DOI:
10.1039/C4RA14612C
(Paper)
RSC Adv., 2015,
5, 12536-12545
Ionic liquid based microemulsion method for the fabrication of poly(methyl methacrylate)–TiO2 nanocomposite as a highly efficient visible light photocatalyst†
Received
15th November 2014
, Accepted 22nd December 2014
First published on 23rd December 2014
Abstract
A series of visible light-responsive poly(methyl methacrylate) (PMMA)/TiO2/IL nanocomposite transparent films, with different loading of TiO2 nanoparticles, were facilely prepared using an ionic liquid-in-oil microemulsion system. The microemulsion system was containing methyl methacrylate monomer as continues phase, 1-butyl-3-methylimidazolium tetrafluoroborate ([bmim][BF4]) as dispersant phase, Triton X-100 as surfactant and 1-butanol as co-surfactant. TiO2 nanoparticles were dispersed into the microemulsion system, and then the oil phase was polymerized by a benzoyl peroxide initiator. Techniques such as UV-vis diffuse reflectance spectra (DRS), TEM, FTIR, XRD, FE-SEM and TGA were used to characterize the resulting nanocomposite. Methylene blue (MB) dye was used as a model pollutant to study the photocatalytic activity of this novel type of PMMA/TiO2/IL nanocomposite. As an interesting result, it is found that the prepared nanocomposite exhibit excellent photocatalytic activity under visible light irradiation and considerably higher photocurrents than bare TiO2. Moreover, influence of various operational parameters such as pH, the amount of loaded TiO2 nanoparticles and recycling of the photocatalyst on the degradation reaction was investigated in detail.
1. Introduction
Polymer–inorganic nanocomposites have attracted extensive attention in recent years due to a combination of the properties of the nanoscopic inorganic particles (typically 10–100 Å) and the organic polymers matrix.1–3 The hybrid nanocomposites obtained, might exhibit improved thermal, electrical, mechanical and optical properties. They show some special applications in optics, electronics, photocatalysis, device fabrication and gas sensors.4–10 To date, several processes have been developed to fabricate nanoscale polymer/inorganic composites, including physical mixing,11 sol–gel technique,12 surface initiated controlled/living radical polymerization,13 dispersion polymerization,14,15 in situ emulsion polymerization and16,17 unsymmetrical square wave current method.18 Among these methods, colloidal approaches regarded as microemulsion mediated synthesis is believed to have a tremendous potential for the realization of tailor-made nanocomposites. In this method, size and size distribution of the filer particles in nanocomposite can be easily controlled at the nanoscale.19 Microemulsions are isotropic, macroscopically homogeneous and thermodynamically stable solutions, including at least three components, namely, a polar phase (usually water), a non-polar phase (usually oil) and a surfactant and sometime co-surfactant.20 Of particular recent interest is the combination of surfactant and ionic liquids (ILs), as a substitute for water, to create novel microemulsion systems.21 It is believed that IL microemulsions, in comparison to traditional microemulsions, can provide hydrophilic or hydrophobic nanodomains, and thereby expand the potential uses of ILs as reaction media,22 and consequently synthesize the special nanocomposites. ILs or “green solvents”, which are liquids at ambient conditions, are attracting considerable interest in many fields of chemistry, due to their remarkable properties containing non-volatility, non-flammability, excellent thermal stability, higher ionic conductivity and wide electrochemical windows.23–25
Poly(methyl methacrylate), as a polymeric glass and engineering plastic, is one of the most versatile, and is an important member of common organic polymers.26 It was chosen as the composite matrix polymer because of its outstanding chemico-physical properties, good environmental stability, simplicity of preparation, and high optically properties.27,28 Extensive investigations have been reported on the incorporation of semiconductor metallic oxide particles into the polymer matrix and enhance its photocatalytic activity and other properties. Over 30 years of studies, semiconductor metallic oxide TiO2 or ZnO-induced heterogeneous photocatalysis is a friendly technique for the complete degradation of recalcitrant organic pollutant and toxic organic substance in water and gaseous streams.29–31 It has been gaining industrial and academic attention to TiO2, because: it is easily available, has a nontoxic nature, low cost, high efficiency, high activity, chemically stable, easy operation and no secondary pollution to the environment.32–35 On the other hand, practical usage of pure TiO2 has various shortcomings: the difficult separation from the aqueous phase, low surface area, low adsorption capacity, rapid formation of aggregates in a suspension, and recycling difficulties.36 In practice, for improving the applicability of TiO2, it should be immobilized as a transparent thin film nanocomposite. Wan et al.37 synthesized nano-TiO2 particles through the hydrolysis of titanium tetrabutoxide (TTB) in W/O microemulsion, and prepared TiO2/polyacrylate nanocomposite by in situ polymerization. Currently Ye et al.38 synthesized the organic nano-TiO2 in reverse (W/O) microemulsion, using tetrabutyltitanate (TBOT) as precursor and γ-methacryloxypropyltrimethoxy silane (KH-570) as a modifier. The prepared nanocomposite had a core–shell structure with a particle size of 155 nm.
Azo compounds, such as methylene blue (MB), constitute about one half of the dyes and are chemically inert, non-biodegradable, high stability, high toxicity and carcinogenic character. MB dye, as illustrated in the ESI (Scheme S1†), has a very short life in the excited state, and is stable in the visible and near-UV ranges of light.39–41 Hence, discoloration and detoxification of MB dye has significant environmental importance. However, the pure TiO2 photocatalyst, as a common detoxifier, can only be excited and generates electron and hole pair (e−/h+) upon irradiation under ultraviolet or near ultraviolet radiation, due to its large band gap (3.2 eV for anatase and 3.0 eV for rutile).42 Ultraviolet accounts for only about 4% of the solar light spectrum, and it has low intensity as compared to other spectrums of solar light. In order to induce visible light activity of TiO2, the band gap must be shifted to lower values. Several attempts have been made to extend the photo response of TiO2 to the visible region and enhance the photocatalytic activity of TiO2, such as metal and nonmetal doping, noble metal deposition and forming composites with fine semiconductors.43–46 Conjugated polymers such as polyaniline and polypyrrole provide a way of achieving this due to their high absorption coefficients in the visible region.47 For example Wang et al.48 prepared a series of polyaniline (PANI)-sensitized TiO2 composite photocatalysts (PANI/TiO2) by a simple solution method. The results showed that the light response of TiO2 was extended to visible-light regions after being sensitized by PANI as a photosensitizer. The composite achieved the best performance in the degradation of the MB dye under visible light. Lettmann et al.49 fabricated photo-stable carbon-modified TiO2 as a new material and proved an increase of photocatalytic activity under visible light irradiation. They proposed that the carbons over TiO2 particles play a sensitizer role in photocatalytic reaction under visible light.
Our opinion is that ILs could be a suitable candidate for the fabrication of a visible light induced photocatalyst. To the best of our knowledge, the architecture of PMMA/TiO2 thin film nanocomposite by IL-in-oil microemulsion has not been reported to date. Thus, in this paper we present the IL-in-oil microemulsion route to fabricate PMMA/TiO2/IL nanocomposite. To stabilize TiO2 nanoparticles in IL-in-oil microemulsion system, hydrophilic IL of [bmim][BF4], as polar phase and methyl methacrylate monomer as oil phase, Triton X-100 as nonionic surfactant and 1-butanol as co-surfactant, were used. After the preparation of the TiO2 nanocolloid system the initiator benzoyl peroxide (BPO) was used to start the polymerization process and produce the modified PMMA/TiO2 nanocomposite. The prepared nanocomposites with different TiO2 loading were characterized using UV-vis-DRS, FTIR, XRD, FE-SEM, TEM and thermo-gravimetric analysis (TGA). In this work MB was used to investigate the photocatalytic activity of the modified PMMA/TiO2/IL nanocomposite under visible light irradiation. The performance evaluation indicates that the modified PMMA/TiO2/IL catalyst shows high photocatalytic activity in the photodegradation of MB under visible light. The effects of some operating factors on the degradation of MB such as, TiO2 dosage, pH and recycling of the photocatalyst, were investigated. Finally, the kinetics of the degradation reaction were studied.
2. Experimental section
2.1. Materials
Hydrophilic ionic liquid, [bmim][BF4], as illustrated in the ESI (Scheme S2†), and the nonionic surfactant Triton X-100 were purchased from Sigma-Aldrich. A commercial titanium dioxide TiO2 nanoparticle was used in this study (ca. 80% anatase, 20% rutile, with a BET surface area of 50 m2 g−1 and particle size of less than 15 nm). Methyl methacrylate (MMA) monomer (AR grade) and benzoyl peroxide (BPO) were received from Merck. All other reagents including, methylene blue (MB), 1-butanol, HNO3 and NaOH were analytical grade reagents and used as received. All the aqueous solutions were prepared with deionized water.
2.2. Preparation of IL-in-oil microemulsion containing TiO2 nanoparticles
The nanometer-sized ionic liquid droplet including TiO2 nanoparticles in the MMA monomer as oil phase (IL/O) was formed as follows. First, a solution of TX-100 surfactant in MMA solvent, with a concentration of 0.1 M was prepared. The IL-based microemulsion system is prepared by fixing the mole ratio of [bmim][BF4] to Triton X-100 at 1. A certain amount of TiO2 nanoparticles was added to 0.1132 g of IL and ultrasonically dispersed until a TiO2/IL homogeneous mixture was achieved. The TiO2/IL mixture was added to the solution of the surfactant and was mixed for 20 min by stirring. A cloudy colloidal solution was obtained. By titrating with 1-butanol, as co-surfactant, a clear phase microemulsion was obtained at room temperature. In this manner, a transparent and stable for over several months IL/Oil microemulsion system containing TiO2 nanoparticles was obtained. It was found that this microemulsion system was also stable even at 60 °C, which is the polymerization condition of MMA.
2.3. Preparation of the modified PMMA/TiO2/IL nanocomposite
An initiator benzoyl peroxide (BPO) (0.2 wt% based on the weight of oil) was added to the previous microemulsion system with rigorous stirring. The system was maintained at 60 °C for 8 h under static condition. Finally, a few films were also prepared with different TiO2 loading, corresponding to the weight percentage in the polymer, ranging from 0.0 wt% to 0.014 wt%. Namely, 0.0, 0.006, 0.008, 0.010, 0.012 and 0.014 wt% for TiO2 loading, was labeled as S0 (for pure PMMA), S1, S2, S3, S4 and S5, respectively. No apparent visible phase separation was observed during and after the polymerization process for all the samples.
2.4. Characterization of the modified PMMA/TiO2/IL nanocomposite
Band gap energies of the nanocomposite samples were determined by UV-visible diffuse reflectance spectra (UV-vis/DRS) in air at room temperature in the wavelength range of 200–600 nm using a UV/Vis/NIR spectrophotometer (JASCO, V-670 (190–2700 nm)). The band gap energies were calculated employing the following equation:where Eg is the band gap energy (eV) and λ is the wavelength of the absorption edges in the spectrum or cut-off wavelength (nm). The cut-off wavelength was determined by linear extrapolation from the inflection point of the curve to baseline. The band gap energies for [bmim][BF4] and PMMA were also determined by the abovementioned method.
Fourier transform-infrared (FTIR) spectroscopy was conducted on a Galaxy series FT-IR 5000. Pellets were prepared using potassium bromide (KBr), 99% purity and FTIR grade (Sigma-Aldrich). Powder was added to KBr in a mass ratio of 1
:
100. Samples were homogenously mixed with a shaker for 20 s prior to forming the pellets.
The X-ray diffraction (XRD) experiment was carried out at room temperature in the 2–80° 2θ range. A Philips (PW 1800) diffractometer instrument with Cu Kα radiation (λ = 1.540 Å) and Ni filter was used to collect the X-ray data.
The field emission scanning electron microscopy (FE-SEM) image was obtained with a Hitachi (F 4160) instrument.
The surface morphology of PMMA/TiO2 (S3 as a typical sample) nanocomposite was observed using a transmission electron microscope (TEM) (Zeiss-EM10C-80 kV). An ultramicrotome was used to prepare the nanocomposite samples for TEM analysis by cutting thin slices with d < 100 nm.
The thermal stability of pure PMMA and the PMMA/TiO2 nanocomposites was investigated by non-isothermal thermo-gravimetric analysis (TGA) using a Perkin-Elmer 6300 (PYRIS TM Diamond) instrument. The measurements were conducted at heating rates of 10 °C min−1 under flowing nitrogen at a constant flow rate 20 cm3 min−1 from 100 to 600 °C.
2.5. Photoreactor, light source and experimental procedure
The experimental setup for the photocatalytic degradation of organic pollutants, as exemplified by methylene blue, is shown in the ESI, Fig. S1.† A glass beaker (photoreactor) was used in the study, in which a 60 W fluorescence lamp as the light source was positioned at the top. The emission spectrum of the fluorescence lamp, taken using Avaspec 2048 TEC instrument is shown in Fig. 1. In photocatalytic assessments, the distance between the light and the reactor was fixed at 10 cm. In order to evaluate the applicability of the synthesized nanocomposite in the photodegradation of MB dye, reaction suspension was prepared by the addition of a desired weight of the PMMA/TiO2, to 15 ml aqueous solution of MB, with concentration of 4 × 10−5 M. The reaction was carried out isothermally at 25 °C. Prior to exposure to the light and commencing illumination, the MB solution with nanocomposite was magnetically stirred in dark conditions for 30 min to establish an adsorption–desorption equilibrium. Then, the solution was irradiated with constant stirring. The 5 ml of methylene blue of the reaction mixture was sampled for quantification by the use of a double beam UV-vis spectrophotometer (Perkin Elmer lambda 15) at different time intervals (every 30 min), for a total reaction time of 6 h. Next, the analyzed sample was taken back into the initial methylene blue solution for continuous testing.
 |
| Fig. 1 Emission spectrum of the light source using photocatalytic degradation setup. | |
3. Results and discussion
3.1. Characterization
3.1.1. UV-visible diffuse reflectance spectra. Fig. 2 shows the UV-vis diffuse reflectance full spectra of bare TiO2, pure PMMA and PMMA/TiO2 nanocomposites, which was prepared in the IL/O and W/O microemulsion systems. The optical absorbance of the TiO2 and the other samples, measured in the region of 200–800 nm. It is obvious that the bare TiO2 sample absorbs light with wavelengths below 400 nm. The band gap energies for all of the samples were obtained from Fig. 2 and are listed in Table 1. As can be seen, the absorbance of the PMMA/TiO2 sample fabricated in the IL/O microemulsion greatly shifted toward the red light, and its band gap was equaled to 2.55 eV, whereas the PMMA/TiO2 nanocomposite sample prepared in W/O microemulsion did not show visible light absorption. It is clear that the absorption edge was shifted to the visible region due to the presence of the IL molecules, which are used as a substitute for water to form a novel microemulsion system. The obtained results confirm that shifting the absorption edge are be related to the interaction of IL molecules and TiO2 nanoparticles.
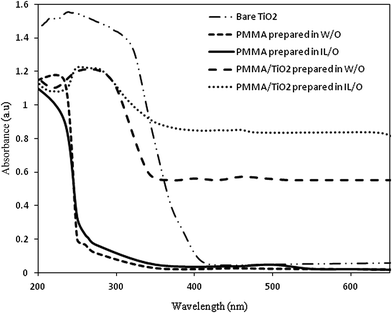 |
| Fig. 2 UV-vis diffuses reflectance spectra of the original TiO2 and other samples. | |
Table 1 The calculated band gap energy of different samples
Samples |
λcut-off (nm) |
Band gap energy (eV) |
Pure TiO2 |
388 |
3.20 |
Pure IL |
482 |
2.57 |
PMMA prepared in W/O |
245 |
5.06 |
PMMA prepared in IL/O |
275 |
4.50 |
PMMA/TiO2 prepared in W/O |
380 |
3.26 |
PMMA/TiO2 prepared in IL/O |
485 |
2.55 |
3.1.2. Surface chemistry bonds analysis by FTIR spectroscopy. FTIR spectroscopy was used to consider the nature of the polymer/inorganic nanocomposite. A broad absorption band, assigned to the hydroxyl groups of TiOH, is observed in the range of 3000–3500 cm−1 for pure TiO2, however, its absolute intensity is relatively low (Fig. 3a). In this figure the IR band at 400–850 cm−1 corresponds to the Ti–O–Ti stretching vibration mode in the TiO2 crystal.50,51 An ester carbonyl stretching vibration band and C–H stretching in C–CH3 for PMMA segments are observed around 1734 and 2953 cm−1, respectively (Fig. 3b).51,52,55 There is a little shift on 1734 cm−1, which is related to the carbonyl stretching vibration, when pure PMMA changed to a PMMA/TiO2 composite. This shifting may be related to the interaction between the carbonyl group and surface of TiO2. All characteristic peaks of the PMMA backbone are also found in the PMMA/TiO2 nanocomposite (Fig. 3c). The peak around 3160 cm−1 shows the stretching vibration of C–H bond in the imidazole ring. The appearance of BF4 anion bands could be observed at 1167, 1061 and 844 cm−1. As can be seen from Fig. 3d, no essential changes were observed after several experimental runs due to its good recyclability. The extra broad peak, which is observed around 3300 cm−1 may be due to the increase in the hydrophilicity (or increasing OH group) on the surface of TiO2 nanoparticles embedded in the PMMA matrix after 6 runs.
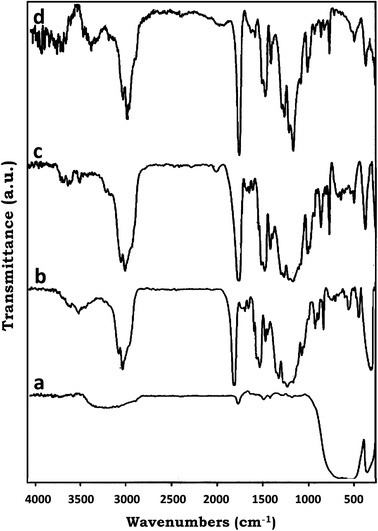 |
| Fig. 3 FTIR spectra of (a) bare TiO2, (b) PMMA, (c) PMMA/TiO2/IL (S3) and (d) PMMA/TiO2/IL (S3), after 6 times recycling. | |
3.1.3. TEM and FE-SEM micrographs. TEM is used to characterize the morphology and particle size of the prepared modified PMMA/TiO2/IL nanocomposite. Fig. 4 displays the TEM micrograph and its image analysis typically for sample S3 of PMMA/TiO2/IL nanocomposite. As can be seen the average particle size in the prepared nanocomposite, calculated by the image analyzer, is about 11 nm (Fig. 4). As shown in Fig. 4, the prepared nanocomposites exhibit a lucid core–shell decorated structure. The IL/TiO2 core–shell microspheres were obtained in the presence of IL as a core, correspond to brighter regions, and a ring of titania as shell which forms darker regions around the soft IL domains. This result indicates that TiO2 particles do not aggregate and show good monodispersity with uniform particle size. The obtained results show that the IL has a main role to disperse the TiO2 nanoparticles in the microemulsion system, which has been proven by the FTIR analysis. The role of the IL as a good dispersant can be explained as follows: on the one hand, the nanoparticles of TiO2, uniformly dispersed in the IL/MMA microemulsion, have a fine interaction with the IL molecules. On the other hand, the IL molecules have a good compatibility with MMA due to the existence of huge organic cations.
 |
| Fig. 4 TEM image of PMMA/TiO2/IL (S3). | |
The FE-SEM micrograph for pure PMMA and sample S3 of PMMA/TiO2/IL nanocomposite are shown in Fig. S2.† Very well-distributed nanoparticles having a spherical shape were observed.
3.1.4. Thermal gravimetric results. In order to study the effect of IL and TiO2 nanoparticles on thermal stability of the synthesized nanocomposites thermo-gravimetric analysis was performed from 100 to 600 °C. The TG curves obtained for the pure PMMA and PMMA//TiO2 nanocomposite samples, which were prepared using IL/O and W/O microemulsion systems at fixed TiO2 loading, in a nitrogen atmosphere are shown in Fig. 6. The obtain TG curves show a single-step degradation, which relates to the PMMA thermal decomposition by depolymerization. An interesting result is that the degradation temperature of the nanocomposite sample slightly moves to higher values in the presence of TiO2 nanoparticles. This result could be related to the interaction between the TiO2 and PMMA, which led to immobilization of free radical chains that they formed during the degradation and/or hindering of the diffusion of volatile decomposition products.52 The weight loss of the S3 nanocomposite sample is 85.49% at about 340–440 °C. As can be seen from Fig. 5, the onset temperature of the polymer decomposition for the PMMA/TiO2 nanocomposite prepared in IL/O microemulsion is shifted to a higher temperature, compared with that of the PMMA/TiO2 nanocomposite designed in the W/O microemulsion system. This phenomenon may be related to the network improvement of polymer chains with IL molecules and restrain the movement of free radicals, and consequently more thermal stability.53
 |
| Fig. 5 TGA of pure PMMA and PMMA/TiO2 nanocomposites obtained under nitrogen atmosphere and heating rate 10 °C min−1. Both of them were prepared in IL/O and W/O microemulsion systems. | |
3.1.5. X-ray diffraction (XRD). In order to clarify the nature and structural characteristics of the prepared nanocomposites, X-ray diffraction measurements were performed. Fig. S3 in the ESI† shows the XRD patterns for the following samples: the bare TiO2 powder, pure PMMA, and composites containing 0.006 wt%, 0.01 wt% and 0.012 wt% of TiO2. The XRD pattern of bare TiO2 (Fig. S3a†) confirms that it is crystallized in the anatase phase.52 The diffraction pattern of PMMA (Fig. S3b†) shows a broad diffraction peak at 2θ = 14°, which is typical for an amorphous material, together with two bands of lower intensities centered at 29.7° and 41.7°.52 In the XRD study for the low dosage of TiO2 in the nanocomposite (Fig. S3c and S3d†), it was difficult to resolve the TiO2 component in the nanocomposite, probably because of the low contrast and low dosing of TiO2 in the polymer matrix. The XRD spectrum for the sample with 0.012 wt% TiO2 (Fig. S3e†) shows two peaks related to TiO2 with low intensity at 2θ = 25° and 28°. These two peaks are shown as inset in Fig. S3.† The obtained results approve that the TiO2 nanoparticles maintained its structure in the nanocomposite and the orientation of the PMMA chains was not influenced during the nanocomposite preparation.
3.2. Photocatalytic results
The reduction of the maximum wavelength absorption intensity (λmax) at 664 nm was observed during the photocatalytic experiment. The reduction in the absorbance is probable due to the degradation of the MB chromophore, and the wavelength shift is due to N-demethylation concurrently with the degradation of the phenothiazine (see inset to Fig. 6). The mechanism of dye degradation by the modified TiO2 under visible light has been shown schematically in the ESI, Fig. S4.†
 |
| Fig. 6 (a) Spectral patterns of MB dye solution (b) decoloration of the MB dye solution during the photocatalytic degradation process in the presence of PMMA/TiO2/IL (S3) composite under visible-light irradiation for 6 h. | |
The present study demonstrate the modification of the TiO2 nanoparticles with the [bmim][BF4], which significantly improve photocatalytic activity under visible light illumination, same as some other research in the dye-sensitized TiO2 systems.36,50 In the combined system of an IL and a semiconductor because the lowest unoccupied molecular orbital (LUMO) level of the IL is energetically higher than the conduction band (CB) edge of TiO2, transferring of the electrons generated from the IL upon visible-light irradiation to the conduction band of TiO2, is thermodynamically feasible.
The following mechanism can be proposed for the mineralization of the MB by the IL-sensitized TiO2 photocatalysis in visible light. After the first step of the mechanism, which involves the excitation of the IL molecule by absorption of visible light (eqn (2-1)), the excited IL molecule (IL*) normally injects electrons into the conduction band (CB) of the TiO2 photocatalyst. Then, (IL*) is converted into its cationic radical (IL˙+) (eqn (2-2)). Next, these electrons aid in producing reactive species that leads to the degradation of the contaminant as summarized by eqn (2-3)–(2-10). However, for better understanding, advance intricate studies on the interaction of TiO2 particles with IL, and the exact mechanism of dye substrate degradation by TiO2 under visible light irradiation needs to be undertaken.
1. The excited IL molecule (IL*) on absorption of visible light irradiation;
2. Commonly injects electrons into the conduction band of TiO2 catalyst and itself is converted into its cationic radical (IL˙+);
|
IL* + TiO2 → IL˙+ + TiO2 (ecb−)
| (2-2) |
3. Oxygen adsorption leading to O2˙− free radicals;
|
(O2) ads + TiO2 (ecb−) → O2˙−
| (2-3) |
|
O2˙− + TiO2 (ecb−) + 2H+ → H2O2 + TiO2
| (2-4) |
|
2O2˙− + 2H+ → H2O2 + O2
| (2-5) |
4. Formation of OH˙ radical by TiO2 (ecb−);
|
H2O2 + TiO2 (ecb−) → OH˙ + OH− + TiO2
| (2-6) |
5. Formation of OH˙ radical by photo-holes;
|
(H2O ↔ H+ + OH−) ads + hvb+ → H+ + OH˙
| (2-7) |
6. Oxidation of organic contaminant (R) by O2˙− free radicals, OH˙ radical or holes
|
R + O2˙− → CO2 + H2O
| (2-8) |
|
R + OH˙ → CO2 + H2O
| (2-9) |
|
R + h+ → R˙+ → degradation products
| (2-10) |
As a result, interfacial charge transfer and separation between the IL and TiO2 takes place, and this could transport a considerable photo response to visible light. The shift in the emission position could be attributed to the charge transfer between the green IL generated band and the conduction band of TiO2 as a semiconductor. It is obvious that, not only IL reduces band gap energy of TiO2, but the using of IL was also able to avoid charge recombination between the (e−/h+) pairs, and accordingly the photocatalytic reactivity efficiency is enhanced.
As can be seen from Fig. S5 in the ESI† the absorption edge of ionic liquid is located at about 482 nm. The band gap energy of the ionic liquid was determined by the eqn (1) equal to 2.57 eV. It is interesting that the obtained band gap energy value is near the band gap energy of some pigments.50 Shang et al.50 have been preparing TiO2 sensitized with Benzimidazolone Yellow H3G and reported that the commercial pigment has band gap energy of 2.32 eV. The results confirm that the ionic liquid, same as pigments, is an efficient electron donor and good transporter upon visible light excitation. In order to understand the role of PMMA in this mechanism, DRS analysis was carried out for the PMMA/TiO2 nanocomposite, which was obtained with two different microemulsion systems, including IL/O and W/O. The absorption edges of both prepared nanocomposite films were determined by UV-vis DRS spectra and the band gaps were calculated from eqn (1). Obviously, in contrast to the PMMA/TiO2 nanocomposite obtained in the IL/O microemulsion, the PMMA/TiO2 nanocomposite prepared in the W/O microemulsion has no absorption above 400 nm. As a result, the ionic liquid molecule, same as a the dye molecule, acts as a sensitizer for TiO2, and PMMA has no effective role for sensitizing TiO2. The objective of the usage of PMMA is to gain a transparent and flexible matrix for the incorporation of small amount of TiO2 nanoparticles. For example Rizzo et al.54 investigated the removal of the MB dye in a photocatalytic reactor using a PMMA supported TiO2 film under UV radiation. Morselli et al.55 fabricated a PMMA/TiO2 nanocomposite by a non-hydrolytic sol–gel method and considered the degradation of the MB dye under UV irradiation.
The removal efficiency and decolorization of the MB dye were measured by applying the following equations:
|
 | (3) |
|
 | (4) |
where
C0 and
A0 are the initial concentration and absorbance of the MB dye at zero time, and
Ct and
At are the concentration and absorbance of the MB dye at
t time. The photodecolorization rate constant was calculated by plotting ln
C0/
C versus times based on the first order reaction according to
eqn (5).
|
 | (5) |
In this equation k represents the rate constant (min−1).
3.2.1. Effect of TiO2 dosage on photodecolorization of the MB dye. The photocatalytic behavior of bare TiO2 and all of the PMMA/TiO2 nanocomposites were determined by photodecolorization of the MB solution under visible irradiation and shown in Fig. 7. The experiment was carried out under the following conditions: 15 ml of aqueous solution of MB with concentration of 12 ppm and 0.009 g of nanocatalyst at pH = 7.2 (pH of the aqueous solution of MB). As can be seen from Fig. 7, the MB concentration decreased as a function of the irradiation time. The efficiency of photodecolorization slowly decreased and was fixed after 6 h. The results indicated that the PMMA/TiO2 nanocomposites provide a better decolorization performance than the pure TiO2. As expected, the bare TiO2 has no significant photocatalytic activity under visible light due to its large band gap (3.2 eV for anatase, which is in the UV region). The observed weak photocatalytic activity of bare TiO2 under visible light is related to the UV part of the applied lamp in the degradation experiment (Fig. 1). As can be seen from Fig. 7, with increasing TiO2 dosage, the degradation of MB first increases and with further loading the degradation reaction decreases. The photocatalytic activity for all samples was observed in the following order: self-photolysis ≈ PMMA < S1 < bare TiO2 < S2 < S3 > S4 > S5. This trend is in agreement with the results of the UV-visible analysis and the band gap values. The maximum photodecolorization efficiency was 92.2%, belonging to sample S3 of PMMA/TiO2 nanocomposite at pH = 7.2, after irradiating for 6 h. It is believed that loading TiO2 with more than the optimum value (S3), it can act as recombination centers of electrons and holes, and hence the photocatalytic activity decreases. As a result, the charge carriers can be trapped more than once on their way to the surface such that they recombine before they can reach the surface of the photocatalyst.42,50
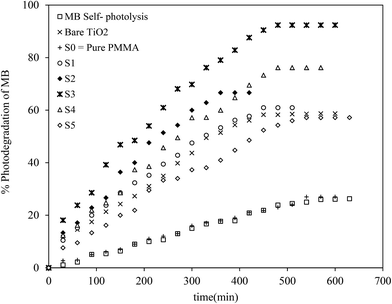 |
| Fig. 7 Effect of TiO2 dosages on the photodecolorization reaction of MB dye under visible irradiation. | |
The photodecolorization rate correlated well with the first order of the reaction model, using the R = k [MB] equation. The rate constant, k, was determined using eqn (5), for MB self-photolysis, PMMA, bare TiO2 and S1 to S5 samples, and reported in Table 2. The obtained rate constants were found to increase up to 0.005 min−1 for S3, and then decreased to 0.0015 min−1 for S5. The rate constant in the case of the S3 sample (k = 0.005 min−1) is 2.63 times greater than the bare TiO2 (0.0019 min−1). After 300 min of visible-light irradiation, no other spectral facial appearances are manifest in the absorption spectra, demonstrating that MB was degraded and completely mineralized via the nanocomposite photocatalyst.
Table 2 First order rate constants of MB photodegradation reaction over PMMA/TiO2/IL with various loading of TiO2, from a plot of ln
C0/Ct versus ta
Photocatalyst |
k × 10−3 (min−1) |
R2 |
Decolorization of MB afterb 2 h (%) |
Aphotoc |
The experiment was carried out under the following conditions: 15 ml of MB dye with a concentration of 12 ppm, 0.009 g photocatalyst and pH = 7.2. Aphoto defined as photocatalytic activity relative to bare TiO2 in terms of first-order rate constants: Aphoto = k/kTiO2. |
MB self-photolysis |
0.5 |
0.9927 |
5.40 |
0.26 |
S0 = PMMA |
0.5 |
0.9975 |
5.00 |
0.26 |
Bare TiO2 |
1.9 |
0.9908 |
21.35 |
1.00 |
S1 |
2.0 |
0.9938 |
23.80 |
1.05 |
S2 |
2.9 |
0.9926 |
26.66 |
1.52 |
S3 |
5.0 |
0.9828 |
39.21 |
2.63 |
S4 |
2.6 |
0.9911 |
24.76 |
1.36 |
S5 |
1.5 |
0.9921 |
16.19 |
0.78 |
As the reduction of the chemical oxygen demand (COD) reflects the extent of degradation, the change in COD concentration in the photodegradation of MB was investigated under visible light for 6 h. The initial COD of the MB solution was obtained at 183.5 mg L−1. After light irradiation for 6 h, the COD concentration decreased to 34.6 mg L−1 over the S3 nanocomposite sample. The reductions of COD further verify that the MB dye was successfully photodegraded by the nanocomposite.
3.2.2. Effect of the pH values on the photodegradation of MB dye. As an important variable in aqueous phase mediated photocatalytic reactions, the effect of pH on the MB degradation reaction was investigated by retaining all other conditions constant and varying the initial pH of the solution between 5 to 11. The results of the photodecolorization of MB for the S3 nanocomposite sample at different pH are shown in Fig. 8. The obtained results show that among these seven pH values, the most favorable pH value for the degradation of MB is around pH = 8. To reach the photocatalytical reaction, it is important to have reasonable interaction between MB and the catalysts. As can be seen from Fig. 8, at low pH, no significant variation was detected for the photodecolorization of MB dye. Adsorption of a dye on a photocatalyst depends on the zero point charge pH (pHzpc) and the ionic nature of the dye. As a result, in acidic solutions, the surface of the catalyst will be positively charged, and then the repulsive forces between the catalyst and the cationic dye will lead to decrease in dye adsorption on the catalyst, and hence the photocatalytic activity will be decreased. In the solutions with pH values more than pHzpc, the surface of the catalyst is negatively charged. Then, electrostatic attraction between the photocatalyst and the cationic dye favors the adsorption of the dye, and hence photocatalytic activity will be increased.56 The interesting result is that the photodecolorization efficiency of MB solution with pH, for this new type of nanocatalyst, is completely different. The photodecolorization efficiency first increased up to pH = 8, and then decreased with increasing pH values (Fig. 8). We believe that the negative charge on the surface of this type of photocatalyst (PMMA/TiO2/IL), is concentrated at pH = 8, and favors the adsorption of MB dye, and hence more photocatalytic activity will occur. To the best of our knowledge, Elfeky et al.57 have also studied the effect of pH on the decolorization of Trypan Blue (TB) as an anionic dye under sunlight by Au–TiO2 (0.08 g)/PMMA thin film nanocomposite, that was prepared via TiO2 suspended in PMMA, dissolved in tetrahydrofuran (THF). They observed that the degradation efficiency was 90% by an Au–TiO2 (0.08 g)/PMMA thin film after 1.75 h at pH = 2 and 87% in 2.5 h by TiO2 (0.08 g)-PMMA thin film, under similar conditions. The maximum photodegradation at pH = 2 was due to the strong interactions between the positive catalyst surface (TiOH2+) and dye anions that lead to strong adsorption of the TB anions on the titania surface.
 |
| Fig. 8 Photodecolorization of MB dye solution over the PMMA/TiO2/IL (S3) nanocomposite under visible irradiation, at different pH. | |
The calculated rate constant of MB degradation over PMMA/TiO2/IL (S3) with pH are reported in Table 3. The results confirm that the maximum efficiency can be reached with S3 nanocomposite sample at pH = 8.
Table 3 First order rate constants of MB photodecolorization reaction over PMMA/TiO2/IL (S3), from a plot of ln
C0/Ct versus t, at different pH valuesa
pH |
k × 10−3 (min−1) |
R2 |
Decolorization of MB afterb 2 h (%) |
The experiment was carried out under the following conditions: 15 ml of MB dye with concentration of 12 ppm, 0.009 g photocatalyst (S3).  |
5 |
1.6 |
0.9119 |
16.8 |
6 |
1.9 |
0.9753 |
17.6 |
7 |
4.4 |
0.9881 |
32.73 |
8 |
6.6 |
0.9043 |
58.20 |
9 |
5.3 |
0.9835 |
48.65 |
10 |
5.2 |
0.9887 |
45.45 |
11 |
3.6 |
0.9684 |
33.28 |
3.2.3. Recycling and photocatalyst stability of the nanocomposite. Catalyst recycling is a key step in assessing its practical application and developing heterogeneous photocatalysis technology for wastewater treatment. To evaluate the photocatalytic stability of the composite photocatalyst, PMMA/TiO2/IL (S3) was used for several photocatalytic runs, and each run lasted 180 min. The photocatalytic degradation efficiency was 88.83% during the first run. After the first run, the photocatalyst was separated and used immediately for further runs without any treatment. The catalyst activity slightly dropped in runs 2, 3, 4, 5 and 6, producing 86.54%, 83.78%, 80.95%, and 76.19% degradation, respectively. The results, which are shown in Fig. S5 in the ESI,† confirm that the composite photocatalyst is reusable and stable, that it can also maintain relatively high activity after several experimental runs. The deactivation of the photocatalyst is perhaps related to two reasons: surface poisoning and aggregation of nanoparticles.50,58–60
4. Conclusions
A new visible light-responsive PMMA/TiO2/IL photocatalyst was successfully fabricated by an ionic liquid based microemulsion system with special properties. The prime focus of the present research was introducing a new type of photosensitizer for TiO2 using an IL based microemulsion system. It is found that IL can extend the photo response of TiO2 to the visible region and improve the photocatalytic efficiency of TiO2 nanoparticles under visible light. In order to evaluate the photocatalytic activity of the prepared nanocomposite, the degradation of aqueous solution of MB under visible light was carried out. The synthesized PMMA/TiO2/IL nanocomposite with a certain loading of TiO2 (0.01 wt%) shows higher photocatalytic activity than bare TiO2 in MB degradation reaction under visible light. It is verified that pH of the MB solution has an important role in the decolorization reaction by the nanocomposite, and the maximum efficiency was obtained at pH = 8. The photodegradation of MB should be initiated by the (e−) injected from the excited states of IL molecules in to the conduction band of TiO2 under visible light, and then produce superoxide and hydroxyl radicals. These radicals are very active and can oxidize or reduce MB molecules, which was adsorbed on the nanocatalyst, to the mineral end-products. The photocatalytic process of the MB over the nanocomposite followed the first-order kinetics model. Moreover, the results of catalyst reusability evaluation revealed that the present photocatalyst remains effective and active after six cycles, which indicates the promising recyclability of PMMA/TiO2/IL photocatalyst.
Acknowledgements
The financial support from Arak University Research Council is gratefully acknowledged (grant no. 93/5251).
References
- C. Sanchez, G. J. D. A. Soler-Illia, F. Ribot, T. Lalot, C. R. Mayer and V. Cabuil, Chem. Mater., 2001, 13, 3061 CrossRef CAS.
- A. Salabat and H. Saydi, Poly. Compos., 2014, 35, 2032 Search PubMed.
- K. Zhang, H. T. Chen, X. Chen, Z. M. Chen, Z. C. Cui and B. Yang, Macromol. Mater. Eng., 2003, 288, 380 CrossRef CAS.
- D. Gutierrez-Tauste, X. Domenech, N. Casan-Pastor and J. A. Ayllon, J. Photochem. Photobiol., A, 2007, 187, 45 CrossRef CAS PubMed.
- V. Bansal, D. Rautaray, A. Bharde, K. Ahire, A. Sanyal, A. Ahmad and M. Sastry, J. Mater. Chem., 2005, 15, 2583 RSC.
- H. Lachheb, E. Puzenat, A. Houas, M. Ksibi, E. Elaloui, C. Guillard and J. M. Herrmann, Appl. Catal., B, 2002, 39, 75 CrossRef CAS.
- F. Caruso, Adv. Mater., 2001, 13, 11 CrossRef CAS.
- I. Y. Jeon and J. B. Baek, Materials, 2010, 3, 3654 CrossRef CAS PubMed.
- H. Tai, Y. Jiangy, G. Xie and J. Yu, J. Mater. Sci. Technol., 2010, 26, 605 CAS.
- A. Pearson, S. K. Bhargava and V. Bansal, Langmuir, 2011, 27, 9245 CrossRef CAS PubMed.
- A. Akleah, N. El-Deen, A. Hiltner, E. Baer and A. Moet, Mater. Lett., 1995, 22, 97 CrossRef.
- S. H. Jang, M. G. Han and S. S. Im, Synth. Met., 2000, 110, 17 CrossRef CAS.
- J. Pyun and K. Matyjaszewski, Chem. Mater., 2001, 13, 3436 CrossRef CAS.
- H. Zou and S. P. Armes, Polym. Chem., 2012, 3, 172 RSC.
- E. Bourgeat-Lami and J. Lang, J. Colloid Interfaces Sci., 1999, 210, 281 CrossRef CAS PubMed.
- Y. H. Yang and Y. Dan, Colloid Polym. Sci., 2003, 281, 794 CAS.
- L. Jiang and Y. Dan, Colloid Polym. Sci., 2004, 282, 1374 CAS.
- H. H. Zhou, X. H. Ning, S. L. Li, J. H. Chen and Y. F. Kuang, Thin Solid Films, 2006, 510, 164 CrossRef CAS PubMed.
- K. Landfester, N. Bechthold, F. Tiarks and M. Antonietti, Macromolecules, 1999, 32, 2679 CrossRef CAS.
- B. K. Paul and S. P. Moulik, J. Dispersion Sci. Technol., 1997, 18, 301 CrossRef CAS.
- H. Gao, J. Li, B. Han, W. Chen, J. Zhang, R. Zhang and D. Yan, Phys. Chem. Chem. Phys., 2004, 6, 2914 RSC.
- Z. H. Li, J. L. Zhang, J. M. Du, B. X. Han and J. Q. Wang, Colloids Surf., A, 2006, 286, 117 CrossRef CAS PubMed.
- K. J. Baranyai, G. B. Deacon, D. R. MacFarlane, J. M. Pringle and J. L. Scott, Aust. J. Chem., 2004, 57, 145 CrossRef CAS.
- P. Migowski and J. Dupont, Chem.–Eur. J., 2007, 13, 32 CrossRef CAS PubMed.
- H. Olivier-Bourbigou, L. Magna and D. Morvan, Appl. Catal., A, 2010, 373, 1 CrossRef CAS PubMed.
- H. M. Chen, C. H. Deng and X. M. Zhang, Angew. Chem., Int. Ed., 2010, 49, 607 CrossRef CAS PubMed.
- V. V. Vodnik, D. K. Bozanic, E. Dzunuzovic, J. Vukovic and J. M. Nedeljkovic, Eur. Polym. J., 2010, 46, 137 CrossRef CAS PubMed.
- F. D. Amore, M. Lanata, S. M. Pietralunga, M. C. Gallazzi and G. Zerbi, Opt. Mater., 2004, 24, 661 CrossRef.
- C. M. Teh and A. R. Mohamed, J. Alloys Compd., 2011, 509, 1648 CrossRef CAS PubMed.
- K. Rajeshwar, M. E. Osugi, W. Chanmanee, C. R. Chenthamarakshan, M. V. B. Zanoni, P. Kajitvichyanukul and R. Krishnan-Ayer, J. Photochem. Photobiol., C, 2008, 9, 171 CrossRef CAS PubMed.
- S. E. Stanca, R. Müller, M. Urban, A. Csaki, F. Froehlich, C. Krafft, J. Popp and W. Fritzsche, Catal. Sci. Technol., 2012, 2, 1472 CAS.
- A. Fujishim a, T. N. Rao and D. A. Tryk, J. Photochem. Photobiol., C, 2000, 1, 1 CrossRef CAS.
- D. Chatterjee and S. Dasgupta, J. Photochem. Photobiol., C, 2005, 6, 186 CrossRef CAS PubMed.
- R. Vinu and G. Madras, J. Indian Inst. Sci., 2010, 90, 189 CAS.
- J. Chang, Vacuum, 2005, 4, 1 Search PubMed.
- S. Singh, H. Mahalingam and P. Kumar Sing, Appl. Catal., A, 2013, 462–463, 178 CrossRef CAS PubMed.
- L. Xiong, R. M. Wang, H. B. Liang, Y. Pang and J. Guan, J. Macromol. Sci., Part A: Pure Appl. Chem., 2010, 47, 903 CrossRef CAS.
- C. H. Ye, K. Li, H. Li, X. Lai, H. Xie and X. Zeng, J. Macromol. Sci., Part A: Pure Appl. Chem., 2013, 50, 836 CrossRef CAS.
- W. Nam, J. Kim and G. Han, Chemosphere, 2002, 47, 1019 CrossRef CAS.
- A. Houas, H. Lachheb, M. Ksibi, E. Elaloui, C. Guillard and J. M. Herrmann, Appl. Catal., B, 2007, 31, 145 CrossRef.
- G. Marbán, T. T. Vu and T. Valdés-Solís, Appl. Catal., A, 2011, 402, 218 CrossRef PubMed.
- M. Pelaez, N. T. Nolan, S. C. Pillai, M. K. Seery, P. Falaras, A. G. Kontos, P. S. M. Dunlop, J. W. J. Hamilton, J. A. Byrne, K. O'Shea, M. H. Entezari and D. D. Dionysiou, Appl. Catal., B, 2012, 125, 331 CrossRef CAS PubMed.
- S. M. Gupta and M. Tripathi, Chin. Sci. Bull., 2011, 56, 1639 CrossRef CAS.
- M. Y. Abdelaal and R. M. Mohamed, J. Alloys Compd., 2013, 576, 201 CrossRef CAS PubMed.
- A. Iwaszuk and M. Nolan, Catal. Sci. Technol., 2013, 3, 2000 CAS.
- F. Han, V. Subba, R. Kambala, M. Srinivasan, D. H. Rajarathnam and R. Naidu, Appl. Catal., A, 2009, 359, 25 CrossRef CAS PubMed.
- A. Pron and P. Rannou, Prog. Polym. Sci., 2002, 27, 135 CrossRef CAS.
- F. Wang, S. H. Min, Y. Han and L. Feng, Superlattices Microstruct., 2010, 48, 170 CrossRef CAS PubMed.
- C. Lettmann, K. Hildenbrad, H. Kisch, W. Macyk and W. F. Maier, Appl. Catal., B, 2001, 32, 215 CrossRef CAS.
- X. Shang, B. Li, C. Li, X. Wang, T. Zhang and S. Jiang, Dyes Pigm., 2013, 98, 358 CrossRef CAS PubMed.
- M. Yang, Z. Di and J.-K. Lee, J. Colloid Interface Sci., 2012, 368, 603 CrossRef CAS PubMed.
- T. E. Motaung, A. S. Luyt, F. Bondioli, M. Messori, M. L. Saladino, A. Spinella, G. Nasillo and E. Caponetti, Polym. Degrad. Stab., 2012, 97, 1325 CrossRef CAS PubMed.
- A. Laachachi, M. Ferriol, M. Cochez and J. M. Lopez-Cuesta, Polym. Degrad. Stab., 2008, 93, 1131 CrossRef CAS PubMed.
- L. Rizzo, J. Koch, V. Belgiorno and M. A. Anderson, Desalination, 2007, 211, 1 CrossRef CAS PubMed.
- D. Morselli, M. Messori and F. Bondioli, J. Mater. Sci., 2011, 46, 6609 CrossRef CAS PubMed.
- A. Houas, H. Lachheb, M. Ksibi, E. Elaloui, C. H. Guillard and J. M. Herrmann, Appl. Catal., B, 2001, 31, 145 CrossRef CAS.
- S. A. Elfeky and A. A. Al-Sherbini, Kinet. Catal., 2011, 52, 391 CrossRef CAS.
- L. X. Zhang, P. Liu and Z. X. Su, Polym. Degrad. Stab., 2006, 91, 2213 CrossRef CAS PubMed.
- S. T. Kochuveedu, Y. H. Jang and D. H. Kim, Chem. Soc. Rev., 2013, 42, 8467 RSC.
- J. Zhang, Y. Zhang, Y. Lei and C. Pan, Catal. Sci. Technol., 2011, 1, 273 CAS.
Footnote |
† Electronic supplementary information (ESI) available. See DOI: 10.1039/c4ra14612c |
|
This journal is © The Royal Society of Chemistry 2015 |
Click here to see how this site uses Cookies. View our privacy policy here.