3 |
8.48 |
0.48 |
— |
— |
0.97 |
0.7 |
650 °C |
1.3 |
EMP4 |
0.15 |
0.21 |
0.04 |
0.29 |
0.32 |
0.21 |
|
|
T
EMP
|
22.79 |
1.7 |
2.63 |
0.29 |
1.29 |
1.47 |
The contents of thermal degradation volatiles at different pyrolysis temperatures in Polypre(Ph-apa-ca) and Poly(Ph-apa) were shown in Table 1. As shown in Table 1, the TEMP values of –NH in Poly(Ph-apa) and Polypre(Ph-apa-ca) were 10.07% and 1.7% respectively, which were significantly different. This result indicated that the amine species were more stable in Polypre(Ph-apa-ca) than that in Poly(Ph-apa) because of the prepolymerization. The Gas began to appear at 520 °C and the release amounts of the Gas both reached maximum at 520 °C in the two polymers. However, the release amounts of Gas were quite different. The EMP3 of Gas in Poly(Ph-apa) was 3.72%, which was nearly four times of that in Polypre(Ph-apa-ca). The TEMP value of Gas in Poly(Ph-apa) was 4.26%, while that in Polypre(Ph-apa-ca) was 1.29%. These phenomena above indicated that the prepolymerization prevented the release of Gas. For secondary degradation products in these two polymers, both began to appear at 420 °C and reached maximum release amounts at 520 °C. The EMP3 values of the secondary degradation products in Poly(Ph-apa) and Polypre(Ph-apa-ca) were 1% and 0.7% respectively. The TEMP value of secondary degradation products in Poly(Ph-apa) was 1.82%, which was slightly higher than that in Polypre(Ph-apa-ca), 1.47%. These phenomena showed that the prepolymerization could also prevent the release of secondary degradation products.
Combined with the above results, it is believed that the prepolymerization makes more acetylene groups transform to polyacetylene and benzene structures in Polypre(Ph-apa-ca). Polypre(Ph-apa-ca) exhibits a higher crosslinking density, which strongly fixes the attached amine species in the crosslinking system. So, when the Ar–C and Ar–N bonds break during the thermal degradation, the complex crosslinked structures can still maintain so that the release of Gas and secondary degradation products become difficult.
In addition, the release of the –OH in the both polybenzoxazines were similar. The EMPns of –OH firstly increased and then decreased with the temperature increasing. The EMP2s of –OH reached the maximum at 420 °C in both polybenzoxazines. This was because that the acetylene groups attached to amines had little influence on the phenolic species. Besides, the total mass percentages of other degradation products, such as Ph, Mannich, were similar in both polybenzoxazines.
3.9 Pyrolysis process of polymer bulk
As shown in Fig. 11, the pyrolysis and char formation processes of the two polybenzoxazines were speculated. The primary degradation reactions of the polymer bulks occurred during 350–420 °C, and the phenols and the amines formed by the breaking of C–C and C–N bonds. Due to the prepolymerization, more polyacetylene and benzene structures formed in Polypre(Ph-apa-ca). These crosslinked structures could further lock the amine species in the polymers so that less amine species were detected in the Polypre(Ph-apa-ca). When the temperature increased from 420 °C to 520 °C, C–C and C–N bands continued to break, and the phenols and the amines were still the major degradation products. Due to the prepolymerization, more crosslinked structures existed in Polypre(Ph-apa-ca), which prevented the release of the secondary degradation products, so that less secondary degradation products were detected in Polypre(Ph-apa-ca) than that in Poly(Ph-apa). When the temperature was above 520 °C, the primary degradation reaction nearly finished, while the secondary degradation reaction became severely and finally formed char. During this process, more chars formed in Polypre(Ph-apa-ca).
 |
| Fig. 11 Evolution of gas and bulk during thermal degradation of Polypre(Ph-apa-ca) and Poly(Ph-apa). | |
4 Conclusion
A new method was applied to cure acetylene-functional benzoxazine by adjusting the curing reaction and changing the crosslinked structures. Nickel acetylacetonate hydrate/triphenyl phosphine was used as the catalyst to prepare the prepolymer at a low temperature. The chemical structures, thermal properties, and degradation behaviors of Polypre(Ph-apa-ca) and Poly(Ph-apa) were discussed in detail. The results showed that the catalytic prepolymeriztion made the whole curing process milder and more controllable in a broader processing window. Polypre(Ph-apa-ca) owned higher crosslinking density, better thermal stability, and more controllable stable char shape than Poly(Ph-apa). Due to the prepolymerization, more acetylene groups transformed into polyacetylene and benzene structures in Polypre(Ph-apa-ca). These crosslinked structures made the amine species more stable. Therefore, less amine compounds were detected in the thermal degradation process of Polypre(Ph-apa-ca). Combined with the above results, we described the thermal degradation process of both polybenzoxazines.
Acknowledgements
This work was supported by the Research Foundation of Sichuan University, Fundamental Research Funds for the Central Universities (No. 2013SCU04A27) and financially supported by State Key Laboratory of Polymer Materials Engineering (Grant No. sklpme2014-3-13).
References
-
H. Ishida, Handbook of Benzoxazine Resins, ed. H. I. Agag, Elsevier, Amsterdam, 2011, pp. 3–81, DOI:10.1016/b978-0-444-53790-4.00046-1.
- N. N. Ghosh, B. Kiskan and Y. Yagci, Prog. Polym. Sci., 2007, 32, 1344–1391 CrossRef CAS PubMed.
- Z. Huachuan, L. Min, D. Yuyuan, Z. Chengxi, R. Qichao and G. Yi, J. Appl. Polym. Sci., 2014, 131, 40823 Search PubMed (40827 pp.)-40823 (40827 pp.).
- Y. L. Liu, C. Y. Chang, C. Y. Hsu, M. C. Tseng and C. I. Chou, J. Polym. Sci., Part A: Polym. Chem., 2010, 48, 4020–4026 CrossRef CAS PubMed.
- Q. C. Ran, Q. Tian and Y. Gu, Chin. Chem. Lett., 2006, 17, 1305–1308 CAS.
- Y. Yagci, B. Kiskan and N. N. Ghosh, J. Polym. Sci., Part A: Polym. Chem., 2009, 47, 5565–5576 CrossRef CAS PubMed.
- T. Agag and T. Takeichi, Macromolecules, 2001, 34, 7257–7263 CrossRef CAS.
- T. Chaisuwan and H. Ishida, J. Appl. Polym. Sci., 2006, 101, 548–558 CrossRef CAS PubMed.
- Y. Gao, F. R. Huang, Q. L. Yuan, Y. Zhou and L. Du, High Perform. Polym., 2013, 25, 677–684 CrossRef PubMed.
- H. M. Qi, G. Y. Pan, Y. Q. Zhuang, F. R. Huang and L. Du, Polym. Eng. Sci., 2010, 50, 1751–1757 CAS.
- Y. Gao, F. R. Huang, Y. Zhou and L. Du, J. Appl. Polym. Sci., 2013, 128, 340–346 CrossRef CAS PubMed.
- Z. Brunovska, R. Lyon and H. Ishida, Thermochim. Acta, 2000, 357, 195–203 CrossRef.
- H. J. Kim, Z. Brunovska and H. Ishida, Polymer, 1999, 40, 6565–6573 CrossRef CAS.
- H. J. Kim, Z. Brunovska and H. Ishida, J. Appl. Polym. Sci., 1999, 73, 857–862 CrossRef CAS.
- H. J. Kim, Z. Brunovska and H. Ishida, Polymer, 1999, 40, 1815–1822 CrossRef CAS.
- H. Y. Low and H. Ishida, J. Polym. Sci., Part B: Polym. Phys., 1999, 37, 647–659 CrossRef CAS.
- H. A. Katzman, J. J. Mallon and W. T. Barry, J. Adv. Mater., 1995, 26, 21–27 CAS.
- W. C. Tseng, Y. Chen and G. W. Chang, Polym. Degrad. Stab., 2009, 94, 2149–2156 CrossRef CAS PubMed.
- G. H. Zhang, H. Yi, G. T. Zhang, Y. Deng, R. P. Bai, H. Zhang, J. T. Miller, A. J. Kropf, E. E. Bunel and A. W. Lei, J. Am. Chem. Soc., 2014, 136, 924–926 CrossRef CAS PubMed.
- Q. B. Liu and D. J. Burton, Tetrahedron Lett., 1997, 38, 4371–4374 CrossRef CAS.
- W. Y. Yin, C. He, M. Chen, H. Zhang and A. W. Lei, Org. Lett., 2009, 11, 709–712 CrossRef CAS PubMed.
- M. J. Langton, J. D. Matichak, A. L. Thompson and H. L. Anderson, Chem. Sci., 2011, 2, 1897–1901 RSC.
- C. H. Lin, S. L. Chang, C. W. Hsieh and H. H. Lee, Polymer, 2008, 49, 1220–1229 CrossRef CAS PubMed.
- K. D. Demir, B. Kiskan and Y. Yagci, Macromolecules, 2011, 44, 1801–1807 CrossRef.
- S. B. Sastri, T. M. Keller, K. M. Jones and J. P. Armistead, Macromolecules, 1993, 26, 6171–6174 CrossRef CAS.
- M. F. Grenierloustalot and P. Grenier, Abstr. Pap. Am. Chem. S., 1994, 207, 22 Search PubMed –Poly.
- R. F. Kovar, G. F. L. Ehlers and F. E. Arnold, J. Polym. Sci., Polym. Chem. Ed., 1977, 15, 1081–1095 CrossRef CAS PubMed.
- M. C. Wang, M. Yang, T. Zhao and J. Pei, Eur. Polym. J., 2008, 44, 842–848 CrossRef CAS PubMed.
- H. Ishida and D. J. Allen, J. Polym. Sci., Part B: Polym. Phys., 1996, 34, 1019–1030 CrossRef CAS.
- K. Hemvichian and H. Ishida, Polymer, 2002, 43, 4391–4402 CrossRef CAS.
- K. Hemvichian, H. D. Kim and H. Ishida, Polym. Degrad. Stab., 2005, 87, 213–224 CrossRef CAS PubMed.
- K. Hemvichian, A. Laobuthee, S. Chirachanchai and H. Ishida, Polym. Degrad. Stab., 2002, 76, 1–15 CrossRef CAS.
- C. Li, Q. C. Ran, R. Q. Zhu and Y. Gu, RSC Adv., 2015, 5, 22593–22600 RSC.
- H. C. Zhang, W. Gu, R. Q. Zhu, Q. C. Ran and Y. Gu, Polym. Degrad. Stab., 2015, 111, 38–45 CrossRef CAS PubMed.
|
This journal is © The Royal Society of Chemistry 2015 |
Click here to see how this site uses Cookies. View our privacy policy here.