DOI:
10.1039/C5RA06650F
(Paper)
RSC Adv., 2015,
5, 54258-54265
Dehydrogenation behavior and microstructure evolution of hydrogenated magnesium–nickel–yttrium melt-spun ribbons
Received
14th April 2015
, Accepted 3rd June 2015
First published on 4th June 2015
Abstract
This paper reports porous Mg67Ni33−xYx (x = 0, 1, 3, 6) ribbons which are prepared by a melt spinning method. The dehydrogenation behaviors, including the thermal decomposition process, dehydrogenation capacities, percentage and kinetics, are investigated in a temperature range of 523–623 K. The microstructure evolution during the dehydrogenation process of metal melt-spun ribbons is discussed with respect to the microstructures of hydrogenated and dehydrogenated ribbons. It is considered that the porous structure in the as-prepared ribbons accelerates the diffusion of hydrogen gas and atoms, and increases dehydrogenation nucleation locations and decreases the diffusion distance. Additionally, the addition of yttrium and melt-spinning decreases the activation energy of dehydrogenation. A low activation energy and a refined microstructure play dominant roles in decreasing the dehydrogenation temperature and increasing the kinetics of Mg-based metal melt-spun ribbons.
1. Introduction
Magnesium-based alloys are considered a promising medium for hydrogen storage for on-board vehicle and stationary applications to solve environment and energy issues, due to their high theoretical storage capacity (e.g. Mg 7.6 wt%), light weight and abundance. However, magnesium-based alloys have the high stability of the hydrides and a low hydrogen atom diffusion rate, which causes a high dehydrogenation temperature and low hydrogen desorption kinetics, and limits industrial applications.1
A great many efforts have been devoted to improving the dehydrogenation properties of Mg-based alloys from two aspects, element doping and microstructure modification. Work has proved that the addition of transition metal elements,2,3 rare metal elements4,5 and catalysts6,7 into Mg-based alloys decreases the stability of hydrides and increases the dehydrogenation kinetics.8 However, the excellent kinetics caused by the addition of transition metal elements are at the expense of low dehydrogenation capacities. It has been found that rare earth (RE) elements not only accelerate the dehydrogenation kinetics, but also enhance the dehydrogenation capacity compared with transition metal elements by substituting B side elements of A2B-type Mg-based alloys, and decrease the hydrogen desorption temperature.9 By adding rare earth elements, the high activation of rare earth elements is able to catalyse the decomposition of hydrogen molecules on the surface of alloy particles.10 During the dehydrogenation process, the compounds and RE hydrides could be formed in the alloys and these products have been proved to provide positive catalysis on the formation and decomposition of other hydrides.11 Yttrium (Y), especially, is lighter than other RE elements, and it favors an increase in gaseous hydrogen absorption/desorption capacities per unit mass. Additionally, strain and defects, which are induced by the formation and decomposition of YH2/YH3, have been proved to facilitate hydrogen absorption and desorption.10 The addition of elements and catalysts can significantly improve the hydrogenation/dehydrogenation rates,12 however, these methods still cannot solve the problems of slow dehydrogenation kinetics well.13
The microstructure is closely related to the thermodynamics and kinetics of hydrogenation/dehydrogenation.8 The diffusion of hydrogen atoms in alloys and hydrides is an important factor in the hydrogen desorption kinetics. A nanoscale-refined grain size and amorphous structure can significantly enhance the hydrogen absorption/desorption kinetics and hydrogen storage capacity since the refined grain generates a large number of interfaces along which hydrogen atoms can diffuse more easily.14,15 For microstructure modification, ball milling16 and melt spinning17 have been proved to be powerful techniques to produce amorphous and nanocrystalline Mg2Ni alloys.8 However, ball milling is still limited by some unavoidable shortcomings: contamination of metal powders by milling equipment and oxygen even in argon atmosphere,18 small scale production and its relatively high cost for special safe handling of the powder such as heat-transfer and pipe blockage.3 In addition, the growth of ball milled particles occurs at a high reaction temperature and deteriorates the kinetic properties.19 On the contrary, the microstructure stability of melt spun ribbons is higher than that of ball milled particles during hydrogenation and dehydrogenation cycles.8,20 Generally speaking, the amorphous and nanocrystalline Mg-based alloys prepared by melt-spinning have faster hydrogen absorption and desorption kinetics.21 Melt spinning has been proved an effective method to reduce grain size and possesses attractive hydrogenation/dehydrogenation properties.22 In addition to the enhanced diffusivity of hydrogen atoms, the diffusion distance is also decreased by melt spinning. The melt-spun ribbons can absorb and release hydrogen from two sides, therefore the ribbons can be hydrogenated completely with the thickness less than 50 μm.23 In addition, increased porosity in metals significantly increases the diffusion of gas.24 The dehydrogenation properties are closely related to the microstructure, and the microstructure evolution during dehydrogenation process is necessary to analyze the dehydrogenation mechanism of melt spun ribbons.
The two important factors affecting hydrogen desorption kinetics are the dehydrogenation energy barrier of hydrides and the diffusion of hydrogen atoms. The addition of RE elements facilitates the glass formation of Mg2Ni-based alloys.8 The melt spinning technique combined with the addition of Y into Mg2Ni alloys is employed in this work to decrease the dehydrogenation energy barrier of hydrides and facilitate the diffusion of hydrogen atoms. Special attention was paid to the microstructure evolution and phase transformation of Y-doped Mg-based melt-spun ribbons during the dehydrogenation process. The activation energy of the dehydrogenation reaction is calculated by the Kissinger method. In addition, the effect of temperature on dehydrogenation kinetics is also emphasized and the corresponding influencing factors are discussed. The corresponding dehydrogenation mechanism of Mg–Ni–Y melt-spun ribbons is proposed in this work.
2. Experimental
Mg-based hydrogen storage alloys with the composition Mg67Ni33−xYx (x = 0, 1, 3, 6 at.%) were melted under the protection of covering flux in a resistance furnace. The alloys were re-melted and spun on a single copper roller with linear velocity 40 ms−1 in an argon atmosphere of 500 mbar.25 The melt-spun ribbons were about 50 μm in thickness, 5 mm in width and 10–30 mm in length. The ribbons, which were prepared by the melt-spinning technique, were directly hydrogenated in an automatic Sieverts apparatus (PCT Pro2000) under an initial hydrogen pressure of 30 bar at two temperatures of 523 and 623 K for 4 h. The dehydrogenation kinetics were measured under initial vacuum at the corresponding hydrogenation temperature for 1 h. Before hydrogenation/dehydrogenation measurements, all the alloy ribbons were activated by three continuous hydrogenation/dehydrogenation cycles maintaining an initial hydrogen pressure of 30 bar at 10 h for hydrogenation and vacuum for 1 h for dehydrogenation. The metallographic samples were prepared without any etching reagent even water. The phase composition and microstructure of the hydrogenated ribbons were characterized by X-Ray Diffraction (XRD), Scanning Electron Microscopy (SEM, TESCAN, MIR A3 XMU) and Transition Electron Microscopy (TEM, TECNAI, F30 G2). The phase transformations during dehydrogenation of the hydrogenated ribbons were analyzed by Differential Scanning Calorimetry (DSC, NETZSCH, STA449C) at various heating rates of 5, 10, 15 and 20 K min−1 from ambient temperature to 723 K in an argon atmosphere.
3. Results and discussion
3.1 Phase analysis of hydrogenated ribbons
The XRD patterns of the hydrogenated Mg67Ni33−xYx (x = 0, 1, 3, 6) melt-spun ribbons are shown in Fig. 1a. The dominant phase of the hydrogenated Mg67Ni33−xYx (x = 0, 1, 3, 6) melt-spun ribbons is monoclinic Mg2NiH4. Bragg peaks of Mg2NiH0.3 and MgH2 are also observed in the XRD patterns. In addition, several Bragg peaks of MgYNi4, YH2, YH3 and cubic structure Mg2NiH4 phases are observed in the XRD pattern of the hydrogenated ribbon with x = 6. The intensity (counts) of the Bragg peaks of the MgH2 phase (∼27.9°) increases from 599 to 2375 with the increasing Y content in the hydrogenated Mg67Ni33−xYx (x = 0, 1, 3, 6) melt-spun ribbons. It indicates that the phase content of MgH2 increases with the increase of Y content, which coincides with the content of reactant α-Mg phase in melt-spun ribbons.25 On the contrary, the phase content of Mg2NiH0.3 decreases with the increase of Y content, which can be seen from the decreasing intensities of the Bragg peaks from Mg2NiH0.3 (about 21, 37 and 47°). Mg2NiH0.3 is a transitional phase of the Mg2Ni–Mg2NiH4 system. The addition of Y is beneficial to decrease the content of the transitional phase Mg2NiH0.3 by facilitating the transformation of Mg2NiH0.3 to Mg2NiH4. The hydride of MgYNi4 is not observed in the XRD patterns of the hydrogenated melt-spun ribbons because the MgYNi4 absorbs hydrogen reversibly at room temperature,26 and almost all of the hydrogen is released under 500 K.27 The formation of hydride YH2, as the catalyst, facilitates the formation of Mg2NiH0.3 and MgH2 during the hydrogenation process.11 Then Mg2NiH0.3 and YH2 are completely hydrogenated to Mg2NiH4 and YH3, respectively. The strain and defects induced by YH2/YH3 are believed to facilitate the hydrogenation/dehydrogenation process.11
 |
| Fig. 1 The XRD patterns of the (a) hydrogenated and (b) dehydrogenated Mg67Ni33−xYx (x = 0, 1, 3, 6) melt-spun ribbons. | |
Fig. 1b shows the XRD patterns of the dehydrogenated Mg67Ni33−xYx (x = 0, 1, 3, 6) ribbons. The dominant phase of dehydrogenated Mg67Ni33−xYx ribbons is Mg2Ni. The MgNi2, which is eliminated by the melt-spinning technique, is separated out from the dehydrogenated ribbons after 4 hydrogenation/dehydrogenation cycles. The Bragg peak intensity of MgNi2 decreases with the increase of Y in the dehydrogenated ribbons. The Bragg peaks of Mg (∼43.3°) and MgYNi4 (∼42.7°) are in the dehydrogenated Mg67Ni33−xYx (x = 1, 3, 6) ribbons, their intensities increase with increasing Y in the dehydrogenated ribbons. The YH2, which is an incomplete dehydrogenation product of YH3, also appears in the Bragg peaks of dehydrogenated Mg67Ni33−xYx ribbons with x = 6. The phases of the dehydrogenated ribbons are similar to those of the melt-spun ribbons25 except for the addition of MgNi2 and YH2 after 4 hydrogenation/dehydrogenation cycles.
From comparing the phase structures of the hydrogenated and dehydrogenated samples, the phase transformations contain Mg2NiH4 to Mg2Ni, Mg2NiH0.3 to Mg2Ni, MgH2 to Mg, and YH3 to YH2. The MgYNi4 phase appears both in hydrogenated and dehydrogenated samples, but the hydride of MgYNi4 is not observed. The hydride of MgYNi4 is probably dehydrogenated in this experimental condition.27 In addition, the trace MgNi2 phase precipitates out in 4 hydrogenation/dehydrogenation cycles. The broadening of the XRD patterns indicates that both amorphous and nanocrystalline regions are included in the hydrogenated and dehydrogenated ribbons.
3.2 Microstructures of hydrogenated ribbons
The crystallite sizes of the ribbons increase from 5 nm to 150 nm with the addition of Y content in the melt-spun Mg67Ni33−xYx (x = 1, 3, 6) ribbons. Fig. 2 shows a high resolution image of the hydrogenated ribbons, the corresponding Selected Area Electron Diffraction (SAED) pattern and Electron Energy-Loss Spectroscopy (EELS) hydrogen mapping. The ribbons contain amorphous and nanocrystalline regions as shown in Fig. 2a, which is consistent with the results of the XRD. The circled area is amorphous and the straight-line portion is nanocrystalline. In addition, the continuous rings with scattered diffraction points in the SAED pattern also indicate that the microstructures of ribbons are amorphous and nanocrystalline. Nanocrystalline hydrides enhance the hydrogenation kinetics.28 The SAED pattern shows that the ribbons are polycrystalline within an electron beam diameter. The major phase Mg2NiH4 is observed in the hydrogenated ribbons in the polycrystalline SAED rings. It has been proven that the amorphous and nanocrystalline regions can provide passageways for the diffusion of hydrogen atoms.29 The grains of the hydrogenated ribbons are refined for the effect of melt-spinning. The amorphous and nanocrystalline regions formed by melt-spinning can shorten the diffusion distance and enhance the diffusivity of hydrogen.
 |
| Fig. 2 HRTEM image and SAED pattern of the Mg67Ni33−xYx (x = 1, 3, 6) ribbons and EELS hydrogen mapping. (a) x = 1, (b) x = 3, (c) x = 6, (d) EELS hydrogen mapping of x = 3 ribbons. | |
The High Resolution Transmission Electron Microscopy (HRTEM) image and the corresponding Fast Fourier Transform (FFT) pattern of the hydrogenated Mg67Ni33−xYx (x = 3) ribbon are shown in Fig. 2b. The amorphous structure and nanocrystallinity are observed in the HRTEM image. The FFT pattern is an amorphous ring with slight scattered diffraction points. Fig. 2c shows the HRTEM image of the hydrogenated Mg67Ni33−xYx (x = 6) ribbons. The interplanar spacing and Miller indices of Mg2NiH4 are marked in the HRTEM image and SAED pattern. A lot of stacking faults are observed in the HRTEM image. Crystal defects are induced by hydrogen absorption/desorption in Mg2Ni and other hydrogen storage alloys.30 It has been reported that the stacking faults are beneficial to the nucleation of hydrides and lead to lower hydrogen desorption temperatures and better kinetics.31 Comparing with the ribbons with x = 1 and 3, the hydrogenated ribbons with x = 6 contain more crystalline structures as shown in Fig. 2c. Plenty of amorphous structures are observed in the melt-spun ribbons of x = 6 before hydrogenation. The crystallization of the amorphous structure occurs in the hydrogenation process.21 In addition, stacking faults are formed in the crystallization process. It has been reported that changing the structure of the Mg2Ni alloy from polycrystalline to nanocrystalline results in a drop of about 100 K in absorption/desorption temperature.32 The amorphous alloy exhibits faster hydrogenation kinetics than the crystallized alloy with the same composition due to the faster hydrogen diffusion in the amorphous phase.4 Amorphous and nanocrystalline regions are helpful to the hydrogenation/dehydrogenation.
In order to analyze the distribution of hydrides, the EELS hydrogen mapping is characterized as shown in Fig. 2d. The white portion is the area including hydrogen atoms. The dark particle surface provides evidence of partial hydrogen atom-release from the particle surface under the high vacuum of the TEM and the effect of the electron beam. The hydrogen desorption process is clearly seen in the EELS maps at ∼400 °C,33 but the Mg-based hydrides are rather stable at room temperature. The SAED pattern shows that the ribbons have been hydrogenated and the dominant hydride can be ascribed to Mg2NiH4.
3.3 Microstructure evolution during dehydrogenation
The dehydrogenation process of ball milled particles has been described by Tanniru et al.34 However, the dehydrogenation process of melt-spun ribbon has not been described. In order to analyze the dehydrogenation process, the microstructures of hydrogenated and dehydrogenated melt-spun ribbons are analyzed in this work as shown in Fig. 3. Plenty of connected pores, which have been observed in the microstructure of melt-spun ribbons,25 are also observed in the microstructure of hydrogenated and dehydrogenated ribbons after 4 hydrogenation/dehydrogenation cycles. Owing to the insulativity and lower z-contrast (atomic number) of the hydride, the hydride phase appears darker than the metal phase in the BSE mode.35,36 The areas around the pores are preferentially hydrogenated as shown in Fig. 3a. The process of hydrogen desorption is the inverse process of absorption.37 The areas around the pores in melt spun ribbons are similar to the surface of ball milled particles. The areas around the pores are the preferential positions for dehydrogenation. Cracks can be observed in the dehydrogenated ribbons as shown in Fig. 3b. The hydrogen absorption and desorption of alloys results in the expansion and contraction of the crystal lattice during the hydrogenation/dehydrogenation cycles, inducing stress in the grain. Hydrogenation/dehydrogenation cycles increase the brittleness of the ribbons, but serious damage did not occur. The melt spun ribbons are distorted during hydrogenation/dehydrogenation cycles and the distortion counteracts the partial distortion energy. Plenty of amorphous and nanocrystalline regions in the melt-spun ribbons provide more diffusion paths for hydrogen atoms. The grain size reduction to the nanoscale decreases the diffusion distance. The porous surface structure increases the hydrogen absorption rate.28 Hydrogen diffusion through the bulk metal (hydride) phase is usually quite slow and often rate-limiting.38 Hydrogen diffusion in the gaseous phase is fast, greater than that in the bulk metal phase. It has been reported that fast hydrogen diffusion through or along the porous carbon phase benefits the kinetics of hydrogen release and uptake.38 The pores in the melt-spun ribbons provide plenty of surfaces, increasing dehydrogenation nucleation locations and decreasing the diffusion distances. In addition, the released hydrogen gas can be exhausted from the ribbons by the connected pores, further improving the hydrogen desorption kinetics. The areas around the pores are the preferential positions for hydrogenation/dehydrogenation.
 |
| Fig. 3 The SEM/BSE images of (a) hydrogenated and (b) dehydrogenated melt-spun ribbons. | |
3.4 Thermal decomposition behavior of hydrogenated ribbons
Fig. 4a shows the dehydrogenation DSC curves and the corresponding first derivative curves (DDSC) of hydrogenated Mg67Ni33−xYx (x = 0, 1, 3, 6) melt-spun ribbons at a heating rate of 10 K min−1. The obvious endothermic peak around 520–560 K observed in each DSC curve can be ascribed to the dehydrogenation peak of the dominant Mg2NiH4 phase. The dehydrogenation phases are Mg2NiH4, Mg2NiH0.3, MgH2 and YH3 from the phase analysis. The dehydrogenation peak of the intermediate hydride Mg2NiH0.3 phase overlaps Mg2NiH4. The dehydrogenation temperature of MgH2 is higher than that of Mg2NiH4, the endothermic peak of MgH2 powder is about 664 K, but it is still over 593 K in the Mg80Ni10Y10 alloy with the addition of Ni and Y.9 The trace endothermic peaks of MgH2 in Fig. 4a are about 600–660 K for the minor content of MgH2. It has been reported that the desorption temperature of YH3 into YH2 in vacuum starts at 443 K and the peak temperature is 533 K.39 The endothermic peak of YH3 to YH2 overlaps that of Mg2NiH4 in the Mg67Ni33−xYx ribbon with x = 6. The main endothermic peak of Mg2NiH4 is not symmetric, peaks overlap the main endothermic peak as can be seen in the DDSC curve. The decomposition of Mg2NiH4 is divided into two steps, which are dehydrogenation of Mg2NiH4 to Mg2NiH0.3 and dehydrogenation of Mg2NiH0.3 to Mg2Ni.40 Therefore, the main dehydrogenation peaks contain overlapping peaks. The area under the peaks reveals the heat of the absorption of ribbons per unit mass. The heat of the absorption of the ribbon with x = 0 exceeds 1700 J g−1, and it is below 1300 J g−1 with x = 1, 3 and 6. The addition of Y decreases the heat of the absorption of ribbons per unit mass in the dehydrogenation process.
 |
| Fig. 4 Dehydrogenation DSC and corresponding first derivative curves of the hydrogenated Mg67Ni33−xYx (x = 0, 1, 3, 6) melt-spun ribbons. (a) Heating rate of 10 K min−1 in Mg67Ni33−xYx (x = 0, 1, 3, 6) melt-spun ribbons, (b) heating rates of 5, 10, 15 and 20 K min−1 in x = 1 ribbons. | |
It is obvious that the peak dehydrogenation temperature (∼525 K) of the melt-spun ribbon with x = 1 is lower compared with that of the melt-spun ribbons with x = 0, 3 and 6 (∼542, ∼539 and ∼554 K, respectively) in Fig. 4a. In order to analyze the activation energy of the dehydrogenation reaction of Mg2NiH4, the dehydrogenation DSC curves of the hydrogenated Mg67Ni33−xYx (x = 0, 1, 3, 6) melt-spun ribbons at heating rates of 5, 10, 15 and 20 K min−1 are measured and the DSC curves of x = 1 ribbons are shown in Fig. 4b. The corresponding dominant dehydrogenation peak temperatures of Mg67Ni33−xYx (x = 0, 1, 3, 6) melt-spun ribbons are summarized in Table 1. The Arrhenius equation,41
, indicates that the lower activation energy Ea is related to faster reaction rate k and lower temperature T. The apparent activation energy for dehydrogenation of the dominant phase Mg2NiH4 in the hydrogenated Mg67Ni33−xYx (x = 0, 1, 3, 6) ribbons is calculated based on the dehydrogenation peak temperatures in Table 1 using the Kissinger equation (eqn (1)).42
| 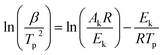 | (1) |
where
β is the heating rate,
Tp is the peak temperature,
Ak is the preexponential factor,
Ek is the dehydrogenation activation energy,
R is the gas constant (8.3145 J (K mol)
−1). ln(
β/Tp2) and 1/
Tp are linear correlation coefficients. Fitting curves of the hydrogenated Mg
67Ni
33−xY
x (
x = 0, 1, 3, 6) melt-spun ribbons using the Kissinger method present a good linear relation between ln(
β/
Tp2) and 1/
Tp with a slope of –
Ek/
R, as shown in
Fig. 5a. The activation energy
Ek of the Mg
67Ni
33−xY
x (
x = 0, 1, 3, 6) ribbons in the dehydrogenation can be summarized as 102, 73, 98 and 80 kJ mol
−1 by the Kissinger equation,
42 respectively. The
Ek of melt-spun ribbons with
x = 0 is 102 kJ mol
−1, which is close to that of Mg
2NiH
4.
43 The trend line of activation energy of the Mg
67Ni
33−xY
x (
x = 0, 1, 3, 6) ribbons is shown in
Fig. 5b. The dehydrogenation activation energy of the ribbons with
x = 1, 3, 6 is lower than that of the hydrogenated ribbon with
x = 0 with the addition of Y. The hydrogenated melt-spun ribbon with
x = 1 possesses the lowest activation energy of the dehydrogenation reaction among the experimental alloys. The small quantity addition of Y and refinement of the particles and grains decreases the apparent activation energy for hydrogen desorption by shortening the diffusion distance and enhancing the diffusivity with the increase of the micro strain and lattice distortion.
44 YH
2 and YH
3 are generated in the Mg-based alloys in hydrogenation and dehydrogenation processes. Fine YH
2/YH
3 particles provide a large number of active sites and paths to enhance the H atom diffusion along abundant phase boundaries and hydride phases.
45 The refined grain size of alloys, the multiphase structure and YH
2/YH
3 decrease the activation energy during dehydrogenation.
Table 1 The dehydrogenation peak temperatures of the hydrogenated Mg67Ni33−xYx (x = 0, 1, 3, 6) melt-spun ribbons at heating rates of 5, 10, 15 and 20 K min−1
Composition Mg67Ni33−xYx |
Dehydrogenation peak temperature |
5 K min−1 |
10 K min−1 |
15 K min−1 |
20 K min−1 |
x = 0 |
527 |
542 |
553 |
556 |
x = 1 |
507 |
525 |
534 |
547 |
x = 3 |
526 |
539 |
549 |
557 |
x = 6 |
538 |
554 |
568 |
577 |
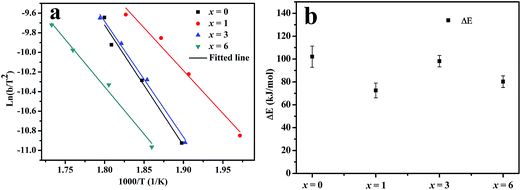 |
| Fig. 5 Fitted Kissinger curves and corresponding dehydrogenation activation energy curves of the hydrogenated Mg67Ni33−xYx (x = 0, 1, 3, 6) ribbons. (a) Fitted Kissinger curves, (b) the activation energy curves of the dehydrogenation reaction. | |
3.5 Dehydrogenation kinetics
The activation energy is related to the reaction temperature as well as the reaction kinetics. The hydrogen desorption capacities of the Mg67Ni33−xYx (x = 0, 1, 3, 6) ribbons detected at 523 and 623 K are shown in Fig. 6. The hydrogen desorption capacities of all the ribbons with added Y are higher than Mg67Ni33−xYx (x = 0) ribbons at 523, 573 (ref. 25) and 623 K. The addition of Y decreases the activation energy of the dehydrogenation reaction and increases the hydrogen desorption capacity corresponding with Mg67Ni33−xYx (x = 0) ribbons. The Mg67Ni33−xYx ribbons are not dehydrogenated completely at the same hydrogenation temperature from the dehydrogenation percent shown in Fig. 6. It can be explained that partial hydrides (such as YH2) do not release hydrogen at this temperature. In addition, hydrogen desorption is related to hydrogen pressure as well as the temperature.46 Hydrogen pressure increases with the hydrogen desorption during the dehydrogenation process, and the partially dissolved hydrogen in the alloys is not released under the increased hydrogen pressure. Further decreasing the hydrogen pressure and raising the temperature can facilitate the dehydrogenation of hydrides. The content of MgYNi4 increases with the increasing Y content in the ribbons with x = 1, 3 and 6.25 Mg is consumed by forming MgYNi4 but the hydride of MgYNi4 is not observed in the hydrogenated ribbons. In addition, partial hydrides (such as YH2) do not release hydrogen at the experimental temperature. The maximum dehydrogenation capacity of ribbons with x = 6 is lower than that of x = 3. The low activation energy of the dehydrogenation reaction makes it easy to release hydrogen. The ribbon with x = 1 has the maximum dehydrogenation capacity of the Mg67Ni33−xYx ribbons for the lowest activation energy of the dehydrogenation reaction. But the ribbon with x = 1 has a relatively high dehydrogenation percentage even at 523 K. The low activation energy of the dehydrogenation reaction of the Mg67Ni33−xYx (x = 1) ribbon not only increases the hydrogen desorption capacity and kinetics but decreases the dehydrogenation temperature.
 |
| Fig. 6 Hydrogen desorption content of the Mg67Ni33−xYx ribbons. | |
Fig. 7 shows the dehydrogenation kinetics curves of the Mg67Ni33−xYx (x = 0, 1, 3, 6) ribbons at 523 and 623 K in the initial 1 and 0.5 h. As can be seen from the kinetics curves, the dehydrogenation rates of ribbons at 523 K are lower than those at 623 K. The increase of temperature improves the dehydrogenation kinetics of ribbons. After the addition of Y, the dehydrogenation kinetics of the Mg67Ni33−xYx (x = 1, 3, 6) ribbons are better than that of ribbons with x = 0 at 523 K. Considering the values of the activation energy of dehydrogenation, the values of the Mg67Ni33−xYx (x = 1, 3, 6) ribbons are lower than that of the ribbon with x = 0. The properties of dehydrogenation kinetics are related to the activation energy of dehydrogenation. In addition, the dehydrogenation kinetics are also related to the microstructure of the ribbons. The grain size of ribbons increases with the addition of Y elements. The dehydrogenation kinetics are the results of the activation energy of the dehydrogenation reaction combined with the microstructure. The ribbon with x = 1 has the highest kinetics in the Mg67Ni33−xYx (x = 1, 3, 6) ribbons at 523 and 623 K. The high dehydrogenation kinetics of Mg67Ni33−xYx ribbons with x = 1 are also related to the high pore percentage.25
 |
| Fig. 7 The dehydrogenation kinetics curves of the Mg67Ni33−xYx (x = 0, 1) ribbons at 523 and 623 K in the initial 1 and 0.5 h. (a) 523 K in the initial 1 h, (b) 623 K in the initial 0.5 h. | |
4. Conclusions
The dehydrogenation phase transformations of Mg2NiH4 to Mg2Ni, Mg2NiH0.3 to Mg2Ni, MgH2 to Mg and YH3 to YH2 of hydrogenated Mg67Ni33−xYx (x = 0, 1, 3, 6) ribbons were investigated. Amorphous and nanocrystalline structures and stacking faults are contained in the Mg67Ni33−xYx (x = 0, 1, 3, 6) ribbons. H is evenly distributed in the hydrogenated ribbons as shown by EELS analysis. The pores in the melt-spun ribbons are the preferential areas for hydrogenation/dehydrogenation. The pores in the metal ribbons generated by melt-spinning to facilitate the diffusion of hydrogen, increase dehydrogenation nucleation locations and decrease the diffusion distances. The high dehydrogenation kinetics are the result of low activation energy combined with amorphous and nanocrystalline regions. The low activation energy of the dehydrogenation reaction, caused by melt-spinning and the addition of Y, decreases the dehydrogenation temperatures and increases the dehydrogenation kinetics of Mg-based melt-spun ribbons.
Acknowledgements
This work is financially supported by the Doctorate Foundation of Northwestern Polytechnical University (CX201107) and Project supported by the Research Fund of the State Key Laboratory of Solidification Processing (NWPU) (95-QZ-2014). The Program of Introducing Talents of Discipline to Universities (B08040) is also acknowledged. Prof. Zhong-min Wang from Guilin University of Electronic Technology is gratefully appreciated for his help in hydrogen absorption/desorption measurements.
References
- P. Vajeeston, P. Ravindran, B. C. Hauback, H. Fjellvåg, A. Kjekshus, S. Furuseth and M. Hanfland, Phys. Rev. B: Condens. Matter Mater. Phys., 2006, 73, 224102 CrossRef.
- D. Vyas, P. Jain, J. Khan, V. Kulshrestha, A. Jain and I. P. Jain, Int. J. Hydrogen Energy, 2012, 37, 3755–3760 CrossRef CAS.
- Y. H. Cho, S. Aminorroaya, H. K. Liu and A. K. Dahle, Int. J. Hydrogen Energy, 2011, 36, 4984–4992 CrossRef CAS.
- Á. Révész, Á. Kis-Tóth, L. K. Varga, E. Schafler, I. Bakonyi and T. Spassov, Int. J. Hydrogen Energy, 2012, 37, 5769–5776 CrossRef.
- J. X. Zou, X. Q. Zeng, Y. J. Ying, X. Chen, H. Guo, S. Zhou and W. J. Ding, Int. J. Hydrogen Energy, 2013, 38, 2337–2346 CrossRef CAS.
- R. K. Singh, H. Raghubanshi, S. K. Pandey and O. N. Srivastava, Int. J. Hydrogen Energy, 2010, 35, 4131–4137 CrossRef CAS.
- X. J. Hou, R. Hu, T. B. Zhang, H. C. Kou, J. S. Li and X. Y. Xue, Int. J. Hydrogen Energy, 2013, 38, 12904–12911 CrossRef CAS.
- Y. Zhang, T. Zhai, B. Li, H. Ren, W. Bu and D. Zhao, J. Mater. Sci. Technol., 2014, 30, 1020–1026 CAS.
- S. Kalinichenka, L. Röntzsch, C. Baehtz and B. Kieback, J. Alloys Compd., 2010, 496, 608–613 CrossRef CAS.
- Z. N. Li, X. P. Liu, L. J. Jiang and S. M. Wang, Int. J. Hydrogen Energy, 2007, 32, 1869–1874 CrossRef CAS.
- J. W. Liu, C. C. Zou, H. Wang, L. Z. Ouyang and M. Zhu, Int. J. Hydrogen Energy, 2013, 38, 10438–10445 CrossRef CAS.
- S. Kalinichenka, L. Röntzsch and B. Kieback, Int. J. Hydrogen Energy, 2009, 34, 7749–7755 CrossRef CAS.
- S. T. Sabitu, G. Gallo and A. J. Goudy, J. Alloys Compd., 2010, 499, 35–38 CrossRef CAS.
- X. J. Hou, R. Hu, T. B. Zhang, H. C. Kou and J. S. Li, Int. J. Hydrogen Energy, 2013, 38, 16168–16176 CrossRef CAS.
- J. Cermák and L. Král, Acta Mater., 2008, 56, 2677–2686 CrossRef.
- Á. Révész and D. Fátay, J. Power Sources, 2010, 195, 6997–7002 CrossRef.
- C. Pohlmann, B. Kieback and L. Röntzsch, Int. J. Hydrogen Energy, 2014, 39, 8331–8339 CrossRef CAS.
- C. Suryanarayana, Prog. Mater. Sci., 2001, 46, 1–184 CrossRef CAS.
- Y. S. Au, M. K. Obbink, S. Srinivasan, P. C. M. M. Magusin, K. P. de Jong and P. E. de Jongh, Adv. Funct. Mater., 2014, 24, 3604–3611 CrossRef CAS.
- G. Y. Liang, D. C. Wu, L. Li and L. J. Huang, J. Power Sources, 2009, 186, 528–531 CrossRef CAS.
- Q. A. Zhang, L. X. Zhang and Q. Q. Wang, J. Alloys Compd., 2013, 551, 376–381 CrossRef CAS.
- E. A. Lass, Int. J. Hydrogen Energy, 2012, 37, 9716–9721 CrossRef CAS.
- I. P. Jain, C. Lal and A. Jain, Int. J. Hydrogen Energy, 2010, 35, 5133–5144 CrossRef CAS.
- V. Bérubé, G. Radtke, M. Dresselhaus and G. Chen, Int. J. Energy Res., 2007, 31, 637–663 CrossRef.
- W. J. Song, J. S. Li, T. B. Zhang, H. C. Kou and X. Y. Xue, J. Power Sources, 2014, 245, 808–815 CrossRef CAS.
- K. Aono, S. Orimo and H. Fujii, J. Alloys Compd., 2000, 309, L1–L4 CrossRef CAS.
- N. Hanada, S.-I. Orimo and H. Fujii, J. Alloys Compd., 2003, 356–357, 429–432 CrossRef CAS.
- B. Sakintuna, F. Lamari-Darkrim and M. Hirscher, Int. J. Hydrogen Energy, 2007, 32, 1121–1140 CrossRef CAS.
- Y. H. Zhang, D. L. Zhao, S. H. Guo, Y. Qi, Z. W. Wu and X. L. Wang, J. Alloys Compd., 2009, 476, 457–461 CrossRef CAS.
- D. Liu, Y. Zhu and L. Li, Int. J. Hydrogen Energy, 2007, 32, 2417–2421 CrossRef CAS.
- N. Takeichi, K. Tanaka, H. Tanaka, T. T. Ueda, Y. Kamiya, M. Tsukahara, H. Miyamura and S. Kikuchi, J. Alloys Compd., 2007, 446–447, 543–548 CrossRef CAS.
- L. H. Kumar, B. Viswanathan and S. S. Murthy, J. Alloys Compd., 2008, 461, 72–76 CrossRef CAS.
- K. Tanaka, T. Miwa, K. Sasaki and K. Kuroda, J. Alloys Compd., 2009, 478, 308–316 CrossRef CAS.
- M. Tanniru, H. Y. Tien and F. Ebrahimi, Scr. Mater., 2010, 63, 58–60 CrossRef CAS.
- M. Vittori Antisari, A. Aurora, D. Mirabile Gattia and A. Montone, Scr. Mater., 2009, 61, 1064–1067 CrossRef CAS.
- H.-Y. Tien, M. Tanniru, C.-Y. Wu and F. Ebrahimi, Int. J. Hydrogen Energy, 2009, 34, 6343–6349 CrossRef CAS.
- K. C. Chou and K. Xu, Intermetallics, 2007, 15, 767–777 CrossRef CAS.
- P. Adelhelm and P. E. de Jongh, J. Mater. Chem., 2011, 21, 2417–2427 RSC.
- V. A. Yartys, O. Gutfleisch, V. V. Panasyuk and I. R. Harris, J. Alloys Compd., 1997, 253–254, 128–133 CrossRef CAS.
- S. Kalinichenka, L. Röntzsch, C. Baehtz, T. Weißgärber and B. Kieback, J. Alloys Compd., 2011, 509(suppl. 2), S629–S632 CrossRef CAS.
- S. Arrhenius, Z. Phys. Chem., 1889, 4, 226 Search PubMed.
- H. E. Kissinger, Anal. Chem., 1957, 29, 1702–1706 CrossRef CAS.
- I. C. Atias-Adrian, F. A. Deorsola, G. A. Ortigoza-Villalba, B. De Benedetti and M. Baricco, Int. J. Hydrogen Energy, 2011, 36, 7897–7901 CrossRef CAS.
- Y. P. Pang, Y. F. Liu, X. Zhang, M. X. Gao and H. G. Pan, Int. J. Hydrogen Energy, 2013, 38, 1460–1468 CrossRef CAS.
- F. P. Luo, H. Wang, L. Z. Ouyang, M. Q. Zeng, J. W. Liu and M. Zhu, Int. J. Hydrogen Energy, 2013, 38, 10912–10918 CrossRef CAS.
- L. Schlapbach and A. Züttel, Nature, 2001, 414, 353–358 CrossRef CAS PubMed.
|
This journal is © The Royal Society of Chemistry 2015 |
Click here to see how this site uses Cookies. View our privacy policy here.