DOI:
10.1039/C4RA11059E
(Paper)
RSC Adv., 2015,
5, 5647-5651
In situ transmission electron microscopy of Ag-incorporated carbon nanofibers: the effect of Ag nanoparticle size on graphene formation†
Received
24th September 2014
, Accepted 2nd December 2014
First published on 2nd December 2014
Abstract
We have studied graphene formation from a single Ag-incorporated carbon nanofiber (CNF) during electron emission using in situ transmission electron microscopy. The formation of graphene from the Ag-incorporated CNF structure was observed under a high current of between 900 nA to 2.03 μA during field and thermal electron emission. Joule heating during the process generated an increased temperature, estimated at approximately 440 K to 1030 K, leading to the transformation of a significant amount of the amorphous carbon surrounding Ag particles to a graphene structure, and to the nearly simultaneous evaporation of Ag particles. This evaporation interrupted the thermal electron emission process, thus leading to a decrease of the emission current to ∼300 nA. Also, graphene stopped forming after the Ag particles had evaporated. In this paper, the effect of Ag particle size on its ability to catalyze the fabrication of high-quality graphene are discussed.
Introduction
Graphene, a two-dimensional monolayer sheet of carbon with a honeycomb lattice structure, has attracted great interest because of its magnificent mechanical, electrical and chemical properties.1–5 These unique properties make it a promising candidate to replace existing materials in various applications.6–8 In order to explore its practical applications, numerous approaches have been developed to synthesize graphene on a large scale with controllable integration of its layers. One popular method for growing graphene is chemical vapor deposition (CVD). When using CVD, high-quality graphene can be grown on a variety of metal substrates, especially nickel, cobalt, and copper (Cu), which act as catalysts.9–13 There have also been recent reports of graphene being grown on bulk surfaces of noble metals such as gold (Au) and silver (Ag),14,15 which had previously been assumed to be poor catalysts for CVD. These results indicate the possibilities and potential to grow and combine graphene with various kinds of metals.
In our previous reports, it was demonstrated that carbon nanofibers (CNFs) can be grown simply by irradiation of Ar+ ions onto the carbon surface, even at room temperature, and that any metal can be readily incorporated into the ion-induced CNFs by a simultaneous supply of the metal during CNF growth.16–19 In situ transmission electron microscopy (TEM) studies revealed that a change in the structure of the metal-incorporated CNF could be induced using a high electron current along the CNF during the field emission (FE) process. For CNFs in which iron (Fe) and Au were incorporated, for example, the initially amorphous CNF became a bamboo-like carbon nanotube (CNT) and a hollow graphitic structure, respectively.20,21 In contrast, pristine CNFs without any metal incorporated in them, showed a totally different structural behavior, where the amorphous CNF was transformed to an unorganized ring-like stack of graphitic structures.22 These are examples of the in situ observation of the formation of crystallized nanocarbons using a solid-phase reaction. Thus, in situ TEM has great potential to reveal the mechanism of graphene formation at the nanoscale.
Ag possesses excellent electrical, thermal and optical properties, making it indispensable in various kinds of applications. It has also been demonstrated that the combination of Ag nanoparticles with nanocarbon materials such as CNFs and graphene can enhance their field electron emission, electrical, and photoresponse properties.19,23,24 Based on this background, in this paper the investigation of graphene growth directly from Ag-incorporated CNF induced by electron emission current by using in situ TEM will be described.
Experimental methods
Fig. 1(a) shows a schematic image of a sample set up for the Ag-incorporated CNFs. Samples were prepared on commercially available graphite foils (5 mm × 10 mm × 100 μm in thickness) using ion irradiation, with a Kaufman-type ion gun (Ion-tech Inc. Ltd., model 3-1500-100FC). In this process, an Ag plate serving as an Ag source was placed perpendicularly to the graphite foil. Both the graphite foil and the Ag plate were co-sputtered with Ar+ at an ion incidence angle of 45° from normal to the graphite and Ag surfaces. The sample fabrication was carried out for 60 min at room temperature. The ion beam employed was 6 cm in diameter, with energy and current density of 600 eV and 6.0 mA cm−2, respectively. The basal and working pressures were 1.5 × 10−5 and 2.0 × 10−2 Pa, respectively. The surface morphology of the sample was observed carefully using a scanning electron microscope (SEM, Jeol JEM-5600). Fig. 1(b) shows that the Ag-incorporated CNFs grew on the tips of conical protrusions. It should be noted that only one CNF formed per conical protrusion. The sample was then cut into a 2 mm width and directly mounted on the TEM holder for the in situ TEM observation (Jeol JEM-2010HR). The sample was mounted as a cathode on a stationary stage, while a platinum–iridium (Pt–Ir) nanoprobe was used as an anode on the piezo-driven stage of the TEM specimen holder (Jeol EM-Z02154T), as illustrated in Fig. 1(c). Electron emission measurements of individual Ag-incorporated CNFs were made at a working pressure of 1 × 10−5 Pa. The microscope was operated at an acceleration voltage of 200 kV. TEM images were continuously recorded using a charge-coupled device camera and an image recording application. While observing the structural behavior of the sample, the electron emission current was measured and controlled by changing the bias voltage.
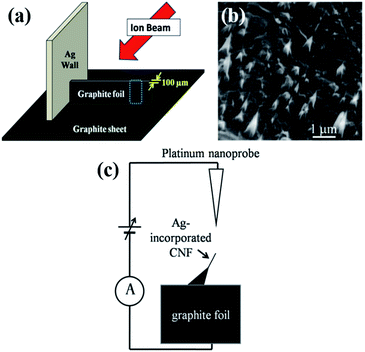 |
| Fig. 1 (a) Schematic diagram of the experimental set up for Ag-incorporated CNF fabrication. The inset circle (blue dotted line) marks the location where the sample was employed for the in situ TEM experiment. (b) SEM image of Ag-incorporated CNFs at the graphite edge. (c) Schematic diagram of the in situ FE measurement experimental set up. | |
Results and discussion
Fig. 2(a)–(c) show the high-resolution TEM (HRTEM) images of a single Ag-incorporated CNF. In Fig. 2(a), the fiber was observed to be approximately 960 nm in length and 10 nm in diameter. Fig. 2(b) and (c) show, high-magnification images of the cone (base) and middle area of the Ag–CNF, respectively. The images reveal that fine Ag crystallites 5–15 nm in diameter were well dispersed in the amorphous carbon CNF matrix. The selected area electron diffraction (SAED) pattern and energy-dispersive X-ray spectrometry (EDS) of the region of the CNF labelled “A” in Fig. 2(a) are shown in Fig. 3(a) and (b), respectively. The diffraction shows the polycrystalline ring pattern of Ag, which indicates that the Ag-incorporated CNF contains a mixture of amorphous carbon and randomly oriented Ag crystallites, which was confirmed by the EDS results.
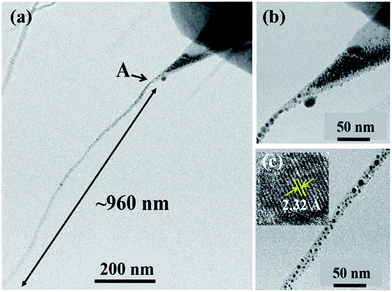 |
| Fig. 2 (a) TEM image of the initial Ag-incorporated CNF used for FE measurement. High magnification images of the part of the fiber pointed to by the arrow: (b) base region of the fiber and (c) middle region of the fiber. The inset of (c) shows a high magnification image of the Ag particle. | |
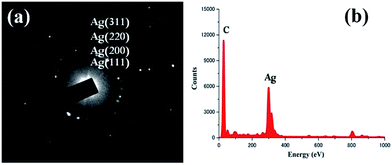 |
| Fig. 3 (a) SAED pattern and (b) EDS spectra of the Ag-incorporated CNF taken of the region of the fiber labelled “A” in Fig. 2(a). | |
The influence of the electron emission process on the structure of Ag-incorporated CNF was investigated in situ using FE measurements in a TEM. The distance of the gap between the Ag-incorporated CNF (cathode) and Pt nanoprobe (anode) was set at 1.5 μm. A bias voltage was applied up to 150 V with incremental steps of 10 V while observing the fiber at 150k× magnification. Fig. 4 shows the FE properties (current–voltage curves) of a single Ag-incorporated CNF. The highest emission current value obtained was 2.03 μA at 100 V μm−1. From the current–voltage curves, FE characteristics were analyzed using a Fowler–Nordheim (F–N) plot, which can be calculated from F–N eqn (1):
|
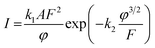 | (1) |
where
k1 = 1.54 × 10
−6 A eV V
−2,
k2 = 6.83 × 10
3 eV
−3/2 μm
−1,
I is the emission current,
A is the emission area, and
φ is the work function. The local electrical field
F is usually proportional to voltage
V, as in
eqn (2):
25 |
 | (2) |
where
β is the field enhancement factor. Here,
β can be estimated from the slope of the F–N plot. The
β value was calculated to be 31, assuming a work function of 4.6 eV for graphite. This
β value was smaller than the value reported from single Fe-incorporated CNF and CNT,
20,26 because the anode–cathode distance
d, was smaller in this case.
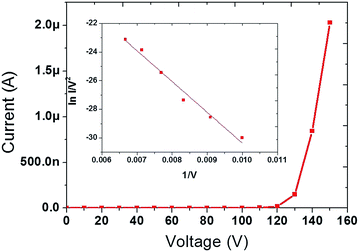 |
| Fig. 4 Field emission I–V curves and F–N plot (inset) of the Ag-incorporated CNF. | |
Fig. 5(a)–(c) show the TEM images of the Ag-incorporated CNF after the electron emission measurement. Fig. 5(a) reveals that the apex of the fiber moved toward the anode direction because of a charge effect during the electron emission process. Furthermore, a significant structural transformation of the fiber part was observed (compare Fig. 5 to Fig. 2). As shown in Fig. 5(a)–(c), Ag particles that had been incorporated in the fiber disappeared after the electron emission process, leaving holes in the fiber. After the electron emission process, the SAED analysis of the region of the fiber labelled “A” in Fig. 5(a) showed a ring pattern (inset), indicating very fine polycrystalline structures. However, the diffraction ring pattern obtained corresponds only to the distance between bonded carbon atoms, and not to that between Ag atoms. This SAED result clarifies the absence of Ag particles in the CNF and the graphitization of amorphous carbon, at the respective locations. To confirm this, higher magnification TEM observations were made. Fig. 6(a) and (b) are high magnification TEM images of the part of the fiber labelled A in Fig. 5(a) taken before and after the electron emission process. Comparing these images reveals that the Ag particles in the fiber evaporated, leaving holes with shapes similar to those of the Ag particles. Furthermore, amorphous carbon around the Ag particles was transformed to a graphene-like structure because of the Joule heating induced by the emission current during the electron emission process.27 The high magnification TEM image shows that the lattice spacing between layers was around 3.47 Å, which was consistent with that of graphite. The elevated temperature of a one-dimensional object such as CNF can be estimated by using a resistive heating model.28 The temperature distribution eqn (3) is:
|
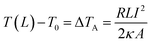 | (3) |
where
κ is the thermal conductivity (100 W mK
−1),
A is the cross section of the fiber,
R is the resistivity of CNT/CNF (2.0 × 10
6 Ω m),
L is the length of the fiber, and
I is the emission current. Here, we consider the emitter length,
L, to be the total distance from the fiber apex to the cone base;
L was measured to be 1.4 μm. As shown in
Fig. 4, the maximum emission current increased markedly to 2.03 μA. At this point, the temperature of the fiber was estimated to reach 1030 K, which should enhance the graphitization through carbon diffusion around the Ag particles. This explanation was further supported by the SAED results in the inset of
Fig. 5(a), which shows a polycrystalline ring pattern that corresponds to the graphitic structure.
29 The evaporation of bulk Ag under high vacuum (pressure equal to 1 × 10
−5 Pa) already started at 850 K, which has been reported in previous studies.
30,31 Thus, we think that the Ag particles that had disappeared evaporated because of the escalated temperature, as Ag evaporation could occur under TEM working pressure conditions at a temperature below 1000 K. One more factor that can be considered is the effect of the size of the Ag particles on the melting temperature of Ag: the melting point of Ag nanoparticles should be lower than that of bulk Ag.
32,33 Thus, the Ag nanoparticles in this case are also likely to have evaporated at a temperature below 1000 K. The graphitization occurred as a result of surface adsorption of carbon atoms on Ag particles.
34 Because the evaporation of the Ag particles and the graphitization process occurred almost simultaneously by Joule heating, this process leaves an imperfect graphitic structure on the surface while maintaining a hole similar in shape to that of the Ag particle.
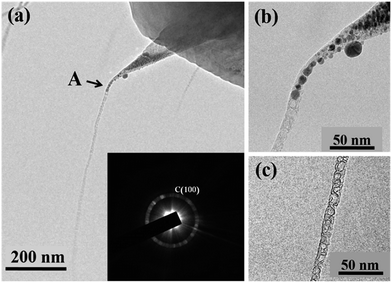 |
| Fig. 5 (a) TEM image of Ag-incorporated CNF after FE measurement. (b and c) High magnification images of the part of the fiber pointed to by the arrow in (a): (b) base area and (c) middle area. The inset of (a) shows the SAED pattern of the fiber. | |
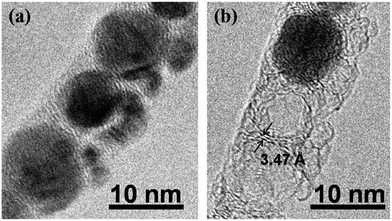 |
| Fig. 6 High magnification images (taken from the part of the fiber labelled A in Fig. 5(a)) (a) before and (b) after the FE process. The arrows in (b) indicate the graphitization of the carbon around a silver particle. | |
TEM images of the fiber's structural behavior at the region labelled “A” (as above) are shown in Fig. 7. The series of images in Fig. 7(a)–(f) show the structural changes that occur in the nanofiber as electrons are being emitted at high current. The applied voltage was increased gradually from 130 V to 150 V. At a 130 V bias voltage, an emission current of ∼150 nA was obtained. During this period, no significant changes of the fiber structure were observed. Then, the applied voltage was increased to 140 V, and the current drastically increased to ∼800 nA. At this emission current, significant changes in the structure of the Ag-incorporated CNF was observed as shown in Fig. 7(a)–(e). At the location of the arrow, it can be seen that the Ag particles had evaporated gradually starting from the apex and then proceeding to the base of the CNF. The focused electrons emitting through the apex triggered the Joule heating, and the resulting increased temperature was channelled to the base of the CNF. This can be understood when considering the larger electric field of the sharp apex area than that of the base of the CNF. When the applied voltage was increased to 150 V, the current reached its maximum, at 2.03 μA. At this moment, almost all of the Ag particles had evaporated from the CNF region labelled “A” [Fig. 7(f)], but then the current suddenly dropped to ∼300 nA. It is believed that in the moment before the Ag particles had fully evaporated [Fig. 7(f)] there were two types of electron emissions taking place: field electron emission and thermal electron emission. Joule heating occurred of the Ag particles incorporated amorphous CNF, which triggered the thermal emission; thus the combination of the two emission processes produced an extremely high 2.03 μA current at 150 V. However, after the Ag particles evaporated, the temperature decreased, and thermal emission also terminated, thus the emission current dropped to 300 nA. Only a small portion of the amorphous carbon, i.e., the portion that adsorbed on the surface of Ag particles, transformed into graphitic layers due to the Joule heating that was generated during the electron emission process. The melting temperature of the carbon nanofiber (∼3773 K) is much higher than that of Ag.35 Therefore, the structure of the carbon nanofiber hardly changed when subjected to a large electric field, while Ag evaporated because of the Joule heating.
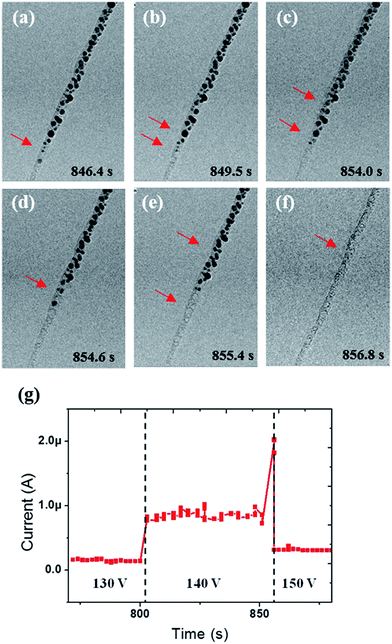 |
| Fig. 7 (a–f) Time-lapsed HRTEM images of Ag-incorporated CNF during the field emission process. (g) Current properties of the fiber corresponding to the TEM images. | |
Conclusions
A transformation of an Ag-incorporated CNF structure was observed directly during FE measurement under a high current between 800 nA to 2.03 μA. The amorphous carbon surrounding the Ag particles changed to a graphene-like structure and the evaporation of Ag particles because of Joule heating effects occurred almost simultaneously, leaving holes in the fiber whose sizes matched those of the Ag particles. The evaporation of the Ag particles led to a decrease in the temperature and the end of the thermal emission, thus decreasing the emission current to ∼300 nA. These results also suggest that Ag particles are less able than Ag bulk to catalyze the synthesis of graphene.
Acknowledgements
This work was partially supported by a grant from the Japan Society for the Promotion of Science (JSPS; Grant-in-Aid for Scientific Research B, Grant no. 23360020).
Notes and references
- A. K. Geim and K. S. Novoselov, Nat. Mater., 2007, 6, 183 CrossRef CAS PubMed.
- A. H. C. Neto, F. Guinea, N. Peres, K. Novoselov and A. Geim, Rev. Mod. Phys., 2009, 81, 109162 Search PubMed.
- Y. Zhang, Y. W. Tan, H. L. Stormer and P. Kim, Nature, 2005, 438, 201 CrossRef CAS PubMed.
- K. S. Novoselov, A. K. Geim, S. Morozov, D. Jiang, Y. Zhang, S. V. Dubonos, I. V. Grigorieva and A. A. Firsov, Science, 2004, 306, 666 CrossRef CAS PubMed.
- C. Lee, X. Wei, J. Kysar and J. Hone, Science, 2008, 321, 385 CrossRef CAS PubMed.
- M. Liu, X. Yin, E. Ulin-Avila, B. Geng, T. Zentgraf, L. Ju, F. Wang and X. Zhang, Nature, 2011, 474, 64 CrossRef CAS PubMed.
- K. Kim, J.-Y. Choi, T. Kim, S.-H. Cho and H.-J. Chung, Nature, 2011, 479, 338 CrossRef CAS PubMed.
- S. Chen, L. Brown, M. Levendorf, W. Cai, S.-Y. Ju, J. Edgeworth, X. Li, C. Magnuson, A. Velamakanni, R. Piner, J. Kang, J. Park and R. Ruoff, ACS Nano, 2011, 5, 1321 CrossRef CAS PubMed.
- L. Gao, J. R. Guest and N. P. Guisinger, Nano Lett., 2010, 10, 3512 CrossRef CAS PubMed.
- A. Reina, X. Jia, J. Ho, D. Nezich, H. Son, V. Bulovic, M. S. Dresselhaus and J. Kong, Nano Lett., 2009, 9, 130 Search PubMed.
- J. Wintterlin and M.-L. Bocquet, Surf. Sci., 2009, 603, 1841 CrossRef CAS PubMed.
- N. Liu, L. Fu, B. Dai, K. Yan, X. Liu, R. Zhao, Y. Zhang and Z. Liu, Nano Lett., 2011, 11, 297 CrossRef CAS PubMed.
- X. Li, W. Cai, J. An, S. Kim, J. Nah, D. Yang, R. Piner, A. Velamakanni, I. Jung, E. Tutuc, S. K. Banerjee, L. Colombo and R. S. Ruoff, Science, 2009, 324, 1312 CrossRef CAS PubMed.
- T. Oznuluer, E. Pince, E. Polat, O. Balci, O. Salihoglu and C. Kocabas, Appl. Phys. Lett., 2011, 98, 183101 CrossRef PubMed.
- M. E. Ayhan, G. Kalita, S. Sharma and M. Tanemura, Phys. Status Solidi RRL, 2013, 7(12), 1076 CrossRef CAS.
- D. Takeuchi, Z. P. Wang, K. Yamaguchi, M. Kitazawa, Y. Hayashi and M. Tanemura, J. Phys.: Conf. Ser., 2008, 100, 012029 CrossRef.
- Z. Wang, M. Z. M. Yusop, T. Hihara, P. Ghosh, A. Hayashi, Y. Hayashi and M. Tanemura, J. Nanosci. Nanotechnol., 2011, 11, 10677 CrossRef CAS PubMed.
- P. Ghosh, M. Z. Yusop, D. Ghosh, A. Hayashi, Y. Hayashi and M. Tanemura, Chem. Commun., 2011, 47, 4820 RSC.
- Y. Yaakob, M. Z. Yusop, C. Takahashi, G. Kalita, P. Ghosh and M. Tanemura, Jpn. J. Appl. Phys., 2013, 52, 11NL01 CrossRef.
- M. Z. M. Yusop, Y. Yaakob, G. Kalita, M. Sasase, Y. Hayashi and M. Tanemura, ACS Nano, 2012, 6, 9567 CrossRef CAS PubMed.
- C. Takahashi, Y. Yaakob, M. Z. M. Yusop, G. Kalita and M. Tanemura, Carbon, 2014, 75, 277 CrossRef CAS PubMed.
- M. Zamri, P. Ghosh, A. Hayashi, M. Sasase, Y. Hayashi and M. Tanemura, J. Vac. Sci. Technol., B: Nanotechnol. Microelectron.: Mater., Process., Meas., Phenom., 2011, 29(4), 04E103 Search PubMed.
- R. Pasricha, S. Gupta and A. K. Srivastava, Small, 2009, 5, 2253 CrossRef CAS PubMed.
- M. E. Ayhan, G. Kalita, M. Kondo and M. Tanemura, RSC Adv., 2014, 4, 26866 RSC.
- C. J. Edgcombe and U. Valdre, J. Microsc., 2001, 203, 188 CrossRef CAS.
- Z. Xu, X. D. Bai, E. G. Wang and Z. L. Wang, Appl. Phys. Lett., 2005, 87, 163106 CrossRef PubMed.
- K. Asaka, M. Karita and Y. Saito, Appl. Phys. Lett., 2011, 99, 091907 CrossRef PubMed.
- P. Vincent, S. T. Purcell, C. Journet and V. T. Binh, Phys. Rev. B: Condens. Matter Mater. Phys., 2002, 66, 075406 CrossRef.
- J. C. Meyer, A. K. Geim, M. I. Katsnelson, K. S. Novoselov, T. J. Booth and S. Roth, Nature, 2007, 446, 05545 Search PubMed.
- H. A. Jones, I. Langmuir and G. M. J. Mackay, Phys. Rev., 1927, 30, 201 CrossRef CAS.
- F. Geiger, C. A. Busse and R. I. Loehrke, Int. J. Thermophys., 1987, 8, 425 CrossRef CAS.
- Q. Jiang, S. Zhang and M. Zhao, Mater. Chem. Phys., 2003, 82, 225 CrossRef CAS.
- S. Xiao, W. Hu and J. Yang, J. Phys. Chem. B, 2005, 109, 20339 CrossRef CAS PubMed.
- D. Takagi, Y. Homma, H. Hibino, S. Suzuki and Y. Kobayashi, Nano Lett., 2006, 6, 2642 CrossRef CAS PubMed.
- A. G. Whittaker, Nature, 1978, 276, 695 CrossRef CAS.
Footnote |
† Electronic supplementary information (ESI) available. See DOI: 10.1039/c4ra11059e |
|
This journal is © The Royal Society of Chemistry 2015 |
Click here to see how this site uses Cookies. View our privacy policy here.