DOI:
10.1039/C4RA16916F
(Paper)
RSC Adv., 2015,
5, 11687-11696
Acyl transfer reactions of carbohydrates, alcohols, phenols, thiols and thiophenols under green reaction conditions†
Received
23rd November 2014
, Accepted 7th January 2015
First published on 7th January 2015
Abstract
Acyl transfer reactions of various carbohydrates, alcohols, phenols, thiols and thiophenols were achieved at room temperature in high yields and catalytic efficiency in the presence of methane sulfonic acid, a green organic acid, under solvent-free conditions over short time periods. The method is mild enough to allow acid labile substituents such as isopropylidene acetals and trityl ethers on the reacting substrates to be left completely unaffected. Esterification of free mono- and dicarboxylic acids such as acetic acid, cinnamic acid, sialic acid and tartaric acid with alcohols such as menthol, ethanol, methanol or propylene glycol has also been achieved efficiently at room temperature. A comparative study of the method with the silica-sulfuric acid is also reported.
Introduction
New methods for the protection and deprotection of organic compounds required during synthetic processes addressing environmental concerns are of increasing topical relevance. Acyl transfer reactions of carbohydrates, alcohols, phenols, amines and thiols form perhaps one of the commonest reactions required to be carried out routinely during synthetic transformations of these classes of organic compounds. Both acids as well as bases serve equally well as catalysts for this purpose. Among the wide variety of Lewis acids that have been in use in this context, a majority such as BF3/BF3·Et2O,1 FeCl3,2 SnCl4,3 TiCl4,4 ZnCl2,5 TMSOTf,6 etc. are extremely sensitive to moisture and are difficult to handle. Among the more recently introduced metal-based Lewis acid substances are the different triflates such as In(OTf)3,7,8 Cu(OTf)2,9 Sc(OTf)3,10 La(OTf)3,11 Bi(OTf)3,12,13 etc. Among others, iodine14 and sulfamic acid15 also have been found good for various acyl transfer reactions, although in the case of the latter the reaction is required to be carried out at 60 °C to be effective. Immobilized catalysts such as solid-supported acids16 have also been used for acid-catalyzed acetylations. Apart from the acids, basic reagents have also been used extensively as acyl transfer agents. Pyridine,17 by far the most widely used reagent, DMAP18 and DABCO19 have all been found to be well suited for this purpose although they are used in stoichiometric quantities (or in excess of it, for example, as solvent in the case of pyridine). Pyridine and their derivatives are toxic/hazardous compounds. New catalysts of high catalytic efficiency and low hazard have therefore been always in utmost demand.
Methane sulfonic acid (MeSO3H, MeSA) is a high boiling liquid, non-corrosive, non-volatile, stable, inexpensive and readily available green chemical reagent.20 These unique features of MeSO3H attracted us to exploring its potential as an acid catalyst for various organic reactions. It was also felt that another closely related acid, namely, chlorosulfonic acid (ClSO3H, CSA) will be also evaluated for comparative purposes. The latter however is corrosive, volatile/fuming and is a very strong acid and hence would be used as supported on silica (SiO2–OSO3H, SiSA, in the form of free-flowing powder)21 thus making it comparatively more environment-friendly (than the free acid) and more convenient to handle. The solid-supported reagents are also less corrosive and of lower toxicity with the added advantage that they can be easily separated from the reaction mixtures by filtration offering possibilities for reuse, particularly important in industrial applications.16 It was rather surprising that a green acid such as MeSA has not so far been investigated in detail for acylation reactions, a class of reactions requiring to be carried out so routinely during organic synthesis, particularly in carbohydrate and medicinal chemistry and natural product synthesis. This was true of CSA as well. For these reasons the potential of both MeSA as well as SiSA was evaluated for acyl transfer reactions of carbohydrates, alcohols and phenols, thiols and thiophenols and the results are presented herein.
Results and discussion
MeSA-catalyzed acetylation (method A)
Considering the polyhydroxylic nature of carbohydrates, acetylation of this class of compounds, considered relatively more demanding than simple alcohols or phenols, was chosen as the first set of substrates to be investigated. MeSA is freely miscible with acetic anhydride and hence was taken as the reagent of choice for the per-O-acetylation to be tried. Moreover, the by-product (acetic acid) formed in the reaction serves as an excellent solvent for the product. Also, AcOH being miscible (soluble) in water, the possibility for its removal from the reaction mixture by washing either as such or after neutralization with an alkali is also attractive. Reactions would be carried out using the acyl donor reagent as required by stoichiometry (or in slight excess of it) and MeSA in only catalytic amounts. As a representative example, when 10 μL MeSA was added to a suspension of methyl α-D-glucoside 1 (1 g, entry 1, Table 1) in Ac2O (2.3 mL, 1.1 mol equiv./OH group) and stirred, the sugar went into solution within 6 min and TLC analysis of the reaction mixture at this stage revealed the formation of a product identical with authentic methyl tetra-O-acetyl-α-D-glucoside 2 in Rf value (TLC, EtOAc–n-heptane, 2
:
3; entry 1, Table 1). The reaction was considerably exothermic and no unreacted methyl α-D-glucoside 1 or any partially acetylated product could be detected (TLC) in the reaction mixture. Aqueous workup gave a colorless crystalline product identical in all respects (physical constants and spectroscopic data) with authentic 2 in 98% yield. When the reaction under identical conditions was carried out using D-glucose (3, entry 2, Table 1) as the starting material, the corresponding pentaacetate 4 was obtained in 99% yield. A generalized view of this acid-catalysed acetylation has been depicted in Scheme 1.
Table 1 MeSA-/SiSA-catalyzed per-acetylation of sugars, alcohols, phenols, thiols and thiophenols
Entry |
Substrate |
Product |
Method Aa (using MeSA) |
Method Ba (using SiSA) |
Ref. |
Time (min) |
Yield, % (α : β) |
Time (min) |
Yield, % (α : β) |
The substrate was treated with Ac2O (1.1 mol equiv. per OH/SH group) in the presence of either MeSA, 1.5–3 mol% (Method A) or SiSA 1 mol% (Method B) and the yields reported are those obtained after isolation of the pure product. Was obtained as a mixture of furanose:pyranose, 1 : 1. 2 mol% SiSA was used under Method B. For the propionylation 1.05 mol equiv. of propionic anhydride per OH group was used at room temperature. |
1 |
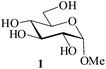 |
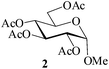 |
5 |
96 |
4 |
95 |
15 |
2 |
 |
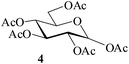 |
5 |
99 (1 : 1) |
3 |
99 (2 : 1) |
15 |
3 |
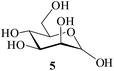 |
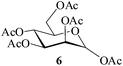 |
2 |
95 (1 : 1.2) |
2 |
98 (1 : 2) |
15 |
4 |
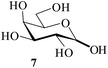 |
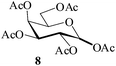 |
3 |
98b |
2 |
98b |
15 |
5c |
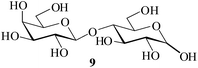 |
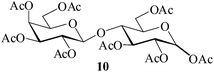 |
15 |
95 (3 : 4) |
10 |
96 (1 : 1) |
15 |
6c |
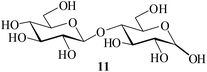 |
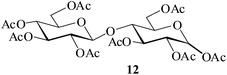 |
25 |
97 (1 : 3) |
15 |
95 (1 : 3) |
22 |
7c |
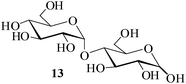 |
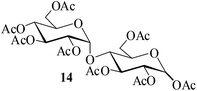 |
20 |
98 (1 : 1) |
10 |
97 (1 : 1) |
15 |
8c |
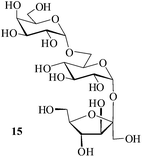 |
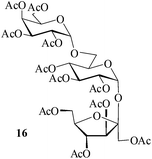 |
20 |
94 |
10 |
92 |
16c |
9 |
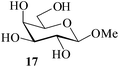 |
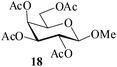 |
6 |
98 |
5 |
96 |
15 |
10 |
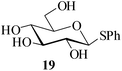 |
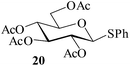 |
10 |
92 |
8 |
93 |
19a |
11 |
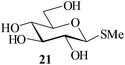 |
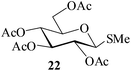 |
10 |
98 |
15 |
97 |
23 |
12 |
 |
 |
15 |
99 |
10 |
99 |
19a |
13 |
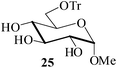 |
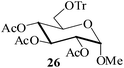 |
15 |
93 |
10 |
95 |
19b |
14 |
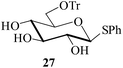 |
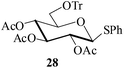 |
10 |
92 |
8 |
93 |
— |
15 |
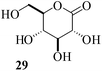 |
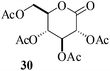 |
60 |
95 |
45 |
93 |
24 |
16 |
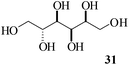 |
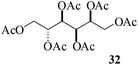 |
5 |
96 |
4 |
95 |
25 |
17 |
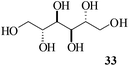 |
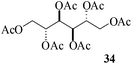 |
60 |
99 |
25 |
98 |
25 |
18 |
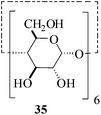 |
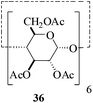 |
10 |
98 |
8 |
96 |
19a |
19c |
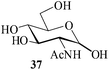 |
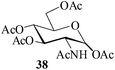 |
120 |
80 (2 : 1) |
60 |
85 (2 : 1) |
15 |
20 |
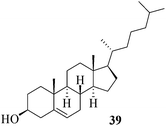 |
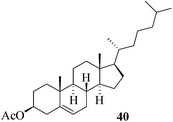 |
30 |
95 |
20 |
92 |
19a |
21 |
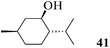 |
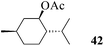 |
10 |
100 |
5 |
100 |
16a |
22 |
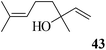 |
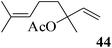 |
20 |
90 |
10 |
92 |
16a |
23 |
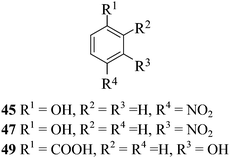 |
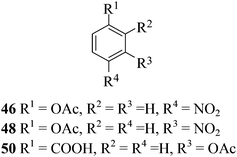 |
25 |
98 |
15 |
96 |
16a |
24 |
25 |
97 |
15 |
95 |
16b |
25 |
5 |
95 |
5 |
95 |
26 |
26 |
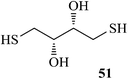 |
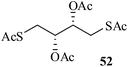 |
5 |
98 |
5 |
98 |
27 |
27 |
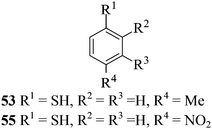 |
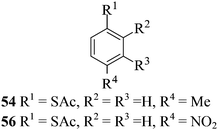 |
15 |
95 |
10 |
94 |
16b |
28 |
10 |
99 |
5 |
97 |
28 |
29 |
3 (at 50 g scale) |
4 |
30 |
99 |
— |
— |
15 |
30d |
17 |
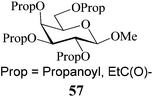 |
10 |
96 |
10 |
98 |
29 |
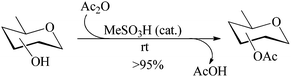 |
| Scheme 1 MeSO3H-catalysed acetylation of carbohydrates using Ac2O as the acyl donor agent. | |
It becomes evident that MeSA serves to extremely efficiently activate the acyl centre of the acid anhydride for a facile reaction of alcoholic nucleophiles that are known to be only poorly nucleophilic in nature giving rise to the desired esters. Moreover, the AcOH generated as a by-product of the reaction being an excellent solvent serves to bring the desired acetylated sugars to solution, thus perhaps also aiding further in the overall process. It may be recalled that the vast majority of unprotected sugars and their simple glycosides are insoluble in acetic anhydride. Therefore a reaction mixture that is heterogeneous at start culminates as a clear colourless solution at finish. In view of the excellent results obtained in the acetylation reactions described above, and with a view to demonstrating the generality of its application to other carbohydrates, the method was extended to some of the other commonly required carbohydrate substrates as well. Thus, excellent results were also obtained in the per-O-acetylation of monosaccharides [hexoses: D-mannose (5), D-galactose (7)], disaccharides [D-lactose (9), D-cellobiose (11), D-maltose (13)] and trisaccharide [D-raffinose (15)] and yielded the desired products 6, 8, 10, 12, 14 and 16 respectively in near quantitative yields (entries 3–8, Table 1).8a,15 Importantly, while the results are well comparable to those obtained using iodine as the Lewis acid catalyst for the reaction,14 it is much superior to the more recent sulfamic acid-assisted acetylation.15 Thus, not only that the current method is faster but also require no heating, unlike the method using sulfamic acid in which it is done at 60 °C to be effective.
Further, to evaluate the applicability of MeSA for the acylation of compounds bearing acid-sensitive groups, in particular those that are easily amenable to acetolysis by the iodine–Ac2O system, various anomeric O-/S-acetals and cyclic O-acetonides were subjected to acetylation conditions as optimized in the foregoing studies. Acetylation of the β-O-glycoside 17 (entry 9, Table 1) to yield the desired tetra-O-acetate 18 occurred, as in the case of 1, without any difficulty. More importantly, the phenylthio- and methylthioglucosides (19, 21, entries 10 and 11, Table 1) when subjected to the acetylation conditions as above, both could be globally acetylated without affecting either the thioacetal protection at the anomeric centre or its configuration. The acetolytically unstable acetonide 23 (entry 12, Table 1) also on subjecting to the acetylation reaction yielded the desired acetate 24 as neat product with the NMR spectra of even the crude product (see ESI† for the spectra) showing it to be virtually pure and suitable for any subsequent further reaction. The acid sensitive trityl ethers 25 and 27 (entries 13 and 14, Table 1) on the other hand when subjected to the above conditions of acetylation, although gave the desired triacetates 26 and 28 in excellent yields of 93 and 92% respectively, did also yield small amounts of some acetolytic by-products, methyl 2,3,4,6-tetra-O-acetyl-α-D-glucopyranoside (2) and phenyl 2,3,4,6-tetra-O-acetyl-1-thio-β-D-glucopyranoside (20), respectively, in 6–7% yields.
In the presence of MeSA, alditols [D-sorbitol (31) and D-mannitol (33)] could also be successfully acetylated to yield the desired products [32 and 34 respectively] in excellent yields (entries 16 and 17, Table 1). Further, α-cyclodextrin (35, entry 18, Table 1) when subjected to the MeSA-catalyzed acetylation, also gave the desired per-O-acetylated α-cyclodextrin 36 in excellent yields. The per-O-acetylation of the 2-acetamido-2-deoxy sugar, N-acetyl-D-glucosamine (37) was comparatively slow, but also yielded the desired acetylated derivative 38 in good yields (entry 19, Table 1).
After having demonstrated successfully the suitability of the MeSA–Ac2O system for the efficient acetylation of carbohydrate substrates, its applicability in the acetylation of non-carbohydrate natural products such as cholesterol (39), menthol (41) and linalool (43) was also evaluated (entries 20–22, Table 1). Satisfyingly, all of the reactions led to the formation of the respective desired acetates 40, 42 and 44 efficiently and in excellent yields without affecting the optical purity in the case of the optically active substrates. Likewise, the reaction of poorly nucleophilic phenols such as p-nitro- (45) and m-nitro- (47) phenols (entries 23 and 24, Table 1) with Ac2O in the presence of catalytic amounts (2 mol%) of MeSA yielded the desired products 46 and 48, respectively, in near quantitative yields in 25 min at rt. These results are well comparable to those obtained by using Mg(ClO4)2 (a highly efficient and powerful Lewis acid used at 1 mol% catalyst concentration) for the same examples with the added advantage that doing the reaction at ambient temperature was adequate under the current protocol unlike the Mg(ClO4)2-catalyzed reaction that required heating at 80 °C for the reaction to be effective.16b In the same manner, when m-hydroxy benzoic acid (49, entry 25, Table 1) was subjected to acetylation under similar conditions, it also led to the formation of the desired neat mono-O-acetate 50 in very short reaction time without any difficulty. From among the classes of thiols and thiophenols also a set of representative compounds were acetylated in order to evaluate the applicability of the method to these classes of compounds. Thus, the dithiothreitol 51 (entry 26, Table 1) gave the tetra-O-/S-acetylated 52 almost instantaneously in the presence of catalytic MeSA. The acetylation was so quick that no chemo-discrimination in the –OH and the –SH groups of 51 towards the reaction was observed. Likewise, the substituted thiophenols, p-toluenethiol (53, bearing electron donating para-substituent) and p-nitrothiophenol (55, bearing an electron withdrawing para-substituent) could also be acetylated neatly and in very short time by acetic anhydride in the presence of MeSA to yield 54 and 56 respectively (entries 27 and 28, Table 1). Notably thus, acetylation of sugars, alcohols, phenols, thiols and thiophenols took place extremely efficiently yielding products without having to resort to any chromatographic purification for the isolation of the product in practically pure form. In the majority of cases studied the products were obtained following a simple aqueous work-up involving precipitation and separation of solids by filtration. The exceptions to this were those at entries 3, 4, 14, 15, 21, 22, 27 and 30 (Table 1) wherein the respective products were obtained as syrup following an extractive work-up in a separatory funnel, the organic solvent used for the extraction being EtOAc.
Based on the fact that per-O-acetylated sugars usually serve as bulk starting materials in multi-step synthetic carbohydrate reactions, a preparative scale model acetylation using D-glucose (3) as the substrate (at 50 g scale) was also carried out. As can be seen from entry 29 (Table 1), the desired pentaacetate 4 could be isolated in excellent yields making this method one of the best hitherto reported procedures for acid-catalyzed acetylation reactions. In large scale reactions, in order to avoid the reaction mixture getting overheated, adding the sugar portion-wise to a solution of the catalyst in the required measure of acetic anhydride was found, however, beneficial. It was observed that usually the reaction was complete with the completion of the addition and the dissolution of the sugar. Further, as a part of the attempt to evaluate the scope of the reaction in other acylations, methyl β-D-galactoside 17 (1 g, entry 30, Table 1) was propionylated using propionic anhydride under the same conditions as optimized for acetylation. Indeed, the desired tetra-O-propionate 57 was also obtained in excellent yields as for the corresponding acetylation reaction.
CSA-catalyzed acetylation (method B)
CSA is a strong organic acid but unlike MeSA, suffers from two major deficiencies that it is a fuming liquid and is corrosive. It may have been for the latter reasons that a literature search on the applications of this acid revealed that it has not yet been investigated in any detail for its possible applications in some of the routine organic reactions such as those described above. Nevertheless, besides being an excellent sulfonating agent, it indeed finds applications in alkylation, halogenation, rearrangements, cyclization and polymerization reactions.30 In view of these factors, alongside the work on MeSA reported above, an investigation of the applications of CSA in the context of the acyl transfer reactions described above was also undertaken. Further, as it was possible to contain the corrosive and fuming nature of the acid by immobilizing it on to the surface of silica, the silica-bound acid (SiSA) prepared in the lab was also investigated simultaneously (see Scheme 2) for its suitability in the acyl transfer reactions as enumerated above. Interestingly, the acid in both the free and the bound forms were found to be exceedingly efficient for all the acyl transfer reactions investigated as can be seen from the results presented below.
 |
| Scheme 2 SiO2–OSO3H-catalysed acetylation of free sugars. | |
Thus, when SiSA (1 mol%) was added to a suspension of D-glucose (1 g, 5.55 mmol) in Ac2O the sugar went into solution within 3 min and the subsequent TLC of the reaction mixture revealed complete conversion of the sugar (3) to its pentaacetate 4 which was obtained in nearly quantitative yield (99%, entry 2, Table 1). The same reaction was also performed using free CSA in place of the bound form (SiSA) for comparison (results not presented in the Table 1). The yield of the pure product 4 obtained in the latter was also excellent, but up to 92% only. It was observed that both reactions were exothermic in nature, as was the case when it was carried out in the presence of MeSA, but between the CSA-promoted and the SiSA-promoted acetylations, the latter was seen as undoubtedly more attractive. There were two important differences observed in the two latter reactions. Firstly, the reaction mixture in the case of the CSA-catalyzed acetylation invariably appeared slightly colored (light amber) in contrast to the colorless reaction mixture that had always resulted in the case of the SiSA-catalyzed reactions. And secondly the somewhat reduced yields obtained in the case of the reactions employing the neat acid, CSA. On close observation it was found that at the time of the addition of the neat acid to the sugar, the solid particles (sugar) that happen to come into its immediate contact gets partially burnt. However, as the dissolution of the acid in Ac2O is also very fast, they become homogeneous with each other very soon thereby leading to an effective dilution of the acid. Thus the detrimental effect caused on the sugar substrate (that affects the yield) gets fortuitously limited. It was found that vigorous stirring at the time of the introduction of the acid could effectively address this problem with near-complete restoration of yields to those comparable to the SiSA-mediated reactions. Addition of the acid prior to the addition of the sugar was also useful in addressing this deficiency. In any case, it may be recalled, the difficulty in handling the corrosive liquid in the case of CSA when it is needed to be used neat indeed remains. In contrast, the SiSA reagent was very easy and convenient to handle. It can be seen from the results presented in Table 1 that the SiSA-catalyzed reactions are as efficient as those catalyzed by MeSA although the latter may be rated as more green and hence the catalyst of choice for the reactions described.
In the light of the above observations a comparison of the current method of acetylation with some of the literature methods was made using the acetonide 23, a somewhat difficult substrate (sensitive to acidic conditions) as the example and the results are shown in Table 2. It was seen that the reaction took place very successfully to afford the desired acetylated product in both the MeSA – as well as the SiSA-catalyzed reactions; and the yields were as good as or better than the methods compared (Table 2). While the literature methods require either controlled reaction conditions or use of a solvent, the current protocols allow the reaction to be performed solvent-free at room temperature.
Table 2 Comparison of the current method with some of the reported methods using the acetonide 23 as the substrate for acetylationa
Substrate |
Catalyst |
Time (min) |
Yield of 24 (%) |
Ref. |
Substrate (1 g) was treated with Ac2O (1.2 mol equiv.) at 25 °C in the presence of either MeSA (2 mol%) or SiSA (1 mol%). For the literature catalysts, the method as reported was used. Pyridine also served as the solvent. MeCN was used as the solvent. The reaction was not complete. The reaction was held at ice-bath temp or below. |
 |
Pyridineb |
45 |
95 |
17 |
Imidazolec |
2 |
98 |
31 |
DABCO |
25 |
98 |
19 |
Al2O3 |
12 |
30d |
32 |
Cu(OTf)2 |
5 |
80 |
9 |
Iodine |
30 |
98e |
14 |
MeSO3H |
15 |
99 |
— |
SiO2–OSO3H |
10 |
99 |
— |
On the MeSA-catalyzed acylations turning out to be efficient and successful [with respect to factors such as: catalytic efficiency-only 1.5–3 mol% catalyst in the case of MeSA and 1 mol% in the case of SiSA, reaction time (short reaction time of a few minutes to 1 h in most cases), reaction conditions (ambient temperatures with no requirement of heating or cooling), solvent-free, yield (nearly quantitative in most cases) and purity of product (practically pure and suitable for further reaction with no requirement for chromatographic purification)] as seen above, a comparison of the cost of the reagent needed for the reaction was attempted (Table 3). Both basic as well as acidic catalysts from among the traditional and more recent categories were chosen for the comparison using the amounts as specified in the respective literature as the basis for the calculation of the cost. It can be seen from the Table 3 that the method using MeSA as the catalyst was proved the cheapest among the lot. In general, it was observed that, using basic catalysts was more expensive than others. Pyridine, the traditional and one of the most trusted/popular catalysts, was seen as the most expensive among the lot compared, not surprisingly though because it is also employed as the solvent in the reaction. Incidentally, it also must generate significantly higher amounts of waste products.
Table 3 Comparison of the reagent-cost involved in the per-O-acetylation of D-glucose on employing various catalysts for the reactiona
Entry |
Description |
Pack size |
Priceb (≠) |
Required for 50 g D-glucose |
Amount |
Cost (₹) |
The price of the reagent was based on the amount needed for a practical-scale (of 50 g) reaction and was based on the respective literature. Aldrich India catalogue price. Wherever possible the listed price of a pack-size of 100 g (or mL) of the reagent was used for the calculation of the cost. Wherever such a pack is not available commercially, the listed price of 25 g or 5 g pack as applicable was used for the calculation. As far as possible the cost of the same grade of the reagent was chosen for the comparison. ₹100 = £1, approximately. Price of the acid only has been used for the calculation. |
1 |
Pyridine17 |
100 mL |
3551 |
250 mL |
8877 |
2 |
DMAP18 |
25 g |
1690 |
27 g |
1825 |
3 |
DABCO19 |
25 g |
2950 |
31 g |
3658 |
4 |
Iodine14 |
100 g |
1520 |
2.5 g |
38 |
5 |
In(OTf)3 (ref. 7 and 8) |
25 g |
3114 |
100 mg |
53 |
6 |
Cu(OTf)2 (ref. 9) |
5 g |
6812 |
50 mg |
68 |
7 |
Sc(OTf)3 (ref. 10) |
5 g |
10 666 |
150 mg |
320 |
8 |
La(OTf)3 (ref. 11) |
25 g |
4703 |
500 mg |
94 |
9 |
CoCl2 (ref. 33) |
25 g |
23 786 |
1.8 g |
1712 |
10 |
NH2SO3H15 |
100 g |
1968 |
10.7 g |
212 |
11 |
MeSO3H |
100 mL |
3692 |
0.2 mL |
7 |
12 |
SiO2–OSO3H |
100 mL |
11 660 |
1.0 g |
7c |
In general, although environmental benefits accrued from catalyst/by-product recovery in chemical reactions may outweigh the cost concern, considering the fact that the method using MeSA is not only environmentally non-hazardous but also is cheap, a need for its recovery after the reaction was not felt very rewarding (lest the cost of recovery overshoot the reagent-cost). In the case of the SiSA-catalyzed reactions also the catalyst is cheap but the possibility for an easy recovery of the silica-bound acid by simple filtration and washing does exist.
Acetylation using AcOH as the acyl donor reagent
Although the reactions using Ac2O reported thus far have been solvent-free and only a small excess over the stoichiometrically required acyl donor reagent had been employed in the acetylations, considering using the free acid as the donor reagent in the reaction wherever possible would also be in context. For this reason a model reaction using (−)-menthol as the alcohol substrate and HOAc (glacial) as the acyl donor was carried out in the presence of MeSA (2 mol%, Scheme 3). It was found that a neat reaction occurred and the acetate 42 16a,34 could be obtained in quantitative yields when a menthol–AcOH mole ratio of 1
:
2 was used for the reaction (Scheme 3). Washing with cold aqueous bicarbonate was the only major step involved in the isolation of the product. At mole ratios of 1
:
1.2 and 1
:
1.5 the conversion of the alcohol to the desired acetate occurred only to the extent of 90 and 95% respectively as determined by chromatography. The latter reactions also required longer reaction time with the added observation that extending the reaction time beyond 4 h did not result in any significant enhancement in the percent conversion (Scheme 3). Measurement of the optical rotation of the product isolated confirmed beyond doubt that the reaction did not affect the optical purity of the chiral compound. It is noteworthy that for the same substrate HClO4–silica gave comparable yields of the acetate, when used at 1 mol% level, in a reaction for 6 h at 80 °C in excess of AcOH (35 mol equiv.).16a The Keggin-type heteropolyacids on the other hand had been reported to be ineffective even under microwave irradiation.34 A similar esterification protocol for (−)-menthol catalyzed by a functionalized carbon material that appeared while this manuscript was under preparation35 required heating in heptane for a period of 8–10 h at 70 °C to be complete. Likewise, another esterification reaction of the same kind, but using a functionalized ionic liquid-based mesoporous organosilica as the catalyst, described during the preparation of this manuscript, also required heating at 60–75 °C for 12–24 h for the reaction to be effective.36 As in the case of menthol, treatment of other alcohols such as n-octanol (58) and propylene glycol (60) with acetic acid also led to the expected mono- and di-O-acetates (59 and 61, respectively) in near quantitative yields (entries 2 and 3, Table 4). Similarly, treatment of other carboxylic acids such as cinnamic acid (62) and tartaric acid (64) with EtOH also afforded with ease the expected cinnamate 63 and tartrate 65 (mono- and diesters) respectively (entries 4 and 5, Table 4). It may be recalled that a recently reported N-methyl-boronopyridinium iodide40a required heating at reflux for 18 h for the conversion of the dicarboxylic acid 64 to its diester 65. Again, when sialic acid (66) was stirred in anhydrous MeOH in the presence of catalytic MeSA, a complete conversion of the acid to its methyl ester 67 also occurred with ease. The latter reactions were conveniently held in the respective alcoholic solutions, and on completion of the reaction, were recovered at ease by distillation under reduced pressure; and the products in these cases were crystalline and sufficiently pure for subsequent reactions.
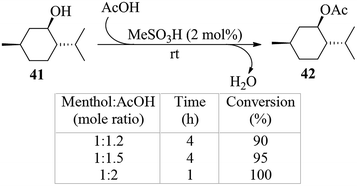 |
| Scheme 3 Acetylation of (−)-menthol using acetic acid as the acyl donor reagent (% conversions were determined by GC & HPLC). | |
Table 4 Esterification of various mono- and dicarboxylic acids under neat conditions in the presence of catalytic MeSAa
Entry |
Acid (R1–COOH) |
Alcohol (R2–OH) |
Time (h) |
Product (% yield) |
The reactions were held at rt in the presence of 2 mol% MeSA. |
1 |
Acetic |
(−)-Menthol (41) |
2 |
(−)-Menthyl acetate (42) (100) |
2 |
Acetic |
n-Octanol (58) |
10 |
Octyl acetate (59) (98) |
3 |
Acetic |
1,2-Propanediol (60) |
6 |
1,2-Diacetoxy propane (61) (97) |
4 |
Cinnamic (62) |
Ethanol |
15 |
Ethyl cinnamate (63) (95) |
5 |
L-(+)-Tartaric (64) |
Ethanol |
12 |
(+)-Diethyl-L-tartrate (65) (99) |
6 |
Sialic (66) |
Methanol |
10 |
Sialic acid methyl ester (67) (98) |
Conclusions
MeSO3H and SiO2–OSO3H have been found to be two highly efficient catalysts for acyl transfer reactions of mono-, di- and trisaccharides and their various partially protected derivatives, as well as various alcohols, phenols, thiols and thiophenols. The method is tolerant to acid sensitive functional groups and can therefore be present on the substrate for acylation. The new method of acetylation using the green organic acid, MeSO3H, is economical, solvent-free, and benign and serves to fulfil most other qualities desired of a green method. Acetylation in the case of an optically active alcohol, menthol by reaction with acetic acid as well as other examples of successful alcohol–carboxylic acid esterifications, without affecting the chiral integrity of the compound, clearly indicate future possibilities of application of this method.
Experimental
General
All reagents (Aldrich India Ltd) used were of analytical grade and were used as purchased without further purification. Reactions were monitored by TLC, which was performed with 0.2 mm Merck pre-coated silica gel 60 F254 aluminium sheets. Compounds were detected by dipping the TLC plates in an ethanolic solution of sulphuric acid (5%, v/v) and heating or using a reagent prepared by dissolving a mixture of 4.2 g ammonium molybdate, 0.2 g cerium sulphate tetrahydrate and 6.2 mL sulphuric acid in 94 mL water. Column chromatography was performed using silica gel (100–200 mesh ASTM). 1H/13C NMR spectra were recorded in CDCl3 at 400/100 MHz on a Bruker AvanceIII spectrometer. The chemical shifts have been reported in ppm using TMS as the internal standard. The multiplicity of the signals have been shown as, s = singlet, d = doublet, t = triplet, q = quartet, m = multiplet with the coupling constant (J value) expressed in Hz. The anomeric ratio of products reported in Table 1 were determined from their NMR spectra. Mass spectra were obtained on an Ultraflex TOF/TOF MALDI or Maxis HRMS equipment. Specific rotations were determined on an AUTOPOL IV polarimeter at 20 °C. IR spectra were recorded on a Nicolet FT-IR Impact 410 instrument either as neat or KBr pellets. Melting points were determined on a Buchi melting point apparatus. All compounds reported here (except compound 28) have been reported previously (2,15 4,15 6,15 8,15 10,15 12,22 14,15 16,16c 18,15 20,19a 22,23 24,19a 26,19b 30,23 32,25 34,25 36,19a 38,15 40,19a 42,16a 44,16a 46,16a 48,16b 50,26 52,27 54,16b 56,27 57,28 59,37 61,38 63,39 65 (ref. 40) and 67 (ref. 41)), many are commercially available and therefore only the spectral data for the new compound (28) are reported.
Preparation of SiO2-sulfuric acid (SiSA) catalyst
CSA (1.45 g, 12.5 mmol) was added to a suspension of SiO2 (23.7 g, 230–400 mesh) in Et2O (70.0 mL). Release of HCl gas that followed immediately after the addition of CSA was found to subside in a short while. The mixture after stirring for a few minutes was concentrated to dryness followed by heating at 100 °C for 48 h in a vacuum oven to furnish SiSA as a free flowing powder. 10 mg of the powder contains approximately 0.005 mmol of the acid enough for the acetylation of a gram of the sugar.
Typical procedure for acetylation using Ac2O as the acyl donor reagent: acetylation of D-glucose
Method A, using MeSO3H. To a suspension of D-glucose (entry 2, Table 1 and 1 g, 5.55 mmol) in acetic anhydride (2.88 mL, 30.53 mmol) taken in a round bottom flask was added, while being stirred at rt (approximately 30–35 °C), MeSA (5–7 μL, 1.5–1.8 mol%) and the stirring was continued until complete dissolution of the sugar occurred. Warming of the reaction mixture occurred immediately following the addition of the catalyst and was indicative of the onset of acetylation. It was soon led to the dissolution of the sugar indicating completion of the reaction which was confirmed by TLC (EtOAc–n-heptane, 2
:
3, v/v) by comparison with authentic penta-O-acetyl-D-glucopyranose. A colorless homogeneous solution was obtained within a few minutes. The reaction mixture was poured into a beaker containing crushed ice and aqueous NaHCO3 during stirring which resulted in the separation of the product as a colorless solid. It was left for a few hours in a refrigerator for solidification of the product to complete. The solids were separated by filtration at the pump and, after washing with cold deionized water to neutrality, was dried (first in the air and then in a vacuum oven/Kugelrohr) when the title product was obtained (2.14 g) as a colorless solid (99% yield).In large scale preparations (5–50 g or more), the sugar was added portion-wise to acetic anhydride containing the catalyst (180 μL MeSA in 145 mL Ac2O for a 50 gram scale reaction) and upon completion of the reaction, the product was isolated as described above and was obtained (107 g pentaacetate from 50 g of glucose) as white powder in near quantitative yield.
Method B, using SiO2–OSO3H (SiSA). To a suspension of D-glucose (entry 2, Table 1 and 1 g, 5.55 mmol) in acetic anhydride (2.88 mL, 30.53 mmol) taken in a round bottom flask was added, while being stirred at rt (approximately 30–35 °C), SiSA (10 mg, 1 mol%) and the stirring was continued until complete reaction occurred. The product was isolated as described under Method A above. The title compound was obtained in near quantitative yield as colourless solid (2.14 g, 99%).
Acylation using free carboxylic acid as the acyl donor reagent: acetylation of (−)-menthol (41)
To a solution of (−)-menthol (41, 1 g, 6.4 mmol) in glacial AcOH (1 mL) was added MeSA (10 μL, 2 mol%) under stirring at room temperature and the stirring was continued for an hour. TLC at this time showed complete consumption of the alcohol. The reaction mixture was poured into crushed ice in a beaker containing NaHCO3. On neutralization the product, (−)-menthyl acetate (42), was isolated by extraction with EtOAc in a separatory funnel. Yield, 1.26 g, quantitative, colorless liquid. The physical constants and the NMR data were in agreement with literature data.16a
Esterification of tartaric acid: preparation of (+)-diethyl-L-tartrate (65)40
MeSA (10 μL, 2 mol%) was added to a solution of (+)-L-tartaric acid (64, 1 g, 6.6 mmol) in absolute alcohol (50 mL) and the solution was stirred for 12 h at room temperature when TLC (EtOAc–n-heptane) showed complete disappearance of the tartaric acid. EtOH (up to 40 mL) was recovered from the reaction mixture by vacuum distillation. The residue was diluted with EtOAc (25 mL) and was washed successively with cold aqueous NaHCO3 solution (to neutrality) and the product was isolated as described above. Colorless liquid, 1.36 g, 99%. Physical constants and spectral data were in agreement with literature values for (+)-diethyl-L-tartrate (65).40
Phenyl-2,3,4-tri-O-acetyl-6-O-trityl-1-thio-β-D-glucopyranoside (28)
Colourless liquid; [α]20D = +1.2 (c = 1, CH2Cl2); 1H NMR (400 MHz, CDCl3, 25 °C, TMS): δ (ppm) = 7.64–7.61 (m, 2H, ArH), 7.45–7.42 (m, 6H, ArH), 7.30–7.20 (m, 12H, ArH), 5.17 (t, J = 9.2 Hz, 1H, H-2), 5.09 (dd, Ja = 9.8 Hz, Jb = 6.8 Hz, 1H, H-3), 5.04 (dd, Ja = 7.2 Hz, Jb = 9.1 Hz, 1H, H-4), 4.73 (d, J = 10.0 Hz, 1H, H-1), 3.58 (m, 1H, H-5), 3.27 (dd, Ja = 2.1 Hz, Jb = 10.1 Hz, 1H, H-6a), 3.15 (dd, Ja = 5.2 Hz, Jb = 10.5 Hz, 1H, H-6b), 2.09 (s, 3H, COCH3), 1.96 (s, 3H, COCH3), 1.69 (s, 3H, COCH3). 13C NMR: (100 MHz, CDCl3, 25 °C): δ (ppm) = 170.3 (CO of COCH3), 169.3 (CO of COCH3), 168.9 (CO of COCH3), 143.5, 133.2, 131.8, 129.0, 128.7, 128.3, 127.8, 127.0, 86.7 (C-1), 85.6, 74.3, 70.1, 68.3, 62.0, 20.8 (CH3 of COCH3), 20.6 (CH3 of COCH3), 20.3 (CH3 of COCH3); IR (cm−1): 2924, 2853, 2104, 1756, 1634, 1490, 1448, 1373, 1242, 1218, 1155, 1047, 912, 765, 748, 703, 632. HRMS-ESI (m/z) calculated for C37H36NaO8S, [M + Na]+ 663.2029, found 663.2021.
Acknowledgements
S.K.G. thanks NIPER, S.A.S. Nagar and the Ministry of Chemicals and Fertilizers, Govt. of India for permission to pursue PhD under its staff development scheme.
Notes and references
- F. J. M. Rajabalee, Angew. Chem., Int. Ed. Engl., 1971, 10, 75 CrossRef CAS; G. Agnihotri, P. Tiwari and A. K. Misra, Carbohydr. Res., 2005, 340, 1393 CrossRef PubMed.
- F. Dasgupta, P. P. Singh and H. C. Srivastava, Carbohydr. Res., 1980, 80, 346 CrossRef CAS; A. I. Vogel, Vogel's Textbook of Practical Organic Chemistry, Wiley, New York, 5th edn, 1989, p. 644 Search PubMed; M. L. Wolfrom and A. Thomson, Methods Carbohydr. Chem., 1963, 2, 211 Search PubMed.
- J. K. Groves, Chem. Soc. Rev., 1972, 1, 73 RSC; S. Yan, N. Ding, W. Zhang, P. Wang, Y. Li and M. Li, J. Carbohydr. Chem., 2012, 31, 571 CrossRef CAS.
- M. Miyashita, I. Shiina, S. Miyoshi and T. Mukaiyama, Bull. Chem. Soc. Jpn., 1993, 66, 1516 CrossRef CAS.
- R. H. Baker and F. G. Bordwell, Org. Synth., 1944, 24, 18 CrossRef CAS; R. H. Baker and F. G. Bordwell, in Organic Syntheses, Wiley, New York, 1955, vol. 3, p. 141 CrossRef; H. B. Wood Jr, H. W. Diehl and H. G. Fletcher Jr, J. Am. Chem. Soc., 1957, 79, 1986 CrossRef; C. Limousin, J. Cleophax, A. Petit, A. Loupy and G. Lukacs, J. Carbohydr. Chem., 1997, 16, 327 CrossRef.
- P. A. Procopiou, S. P. D. Baugh, S. S. Flack and G. G. A. Inglis, J. Org. Chem., 1998, 63, 2342 CrossRef CAS.
- K. K. Chauhan, C. G. Frost, I. Love and D. Waite, Synlett, 1999, 1743 CrossRef CAS PubMed.
-
(a) S. K. Giri, M. Verma and K. P. R. Kartha, J. Carbohydr. Chem., 2008, 27, 464 CrossRef CAS;
(b) S. K. Giri and K. P. R. Kartha, Synth. Commun., 2010, 40, 3378 CrossRef CAS.
- C.-A. Tai, S. S. Kulkarni and S.-C. Hung, J. Org. Chem., 2003, 68, 8719 CrossRef CAS PubMed.
- R. Shogren, Carbohydr. Polym., 2008, 72, 439 CrossRef CAS PubMed; J.-C. Lee, C.-A. Tai and S.-C. Hung, Tetrahedron Lett., 2002, 43, 851 CrossRef.
- S. Dasgupta, V. K. Rajput, B. Roy and B. Mukhopadhyay, J. Carbohydr. Chem., 2007, 26, 91 CrossRef CAS; A. Dzudza and T. J. Marks, J. Org. Chem., 2008, 73, 4004 CrossRef PubMed.
- A. Orita, C. Tanahashi, A. Kakuda and J. Otera, Angew. Chem., Int. Ed., 2000, 39, 2877 CrossRef CAS; A. Orita, C. Tanahashi, A. Kakuda and J. Otera, J. Org. Chem., 2001, 66, 8926 CrossRef PubMed.
- M. D. Carrigan, D. Freiberg, R. C. Smith, H. M. Zerth and R. S. Mohan, Synthesis, 2001, 2091 CrossRef CAS.
- K. P. R. Kartha and R. A. Field, Tetrahedron, 1997, 53, 11753 CrossRef CAS.
- A. Santra, G. Guchhait and A. K. Mishra, Green Chem., 2011, 13, 1345 RSC.
-
(a) A. K. Chakraborti and R. Gulhane, Chem. Commun., 2003, 1896 RSC;
(b) A. K. Chakraborti, L. Sharma, R. Gulhane and Shivani, Tetrahedron, 2003, 59, 7661 CrossRef CAS PubMed;
(c) A. K. Misra, P. Tiwari and S. K. Madhusudan, Carbohydr. Res., 2005, 340, 325 CrossRef CAS PubMed;
(d) B. Mukhopadhyay, D. A. Russell and R. A. Field, Carbohydr. Res., 2005, 340, 1075 CrossRef CAS PubMed.
- C. S. Hudson and J. K. Dale, J. Am. Chem. Soc., 1915, 37, 1264 CrossRef CAS; T. G. Bonner and P. McNamara, J. Chem. Soc. B, 1968, 795 RSC.
- G. Hofle, W. Steglich and H. Vorbruggen, Angew. Chem., Int. Ed., 1978, 17, 569 CrossRef CAS; E. F. V. Scriven, Chem. Soc. Rev., 1983, 12, 129 RSC; T. W. Greene and P. G. M. Wuts, Protective Groups in Organic Synthesis, Wiley, New York, 3rd edn, 1999 Search PubMed; J. R. Hanson, Protective Groups in Organic Synthesis, Blackwell Science Inc., MA, 1st edn, 1999 Search PubMed.
-
(a) R. Ch, M. Tyagi, P. R. Patil and K. P. R. Kartha, Tetrahedron Lett., 2011, 52, 5841 CrossRef CAS PubMed;
(b) B. K. Gadakh, P. R. Patil, S. Malik and K. P. R. Kartha, Synth. Commun., 2009, 39, 2430 CrossRef CAS.
- R. Boyle and E. S. Venkataramani, PCT Int. Appl. WO 9521135, CAN 123:207938, 1995 CrossRef CAS PubMed; M. C. Wilkinson, Org. Lett., 2011, 13(9), 2232 CrossRef CAS PubMed; M. Jamshad, J. C. Murrell and V. Fülöp, Protein Expression Purif., 2007, 52, 472 CrossRef PubMed.
- M. A. Zolfigol, Tetrahedron, 2001, 57, 9509 CrossRef CAS; M. A. Zolfigol, E. Madrakian and E. Ghaemi, Molecules, 2002, 7, 734 CrossRef PubMed; A. R. Hajipour, A. Zarei, L. Khazdooz, S. A. Pourmousavi, S. Zahmatkesh and A. E. Ruoho, Indian J. Chem., 2006, 45B, 305 Search PubMed; D. M. Pore, U. V. Desai, R. B. Mane and P. P. Wadgaonkar, Indian J. Chem., 2006, 45B, 1291 Search PubMed; A. R. Modarresi-Alam, M. Nasrollahzadeh and F. Khamooshi, ARKIVOC, 2007, 16, 238 CrossRef; F. Heidarizadeh and S. Elahi, Orient. J. Chem., 2011, 27, 1531 Search PubMed; B. Datta and M. A. Pasha, Chin. J. Catal., 2011, 32, 1180 CrossRef; A. Khalafi-Nezhad, H. Foroughi, M. M. Doroodmand and F. Panathi, J. Mater. Chem., 2011, 21, 12842 RSC; L. Torkian, P. Salehi, M. Dabiri and S. Kharrazi, Synth. Commun., 2011, 41, 2115 CrossRef; K. Niknam, D. Saberi and M. Baghernejad, Phosphorus, Sulfur Silicon Relat. Elem., 2010, 185, 875 CrossRef; R. Badri, A. Alireza-haddad, M. adlu and M. K. Mohammadi, Bull. Chem. Soc. Ethiop., 2013, 27, 131 Search PubMed; S. Pathak, K. Debnath and A. Pramanik, Beilstein J. Org. Chem., 2013, 9, 2344 CrossRef PubMed.
- C. S. Hudson and J. K. Dale, J. Am. Chem. Soc., 1918, 40, 992 CrossRef CAS.
- C. A. Sanhueza, R. L. Dorta and J. T. Vázquez, Tetrahedron: Asymmetry, 2008, 19, 258 CrossRef CAS PubMed.
- C. C. Joseph, H. Regeling, B. Zwanenburg and G. J. F. Chittenden, Tetrahedron, 2002, 58, 6907 CrossRef CAS.
- M. K. Hlggins, R. S. Bly and S. L. Morgan, Anal. Chem., 1994, 66, 2656 CrossRef.
- A. Cipiciani, F. Fringuelli and A. M. Scappini, Tetrahedron, 1996, 52, 9869 CrossRef CAS.
- M. E. Shoman, J. F. DuMond, T. S. Isbell, J. H. Crawford, A. Brandon, J. Honovar, D. A. Vitturi, C. R. White, R. P. Patel and S. B. King, J. Med. Chem., 2011, 54, 1059 CrossRef CAS PubMed.
- A. V. D. Hoogenb, J. H. M. Lange, R. P. J. Bronger, A. R. Stoit and J. W. Terpstra, Tetrahedron Lett., 2010, 51, 6877 CrossRef PubMed.
- C. D. Hurd and K. M. Gordon, J. Am. Chem. Soc., 1941, 63, 2657 CrossRef CAS.
- R. J. Cremlyn, Chlorosulfonic acid A Versatile Reagent, Royal Society of Chemistry, Cambridge, UK, 2002 Search PubMed.
- P. Tiwari, R. Kumar, P. R. Maulik and A. K. Mishra, Eur. J. Org. Chem., 2005, 4265 CrossRef CAS.
- V. K. Yadav and G. K. Babu, J. Org. Chem., 2004, 69, 577 CrossRef CAS PubMed.
- J. Iqbal and R. R. Srivastava, J. Org. Chem., 1992, 57, 2001 CrossRef CAS.
- E. Rezaei-Seresht, F. M. Zonoz, M. Estiri and R. Tayebee, Ind. Eng. Chem. Res., 2011, 50, 1837 CrossRef CAS.
- S. Zhan, X. Tao, L. Cai, X. Liu and T. Liu, Green Chem., 2014, 16, 4649 RSC.
- D. Elhamifar, B. Karimi, A. Moradi and J. Rastegar, ChemPlusChem, 2014, 79, 1147 CrossRef CAS.
- A.-X. Li, T.-S. Li and T.-H. Ding, Chem. Commun., 1997, 1389 RSC.
- L. Zhu and X. Liang, Kinet. Catal., 2012, 53, 684 CrossRef CAS.
- K. C. Nguyen and H. Weizman, J. Chem. Educ., 2007, 84, 119 CrossRef CAS.
-
(a) T. Maki, K. Ishihara and H. Yamamoto, Org. Lett., 2005, 7, 5047 CrossRef CAS PubMed;
(b) Y. N. Belokon, V. I. Maleev, Z. T. Gugkaeva, M. A. Moskalenko, A. T. Tsaloev, A. S. Peregudov, S. C. Gagieva, K. A. Lyssenko, V. N. Khrustalev and A. V. Grachev, Russ. Chem. Bull., 2007, 56, 1507 CrossRef CAS PubMed.
- R. Kuhn, P. Lutz and D. L. MacDonald, Chem. Ber., 1966, 99, 611 CrossRef CAS.
Footnote |
† Electronic supplementary information (ESI) available: Archive entries of 1H and 13C spectra of parent compounds synthesized. See DOI: 10.1039/c4ra16916f |
|
This journal is © The Royal Society of Chemistry 2015 |
Click here to see how this site uses Cookies. View our privacy policy here.