DOI:
10.1039/C5RA00537J
(Paper)
RSC Adv., 2015,
5, 19091-19105
Superior elastomeric nanocomposites with electrospun nanofibers and nanoparticles of CoFe2O4 for magnetorheological applications†
Received
10th January 2015
, Accepted 9th February 2015
First published on 9th February 2015
Abstract
We show for the first time the greatly enhanced magnetic and magnetorheological (MR) properties of CoFe2O4–silicone elastomer (cross-linked polydimethylsiloxane) composites containing electrospun CoFe2O4 nanofibers. The effects of CoFe2O4 particle shape (spherical to fibrous), concentration and degree of alignment in the elastomeric matrix are explored. Low nanofiber loadings (5–10 wt%) give MR properties comparable to those obtained by much higher microparticle additions (60–80 wt%) for the same polymer matrix. Compared to spherical nanoparticles, the nanofiber composites have 100–400% improvement in MR properties that are vital in tunable rheology applications such as vibration damping, variable stiffness devices, actuators, etc. The nanofibers effectively formed an interconnected network within the polymer matrix but nanoparticles exhibited large gaps between two disconnected short particle chains at lower filler loading. Spherical particles with 69.46 emu g−1 saturation magnetization were synthesized by ultrasonic assisted co-precipitation method using a novel precipitating solvent (i.e. propylamine) followed by calcination. The nanofibers were prepared by electrospinning a precursor of CoFe2O4 in a sacrificial polymer solution of polyvinylpyrrolydone (PVP) followed by calcination of electrospun fibers. Crystal structure and magnetic properties of the CoFe2O4 nanofillers were evaluated by X-ray diffraction (XRD), transmission electron microscopy (TEM) and vibrating sample magnetometery (VSM), which showed the generation of larger crystallite size with greater coercivity and remnant magnetization in the nanofibers compared to nanoparticles. Thin films of the nanocomposites containing nanoparticles and nanofibers were prepared with 5 and 10 wt% of CoFe2O4. Anisotropic characteristics of the nanocomposites were generated by applying an in situ magnetic field of 0.4 T during solution casting of thin composite films. The magnetorheological study revealed that at 1.023 T, the isotropic nanocomposites with 10 wt% nanofibers showed absolute and relative MR effects of 4.4 kPa and 3.21%, respectively, compared to the corresponding nanoparticle containing counterpart's values of 2.0 kPa and 0.64%.
1. Introduction
Magnetorheological elastomers (MREs) comprising an elastomer matrix filled with micro- or nano-sized inorganic magnetic particles have attracted much attention owing to their tunable magnetic and rheological properties harvested for applications involving actuators,1,2 sensors,3,4 vibration dampers,5,6 variable stiffness devices,7–9 valves,10 etc. An effective MRE must possess a high relative MR effect (ratio of increase in the storage modulus under the external magnetic field to the zero field modulus) as well as a large magnetic field induced storage modulus.11 The ultimate magnetorheological, mechanical and magnetic properties of MREs are dependent on the choice of elastomer matrix and magnetic particles, strength of external magnetic field, volume fraction of each component, distribution of particles in the elastomer matrix, permeability of the magnetic particles, interface between particles and elastomer matrix, particle shape, particle size, orientation, etc.12–18 Plasticization of a polymer matrix by silicon oil is another efficient method to achieve a higher MR effect by reducing the zero field storage modulus of the MRE.19–21 Apart from these functions, a plasticizer helps in the dissipation of internal stress of the MRE by averaging its distribution within the matrix.22
In the literature different elastomer matrix, e.g., natural rubber (NR), polyurethane (PU), cis-polybutadiene (BR), silicone rubber (SR) and silicone elastomer (SE) with spherical micron sized carbonyl iron particle have been extensively tried for development of MREs.23–29 There are also several reports on the use of different types of other magnetic particles e.g. SrFe12O19, BaFe12O19, SmCo5, Nd2Fe14B, and iron in silicone elastomer (SE) for efficient MRE applications.2,30,31 Silicone rubber and silicone elastomer has been the widely used polymer matrix because of their low temperature curability and low initial storage modulus which ultimately leads to the greater MR effect in the MREs.
Most of the above studies are on higher percentage (60 to 80 wt%) of micron sized magnetic particles based MREs. This high particle content may cause non-uniformities in the composites by particle agglomeration, destroy the continuity of the filler particles and negatively affect the elasticity of elastomer matrix.32 Moreover, high loading severely affects the viscosity, make processing difficult and increases material cost. Therefore, efforts are being made to develop MRE with low particle loading which eventually leads to low material cost. Nanoparticles are the materials of choice to achieve significant MR effect at low filler loading as they can readily form 3D network structure of the magnetic particles inside the polymer matrix. This network structure leads to the better specific interaction of the magnetic fillers with externally applied magnetic field and hence results in enhanced MR performance.33 However, optimization of saturation magnetization, physical shape and size of nanofiller, extent of their orientation during fabrication are needed to get high performance MREs at low nano filler loading.
Recently magnetorheological properties of polydimethylsiloxane (PDMS)/bimetallic FeCo3 nanoparticles (20–30 nm) have been investigated which show that relatively low (5–20 wt%) loadings of nanoparticles can achieve the MR characteristics obtainable with much higher loadings of microparticles.34 There are also several reports which revealed improved mechanical (like tensile strength, yield stress and damping properties, compressive modulus), magnetic, rheological and magnetorheological properties of different magnetic nanocomposites.35–40
Nanowire/nanofiber based MREs are expected to be superior compared to the nanoparticles based MREs because of their large aspect ratio which enables them to form more efficient interconnected 3D network at the lower concentrations than that of the nanoparticles. Excellent magnetic properties like greater saturation magnetization, coercivity, remnant magnetization and magnetic anisotropy have been reported for fiber, nanowire and nanochains containing PDMS nanocomposites compared to that of nanoparticles filled nanocomposites at low filler loading.41–43 Although there are several reports on the magnetic and mechanical properties of nanofibers/nanowires based MREs, there are only few reports on the investigation of magnetorheology (change in dynamic stiffness and equivalent damping coefficient as function of frequency or strain amplitude under variable magnetic field) of the nanowires/nanochains filled silicone rubber and silicone elastomer composites.44,45 However, to the best of our knowledge, magnetorheological properties like shear modulus, storage and loss moduli as function of frequency, strain amplitude and variable magnetic field have not been explored for magnetic nanofibers based elastomer composites. These properties are of paramount importance when considering the applications of MREs. In this context, the relative efficacy of the nanowires and nanofibres in place of nanoparticles could be utilized to make superior MREs.
Among the different types of magnetic materials, CoFe2O4 shows moderately high saturation magnetization and coercivity along with large magnetic anisotropy.46 Hence it is an appropriate material for development of MREs. Antonel et al.47 investigated the elastic and magnetic properties of the PDMS based MRE containing ferro- and super paramagnetic CoFe2O4 nanoparticles. However, magnetorheology of CoFe2O4 nanofiller in fiber and particulate forms in PDMS elastomer matrix have not been explored to date. This work investigates for the first time the comparative efficiency of nanofibers and nanoparticles on MR properties of CoFe2O4 filled PDMS nanocomposites. The nanoparticles with high saturation magnetization value were synthesized by co-precipitation method using unique precipitating solvent i.e. propylamine. The nanofibers of comparable saturation magnetization were prepared via electrospinning techniques. Magnetic nanofillers were characterized for structural, morphological and magnetic properties in transmission electron microscope (TEM) and vibrating sample magnetometer (VSM). The effect of nanofiller concentration and their relative orientation on magnetic and MR properties of PDMS were demonstrated by fabricating nanocomposites with varying nanofiller content in presence and absence of magnetic field. FESEM and optical microscopic studies were carried out to acquire further insights into phase morphology and correlation between the microstructure and observed MR properties.
2. Experimental section
2.1 Materials
FeCl3·6H2O (purity 99.0%) and sodium salt of dodecyl sulfate (85%) were supplied by Across Organics, USA. Fe(NO3)3·9H2O (purity 98.0%) was purchased from Qualigens Fine Chemicals Ltd., India. Co(NO3)2·6H2O (purity 99%), citric acid monohydrate (purity 99.5%) and glacial acetic acid (purity 99.7%) were obtained from Samir Tech-Chem Pvt. Ltd., India. CoCl2·6H2O (purity 98%) was purchased from E. Merck (India) Ltd. Propyl amine (purity >99%) and ethanol (purity 99.5%) were obtained from E. Merck, Germany. Polyvinylpyrrolydone (PVP, MW = 1
300
000), acetone (purity 99.0%) were supplied by Alfa Aesar Co., USA. Sylgard 184 [(silicone elastomer (SE)] was purchased from Dow Corning Corporation, USA and silicon oil [i.e. polydimethylsiloxane 200 fluid, viscosity 100 cSt)] was supplied by Aldrich Chemical Co., USA.
2.2 Synthesis of CoFe2O4 nanoparticle
Initially 50 ml 0.5 M FeCl3·6H2O and 50 ml 0.25 M CoCl2·6H2O solutions were prepared by dissolving calculated amount (weighed in an electronic balance, accuracy ±0.1 mg) of the above chemicals in de-ionized water in a 500 ml beaker at room temperature (RT). Afterwards 125 ml of 6 mM solution of sodium dodecyl sulfate (NaDS) was added. Fe3+ and Co2+ ions present in the solution combined with the dodecyl sulfate to form micellar solution of Fe(DS)3 and Co(DS)2. These micelles acted as a separate entity and prevent the nanoparticle from agglomeration during co-precipitation. The temperature of the solution was raised to 50 °C and 100 ml of 40% propyl amine solution was added drop wise under continuous stirring followed by ultrasonication by an ultrasonicator (Model no. GEX 750, Cole-Parmer India, power 750 Watt, frequency 20 kHz) for 5 h to complete the co-precipitation. The dark colored precipitate was filtered and washed with de-ionized water for 6 times to remove any residual NaDS. The precipitate was then dried in vacuum oven at 100 °C for 6 h and grinded in mortar pestle. Calcination was done in a muffle furnace at 600 °C in air for 6 h at a heating rate of 20 °C min−1 and was allowed to cool down to RT by ambient cooling.
2.3 Preparation of CoFe2O4 precursor solution for electrospinning
2.02 g of Fe(NO3)3·9H2O and 0.7275 g of Co(NO3)2·6H2O were dissolved in 15 ml of de-ionized water in a 100 ml beaker in order to maintain the molar ratio of Fe3+ and Co2+ at 2
:
1. Then 1.577 g of citric acid monohydrate was added to maintain the molar ratio of metal nitrates and citric acid at 1
:
1. 3 g glacial acetic acid was added to make pH < 7. The mixture was then stirred by magnetic stirrer at 60 °C for 3.5 h at slow stirring rate and finally at 80 °C for another 1.5 h to obtain the cobalt ferrite precursor gel. Simultaneously the polymer solution was made by dissolving 0.5 g PVP in 3.5 ml de-ionized water by magnetically stirring for 6 h. 1.5 ml (2.24 g) of the above precursor gel was mixed with the PVP solution with continued stirring for 12 h to prepare a homogeneous solution for electrospinning.
2.4 Electrospinning of CoFe2O4 nanofibers
The spinning solution was loaded in a 5 ml disposable syringe having a 0.55 × 25 mm/24 × 1 needle (see schematic of electrospinning setup in Fig. S1 of ESI†). The distance between the drum and needle was maintained at 9.5 cm. The drum wrapped with an aluminium foil acted as a collector on rotation at speed fixed at 500 r.p.m. The anode of the high voltage power supply system was attached to the needle by means of a clip and a positive voltage of 19 kV was applied. The solution was then pumped through the needle at a constant flow rate of 5 μl min−1. The charged solution formed a Taylor cone from which a jet stretched to form nanofibers and drawn on an aluminium foil glued on a rotating drum electrode. Electrospun nanofibers were subsequently removed from the foil and dried at 80 °C for 3 h. The dried nanofibers were calcined both at 600 °C and 800 °C for 6 h in a tubular furnace under air atmosphere and optimized for calcination temperature. The heating rate of the furnace was set at 5 °C min−1 and after 6 h calcination the furnace was allowed to cool to room temperature by ambient cooling. During calcination the polymer was completely burnt, as confirmed by TGA analysis and only the nanofibers of CoFe2O4 were formed. The CoFe2O4 nanofibers calcined at 800 °C temperature were used for composite fabrication because of its comparable saturation magnetization value as that of the CoFe2O4 nanoparticles. In what follows, only the CoFe2O4 nanofibers fabricated under the optimal conditions of electrospinning and calcination are discussed unless otherwise stated.
2.5 Fabrication of CoFe2O4–PDMS nanocomposites
In this study both CoFe2O4 particle based PDMS nanocomposites (p-CoFe2O4–PDMS NCs) and CoFe2O4 fiber based PDMS nanocomposites (f-CoFe2O4–PDMS NCs) containing 5 wt% and 10 wt% magnetic fillers with respect to the Sylgard 184 were fabricated by casting technique (see ESI for details about Sylgard 184 and its crosslinking reaction (Scheme I†)). Sylgard 184 is available in two pack system.48 In a typical method measured quantity of magnetic fillers were first dispersed in the mixture of base polymer (Sylgard 184 Part 1), silicon oil and 0.5 ml acetone by ultrasonication for 30 minutes. Acetone evaporated and left behind a homogeneous mixture. Curing agent (Sylgard 184 Part 2) was then added and mixed thoroughly. The resultant mixture was then kept under vacuum of −30 inches of mercury for 15 minutes in a vacuum oven to eliminate the bubbles of the curing reaction. Finally it was divided into two parts equally by weighing and casted on two separate Petridis of same size. Petridis 1 was subjected to the homogeneous magnetic field of 0.4 T for 30 minutes in an electromagnet (Walker Scientific Inc., Worcester, USA, Model no. HV-5H) by placing it between the two poles of the electromagnet to orient the magnetic fillers along the direction of magnetic field lines. To fabricate the anisotropic nanocomposite, the mixture was cured at 40 °C for 4 hours to freeze the filler orientation quickly and then cured at the room temperature for another 24 hours. Similar curing condition was followed for Petridis 2 without prior magnetic alignment of the fillers to obtain the isotropic nanocomposites. Finally after curing, circular nanocomposite samples of 0.7 mm thickness were obtained and used for characterization (see Fig. S2 and S3 of ESI† for the evidence of crosslinking).
The compositions of the nanocomposites are presented in Table 1. All the above nanocomposites in the Table 1 and the neat PDMS control contain 6 g base polymer (Sylgard 184 Part 1), 0.4 g curing agent (Sylgard 184 Part 2) and 1.8 g silicon oil.
Table 1 Composition of the CoFe2O4–PDMS nanocomposites
Sample details |
CoFe2O4 nanoparticles (g) |
CoFe2O4 nanofibers (g) |
5 wt% p-CoFe2O4–PDMS isotropic NC |
0.3 |
— |
5 wt% p-CoFe2O4–PDMS anisotropic NC |
0.3 |
— |
10 wt% p-CoFe2O4–PDMS isotropic NC |
0.6 |
— |
10 wt% p-CoFe2O4–PDMS anisotropic NC |
0.6 |
— |
5 wt% f-CoFe2O4–PDMS isotropic NC |
— |
0.3 |
5 wt% f-CoFe2O4–PDMS anisotropic NC |
— |
0.3 |
10 wt% f-CoFe2O4–PDMS isotropic NC |
— |
0.6 |
10 wt% f-CoFe2O4–PDMS anisotropic NC |
— |
0.6 |
3. Characterization
3.1 Thermogravimetric analysis
The thermal degradation temperature of pure PVP was investigated in Thermogravimetric Analyzer (Model SDT Q 600, TA Instrument, USA) under air atmosphere by heating the sample to 700 °C at a rate of 10 °C min−1.
3.2 X-ray diffraction
X-ray diffraction spectra of CoFe2O4 nanofibers and nanoparticles were recorded at room temperature in X'Pert PRO, PAN-analytical, Netherland, XRD instrument using Cu Kα radiation in the 2θ range of 10° to 80° with step size 0.0295431° per second to examine the crystal structure and crystalline phase present in the samples.
3.3 Vibrating sample magnetometer study
Vibrating sample magnetometer study of the CoFe2O4 nanofibers and nanoparticles were performed in GMW Magnet System (Model no. 3472-70), San Carlos, USA at room temperature to investigate the magnetic properties of the samples. Rectangular elastomeric nanocomposite samples were also investigated for magnetic properties and magnetic anisotropy by recording the hysteresis curves at 0° (parallel to the particle chain alignment in the anisotropic nanocomposite and along the length in isotropic nanocomposite) and 90° (perpendicular to the particle chain alignment in the anisotropic nanocomposite and along the width in isotropic nanocomposite). The Zero Field Cooled (ZFC) and Field Cooled (FC) curves of CoFe2O4 (both nanoparticles and nanofibers) were obtained in VSM attached to the Physical Property Measurement System (PPMS), Model 6000, Quantum Design, USA. During ZFC measurement the sample was cooled to 4 K without applied magnetic field. At 4 K temperature, very weak magnetic fields of 100 Oe was applied on the sample and subsequently heated from 4 K to 100 K at a heating rate of 2 K min−1 and from 100 K to 350 K at a rate of 5 K min−1 to acquire the magnetization curve as a function of temperature. However, FC curves was obtained first by cooling the sample to 4 K with 100 Oe applied magnetic field and consequently magnetization curve was recorded by heating the sample to 350 K under similar heating conditions as mentioned earlier.
3.4 Microscopic analysis
Cobalt ferrite precursor/PVP composite nanofibers, CoFe2O4 nanofibers, CoFe2O4 nanoparticles and elastomeric nanocomposites were investigated in the FESEM (Quanta 200, Zeiss, Germany) for morphological analysis, fiber diameter determination and microstructure evaluation. All the samples were made conductive by sputter coating prior to the investigation in the microscope. TEM analysis was carried out in Tecnai, USA (Model no. FEIG2 T2) to investigate the microstructure, particle size distribution and crystalline structure of the nanofillers. Elastomeric nanocomposites were also examined in Zeiss Inverted Optical Microscope to examine the filler distribution and alignment within the nanocomposites.
3.5 Rheological analysis
The magnetorheological properties of the elastomeric nanocomposites were evaluated in a Parallel plate rheometer (Physica MCR 301, Anton Paar, Germany) using a magnetorheological device (MRD 180). The device can generate variable magnetic field perpendicular to the shear flow during the measurement. The magnetic field can be changed by controlling the current through the coil. Both steady-state rotary and oscillatory shear test were performed by placing the nanocomposite samples in the cavity of the base plate. The samples were subsequently sheared between the base plate and top plate (diameter 20 mm) to investigate the static and dynamic mechanical properties. In the static test the strain was varied from 0 to 300% to obtain the stress vs. strain curve at four different magnetic fields, namely, 0.281 T, 0.567 T, 0.819 T and 1.023 T. Dynamic mechanical properties were evaluated by conducting strain amplitude sweep test and angular frequency sweep test. In strain amplitude sweep test both storage and loss moduli were measured in the strain range 0.01 to 100 % at constant frequency of 1 Hz under aforesaid four different magnetic fields. Similarly angular frequency sweep tests were performed by measuring the storage and loss moduli of the nanocomposites in the frequency range 1 to 200 rad s−1 at constant strain amplitude of 1%. To investigate the MR properties of the nanocomposites magnetic flux density sweep test was carried out in the range of 0 to 1.023 T at constant strain amplitude and frequency of 1% and 1 Hz, respectively.
4. Results and discussion
4.1 Thermogravimetric analysis
Fig. 1(a) and (b) are the TGA thermogram and corresponding derivative plot of pure PVP. It is observed that the onset of degradation and peak degradation temperatures of PVP are 387 °C and 417 °C, respectively. Maximum amount of PVP is degraded within 462 °C temperature and thereafter degradation of the polymer takes place very slowly. At 600 °C, 96.764 wt% polymers is degraded and left with 3.236 wt% polymer residue. However, all residual polymers are completely burnt off at 650 °C temperature. Hence the composite nanofibers are finally heated at 800 °C temperature to ensure no polymer residue in the resultant CoFe2O4 nanofibers as well as to achieve higher saturation magnetization value.
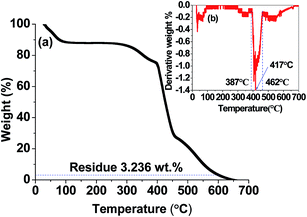 |
| Fig. 1 (a) TGA thermogram of pure PVP (b) derivative plot of TGA thermogram. | |
4.2 X-ray diffraction
The synthesized magnetic nanoparticles are characterized by X-ray diffraction technique to confirm the magnetic phase present in it. Fig. 2(a) corresponds to the X-ray diffraction pattern of synthesized magnetic nanoparticles. The spectra exhibit crystalline peaks at 2θ value 30.29°, 35.43°, 37.18°, 43.14°, 53.46°, 56.90°, 62.54° and 74.20°, respectively. The peaks are compared with JCPDS file no. 22-1086 and corresponds to the (220), (311), (222), (400), (422), (511), (440) and (533) crystal planes, respectively. The most intense peak is observed at 2θ value of 35.43° which is also identical with the database. This above diffraction pattern supports the formation of CoFe2O4 phase within the magnetic nanoparticles and also reveals the presence of cubic spinel type lattice structure of CoFe2O4. Lattice parameter ‘a’ calculated from the XRD spectra corresponding to the (311) plane is found to be 0.83824 nm which is almost equal to reported value of 0.83919 nm in the JCPDS 22-1086. The average crystallite size (D) of the nanoparticles is determined from most intense peak using the Debye–Scherrer equation,49 D = kλ/β
cos
θ, where k is the Scherrer constant and its value is 0.9, λ is the wavelength of the X-ray radiation in nm, β is the full angular line width in radians at half maximum intensity, θ is the Bragg's angle in degree. From this equation the average crystallite size appears to be 63.86 nm.
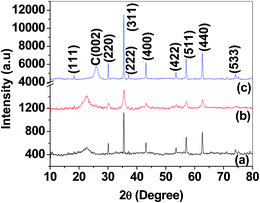 |
| Fig. 2 X-ray diffraction spectra of (a) CoFe2O4 nanoparticles (b) CoFe2O4 nanofibers calcined at 600 °C (c) CoFe2O4 nanofibers calcined at 800 °C. | |
Fig. 2(b) represents the XRD spectra of CoFe2O4 nanofibers obtained after calcination at 600 °C. The spectra show that all the crystalline peaks are in their anticipated positions as described in the XRD spectra of CoFe2O4 nanoparticles. It is also characterized by a broad peak at 2θ value of 22.73° due to the presence of carbon (3.236 wt% as revealed by TGA) by the incomplete oxidation of PVP during the calcination. The presence of carbon is also supported by the low saturation magnetization value of CoFe2O4 nanofibers obtained in the VSM study. Fig. 2(c) shows the XRD spectra of CoFe2O4 nanofibers obtained after calcination at 800 °C. The additional peaks at 2θ value 18.27° and 25° are attributed to the (111) crystal plane of the CoFe2O4 and traces of impurities or entrapped carbon inside the nanofibers. The lattice parameter ‘a’ calculated from the XRD spectra corresponding to the (311) planes appears to be 0.83687 nm and 0.83860 nm for the CoFe2O4 nanofibers calcined at 600 °C and 800 °C temperature, respectively. The VSM study also reveals 2.35 fold increases in the saturation magnetization value for the CoFe2O4 nanofibers calcined at 800 °C. Average crystallite size measured by the Debye–Scherrer equation is found to be 27.4 nm and 72.7 nm respectively for 600 °C and 800 °C calcined nanofibers. Hence the crystallite size and saturation magnetization value increases with increase in calcination temperature. This could be attributed to the fact that higher calcination temperature leads to the more pure spinel structure with higher crystallization degree and larger crystallite size which in turn increases the magnetic phase and thus the specific magnetization value of the nanofibers. As the energy of the magnetic material in the external magnetic field depends on the number of magnetic molecules present within the single magnetic domain therefore increased particle size or crystallite size always bring about the higher saturation magnetization value.50
4.3 Vibrating sample magnetometer study
Fig. 3(a) corresponds to the specific magnetization curve of CoFe2O4 nanoparticles and Fig. 3(b) and (c) are that of nanofibers calcined at 600 °C and 800 °C temperature, respectively. The saturation magnetization, coercive field and remnant magnetization of CoFe2O4 nanoparticles appears to be 69.46 emu g−1, 861.01 Oe and 29.57 emu g−1, respectively. Whereas the corresponding values for nanofibers calcined at 600 °C and 800 °C temperature are 28.61 emu g−1, 758.62 Oe, 8.28 emu g−1 and 67.24 emu g−1, 2221.51 Oe, 35.11 emu g−1, respectively. From the above values we can observe that the saturation magnetization value of nanofibers calcined at 600 °C is very much lower than that of the nanoparticle's saturation magnetization which can be attributed to the incomplete oxidation of PVP during the calcination process as evidenced by TGA and the broad peak in the XRD spectrum. This result is further supported by the low saturation magnetization value of the same. Increase of calcination temperature from 600 °C to 800 °C leads to the 2.35 fold increase in the saturation magnetization value of the CoFe2O4 nanofibers, however the saturation magnetization value of the nanoparticles is still higher than the nanofibers calcined at 800 °C temperature. Moreover, saturation magnetization value of both nanoparticles and nanofibers are lower than the bulk value of 80.8 emu g−1.51 This can be explained considering the core–shell model which demonstrates that the finite size effect of nanofillers results in non-collinearity or canting of spin on their surface and ultimately lead to the reduced magnetization value.52,53 Traces of carbon and entrapped air within the nanofibers also contribute in reducing the magnetization value. The hysteresis patterns of the nanoparticles and nanofibers calcined at 600 °C and 800 °C temperature reveals their soft magnetic nature with hysteresis ferromagnetism in the applied field range of ±5500 Oe, ±6500 Oe and ±9500 Oe, respectively. High temperature calcined CoFe2O4 nanofibers shows increased coercive field value than the low temperature calcined nanofibers. This is attributed to the larger particle or crystallite size of the CoFe2O4 nanofibers.54 Therefore the nanofibers become magnetically harder as the calcination temperature is increased from low to the higher value. Fig. 3 (d) and (e) are the ZFC and FC curves of CoFe2O4 nanoparticles and nanofibers, respectively. It can be observed that for both nanoparticles as well as nanofibers, the ZFC and FC curves approaches close to each other with the increase in temperature and at 350 K temperature the curves almost overlap to each other. This clearly indicates that blocking temperature is higher than 350 K and above this temperature both nanoparticle and nanofibers exhibit superparamagnetic behavior. Both the nanoparticles and nanofibers show a significant change in magnetization value (shift in FC curves) at 115.17 K and 315.72 K temperature, respectively which could be attributed to the long range coupling of nanocrystal assembly constituting the nanoparticles and nanofibers. The higher coupling temperature of nanofibers with respect to the nanoparticle may be due to the larger crystallite size (72.7 nm) of the nanofibers than the nanoparticles (63.86 nm). Moreover magnetization value of the nanofibers is observed to be increased at higher rate in comparison to the nanoparticle. This is due to the higher magnetocrystalline anisotropy resulting from the inter particle interaction and geometrical shapes of the nanofibers.55 Mr/Ms value is the measure of magnetocrystalline anisotropy and exchange interactions for ferrite nano materials.56 Stoner–Wohlfarth model suggests that a theoretical value of 0.5 for Mr/Ms corresponds to non-interacting particles with uniaxial single domain and randomly oriented easy axis.57 In our case nanoparticles and 800 °C calcined nanofibers show Mr/Ms value of 0.425 and 0.522, respectively. Hence CoFe2O4 nanoparticle exhibits uniaxial single domain whereas nanofibers indicate the presence of multidomain particles and thus the greater magnetocrystalline anisotropy as discussed earlier.
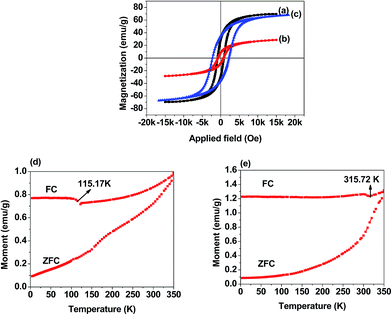 |
| Fig. 3 M vs. H curve of (a) CoFe2O4 nanoparticles (b) CoFe2O4 nanofibers calcined at 600 °C (c) CoFe2O4 nanofibers calcined at 800 °C; M vs. T curve of (d) CoFe2O4 nanoparticles (e) CoFe2O4 nanofibers. | |
Magnetic parameters (obtained from corresponding hysteresis curves) of all the nanocomposites are presented in Table 2. (See Fig. S4(a) to (h) in ESI† for hysteresis curves of isotropic and anisotropic p-CoFe2O4–PDMS NCs and f-CoFe2O4–PDMS NCs). It is observed that for both isotropic and anisotropic f-CoFe2O4–PDMS NCs and isotropic p-CoFe2O4–PDMS NCs coercive field measured at 0° are higher than the corresponding 90° measured value. However, for anisotropic p-CoFe2O4–PDMS NCs reverse trend is observed. The remnant magnetization and saturation magnetization are always higher at 0° than the corresponding 90° measured value irrespective of the type of magnetic filler (nanoparticles or nanofibers) present in the composites.
Table 2 Magnetic properties of the p-CoFe2O4–PDMS and f-CoFe2O4–PDMS nanocomposites
Sample name |
Hc (Oe) |
Mr (emu g−1) |
Ms (emu g−1) |
Diff. between Ms values (emu g−1) |
0° |
90° |
0° |
90° |
0° |
90° |
5 wt% p-CoFe2O4–PDMS isotropic NC |
1800 ± 9 |
1798 ± 8.99 |
0.98 ± 0.01 |
0.82 ± 0.008 |
2.52 ± 0.025 |
2.10 ± 0.020 |
0.42 ± 0.005 |
5 wt% p-CoFe2O4–PDMS anisotropic NC |
1800 ± 9 |
1807 ± 9.04 |
1.28 ± 0.013 |
0.75 ± 0.007 |
3.07 ± 0.030 |
2.10 ± 0.020 |
0.97 ± 0.009 |
10 wt% p-CoFe2O4–PDMS isotropic NC |
1798 ± 8.99 |
1790 ± 8.95 |
2.22 ± 0.022 |
1.87 ± 0.019 |
5.78 ± 0.058 |
4.81 ± 0.050 |
0.97 ± 0.008 |
10 wt% p-CoFe2O4–PDMS anisotropic NC |
1787 ± 8.93 |
1805 ± 9.02 |
1.56 ± 0.016 |
0.88 ± 0.009 |
3.61 ± 0.036 |
2.52 ± 0.025 |
1.09 ± 0.011 |
5 wt% f-CoFe2O4–PDMS isotropic NC |
2360 ± 11.8 |
2353 ± 11.76 |
1.73 ± 0.017 |
1.08 ± 0.010 |
3.32 ± 0.033 |
2.19 ± 0.021 |
1.13 ± 0.012 |
5 wt% f-CoFe2O4–PDMS anisotropic NC |
2384 ± 11.92 |
2338 ± 11.69 |
1.81 ± 0.018 |
1.04 ± 0.010 |
3.11 ± 0.031 |
2.20 ± 0.022 |
0.91 ± 0.009 |
10 wt% f-CoFe2O4–PDMS isotropic NC |
2360 ± 11.8 |
2355 ± 11.77 |
2.59 ± 0.026 |
2.03 ± 0.02 |
5.00 ± 0.050 |
4.10 ± 0.041 |
0.90 ± 0.009 |
10 wt% f-CoFe2O4–PDMS anisotropic NC |
2418 ± 12.09 |
2307 ± 11.54 |
2.31 ± 0.023 |
1.79 ± 0.018 |
5.40 ± 0.055 |
3.96 ± 0.040 |
1.44 ± 0.015 |
Anisotropic coefficient is expressed as the ratio of saturation magnetization measured at 0° (M2) and 90° (M1) of the composite samples under 103 Oe magnetic field. Table 3 lists the anisotropic coefficients of all the nanocomposites and demonstrates that the value of anisotropy coefficient is greater for anisotropic nanocomposites than their corresponding isotropic counterparts except for the 5 wt% f-CoFe2O4–PDMS NC. This result clearly proves the particle alignment in the anisotropic nanocomposites.
Table 3 Anisotropic coefficient of the p-CoFe2O4–PDMS and f-CoFe2O4–PDMS nanocomposites at 103 Oe magnetic field
Sample details |
Magnetization (M2) in emu g−1 measured at 0° and 103 Oe |
Magnetization (M1) in emu g−1 measured at 90° and 103 Oe |
Anisotropic coefficient (M2/M1) |
5 wt% p-CoFe2O4–PDMS isotropic NC |
2.35 ± 0.023 |
1.96 ± 0.019 |
∼1.198 |
5 wt% p-CoFe2O4–PDMS anisotropic NC |
2.85 ± 0.028 |
1.97 ± 0.02 |
∼1.446 |
10 wt% p-CoFe2O4–PDMS isotropic NC |
5.38 ± 0.054 |
4.46 ± 0.044 |
∼1.206 |
10 wt% p-CoFe2O4–PDMS anisotropic NC |
3.38 ± 0.034 |
2.33 ± 0.023 |
∼1.45 |
5 wt% f-CoFe2O4–PDMS isotropic NC |
3.10 ± 0.031 |
2.06 ± 0.021 |
∼1.50 |
5 wt% f-CoFe2O4–PDMS anisotropic NC |
2.91 ± 0.029 |
2.05 ± 0.020 |
∼1.43 |
10 wt% f-CoFe2O4–PDMS isotropic NC |
4.66 ± 0.047 |
3.83 ± 0.038 |
∼1.21 |
10 wt% f-CoFe2O4–PDMS anisotropic NC |
5.07 ± 0.050 |
3.70 ± 0.037 |
∼1.37 |
Furthermore anisotropic coefficient values are almost same both in 5 wt% and 10 wt% anisotropic p-CoFe2O4–PDMS NCs, but a large reduction in anisotropic coefficient is observed between 5 wt% and 10 wt% anisotropic f-CoFe2O4–PDMS NCs. This suggests that much higher nanoparticles loading is required for the conversion of anisotropic nanocomposites to the isotropic one. However, for the nanofibers filled composites, this conversion takes place at much lower filler loading. Due to the larger aspect ratio, nanofibers can form interconnected network at much lower filler loading compared to nearly spherical nanoparticles which could not form interconnected particle chain networks at low filler content (as evident by large gaps between the two disconnected short particles chains). As evidenced from the hysteresis curves, both p-CoFe2O4–PDMS NCs and f-CoFe2O4–PDMS NCs show the characteristics of soft ferromagnetic behavior.
Table 2 depicts that the nanocomposites with higher magnetic filler loading show greater saturation magnetization values. This can be attributed to the decrease in both the distance between the magnetic fillers and quantity of anti-ferromagnetic PDMS matrix layer on the surface of magnetic fillers. It is also noticeable that the saturation magnetization of f-CoFe2O4–PDMS NCs are greater than the respective p-CoFe2O4–PDMS NCs at 5 wt% filler loading. However, at 10 wt% filler loading, isotropic p-CoFe2O4–PDMS NC shows greater saturation magnetization compared to f-CoFe2O4–PDMS NCs and reverse phenomena is observed in anisotropic nanocomposites. This can be explained considering two parallel phenomena (viz. interparticle distance and saturation magnetization value of the magnetic fillers) contributing to the saturation magnetization value of the nanocomposites. Since the distance between the nanofibers is smaller than the distance between the nanoparticles, f-CoFe2O4–PDMS NCs exhibit greater saturation magnetization than the p-CoFe2O4–PDMS NCs at low filler loading.41 However, at 10 wt% filler loading, the contribution from the saturation magnetization value of the magnetic filler predominates over the contribution from the decreased distance because of higher saturation magnetization of CoFe2O4 nanoparticles than the CoFe2O4 nanofibers. Thus, 10 wt% isotropic p-CoFe2O4–PDMS NCs exhibit greater saturation magnetization value than their corresponding f-CoFe2O4–PDMS NCs. The higher saturation magnetization of 10 wt% anisotropic f-CoFe2O4–PDMS NC compared to the 10 wt% anisotropic p-CoFe2O4–PDMS NC derives from the better interconnected structure of the former.
4.4 Structure, morphology and particle distribution
Fig. 4(a), (c) and (e) are the FESEM images of CoFe2O4 precursor gel/PVP composite nanofibers before calcination and CoFe2O4 nanofibers obtained after calcination at 600 °C and 800 °C temperature, respectively. Fig. 4 (b), (d) and (f) show the fiber diameter distribution histograms of the respective nanofibers. These images reveal that the electrospun nanofibers fabricated under optimized conditions are free from any beads. The composite nanofibers are characterized by wide fiber diameter distribution with mean diameter of 271 nm. CoFe2O4 nanofibers obtained by calcination at 600 °C have a reduced mean diameter of 145 nm, which decreases further to 131 nm as the calcination temperature is raised to 800 °C. This demonstrates that the higher calcination temperature leads to the small fiber diameter of the nanofibers. Fig. 4(g) is the FESEM images of broken CoFe2O4 nanofibers (calcined at 800 °C) resulting after ultrasonication for 15 minutes in acetone. The micrograph shows a wide distribution of the fiber lengths from few hundreds of nanometer to few micrometers. Fig. 4(h) and (i) represent the morphology and particle size of the CoFe2O4 nanoparticles synthesized by co-precipitation method. From Fig. 4(h) it is seen that the nanoparticles form clusters. Higher magnification image {Fig. 4(i)} further shows that the primary nanoparticles are nearly spherical with maximum population in the size range between 60 to 75 nm which also matches well with the average crystallite size determined by the Debye–Scherrer equation.
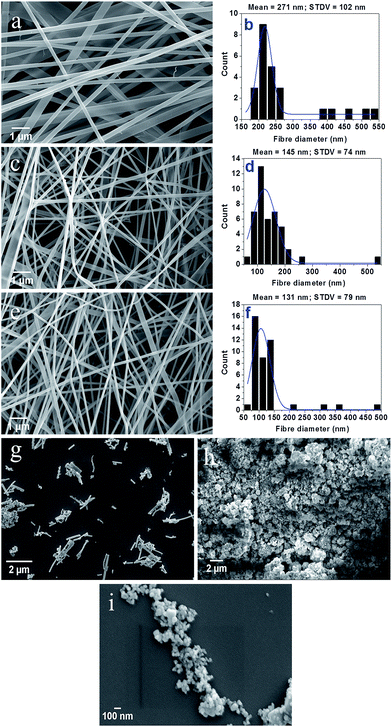 |
| Fig. 4 FESEM image of (a) CoFe2O4 precursor gel/PVP composite nanofibers, (b) diameter distribution; (c) CoFe2O4 nanofibers (calcination temperature 600 °C), (d) diameter distribution; (e) CoFe2O4 nanofibers (calcination temperature 800 °C), (f) diameter distribution, (g) ultrasonicated nanofibers; CoFe2O4 nanoparticles at (h) 10k× (i) 100k× magnification. | |
Fig. 5(a) and (b) are the low and high magnification TEM images of CoFe2O4 nanoparticles, whereas Fig. 5(c) and (d) represent the particle size distribution histogram and selected area electron diffraction (SAED) pattern of the same. As can be seen from the histogram, the nanoparticles are of nearly spherical shape with mean particle diameter of 61 nm. This result is in good agreement with the average crystallite size (∼63.86 nm) measured by the Debye–Scherrer equation.
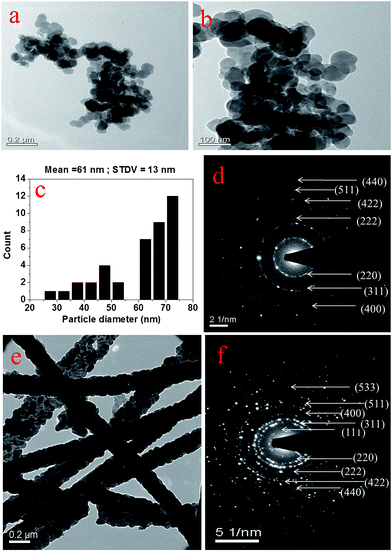 |
| Fig. 5 TEM images of CoFe2O4 nanoparticles at (a) low magnification, (b) high magnification, (c) particle size distribution, (d) SAED pattern; (e) CoFe2O4 nanofibers (calcination temperature 800 °C), (f) SAED pattern. | |
Fig. 5(e) and (f) are the TEM image and SAED pattern of the CoFe2O4 nanofibers calcined at 800 °C. It can be seen from the TEM image that several crystallite or particle like units combines in a densely packed configuration to form the CoFe2O4 nanofibers. Both nanoparticles and nanofibers exhibited ring diffraction patterns which can be accounted for the electron diffraction at (220), (311), (222), (400), (422), (511) and (440) crystal plane respectively. In addition to these diffraction rings, two extra rings arise one at the interior and other at the exterior of the SAED pattern of nanofibers which are due to the diffraction at (111) and (533) crystal planes, respectively. The ring diffraction pattern of both the nanoparticles and nanofibers reveals that they are polycrystalline in nature with bcc crystal structure. Strong diffraction pattern of the nanofibers correspond to larger crystallite size and occurrence of spinel structure with greater crystallinity compared to the nanoparticles.
Fig. 6(a) and (c) exhibit the inverted microscopic images of 5 and 10 wt% p-CoFe2O4–PDMS isotropic nanocomposites, while Fig. 6(b) and (d) represent the corresponding anisotropic nanocomposites. The nanoparticles are homogeneously distributed to make isotropic nanocomposites. However, the anisotropic nanocomposites are characterized by aligned particle chains in some regions and most of the matrix is devoid of any magnetic particles. Increase in the filler loading to 10 wt% leads to the increase in the density and width of particle chains within the matrix, but large voids devoid of magnetic particles still remain. Fig. 6(e) and (g) show the inverted microscopic images of 5 and 10 wt% f-CoFe2O4–PDMS isotropic nanocomposites. In contrast, Fig. 6(f) and (h) are for the corresponding anisotropic nanocomposites (see also Fig. S5 of ESI† for FESEM images of all nanocomposites). The isotropic nanocomposites are characterized by an interconnecting fiber network throughout the matrix. Higher fiber loading leads to the formation of more densely packed fiber network with homogeneous fiber distribution. Anisotropic nanocomposites are characterized by continuous fiber chains forming the columnar structure in the direction of the magnetic field. Furthermore it is seen that the effective volume coverage of the nanofibers is greater than that of nanoparticles at same filler loading due to the higher aspect ratio.
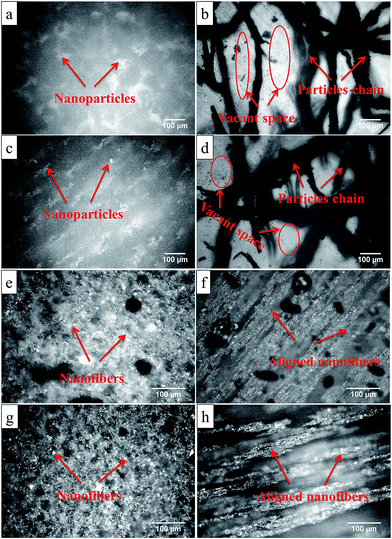 |
| Fig. 6 Inverted microscopic images of p-CoFe2O4–PDMS nanocomposites (a) 5 wt% isotropic, (b) 5 wt% anisotropic, (c) 10 wt% isotropic, (d) 10 wt% anisotropic; f-CoFe2O4–PDMS nanocomposites (e) 5 wt% isotropic, (f) 5 wt% anisotropic, (g) 10 wt% isotropic, (h) 10 wt% anisotropic. | |
4.5 Magnetorheological properties
4.5.1 Steady state test. Fig. 7(a) and (b) are the shear stress versus shear strain curves of 10 wt% isotropic and anisotropic p-CoFe2O4–PDMS NCs (see Fig. S6(a) and (b) in ESI† for 5 wt% isotropic and anisotropic p-CoFe2O4–PDMS NCs). Fig. 8(a) and (b) present the shear modulus of the isotropic and anisotropic p-CoFe2O4–PDMS NCs as function of nanoparticle loading at 31.58% shear strain. This particular strain value is chosen for modulus comparison since all the nanocomposites except 10 wt% p-CoFe2O4–PDMS isotropic NC show linear stress–strain characteristics within this strain limit as shown in Table 4. From these figures it is observed that the shear modulus of anisotropic p-CoFe2O4–PDMS NCs under different magnetic fields are greater than their corresponding isotropic p-CoFe2O4–PDMS NCs at 5 wt% filler loading, but the trend is reversed at 10 wt%. Furthermore peak shear stress values {see Fig. 8(e)} achieved under 1.023 T magnetic field and 200% strain are also greater for anisotropic nanocomposites than their corresponding isotropic counterpart for both nanoparticles and nanofibers filled nanocomposites except 10 wt% anisotropic f-CoFe2O4–PDMS NC. This can be attributed to the aligned particles forming chains in the anisotropic nanocomposites during the fabrication under the magnetic field. Moreover, with the increase in nanofiller loading shear modulus are observed to be decreased gradually owing to progressively increasing resistance of the nanofillers in crosslinking reaction (retardation effect) of the polymer matrix.34
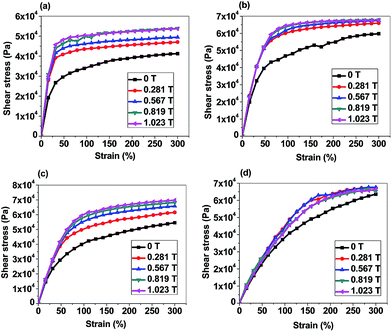 |
| Fig. 7 Shear stress vs. Shear strain curves of p-CoFe2O4–PDMS nanocomposites (a) 10 wt% isotropic, (b) 10 wt% anisotropic; f-CoFe2O4–PDMS nanocomposites (c) 10 wt% isotropic, (d) 10 wt% anisotropic. | |
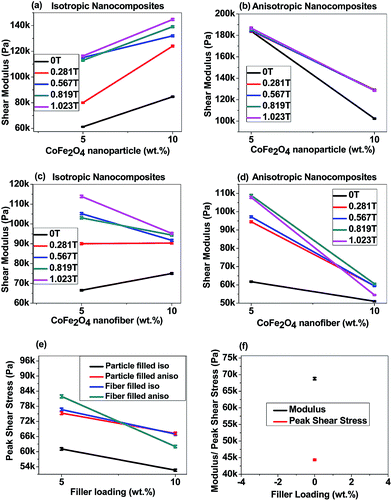 |
| Fig. 8 Shear Modulus vs. filler loading plots of p-CoFe2O4–PDMS nanocomposites (a) isotropic, (b) anisotropic; f-CoFe2O4–PDMS nanocomposites (c) isotropic, (d) anisotropic; (e) peak shear stress vs. filler loading plot of nanocomposites, (f) modulus and peak shear stress of neat PDMS. | |
Table 4 Linear region of the stress–strain response at different magnetic field
Sample name |
Strain (%) |
0 T |
0.281 T |
0.567 T |
0.0.819 T |
1.023 T |
5 wt% p-CoFe2O4–PDMS isotropic NC |
31.59 ± 1.58 |
63.15 ± 3.16 |
63.18 ± 3.16 |
63.15 ± 3.16 |
63.15 ± 3.16 |
5 wt% p-CoFe2O4–PDMS anisotropic NC |
42.11 ± 2.10 |
42.09 ± 2.10 |
42.09 ± 2.10 |
42.09 ± 2.10 |
42.09 ± 2.10 |
10 wt% p-CoFe2O4–PDMS isotropic NC |
15.8 ± 0.79 |
31.60 ± 1.58 |
31.57 ± 1.58 |
31.57 ± 1.58 |
31.58 ± 1.58 |
10 wt% p-CoFe2O4–PDMS anisotropic NC |
31.59 ± 1.58 |
47.38 ± 2.37 |
47.35 ± 2.37 |
63.12 ± 3.16 |
63.11 ± 3.16 |
5 wt% f-CoFe2O4–PDMS isotropic NC |
52.67 ± 2.63 |
63.16 ± 3.16 |
63.15 ± 3.16 |
63.15 ± 3.16 |
63.14 ± 3.16 |
5 wt% f-CoFe2O4–PDMS anisotropic NC |
47.38 ± 2.37 |
63.19 ± 3.16 |
78.52 ± 3.95 |
78.93 ± 3.95 |
78.93 ± 3.95 |
10 wt% f-CoFe2O4–PDMS isotropic NC |
31.62 ± 1.58 |
47.36 ± 3.95 |
63.14 ± 3.16 |
63.13 ± 3.16 |
63.13 ± 3.16 |
10 wt% f-CoFe2O4–PDMS anisotropic NC |
63.19 ± 3.16 |
78.94 ± 3.95 |
78.94 ± 3.95 |
78.94 ± 3.95 |
78.94 ± 3.95 |
Neat PDMS |
31.62 ± 1.58 |
— |
— |
— |
— |
Fig. 7(c) and (d) represent the shear stress versus shear strain curves of 10 wt% isotropic and anisotropic f-CoFe2O4–PDMS NCs (see Fig. S6(c) and (d)† for 5 wt% isotropic and anisotropic f-CoFe2O4–PDMS NCs). Fig. 8(c) and (d) denote the shear modulus of the isotropic and anisotropic f-CoFe2O4–PDMS NCs as a function of nanofiber loading at 31.58% shear strain. It is observed that isotropic f-CoFe2O4–PDMS NCs show greater shear modulus than their respective anisotropic f-CoFe2O4–PDMS NCs at both 5 wt% and 10 wt% filler loading under most of the variable magnetic fields. The linear strain range is observed to increase gradually with the increase in the magnetic field and eventually becomes constant after a critical magnetic field as shown in Table 4. Fig. 8(f) shows the modulus and peak shear stress of the neat PDMS (control sample) at 0 T magnetic field (see Fig. S6(e)† for corresponding shear stress versus shear strain curve of neat PDMS). Comparing the nanoparticles and nanofibers filled nanocomposites at 1.023 T magnetic field, the maximum peak shear stress is achieved with nanofibers filled nanocomposites. This can be attributed to the homogeneous distribution of interconnected network of the nanofibers owing to their higher aspect ratio and greater effective volume coverage capability. Inverted microscopic images also support this feature of nanofibers where the vacant spaces are more uniformly distributed and have less free volume compared to the nanoparticle based nanocomposites.
The degree of perturbation experienced by the MR elastomer has direct relationship with strength of applied magnetic field and the effect is reversible. The extent of enhancement of modulus under the magnetic field is dependent on the morphology, concentration, polymer–filler and filler–filler interactions. Applied magnetic field orients the filler along the magnetic field direction. This exerts a deformation force on the polymer matrix which in turn increases the shear modulus of the composite. Under the influence of external magnetic field, filler particles are driven to its equilibrium state determined by a combined effect of visco-elastic property of the polymer as well as interparticle coulombic interaction. The composite system finally assume equilibrium configuration with effective local energy minimum of the system. Each time magnetic field is changed, the sample attains a new equilibrium. Once the magnetic field is removed, the magnetic fillers restore their original position by virtue of the elastic force in the matrix material.33,58 Moreover, deformation of the polymer matrix occurs only in those regions where magnetic fillers are in direct contact with the polymer matrix. Thus, most of the polymer matrix remains unaffected in nanoparticles filled nanocomposites because a large amount of void spaces are present in the nanocomposites at this low filler loading regime. In contrast, nanofibers filled nanocomposites experience more deformation due to greater volume coverage capability of the nanofibers which eventually provide larger deformation point on the matrix and thus show greater magnetic field induced ultimate shear stress.
It has also been noted that in most cases, the increase in the shear modulus is larger as the magnetic field is increased from zero to 0.281 T. This is true both for the nanoparticles and nanofibers filled isotropic and anisotropic nanocomposites. However, the change is less when the field strength is moderate to high, e.g., from 0.281 T to 0.567 T. Only a marginal increment in the shear modulus is observed when the magnetic field is increased from 0.819 T to 1.023 T due to magnetic saturation of the nanofillers. The MR effect in shear stress of the nanocomposites is estimated from the ratio of maximum shear modulus achieved under the magnetic field to the zero field shear modulus.
4.5.2 Dynamic test.
4.5.2.1 Strain sweep test. Fig. 9(a) and (b) demonstrate the strain amplitude sweep curves of 10 wt% isotropic and anisotropic p-CoFe2O4–PDMS NCs. In contrast, Fig. 9(c) and (d) represent the strain amplitude sweep curves of 10 wt% isotropic and anisotropic f-CoFe2O4–PDMS NCs (see Fig. S7(a) to (e) in ESI† for 5 wt% p-CoFe2O4–PDMS NCs (isotropic and anisotropic), 5 wt% f-CoFe2O4–PDMS NCs (isotropic and anisotropic) and neat PDMS). It can be seen from the curves that storage modulus of both p-CoFe2O4–PDMS NCs, f-CoFe2O4–PDMS NCs show almost linear relation up to 10 strain% and beyond that a sharp drop in the magnitude of the storage modulus is observed. This is because the magnetic interaction forces are inversely proportional to the distance separating the magnetic fillers. Hence reduction in the storage modulus of the nanocomposites under magnetic field can be attributed to the reduced inter-filler interaction forces resulting from the larger inter-filler distance due to increase in the strain amplitude. Therefore the nanocomposites start to exhibit nonlinear viscoelastic properties beyond this critical strain%. Both isotropic and anisotropic p-CoFe2O4–PDMS NCs exhibited higher initial storage and loss modulus than their corresponding f-CoFe2O4–PDMS NCs. This might be because of better reinforcing nature and larger intrinsic modulus of the nanoparticles than the nanofibers. Fig. 10(a) and (b) are the storage modulus vs. filler loading plot of nanoparticle filled isotropic and anisotropic nanocomposites at 96% strain value whereas Fig. 10(c) and (d) demonstrate the similar curves for neat PDMS, isotropic f-CoFe2O4–PDMS NCs and anisotropic f-CoFe2O4–PDMS NCs. All the nanocomposites show higher storage modulus value than the control neat PDMS. It is also observed that the storage modulus of the isotropic p-CoFe2O4–PDMS NC is lower than the corresponding f-CoFe2O4–PDMS NC at 5 wt% filler loading due to formation of better nanofibres network at low filler loading. However, this trend gets reversed at 10 wt% owing to the contribution in modulus increment by the greater intrinsic modulus of the nanoparticles in p-CoFe2O4–PDMS NCs. In contrast, at most values of the magnetic field, anisotropic p-CoFe2O4–PDMS NC shows greater storage modulus compared to the f-CoFe2O4–PDMS NC at both 5 wt% and 10 wt% filler loading because of superior reinforcing characteristics of aligned nanoparticles chains.
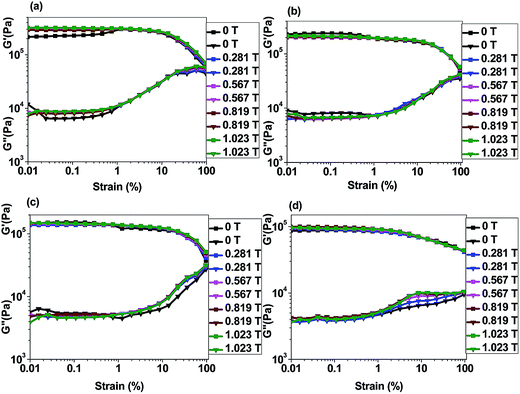 |
| Fig. 9 Strain sweep curves of p-CoFe2O4–PDMS nanocomposites (a) 10 wt% isotropic, (b) 10 wt% anisotropic; f-CoFe2O4–PDMS nanocomposites (c) 10 wt% isotropic, (d) 10 wt% anisotropic. | |
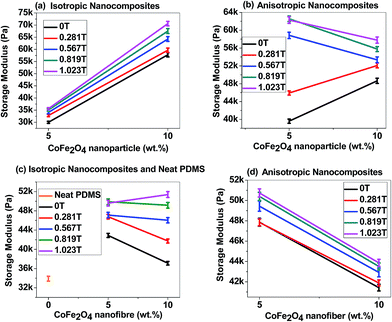 |
| Fig. 10 Storage Modulus (at 96% shear strain) vs. filler loading plots of p-CoFe2O4–PDMS nanocomposites (a) isotropic, (b) anisotropic; f-CoFe2O4–PDMS nanocomposites (c) isotropic and neat PDMS, (d) anisotropic. | |
Fig. 11(a) and (b) represent the damping factor of nanocomposites and neat PDMS as a function of strain amplitude under 1.023 T and 0 T applied magnetic field, respectively. All nanocomposites and neat PDMS have demonstrated increasing damping properties with the growth of strain amplitude. It also reveals that isotropic p-CoFe2O4–PDMS NCs are superior in terms of damping properties than their respective isotropic f-CoFe2O4–PDMS NCs. In contrast anisotropic f-CoFe2O4–PDMS NCs show better damping properties than their corresponding anisotropic p-CoFe2O4–PDMS NCs, except for the 10 wt% f-CoFe2O4–PDMS anisotropic nanocomposite which shows lower damping factor after 10 strain%.
 |
| Fig. 11 Damping factor vs. strain amplitude curves (a) p-CoFe2O4–PDMS and f-CoFe2O4–PDMS nanocomposites at 1.023 T; (b) neat PDMS at 0 T. | |
This better dissipation and damping of anisotropic f-CoFe2O4–PDMS NCs than anisotropic p-CoFe2O4–PDMS NCs can be correlated to the interconnected network with uniformly distributed less void spaces {compare Fig. 6(b) and (d) with Fig. 6(f) and (h)}. Moreover, all the isotropic nanocomposites except 10 wt% f-CoFe2O4–PDMS nanocomposite show superior damping characteristics than their corresponding anisotropic nanocomposites as homogeneous distribution of fillers in isotropic nanocomposites favors dissipation of energy to a greater ease.
4.5.2.2 Angular frequency sweep test. Fig. 12(a) to (d) represent the log–log plot of storage and loss moduli as a function of angular frequency. All the nanocomposites (see Fig. S8(a) to (e) in ESI† for 5 wt% p-CoFe2O4–PDMS NCs (isotropic and anisotropic), 5 wt% f-CoFe2O4–PDMS NCs (isotropic and anisotropic) and neat PDMS) show logarithmically linear increase in both storage and loss moduli with the rise in angular frequency. Initial deviation of the loss modulus from the linear relationship in Fig. 12(a) and (c) might have resulted from the slippage between the upper steel plate and nanocomposite samples during the analysis. Static friction and sample roughness also may lead to the overshoot in the magnitude of modulus as seen in Fig. 12(b). This linear relationship of the storage and loss moduli with angular frequency could be employed to estimate the modulus values of the nanocomposites at certain angular frequencies. Similar to strain amplitude sweep test, all the p-CoFe2O4–PDMS NCs show greater initial storage and loss moduli compared to the f-CoFe2O4–PDMS NCs under angular frequency sweep test. Only slight increase in the storage and loss modulus values is achieved in the nanocomposites when subjected to the increased magnetic field. This could be attributed to the very low magnetic filler content in the nanocomposites compared to conventional MRE where magnetic filler content mostly lies between 60 wt% to 80 wt%.23,25,59,60 Moreover, in our study magnetic field is applied perpendicular to the particles chains or plane of the samples which is also one of the important reason towards achieving lower storage modulus increment in these nanocomposites.
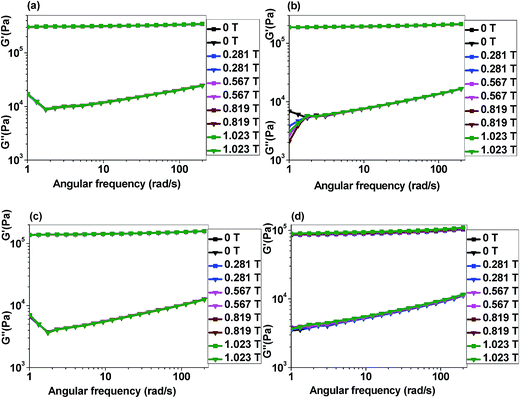 |
| Fig. 12 Angular frequency sweep curves of p-CoFe2O4–PDMS nanocomposites (a) 10 wt% isotropic, (b) 10 wt% anisotropic; f-CoFe2O4–PDMS nanocomposites (c) 10 wt% isotropic, (d) 10 wt% anisotropic. | |
4.5.2.3 Magnetic flux density sweep test. Fig. 13(a) indicates the storage modulus versus magnetic flux density curves of isotropic nanocomposites while Fig. 13(b) represent the similar curves for anisotropic nanocomposites (see Fig. S9 in ESI† for loss modulus versus magnetic flux density curves of all nanocomposites and neat PDMS). The magnetic field induced change in storage modulus eventually gives the idea about absolute and relative MR effects which help to evaluate the actual performance of MRE. Absolute MR effect (ΔG) is calculated from the difference between the maximum storage modulus achieved under magnetic field (GMax) and zero field storage modulus (G0).
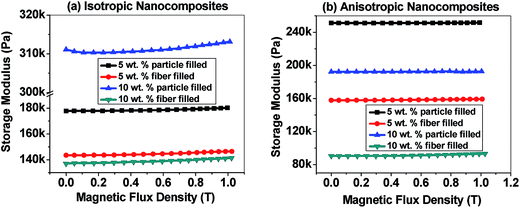 |
| Fig. 13 Storage modulus vs. magnetic flux density curve of (a) isotropic nanocomposites, (b) anisotropic nanocomposites. | |
Relative MR effect (ΔGr) is evaluated by the following equation
ΔGr = {(GMAX − G0) × 100}/G0 [%] = (ΔG × 100)/G0 [%] |
Magnitudes of the absolute and relative MR effect of all the nanocomposites and neat PDMS are exhibited in Table 5. As can be seen from the table, neat PDMS does not exhibit any MR effect due to its nonmagnetic nature. All the isotropic nanocomposites show greater absolute and relative MR effect than their corresponding anisotropic nanocomposites. Moreover, at 5 wt% filler loading, both f-CoFe2O4–PDMS and p-CoFe2O4–PDMS isotropic nanocomposites show low zero field storage modulus than their corresponding anisotropic nanocomposites. But at 10 wt% filler loading the reverse phenomena is observed as particle alignment reduces the storage modulus values in the anisotropic nanocomposites at higher filler loading.14 Both isotropic and anisotropic nanocomposites with 10 wt% filler loading show greater absolute MR effect than their corresponding 5 wt% filled nanocomposites except 10 wt% p-CoFe2O4–PDMS isotropic nanocomposite. This could be because of increased dipole magnetic attraction forces between the fillers resulting from the decreased inter filler distance at higher filler content. The lower MR effect in 10 wt% p-CoFe2O4–PDMS isotropic nanocomposite is due to increase in zero field storage modulus value resulting from the reinforcement effect of nanoparticles. It is also noteworthy that all the f-CoFe2O4–PDMS NCs exhibited much higher MR effect than the p-CoFe2O4–PDMS NCs. This can be accounted for the greater zero field storage modulus vales of the p-CoFe2O4–PDMS NCs than their respective f-CoFe2O4–PDMS NCs.
Table 5 MR effect of the nanocomposites
Sample details |
Absolute MR effect (Pa) at 1.023 T |
Relative MR effect (%) at 1.023 T |
5 wt% f-CoFe2O4–PDMS isotropic NC |
3000 ± 5 |
2.09 ± 0.003 |
5 wt% f-CoFe2O4–PDMS anisotropic NC |
1400 ± 3 |
0.88 ± 0.004 |
10 wt% f-CoFe2O4–PDMS isotropic NC |
4400 ± 8 |
3.21 ± 0.008 |
10 wt% f-CoFe2O4–PDMS anisotropic NC |
2730 ± 5 |
3.01 ± 0.005 |
5 wt% p-CoFe2O4–PDMS isotropic NC |
2400 ± 4 |
1.34 ± 0.005 |
5 wt% p-CoFe2O4–PDMS anisotropic NC |
300 ± 2 |
0.11 ± 0.004 |
10 wt% p-CoFe2O4–PDMS isotropic NC |
2000 ± 4 |
0.64 ± 0.003 |
10 wt% p-CoFe2O4–PDMS anisotropic NC |
600 ± 3 |
0.31 ± 0.01 |
Neat PDMS |
30 ± 2 |
0.016 ± 0.002 |
Moreover, better interconnected nanofibers network also contributed to the greater MR effect enhancement in nanofibers filled nanocomposites than the nanoparticles filled nanocomposites.
Li et al.20,61 studied the effects of micron sized (3 to 5 μm) carbonyl iron particle on the MR characteristic of PDMS elastomer and showed 4.5 and 4.8% relative MR effect in isotropic and anisotropic composites under 440 mT external magnetic field and 62.5 wt% filler loading. They also reported very small enhancement of 1.27, 1.30, 1.74 and 1.81% in relative MR effect for 60, 70, 80 and 90 wt% carbonyl iron content, respectively in homogeneous composites with same magnetic field. Clearly, the nanofibers used here can achieve similar MR effect at much smaller loadings of 10 wt% nanofiller at 1.023 T magnetic field. Although magnetic fields are higher in our case but, the filler loading is very low compared to their studies.
5. Conclusions
MR characteristics of PDMS nanocomposites containing CoFe2O4, in the form of either nanoparticles or nanofibers, have been investigated for the first time. Nano-sized particles and fibres with high saturation magnetization of 69.46 emu g−1 and 67.24 emu g−1 are synthesized either by co-precipitation or by electrospinning methods. Increase of calcination temperature from 600 to 800 °C leads to 135% increase in the saturation magnetization in case of nanofibers coupled with increased coercivity and remnant magnetization.
Nanofiber filled composites exhibit greater saturation magnetization compared to nanoparticle composites at low filler concentration (∼5 wt%). Formation of an interconnected network with the nanofibers at low concentration results in enhanced magnetic field induced interaction among the nanofibers. At higher (∼10 wt%) filler loading, particulate filled nanocomposites show greater saturation magnetization compared to the nanofibers because of greater intrinsic saturation magnetization of the nanoparticles. Besides, higher aspect ratio of the nanofibers compared to particles generates lower anisotropic coefficient in their composites except 5 wt% nanofiber filled one.
Rheological study reveals that low nanofiber loadings (5–10 wt%) give the MR properties comparable to those obtained by much higher microparticle additions (60–80 wt%) for the same polymer matrix. All the nanofiber based composites, except 10 wt% anisotropic nanocomposite exhibit larger magnetic field induced peak shear stress due to better interconnected network. Isotropic nanocomposites exhibited superior damping behaviour compared to their corresponding anisotropic nanocomposites due to homogeneous distribution of nanofillers which facilitate better dissipation of energy. Both absolute and relative MR effects are observed to be greater in the fibre filled nanocomposites than the corresponding particulate ones. Increasing filler content leads to the increased MR effect and highest absolute as well as relative MR effect of 4.4 kPa and 3.21% are achieved in 10 wt% fibre filled isotropic nanocomposite. Therefore from the above study we may conclude that CoFe2O4 nanofibers are more effective in achieving higher magnetic field induced MR effect than the CoFe2O4 nanoparticles and are the promising candidates for future MRE applications.
Acknowledgements
This work was supported by the Department of science and technology, India through its funding to the Nanoscience Center at IITK. We are thankful to Prof. V. K. Jain and Mr Sanjeev Kumar for their help in carrying out magnetorheological analysis. Authors also would like to acknowledge Director DMSRDE and Nano Science Division of DMSRDE for providing their electromagnet setup for composite fabrication.
References
- S. Kashima, F. Miyasaka and K. Hirata, IEEE Trans. Magn., 2012, 48, 1649 CrossRef.
- J.-H. Koo, A. Dawson and H.-J. Jung, J. Intell. Mater. Syst. Struct., 2012, 23, 1049 CrossRef PubMed.
- G. Du and X. Chen, Measurement, 2012, 45, 54 CrossRef PubMed.
- K. L. Phan, A. Mauritz and F. G. A. Homburg, Sens. Actuators, A, 2008, 145–146, 109 CrossRef CAS PubMed.
- J. Lejon and L. Kari, Plast., Rubber Compos., 2009, 38, 321 CrossRef CAS PubMed.
- H. X. Deng, X. L. Gong and L. H. Wang, Smart Mater. Struct., 2006, 15, N111 CrossRef.
- J. M. Ginder, M. E. Nichols, L. D. Elie and S. M. Clark, Smart Mater. Struct., 2000, 3985, 418 Search PubMed.
- H. Du, W. Li and N. Zhang, Smart Mater. Struct., 2011, 20, 105003 CrossRef.
- L. Lanotte, G. Ausanio, C. Hison, V. Iannotti and C. Luponio, Sens. Actuators, A, 2003, 106, 56 CrossRef CAS.
- H. Bose, R. Rabindranath and J. Ehrlich, J. Intell. Mater. Syst. Struct., 2011, 23, 989 CrossRef PubMed.
- Y. Xu, X. Gong, S. Xuan, W. Zhang and Y. Fan, Soft Matter, 2011, 7, 5246 RSC.
- M. R. Jolly, J. D. Carlson, B. C. Munoz and T. A. Bullions, J. Intell. Mater. Syst. Struct., 1996, 7, 613 CrossRef CAS PubMed.
- H. M. Yin and L. Z. Sun, Appl. Phys. Lett., 2005, 86, 261901 CrossRef PubMed.
- L. C. Davis, J. Appl. Phys., 1999, 85, 3348 CrossRef CAS PubMed.
- L. Chen and S. Jerrams, J. Appl. Phys., 2011, 110, 013513 CrossRef PubMed.
- Y. Fan, X. Gong, S. Xuan, W. Zhang, J. Zheng and W. Jiang, Smart Mater. Struct., 2011, 20, 035007 CrossRef.
- A. Boczkowska, S. F. Awietjan, S. Pietrzko and K. J. Kurzydłowski, Composites, Part B, 2012, 43, 636 CrossRef CAS PubMed.
- M. Lokander and B. Stenberg, Polym. Test., 2003, 22, 677 CrossRef CAS.
- S. S. Abramchuk, D. A. Grishin, E. Y. Kramarenko, G. V. Stepanov and A. R. Khokhlov, Polym. Sci., Ser. A, 2006, 48, 138 CrossRef.
- T. F. Tian, W. H. Li, G. Alici, H. Du and Y. M. Deng, Rheol. Acta, 2011, 50, 825 CrossRef CAS PubMed.
- Y. Hu, Y. L. Wang, X. L. Gong, X. Q. Gong, X. Z. Zhang, W. Q. Jiang, P. Q. Zhang and Z. Y. Chen, Polym. Test., 2005, 24, 324 CrossRef CAS PubMed.
- J. L. Leblanc, Prog. Polym. Sci., 2002, 27, 627 CrossRef CAS.
- X. L. Gong, L. Chen and J. F. Li, Int. J. Mod. Phys. B, 2007, 21, 4875 CrossRef CAS.
- B. Wei, X. Gong and W. Jiang, J. Appl. Polym. Sci., 2010, 116, 771 CAS.
- T. L. Sun, X. L. Gong, W. Q. Jiang, J. F. Li, Z. B. Xu and W. H. Li, Polym. Test., 2008, 27, 520 CrossRef CAS PubMed.
- M. Farshad and A. Benine, Polym. Test., 2004, 23, 347 CrossRef CAS.
- M. Yu and S. Wang, Smart Mater. Struct., 2010, 19, 065023 CrossRef.
- J. Li, M. Zhang, L. Wang, W. Li, P. Sheng and W. Wen, Microfluid. Nanofluid., 2011, 10, 919 CrossRef CAS.
- C. Bellan and G. Bossis, Int. J. Mod. Phys. B, 2002, 16, 2447 CrossRef CAS.
- P. v. Lockette, S. E. Lofland, J. Biggs, J. Roche, J. Mineroff and M. Babcock, Smart Mater. Struct., 2011, 20, 105022 CrossRef.
- B. K. S. Woods, N. Wereley, R. Hoffmaster and N. Nersessian, Int. J. Mod. Phys. B, 2007, 21, 5010 CrossRef CAS.
- I. Bica, Y. D. Liu and H. J. Choi, Colloid Polym. Sci., 2012, 290, 1115 CAS.
- G. V. Stepanov, S. S. Abramchuk, D. A. Grishin, L. V. Nikitin, E. Y. Kramarenko and A. R. Khokhlov, Polymer, 2007, 48, 488 CrossRef CAS PubMed.
- B. Mordina, R. K. Tiwari, D. K. Setua and A. Sharma, J. Phys. Chem. C, 2014, 118, 25684 CAS.
- Y. Tian, Y. Liu, M. He, G. Zhao and Y. Sun, Mater. Res. Bull., 2013, 48, 2002 CrossRef CAS PubMed.
- S.-P. Rwei, L. Y. Wang and P.-W. Yang, J. Nanomater., 2013, 2013, 1 Search PubMed.
- B. A. Evans, B. L. Fiser, W. J. Prins, D. J. Rapp, A. R. Shields, D. R. Glass and R. Superfine, J. Magn. Magn. Mater., 2012, 324, 501 CrossRef CAS PubMed.
- I. G. Yanez-Flores, R. Betancourt-Galindo, J. A. Matutes Aquino and O. Rodrıguez-Fernandez, J. Non-Cryst. Solids, 2007, 353, 799 CrossRef CAS PubMed.
- S. Mousavian, H. Ebadi-Dehaghani, D. Ashouri, H. Sadeghipour and F. Jabbari, J. Polym. Res., 2012, 19, 9991 CrossRef PubMed.
- S. J. Moeen, M. R. Vaezi, A. A. Yousefi and E. Ghasemi, J. Appl. Polym. Sci., 2012, 123, 2534 CrossRef CAS.
- L. Zhu, D. Xie, J. Ma, J. Shao and X. Shen, Smart Mater. Struct., 2013, 22, 045015 CrossRef.
- H. Denver, T. Heiman, E. Martin, A. Gupta and D.-A. Borca-Tasciuc, J. Appl. Phys., 2009, 106, 064909 CrossRef PubMed.
- R. A. Landa, P. S. Antonel, M. M. Ruiz, O. E. Perez, A. Butera, G. Jorge, C. L. P. Oliveira and R. M. Negri, J. Appl. Phys., 2013, 114, 213912 CrossRef PubMed.
- O. Padalka, H. J. Song, N. M. Wereley, J. A. Filer II and R. C. Bell, IEEE Trans. Magn., 2010, 46, 2275 CrossRef CAS.
- H. J. Song, N. M. Wereley, R. C. Bell, J. L. Planinsek and J. A. Filer II, J. Phys.: Conf. Ser., 2009, 149, 012097 CrossRef.
- C. N. Chinnasamy, M. Senoue, B. Jeyadevam, O. Perales-Perez, K. Shinoda and K. Tohji, J. Colloid Interface Sci., 2003, 263, 80 CrossRef CAS.
- P. S. Antonel, G. Jorge, O. E. Perez, A. Butera, A. G. Leyva and R. M. Negri, J. Appl. Phys., 2011, 110, 043920 CrossRef PubMed.
- D. J. Campbell, K. J. Beckman, C. E. Calderon, P. W. Doolan, R. M. Ottosen, A. B. Ellis and G. C. Lisensky, J. Chem. Educ., 1999, 75, 537 Search PubMed.
- B. D. Cullity, in Elements of X-ray diffraction, ed. M. Cohen, Addison-Wesley publishing company, Inc., Massachusetts, 1978, vol. 102 Search PubMed.
- M. Sangmanee and S. Maensiri, Appl. Phys. A, 2009, 97, 167 CrossRef CAS PubMed.
- E. Veena Gopalan, P. A. Joy, I. A. Al-Omari, D. K. Sakthi, Y. Yoshida and M. R. Anantharaman, J. Alloys Compd., 2009, 485, 711 CrossRef PubMed.
- R. H. Kodama, J. Magn. Magn. Mater., 1999, 200, 359 CrossRef CAS.
- P. Priyadarshini, A. Pradeep, P. S. Rao and G. Chandrasekharan, Mater. Chem. Phys., 2009, 116, 207 CrossRef PubMed.
- L. Zhao, H. Yang, X. Zhao, L. Yu, Y. Cui and S. Feng, Mater. Lett., 2006, 60, 1 CrossRef CAS PubMed.
- J. Fu, J. Zhang, Y. Peng, J. Zhao, G. Tan, N. J. Mellors, E. Xie and W. Han, Nanoscale, 2012, 4, 3932 RSC.
- C. N. Chinnasamy, B. Jeyadevan, K. Shinoda, K. Tohji, D. J. Djayaprawira and M. Takahashi, Appl. Phys. Lett., 2003, 83, 2862 CrossRef CAS PubMed.
- E. C. Stoner and E. P. Wohlfarth, Philos. Trans. R. Soc., A, 1948, 240, 599 CrossRef.
- S. Abramchuk, E. Kramarenko, G. Stepanov, L. V. Nikitin, G. Filipcsei, A. R. Khokhlov and M. Zrinyi, Polym. Adv. Technol., 2007, 18, 883 CrossRef CAS.
- A. Fuchs, Q. Zhang, J. Elkins, F. Gordaninejad and C. Evrensel, J. Appl. Polym. Sci., 2007, 105, 2497 CrossRef CAS.
- L. Chen, X.-L. Gong, W.-Q. Jiang, J.-J. Yao, H.-X. Deng and W.-H. Li, J. Mater. Sci., 2007, 42, 5483 CrossRef CAS.
- W. H. Li and M. Nakano, Smart Mater. Struct., 2013, 22, 055035 CrossRef.
Footnote |
† Electronic supplementary information (ESI) available. See DOI: 10.1039/c5ra00537j |
|
This journal is © The Royal Society of Chemistry 2015 |
Click here to see how this site uses Cookies. View our privacy policy here.