DOI:
10.1039/C5RA02113H
(Paper)
RSC Adv., 2015,
5, 20459-20466
Self assembled polyaniline nanofibers with enhanced electromagnetic shielding properties†
Received
20th January 2015
, Accepted 9th February 2015
First published on 9th February 2015
Abstract
Polyaniline nanofibers have been synthesized by simple chemical polymerization method without using any structure directing agents and organic solvents. The effects of various reaction conditions on the morphology and electromagnetic interference (EMI) shielding properties of the polyaniline nanofibers were investigated. The detailed study of various reaction conditions indicates that stable surfactant free, room temperature oxidation of aniline hydrochloride by ammonium persulfate at low oxidant to monomer ratio in acidic media yields self-assembled uniform polyaniline nanofibers. The nanofibers have excellent EMI shielding efficiency of about 71–77 dB in the frequency range of 8.2–18 GHz.
1. Introduction
The emerging growth of the electric and electronic industry leads to increased use of electronic products and telecommunication equipment which in turn cause the problem of electromagnetic interference (EMI). EMI has received attention, as it affects human health, and reduces the lifetime and performance of the instruments. It also affects the safe operation of many electronic devices from those used in day to day life to space exploration.1 This problem can be solved by shielding all electronic equipment against electromagnetic interference.2 Shielding of the unusually high frequencies of electromagnetic radiation in the microwave frequency region of 8.2–18 GHz (X and Ku band) has great importance because of its utilization in commercial, military and biological fields.1 Extensive research has been done for the development of new lightweight microwave shielding materials with high efficiency and strength. In aerospace applications, metallic shields are commonly used but have the disadvantages of high density and weight.3
Over the past few decades, conducting polymers have been an area of immense interest owing to the growing technological applications. The applications are in rechargeable batteries,4,5 EMI shielding,6,7 microelectronics,8,9 sensors,10,11 electrochromic displays,12 photovoltaic devices13 etc. That is due to their light weight, versatility, processability and tunable electrical properties.14–17 Among the various conducting polymers, polyaniline (PANI) has gained particular attention for use in commercial applications. That is because of its superior conductivity control through doping with relatively natural polymerization of high yield, low cost, low density, environmental stability, interesting redox reversibility and excellent corrosion resistance.18–24 Hence polyaniline finds potential applications as corrosion protection of metals, light-emitting devices, biocompatible materials, catalysts, electrodes, sensors, control of electromagnetic radiation and antistatic coatings.25–29 The intrinsic conductivity of polyaniline makes it a viable material in the field of EMI shielding over wide frequency range of 100 MHz to 20 GHz. In addition, polyaniline exhibits notable EMI shielding through absorption that provides shielding against potential internal EMI, which differs from the dominant metal based shielding mechanism of reflection which is very interesting for military applications.30 Mn0.5Zn0.5Fe2O4 polyaniline composite prepared by in situ emulsion polymerization exhibits shielding effectiveness (SE) of 35 dB in the X-band (8.2–12.4 GHz).31 While the polyaniline-MWCNT nanocomposites has EMI SE of about 28–39 dB in the Ku-band (12.4–39.2 GHz) frequency range.31 EMI shielding of 55 dB obtained in the Ku-band for DBSA (Dodecyl Benzene Sulfonic Acid) doped polyaniline nanostructures.32 Polyaniline tubes consisting of reduced graphene oxide decorated with iron oxide nanoparticles exhibit a shielding effectiveness of 51 dB in the X-band.33 In recent times, polyaniline based composites report shielding effectiveness of 100% at X and Ku-band frequency range.34 As a result, polyaniline based EMI shielding materials are of high demand.
Nanofiber is the most attractive nanostructure of polyaniline because of large aspect ratio, high specific surface area, and excellent processability.35 Traditional polymerization with common mineral acids produces polyaniline with granular morphology.36 Many synthetic methods have been developed to synthesize one-dimensional polyaniline structures through aniline chemical oxidation assisted by templates like zeolite, track-etched polymeric membranes, anodized alumina, polymer fibers etc.37–40 Another method of synthesis of nanofibers is by the addition of surfactants that act as structure directing agents.41–45 There are several other approaches for the synthesis of polyaniline nanofibers such as interfacial polymerization, seeding polymerization, dilute polymerization, ultraviolet light, gamma ray radiation, ultrasonic irradiation, microwave assisted polymerization, etc.36,46–52 Most of these methods yield nanofibers on a limited scale, often require tedious synthesis process as well as post-synthesis process to remove templates and surfactants. In the present case, we report a simple, template or emulsifier free (self-assembled)53 synthesis of an excellent EMI shielding polyaniline nanofibers at room temperature by chemical polymerization route. The present paper investigated the effect of reaction medium, surfactant, temperature, stirring and reaction time on the morphology and shielding properties of polyaniline nanofibers in the frequency range of 8.2–18 GHz.
2. Methodology and characterization
The reactants used in the synthesis of polyaniline were aniline hydrochloride monomer (Alfa Aesar, Ward Hill, MA, USA), ammonium persulfate (APS) (Aldrich, Chemical Company, Inc., Milwaukee, WI, USA) and sodium dodecylbenzenesulfonate (SDBS) (Aldrich, Chemical Company, Inc., Milwaukee, WI, USA). The aniline hydrochloride monomer is less toxic than liquid aniline and persulfate ammonium salt was preferred to the potassium counter part because of its better solubility in water and is a commonly used oxidant. The synthesis was achieved by the drop wise addition of APS dissolved in water into the aniline hydrochloride solution in water with an oxidant monomer molar ratio of 1.35 at 0 °C. Sodium dodecylbenzenesulfonate (SDBS) was used as the surfactant (0.12 M) and the reaction mixture was kept undisturbed at 0 °C for 36 h45 The polyaniline (emaraldine HCl salt) powder precipitate obtained was filtered and washed with water and methanol to remove excess acids and by products from polymerization. Resulting powder was dried in vacuum oven at 60 °C for 24 h. The reaction conditions were varied as given in Table 1 to observe their effects on the formation of polyaniline and its EMI shielding property. In the reaction process, the acidity of the reaction mixture was increased by replacing water with 1 M HCl and temperature at which reaction was kept stable was changed from 0 °C to room temperature (25–30 °C). The surfactant was also removed and the stable condition was changed to stirring for 36 h to analyze its effects. As well as the APS to aniline hydrochloride molar ratio was varied from 1.35 to 1.15 and the reaction was kept at different time duration of 1–60 h.
Table 1 Reaction conditions and conductivity of prepared polyaniline nanofibers
No |
APS/aniline hydrochloride |
Solvent |
Temperature (°C) |
Surfactant |
Stirring |
Reaction time (hrs) |
Sample code |
Conductivity (S cm−1) |
1 |
1.35 |
Water |
0 |
0.12 SDBS |
No |
36 |
P1 |
0.06 |
2 |
1.35 |
1 M HCl |
0 |
0.12 SDBS |
No |
36 |
P2 |
1.50 |
3 |
1.35 |
1 M HCl |
RT (28) |
0.12 SDBS |
No |
36 |
P3 |
6.00 |
4 |
1.15 |
1 M HCl |
RT (28) |
0.12 SDBS |
No |
36 |
P4 |
11.00 |
5 |
1.35 |
1 M HCl |
RT (28) |
No |
No |
36 |
P5 |
10.00 |
6 |
1.15 |
1 M HCl |
RT (28) |
No |
No |
36 |
P6 |
18.50 |
7 |
1.35 |
1 M HCl |
RT (28) |
No |
Yes |
36 |
P7 |
7.50 |
8 |
1.15 |
1 M HCl |
RT (28) |
No |
Yes |
36 |
P8 |
14.50 |
9 |
1.15 |
1 M HCl |
RT (28) |
No |
No |
1 |
P9 |
9.00 |
10 |
1.15 |
1 M HCl |
RT (28) |
No |
No |
12 |
P10 |
10.70 |
11 |
1.15 |
1 M HCl |
RT (28) |
No |
No |
60 |
P11 |
15.00 |
The polymerization yield is found to depend on the reaction conditions. The polymerization yield increased from 78% (P1) to 81% (P2) when the acidity of the reaction mixture was increased, while the reaction temperature was kept fixed at 0 °C. The polymerization yield further increased to 85% with change in reaction temperature to room temperature (P3). However, with changing APS/aniline hydrochloride molar ratio from 1.35 to 1.15 (P4), the polymerization with the same reaction temperature of room temperature exhibits yield of 89%. The removal of surfactant further improves the polymerization yield to 91% for P5 and maximum yield of 95% is achieved for P6. It is found that higher yield can be achieved by unstirred polymerization, as P7 and P8 exhibit yield of 86% and 90% respectively. The polymerization yield obtained when duration of the reaction was varied to 1 (P9), 12 (P10), 60 (P11) hrs was 84%, 87% and 93% respectively. It is clear from these results that higher yields were obtained, as compared with 7–10% for interfacial polymerization,54 13.4–42.3% for rapid mixing polymerization and dilute polymerization.55,56
The morphology of the synthesized polyaniline structures was analyzed using Scanning Electron Microscope (SEM) (JEOL, JSM-5600LV, Tokyo, Japan) and Transmission Electron Microscope (TEM) (FEI Tecnai-G2 30S-TWIN, FEI Company, Hillsboro, OR). The phase purity of the polyaniline was measured using X-ray diffraction (XRD) pattern using CuKα radiation (X'Pert PRO MPD X-ray diffractometer, PANalytical, Almelo, Netherlands) and 1H NMR spectroscopic measurement was done using Bruker 500 MHz NMR spectrometer. The FTIR analysis was obtained by PerkinElmer spectrum two IR spectrometer and UV-vis absorption spectrum by Shimadzu 3600 UV-vis-NIR spectrophotometer. The EMI shielding measurements were performed by waveguide method using vector network analyzer (Agilent Technologies E5071C, ENA series, 300 kHz to 20 GHz, CA) from the magnitude of complex scattering parameters S11 and S12. The obtained polyaniline powders were pressed into 1 mm thick samples of dimension 22.86 × 10.8 mm for X band (8.2–12.4 GHz) and 15.80 × 7.90 mm for Ku band (12.4–18 GHz) frequency range measurements. The DC conductivity of the samples was measured using four probe method from the current and voltage relationships using current source Aplab 9710 P and nanovoltmeter Keithley 2182 A using the same samples used for X band shielding measurements.
3. Results and discussion
The reaction conditions play a vital role in the morphology and properties of polyaniline. Scheme 1 represents the polymerization of polyaniline by the oxidation of aniline hydrochloride by ammonium persulfate (APS) and the products obtained during various reaction conditions. The different reaction conditions and the product designation of the obtained polyaniline structures are depicted in Table 1.
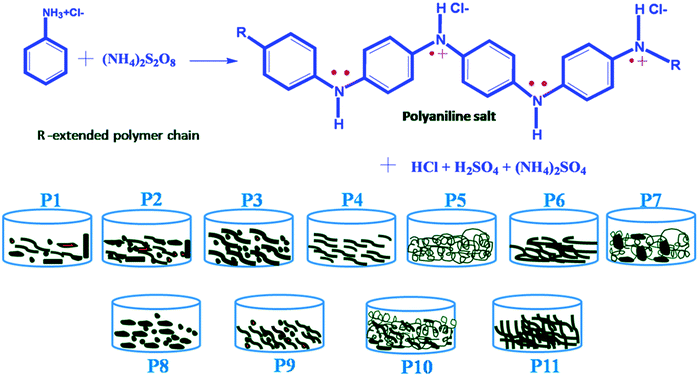 |
| Scheme 1 Polymerization of aniline monomer by ammonium persulfate yielding polyaniline emaraldine salt of varying morphology. | |
3.1 Morphology
3.1.1 Effect of reaction medium. The polyaniline morphology appears to be affected by the solvent used in the polymerization process. Non-uniform agglomerated fibers (P1) of varying sizes along with granular and rod structures are observed for polymerization carried out in water medium (Fig. 1(a)). A change in the morphology is observed for 1 M HCl (P2) with some polyaniline tubes also obtained along with fibers, rods and particles as depicted in Fig. 1(b). The fibrillar polymer growth is found to be enhanced with 1 M HCl, since the quality and uniformity of polyaniline is affected by the acid concentration in the aqueous phase.36
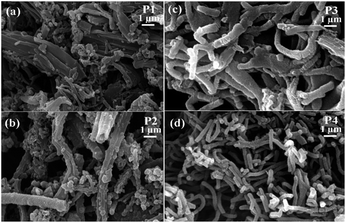 |
| Fig. 1 SEM images of synthesized (a) P1 (b) P2 (c) P3 and (d) P4 powders. | |
The lower the acid concentration, the lower the amount of nanofibers obtained in the final product. A decrease in the acid concentration leads to an increase in the granular particles over the nanofibers which are clear from Fig. 1(a) and (b). Aniline monomer themselves is considered as molecular templates for the growth of polyaniline nanofibers which is further enhanced by the increase in acid concentration.57 The HCl which is a strong polar solvent may play an important role in connecting the polyaniline particles leading to the self-assembled fiber structure by suppressing secondary growth.46 The obtained fibers are non-uniform with average diameter less than 1 μm.
3.1.2 Effect of reaction temperature. The nucleation behaviour of polyaniline depends on the polymerization rate and hence is temperature sensitive.46 At lower temperature of 0 °C, the new nuclei will more likely to create heterogeneous nuclei which induce aggregation. Hence granular particles could be obtained and is evident in the SEM images given in Fig. 1(a) and (b). Excessive active centres and quick reaction rate in the reaction process is achieved with increase in temperature (P3) which in turn leads to higher transient concentration. Hence nanofibrous structure of polyaniline with average diameter of 750 nm is obtained as shown in Fig. 1(c). The nanofibers are found to be more uniform in size and appearance with fewer particle aggregates, when polymerization is carried out at room temperature (28 °C).
3.1.3 Effect of oxidant monomer molar ratio. The monomer to oxidant ratio has significant effect on the morphology of synthesized polyaniline. Nanofibers with more uniform diameter of about 500 nm and shorter length (nanorods) are obtained with change of oxidant monomer molar ratio from 1.35 to 1.15 (P4) as depicted in Fig. 1(d). The obtained nanofibers look similar both in size and uniformity. Granular particles will be formed when ammonium persulfate (oxidant) content is low due to insufficient activation centres which results in secondary nucleation. High oxidant content leads to excess active centres which hinder one dimensional growth and coral like aggregates are formed. The oxidant monomer molar ratio of 1.15 and 1.35 can yield polyaniline nanofibers as evident from the SEM images Fig. 1(c) and (d) respectively.
3.1.4 Effect of surfactant. Fine fibrous structure of polyaniline with smaller diameter and clean surfaces are obtained with the removal of surfactant for both molar ratios as shown in Fig. 2(a) and (b) (P5 and P6). The obtained nanofibers are more uniform in diameter than those with surfactant.
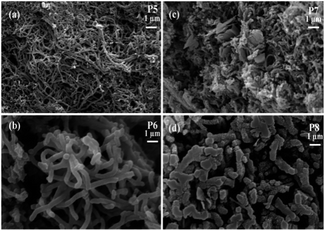 |
| Fig. 2 SEM images of synthesized (a) P5 (b) P6 (c) P7 and (d) P8 powders. | |
This may be due to the presence of some amount of surfactant on the surface of nanofibers which deteriorates its quality. The average diameter of nanofibers obtained are 100 and 200 nm respectively for oxidant monomer molar ratio of 1.35 (P5) and 1.15 (P6). The nanofibers synthesized with oxidant to monomer molar ratio of 1.15 have good uniformity in diameter and are found to be interconnected to form branched structures. The formation of nanofibers synthesized with oxidant monomer ratio 1.35 is found to be incomplete. There are regions of coagulation along with some particles as evident from the SEM image (Fig. 2(a)), which indicate that the formation of polyaniline nanofibers is not uniform.
3.1.5 Effect of stirring. The stable preparation condition is varied by providing a constant stirring of 600 rpm for 36 h and is found to have affected the morphology of polyaniline nanofibers for both molar ratios (P7 and P8). Fibrous morphology appears to be destroyed with stirring and hence broken fibers are obtained for both molar ratios (1.35 and 1.15) as evident from Fig. 2(c) and (d) respectively. Mechanical shear force leads to the collision of initial nanofibers inducing heterogeneous nucleation resulting to the loss of fibrillar morphology.58The TEM images of the polyaniline obtained by varying the reaction conditions are given in Fig. 3, which gives the morphology of obtained polyaniline (PANI) rods, tubes and fibers. PANI rods shown in Fig. 3(a) are of shorter in length and are obtained with oxidant monomer molar ratio of 1.15 at room temperature for reaction time of 36 h in the presence of surfactant (P4). The PANI tube (Fig. 3(b)) with tubular morphology is observed with increase in the acidity of the reaction medium for oxidant monomer molar ratio of 1.35 at 0 °C (P2). The PANI fiber depicted by the TEM image given in Fig. 3(c) is synthesized with oxidant monomer molar ratio of 1.15 (P6) at room temperature for reaction time of 36 h without any surfactant. On the other hand, the PANI fiber (P3) synthesized with oxidant monomer molar ratio of 1.35 at room temperature for reaction time of 36 h in the presence of surfactant is depicted in the Fig. 3(d). The diameter of these two PANI fibers is different and was synthesized at different reaction conditions.
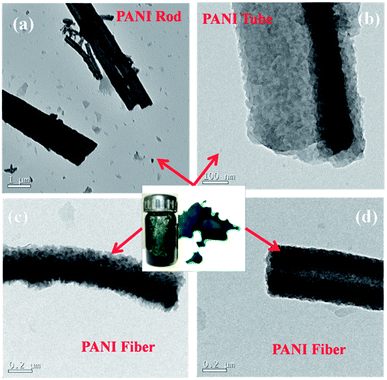 |
| Fig. 3 TEM images of synthesized polyaniline structures. | |
3.1.6 Effect of reaction time. The reaction time is found to play an important role to obtain high quality uniform sized nanofibers. The reaction time of the reaction process with molar ratio 1.15 is varied for 1, 12 and 60 h (P9, P10, P11) and is found to influence the morphology significantly as shown in Fig. 4(a)–(c) respectively. It can be found that the diameter of nanofibers obtained is not uniform for 1 h and 12 h of reaction time, while that for 60 h no significant improvement is observed. Thus reaction time of 36 h is observed to be ideal to obtain uniform nanofibers (P6). The fractured surface of uniaxially pressed rectangular sheet of polyaniline nanofibers (P6) is shown in Fig. 4(d) which clearly reveals that the fibrous morphology is maintained after pelletization. Uniform sized nanofibers are obtained without using any structural directing molecules at room temperature due to the combined effect of various reaction conditions. The acid complexes with the monomer to form micelles that guide the self-assembled growth of nanofibers formed at the initial stage of polymerization. The room temperature facilitates the reaction process while the stable condition promotes the growth of fibers which all leads to the suppression of secondary growth of polyaniline yielding uniform polyaniline nanofibers.59
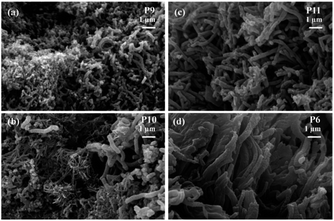 |
| Fig. 4 SEM images of (a) P9 (b) P10 (c) P11 powders and (d) fractogram of the sheet of P6. | |
3.2 Structural characterization
The crystallinity and orientation of conducting polymers are of great interest, as highly ordered systems have a metallic conductive state. X-ray diffraction pattern of metallic polyaniline consist of three peaks at 2θ values of 15°, 20° and 25°.60 The XRD of the synthesized polyaniline nanofibers (Fig. 5(a)) also has three peaks at 2θ values of 15°, 20° and 25° indicating the crystallinity of the obtained nanofibers. The peaks centred at 20° and 25° respectively correspond to the periodicities parallel and perpendicular to the polymer chain. The peak at 2θ of 25° indicates the formation of doped polyaniline nanofibers since this peak is the characteristic of highly doped emaraldine salt of polyaniline.61 The formation of doped polyaniline nanofibers is also evident from the spectroscopic studies. The 1H NMR spectrum of P6 in DMSO-d6 is shown in the Fig. S1 (ESI†). The solvents resonate at 2.5 ppm from the residual d6 and the polyaniline nanofibers (emaraldine salt) resonate at 7.01, 7.11, 7.22 ppm due to the presence of proton on phenylene and distributed phenylene units.62
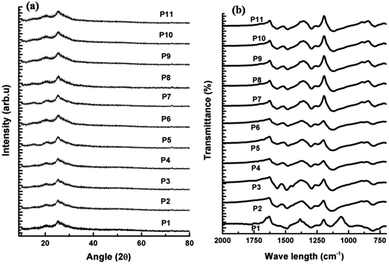 |
| Fig. 5 (a) XRD and (b) FT-IR spectra of synthesized polyaniline nanofibers at various reaction conditions. | |
The FTIR spectra of the obtained polyaniline nanofibers are depicted in the Fig. 5(b). The band at 804 cm−1 confirms the para-coupling structure of the polymer as it correspond to the out of plane deformation of C–H in the 1,4-di substituted benzene ring, which is identical to emaraldine salt of polyaniline.63,64 The band around 1300 cm−1 correspond to C–N stretching of secondary aromatic amine. The band characteristic of conducting protonated polyaniline is found at 1240 cm−1, which corresponds to π electron delocalization induced in the polymer by protonation. The characteristic absorption peaks around 1490 cm−1 and 1560 cm−1 are attributed to the C
C stretching mode of benzenoid (B–NH–B) and quinonoid (–N
Q
N) rings respectively.65–67 The band observed at 1140 cm−1 of P1 corresponds to C–H flexural vibration of aromatic ring and is associated with the high degree of electron delocalization which is the characteristic of conducting polyaniline. This peak shifts to lower frequency of around 1120 cm−1 for all other polyaniline nanofibers indicating their high doping degree due to the increased concentration of HCl during their synthesis.64,46 These results agree with the conductivity and EMI shielding properties of these nanofibers and are higher than that of P1. The solid state absorption spectra depicted in Fig. 6(a) reveals the emaraldine state of obtained nanofibers with two prominent bands attributed to the π–π* transition and charge transfer exciton transition formed in a benzenoid ring with its adjacent quinoid ring.31 The protonated emaraldine form of obtained polyaniline nanofibers is confirmed by the presence of three distinct bands in the absorption spectra of P6 in DMSO given in Fig. 6(b). The additional absorbance at 410 nm corresponds to polaron–π* transition is the characteristic of emaraldine salt of polyaniline suggesting the presence of polaronic concentration.33,68 These polarons interact effectively with the incident EM radiation leading to the good EMI shielding properties of obtained polyaniline nanofibers as shown in Fig. 6(c).
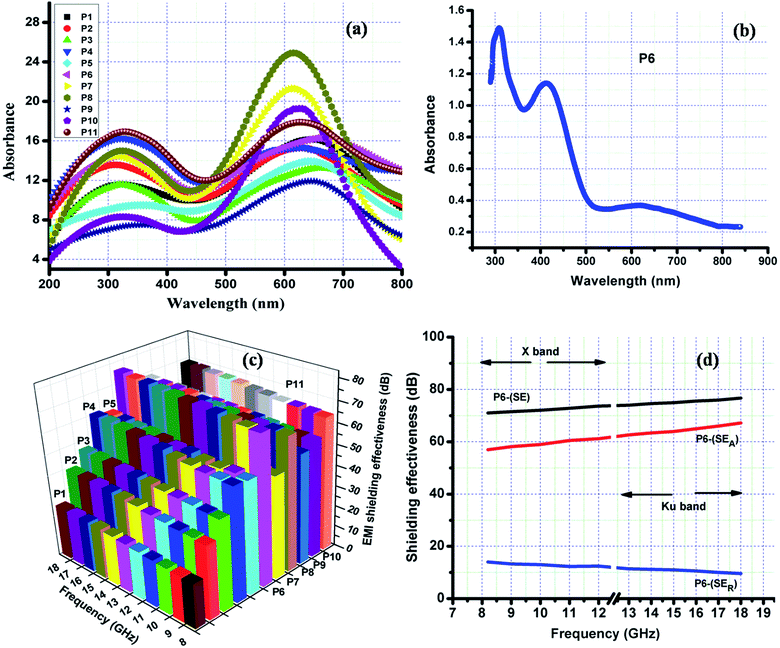 |
| Fig. 6 (a) Solid state UV-vis spectra of polyaniline nanofibers (b) absorbance spectrum of P6 in DMSO, frequency dependence of (c) SE of synthesized polyaniline nanofibers and (d) SE, SEA and SER of P6 in the frequency range of 8.2–18 GHz. | |
3.3 Conductivity and EMI shielding effectiveness
The conductivity of the synthesized polyaniline structures are given in Table 1. It is observed that the synthesis conditions had a considerable effect on the conductivity of the synthesized polyaniline structures. The electrical conductivity increases from 0.06 S cm−1 (P1) to 1.5 S cm−1 (P2) with change in reaction medium from water to 1 M HCl. Conductivity of 6 S cm−1 is obtained when polymerization temperature is increased from 0 °C to room temperature (P3). Change of molarity further improves the conductivity and increases to 11 S cm−1 (P4) with change in oxidant monomer molar ratio from 1.35 to 1.15 at room temperature. Conductivity of 10 S cm−1 (P5) and 18.5 S cm−1 (P6) is achieved by the removal of surfactant for oxidant monomer molar ratio of 1.35 and 1.15 respectively. The conductivity is found to be decreased with stirring as well as with change of reaction time. These results conclude that all these polyaniline structures exhibit high conductivity which can provide good EMI shielding properties69 and is evident from Fig. 6(c).
The electromagnetic interference (EMI) shielding effectiveness (SE) is the measure of shielding against the penetration of electromagnetic radiation into a material. It includes the measure of power lost due to absorption (absorption shielding effectiveness (SEA)) and reflection by the material (reflection shielding effectiveness (SER)) during transmission. It is given as EMI shielding effectiveness
SEA (dB) = −10 log[(S212)/(1 − S112)] |
SER (dB) = −10 log(1 − S112), |
where S11 and S12 are the magnitude of scattering parameters.
70,71
The frequency variation of the SE of polyaniline nanofibers in the X and Ku band frequency range (8.2–12.4 & 12.4–18 GHz) is given in the Fig. 6(c). It is found that the shielding effectiveness is greatly influenced by the synthesis conditions. The polyaniline synthesized with monomer oxidant molar ratio of 1.35, stable for 36 h at 0 °C with water as reaction medium (P1) has average SE of 23 dB and increases to 38 dB with 1 M HCl medium (P2) over the measured frequency range. This increase in the shielding effectiveness is due to the dual advantage provided by the increase in acid concentration. It enhances nanofibrillar morphology of the polymer resulting in the larger amount of nanofibers. Polymerization proceeds faster in the presence of excess 1 M HCl i.e. at higher acidity than in its absence and serves as the anion dopants to yield a product of enhanced conductivity.72 An increase in the shielding effectiveness is observed with change in the reaction temperature from 0 °C to room temperature (P3) and average SE of 45 dB is obtained. An increase in the rate of reaction with increase in temperature leads to the formation of more nanofibers. The formed nanofibers provide connectivity for the charge carries which improves the conductivity and thus enhance the shielding property.
The change of oxidant to monomer molar ratio to 1.15 (P4) leads to further increase in the average SE to 58 dB in the X and Ku band frequency range. This may be due to the formation of increased amount of uniform sized nanofibers with good conductivity at this molar ratio. The removal of surfactant further improves the shielding efficiency and average SE for molar ratio 1.35 increases from 45 dB of P3 to 56 dB for P5, while that for 1.15 molar ratio the increase is from 58 dB of P4 to 74 dB (P6) in this frequency range. This can be attributed to the formation of more uniform polyaniline nanofibers without surfactants and presence of trace amount of surfactant on the surface of nano fibers may also degrade their conducting property.
The shielding effectiveness of P7 and P8 at the measured frequency range indicates that stirring for 36 h degrades the shielding property. This is due to the damage of fibrillar morphology by stirring as clear from Fig. 2(c) and (d) which leads to the decrease in conductivity as. All the observed results indicate that among all the synthesized polyaniline fiber structures, P6 which is the surfactant free polyaniline with good morphology of uniform sized nanofibers (Fig. 2(b) and 4(d)) has good shielding effectiveness. This polyaniline is obtained by keeping the reaction stable for 36 h at room temperature in excess of 1 M HCl with 1.15 oxidant to monomer molar ratio as given in the Table 1. The effect of reaction time on the SE is analyzed by varying the reaction time of P6 and found that the reaction time also influences the shielding property of polyaniline structures. The P9 is found to have low shielding effectiveness than P10 at this frequency range. This is due to non-uniform polyaniline nanofibers obtained for 1 h and 12 h of reaction time (Fig. 4(a) and (b)). The 60 h reaction time slightly decrease the shielding effectiveness and average SE of 67 dB is obtained in the 8.2–18 GHz frequency range. The SE of all the obtained polyaniline nanofibers shows a slightly increasing trend with frequency due to the increase in the conductivity with frequency.73
The total shielding effectiveness is the combined effect of SEA and SER. The frequency dependence of SE, SEA and SER of P6 over the X and Ku band frequency range is shown in Fig. 6(d). The SE of P6 is almost independent of frequency with slightly increasing trend and varies from 71–77 dB. Hence it can provide a broad band width for shielding. The SEA is showing an increasing trend with frequency and increases from 57–67 dB in the measured frequency range. A decreasing trend with frequency is observed for SER and varies from 14–10 dB in the 8.2–18 GHz frequency range indicating that the dominant shielding mechanism is absorption. All other synthesized polyaniline structures also follows similar trend with absorption as the dominant shielding mechanism. Thus uniform sized polyaniline nanofibers with excellent shielding property are obtained which can prove to be potential candidates for EMI shielding applications.
4. Conclusion
Polyaniline nanofibers were synthesized by chemical oxidation of aniline hydrochloride by ammonium persulfate. The effect of solvent, temperature, surfactant, stirring, reaction time, and oxidant to monomer molar ratio on the morphology and EMI shielding properties of polyaniline nanofibers were investigated to generate nanofibers of good morphology with excellent shielding properties. Based on the results it was observed that these reaction conditions greatly influence the morphology and EMI shielding property of synthesized polyaniline nanofibers. Uniform polyaniline nanofibers of average diameter 200 nm and EMI shielding effectiveness of 71–77 dB was obtained in the frequency range of 8.2–18 GHz. This polyaniline nanofiber was synthesized by a simple surfactant free room temperature oxidation of aniline hydrochloride by ammonium persulfate at stable condition for 36 h with oxidant to monomer molar ratio of 1.15 in an excess of 1 M HCl. Hence a simple, economic, scalable and environmentally friendly synthesis method is achieved to attain uniform nanofibers with attracting EMI shielding properties which elucidates the difficulties in other tedious nanofiber synthesis methods.
Notes and references
- N. Joseph, S. K. Singh, R. K. Sirugu du, V. R. K. Murthy, S. Ananthakumar and M. T. Sebastian, Mater. Res. Bull., 2013, 48, 1681 CrossRef CAS; H. A. Reshi, A. P. Singh, S. Pillai, R. S. Yadav, S. K. Dhawan and V. Shelke, J. Mater. Chem. C, 2015, 3, 820 RSC.
- D. A. Weston, Electromagnetic Compatibility: Principles and Applications, Marcel Dekker, New York, 2001 Search PubMed; X. C. Tong, Advanced Materials and Design for Electromagnetic Interference Shielding, CRC Press, United States, 2009 Search PubMed.
- Y. Wang and X. Jing, Polym. Adv. Technol., 2005, 16, 344 CrossRef CAS.
- K. Ghanbari, M. F. Mousavi and M. Shamsipur, Electrochim. Acta, 2006, 52, 1514 CrossRef CAS.
- C. Y. Wang, V. Mottaghitalab, C. O. Too, G. M. Spinks and G. G. Wallace, J. Power Sources, 2007, 163, 1105 CrossRef CAS.
- A. Bhattacharya and A. De, Prog. Solid State Chem., 1996, 24, 141 CrossRef CAS.
- T. Taka, Synth. Met., 1991, 41, 1177 CrossRef CAS.
- J. Unsworth, B. A. Lunn, P. C. Innis, Z. Jin, A. Kaynak and N. G. Booth, J. Intell. Mater. Syst. Struct., 1992, 3, 380 CrossRef.
- M. Angelopoulos, IBM J. Res. Dev., 2001, 45, 57 CrossRef CAS.
- R. Gangopadhyay and A. De, Sens. Actuators, B, 2001, 77, 326 CrossRef CAS.
- H. Liu, J. Kameoka, D. A. Czaplewski and H. G. Craighead, Nano Lett., 2004, 4, 671 CrossRef CAS.
- T. Kobayashi, H. Yaneyama and H. Tamura, J. Electroanal. Chem., 1984, 161, 419 CrossRef CAS.
- E. W. Paul, A. J. Ri cco and M. S. Wrighton, J. Phys. Chem., 1985, 89, 1441 CrossRef CAS.
- P. Chandrasekhar, Conducting Polymers, Fundamentals and Applications: A Practical Approach, Kluwer Academic, Netherlands, 1999 Search PubMed.
- T. A. Skotheim, R. L. Elsenbaumer and J. R. Reynolds, Handbook of Conducting Polymers, Marcel Dekker, New York, 1998 Search PubMed.
- G. Cao, Nanostructures and Nanomaterials: Synthesis, Properties, and Applications, Imperial College Press, London, 2004 Search PubMed.
- A. Kaynak, Mater. Res. Bull., 1996, 31, 845 CrossRef CAS.
- J. Joo, Appl. Phys. Lett., 1994, 65, 2278 CrossRef CAS.
- P. Alexander, N. Ogurtsov, A. Korzhenko and G. Shapoval, Prog. Polym. Sci., 2003, 28, 1701 CrossRef.
- N. Gospodinova and L. Terlemezyan, Prog. Polym. Sci., 1998, 23, 1443 CrossRef CAS.
- L. Zhang, M. Wan and Y. Wei, Macromol. Rapid Commun., 2006, 27, 366 CrossRef CAS.
- D. Chen, Y. E. Miao and T. Liu, ACS Appl. Mater. Interfaces, 2013, 5, 1206 CAS.
- D. K. Moon, M. Ezuka, T. Maruyama, K. Osakada and T. Yamamoto, Macromolecules, 1993, 26, 364 CrossRef CAS.
- P. M. McManus, R. J. Cushman and S. C. Yang, J. Phys. Chem., 1987, 91, 744 CrossRef CAS.
- S. Bhadra, D. Khastgir, N. K. Singha and J. H. Lee, Prog. Polym. Sci., 2009, 34, 783 CrossRef CAS.
- S. Sivaram, Polymer Science Contemporary Themes, Tata McGraw-Hill, India, 1991 Search PubMed.
- M. Aldissi, Intrinsically Conducting Polymers: An Emerging Technology, Kluwer
Academic, Netherlands, 1993 Search PubMed.
- Y. Chen, E. T. Kang, K. G. Neoh, C. H. Wang and K. L. Tan, Synth. Met., 2000, 110, 47 CrossRef CAS.
- C. H. Wang, Y. Q. Dong, K. Sengothi, K. L. Tan and E. T. Kang, Synth. Met., 1999, 102, 1313 CrossRef CAS; T. A. Skotheim and J. R. Reynolds, Handbook of Conducting Polymers Third Edition: Conjugated Polymers−Processing and Applications, CRC Press, United States, 2007 Search PubMed.
- M. A. Dar, R. K. Kotnala, V. Verma, J. Shah, W. A. Siddiqui and M. Alam, J. Phys. Chem. C, 2012, 116, 5277 CAS.
- P. Saini, V. Choudhary, B. P. Singh, R. B. Mathur and S. K. Dhawan, Mater. Chem. Phys., 2009, 113, 919 CrossRef CAS.
- P. Saini and M. Arora, J. Mater. Chem. A, 2013, 1, 8926 CAS.
- A. P. Singh, M. Mishra, P. Sambyal, B. K. Gupta, B. P. Singh, A. Chandra and S. K. Dhawn, J. Mater. Chem. A, 2014, 2, 3581 CAS.
- R. R. Mohan, S. J. Varma, M. Faisal and S. Jayalekshmi, RSC Adv., 2015, 5, 5917 RSC; P. Sambyal, A. P. Singh, M. Verma, M. Farukh, B. P. Sinngh and S. K. Dhawan, RSC Adv., 2014, 4, 12614 RSC.
- D. H. Zhang and Y. Y. Wang, Mater. Sci. Eng., B, 2006, 134, 9 CrossRef CAS.
- J. Huang and R. B. Kaner, J. Am. Chem. Soc., 2004, 126, 851 CrossRef CAS PubMed.
- C. G. Wu and T. Bein, Science, 1994, 17, 1757 Search PubMed.
- C. R. Martin, Science, 1994, 23, 1961 Search PubMed.
- R. V. Parthasarathy and C. R. Martin, Chem. Mater., 1994, 6, 1627 CrossRef CAS.
- H. Dong, S. Prasad, V. Nyame and W. E. Jones Jr, Chem. Mater., 2004, 16, 371 CrossRef CAS.
- Z. Zhang, Z. Wei and M. Wan, Macromolecules, 2002, 35, 5937 CrossRef CAS.
- W. Li and H. L. Wang, J. Am. Chem. Soc., 2004, 126, 2278 CrossRef CAS PubMed.
- G. Li and Z. Zhang, Macromolecules, 2004, 37, 2683 CrossRef CAS.
- G. Li, H. Peng, Y. Wang, Y. Qin, Z. Cui and Z. Zhang, Macromol. Rapid Commun., 2004, 25, 1611 CrossRef CAS.
- G. Li, S. Pang, J. Liu, Z. Wang and Z. Zhang, J. Nanopart. Res., 2006, 8, 1039 CrossRef CAS.
- R. Li, Z. Chen, J. Li, C. Zhang and Q. Guo, Synth. Met., 2013, 171, 39 CrossRef CAS.
- X. Zhang, W. J. Goux and S. K. Manohar, J. Am. Chem. Soc., 2004, 126, 4502 CrossRef CAS PubMed.
- N. R. Chiou and A. J. Epstein, Adv. Mater., 2005, 17, 1679 CrossRef CAS.
- J. Li, H. Tang, A. Zhang, X. Shen and L. Zhu, Macromol. Rapid Commun., 2007, 28, 740 CrossRef CAS.
- S. K. Pillalamarri, F. D. Blum, A. T. Tokuhiro, J. G. Story and M. F. Bertino, Chem. Mater., 2005, 17, 227 CrossRef CAS.
- X. L. Jing, Y. Y. Wang, D. Wu and J. P. Qiang, Ultrason. Sonochem., 2007, 14, 75 CrossRef CAS PubMed.
- M. R. G. Nikolaidis, D. R. Stanisavljev, A. J. Easteal and Z. D. Zujovic, Macromol. Rapid Commun., 2010, 31, 657 CrossRef PubMed.
- Y. Yao, E. Metwalli, J. F. Moulin, B. Su, M. Opel and P. Müller-Buschbaum, ACS Appl. Mater. Interfaces, 2014, 6, 18152 CAS.
- J. X. Huang, S. Virji, B. H. Weiller and R. B. Kaner, J. Am. Chem. Soc., 2003, 125, 314 CrossRef CAS PubMed.
- N. R. Chiou and A. J. Epstein, Synth. Met., 2005, 153, 69 CrossRef CAS.
- N. R. Chiou and A. J. Epstein, Adv. Mater., 2005, 73, 1679 CrossRef.
- N. R. Chiou, L. J. Lee and A. J. Epstein, Chem. Mater., 2007, 19, 3589 CrossRef CAS.
- D. Li and R. B. Kaner, J. Am. Chem. Soc., 2006, 128, 968 CrossRef CAS PubMed.
- H. D. Tran, J. M. D'Arcy, Y. Wang, P. J. Beltramo, V. A. Strong and R. B. Kaner, J. Mater. Chem., 2011, 21, 3534 RSC.
- K. Lee, S. Cho, S. H. Park, C. Heeger, W. Lee and S. H. Lee, Nature, 2006, 441, 65 CrossRef CAS PubMed.
- J. P. Pouget, M. E. Jozefowicz, A. J. Epstein, X. Tang and A. G. MacDiarmid, Macromolecules, 1991, 24, 779 CrossRef CAS.
- M. Shaolin and Y. Yang, J. Phys. Chem. B, 2008, 112, 11558 CrossRef PubMed.
- Y. Zhu, J. Li, H. He, M. Wan and L. Jiang, Macromol. Rapid Commun., 2007, 28, 2230 CrossRef CAS.
- H. Ding, J. Shen, M. Wan and Z. Chen, Macromol. Chem. Phys., 2008, 209, 864 CrossRef CAS.
- S. R. C. Vivekchand, K. C. Kam, G. Gundiah, A. Govindaraj, A. K. Cheetham and C. N. R. Rao, J. Mater. Chem., 2005, 15, 4922 RSC.
- H. R. Tantawy, D. E. Aston, J. R. Smith and J. L. Young, ACS Appl. Mater. Interfaces, 2013, 5, 4648 CAS.
- N. K. Guimard, N. Gomez and C. E. Schmidt, Prog. Polym. Sci., 2007, 32, 876 CrossRef CAS.
- C. C. Yang, Y. J. Gung, W. C. Hung, T. H. Ting and K. H. Wu, Compos. Sci. Technol., 2010, 70, 466 CrossRef CAS.
- R. Ramasubramaniam, J. Chen and H. Liu, Appl. Phys. Lett., 2003, 83, 2928 CrossRef CAS.
- D. Annapurna and K. D. Sisir, Microwave Engineering, Tata McGraw Hill, India, 2009 Search PubMed.
- N. Joseph and M. T. Sebastian, Mater. Lett., 2013, 90, 64 CrossRef CAS.
- J. Stejskal, I. Sapurina, J. Prokeš and J. Zemek, Synth. Met., 1999, 105, 195 CrossRef CAS.
- D. D. L. Chung, Carbon, 2001, 39, 279 CrossRef CAS.
Footnote |
† Electronic supplementary information (ESI) available: 1H NMR spectroscopy of P6 in DMSO-d6. See DOI: 10.1039/c5ra02113h |
|
This journal is © The Royal Society of Chemistry 2015 |