DOI:
10.1039/C5RA05942A
(Paper)
RSC Adv., 2015,
5, 57187-57192
Fabrication of hierarchically porous monolithic layered double hydroxide composites with tunable microcages for effective oxyanion adsorption†
Received
3rd April 2015
, Accepted 22nd June 2015
First published on 23rd June 2015
Abstract
Removal of toxic substances from industrial wastes is an urgent issue for realizing a sustainable society. Layered double hydroxides (LDHs) are expected to be an effective adsorbent for toxic anions, especially oxyanions, because of their high anion adsorption capacity and reusability. Monolithic LDH materials with rational meso- and macropores are expected to show high adsorption capacity/rate towards targeted toxic substances owing to their large specific surface area and liquid transport property. Besides fabricating hierarchical pores, size control of microcages in LDH crystals is required to achieve selective removal of oxyanions. Herein, we prepared hierarchically porous monolithic LDH composites with tunable microcages by changing the combination of cationic species in the LDH crystal. Monolithic Mg–, Mn–, Fe–, Co– and Ni–Al type LDH composites with hierarchical pores were successfully prepared via an epoxide-mediated sol–gel reaction accompanied with phase separation. The monolithic Co–Al type LDH composite with hierarchical pores exhibited the highest CrO42− adsorption capacity because its microcage size easily fits the CrO42− size. Also Co–Al type LDH composites adsorbed different oxyanions, depending on their affinity with the LDH, in a SO42−, CrO42−, MoO42− and HVO42− co-existing solution. The pore size controllability in discrete length-scales of micrometers, nanometers, and picometers offers LDHs with tailored surface chemistries and physical properties desirable for effective and selective oxyanion adsorption.
Introduction
Oxyanions such as CrO42−, TeO42−, and AsO43− are soluble in water and very harmful to human health as well as natural environments due to their carcinogenic and mutagenic properties.1 Highly efficient adsorbents of toxic oxyanions are strongly required for minimizing pollution and preventing health hazards. Layered double hydroxides (LDHs) are efficient adsorbents for toxic oxyanions owing to their high anion adsorption capacity and reusability.2 LDHs are crystalline lamella compounds composed of positively charged hydroxide sheets with accommodating anions in their interlayers. The general formula of M(II)–M(III) type LDH is [M(II)1−xM(III)x(OH)2]x+[An−x/n]x−·zH2O, where M(II) and M(III) are di- and trivalent metal cations, respectively, An− is the charge compensating anion, and x has a nominal value of 0.2–0.4.3,4 Oxyanions are known to be adsorbed onto sites located at the crystal edges of LDHs. These adsorption sites are called “microcages” and their adsorption property is highly sensitive to their relative sizes to oxyanions.5 Hence, controlling the microcage size leads LDH to be an effective adsorbent with selectivity of oxyanions.
While LDHs are generally obtained as crystalline powders,4 monolithic LDH materials are potential candidates for large-scale adsorption applications. A monolithic shape enables the materials to be handled more easily, which removes a time-consuming separation/collection process required for powdery LDH adsorbents. Porous, especially hierarchically (μm- and nm-scale) porous, monolithic LDH materials are highly desirable because μm-scale macropores enhance molecule/ion transport deep inside the materials, while nm-scale mesopores increase the accessible surface area. Thus, hierarchically porous monolithic LDH materials are expected to be viable candidates for effective, selective and large-scale toxic oxyanion removal. However, the formation of controlled hierarchical pores is difficult for LDHs due to rapid crystallization kinetics.
We have recently succeeded in synthesizing monolithic Mg–Al type LDH/Al(OH)3 composites with size controllable μm and nm-scale hierarchical pores.6,7 These monolithic Mg–Al type LDH composites were fabricated from an aqueous/ethanolic solution of metal salts, poly(ethylene oxide) (PEO), and propylene oxide (PO). PO raises pH of the solution homogeneously, which promotes the formation of gel networks comprising Mg–Al type LDH crystals and amorphous Al(OH)3. Simultaneously, phase separation takes place to form a PEO-rich fluid phase and a Mg–Al type LDH/Al(OH)3-rich solid phase along with the sol–gel transition. Subsequent removal of the fluid phase leaves μm and nm-scale hierarchical pores in the materials. These hierarchically porous monolithic Mg–Al type LDH composites exhibited a considerably high adsorption capacity compared with that of a densely-packed LDH compact. The adsorption kinetics/capacity were controllable by the tuning of the macro/mesopore dimensions. Such monolithic LDH composites with tailored hierarchical pores are useful to fully take advantage of their surface chemistry in application. Thus, hierarchically porous monolithic LDH composites with size-controlled microcages should be the best candidates for an oxyanion removal.
Herein, we successfully control the microcage size of macro/meso hierarchically porous monolithic LDH composites, by substituting the M(II) of the LDH crystals. The choice of M(II) and M(II)/M(III) molar ratio considerably affects both LDH crystallization and the formation of macro/mesopore. We systematically investigated the effect of the synthetic conditions on LDH crystallization and formation of hierarchical pores using M(II)–Al type LDH (M(II) = Mg, Mn, Fe, Co, Ni, Cu, Zn and Ca). The hierarchically porous monolithic LDH composites showed adsorption capacities for pollutant oxyanion CrO42− as a function of their microcage dimensions. Also Co–Al type LDH composite adsorbed SO42−, CrO42−, MoO42− and HVO42− from a solution of their mixture depending on their affinity for the adsorption sites on the LDH. Optimization of the microcage size of hierarchically porous LDH composites will open up possibility of further application, such as rapid pollutant removal with size selectivity.
Experimental section
Materials
Aluminium chloride hexahydrate (AlCl3·6H2O, 98.0%), magnesium chloride hexahydrate (MgCl2·6H2O, 98.0%), manganese(II) chloride tetrahydrate (MnCl2·4H2O, 99.0%), iron(II) chloride tetrahydrate (FeCl2·4H2O, 99.0–102.0%), cobalt chloride hexahydrate (CoCl2·6H2O, 99.0%), nickel chloride hexahydrate (NiCl2·6H2O, 98.0%), copper chloride dihydrate (CuCl2·2H2O, 99.0%), zinc chloride (ZnCl2, 98.0%), calcium chloride dihydrate (CaCl2·2H2O, 99.0–103.0%), sulfuric acid (H2SO4, 95%), potassium chromate (K2CrO4, 99%), sodium molybdate dihydrate (Na2MoO4·2H2O, 99%), sodium vanadate (Na3VO4, 75%), ethanol (99.5%), PEO (Mw = 1.0 × 106), PO (>99%), and 2-propanol (99.7%) were used as received. PEO and PO were purchased from Sigma-Aldrich Co. All other reagents were purchased from Wako Pure Chemical Industries, Ltd. Ultrapure water of 18.2 MΩ cm resistivity was used in all experiments.
Preparation of hierarchically porous monolithic LDH composites
Hierarchically porous monolithic LDH composites were synthesized by our previously reported procedure for the Mg–Al type LDHs.6,7 AlCl3·6H2O, MCl2·nH2O (M = Mg, Mn, Fe, Co, Ni, Cu, Zn and Ca; n = 0–6) and PEO (30.0 mg) were dissolved in water/ethanol (4.00/3.00 mL) at 25 °C. The total metal cation amount was 11.5 mmol, and the molar ratio of cations, M(II)/Al, is 0.1–3.0. PO (2.27 mL, 32.5 mmol) was added, and the resulting solution was stirred for 1 min to obtain a homogenous sol. The sol was transferred to a polystyrene container, which was sealed and left to stand at 40 °C to form a wet gel. After aging for 24 h, the wet gel was soaked in 50 mL of 2-propanol, and subjected to solvent exchange eight times at 40 °C. Monolithic materials were obtained by evaporative drying at 40 °C.
Adsorption test
Mg–, Mn–, Fe–, Co– and Ni–Al type LDH monolithic composites, prepared at M(II)/Al = 0.5, were used as adsorbents. Monolithic LDH composites (4 g L−1) were soaked in a 1.0 mmol L−1 solution of K2CrO4 at 40 °C. The supernatants were collected after 12 h and analysed by ultraviolet-visible (UV-vis) absorption spectroscopy. The concentration of CrO42− oxyanion in the solutions was estimated using the Beer–Lambert law. The adsorption test was also conducted for an aqueous solution containing various oxyanions using Co–Al type LDH monolithic composite. The Co–Al type LDH composite (4 g L−1) was soaked in a solution containing 2.5 mmol L−1 of H2SO4, K2CrO4, Na2MoO4·2H2O and Na3VO4 at 40 °C. The supernatants were collected after 18 h and the concentrations of respective oxyanions were determined by inductively coupled plasma emission spectroscopy (ICP: ICPS-8000, Shimadzu Corp.).
Characterization
Field emission scanning electron microscopy (FE-SEM; S-4800, Hitachi, Japan) was used to observe the morphologies of the obtained monolithic materials. X-ray diffraction (XRD) using CuKα radiation (λ = 0.154 nm) on a Rigaku diffractometer (MultiFlex) was used to characterize crystal phases. The mesoporous characteristics of monolithic materials calcined at 500 °C were analysed by N2 sorption measurements (Belsorp-mini II, Bel Japan Inc., Japan). Prior to N2 sorption measurements, samples were outgassed under vacuum at 200 °C. The specific surface area was estimated according to the Brunauer–Emmett–Teller method, and the pore size distribution was calculated using the Barrett–Joyner–Halenda method. UV-vis absorption spectroscopy was used to measure the absorbance intensity of CrO42−. The concentrations of CrO42− in the solutions were estimated from the Beer–Lambert law, using the peak intensities observed at 372.5 nm. ICP was used to determine concentrations of SO42−, CrO42−, MoO42− and HVO42− oxyanions after the adsorption test.
Results and discussion
A typical example of XRD pattern of the obtained materials is shown in Fig. 1(a). All the diffraction peaks could be assigned to hydrotalcite type LDHs. Considering the formation mechanism of monolithic material previously reported,6,7 the obtained material is a composite of LDH crystal and amorphous Al(OH)3. The LDH composite was obtained as a cm-scale monolithic shape (inset of Fig. 1(a)). The microcage size of the LDH crystal was estimated to be 495 pm (see ESI, Fig. S1†). Macropores (∼1 μm) and mesopores (∼10 nm) were observed in the monolithic composites by using scanning electron microscopy (SEM) and N2 adsorption/desorption measurement, respectively (Fig. 1(b) and (b) inset). An ethanol–water mixture containing di- and trivalent metal chlorides and PEO was used as a starting solution. The solution pH was rapidly increased by PO addition, because PO scavenges protons from the solution.8 The pH increase induced formation of Al(OH)3 and LDH and eventually led gelation. Before completion of the sol–gel transition, phase separation took place to form a LDH/Al(OH)3 rich solid phase and a PEO rich fluid phase if the compatibility between LDH/Al(OH)3 and PEO became low enough in the course of the pH increase.6,7 The fluid phase can be removed after gelation by drying, that leaves macropores (Fig. 1(b)). The LDH/Al(OH)3 skeletons have meso-scale voids inside them (Fig. S2†). The mesoporosity of the obtained monolithic composites is derived from these textural pores.
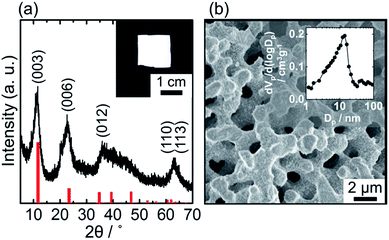 |
| Fig. 1 (a) XRD pattern and optical image (inset), (b) SEM image and mesopore size distribution (inset) of hierarchically porous monolithic LDH composite prepared with Mg/Al = 0.5. Red diffraction lines in (a): Mg4Al2(OH)12CO3(H2O)3 (JCPDS card no. 70-2151). Dp: pore diameter, Vp: pore volume. | |
Hierarchically porous monolithic LDH composites were obtained from the Mg–, Mn–, Fe–, Co– and Ni–Al systems. As well as the selection of M(II), the M(II)/Al molar ratio was found to be an important parameter to obtain LDH crystal phase and hierarchically porous structure. First, the Mg–Al system is discussed to clarify the effect of the M(II)/Al molar ratio of the precursor solution on hierarchical pore formation and LDH crystallization.
Hierarchically porous monolithic Mg–Al type LDH composites
Fig. 2 shows XRD patterns of monolithic composites prepared with various Mg/Al molar ratios. In the case of Mg/Al = 0.1, the monolithic composite was amorphous (black lines in Fig. 2). The same results were obtained for Mg/Al < 0.3. LDH single phase was obtained within the composition range, 0.3 ≤ Mg/Al ≤ 2.0 (Mg/Al = 0.8 and 1.5 are plotted in Fig. 2). For Mg/Al > 2.0, Mg(OH)2 phase was also formed (Mg/Al = 3.0 is shown in Fig. 2 as blue line). These results indicate that all of the monolithic composites prepared at 0.3 ≤ Mg/Al ≤ 3.0 include hydrotalcite type LDH crystals possessing microcages (Fig. S3†). The addition of PO to the metal salt precursor solution induced a rapid pH increase for all Mg/Al values (Fig. S4†). On the other hand, the final pH of the precursor solution depended on the Mg/Al molar ratio. The final pH affects the crystal phase of the obtained materials; considering the solubility products of the metal hydroxides,9 Al(OH)3 is formed at pH ∼ 3 and Mg–Al type LDH and Mg(OH)2 nucleate at higher value (pH > 4). LDH crystallization behaviour thus depends on the Mg/Al molar ratio of the starting mixture.
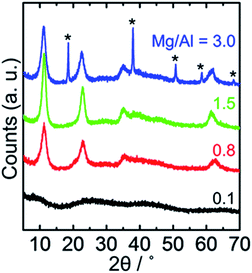 |
| Fig. 2 XRD patterns of monolithic composites prepared with various Mg/Al ratios. *: Mg(OH)2. | |
The meso- and macropores were evaluated using N2 adsorption/desorption measurements and SEM. The N2 measurements indicated that all of the prepared monolithic LDH composites (0.3 ≤ Mg/Al ≤ 3.0) have pores in meso-scale (typical example is shown in Fig. 1(b) inset). Fig. 3 shows cross-sectional SEM images of obtained monolithic composites. Isolated pores were confirmed in Mg/Al < 0.3 (Fig. 3(a)). Interconnected macropores, which were controllable between 0.5 and 5 μm in diameter, were observed in the monolithic composites with 0.3 ≤ Mg/Al ≤ 1.0 (Fig. 3(b)). Aggregated particles were observed in Mg/Al > 1.0 (Fig. 3(c)). The pore diameter became coarser with increasing Mg/Al molar ratio. However, when Mg/Al values beyond 1.0, that is the threshold of the formation of porous monolithic composites, the products were composed of aggregated powder. The morphologies of the obtained structures depended on the progress of phase separation before solidification. A coarser pore was formed when the phase separation was terminated at a later stage by the sol–gel transition.10 Increasing the Mg/Al ratio decreased the compatibility between LDH/Al(OH)3 and PEO, and accelerated phase separation relative to solidification. In summary, both hierarchical pore formation and LDH crystallization (microcage formation) are determined according to the M(II)/Al molar ratio of precursor solution.
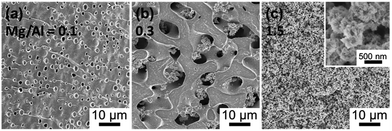 |
| Fig. 3 SEM images of fractured surfaces of the monolithic composites, prepared with various Mg/Al ratios; (a) 0.1 (isolated pores), (b) 0.3 (interconnected pores) and (c) 1.5 (aggregated particles) (inset shows magnified image). | |
Hierarchically porous monolithic M(II)–Al type LDH composites (M(II) = Mn, Fe, Co, Ni, Cu, Zn and Ca)
Mg as M(II) was substituted with Mn, Fe, Co, Ni, Cu, Zn and Ca to prepare LDHs with variety of microcage sizes. Fig. 4 shows the microcage sizes of M(II)–Al type LDHs (M(II)/Al = 0.5). The microcage size decreased with increasing ionic radius of M(II) species, except for Mn. The result is in good agreement with a reported study which demonstrated that LDHs composed of larger cations have smaller microcage sizes.5 The reason for the deviation of Mn from the trend is not clear. Thus, fine control of microcage size is accomplished by changing the M(II) metal cation of LDH.
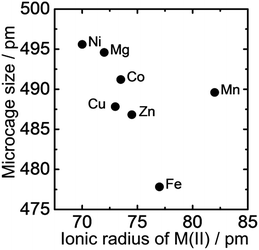 |
| Fig. 4 Relationship between microcage size of M(II)–Al type LDH crystals (prepared with M(II)/Al = 0.5) and ionic radii of the corresponding M(II) cations.15 | |
Fig. 5 shows the M(II)/Al molar ratio ranges to achieve LDH crystallization and the formation of hierarchical pores for various M(II)–Al combinations. LDH crystals were obtained at specific M(II)/Al molar ratio ranges for all M(II) except for Ca. The relationship between the minimum M(II)/Al molar ratio required for LDH crystallization, Mmin, and solubility product of M(OH)2, Ksp, is shown in Fig. 5 inset. A divalent metal cation that forms a hydroxide of a lower solubility product produces corresponding LDHs at a lower pH.9 Because the pH value was lower at a lower M(II)/Al molar ratio (see Fig. S4†), Mmin decreased with the solubility product of M(OH)2. On the other hand, the maximum molar ratio for the LDH crystallization depended on the formation of impurity divalent metal compound phases. Metal chloride hydroxide formed along with LDH in the case of the Co–, Zn– and Cu–Al systems. Mg(OH)2 and Mn2O3 formed along with LDH in the Mg– and Mn–Al systems, respectively. In the Ca–Al system, only CaCl2 formed in the entire molar ratio range. The pH value of the reaction system could not reach the pH value required for Ca–Al type LDH crystallization (pH = 10.5–13).
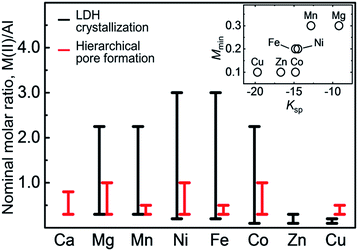 |
| Fig. 5 Nominal molar ratio ranges at which interconnected pores (black) and LDH (red) were achieved for the different M(II)–Al systems. Inset: relationship between the minimum M(II)/Al molar ratio, Mmin, for LDH formation, and solubility product, Ksp, of M(OH)2 (M = Mg, Mn, Fe, Co, Ni, Cu, and Zn).16 | |
The formation of hierarchical pores also depended on the choice of the M(II) cation (Fig. 5). In the case of the Mg–, Co–, and Ni–Al systems, monolithic LDH composites had hierarchical pores in relatively wide compositional range, M(II)/Al = 0.3–1.0. In contrast, the molar ratio range was relatively narrow (M(II)/Al = 0.3–0.5) for the Mn–, Fe–, and Cu–Al systems. A critical factor that influences on the macropore formation is secondary particle size. In the case of the latter three systems, secondary particles over several hundred nm were observed when M(II)/Al value increased. Large particles of a size comparable to the phase separated macrostructures (0.5–5 μm) disturbed phase separation and limited the compositional range of hierarchical pore formation. Although large secondary particles were not observed in the Zn–Al system, only isolated pore formed. The formation of Zn–Al type LDH might have few effects on the accelerating phase separation, and solidification may have occurred before the phase separated structure developed. We achieved hierarchically porous monolithic LDH composites with finely controlled microcage size from 478 to 496 pm (Table 1).
Table 1 Macropore, mesopore, and microcage characteristics and crystallite sizes of Mg–, Mn–, Fe–, Co–, and Ni–Al type LDH monolithic composites
LDH type |
dmacroa/μm |
dmesob/nm |
SBETc/m2 g−1 |
Vmesod/cm3 g−1 |
dmicroe/pm |
D003f/nm |
Macropore diameter estimated from SEM images. Mesopore diameter evaluated by N2 sorption measurements. Specific surface area evaluated by N2 sorption measurements. Mesopore volume evaluated by N2 sorption measurements. Microcage size calculated from (003) lattice spacing and hydroxide sheet thickness. Crystallite size estimated by the Scherrer equation from (003) reflection of the XRD pattern. |
Mg–Al |
1.26 |
11.6 |
293 |
0.49 |
495 |
3.62 |
Mn–Al |
1.41 |
18.4 |
244 |
0.84 |
490 |
15.9 |
Fe–Al |
0.74 |
24.7 |
171 |
0.66 |
478 |
14.3 |
Co–Al |
1.44 |
11.4 |
175 |
0.32 |
491 |
4.21 |
Ni–Al |
1.47 |
6.5 |
314 |
0.33 |
496 |
3.41 |
Oxyanion adsorption
It is expected that LDHs with optimized microcages will be useful for a selective oxyanion adsorption because the oxyanion adsorption ability depends on the size of its microcage.5 In this study, monolithic LDH composites were examined as a water decontaminating agent for removing CrO42−, which is one of the toxic oxyanions in industrial waste water.11 The macropore, mesopore, and microcage characteristics and the crystallite size of M(II)–Al type LDH monolithic adsorbents are shown in Table 1 (M(II) = Mg, Mn, Fe, Co, and Ni). These monolithic adsorbents had hierarchical pores in discrete scales. Mesopore size (specific surface area),12 microcage size,5 and crystallite size13 are anticipated to affect adsorption capacity. On the other hand, macropore size of porous monolithic LDH composite does not affect adsorption capacity.7 Fig. 6(a) shows the relationship between the adsorbed amount of CrO42− and the microcage sizes of monolithic M(II)–Al type LDH adsorbents. The adsorption was maximized in the case of Co–Al type LDH composite. However, the amount of CrO42− adsorption did not correlate with the specific surface area or crystallite size of the composites (Fig. S5†). Instead, the differences in adsorption amount can be explained by the microcage size. The microcage size of the Co–Al type LDH composite was 491 pm, which is comparable to the size of CrO42− (480 pm (ref. 14)). Thus, changing the M(II) metal cation in hierarchically porous monolithic LDH composites allowed the fine tuning of microcage size to a target adsorbent.
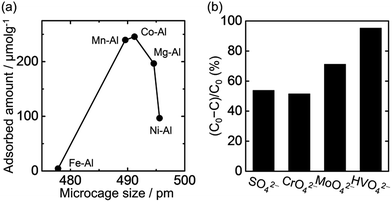 |
| Fig. 6 (a) Amount of CrO42− adsorbed by hierarchically porous monolithic M(II)–Al type LDH composites (M(II) = Mg, Mn, Fe, Co, Ni) having different microcage size. (b) The fractions of oxyanions removed from an aqueous solution containing four oxyanions, (C0 − C)/C0, by Co–Al type LDH. C0 is initial concentration (2.5 mmol L−1). C is concentration after 18 h adsorption. | |
Fig. 6(b) shows the fractions of oxyanions removed by Co–Al type LDH composite, (C0 − C)/C0, from an aqueous solution containing four different oxyanions; C0 and C are the initial and the final molar concentrations of an oxyanion in the solution, respectively. The four oxyanions have different sizes: SO42− (460 pm), CrO42− (480 pm), MoO42− (492 pm) and HVO42− (520 pm).14 The adsorption occurs preferentially in the order of CrO42− ≈ SO42− < MoO42− < HVO42−, and not correlated with the degree of size-matching between microcage and oxyanions. The oxyanion adsorption accompanies exchange of OH groups with oxyanions at Al sites,17 and therefore, the affinity between oxyanions and the binding sites also affects adsorption characteristics, so-called a screening effect, as well as microcage size. The trend of sorption competition observed in the present study is consistent with a previous report on powdery LDHs,18 confirming that the present LDHs with controlled hierarchical structures possess a distinctive adsorption property of LDHs. Thus obtained LDHs with hierarchical structures in pm, nm, μm, cm scale will find applications, such as rapid and easy-handling pollutant removal with a rational ion selectivity.
Conclusions
The monolithic Mg–Al type LDH composites with macropores, mesopores and microcages were synthesized via an epoxide-mediated sol–gel reaction within a specific molar ratio range (Mg/Al = 0.3–1.0). Through systematic experiments, hierarchically porous monolithic M(II)–Al type LDH composites were also obtained (M(II) = Mn, Fe, Co and Ni). Tuning of microcage size was accomplished by changing a combination of metal cations of LDHs, which led to high adsorption capacity for CrO42−. Hierarchically porous monolithic LDH composites with various microcage sizes can be fabricated based on knowledge of this study, and are expected to be useful for specific toxic oxyanion removal.
Acknowledgements
The study was supported by JSPS KAKENHI (no. 26288108, 26630322). This work is partially supported by the Kazuchika Okura Memorial Foundation and the Hosokawa Powder Technology Foundation. Strategic Young Researcher Overseas Visits Program for Accelerating Brain Circulation from JSPS is gratefully acknowledged.
Notes and references
- A. Léonard and R. R. Lauwerys, Mutat. Res., 1980, 76, 227 Search PubMed.
- K. Goh, T. Lim and Z. Dong, Water Res., 2008, 42, 1343 CrossRef CAS PubMed.
- G. Brown and M. C. Gastuche, Clay Miner., 1967, 7, 193 CAS.
- G. W. Brindley and S. Kikkawa, Am. Mineral., 1979, 64, 836 CAS.
- Y. Wang and H. Gao, J. Colloid Interface Sci., 2006, 301, 19 CrossRef CAS PubMed.
- Y. Tokudome, N. Tarutani, K. Nakanishi and M. Takahashi, J. Mater. Chem. A, 2013, 1, 7702 CAS.
- N. Tarutani, Y. Tokudome, K. Nakanishi and M. Takahashi, RSC Adv., 2014, 4, 16075 RSC.
- A. E. Gash, T. M. Tillotson, J. H. Satcher Jr, J. F. Poco, L. W. Hrubesh and R. L. Simpson, Chem. Mater., 2001, 13, 999 CrossRef CAS.
- J. W. Boclair and P. S. Braterman, Chem. Mater., 1999, 11, 298 CrossRef CAS.
- K. Nakanishi, J. Porous Mater., 1997, 4, 67 CrossRef CAS.
- C. Françoise and A. C. M. B. Richard, Wat. Res., 1991, 25, 807 CrossRef.
- J. Inacio, C. Taviot-Guého, C. Forano and J. P. Besse, Appl. Clay Sci., 2001, 18, 255 CrossRef CAS.
- T. Hongo, M. Takahashi and A. Yamazaki, Chem. Lett., 2006, 35, 1296 CrossRef CAS.
- K.-H. Goh, T.-T. Lim and Z. Dong, Water Res., 2008, 42, 1343 CrossRef CAS PubMed.
- D. A. Sverjensky and P. A. Molling, Nature, 1992, 356, 231 CrossRef CAS PubMed.
- H. Einaga, in Inorganic synthesis via liquid phase method (printed in Japanese), Baifukan, Tokyo, 2000, pp. 103–106 Search PubMed.
- K.-H. Goh, T.-T. Lim and Z. Dong, Environ. Sci. Technol., 2009, 43, 2537 CrossRef CAS.
- K.-H. Goh and T.-T. Lim, J. Hazard. Mater., 2010, 180, 401 CrossRef CAS PubMed.
Footnote |
† Electronic supplementary information (ESI) available. See DOI: 10.1039/c5ra05942a |
|
This journal is © The Royal Society of Chemistry 2015 |
Click here to see how this site uses Cookies. View our privacy policy here.