Lead removal from solution by a porous ceramisite made from bentonite, metallic iron, and activated carbon†
Received
12th April 2015
, Accepted 21st June 2015
First published on 22nd June 2015
Abstract
There is increasing interest in using a porous ceramisite as the filter medium for removing heavy metals from wastewater in China given its low cost, easy preparation, large available quantities, high mechanical strength, and good performance to remove various pollutants. In this study, bentonite, metallic iron (Fe0), and activated carbon (AC) were used to prepare a Fe0/AC-ceramisite (diameter 2–4 mm) by sintering at 800 °C in a N2 environment. The Fe0/AC-ceramisite achieved a high Pb2+ removal efficiency (>99%) at ceramisite dosages of 5–10 g L−1, an initial solution pH of 3.0–5.7, and initial Pb2+ concentrations of 50–200 mg L−1. Compared with three control ceramisites including B-ceramisite (made by bentonite only), AC-ceramisite (made by bentonite and AC), and Fe0-ceramisite (made by bentonite and Fe0), the enhanced Pb2+ removal by the Fe0/AC-ceramisite was mainly attributed to the iron–carbon micro-electrolysis induced by the addition of AC. A first-order kinetics model fit well for the Pb2+ removal by the Fe0/AC-ceramisite, and the Pb2+ uptake rate increased linearly with the increasing initial solution pH. Results from scanning electron microscopy equipped with energy dispersive X-ray spectroscopy (SEM/EDX), X-ray diffraction (XRD), and X-ray photoelectron spectroscopy (XPS) indicated that the Pb2+ removal by the Fe0/AC-ceramisite involved multiple mechanisms including sorption, reduction (from Pb2+ to Pb0), and precipitation (in the forms of PbCO3 and Pb3(CO3)2(OH)2).
Water impact
Porous ceramisites are considered as one of the most promising candidates for large-scale wastewater treatment in China because of their low cost, large available quantities, easy preparation, and high capability to remove various pollutants. However, little is known about their effectiveness and underlying mechanisms on the removal of heavy metals. In this study, a porous ceramisite (Fe0/AC-ceramisite) made from bentonite, metallic iron, and activated carbon was prepared in a N2 environment, and it exhibited very good performance on aqueous Pb2+ removal under various conditions. SEM/EDX, XRD, and XPS analyses reveal that sorption, reduction, and precipitation were responsible for removing aqueous Pb2+ by the Fe0/AC-ceramisite. This study provides new insights for understanding the effectiveness and mechanisms of the porous ceramisite for aqueous Pb2+ removal and will contribute greatly to solving this significant environmental problem.
|
1. Introduction
Lead (Pb) contamination is a global environmental problem due to its ubiquitous presence in the environment and its damaging toxicity to human beings and ecosystems.1–4 Increasing discharge of Pb-containing wastewater from industries such as storage batteries, automotive, lead smelting, tetraethyl-lead manufacturing, and mining is posing a great threat to water resources and public health.5–8 In fact, Pb is listed second among 275 human toxins in the priority list of hazardous substances.9 According to the World Health Organization (WHO), Pb exposure is annually estimated to account for 143
000 deaths in developing regions and 600
000 new cases of children with intellectual disabilities.10 In order to protect human health, the U.S. Environmental Protection Agency (EPA) has established an action level of 15 μg L−1 for Pb in public drinking water since 1991, which further highlights the need to develop cost-effective Pb removal technologies for industrial wastewater.
Various technologies such as adsorption,11 ion exchange,12 reverse osmosis,13 electrochemical treatment,14 oxidation/reduction methods,15 and chemical precipitation16 have been developed to remove heavy metals from water. However, the practical use of these techniques is often limited by high reagent and energy requirements, incomplete metal removal, expensive equipment, and/or the generation of hazardous waste that requires further treatment.17,18 Take adsorption for example, although using activated carbon (AC), biosorbents (i.e. bacteria and algae), and clay minerals are very effective for heavy metal removal,19–23 the large-scale application of these sorbents is often compromised by the lack of durability and mechanical strength for long-term metal control and difficulties in separation and recovery from the treated effluent.24 Porous ceramisite offers a promising alternative to the existing methods because of its low cost, easy preparation, large available quantities, high mechanical strength, and good performance for simultaneously removing various pollutants, which enable it to provide a long-term and large-scale control for various pollutants.25 Moreover, the bigger particle size of the porous ceramisite, ranging from millimeters to centimeters,26,27 offers the advantages of easier separation from treated water and a reduced pressure drop in flow-through systems over fine particles like AC, biosorbents, and clay minerals.28,29 In fact, porous ceramisite has been commercially available and commonly practiced as the filter medium in wastewater treatment systems, such as constructed wetlands (CWs) and biological aerated filters (BAFs), in China.30–36 However, previous studies have been focused on its effectiveness for the removal of nitrogen, phosphorus, and organic matters.37–41 Up to now, research on porous ceramisite being capable of removing heavy metals from water is scarce, and the underlying removal mechanism also remains largely unknown.
In our previous work, more than 97% of aqueous Pb2+ was removed using an Fe2O3-ceramisite prepared by bentonite, metallic iron powder (Fe0), and AC at 800 °C.29 However, this ceramisite was prepared under air conditions, leading to the oxidation of Fe0 into ferric oxide (Fe2O3) and AC into carbon dioxide (CO2). Thus, the oxidized Fe0 and AC played no contribution to the Pb2+ removal. In order to keep the reactivity of Fe0 and AC for the Pb2+ removal, in this study, a new ceramisite (named as “Fe0/AC-ceramisite”) was prepared by the same raw materials at 800 °C under N2 conditions rather than under air conditions to prevent the oxidation of Fe0 and AC. Previous studies have demonstrated the effectiveness of Fe0 and AC in the removal of various contaminants,19,20,42,43 and the couple of Fe0 and AC is believed to exhibit an enhanced performance owing to the iron–carbon internal electrolysis reaction.44–46 For example, the Fe0/AC couple was capable of removing 100% of As(V) from aqueous solution, whereas only about 60% and 5% of As(V) could be removed by Fe0 alone and AC alone, respectively, under the same conditions.44 Owing to the presence of Fe0 and AC, the removal performance of Pb2+ by Fe0/AC-ceramisite was expected to be enhanced compared with the Pb2+ removal by the Fe2O3-ceramisite. To verify this hypothesis, a series of controlled experiments were conducted under varying conditions, including different ceramisite dosages, initial solution pHs, and initial Pb2+ concentrations. The combined effect of the AC and Fe0 on the Pb2+ removal was studied by comparing the Pb2+ removal efficiencies of Fe0/AC-ceramisite and three control ceramisites, B-ceramisite (made by bentonite only), AC-ceramisite (made by bentonite and AC), and Fe0-ceramisite (made by bentonite and Fe0). The Fe0/AC-ceramisite was characterized using scanning electron microscopy equipped with energy dispersive X-ray spectroscopy (SEM/EDX), X-ray diffraction (XRD), and X-ray photoelectron spectroscopy (XPS) to reveal the removal pathways of Pb2+ by the Fe0/AC-ceramisite.
2. Materials and methods
2.1 Materials
Detailed information of the raw materials including bentonite, Fe0, and AC was described in our previous work.29 Lead nitrate (Pb(NO3)2), (Beijing Chemical Plant, China) was used to prepare the Pb2+ stock solution (1000 mg L−1) with nanopure water (Millipore Milli-Q). Pb2+ working solutions (50, 100, and 200 mg L−1) were obtained by diluting Pb2+ stock solution with nanopure water. The initial pH of the Pb2+ working solution (3.0, 3.8, 4.7, and 5.7) was adjusted by adding 0.1 M HNO3 and/or NaOH. All the chemicals used in this study were analytical grade.
2.2 Ceramisite preparation
The production process of the Fe0/AC-ceramisite included mixing the raw materials, pelletizing, drying, sintering, and cooling. 20% w/w of Fe0, 6% w/w of AC, and 74% w/w of bentonite were well mixed with an appropriate amount of distilled water, and then spherical pellets were manually made, with diameters ranging from 2 to 4 mm. These pellets were then oven dried at 105 ± 5 °C for 3 h, and sintered in an electric tube furnace. The tube furnace temperature was initiated at 25 °C, ramped at 10 °C min−1 to 400 °C and held for 20 min, then ramped at 5 °C min−1 to 800 °C and held for 1 h. Afterwards, the tube furnace gradually cooled down to room temperature within 6 h, and the obtained Fe0/AC-ceramisite was kept dry in sealed storage bags prior to use. Three control ceramisites including AC-ceramisite (made by 6% w/w of AC and 94% w/w of bentonite), Fe0-ceramisite (made by 20% w/w of Fe0 and 80% w/w of bentonite), and B-ceramisite (made by 100% w/w of bentonite) were prepared following the same procedure described above. A N2 environment was supplied during the whole preparation process to prevent oxidation of the Fe0 and AC.
2.3 Pb2+ uptake experiments
Batch experiments were conducted on a thermostatic shaker at 130 ± 10 rpm (20 ± 0.5 °C) to investigate the Pb2+ removal performance by Fe0/AC-ceramisite. The solution pH was recorded at the end of the experiments. To investigate the effect of the ceramisite dosage on the Pb2+ removal, 0.15, 0.25, 0.35, 0.50, 0.60, and 0.70 g of Fe0/AC-ceramisite were added into six conical flasks each containing 50 mL of 200 mg L−1 Pb2+ solution with an initial solution pH of 4.7. After 20 h, the supernatants were sampled and filtered through a 0.45 μm membrane filter (Millipore), and the residual Pb2+ concentrations were determined using an inductively coupled plasma atomic emission spectrometer (ICP-AES, Teledyne Leeman labs prodigy ICP).
To investigate the effect of the initial Pb2+ concentration on the Pb2+ removal kinetics, 2.0 and 4.0 g of Fe0/AC-ceramisite were added into six conical flasks each containing 400 mL of 50, 100, and 200 mg L−1 Pb2+ solutions with an initial solution pH of 4.7. To investigate the effect of the initial solution pH on the Pb2+ removal kinetics, 4.0 g of Fe0/AC-ceramisite was added into four conical flasks each containing 400 mL of 100 mg L−1 Pb2+ solutions with initial solution pHs of 3.0, 3.8, 4.7, and 5.7. At certain reaction time intervals, the supernatants were sampled and filtered for residual Pb2+ concentration measurement. The soluble Fe concentrations in the supernatants were also measured using the ICP-AES during the removal process of Pb2+ by Fe0/AC-ceramisite.
To investigate whether AC and Fe0 had a combined effect on the Pb2+ removal, 0.50 g of B-ceramisite, AC-ceramisite, Fe0-ceramisite, and Fe0/AC-ceramisite were added into four conical flasks each containing 50 mL of 100 mg L−1 Pb2+ solution with an initial solution pH of 4.7. After 20 h, the supernatants were sampled and filtered for residual Pb2+ concentration measurement.
2.4 Characterization methods
The compressive strength of the Fe0/AC-ceramisite was determined according to the previously described procedure.39 The specific surface areas of Fe0/AC-ceramisite, Fe0, and AC were analyzed by using a BET surface area analyzer (Micromeritics ASAP 2010, U.S.A.); element compositions and micrographs of the surface of the Fe0/AC-ceramisite before and after removing the Pb2+ were characterized using a Quanta 200FEG SEM/EDX; crystalline phases of the Fe0/AC-ceramisite before and after removing the Pb2+ were determined using a Rigaku Dmax-2400 XRD analyzer; the detailed information about these three measurements was provided in our previous work.29 The surface composition and the valences of the elements of Fe0/AC-ceramisite before and after removing Pb2+ were investigated using an Axis Ultra XPS with monochromatized Al Kα radiation. Binding energies were calibrated using the C 1s hydrocarbon peak at 284.80 eV to compensate for surface charge effects. Prior to the SEM/EDX, XRD and XPS analyses, the ceramisite samples after the Pb2+ removal were taken out from the liquid and dried at room temperature in a N2 atmosphere. For the XRD and XPS analyses, the dried ceramisite samples were further ground into powder (<200 mesh).
2.5 Data analysis
The removal efficiency R (%) and Pb2+ uptake capacity q (mg g−1) of the tested ceramisites were calculated by eqn (1) and (2), respectively. The first-order kinetic model expressed by eqn (3) was used to determine the Pb2+ uptake rate k (h−1). | 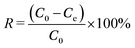 | (1) |
| 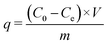 | (2) |
|  | (3) |
where C0, Ct, and Ce (mg L−1) are Pb2+ concentrations at the beginning, time t, and equilibrium, respectively. V (L) is the solution volume and m (g) is the dry weight of the tested ceramisites. The uptake rate constant k (h−1) is the slope of the plot of −ln(Ct/C0) versus time.
3. Results and discussion
3.1 Characterization of the Fe0/AC-ceramisite
Among clays, bentonite is considered as a main candidate for the removal of heavy metals and organic contaminants due to its good adsorption capacity, low cost, and abundant availability.47–49 In particular, the composite of bentonite and Fe0/iron oxides exhibited very good removal performance for heavy metals.48,50–52 However, the application of these composite materials in flow-through systems is not feasible or even possible due to the high pressure drops.53 Besides, after wastewater purification, the composites would become a viscous sludge with a high content of water, which is very difficult for the dewatering process.54 Follow-up treatments have to be considered before disposal of these slurries with high concentrations of heavy metals, thus resulting in increased cost for heavy metals treatment.29 To overcome these issues, in this study, bentonite was used as a supporting material to prepare a porous ceramisite with large diameters of 2–4 mm, which could be easily separated and recovered from treated water. The synthesized Fe0/AC-ceramisite also exhibited a good mechanical strength (6.9 ± 0.3 MPa), meeting China’s standard for filter materials for wastewater treatment (GB 2838-81, compressive strength ≥ 6.5 MPa). Besides, the Fe0/AC-ceramisite had a specific surface area of 106.6 m2 g−1, which was higher than the raw materials, including AC (81.4 m2 g−1) and Fe0 (0.763 m2 g−1). SEM/EDX (Fig. 5a and d) and XRD (Fig. 6) analyses revealed the presence of AC and Fe0 in the Fe0/AC-ceramisite, demonstrating that the N2 environment was effective for protecting the AC and Fe0 from oxidation during the preparation process. Montmorillonite (at 2θ of 19.7°, 29.6°, 34.7°, and 61.8°)55,56 and quartz (at 2θ of 20.9°, 26.4°, and 50.2°)56,57 exhibited small/insignificant peaks, indicating they had poor crystallinity. This could be explained as the calcination at 800 °C breaking the crystal structure of bentonite, making it become amorphous in XRD.58 A similar result was observed by Y. Turhan et al.59 who reported that the peaks of the calcinated bentonite were completely disappeared at 650 °C.
3.2 Pb2+ removal performance of the Fe0/AC-ceramisite
3.2.1 Effect of the ceramisite dosage on the Pb2+ removal.
The effect of the ceramisite dosage on the removal of Pb2+ by the Fe0/AC-ceramisite is shown in Fig. 1. With the increase of ceramisite dosage from 3.0 to 14.0 g L−1, the removal efficiency for Pb2+ increased from 67.8% to 99.9%, while the Pb2+ uptake capacity decreased from 45.2 to 14.3 mg g−1. The higher removal efficiency obtained at elevated ceramisite dosage was because the increasing ceramisite provided a larger amount of active sites for Pb2+ ions, which coincided with previous studies.60 In order to balance the high removal efficiency and the good uptake capacity of Pb2+, a ceramisite dosage of 10 g L−1 was chosen for further studies, unless otherwise stated, since the Pb2+ removal efficiency was greater than 99.5% when the ceramisite dosage was higher than 10 g L−1.
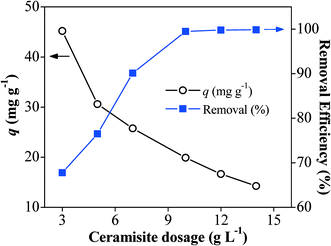 |
| Fig. 1 Effect of the ceramisite dosage (3–14 g L−1) on the removal of Pb2+ by the Fe0/AC-ceramisite. | |
3.2.2 Effect of initial Pb2+ concentration on removal kinetics.
As shown in Fig. 2a and b, the Fe0/AC-ceramisite was very effective for Pb2+ removal with the residual Pb2+ concentration being less than 0.6 mg L−1 and the Pb2+ removal efficiency being higher than 99% at initial Pb2+ concentrations of 50–200 mg L−1 and ceramisite dosages of 5 and 10 g L−1. Our Pb2+ data fit the first-order kinetic model very well with regression coefficient (R2) values higher than 0.9782 under all conditions (Fig. 2c and d). A higher Pb2+ uptake rate constant (k) was obtained at a lower initial Pb2+ concentration and higher ceramisite dosage. For example, at an initial Pb2+ concentration of 50 mg L−1 and ceramisite dosage of 10 g L−1, the Pb2+ uptake rate constant (k) was 1.349 h−1, while at an initial Pb2+ concentration of 200 mg L−1 and ceramisite dosage of 5 g L−1, remarkably k decreased to 0.0699 h−1. This result indicated that a prolonged reaction time was needed, especially at higher initial Pb2+ concentrations and lower ceramisite dosages in order to achieve a good Pb2+ removal efficiency.
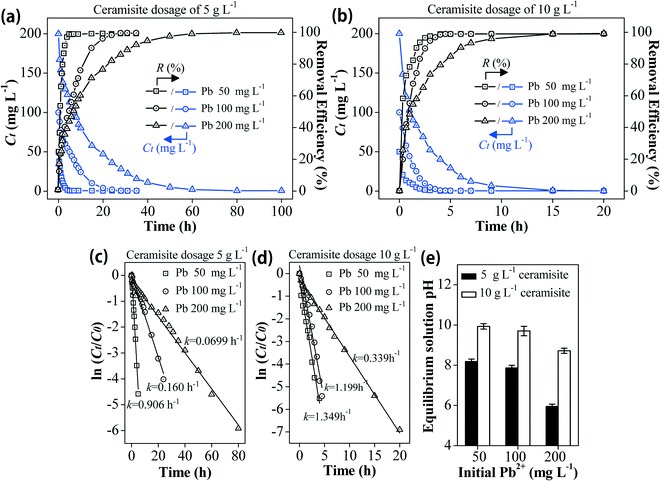 |
| Fig. 2 Effect of the initial Pb2+ concentration (50–200 mg L−1) on the removal kinetics of Pb2+ by the Fe0/AC-ceramisite at ceramisite dosages of 5 g L−1 (a) and 10 g L−1 (b); panels (c) and (d) show the Pb2+ data fitting using the a first-order kinetic model at a ceramisite dosage of 5 g L−1 (R2 ranging from 0.9880 to 0.9943) and 10 g L−1 (R2 ranging from 0.9782 to 0.9969), respectively; and (e) equilibrium solution pH at different initial Pb2+ concentrations. | |
At the initial Pb2+ concentrations of 50, 100, and 200 mg L−1, an elevated solution pH was also observed (Fig. 2e), which increased from 4.7 to 8.2, 7.9, and 6.0 at a ceramisite dosage of 5 g L−1 and to 9.9, 9.7, and 8.7 at a ceramisite dosage of 10 g L−1, respectively. The increased solution pH could be attributed to the reactions between Fe0, water, and dissolved O2 (eqn (4) and (5)),61 in which H+ was consumed by Fe0 in the Fe0/AC-ceramisite:
| 2Fe0 + 4H+ + O2 → 2Fe2+ + 2H2O | (4) |
|  | (5) |
Soluble Fe was also detected during the Pb2+ removal process (shown in Fig. S1 and S2†), further demonstrating that reactions (4) and (5) were involved in the Pb2+ removal. The increased solution pH would lead to a more negatively charged ceramisite surface, enhancing the removal of the positively charged Pb2+ ions through electrostatic attraction.62,63 Besides, the primary forms of Pb in solution would convert from free Pb2+ ions at pH < 7 to Pb(OH)+ and Pb(OH)2 at pH 7–10,64 indicating that precipitation would also contribute to Pb2+ removal (confirmed by XRD analysis in Fig. 6).
3.2.3 Effect of the initial solution pH on the Pb2+ removal kinetics.
As shown in Fig. 3a, the Pb2+ removal efficiency by the Fe0/AC-ceramisite remained over 99.5% despite the initial solution pH increasing from 3.0 to 5.7, indicating that the Fe0/AC-ceramisite was very effective for Pb2+ removal in this pH range. The Pb2+ uptake rate constant (k) decreased linearly from 1.760 h−1 (R2 = 0.9681) at pH 5.7 to 0.323 h−1 (R2 = 0.9879) at pH 3.0 (Fig. 3b and c), suggesting that the lower initial solution pH reduced the Pb2+ removal rate. This result agreed well with other reports, indicating that the removal rate of some pollutants was pH-sensitive60 and thus an optimal solution pH was needed for achieving the best removal performance. Similar to Fig. 2e, an elevated solution pH was also observed at the end of this experiment, and it increased to 9.1, 9.6, 9.7, and 10.2 for initial solution pHs of 3.0, 3.8, 4.7, and 5.7, respectively. Hence, precipitation was expected to be involved in the removal of Pb2+ by the Fe0/AC-ceramisite at an initial solution pH of 3.0–5.7. These results further demonstrated the effectiveness of the Fe0/AC-ceramisite in treating Pb2+-containing solutions at different initial solution pHs.
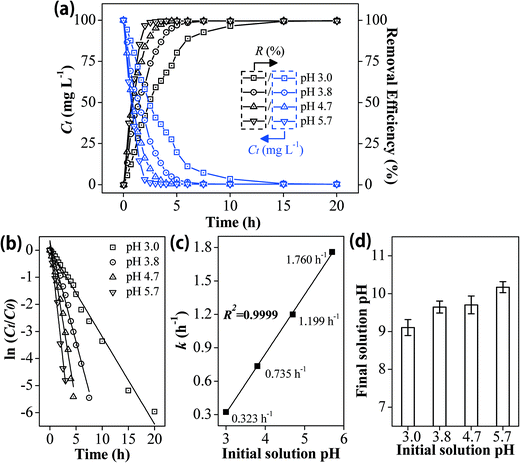 |
| Fig. 3 Effect of the initial solution pH (3.0–5.7) on the removal kinetics of Pb2+ by the Fe0/AC-ceramisite (a); panel (b) shows the Pb2+ data fitting using a first-order kinetic model (R2 ranging from 0.9681 to 0.9879); (c) linear regression between the Pb2+ uptake rate constant (k) and the initial solution pH; and (d) equilibrium solution pH at different initial solution pHs. | |
3.2.4 The combined effect of AC and Fe0 on Pb2+ removal.
As shown in Fig. 4, the Fe0/AC-ceramisite achieved the highest Pb2+ removal efficiency (99.5%) compared with the B-ceramisite (4.8%), AC-ceramisite (7.8%), and Fe0-ceramisite (39.6%). Assuming that there were no combined effects between AC and Fe0 on the Pb2+ removal, the individual Pb2+ uptake capacities of Fe0, AC, and bentonite would be 17.9, 5.5, and 0.5 mg g−1 based on the their mass percentages and the Pb2+ removal efficiencies of these three control ceramisites. Thus, the Pb2+ uptake capacity of the Fe0/AC-ceramisite would theoretically be 4.3 mg g−1, which was much lower than its obtained Pb2+ uptake capacity (10.0 mg g−1). This discrepancy indicated that the combined effect between Fe0 and AC was likely involved in the enhanced Pb2+ removal by the Fe0/AC-ceramisite. According to previous studies, the combined effect was attributed to the iron–carbon micro-electrolysis reaction, in which Fe(II), hydroxyl, and atomic hydrogen were released, enhancing the reactivity of Fe0 for the removal of heavy metals and organic contaminants.44–46
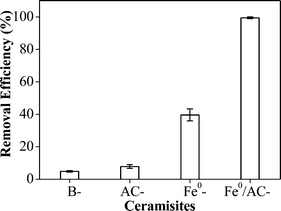 |
| Fig. 4 Comparison of Pb2+ removal efficiencies of the Fe0/AC-ceramisite, B-ceramisite, AC-ceramisite, and Fe0-ceramisite. | |
3.3 Pb2+ removal mechanisms
3.3.1 SEM/EDX and XRD analyses.
To investigate the removal mechanisms of Pb2+, the SEM/EDX and XRD techniques were applied to characterize the Fe0/AC-ceramisite before and after the removal of Pb2+. As shown in Fig. 5b and c, two new mineral phases containing Pb were developed on the surface of the Fe0/AC-ceramisite after Pb2+ removal compared with the original ceramisite (Fig. 5a). The corresponding EDX spectra (Fig. 5f and g) revealed that the Pb mass percentages in the prismatic and cuboid crystals were 79.1% and 73.9%, which were close to the mass percentages of Pb in Pb3(CO3)2(OH)2 (80.1%) and PbCO3 (77.5%), respectively. The slight discrepancy could be due to the emergence of some other elements (such as Si, Al, and Fe) during the formation of these Pb-containing crystals, therefore reducing the Pb concentration after the reaction. XRD analysis (Fig. 6) further confirmed the presence of PbCO3 and Pb3(CO3)2(OH)2, suggesting that Pb2+ could be removed from water by precipitation of PbCO3 and Pb3(CO3)2(OH)2. This result coincided well with previous studies56,65 and the carbonates were previously reported to originate from atmospheric CO2
56,66,67 and/or impurities such as calcite65 present in the bentonite. Besides, Pb2+ may also be removed from solution via sorption by AC, as shown in Fig. 5d; although no Pb-containing crystals were observed, 10.6% Pb was present on the AC by EDX analysis. Compared to the XRD pattern of the Fe0/AC-ceramisite before Pb2+ removal, Fig. 6 shows the presence of Pb0, which is located at 55.39° and 62.39°,42 suggesting that the Fe0/AC-ceramisite could also remove Pb2+ from solution by the reduction of the Pb2+ to Pb0. This was evidenced by the standard reduction potential of Pb2+/Pb0 (−0.13 V) being higher than that of Fe2+/Fe0 (−0.41 V),51 leading to the occurrence of the electrochemical reaction between Pb2+ and Fe0. In the meantime, Fe0 was oxidized into iron oxides such as γ-FeOOH and Fe3O4 after removing Pb2+ (Fig. 6).
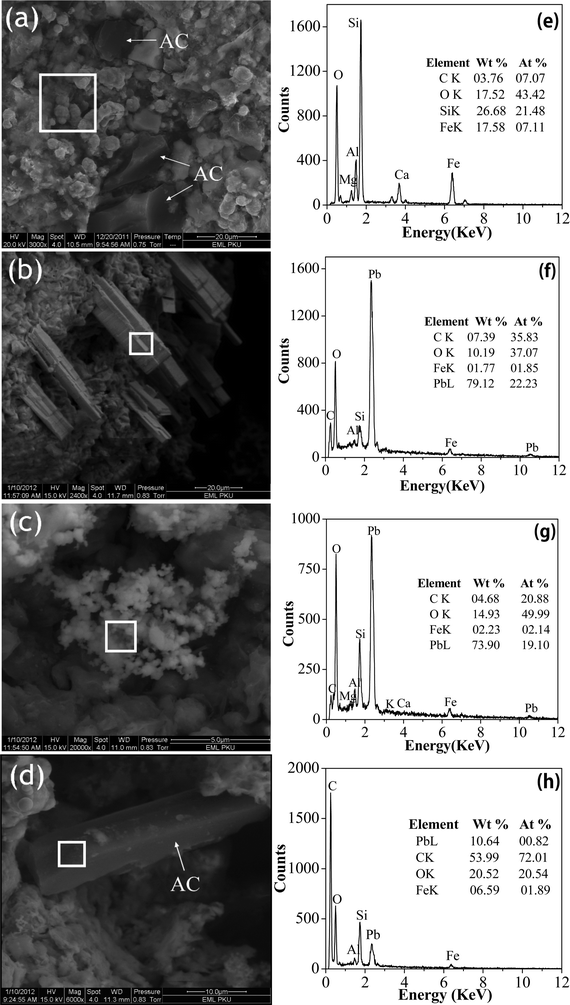 |
| Fig. 5 SEM/EDX results of the Fe0/AC-ceramisite before (a and e) and after (b and f, c and g, d and h) Pb2+ removal. For the EDX spectra, only the top four major elements were listed. | |
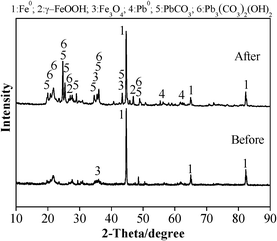 |
| Fig. 6 XRD patterns of the Fe0/AC-ceramisite before and after Pb2+ removal. | |
3.3.2 XPS analysis.
The XPS technique was employed to identify the valence states of Fe and Pb in the Fe0/AC-ceramisite. As shown in Fig. 7a, the elements O, Fe, Mg, C, Si, and Al were observed in the Fe0/AC-ceramisite samples both before and after Pb2+ removal, whereas the element Pb could be only detected in the Fe0/AC-ceramisite sample after Pb2+ removal. From the obtained high-resolution Pb 4f spectrum (Fig. 7b), two peaks centred at 141.5 eV (Pb 4f5/2) and 136.8 eV (Pb 4f7/2) were observed. According to ref. 42 and 68, these peaks could be assigned to the Pb oxidized state Pb2+, which was in good agreement with our SEM/EDX and XRD analyses that PbCO3 and Pb3(CO3)2(OH)2 were formed on the Fe0/AC-ceramisite after Pb2+ removal. The high-resolution Fe 2p spectra (Fig. 7c) of the Fe0/AC-ceramisite after the Pb2+ removal showed two peaks centred at 726.2 eV (Fe 2p1/2) and 712.5 eV (Fe 2p3/2), which were in close agreement with Fe2+/Fe3+ at 725.2 eV and Fe3+ at 710.7 eV, respectively.69 This observation implied that the Fe0 in the Fe0/AC-ceramisite after the Pb2+ removal was enveloped by a layer of iron oxides such as γ-FeOOH and Fe3O4 (confirmed in Fig. 6). Although both Pb0 and Fe0 were observed by XRD analysis, neither of them appeared in the XPS patterns, which may result from the 10 nm detection depth of XPS.
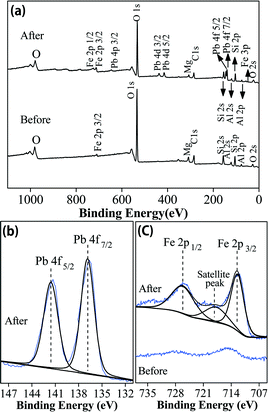 |
| Fig. 7 XPS patterns of the Fe0/AC-ceramisite before and after Pb2+ removal: (a) wide-scan survey; (b) high-resolution XPS spectrum of Pb; and (c) high-resolution XPS spectra of Fe. | |
Based on the results described above, the Pb2+ removal mechanism by the Fe0/AC-ceramisite involves three components: one is that Pb2+ ions in aqueous solution are absorbed by the AC in the Fe0/AC-ceramisite since the AC can absorb the metal ions;70 one is that the Pb2+ ions can precipitate in the forms of PbCO3 and Pb3(CO3)2(OH)2 on the surface of the Fe0/AC-ceramisite; another is that some of the absorbed Pb2+ can be reduced by Fe0 to Pb0. Through these three pathways, the Fe0/AC-ceramisite could effectively remove Pb2+ ions from the aqueous solution and thus it could be considered as a promising filter medium for the existing wastewater treatment systems in China.
4. Conclusions
In this study, a novel porous ceramisite, Fe0/AC-ceramisite, was prepared with bentonite, Fe0, and AC by sintering at 800 °C in a N2 environment. Batch experiments have demonstrated its effectiveness in removing Pb2+ ions from water under various environmental conditions. The Pb2+ removal efficiency was enhanced by the addition of AC in the Fe0/AC-ceramisite due to the iron–carbon micro-electrolysis reaction, and the Pb2+ uptake rate was influenced by initial Pb2+ concentration, initial solution pH, and ceramisite dosage. The results obtained from SEM/EDX, XPS, and XRD indicated that the Fe0/AC-ceramisite was capable of removing Pb2+ ions via reduction, sorption, and precipitation. The synthesized Fe0/AC-ceramisite offers a great potential for the Pb2+ removal from wastewater.
Acknowledgements
We acknowledge the two anonymous reviewers for their thorough, insightful, and constructive comments that have significantly improved the paper. This work was supported by the National Natural Science Foundation of China (no. 21077002 and 41201532). Li Yuan acknowledges support from the China Scholarship Council (CSC) visiting scholarship.
References
- G. Flora, D. Gupta and A. Tiwari, Interdiscip. Toxicol., 2012, 5(2), 47–58 CrossRef CAS PubMed.
- M. I. Khan, N. Islam, A. A. Sahasrabuddhe, A. A. Mahdi, H. Siddiqui, M. Ashquin and I. Ahmad, J. Hazard. Mater., 2011, 189(1), 255–264 CrossRef CAS PubMed.
- D. A. Gidlow, Lead toxicity, Occup. Med., 2004, 54(2), 76–81 CrossRef CAS PubMed.
- L. Yuan, W. Zhi, Y. Liu, S. Karyala, P. J. Vikesland, X. Chen and H. Zhang, Environ. Sci. Technol., 2015, 49(2), 824–830 CrossRef CAS PubMed.
- T. Bahadir, G. Bakan, L. Altas and H. Buyukgungor, Enzyme Microb. Technol., 2007, 41(1), 98–102 CrossRef CAS PubMed.
- R. Shanmugavalli, P. Shabudeen, R. Venckatesh, K. Kadirvelu, S. Madhavakrishnan and S. Pattabhi, Uptake of Pb(II) ion from aqueous solution using silk cotton hull carbon: an agricultural waste biomass, J. Chem., 2006, 3(4), 218–229 CAS.
- M. M. Matlock, B. S. Howerton and D. A. Atwood, Ind. Eng. Chem. Res., 2002, 41(6), 1579–1582 CrossRef CAS.
- J. R. Peralta-Videa, M. L. Lopez, M. Narayan, G. Saupe and J. Gardea-Torresdey, Int. J. Biochem. Cell Biol., 2009, 41(8), 1665–1677 CrossRef CAS PubMed.
-
ATSDR (Agency for Toxic Substances and Disease Registry), Priority List of Hazardous Substances, http://www.atsdr.cdc.gov/SPL/, Accessed 7 May, 2014 Search PubMed.
-
WHO (World Health Organization), Lead poisoning and health, http://www.who.int/mediacentre/factsheets/fs379/en/, Accessed October, 2014 Search PubMed.
- M. Kobya, E. Demirbas, E. Senturk and M. Ince, Bioresour. Technol., 2005, 96(13), 1518–1521 CrossRef CAS PubMed.
- A. D
browski, Z. Hubicki, P. Podkościelny and E. Robens, Chemosphere, 2004, 56(2), 91–106 CrossRef PubMed.
- H. Ozaki, K. Sharma and W. Saktaywin, Desalination, 2002, 144(1), 287–294 CrossRef CAS.
- M. Hunsom, K. Pruksathorn, S. Damronglerd, H. Vergnes and P. Duverneuil, Water Res., 2005, 39(4), 610–616 CrossRef CAS PubMed.
- S. Chen, W. Chen and C. Shih, Water Sci. Technol., 2008, 58(10), 1947–1954 CrossRef CAS PubMed.
- M. M. Matlock, B. S. Howerton and D. A. Atwood, Water Res., 2002, 36(19), 4757–4764 CrossRef CAS.
- O. Chaalal, A. Y. Zekri and R. Islam, Energy Sources, 2005, 27(1–2), 87–100 CrossRef CAS PubMed.
- E. Malkoc, Y. Nuhoglu and M. Dundar, J. Hazard. Mater., 2006, 138(1), 142–151 CrossRef CAS PubMed.
- M. Corapcioglu and C. Huang, Water Res., 1987, 21(9), 1031–1044 CrossRef CAS.
- K. Pyrzyńska and M. Bystrzejewski, Colloids Surf., A, 2010, 362(1), 102–109 CrossRef PubMed.
- M. Pazirandeh, B. M. Wells and R. L. Ryan, Appl. Environ. Microbiol., 1998, 64(10), 4068–4072 CAS.
- T. A. Davis, B. Volesky and A. Mucci, Water Res., 2003, 37(18), 4311–4330 CrossRef CAS.
- E. Alvarez-Ayuso and A. Garcia-Sanchez, Clays Clay Miner., 2003, 51(5), 475–480 CrossRef CAS.
- G. M. Gadd, J. Chem. Technol. Biotechnol., 2009, 84(1), 13–28 CrossRef CAS PubMed.
- G. Xu, J. Zou and G. Li, Water Res., 2009, 43(11), 2885–2893 CrossRef CAS PubMed.
- S. Z. Yuan, H. Lu, J. Wang, J. T. Zhou, Y. Wang and G. F. Liu, Process Biochem., 2012, 47(2), 312–318 CrossRef CAS PubMed.
- C. Zhang, K. Wang, S. Tan, X. Niu and P. Su, Chem. Ecol., 2013, 29(8), 668–675 CrossRef CAS PubMed.
- B. Pan, Q. Zhang, W. Zhang, B. Pan, W. Du, L. Lv, Q. Zhang, Z. Xu and Q. Zhang, J. Colloid Interface Sci., 2007, 310(1), 99–105 CrossRef CAS PubMed.
- L. Yuan and Y. Liu, Chem. Eng. J., 2013, 215, 432–439 CrossRef PubMed.
- W. Zhi, L. Yuan, G. Ji and C. He, Environ. Sci. Technol., 2015, 49(7), 4575–4583 CrossRef CAS PubMed.
- W. Zhi and G. Ji, Water Res., 2014, 64, 32–41 CrossRef CAS PubMed.
- W. Zhi and G. Ji, Sci. Total Environ., 2012, 441, 19–27 CrossRef CAS PubMed.
- G. Ji, R. Wang, W. Zhi, X. Liu, Y. Kong and Y. Tan, Distribution patterns of denitrification functional genes and microbial floras in multimedia constructed wetlands, Ecol. Eng., 2012, 44, 179–188 CrossRef PubMed.
- W. Weiliang, Procedia Environ. Sci., 2012, 12, 79–86 CrossRef PubMed.
- S. Cao, W. Chen and Z. Jing, Afr. J. Biotechnol., 2014, 11(16), 3825–3831 Search PubMed.
- M. Wu, Q. Li, X. Tang, Z. Huang, L. Lin and M. Scholz, Int. J. Environ. Anal. Chem., 2014, 94(6), 618–638 CrossRef CAS PubMed.
- M. Hartman, O. Trnka and M. Pohorelý, Ind. Eng. Chem. Res., 2007, 46(22), 7260–7266 CrossRef CAS.
- Y. Liu, F. Du, L. Yuan, H. Zeng and S. Kong, J. Hazard. Mater., 2010, 178(1), 999–1006 CrossRef CAS PubMed.
- J. L. Zou, G. R. Xu, K. Pan, W. Zhou, Y. Dai, X. Wang, D. Zhang, Y. Hu and M. Ma, Sep. Purif. Technol., 2012, 94, 9–15 CrossRef CAS PubMed.
- G. Ji, Y. Zhou and J. Tong, Environ. Eng. Sci., 2010, 27(10), 871–878 CrossRef CAS.
- M. Ji, W. Liu, J. Zhou and L. Sun, A Study of Pre-Treatment of Slightly-Polluted Water with Biological Ceramsite Filter Tank, Gongye Yongshui Yu Feishui, 2003, 34(6), 22–25 CAS.
- X. Zhang, S. Lin, Z. Chen, M. Megharaj and R. Naidu, Water Res., 2011, 45(11), 3481–3488 CrossRef CAS PubMed.
- S. M. Ponder, J. G. Darab and T. E. Mallouk, Environ. Sci. Technol., 2000, 34(12), 2564–2569 CrossRef CAS.
- X. Dou, R. Li, B. Zhao and W. Liang, J. Hazard. Mater., 2010, 182(1), 108–114 CrossRef CAS PubMed.
- L. Fan, J. Ni, Y. Wu and Y. Zhang, J. Hazard. Mater., 2009, 162(2), 1204–1210 CrossRef CAS PubMed.
- B. Liang, Q. Yao, H. Cheng, S. Gao, F. Kong, D. Cui, Y. Guo, N. Ren and A. Wang, Environ. Sci. Pollut. Res., 2012, 19(5), 1385–1391 CrossRef CAS PubMed.
- M. Jiang, X. Jin, X. Lu and Z. Chen, Desalination, 2010, 252(1), 33–39 CrossRef CAS PubMed.
- M. Ranđelović, M. Purenović, A. Zarubica, J. Purenović, B. Matović and M. Momčilović, J. Hazard. Mater., 2012, 199, 367–374 CrossRef PubMed.
- D. Tomašević, G. Kozma, D. V. Kerkez, B. Dalmacija, M. Dalmacija, M. Bečelić-Tomin, Á. Kukovecz, Z. Kónya and S. Rončević, J. Nanopart. Res., 2014, 16(8), 1–15 CrossRef.
- L. Shi, X. Zhang and Z. Chen, Water Res., 2011, 45(2), 886–892 CrossRef CAS PubMed.
- Y. Zhang, Y. Li, J. Li, G. Sheng, Y. Zhang and X. Zheng, Chem. Eng. J., 2012, 185, 243–249 CrossRef PubMed.
- Y. Li, J. Li and Y. Zhang, J. Hazard. Mater., 2012, 227, 211–218 CrossRef PubMed.
-
L. Z. Pillon, Interfacial properties of petroleum products, CRC Press, 2007, p. 205 Search PubMed.
- H. Wright and J. Kitchener, J. Colloid Interface Sci., 1976, 56(1), 57–63 CrossRef CAS.
- E. Eren and B. Afsin, J. Hazard. Mater., 2008, 151(2), 682–691 CrossRef CAS PubMed.
- H. Zhang, Z. Tong, T. Wei and Y. Tang, Appl. Clay Sci., 2012, 65, 21–23 CrossRef PubMed.
- S. Hashemian, H. Saffari and S. Ragabion, Water, Air, Soil Pollut., 2015, 226(1), 1–10 CrossRef.
- B. Ritherdon, C. R. Hughes, C. D. Curtis, F. R. Livens, J. F. Mosselmans, S. Richardson and A. Braithwaite, Appl. Geochem., 2003, 18(8), 1121–1135 CrossRef CAS.
- Y. Turhan, Z. G. Alp, M. Alkan and M. Doğan, Microporous Mesoporous Mater., 2013, 174, 144–153 CrossRef CAS PubMed.
- M. Hou, C. Ma, W. Zhang, X. Tang, Y. Fan and H. Wan, J. Hazard. Mater., 2011, 186(2), 1118–1123 CrossRef CAS PubMed.
- R. Crane and T. Scott, J. Hazard. Mater., 2012, 211, 112–125 CrossRef PubMed.
- H. Elliott and C. Huang, Water Res., 1981, 15(7), 849–855 CrossRef CAS.
- O. Abollino, M. Aceto, M. Malandrino, C. Sarzanini and E. Mentasti, Water Res., 2003, 37(7), 1619–1627 CrossRef CAS.
- S. Yang, D. Zhao, H. Zhang, S. Lu, L. Chen and X. Yu, J. Hazard. Mater., 2010, 183(1), 632–640 CrossRef CAS PubMed.
- A. Nakano, L. Li, M. Ohtsubo, A. Mishra and T. Higashi, Environ. Technol., 2008, 29(5), 505–514 CrossRef CAS PubMed.
- F. Bouchelaghem and N. Jozja, Eng. Geol., 2009, 108(3), 286–294 CrossRef PubMed.
- R. Herrera-Urbina and D. Fuerstenau, Colloids Surf., A, 1995, 98(1), 25–33 CrossRef CAS.
-
C. D. Wagner and G. Muilenberg, Handbook of x-ray
photoelectron spectroscopy: a reference book of standard data for use in x-ray photoelectron spectroscopy, Perkin-Elmer Corp., 1979 Search PubMed.
- H. Peng, Z. Mo, S. Liao, H. Liang, L. Yang, F. Luo, H. Song, Y. Zhong and B. Zhang, Sci. Rep., 2013, 3, 1765 Search PubMed.
- A. Netzer and D. Hughes, Water Res., 1984, 18(8), 927–933 CrossRef CAS.
Footnote |
† Electronic supplementary information (ESI) available. See DOI: 10.1039/c5ew00091b |
|
This journal is © The Royal Society of Chemistry 2015 |
Click here to see how this site uses Cookies. View our privacy policy here.