DOI:
10.1039/C5RA12773D
(Paper)
RSC Adv., 2015,
5, 89985-89992
Synthesis of ZnO nanorods on a flexible Phynox alloy substrate: influence of growth temperature on their properties†
Received
1st July 2015
, Accepted 2nd October 2015
First published on 7th October 2015
Abstract
A novel flexible alloy substrate (Phynox, 50 μm thick) was used for the synthesis of zinc oxide (ZnO) nanorods via a low-temperature solution growth method. The growth of ZnO nanorods was observed over a low temperature range of 60–90 °C for a growth duration of 4 hours. The as-synthesized nanorods were characterized using field-emission scanning electron microscopy (FE-SEM), X-ray diffraction (XRD), transmission electron microscopy (TEM), and X-ray photoelectron spectroscopy (XPS) for their morphology, crystallinity, microstructure and composition. The as-grown ZnO nanorods were observed to be relatively vertical to the substrate. However, the morphology of the ZnO nanorods in terms of their length, diameter and aspect ratio was found to vary with the growth temperature. The morphological variation was mainly due to the effects of the various relative growth rates observed at the different growth temperatures. The growth temperature influenced ZnO nanorods were also analyzed for their wetting (either hydrophobic or hydrophilic) properties. After carrying out multiple wetting behaviour analyses, it has been found that the as-synthesized ZnO nanorods are hydrophobic in nature. The ZnO nanorods have potential application possibilities in self-cleaning devices, sensors and actuators as well as energy harvesters such as nanogenerators.
1. Introduction
Zinc oxide (ZnO) is one of the most promising potential materials due to its remarkable properties such as wide band-gap (3.37 eV), large exciton binding energy (60 meV), excellent chemical and thermal stability, transparency and biocompatibility. In view of these properties, ZnO has become more popular and has drawn increased interest in the area of nanotechnology also for its utilization in different fields, such as electronics, optoelectronics, electrochemical and electromechanical.1–4 ZnO is a very flexible functional material, exhibiting a wide range of structural morphologies such as nanocombs,5 nanorings,6 nanohelixes/nanosprings,7 nanobelts,8 nanowires/nanorods,9,10 nanotubes,11 nanocages12 and nanosheets.13 Among these, one-dimensional (1D) ZnO nanorods/nanowires have been extensively studied in the recent past due to their multifunctional device applications in the areas of ultraviolet (UV) lasers,14,15 light emitting diodes,16 field emission devices,17,18 solar cells,19,20 surface acoustic wave devices,21 piezoelectric sensors and actuators22,23 and nanogenerators.23,24 The 1D ZnO nanorods can be synthesized using various methods such as physical vapour deposition (PVD),8 chemical vapour deposition (CVD),25 metal organic chemical vapour deposition (MOCVD),26 molecular beam epitaxy (MBE),27 pulsed laser deposition (PLD),28 hydrothermal synthesis3,24,29 and electrochemical deposition.30 Among all these methods, solution growth-assisted hydrothermal synthesis is most favourable due to its flexibility to carry out the synthesis process on a variety of substrates (both conducting and non-conducting) at low temperatures (<100 °C). Moreover, this process is relatively simple, cost effective, less hazardous and most suitable for the synthesis of uniform ZnO nanorods over larger surface areas.3,13,29
In any synthesis process, the choice of substrate plays an important role in controlling the structure, orientation and density of the nanorods formed, which directly affect their properties as well as their utility in their corresponding applications.31 Therefore, large-scale, low-cost and highly-oriented 1D ZnO nanorods on various conducting flexible substrates is still expected for novel device applications.32 Well-oriented vertically grown ZnO nanorods on metallic substrates are preferable for some device fabrications due to their improved electrical and thermal conduction. In addition, the electrically conductive substrate could act as one of the electrodes and therefore reduce the fabrication complexities.33 Moreover, in some cases the working mechanism and device performance are also affected by the flexibility of the substrate itself. In recent years, most papers have reported the synthesis of piezoelectric ZnO nanorods on various non-flexible substrate materials, such as Si, sapphire and ITO glass, for nanogenerators. However, these non-flexible substrates suffer from the problem of very low electrical output response (piezoelectricity). In addition, few investigations have also been carried out to study piezoelectric ZnO nanostructures grown on polymer flexible substrates such as polyethylene terephthalate (PET), Kapton, polyethylene naphthalate (PEN) and polyester (PS). However, these polymer flexible substrates suffer from the disadvantages that they cannot withstand higher temperatures and the possibility of crack formation in the seed layer films.34 Therefore, a flexible metal alloy substrate that is thermally and electrically conductive, and can easily withstand higher temperatures will be a good alternative for the growth of nanorods as well as for sensor fabrication processes.35 The use of electrically-conductive flexible substrate as one of the electrodes reduces the number of overall device fabrication process steps. During recent years, our group is one of the forefront groups in exploring the abovementioned advantages of flexible conductive substrates. In this regard, we have reported our study on the integration of piezoelectric ZnO thin films on flexible metal alloy substrate for various thin film sensor applications such as impact sensor,36 vibration sensor37 and flow sensor.38 However, considering the wide applicability of 1D ZnO nanostructures, it is important to explore high-quality ZnO nanorods synthesis on various metal alloy substrates for the realization of different piezoelectric devices.
In the present study, we now report the detailed studies performed on the synthesis of ZnO nanorods over a novel substrate namely Phynox alloy. In our study, we have adopted a low temperature solution growth method for the synthesis of ZnO nanorods. In addition to the general characterization of the as-synthesized, wetting behaviour analysis was also performed to confirm whether the ZnO nanorods were hydrophobic or hydrophilic in nature.
2. Experimental
2.1. Selection of the Phynox alloy substrate
In the present study, we have chosen Phynox (Elgiloy, Lamineries, MATTHEY SA) as a substrate, which is a cobalt chromium based alloy (40% Co, 20% Cr, 16% Ni, 7% Mo, (Table S1, ESI†)), flexible and thermally and electrically conductive.39 Herein, the Phynox alloy serves both as the substrate for the synthesis of ZnO nanorods and as the bottom electrode in the device fabrication process. Furthermore, it can easily withstand temperatures from −268.8 °C to 500 °C; it is extremely resistant to corrosion and also biocompatible. Therefore, the selection of the Phynox alloy substrate has several advantages as mentioned before; it reduces the overall complexity of synthesis and device fabrication process in comparison with other non-conducting flexible substrates and also helpful for improving the performance characteristics of the resulting devices.
2.2. Synthesis of ZnO nanorods on a Phynox alloy substrate
The different process steps followed for the synthesis of ZnO nanorods are shown in Fig. 1. Prior to the synthesis of ZnO nanorods, the Phynox alloy substrate was thoroughly cleaned using acetone, isopropyl alcohol and DI (de-ionized) water by ultrasonication for 10 minutes. The cleaned alloy substrate was deposited with a ZnO seed layer (∼100 nm, S1(a), ESI†) via DC reactive-magnetron sputtering. The growth process of nanorods over the seed layer was performed using a simple solution growth-assisted hydrothermal method, similar to the method followed in our previous study.9,13 In this process, an aqueous solution consisting of an equal amount of zinc nitrate hexahydrate (Zn (NO3)2·6H2O) and hexamethylenetetramine (HMTA, C6H12N4) at a concentration of 25 mM was prepared. The ZnO-film-coated substrate was placed over the surface of the solution (∼60 ml) in a screw reagent bottle. Subsequently, the ZnO-coated substrates were maintained at growth temperature of 90 °C for 4 hours duration by keeping the closed bottle inside a hot air oven. To study the temperature influence over the morphology of the ZnO nanorods, the growth temperature was varied from 50 °C to 90 °C separately while maintaining all other process parameters constant. The growth process of the ZnO nanorods involves the chemical reactions mentioned below.40
 |
| Fig. 1 Schematic of the process steps followed for the synthesis of hydrothermally grown ZnO nanorods. | |
Decomposition reaction:
(CH2)6N4 + 6H2O ↔ 4NH3 + 6HCHO |
Hydroxyl supply reaction:
Supersaturation reaction:
ZnO nanorod growth reaction:
After the growth process, the substrates were allowed to cool down to room temperature. Furthermore, the ZnO-coated substrates were taken out and thoroughly cleaned with DI water to remove the organic salts and were allowed to dry at room temperature.3,13,29,40 After this process, the formation of white coloured nano-structured films were observed over the substrates.
2.3. Characterization
The as-synthesized ZnO nanostructures on the Phynox alloy substrate were characterized by the following techniques.
A Bruker D8 Advance diffractometer (Model no. A18-A100/D76182) was used for X-ray diffraction (XRD) studies. Herein, the diffractometer was adjusted in reflective mode powered at 40 kV and 30 mA at room temperature. The Cu Kα radiation (λ = 1.5406 Å), with a nickel filter at a scan rate of 2° min−1 in the range of 10–90°, was used to examine the crystalline phase of the films.
Microscopy images were acquired using a field-emission scanning electron microscopy (FE-SEM) instrument (Carl Zeiss, Ultra 55) equipped with SE2 and InLense detectors. Herein, the accelerating voltage was maintained between 5 and 10 kV. Energy dispersive X-ray spectroscopy (EDXS) measurements were carried out using the same instrument equipped with an Oxford INCA x-sight X-ray detector. The EDXS data were acquired at an accelerating voltage of 15 kV.
Transmission electron microscopy (TEM) and high resolution (HR-TEM) analyses were also carried out using a TEM, F30, Tecnai 30 D264 S-Twin microscope operated at 300 kV with 0.14 nm point resolution. The TEM-sample was prepared by scraping the nanorods from the Phynox alloy substrate and dispersing them in acetone solution. The solution of dispersed nanorods was subjected to ultrasonication for 10 min. Finally, the solution was drop-cast onto a carbon coated copper grid and dried.
X-ray photoelectron spectroscopy (XPS, Kratos Axis Ultra DLD system) was performed using an Al Kα radiation dual anode source (energy, hν = 1486.6 eV) with an X-ray power of 150 W in an ultra-high vacuum environment (base pressure of 3 × 10−9 Torr). All XPS peaks were calibrated with respect to carbon (C 1s) at 284.8 eV. XPS spectra were obtained at constant pass energy of 160 eV for the survey scans and 20 eV for the high-resolution scans. Data fitting and quantification analysis were carried out using the CASA XPS software after considering the relative sensitivity factors (RSF) for each element in the compound. Gaussian–Lorentzian functions and a Shirley-type background were employed during the analysis.
2.4. Wetting behaviour analysis
Wetting behaviour (hydrophobic/hydrophilic) analysis was studied using water contact-angle (WCA) measurements. The WCA measurements were performed over the as-synthesized ZnO nanorods on an Phynox alloy substrate using an optical contact angle measuring instrument (Data Physics, Model # OCA 30/6), using the sessile drop method. A 2 μL droplet of DI water was positioned on the surface via a micro syringe and images were captured to measure the contact-angle formed at the interface of the liquid to the solid surface. The contact angle was calculated via fitting the experimental data using the SCA 20 software.
3. Results and discussion
The surface morphologies of the as-grown ZnO nanostructures on the flexible Phynox alloy substrate at different growth temperatures in the range of 60–90 °C are shown in Fig. 2(a)–(d), respectively. As can be observed in the FE-SEM images, the ZnO nanorods are present all over the substrate and are uniformly distributed. The cross-sectional view of the ZnO nanorods is shown in the insets of Fig. 2(a)–(d). The FE-SEM images and measured average tilt angles (Table S2, ESI†) of the nanorods with respect to the substrate confirms that the orientation of the ZnO nanorods were relatively vertical to the substrate. Table S3 (ESI†) shows the average length and diameter of the as-grown ZnO nanorods for the growth temperature of 60 °C, 70 °C, 80 °C and 90 °C, respectively. It can be observed that the length and diameter of the ZnO nanorods increased with an increase in the growth temperature (Fig. 3(a) and (b)). Therefore, it is clearly evident that the growth temperature has a pronounced effect on the morphology in terms of the length as well as the diameter of the nanorods. It means that the aspect ratio of the nanorods also increases with an increase in the growth temperature (Fig. 3(c)). A similar study has been reported by Willander et al., wherein the effect of the growth temperature on the aspect ratio and morphology of nanorods on a Si substrate were studied.41 Furthermore, Wang et al., have attempted a similar type of study (the growth temperature effect on the aspect ratio of ZnO nanorods) on an Au coated Si substrate on the basis of crystal nucleation and growth theory. It was found that the diffusion length and mobility of ions critically depend upon the growth temperature.42 Considering the same theory for the present study, at higher temperature (90 °C), the mobility and diffusion length of the ions (Zn2+ and OH−) are large enough in the precursor solution to reach the sites of the nuclei for the subsequent growth of nanorods. Thus, these precursor ions exhibit a higher affinity towards the already-formed seeds. Moreover, at 90 °C, HMTA decomposes promptly to provide a sufficient number of hydroxide ions (OH−) resulting in higher vertical growth rate. The above discussed phenomenon is considered to be the main reason behind the higher aspect ratio (i.e., 12.265) of the nanorods grown at 90 °C. Similarly, at a lower temperature (60 °C), due to the lower decomposition rate of HMTA, the mobility and the diffusion length of the Zn2+ and OH− ions on the substrate are rather limited, which prohibits ion diffusion and consequently lowers the aspect ratio (i.e., 1.97). Considering that the process uses an aqueous solution based hydrothermal method, the growth temperature studies were performed below 100 °C.41 Furthermore, to observe the lower limit of the growth temperature, the nanorods growth study was performed at 50 °C. Interestingly, the nanorods growth was not noticed on the substrate at a growth temperature of 50 °C. This can be due to the insufficient thermal energy available at 50 °C and the incomplete decomposition of HMTA ultimately affecting the concentration of hydroxide ions, which affects improper ZnO nucleation as well as nanorod growth. Therefore, it was concluded that the nanorods growth starts above the temperature of 50 °C (S2(a and b), ESI†).
 |
| Fig. 2 FE-SEM images for the as-grown ZnO nanorods at different growth temperatures of (a) 60 °C, (b) 70 °C, (c) 80 °C, and (d) 90 °C (note: the inset figures show the corresponding cross-sectional images). | |
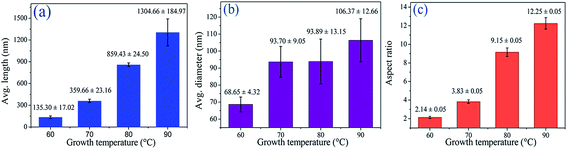 |
| Fig. 3 (a) Growth temperature vs. avg. length, (b) growth temperature vs. avg. diameter and (c) growth temperature vs. aspect ratio of the ZnO nanorods. | |
Furthermore, energy dispersive X-ray spectroscopy (EDXS) analysis was also performed on the surface of the ZnO nanorods grown at 90 °C (Fig. 4(a) and (b)), primarily to confirm the presence of Zn and O atoms, and to also confirm if any foreign impurities are present. The presence of Cr and Co elements is because of the substrate Phynox, which is basically an alloy composed of Cr–Co. It may be noted that Au (∼10 nm) was sputtered on the synthesized ZnO nanorod films to avoid charging during the SEM imaging (Fig. 4(b)).
 |
| Fig. 4 (a) A lower magnification FE-SEM image of the as-grown ZnO nanorods (growth temperature of 90 °C) and (b) the EDXS spectrum corresponding to the scanned area. | |
The X-ray diffraction patterns recorded of the ZnO nanorods grown at different growth temperatures (60–90 °C) are shown in Fig. 5(a)–(d). The highest intensity diffraction peak at 2θ = 34.3° is the corresponding plane (002) of ZnO nanorods and was observed at a growth temperature of 90 °C, as shown in Fig. 5(d) (JCPDS # 36-1451). In all the cases, a highly intense diffraction peak was observed at 34.3° (002), which indicates that the ZnO nanorods are strongly oriented along the (002) plane.29,40,41 Furthermore, the sharp and narrow diffraction peaks indicate that the ZnO nanorods have good crystallinity. The full width at half maxima (FWHM) and d-spacing values of the as-grown ZnO nanorods (grown at 90 °C) were found to be 0.126° and 0.261 nm, respectively. The other peaks appearing at 2θ values of 43.5° and 74.6° are the major substrate elements (bare Phynox alloy) (S4, ESI†). These substrate peaks are marked with an “*” and show the Phynox alloy substrate. Moreover, the observed nanorods grown at a growth temperature of 60 °C (Fig. 5(a)) showed a poor crystalline nature when compared to those grown at 90 °C. It was observed that the highly intense peak at 34.3° (002) was gradually increased when the growth temperature was increased from 60 to 90 °C. However, all the samples showed a similar type of XRD pattern except in the intensity variations. The FWHM values for the ZnO nanorods grown at different growth temperatures (60–90 °C) were also relatively reduced as the growth temperature increased (S4, ESI†). Likewise, the XRD pattern was recorded for the growth temperature of 50 °C (S2(c), ESI†). Considering the negligible nanorod growth at 50 °C, the observed intensity peak at 2θ = 34.3° was believed to be due to the ZnO seed layer film.
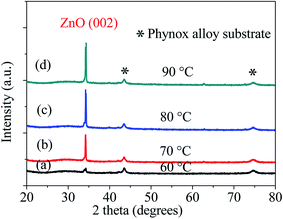 |
| Fig. 5 XRD pattern of the ZnO nanorods on Phynox alloy substrate at different growth temperatures of (a) 60 °C, (b) 70 °C, (c) 80 °C and (d) 90 °C. | |
Apart from the abovementioned analyses, structural characterization and composition analysis of a single ZnO nanorod were also carried out using TEM. Low and high magnification bright field images of the nanorods are shown in Fig. 6(a) and (b), respectively. These nanorods confirm the 1D nature of the ZnO nanorods. The captured single nanorod diameter was about 95 nm (Fig. 6(b)). The dimensions of the nanorods under TEM observation are in good agreement with the FE-SEM results. The HR-TEM (High Resolution-TEM) image of single ZnO nanorod is shown in Fig. 6(c) and it indicates that the growth direction was along the (001) facet.43,44 The measured d-spacing value obtained from the HR-TEM image and its FFT image (local diffraction, inset Fig. 6(c)) was found to be 0.268 nm, which corresponds to the inter-planar spacing of the (002) plane in ZnO.45 There were no noticeable crystalline defects in the ZnO nanorod found in the HR-TEM image, which indicates a good quality crystalline structure. Fig. 6(d) shows the selected area electron diffraction (SAED) pattern recorded on the same ZnO nanorod carried out under the [−120] zone axis. Sharp and clear diffraction spots were observed, which indicate the fact that the ZnO nanorods have a good single-crystalline structure grown along the c-axis direction. The reflections correspond to the (002), (−210) and (−212) lattice planes of ZnO with an hexagonal structure indexed.44,45 The EDXS measurement recorded on the single ZnO nanorod is shown in Fig. 6(e), wherein the presence of Zn, O, Cu and C are clearly evident. The presence of Cu and C is due to the carbon-coated TEM grid used for TEM analysis.
 |
| Fig. 6 TEM analysis of the ZnO nanorods with a growth temperature of 90 °C: (a) low magnification image, (b) higher magnification of a single nanorod, (c) HR-TEM image (the inset shows the corresponding FFT image), (d) SAED pattern, and (e) the corresponding EDS pattern. | |
Furthermore, surface analysis, chemical composition and oxidation state of the as-grown ZnO nanorods were measured using XPS. Zn, O and C peaks were detected as shown in the survey spectra of Fig. 7(a), indicating that no elements were found other than C. The detected C was related to carbon adsorbed on the surface during the exposure of the sample to the ambient atmosphere. All peaks were calibrated with respect to carbon (C 1s) at 284.8 eV.13,46 Fig. 7(b) shows the high resolution XPS spectra of the Zn 2p region. The Zn 2p core-level of the ZnO nanorods has two fitting peaks located at about 1020.80 eV and 1043.84 eV attributed to Zn 2p3/2 and Zn 2p1/2, respectively. These results indicate that the chemical valence (oxidation state) of Zn at the surface morphology of ZnO was +2. The binding energy difference between Zn 2p1/2 and Zn 2p3/2 was 23 eV for morphology of ZnO. These values are in good agreement with the ZnO nanorods previously reported.46,47 In addition, the measured Auger parameter of Zn value (2009.61 eV) was in close agreement with the ZnO nanostructures previously reported, which confirms the formation of ZnO.13,48 Fig. 7(c) displays the XPS spectra of O 1s region of ZnO nanorods. It is demonstrated that the O 1s core-level spectrum of the ZnO nanorods involves two different forms of oxygen. Two fitting Gaussians peaks marked as (1) and (2) were used to fit the experimental data. Peak (1), positioned at the lower binding energy of 530.69 eV, was assigned to O2− ions in the Zn–O bonding of the wurtzite structure of ZnO. The other peak (2) was located at 532.2 eV and related to the OH− groups absorbed onto the surface of the ZnO nanorods. These values are in good agreement with the reported study of ZnO nanorods.46,47 The detailed quantification data of ZnO nanorods are provided in the ESI† (Table S4). In this, the binding energy (BE) for the core levels of Zn 2p and O 1s, corresponding FWHM values and their respective atomic concentrations, are listed.
 |
| Fig. 7 (a) XPS survey spectra, (b) Zn 2p peak and (c) O 1s peak. | |
4. Application: contact angle measurements for the surface analysis of the ZnO nanorods
The surface wettability (hydrophobicity or hydrophilicity) nature of the synthesized ZnO nanorods was determined by carrying out water contact angle (WCA) measurements. If the solid surface of the nanorods has a contact angle with liquid droplet (DI water) that is greater than 90°, then the surface is classed as hydrophobic and if the contact angle is less than 90°, the surface is hydrophilic in nature.49,50 Fig. 8(a)–(d) shows the variation of the WCA measurements with growth temperature (60–90 °C) for the as-grown ZnO nanorods. The ZnO nanorods with different growth temperatures show WCA values of 117.90° ± 2.42°, 137.96° ± 1.79°, 137.00° ± 1.95° and 139.53° ± 2.36° (Table S5, ESI†). All the measurements were carried out under the same conditions. As can be observed in the images (Fig. 8(a)–(d)), for all the samples the observed WCA was greater than 90°. Therefore, we can conclude that the synthesized ZnO nanorods are hydrophobic in nature. The measured WCA of the nanorods grown at 50 °C was 103.56° ± 1.92°, which was mainly from the ZnO seed layer and not from nanorods (S2(d), ESI†). The increase in growth temperature resulted in different WCA values for the ZnO nanorods (Fig. 9). Hsieh et al., reported that the variation of WCA was mainly because of the height variation of the ZnO nanorods, which indirectly reveals the fact that the aspect ratio of ZnO nanorods plays an important role for the variation of WCA. Therefore, it is possible that the morphology of ZnO nanorods and their aspect ratio are responsible for preventing the penetration of water droplets due to a large amount of air trapped in the interspaces between each nanorod on a nano-scale level.51 Wang et al. reported the variation of WCA with respect to the aspect ratio, growth time and growth temperature.52 In the study reported by Gong et al., the variations of WCA were based on changes in the surface roughness of the nanowires.53 From the abovementioned references, it can be deduced that the morphology and surface roughness variation affect the WCA. In the present study, the observed change in the aspect ratio, i.e. variation of height/diameter ratio was due to dissimilar rates of increases in the height and diameter (Table S2, ESI†). There is a significant change in the WCA from 50 to 70 °C due to the aspect ratio as well as the increased air trappings, which tends to saturated at higher temperatures (≥70 °C) due to higher influence of the surface roughness in the nanorod forest. The WCAs are closely identical for the samples above 70 °C. It was believed that the minor variation in the WCA was due to the small variation in surface roughness of the nanorods. The change in the surface roughness can be clearly observed in the top view of the SEM images (Fig. 2). For samples grown at ≤70 °C, the factor playing an important role in determining the WCA is the air trapped between these nanorods, which will be decided primarily by the height of the nanorods (the Cassie–Baxter model) and also up to a certain extent by the aspect ratio. This is because the aspect ratio will also be affected by the surface roughness of the nanorod forest along with the air trapped between them. The change in the surface roughness can change the WCA irrespective of their aspect ratio/height of the nanorods. Finally, we conclude that the WCA variation with an increase in growth temperature not only depends upon the height/aspect ratio but also on the morphology (surface roughness) of the ZnO nanorods.
 |
| Fig. 8 Water contact angle (WCA) measurements over the surface of the ZnO nanorods with a growth temperature of (a) 60 °C, (b) 70 °C, (c) 80 °C, and (d) 90 °C. | |
 |
| Fig. 9 WCA measurements with respect to growth temperature. | |
5. Conclusions
Highly-oriented ZnO nanorods were successfully synthesized on a novel flexible Phynox alloy substrate by altering the growth temperature parameter in a low-temperature solution growth method. The growth temperature was varied from 50 to 90 °C in steps of 10 °C. This novel Phynox substrate, which is electrically conductive, can easily withstand a wide temperature range (−268.8 to 500 °C), is extremely resistant to corrosion and biocompatible, and paves the way for not only an easy fabrication process by avoiding one of the electrode deposition steps but also improves the reliability as well as the self-life of the fabricated device. Considering these advantages, Phynox may be useful for a variety of material synthesis processes as well as flexible electronics. Due to its biocompatibility, the alloy substrate can be used in biomedical applications especially in pacemakers (an implantable medical device) as one of the electrodes. Phynox material in its different forms is used as springs, seal components and components for watches. Furthermore, several industries, such as aerospace, telecommunication, petrochemical, marine engineering and process control plants, also employ Phynox alloy strips as membranes for pressure sensors and in some cases in relays and switches. The study of the temperature dependent synthesis of ZnO nanorods has brought an insight in term of the variation in the aspect ratio and subsequently brought an idea of their wettability property (hydrophobicity). Integration of the as-synthesized ZnO nanorods grown on flexible Phynox alloy substrate can offer various device application possibilities namely self-cleaning devices, sensors (impact, flow, pressure and acoustic) as well as micro-actuators and energy harvesting devices such as nanogenerators.
Acknowledgements
The authors are grateful to the SERB, DST, Govt. of India for kindly supporting the study reported in this paper, in the form of this project (Project No. # SB/EMEQ-320/2013). The authors are also thankful to the Advanced Facility for Microscopy and Microanalysis (AFMM), IISc, for providing the microscopy facility. The authors would also like to thank the Centre for Nano Science and Engineering (CeNSE) for providing the FE-SEM and XPS facility, IISc. Thanks to the IPC department for providing the XRD facility, IISc. The authors gratefully acknowledge Prof. Satish Vasu Kailas (Dept. of Mechanical Engg), IISc, for allowing the use of the water contact angle measurement facility.
References
- Z. L. Wang, J. Phys.: Condens. Matter, 2004, 6(25), R829–R858 CrossRef.
- B. Kumar and S. W. Kim, Nano Energy, 2012, 1(3), 342–355 CrossRef CAS PubMed.
- S. Xu and Z. L. Wang, Nano Res., 2011, 4(11), 1013–1098 CrossRef CAS.
- Z. L. Wang, Appl. Phys. A: Mater. Sci. Process., 2007, 88(1), 7–15 CrossRef CAS.
- C. S. Lao, P. X. Gao, R. S. Yang, Y. Zhang, Y. Dai and Z. L. Wang, Chem. Phys. Lett., 2006, 417(4), 358–362 CrossRef CAS PubMed.
- F. Li, Y. Ding, P. Gao, X. Xin and Z. L. Wang, Angew. Chem., Int. Ed., 2004, 43(39), 5238–5242 CrossRef CAS PubMed.
- R. Yang, Y. Ding and Z. L. Wang, Nano Lett., 2004, 4(7), 1309–1312 CrossRef CAS.
- Z. W. Pan, Z. R. Dai and Z. L. Wang, Science, 2001, 291(5510), 1947–1949 CrossRef CAS PubMed.
- V. Gaddam, S. Joshi, M. Parmar, M. M. Nayak and K. Rajanna, Proc. IEEE Sens., 2012, 1870–1873 Search PubMed.
- P. X. Gao, Y. Ding and Z. L. Wang, Nano Lett., 2003, 3(9), 1315–1320 CrossRef CAS.
- G. W. She, X. H. Zhang, W. S. Shi, X. Fan, J. C. Chang, C. S. Lee, S. T. Lee and C. H. Liu, Appl. Phys. Lett., 2008, 92(5), 3111 CrossRef PubMed.
- X. L. Yu, H. M. Ji, H. L. Wang, J. Sun and X. W. Du, Nanoscale Res. Lett., 2010, 5(3), 644–648 CrossRef CAS PubMed.
- V. Gaddam, R. R. Kumar, M. Parmar, G. R. K. Yaddanapudi, M. M. Nayak and K. Rajanna, RSC Adv., 2015, 5, 13519 RSC.
- M. H. Huang, S. Mao, H. Feick, H. Yan, Y. Wu, H. Kind, E. Weber, R. Russo and P. Yang, Science, 2001, 292(5523), 1897–1899 CrossRef CAS PubMed.
- K. Govender, D. S. Boyle, P. O'Brien, D. Binks, D. West and D. Coleman, Adv. Mater., 2002, 14(17), 1221–1224 CrossRef CAS.
- W. I. Park and G. C. Yi, Adv. Mater., 2004, 16(1), 87–90 CrossRef CAS PubMed.
- Y. W. Zhu, H. Z. Zhang, X. C. Sun, S. Q. Feng, J. Xu, Q. Zhao, R. M. Wang and D. P. Yu, Appl. Phys. Lett., 2003, 83(1), 144–146 CrossRef CAS PubMed.
- W. Z. Wang, B. Q. Zeng, J. Yang, B. Poudel, J. Y. Huang, M. J. Naughton and Z. F. Ren, Adv. Mater., 2006, 18(24), 3275–3278 CrossRef CAS PubMed.
- M. Law, L. E. Greene, J. C. Johnson, R. Saykally and P. Yang, Nat. Mater., 2005, 4(6), 455–459 CrossRef CAS PubMed.
- Y. Wei, C. Xu, S. Xu, C. Li, W. Wu and Z. L. Wang, Nano Lett., 2010, 10(6), 2092–2096 CrossRef CAS PubMed.
- C. R. Gorla, N. W. Emanetoglu, S. Liang, W. E. Mayo, Y. Lu, M. Wraback and H. Shen, J. Appl. Phys., 1999, 85(5), 2595–2602 CrossRef CAS PubMed.
- X. Wang, J. Zhou, J. Song, J. Liu, N. Xu and Z. L. Wang, Nano Lett., 2006, 6(12), 2768–2772 CrossRef CAS PubMed.
- B. A. Buchine, W. L. Hughes, F. L. Degertekin and Z. L. Wang, Nano Lett., 2006, 6(6), 1155–1159 CrossRef CAS PubMed.
- S. Xu, Y. Qin, C. Xu, Y. Wei, R. Yang and Z. L. Wang, Nat. Nanotechnol., 2010, 5(5), 366–373 CrossRef CAS PubMed.
- J. J. Wu and S. C. Liu, Adv. Mater., 2002, 14(3), 215 CrossRef CAS.
- W. I. Park, D. H. Kim, S. W. Jung and G. C. Yi, Appl. Phys. Lett., 2002, 80(22), 4232–4234 CrossRef CAS PubMed.
- Y. W. Heo, V. Varadarajan, M. Kaufman, K. Kim, D. P. Norton, F. Ren and P. H. Fleming, Appl. Phys. Lett., 2002, 81(16), 3046–3048 CrossRef CAS PubMed.
- Y. Sun, G. M. Fuge and M. N. Ashfold, Chem. Phys. Lett., 2004, 396(1), 21–26 CrossRef CAS PubMed.
- L. Vayssieres, Adv. Mater., 2003, 15(5), 464–466 CrossRef CAS PubMed.
- Z. Yin, S. Wu, X. Zhou, X. Huang, Q. Zhang, F. Boey and H. Zhang, Small, 2010, 6(2), 307–312 CrossRef CAS PubMed.
- J. Nayak, S. N. Sahu, J. Kasuya and S. Nozaki, J. Phys. D: Appl. Phys., 2008, 41(11), 115303 CrossRef.
- J. Liu, X. Huang, Y. Li, X. Ji, Z. Li, X. He and F. Sun, J. Phys. Chem. C, 2007, 111(13), 4990–4997 CAS.
- T. Ngo-Duc, K. Singh, M. Meyyappan and M. M. Oye, Nanotechnology, 2012, 23(19), 194015 CrossRef PubMed.
- C. L. Hsu and K. C. Chen, J. Phys. Chem. C, 2012, 116(16), 9351–9355 CAS.
- S. Joshi, M. M. Nayak and K. Rajanna, Proc. IEEE Sens., 2012, pp. 1866–1869 Search PubMed.
- S. Joshi, G. M. Hegde, M. M. Nayak and K. Rajanna, Sens. Actuators, A, 2013, 199, 272–282 CrossRef CAS PubMed.
- S. Joshi, M. M. Nayak and K. Rajanna, Appl. Surf. Sci., 2014, 296, 169–176 CrossRef CAS PubMed.
- S. Joshi, M. Parmar and K. Rajanna, Sens. Actuators, A, 2012, 187, 194–200 CrossRef CAS PubMed.
- http://www.matthey.ch/fileadmin/user_upload/downloads/fichetechnique/EN/Phynox_C.pdf.
- Y. Zhang, M. K. Ram, E. K. Stefanakos and D. Y. Goswami, J. Nanomater., 2012, 2012, 1–22 Search PubMed.
- G. Amin, M. H. Asif, A. Zainelabdin, S. Zaman, O. Nur and M. Willander, J. Nanomater., 2011, 2011, 1–8 CrossRef PubMed.
- S. Xu, C. Lao, B. Weintraub and Z. L. Wang, J. Mater. Res., 2008, 23(8), 2072–2077 CrossRef CAS.
- H. Li, C. Liang, K. Zhong, M. Liu, G. A. Hope, Y. Tong and P. Liu, Nanoscale Res. Lett., 2009, 4(10), 1183–1190 CrossRef CAS PubMed.
- H. K. Park, S. P. Hong and Y. R. Do, J. Electrochem. Soc., 2012, 159(6), D355–D361 CrossRef CAS PubMed.
- F. Ahmed, S. Kumar, N. Arshi, M. S. Anwar and B. H. Koo, CrystEngComm, 2012, 14, 4016–4026 RSC.
- R. Al-Gaashani, S. Radiman, A. R. Daud, N. Tabet and Y. Al-Douri, Ceram. Int., 2013, 39(3), 2283–2292 CrossRef CAS PubMed.
- V. P. Dinesh, P. Biji, A. Ashok, S. K. Dhara, M. Kamruddin, A. K. Tyagi and B. Raj, RSC Adv., 2014, 4, 58930 RSC.
- S. Bera, S. Dhara, S. Velmurugan and A. K. Tyagi, Int. J. Spectrosc., 2011, 2012, 1–4 Search PubMed.
- J. Lv, J. Zhub, K. Huangd, F. Menga, X. Songa and Z. Sun, Appl. Surf. Sci., 2011, 257(17), 7534–7538 CrossRef CAS PubMed.
- P. R. Elliott, S. P. Stagon, H. Huang, D. U. Furrer, S. F. Burlatsky and T. P. Filburn, Sci. Rep., 2015, 5, 9260 CrossRef CAS PubMed.
- C. T. Hsieh, S. Y. Yang and J. Y. Lin, Thin Solid Films, 2010, 518(17), 4884–4889 CrossRef CAS PubMed.
- G. He and K. Wang, Appl. Surf. Sci., 2011, 257(15), 6590–6594 CrossRef CAS PubMed.
- M. G. Gong, Y. Z. Long, X. L. Xu, H. D. Zhang and B. Sun, Synthesis, Superhydrophobicity, Enhanced Photoluminescence and Gas Sensing Properties of ZnO Nanowires, TECH Open Access Publisher, 2012, ch. 5, pp. 77–100 Search PubMed.
Footnote |
† Electronic supplementary information (ESI) available. See DOI: 10.1039/c5ra12773d |
|
This journal is © The Royal Society of Chemistry 2015 |
Click here to see how this site uses Cookies. View our privacy policy here.