DOI:
10.1039/C5RA00691K
(Paper)
RSC Adv., 2015,
5, 19058-19066
Polymorphism of a high-molecular-weight racemic poly(L-lactide)/poly(D-lactide) blend: effect of melt blending with poly(methyl methacrylate)
Received
13th January 2015
, Accepted 9th February 2015
First published on 9th February 2015
Abstract
The effect of melt blending with poly(methyl methacrylate) (PMMA), a miscible polymer with polylactide (PLA), on the crystallization and melting behaviors and crystalline structure of high-molecular-weight poly(L-lactide)/poly(D-lactide) (PLLA/PDLA) blend was investigated by differential scanning calorimetry (DSC) and wide-angle X-ray diffraction (WAXD). Due to the decreased segmental mobility of PLA chains and the dilution effect of the introduced PMMA, the crystallization of PLA is hindered. The polymorphic crystallization of the PLLA/PDLA blend can be tailored by the amount of PMMA and dynamic and isothermal crystallization conditions. The formation of stereocomplex (sc) crystallites is favored for the blends containing PMMA lower than 50 wt% during cold crystallization. During isothermal melt crystallization, the formation of sc crystallites is always accompanied by the generation of homochiral (hc) crystallites at a crystallization temperature (Tc) ranging from 110 to 160 °C for neat PLLA/PDLA blend, while the crystallization window for exclusive sc crystallites is widened to 160 °C, 140–160 °C, and 110–150 °C for PLLA/PDLA blends containing 10, 25, and 50 wt% PMMA, respectively. Especially, the formation of sc crystallites can be enhanced over the entire Tc range of 110–160 °C when the PMMA content is lower than 25 wt%. The enhanced sc crystallite formation can be ascribed to the reduced crystallization competition resulting from highly restricted hc crystallization. With the PMMA content increasing to 75 wt%, the inhibition effect on the crystallization of PLA suppresses either hc or sc crystallization.
Introduction
The stereocomplex (sc) crystallites formed between enantiomeric poly(L-lactide) (PLLA) and poly(D-lactide) (PDLA) are an important crystal modification of polylactide (PLA), generally produced in the crystallization of an equimolar racemic PLLA/PDLA blend from melt or solution.1–3 One of the most characteristic features of sc crystallites is their high melting point, 50 °C higher than that of PLLA or PDLA homochiral (hc) crystallites.1,4,5 Because of improved physical properties, PLA stereocomplexation has drawn much attention since its first discovery by Ikada et al.4 Sc crystallization has been proven to be one of the most effective methods to enhance the properties of PLA, including mechanical performance,6–8 thermal stability,9,10 and hydrolysis resistance.11,12
Many attempts have been made to identify the mechanism and the effect of different parameters on the formation of sc crystallites such as homopolymer molecular weight (Mw), blending ratio, optical purity, preparation methods and crystallization conditions.13–29 Generally, blending of high Mw PLLA and PDLA always leads to hc crystallization together with sc crystallization. For the bulk crystallization from melt, exclusive sc formation is limited to PLLA and PDLA at least either of which has a Mw lower than 1 × 104 g mol−1, whereas solely hc crystallites is obtained in the PLLA/PDLA blend where both polymers have the Mws higher than 1 × 105 g mol−1.1,15
Miscible blending has been successfully utilized to control the polymorphic behavior of syndiotactic polystyrene (s-PS), and the formation of the β-form crystals of s-PS is facilitated in the blends of s-PS with atactic polystyrene (a-PS).30 Yang et al.31 also studied the polymorphic crystallization of poly(butylene adipate) (PBA) in its miscible crystalline/crystalline blend with poly(vinylidene fluoride) (PVDF). They found that the polymorphic crystalline structure of PBA can be controlled upon blending with PVDF, and the incorporated PVDF facilitates the formation of PBA α-crystals.
PLLA is known to be miscible or partially miscible with a few components such as poly(vinyl acetate) (PVAc),32 poly(methyl methacrylate) (PMMA),33 poly(vinylphenol) (PVPh),34 poly(ethylene glycol) (PEG),35 and atactic poly(D,L-lactide) (PDLLA).36 The glass transition temperature (Tg), which is an important factor governing the crystallization behavior, depends on the composition of miscible blends.37 Then PDLLA is usually selected as a model polymer to study the effects of miscible blending on the polymorphic crystallization of PLLA due to its similar Tg with PLLA. Pan et al.36 found that the crystallization of PLLA is hindered with the presence of PDLLA due to the dilution effect, and the polymorphic behavior of PLLA is influenced by the miscible blending with PDLLA. With the incorporation of 50 wt% PDLLA, the critical temperature for the formation of δ- and α-form crystals decreases from ∼110 (of neat PLLA) to ∼80 °C. Li et al.38,39 studied the effect of PDLLA on the polymorphism of PLLA/PDLA blends, and found that the polymorphic crystallization of PLLA/PDLA blend could be controlled by incorporation of miscible PDLLA with different dynamic and isothermal crystallization conditions. Full sc crystallites can be formed with 70 wt% PDLLA, irregardless of the crystallization conditions.
In the field of PLLA-based polymer blends, the use of PMMA attracts broad interests due to its ability to tune the properties of PLLA.33,40–44 Shirahase et al.44 investigated the miscibility and hydrolytic degradation of PLLA/PMMA blends, and found the hydrolytic degradation rate of the blends could be widely controlled by PMMA content in the blend. Samuel et al.43 designed multiple-shape memory polymers with miscible PLLA/PMMA blends. Meanwhile, it is noticed that PLLA crystallization is restricted by the presence of PMMA chains in binary PLLA/PMMA blends, inducing a lower crystallization rate of PLLA. In our previous work,45 the decreased Tg and increased segmental mobility of PLAs chains induced by PEG is shown to play a dominant role on the melt crystallization of sc crystallites from high-Mw PLLA/PDLA. The crystalline structures of PLLA/PDLA blends can be tailored through the Mw and the content of PEG, and exclusive formation of sc crystallites is achieved in the blends with 10 wt% PEG having Mws of 1000 or 2000 g mol−1. In this work, the miscible blending with PMMA results in increased Tg and decreased segmental mobility of PLAs chains, and the effects of blend composition and crystallization conditions on the polymorphic crystalline structure of high-Mw PLLA/PDLA blend are investigated.
Experimental section
Materials
PLLA (trade name 4032D) with Mw = 2.1 × 105 g mol−1 and the polydispersity (PDI) = 1.7 was purchased from NatureWorks LLC, U.S.A. The PDLA with Mw = 1.0 × 105 g mol−1 and PDI = 1.7, synthesized by the ring-opening polymerization of D-lactic acid, was kindly supplied by Professor Chen Xue-Si at State Key Lab oratory of Polymer Physics and Chemistry, China. PMMA (trade name IF850) with Mw = 8.1 × 104 g mol−1 and PDI = 1.9 was purchased from LG Co. Ltd, Korea.
PLLA, PDLA, and PMMA were vacuum dried at 60 °C for 12 h before melt processing. The blends were then melt blended using a conical co-rotating twin screw extruder (HAAKE Mimilab II, Germany) at 210 °C and 50 rpm for 5 min. The content of PMMA ranged from 0 to 100 wt% based on the total weight of the PLLA/PDLA/PMMA blends, with the weight ratio of PLLA to PDLA maintained at 1
:
1. Taking PMMA content of 10 wt% as an example, the weight ratio of the components is: PLLA
:
PDLA
:
PMMA = 45 wt%
:
45 wt%
:
10 wt%.
Characterizations
The thermal properties of the blends were characterized by differential scanning calorimetry (DSC) with a DSC Q20 (TA Instruments, USA) under a 50 mL min−1 nitrogen gas flow. In the non-isothermal cold crystallization, the samples were quenched to 0 °C after melting at 270 °C for 2 min, and then heated to 270 °C at a rate of 10 °C min−1. Tg was evaluated from the cold crystallization curves. In the case of melt crystallization, after melting at 270 °C for 2 min, the samples were cooled down to 0 °C at 5 °C min−1 for non-isothermal crystallization, or were cooled to the desired crystallization temperature (Tc = 110–160 °C) at 50 °C min−1 for a isothermal crystallization period of 60 min. After the completion of crystallization, the samples were reheated to 270 °C at 10 °C min−1 to examine the melting behavior.
After the completion of isothermal melt crystallization, the sample was quenched at 0 °C for 5 min, and the crystalline structure of the blend melt crystallized at different Tc was investigated by wide-angle X-ray diffraction (WAXD). WAXD profiles were recorded on a DX-1000 X-ray diffractometer (Dandong Fanyuan Instrument Co. LTD) using a CuKα radiation source (λ = 0.154056 nm, 40 kV, 25 mA) in the scanning angle range of 2θ = 5–50° at a scanning speed of 3° min−1. The crystallinity of hc crystallites (Xc(hc)) and sc crystallites (Xc(sc)) were determined from WAXD profiles, and the peak fitting was conducted by software JADE. A quenched sample was used to describe the amorphous halo, and for a 2θ range of 10–26°, two broad amorphous peaks were used to give close description of the amorphous halo. The amorphous peaks at 2θ values consisting of those of the quenched sample were incorporated to provide proper description of the amorphous halo, then crystalline peaks for sc crystallites at 2θ values of 11.6, 20.6, and 23.5° and for hc crystallites at 2θ values of 14.9, 16.7, 19.1, and 22.4° were further added. The crystalline peak areas for sc crystallites and for hc crystallites relative to the total areas were used to estimate Xc(sc) and Xc(hc), respectively. The fraction of sc crystallites, fsc, can be obtained from the following equation
Results and discussion
Non-isothermal crystallization
Fig. 1 shows DSC heating curves of quenched PLLA/PDLA/PMMA blends recorded at the heating rate of 10 °C min−1, and the thermal parameters including Tg, cold crystallization temperature (Tcc), normalized cold crystallization enthalpy (ΔHcc), melting point of hc and sc crystallites (Tm(hc) and Tm(sc)), and normalized melting enthalpy of hc and sc crystallites (ΔHm(hc) and ΔHm(sc)) of the cold crystallized samples are summarized in Table 1. As shown in Fig. 1 and Table 1, all the blends with different PMMA contents exhibit a single Tg. The Tgs are 59.9 and 114.8 °C for neat PLLA/PDLA blend and PMMA, respectively, and Tg shifts to a higher temperature with an increase in PMMA content. It is well-known that a single composition dependent Tg indicates the miscibility of polymer blends, when the difference in their Tg values is over 20 °C.46 The obvious cold crystallization peak at 105.5 °C, and two melting peak at about 169 and 217 °C, corresponding to the melting of hc and sc crystallites, respectively, are observed for the neat PLLA/PDLA blend. Tcc shifts to higher temperature with an increase in PMMA content to 50 wt%. The Tcc of 180.2 °C for the sample with 50 wt% PMMA is higher than Tm of hc crystallites of about 167 °C, then only the sc crystallization is possible, and the crystallization of hc crystallites cannot occur though the nuclei exists during the cold crystallization process. As shown in Fig. 1, the cold crystallization peak is followed closely by the melting peak of sc crystallites. No cold crystallization peak can be observed when the PMMA content is higher than 75%. It can be inferred that Tcc may be higher than Tm of sc crystallites, then either the hc or sc crystallization cannot take place. Moreover, no any cold crystallization and melting peak is detected for neat PMMA, confirming its amorphous nature.
 |
| Fig. 1 DSC heating curves of quenched PLLA/PDLA/PMMA blends recorded at a heating rate of 10 °C min−1. | |
Table 1 DSC data of quenched PLLA/PDLA/PMMA blends during heating scans
|
Tg °C |
Tcc °C |
ΔHcca J g−1 |
Tm(hc) °C |
ΔHm(hc)a J g−1 |
Tm(sc) °C |
ΔHm(sc)a J g−1 |
Both the crystallization and melting enthalpy are normalized by the weight of PLLA/PDLA component. |
0% |
59.9 |
105.5 |
35.8 |
168.8 |
24.7 |
217.1 |
20.4 |
10% |
60.2 |
129.7 |
25 |
165.9 |
13.7 |
215.5 |
28.7 |
25% |
60.9 |
146.2 |
23.5 |
166.7 |
0.67 |
214.4 |
37.1 |
50% |
70.7 |
180.2 |
31.8 |
|
|
214.8 |
36 |
75% |
91.9 |
|
|
|
|
|
|
100% |
114.8 |
|
|
|
|
|
|
Fig. 2 shows the DSC curves of non-isothermal melt crystallization at a cooling rate of 5 °C min−1 and subsequent heating scans at 10 °C min−1 for PLLA/PDLA/PMMA blends, and the DSC data are listed in Table 2. As shown in Fig. 2(a), evident crystallization peaks can be observed for neat PLLA/PDLA blend. With an increase in PMMA composition, the crystallization temperature (Tc) decrease, and the normalized crystallization enthalpy (ΔHc) decreases significantly. No crystallization peak can be observed when the PMMA content is higher than 50%. As seen in Fig. 2(b), after the non-isothermal melt crystallization at 5 °C min−1, a cold crystallization peak appears in PLLA/PDLA/PMMA blends during subsequent heating process, while it is absent in neat PLLA/PDLA blend. With increasing PMMA content, the changes of cold crystallization behavior during subsequent heating process in Fig. 2(b) are very similar to that in typical cold crystallization as shown in Fig. 1. All these results indicate the depression of crystallization rate of PLLA/PDLA blends upon blending with non-crystallizable PMMA. This is ascribed to the decreased segmental mobility of PLA chains and the dilution effects of PMMA on the PLLA/PDLA component. On the one hand, a clear increase in Tg due to decreased segmental mobility of PLA chains caused by the presence of PMMA can be seen in Table 1, and Tg increases with increasing PMMA content. On the other hand, an extra energy is required for demixing the polymer components in the crystallization of miscible blends and thus a higher energy is needed for PLA component to transport from miscible melt to the growth front of crystals. As PMMA content increases to 75%, the combined effect of both decreased segmental mobility of PLA chains and dilution of a large amount of PMMA totally depresses the crystallization of PLA.
 |
| Fig. 2 DSC curves of (a) non-isothermal melt crystallization at a cooling rate of 5 °C min−1 and (b) subsequent heating scans at 10 °C min−1 for PLLA/PDLA/PMMA blends. | |
Table 2 DSC data of PLLA/PDLA/PMMA blends during non-isothermal melt crystallization and subsequent heating scans
|
Tc °C |
ΔHca J g−1 |
Tcc °C |
ΔHcca J g−1 |
Tm(hc) °C |
ΔHm(hc)a J g−1 |
Tm(sc)a °C |
ΔHm(sc)a J g−1 |
Both the crystallization and melting enthalpy are normalized by the weight of PLLA/PDLA component. |
0% |
123.8 |
44.7 |
|
|
166.1 |
30.6 |
215.3 |
24.2 |
10% |
121.2 |
5.7 |
126.1 |
20 |
165.3 |
13.6 |
214.4 |
29.6 |
25% |
113.7 |
4 |
137.7 |
15.2 |
167.1 |
0.4 |
213.8 |
33.7 |
50% |
|
|
174.4 |
36.2 |
|
|
213.8 |
42.8 |
75% |
|
|
|
|
|
|
|
|
All these results of non-isothermal crystallization suggest that the polymorphic behaviors of PLLA/PDLA/PMMA blends differ from that of neat PLLA/PDLA blend. During typical cold crystallization in Fig. 1 and cold crystallization after melt crystallization in Fig. 2(b), the melting peaks of hc and sc crystallites can be observed for the blends with PMMA content lower than 25 wt%. As shown in Tables 1 and 2, a large decrease in ΔHm(hc), and considerable increase in ΔHm(sc) with increasing PMMA content from 0 to 50 wt% are observed, suggesting that the formation of hc crystallites is restricted and the generation of sc crystallites is enhanced. For the blends with 50 wt% PMMA, the melting peak of hc crystallites disappears completely and only the melting peak of sc crystallites presents, indicating exclusive sc crystallites form in the blends. With PMMA content increasing to be above 75 wt%, not any melting peak is detected due to that the crystallization of PLA cannot occur. Moreover, both Tm(hc) and Tm(sc) for PLLA/PDLA/PMMA blends show a 2–3 °C decrease compared to those of pure PLLA/PDLA blend as shown in Tables 1 and 2, due to the dilution effects of miscible PMMA.
Isothermal melt crystallization
The DSC melting curves of PLLA/PDLA/PMMA blends with PMMA content of 0, 10, 25, 50 wt% melt crystallized isothermally at various temperatures are shown in Fig. 3. As shown in Fig. 3(a), both the melting peaks of hc and sc crystallites can be observed for neat PLLA/PDLA blends in the whole Tc range of 110–160 °C, indicating that the formation of sc crystallites is accompanied by hc crystallites. For neat PLLA/PDLA blend crystallized at Tc of 160 °C, the strength of the melting peak for sc crystallites is much higher than that of hc crystallites. At a higher Tc of 150 and 160 °C, the double melting peak behavior of sc crystallites is observed above 200 °C. It can be associated with a dual crystalline morphology for sc crystallites comprising a spherulitic and a network structure revealed by optical microscopy observations according to Saeidlou et al.47 The lower temperature melting peak is associated to the network structure, and the higher temperature peak is the characteristic peak for spherulite melting. The polymorphic crystallization of PLLA/PDLA blend could be tailored by incorporation of miscible PMMA and isothermal crystallization conditions. For PLLA/PDLA blends with 10 wt% PMMA in Fig. 3(b), the strength of the melting peak for sc crystallites is much higher than that of hc crystallites at Tc of 150 and 160 °C; especially, the melting peak of hc crystallites disappears and only that of sc crystallites can be observed at Tc of 160 °C, indicating exclusive sc crystallites can be formed. For PLLA/PDLA blends with 25 wt% PMMA in Fig. 3(c), the strength of the melting peak for sc crystallites is higher than that of hc crystallites in the whole Tc range of 110–160 °C, and unique melting peak for sc crystallites can be observed at Tc of 140–160 °C. With the PMMA content increasing to 50 wt% as shown in Fig. 3(d), unique melting peak for sc crystallites can be observed at Tc of 110–150 °C. The cold crystallization can be observed in heating scan for sample crystallized at Tc of 110 °C, indicating that the crystallization of sc crystallites cannot complete in the tested crystallization period of 60 min. This can be ascribed to that the decreased segmental mobility of PLA chains make the sc crystallization at low Tc difficult. Moreover, no melting peaks of either hc crystallites or sc crystallites can be observed for PLLA/PDLA blends with 50 wt% PMMA at Tc of 160 °C, indicating that no crystallization can take place due to the dilution effect of PMMA. As the PMMA content increases to 75 wt%, no melting of crystals can be observed on the melting curves at all the Tcs (the curves were not shown here), indicating no crystallization occurs due to the combined effect of decreased segmental mobility of PLA chains and dilution of a large amount of PMMA.
 |
| Fig. 3 DSC melting curves of PLLA/PDLA/PMMA blends with PMMA content of (a) 0, (b) 10, (c) 25, (d) 50 wt% melt crystallized isothermally at various temperatures. | |
Crystalline structures
The crystalline structure of the blends melt crystallized isothermally at different Tcs was further investigated by WAXD analysis, and WAXD patterns are shown in Fig. 4. In Fig. 4(a), the diffraction peaks of hc crystallites at 2θ values of 14.9, 16.7, 19.1, and 22.4°, corresponding to the (010) plane, (110) and/or (200) planes, (203) plane, and (210) plane of the α or δ form crystals of PLLA or PDLA,48 and diffraction peaks of sc crystallites at 2θ values of 11.6, 20.6, and 23.5°, corresponding to the (110) plane, (300) and/or (030) planes, and (220) plane49 can be observed for neat PLLA/PDLA blends in the whole Tc range of 110–160 °C. Both DSC and WAXD results indicate that the formation of sc crystallites is accompanied by the formation of hc crystallites in the whole Tc range of 110–160 °C due to that high-Mw PLLA and PDLA were used. It is interesting to note that, for PLLA/PDLA blends with 10 wt% PMMA crystallized at Tc of 160 °C in Fig. 4(b), with 25 wt% PMMA crystallized at Tc of 140–160 °C in Fig. 4(c), and with 50 wt% PMMA crystallized at Tc of 110–150 °C in Fig. 4(d), the diffraction peaks of hc crystallites disappear and only those of sc crystallites can be observed, indicating exclusive sc crystallites can be formed. As shown in Fig. 4(d), no diffraction peaks corresponding to either hc crystallites or sc crystallites can be observed on WAXD patterns for PLLA/PDLA blends with 50 wt% PMMA at Tc of 160 °C, indicating that no crystallization can take place. The above polymorphic structures revealed by WAXD results are consistent with those of DSC analysis, which demonstrate that the polymorphic behaviors of PLLA/PDLA blends are influenced by the miscible blending with PMMA, and the crystallization window for exclusive sc crystallites is widened to lower temperature with an increase in PMMA composition. The crystallization window for generating exclusive sc crystallites are 160 °C, 140–160 °C, 110–150 °C for PLLA/PDLA blends with 10, 25, and 50 wt% PMMA, respectively.
 |
| Fig. 4 WAXD patterns of PLLA/PDLA/PMMA blends with PMMA content of (a) 0, (b) 10, (c) 25, (d) 50 wt% melt crystallized isothermally at various temperatures. | |
Fig. 5 shows the crystallinity of hc crystallites (Xc(hc)), crystallinity of sc crystallites (Xc(sc)), and fraction of sc crystallites (fsc) measured by WAXD method for PLLA/PDLA/PMMA blends melt crystallized isothermally at various temperatures. As shown in Fig. 5(a), with increasing in PMMA content, the values of Xc(hc) at the same Tc decrease in the whole Tc range of 110–160 °C, indicating that the hc crystallization is restricted. For blends with 10 wt% PMMA at Tc of 160 °C, with 25 wt% PMMA at Tcs of 140–160 °C, the values of Xc(hc) is 0%. With the PMMA content increasing to 50 wt%, the values of Xc(hc) is 0% at the whole Tc range of 110–160 °C. In contrast to that of Xc(hc), a considerable increase in Xc(sc) with an increase in the PMMA content to 25% are observed in Fig. 5(b), indicating that the formation of sc crystallites is enhanced. The values of Xc(sc) for the blends with 50 wt% PMMA crystallized at Tc range of 110–130 °C are still higher than those of blends with 25 wt% PMMA, but a decrease is observed above Tc of 130 °C. The values of Xc(sc) at Tc of 140 °C is still higher than that of neat PLLA/PDLA blend. These results demonstrate the formation of sc crystallites can be enhanced at Tc lower than 140 °C for PLLA/PDLA blends with 50 wt% PMMA. An obvious increase in fsc with increasing the PMMA content can be observed in Fig. 5(c). For PLLA/PDLA blends with 10 wt% PMMA crystallized at Tc of 160 °C, with 25 wt% PMMA crystallized at Tc range of 140–160 °C, and with 50 wt% PMMA crystallized at Tc range of 110–150 °C, a fsc value of 100% can be achieved.
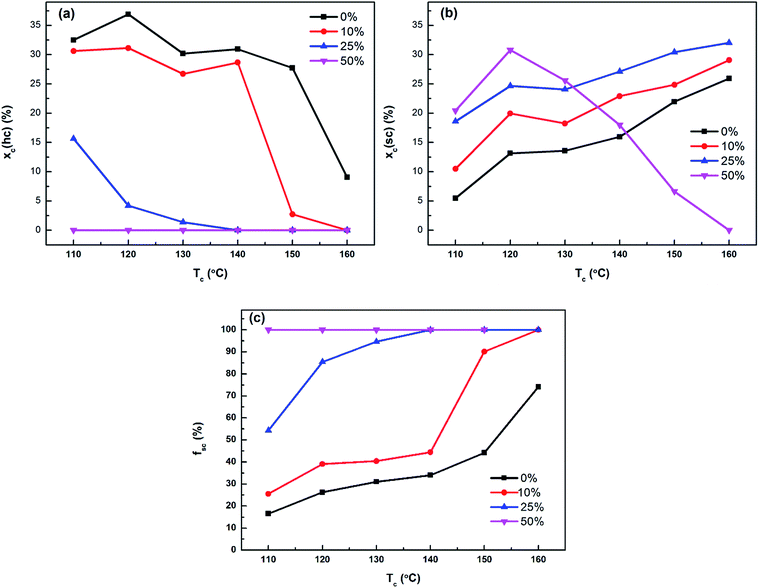 |
| Fig. 5 (a) The crystallinity of hc crystallites (Xc(hc)), (b) crystallinity of sc crystallites (Xc(sc)), and (c) fraction of sc crystallites (fsc) measured by WAXD method for PLLA/PDLA/PMMA blends melt crystallized isothermally at various temperatures. | |
All of the DSC and WAXD results indicate that the crystalline structure of PLLA/PDLA blend is influenced by the miscible blending with PMMA, and the formation of sc crystallites is facilitated in the blends when PMMA content is lower than 50 wt%. This is caused by the effects of blending on the thermodynamic and kinetics environments of PLA crystallization.
Discussions
Tsuji et al.17 investigated the spherulite growth of sc crystallites in the blend of low-Mw PLLA and PDLA from melt, together with that of the hc crystallites in pure PLLA and PDLA films. The spherulite growth of sc crystallites occurred at a wider temperature range (≤190 °C) compared with that of hc crystallites (≤140 °C). In fact, for high-Mw PLLA/PDLA blends, sc crystallites formed during melt crystallization act as nucleating agent for hc crystallization, and both hc and sc crystallization take place simultaneously in a wide temperature range lower than the Tm of hc crystallites, resulting a serious crystallization competition between hc and sc crystallites. The Tgs of PLLA/PDLA/PMMA blends can be adjusted in a wide range due to the miscible blending with PMMA and the large differences in Tg between neat PLLA/PDLA blend and PMMA. The decreased segmental mobility induced by increased Tg and the diffusion effect upon miscible blending with PMMA inhibit the crystallization of PLA chains including hc and sc crystallization. Tcc shifts to higher temperature in non-isothermal cold crystallization (Fig. 1 and Table 1), and Tc shifts to lower temperature in non-isothermal melt crystallization (Fig. 2 and Table 2) with an increase in PMMA content. However, due to the higher equilibrium melting point (T0m) of sc crystallites (279 °C) than that of hc crystallites (212 °C),1 the degree of supercooling for sc crystallization is far higher than that for hc crystallization. Therefore, only sc crystallization can occur with higher PMMA content of 25 and 50 wt% in Fig. 5(a and b). As shown in Fig. 5(a and b), Xc(hc) decreases and Xc(sc) increases at whole Tc range of 110–160 °C with PMMA content increasing to 25 wt%. With PMMA content lower than 25 wt%, the highly restricted hc crystallization reduces the competition between the hc and sc crystallization, then sc crystallization can be enhanced in the Tc range lower than the Tm of hc crystallites. In fact, it is also reported that hc crystallization within a binary PLLA/PMMA miscible blend with the PMMA content up to 30 wt% is highly restricted.44
As shown in Tables 1 and 2, for PLLA/PDLA blends with 50 wt% PMMA quenched and experienced melt crystallization, Tcc values of 180.2 and 174.4 °C are higher than the Tm of hc crystallites, then only sc crystallization is possible, and the crystallization of hc crystallites cannot occur though the nuclei exists during cold crystallization process. On the other hand, the crystallization of sc crystallites requires that alternatively PLLA and PDLA molecules reach the growth front. This requirement sets a very stringent limitation to the growth of sc crystallites under quiescent condition, in that there may be local enrichment (or depletion) of the PLA species that is needed, and sc crystallization is limited by the local non-availability of the enantiomer that would allow further growth due to the dilution effect of PMMA component. Yang et al.50 also found that adequate population of racemic helical pairs is needed for formation of their mesomorphic clusters in the melt matrix as precursors of sc nuclei. Then with PMMA content increasing to 50 wt%, the formation of sc can be enhanced in the condition of cold crystallization where the nuclei exists, but depressed in the condition of melt crystallization at high Tcs. With the PMMA content increasing to 75 wt%, both the hc and sc crystallization is restricted due to the continuous decreased segmental mobility and dilution effect of a large amount of PMMA.
Conclusion
The polymorphic crystalline structures of PLLA/PDLA/PMMA blends at different crystallization conditions are investigated. The non-isothermal cold and melt crystallization results demonstrate the crystallization of PLA chains including hc and sc crystallization is hindered by miscible blending with PMMA due to the decreased segmental mobility and diffusion effect. However, the formation of sc crystallites is favored for the blends with PMMA content lower than 50 wt% during cold crystallization process. Isothermal melt crystallization and the corresponding crystalline structures also clearly show that polymorphic behaviors of high-Mw PLLA/PDLA is influenced by the miscible blending with PMMA. The formation of sc crystallites is always accompanied by the generation of hc crystallites in the whole Tc range of 110–160 °C for neat PLLA/PDLA blend, while the crystallization window for exclusive sc crystallites is widened to 160 °C, 140–160 °C, 110–150 °C for PLLA/PDLA blends with 10, 25, and 50 wt% PMMA, respectively. Especially, the formation of sc crystallites can be enhanced in the whole Tc range of 110–160 °C as the PMMA content lower than 25 wt%. The enhanced sc crystallites formation can be ascribed to the reduced crystallization competition resulting from highly restricted hc crystallization. With the PMMA content increasing to 75 wt%, the inhibition on crystallization totally depressed either hc or sc crystallization.
Acknowledgements
This work was supported by the National Natural Science Foundation of China (NNSFC Grants 51422305, 21374065 and 51421061), Major State Basic Research Development Program of China (973 program) (Grant no. 2012CB025902), the Innovation Team Program of Science & Technology Department of Sichuan Province (Grant 2013TD0013) and State Key Laboratory of Polymer Materials Engineering (Grant no. sklpme2014-2-02).
References
- H. Tsuji, Macromol. Biosci., 2005, 5, 569–597 CrossRef CAS PubMed.
- P. Pan and Y. Inoue, Prog. Polym. Sci., 2009, 34, 605–640 CrossRef CAS PubMed.
- G. Liu, X. Zhang and D. Wang, Adv. Mater., 2014, 26, 6905–6911 CrossRef CAS PubMed.
- Y. Ikada, K. Jamshidi, H. Tsuji and S. H. Hyon, Macromolecules, 1987, 20, 904–906 CrossRef CAS.
- S. C. Schmidt and M. A. Hillmyer, J. Polym. Sci., Part B: Polym. Phys., 2001, 39, 300–313 CrossRef CAS.
- S. Rathi, X. Chen, E. B. Coughlin, S. L. Hsu, C. S. Golub and M. J. Tzivanis, Polymer, 2011, 52, 4184–4188 CrossRef CAS PubMed.
- S. R. Rathi, E. B. Coughlin, S. L. Hsu, C. S. Golub, G. H. Ling and M. J. Tzivanis, Polymer, 2012, 53, 3008–3016 CrossRef CAS PubMed.
- H. Tsuji and Y. Ikada, Polymer, 1999, 40, 6699–6708 CrossRef CAS.
- H. Tsuji and I. Fukui, Polymer, 2003, 44, 2891–2896 CrossRef CAS.
- P. Purnama, S. Lim, Y. Jung and S. Kim, Macromol. Res., 2012, 20, 545–548 CrossRef CAS PubMed.
- H. Tsuji, Polymer, 2000, 41, 3621–3630 CrossRef CAS.
- H. Tsuji, Biomaterials, 2003, 24, 537–547 CrossRef CAS.
- H. Tsuji and S. Yamamoto, Macromol. Mater. Eng., 2011, 296, 583–589 CrossRef CAS.
- H. Tsuji, M. Nakano, M. Hashimoto, K. Takashima, S. Katsura and A. Mizuno, Biomacromolecules, 2006, 7, 3316–3320 CrossRef CAS PubMed.
- H. Tsuji and Y. Ikada, Macromolecules, 1993, 26, 6918–6926 CrossRef CAS.
- H. Tsuji, K. Tashiro, L. Bouapao and M. Hanesaka, Polymer, 2012, 53, 747–754 CrossRef CAS PubMed.
- H. Tsuji and Y. Tezuka, Biomacromolecules, 2004, 5, 1181–1186 CrossRef CAS PubMed.
- P. Purnama and S. H. Kim, Macromolecules, 2010, 43, 1137–1142 CrossRef CAS.
- P. Purnama and S. Hyun Kim, Polym. Int., 2012, 61, 939–942 CrossRef CAS.
- P. Purnama, Y. Jung and S. H. Kim, Macromolecules, 2012, 45, 4012–4014 CrossRef CAS.
- M. Fujita, T. Sawayanagi, H. Abe, T. Tanaka, T. Iwata, K. Ito, T. Fujisawa and M. Maeda, Macromolecules, 2008, 41, 2852–2858 CrossRef CAS.
- J. M. Zhang, K. Tashiro, H. Tsuji and A. J. Domb, Macromolecules, 2007, 40, 1049–1054 CrossRef CAS.
- S. Brochu, R. E. Prud'homme, I. Barakat and R. Jerome, Macromolecules, 1995, 28, 5230–5239 CrossRef CAS.
- R.-Y. Bao, W. Yang, W.-R. Jiang, Z.-Y. Liu, B.-H. Xie, M.-B. Yang and Q. Fu, Polymer, 2012, 53, 5449–5454 CrossRef CAS PubMed.
- R.-Y. Bao, W. Yang, W.-R. Jiang, Z.-Y. Liu, B.-H. Xie and M.-B. Yang, J. Phys. Chem. B, 2013, 117, 3667–3674 CrossRef CAS PubMed.
- B. Na, J. Zhu, R. Lv, Y. Ju, R. Tian and B. Chen, Macromolecules, 2014, 47, 347–352 CrossRef CAS.
- J. Zhu, B. Na, R. H. Lv and C. Li, Polym. Int., 2014, 63, 1101–1104 CrossRef CAS.
- Y. Sun and C. He, RSC Adv., 2013, 3, 2219–2226 RSC.
- K. Takemura, H. Ajiro, T. Fujiwara and M. Akashi, RSC Adv., 2014, 4, 33462–33465 RSC.
- E. M. Woo, Y. S. Sun and C. P. Yang, Prog. Polym. Sci., 2001, 26, 945–983 CrossRef CAS.
- J. Yang, P. Pan, L. Hua, B. Zhu, T. Dong and Y. Inoue, Macromolecules, 2010, 43, 8610–8618 CrossRef CAS.
- J. W. Park and S. S. Im, Polymer, 2003, 44, 4341–4354 CrossRef CAS.
- G. B. Zhang, J. M. Zhang, S. G. Wang and D. Y. Shen, J. Polym. Sci., Part B: Polym. Phys., 2003, 41, 23–30 CrossRef CAS.
- E. Meaurio, E. Zuza and J.-R. Sarasua, Macromolecules, 2005, 38, 1207–1215 CrossRef CAS.
- Y. Zhang, Z. Wang, F. Jiang, J. Bai and Z. Wang, Soft Matter, 2013, 9, 5771–5778 RSC.
- P. Pan, Z. Liang, B. Zhu, T. Dong and Y. Inoue, Macromolecules, 2009, 42, 3374–3380 CrossRef CAS.
- J. Bai, H. Fang, Y. Zhang and Z. Wang, CrystEngComm, 2014, 16, 2452–2461 RSC.
- Y. Li, C. Han, X. Zhang, Q. Dong and L. Dong, Thermochim. Acta, 2013, 573, 193–199 CrossRef CAS PubMed.
- Y. Li, C. Y. Han, Y. J. Bian, Q. L. Dong, H. W. Zhao, X. Zhang, M. Z. Xu and L. S. Dong, Thermochim. Acta, 2014, 580, 53–62 CrossRef CAS PubMed.
- J. L. Eguiburu, J. J. Iruin, M. J. Fernandez-Berridi and J. S. Roman, Polymer, 1998, 39, 6891–6897 CrossRef CAS.
- C. Samuel, J.-M. Raquez and P. Dubois, Polymer, 2013, 54, 3931–3939 CrossRef CAS PubMed.
- C. Samuel, J. Cayuela, I. Barakat, A. J. Müller, J.-M. Raquez and P. Dubois, ACS Appl. Mater. Interfaces, 2013, 5, 11797–11807 CAS.
- C. Samuel, S. Barrau, J. M. Lefebvre, J. M. Raquez and P. Dubois, Macromolecules, 2014, 47, 6791–6803 CrossRef CAS.
- T. Shirahase, Y. Komatsu, Y. Tominaga, S. Asai and M. Sumita, Polymer, 2006, 47, 4839–4844 CrossRef CAS PubMed.
- R.-Y. Bao, W. Yang, X.-F. Wei, B.-H. Xie and M.-B. Yang, ACS Sustainable Chem. Eng., 2014, 2, 2301–2309 CrossRef CAS.
- M. Weng and Z. Qiu, Macromolecules, 2014, 47, 8351–8358 CrossRef CAS.
- S. Saeidlou, M. A. Huneault, H. Li, P. Sammut and C. B. Park, Polymer, 2012, 53, 5816–5824 CrossRef CAS PubMed.
- S. Barrau, C. Vanmansart, M. Moreau, A. Addad, G. Stoclet, J. M. Lefebvre and R. Seguela, Macromolecules, 2011, 44, 6496–6502 CrossRef CAS.
- L. Cartier, T. Okihara and B. Lotz, Macromolecules, 1997, 30, 6313–6322 CrossRef CAS.
- C.-F. Yang, Y.-F. Huang, J. Ruan and A.-C. Su, Macromolecules, 2012, 45, 872–878 CrossRef CAS.
|
This journal is © The Royal Society of Chemistry 2015 |
Click here to see how this site uses Cookies. View our privacy policy here.