DOI:
10.1039/C5RA00739A
(Paper)
RSC Adv., 2015,
5, 23530-23539
A pH-responsive PVDF membrane with superwetting properties for the separation of oil and water
Received
13th January 2015
, Accepted 16th February 2015
First published on 16th February 2015
Abstract
Responsive materials with surfaces that have controllable oil wettability under water offer considerable potential in advanced applications. We have developed an economical and convenient method for constructing a superwetting polyvinylidene fluoride (PVDF) membrane, giving super-hydrophobicity under oil and super-oleophobicity under water. The membrane has been achieved by incorporating pH-responsive N,N-dimethylaminoethylmethacrylate (DMAEMA) hydrogels into PVDF using a combination of in situ polymerization and conventional phase separation. In pure or acidic water the poly-DMAEMA chains modify wettability by the protonation or deprotonation of their tertiary amine side-groups, affecting the wettability of the membrane under water. In addition, this responsive membrane has been utilized for the separation of surfactant-stabilized water-in-oil and oil-in-water emulsions. High flux and separation efficiency can be obtained, together with excellent antifouling properties, suggesting that the membranes will find wide application in the separation of oil and water systems.
1. Introduction
Stimulus-responsive polymers have attracted wide attention over recent decades and have been closely studied due to their potential in materials offering intelligent control.1 The injection of water into oil fields, the occurrence of oil spills in sea water, and the wastewater generated in machining are examples of long-term adverse impacts, not only in the marine and land environments but also on aquatic ecosystems.2–4 The elimination of oil spills in sea water is currently a worldwide challenge, and functional materials that can effectively assist the separation of oil and water are attracting wide attention.5–7 It is anticipated that a responsive surface able to change its wettability in contact with aqueous media in response to an external stimulus such as light,8,9 an electric field,1 temperature10 or pH,11,12 would offer considerable promise in the separation of oil and water. Although considerable efforts have been devoted to the control of oil wettability and its adhesion to surfaces under water, a feasible method of producing responsive materials with switchable super-oleophilicity (oil contact angle below 10°) and super-oleophobicity (oil contact angle above 150°) under water is still required.
Felix Schacher's group have constructed a double stimulus-responsive membrane using polystyrene-block-poly(N,N-dimethylaminoethylmethacrylate) copolymers.13 In these, water flux, pore size and separation properties respond to two independent stimuli (pH and temperature), but further applications have not been reported, probably due to the long-term instability of the copolymer under aggressive aqueous conditions. This stimulus-responsive material has recently been coated on a stainless steel mesh to enable the separation of oil and water.14 However, the mesh is limited to a pore size below 40 μm and can only deal with free oil and water mixtures; it is unsuitable for the separation of emulsions, particularly in the presence of surfactants.
A surface with switchable super-oleophilicity and super-oleophobicity in aqueous media has also been realized on textiles and sponges by grafting the pH-responsive block copolymer, poly(2-vinyl-pyridine) with polydimethylsiloxane (P2VP-b-PDMS).15 The modified material shows selective permeation of water and oil due to the protonation and deprotonation of P2VP chains in response to the pH of the aqueous medium. However, the preparation of the material is difficult and time-consuming, and in addition the product is not capable of separating emulsified oil and water mixtures.
There have been few reports of superwetting PVDF membranes, with a responsive surface for the separation of surfactant-stabilized oil and water mixtures. We have however described an intelligent PVDF membrane able to separate both oil-in-water and water-in-oil emulsions.16 It is generally accepted that wettability is governed mainly by surface chemistry and the hierarchical structure of the surface.17–19 A hierarchical surface structure of a PVDF membrane was therefore created using a soft template stripping method to improve its superwettability, and the resulting membrane exhibits high permeability and excellent antifouling properties. However, the long-awaited environmentally responsive polymeric membrane remains an interesting and challenging issue for practical application.
We are now able to describe an economic and convenient method for constructing a PVDF membrane with the ability to switch between underwater super-oleophilicity and super-oleophobicity in response to a change in pH. The membrane shows excellent performance in treating either water-in-oil or oil-in-water emulsions. The membrane is prepared by a conventional non-solvent-induced phase separation technique, and pH response is provided by in situ crosslinking with N,N-dimethylaminoethylmethacrylate (DMAEMA) as monomer and triethoxyvinylsilane (VTES) as crosslinker. A soft template stripping method has been applied for generating an abundant surface microstructure.
2. Experimental
2.1 Materials
PVDF (FR904) was supplied by Shanghai 3F New Material Co. Ltd., China. DMAEMA, azodi-isobutyronitrile (AIBN), n-hexane and bovine serum albumin (BSA, for molecular biology) were purchased from Shanghai Aladdin Chemistry Co. Ltd., China. After passing through an inhibitor-removal column (alkaline Al2O3), the DMAEMA monomer was stored in a sealed clean vessel at 4 °C before use. The initiator, AIBN, was recrystallized from n-hexane to remove inhibitors. VTES, hydrochloric acid, N,N-dimethylacetamide (DMAC), chloroform, dichloromethane and toluene were obtained from Sinopharm Chemical Reagent Co. Ltd., China. High purity nitrogen was supplied by Wanli Gas of Ningbo, China. Unless specified, other chemical reagents were used as received.
2.2 Construction of a pH-responsive PVDF membrane
5.5 g DMAEMA, 1.0 g VTES and 0.08 g AIBN, 18 g PVDF and 130 g DMAC were charged into a 250 mL three-necked flask. Oxygen was eliminated by bubbling nitrogen through the solution for 30 min. Polymerization was then carried out under nitrogen at 80 °C for 18 h with vigorous stirring. The homogeneous casting solution was held overnight to remove residual air bubbles and then cast uniformly onto PET nonwoven fabric (NWF, 70 g m−2) using a casting knife with 200 μm gap. The nascent membrane was immediately immersed in a bath comprising a DMAC
:
water mixture (3
:
7 v/v) for 1 min, and then moved to a bath of pure water for 48 h to complete the solidification and to eliminate solvent and possible unreacted monomer, after which the PVDF membranes were dried in air. The membranes are referred to as PVDF–PDMAEMA.
2.3 Instruments and characterization
The morphology of the PVDF membrane and PET NWF were studied using a field-emission scanning electron microscope (S-4800, Hitachi, Japan), and the roughness of the membrane surface was determined by atomic force microscopy (AFM; Veeco Dimension 3100 V, USA) in tapping mode with silicone tip cantilevers exerting a constant force 20 mN cm−1. The mechanical properties of the membranes were measured on a tensile tester (5567, Instron, USA), and their chemical composition close to the lower surface was determined by X-ray photoelectron spectroscopy (XPS; Shimadzu Axis UltraDLD, Japan) with Mg–Kα as radiation resource. The take-off angle of the XPS was set to 90°. The functional groups on the lower membrane surface and the composition of the emulsions were measured by attenuated total reflectance Fourier transform infrared spectra (ATR-FTIR; Thermo-Nicolet 6700, USA). The content of PDMAEMA in the membrane was determined by thermo-gravimetric analysis (TGA; Mettler-Toledo, Switzerland) at 10 °C min−1 between 50 and 700 °C under nitrogen (20 mL min−1). Contact angles were measured using a OCA20 contact angle meter (Dataphysics, Germany), at least five measurements being taken at different locations on each sample. UV-VIS spectra were determined using a UV-VIS-NIR spectrometer (Lambda 950, PerkinElmer, USA). The purity of the purified filtrates was analyzed by Karl Fischer titrator (Mettler Toledo DL, Switzerland). Optical microscopy images were recorded on a BX 51 TF Instec H601 (Olympus, Japan). The pH of water and the BSA solution were determined using a model 8685 pH meter (China).
2.4 Preparation of water-in-oil and oil-in-water emulsions
For water-in-toluene (W/T), water-in-chloroform (W/C) and water-in-dichloromethane (W/DCM) emulsions, Span80 with a hydrophilic–lipophilic balance (HLB) of 4.3 was chosen as emulsifier, used with pure water. For toluene-in-water (T/W), chloroform-in-water (C/W) and dichloromethane-in-water (DCM/W) emulsions, Tween80 (Sigma-Aldrich) with HLB value of 15 was selected as emulsifier, and water acidified with hydrochloric acid at pH 2.0 (adjusted by hydrochloric acid) was used. The preparation method and the droplet size of the feed are summarized in Table 1 and the density and viscosity of the oils used in the study are listed in Table 2. The mixtures were stirred for 3 h to produce emulsions which were stable for at least 4 h, and no demulsification or precipitation was observed.
Table 1 Preparation method and droplet size of oil-in-water emulsions
Emulsion |
Toluene (mL) |
Chloroform (mL) |
Dichloromethane (mL) |
Span80 (g) |
Tween80 (g) |
Pure water (mL) |
Acid water (mL) |
Droplet size |
W/T |
80 |
— |
— |
0.135 |
— |
2 |
— |
500 nm to 10 μm |
W/C |
— |
80 |
— |
0.101 |
— |
2 |
— |
500 nm to 1 μm |
W/DCM |
— |
— |
80 |
0.070 |
— |
0.8 |
— |
500 nm to 1 μm |
T/W |
2 |
— |
— |
— |
0.081 |
— |
80 |
1 to 15 μm |
C/W |
— |
2 |
— |
— |
0.050 |
— |
80 |
100 nm to 1 μm |
DCM/W |
— |
— |
2 |
— |
0.065 |
— |
80 |
500 nm to 10 μm |
Table 2 Density and viscosity of the oils used in the study
Oil |
Density (g cm−3) |
Viscosity (mPa S) |
Toluene |
0.866 |
0.587 |
Chloroform |
1.498 |
0.563 |
Dichloromethane |
1.327 |
0.430 |
2.5 Water flux through the membranes
The pH-responsive PVDF membrane was sealed between a vertical glass tube of area 3.14 cm2 and a conical flask. A certain volume of water with different pH adjusted by hydrochloric acid was poured onto the membrane, and the flux measured under the vacuum (−0.09 MPa) generated by the laboratory filtration system. The flux was calculated from the permeation volume as a function of time. The water flux J (L m−2 h−1) is defined by eqn (1): |
 | (1) |
where V is the volume of permeated water (L), A the membrane area (m2) and Δt the permeation time (h).
2.6 Emulsion separation experiments
The apparatus and operating conditions are described above, in 2.5. After fixing the PVDF membrane a quantity of freshly prepared emulsion was poured onto it. The fluxes for the emulsions were determined by eqn (1). For each emulsion at least five samples were assessed to obtain an average, and the filtrate finally obtained was collected for evaluation of its purity. To determine the stability of the membrane for separation of oil-in-water emulsions, repeated emulsion separation experiments were conducted. After each experiment the membrane was washed with ethanol to remove possible deposited surfactant and dried in the oven at 40 °C.
2.7 Antifouling performance
Due to the complicated oil-in-water separation conditions, antifouling properties are very important in long-term membrane use. The PVDF membrane showed different hydrophilicity (closely related to antifouling performance), depending on the PDMAEMA chains being protonating or deprotonating in character. Antifouling experiments were therefore performed using acidified water (PDMAEMA chains in protonation state) or pure water (PDMAEMA chains in deprotonation state) or in 1.0 g L−1 BSA solution prepared from the corresponding water with the identical apparatus and operating conditions described in section 2.5. Initially, water was allowed to permeate through the membrane, then BSA solution prepared from the corresponding water was applied, and the flux (Jw1) and (JBSA) in L m−2 h−1 for water and BSA solution, respectively, were calculated using eqn (1). After filtration of the BSA solution, the membrane was rinsed with ethanol and water to recover the flux, then the water flux of the cleaned membrane Jw2 (L m−2 h−1) was again measured using eqn (1).
To analyze the antifouling property in detail, a number of ratios were defined. The flux recovery ratio (FRR) was calculated using eqn (2):
|
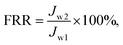 | (2) |
A higher value of FRR implying better antifouling properties of the membrane. The reversible fouling ratio (DRr) describes the flux decline caused by cake layer formation; the irreversible fouling ratio (DRir) indicates the non-recoverable flux decline induced by pore plugging and adsorption or deposition of foulants on membrane surface and pores, and the total fouling ratio (DRt) shows the total flux decline arising from the reversible and irreversible fouling. The three ratios may be expressed as follows:
|
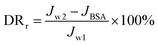 | (3) |
|
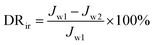 | (4) |
3. Results and discussion
3.1 Morphology of the pH-responsive PVDF membrane
In general, a rough surface is a prerequisite for achieving superwettability, particularly a hierarchically micro- or nano-structured surface which amplifies the intrinsic wetting behaviour of the surface.1,20–22 In the present case a nonwoven fabric was chosen as the soft template due to its low cost, easy availability and, importantly, its inherent concavo–convex rough surface, which provided the membrane with a unique micro- and nano-microporous structure. Scanning electron microscopy (SEM) measurements were carried out to investigate the membrane surface peeled off from the NWF, and also the inherent structure of the NWF, as shown in Fig. 1(a)–(c). The large number of irregular grooves about 10 μm in width endowed the membrane surface with considerable roughness. At higher magnification circular micropores of about 500 nm were observed. The thickness of the membrane was around 65 μm. Finger-like pores were totally absent and uniform cellular pores were generated, as shown in Fig. 1(d) and (e). On the upper surface of the membrane (Fig. 1(f)), a number of small white dots were present due to the surface segregation of PDMAEMA–VTES during the phase separation process.
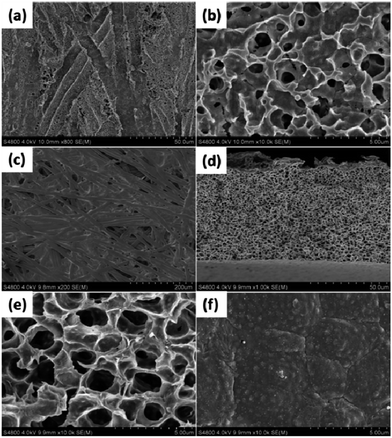 |
| Fig. 1 Characterization of the PVDF membrane and NWF. (a) and (b) SEM images of the PVDF membrane surface in contact with NWF; (c) SEM image of the NWF surface; (d) and (e) SEM images of the PVDF membrane cross-section; and (f) SEM images of the PVDF upper membrane surface. | |
AFM measurements were used to determine the roughness of the membrane surface. The results shown in Fig. 2 indicate that the new surface peeled off from NWF had an arithmetic mean surface roughness (Ra) of 940 nm, twice as high as that of the upper surface (Ra = 419 nm) directly in contact with non-solvent. In addition, the PVDF membrane exhibited good mechanical tensile strength (5.3 MPa) and elongation (14.4%), as shown in Fig. 3.
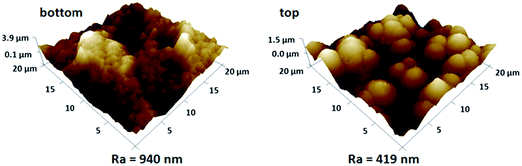 |
| Fig. 2 3D AFM images for PVDF membrane surfaces (20 μm × 20 μm). | |
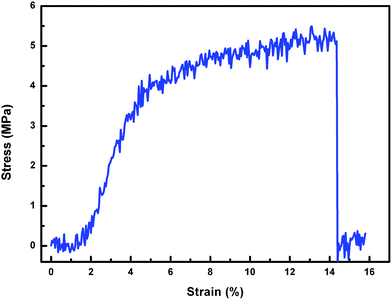 |
| Fig. 3 Stress–displacement curve of the membrane (sized at 5 cm × 1 cm). | |
3.2 Chemical composition of pH-responsive PVDF membrane
To confirm that the pH-responsive PDMAEMA was in fact blended with the PVDF membrane, pure PVDF membrane was constructed as control. The preparation method was similar to that in section 2.2, but without the functional monomer DMAEMA, crosslinking VTES or initiator AIBN. The XPS result is shown in Fig. 4(a) for the pure PVDF membrane, and signals at 284 and 686 eV ascribed to the elements carbon (C) and fluorine (F) are labelled. On the other hand, for the PVDF–PDMAEMA membrane, in addition to the elements C and F, signals representing oxygen (O), nitrogen (N) and silicon (Si) were additionally detected at 530, 396 and 154 eV, respectively, indicating that PDMAEMA, together with the crosslinker VTES, had been successfully blended and had migrated to some extent to the membrane surface.
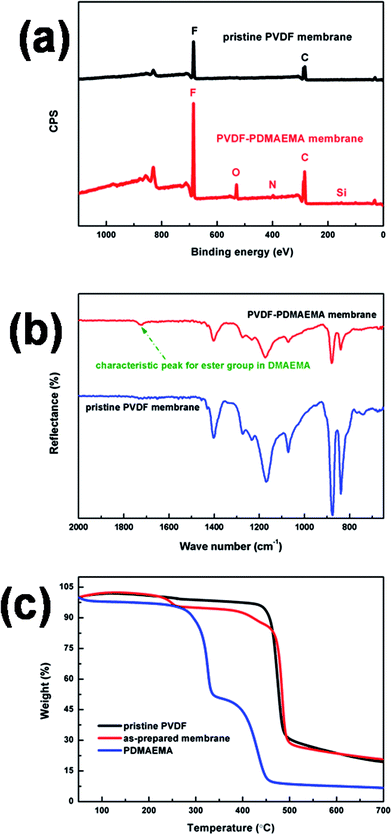 |
| Fig. 4 (a) Wide-scan XPS spectra and (b) FTIR-ATR spectra of the pure PVDF membrane and the PVDF–PDMAEMA membrane; (c) TGA curves for the newly synthesized PDMAEMA, pure PVDF membrane and the PVDF–PDMAEMA membrane. PDMAEMA was synthesized from 5.5 g DMAEMA and 0.08 g AIBN at 80 °C with vigorous stirring under nitrogen for 18 h. | |
According to the mass concentration of each of the elements listed in Table 3, the content of the pH-responsive PDMAEMA component in the membrane surface was calculated to be about 22 wt%. The characteristic peak in the FTIR-ATR spectrum at around 1721 cm−1, attributed to C
O stretching vibration in the ester group, also implied the presence of PDMAEMA, as shown in Fig. 4(b). TGA measurements were carried out to calculate the content of PDMAEMA in the membrane, and the result (Fig. 4(c)) showed that the membrane contained around 13 wt% of pH-responsive PDMAEMA. Compared to the XPS result, the difference in the values indicated significant migration of PDMAEMA to the surface of the membrane.
Table 3 Elemental analysis of the PVDF membrane by XPS
Element |
F |
O |
N |
C |
Si |
Atomic concentration (%) |
36.06 |
6.75 |
2.64 |
53.02 |
1.54 |
Mass concentration (%) |
45.36 |
7.15 |
2.44 |
42.17 |
2.87 |
3.3 Wettability of the pH-responsive PVDF membrane
The tunable wettability was investigated by measuring the contact angle of the PVDF membrane in aqueous media at different pH values, as shown in Fig. 5(a). An acidic water droplet with a pH of 2.0 gave a water contact angle (WCA) of about 76 ± 1° in air, but the WCA for a pure water droplet at pH 7.4 increased substantially to 126 ± 1°. The tunable wettability was closely related to the pH-responsive PDMAEMA chain conformation via protonation and deprotonation of the tertiary amine side-groups.23,24 The pKa of PDMAEMA was around 7.0. When the membrane surface made contact with an acidic water droplet at a pH of 2.0, the surface segregated PDMAEMA chains became protonated and exhibited an extended conformation due to electrostatic repulsion of like charges, and the membrane surface thus acquired a relatively hydrophilic character. On the other hand, when the membrane was in contact with a water droplet at pH 7.4, the PDMAEMA chains were deprotonated and adopted a collapsed conformation due to hydrophobic interaction between the deprotonated PDMAEMA chains. In this state, the water droplet was primarily in contact with hydrophobic PVDF chains, leading to a larger WCA. The PVDF membrane is naturally oleophilic, due to its lower surface tension. As soon as an oil (e.g. chloroform) droplet made contact with the membrane surface it immediately became spread out and the oil contact angle (OCA) decreased to 0° within 1 s, indicating membrane super-oleophilicity in air (Fig. 5(b)).
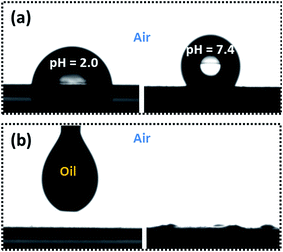 |
| Fig. 5 Wettability and water flux at different pH of the PVDF membrane. (a) Static CA for a water droplet (2 μL) at pH 2.0 and 7.4 applied to the lower membrane surface in air; (b) static CA for an oil droplet (chloroform, 3 μL) similarly applied to the lower membrane surface in air. | |
In order to apply the pH-responsive PVDF membrane to the practical separation of oil and water, under-oil super-hydrophobicity and underwater super-oleophobicity are a prerequisite. For this reason, both under-oil water wettability and under water oil wettability of the lower membrane surface (peeled from NWF) were evaluated. As shown in Fig. 6(a), water droplets at pH 2.0 and 7.4 each attained a quasi-spherical shape at the membrane surface under oil, with CA of 154 ± 0.5° and 153 ± 0.7° respectively, regardless of the pH value of the water, indicating its under oil super-hydrophobicity. In this state, the membrane provided the possibility of separating water-in-oil emulsions.
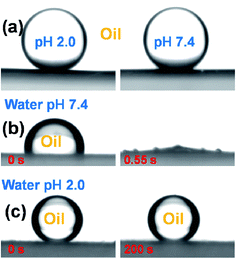 |
| Fig. 6 Wettability of the PVDF membrane in oil and water. (a) Static CA for a water droplet (4 μL) with pH of 2.0 and 7.4 applied in oil (n-hexane); (b) static CA for an oil droplet (chloroform, 3 μL) applied to the lower membrane surface in pure water at pH 7.4; (c) static CA for an oil droplet (chloroform, 3 μL) applied to the lower membrane surface in acidic water, adjusted to pH 2.0 with hydrochloric acid. | |
To separate an oil-in-water emulsion, underwater super-oleophobicity is a necessary feature of our membrane. However, when the membrane was immersed in pure water at pH 7.4, the unstable water molecular layer was repelled from the deprotonated PDMAEMA network by the oil droplet (chloroform), which is immediately sucked into the membrane within 0.55 s, implying underwater super-oleophilicity, as shown in Fig. 6(b). In this state, the membrane was incapable of separating an oil-in-water emulsion. In order to overcome this feature, we took advantage of the pH-responsive properties of PDMAEMA chains, and adjusted the pH of the aqueous medium to 2.0 using hydrochloric acid. When the pH-responsive PVDF membrane was immersed in acidic water at this pH the oil droplet formed a sphere with a CA of 156 ± 0.8°, and regained its initial shape within 200 s, as shown in Fig. 6(c).
The mechanism proposed for tunable affinity and pore size is illustrated in Scheme 1. When immersed in pure water (pH 7.4), the deprotonated PDMAEMA network was no longer immobilized and an oil droplet could penetrate easily. In consequence, in contact with acidic water (pH 2.0) the PDMAEMA chains became protonated, generating a hydrophilic layer on the membrane surface, and the layer of stable trapped water molecules blocked the access of oil,5,25 giving underwater super-oleophobicity. As discussed earlier, by adjusting the pH of the aqueous medium the pH-responsive membrane acquired the additional possibly of separating oil-in-water emulsions.
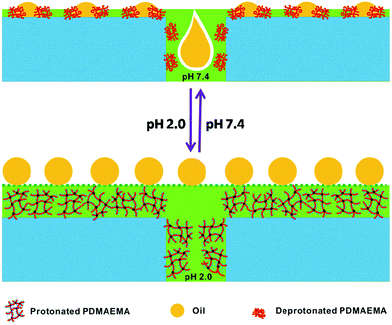 |
| Scheme 1 Schematic representation of the switchable oil wettability of a PDMAEMA-modified PVDF membrane under water at a pH of 7.4 (upper) or 2.0 (lower). | |
Membrane wettability can be considered to be controlled by a combination of surface chemistry and microstructure. The influence of the former has been discussed above, and we may now consider the effect of hierarchical structure on the amplification of under-oil super-hydrophobicity and underwater super-oleophobicity by probing the wettability of the upper membrane surface in direct contact with the non-solvent. The result, shown in Fig. 7, indicates that the WCA in oil of this smooth surface was only 139 ± 1° and the OCA in acidic water (pH 2.0) was 120 ± 3°. Compared with the rough surface peeled from NWF, this value is lower, and a long way short of super-wetting. These results emphasize the importance of template stripping in improving the microstructure of our membrane.
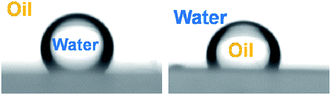 |
| Fig. 7 Wettability of the upper surface of the PVDF membrane in oil and water at pH 2.0. (left) Static CA for a water droplet (2 μL) applied to the upper membrane surface in oil (n-hexane); (right) static CA for an oil (chloroform) droplet (2 μL) applied to the upper membrane surface in water at pH 2.0. | |
3.4 Membrane flux caused by pH of the water
In addition to tunable wettability, variation in the conformation of PDMAEMA can also be expected to change the pore size of the membrane in response to variations in pH. To test this, water flux at different pH was assessed, as shown in Fig. 8. In order to avoid the adverse influence of the intrinsic instability of the PVDF membrane in a strongly alkaline environment, only acidic or weakly alkaline water was considered. The results demonstrated that the flux was around 16
000 L m−2 h−1 at pH 2.0, and increased strongly to 26
000 L m−2 h−1 at pH 6.5, before decreasing again to 16
500 L m−2 h−1 at pH 7.5.
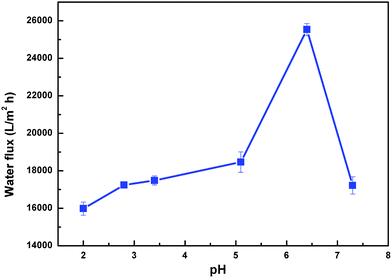 |
| Fig. 8 Membrane flux for water at different pH values. | |
The competitive balance between wettability and pore size determines the variation in permeability. At low pH (2.0), PDMAEMA chains on the membrane were highly protonated and stretched, reducing the pore size, and hence the water flux. However, on increasing pH below the pKa of PDMAEMA (7.0), the PDMAEMA chains were partially protonated, and shrank to enlarge the pore size and gradually increase the water flux. Nevertheless, at pH above pKa the PDMAEMA chains were completely deprotonated and collapsed, exposing the more hydrophobic PVDF to the membrane surface. Its hydrophobicity accordingly dominated the decreased water flux.
3.5 Separation of water-in-oil and oil-in-water emulsions
As mentioned above, our membrane possesses under-oil super-hydrophobicity and underwater super-oleophobicity, which are prerequisites for the separation of both water-in-oil and oil-in-water emulsions. To test the separation capability of the PVDF membrane, a series of surfactant-stabilized oil and water emulsions, namely water-in-toluene (W/T), water-in-chloroform (W/C), water-in-dichloromethane (W/DCM), toluene-in-water (T/W), chloroform-in-water (C/W) and dichloromethane-in-water (DCM/W), were prepared. For water-in-oil emulsions, oil is the continuous phase in direct contact with the membrane surface, and the pH of the water has no effect on separation effectiveness, since it has been shown that in oil the membrane shows super-hydrophobicity with pure water, so this water was applied directly. Nevertheless, as discussed earlier, this pH-responsive membrane showed super-oleophilicity under pure water (pH 7.4) and super-oleophobicity under acidic water (pH 2.0).
With the purpose of separating oil-in-water emulsions, the pH of water for preparation of oil-in-water emulsions was adjusted to 2.0. The freshly prepared emulsions were poured onto the membrane in order to assess filtration separation under a vacuum of 0.09 MPa. Fig. 9 gives a clear indication under an optical microscope of the effective separation of water-in-oil and oil-in-water emulsions, using a water–toluene system as an example. Not a single droplet was observed in the collected filtrates. In contrast to the original milky-white feed emulsions, the collected filtrates were totally transparent, indicating the high rejection efficiency of the membrane for separating both water-in-oil and oil-in-water emulsions.
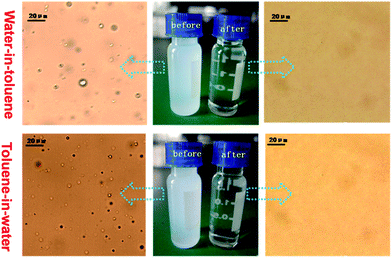 |
| Fig. 9 Optical microscopy images for water-in-toluene emulsion (upper) and toluene-in-water emulsion (lower), before and after filtration. | |
UV-VIS and FTIR-ATR spectrometers were used to analyze the treated filtrates from the oil-in-water emulsions. As shown in Fig. 10(a), the absence of the characteristic peak in the UV-VIS spectrum for toluene confirmed the high rejection efficiency of our membrane. Similarly effective separation was also confirmed by FTIR-ATR for other two emulsions, C/W and DCM/W. The results shown in Fig. 10(b) and (c) showed that the characteristic peaks of chloroform and dichloromethane were absent after the separation process. The purity of all the filtrates is summarised in Table 4, the values in all cases being above 99.9%.
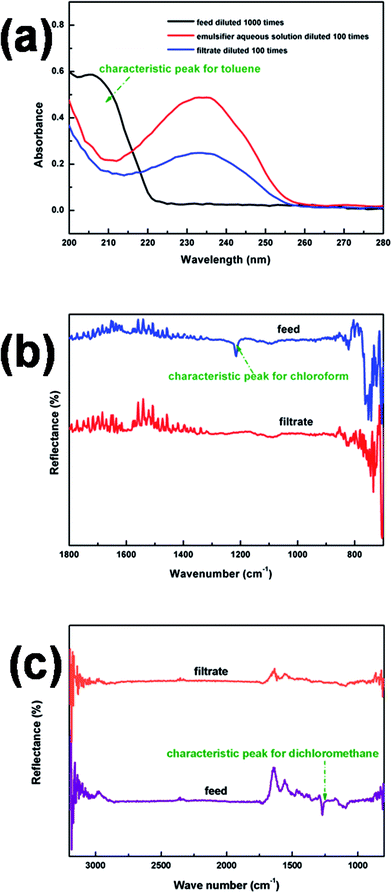 |
| Fig. 10 In each case the result before and after filtration is illustrated: (a) UV-VIS spectra for a toluene-in-water emulsion; (b) FTIR-ATR spectra for a chloroform-in-water emulsion; and (c) FTIR-ATR spectra for a dichloromethane-in-water emulsion. | |
Table 4 Purity of filtrates for a range of emulsions
Emulsion |
Purity of filtrate (%) |
W/T |
99.9928 |
W/C |
99.9901 |
W/DCM |
99.9964 |
T/W |
99.9815 |
C/W |
99.9912 |
DCM/W |
99.9937 |
The flux of the membrane was measured for various water-in-oil and oil-in-water emulsions. As shown in Fig. 11, with 0.09 MPa of applied pressure across the membrane all the emulsions exhibited high flux. The fluxes of 3347, 2798, 2574 L m−2 h−1 for Span80-stabilized W/T, W/C and W/DCM, and 1603, 1306, 1274 L m−2 h−1 for Tween80-stabilized T/W, C/W and DCM/W, were obtained. The values were several times higher than those obtained with traditional filtration membranes of similar permeability properties,26,27 and this separation performance is thus very attractive from the standpoint of practical application.
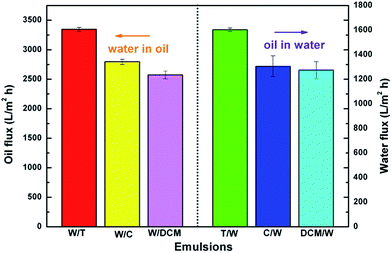 |
| Fig. 11 Membrane permeability flux for various emulsions. | |
3.6 Stability and antifouling properties of pH-responsive PVDF membranes
In order to assess the stability oil and water separation of our membrane, 10 repeated separation experiments were carried out, using a toluene–water system as an example. The results, shown in Fig. 12(a), confirmed that both W/T and T/W maintained a stable flux value, around 3300 and 1600 L m−2 h−1, respectively. The purity of the filtrate in both cases was above 99.9% (Fig. 12(b)), indicating that wettability, morphology and mechanical strength had been well maintained.
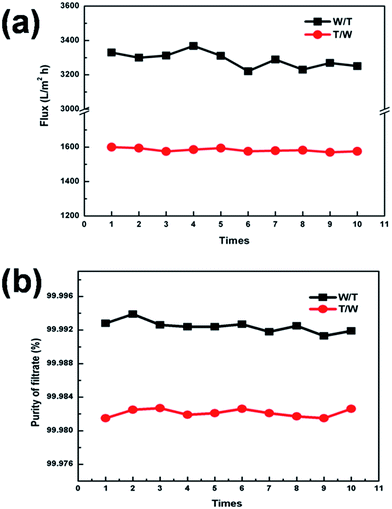 |
| Fig. 12 Results of water-in-toluene (W/T) and toluene-in-water (T/W) in separation experiments repeated ten times. Following each separation process, the membrane was washed with ethanol and dried in the oven at 40 °C. (a) Flux of W/T and T/W in separation experiments repeated ten times; (b) the purity of the filtrate for the repeated separation experiments. | |
Due to the complicated conditions of oil and water separation, unavoidable settlement and accumulation of foulants (including microorganisms, proteins and other organic molecules found in feed streams) on the membrane surface would hinder the practical application of membrane technology.28,29 In the first place, uncontrollable membrane fouling would decrease membrane performance, and increased operating pressure and frequency of chemical cleaning would be required to maintain membrane performance. In addition, frequent chemical cleaning would inevitably shorten the life of the membrane and increase maintenance costs.30,31
Membrane antifouling properties, which are closely related to membrane hydrophilicity and low surface free energy, are very important in long-term practical usage.27,32–35 Repeated separation experiments did not take foulants such as proteins into consideration. In order to evaluate the antifouling properties of our membrane, 1 g L−1 BSA solutions prepared, respectively, from pure and acidic water were employed as the contaminant model. For each experiment, a certain volume of pure water, acidic water and BSA solutions prepared from the corresponding water was employed to permeate the membrane, and the membrane was then simply rinsed with ethanol and water to recover flux.
The variation in flux during the process is illustrated in Fig. 13(a). It is seen that when the BSA solution was applied the flux decreased to a relatively low value, but largely recovered after the washing step. A further analysis of the antifouling properties of the membrane in pure water and acidic water is also shown (Fig. 13(b)). The membrane flux recovery ratio (FRR) was 69% and 97% for pure and acidic water, respectively. The reversible fouling ratio (DRr), irreversible fouling ratio (DRir) and total fouling ratio (DRt) for pure water was 19%, 31% and 50%, and 27%, 3% and 30% for acidic water. Higher FRR values, together with lower DRt values, indicated better antifouling properties in acidic water. Moreover, an increased DRr and decreased DRir implied that in acidic water, protonated or stretched PDMAEMA chains made the membrane more hydrophilic, avoiding more BSA adsorption and deposition, and causing BSA to be removed from the membrane surface by simple washing. These results confirmed the excellent antifouling property of our membrane under acidic aqueous media.
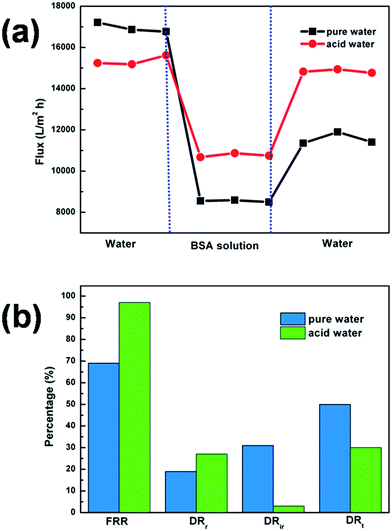 |
| Fig. 13 Membrane antifouling properties in pure or acidic water at pH 2.0. (a) Variation in flux and flux recovery by treating with water (at pH 7.4 or 2.0, respectively) or BSA solution; (b) flux recovery ratio (FRR), reversible fouling ratio (DRr), irreversible fouling ratio (DRir) and total fouling ratio (DRt), for PVDF membrane in water at pH 7.4 or 2.0. | |
4. Conclusions
We have demonstrated that a pH-responsive membrane with oil super-hydrophobicity and underwater super-oleophobicity can be achieved by incorporating DMAEMA hydrogels into PVDF via in situ polymerization and phase separation, indicating convenience and the possibility of production on a large scale. The oil super-hydrophobicity is derived from hydrophobic PVDF chains, and is unaffected by the pH value of the water. On the other hand, underwater wettability can be switched by the pH value. In aqueous media with pH above pKa, deprotonated and collapsed PDMAEMA chains lead to an underwater superoleophilic surface. Nevertheless, in acidic water with pH below pKa, the membrane surface with protonated and stretched PDMAEMA chains showed underwater super-oleophobicity. The responsive ability of the surface could be attributed to the combined effect of the variation in surface chemistry and the roughness of the structure. In addition, we have applied the membrane to the separation of surfactant-stabilized emulsions, including both water-in-oil and oil-in-water types. Relatively high flux and separation efficiency, together with excellent antifouling properties, make our membrane extremely promising for the practical separation of oil and water.
Acknowledgements
The authors are grateful for financial support from the National Natural Science Foundation of China (nos 51273211 and 51473177), the Ministry of Science and Technology of China (nos 2012AA03A605 and 2012DFR50470), and the Bureau of Science and Technology of Ningbo (no. 2014B81004).
References
- B. Brugger and W. Richtering, Adv. Mater., 2007, 19, 2973–2978 CrossRef CAS.
- A. Jernelov, Nature, 2010, 466, 182–183 CrossRef PubMed.
- D. Dudgeon, A. H. Arthington, M. O. Gessner, Z. Kawabata, D. J. Knowler, C. Leveque, R. J. Naiman, A. H. Prieur-Richard, D. Soto, M. L. Stiassny and C. A. Sullivan, Biol. Rev. Cambridge Philos. Soc., 2006, 81, 163–182 CrossRef PubMed.
- C. Wu, C. Maurer, Y. Wang, S. Xue and D. L. Davis, Environ. Health Perspect., 1999, 107, 251–256 CrossRef CAS.
- Q. Wen, J. Di, L. Jiang, J. Yu and R. Xu, Chem. Sci., 2013, 4, 591–595 RSC.
- L. Feng, Z. Y. Zhang, Z. H. Mai, Y. M. Ma, B. Q. Liu, L. Jiang and D. B. Zhu, Angew. Chem., Int. Ed., 2004, 43, 2012–2014 CrossRef CAS PubMed.
- Y. Zhu, F. Zhang, D. Wang, X. F. Pei, W. Zhang and J. Jin, J. Mater. Chem. A, 2013, 1, 5758–5765 CAS.
- M. Liu, F.-Q. Nie, Z. Wei, Y. Song and L. Jiang, Langmuir, 2010, 26, 3993–3997 CrossRef CAS PubMed.
- X. Gui, Z. Zeng, Z. Lin, Q. Gan, R. Xiang, Y. Zhu, A. Cao and Z. Tang, ACS Appl. Mater. Interfaces, 2013, 5, 5845–5850 CAS.
- L. Chen, M. Liu, L. Lin, T. Zhang, J. Ma, Y. Song and L. Jiang, Soft Matter, 2010, 6, 2708–2712 RSC.
- A. K. Kota and A. Tuteja, NPG Asia Mater., 2013, 5, e58 CrossRef CAS.
- M. H. Tai, P. Gao, B. Y. L. Tan, D. D. Sun and J. O. Leckie, ACS Appl. Mater. Interfaces, 2014, 6, 9393–9401 CAS.
- F. Schacher, M. Ulbricht and A. H. E. Müller, Adv. Funct. Mater., 2009, 19, 1040–1045 CrossRef CAS.
- Y. Xiu, L. Zhu, D. W. Hess and C. Wong, Nano Lett., 2007, 7, 3388–3393 CrossRef CAS PubMed.
- L. Zhang, Z. Zhang and P. Wang, NPG Asia Mater., 2012, 4, e8 CrossRef.
- M. Tao, L. Xue, F. Liu and L. Jiang, Adv. Mater., 2014, 26, 2943–2948 CrossRef CAS PubMed.
- H. Liu, S. Li, J. Zhai, H. Li, Q. Zheng, L. Jiang and D. Zhu, Angew. Chem., Int. Ed., 2004, 43, 1146–1149 CrossRef CAS PubMed.
- L. Feng, S. Li, H. Li, J. Zhai, Y. Song, L. Jiang and D. Zhu, Angew. Chem., 2002, 114, 1269–1271 CrossRef.
- L. Feng, Y. Song, J. Zhai, B. Liu, J. Xu, L. Jiang and D. Zhu, Angew. Chem., 2003, 115, 824–826 CrossRef.
- X. Huang, D. Kim, M. Im, J. Lee, J. Yoon and Y. Choi, Small, 2009, 5, 90–94 CrossRef CAS PubMed.
- Y. Cao, X. Zhang, L. Tao, K. Li, Z. Xue, L. Feng and Y. Wei, ACS Appl. Mater. Interfaces, 2013, 130506143336000 Search PubMed.
- Y. Yang, Z. Tong, T. Ngai and C. Wang, ACS Appl. Mater. Interfaces, 2014, 6, 6351–6360 CAS.
- J. Karppi, S. Åkerman, K. Åkerman, A. Sundell, K. Nyyssönen and I. Penttilä, Int. J. Pharm., 2007, 338, 7–14 CrossRef CAS PubMed.
- X. Qiu, X. Ren and S. Hu, Carbohydr. Polym., 2013, 92, 1887–1895 CrossRef CAS PubMed.
- J. Chen, T. Liu, L. Zhao and W.-k. Yuan, Ind. Eng. Chem. Res., 2013, 52, 5100–5110 CrossRef CAS.
- B. Chakrabarty, A. K. Ghoshal and M. K. Purkait, J. Membr. Sci., 2008, 325, 427–437 CrossRef CAS PubMed.
- Z. Cheng, H. Lai, Y. Du, K. Fu, R. Hou, C. Li, N. Zhang and K. Sun, ACS Appl. Mater. Interfaces, 2014, 6, 636–641 CAS.
- D. Rana and T. Matsuura, Chem. Rev., 2010, 110, 2448–2471 CrossRef CAS PubMed.
- G. M. Geise, H. S. Lee, D. J. Miller, B. D. Freeman, J. E. McGrath and D. R. Paul, J. Polym. Sci., Part B: Polym. Phys., 2010, 48, 1685–1718 CrossRef CAS.
- V. Vatanpour, S. S. Madaeni, R. Moradian, S. Zinadini and B. Astinchap, Sep. Purif. Technol., 2012, 90, 69–82 CrossRef CAS PubMed.
- Y. Li, Y. Su, X. Zhao, X. He, R. Zhang, J. Zhao, X. Fan and Z. Jiang, ACS Appl. Mater. Interfaces, 2014, 6, 5548–5557 CAS.
- H. S. Sundaram, Y. Cho, M. D. Dimitriou, C. J. Weinman, J. A. Finlay, G. Cone, M. E. Callow, J. A. Callow, E. J. Kramer and C. K. Ober, Biofouling, 2011, 27, 589–602 CrossRef CAS PubMed.
- J. A. Callow and M. E. Callow, Nat. Commun., 2011, 2, 244–254 CrossRef PubMed.
- M. Zhang, C. Wang, S. Wang and J. Li, Carbohydr. Polym., 2013, 97, 59–64 CrossRef CAS PubMed.
- Y. Yang, H. Wang, J. Li, B. He, T. Wang and S. Liao, Environ. Sci. Technol., 2012, 46, 6815–6821 CrossRef CAS.
|
This journal is © The Royal Society of Chemistry 2015 |
Click here to see how this site uses Cookies. View our privacy policy here.