DOI:
10.1039/C5RA05595D
(Paper)
RSC Adv., 2015,
5, 56020-56027
Water-mediated promotion of direct oxidation of benzene over the metal–organic framework HKUST-1
Received
30th March 2015
, Accepted 19th June 2015
First published on 19th June 2015
Abstract
Pretreatment of a HKUST-1 catalyst with water significantly accelerated the catalytic oxidation of benzene to phenol and hydroquinone with hydrogen peroxide as an oxidant. The corresponding oxygenates had a yield of 36.5%, and the selectivity to phenol and hydroquinone was 53.2% and 35.5%, respectively. The turnover frequency (TOF) was 35.1 h−1. Comparatively, the product yield was only 2.7% over the original HKUST-1, and the TOF was 2.6 h−1. Moreover, water treatment protected HKUST-1 from decomposition due to formation of a new oxidation mode. Therefore, the catalytic system in the presence of water opened a new door towards a facile and efficient preparation of phenol and hydroquinone.
Introduction
Oxidation of unsaturated C–C bonds in benzene is crucial for synthesis of chemical intermediates in organic chemistry. Nevertheless, it is usually difficult to obtain benzene oxygenates from benzene, because the activating energy of C–H in a benzene ring is 111 kcal mol−1, higher than those in most alkanes (90–101 kcal mol−1) and even higher than that in methane (105 kcal mol−1).1 One-step synthesis of benzene oxygenates with H2O2 or molecular oxygen as green oxidants is a great challenge in modern synthetic chemistry.2 For such purposes, great efforts have been devoted to develop suitable oxidation catalysts. Currently, both homogeneous and heterogeneous catalysts have been extensively investigated, such as Fe2+, Cu2+, Mn2+ or V2+ complexes,3 metal-incorporated molecular sieves,4,5 and carbon-based materials.6 Among of them, copper-based catalysts have shown a high catalytic activity.7 Up to now, it has been still attractive to develop a highly efficient and green catalytic route to prepare benzene oxygenates from easily available benzene.
Metal–organic frameworks (MOFs)8–13 are compounds consisting of metal ions coordinated to organic ligands such as aromatic substances and derivatives,14 or nitrogen heterocyclic compounds15 to form one-, two-, or three-dimensional structures. Compared to conventionally used catalysts, MOFs have large surface area,16 high thermal and chemical stability,17 as well as diverse skeleton structures obtained by modulating the functional architecture of the metal ions and the organic ligands.18 Therefore, MOFs have been reported as catalysts or catalyst supports in many catalytic reactions such as oxidation,19 hydrogenation,20 Knoevenagel condensation,21 Suzuki cross-coupling,22 transesterification reaction,23 catalytic cracking24 and aldolcondensation.25
According to the reports, copper-based metal–organic framework HKUST-1 has been employed as a heterogeneous catalyst or catalyst support in many reactions such as oxidation, epoxidation, hydroxylation, condensation and esterification.26 It has a 3D square-shaped porous structure (9 × 9 Å). Commonly, it was also referred to MOF-199 or [Cu3(BTC)2], where BTC represents benzene-1,3,5-tricarboxylate. A monomeric unit of the material contains a dicopper cluster with a copper–copper distance of 2.63 Å, in which each copper atom is coordinated by four oxygen atoms from the four BTC linkers, and each BTC binds to three different Cu2+ ions.27 Thus, the coordinative vacancy on Cu2+ species occurs naturally in the face-centered crystal lattice of HKUST-1.28 In this research, original HKUST-1 hardly showed catalytic activity in oxidation of benzene with H2O2 as an oxidant in MeCN within 30 min. Interestingly, water pretreated HKUST-1 displayed a highly catalytic oxidation activity in the reaction under the same reaction conditions, suggesting that water treatment of this material played an important role in promoting the catalytic activity. Moreover, the absorbed water avoided direct exposure of the active sites on HKUST-1 to H2O2 and protected the catalyst from being damaged in the oxidation of benzene. Therefore, the water involved catalytic system opens a green and economical door towards facile oxidation of benzene to its corresponding oxygenates.
Experimental
Materials
Acetonitrile (MeCN, HPLC grade) was acquired from Merck company. The analytical grade solvents of N,N-dimethylformamide (DMF), ethanol (EtOH), methanol (MeOH), acetone, chlorobenzene and triethylamine were obtained from Sinopharm Chemical Reagent Co. Ltd. Cupric acetate (Cu(OAc)2·H2O) was purchased from Tianjin Damao Chemical Reagent Factory and BTC was purchased from Sun Chemical Technology (Shanghai) Co., Ltd. All materials were used without further purification.
Synthesis of HKUST-1
HKUST-1 was prepared according to ref. 29. Firstly, a mixture consisting of DMF, EtOH and H2O was prepared with a volume ratio of 1
:
1
:
1. Cu(OAc)2·H2O (1720 mg, 8.62 mmol) was dissolved in 24 mL of the above mixture solvent under ultrasonic vibration, in which BTC (1000 mg, 4.76 mmol) in 24 mL of the same mixture solvent was dropped with a rate of 0.2 mL min−1 under vigorous stirring, followed by adding triethylamine (1.0 mL) and stirring at 25 °C for 23 h. The precipitate was separated by vacuum filtration and washed with DMF. Afterwards, the solid was dispersed in 100 mL of CH2Cl2 overnight, then separated by vacuum filtration and washed with CH2Cl2. The product was dried at 170 °C for 6 h under vacuum.
Characterization
Fourier transform infrared (FTIR) spectra was collected on a Bruker FT-IR Tensor 27 using KBr pellets. Quantification of C, H, and N was performed on an Elementar Vario Micro cube elemental analyzer. Powder X-ray diffraction (XRD) was performed on Rigaku D-Max with 40 kV and Cu-Kα radiation. Thermal gravimetric analyses (TGA) were obtained by a TA Q600 thermal analysis system with ∼6 mg of sample in each test. The tests were carried out under a continuous nitrogen flow with a heating rate of 10 °C min−1. Surface areas and pore sizes of the samples were assessed via nitrogen physisorption analysis using Quantachrome Autosorb-1. Sample morphologies were observed by scanning electron microscope (SEM) on a Hitachi S4800 with an accelerating voltage 3.0 kV. Raman spectra were collected on a Renishaw in Via Raman microscope with 514.5 nm laser excitation at room temperature and taken with a 20× microscope objective at 2 mW laser power on the sample. HKUST-1 (7.2 mg) was dispersed in 1 mL of ultra-purified water (an electrical resistance of 18.2 MΩ cm) for 2 h under ultrasonic of 200 W. Benzene (0.15 mL) was added in the heterogeneous system for a while. The obtained heterogeneous mixture was dropped on the slide for Raman scattering spectrum. Raman spectra were collected from the resulting heterogeneous mixture with an integration time of 2 min for each scattering.
Oxidation of benzene
Firstly, HKUST-1 (140 mg, 0.23 mmol) was immersed in H2O (20 mL) under ultrasonic of 200 W for different times and separated by centrifugation. All the water treated HKUST-1 samples were denoted as HKUST-1 (H2O)-time. The wet samples were directly used as catalysts for the oxidation of benzene. In a typical reaction, 140 mg of catalyst was placed into a 50 mL two-necked flask with a reflux condenser of ice water. And then, 5 mL of MeCN, 1 mL (11.2 mmol) of benzene and 3 mL of H2O2 (30 wt%) were added into the flask. The mixture reacted for 0.5 h at 60 °C in a water bath. After the reaction, hydrogen peroxide in the mixture was detected with starch potassium iodide paper. The products were analyzed by a gas chromatograph Agilent 6890 equipped with 30 m of Innowax column and flame ionization detector (FID). Chlorobenzene was used as internal standard.
Results and discussion
The FT-IR spectra of BTC and HKUST-1 were shown in Fig. 1. The bands at 1607 and 1454 cm−1 in Fig. 1a are associated with the C–C skeletal vibration of benzene while the bands at 3086 and 3003 cm−1 are attributed to the stretching mode of
C–H in benzene ring. The bands at 1722, 1193, and 919 cm−1 are assigned to the C
O stretching, C–O stretching and out-of-plane O–H bending vibration frequencies, respectively, indicating the presence of a carboxylic acid group.30 The broad band in the region of 3200–2500 cm−1 is due to formation of hydrogen bond among the carboxylic acid groups. Compared to BTC (Fig. 1a), a significant difference for HKUST-1 (Fig. 1b) is that the asymmetric stretch of O
C–O at 1632 cm−1 and the symmetric modes at 1374 cm−1 can be observed, which confirmed the deprotonation of –COOH groups in BTC upon the reaction with copper metal ions.30,31 In addition, the band around 760 cm−1 is attributed to Cu substituted groups in benzene and the weak band at 1110 cm−1 is due to C–O–Cu stretching.32 The FT-IR analysis of HKUST-1: IR (KBr pellet cm−1) 3444 (br), 1632 (s), 1582 (m), 1444 (m), 1374 (s), 1110 (w), 1060 (w), 938 (w), 760 (m), 729 (m), 665 (w), 589 (w), 489 (w), the results are consistent with the literature.33 It is an indicative of the HKUST-1 structure. In addition, the percentage contents of C, H and N in HKUST-1 were 35.25, 1.29, and 0.02%, respectively. The result fits with anal. calcd for HKUST-1 ([Cu3(BTC)2]): C, 35.64; H, 0.99; N, 0%.33
 |
| Fig. 1 FTIR spectra of samples. (a) BTC, (b) HKUST-1. | |
XRD patterns of the samples are displayed in Fig. 2. The XRD pattern of the as-synthesized HKUST-1 was in good agreement with the simulated one, as shown in Fig. 2a and b, indicating a high purity of the sample. Fig. 2c–f display the XRD patterns of HKUST-1 samples treated with water for different times. It can be found that the crystalline phase apparently changed due to a possible hydration of HKUST-1. However, among the water treated samples, the diffraction peak position and peak numbers of HKUST-1 (H2O)-1 h, HKUST-1 (H2O)-2 h and HKUST-1 (H2O)-3 h were totally similar revealing the same crystalline phase (Fig. 2d–f). Surprisingly, the initial crystalline phase of HKUST-1 was recovered after the catalytic oxidation of benzene, despite of slight difference in some peak intensities by comparing Fig. 2b–g. The intensities of the (200) and (220) crystal planes was changed relatively due to preferred orientation of the crystallites.
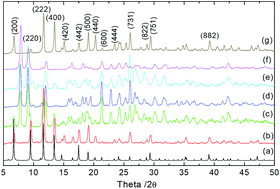 |
| Fig. 2 XRD patterns of the samples, (a) simulated from the crystallographic data of HKUST-1 (ref. 28), (b) as-synthesized HKUST-1, (c) HKUST-1 (H2O)-5 min, (d) HKUST-1 (H2O)-1 h, (e) HKUST-1 (H2O)-2 h, (f) HKUST-1 (H2O)-3 h, (g) HKUST-1 (H2O) after catalytic reaction. | |
The as-synthesized HKUST-1 crystals had a needle-like morphology with a diameter of ∼5 nm, as shown in Fig. 3a. Comparatively, most of the reported HKUST-1 crystals were octahedral with a size of 15 μm.34 Besides the crystalline phase, water treatment also changed the morphology evidenced in Fig. 3. The HKUST-1 (H2O)-5 min looked like rods with a length of over 10 μm (Fig. 3b). Nevertheless, the rod-like morphology gradually transformed to tablets, and the crystal size gradually decreased with an increase of the water treatment time (Fig. 3c–e). The HKUST-1 (H2O)-1, HKUST-1 (H2O)-2 h and HKUST-1 (H2O)-3 h were less than 5 μm. The samples were blue as seen from the digital photo in Fig. 3f. The appearance of HKUST-1 suspended in water changed gradually with the water treatment time. Fig. 3f-2 and f-3 showed a relatively homogeneous dispersion of small granules in water. However, the granule size would increase and precipitate due to possible adsorption more water (Fig. 3f-4 and f-5).
 |
| Fig. 3 SEM images of HKUST-1 and HKUST-1 (H2O), (a) HKUST-1, (b) HKUST-1 (H2O)-5 min, (c) HKUST-1 (H2O)-1 h, (d) HKUST-1 (H2O)-2 h, (e) HKUST-1 (H2O)-3 h. (f) Digital photo of HKUST-1 and HKUST-1 (H2O), (f-1) HKUST-1, (f-2) HKUST-1 (H2O)-5 min, (f-3) HKUST-1 (H2O)-1 h, (f-4) HKUST-1 (H2O)-2 h, (f-5) HKUST-1 (H2O)-3 h. | |
The thermal stabilities of the samples were evaluated by TGA, as shown in Fig. 4. The HKUST-1 was dried at 170 °C for 6 h under vacuum for TGA testing. The blue-violet HKUST-1 adsorbed moisture immediately and became deep blue when it was exposed to air. As seen in Fig. 4a, the first weight lost stage occurred between 25 °C and 150 °C with a weight loss of 20.0% for the inevitable air adsorption during TGA analysis. No significant weight loss was seen in the temperature range of 150 °C to 250 °C, indicating the thermal stability of HKUST-1. The second weight loss (48.3%) started from 250 °C to 420 °C, and the HKUST-1 structure totally collapsed at ∼420 °C as reported in literature.35,36 The process was accompanied by the release of CO2 due to the decomposition of carboxylic groups and the disintegration of the crystal structure,37 which led to the formation of Cu2O and CuO.35 Before TGA analysis, the wet samples of HKUST-1 (H2O) were exposed to air for around 2 h at ambient temperature to remove free water. Fig. 4b revealed two continuous weight loss peaks from 25 °C to 150 °C for the HKUST-1 (H2O)-5 min. The weight loss was 27.6% corresponding to the 13 water molecules per [Cu3(BTC)2(H2O)3] unit. The theoretical weight loss was 27.9%.28 Among them, 3 water molecules complexed with Cu atoms and directed to the interior of nanopores by the terminal axial water ligands, and others were disorder in the accessible pore volume.28 The similar TGA result was also observed for HKUST-1 (H2O)-1 h with a slight enhancement of weight loss by 5.3%. However, further prolonging the water treatment time, another two continuous weight loss peaks appeared from 120 °C to 250 °C for the HKUST-1 (H2O)-2 h and HKUST-1 (H2O)-3 h as well as two peaks occurred from 25 °C to 120 °C (Fig. 4d and e). The weight loss from 120 °C to 250 °C was 5.2% and 5.1% for the HKUST-1 (H2O)-2 h and HKUST-1 (H2O)-3 h, respectively. Fig. 4d and e were obviously different from Fig. 4b and c. It implied that some water molecules were possibly absorbed in the relatively small pores. We surmised that HKUST-1 (H2O)-2 h and HKUST-1 (H2O)-3 h had absorbed water completely, which was also judged from their appearance (Fig. 3f-4 and f-5).
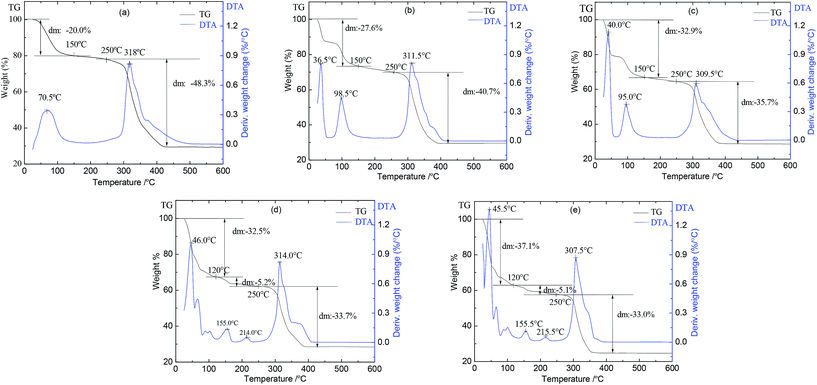 |
| Fig. 4 TGA and DTA of the samples. (a) HKUST-1, (b) HKUST-1 (H2O)-5 min, (c) HKUST-1 (H2O)-1 h, (d) HKUST-1 (H2O)-2 h, (e) HKUST-1 (H2O)-3 h. | |
The textural properties of HKUST-1 and HKUST-1 (H2O) were summarized in Table 1. After adsorption water, the HKUST-1 (H2O) had much lower BET surface area and pore volume compared to the HKUST-1 due to transformation of the crystal phase caused by water treatment. Fig. 4b–e revealed that the HKUST-1 (H2O) samples had more dense structure and larger size than those of HKUST-1 (Fig. 4a). We speculated that relatively small mesopores of HKUST-1 (H2O) disappeared or were wrapped in the interior of solid. The HKUST-1 (H2O) exhibited higher catalytic activities than the HKUST-1 in subsequent oxidation of benzene. Obviously, the adsorpted water on HKUST-1 played a significant role in the catalytic reactions.
Table 1 Surface area and pore volume analysis of HKUST-1 (H2O) and HKUST-1
Entry |
Sample |
BET surface area (cm2 g−1) |
Pore volume (cm3 g−1) |
Pore size (nm) |
1 |
HKUST-1 |
1095 |
1.05 |
173.0 |
2 |
HKUST-1 (H2O)-5 min |
5.67 |
0.05 |
26.77 |
3 |
HKUST-1 (H2O)-1 h |
18 |
0.08 |
26.78 |
4 |
HKUST-1 (H2O)-2 h |
20.04 |
0.12 |
23.98 |
5 |
HKUST-1 (H2O)-3 h |
25 |
0.14 |
23.97 |
Hydroxylation of benzene
In hydroxylation of benzene, MeCN was used as a solvent to disperse the catalyst in the mixture of water and benzene. Without catalyst, the blank run (Table 2, entry 1) did not produce the detectable products. For the original HKUST-1, the product yield was only 2.7%, and the corresponding TOF was 2.6 h−1 at 60 °C (Table 2, entry 2). In the catalytic reaction, the color of the mixture changed slightly, indirectly suggesting a very slow oxidation of benzene. Comparatively, when HKUST-1 (H2O)-2 h, water treated HKUST-1, was applied to the oxidation of benzene, the reaction mixtures changed into dark green in the first 4 min, then changed into brown immediately in 6–8 min, and then kept brown in the reaction, which revealed that the reaction proceeded very fast. The product yield was increased to 36.5%, the TOF was 35.1 h−1, and the selectivity of phenol was 53.2% (Table 2, entry 3). The effect of reaction temperature was also investigated over the HKUST-1 (H2O)-2 h. The yields were low as the temperature below 60 °C (Table 2, entries 4–6). Meanwhile, it can be found that the yield was rapidly decreased to 13.8% at 70 °C due to the rapid decomposition of H2O2, because we observed that a large number of bubbles violently generated in the reaction at 70 °C. After each reaction, starch potassium iodide paper was used to detect H2O2 left in the reaction mixture. However, no color change was observed on the starch potassium iodide paper, which meant that H2O2 was exhausted. Therefore, the optimum reaction temperature was ∼60 °C.
Table 2 Catalytic performance of HKUST-1 and HKUST-1 (H2O) in the oxidation of benzeneafgh
Entry |
Catalyst |
Selectivity of the oxygenates (%) |
Yield (%) |
TOF (h−1) |
PH |
BE |
CA |
HY |
PH = phenol, BE = benzoquinone, CA = catechol, HY = hydroquinone. The temperature of the water bath was 60 °C. The temperature of the water bath was 40 °C. The temperature of the water bath was 50 °C. The temperature of the water bath was 70 °C. TOF = mole of the oxygenates/(mole of HKUST-1 × reaction time). Selectivity = mole of some oxygenate/mole of all the oxygenates. Yield = mole of all the oxygenates/mole of benzene. |
1 |
None |
0 |
0 |
0 |
0 |
0 |
0 |
2 |
HKUST-1 |
36.0 |
61.9 |
0 |
2.1 |
2.7 |
2.6 |
3 |
HKUST-1 (H2O)b |
53.2 |
1.5 |
9.8 |
35.5 |
36.5 |
35.1 |
4 |
HKUST-1 (H2O)c |
43.1 |
43.1 |
2.4 |
11.4 |
12.6 |
13.5 |
5 |
HKUST-1 (H2O)d |
52.0 |
5.3 |
16.4 |
26.3 |
18.2 |
19.5 |
6 |
HKUST-1 (H2O)e |
56.9 |
2.8 |
14.2 |
26.1 |
13.8 |
14.8 |
7 |
HKUST-1 (H2O)-5 min |
41.5 |
38.7 |
0 |
19.8 |
7.5 |
7.4 |
8 |
HKUST-1 (H2O)-1 h |
77.0 |
5.2 |
0 |
17.8 |
9.5 |
9.3 |
9 |
HKUST-1 (H2O)-3 h |
53.1 |
2.3 |
7.8 |
36.8 |
35.8 |
34.9 |
10 |
HKUST-1 (dehydration) |
54.4 |
43.8 |
0 |
1.8 |
6.6 |
6.4 |
The catalytic performance of HKUST-1 (H2O) might be affected by the adsorption level of water. Inspired by this idea, the wet samples of HKUST-1 (H2O) with different water treating times were tested in the oxidation of benzene. Since the HKUST-1 (H2O)-2 h and HKUST-1 (H2O)-3 h had sufficiently adsorbed water (Fig. 4d and e), their catalytic activities were much higher than those of HKUST-1 (H2O)-5 min and HKUST-1 (H2O)-1 h (Table 2, entries 4 and 7–9). In other words, the water in the small pores as well as that in the big pores or on the surface of HKUST-1 played significant roles in enhancing the catalytic activity.
Meanwhile, ultrasonic treatment broke the HKUST-1 crystals and might increase the outside surface area, which was confirmed by some relative works. However, ultrasonic disruption was not the key factor for the enhancement of catalytic activities. When the wet broken HKUST-1 (H2O)-2 h was dewatered at 100 °C for 3 h under vacuum, the product yield was decreased to 6.6% from 36.5% for the wet HKUST-1 (H2O)-2 h (Table 2, entries 3 and 10). Hence, water played more significant role in the promotion of catalytic activity than the crystal size.
To further confirm that water promoted the reactivity of HKUST-1 in the hydroxylation of benzene, HKUST-1 (140 mg, 0.23 mmol) was treated with other solvents (DMF, EtOH, MeOH, MeCN and acetone) for 2 h. The obtained samples were named as HKUST-1 (solvent), where the solvent in the bracket referred to DMF, EtOH, MeOH, MeCN and acetone. Then the HKUST-1 (solvent) was also applied to the oxidation of benzene under the investigated conditions. However, these solvents treated HKUST-1 didn't significantly improve the yield compared with the HKUST-1, as shown in Table 3.
Table 3 Catalytic activity of the HKUST-1 pretreated by different solvents in the oxidation of benzenea
Entry |
Catalyst |
Selectivity of the oxygenates (%) |
Yield (%) |
TOF (h−1) |
PH |
BE |
CA |
HY |
Catalytic reaction conditions: 140 mg of HKUST-1 (solvent), 5 mL of MeCN, 1 mL of benzene (11.2 mmol) and 3 mL of 30 (wt)% H2O2 (29.4 mmol) were mixed and heated in a water bath at 60 °C for 0.5 h. |
1 |
HKUST-1 (H2O) |
53.2 |
1.5 |
9.8 |
35.5 |
36.5 |
35.1 |
2 |
HKUST-1 (DMF) |
79.8 |
20.2 |
0 |
0 |
1.2 |
1.1 |
3 |
HKUST-1 (EtOH) |
60.8 |
39.2 |
0 |
0 |
1.9 |
1.9 |
4 |
HKUST-1 (MeOH) |
63.0 |
37.0 |
0 |
0 |
1.3 |
1.2 |
5 |
HKUST-1 (MeCN) |
52.6 |
47.4 |
0 |
0 |
4.8 |
4.6 |
6 |
HKUST-1 (acetone) |
61.1 |
38.9 |
0 |
0 |
0.5 |
0.5 |
To study of the catalysts reusability, the HKUST-1 (H2O)-2 h and the HKUST-1 were reused three times in the oxidation of benzene under investigated conditions. The catalysts were washed with 3 × 5 mL of H2O after each reaction and reused. The results were listed in Table 4. It indicated that the catalyst HKUST-1 (H2O)-2 h could be reused for more than twice without mainly loss of activity. And for HKUST-1, when it was employed a second time in the reaction, a slight improvement in activity was observed. This enhancement in activity could probably be considered that the water contributed a lot in the activity of the catalyst HKUST-1 (Table 4).
Table 4 Reusability of the HKUST-1 (H2O) and HKUST-1 in the oxidation of benzenea
Recycle time |
Catalysts |
Selectivity of the oxygenates (%) |
Yield (%) |
TOF (h−1) |
PH |
BE |
CA |
HY |
Conditions: 140 mg of catalyst, 5 mL of MeCN, 1 mL of benzene (11.2 mmol) and 3 mL of 30 (wt)% H2O2, 60 °C, 0.5 h. |
1 |
HKUST-1 (H2O)-2 h |
53.2 |
1.5 |
9.8 |
35.5 |
36.5 |
35.1 |
2 |
46.9 |
41.7 |
4.0 |
7.4 |
35.2 |
33.8 |
3 |
41.1 |
36.8 |
10.2 |
11.9 |
11.9 |
11.4 |
1 |
HKUST-1 |
36.0 |
61.9 |
0 |
2.1 |
2.7 |
2.6 |
2 |
43.1 |
47.6 |
0.0 |
9.3 |
4.8 |
4.6 |
3 |
45.6 |
50.1 |
0.0 |
4.3 |
2.1 |
2.0 |
Catalytic mechanism of HKUST-1 (H2O)
To identify the catalytic sites on the HKUST-1 in the oxidation of benzene, we examined the catalytic efficiency of BTC in the reaction. The reaction did not proceed when the same amount of BTC was employed as a substitute for HKUST-1, suggesting that the constituent metal ions (i.e. Cu2+) in the HKUST-1 structure were the catalytic sites. The unsaturated copper can be hydrated in water for several minutes and dehydrated under vacuum. The crystalline phase of HKUST-1 was changed upon adsorpting water (Fig. 2c–f). However, the original crystalline phase can be recovered after being used as catalyst for twice (Fig. 2g), which indicated that the crystalline structure of HKUST-1 maintained stable in water for a certain period of time. HKUST-1 shows high structural stability upon water adsorption or desorption.38
The catalytic characteristics of HKUST-1 are determined not only by the coordinative position of Cu2+ available for bonding small molecules, but also by the dispersive interactions of the organic ligand of BTC. HKUST-1 possesses an intersecting 3D channels with large square-shaped pores (9 Å by 9 Å)28,39 and Lewis acid coordination sites (open copper sites) on the interior walls of the pores.40 In addition, HKUST-1 consists of two types of “cages”, which was separated by two types of “windows”.33,41 Such crystal structure and pore feature facilitate absorption of water. The pores contain 3 terminal axial water molecules whose ligands are directed from the Cu atoms to the interior of the nanopores and up to 10 additional water molecules per [Cu3(BTC)2(H2O)3]n unit by thermal gravimetric analysis (TGA) (Fig. 4), as is in accord with the literature.28 When HKUST-1 was used as catalyst, π–π interaction of the aromatic rings of benzene with the BTC framework and π-complexation of electron-rich benzene to the Lewis acid sites in HKUST-1 (ref. 40 and 42) were not propitious to the interaction of benzene with Cu2+ active sites in HKUST-1. However, interestingly, the utilization of catalyst, the reaction rate and the yield of oxygenates were improved significantly for the same reaction with HKUST-1 (H2O) as catalyst. Actually, in aqueous solution containing benzene, water–water hydrogen bond (wHB) provides an energetically and statistically competitive alternative to benzene–water π H-bond (πHB).43 H atom of H2O points toward the π-cloud of benzene to form O–H⋯π H-bond, and H2O interacts with the benzene via O–H⋯π H-bond.44 It is a formidable challenge to obtain the evidence of the πHB formation between benzene and water because of the low aqueous solubility of benzene (∼20 mM), which means that the πHB OH vibrational peak of interest is more than 1000 times smaller than the broad overlying bulk water OH stretch band. The Raman spectrum of HKUST-1, H2O and benzene revealed a small, broad OH peak at ∼3610 cm−1 assigned to a πHB peak between benzene and H2O,43 as shown in Fig. 5. High-resolution rotational and in vibrational spectra of πHB benzene–H2O dimer indicate that the formation of a πHB leaves water remarkable free to rotate,45 which reveals that πHB is far more flexible (has greater entropy) than OH⋯O hydrogen bonds.43 The water molecule nearest to benzene's center of mass has a greater conformational flexibility when one of its two OH groups forms a πHB than it does when both of its OH groups form a wHB.43 The water molecules existing in the pores of the HKUST-1 or surrounding around the HKUST-1 interacting with benzene via πHB ought to impel benzene to contact with the Cu2+ sites.
 |
| Fig. 5 Aqueous solutions containing dissolved benzene reveal vibrational peaks assigned to water πHB OH groups. (a) The total Raman scattering spectrum of HKUST-1 in water looks virtually identical to that of bulk water. (b) The resulting Raman spectrum of HKUST-1, water and benzene reveals a small, relatively broad peak at ∼3610 cm−1 assigned to a πHB peak between benzene and liquid water. | |
Considering all the above results, we propose a comprehensive summary of the mechanisms of the catalytic process of benzene on both HKUST-1 and HKUST-1 (H2O), as schematized in Scheme 1. In the case of using the HKUST-1 as the catalyst, owing to the adsorption of H2O2 on HKUST-1, it was very likely the negative HO2− ions dissociated from H2O2 directly coordinate to the copper sites to form –Cu
O,46 and then benzene bonds to O atom of –Cu
O by the intermolecular bonds to produce phenol. However, in this process, –Cu
O is formed and simultaneously two sites of coordination between Cu and BTC are lost, the previously coordinated BTC units have to be released, that is, the coordination sites between Cu and BTC would reduce. However, interestingly, the yield of oxygenates, reaction speed, and the stability of HKUST-1 underwent pronounced improvement using HKUST-1 (H2O) as catalyst for the oxidation of benzene. The water-mediated promotion of catalytic activity of HKUST-1 is described in Scheme 1. Water can be coordinated to the Cu sites by strong metal–organic bond, and simultaneously additional water molecules can retain in the pores of HKUST-1 and surroundings around HKUST-1 through hydrogen-bonding interactions or physical adsorption. Water bonding and solvation of surrounding bulk water are the keys for the switch of benzene adsorption mode, the promotion of catalyst reactivity and the enhancement of products yield. We speculated that H2O2 can coordinate to Cu sites instantaneously by situ substitution for water, which can be highly effective in protecting the structure of HKUST-1. In addition, benzene interacting with water molecules coordinated to Cu sites or retained in pores or surroundings of HKUST-1 via O–H⋯π H-bond has been certified by analysis of Raman scattering spectrum, which spurs benzene approach the active sites of HKUST-1 and accelerates the reaction of benzene with H2O2. With this consideration, the effect should be valid for the oxidation of single ring aromatic substances with H2O2 as oxidant.
 |
| Scheme 1 Proposed reaction pathway for the oxidation of benzene on the initial HKUST-1 and water-mediated HKUST-1. | |
Conclusions
In summary, we have disclosed a novel catalytic system in the presence of HKUST-1 preadsorbed water for the oxidation of benzene with H2O2 as oxidant. Simple water treatment can significantly rearrange reaction mode of H2O2 with HKUST-1, switch adsorption mode of benzene, promote catalyst reactivity and enhance products yield. The catalytic system with water active participation opens a door toward facile improvement in the reaction efficiency of the direct oxidation of benzene to its corresponding oxygenates with a simple, green, and cheap method. In addition, the present work reminds us of some important but often ignored issues. Furthermore, the combination of water with HKUST-1 is expected to be utilized in the oxidation of other single ring aromatic substances with H2O2.
Acknowledgements
Funding supports from National Natural Science Foundation of China (21103121, 21276187), Research Fund for the Doctoral Program of Higher Education of China (20110032120011), and Tianjin Municipal Natural Science Foundation (13JCQNJC05800) are gratefully acknowledged.
Notes and references
- J. M. Mayer, in Biomimetic Oxidations Catalyzed by Transition Metal Complexes, Imperial College Press, London, 2000 Search PubMed.
- S.-I. Niwa, M. Eswaramoorthy, J. Nair, A. Raj, N. Itoh, H. Shoji, T. Namba and F. Mizukami, Science, 2002, 295, 105 CrossRef CAS PubMed.
-
(a) A. Raba, M. Cokoja, W. A. Herrmann and F. E. Kühn, Chem. Commun., 2014, 50, 11454 RSC;
(b) L. M. Zhao, Z. C. Liu, W. Y. Guo, L. Z. Zhang, F. Y. Zhang, H. Y. Zhu and H. H. Shan, Phys. Chem. Chem. Phys., 2009, 11, 4219 RSC;
(c) H. Yang, Q. Wu, J. Li, W. Dai, H. Y. Zhang, D. Lu, S. Gao and W. S. You, Appl. Catal., A, 2013, 457, 21 CrossRef CAS PubMed;
(d) X. Wang, T. Zhang, Q. Yang, S. Jiang and B. Li, Eur. J. Inorg. Chem., 2015, 5, 817 CrossRef PubMed;
(e) Y. Wang, T. Zhang, B. Li, S. Jiang and L. Sheng, RSC Adv., 2015, 5, 29022 RSC.
- A. B. Ene, T. Archipov and E. Roduner, J. Phys. Chem. C, 2011, 115, 3688 CAS.
- L. Hu, B. Yue, X. Chen and H. He, Catal. Commun., 2014, 43, 179 CrossRef CAS PubMed.
- W. Wang, G. Ding, T. Jiang, P. Zhang, T. Wu and B. Han, Green Chem., 2013, 15, 1150 RSC.
- P. Nagababu, S. Maji, M. P. Kumar, P. P.-Y. Chen, S. S.-F. Yu and S. I. Chan, Adv. Synth. Catal., 2012, 354, 3275 CrossRef CAS PubMed.
- B. D. Chandler, J. O. Yu, D. T. Cramb and G. K. H. Shimizu, Chem. Mater., 2007, 19, 4467 CrossRef CAS.
- G. Chaplais, A. Simon-Masseron, F. Porcher, C. Lecomte, D. Bazer-Bachi, N. Bats and J. Patarin, Phys. Chem. Chem. Phys., 2009, 11, 5241 RSC.
- P. Jain, V. Ramachandran, R. J. Clark, H. D. Zhou, B. H. Toby, N. S. Dalal, H. W. Kroto and A. K. Cheetham, J. Am. Chem. Soc., 2009, 131, 13625 CrossRef CAS PubMed.
- B. Cai, P. Yang, J. W. Dai and J. Z. Wu, CrystEngComm, 2011, 13, 985 RSC.
- D. X. Xue, A. J. Cairns, Y. Belmabkhout, L. Wojtas, Y. Liu, M. H. Alkordi and M. Eddaoudi, J. Am. Chem. Soc., 2013, 135, 7660 CrossRef CAS PubMed.
- H. Furukawa, K. E. Cordova, M. O'Keeffe and O. M. Yaghi, Science, 2013, 341, 974 CrossRef CAS PubMed.
- J. Kim, D. O. Kim, D. W. Kim and K. Sagong, J. Solid State Chem., 2013, 197, 261 CrossRef CAS PubMed.
-
(a) H. L. Gao, L. Yi, B. Zhao, X. Q. Zhao, P. Cheng, D. Z. Liao and S. P. Yan, Inorg. Chem., 2006, 45, 5980 CrossRef CAS PubMed;
(b) J. An, S. J. Geib and N. L. Rosi, J. Am. Chem. Soc., 2009, 132, 38 CrossRef PubMed;
(c) W. L. Liu, L. H. Ye, X. F. Liu, L. M. Yuan, X. L. Lu and J. X. Jiang, Inorg. Chem. Commun., 2008, 11, 1250 CrossRef CAS PubMed;
(d) W. Morris, B. Volosskiy, S. Demir, F. Gándara, P. L. McGrier, H. Furukawa, D. Cascio, J. F. Stoddart and O. M. Yaghi, Inorg. Chem., 2012, 51, 6443 CrossRef CAS PubMed.
-
(a) K. Sumida, D. L. Rogow, J. A. Mason, T. M. McDonald, E. D. Bloch, Z. R. Herm, T.-H. Bae and J. R. Long, Chem. Rev., 2012, 112, 724 CrossRef CAS PubMed;
(b) J.-R. Li, J. Sculley and H.-C. Zhou, Chem. Rev., 2012, 112, 869 CrossRef CAS PubMed;
(c) O. K. Farha, I. Eryazici, N. C. Jeong, B. G. Hauser, C. E. Wilmer, A. A. Sarjeant, R. Q. Snurr, S. T. Nguyen, A. Ö. Yazaydin and J. T. Hupp, J. Am. Chem. Soc., 2012, 134, 15016 CrossRef CAS PubMed;
(d) J. A. Mason, M. Veenstra and J. R. Long, Chem. Sci., 2014, 5, 32 RSC.
-
(a) V. Colombo, S. Galli, H. J. Choi, G. D. Han, A. Maspero, G. Palmisano, N. Masciocchi and J. R. Long, Chem. Sci., 2011, 2, 1311 RSC;
(b) I. J. Kang, N. A. Khan, E. Haque and S. H. Jhung, Chem.–Eur. J., 2011, 17, 6437 CrossRef CAS PubMed;
(c) T. Li, F. L. Wang, S. T. Wu, X. H. Huang, S. M. Chen and C. C. Huang, Cryst. Growth Des., 2013, 13, 271 Search PubMed.
-
(a) H. D. Guo, X. M. Guo, H. Y. Zou, Y. J. Qi and R. Z. Chen, CrystEngComm, 2014, 16, 2176 RSC;
(b) V. Guillerm, D. Kim, J. F. Eubank, R. Luebke, X. F. Liu, K. Adil, M. S. Lah and M. Eddaoudi, Chem. Soc. Rev., 2014, 43, 6141 RSC;
(c) A. Schneemann, V. Bon, I. Schwedler, I. Senkovska, S. Kaskel and R. A. Fischer, Chem. Soc. Rev., 2014, 43, 6062 RSC.
- J. L. Long, L. M. Wang, X. F. Gao, C. H. Bai, H. F. Jiang and Y. W. Li, Chem. Commun., 2012, 48, 12109 RSC.
- S. Schuster, E. Klemm and M. Bauer, Chem.–Eur. J., 2012, 19, 15831 CrossRef PubMed.
- Y. K. Hwang, D. Y. Hong, J. S. Chang, H. Seo, M. Yoon, J. Kim, S. H. Jhung, C. Serre and G. Férey, Appl. Catal., A, 2009, 358, 249 CrossRef CAS PubMed.
- V. Pascanu, Q. X. Yao, A. B. Gómez, M. Gustafsson, Y. F. Yun, W. Wan, L. Samain, X. D. Zou and B. Martín-Matute, Chem.–Eur. J., 2013, 19, 17483 CrossRef CAS PubMed.
- C. Chizallet, S. Lazare, D. Bazer-Bachi, F. Bonnier, V. Lecocq, E. Soyer, A.-A. Quoineaud and N. Bats, J. Am. Chem. Soc., 2010, 132, 12365 CrossRef CAS PubMed.
- A. Corma, M. J. Diaz-Cabanas, J. L. Jorda, C. Martinez and M. Moline, Nature, 2006, 443, 842 CrossRef CAS PubMed.
- S. Horike, M. Dincǎ, K. Tamaki and J. R. Long, J. Am. Chem. Soc., 2008, 130, 5854 CrossRef CAS PubMed.
-
(a) J. M. Zamaro, N. C. Pérez, E. E. Miró, C. Casado, B. Seoane, C. Téllez and J. Coronas, Chem. Eng. J., 2012, 195–196, 180 CrossRef CAS PubMed;
(b) S. Abednatanzi, A. Abbasi and M. Masteri-Farahani, J. Mol. Catal. A: Chem., 2015, 399, 10 CrossRef CAS PubMed;
(c) H. Yang, J. Li, H. Zhang, Y. Lv and S. Gao, Microporous Mesoporous Mater., 2014, 195, 87 CrossRef CAS PubMed;
(d) Q. Luo, X. Song, M. Ji, S. Park, C. Hao and Y. Li, Appl. Catal., A, 2014, 478, 81 CrossRef CAS PubMed;
(e) S. A. Sotnik, K. S. Gavrilenko, A. S. Lytvynenko and S. V. Kolotilov, Inorg. Chim. Acta, 2015, 426, 119 CrossRef CAS PubMed;
(f) L. H. Wee, N. Janssens, S. R. Bajpe, C. E. A. Kirschhock and J. A. Martens, Catal. Today, 2011, 171, 275 CrossRef CAS PubMed.
- L. Alaerts, E. Séguin, H. Poelman, F. Thibault-Starzyk, P. A. Jacobs and D. E. DeVos, Chem.–Eur. J., 2006, 127, 353 Search PubMed.
- S. S. Y. Chui, S. M. F. Lo, J. P. H. Charmant, A. G. Orpen and I. D. Williams, Science, 1999, 283, 1148 CrossRef CAS.
- D. J. Tranchemontagne, J. R. Hunt and O. M. Yaghi, Tetrahedron, 2008, 64, 8553 CrossRef CAS PubMed.
- L. T. L. Nguyen, T. T. Nguyen, K. D. Nguyen and N. T. S. Phan, Appl. Catal., A, 2012, 425–426, 44 CrossRef CAS PubMed.
- C. H. Specht and F. H. Frimmel, Phys. Chem. Chem. Phys., 2011, 3, 5444 RSC.
- J. Hu, H. Cai, H. Ren, Y. Wei, Z. Xu, H. Liu and Y. Hu, Ind. Eng. Chem. Res., 2010, 49, 12605 CrossRef CAS.
- J. L. C. Rowsell and O. M. Yaghi, J. Am. Chem. Soc., 2006, 128, 1304 CrossRef CAS PubMed.
- K. S. Lin, A. K. Adhikari, C. N. Ku, C. L. Chiang and H. Kuo, Int. J. Hydrogen Energy, 2012, 37, 13865 CrossRef CAS PubMed.
- Y. K. Seo, G. Hundal, I. T. Jang, Y. K. Hwang, C. H. Jun and J. S. Chang, Microporous Mesoporous Mater., 2009, 119, 331 CrossRef CAS PubMed.
- Q. M. Wang, D. Shen, M. Bülow, M. L. Lau, S. Deng, F. R. Fitch, N. O. Lemcoff and J. Semanscin, Microporous Mesoporous Mater., 2002, 55, 217 CrossRef CAS.
- G. S. Szymanski, Z. Karpinski, S. Biniak and A. Swatkowski, Carbon, 2002, 40, 2627 CrossRef CAS.
- K. Schlichet, T. Kratzke and S. Kaskel, Microporous Mesoporous Mater., 2004, 73, 81 CrossRef PubMed.
- A. Vishnyakow, P. I. Ravikovitch, A. V. Neimark, M. Bülow and Q. M. Wang, Nano Lett., 2003, 3, 713 CrossRef.
- X. Y. Cui, Z. Y. Gu, D. Q. Jiang, Y. Li, H. F. Wang and X. P. Yan, Anal. Chem., 2009, 81, 9771 CrossRef CAS PubMed.
- C. Chmelic, J. Kärger, M. Wiebcke, J. Caro, J. M. van Baten and R. Krishna, Microporous Mesoporous Mater., 2008, 117, 22 CrossRef PubMed.
- Z. Y. Gu, C. X. Yang, N. Chang and X. P. Yan, Acc. Chem. Res., 2012, 45, 734 CrossRef CAS PubMed.
- K. P. Gierszal, J. G. Davis, M. D. Hands, D. S. Wilcox, L. V. Slipchenko and D. Ben-Amotz, J. Phys. Chem. Lett., 2011, 2, 2930 CrossRef CAS.
- M. Prakash, K. G. Samy and V. Subramanian, J. Phys. Chem. A, 2009, 113, 13845 CrossRef CAS PubMed.
-
(a) S. Suzuki, P. G. Green, R. E. Bumgarner, S. Dasgupta, W. A. Goddard and G. A. Blake, Science, 1992, 257, 924 Search PubMed;
(b) R. N. Pribble, A. W. Garrett, K. Haber and T. S. Zwier, J. Chem. Phys., 1995, 103, 531 CrossRef CAS PubMed;
(c) J. Gruenloh, J. R. Carney, C. A. Arringto, T. S. Zwier, S. Y. Fredericks and K. D. Jordan, Science, 1997, 276, 1678 CrossRef;
(d) J. Gruenloh, J. R. Carney, F. C. Hagemeister, T. S. Zwier, J. T. Wood and K. D. Jordan, J. Chem. Phys., 2000, 113, 2290 CrossRef PubMed.
- C. Petit, B. Levasseur, B. Mendoza and T. J. Bandosz, Microporous Mesoporous Mater., 2012, 154, 107 CrossRef CAS PubMed.
|
This journal is © The Royal Society of Chemistry 2015 |
Click here to see how this site uses Cookies. View our privacy policy here.