DOI:
10.1039/C5OB00019J
(Communication)
Org. Biomol. Chem., 2015,
13, 2550-2554
Cyclopropanation using flow-generated diazo compounds†
Received
6th January 2015
, Accepted 6th January 2015
First published on 7th January 2015
Abstract
We have devised a room temperature process for the cyclopropanation of electron-poor olefins using unstabilised diazo compounds, generated under continuous flow conditions. This protocol was applied to a wide range of different diazo species to generate functionalised cyclopropanes which are valuable 3D building blocks.
Introduction
Flow chemistry is finding increasing use as an enabling technology in both industrial and academic settings,1 providing a number of advantages over traditional batch mode processes and thereby leading to a variety of interesting opportunities. Many reports to date have involved the adaptation of a single transformation from batch to flow modes.2 From our perspective, a more important goal would be the discovery of new patterns of reactivity. Using flow chemistry methods the space/time dynamics of a reaction profile can be adjusted along with other reaction parameters (i.e. pressure, temperature and mixing) that can be controlled accurately. New opportunities arise especially in harnessing reactive intermediates, which can be very challenging when using conventional methods. In a flow mode, it is possible to continuously generate highly reactive species free from contaminating reagents and then deliver these to a reaction zone for combination with various partners to afford a range of products.
Using this approach, we have previously established a continuous process for the production of transient diazo species on demand, as a class of interesting reactive building blocks (Scheme 1).3 Notably, this approach enabled the continuous generation of highly reactive intermediates and avoided the hazards associated with bulk handling of these species.4
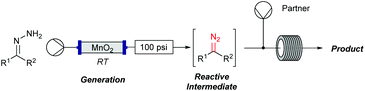 |
| Scheme 1 Flow generation, translocation and reaction of diazo intermediates. | |
The cyclopropane ring features in many natural products and often in bioactive and other functional materials due to its particular conformational constraints and properties.5 Accordingly, cyclopropanation of olefins using stabilised electrophilic diazo compounds has been well studied. In particular, transition-metal catalysis for the coupling of olefins and diazo compounds are amongst the most well developed methods for cyclopropane preparation.6 By contrast, unstabilised diazo compounds are underexplored. Interestingly, this highly energetic species often demonstrates a reversed reactivity pattern due to their amphiphilic character (Scheme 2).7 Further to our initial investigations using the flow generate/translocate/react protocol for sp2–sp3 cross couplings, we envisaged that the diazo species could react with different electron poor olefins in order to give access to substituted cyclopropanes, under mild conditions and without the need for any transition metals in the coupling step. This method would represent an attractive alternative approach to the preparation of poly functional cyclopropanes.
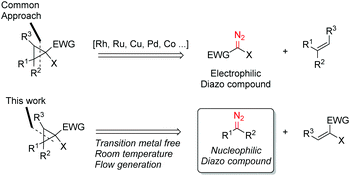 |
| Scheme 2 Cyclopropanation of diazo species. | |
Results and discussion
The study commenced with the use of the readily prepared hydrazone 1a as model substrate for the reaction.8 We soon found that in AcOEt as solvent, a consistent and clean stream of diazo compounds 2a was generated by passage through a column packed with activated manganese dioxide. As in previous studies,3 the use of Hünig's base was necessary to suppress the formation of by-products. Using this protocol, we were able to rapidly establish the cyclopropanation procedure using the olefin substrate 3a. Under optimised conditions, a solution of 1a (0.1 M in AcOEt, 2 equiv. of DIPEA) was passed through a column reactor packed with activated MnO2. The exiting stream of diazo (0.5 mL min−1) was combined with a solution of olefin (3a, 0.05 M in AcOEt, 0.5 mL min−1) after mixing at a T-piece and then stirred at room temperature for 2 h. With these optimised conditions, 4a was isolated in 89% yield (Scheme 3). The process was scaled up using a column of 3 g MnO2 to produce 1.14 g of cyclopropane 4a (86% yield) in one run using only 1.2 equiv. of diazo compound. Notably, the transformation was also achieved with high diastereoselectivity (10
:
1). No attempt was made at this stage to further increase the scale of the reaction.
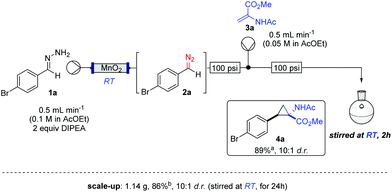 |
| Scheme 3 Cyclopropanation reaction via the generate/translocate/react protocol (major isomer reported in scheme); a 0.2 mmol scale; b 4.25 mmol scale. | |
With the aim of continuously processing material, we briefly investigated the flow cyclopropanation under different conditions (i.e. temperature and residence time) and rapidly found that running the reaction continuously in a 20 mL polymer (PFA) coil at 60 °C, a continuous throughput of 0.93 g h−1 of material could be obtained. Notably, in addition to this we found that the combination of the two reaction streams and the direct feed into a rotary evaporator gave complete conversion to the cyclopropyl derivative 4ain situ (Scheme 4).
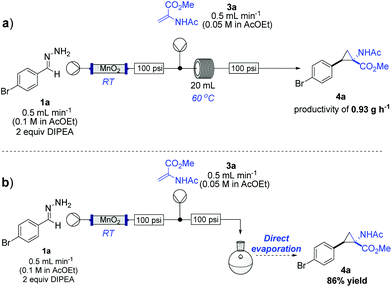 |
| Scheme 4 Flow diazo preparation and cyclopropanation sequence using: (a) a heated reactor coil; (b) direct evaporation. | |
Next we wished to assess the scope of this new room temperature cyclopropanation process. Electron-withdrawing substituents on the aryl ring of diazo species (Table 1) were well tolerated, giving cyclopropanes 4a, 4e and 4f in very good yields (79–89%). Similarly, electron-donating groups also generated cyclopropanes in high yields (4b–d, 89–99%). Importantly, the steric hindrance exerted by ortho substituents seems not to affect the reaction outcome, as illustrated by comparison between 4c and 4d. This unusual feature of the protocol contrasts with metal-catalysed procedures for cyclopropanation.6 Heterocycles are well tolerated (4g, 4h) as is the presence of unsaturation (4i and 4k). Notably, the use of the ketone derivatives (Table 1, entry 10) gave an interesting 55% isolated yield of the product 4j, with a good level of diastereoselectivity (5
:
1). One remarkable aspect of the protocol is that all the products were obtained with good to excellent diastereoselectivity (Table 1).
Table 1 Cyclopropanation of different diazo species with olefin 3aa
Additionally, we were also pleased to find that increasing the functional complexity of the olefinic partner did not affect the outcome of the reaction as shown by reacting the diazo species 2a with the more elaborate structures (i.e.5, Scheme 5) which gave high yield of the corresponding cyclopropyl peptides 6a and 6b.
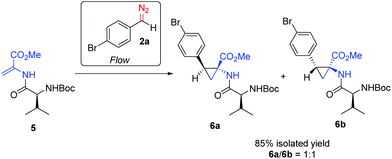 |
| Scheme 5 Diastereoselective cyclopropanation of dipeptide 5 to 6a/6b. | |
We also decided to investigate the preparation of specifically challenging, unstable and difficult to access cyclopropyl compounds, in particular substituted donor–acceptor cyclopropanes.9
For example, the reaction of the diazo 2a with olefin 3c gave 7a in 55% yield as a single diastereoisomer (Scheme 6).
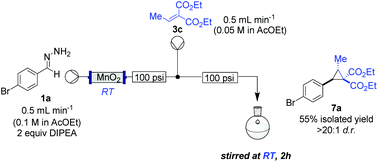 |
| Scheme 6 Diastereoselective cyclopropanation of 3b. | |
While this yield was lower than desired, the olefin starting material had all been consumed. Further attempts with different diazo species failed to give any isolable products. We quickly realised the chemical sensitivity of this class of cyclopropane products to silica gel chromatography and devised an alternative “work-up” involving the use of LiAlH4 (Scheme 7) to give the corresponding diols which were readily isolated (Table 2). This 2-step transformation provides synthetically useful yields with very high diastereoselectivities.
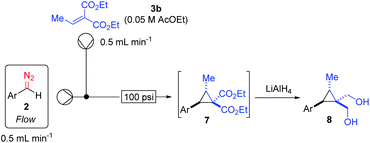 |
| Scheme 7 Diastereoselective cyclopropanation of 3b, followed by reduction to diol 8. | |
Table 2 Cyclopropanation of different diazo species with olefin 3ba followed by reduction to diol 8
Entry |
Substrate |
Product |
|
Yieldb |
dr |
One-pot procedure at 0.2 mmol scale.
Isolated yield after aqueous work-up and silica gel plug filtration.
Ratio of E/Z 1.2 : 1.
|
1 |
|
|
8a
|
48% |
>20 : 1 |
2 |
|
|
8b
|
55% |
>20 : 1 |
3 |
|
|
8c
|
58% |
>20 : 1 |
4 |
|
|
8d
|
40%c |
>20 : 1 |
Another valuable aspect of flow chemistry is associated with the advantages of continuously flowing material though a multistep sequence without the need to isolate intermediates. To showcase this aspect, we devised a 4-step sequence, whereby the use of a very cheap source of material (geraniol) would generate a more complex molecular product, 4k (Scheme 8).
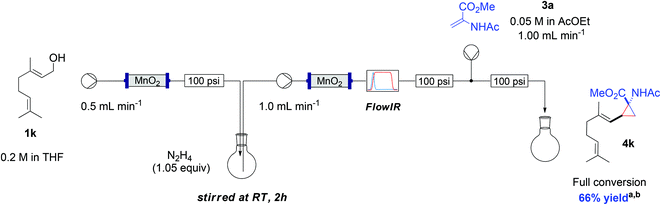 |
| Scheme 8 Telescoped sequence for the preparation of cyclopropane amino acid 4k. a Yield following concentration, measured by 1H-NMR compared to an internal standard; b reaction run on 1 mmol scale. | |
During optimisation of this procedure, we discovered that an excess of MnO2 (7 g) was required for the complete oxidation of geraniol (delivered at 0.5 mL min−1 as a 0.2 M solution in THF) to geranial (step 1).10 The output from the reagent column was collected in a reactor flask containing 1.05 equiv. of hydrazine. After stirring for 2 h at room temperature (step 2), the crude reaction mixture was pumped through a pre-activated column of MnO2 (1.0 mL min−1) to generate the diazo intermediate (step 3). The MnO2 column served also to decompose any residual hydrazine.11 In-line IR monitoring at around 2070 cm−1 identified the diazo product exiting the reactor. This diazo stream was finally combined in a T-piece with a stream (1.0 mL min−1) containing olefin 3a (step 4). Direct evaporation of the final reaction mixture in a rotary evaporator gave 4k in good yield.
Conclusions
In conclusion, we devised a system that could deliver, rapidly and efficiently, differently decorated cyclopropanes under flow conditions, with no need for precious metal catalysis and under remarkable mild conditions (room temperature). The process was successfully applied to a wide range of different unstabilised nucleophilic diazo species which were combined with electron-poor olefins. In this work, we demonstrated how flow chemistry can serve as a discovery tool for generating new chemical reactivity windows to prepare valuable products. This approach again exemplifies the opportunities that arise by using flow chemistry methods.
Acknowledgements
We are grateful to Pfizer Worldwide Research and Development (CB, RJI and JMH), the Swiss National Science Foundation (DNT), CAPES (RL, no 9865/13-6) and the EPSRC (SVL, grant no EP/K0099494/1 and no EP/K039520/1) for financial support.
Notes and references
- Selected recent reviews for chemical flow systems:
(a) R. L. Hartman, J. P. McMullen and K. F. Jensen, Angew. Chem., Int. Ed., 2011, 50, 7502–7519 CrossRef CAS PubMed
;
(b) J. Wegner, S. Ceylan and A. Kirschning, Adv. Synth. Catal., 2012, 354, 17–57 CrossRef CAS
;
(c) C. Wiles and P. Watts, Green Chem., 2012, 14, 38–54 RSC
;
(d) L. Malet-Sanz and F. Susanne, J. Med. Chem., 2012, 55, 4062–4098 CrossRef CAS PubMed
;
(e) I. R. Baxendale, J. Chem. Technol. Biotechnol., 2013, 88, 519–552 CrossRef CAS
;
(f) J. C. Pastre, D. L. Browne and S. V. Ley, Chem. Soc. Rev., 2013, 42, 8849–8869 RSC
;
(g) S. V. Ley, D. E. Fitzpatrick, R. J. Ingham and R. M. Myers, Angew. Chem., Int. Ed., 2014, 53, 2–17 CrossRef
.
- Selected recent examples for chemical flow systems:
(a) H. Kim, A. Nagaki and J.-I. Yoshida, Nat. Commun., 2011, 2, 264 CrossRef PubMed
;
(b) F. Levesque and P. H. Seeberger, Angew. Chem., Int. Ed., 2012, 51, 1706–1709 CrossRef CAS PubMed
;
(c) B. J. Deadman, C. Battilocchio, E. Sliwinski and S. V. Ley, Green Chem., 2013, 15, 2050–2055 RSC
;
(d) Z. He and T. F. Jamison, Angew. Chem., Int. Ed., 2014, 53, 3353–3357 CrossRef CAS PubMed
;
(e) M. Baumann and I. R. Baxendale, Beilstein J. Org. Chem., 2013, 9, 1613–1619 CrossRef PubMed
;
(f) S. Newton, C. F. Carter, C. M. Pearson, L. de C. Alves, H. Lange, P. Thansandote and S. V. Ley, Angew. Chem., Int. Ed., 2014, 53, 4915–4920 CrossRef CAS PubMed
;
(g) A. M. Nightingale, T. W. Phillips, J. H. Bannock and J. C. de Mello, Nat. Commun., 2014, 5, 3777 Search PubMed
;
(h) X. Fan, V. Sans, P. Yaseneva, D. D. Plaza, J. Williams and A. Lapkin, Org. Process Res. Dev., 2012, 16, 1039–1042 CrossRef CAS
;
(i) S. Glöckner, D. N. Tran, R. J. Ingham, S. Fenner, Z. E. Wilson, C. Battilocchio and S. V. Ley, Org. Biomol. Chem., 2015, 13, 207–214 RSC
;
(j) T. Ouchi, C. Battilocchio, J. M. Hawkins and S. V. Ley, Org. Process Res. Dev., 2014, 18, 1560–1566 CrossRef CAS
. Example of flow cyclopropanation using diazomethane:
(k) F. Mastronardi, B. Gutmann and C. O. Kappe, Org. Lett., 2013, 15, 5590–5593 CrossRef CAS PubMed
.
- D. N. Tran, C. Battilocchio, S.-B. Lou, J. M. Hawkins and S. V. Ley, Chem. Sci. 10.1039/C4SC03072A
.
- Recent review about generation of diazo species in flow: B. J. Deadman, S. G. Collins and A. R. Maguire, Chem. – Eur. J. DOI:10.1002/chem.201404348
.
- Selected reviews on cyclopropanes:
(a) W. A. Donaldson, Tetrahedron, 2001, 57, 8589–8627 CrossRef CAS
;
(b) H. Lebel, J.-F. Marcoux, C. Molinaro and A. B. Charette, Chem. Rev., 2003, 103, 977–1050 CrossRef CAS PubMed
;
(c) L. A. Wessjohann, W. Brandt and T. Thiemann, Chem. Rev., 2003, 103, 1625–1648 CrossRef CAS PubMed
;
(d) F. Brackmann and A. de Meijere, Chem. Rev., 2007, 107, 4493–4537 CrossRef CAS PubMed
.
- Selected recent examples for metal-catalysed cyclopropanation:
(a) J.-J. Shen, S.-F. Zhu, Y. Cai, H. Xu, X.-L. Xie and Q.-L. Zhou, Angew. Chem., Int. Ed., 2014, 53, 13188–13191 CrossRef CAS PubMed
;
(b) V. N. G. Lindsay, D. Fiset, P. J. Gritsch, S. Azzi and A. B. Charette, J. Am. Chem. Soc., 2013, 135, 1463–1470 CrossRef CAS PubMed
;
(c) X. Xu, H. J. Lu, J. V. Ruppel, X. Cui, S. L. de Mesa, L. Wojtas and X. P. Zhang, J. Am. Chem. Soc., 2011, 133, 15292–15295 CrossRef CAS PubMed
;
(d) S. F. Zhu, X. Xu, J. A. Perman and X. P. Zhang, J. Am. Chem. Soc., 2010, 132, 12796–12799 CrossRef CAS PubMed
;
(e) M. P. Doyle, Angew. Chem., Int. Ed., 2009, 48, 850–852 CrossRef CAS PubMed
.
-
(a) M. Doyle, Acc. Chem. Res., 1986, 19, 348–356 CrossRef CAS
;
(b) A. J. Padwa, Organomet. Chem., 2001, 617, 3–16 CrossRef
;
(c)
M. Regitz and G. Mass, Diazo Compounds Properties and Synthesis, Academic Press, Inc., Orlando, 1986 Search PubMed
;
(d)
M. P. Doyle, M. A. McKervey and T. Ye, Modern Catalytic Methods for Organic Synthesis with Diazo Compounds, Wiley, New York, 1998 Search PubMed
;
(e) J. N. Johnston, H. Muchalski and T. L. Troyer, Angew. Chem., Int. Ed., 2010, 49, 2290–2298 CrossRef CAS PubMed
;
(f) G. Maas, Angew. Chem., Int. Ed., 2009, 48, 8186–8195 CrossRef CAS PubMed
;
(g) V. L. Rendina and J. S. Kingsbury, J. Org. Chem., 2012, 77, 1181–1185 CrossRef CAS PubMed
;
(h) A. J. Wommack and J. S. Kingsbury, J. Org. Chem., 2013, 78, 10573–10587 CrossRef CAS PubMed
;
(i) T. L. Holton and H. Shechter, J. Org. Chem., 1995, 60, 4725–4729 CrossRef CAS
;
(j) L. A. Adams, V. K. Aggarwal, R. V. Bonnert, B. Bressel, R. J. Cox, J. Shepherd, J. de Vicente, M. Walter, W. G. Whittingham and C. L. Winn, J. Org. Chem., 2003, 68, 9433–9440 CrossRef CAS PubMed
.
- Hydrazones can be safely synthesised in flow manner starting from aldehydes/ketones and hydrazine. A preliminary example was shown in the telescoped synthesis of 4k (Scheme 8).
- Selected recent reviews for donor–acceptor cyclopropanes:
(a) T. F. Schneider, J. Kaschel and D. B. Werz, Angew. Chem., Int. Ed., 2014, 53, 5504–5523 CrossRef CAS PubMed
;
(b) M. A. Cavitt, L. H. Phun and S. France, Chem. Soc. Rev., 2014, 43, 804–818 RSC
.
- I. Hemeon, N. W. Barnett, N. Gathergood, P. J. Scammells and R. D. Singer, Aust. J. Chem., 2004, 57, 125–128 CrossRef CAS
.
- I. Bhatnagar and M. V. George, J. Org. Chem., 1968, 33, 2407–2411 CrossRef CAS
.
Footnote |
† Electronic supplementary information (ESI) available. See DOI: 10.1039/c5ob00019j |
|
This journal is © The Royal Society of Chemistry 2015 |
Click here to see how this site uses Cookies. View our privacy policy here.