DOI:
10.1039/C5RA04874E
(Paper)
RSC Adv., 2015,
5, 44326-44335
Reverse iodine transfer polymerization (RITP) of chloroprene†
Received
19th March 2015
, Accepted 8th May 2015
First published on 8th May 2015
Abstract
Reversible-deactivation radical polymerization (RDRP) of chloroprene (2-chloro-1,3-butadiene, CP) using reverse iodine transfer polymerization (RITP) has been demonstrated for the first time. Reverse iodine transfer polymerizations of CP were studied in benzene at 50 °C using 2,2′-azobis(isoheptonitrile) (ABVN) as a radical initiator, where a molar ratio ABVN/I2 = 1.7 was used. The process efficiently controls the molar mass (characterized by size exclusion chromatography, SEC) and the structure of the polymer (confirmed by 1H NMR spectra). For example, polychloroprene (PCP) samples of Mn,SEC = 4900 g mol−1 and Mw/Mn = 1.73 (Mn,th = 4800 g mol−1), Mn,SEC = 7300 g mol−1 and Mw/Mn = 1.89 (Mn,th = 7300 g mol−1), and Mn,SEC = 9000 g mol−1 and Mw/Mn = 1.86 (Mn,th = 9300 g mol−1) were successfully obtained. Furthermore, the influence of solvent, initiator and temperature were studied. Last, the controlled nature of the polymer was confirmed by the preparation of polychloroprene-b-polystyrene (PCP-b-PSt) and polychloroprene-b-poly(methyl methacrylate) (PCP-b-PMMA) diblock copolymers.
Introduction
Over the last few years reversible-deactivation radical polymerization (RDRP)1 has led to interesting academic and industrial research due to the ability to synthesize well-defined polymers and complex macromolecular architectures such as block, comb and star copolymers. To date, the most important RDRP techniques are nitroxide mediated polymerization (NMP),2,3 atom transfer radical polymerization (ATRP),4,5 iodine transfer polymerization (ITP),6–9 and reversible addition fragmentation chain transfer (RAFT) polymerization.10,11
Chloroprene (2-chloro-1,3-butadiene; CP) is a very important monomer, which utilized primarily in the manufacture of chloroprene rubber (polychloroprene, CR). CR is one of the most commonly used synthetic rubbers in the rubber industries. CR has been widely used in industrial rubbers, contact adhesives, wires, and various other numerous applications due to its many fascinating properties. To meet these emerging needs and for new material development for more demanding applications, improvements of CR products are very desirable. The physical modification of CR is frequently carried out through polymer blends.12–14 Graft copolymerization is also an important method in modifying chemical and physical properties of CR.15 As a matter of fact, the choice of the RDRP techniques, which open the door to synthesize block, comb and star copolymers, becomes of great relevance via the introduction of specific functionalities on polymer backbones or chain ends.16,17
Regarding the synthetic aspect, CR synthesizes via uncontrolled fashion with sulfur or mercaptans used as chain-terminating agents in industrial field. There has been limited success of the reversible-deactivation radical polymerization behavior of CP despite the fact that it can be polymerized via a radical mechanism. This is partially due to the high reactivity of the CP monomer because of a chlorine substituent. To date, CP was only involved in a few examples of RDRP such as NMP, ITP and RAFT polymerization. However, NMP, ITP and RAFT polymerization suffer drawbacks of different kinds. NMP requires relatively high reaction temperature (100 °C).18 The RAFT polymerization of CP was previously demonstrated by our group19 and by others workers.20 The drawback of the RAFT method is high cost, difficult availability of RAFT agents. In ITP examples, the emulsion polymerization of CP is carried out using iodoform (CHI3) as the chain transfer agent.21 Iodoform presents the disadvantage of being unstable and difficult to handle, which is known to be one of the main problem in ITP process. It is widely known that iodine is a strong radical scavenger and inhibitor of radical polymerizations. The recent discovery of the reverse iodine transfer polymerization (RITP) process is a breakthrough in the field of radical polymerization.22 Lacroix-Desmazes and co-workers showed that the iodinated chain transfer agents is in situ synthesized based on the direct reaction of the initiator with I2, avoiding the presynthesis and storage of the unstable alkyl iodide in RITP mechanism. The consumption of monomer in this step is low and it is called the inhibition period. Once all molecular iodine is consumed, the polymerization period takes place (Scheme 1). This technique has been successfully used to polymerize styrenic monomers (styrene),23–25 acrylic monomers (methyl acrylate,22 methyl methacrylate,26,27 n-butyl acrylate22,28…) in homogeneous and heterogeneous polymerizations.28–31 However, to the best of our knowledge, no chloroprene has been polymerized under RITP.
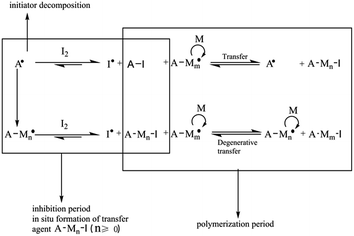 |
| Scheme 1 Simplified reaction scheme for the mechanism of reverse iodine transfer polymerization (RITP). | |
In this article, RITP of chloroprene is reported for the first time. We examine the effect of solvent, initiator and temperature on the degree of control achieved in RITP of CP. As an extension of this investigation, we present the possibility to synthesize polychloroprene-block-polystyrene (PCP-b-PSt) and polychloroprene-block-poly(methyl methacrylate) (PCP-b-PMMA) diblock copolymers by sequential RITP of chloroprene followed by ITP of St and MMA, respectively. Thus, one can obtain adhesives and blend compatibilizers, or thermoplastic elastomers, etc.
Experimental section
Materials
Chloroprene was provided by China Blue Star Shanxi Synthetic Rubber Group Co., Ltd. (Datong, China) and used without further purification. Styrene (St) and methyl methacrylate (MMA) (99%, Tianjin fuchen chemical plant) were distilled under reduced pressure and stored in a freezer before use. Benzoyl peroxide (BPO) was dissolved in chloroform and precipitated into cooled ethanol; the crystals were filtered off and dried. 2,2′-Azobis(isobutyronitrile) (AIBN) was recrystallized from ethanol. 2,2′-Azobis(isoheptonitrile) (ABVN) was recrystallized from methanol. Iodine (I2, Aladdin, 99.8%), was used as received. Benzene, toluene, dimethylbenzene and tetrahydrofuran (THF) were dried over CaH2, distilled before use.
Synthesis of polychloroprene oligomers with Mn,targeted = 5000 g mol−1 by reverse iodine transfer polymerization (RITP) ([CP]/[ABVN]/[I2] = 107.6/1.7/1)
In a typical RITP procedure, CP (10.000 g, 1.13 × 10−1 mol), ABVN (0.4432 g, 1.78 × 10−3 mol), iodine (I2) (0.2666 g, 1.05 × 10−3 mol), and benzene (15 mL) were placed in a 50 mL round bottomed flask equipped with a magnetic bar. The reaction medium was purged with argon for 10 min at 0 °C to remove oxygen. Five freeze–thaw–pump cycles were completed and the flask was placed in an oil bath at 50 °C. The polymerization was conducted in the dark, with magnetic stirring and under argon atmosphere. Samples were withdrawn periodically under argon using a deoxygenated syringe, cooled in an ice bath, and analyzed by size exclusion chromatography (SEC), 1H NMR to determine the molar masses and their composition, respectively. The monomer conversions were calculated by gravimetric analysis.
Synthesis and characterization of a macro-chain transfer agent PCP-I with Mn,targeted = 2900 g mol−1 ([CP]/[ABVN]/[I2] = 60/1.7/1)
CP (10 g, 1.13 × 10−1 mol), ABVN (0.7948 g, 3.20 × 10−3 mol), iodine (0.4781 g, 1.88 × 10−3 mol), and benzene (15 mL) were introduced in a 50 mL round bottomed flask equipped with a magnetic bar. The reaction medium was purged with argon for 10 min at 0 °C to remove oxygen. Five freeze–thaw–pump cycles were completed and the flask was placed in an oil bath at 50 °C. The polymerization was conducted in the dark, with magnetic stirring and under argon atmosphere. The reaction was stopped when the monomer conversion reached 100% for 18 h.
Chain extension of PCP
In a typical procedure for the chain extension reaction with CP, in the Schlenk flask containing the crude sample of the above mentioned PCP-I were added 45.8 g (517 mmol) of CP and 0.1427 g (0.57 mmol) of ABVN ([ABVN]/[PCP-I] = 0.17). Five freeze–thaw–pump cycles were carried out, and then the flask was placed in an oil bath at 50 °C. The polymerization was conducted for 25 h in the dark, with magnetic stirring and under argon atmosphere.
Synthesis of block copolymers
Block copolymers were prepared by the macro-chain transfer agent (macro-CTA) method.
Synthesis of PCP-b-PSt diblock copolymer
In a typical procedure for block copolymerization, in the Schlenk flask containing the crude sample of the above mentioned PCP-I were added 37.2 g (357 mmol) of styrene and 0.1955 g (1.19 mmol) of AIBN ([AIBN]/[PCP-I] = 0.3). Five freeze–thaw–pump cycles were carried out, and then the flask was placed in an oil bath at 65 °C. The polymerization was conducted in the dark, with magnetic stirring and under argon atmosphere to prepare a PCP-b-PSt copolymer. The tube was removed from the oil bath after a given time interval and the reaction mixture was immediately immersed in a water/ice bath to stop the reaction. A fraction of the reaction mixture was directly used for gravimetric analysis. The polymer obtained was also subjected to SEC and 1H NMR.
Synthesis of PCP-b-PMMA diblock copolymer
In a typical procedure for block copolymerization, in the Schlenk flask containing the crude sample of the above mentioned PCP-I were added 34.5 g (345 mmol) of methyl methacrylate and 0.1132 g (0.69 mmol) of AIBN ([AIBN]/[PCP-I] = 0.2). Five freeze–thaw–pump cycles were carried out, and then the flask was placed in an oil bath at 55 °C. The polymerization was conducted in the dark, with magnetic stirring and under argon atmosphere to prepare a PCP-b-PMMA copolymer. The tube was removed from the oil bath after a given time interval and the reaction mixture was immediately immersed in a water/ice bath to stop the reaction. A fraction of the reaction mixture was directly used for gravimetric analysis. The polymer obtained was also characterized by the following techniques: SEC and 1H NMR.
Characterization
The monomer conversion was determined by the gravimetric method. The molar mass and the molar mass dispersities (Đ = Mw/Mn) of the synthesized polymers were measured by SEC using a TOSOH HLC-8320 instrument, which consisted of a solvent delivery system, a column set with two TSK gel Super Multipore HZ-M columns, and a differential refractometer index (RI) detector. The eluent was THF at a flow rate of 0.35 mL min−1 at 40 °C. Polystyrene standards were used to generate the calibration curve. 1H NMR spectra were obtained on a Bruker AV400-MHz spectrometer in CDCl3 at room temperature. 1H chemical shifts were referenced to tetramethylsilane (TMS) via the residual non-deuterated solvent signal at δ = 7.26 ppm.
Results and discussion
RITP homopolymerization of chloroprene
In RITP, it was determined that the ratio of [initiator]/[I2] is a very important factor for obtaining high monomer conversions. With a ratio under 1.5 the reaction medium remains colored (reddish) and the polymerization yield is very low.22 Due to these previous observations, we focused on an [initiator]/[I2] ratio of over 1.7 for all experiments.
Effect of the solvent
In order to determine what effect, if any, the solvents had upon the control of the polymerization, various solvents were used in the RITP of chloroprene. A study of RITP of chloroprene was then carried out with ABVN as the initiator in various solvents: benzene, toluene and dimethylbenzene at 50 °C, for 17 h. The targeted molar mass is 8000 g mol−1 at 100% monomer conversion. Fig. 1 shows the SEC curves of the PCP samples prepared. The SEC curves show symmetrical and unimodal. Table 1 lists the compounds which were used along with monomer conversion and polymer molar mass data. The monomer conversion varied between 74% and 86%. The molar mass distributions of the polymers were not very narrow although the number-average molar masses (Mn) were close to the calculated values. During the PCP syntheses high conversions were observed and molar mass dispersities around 1.9 were similar to the results reported for ITP of CP in emulsion.21 RITP of CP carried out in benzene, final Mn = 5700 at 74% conversion (entry 1). The lowest molar mass distribution PCP was obtained in benzene, Đ = 1.89. In this context, solution polymerization of CP in toluene/dimethylbenzene is also viable (entry 2, 3). Hence, benzene/toluene/dimethylbenzene was a good solvent for RITP of chloroprene.
 |
| Fig. 1 SEC traces of the polymerization product of chloroprene initiated with ABVN in (a) benzene, (b) toluene and (c) dimethylbenzene. | |
Table 1 Polymerization of chloroprene by Reverse Iodine Transfer Polymerization (RITP) in various solventsa
Entry |
Solvent |
T (°C) |
t (h) |
[ABVN]/[I2] |
Con. (%) |
Mn,thb (g mol−1) |
Mn,SECc (g mol−1) |
Đ |
Polymerization of chloroprene ([chloroprene] = 4.08 M) at 50 °C in the presence of ABVN as initiator with [ABVN]/[I2] = 1.7, for 17 h. Calculated by Mn,th = (mass of monomer) × conversion/(2 × (moles of I2)) + MA–I where MA–I = Mchain ends = 237 g mol−1. Determined by size exclusion chromatography (SEC) with polystyrene calibration. |
1 |
Benzene |
50 |
17 |
1.7 |
74.0 |
6000 |
5700 |
1.89 |
2 |
Toluene |
50 |
17 |
1.7 |
76.5 |
6200 |
6700 |
1.99 |
3 |
Dimethylbenzene |
50 |
17 |
1.7 |
86.0 |
6900 |
7000 |
2.00 |
Effect of the initiator and temperature
In the next step we examined the influence of initiator and temperature on RITP of CP. Experiments were carried out in benzene using ABVN (50 °C), AIBN (60 °C) and BPO (65 °C) as initiator, respectively. Initial ratios of [initiator]0 and [I2]0, were the same (1.7
:
1) for all experiments and have been chosen to obtain a final theoretical molar mass (Mn,th), Mn,th = 8000. The molar mass and the molar mass dispersities of these PCP were determined by SEC and are summarized in Table 2 and Fig. 2. In all three cases, the monomer conversions are close in the range of 72–77%. Fig. 2 shows the SEC curves of the PCP samples prepared at 50 °C (ABVN), 60 °C (AIBN) and 65 °C (BPO), respectively. The SEC chromatograms show symmetrical and unimodal. Good agreement between theoretical and experimental molar masses was observed for reaction performed at 50 °C using ABVN as radical initiator and polymers with molar mass dispersity of 1.89 remained in an acceptable interval for reverse iodine transfer polymerization was obtained. There was only a modest increase in molar mass dispersity (Đ = 2.06) but a upward deviation of the molar mass is observed (Mn,th = 5800 g mol−1, Mn,SEC = 8600 g mol−1) for the reaction performed at 60 °C using AIBN as radical initiator (Run 5 in Table 2). In Run 6, RITP of chloroprene with BPO as the initiator at 65 °C leads to much broader molar mass dispersity (Đ = 2.80), and the deviation of the molar mass is much more significant (Mn,th = 6200 g mol−1, Mn,SEC = 9800 g mol−1). The results could be influenced by the nature of the initiator, and temperature. According to the RITP mechanism (Scheme 1), very short A–Mn–I (n = 1, 2, and 3) oligomers are predominantly present in the reaction medium at the end of the inhibition period. So, the end groups of the CTAs exhibit similar structure and reactivity. The half-lifetime is 10 h, 22.8 h, and 59.78 h for ABVN (50 °C), AIBN (60 °C), and BPO (65 °C), respectively.32 And the initiator efficiency of these azonitriles is higher than BPO. Thus, it is possible to classify the reactivities of the initiators in the following decreasing order: ABVN > AIBN > BPO. This indicates that ABVN reacts with I2 to give the largest concentration of iodinated A–Mn–I transfer agents. This leads to the fastest exchange between active and dormant chains, and controlled PCP endowed with experimental molar mass close to the targeted one and with the lowest Đ. Another key factor is the reaction temperature. This could arise from the labile and temperature-sensitive C–I bond. The loss of the iodide chain ends may be intensified at higher reaction temperatures. Thus, at higher temperature, the control of the polymerization of chloroprene by RITP with BPO is rather poor. It is clear from Table 2 that the polymers with predetermined molar mass and the lowest Đ are obtained only at 50 °C using ABVN as radical initiator. On the basis of the results, the reverse iodine transfer polymerization of chloroprene with ABVN at low temperatures (50 °C) is recommended.
Table 2 Polymerization of chloroprene by Reverse Iodine Transfer Polymerization (RITP) initiated with various initiators in benzenea
Entry |
T (°C) |
Initiator |
t (h) |
[Initiator]/[I2] |
Con. (%) |
Mn,thb (g mol−1) |
Mn,SECc (g mol−1) |
Đ |
Polymerization of chloroprene ([chloroprene] = 4.08 M) in benzene initiated with various initiators, such as ABVN (50 °C), AIBN (60 °C), BPO (65 °C) with [initiator]/[I2] = 1.7, respectively. Calculated by Mn,th = (mass of monomer) × conversion/(2 × (moles of I2)) + MA–I where MA–I = Mchain ends = 237 g mol−1. Determined by size exclusion chromatography with polystyrene calibration. |
4 |
50 |
ABVN |
17 |
1.7 |
74.0 |
6000 |
5700 |
1.89 |
5 |
60 |
AIBN |
17 |
1.7 |
72.3 |
5800 |
8600 |
2.06 |
6 |
65 |
BPO |
17 |
1.7 |
76.8 |
6200 |
9800 |
2.80 |
 |
| Fig. 2 SEC traces of the polymerization product of chloroprene initiated with (a) ABVN (50 °C), (b) AIBN (60 °C) and (c) BPO (65 °C) in benzene. | |
These preliminary studies highlight that chloroprene can be polymerized by RITP, so we subsequently study the RITP of chloroprene in more detail.
RITP homopolymerization of CP initiated with ABVN in benzene at 50 °C
Three experiments were performed by RITP to produce PCP with different targeted molar masses. Considering the above discussed experiments, polymerizations were finally carried out in benzene, using ABVN as initiator. In our study, polychloroprene was synthesized by RITP at 50 °C, where a molar ratio ABVN/I2 = 1.7 was used, which is common in an RITP experiment, and the targeted molar masses for experiments were 5000, 8000 and 10
000 g mol−1, respectively.
Fig. 3 shows the evolution of the monomer conversion and values of ln([M]0/[M]) versus time for the RITP-solution polymerization of CP with [CP]0
:
[ABVN]0
:
[I2]0 = 107.6
:
1.7
:
1, [CP]0
:
[ABVN]0
:
[I2]0 = 175.4
:
1.7
:
1, [CP]0
:
[ABVN]0
:
[I2]0 = 220.5
:
1.7
:
1 at 50 °C. The polymerization of chloroprene by RITP can be divided into two main stages, including inhibition period and polymerization period, as shown in Fig. 3. It is believed that the inhibition is associated with in situ formation of a chain-transfer agent A–I and/or A–Mn–I and is complete after full consumption of molecular iodine.33 Indeed, the reaction mixture became colorless after inhibition period, whereas it was brown at the beginning of the reaction. With the color of iodine fading at the end of the inhibition period, the polymerization occurs. From Fig. 3 the inhibition period took less than 2 h for an initial [ABVN]0/[I2]0 molar ratio of 1.7, it is evident that the inhibition time (tinh) of CP is much shorter than those of the other monomers.22,24 This could be due to the high reactivity of the monomer. Shiman et al. reported the inhibition time for styrene is dependent on the targeted molar mass.23 The inhibition period of the polymerization of chloroprene at 50 °C is about 110, 67, and 56 min with Mn,targeted = 5000, 8000, 10
000 g mol −1, respectively. It can also be seen that tinh decreases with increasing targeted molar mass. Variations in the length of the inhibition period could readily be ascribed to different iodine concentrations. A long inhibition period may be unfavorable for the industrial application. Therefore, the much shorter inhibition period is a great advantage of RITP of CP. From Fig. 3, it can be seen that the targeted molar mass did also affect the rate of polymerization, as expected. The reaction required 24.0 h to reach 91% conversion with [CP]0
:
[ABVN]0
:
[I2]0 = 175.4
:
1.7
:
1, while for [CP]0
:
[ABVN]0
:
[I2]0 = 220.5
:
1.7
:
1, 25.0 h was required. However, when the polymerization was carried out in the experimental conditions: [CP]0
:
[ABVN]0
:
[I2]0 = 107.6
:
1.7
:
1, ninety percent conversion was reached after only 12.0 h. The evolution of monomer conversion with time clearly shows that RITP of CP is relatively fast. The plot of ln([M]0/[M]) is linear in a wide range of conversion, which indicates that the concentration of the active centers is constant (see Fig. 3b). The polymerization follows pseudo-first order kinetics as would be expected for a controlled polymerization.
 |
| Fig. 3 (a) Time-conversion curves, and (b) kinetic plots of ln([M0]/[M]) vs. time, performed during the synthesis of PCP by RITP of CP initiated with ABVN in benzene at 50 °C under different experimental conditions: ■ [CP]0 : [ABVN]0 : [I2]0 = 107.6 : 1 .7 : 1, Mn,targeted = 5000 g mol−1 (CP (10 g, 1.13 × 10−1 mol), ABVN (0.4432 g, 1.78 × 10−3 mol), iodine (0.2666 g, 1.05 × 10−3 mol), and benzene (15 mL)); ● [CP]0 : [ABVN]0 : [I2]0 = 175.4 : 1.7 : 1, Mn,targeted = 8000 g mol −1; ▲ [CP]0 : [ABVN]0 : [I2]0 = 220.5 : 1.7 : 1, Mn,targeted = 10 000 g mol−1. | |
Fig. 4a shows Mn as a function of monomer conversion. The theoretical Mns are shown as solid lines, and the dotted lines indicate the experimental evolution of molar masses with conversion in Fig. 4a. In all three cases, the molar masses increased with conversion, as they should in a controlled polymerization. Initially, the experimental molar masses were higher than predicted by ideal behavior, which is expected for a system solely governed by RITP and in close agreement with comparable systems from the literature.22 This upward deviation is normal and can be attributed to an insufficient rate of the degenerative transfer in comparison to propagation. More importantly, the molar mass of the polymer increased with conversion and approached the theoretical molar mass at high monomer conversion. These results agree very well with those obtained by Lacroix-Desmazes et al. who prepared poly(methyl methacrylate) via RITP.26 For these three polymerizations, molar mass dispersities values remained in the range of 1.4–1.9 (Fig. 4b). Plots of Đ value versus the chloroprene conversion showed first a increase of Đ followed by a constant. The molar mass dispersities, which are similar to the results reported for ITP of CP in emulsion,21 remained in an acceptable interval for reverse iodine transfer polymerization. However, the molar mass dispersities were broader than that of PCP prepared by RAFT polymerization.19 The relatively high molar mass dispersities relevant in the RITP of CP at 50 °C are explained by the relatively low degenerative chain transfer constant implied in iodine transfer polymerizations. In conclusion, the molar masses increase with conversion, while molar mass dispersities values remained reasonably low, indicating that the RITP process does allow for control of the radical polymerization of CP.
 |
| Fig. 4 Dependence of (a) number-average molar mass, and (b) molar mass dispersities (Đ = Mw/Mn) on conversion, performed during the synthesis of PCP by RITP of CP initiated with ABVN in benzene at 50 °C under different experimental conditions: ■ [CP]0 : [ABVN]0 : [I2]0 = 107.6 : 1.7 : 1, Mn,targeted = 5000 g mol−1; ● [CP]0 : [ABVN]0 : [I2]0 = 175.4 : 1.7 : 1, Mn,targeted = 8000 g mol−1; ▲ [CP]0 : [ABVN]0 : [I2]0 = 220.5 : 1.7 : 1, Mn,targeted = 10 000 g mol−1. | |
Fig. 5 shows the corresponding SEC chromatograms of polymers formed at different time intervals. Although the molar mass distribution is broader than that of PCP prepared by RAFT polymerization,19 the chromatogram is unimodal over the range of conversions investigated in this study. Furthermore, a continuous shift of the curves toward shorter elution times is observed, indicating continuously increasing molar masses.
 |
| Fig. 5 Typical SEC traces from the synthesis of PCP by RITP of CP initiated with ABVN in benzene at 50 °C under different experimental conditions: (a) [CP]0 : [ABVN]0 : [I2]0 = 107.6 : 1.7 : 1, Mn,targeted = 5000 g mol−1; (b) [CP]0 : [ABVN]0 : [I2]0 = 175.4 : 1.7 : 1, Mn,targeted = 8000 g mol−1; (c) [CP]0 : [ABVN]0 : [I2]0 = 220.5 : 1.7 : 1, Mn,targeted = 10 000 g mol−1. | |
In the RITP mechanism, the reversible C–I bond activation relies on the reverse iodine transfer process among the polymer chain ends similar to the iodine transfer radical polymerizations.34 Fig. 6 shows a typical 1H NMR spectrum of a low molar mass PCP prepared via RITP. The polymerization of chloroprene was carried out at 50 °C with a molar ratio [CP]0
:
[ABVN]0
:
[I2]0 = 60
:
1.7
:
1. The spectrum obtained after 5 h is analyzed here. The large signals were assigned to the main chain protons of the PCP: the methylidyne protons in the CP units absorb at 5.2–6.0 ppm (b). In addition to these large resonances, there are characteristic signals that originated from the ω-end group, which was observed at 4.5–4.8 ppm (a). This confirms the PCP-I structure, which is consistent with that referenced in the literature.21 The area of peak a was compared to that of peak b in order to determine Mn,NMR. The calculated Mn,NMR = 1300 g mol−1 was in good agreement with Mn,th = 1300 g mol−1 for 38.3% convs and slightly lower than Mn,SEC = 1400 g mol−1 against the polystyrene calibration. This confirms the structure of the polymer according to the mechanism of RITP previously described in the introduction.
 |
| Fig. 6 1H NMR spectrum in CDCl3 of a PCP sample synthesized by RITP process in benzene and precipitated in cold petroleum ether (CP (10 g, 1.13 × 10−1 mol), ABVN (0.7948 g, 3.20 × 10−3 mol), iodine (0.4781 g, 1.88 × 10−3 mol), and benzene (15 mL), 50 °C, 5 h, monomer conversion 38.3%, Mn,th = [(mCP × conversion)/(2 × nI2) + Mchain ends] = 1300 g mol−1 with Mchain ends = 237 g mol−1, Mn,SEC = 1400 g mol−1, Mn,NMR = [(2 × Ib/Ia) × MCP + Mchain ends] = 1300 g mol−1). | |
If every PCP macromolecule chain possesses an iodine atom at the ω-end, they should be able to act as the macro-chain transfer agent in the polymerization of the second monomer, so block copolymers are generated. To further demonstrate the controlled nature of these polymerizations, the study on the synthesis of block copolymers is thus considered in the last part of this work.
Synthesis and characterization of a macro-chain transfer agent PCP-I with Mn,targeted = 2900 g mol−1 ([CP]/[ABVN]/[I2] = 60/1.7/1)
The solution polymerization of chloroprene initiated by ABVN at 50 °C was stopped after 18 h ([CP]
:
[ABVN]
:
[I2] = 60
:
1.7
:
1) to obtain a PCP-I block of short chain length. Full conversion was achieved within the 18 h period monitored. Using a low monomer to initiator ratio ([CP]
:
[ABVN]
:
[I2] = 60
:
1.7
:
1), the molar mass was controlled even at high monomer conversions and good iodo-functional PCP was obtained (see ESI†). Conversions close to 100% attainable for CP are advantageous to avoid a purification step and continue directly with the formation of the second block since few amount of residual monomer should not affect the properties of the second block.
Chain extension of PCP
The controlled feature of the obtained polymer (Mn = 2900 g mol−1, Mw/Mn = 1.78, conversion = 100%) was further verified by a chain-extension experiment. Typically, PCP-I was further reacted with CP in benzene at 50 °C for 25 h ([CP]0/[PCP-I]0/[ABVN]0 = 900
:
6
:
1). The experimental molar mass increased from 2900 g mol−1 to 10
000 g mol−1; this indicated that the original polymers were active (Fig. 7). However, a small tail was found in the SEC trace of the chain extended PCP, and this resulted in an increase in Đ. This may have been caused by the existence of dead chains in the original polymer (macro-CTA), which cannot be avoided in any RDRP technique, and the loss of the iodide chain ends may be intensified in a long reaction time (25 h) in the case of RITP.
 |
| Fig. 7 SEC traces of PCP (a) before and (b) after the chain-extension reaction. Polymerization conditions: [CP]0/[PCP macro-CTA]0/[ABVN]0 = 900 : 6 : 1 at 50 °C for 25 h. | |
Synthesis of polychloroprene-based block copolymers
CP is a monomer with a high reactivity in free radical polymerization, and in a copolymerization process the reactivity ratios are very different (rCP = 7.84, rSt = 0.05; rCP = 6.33, rMMA = 0.08, respectively) and there is practically no incorporation of St/MMA into the polychloroprene backbone.35 Sequential step block copolymerization of different monomers by RDRP is an area of active interest from both the technological and scientific points of view. As a consequence of RITP process, polychloroprene with an iodine end group results (Scheme 1), which can further act as a degenerative transfer agent, leading to the insertion of new monomer molecules into the polychloroprene chain.
To obtain PCP-b-PSt/MMA, PCP-I must be previously synthesized by RITP process as shown in Schemes 2 and 3.
 |
| Scheme 2 Synthetic pathways for the preparation of polychloroprene-block-polystyrene diblock copolymers via RITP. | |
 |
| Scheme 3 Synthetic pathways for the preparation of polychloroprene-block-poly(methyl methacrylate) diblock copolymers via RITP. | |
Synthesis of polychloroprene-block-polystyrene
PCP-b-PSt block copolymers were prepared by sequential RITP of CP followed by ITP of St. In the first step, the PCP-I macro-chain transfer agent was prepared by using identical conditions as discussed above, RITP of CP. Owing to the end functionality of iodine group, the PCP chains can serve as macro-CTA for subsequent block polymerization. The resulting PCP-I has a Mn,SEC = 2800 g mol−1 and Đ of 1.78. In the second one, ITP of styrene was performed at 65 °C, in the presence of PCP-I and AIBN as the macro-chain transfer agent and the initiator, respectively. The synthesis was carried out in the experimental conditions: [St]0
:
[PCP-I]0
:
[AIBN]0 = 300
:
3
:
1.
The results of the block copolymers obtained at various time intervals are listed in Table 3. Table 3 shows an increase of the conversion with increasing time. The molar mass of the block copolymer was found to increases with conversion, while the Đ decreased. The final block copolymer presents Mn,SEC = 7400 g mol−1 and Đ = 1.66 at 46.2% conversion. In these cases, a good agreement was obtained between the experimental molar mass and the theoretical molar mass. This confirms the successful synthesis of a macro-transfer reagent PCP-I with good end-group functionality and further confirms the controlled nature of these polymerizations.
Table 3 Results of PCP-b-PSt diblock copolymer synthesized by sequential RITP of CP followed by ITP of St
No. |
h |
Conv.% |
Mn,tha |
Mn,SECb |
Đb |
Calculated by , where Mn(1) is the number average molecular weight of the first block, m(2) is the mass of the second monomer, n(1) is the number of moles of the macro-CTA, and c2 is the conversion of the second monomer. Mn,SEC and Đ were obtained by SEC with polystyrene calibration. |
7 |
8 |
24.1 |
5300 |
5100 |
1.75 |
8 |
16 |
34.5 |
6400 |
6600 |
1.66 |
9 |
24 |
46.2 |
7600 |
7400 |
1.66 |
Fig. 8 shows the overlay of the molar mass distributions of PCP-b-PSt and PCP-I precursor. As can be seen from SEC data shown in Fig. 8, the molar mass of the polymer yielded increases progressively with polymerization time. Obviously, all curves had a single peak without a marked shoulder. Therefore, most of the polychloroprene chains were controlled and took part in the formation of the desired block copolymer.
 |
| Fig. 8 SEC traces of PCP-b-PSt block copolymers synthesized by sequential RITP of CP followed by ITP of St ([St]0/[PCP-I]0/[AIBN]0 = 300 : 3 : 1 at 65 °C). | |
A typical 1H NMR spectrum of the copolymers prepared is shown in Fig. 9. It can be seen that besides the absorptions of chloroprene repeating units (5.2–5.9 ppm, a), the signals originating from styrene units (6.3–7.3 ppm, b) also appears. The characteristic signals originating from the ω-end groups (4.5–4.7 ppm, c) were observed. Ia and Ib are the integral values of the peaks a and b. Thus, from the integral Ia and the integral Ib, the DPn,st was given by [Ib/(5Ia) DPn,CP], giving DPn,st = 29. An average of 29 units of styrene is built into every PCP macromolecule chain, which is in agreement with the theoretical composition of the copolymer. 1H NMR spectrum further confirms the formation of PCP-b-PSt block copolymer.
 |
| Fig. 9 1H NMR spectrum recorded in CDCl3 of PCP-b-PSt diblock copolymer synthesized by sequential RITP of CP followed by ITP of St (time = 8 h, conversion = 24.1%, and Mn,SEC = 5100 g mol−1). | |
Synthesis of polychloroprene-block-poly(methyl methacrylate)
The procedures were similar to those used for synthesis of the PCP-b-PSt block copolymers, except using MMA as the second monomer via a conventional ITP process at 55 °C. The molar ratio of the monomer (MMA) to PCP-I (macro-CTA controlling the process) to AIBN (generator of radicals) was chosen to 500
:
5
:
1. The polymerization proceeds smoothly within 17 h at 55 °C. PCP-b-PMMA block copolymers prepared in this work were analyzed by SEC and 1H NMR to determine their molar mass, Đ, and composition.
The syntheses of diblock copolymers PCP-b-PMMA by addition of methyl methacrylate starting from PCP-I homopolymer as macro-CTA are presented in Table 4 and Fig. 10. With increasing reaction time, the molar mass of the resulting block copolymer increases with conversion. At the same time, there was only a modest increase in molar mass dispersity. Fig. 10 displays the SEC chromatograms of the initial and diblock copolymer. The SEC analysis of the block copolymer showed an near-monomodal distribution with a visible shift toward higher molar masses as compared to the macro-CTA, confirming that most of the polychloroprene chains were controlled and took part in the formation of the desired block copolymer. However, when the reaction time was extended to 17 h, a bad control of the polymerization was observed: a tail was found in the SEC spectrum of the diblock polymers, and this resulted in an increase in Đ of the diblock polymers (Đ = 1.97). The tail was attributed to inactive polymers existing in the original polymers, which is unavoidable in an RITP experiment. These results agree very well with our previous study. A small shoulder peak at a high molar mass was observed in the SEC spectrum of the diblock polymer, and this resulted in an increase in Đ of the diblock copolymers, when PMMA-b-PCP diblock copolymer was prepared by RAFT technique.19 Previously, the RITP of MMA has been studied in detail at 80 °C by Boutevin and co-workers.26 Even at high monomer conversion (50%), a small tail was observed in the SEC traces. The experiment results also may reveal that the introduction of MMA decreases the control level of the polymerization. Due to the differences in hydrodynamic volumes of PCP-b-PMMA block copolymers and polystyrene standards, experimental molar masses of the diblock copolymers evaluated by SEC were slightly lower than the theoretical molar masses at low conversion, whereas at moderate conversion, the experimental molar masses appeared to be above the theoretical molar masses. However, block copolymer formation was clearly successful, even if the resulting Mw/Mn is large.
Table 4 Results of PCP-b-PMMA diblock copolymer synthesized by sequential RITP of CP followed by ITP of MMA
No. |
h |
Conv.% |
Mn,tha |
Mn,SECb |
Đb |
Calculated by , where Mn(1) is the number average molecular weight of the first block, m(2) is the mass of the second monomer, n(1) is the number of moles of the macro-CTA, and c2 is the conversion of the second monomer. Mn,SEC and Đ were obtained by SEC. |
10 |
8 |
27.3 |
5600 |
4600 |
1.68 |
11 |
12 |
31.3 |
6000 |
6700 |
1.91 |
12 |
16 |
49.1 |
7800 |
8300 |
1.86 |
13 |
17 |
55.2 |
8400 |
9800 |
1.97 |
 |
| Fig. 10 SEC traces for PCP-b-PMMA block copolymers synthesized by sequential RITP of CP followed by ITP of MMA ([MMA]0/[PCP-I]0/[AIBN]0 = 500 : 5 : 1 at 55 °C). | |
1H NMR spectrum and the corresponding peak assignments of PCP-b-PMMA are shown in Fig. 11. The signals at around 5.2–5.9 ppm (a) are attributed to the proton signals of PCP block. The signals at 3.60 ppm are assigned to the methoxy –OCH3 (b) groups of the repeat unit of MMA. The signal at about 2.9 ppm is attributed to the methylene in the β position of iodine (c) at the chain end. 1H NMR spectroscopy results showed the presence of both species (i.e., PCP segment and PMMA segment) within the copolymer. Additionally, a clear shift of the SEC curves toward higher molecular weights is observed. These confirm the incorporation of the PMMA onto the PCP chains.
 |
| Fig. 11 1H NMR spectrum recorded in CDCl3 of PCP-b-PMMA diblock copolymer synthesized by sequential RITP of CP followed by ITP of MMA (time = 8 h, conversion = 27.3%, and Mn,SEC = 4600 g mol−1). | |
A block copolymer prepared by RDRP technical, may often in fact contain homopolymer, unreacted macroinitiator as well as copolymer.36 Therefore, the GPEC method was attempted to separate the PCP–PSt/PMMA copolymer (see the ESI†). Unfortunately, the retention time of PSt/PMMA and PCP are almost same, it may be caused by the similar solubility or the polarity of the PSt/PMMA and PCP. Greesh37 reported that preparation of PSt-b-PHEA block copolymers via RITP. The successful separation of PSt-b-PHEA block copolymers by HPLC is due to the different solubility or the polarity of PSt and PHEA homopolymers. They found that the amount of homopolymer was small. Additionally, acetone could dissolve homopolymers of PSt with low Mn and PMMA, and couldn't dissolve homopolymers of PCP. PCP-based block copolymers are generally insoluble in acetone. The reserved copolymers were precipitated from acetone and dried under vacuum for SEC analysis. In contrast to the previous SEC traces, similar SEC traces were observed. In other words, most of the polychloroprene chains were controlled and took part in the formation of the desired block copolymer although small amount of PSt/PMMA homopolymers were unavoidable.
As mentioned earlier, the formation of novel block copolymers consisting of CP and St/MMA segments via RITP has not been reported before. These results indicate the preparation of block copolymers of PCP-b-PSt/MMA was successful.
Conclusion
For the first time, the reversible-deactivation radical polymerization of chloroprene has been described using RITP technique. We studied the effects of various parameters such as solvent, initiator and temperature in the polymerization of CP. Three different solvents (benzene, toluene, dimethylbenzene) gave a reasonable control of CP using 2,2′-azobis(isoheptonitrile) (ABVN) as initiator. The effect of initiator and temperature upon the polymerization of CP was investigated using ABVN, 2,2′-azobis(isobutyronitrile) (AIBN) and benzoyl peroxide (BPO) as initiator at 50 °C, 60 °C, and 65 °C, respectively. It is clear that the polymerization of CP was well-controlled at a low temperature (50 °C) in the presence of ABVN as initiator. Thus, RITP of CP is highly versatile and robust. Thereafter, homopolymerization of CP was successfully performed in benzene at 50 °C using ABVN as radical initiator, where a molar ratio ABVN/I2 = 1.7 was used. SEC and 1H NMR techniques were used to analyze the structure of the polymers. RITP technique proved to be a very efficient method to obtain PCP of well-defined molar mass. Novel diblock copolymers of PCP-b-PSt and PCP-b-PMMA can also be successfully synthesized by sequential RITP of chloroprene followed by ITP of St and MMA, respectively. Hence, the controlled nature of the RITP process opens the door to a wide range of well designed macromolecular architectures for CP.
Acknowledgements
Thank the financial supports of the National Natural Science Foundation of China under Grant no. 51073010 and 51373021 are gratefully acknowledged.
References
- A. D. Jenkins, R. G. Jones and G. Moad, Pure Appl. Chem., 2010, 82, 483–491 CAS.
- M. K. Georges, R. P. N. Veregin, P. M. Kazmaier and G. K. Hamer, Macromolecules, 1993, 26, 2987–2988 CrossRef CAS.
- V. Delplace, S. Harrisson, A. Tardy, D. Gigmes, Y. Guillaneuf and J. Nicolas, Macromol. Rapid Commun., 2014, 35, 484–491 CrossRef CAS PubMed.
- K. Matyjaszewski and N. V. Tsarevsky, J. Am. Chem. Soc., 2014, 136, 6513–6533 CrossRef CAS PubMed.
- C. Scholz and K. Matyjaszewski, Polym. Int., 2014, 63, 801–802 CrossRef CAS PubMed.
- K. Matyjaszewski, S. Gaynor and J. Wang, Macromolecules, 1995, 28, 2093–2095 CrossRef CAS.
- K. Koumura, K. Satoh, M. Kamigaito and Y. Okamoto, Macromolecules, 2006, 39, 4054–4061 CrossRef CAS.
- H. Sawada, T. Tashima, Y. Nishiyama, M. Kikuchi, Y. Goto, G. Kostov and B. Ameduri, Macromolecules, 2011, 44, 1114–1124 CrossRef CAS.
- N. Durand, B. Ameduri and B. Boutevin, J. Polym. Sci., Part A: Polym. Chem., 2011, 49, 82–92 CrossRef CAS PubMed.
- A. Goto, K. Sato, Y. Tsujii, T. Fukuda, G. Moad, E. Rizzardo and S. H. Thang, Macromolecules, 2001, 34, 402–408 CrossRef CAS.
- L. H. Zhang, L. R. Cool, C. Wesdemiotis, R. A. Weiss and K. A. Cavicchi, Polym. Chem., 2014, 5, 1180–1190 RSC.
- A. Das and D. K. Basu, J. Appl. Polym. Sci., 2005, 96, 1492–1504 CrossRef CAS PubMed.
- M. Sohail Khan, D. Lehmann and G. Heinrich, Acta Mater., 2009, 57, 4882–4890 CrossRef CAS PubMed.
- B. P. Kapgate and C. Das, RSC Adv., 2014, 4, 58816–58825 RSC.
- F. Yue-E, J. Jun and M. Chaoxiong, Radiat. Phys. Chem., 1999, 54, 159–163 CrossRef.
- A. D. Asandei, O. I. Adebolu and C. P. Simpson, J. Am. Chem. Soc., 2012, 134, 6080–6083 CrossRef CAS PubMed.
- D. J. Keddie, Chem. Soc. Rev., 2014, 43, 496–505 RSC.
- N. Ajellal, C. M. Thomas and J. F. Carpentier, Polymer, 2008, 49, 4344–4349 CrossRef CAS PubMed.
- J. Hui, Z. Dong, Y. Shi, Z. Fu and W. Yang, RSC Adv., 2014, 4, 55529–55538 RSC.
- N. Pullan, M. Liu and P. D. Topham, Polym. Chem., 2013, 4, 2272–2277 RSC.
- J. Gu, X. Yan, Z. Fu, W. Yang and Y. Shi, J. Appl. Polym. Sci., 2013, 128, 2291–2296 CrossRef CAS PubMed.
- P. Lacroix-Desmazes, R. Severac and B. Boutevin, Macromolecules, 2005, 38, 6299–6309 CrossRef CAS.
- D. I. Shiman, S. V. Kostyuk, L. V. Gaponik and F. N. Kaputskii, Russ. J. Appl. Chem., 2010, 83, 2028–2034 CrossRef CAS.
- T. Wright, H. Chirowodza and H. Pasch, Macromolecules, 2012, 45, 2995–3003 CrossRef CAS.
- C. Ladavière, P. Lacroix-Desmazes and F. Delolme, Macromolecules, 2008, 42, 70–84 CrossRef.
- C. Boyer, P. Lacroix-Desmazes, J. Robin and B. Boutevin, Macromolecules, 2006, 39, 4044–4053 CrossRef CAS.
- B. Nottelet, P. Lacroix-Desmazes and B. Boutevin, Polymer, 2007, 48, 50–57 CrossRef CAS PubMed.
- J. Tonnar, P. Lacroix-Desmazes and B. Boutevin, Macromol. Rapid Commun., 2006, 27, 1733–1738 CrossRef CAS PubMed.
- J. Tonnar and P. Lacroix-Desmazes, Angew. Chem., Int. Ed. Engl., 2008, 47, 1294–1297 CrossRef CAS PubMed.
- H. C. Shin, H. G. Oh, K. Lee, B. H. Lee and S. Choe, Polymer, 2009, 50, 4299–4307 CrossRef CAS PubMed.
- D. Rayeroux, B. N. Patra and P. Lacroix-Desmazes, J. Polym. Sci., Part A: Polym. Chem., 2013, 51, 4389–4398 CrossRef CAS PubMed.
- J. Brandrup, E. H. Immergut and E. A. Grulke, Polymer Handbook, Wiley, New York, 4th edn, 1999 Search PubMed.
- S. Moulay, Des. Monomers Polym., 2014, 17, 501–527 CrossRef CAS PubMed.
- M. Farrokhi, M. Abdollahi and M. Hemmati, Polym. Int., 2014, 63, 1494–1504 CrossRef CAS PubMed.
- D. L. Dineen and K. W. Doak, J. Am. Chem. Soc., 1951, 73, 1084–1087 CrossRef.
- M. Tanishima, A. Goto, L. Lei, A. Ohtsuki, H. Kaji, A. Nomura, Y. Tsujii, Y. Yamaguchi, H. Komatsu and M. Miyamoto, Polymers, 2014, 6, 311–326 CrossRef PubMed.
- N. Greesh, R. Sanderson and P. Hartmann, J. Appl. Polym. Sci., 2012, 126, 1773–1783 CrossRef CAS PubMed.
Footnote |
† Electronic supplementary information (ESI) available. See DOI: 10.1039/c5ra04874e |
|
This journal is © The Royal Society of Chemistry 2015 |
Click here to see how this site uses Cookies. View our privacy policy here.