DOI:
10.1039/C5PY00842E
(Review Article)
Polym. Chem., 2015,
6, 6435-6451
Polymeric ionic liquids for CO2 capture and separation: potential, progress and challenges
Received
3rd June 2015
, Accepted 2nd August 2015
First published on 4th August 2015
Abstract
The increasing level of carbon dioxide (CO2) in the atmosphere is a big threat to the environment and plays a key role towards global warming and climate change. In this context to combat such issues, polymeric ionic liquids (PILs) serve as potential substitutes that offer an extremely versatile and tunable platform to fabricate a wide variety of sorbents for CO2 capture, in particular, for flue gas separation (CO2/N2) and natural gas purification (CO2/CH4). Formerly, there have been several reports on exploitation of ionic liquids for CO2 sorption with promising results. However, just a few have focused on polymeric ionic liquids which significantly over-performed the sorption efficiency of the molecular ionic liquids. This review is first ever of its kind which showcases the potential of PILs as a new member of the CO2 adsorbent family. The most dynamic aspect of PILs research at present is the curiosity to explore their potential as solid sorbents for CO2 capture and separation. This review not only highlights the recent advances in the area of PILs as sorbents for CO2 uptake but also portrays the forthcoming challenges in improving their efficiency. The effect of various cations, anions, polymer backbones, alkyl substituents, porosity, cross-linking, molecular weight and moisture on the CO2 sorption capacity and separating efficiency is scrutinized in detail. Moreover, future strategies to increase the CO2 capture performance of PILs are also discussed.
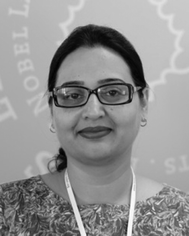 Sonia Zulfiqar | Sonia Zulfiqar is working as an associate professor at the Department of Chemistry, School of Natural Sciences (SNS), National University of Sciences & Technology (NUST), Pakistan. She has vast experience in international research and owing to her outstanding contributions in the field of Polymer & Environmental Chemistry, she has been conferred the Civil Award “Tamgha-i-Imtiaz” by the President of Pakistan in 2012. She is also a recipient of the prestigious Marie-Curie-IIF research grant (2014–16) from the European Commission under the 7th Framework Programme (FP7). Her research interests focus on polymers for CO2 capture and separation, polymeric ionic liquids, polymer based nanocomposites and nanomaterials for energy applications. |
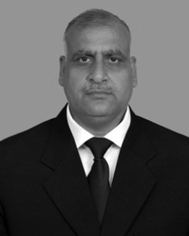 Muhammad Ilyas Sarwar | Muhammad Ilyas Sarwar is a full Professor and the Head, Department of Chemistry, School of Natural Sciences (SNS), National University of Sciences & Technology (NUST), Pakistan. He has made numerous contributions in the field of Polymer/Materials/Environmental Chemistry. He is a recipient of the prestigious fellowships, JICA (Japan) and Fulbright (USA). His research interests include nanoporous polymers for CO2 capture, synthesis and structure–property relationship of nanomaterials, especially, nanoscale incorporation of metal particles/clusters into polymer films, nanocomposites, polymeric blends and their potential applications. He has published plenty of research articles in journals of international repute and also supervised many M.Phil. and Ph.D. students. |
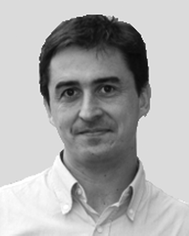 David Mecerreyes | David Mecerreyes is an Ikerbasque Research Professor at POLYMAT, University of the Basque Country, Spain. He is one of the pioneers in the field of Poly(ionic liquids). He is leading the Innovative Polymers Group, specialized in polymer chemistry for new technologies. In 2012, he was granted a prestigious consolidator grant by the European Research Council (ERC) iPes. He is also the coordinator of Marie Curie ITN RENAISSANCE (http://www.renaissance-itn.eu) dedicated to the training of researchers in the field of polyelectrolytes for energy and environment. |
Introduction
Climate change owing to escalating carbon dioxide (CO2) concentration and renewable energy are indeed issues of foremost importance.1,2 From the environmental perspective, it is vital to mitigate anthropogenic CO2 emissions emanating from the burning of fossil fuels, which is the world's primary energy source at present.3 While the chief concern in energy sector is the purification of natural gas which predominantly comprises of methane (CH4) along with other non-hydrocarbon contaminants like CO2, nitrogen (N2), hydrogen sulfide (H2S) and helium (He). These impurities ought to be removed prior to use as fuel thus augmenting the calorific value of natural gas and preventing pipeline and equipment corrosion. Utilization of CH4 is not only limited as clean fuel, rather it is also exploited as a key source of hydrocarbons for petrochemical feed stocks as well as in the production of syngas and high purity hydrogen.4 Keeping in view the role of CO2 in causing greenhouse gas (GHG) emissions and as a principal contaminant found in natural gas, technologies for carbon capture from energy sources and CO2 removal from natural gas needs special attention. Carbon capture and storage (CCS) is an imperative approach appealing the environmentalists at present. Basically, CCS accounts for reducing CO2 levels in the atmosphere owing to anthropogenic activities. Nature has its own mode of capturing CO2 using trees, resulting in its biological fixation. Though experts are more curious in developing novel non-biological processes to capture CO2 from large point sources, several viable CO2 capture and separation options entail different processes3 like pre-combustion capture that involves the removal of CO2 from fuel prior to combustion. Fuel is reacted with oxygen or air at high pressure and temperature resulting in the production of syn gas consisting of carbon monoxide (CO), hydrogen (H2) and carbon dioxide. Reaction of this gas stream containing CO with steam in a catalytic reactor, called a shift converter, produces a mixture of CO2 and H2 gases from which H2 is separated; oxy-fuel or oxyfiring combustion involves the combustion of fuel in the presence of pure oxygen instead of air producing a CO2/H2O mixture. Flue gas with high concentration of CO2 is produced as a consequence of this process because of the absence of nitrogen. Subsequently, the water vapors are removed by cooling and compression of gas stream; post-combustion capture requires the removal of CO2 from the flue gas after combustion and before release into the atmosphere. Low CO2 concentration and high energy for regeneration are among the most significant challenges associated with this process. So far, this strategy has been extensively used for CO2 capture (Fig. 1) and typically accounts for CO2/N2 separation. Researchers in this domain usually employ various technologies to separate CO2 from gas streams such as solvent absorption, membrane separation, cryogenic fractionation, chemical looping and physical adsorption (Fig. 2).5 Solvent absorption entails the use of liquid amine solutions for CO2 sorption from flue gas and consequently the CO2 free flue gas is released into the atmosphere. Afterwards, the CO2 is removed from the liquid and compressed for storage. Membrane technology makes use of preferential separation of the molecules from the mixture and can be used to sieve out CO2 from the flue gas, however, this process has not yet been employed at the commercial scale. The cryogenic technique utilizes low temperatures to cool, condense and purify CO2 from flue gas, and can only be applied to reasonably concentrated CO2 streams. Chemical looping involves the removal of O2 from air by treating with metal particles yielding metal oxides. The combustion of fuel in the presence of metal oxides produces CO2 and water. Nevertheless, chemical absorption of CO2 with alkanolamine solutions is the most extensively used benchmark technology in industry. Owing to volatility and corrosive nature of amines coupled with shortcomings like high energy requirement for regeneration make this process unattractive thus fostering efficient alternative routes.6 One viable strategy to combat such problems is physical adsorption that exploits solid materials for adsorption of CO2 from the flue gas. CO2 free gas stream is then emitted to the atmosphere and subsequently a solid sorbent is regenerated using pressure swing adsorption (PSA) or temperature swing adsorption (TSA) processes and CO2 is removed. The key controlling factors in this respect are temperature, partial pressure, surface force and adsorbent pore size.5 Many efforts are ongoing to design smart and versatile solid sorbents with high surface area, high porosity, low density, high thermal and chemical stability combined with high CO2 capacity for energy efficient CO2 separation processes.5 The pore structure of porous adsorbents is the governing factor for CO2 capture at a low partial pressure whereas at high pressures, surface area and specific pore volume are more influential. Materials typically known in this field include silica, activated carbons, zeolites, metal–organic frameworks (MOFs), covalent organic frameworks (COFs), porous organic polymers (POPs), polymers of intrinsic microporosity (PIMs), conjugated microporous polymers (CMPs), hypercrosslinked polymers (HCPs), porous aromatic frameworks (PAFs) and others.5,7–16 Besides adsorption efficiency, CO2/N2 and CO2/CH4 selectivities are also very imperative and are often related to the presence of highly polar functional groups.17 To curtail CO2 emissions to the atmosphere, many endeavors have already been carried out with a great degree of success but there are many issues that still need to be addressed. Although several challenges enclosing CO2 capture, and the different political, regulatory and economic drivers will eventually declare the time-to-deployment for new CCS systems, now is the suitable time for the scientific community to play a crucial role in resolving the challenge of CO2 capture.
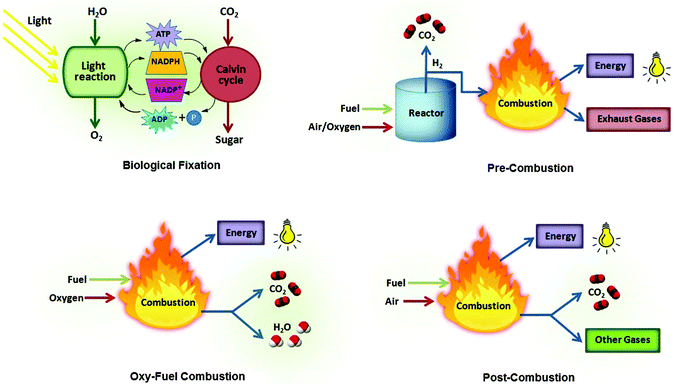 |
| Fig. 1 Illustration of various CO2 capture processes. | |
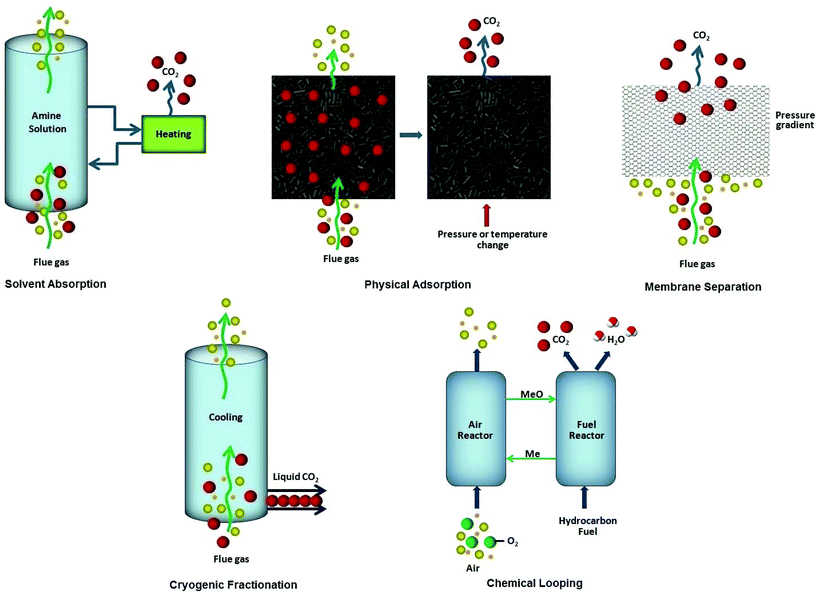 |
| Fig. 2 Overview of various CO2 capture technologies. | |
Interestingly, ionic liquids (ILs) broadly known as “green solvents” have recently been noticed for their outstanding physicochemical properties and applications specifically in CO2 capture and separation.18–24 It is worth mentioning here that ILs possess significant CO2 solubility and selectivity over other light gases and also exhibit strong CO2 affinity that stems from varying cations and anions or by adding functional groups.20,25–28 Moreover, task-specific ionic liquids having amine moieties have been exclusively designed for improved CO2 capture.23 Hence, it has been deduced that anions of the conventional ILs have a substantial impact on CO2 solubility than the cations.29–32 Such findings about ILs urge to polymerize IL monomers and constitute a new family of functional polymers generally known as polymeric ionic liquids or poly(ionic liquid)s (PILs) possessing unique characteristics of ILs and a macromolecular framework.33–35 PILs are a kind of polyelectrolytes bearing IL species in the form of cations or anions, in monomers attached to the polymeric chain yielding a giant molecular design. The small IL molecules are liquid at room temperature owing to the weak intermolecular forces, while PILs are macromolecules with strong intermolecular forces between the chains and hence are solids demonstrating appreciably higher CO2 sorption than the corresponding ionic liquids. PILs are usually synthesized from ionic liquid monomers (ILMs) and possess improved processability, enhanced stability, durability, as well as better control over their meso- to nano-structures. Most of the PIL research studies spotlight the incorporation of polymerizable species into IL cations and the extensively studied ones include an acryloyl or a vinyl group. Whereas diversity of anions are available to serve as counter-ions which are typically introduced by the metathesis reaction of halide ions with a variety of other salts. Polymerization via IL anions has been relatively less investigated. The research domain of PILs has progressed incredibly illustrating many synthetic approaches exploited to produce such polymers, their structure–property relationship and relevance as novel promising solutions in the area of electrochemistry, analytical chemistry, biosciences, catalysis, sensors, magnetism, energy, environment, etc.33,34,36–39 Furthermore, the previous investigations envisaged the exploitation of PILs as superior polyelectrolytes, though in a nascent stage, some studies have also been conducted to explore the CO2 sorption and separation ability of PILs.33,34 These initial attempts revealed the promise of PILs, nonetheless an extensive research is required to fully understand their potential in this area and more work needs to be done by varying polycation–anion pairs that can control the CO2 uptake capacity of PILs. These sorbents could be helpful to capture carbon dioxide and facilitate the separation. Global climate change mitigation technology based on carbon capture and storage extended from amine-scrubbing to 2nd or 3rd generation technologies with conceivably superior thermodynamics, such as chemical or carbonate looping. The introduction of porous polymeric sorbents gets optimum benefits of their high surface area and well-developed porosity in many applications. Various functionalities incorporated onto the surface or interior of their polymeric frameworks offer interesting features to the porous polymers, including responding selectively and reversibility. The key parameters for ideal CO2 uptake are high CO2 solubility, low energy input for regeneration, low cost, long-term reusability, and being environmentally benign. The current review reveals the potential application of PILs as CO2 scavengers and describes a green solution to tackle the threatening global environmental issues.
Factors affecting the PIL performance
Efficient and economical removal of CO2 from various industrial processes containing light gases (N2, CH4 or H2) is very vital and of crucial importance. Ionic liquids offer themselves as better CO2 sorbents due to their non-volatility, reversibility and liquid nature. They have extensively been exploited to curb carbon dioxide as green solvent but issues with their long term stability are major hurdles toward successful utilization. To overcome such problems, PILs are being explored as promising alternatives. They are emerging as unique solid members of the adsorbent family that are environmentally friendly and have great potential for CO2 sorption as compared to ionic liquids.22,23 Some reports revealed the potential of PILs for CO2 capture and separation. In the following sections, we analyze the effect of structural variation in PILs on the said phenomena, particularly the choice of cation, anion, backbone, alkyl chain length, porosity and cross-linking are amongst the most noteworthy. The subsequent discussion intends to emphasize on the factors affecting CO2 capture and separation in this class of sorbents.
Influence of cations
The choice of cations is of paramount importance in the construction of a PIL skeleton for CO2 uptake. The type of cation plays a key role in defining the PIL features in contrast to ILs in which anions are more imperative. Curiosity to know the influence of cations on the CO2 sorption led to several pioneering studies on imidazolium based PIL-1 to PIL-4 synthesized using free radical polymerization of their IL monomers.40–43 Tang et al. have investigated the CO2 sorption potential of PILs for the first time, namely poly[1-(p-vinylbenzyl)-3-butylimidazolium tetrafluoroborate] (PIL-2a), poly[1-(p-vinylbenzyl)-3-butylimidazolium hexafluorophosphate] (PIL-2b) and poly[2-(methacryloyloxy)ethyl-3-butylimidazolium tetrafluoroborate] (PIL-3). The CO2 sorption capacity of room temperature ionic liquid (RTIL), 1-butyl-3-methylimidazolium tetrafluoroborate [bmim][BF4] was reported to be 1.30 mol% at 592.3 mmHg CO2 and 22 °C.40 While the sorption values for PIL-2b, PIL-2a and PIL-3 were found to be 2.8 mol%, 2.27 mol% and 1.78 mol% respectively. In terms of moles, this is around 2.1 (PIL-2b), 1.7 (PIL-2a), and 1.4 (PIL-3) times the capacity of [bmim][BF4]. Their IL monomers unexpectedly showed no CO2 uptake due to the crystalline structures. These PILs reached their 90% sorption capacities in just 3–4 min. Moreover, full CO2 capacities for these PILs were attained within 30 min relative to RTIL [bmim][BF4], that needed above 400 min to reach the equilibrium.43
The same group figured out that tetraalkylammonium based PILs exhibited 6.0–7.6 times higher CO2 sorption capacities41 and reversible sorption/desorption at faster rates than that of room temperature ILs.42 Moreover, tetraalkylammonium based PILs with same anions yielded superior CO2 sorption than the imidazolium-based PILs reported earlier by them.40,43 The strong interaction of the tetraalkylammonium cation with CO2 is attributed to its high positive charge density as compared to the imidazolium cation in which the positive charge is delocalized. Various types of PILs, especially, imidazolium and ammonium-based polymers have been extensively synthesized40–43 and compared for their relative CO2 uptake. The chemical structures of different imidazolium, ammonium, pyridinium, phosphonium based cationic poly(ionic liquid)s (PIL-1 to PIL-16), anionic poly(ionic liquid)s (PIL-17, PIL-18), counter cations and anions used for CO2 sorption are illustrated in Fig. 3. Imidazolium-based polymers exhibited an optimum CO2 sorption of 3.05 mol% for poly[1-(p-vinylbenzyl)-3-methylimidazolium tetrafluoroborate] (PIL-1) and 2.8 mol% for poly[1-(p-vinylbenzyl)-3-butylimidazolium hexafluorophosphate] (PIL-2b), whereas ammonium-based PILs displayed a maximum CO2 uptake of 10.66 mol% for poly[1-(p-vinylbenzyl)-trimethylammonium hexafluorophosphate] (PIL-8b) and 10.22 mol% for poly[1-(p-vinylbenzyl)-trimethylammonium tetrafluoroborate] (PIL-8a) respectively.41–43 These values implied that tetraalkylammonium based PILs rendered higher CO2 sorption capacities. Additionally, monomers of the above mentioned PILs did not show any CO2 sorption owing to their crystalline nature.42 This contrast clearly displays that converting ILs into macromolecules can substantially enhance the CO2 sorption properties. Moreover, the CO2 sorption capacities exhibited by these PILs are considerably higher than other polymers such as polystyrenes/polycarbonates, polymethacrylates and polyethylenes.44–46 The influence of cations can be seen more clearly in the PIL structures having the same backbone and anion. For instance, poly[2-(methacryloyloxy)ethyltrimethylammonium tetrafluoroborate] (PIL-11) and poly[2-(methacryloyloxy)ethyl-3-butylimidazolium tetrafluoroborate] (PIL-3) possess the same BF4 anion and methacrylate backbone but owing to the presence of different cations, i.e. ammonium and imidazolium, the former demonstrated higher CO2 uptake (7.99 mol%) than the latter (1.78 mol%).42,43 In another study, the same authors established that various types of cations strongly affect the CO2 sorption and PIL-1, poly [1-(p-vinylbenzyl)triethylammonium tetrafluoroborate] (PIL-9a), poly[1-(p-vinylbenzyl)pyridinium tetrafluoroborate] (PIL-14), poly[1-(p-vinylbenzyl)-triethylphosphonium tetrafluoroborate] (PIL-15) with similar structures and the same anions followed the decreasing order: ammonium > pyridinium > phosphonium > imidazolium cations.47 The CO2 solubility of ammonium-based PILs is generally higher than that of all the imidazolium- and pyridinium-based PILs, owing to the presence of sp3 hybridization in the tetraalkylammonium cations that can readily rearrange and become more accessible to CO2 thus facilitating CO2 sorption in contrast to other ILs having sp2 hybridization in the aromatic cation groups. Appropriate changes carried out in the PIL structures and the effects of different functional groups introduced to enhance CO2 sorption have been scrutinized. In this connection, some studies were focused on ethylene oxide imidazolium, vinylimidazolium, methacrylate imidazolium and ester imidazolium based PIL-4, PIL-5a–f, PIL-6a,b and PIL-7a–f to investigate their CO2 sorption behaviors.43,48–51 Likewise, other polymers such as vinylbenzyl-tributylammonium, methacrylate dimethylheptylammonium and diallyldimethyl ammonium based PIL-10, PIL-12a–c and PIL-13a–j have also been probed for their CO2 uptake.42,52,53
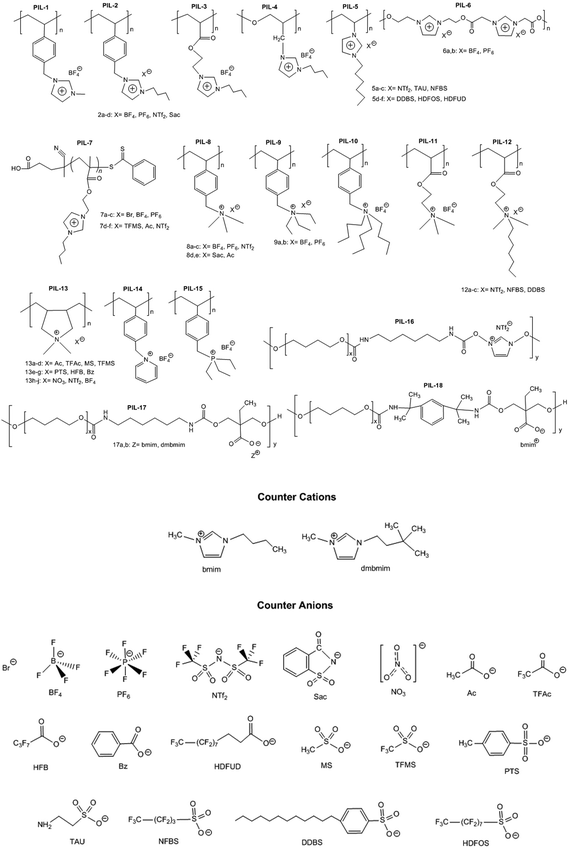 |
| Fig. 3 Chemical structures of various PILs, counter cations and anions used for CO2 sorption. | |
Instead of using the aforementioned cations, recently Einloft et al.54 adopted two different approaches to fabricate novel polyurethane-based PIL-16 to PIL-18; the first route involved a single step cationic polymer synthesis while the second method produced the anionic polyurethane in two steps (Fig. 3). Imidazolium cations incorporated into the backbone of polyurethane (PIL-16) showed lower CO2 sorption (56.3 mol%) relative to the imidazolium used as a counter-cation in PIL-17a (62.3 mol%) at 5 bar. Comparison of PIL-17a with PIL-17b having counter cations [bmim]+ and [dmbmim]+, respectively, showed that [bmim]+ exhibited higher CO2 uptake compared to [dmbmim]+ due to steric reasons of the branched structure relative to that of the linear one.54PIL-17a presented a CO2 sorption of 62.3 mol% and PIL-18 gave a sorption value of 52.2 mol% implying that introduction of the benzene ring into the polymer chain did not improve appreciably the sorption properties. The aromatic structures are believed to improve the sorption capacity55,56 but the steric effect is more pronounced making CO2 interaction difficult with PIL structures at low pressure.
In order to explore the ability of homopolymers/copolymers as CO2 sensing materials, methacrylate dimethylheptyl ammonium-based PIL-12a–c and coPIL-1a,b were prepared by a free radical mechanism (Fig. 4).52 These polymers showed significant CO2-philicity and potential relevance as sensing materials for CO2. Frequencimetric responses were very fast, reversible and no memory-effect provoked. The swiftness of response is a fundamental quality parameter of chemical sensors. Among all the polymers, PIL-12c exhibited a response time less than a second that is inadequate for adjusting the N2 and CO2 flows. The low cost and easy coating process made these materials as excellent contenders for the development of sensors. To enhance CO2 uptake, imidazolium and ammonium based co-PILs (coPIL-2a,b, coPIL-3), crosslinked PILs (clPIL-1, clPIL-2 and clPIL-3) and PIL based nanocomposites (ncPIL-1a,b) have also been synthesized.57–62 Among all the cations, the ammonium cation in simple/porous PILs generally showed better CO2 sorption than other cations while in cross-linked porous polymers the imidazolium cation gave the highest CO2 sorption (Table 1).
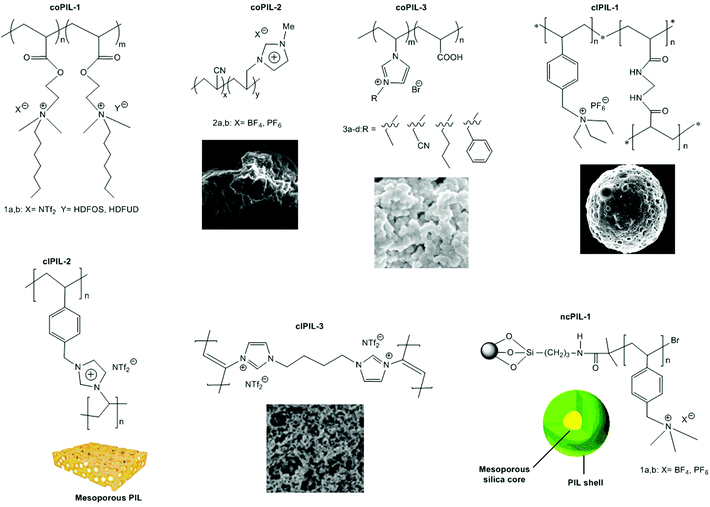 |
| Fig. 4 Chemical structures of co-PILs, crosslinked PILs and PIL based nanocomposites used for CO2 sorption. | |
Table 1 CO2 sorption performance of various types of PILs
PIL |
CO2 loading (mol%) |
CO2 loading (mg g−1) |
Conditions (P, T) |
Ref. |
PIL-1
|
3.05 |
4.64 |
0.78 bar, 295 K |
43
|
PIL-2a
|
2.27 |
3.20 |
0.78 bar, 295 K |
43
|
PIL-2b
|
2.8 |
3.16 |
0.78 bar, 295 K |
43
|
PIL-2c
|
2.23 |
1.87 |
0.78 bar, 295 K |
43
|
PIL-2d
|
1.55 |
1.59 |
0.78 bar, 295 K |
43
|
PIL-3
|
1.78 |
2.49 |
0.78 bar, 295 K |
43
|
PIL-4
|
1.06 |
1.72 |
0.78 bar, 295 K |
43
|
PIL-6a
|
4.5 |
4.77 |
0.86 bar, 298 K |
50
|
PIL-6b
|
4.2 |
3.90 |
0.86 bar, 298 K |
50
|
PIL-7a
|
— |
2.88 |
1 bar, 298 K |
51
|
PIL-7b
|
— |
2.99 |
1 bar, 298 K |
51
|
PIL-7c
|
— |
3.31 |
1 bar, 298 K |
51
|
PIL-7d
|
— |
2.05 |
1 bar, 298 K |
51
|
PIL-7e
|
— |
12.46 |
1 bar, 298 K |
51
|
PIL-7f
|
— |
1.53 |
1 bar, 298 K |
51
|
PIL-8a
|
10.22 |
17.09 |
0.78 bar, 295 K |
42
|
PIL-8b
|
10.66 |
14.60 |
0.78 bar, 295 K |
42
|
PIL-8c
|
2.85 |
2.74 |
0.78 bar, 295 K |
42
|
PIL-8d
|
2.67 |
3.27 |
0.78 bar, 295 K |
42
|
PIL-9a
|
4.85 |
6.99 |
0.78 bar, 295 K |
42
|
PIL-9b
|
— |
10.36 |
1 bar, 298 K |
60
|
PIL-10
|
3.1 |
3.5 |
0.78 bar, 295 K |
42
|
PIL-11
|
7.99 |
14.35 |
0.78 bar, 295 K |
42
|
PIL-16
|
56.3 |
38.86 |
5 bar, 298 K |
54
|
PIL-17a
|
62.3 |
50.52 |
5 bar, 298 K |
54
|
PIL-17b
|
66.1 |
50.96 |
20 bar, 298 K |
54
|
PIL-18
|
52.2 |
37.12 |
5 bar, 298 K |
54
|
coPIL-2a
|
— |
14.3 |
1 bar, 273 K |
57
|
coPIL-2b
|
— |
2.2 |
1 bar, 273 K |
57
|
clPIL-1
|
— |
14.04 |
1 bar, 298 K |
60
|
PIL |
CO2 loading (mmol g−1) |
CO2 loading (mg g−1) |
Conditions (P, T) |
Ref. |
clPIL-2
|
0.46 |
20.24 |
1 bar, 273 K |
61
|
clPIL-3
|
0.1 |
4.4 |
1 bar, 293 K |
72
|
ncPIL-1a
|
0.4025 |
17.71 |
1 bar, 303 K |
62
|
ncPIL-1b
|
0.3793 |
16.69 |
1 bar, 303 K |
62
|
Role of anions
The nature of counter ions influenced the CO2 sorption of polymers including organic anions such as carboxylates (Ac, TFAc, HFB, Bz, HDFUD), sulfonates (MS, TFMS, PTS, TAU, NFBS, DDBS, HDFOS), imides (NTf2, Sac) and inorganic anions (PF6, BF4, NO3, Br). Various anions used in the preparation of PILs for CO2 uptake are illustrated in Fig. 3. The CO2 sorption of imidazolium-based PILs with variable anions has been described to be 2.80 mol% for PIL-2b, 2.27 mol%, 2.23 mol%, 1.55 mol% for PIL-2a,c, andd, 1.78 mol% for PIL-3 and 1.06 mol% for PIL-4, respectively. Higher efficiency was observed in PILs with PF6 and BF4 anions than NTf2 and Sac based polymers. This behaviour is entirely different from smaller IL species and PILs containing inorganic anions gave higher efficiency.43 To evaluate the effect of changing anion type on CO2 sorption, five anions with different anionic functional groups (imide, sulfonate, and carboxylate)/fluorination degrees of the alkyl chain were used to make PIL-5a,c–f films and were analyzed for their CO2-philicity.49 The results implied outstanding sensitivity towards CO2 sorption in terms of quickness, reproducibility, and reversibility over the whole concentration range. The performance of PIL-5e (sulfonate) was better than PIL-5f (carboxylate), although both contain the same polyfluorinated chains but different anion functional groups. On the other hand, nonfluorinated sulfonate PIL-5d showed improved CO2 sensitivity compared to fluorinated sulfonate PIL-5c. The effect of anions on uptake of carbon dioxide was further investigated by Xiong et al.50 (PIL-6a,b) using two anions (BF4, PF6) and an imidazolium based polyester prepared through melt condensation polymerization. The CO2 sorption capacity of PIL-6a (4.5 mol%) was higher than PIL-6b (4.2 mol%) probably due to the association of CO2 with the anion.50
In previous studies, BF4 and PF6 anions were used continuously in the preparation of the PILs while the acetate anion was largely ignored that has proven high efficiency to capture CO2 in room temperature ILs. Butylimidazolium methacrylate based PIL-7a–f have been fabricated including acetate anions along with other counter ions. PIL-7e containing acetate as counter ions synthesized for the first time gave CO2 sorption four-fold higher (12.46 mg gPIL−1) relative to 2.88, 2.99, 3.31, 2.05 and 1.53 mg gPIL−1 for PIL-7a–d, f respectively (Table 1).51 Bulky structures of TFMS and NTf2 anions reduced the free volume hindering CO2 penetration towards the cation, which is mainly responsible for sorption.40,42 Exchange of Br in place of NTf2 can reduce the volume of microvoids in PIL by 37%.63 The fluorinated organic anions TFMS and NTf2 lowered the Tg value of PILs in comparison with inorganic fluorinated phosphates and borates due to the plasticization effect.40,42 Additionally, a low Tg was verified for PIL-7e with no fluorine atoms. Tang et al. reported the CO2 sorption trend of vinylbenzyl-trimethylammonium based PILs similar to that of imidazolium ones but entirely different from ILs.42 They studied the effect of four anions (PIL8a–d) with the same cation and CO2 uptake follows the order PF6 > BF4 > NTf2 > Sac having the values 10.66, 10.22, 2.85, 2.67 mol% respectively. Unlike ILs, CO2 uptake by PIL-8c with the NTf2 anion is much lower than PIL-8a and PIL-8b having BF4 and PF6 anions implying the superiority of inorganic anions. Moreover, PIL-8c having fluorinated anions possesses CO2 sorption comparable to PIL-8d with Sac as the non-fluorinated anion indicating that the presence of fluorine atoms in the anion doesn't favor CO2 sorption. Furthermore, the effect of anions on the glass transition temperatures of PILs was established and with the same cation, anions follow the order PF6 > BF4 > NTf2 > Sac (255 °C, 235 °C, 74 °C, 65 °C). PIL-8c and PIL-8d with NTf2 and Sac anions significantly reduced the Tg owing to the plasticization of anions. Bhavsar and co-workers used acetate anions with the same vinylbenzyl-trimethylammonium cation (PIL-8e) and deduced that the acetate anions would greatly enhance the CO2 solubility and also possess high selectivity over N2 as compared with PIL-8a53 owing to the high basicity of acetate anions.64,65
Mineo et al. studied the dependence of CO2 uptake by changing various anions. They synthesized PIL-12a–c homopolymers based on the 2-(methacryloyloxy)ethyl]dimethylheptylammonium cation and NTf2, NFBS, and DDBS anions.52PIL-12b having the NFBS anion was found to be the best in terms of sensitivity relative to PIL-12a and PIL-12c.52 PILs based on the diallyldimethylammonium cation and different counter ions such as carboxylates (PIL-13a,b,f,g), sulfonates (PIL-13c,d,e), imide (PIL-13i) and inorganic nature (PIL-13h,j) were scrutinized.53PIL-13a with the Ac anion revealed the maximum CO2 uptake and high selectivity over H2 and N2 among all anions studied. Additionally, it was observed that an increase in anion basicity led to enhanced CO2 uptake similar to ILs.65 CO2 uptake of PIL-13g and PIL-13d with Bz and TFMS anions is superior relative to other polymers66 such as polysulphone, polyhydroxyether, polyetherimide and polyarylate, signifying the promise of PILs for CO2 sorption. The selectivity in the case of PILs with sulfonated anions is not significant in contrast to those with carboxylated anions. Some other important factors influencing the CO2 sorption are fractional free volume (FFV) and molar mass of anion. For instance, PIL-13h,j with inorganic anions (NO3 and BF4) displayed increased solubility as well as selectivity with increase in the molar mass of anions.53 Moreover, the same authors also found that this factor of molar mass is not valid for carboxylated and sulfonated anions and incorporation of the fluorine group into various polymers augments the gas sorption characteristics because of increase in the free volume. In this context, PIL-13a,b,c,d were compared and in the case of carboxylated anions, it was noted that the replacement of just the CH3 group of Ac with CF3 in TFAc brought about reduction in CO2 solubility. It is well recognized that CF3 is an electron withdrawing group and thus reduces the basicity of anions and ultimately CO2 solubility. On the contrary, PILs with sulfonated anions showed higher CO2 solubility in fluorine containing anions. For instance, TFMS possesses 3.8 times higher CO2 solubility than MS. These results give detailed insight into anion effects and thus are very helpful for further tuning of PIL properties.53
High physicochemical stability and surface area, low framework density, tunable porosity and versatile synthetic strategies have developed strong interest in porous polymers as gas sorbents. Porous copolymers derived from methacrylate dimethylheptyl ammonium as the CO2 sensing material (coPIL-1a,b) have been produced as shown in Fig. 4.52 These PILs were found CO2-philic and sensitive to CO2 sorption. Both the copolymers showed a similar trend as far as the CO2-philicity is concerned. coPIL-1a,b have anions with same perfluorinated chains and differ for the anionic functional group (carboxylate vs. sulfonate). The gas sensing results displayed that the nature of anionic functionality does not affect CO2-philicity. Allylmethylimidazolium and acrylonitrile porous copolymers (coPIL-2a,b) were also prepared by the seed swelling method.57 The CO2 sorption capacity was dependent on the type of anion used in these polymers. coPIL-2a with BF4 anions gave a higher CO2 sorption capacity (14.3 mg g−1) with a pore-forming agent while coPIL-2b with PF6 anions yielded 2.2 mg g−1 at 0 °C and 0.101 MPa which is opposite to the trend described in the previous reports.40,42 The effect of anions was much pronounced in the case of crosslinked PILs and clPIL-2 with NTf2 anions resulted in better CO2 sorption relative to clPIL-1 with PF6 anions. Recently, Cheng et al. have prepared nanocomposites (ncPIL-1a,b) using a mesoporous silica (meso-silica) support by surface-initiated atom-transfer radical polymerization. The sorbents remained porous and possessed reasonably high surface areas after grafting onto the meso-silica. ncPIL-1a with BF4 anions showed higher CO2 sorption capacity as compared to ncPIL-1b with PF6 anions.62 The above-mentioned discussion clearly described the superiority of using BF4 and PF6 anions in PILs for capturing carbon dioxide whereas, NTf2 anions in cross-linked PILs performed remarkably well.
Selection of backbone and alkyl chain substituents
The dependence of CO2 sorption by changing the backbone of PILs has been investigated by Shen and co-workers.41–43PIL-2a, PIL-3 and PIL-4 serves as a very good example of this effect in which the same butylimidazolium cation and the BF4 anion was present. The variation of the backbone from polystyrene (PS) to polymethylmethacrylate (PMMA) and then to polyethylene glycol (PEG) was carried out. Interestingly, the results revealed a substantial increase in CO2 sorption performance in terms of their monomer units for PIL-2a with the PS backbone as compared to PIL-3 with PMMA and PIL-4 with PEG at 592.3 mmHg of CO2 and 22 °C. The CO2 sorption values follow the decreasing order: PS (2.27 mol%) > PMMA (1.78 mol%) > PEG (1.06 mol%) respectively. Incorporation of the PS backbone led to more pronounced sorption owing to its more rigid structure while PMMA appeared moderate and PEG showed the lowest CO2 uptake.43 Additionally, the effect of backbone is also evident from the glass transition temperatures (Tg) of PILs. Consequently, PIL-4 with a more flexible PEG backbone showed lower Tg in contrast to PIL-3 with PMMA and PIL-2a with a rigid PS backbone. The Tg values follow the increasing order as PEG (33 °C) < PMMA (54 °C) < PS (78 °C) correspondingly.43 Another case study by the same group focused on PIL-8a and PIL-11 having the same ammonium cation and the BF4 anion. The presence of a PS backbone in PIL-8a led to a higher CO2 sorption capacity41,67 (10.22 mol%) and higher Tg42 relative to PIL-11 (7.99 mol%) owing to the PMMA backbone. Einloft et al. also compared the effect of the backbone in PIL-17a and PIL-18 with the same anion and the counter cation.54 Usually, the presence of aromatic groups in the polymer backbone significantly improves the CO2 uptake but conversely, at low pressure, PIL-17a having an aliphatic backbone demonstrated a higher CO2 sorption value of 62.3 mol% relative to PIL-18 (52.2 mol%) with an aromatic backbone. Nonetheless, at higher pressure the CO2 uptake exhibited by PIL-18 was comparable to PIL-17a suggesting the decrease of the steric effect.54
Many attempts have been carried out to study the role of alkyl chain substituents on the CO2 sorption performance of PILs. Exploitation of oligo(ethylene glycol) or nitrile-containing alkyl groups is believed to enhance CO2 uptake.68 Generally, long alkyl substituents attached to cations resulted in reduction of CO2 uptake in PILs in contrast to ILs in which long alkyl chains promote gas permeability and diffusivity. Low uptake of CO2 in PILs with increasing alkyl chain lengths may be due to steric hindrance. This effect can be clearly seen in the case of PIL-1 and PIL-2a, both possessing the same imidazolium cation and the same BF4 anion but different alkyl substituents. The CO2 sorption capacity of PIL-1 (3.05 mol%) having smaller methyl substituents is more than PIL-2a (2.27 mol%) with longer butyl chains.43 Furthermore, PIL-1 with the methyl substituent has a higher Tg (110 °C) as compared to PIL-2a with the butyl group (78 °C) due to the loss of plasticization effect of the butyl group on the imidazolium units.43 In another related work on ammonium based PILs, this effect is much more pronounced. The structures of PIL-8a, PIL-9a and PIL-10 serve as very helpful examples in explaining this phenomenon because the three of them possess the same ammonium cation, BF4 anion and PS backbone and only differ in the alkyl chain length attached to the cation, i.e. methyl, ethyl and butyl groups. CO2 sorption of these PILs follows the decreasing order as PIL-8a (10.22 mol%, Me) > PIL-9a (4.85 mol%, Et) > PIL-10 (3.1 mol%, Bu) respectively.42 Long alkyl substituents attached to cations minimize the CO2 uptake owing to the hindrance posed by them in the interaction of cations with CO2. A similar trend in Tg’s of these PILs was also observed following the sequence PIL-10 (135 °C) < PIL-9a (185 °C) < PIL-8a (235 °C). Higher Tg was shown by PIL-8a having the methyl substituent while the lowest Tg was found for PIL-10 having the butyl chain attached to the cation which resulted in plasticization and a low microvoid volume fraction in the PIL, therefore lowering the CO2 sorption.42 In the end, the PS backbone and small alkyl chain substituents were found to be more suitable for optimum CO2 performance.
Impact of porosity and crosslinking
Porous sorbents are believed to be versatile materials for CO2 uptake owing to their unique features such as high surface area, high porosity, low crystal density combined with high thermal and chemical stability. Early kinetic studies indicated that the fast sorption rates of PILs are not dependent on their particle sizes and surface areas.41 PIL particles with specific areas less than 1 m2 g−1 can take up CO2 as fast as porous PIL-11 particles with the specific area of 20 m2 g−1. Even PIL-2c having larger particles (∼500 μm) capture CO2 quickly. When the BF4 anion in PIL-2a was exchanged with a halide anion, the resulting polymer showed a slower rate of CO2 sorption even with the same particle sizes. Hence the fast CO2 sorption is the peculiar feature of PILs. However, these observations contradict the outcome of the latest reports on CO2 sorption. To enhance CO2 uptake, porous coPIL-2a,b were developed by a two-step swelling method using allylmethylimidazolium and acrylonitrile with a 70
:
30 monomer ratio (Fig. 4).57 The results proved that this route was very effective in enhancing CO2 uptake of coPIL-2a to 14.3 mg g−1 at 0 °C and 0.101 MPa while coPIL-2b gave similar CO2 sorption to the corresponding non-swelling copolymer. Moreover, ammonium-based PIL-8a when treated by the same method yielded noticeably smaller CO2 sorption capacity. The nature of pore-forming agents was also found to affect the porosity of polymers and gave different CO2 sorption capacities.58 PILs with a pore size distribution (PSD) in the range of 0.4–0.6 nm and a high cumulative specific surface area revealed ample sorption capacity towards CO2. Mesoporous polyampholytes reported by Soll et al. through self-complexation of imidazolium cations and the carboxylic acid units of coPIL-3a–d led to a network structure upon precipitation in basic organic medium.59 Interstitial spaces remained open as mesopores of 6–12 nm in diameter and a specific surface area up to 260 m2 g−1 was achieved. The CO2 sorption behaviour of a selected mesoporous polyampholyte was studied through two effective processes: adsorption at the external surface and absorption into the polymer matrix.
Cross-linking also influenced the CO2 sorption capacity and is generally declined due to the reduced void volume and hindered interaction between CO2 and the PIL.42 The CO2 sorption capacity of PIL-8a was decreased by 20%, probably due to the decreased void volume of PIL upon crosslinking. For improved CO2 sorption, a cross-linked and porous clPIL-1 was synthesized using N,N-methylenebisacrylamide and vinylbenzyl-triethylammonium by inverse suspension polymerization.60PIL-9b was also prepared by free radical polymerization to compare the CO2 uptake of both the polymers. clPIL-1 rendered a high thermal stability, an average particle size of 16.9 μm, porosity and a specific surface of 64.3% and 39.12 m2 g−1, respectively and a high CO2 sorption capacity of 14.04 mg g−1 relative to 10.36 mg g−1 for PIL-9b measured at 0.1 MPa and 25 °C. Under the same conditions, clPIL-1 gave better sorption efficiency than some other PILs.40,41,43,58,67,69,70 The recovery and reusability of clPIL-1 were also evaluated and it can be regenerated with a loss of even <1% CO2 adsorption capacity after four cycles.60 Therefore, this study proved that clPIL-1 is a superior contender for CO2 sorption. Wilke et al. have synthesized a cross-linked imidazolium based clPIL-2 through a hard-templating of mesoporous silica subsequently yielding mesoporous polymers.61 The clPIL-2 captured carbon dioxide at a faster rate than its nonporous counterpart. Several reports indicated that bulk PILs presented rapid and superior CO2 uptake relative to their ILs. Many porous PILs reported in the literature are macroporous (pore size > 50 nm)63 but to design mesoporous materials (pore size between 2–50 nm) with a reasonably high surface area is the active area of research at present. Optimum carbon dioxide capture was found with clPIL-2 (0.46 mmol g−1) relative to bulk PILs and monomeric ILs. This sorption occurred with strong interactions giving a high selectivity of ∼45 for a 50
:
50 mixture of CO2 and N2 at 273 K and 760 mmHg. The selectivity for a mixture containing 15% CO2 is even higher (100–200), representing that clPIL-2 is more appropriate for CO2 capture.61 Typically, all samples showed a hysteresis upon desorption; the hysteresis of clPIL-2 was less pronounced. This hysteresis is either related to kinetic effects, strong binding events, or a mixture of both. The origin of the observed weak hysteresis may be due to CO2–PIL interactions. The interaction strength determined from isosteric heat of adsorption (qst) was found to be in the range of 40–30 kJ mol−1, which is significantly higher than in, for example, activated carbon.71 The selectivity of clPIL-2 was even higher, demonstrating that this polymer is a more appropriate material for CO2 capture. clPIL-3 gave a maximum CO2 sorption of 4.4 mg g−1 which is much lower than clPIL-1 and clPIL-2.72 Cheng and co-workers prepared vinylbenzyl trimethylammonium based ncPIL-1a,b from IL monomers and a mesoporous silica (meso-silica) support by surface-initiated atom-transfer radical polymerization.62 The sorbents remained porous and possessed reasonably high surface areas after grafting onto the meso-silica. They showed fast and excellent CO2 sorption capacities, selectivity and reproducibility. ncPIL-1a yielded the highest CO2 sorption of 0.4025 mmol g−1 at 30 °C, while ncPIL-1b gave a maximum CO2 sorption capacity of 0.3793 mmol g−1 for a simulated flue gas containing 10 vol% CO2. The presence of a meso-silica core enhanced the CO2 sorption capacity relative to bulk PILs. However, high temperatures reduced the CO2 sorption capacity, indicating that the nanocomposite polymers should be used at low temperatures.62 So, the increase in porosity of PILs augmented the CO2 uptake to a great extent.
Effect of molar mass, moisture, temperature & pressure
Privalova and co-workers investigated the effect of the molecular weight of PILs on the CO2 sorption capacity and deduced that this factor has the least impact on the CO2 uptake.51 In this connection, PIL-7a with Br anions and PIL-7b with BF4 anions having different molecular weights were compared. CO2 uptake of Br containing PIL-7a was amplified with increase in the molecular weight. For instance the CO2 loading of PIL-7a with molecular weights of 6571 and 19
361 g mol−1 was found to be 2.88 and 3.34 mgCO2 gPIL−1 which clearly explains the slight dependence of CO2 sorption on the molecular weight of PILs. Whereas in PIL-7b the effect of molecular weight is not significant and CO2 loading with molecular weights of 6708, 11
533, 21
937, 22
257 and 77
017 g mol−1 was observed to be 2.99, 3.10, 3.11, 3.09 and 3.10 mgCO2 gPIL−1 respectively. These results proved that CO2 sorption is not much dependent on the particle size.51 The presence of moisture can also cause problems in processing and practical applications and even trace amounts may considerably alter the functionality of PILs. So, the moisture is considered to decrease CO2 sorption performance of PILs. For instance, dry PIL-8a exhibited 10.22 mol% of CO2 uptake while, wet PIL-8a with 13.8 mol% of water revealed a reduction in CO2 capacity with only 7.9 mol%. This decrease in the value of CO2 sorption clearly indicates impairment due to the existence of moisture41 which forms complexes with anions through hydrogen bonding and occupies the sites for CO2 sorption. Zhao and Anderson studied two different task-specific PIL-based coatings, PIL-5a&b and commercial Carboxen fibers to understand the effect of humidity and temperature on CO2 extraction.48 The extraction efficiency of CO2 for all fibers decreased considerably in the presence of water vapor. However, PIL-5b coating displayed the lowest sensitivity drop (28%) in the presence of water vapor, while the sensitivity of PIL-5a dropped by 40% and that of Carboxen fibers by about 75%. Moreover, PIL-5b demonstrated improved water resistance most likely owing to the exclusive mechanism of CO2 sorption,48 thus showing enhanced resistance to reduction of CO2 extraction sensitivity under humid conditions. PIL-5a sorbent coating was found to possess higher CO2/CH4 and CO2/N2 selectivities relative to PIL-5b and Carboxen fibers.
CO2 sorption performance of PILs is very much dependent on the temperature and to understand this effect, usually the sorption is carried out at various temperatures. Flue gas emanating from power plants mostly contains a mixture of gases like N2, CO2, O2 and H2O present in various concentrations and its temperature often fluctuates depending on the scrubbing system used. Therefore, it is vital to foster the materials exhibiting high CO2/N2 selectivity in the presence of moisture or water vapor without sacrificing their performance at different temperatures. The effect of temperature on the extraction efficiency of PIL and commercial Carboxen fibers at different temperatures (0 °C, 30 °C, 40 °C and 65 °C) was monitored.48 The results inferred that it was lengthy to reach equilibrium for PIL fibers, when extractions were done at 0 °C whereas almost the same extraction time was used for each fiber at all other temperatures. Moreover, the quantity of dry CO2 extracted by PIL-5b coating decreased with increasing temperature and the behavior of coating demonstrated great linearity when the CO2 pressure was varied between 1.5–125 kPa at all temperatures.48 In the case of ncPIL-1a,b, the increase in temperature resulted in the deterioration of CO2 sorption performance implying the preferable use of nanocomposites at low temperatures.62 CO2 sorption performance of PILs greatly changes with varying pressure. PIL-8a was evaluated for its CO2 uptake as a function of pressure and interestingly, the CO2 sorption augmented by increasing pressure and adsorbed 44.8 mol% of CO2 (in terms of its monomer units) at a 12 bar pressure.41
Separation via selective adsorption
For designing new PILs as CO2 sorbents, it is critical to focus on the adsorption sites and adsorption/binding modes. CCS is conceived as an appropriate strategy for gas separation, predominantly CO2/N2 separation, in post-combustion capture, and CO2/CH4 separation in the purification of natural gas. Selective adsorption of CO2 over CH4 and N2 is an imperative way in which both adsorption capacity and diffusion selectivity are of particular interest in order to scrutinize the potential of sorbents for separation depending on size exclusion or a favorable gas–pore surface interaction. The main concern in gas separation is the small difference in properties of the gases that have to be separated which is very much evident from the kinetic diameters of CO2 (3.30 Å), CH4 (3.76 Å), and N2 (3.64 Å). On the other hand, the electronic properties of gases, i.e. quadrupolar moment and polarization exhibit some differences. Likewise, CO2 possesses a large quadrupole moment of 13.4 × 10−40 Cm2 relative to N2 (4.7 × 10−40 Cm2) whereas CH4 is non-polar, but owing to its higher polarizability 26.0 × 10−25 cm3, it adsorbs preferentially over N2 (17.6 × 10−25 cm3 for N2 and 26.3 × 10−25 cm3 for CO2).5 Consequently, the difference in chemical reactivity of gases can facilitate control at the molecular level leading to strong interactions with the pore surface of the sorbents and enhanced selectivity. Therefore, to attain high separation selectivity, the difference in quadrupole of gas molecules and pore size must be taken into account. Accordingly, to calculate sorbent's selectivity factor, single-component isotherms and the Ideal Adsorbed Solution Theory (IAST)73 are used to give a quantitative estimate of the adsorption selectivity whereas the qualitative information can be acquired from the differences in uptake between the separated gases under the given measurement conditions. From single-component adsorption, at low loadings within Henry's regime, the adsorption selectivity is obtained by the ratio of Henry's constants for each species.74 On the other hand, at non-dilute loadings, IAST aids in predicting multi-component adsorption isotherms and selectivity based on single-component adsorption isotherms. IAST theory works very well especially in the case of porous materials. The credit goes to pioneering work of Snurr and Hupp75 who employed experimental single-component adsorption isotherms to calculate the adsorption selectivity of a multi-component mixture using IAST. They showed that selectivity increases with decreasing CO2 pressure and also as N2 content, y(N2) approaches unity. Wilke et al. used the same approach to calculate the selectivity in the mesoporous PIL network.61
Cations and anions plays a key role in PILs particularly in CO2 capture, so modifications in their structures can effectively enhance the sorption performance of PILs. Furthermore, the presence of aromatic rings in sorbents is particularly advantageous for producing more rigid architecture and it is established that the strength of CO2–aromatic ring interactions can be tuned by incorporating some polar CO2-philic functionalities into the ring structure such as –NH2, –SO3H, and –COOH, thus enhancing the adsorption capacity and selectivity of CO2 adsorption. The design, synthetic route, structure and porosity of sorbents, plus the nature of gases involved in CO2 separation led to the formulation of several approaches for increasing the separation ability of CO2. The separation strategies encompass adsorptive separation and membrane-based separation but both are entirely different in terms of the materials used. In the case of adsorptive separation, high CO2 sorption capacity and selectivity from other gases are equally crucial for a sorbent material; on the contrary, high penetrability and selectivity are of major interest in membrane-based separation. Nonetheless, practical application is the eventual goal of any of these processes and common themes must be taken into account covering all aspects like efficient separation at room temperature or higher and at low pressure; robust materials to withstand harsh real-environmental conditions, and economical preparation and regeneration of materials. In selecting a porous material for separation, the pore size and shape are of primary importance. Zeolites and other porous materials utilized the molecular sieve effect for gas separation. Conversely, in kinetic separation, the performance of a porous material is directly associated with the pore size and shape of adsorbents in both adsorptive and membrane-based separation. A smart balance must be maintained so as to control the separation, being small enough to separate the desired gas mixture and also in trapping the molecules and stop gas flow all together. The pore size of 5.0–10.0 Å is considered to be suitable for CO2/N2 separation.76 CO2 is a highly quadrupolar gas in contrast to N2 and CH4 being non-polar or weakly polar that led to great differences in the interaction between these gas molecules and the pore surface of porous materials resulting in enhanced adsorption and separation ability. Accordingly, adsorptive separation is getting more popularity owing to the pressing need for green separation procedures thus rendering a significant role in future energy and environmental technologies.
Many studies revealed that PILs can selectively capture CO2 and possess a sizeable uptake capacity coupled with faster absorption/desorption rates in contrast to ILs rendering them outstanding candidates as CO2 sorbent materials. PIL-8b probed by Supasitmongkol and Styring was also found to readily desorb CO2 gas.77 Flue gas stack from power plants typically contain only 15% concentration of CO2 as compared to nitrogen, therefore, CO2/N2 selectivity is of foremost importance. Many groups working in the field of PILs extensively studied the selectivity of CO2 over other gases and found that CO2 sorption was selective and no weight gain was noticed on exposure of PILs to N2 or O2 under similar conditions signifying that PILs can selectively absorb CO2.41–43 Additionally, PIL-8b was found to give a remarkable CO2 selectivity over nitrogen of 70
:
1 which was consistent over repeated cycles.77 A related study focused on PIL-5a demonstrated its superior CO2/CH4 and CO2/N2 selectivities as compared to Carboxen fibers while the change in morphology evidenced by microscopic examination of PIL-5b also showed promise for selectively reacting the amine group of the TAU anion with CO2 instead of CH4 or N2.48 Privalova et al. also reported that the captured CO2 was released from PIL-7a–f thus validating the reversible nature of CO2 sorption mechanism without providing extra heat.51 Another report illustrated the fast desorption of CO2 by PIL-8a and PIL-11 indicating fast diffusion of CO2 inside the solid polymers by releasing CO2 in less than 15 min even under vacuum. Moreover, no changes in sorption/desorption kinetics and sorption capacity were noticed after four cycles of sorption/desorption measurements, implying its reversible nature in contrast to ILs.41
Comparison with other sorbents & future outlook
Regardless of the promising characteristics of PILs, their CO2 sorption performance is, however, lesser than other common sorbents well known for CO2 capture.71,78–88 Various sorbents scanned for CO2 sorption showed better separation and capture ability and the sorption values are typically expressed in mg g−1 for the evaluation of sorbents (see Table 2). MOFs owing to their large surface area and pore volume adsorbed a significant amount of CO2 at a high pressure while at low pressure they exhibited small CO2 uptake. Polar (amine) functionalized MOFs have been ascertained to be useful for improving their affinity to CO2 at low pressure.80–82 Zeolites with low Si/Al ratios (ZEO13X) and monoethanolamine modified zeolite (ZEO13X/MEA) took up 206 and 136 mg g−1 CO2 at low pressure.78 Mesoporous silica renders weak CO2 sorption capacity at low pressure irrespective of their high pore volume. Surface functionalization with alkylamines provided these materials with improved low-pressure CO2 sorption, i.e., poly(ethyleneimine)/silica gave CO2 uptake of 105 mg g−1.79 Similarly, pure carbon sorbents possess weak affinity for CO2 and surface modification/doping significantly augmented their sorption properties, thus, activated carbon rendered CO2 loading around 83 mg g−1.78 The aforementioned materials have their own advantages and limitations as well. Therefore, porous organic materials such as triazine based microporous polycarbazoles (PCBZ),83 nanoporous organic frameworks (NPOF-4),84 porous polymer networks (PPN-80),85 conjugated microporous polymers (CMP-1-COOH),71 microporous polyimides (PI-1),86 porous aromatic frameworks (PAF-1)87 and hypercrosslinked polymers (HCP-1)88 have been designed for better CO2 sorption. Among the PILs as shown in Table 2, clPIL-2 adsorbed the highest carbon dioxide (20.24 mg g−1) at low pressure (1 bar), which provides opportunities to tailor and design new PILs leading to increase in CO2 sorption performance especially by immobilizing these PILs on various supports,89 changing the polycation, and increase of porosity. PIL-8a,b bearing BF4 and PF6 displayed CO2 sorption capacities of 17.09 and 14.60 mg g−1 respectively as reported by Tang et al. based on the mole percentages of monomer units.42 Moreover, the nanocomposites of these two PILs with meso-silica prepared by Cheng et al. yielded 17.71 mg g−1 carbon dioxide uptake for ncPIL-1a and 16.69 mg g−1 CO2 sorption for ncPIL-1b with the same anions. These results showed that introduction of mesoporous silica increased the porosity of these materials, which in turn raised the carbon dioxide uptake of nanocomposites.62 Hence, high surface area 2D and 3D porous PILs bearing CO2-philic groups similar to organic polymers have to be designed and developed.90–92 Additionally various groups possessing high CO2 affinity could be inserted into the backbone of PILs like amines, acids, amidoximes and others to coin the versatility and inherent advantages of PILs for CO2 capture and separation.93–112 Keeping in mind, all the proposed modifications in PILs, we anticipate that the next generation PILs may surpass the CO2 sorption values of microporous polymers as given in the Table 2. The potential of PILs as solid sorbents is highly attractive, right now their capture rate is not the same compared to aqueous amine technologies but the fact remains that amines for CO2 capture have been evolved over the past few years while PILs is relatively a new research area leaving a big challenge for further investigation and improvement. The foremost challenges for the use of PILs as a green solution for CO2 capture are their availability, cost, purity, and compatibility. These challenges are confronted currently on a laboratory scale and must be addressed before scale up at a commercial level. The benefits and shortcomings of ionic liquids and amines seem to be equally balanced. Amines have the edge over other materials of having high CO2 solubility and being of low cost nowadays. However, PILs have the potential to be synthesized and developed in such a way so as to reduce the cost through increasing research and commercialization. Therefore, more research on new PIL solid sorbents, and techniques with higher efficiency and cost effectiveness is essential, the challenges to scale-up novel technologies from a laboratory to industrial level have to be addressed to overcome the technical difficulties in the CCS.
Table 2 Comparison of CO2 sorption capacity of various selected sorbents at low pressure
Sorbent |
CO2 (mg g−1) |
Conditions (P, T) |
Ref. |
ZEO13X |
206 |
1 bar, 298 K |
78
|
ZEO13X/MEA |
136 |
1 bar, 298 K |
78
|
Poly(ethyleneimine)/silica |
105 |
1 bar, 298 K |
79
|
Activated carbon |
83 |
1 bar, 298 K |
78
|
Bio MOF-11 |
264 |
1 bar, 273 K |
80
|
Zeolitic tetrazolate framework (ZTF-1) |
246 |
1 bar, 273 K |
81
|
Zeolitic imidazolate framework (ZIF-78) |
147 |
1 bar, 273 K |
82
|
Nanoporous organic framework (NPOF-4) |
109.9 |
1 bar, 273 K |
84
|
Porous aromatic framework (PAF-1) |
90.2 |
1 bar, 273 K |
87
|
Hypercrosslinked polymer (HCP-1) |
74.8 |
1 bar, 298 K |
88
|
Porous polymer network (PPN-80) |
71.2 |
1 bar, 295 K |
85
|
Conjugated microporous polymer (CMP-1-COOH) |
70.4 |
1 bar, 273 K |
71
|
Polycarbazole (PCBZ) |
49.7 |
1 bar, 273 K |
83
|
Polyimide (PI-1) |
30.3 |
1 bar, 273 K |
86
|
|
20.24 |
1 bar, 273 K |
61
|
|
17.71 |
1 bar, 303 K |
62
|
|
17.09 |
0.78 bar, 295 K |
42
|
|
16.69 |
1 bar, 303 K |
62
|
|
14.60 |
0.78 bar, 295 K |
42
|
|
14.35 |
0.78 bar, 295 K |
42
|
|
14.04 |
1 bar, 298 K |
60
|
|
12.46 |
1 bar, 298 K |
51
|
|
10.36 |
1 bar, 298 K |
60
|
Conclusions
This review uncovers the advancement in the domain of CO2 capture and adsorptive separation by PILs in the last few years and also highlights all related prospects that might be helpful in designing new high performance polymeric ionic liquid sorbents. As exploitation of PILs for carbon capture is an emerging area of research but still in adolescence and necessitates much work to be done and many secrets have yet to be revealed since the quest to produce novel PILs for CO2 sorption and separation is far from being over. Although the CO2 sorption data of PILs demonstrate their potential for such application relative to ILs, yet their efficiency ought to be improved like well known competitors in this field. The imperative factors which should be kept in mind while tailoring PILs’ architecture are the appropriate selection of cations, introduction of new anions, backbones and porosity. The high performance players in this area possess ammonium and imidazolium cations, NTf2, BF4, PF6 and acetate anions, rigid polystyrene backbone, high surface area and porosity together with high separation efficiency. Additionally, the variation of CO2 sorption with temperature and under moist conditions is particularly crucial from real industrial application viewpoint. Innovation in making unique copolymers, nanocomposites and supramolecular networks may help in producing new promising sorbents and improving the performance of the existing ones. Based on our earlier experience, the incorporation of basic groups and enhanced porosity may aid in improving CO2 capture and separation performance of PILs. From the practical viewpoint, substantial amounts of efforts are required to make use of IL chemistry and explore the broad range of chemical and structural variations to increase both CO2 uptake and separation performance leading to revitalization of this field.
List of abbreviations & symbols
Ac | Acetate |
BF4 | Tetrafluoroborate |
Bmim | 1-Butyl-3-methylimidazolium |
Br | Bromide |
Bz | Benzoate |
CCS | Carbon dioxide capture and storage |
CMPs | Conjugated microporous polymers |
COFs | Covalent organic frameworks |
DDBS | Dodecylbenzenesulfonate |
dmbmim | Dimethylbutyl methylimidazolium |
FFV | Fractional free volume |
GHG | Greenhouse gas |
HCP | Hypercrosslinked polymers |
HDFOS | Heptadecafluorooctanesulfonate |
HDFUD | 4,4,5,5,6,6,7,7,8,8,9,9,10,10,11,11,11-Heptadecafluoroundecanoate |
HFB | Heptafluorobutyrate |
IAST | Ideal adsorbed solution theory |
ILs | Ionic liquids |
ILMs | Ionic liquid monomers |
MOFs | Metal–organic frameworks |
MS | Methanesulfonate |
NFBS | Nonafluoro-1-butanesulfonate |
NO3 | Nitrate |
NPOFs | Nanoporous organic frameworks |
NTf2 | Bis(trifluoromethylsulfonyl)imide |
PAFs | Porous aromatic frameworks |
PCBZ | Polycarbazole |
PEG | Polyethylene glycol |
PF6 | Hexafluorophosphate |
PI | Polyimide |
PILs | Polymeric ionic liquids |
PIMs | Polymers of intrinsic microporosity |
PMMA | Polymethylmethacrylate |
POPs | Porous organic polymers |
PPNs | Porous polymer networks |
PS | Polystyrene |
PSA | Pressure swing adsorption |
PSD | Pore size distribution |
PTS |
p-Toluenesulfonate |
qst | Isosteric heat of adsorption |
RTIL | Room temperature ionic liquid |
Sac |
o-Benzoic sulphimide |
TAU | Taurate |
TFAc | Trifluoroacetate |
TFMS | Trifluromethanesulfonate |
T
g
| Glass transition temperature |
TSA | Temperature swing adsorption |
ZIF | Zeolitic imidazolate framework |
ZTF | Zeolitic tetrazolate framework |
Acknowledgements
Dr Sonia Zulfiqar would like to acknowledge financial support provided by Marie Curie IIF grant “NABPIL” (No. 629050) from the European Commission under the 7th Framework Programme (FP7-PEOPLE-2013-IIF).
References
- R. A. Kerr, Science, 2007, 316, 188–190 CrossRef CAS PubMed.
- M. Z. Jacobson, Energy Environ. Sci., 2009, 2, 148–173 CAS.
- S. D. Kenarsari, D. Yang, G. Jiang, S. Zhang, J. Wang, A. G. Russell, Q. Wei and M. Fan, RSC Adv., 2013, 3, 22739–22773 RSC.
- C. A. Scholes, G. W. Stevens and S. E. Kentish, Fuel, 2012, 96, 15–28 CrossRef CAS.
- D. M. D′Alessandro, B. Smit and J. R. Long, Angew. Chem., Int. Ed., 2010, 49, 6058–6082 CrossRef PubMed.
- Q. Wang, J. Luo, Z. Zhong and A. Borgna, Energy Environ. Sci., 2011, 4, 42–55 CAS.
- P. M. Budd, N. B. McKeown and D. Fritsch, Macromol. Symp., 2006, 245–246, 403–405 CrossRef.
- B. Lukose, A. Kuc and T. Heine, Chem. – Eur. J., 2011, 17, 2388–2392 CrossRef CAS PubMed.
- A. I. Cooper, Adv. Mater., 2009, 21, 1291–1295 CrossRef CAS.
- S. Xu, Y. Luo and B. Tan, Macromol. Rapid Commun., 2013, 34, 471–484 CrossRef CAS PubMed.
- R. Babarao, S. Dai and D. Jiang, Langmuir, 2011, 27, 3451–3460 CrossRef CAS PubMed.
- F. Karadas, C. T. Yavuz, S. Zulfiqar, S. Aparicio, G. D. Stucky and M. Atilhan, Langmuir, 2011, 27, 10642–10647 CrossRef CAS PubMed.
- J. Y. Jung, F. Karadas, S. Zulfiqar, E. Deniz, S. Aparicio, M. Atilhan, C. T. Yavuz and S. M. Han, Phys. Chem. Chem. Phys., 2013, 15, 14319–14327 RSC.
- S. Zulfiqar, M. I. Sarwar and C. T. Yavuz, RSC Adv., 2014, 4, 52263–52269 RSC.
- S. Zulfiqar and M. I. Sarwar, J. Environ. Sci., 2014, 26, 1423–1427 CrossRef CAS PubMed.
- S. Zulfiqar and M. I. Sarwar, J. Ind. Eng. Chem., 2015, 21, 1373–1378 CrossRef CAS.
- J. J. Gassensmith, H. Furukawa, R. A. Smaldone, R. S. Forgan, Y. Y. Botros, O. M. Yaghi and J. F. Stoddart, J. Am. Chem. Soc., 2011, 133, 15312–15315 CrossRef CAS PubMed.
- M. Ramdin, T. W. de Loos and T. J. H. Vlugt, Ind. Eng. Chem. Res., 2012, 51, 8149–8177 CrossRef CAS.
- M. M. Wan, H. Y. Zhu, Y. Y. Li, J. Ma, S. Liu and J. H. Zhu, ACS Appl. Mater. Interfaces, 2014, 6, 12947–12955 CAS.
- X. Zhang, X. Zhang, H. Dong, Z. Zhao, S. Zhang and Y. Huang, Energy Environ. Sci., 2012, 5, 6668–6681 CAS.
- C. Wang, X. Luo, X. Zhu, G. Cui, D. Jiang, D. Deng, H. Li and S. Dai, RSC Adv., 2013, 3, 15518–15527 RSC.
- J. F. Brennecke and B. E. Gurkan, J. Phys. Chem. Lett., 2010, 1, 3459–3464 CrossRef CAS.
- E. D. Bates, R. D. Mayton, I. Ntai and J. R. Davis, J. Am. Chem. Soc., 2002, 124, 926–927 CrossRef CAS PubMed.
- J. E. Bara, D. E. Camper, D. L. Gin and R. D. Noble, Acc. Chem. Res., 2010, 43, 152–159 CrossRef CAS PubMed.
- Y.-F. Hu, Z.-C. Liu, C.-M. Xu and X.-M. Zhang, Chem. Soc. Rev., 2011, 40, 3802–3823 RSC.
- M. S. Shannon and J. E. Bara, Sep. Sci. Technol., 2011, 47, 178–188 CrossRef.
- T. K. Carlisle, J. E. Bara, C. J. Gabriel, R. D. Noble and D. L. Gin, Ind. Eng. Chem. Res., 2008, 47, 7005–7012 CrossRef CAS.
- G. D. Smith, O. Borodin, L. Li, H. Kim, Q. Liu, J. E. Bara, D. L. Gin and R. Nobel, Phys. Chem. Chem. Phys., 2008, 10, 6301–6312 RSC.
- M. J. Muldoon, S. N. V. K. Aki, J. L. Anderson, J. K. Dixon and J. F. Brennecke, J. Phys. Chem. B, 2007, 111, 9001–9009 CrossRef CAS PubMed.
- J. L. Anthony, J. L. Anderson, E. J. Maginn and J. F. Brennecke, J. Phys. Chem. B, 2005, 109, 6366–6374 CrossRef CAS PubMed.
- C. Cadena, J. L. Anthony, J. K. Shah, T. I. Morrow, J. F. Brennecke and E. J. Maginn, J. Am. Chem. Soc., 2004, 126, 5300–5308 CrossRef CAS PubMed.
- J. L. Anderson, J. K. Dixon and J. F. Brennecke, Acc. Chem. Res., 2007, 40, 1208–1216 CrossRef CAS PubMed.
- D. Mecerreyes, Prog. Polym. Sci., 2011, 36, 1629–1648 CrossRef CAS.
- J. Yuan, D. Mecerreyes and M. Antonietti, Prog. Polym. Sci., 2013, 38, 1009–1036 CrossRef CAS.
- Z. Zhijun, D. Haifeng and Z. Xiangping, Chin. J. Chem. Eng., 2012, 20, 120–129 CrossRef.
- O. Green, S. Grubjesic, S. Lee and M. A. Firestone, Polym. Rev., 2009, 49, 339–360 CrossRef CAS.
- J. Lu, F. Yan and J. Texter, Prog. Polym. Sci., 2009, 34, 431–448 CrossRef CAS.
- J. Yuan and M. Antonietti, Polymer, 2011, 52, 1469–1482 CrossRef CAS.
- Y.-S. Ye, J. Rick and B.-J. Hwang, J. Mater. Chem. A, 2013, 1, 2719–2743 CAS.
- J. Tang, W. Sun, H. Tang, M. Radosz and Y. Shen, Macromolecules, 2005, 38, 2037–2039 CrossRef CAS.
- J. Tang, H. Tang, W. Sun, H. Plancher, M. Radosz and Y. Shen, Chem. Commun., 2005, 3325–3327 CAS.
- J. Tang, H. Tang, W. Sun, M. Radosz and Y. Shen, Polymer, 2005, 46, 12460–12467 CrossRef CAS.
- J. Tang, H. Tang, W. Sun, M. Radosz and Y. Shen, J. Polym. Sci., Part A: Polym. Chem., 2005, 43, 5477–5489 CrossRef CAS.
- S. Kato, Y. Tsujita, H. Yoshimizu, T. Kinoshita and J. S. Higgins, Polymer, 1997, 38, 2807–2811 CrossRef CAS.
- Z. Mogri and D. R. Paul, Polymer, 2001, 42, 7781–7789 CrossRef CAS.
- J. L. Budzien, J. D. McCoy, D. H. Weinkauf, R. A. LaViolette and E. S. Peterson, Macromolecules, 1998, 31, 3368–3371 CrossRef CAS.
- J. Tang, Y. Shen, M. Radosz and W. Sun, Ind. Eng. Chem. Res., 2009, 48, 9113–9118 CrossRef CAS.
- Q. Zhao and J. L. Anderson, J. Chromatogr., A, 2010, 1217, 4517–4522 CrossRef CAS PubMed.
- P. G. Mineo, L. Livoti, S. L. Schiavo and P. Cardiano, Polym. Adv. Technol., 2012, 23, 1511–1519 CrossRef CAS.
- Y.-B. Xiong, H. Wang, Y.-J. Wang and R.-M. Wang, Polym. Adv. Technol., 2012, 23, 835–840 CrossRef CAS.
- E. I. Privalova, E. Karjalainen, M. Nurmi, P. Mäki-Arvela, K. Eränen, H. Tenhu, D. Y. Murzin and J.-P. Mikkola, ChemSusChem, 2013, 6, 1500–1509 CrossRef CAS PubMed.
- P. G. Mineo, L. Livoti, M. Giannetto, A. Gulino, S. L. Schiavo and P. Cardiano, J. Mater. Chem., 2009, 19, 8861–8870 RSC.
- R. S. Bhavsar, S. C. Kumbharkar and U. K. Kharul, J. Membr. Sci., 2012, 389, 305–315 CrossRef CAS.
- T. O. Magalhães, A. S. Aquino, F. D. Vecchia, F. L. Bernard, M. Seferin, S. C. Menezes, R. Ligabue and S. Einloft, RSC Adv., 2014, 4, 18164–18170 RSC.
- P. Król, Prog. Mater. Sci., 2007, 52, 915–1015 CrossRef.
- H. W. Pennline, D. R. Luebke, K. L. Jones, C. R. Myers, B. I. Morsi, Y. J. Heintz and J. B. Ilconich, Fuel Process. Technol., 2008, 89, 897–907 CrossRef CAS.
- J. M. Zhu, K. G. He, H. Zhang and F. Xin, Adsorpt. Sci. Technol., 2012, 30, 35–41 CrossRef CAS.
- J. Zhu, J. Zhou, H. Zhang and R. Chu, J. Polym. Res., 2011, 18, 2011–2015 CrossRef CAS.
- S. Soll, Q. Zhao, J. Weber and J. Yuan, Chem. Mater., 2013, 25, 3003–3010 CrossRef CAS.
- G. Yu, Q. Li, N. Li, Z. Man, C. Pu, C. Asumana and X. Chen, Polym. Eng. Sci., 2014, 54, 59–63 CAS.
- A. Wilke, J. Yuan, M. Antonietti and J. Weber, ACS Macro Lett., 2012, 1, 1028–1031 CrossRef CAS.
- H. Cheng, P. Wang, J. Luo, J. Fransaer, D. E. De Vos and Z.-H. Luo, Ind. Eng. Chem. Res., 2015, 54, 3107–3115 CrossRef CAS.
- J. Huang, C. Tao, Q. An, W. Zhang, Y. Wu, X. Li, D. Shen and G. Li, Chem. Commun., 2010, 46, 967–969 RSC.
- D. R. MacFarlane, J. M. Pringle, K. M. Johansson, S. A. Forsyth and M. Forsyth, Chem. Commun., 2006, 1905–1917 RSC.
- C. Wang, X. Luo, H. Luo, D. Jiang, H. Li and S. Dai, Angew. Chem., Int. Ed., 2011, 50, 4918–4922 CrossRef CAS PubMed.
- T. A. Barbari, W. J. Koros and D. R. Paul, J. Membr. Sci., 1989, 42, 69–86 CrossRef CAS.
- A. Blasig, J. Tang, X. Hu, Y. Shen and M. Radosz, Fluid Phase Equilib., 2007, 256, 75–80 CrossRef CAS.
- J. E. Bara, C. J. Gabriel, E. S. Hatakeyama, T. K. Carlisle, S. Lessmann, R. D. Noble and D. L. Gin, J. Membr. Sci., 2008, 321, 3–7 CrossRef CAS.
- H. Tang, J. Tang, S. Ding, M. Radosz and Y. Shen, J. Polym. Sci., Part A: Polym. Chem., 2005, 43, 1432–1443 CrossRef CAS.
- A. Blasig, J. Tang, X. Hu, S. P. Tan, Y. Shen and M. Radosz, Ind. Eng. Chem. Res., 2007, 46, 5542–5547 CrossRef CAS.
- R. Dawson, D. J. Adams and A. I. Cooper, Chem. Sci., 2011, 2, 1173–1177 RSC.
- I. Azcune, I. Garcia, P. M. Carrasco, A. Genua, M. Tanczyk, M. Jaschik, K. Warmuzinski, G. Cabanero and I. Odriozola, ChemSusChem, 2014, 7, 3407–3412 CrossRef CAS PubMed.
- A. L. Myers and J. M. Prausnitz, AIChE J., 1965, 11, 121–127 CrossRef CAS.
-
A. L. Myers, in Fundamental of Adsorption, ed. A. Liapis, Engineering Foundation, 1986 Search PubMed.
- Y. S. Bae, O. K. Farha, J. T. Hupp and R. Q. Snurr, J. Mater. Chem., 2009, 19, 2131–2134 RSC.
- J.-R. Li, Y. Ma, M. C. McCarthy, J. Sculleya, J. Yub, H.-K. Jeong, P. B. Balbuena and H.-C. Zhou, Coord. Chem. Rev., 2011, 255, 1791–1823 CrossRef CAS.
- S. Supasitmongkol and P. Styring, Energy Environ. Sci., 2010, 3, 1961–1972 CAS.
- D. P. Bezerra, R. S. Oliveira, R. S. Vieira, C. L. Cavalcante and D. C. S. Azevedo, Adsorption, 2011, 17, 235–246 CrossRef CAS.
- A. Goeppert, H. Zhang, M. Czaun, R. B. May, G. K. S. Prakash, G. A. Olah and S. R. Narayanan, ChemSusChem, 2014, 7, 1386–1397 CrossRef CAS PubMed.
- J. An, S. J. Geib and N. L. Rosi, J. Am. Chem. Soc., 2010, 132, 38–39 CrossRef CAS PubMed.
- T. Panda, P. Pachfule, Y. Chen, J. Jiang and R. Banerjee, Chem. Commun., 2011, 47, 2011–2013 RSC.
- R. Banerjee, H. Furukawa, D. Britt, C. Knobler, M. O'Keeffe and O. M. Yaghi, J. Am. Chem. Soc., 2009, 131, 3875–3877 CrossRef CAS PubMed.
- M. Saleh, S. B. Baek, H. M. Lee and K. S. Kim, J. Phys. Chem. C, 2015, 119, 5395–5402 CAS.
- T. Islamoglu, M. G. Rabbani and H. M. El-Kaderi, J. Mater. Chem. A, 2013, 1, 10259–10266 CAS.
- L. B. Sun, A. G. Li, X. D. Liu, X. Q. Liu, D. Feng, W. Lu, D. Yuan and H. C. Zhou, J. Mater. Chem. A, 2015, 3, 3252–3256 CAS.
- Y. Liao, J. Weber and C. F. J. Faul, Macromolecules, 2015, 48, 2064–2073 CrossRef CAS.
- T. Ben, C. Pei, D. Zhang, J. Xu, F. Deng, X. Jing and S. Qiu, Energy Environ. Sci., 2011, 4, 3991–3999 CAS.
- C. F. Martín, E. Stöckel, R. Clowes, D. J. Adams, A. I. Cooper, J. J. Pis, F. Rubiera and C. Pevida, J. Mater. Chem., 2011, 21, 5475–5483 RSC.
- J. Yang, Y. Sang, F. Chen, Z. Fei and M. Zhong, J. Supercrit. Fluids, 2012, 62, 197–203 CrossRef CAS.
- D. Wu, F. Xu, B. Sun, R. Fu, H. He and K. Matyjaszewski, Chem. Rev., 2012, 112, 3959–4015 CrossRef CAS PubMed.
- R. Dawson, A. I. Cooper and D. J. Adams, Prog. Polym. Sci., 2012, 37, 530–563 CrossRef CAS.
- Y.-S. Bae and R. Q. Snurr, Angew. Chem., Int. Ed., 2011, 50, 11586–11596 CrossRef CAS PubMed.
- L. L. He, M. H. Fan, B. Dutcher, S. Cui, X. D. Shen, Y. Kong, A. G. Russell and P. McCurdy, Chem. – Eng. J., 2012, 189–190, 13–23 CrossRef CAS.
- L. Zhao, Z. Bacsik, N. Hedin, W. Wei, Y. H. Sun, M. Antonietti and M. M. Titirici, ChemSusChem, 2010, 3, 840–845 CrossRef CAS PubMed.
- B. Zheng, J. Bai, J. Duan, L. Wojtas and M. J. Zaworotko, J. Am. Chem. Soc., 2011, 133, 748–751 CrossRef CAS PubMed.
- C. Zhang, W. Song, G. Sun, L. Xie, J. Wang, K. Li, C. Sun, H. Liu, C. E. Snape and T. Drage, Energy Fuels, 2013, 27, 4818–4823 CrossRef CAS.
- F. Rezaei, R. P. Lively, Y. Labreche, G. Chen, Y. Fan, W. J. Koros and C. W. Jones, ACS Appl. Mater. Interfaces, 2013, 5, 3921–3931 CAS.
- M. L. Gray, Y. Soong, K. J. Champagne, J. Baltrus, R. W. Stevens Jr., P. Toochinda and S. S. C. Chuang, Sep. Purif. Technol., 2004, 35, 31–36 CrossRef CAS.
- M. G. Plaza, C. Pevida, A. Arenillas, F. Rubiera and J. J. Pis, Fuel, 2007, 86, 2204–2212 CrossRef CAS.
- S. Zulfiqar, S. Awan, F. Karadas, M. Atilhan, C. T. Yavuz and M. I. Sarwar, RSC Adv., 2013, 3, 17203–17213 RSC.
- S. Zulfiqar, F. Karadas, J. Park, E. Deniz, G. D. Stucky, Y. Jung, M. Atilhan and C. T. Yavuz, Energy Environ. Sci., 2011, 4, 4528–4531 CAS.
- M. E. Boot-Handford, J. C. Abanades, E. J. Anthony, M. J. Blunt, S. Brandani, N. Mac Dowell, J. R. Ferńandez, M.-C. Ferrari, R. Gross, J. P. Hallett, R. S. Haszeldine, P. Heptonstall, A. Lyngfelt, Z. Makuch, E. Mangano, R. T. J. Porter, M. Pourkashanian, G. T. Rochelle, N. Shah, J. G. Yao and P. S. Fennell, Energy Environ. Sci., 2014, 7, 130–189 CAS.
- Q. Sun, Z. Li, D. J. Searles, Y. Chen, G. Lu and A. Du, J. Am. Chem. Soc., 2013, 135, 8246–8253 CrossRef CAS PubMed.
- M. M. Gui, Y. X. Yap, S. P. Chai and A. R. Mohamed, Int. J. Greenhouse Gas Control, 2013, 14, 65–73 CrossRef CAS.
- S. P. Wang, S. L. Yan, X. B. Ma and J. H. Gong, Energy Environ. Sci., 2011, 4, 3805–3819 CAS.
- K. M. K. Yu, I. Curcic, J. Gabriel and S. C. E. Tsang, ChemSusChem, 2008, 1, 893–899 CrossRef CAS PubMed.
- M. Radosz, X. Hu, K. Krutkramelis and Y. Shen, Ind. Eng. Chem. Res., 2008, 47, 3783–3794 CrossRef CAS.
- C. Lu, H. Bai, B. Wu, F. Su and J. F. Hwang, Energy Fuels, 2008, 22, 3050–3056 CrossRef CAS.
- F. J. Uribe-Romo, J. R. Hunt, H. Furukawa, C. Kloeck, M. O'Keeffe and O. M. Yaghi, J. Am. Chem. Soc., 2009, 131, 4570–4571 CrossRef CAS PubMed.
- L. C. Tomé, D. Mecerreyes, C. S. R. Freire, L. P. N. Rebelo and I. M. Marrucho, J. Membr. Sci., 2013, 428, 260–266 CrossRef.
- L. C. Tomé, M. Isik, C. S. R. Freire, D. Mecerreyes and I. M. Marrucho, J. Membr. Sci., 2015, 483, 155–165 CrossRef.
-
L. C. Tomé and I. M. Marrucho, in Applications of Ionic Liquids in Polymer Science and Technology, ed. D. Mecerreyes, Springer, Heidelberg, 2015, Ch. 10, pp. 267–295 Search PubMed.
|
This journal is © The Royal Society of Chemistry 2015 |
Click here to see how this site uses Cookies. View our privacy policy here.