DOI:
10.1039/C4RA14111C
(Paper)
RSC Adv., 2015,
5, 14277-14284
Zn-based ionic liquids as highly efficient catalysts for chemical fixation of carbon dioxide to epoxides†
Received
8th November 2014
, Accepted 6th January 2015
First published on 12th January 2015
Abstract
The novel Zn-based task-specific ionic liquids (Zn-TSILs) catalysts were developed for the coupling of carbon dioxide and epoxides to form cyclic carbonates under mild reaction conditions without using additional organic solvents and cocatalysts. Due to the synergistic effects of the cation and anion in this catalytic system, excellent yields and selectivities to cyclic carbonates were achieved with high TOF values up to 794 h−1. Among the catalysts investigated, OH-containing Zn-TSILs showed better activity than COOH-containing Zn-TSILs, and [(CH2CH2OH)Bim]ZnBr3 was found to be the best. Additionally, the influences of CO2 pressure and catalyst concentration were also investigated over [(CH2CH2OH)Bim]ZnBr3. In addition, the rate constants as well as the activation energies for the cycloaddition reaction catalyzed by Zn-TSIL and TSIL were comparatively determined. The activation energy was calculated to be 34.1 kJ mol−1 for bare TSIL catalyst, whereas the Zn-TSIL reduced the activation energy value by 14.7 kJ mol−1. Moreover, the Zn-TSIL was easily recyclable without significant loss of activity, representing the exceptionally promising candidate for the effective fixation of CO2 to epoxides.
1. Introduction
Carbon dioxide is has been in the spotlight as a renewable C1 feedstock because it is ubiquitous and readily available, either from decomposition of organic matter or artificial production by human activities. Conversion of CO2 into industrially useful chemicals has dual significance in view of both environmental protection and sustainable chemistry.1 One of the most promising strategies in this area is the synthesis of cyclic carbonates via the cycloaddition of epoxides and CO2 (Scheme 1), especially the synthesis of propylene carbonate (PC) and ethylene carbonate (EC). The formation of cyclic carbonates is green for 100% atom efficiency and cyclic carbonates have found applications not only as polar aprotic solvents, electrolytes for lithium-ion batteries, and as intermediates in the manufacture of fine chemicals,2–4 but are also used as constituents of oils and paints and as raw materials in the synthesis of polycarbonates5,6 and polyurethanes7,8 as shown in Scheme 2.
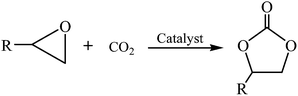 |
| Scheme 1 Cycloaddition reaction of CO2 with epoxides. | |
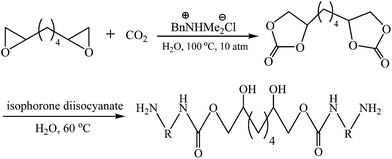 |
| Scheme 2 Synthesis of polyurethanes via cyclic carbonates.7 | |
Because carbon dioxide contains carbon in its most oxidized state, it has inherent thermodynamic stability and kinetic inertness.9 Therefore, catalysts are needed to reduce the activation energy of any reaction in which CO2 is involved. Accordingly, a wide range of catalysts have been explored for the synthesis of cyclic carbonates, including metal oxides,10,11 alkali metal salts,12,13 quaternary ammonium salts,14 phosphonium salts,15 Schiff bases16–18 and transition metal complexes.19 However, in many cases, additives and/or cocatalysts as well as organic solvents are needed. In addition, unsatisfactory activity, harsh reaction conditions and inexhaustive separation of products from the catalysts are still drawbacks that need to be overcome. Hence, the design of a novel, solvent/cocatalyst-free catalyst with enhanced activity still remains to be developed toward effective conversion of CO2.20
More recently, ionic liquids (ILs) have attracted considerable interest and CO2 cycloaddition to epoxides has been effectively carried out in ILs, which possess unique characteristics, such as thermal and chemical stability, negligible vapor pressure, selective solubility towards organic and inorganic materials, and high reusability of the catalysts.21 In 2001, Peng and Deng22 first reported the quantitative conversion of propylene oxide (PO) to PC catalyzed by 1-butyl-3-methylimidazolium (BmimBF4) ionic liquid. Thereafter, series of imidazolium salts,23–25 quaternary ammonium salts,26 quaternary phosphonium salts,27 pyridinium salts,28 guanidinium salts,29 polymeric30,31 and other immobilized ILs32,33 were developed as catalysts for the cycloaddition of CO2 into epoxides. Among these, Kim's group found that imidazolium zinc tetrahalides showed surprisingly high activities for the coupling reaction of CO2 and ethylene oxide or propylene oxide to produce corresponding cyclic carbonates and the highest TOF were up to 3545 h−1 for 1-butyl-3-methylimidazolium bromide-ZnBr2 at 100 °C and 3.5 MPa.34 Sun35 and Zhou et al.36 have reported that hydroxyl-functionalized (HFILs)/carboxyl-functionalized ionic liquids (CFILs) could coordinate with the oxygen atom of epoxides and thus lead to the activation of the epoxide. Furthermore, a theoretical study also indicated that the formation of hydrogen bonds between catalyst and epoxide could accelerate the ring-opening reaction of the epoxide, enhancing the activity significantly.37 However, the catalytic activity was unsatisfactory and needed further improvement. Previous literature also reported that zinc halides could coordinate with the oxygen atom to activate the epoxide by forming the zinc-epoxide adduct.15,38,39 Herein, we designed novel Zn-based task-specific ionic liquids composed of ZnBr2 and hydroxyl/or carboxyl group-functionalized ILs, which are expected to be excellent catalysts for the CO2 cycloaddition reaction. The Zn-based task-specific ionic liquids (Zn-TSILs) were facilely obtained from the reaction of ZnBr2 with HFILs/or CFILs. The catalytic activities were examined for CO2 coupling with PO as well as other epoxides, especially the less active epoxides, such as styrene oxide and cyclohexene oxide. Systematic investigations on the effects of CO2 pressure and catalyst concentration on the target reaction were also conducted. Additionally, the contrast calculations for the activation energies were provided over HFIL and Zn-HFIL catalysts. A plausible reaction mechanism was proposed based on the experimental results.
2. Experimental
2.1. General information
Carbon dioxide with purity of 99.99% was purchased from Harbin Qinghua Industrial gases Co. Ltd. PO, sodium hydride (60%), imidazole (99%), N-methylimidazole (99%), n-butyl bromide (≥99%), 2-bromoethanol (96%), bromoacetic acid (98%), tetrahydrofuran (extra dry, >99%) were purchased from Aladdin Chemical Co. ZnBr2 (CP) was purchased from Adamas Reagent Co. Ltd. All other chemicals were purchased from Beijing InnoChem Science & Technology Co. Ltd. and were of analytical grade and used without further purification.
FT-IR spectra were measured on a Perkin-Elmer Spectrum 100 FT-IR Spectrometer. 1HNMR spectra were detected on a Bruker 400 spectrometer in D2O (4.79 ppm) at ambient temperature. GC analyses were performed on an Agilent GC-7890A equipped with a capillary column (Agilent 19091J-413), using a flame ionization detector.
2.2. Synthesis of Zn-based task-specific ionic liquids
Four ILs composed of ZnBr3− anions and different cations were prepared according to Scheme 3. The detailed synthesis procedures are described in ESI† and characterization results are as follows.
 |
| Scheme 3 Synthesis process for Zn-based task-specific ionic liquids. | |
[(CH2CH2OH)Mim]ZnBr3: yield: 97%; 1H NMR (400 MHz, D2O): δ = 8.78 (s, 1H), 7.54 (m, 1H), 7.48 (m, 1H), 4.51–4.21 (m, 2H), 3.99–3.94 (m, 2H), 3.93 (s, 3H). FT-IR: 3497, 3152, 2955, 1619, 1567, 1384, 1165, 1061, 826, 748, 643 cm−1.
[(CH2COOH)Mim]ZnBr3: yield: 93%; 1H NMR (400 MHz, D2O): δ = 8.66 (s, 1H), 7.43–7.22 (m, 2H), 4.66 (s, 2H), 3.87 (s, 3H). FT-IR: 3400, 3134, 2617, 1747, 1593, 1171, 1082, 974, 834, 749, 623 cm−1.
[(CH2CH2OH)Bim]ZnBr3: yield: 95%; 1H NMR (400 MHz, D2O): δ = 8.78 (s, 1H), 7.70–7.11 (m, 2H), 4.35–4.25 (m, 2H), 4.18 (t, J = 7.2 Hz, 2H), 3.95–3.84 (m, 2H), 1.92–1.71 (m, 2H), 1.37–1.19 (m, 2H), 0.87 (t, J = 7.4 Hz, 3H). FT-IR: 3449, 3142, 2959, 2871, 1937, 1614, 1562, 1458, 1161, 1057, 947, 832, 749 cm−1.
[(CH2COOH)Bim]ZnBr3: yield: 90%; 1H NMR (400 MHz, D2O): δ = 8.75 (s, 1H), 7.54–7.33 (m, 2H), 4.71 (s, 2H), 4.16 (t, J = 7.3 Hz, 2H), 1.93–1.71 (m, 2H), 1.35–1.13 (m, 2H), 0.84 (t, J = 7.4 Hz, 3H). FT-IR: 3432, 2959, 2285, 1746, 1616, 1572, 1168, 1081, 838, 751, 621 cm−1.
2.3. General procedure for PC synthesis from PO and CO2
The cycloaddition reaction of PO and CO2 was conducted in a 50 mL high pressure stainless-steel reactor equipped with a magnetic stirring bar. In a typical run, the reactor was purged with CO2 to evacuate air, and then Zn-TSIL catalyst (0.035 mmol, 0.12 mol% of PO) and PO (34.5 mmol) were added successively, then the reactor was heated using an oil bath. At a fixed reaction temperature such as 120 °C, CO2 was introduced into the reactor and the pressure was adjusted to 2.0 MPa. The autoclave was heated at that temperature for a designated period of time. After the reaction was completed, the reactor was cooled to 0 °C in an ice-water bath, and the remaining CO2 was released. The product was extracted with ethyl acetate and analyzed by GC and Zn-TSILs were separated by centrifugation, washed with ethyl acetate (3 × 5 mL), dried under vacuum and then reused directly for the next run.
3. Results and discussion
3.1. Catalyst screening for the cycloaddition of CO2 to PO
The activities of different catalysts were tested on the reaction of PO and CO2, and the corresponding results are summarized in Table 1. Almost no reaction occurred in the absence of any catalyst or in the presence of only ZnBr2 catalyst (entries 1 and 2). Although the hydroxyl-functionalized (HFILs) and carboxyl-functionalized ionic liquids (CFILs) showed higher catalytic activity (entries 7–10) compared with non-functionalized ionic liquids, such as [Emim]Br (1-ethyl-3-methylimidazolium bromide) and [Bmim]Br (1-butyl-3-methylimidazolium bromide) (entries 3 and 4), the activities were still unsatisfactory. Almost no reactivity was observed in the presence of BrCH2CH2OH or BrCH2COOH (entries 5 and 6). However, the Zn-based task-specific ionic liquids realized the obvious enhancements in catalytic activity in comparison with the former non Zn-based ILs, indicating the necessary cooperative effects between Zn and IL, which stabilized intermediates through hydrogen bonds and Zn–O bonds for accelerating the reaction (entries 11–14). Notably, the [(CH2CH2OH)Bim]ZnBr3 catalyst showed the best activity and PO conversion approached 93% with 92% PC yield under cocatalyst and solvent free conditions of 120 °C and 2.0 MPa CO2 for 1.0 h (entry 13), and the high turnover frequency (TOF) value was up to 794 h−1. The catalytic activity decreased in the order of [(CH2CH2OH)Bim]ZnBr3 > [(CH2CH2OH)Mim]ZnBr3 > [(CH2COOH)Bim]ZnBr3 > [(CH2COOH)Mim]ZnBr3. As hydrogen-bond donors, the –OH and –COOH played the same roles of interacting with epoxides to polarize the C–O ring bond and facilitate the nucleophilic attack by the halide anion for subsequent ring opening. The OH-containing Zn-TSILs showed better activities than the COOH-containing Zn-TSILs (entries 11 and 13 vs. entries 12 and 14), which were accordant with the effects of HFILs and CFILs (entries 7 and 9 vs. entries 8 and 10). The different activities presumably were attributed to the carbonyl oxygen in COOH-containing Zn-TSILs forming intramolecular hydrogen bonds, thus competing with the hydrogen bonds formed between Zn-TSILs and PO, thereby lowering the product yield.24 Besides, it was detected that a slight increase in PC yield resulted from increasing the alkyl chain length of the imidazolium cation with the same functional groups, due to the higher solubility of CO2 and PO in the IL phase.23 Compared with the imidazolium zinc tetrahalides catalyst reported by Kim et al.,34 the same reaction temperature of 100 °C was used and the PC yield reached 86% with TOF of 742 h−1 under a lower reaction pressure of 2.0 MPa (entry 15) for 1.0 h, proving that [(CH2CH2OH)Bim]ZnBr3 possessed excellent catalytic performance.
Table 1 Effect of various catalysts on the cycloaddition reaction of PO and CO2a
Entry |
Catalyst |
Conversionb (%) |
Yieldb (%) |
TOFc (h−1) |
Reaction conditions: 34.5 mmol PO, 0.04 mmol Cat., T = 120 °C, P (CO2) = 2.0 MPa, t = 1.0 h. Based on GC analysis. Moles of PC produced per mole of catalyst per hour. T = 100 °C. The fourth run. The fifth run, t = 1.5 h. |
1 |
None |
Trace |
Trace |
— |
2 |
ZnBr2 |
Trace |
Trace |
— |
3 |
[Emim]Br |
33 |
32 |
276 |
4 |
[Bmim]Br |
35 |
35 |
302 |
5 |
BrCH2CH2OH |
Trace |
Trace |
— |
6 |
BrCH2COOH |
Trace |
Trace |
— |
7 |
[(CH2CH2OH)Mim]Br |
54 |
53 |
457 |
8 |
[(CH2COOH)Mim]Br |
49 |
48 |
414 |
9 |
[(CH2CH2OH)Bim]Br |
55 |
54 |
466 |
10 |
[(CH2COOH)Bim]Br |
53 |
51 |
440 |
11 |
[(CH2CH2OH)Mim]ZnBr3 |
90 |
89 |
768 |
12 |
[(CH2COOH)Mim]ZnBr3 |
83 |
81 |
699 |
13 |
[(CH2CH2OH)Bim]ZnBr3 |
93 |
92 |
794 |
14 |
[(CH2COOH)Bim]ZnBr3 |
85 |
83 |
716 |
15d |
[(CH2CH2OH)Bim]ZnBr3 |
86 |
86 |
742 |
16e |
[(CH2CH2OH)Bim]ZnBr3 |
91 |
90 |
776 |
17f |
[(CH2CH2OH)Bim]ZnBr3 |
92 |
91 |
523 |
For a potential application in a green and economic process, the recyclability of the catalyst plays an important role. Fig. S1 in ESI† displays the recyclability of [(CH2CH2OH)Bim]ZnBr3 at 120 °C and 2.0 MPa CO2 pressure. No significant decrease in PC yields was observed after four cycles (entry 16), and in the 5th reuse, the catalyst still exhibited high PO conversion and PC yield with reaction time of 1.5 h (entry 17). Further reuse of the spent catalyst could still achieve a high PO conversion and PC yield, but at the expense of a little longer reaction time because of the washing loss of the IL catalyst, demonstrating a very feasible and reusable catalyst for the CO2 cycloaddition reaction.
3.2. Effects of reaction parameters
The influence of CO2 pressure on the PC yield was investigated at 120 °C for 1.0 h with [(CH2CH2OH)Bim]ZnBr3 catalyst. As shown in Fig. 1, the reaction pressure had a significant effect on PC yield. With the increase of CO2 pressure from 0.5–1.5 MPa, the PC yield increased rapidly. In the range of 1.5–2.5 MPa, there was a moderate increase in yield and in the range of 2.5–3.0 MPa, the PC yield was almost constant, but decreased initially when the CO2 pressure was above 3.0 MPa. To our delight, there were no obvious changes in PC selectivity. A similar influence of CO2 pressure on catalytic activity was observed in other catalytic systems in the literature.15,40,41 The reason for this could be ascribed to the phase behavior of the CO2–PO system. There appeared two phases; a CO2-rich gas phase and a PO-rich liquid phase in the system under experimental conditions, and the reaction mainly took place in the liquid phase, which dispersed the catalyst. The concentration of CO2 in the liquid phase rose remarkably with increasing pressure when the reaction was carried out in the low-pressure region, thus significantly promoting the reaction. However, too high a CO2 pressure would decrease PC yield because of the lower concentration of PO in the liquid phase because more PO was extracted into the vapor phase. Therefore, 2.5 MPa was chosen as the most suitable pressure for PC synthesis.
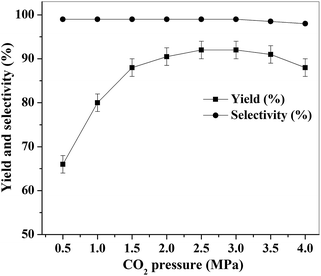 |
| Fig. 1 Effect of CO2 pressure on the synthesis of PC. Conditions: 34.5 mmol PO, 0.04 mmol [(CH2CH2OH)Bim]ZnBr3, T = 120 °C, t = 1.0 h. | |
Additionally, the effects of the catalyst concentration on the reaction were investigated with the molar percentage of [(CH2CH2OH)Bim]ZnBr3 to PO in the range 0.05–0.30 mol% (Fig. 2). It is worth mentioning that only 0.05 mol% of catalyst showed good catalytic performance at 85% PC yield. The PC yield increased smoothly from 85% to around 98% with catalyst concentration increasing from 0.05 to 0.25 mol%, and no obvious changes in PC selectivities. Further increase in the catalyst concentration caused a slight decrease in PC yield, presumably due to side reactions such as isomerization of PO as shown in Scheme 4. As a consequence, 0.25 mol% was chosen as the most suitable catalyst concentration.
 |
| Fig. 2 Dependence of catalyst concentration on the synthesis of PC. Conditions: 34.5 mmol PO, T = 120 °C, P (CO2) = 2.5 MPa, t = 1.0 h. | |
 |
| Scheme 4 Possible side reactions of PO. | |
3.3. The activation energy and kinetic equation for PC synthesis
In order to illustrate the unique features of ZnBr2, the synthesis of PC using the respective [(CH2CH2OH)Bim]Br and [(CH2CH2OH)Bim]ZnBr3 catalysts was undertaken as a function of temperature and the contrast calculations of the activation energies were provided. The kinetic parameters were studied over a temperature range from 90 to 130 °C and the rate laws for this process were fitted to eqn (1).20,42,43 |
Rate = k[epoxide]a[CO2]b[Cat]c
| (1) |
where k represents the rate constant; [epoxide], [CO2], [Cat] represents propylene oxide, carbon dioxide and catalyst concentration, respectively; a, b, c is the reaction order of corresponding substrates.
As the reaction was carried out in a constant volume reactor, CO2 was present in large excess, and the concentrations of CO2 and catalyst would be effectively constant during the reaction, then eqn (1) could be simplified to eqn (2):
|
Rate = kobs[epoxide]a, where kobs = k[CO2]b[Cat]c
| (2) |
The reaction was assumed to follow first-order kinetics and the observed pseudo-first-order rate constant (kobs) could be calculated from eqn (3):
|
 | (3) |
Integrating eqn (3) as a function of time yielded eqn (4)
where
t is time and
kobs is the observed pseudo-first-order rate constant for PO conversion.
After CO2 was introduced into the reaction system containing [(CH2CH2OH)Bim]Br or [(CH2CH2OH)Bim]ZnBr3 catalyst at different temperatures, the PO concentrations decreased with reaction time as shown in Fig. S2 and S3.† The kobs could be determined from the slope of the natural logarithm of remaining PO concentration versus time at different temperatures based on eqn (4). The plots were linear as shown in Fig. S4.† The kinetic equations, correlation coefficient R and observed pseudo-first-order rate constant (kobs) are listed in Table S1.†
According to the Arrhenius equation, the activation energies with respect to the CO2 cycloaddition to PO catalyzed by [(CH2CH2OH)Bim]Br and [(CH2CH2OH)Bim]ZnBr3 could be calculated as shown in Fig. 3. The derived data are summarized in Table 2.
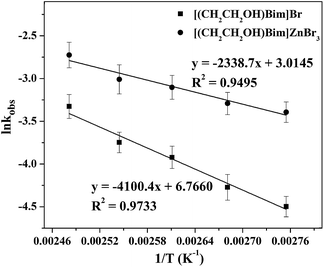 |
| Fig. 3 Arrhenius plots for the CO2 cycloaddition to PO catalyzed by [(CH2CH2OH)Bim]Br (■) and [(CH2CH2OH)Bim]ZnBr3 (●). Conditions: 34.5 mmol PO, 0.25 mol% Cat., P (CO2) = 2.5 MPa. The average and standard deviation of ln kobs were obtained from the experiments at each temperature. | |
Table 2 Kinetic parameters of CO2 cycloaddition to PO over different catalystsa
Catalyst |
Kinetic parameters |
Ea (kJ mol−1) |
A (min−1) |
R2 |
The values of kinetic parameters obtained from the linear Arrhenius plot of ln kobs against 1/T. |
[(CH2CH2OH)Bim]Br |
34.1 |
867.8 |
0.9733 |
[(CH2CH2OH)Bim]ZnBr3 |
19.4 |
20.4 |
0.9495 |
The activation energies were 34.1 kJ mol−1 and 19.4 kJ mol−1 for [(CH2CH2OH)Bim]Br and [(CH2CH2OH)Bim]ZnBr3, respectively, indicating that ZnBr2 played the main role in reducing the activation energy. This was specifically attributable to the synergistic effects of the zinc halides, which acted as Lewis acids to form the zinc-epoxide adduct, cooperating with hydroxyl groups and bromide anions to facilitate the ring-opening reaction of PO, which was the rate-limiting step of CO2 cycloaddition to PO.
3.4. Catalytic activity towards CO2 cycloaddition to other epoxides
In order to show the potential and general applicability of the novel Zn-TSILs catalysts, the coupling reactions of CO2 with various epoxides were carried out over [(CH2CH2OH)Bim]ZnBr3 in Table 3. [(CH2CH2OH)Bim]ZnBr3 was an efficient catalyst for the conversions of a variety of substrates to the corresponding cyclic carbonates with high yields and selectivities. It is worth mentioning that although the catalytic reaction was impeded by the increase in the steric hindrance from the side chains of the substrates, the activities of styrene oxide and cyclohexene oxide were still excellent under longer reaction times at 120 °C and 2.5 MPa CO2 pressure (entries 4 and 6). Especially for cyclohexene oxide, a much longer reaction time was needed to complete the conversion due to the higher steric hindrance originating from the two rings, which obstructed the nucleophilic attack by Br−, causing a decreased ring-opening rate.27,44 Hence, the extension to various epoxides reflected the outstanding efficiency of the Zn-TSILs catalysts.
Table 3 Coupling reaction of CO2 with various epoxides catalyzed by [(CH2CH2OH)Bim]ZnBr3a
Entry |
Epoxide |
Product |
T (°C) |
t (h) |
Reaction resultsb |
YPC (%) |
SPC (%) |
Reaction conditions: 34.5 mmol epoxide, 0.25 mol% Cat., P (CO2) = 2.5 MPa. YPC: PC yield; SPC: PC selectivity; all based on GC analysis. |
1 |
 |
 |
90 |
4.0 |
96 |
≥99 |
2 |
 |
 |
120 |
2.0 |
99 |
≥99 |
3 |
 |
 |
120 |
2.0 |
97 |
≥99 |
4 |
 |
 |
120 |
4.0 |
94 |
≥98 |
5 |
 |
 |
120 |
12.0 |
68 |
≥99 |
6 |
 |
 |
120 |
16.0 |
85 |
≥98 |
3.5. Plausible reaction mechanism
In order to gain a deeper insight into the reaction mechanism, FT-IR spectra were employed to identify the possible intermediate under CO2 pressure during the reaction. As shown in Fig. 4, after the reaction of CO2 with the [(CH2CH2OH)Bim]ZnBr3 catalyst, there appeared a new band at 1789 cm−1 (Fig. 4A), which corresponded to the new asymmetric (C
O) vibration of the carbamate salt, presumably implying the activation of CO2 by the alkaline nitrogen from [(CH2CH2OH)Bim]ZnBr3.45,46 Similarly, tracking the change and reaction degree during the process, the absorption peak at 1790 cm−1 ascribed to the carbonyl group of the PC product increased gradually along with the reaction time (Fig. 4B), proving the efficient proceeding of the cycloaddition reaction of PO and CO2.
 |
| Fig. 4 (A) FT-IR spectra monitoring the interaction between the catalyst and CO2. Reaction conditions: n (cat.) = 0.08 mmol, P (CO2) = 2.5 MPa, T = 120 °C, t = 30 min; (B) FT-IR spectra monitoring the PC synthesis at various reaction times. Reaction conditions: 34.5 mmol PO, 0.25 mol% Cat., P (CO2) = 2.5 MPa, T = 120 °C. | |
Based on the above results and previous literature,47 we proposed a plausible mechanism for the CO2 cycloaddition to epoxides in the presence of Zn mediated hydroxyl-functionalized ionic liquids (Scheme 5). It has been proved that epoxides can be activated by zinc halides through the formation of zinc-epoxide adducts.15,38,39 Meanwhile, the hydroxyl groups in (CH2CH2OH)Bim+ coordinated with the oxygen of PO through hydrogen bonds, also resulting in the activation of the PO molecule (step 1). Simultaneously, the bromide anion as a Lewis base nucleophilically attacked the less sterically hindered β-carbon atom of the epoxide, facilitating the ring-opening of PO (step 2). The cooperative interactions between cation and anion stabilized the intermediate oxyanion (I) before the insertion of CO2. In parallel, the tertiary nitrogen from the IL cation reacted reversibly with CO2 to form the carbamate salt (II) as the activated species of CO2.45,46,48 Thereafter, the intermediate (I) made a nucleophilic attack on the carbamate salt (II) producing the new alkyl carbonate compound (III) (step 3), which eventually afforded the cyclic carbonate PC and regenerated the catalyst by the subsequent intramolecular ring-closure (step 4). Hence, the synergetic effects from the hydrogen bond donor (–OH), ionic liquid cation, and ZnBr3− anion in this catalytic system promoted the reaction smoothly.
 |
| Scheme 5 A plausible mechanism for the cycloaddition of CO2 and PO catalyzed by [(CH2CH2OH)Bim]ZnBr3. | |
4. Conclusions
In conclusion, the novel Zn-based task-specific ionic liquids (Zn-TSILs) were developed, and exhibited highly catalytic activity toward the cycloaddition of CO2 with various epoxides without using additional cocatalyst and solvent. Due to the synergetic effects of hydrogen bond donors (–OH), ionic liquid cations, and ZnBr3− anions in this catalytic system, excellent yields of carbonates and high TOF values up to 794 h−1 were achieved in the presence of Zn-TSILs, and the catalyst could be reused at least four times without significant loss of reactivity. Further, comparative studies showed that the [(CH2CH2OH)Bim]ZnBr3 catalyst reduced the activation energy by 14.7 kJ mol−1 compared with the [(CH2CH2OH)Bim]Br catalyst, displaying the unique feature of ZnBr2. The facile synthesis and good catalytic property of Zn-TSILs make them good candidates for further developments and applications in sustainable processes concerned with CO2 fixation.
Acknowledgements
We sincerely acknowledge the financial support from National Natural Science Foundation of China (21373069), Science Foundation of Harbin City (NJ20140037), State Key Lab of Urban Water Resource and Environment of Harbin Institute of Technology (HIT2013TS01) and the Fundamental Research Funds for the Central Universities (HIT. IBRSEM. 201327).
References
- M. E. Wilhelm, M. H. Anthofer, M. Cokoja, I. E. Markovits, W. A. Herrmann and F. E. Kühn, ChemSusChem, 2014, 7, 1357–1360 CrossRef CAS PubMed.
- T. Sakakura, J. C. Choi and H. Yasuda, Chem. Rev., 2007, 107, 2365–2387 CrossRef CAS PubMed.
- M. Aresta and A. Dibenedetto, Dalton Trans., 2007, 28, 2975–2992 RSC.
- S. Fukuoka, M. Kawamura, K. Komiya, M. Tojo, H. Hachiya, K. Hasegawa, M. Aminaka, H. Okamoto, I. Fukawa and S. Konno, Green Chem., 2003, 5, 497–507 RSC.
- T. Sakakura and K. Kohno, Chem. Commun., 2009, 11, 1312–1330 RSC.
- M. Mikkelsen, M. Jørgensen and F. C. Krebs, Energy Environ. Sci., 2010, 3, 43–81 CAS.
- M. North, R. Pasquale and C. Young, Green Chem., 2010, 12, 1514–1539 RSC.
- R. Zevenhoven, S. Eloneva and S. Teir, Catal. Today, 2006, 115, 73–79 CrossRef CAS PubMed.
- Z. Z. Yang, Y. N. Zhao, L. N. He, J. Gao and Z. S. Yin, Green Chem., 2012, 14, 519–527 RSC.
- B. M. Bhanage, S. Fujita, Y. Ikushima and M. Arai, Appl. Catal., A, 2001, 219, 259–266 CrossRef CAS.
- M. Aresta, A. Dibenedetto, L. Gianfrate and C. Pastore, J. Mol. Catal. A: Chem., 2003, 204–205, 245–252 CrossRef CAS.
- P. Ramidi, P. Munshi, Y. Gartia, S. Pulla, A. S. Biris, A. Paul and A. Ghosh, Chem. Phys. Lett., 2011, 512, 273–277 CrossRef CAS PubMed.
- J. L. Song, B. B. Zhang, P. Zhang, J. Ma, J. L. Liu, H. L. Fan, T. Jiang and B. X. Han, Catal. Today, 2012, 183, 130–135 CrossRef CAS PubMed.
- Y. Tsutsumi, K. Yamakawa, M. Yoshida, T. Ema and T. Sakai, Org. Lett., 2010, 12, 5728–5731 CrossRef CAS PubMed.
- S. S. Wu, X. W. Zhang, W. L. Dai, S. F. Yin, W. S. Li, Y. Q. Ren and C. T. Au, Appl. Catal., A, 2008, 341, 106–111 CrossRef CAS PubMed.
- S. Supasitmongkol and P. Styring, Catal. Sci. Technol., 2010, 3, 1961–1972 CAS.
- L. C. Aluja, M. Djoufak, A. Aghmiz, R. Rivas, L. Christ and A. M. Bultó, J. Mol. Catal. A: Chem., 2014, 381, 161–170 CrossRef PubMed.
- A. Decortes, A. M. Castilla and A. W. Kleij, Angew. Chem., Int. Ed, 2010, 49, 9822–9837 CrossRef CAS PubMed.
- D. W. Tian, B. Y. Liu, L. Zhang, X. Y. Wang, W. Zhang, L. N. Han and D. W. Park, J. Ind. Eng. Chem., 2012, 18, 1332–1338 CrossRef CAS PubMed.
- B. Chatelet, L. Joucla, J. P. Dutasta, A. Martinez, K. C. Szeto and V. Dufaud, J. Am. Chem. Soc., 2013, 135, 5348–5351 CrossRef CAS PubMed.
- D. S. Zhao, M. S. Liu, J. Zhang, J. P. Li and P. B. Ren, Chem. Eng. J., 2013, 221, 99–104 CrossRef CAS PubMed.
- J. J. Peng and Y. Q. Deng, New J. Chem., 2001, 25, 639–641 RSC.
- H. Kawanami, A. Sasaki, K. Matsui and Y. Ikushima, Chem. Commun., 2003, 7, 896–897 RSC.
- M. H. Anthofer, M. E. Wilhelm, M. Cokoja, I. E. Markovits, A. Pöthig, J. Mink, W. A. Herrmann and F. E. Kühn, Catal. Sci. Technol., 2014, 4, 1749–1758 CAS.
- J. Q. Wang, W. G. Cheng, J. Sun, T. Y. Shi, X. P. Zhang and S. J. Zhang, RSC Adv., 2014, 4, 2360–2367 RSC.
- J. M. Sun, S. Fujita, B. M. Bhanage and M. Arai, Catal. Today, 2004, 93–95, 383–388 CrossRef CAS PubMed.
- W. L. Dai, B. Jin, S. L. Luo, X. B. Luo, X. M. Tu and C. T. Au, Appl. Catal., A, 2014, 470, 183–188 CrossRef CAS PubMed.
- W. L. Wong, P. H. Chan, Z. Y. Zhou, K. H. Lee, K. C. Cheung and K. Y. Wong, ChemSusChem, 2008, 1, 67–70 CrossRef CAS PubMed.
- S. Foltran, J. Alsarraf, F. Robert, Y. Landais, E. Cloutet, H. Cramail and T. Tassaing, Catal. Sci. Technol., 2013, 3, 1046–1055 CAS.
- S. G. Esfahani, H. B. Song, E. Păunescu, F. D. Bobbink, H. Z. Liu, Z. F. Fei, G. Laurenczy, M. Bagherzadeh, N. Yan and P. J. Dyson, Green Chem., 2013, 15, 1584–1589 RSC.
- Z. Z Yang, Y. F. Zhao, G. P. Ji, H. Y. Zhang, B. Yu, X. Gao and Z. M. Liu, Green Chem., 2014, 16, 3724–3728 RSC.
- D. W. Kim, K. A. Park, M. J. Kim, D. H. Kang, J. G. Yang and D. W. Park, Appl. Catal., A, 2014, 473, 31–40 CrossRef CAS PubMed.
- P. Agrigento, S. M. Al-Amsyar, B. Sorée, M. Taherimehr, M. Gruttadauria, C. Aprile and P. P. Pescarmona, Catal. Sci. Technol., 2014, 4, 1598–1607 CAS.
- H. S. Kim, J. J. Kim, H. Kim and H. G. Jang, J. Catal., 2003, 220, 44–46 CrossRef CAS.
- J. Sun, S. J. Zhang, W. G. Cheng and J. Y. Ren, Tetrahedron Lett., 2008, 49, 3588–3591 CrossRef CAS PubMed.
- Y. X. Zhou, S. Q. Hu, X. M. Ma, S. G. Liang, T. Jiang and B. X. Han, J. Mol. Catal. A: Chem., 2008, 284, 52–57 CrossRef CAS PubMed.
- J. Q. Wang, J. Sun, W. G. Cheng, K. Dong, X. P. Zhang and S. J. Zhang, Phys. Chem. Chem. Phys., 2012, 14, 11021–11026 RSC.
- L. F. Xiao, D. W. Lv and W. Wu, Catal. Lett., 2011, 141, 1838–1844 CrossRef CAS.
- J. K. Lee, Y. J. Kim, Y. S. Choi, H. Lee, J. S. Lee, J. Hong, E. K. Jeong, H. S. Kim and M. Cheong, Appl. Catal., B, 2012, 111–112, 621–627 CrossRef CAS PubMed.
- Y. Y. Zhang, S. F. Yin, S. L. Luo and C. T. Au, Ind. Eng. Chem. Res., 2012, 51, 3951–3957 CrossRef CAS.
- Y. Xie, Z. F. Zhang, T. Jiang, J. L. He, B. X. Han, T. B. Wu and K. L. Ding, Angew. Chem., Int. Ed., 2007, 46, 7255–7258 CrossRef CAS PubMed.
- S. Supasitmongkol and P. Styring, Catal. Sci. Technol., 2014, 4, 1622–1630 CAS.
- M. North and R. Pasquale, Angew. Chem., Int. Ed., 2009, 48, 2946–2948 CrossRef CAS PubMed.
- R. C. Luo, X. T. Zhou, W. Y. Zhang, Z. X. Liang, J. Jiang and H. B. Ji, Green Chem., 2014, 16, 4179–4189 RSC.
- K. M. K. Yu, I. Curcic, J. Gabriel, H. Morganstewart and S. C. Tsang, J. Phys. Chem. A, 2010, 114, 3863–3872 CrossRef CAS PubMed.
- F. Adam and M. S. Batagarawa, Appl. Catal., A, 2013, 454, 164–171 CrossRef CAS PubMed.
- C. J. Whiteoak, N. Kielland, V. Laserna, F. C. Gómez, E. Martin, E. C. Escudero-Adán, C. Bo and A. W. Kleij, Chem.–Eur. J., 2014, 20, 2264–2275 CrossRef CAS PubMed.
- J. O. Gómez, O. G. J. Aberasturi, C. R. López, J. N. Mestre, B. M. Madurga and M. Belsué, Chem. Eng. J., 2011, 175, 505–511 CrossRef PubMed.
Footnote |
† Electronic supplementary information (ESI) available. See DOI: 10.1039/c4ra14111c |
|
This journal is © The Royal Society of Chemistry 2015 |
Click here to see how this site uses Cookies. View our privacy policy here.