DOI:
10.1039/C5RA08303F
(Paper)
RSC Adv., 2015,
5, 67299-67307
Facilitated transport of CO2 through novel imidazole-containing chitosan derivative/PES membranes
Received
5th May 2015
, Accepted 24th July 2015
First published on 24th July 2015
Abstract
In the present study, a new imidazole alkyl derivative of chitosan (Im-CS) is synthesized and characterized by FT-IR and 1H-NMR spectroscopy. This derivative was blended in various ratios with polyethersulfone (PES) to fabricate newly integrally skinned PES membranes. Scanning Electron Microscopy (SEM) was used to study the changes in the membrane morphologies. The prepared membranes were used for the separation of CO2 from CH4. Our findings indicated that by adding a small amount of Im-CS, membrane performance was improved significantly. In addition, the effect of feed pressure and feed temperature on the performance of the prepared membranes was investigated in this study.
1. Introduction
Natural gas sweetening is a well-known process for the separation of acidic gases like CO2 and H2S from methane and ethane, the main components of the natural gas. This process prevents the corrosion of pipelines and equipment and enhances the heat value of transported natural gas. To date, several techniques have been reported for the separation of CO2 from the gas mixture. Separation by solvent/sorbent, cryogenic distillation and membranes are three basic methods that have been used for gas separation. The solvent/sorbent process and cryogenic distillation have some drawbacks including high energy and chemical consumption and environmental pollution.1 Membrane processes in comparison with other methods have some advantages such as less energy consumption, lower capital cost and ease of operation.2–4
Various types of membranes including inorganic, metal and polymeric ones are used for gas separation. Mechanical and thermal stability, cheapness and appropriate chemical strength make PES a viable polymer for the preparation of integrally skinned asymmetric membranes that provide high gas permeation because of their thin skin layer.5–13
Many researchers have used amine-containing polymers for facilitated transport of CO2 using thin film composite (TFC) membranes. In their research, the effects of the concentration of the amine containing polymer, feed pressure, feed temperature and relative humidity were investigated.14–19
Generally, high selectivity and permeability can be achieved using facilitated transport membranes (FTMs). The presence of some CO2 carriers in the FTMs is the reason for their high CO2/CH4 selectivity. An amine functional group is a good carrier for CO2 and can transport this via the following reversible reactions. CH4 cannot contribute in these reactions, so the final result is the enhancement of CO2 flux across the membrane.11
CO2 + 2RNH2 ↔ RNHCOO− + RNH3+ |
CO2 + 2R2NH ↔ R2NCOO− + R2NH2+ |
R3N + H2O + CO2 ↔ R3NH+ + HCO3− |
There are many reports about using amino-containing polymers as fixed site carriers in facilitated transport membranes. Shen et al. prepared composite membranes consisting of poly(2-N,N-dimethyl aminoethyl methacrylate-co-acrylic acid sodium) as a selective layer and a polysulfone (PS) ultrafiltration membrane as a porous non-selective support. By measuring the real and ideal CO2/CH4 selectivity of the prepared membranes, it was shown that the real selectivity was not as good as the ideal selectivity.16 Hägg et al. used high molecular weight polyvinyl amine (PVAm) casted on polysulfone (PSf) supports for CO2/N2 separation. Selectivity up to 197 was obtained by using these membranes.20 Poly(N-vinyl-sodium aminobutyrate-co-sodiumacrylate) (VSA-SA)/polysulfone (PS) composite membranes were used by Wang et al. for CO2/CH4 separation. They found that the ideal selectivity is 10 times higher than real selectivity.21 Deng et al. prepared some composite membranes consisting of a polyvinyl amine (PVAm)/PVA blend as a separation layer and porous polysulfone (PSF) as a support for separation of the CO2/CH4 mixture. They investigated the effect of feed pressure and relative humidity. They documented a CO2/N2 separation factor of up to 174 and a CO2 permeance of up to 0.58 m3 (STP) (m−2 h−1 bar−1).22 Cai et al. prepared a polyallylamine (PAAm)/PVA blend coated on a PSF ultrafiltration membrane. The real and ideal performances of the synthesized composite membrane for the separation of CO2 from CH4 and N2 were investigated. They found that the membrane performance was improved with an increase in PAAm content followed by separation under optimum conditions.23
Investigation of the CO2/N2 permeation of PVA/poly(ethyleneimine) (PEI)/poly(ethyleneglycol) (PEG) blend membranes at various blend compositions by Hamouda et al. showed that only CO2 is transported by the facilitated transport mechanism.24
It has been confirmed that the presence of water increases the CO2 permeability in the facilitated transport mechanism. Therefore, hydrophilic polymers such as PVA and PEG have been widely used as suitable and compatible materials for holding the amino containing polymer in membrane fabrication.14,15,22–25
Chitosan is a linear polyamine polysaccharide produced by the deacetylation of chitin. The presence of an NH2 group in the chitosan backbone makes it soluble in some organic acid diluents, so membranes can be made by the casting of these solutions.26 However, low solubility is the main drawback of chitosan, therefore, numerous chemical modifications have been introduced into the chitosan backbone to make it soluble in water or organic solvent systems.27–30
Nevertheless, in the gas membrane separation field, the application of chitosan is limited and fairly few articles have been published in this field. Ito et al. used water-swollen chitosan for CO2/N2 separation. They achieved a CO2 permeability of 2.5 × 10−8 cm3 (STP) cm S−1 cm−2 cmHg−1 and a CO2/N2 selectivity of 70.31 Feng et al. used trimesoyl chloride crosslinked chitosan membranes for CO2/N2 separation. They observed that the membranes with higher degrees of crosslinking undergo more swelling.32 Through using a series of chitosan/Pebax blend membranes for CO2/CH4 and CO2/N2 separation, Jiang et al. found that the membranes show high CO2 permeability and high stability. They observed that the highest CO2 permeability was achieved when the chitosan to Pebax mass ratio was 1
:
1. They related the high CO2 permeability of these membranes to the incorporation of Pebax.33 El-Azzami et al. prepared swollen chitosan membranes for CO2 separation from hydrogen and nitrogen. They used the prepared membranes at elevated temperatures of up to 150 °C and a low feed pressure of 5 atm.34 They also used arginine salt–chitosan membranes for the separation of CO2 from H2/N2, and found that the presence of arginine salts in swollen chitosan membranes enhances the CO2 permeability because the arginine salts increase the number of amino groups as well as the water levels in the membranes.35 Shen et al. developed miscible carboxymethyl chitosan/polyethyleneimine blend membranes for CO2/N2 separation. It was observed that water vapor enhances the membrane performance.36 As far as we know, in this field, no chemically modified chitosan except carboxymethyl chitosan has been used for CO2 separation. So in the current study, we tried to synthesize a new organic soluble derivative of chitosan and use it as a fixed carrier for the facilitated transport of CO2 to produce newly integrally skinned asymmetric membranes based on PES. Herein, the effect of Im-CS concentration on the morphology and the separation performance of the fabricated membranes were investigated. Furthermore, the effects of feed temperature and feed pressure on the permeance and selectivity of the produced membrane were studied.
2. Experimental
2.1. Materials
Polyethersulfone (PES Ultrason E6020P with MW = 58
000 g mol−1) was obtained from BASF (Germany) and poly(vinyl alcohol) (PVA) was purchased from Kuraray. Chitosan (medium molecular weight), phenyl chloroformate, N-(3-aminopropyl)-imidazole, phthalic anhydride, and pyridine were obtained from Sigma-Aldrich. All other solvents and chemicals were reagent grade and used without further purification.
2.2. Instrumental analysis
1H-NMR spectra were measured by a Bruker 400 MHz NMR spectrometer in DMSO-d6 at ambient temperature. FTIR spectra of samples were taken in KBr pellets using an ABB Bomem MB-100FTIR spectrophotometer. Elemental analysis was used to establish the DS-values of the chitosan derivative. A KYKY-EM3200 Scanning Electron Microscope (SEM) was used for investigating the cross-sections of the membranes.
2.3. Synthesis of N-phthaloylchitosan (phth-CS)
N-Phthaloylchitosan was prepared according to the procedure reported by Kurita.37 A 500 mL round-bottom flask was charged with chitosan (5 g, 30.8 mmol of glycosidic units), N,N-dimethylformamide (200 mL) and water (10 mL). Then, the reaction flask was heated to 120 °C and 13.83 g phthalic anhydride was added. After that, the mixture was stirred for 8 hours at 120 °C. Afterwards, the reaction mixture was cooled to room temperature and poured into 2 L of ice water with stirring, and the precipitate was washed repeatedly with deionized water. The resulting product was then washed with methanol several times and dried at room temperature to give 7.3 g of a light orange solid. The degree of substitution (DS) was 1.0.
2.4. Synthesis of phenylcarbonated-N-phthaloylchitosan (carbonate-Phth-CS)
A 250 mL flask was charged with 150 mL of N,N-dimethylacetamide and 6 g of N-phthaloyl chitosan and the mixture was stirred at 80 °C overnight to swell completely. Then, 8 g lithium chloride was added and the reaction mixture was cooled slowly to room temperature to obtain a brown viscous solution. Then, 10 mL pyridine (126.6 mmol) was added and the reaction flask was cooled in a salt–ice bath (−5 to 0 °C). After that, 4 mL phenyl chloroformate (31.70 mmol) was added dropwise to this solution with stirring. The reaction mixture was stirred at 0 °C for 2 hours. Then, the ice bath was removed and the mixture was stirred for an additional 22 hours at room temperature. Finally, the mixture was poured into a large amount of ice-water with stirring, and the yellow precipitate was washed repeatedly with deionized water. The resulting product was then washed with methanol several times and dried at room temperature to give 7.9 g of a light yellow solid. The degree of carbonate substitution (DS) was 0.85.
2.5. Synthesis of the imidazole containing derivative of chitosan (Im-CS)
50 mL DMF and 5 g phenylcarbonated-N-phthaloylchitosan were added to a 100 mL flask and the mixture was stirred at room temperature until a solution was obtained. To this 10 mL (83.8 mmol) of N-(3-aminopropyl)-imidazole was added and the solution was stirred for 24 hours at room temperature. The resultant solution was precipitated in THF. The precipitate was filtered and washed repeatedly with THF and then with diethyl ether, and dried at room temperature to give 2.40 g of a yellow powder.
2.6. Membrane preparation
The various amounts of Im-CS were dissolved in NMP. Then, PES was added until the total polymer concentration reached 29.5 wt%. The compositions of the solutions of PES
:
Im-CS were 29.5
:
0, 29
:
0.5, 28.5
:
1, 28
:
1.5, and 27.5
:
2. A dry/wet phase inversion technique was used for preparation of the integrally skinned asymmetric membranes. A stainless steel homemade applicator was used to prepare polymeric films with the thickness of 250 μm. The polymer-coated glass plates were kept at ambient temperature for 2 min and then immersed in a non-solvent bath containing water and isopropanol in the composition of 75
:
25. After detaching the membrane from the glass plate in the non-solvent bath, it was rinsed with fresh tap water, kept in distilled water overnight and then dried at ambient temperature for 24 h.
2.7. Gas permeation apparatus
A mixed gas setup as shown schematically in Fig. 1 was used for gas permeation studies. The prepared membranes were cut into rectangular 5 × 3 cm shapes and were placed in an appropriate stainless steel cell that was housed in a temperature-controlled electronic oven. The composition of the feed gas was controlled by mixing the specific mass flow rate of CO2 and CH4 using a Brooks mass flow controller. Although primary and secondary amines can transport the CO2 by the facilitated transport mechanism in the absence of water (as discussed before); it is believed that in the presence of the water and carrier (primary and secondary amine), CO2 can form amine–CO2–H2O complexes and small HCO3− ions. Bicarbonate ions (HCO3−) act as a mobile carriers that can transport CO2 across the membrane and enhance the diffusion rate of CO2 through the membrane significantly. Because of the acceleration of the facilitated transport of CO2 and higher CO2 permeability in the presence of water vapor, for the separation of CO2 from gas streams in facilitated transport membranes,22 the feed gas is saturated with water vapor. Here a bubble humidifier was used for humidifying the feed. The desired feed pressure in the permeation cell was achieved by using a backpressure regulator. The argon gas was used to sweep the permeate gas. The permeate was cooled down to ambient temperature and condensed water was removed using a water knockout. The composition of the permeate stream was determined using an Agilent gas chromatograph equipped with a thermal conductive detector (TCD). When the thickness of the membrane is measurable, such as for a dense polymeric membrane, the performance of the membranes is reported using gas permeability. Barrer is the most common unit for reporting the permeability of the membrane, which is defined as
1 Barrer = 1 × 10−10 cm3 (STP) cm cm−2 s−1 cmHg−1 |
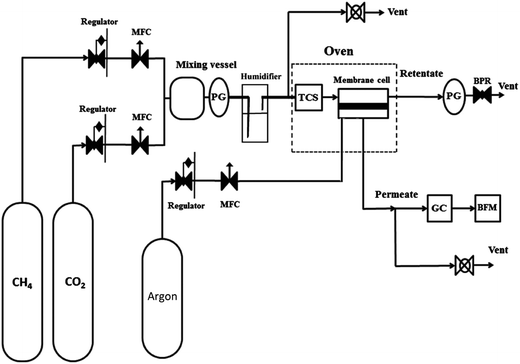 |
| Fig. 1 Schematic diagram of the experimental setup for gas permeation tests. | |
In integrally skinned asymmetric membranes, the skin layer is not correctly detectable or measurable. Hence the pressure-normalized fluxes (P/l)i are more common for determining the gas permeability of the asymmetric membranes which can be presented using the following equation:
|
 | (1) |
where
Qi is the volumetric flow rate of the permeate gas i at STP, Δ
pi is the trans membrane pressure and
A is the effective surface area of the membrane. Gas permeation unit (GPU) is the most common unit for pressure-normalized flux and is calculated as follows:
GPU = 1 × 10−6 cm3 (STP) cm−2 s−1 cmHg−1 |
The following equation was used to calculate membrane selectivity.38,39
|
αCO2/CH4 = (P/l)CO2/(P/l)CH4 = [xCO2-p/xCH4-p]/[xCO2-f/xCH4-f]
| (2) |
3. Results and discussion
3.1. Synthesis and characterization of the chitosan derivatives
The process for the synthesis of Im-CS in this research is shown in Scheme 1. First, the amino groups of chitosan were blocked using phthalic anhydride in a DMF/H2O (95
:
5) mixture to prevent their participation in the subsequent reaction. In the following step, the primary hydroxyl groups of N-phthaloylchitosan were converted to active phenyl carbonate groups. Finally, the carbonate derivative was reacted with N-(3-aminopropyl)-imidazole, which eliminates phenol as a leaving group. According to the literature,40 the phthalimido groups of the glycosidic units then can be deprotected by a primary amine. The final derivative has two types of basic groups (i.e. imidazole groups and primary amino groups) which can work as good carriers for CO2 facilitated transportation.
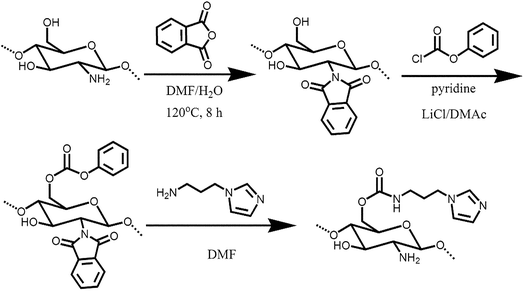 |
| Scheme 1 Synthetic procedure for the chitosan derivatives. | |
3.2. Spectral characterization of the chitosan derivatives
The chemical structure of the chitosan derivatives was characterized by FT-IR and 1H NMR analysis. The FTIR spectra of chitosan (CS) and its derivatives are shown in Fig. 2. In the spectrum of N-phthaloylchitosan, characteristic peaks of the phthalimido group have appeared at 1775 (imide C
O), 1710 (imide C
O), and 719 cm−1 (aromatic). In the spectrum of the carbonate derivative, the signal at 3070 cm−1 is related to the aromatic C–H bonds, signals at 1600 and 1495 cm−1 are related to the aromatic C
C bonds, and the peak at 1765 cm−1 is related to the carbonate group on the chitosan backbone. Furthermore, the intensity of the OH band around 3500 cm−1 is decreased in the carbonate derivative spectrum. In the spectrum of Im-CS, the characteristic peaks of phenylcarbonate and phthalimido groups are eliminated and a new peak at 1712 cm−1 appears that is related to the carbonyl of the carbamate group.
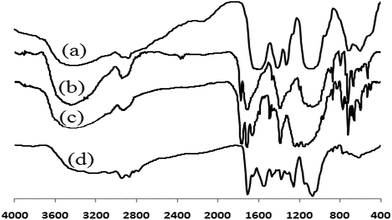 |
| Fig. 2 FT-IR spectra of CS (a), Phth-CS (b), carbonate-Phth-CS (c), and Im-CS (d). | |
The 1H-NMR spectra of carbonate-Phth-CS and Im-CS are shown in Fig. 3. The protons in both structures are completely assigned in the figures. In the spectrum of carbonate-Phth-CS signals in the range of 6.95–7.35 ppm correspond to the aromatic hydrogens of the phenyl group and the signal at 7.78 ppm corresponds to the aromatic hydrogens of the phthaloyl group. The signals in the range of 4.9–5.3 ppm are related to the anomeric hydrogen of the chitosan backbone, and the other glycosidic protons of chitosan are observed in the range of 3.20–4.60 ppm. In the 1H-NMR spectrum of Im-CS the characteristic peaks of the phenyl and phthaloyl groups disappeared. Instead, new signals corresponding to the propylimidazole group appeared at ∼1.84, 3.18, 6.85, 7.17, and 7.46 ppm.
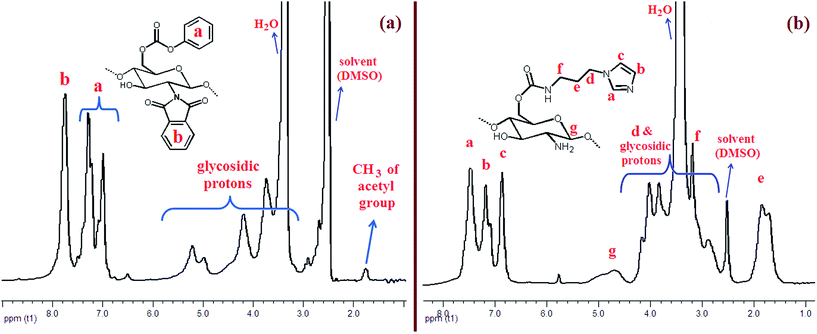 |
| Fig. 3 1H NMR spectra of carbonate-Phth-CS (a), and Im-CS (b). | |
3.3. Effect of Im-CS on the membrane morphology
According to the literature, the morphology and performance of asymmetric membranes can be affected by additives;41,42 therefore, the SEM images of cross sections of the prepared membranes are taken to investigate the effect of Im-CS on the morphology of PES membranes (Fig. 4).
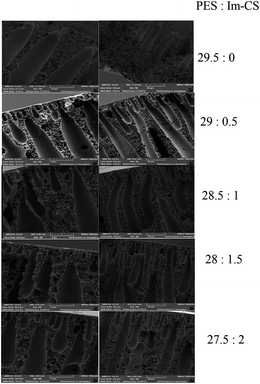 |
| Fig. 4 Effect of Im-CS concentration on the morphology of PES integrally skinned asymmetric membranes. | |
As can be seen in Fig. 4, all of the prepared membranes show a thin skin layer at the top surface and tear like and finger like pores at the porous sublayer. This structure is a classical asymmetric structure for integrally skinned asymmetric membranes.5,13 For integrally skinned asymmetric membranes and in a solution–diffusion mechanism, the membranes’ properties including skin layer thickness,13,43 overall porosity of the membrane7 and surface micro defects43 significantly affect the gas permeability of membranes. Higher membrane porosity, a thinner skin layer and the presence of micro defects lead to higher gas permeability across the membrane.7 As is evident from Fig. 4, PES
:
Im-CS membranes in comparison to pure PES membranes have larger finger like pores. Also small pores near the skin layer disappear in the PES
:
Im-CS membranes.
Higher porosity of the sublayer in integrally skinned asymmetric membranes resulted from a higher phase inversion rate throughout the membrane formation from the polymeric film.42 The presence of an additive can affect the phase inversion rate significantly.44 The presence of a hydrophilic additive in the casting solution enhances the phase inversion rate and results in a more highly porous sublayer.45,46 The non-solvent used was a mixture of 75 V% of water and 25 V% of isopropyl alcohol, therefore Im-CS as a hydrophilic polymer enhanced the phase inversion rate significantly. A higher phase inversion rate leads to higher porosity of the sublayer and an enhancement of the size of finger like pores of the sublayer.
Skin layer thickness is another membrane property that is determined by the phase inversion process.47 In integrally skinned asymmetric membranes the skin layer often has different thicknesses at different point of the membrane. Also measuring the skin layer thickness of this type of membrane using SEM images is not easy as for thin film composite membranes, because the boundary between the real skin layer and the transition layer is not easily detectable.
Therefore for integrally skinned asymmetric membranes, the apparent skin layer thickness is defined and can be calculated using following equation:
|
 | (3) |
where
Pi is the intrinsic permeability of the dense membrane for gas i and (
P/
l)
i is the pressure-normalized flux of membrane for gas i.
13 The intrinsic permeability of a dense membrane for a specific gas is a constant value. Hence an increase in the pressure-normalized flux of membrane for a non-reactive gas implies that the apparent skin layer thickness decreases. As can be seen in
Fig. 5 generally by increasing the Im-CS concentration the pressure-normalized flux of CH
4 (as a non-reactive gas in contrast with CO
2) enhances; that implies the thickness of the skin layer (
l) in the equation decreases.
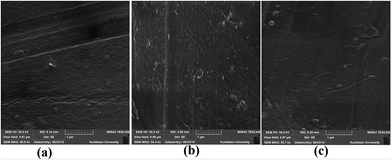 |
| Fig. 5 SEM images of the top surface of uncoated prepared membranes; (a) pure PES, (b) PES : Im-CS with the blend composition of 28.5 : 1, and (c) PES : Im-CS with the blend composition of 27.5 : 2. | |
As described by the Kawakami et al.48 in a ternary polymer/solvent/coagulant system, skin layer thickness is determined by liquid–liquid demixing as well as polymer–liquid demixing in the phase separation process. In an instantaneous demixing between solvent and no-solvent, an ultrathin skin layer supported by a porous substrate is formed. In contrast, in a delayed demixing process between solvent and no-solvent a dense and thick skin layer is formed.
In other words by increasing the Im-CS concentration the apparent skin layer thickness of the integrally skinned asymmetric membranes decreases, because a high phase inversion rate results in a hurried formation of the skin layer and subsequently a thinner skin layer.
As mentioned before, another interesting observation is the decrease of the small tear like pores near the top surface of the membranes. These tear like pores near the skin layer create micro defects and decrease the membrane selectivity. Le Roux and Van Schalkwyk49 reported that gas permeability as well as the gas pair selectivity of polysulfone hollow fiber membranes was enhanced by the surfactant additive. They reasoned that the surface tension of the spinning solution is affected by the additive and this leads to a decrease of defects during phase inversion. Therefore, the same justification can be used for the smaller tear like pores of the membranes formed in the presence of Im-CS that may affect the surface defects of membranes.
The SEM images of the top surface of uncoated pure PES membrane (a), PES
:
Im-CS with the blend composition of 28.5
:
1 (b), and PES
:
Im-CS with the blend composition of 27.5
:
2 (c) are shown in Fig. 5.
As can be seen from these images, the uncoated pure PES membrane has a dark point on the top surface. This dark point is a pinhole or defect of the membrane surface that disappears in the PES
:
Im-CS membranes. This observation confirms our previous discussion about the disappearance of tear like pores near the skin layer and the surface defects in the presence of the Im-CS additive.
3.4. Effects of Im-CS concentration and feed pressure on membrane performance
The effects of the Im-CS content and feed pressure on the CO2 and CH4 permeance and CO2/CH4 selectivity of prepared membranes are shown in Fig. 6–8, respectively. From these figures, it is obvious that higher quantities of Im-CS enhance the CO2 and CH4 permeance, and also increase the CO2/CH4 selectivity. As shown in the previous section, the presence of Im-CS enhances the porosity of the sublayer of membranes, so the permeance of CO2 as well as the permeance of CH4 has been raised. For the PES
:
Im-CS membranes besides the solution–diffusion mechanism, there is a facilitated transport mechanism for the transportation of CO2. As the concentration of Im-CS increases, more facilitated transport sites are provided. Therefore, the total transportation of CO2 enhances significantly and results in a higher CO2/CH4 selectivity. In other words, in Im-CS/PES membranes, the total CO2 permeance is determined by the CO2 transportation via the solution–diffusion mechanism and the facilitated transport mechanism. A higher amount of Im-CS can create more active sites for CO2 facilitated transportation across the membrane, which in turn results in an improved CO2 permeance.14,24,39
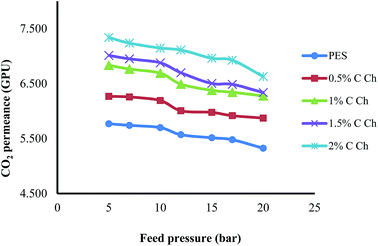 |
| Fig. 6 Effect of Im-CS concentration and feed pressure on the CO2 permeance. | |
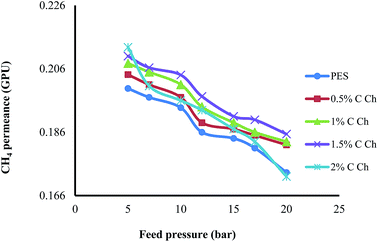 |
| Fig. 7 Effect of Im-CS concentration and feed pressure on the CH4 permeance. | |
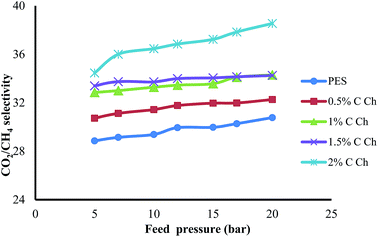 |
| Fig. 8 Effect of Im-CS concentration and feed pressure on the CO2/CH4 selectivity. | |
As is obvious from Fig. 6–8, by increasing the feed pressure for the pure PES membrane as well as the PES
:
Im-CS membranes, the CH4 permeance decreases while CO2 permeance decreases slightly, and so it is possible to obtain a higher CO2/CH4 selectivity as feed pressure increases. Generally, for glassy membranes like PES as the feed pressure increases under plasticization pressure, compaction of the membrane is the dominant effect. In other words, despite the fact that the gas sorption and plasticization of CO2 increase the membrane permeance at higher feed pressure, an obvious decline of gas permeance is observed. As can be seen, the PES
:
Im-CS membranes show normal trends of a glassy membrane.8,50–53
3.5. Effect of feed temperature on the membrane performance
In a dense membrane, the gas permeability is described by a solution–diffusion model. The Arrhenius equation describes the temperature dependency of gas permeability. |
P = P0 exp(−Ep/RT)
| (4) |
where P is the permeability coefficient [Barrer = 10−10 cm3 (STP) cm cm−2 cmHg−1 s−1], P0 is the pre-exponential factor [Barrer], and the temperature independent constant, Ep, is the apparent activation energy of the permeation [kJ mol−1], R is the universal gas constant [8.314 × 10−3 kJ mol−1 K−1] and T is the absolute feed temperature [K].50,54
As can be seen, when Ep > 0, increasing the feed temperature leads to the enhancement of gas permeability. Summation of the activation energy of diffusion (ED) and the enthalpy of sorption (ΔHS) as two independent factors results in EP
Generally, in a glassy membrane Ep > 0 because usually in glassy polymers ED > 0 and |ΔHS| < ED. Hence, as a predictable result by increasing the feed temperature, the gas permeability of all gas species enhances. As the size of the penetrant increases, Ep becomes greater, which means that the feed temperature affects the permeability of the larger penetrant more effectively. Therefore, the feed temperature decreases the selectivity of glassy membranes. As a qualitative description, the increased motion of polymer chains at higher temperatures results in increasing the fractional free volume. Therefore, since temperature improves the permeation rate of less diffusive gases like CH4 more than CO2, at higher temperatures the permeance for all the components enhances and subsequently the selectivity of the membrane decreases.16,55,56 The effect of the feed temperature on the membrane’s performance was investigated in the range of 303–343 K while the feed pressure remained constant at 5 bars. The behavior of the membrane against feed temperature is illustrated in Fig. 9–11. As it is evident from these figures, generally all of the membranes including pure PES and PES
:
Im-CS show normal glassy membrane behavior. Although some of the PES
:
Im-CS membranes show a slight decline in CO2 permeance with increasing feed temperature, generally this rate of decrease of CO2 permeance in the PES
:
Im-CS membranes is less than that of the pure PES. For the PES
:
Im-CS membranes, a higher feed temperature enhances the kinetics of the facilitated transport reaction of CO2 but decreases the equilibrium constant of this reversible reaction.16 It has been observed that the latter effect of feed temperature is dominant and higher feed temperature decreases the facilitated transport of CO2.16,38,39,57 So our results can be justified by this fact that in PES
:
Im-CS membranes lower facilitated transport of CO2 at higher temperatures offsets the effect of feed temperature on the solution–diffusion mechanism. Therefore, we observe a lower increasing rate for CO2 permeance at higher feed temperature in PES
:
Im-CS membranes.
 |
| Fig. 9 Effect of feed temperature on CO2 permeance. | |
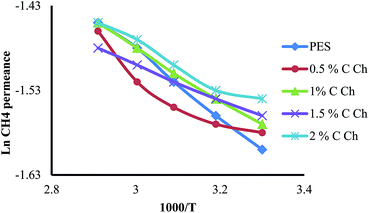 |
| Fig. 10 Effect of feed temperature on CH4 permeance. | |
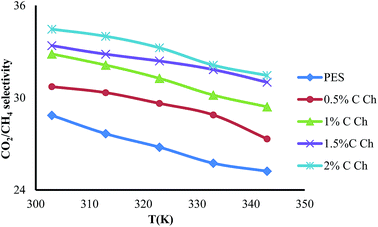 |
| Fig. 11 Effect of feed temperature on CO2/CH4 selectivity. | |
4. Conclusion
A new derivative of chitosan containing an imidazole group (Im-CS) was synthesized successfully. Integrally skinned membranes from Im-CS/PES were prepared in various ratios and utilized for CO2/CH4 separation. Our results showed that the addition of Im-CS as a hydrophilic additive to the PES casting solution enhances the porosity and CO2 permeance of the resulting integrally skinned membranes. Our findings also exhibited that the overall performance of the PES membranes was improved significantly. In contrast to the pure PES, the behavior of the Im-CS/PES membranes against feed temperature was slightly different because of the facilitated transport mechanism of CO2. However, the feed pressure similarly affected both the pure PES and the Im-CS/PES membranes.
References
- Y. Xiao, B. T. Low, S. S. Hosseini, T. S. Chung and D. R. Paul, Prog. Polym. Sci., 2009, 34, 561–580 CrossRef CAS PubMed.
- X. Yu, Z. Wang, J. Zhao, F. Yuan, S. Li, J. Wang and S. Wang, Chin. J. Chem. Eng., 2011, 19, 821–832 CrossRef CAS.
- K. Simons, K. Nijmeijer, J. G. Sala, H. van der Werf, N. E. Benes, T. J. Dingemans and M. Wessling, Polymer, 2010, 51, 3907–3917 CrossRef CAS PubMed.
- H. Lin and B. D. Freeman, J. Mol. Struct., 2005, 739, 57–74 CrossRef CAS PubMed.
- J. Han, W. Lee, J. M. Choi, R. Patel and B.-R. Min, J. Membr. Sci., 2010, 351, 141–148 CrossRef CAS PubMed.
- M. Sadrzadeh, M. Amirilargani, K. Shahidi and T. Mohammadi, J. Membr. Sci., 2009, 342, 236–250 CrossRef CAS PubMed.
- S. Saedi, S. S. Madaeni, A. Arabi Shamsabadi and F. Mottaghi, Sep. Purif. Technol., 2012, 99, 104–119 CrossRef CAS PubMed.
- S. Sridhar, R. Veerapur, M. Patil, K. Gudasi and T. Aminabhavi, J. Appl. Polym. Sci., 2007, 106, 1585–1594 CrossRef CAS PubMed.
- F. A. Hamad, G. Chowdhury and T. Matsuura, J. Membr. Sci., 2001, 191, 71–83 CrossRef CAS.
- F. Hamad, K. C. Khulbe and T. Matsuura, J. Membr. Sci., 2005, 256, 29–37 CAS.
- J. Zhao, Z. Wang, J. Wang and S. Wang, J. Membr. Sci., 2006, 283, 346–356 CrossRef CAS PubMed.
- D. Wang, K. Li and W. Teo, J. Membr. Sci., 2000, 176, 147–158 CrossRef CAS.
- A. F. Ismail, R. Norida, W. Rahman, T. Matsuura and S. Hashemifard, Desalination, 2011, 273, 93–104 CrossRef CAS PubMed.
- C. Yi, Z. Wang, M. Li, J. Wang and S. Wang, Desalination, 2006, 193, 90–96 CrossRef CAS PubMed.
- Z. Wang, M. Li, Y. Cai, J. Wang and S. Wang, J. Membr. Sci., 2007, 290, 250–258 CrossRef CAS PubMed.
- J. Shen, J. Qiu, L. Wu and C. Gao, Sep. Purif. Technol., 2006, 51, 345–351 CrossRef CAS PubMed.
- J. Shen, L. Wu, D. Wang and C. Gao, Desalination, 2008, 223, 425–437 CrossRef CAS PubMed.
- Z. Tong, V. K. Vakharia, M. Gasda and W. W. Ho, React. Funct. Polym., 2015, 86, 111–116 CrossRef CAS PubMed.
- J. Ghogomu, H. Belabbes, D. Langevin, R. Roux and E. Sélégny, React. Funct. Polym., 1996, 29, 41–49 CrossRef CAS.
- M. Sandru, T.-J. Kim and M.-B. Hägg, Desalination, 2009, 240, 298–300 CrossRef CAS PubMed.
- Z. Wang, C. Yi, Y. Zhang, J. Wang and S. Wang, J. Appl. Polym. Sci., 2006, 100, 275–282 CrossRef CAS PubMed.
- L. Deng, T.-J. Kim and M.-B. Hägg, J. Membr. Sci., 2009, 340, 154–163 CrossRef CAS PubMed.
- Y. Cai, Z. Wang, C. Yi, Y. Bai, J. Wang and S. Wang, J. Membr. Sci., 2008, 310, 184–196 CrossRef CAS PubMed.
- S. B. Hamouda, Q. T. Nguyen, D. Langevin and S. Roudesli, C. R. Chim., 2010, 13, 372–379 CrossRef PubMed.
- H. Matsuyama, A. Terada, T. Nakagawara, Y. Kitamura and M. Teramoto, J. Membr. Sci., 1999, 163, 221–227 CrossRef CAS.
- B. Krajewska, React. Funct. Polym., 2001, 47, 37–47 CrossRef CAS.
- M. Vakili, M. Rafatullah, B. Salamatinia, A. Z. Abdullah, M. H. Ibrahim, K. B. Tan, Z. Gholami and P. Amouzgar, Carbohydr. Polym., 2014, 113, 115–130 CrossRef CAS PubMed.
- C. Liu and R. Bai, Curr. Opin. Chem. Eng., 2014, 4, 62–70 CrossRef PubMed.
- M. R. Kumar, R. A. Muzzarelli, C. Muzzarelli, H. Sashiwa and A. Domb, Chem. Rev., 2004, 104, 6017–6084 CrossRef PubMed.
- G. Zampano, M. Bertoldo and F. Ciardelli, React. Funct. Polym., 2010, 70, 272–281 CrossRef CAS PubMed.
- A. Ito, M. Sato and T. Anma, Angew. Makromol. Chem., 1997, 248, 85–94 CrossRef CAS PubMed.
- S. Xiao, X. Feng and R. Y. M. Huang, J. Membr. Sci., 2007, 306, 36–46 CrossRef CAS PubMed.
- Y. Liu, S. Yu, H. Wu, Y. Li, S. Wang, Z. Tian and Z. Jiang, J. Membr. Sci., 2014, 469, 198–208 CrossRef CAS PubMed.
- L. A. El-Azzami and E. A. Grulke, J. Membr. Sci., 2008, 323, 225–234 CrossRef CAS PubMed.
- L. A. El-Azzami and E. A. Grulke, J. Membr. Sci., 2009, 328, 15–22 CrossRef CAS PubMed.
- J. N. Shen, Y. S. Chen, G. N. Zeng and J. H. Qiu, Procedia Eng., 2012, 44, 1063–1064 CrossRef PubMed.
- K. Kurita, H. Ikeda, Y. Yoshida, M. Shimojoh and M. Harata, Biomacromolecules, 2002, 3, 1–4 CrossRef CAS PubMed.
- S. Saedi, S. S. Madaeni, F. Seidi, A. A. Shamsabadi and S. Laki, Chem. Eng. J., 2014, 236, 263–273 CrossRef CAS PubMed.
- S. Saedi, S. S. Madaeni, F. Seidi, A. A. Shamsabadi and S. Laki, Int. J. Greenhouse Gas Control, 2013, 19, 126–137 CrossRef CAS PubMed.
- P. J. Kocienski, Protecting groups, Thieme, 2005 Search PubMed.
- E. Saljoughi, M. Amirilargani and T. Mohammadi, Desalination, 2010, 262, 72–78 CrossRef CAS PubMed.
- S. Saedi, S. S. Madaeni, K. Hassanzadeh, A. A. Shamsabadi and S. Laki, J. Ind. Eng. Chem., 2014, 20, 1916–1929 CrossRef CAS PubMed.
- Y. Li, C. Cao, T.-S. Chung and K. P. Pramoda, J. Membr. Sci., 2004, 245, 53–60 CrossRef CAS PubMed.
- Y. Ma, F. Shi, J. Ma, M. Wu, J. Zhang and C. Gao, Desalination, 2011, 272, 51–58 CrossRef CAS PubMed.
- A. Rahimpour, S. S. Madaeni and Y. Mansourpanah, Desalination, 2010, 258, 79–86 CrossRef CAS PubMed.
- C. H. Loh, R. Wang, L. Shi and A. G. Fane, J. Membr. Sci., 2011, 380, 114–123 CrossRef CAS PubMed.
- A. F. Ismail, N. Ridzuan and S. Abdul Rahman, Songklanakarin J. Sci. Technol., 2002, 24, 1025–1043 CAS.
- H. Kawakami, K. Nakajima and S. Nagaoka, J. Membr. Sci., 2003, 211, 291–298 CrossRef CAS.
- J. D. Le Roux and O. G. Van Schalkwyk, J. Appl. Polym. Sci., 1999, 71, 163–175 CrossRef CAS.
- A. L. Khan, X. Li and I. F. J. Vankelecom, J. Membr. Sci., 2011, 380, 55–62 CrossRef CAS PubMed.
- G. Härtel and T. Püschel, J. Membr. Sci., 1999, 162, 1–8 CrossRef.
- A. F. Ismail and N. Yaacob, J. Membr. Sci., 2006, 275, 151–165 CrossRef CAS PubMed.
- A. Ismail and N. Yaacob, J. Membr. Sci., 2006, 275, 151–165 CrossRef CAS PubMed.
- B. Freeman, Y. Yampolskii and I. Pinnau, Materials science of membranes for gas and vapor separation, John Wiley & Sons, 2006 Search PubMed.
- A. Car, C. Stropnik, W. Yave and K.-V. Peinemann, Sep. Purif. Technol., 2008, 62, 110–117 CrossRef CAS PubMed.
- A. L. Khan, X. Li and I. F. J. Vankelecom, J. Membr. Sci., 2011, 372, 87–96 CrossRef CAS PubMed.
- R. Yegani, H. Hirozawa, M. Teramoto, H. Himei, O. Okada, T. Takigawa, N. Ohmura, N. Matsumiya and H. Matsuyama, J. Membr. Sci., 2007, 291, 157–164 CrossRef CAS PubMed.
|
This journal is © The Royal Society of Chemistry 2015 |
Click here to see how this site uses Cookies. View our privacy policy here.