In this study, we highlight three current and delicate issues of SEI investigations for nano-silicon electrodes in Li-ion batteries: (I) the washing procedure for reliable post-mortem electrode characterization is addressed which is based on a short sonication treatment verified as an effective non-destructive procedure to remove only electrolyte components from the surface. (II) We focus on the superior electrochemical performance due to the addition of FEC and discuss the role of interfacial compounds in silicon electrodes, in particular Li2O, LiF and phosphates formed during electrochemical cycling. (III) The significant effect of two well-known binders for silicon-based electrodes, namely carboxymethyl cellulose/styrene-butadiene rubber (CMC/SBR)31 and polyacrylic acid (PAA),34 on SEI formation on nanoparticulate silicon is fundamentally investigated. As the Si anodes prepared with the help of the aforementioned binders show similar electrochemical performance and characteristics in the pristine state, post-mortem characterization identifies different organic surface species induced by just changing the binder. A model for the SEI formation is proposed and major challenges obtained in comparing the literature results under unique experimental conditions are discussed. We highlight the SEI properties and the SEI formation mechanism on silicon nanocrystallites with 2–5 nm in size embedded in a porous carbon scaffold after 400 galvanostatic cycles at high current rates for example for highly reversible and highly stable nanoparticulate Si-based negative electrode materials.
3.3.2 FEC effects on SEI formation.
For clarity, we applied the sonication procedure to remove any electrolyte components. EDXS (Table 1) provides valuable information of the elemental composition of the entire post-mortem electrode. It reveals the lowest silicon and highest carbon content cycled in the additive-free electrolyte suggesting pronounced decomposition of electrolyte components. For the additive-containing electrolyte an increase of silicon concentration from approximately 7 wt% to about 10 wt% and a lower carbon concentration are observed. This result points to less organic material and thus weaker decomposition of the electrolyte. A significant difference is detected for the fluorine concentration which is eight times higher in the presence of FEC as electrolyte additive. A larger amount of additive decomposed during cycling is concluded from these observations and is also in accordance with recent reports.18,20 Interestingly, considerable amounts of phosphorus are only present when FEC is used.
Table 1 Elemental composition of the silicon electrode with CMC/SBR as a binder after 400 time cycling depending on FEC addition determined by EDXS
Sample |
Si (at%) |
C (at%) |
O (at%) |
F (at%) |
P (at%) |
w/o FEC |
6.8 |
42.1 |
48.8 |
2.2 |
0 |
With FEC |
10 |
37.8 |
39.5 |
11.1 |
0.7 |
X-ray diffraction gives insights about structure and morphology of the entire post-mortem electrode and the results are depicted in Fig. 5. No reflections appear in the case of the additive-free sample, indicating a completely amorphous material. Note that the silicon reflections typically disappear after cycling due to an amorphization process during lithiation.42 In the case of FEC, we observe the reflections of LiF with a cubic crystal structure (Fm
m). From the XRD pattern a crystallite size of roughly 4 nm is determined by Rietveld analysis. The formation of crystalline LiF is also confirmed by TEM (Fig. 5b). The bright-field images show an agglomeration of the porous carbon scaffold attached to silicon nanoparticles after cycling. A high-resolution analysis is impossible because the high-energy electron beam decomposes the SEI components. However, selected area electron diffraction (SAED) proves the formation of nanocrystalline LiF only for the addition of FEC. LiF is often detected by XPS measurements, but has not yet been reported in diffraction experiments after cycling. It is likely formed in the initial cycles where a two-phase transition is observed which suggests a precipitation from the liquid phase. The role of fluorides in Li-ion batteries is controversially discussed.43 LiF is recognized as an insulator for both lithium ions and electrons and its formation should be avoided.44 In contrast to this, LiF is often associated, among other compounds, as a SEI-stabilizing component for silicon-based electrodes resulting in an enhanced cycling stability.13,26,45,46 The rather controversial literature reports suggest that LiF may be neither beneficial nor disadvantageous for the reversibility. From the aspect of diffraction experiments, we can detect LiF only in the presence of FEC. From this point of view LiF indeed supports a better cycling stability. However, since most of the material is amorphous, further information for evaluation is provided by XPS measurements.
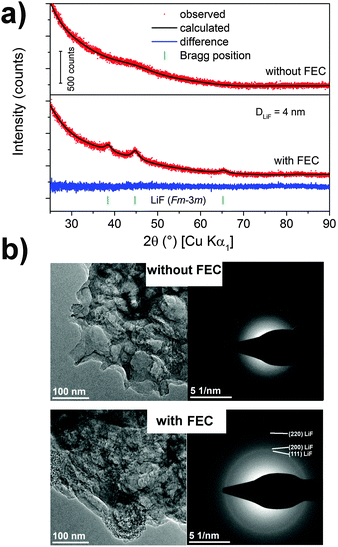 |
| Fig. 5 (a) XRD pattern and (b) TEM bright-field images (left) with selected area electron diffraction (SAED) (right) of the cycled silicon electrodes with CMC/SBR depending on FEC addition. | |
Fig. 6 displays the XPS results and the chemical composition. We detect a concentration of ∼1 at% silicon for both samples. Higher amounts of lithium in the FEC sample indicate lithium salts as major components of the interfacial layer on silicon. Further differences are found in the carbon/oxygen ratio and the fluorine concentration. With FEC the carbon/oxygen ratio is higher (1.31) than without additive (0.8). The fluorine and phosphorus concentration is up to five times higher with FEC suggesting high decomposition of the additive and an integration of hydrolysis products of LiPF6 into the SEI. Higher amounts of phosphorus with FEC addition were reported by Elazari et al. and Chen et al. on, respectively, thin silicon films and silicon nanoparticles, suggesting pronounced decomposition of the conductive salt as well as the integration of the products into the SEI.17,22 However, almost no phosphorus is detected without the additive.
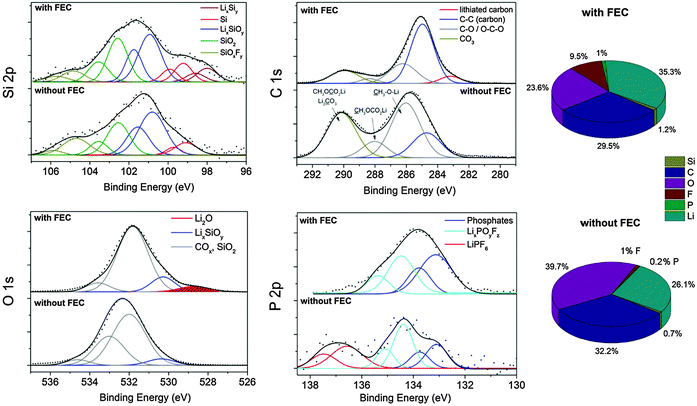 |
| Fig. 6 XP spectra and concentrations of the silicon electrodes with CMC/SBR as a binder cycled 400 times depending on FEC addition. | |
Both Si 2p spectra in Fig. 6 show signals with a maximum at approximately 101 eV which correspond to LixSiOy.24 This compound is an initial reaction product of lithium with SiO2 which is present in large concentrations on the pristine electrode (Fig. 1). From literature24 it is known that SiO2 undergoes different reactions during cycling which are summarized here:
| SiO2 + 4Li → Si + 2Li2O | (I) |
| 2SiO2 + 4Li → Si + Li4SiO4 | (II) |
| SiO2 + HF → SiOxFy + H2O | (III) |
The release of HF is a by-product of the reaction of the PF
6− ion with traces of water and the decomposition of the FEC additive. From
reactions (I)–(III), it is clear that large amounts of both Li
2O and Li
4SiO
4 can be formed during the first discharge process which was reported by Philippe
et al.25 For the additive-free sample we additionally observe a shoulder at 105 eV which corresponds to fluorinated silicon suboxides (SiO
xF
y)
25 and SiO
2. SiO
2 may partially be the result of residues from the glass fiber separator. Considering the sample cycled in the FEC-containing electrolyte, an additional elemental silicon signal at 99 eV is present which corresponds to the active material for reversible lithium storage. By fitting each silicon species we determined an elemental silicon contribution of approximately 23% whereas the additive-free sample shows less than 10%. This observation suggests a very thin initial SEI of less than 4 nm in the case of additional FEC since the XP attenuation length of laboratory X-ray sources (here, 1253.6 eV energy) is around 2–3 nm.
The total amount of carbon–oxygen (COx) species on the pristine electrode was estimated to be 34%. After cycling in the additive-free electrolyte the C 1s binding energy position features a maximum at 285.7 eV majorly corresponding to C–O species and to conductive carbon (C–C species at 284.5 eV).47 A second local maximum at 290 eV is observed caused by lithium carbonates and diverse semi organic lithium carbonates. These results evidence the presence of (CH2OCO2Li)2, CH3OCO2Li, CH3OLi and Li2CO3 as typical SEI components in alkyl carbonates.41 The total amount of COx species increased to 83% indicating a strong electrolyte decomposition. With FEC as an additive the dominant signal is shifted to 284.9 eV which majorly corresponds to the conductive carbon scaffold as a result of the thin SEI. The low energy signal at 283 eV corresponds to lithiated carbon.48 Only low amounts of CO3 and C–O species with a total concentration of 39% are present which is only slightly higher than for the pristine electrode (34%). This observation provides the proof of a negligible decomposition of the electrolyte solvents DMC and EC. The low concentration of CO3/C–O species and the high intensity of C–C/C–H bonds point to the formation of a thin layer-like polymer, presumably a vinyl polymer with functional C–O/CO3 groups, on the silicon–carbon composite. It was proposed that FEC can decompose to HF and vinylene carbonate which oligomerizes to polycarbonates as the stable SEI on silicon.19 Vinylene carbonate has been proven to be an effective stabilizer in LIBs owing to the formation of stable polycarbonates.49 Nakai et al.20 proposed HF and Li2CO3 formation by a ring opening reaction of FEC and its subsequent polymerization to a vinyl polymer. A recent report17 suggests the formation of poly(-vinyl carbonates).
The binding energy position of the Li 1s core level spectra (Fig. S4, ESI†) is located at about 56 eV for both samples and corresponds to various lithium salts in the SEI.48 The characteristics in the O 1s spectrum are similar. For the additive-free a peak maximum at 532.5 eV is observed. The addition of FEC shifts this peak maximum to lower energies (531.5 eV). Higher energies indicate the presence of more COx species whereas the lower O 1s binding energy position is attributed to the presence of LixSiOy which is supposed to be a major component of the SEI on silicon.24 Taking into account the integrated peak area and the silicon/oxygen concentration, we determined a stoichiometric oxygen number of about 3 for the additive-free sample and 4 with FEC according to reaction (II). Interestingly, we observe a peak maximum at 528.5 eV only in the FEC sample which corresponds to Li2O. Li2O is typically formed in the first cycle due to the reaction of SiO2 with lithium, as explained earlier (reaction (I)). Philippe et al.24 reported that Li2O was reversibly detected in nano-silicon anodes even after many cycles but seems to disappear owing to a dissolution by HF from the decomposition of FEC and LiPF6:
| Li2O + 2HF → 2LiF + 2H2O | (IV) |
To further investigate the presence of Li
2O, we sputtered the sample for 5 min in order to remove the first 15–20 nm of the surface. Although sputtering is known as a destructive method, it does not necessarily destroy all chemical compounds in the SEI. Previous investigations of metallic lithium anodes show that Li
2O is stable during sputtering with an Ar
+ beam.
50 After sputtering (
Fig. 7), the Li
2O peak in the O 1s spectrum appears significantly more intense in the case of the FEC sample. In contrast, no Li
2O is observed in the sample cycled in the additive-free electrolyte. Note that Li
2O can also be formed by decomposition of lithium carbonate by Ar
+ sputtering. However, if this reaction occurs, Li
2O will be predominantly present in the additive-free electrolyte due to the higher amount of carbonates in the SEI. The results indicate that Li
2O must be located between the silicon and the upper SEI and can be retained with FEC addition. We will also consider the C 1s energy (
Fig. 7) after sputtering to show that the results for carbon species are reasonable. The peak maximum is shifted to lower energies as a result of the partially uncovered carbon scaffold and residues of lithiated carbon in both samples. Furthermore, the amount of CO
x compounds decreases due to the removed SEI matrix. These observations agree well with results from non-destructive depth-profiling.
24,48 Based on this observation, we propose that the thin SEI formed with FEC is sufficiently stable to prevent the dissolution of Li
2O by HF. This result is surprising since HF readily diffuses through any thin polymer. The SEI formed with FEC effectively suppresses HF diffusion and is chemically very stable. This property of the SEI is in accordance with a recent study which proved good thermal stability of the SEI formed with FEC of up to 200 °C on highly reactive lithiated silicon.
23 Another study reports an enhanced reversibility for nano-silicon anodes with the conductive salt lithium bis(fluorosulfonyl)imide (LiFSI) as well.
14 Similar to FEC, the dissolution of Li
2O was successfully suppressed here but could be rather a result of a weaker HF generation from the more stable LiFSI salt (compared to LiPF
6) than from a protective layer. However, it suggests that an inhibited dissolution of Li
2O and its formation from silicon dioxide may be a good indication for better cycle stability.
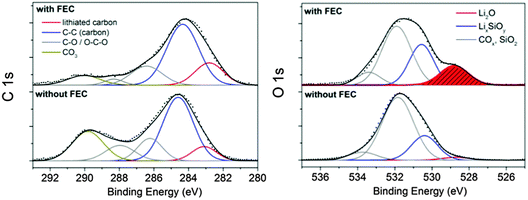 |
| Fig. 7 XP spectra of the silicon electrodes with CMC/SBR as a binder cycled 400 times depending on FEC addition after Ar+ ion sputtering (∼15 nm surface removal). | |
The F 1s spectrum (Fig. S5, ESI†) of the additive-free sample in the non-sputtered state consists of a signal at 687.7 eV with low intensity and a distinct signal at 685.5 eV corresponding to traces of LiPF6, LixPOyFz and LiF, respectively. The phosphorus species are confirmed by the P 2p spectrum (Fig. 6). The signal at 137.5 eV points to traces of the conductive salt and the one at 134.5 eV to partially fluorine-substituted phosphates (reaction (V)). The presence of fluorine-substituted phosphates as part of the SEI after cycling in a conventional carbonate-based electrolyte has been reported previously.19,22,25 The concentrations of these phosphates seem to vary noticeably. Our results suggest that negligible concentrations of partially fluorinated phosphates participate in the SEI formation on silicon in the additive-free electrolyte. With addition of FEC, the F 1s spectrum exhibits solely one signal at 685.5 eV corresponding to (nanocrystalline) LiF as already confirmed with XRD. The LiF cannot be present as a closed layer since a crystallite size of 4 nm (determined by diffraction experiments) in a layer-like structure would cause the absence of any other signal in the XP spectrum as a result of the low attenuation length of these photons (2–3 nm) at this energy. Thus, the overall morphology of LiF is present as nanoparticles or as a fragmentary scaffold. This finding contradicts a recent work suggesting that a layer-like structure of LiF stabilizes the SEI.26 Our findings support other reports attributing the enhanced reversibility to an organic polymeric film structure.40 The P 2p spectrum (Fig. 6) reveals a binding energy position at 134.0 eV proving the presence of majorly phosphates and fluorine-substituted phosphates. The presence of FEC causes the hydrolysis of considerable amounts of LiPF6 to (fluorinated) phosphates which are integrated into the inorganic part of the SEI. The general reaction path of the phosphate formation was described in literature.25 (reaction (V)).
| PF6− + H2O → POF3− + 2HF | (V) |
Hence, more water is generated in the presence of an additive, which may be formed by the reaction of silica and Li
2O with HF (
reaction (III) and (IV)). Latter is generated by the decomposition of the fluorine additive. Similar results were reported by Choi
et al.13 and Elazari
et al.22 on thin silicon films. Hydrolysis of PF
6− ions is considered as a major factor for irreversible capacity loss in LIBs, but it seems to influence the electrochemical performance positively. This behavior is consistent with a report of Dalavi
et al.15 who observed a positive effect for the incorporation of decomposed LiPF
6 into the SEI. However, in a recent study dealing with silicon nanoparticles (>50 nm) less decomposition of PF
6− was observed when FEC is added.
40 This observation may result from less silicon dioxide on large silicon nanoparticles which is considered as a major reason for a pronounced water generation (
reaction (III)). We propose that the amount of silicon dioxide plays a critical role in cycle retention. It was shown that a certain amount of silicon dioxide can stabilize the electrochemical performance.
51 This finding likely correlates with the observed Li
2O and phosphates which are the successive reaction product of silicon dioxide on the pristine electrode surface with the electrolyte.