DOI:
10.1039/C4RA09173F
(Paper)
RSC Adv., 2014,
4, 51830-51837
Rapid synthesis of MgO nanoparticles & their utilization for formulation of a propylene glycol based nanofluid with superior transport properties
Received
24th August 2014
, Accepted 8th October 2014
First published on 8th October 2014
Abstract
Experiments were performed on the synthesis of magnesium oxide nanoparticles (30–40 nm), followed by their dispersion in propylene glycol to prepare stable MgO–propylene glycol nanofluids through extensive probe ultrasonication for 25 h. The influence of MgO nanoparticle concentration (0–2 vol%) and temperature on viscosity and thermal conductivity of MgO–propylene glycol nanofluids was investigated. While the relative viscosity of the nanofluid decreased with nanoparticle concentration to a temperature of 30 °C, the relative viscosity–nanoparticle concentration exhibited a minimum at 1 vol% in the temperature range of 35–60 °C. The enhancement in thermal conductivity of nanofluids increased linearly with nanoparticle concentration and was found to be independent of temperature, with an average enhancement of ∼20% for 2 vol% MgO–propylene glycol nanofluid. Our results show that the thermal conductivity enhancement in MgO–propylene glycol can be attributed to both interfacial layering and Brownian motion.
Introduction
Intensification of heat transfer has gained importance due to the widespread application of processes involving heat transfer in chemical, automobile, manufacturing and refining industries. The goals of heat transfer intensification include improving the heat duty through reduction of thermal resistance and provision of higher area densities (heat transfer area per unit heat exchanger volume). While higher area densities have been achieved in passive mode through use of compact heat exchangers,1 reduction in thermal resistance often requires turbulent conditions leading to higher energy consumption for pumping. Lower viscosity, higher thermal conductivity and higher specific heat are the desirable thermo-physical properties of a coolant. The use of such a coolant will consume lower pumping power, achieve higher rates of cooling while requiring lower heat transfer area for a given heat duty. One of the methods to improve thermal conductivity of a coolant is to disperse particles of higher thermal conductivity in the coolant. Nanofluid is result of such an attempt, in which nanoparticles (<100 nm) are dispersed in a coolant leading to a stable dispersion of nanoparticles in liquid and resulting in thermal conductivity enhancement in comparison to the single-phase coolant.2–6 However, in majority of cases, enhancement in thermal conductivity is accompanied by increase in viscosity also.7–15 In addition, the increase in thermal conductivity is overshadowed by increase in viscosity due to higher magnitude of the later.16–19 It has been recently shown that the transport properties of propylene glycol-based nanofluids could be improved through adoption of appropriate two-step method for formulation of nanofluids.20
Propylene glycol is an essential component of heat transfer fluid utilized in solar water heaters, employing two fluid loops.21–25 Propylene glycol possesses higher viscosity and lower thermal conductivity than ethylene glycol.26 However, choice of propylene glycol over ethylene glycol as anti-freeze agent is due to non-toxic nature of the former.27 While choosing an appropriate nanomaterial to be dispersed, attention is normally paid to chemical stability, ease of sustenance of colloidal stability and solid phase thermal conductivity. Metal oxides exhibit better chemical stability in polar liquids. Certain metal oxides such as zinc oxide, silica, cupric oxide, ferric oxide can be dispersed in propylene glycol without use of surfactant.28–31 Magnesium oxide (MgO) possess higher thermal conductivity (∼48.4 W m−1 K−1) among oxide materials.32 The ratio of thermal conductivity of bulk magnesium oxide to that of propylene glycol is very high (∼242). According to simplified Hamilton–Crosser model,33 3% enhancement in thermal conductivity could be expected while dispersing 1 vol% of MgO spherical nanoparticles in propylene glycol. However, when other mechanisms of thermal conductivity enhancement such as Brownian motion, interfacial layering and particle clustering are involved, higher enhancement in thermal conductivity can be obtained.34 The density of magnesium oxide is lower than that of other metal oxides such as zinc oxide, iron oxide, cupric oxide and alumina. Hence, the mass of MgO nanoparticles required to prepare nanofluid of a specified volume fraction is lower than that required with most other commonly used metal oxide nanoparticles. The colloidal stability of nanofluids is also improved with use of nanoparticles of lower density. There are relatively few experimental reports on nanofluids involving MgO nanoparticles such as those of MgO–ethylene glycol35 and MgO–water.36,37 To the best of our knowledge, there are no reports on preparation, detailed and methodological investigation of thermophysical properties of MgO–propylene glycol nanofluids. In the present work, MgO–propylene glycol nanofluids of different concentrations were prepared using two-step method and their viscosity and thermal conductivity studied as a function of nanoparticle concentration and temperature. A procedure for rapid synthesis of MgO nanoparticles at high temperature through bulk addition of precursors has been adopted in the present work.
Materials & methods
Materials
The precursor used for synthesis of magnesium oxide nanoparticles was magnesium nitrate hexahydrate procured from S D Fine-Chem Ltd. Mumbai, India. Ammonium carbonate used for the synthesis was procured from Qualigens Fine Chemicals, Mumbai, India. Distilled water was used for the preparation of solutions. Propylene glycol and ethylene glycol were procured from M/s. Merck, India. The density of MgO is 3.58 g cm−3.38
Methods
Preparation of MgO nanoparticles. Equimolar solutions of magnesium nitrate hexahydrate and ammonium carbonate were prepared and stored separately. The ammonium carbonate solution was heated to 70 °C and maintained at the same temperature, followed by addition of ammonium carbonate solution in bulk. The reaction mixture was filtered to recover the solid mass followed by calcination at 800 °C for 1 hour to obtain nanopowder.
Characterization of nanoparticles. A field emission scanning electron microscope (JSM 6701F, JEOL, Japan) was used to study the surface morphology of synthesized powders and to ascertain the presence of nanoparticles. The synthesized nanopowders were sprinkled on a carbon tape and mounted on stub for imaging using electron beam at an acceleration voltage of 3 kV. A diffractometer (D8Focus, Bruker, Germany) was used to record the powder X-ray diffraction patterns of the synthesized product, by scanning over the 2θ range of 30 to 60°.
Preparation of MgO–propylene glycol nanofluids. MgO–propylene glycol nanofluids were prepared by two-step method, in which the synthesized MgO nanoparticles were dispersed in propylene glycol through probe ultrasonication. No surfactant was employed for dispersion of MgO in propylene glycol. In a typical experiment, the predetermined mass of MgO nanopowders corresponding to 2 vol%, was added to propylene glycol and subjected to probe ultrasonication (Vibracell™, Sonics, USA). The amplitude, cycle time and off-time were 60%, 45 seconds and 15 seconds respectively. Thermal conductivity and viscosity of 2 vol% MgO–propylene glycol were measured at various time points during probe ultrasonication. Usually, increase in thermal conductivity and decrease in viscosity28–31,39,40 are observed during probe ultrasonication of dispersion. However, thermal conductivity and viscosity tend to saturate with ultrasonication after certain time, beyond which changes in thermal conductivity and viscosity with ultrasonication time are insignificant. MgO–propylene glycol nanofluids of different MgO concentrations were prepared from optimally ultrasonicated 2 vol% MgO–propylene glycol stock by serial dilution with propylene glycol.
Characterization of MgO–propylene glycol nanofluids. Thermal conductivity and viscosity are the important transport properties of nanofluids. The measurement of thermal conductivity of nanofluids and propylene glycol was carried out using a thermal property analyser (KD2 Pro, Decagon Devices, USA) that utilizes transient hot-wire technique. The probe (KS-1) acts both as a heat source as well as temperature sensor. Necessary precautions were taken to minimize the effect of convection during thermal conductivity measurements. A rotational viscometer (LVDV-II+Pro, Brookfield Engineering, USA) was used to measure the viscosity of nanofluid samples and propylene glycol, by employing spindle (S00). The constancy of temperature during the measurement of thermal conductivity and viscosity was ensured through use of constant temperature bath (TC-502, Brookfield Engineering, USA). Thermal conductivity and viscosity measurements were carried out atleast three times to determine the standard deviation, which has been taken as the uncertainty of respective measurements. The maximum relative standard deviations for thermal conductivity and viscosity measurements were 1.2% and 0.5% respectively. Uncertainty for thermal conductivity ratio was calculated using the standard deviations of thermal conductivity measurements of nanofluid and base fluid as described in literature.8To study the nature of interactions between MgO and propylene glycol, Fourier Transform Infrared Spectra (Spectrum One, Perkin Elmer, USA) were recorded for as-synthesized MgO nanoparticles and MgO nanoparticles separated from 2 vol% MgO–propylene glycol nanofluid through centrifugation. The spectra were recorded over the wave number range of 400–4000 cm−1. The hydrodynamic size of MgO–propylene glycol (2 vol%) nanofluid was determined using dynamic light scattering (Nano ZS, Malvern Instruments, UK).
Results & discussion
Characteristics of synthesized product
The scanning electron micrograph of synthesized powder shown in Fig. 1a, indicates the presence of spherical nanoparticles in the size range of 30 to 38 nm in the product. The X-ray diffraction patterns (Fig. 1b) confirm the crystalline nature of the product, with sharp peaks at 2θ values, characteristic of face-centered cubic MgO, in accordance with JCPDS no. 45-0946. Scherrer formula was used to estimate the crystallite size from diffraction patterns and was found to be 16.5 nm.
 |
| Fig. 1 [a] Scanning electron micrograph of MgO nanoparticles; [b] powder X-ray diffraction patterns of MgO nanoparticles. | |
Optimum ultrasonication time
It may be recalled that probe ultrasonication was utilized to disperse MgO nanoparticles in propylene glycol. The variation of thermal conductivity and viscosity with ultrasonication time are shown in Fig. 2a and b respectively. It is evident from Fig. 2a and b that the thermal conductivity increased with ultrasonication time, while the viscosity decreased with ultrasonication time. The increase in thermal conductivity and decrease in viscosity with ultrasonication time is attributed to improved dispersion characteristics. With increase in ultrasonication time, the fraction of nanoparticles remaining in well-dispersed state in nanofluid increases, thereby increasing its thermal conductivity. Also, it is well established that the viscosity of a well-dispersed nanofluid is lower than that of a nanofluid containing the same volume fraction of nanoparticles in aggregated state.41,42 Between the ultrasonication times of 21 h and 25 h, the changes in thermal conductivity and viscosity were insignificant and hence ultrasonication was stopped after 25 h. Therefore the 2 vol% MgO–propylene glycol dispersion ultrasonicated for 25 h possessed better transport properties due to higher volume fraction of nanoparticles in dispersed state and lower aggregate sizes. The average hydrodynamic size of nanoparticles in propylene glycol before ultrasonication and after 25 h of ultrasonication were found to be 666 ± 48 and 121 ± 3 nm respectively, testifying the effect of probe ultrasonication in reducing the size of aggregates. MgO–propylene glycol nanofluids of different concentrations were prepared from 25 h ultrasonicated 2 vol% MgO–propylene glycol nanofluid through serial dilution with propylene glycol.
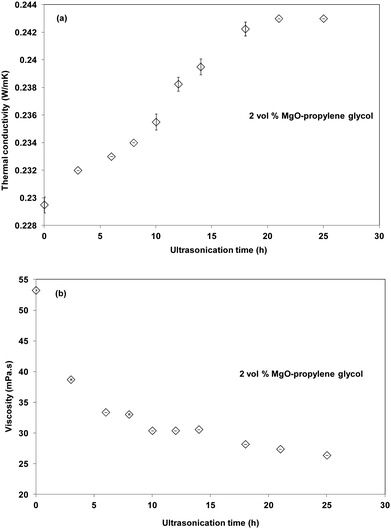 |
| Fig. 2 Influence of ultrasonication time on [a] thermal conductivity and [b] viscosity of 2 vol% MgO–propylene glycol nanofluid. | |
Viscosity of MgO–propylene glycol nanofluids
The major factors influencing the viscosity of nanofluids are nanoparticle concentration, particle shape, aggregate-to-primary particle size and temperature.9,43–46 Having chosen spherical nanoparticles and optimally ultrasonicated nanofluids with lower aggregate-to-particle size for the present work, the influence of other two factors viz. nanoparticle concentration and temperature on nanofluid viscosity has been studied.
The variation of viscosity of nanofluids and propylene glycol with shear rate is shown in Fig. 3a. It is evident from Fig. 3a that the viscosity is nearly independent of shear rate in the range of 66 to 105.6 s−1, as indicated by very low absolute values for the exponent (<0.1). Hence, the viscosity data acquired at the shear rate of 79.2 s−1 (operable shear rate closer to midpoint between shear rates of 66 & 105.6 s−1) are presented in Fig. 3b in which the variation of nanofluid viscosity with nanoparticle concentration is shown.
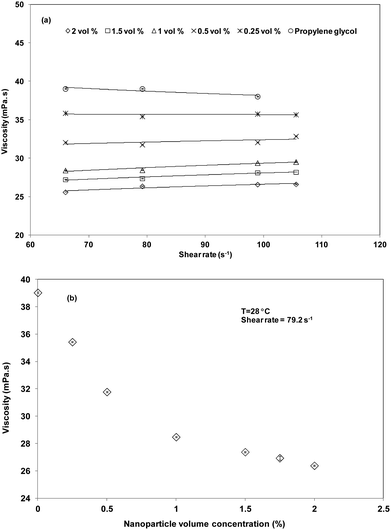 |
| Fig. 3 [a] Influence of shear rate on viscosity of propylene glycol and MgO–propylene glycol nanofluids; [b] influence of nanoparticle volume concentration on viscosity of MgO–propylene glycol nanofluids. | |
The viscosity of MgO–propylene glycol decreases with increase in concentration of MgO nanoparticles (Fig. 3). The decrease in nanofluid viscosity is rapid over a narrow range of nanoparticle concentration (<0.5%), while the decrease in nanofluid viscosity is low over the MgO nanoparticle concentration range of 1–2%. It has been recently shown that the dispersion of nanoparticles of hydrophilic metal oxides in a strongly polar liquid like propylene glycol, results in the reduction of viscosity due to perturbation of intermolecular hydrogen bonds in propylene glycol caused by nanoparticle–polar liquid interaction.28,30,40 The interactions between MgO nanoparticles and propylene glycol is evident from the comparison of FTIR spectra of MgO nanoparticles separated from 2 vol% MgO–PG nanofluid with those of as-synthesized MgO nanoparticles (Fig. 4). The presence of bands around 1050–1150 cm−1 corresponds to C–O stretching of alcohol (Fig. 4) in the FT-IR spectra. The intensity of band corresponding to Mg–O stretching vibrations (680–700 cm−1) in MgO separated from MgO–propylene glycol nanofluid is lower than that observed for as-synthesized MgO nanoparticles (Fig. 4). The band corresponding to O–H stretching vibration (3450–3480 cm−1) in MgO separated from MgO–propylene glycol nanofluids is broadened when compared to that in as-synthesized MgO nanoparticles. All these indicate interactions between hydroxyl group on MgO surface with propylene glycol.47
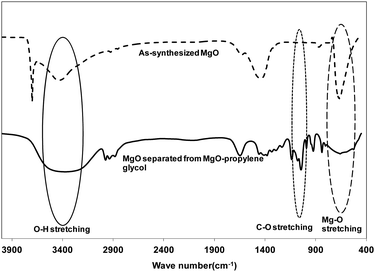 |
| Fig. 4 FT-IR spectra of as-synthesized MgO nanoparticles and MgO–propylene glycol nanofluid. | |
The nanofluid viscosity–nanoparticle concentration relationship in propylene glycol-based nanofluids exhibit monotonous decrease in viscosity30,31,40 or biphasic trend28,39 depending on the magnitude of viscosity reduction brought about by the perturbation of hydrogen bonds and the increase in viscous dissipation caused by presence of nanoparticles.28,30,31,39,40 The steep decrease in nanofluid viscosity in the concentration range of 0–0.5% may be attributed to the perturbations of hydrogen bonding network being predominant in comparison to the increased viscous dissipation. While increasing the nanoparticle concentration from 1% to 2%, the viscous dissipation too influences the nanofluid viscosity albeit insufficient to overcome the viscosity reduction due to hydrogen bond perturbations in propylene glycol at 28 °C. The present result on viscosity reduction (32.4%) is comparable to percentage reduction in viscosity of 2 vol% ZnO–propylene glycol (32%),29 Fe2O3–propylene glycol (38.9%).31 Reduction in nanofluid viscosity with nanoparticle concentration for surfactant-stabilized MWCNT-water nanofluid has been reported48 and the same was attributed to lubricating effect of nanoparticles. In another independent work, reduction in viscosity of PVA with addition of reduced graphene oxide was reported49 which was attributed to reduction in density of hydrogen bonds in PVA caused by dispersion of reduced graphene oxide.49
The influence of temperature on viscosity of MgO–propylene glycol nanofluids and propylene glycol is shown in Fig. 5. It is evident that MgO–propylene glycol nanofluids with nanoparticle concentration upto 1.75 vol% behave similar to that of propylene glycol with reduction in viscosity upon increasing the temperature.
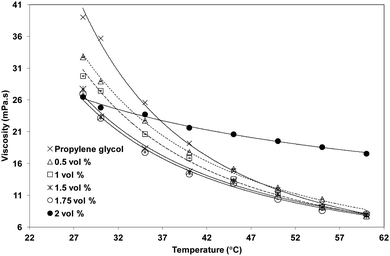 |
| Fig. 5 Influence of temperature on viscosity of propylene glycol and MgO–propylene glycol nanofluids. | |
The change in the viscosity of 0.5 vol%, 1 vol%, 1.5 vol% and 1.75 vol% nanofluids show relatively weak temperature dependence, with the exponent being −1.773, −1.81, −1.579, −1.575 respectively, in comparison with pure propylene glycol whose viscosity change with temperature increase has an exponent of −2.156 (Fig. 5).
A marked difference in viscosity–temperature relationship of 2 vol% MgO–propylene glycol was observed in comparison to that of pure propylene glycol, with appreciable difference in exponents. The viscosity of 2 vol% MgO–propylene glycol nanofluid was higher than that of pure propylene glycol when temperature was increased to 40 °C and beyond. MgO–propylene glycol nanofluids with nanoparticle concentration greater than 1 vol% underwent irreversible transformation to gel when heated above 60–70 °C. As this aspect needs further investigation and the primary focus of this work being study of nanofluids under the conditions during which they behave as liquids, the temperature during experiments were confined to a maximum value of 60 °C. The slow decrease in viscosity of 2 vol% MgO–propylene glycol nanofluid with temperature increase may be attributed to state of nanofluid, which is transferring from dispersion to gel-like phase, while at other nanoparticle concentrations (≤1.75 vol%), the nanofluids behaved like liquid at this temperature range (30–60 °C).
The viscosity of nanofluids is compared with that of liquid (base fluid) in which they are dispersed through use of relative viscosity.43,45,50 The ratio of nanofluid-to-base fluid viscosity gives relative viscosity, which is an indication of degree of deviation of nanofluid viscosity from the viscosity of base fluid. The variation of relative viscosity of MgO–propylene glycol nanofluids with temperature is given in Fig. 6. It is evident from Fig. 6 that the relative viscosity increased with increase in temperature. The strength of hydrogen bonding interactions is temperature dependent, with reduced magnitude at elevated temperatures.51 Hence with increase in temperature, the contribution of hydrogen bonding interactions to viscosity of propylene glycol decreases. Hence, the perturbations in hydrogen bonding network has lower effect on viscosity at higher temperatures, while the contribution of viscous dissipation to viscosity increase is either independent of temperature50 or increases with temperature due to increase in Brownian velocity.30 Hence the relative viscosity of MgO–propylene glycol nanofluids increase with temperature.
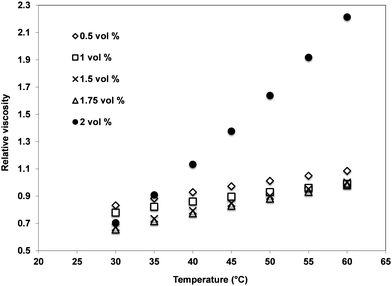 |
| Fig. 6 Influence of temperature on relative viscosity of MgO–propylene glycol nanofluids. | |
Thermal conductivity of MgO–propylene glycol nanofluids
Considerable interest in nanofluids is attributed to its increased thermal conductivity when compared to that of the base fluid. Hence the study of thermal conductivity as a function of nanoparticle concentration and temperature is essential to identify an appropriate nanofluid for thermal engineering applications. The variation of thermal conductivity of MgO–propylene glycol nanofluid with the concentration of MgO nanoparticles is shown in Fig. 7, from which it is evident that the thermal conductivity increases with increase in concentration of MgO nanoparticles. This trend is observed in the entire temperature range investigated, as typically shown for 28 and 50 °C. The linear increase in thermal conductivity of MgO–propylene glycol nanofluid with increasing MgO nanoparticle concentration indicates well-dispersed nature of nanoparticles in the nanofluid.
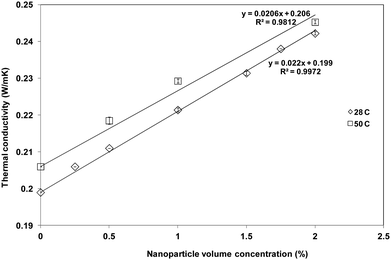 |
| Fig. 7 Influence of nanoparticle volume concentration on thermal conductivity of MgO–propylene glycol nanofluids at 28 & 50 °C. | |
The thermal conductivity (k) – MgO nanoparticle volume fraction (ϕ) relationship at 28 °C is given by:
Expressing eqn (1) in terms of thermal conductivity ratio (kr), which is the ratio of thermal conductivity of MgO–propylene glycol nanofluid to that of propylene glycol, eqn (2) is obtained as follows:
The slope of 11.16 in eqn (2) is comparable to slope of ‘kr’ vs. ‘ϕ’ relationships of ZnO–propylene glycol (12.8),29 Fe2O3–propylene glycol (10.79),31 sand–propylene glycol (11.99)30 nanofluid systems, which were surfactant-free and optimally ultrasonicated, well-dispersed nanofluid systems.
The study of temperature dependence of thermal conductivity ratio is essential to establish the mechanisms responsible for thermal conductivity enhancements in nanofluids. The influence of temperature on thermal conductivity ratio of MgO–propylene glycol nanofluids is shown in Fig. 8, from which it is evident that temperature has very little influence on thermal conductivity ratio. The difference in thermal conductivity ratio for 1 vol% and 2 vol% MgO–propylene glycol nanofluids between 15 and 50 °C are 0.0036 and 0.0070 respectively.
 |
| Fig. 8 Influence of temperature on thermal conductivity of MgO–propylene glycol nanofluids. | |
When the thermal conductivity ratio of nanofluids is greater than that predicted from effective medium approximation, given by kr = 1 + 3Ø for nanofluids containing spherical nanoparticles, the thermal conductivity of nanofluids are influenced by one or more of the mechanisms such as nanoparticle clustering, Brownian motion and interfacial layering.8,17,29,52–57 Nanofluids whose properties are influenced by nanoparticle clustering exhibit non-linear increase in relative viscosity with nanoparticle concentration18 and temperature independent thermal conductivity ratio.17,28,39 Microconvection caused by Brownian motion is thermally activated phenomenon and hence nanofluids influenced by Brownian motion possess higher thermal conductivity enhancement (or ratio) at higher temperatures.8,58,59 The effect of interfacial layering on thermal conductivity ratio of nanofluids is reflected as higher thermal conductivity ratios at lower temperatures.20,29 The contributions of interfacial layering and Brownian motion to thermal conductivity ratio are directly proportional to nanoparticle concentration.29,30
Though the thermal conductivity ratios of MgO–propylene glycol nanofluids are quite independent of temperature, the nanoparticles are well dispersed as evident from low nanofluid viscosities. Hence nanoparticle clustering may not be the dominant mechanism influencing thermal conductivity of nanofluids. It appears as though both the interfacial layering and Brownian motion contribute to thermal conductivity enhancement and the temperature effect of each factor nullifies that of the other, leading to nearly constant thermal conductivity ratio over the temperature range of 15–50 °C (Fig. 8). Feeble decrease in thermal conductivity ratio between 25–35 °C and another feeble increase in thermal conductivity ratio between 35–50 °C may also be results of small imbalance between the roles of interfacial layering and Brownian motion.
Stability
Particle dispersions tend to settle in static liquid at a rate determined by the particle size, particle & liquid densities and liquid viscosity. The terminal settling velocity of particles (ut) is related to its size (dp) & density (ρp), fluid viscosity (μ) and density (ρ) as60 |
 | (3) |
The Brownian velocity (uB) is related to particle size, temperature (T), fluid viscosity and density as14
|
 | (4) |
The terminal settling velocity of 124 nm diameter particles (121 ± 3 nm) of MgO in propylene glycol at 25 °C is 5.3 × 10−10 m s−1. Under the same conditions, Brownian velocity is about 4.26 × 10−6 m s−1. Though the primary particle size was 30–40 nm as observed in scanning electron micrograph, both settling velocity and Brownian velocity were calculated using 124 nm (hydrodynamic diameter) as particle size as determined by dynamic light scattering. Utilizing the hydrodynamic diameter provides a conservative estimate of Brownian velocity and higher estimate for settling velocity. Despite this, Brownian velocity is about 4 orders of magnitude greater than settling velocity, implying that the random motion of nanoparticles are likely to contribute to their better dispersion in propylene glycol. The nanofluids were found to be stable for about 1 month when left undisturbed.
MgO–propylene glycol vs. ethylene glycol
The thermal conductivity and viscosity of 2 vol% MgO–propylene glycol nanofluid were compared with those of pure ethylene glycol to explore the possibility of replacing ethylene glycol by 2 vol% MgO–propylene glycol nanofluid as the coolant. The thermal conductivity of 2 vol% MgO–propylene glycol is 0.242 W m−1 K−1 at 28 °C, which is comparable to thermal conductivity of pure ethylene glycol (0.248 W m−1 K−1 at 28 °C). However the viscosity of 2 vol% MgO–propylene glycol (26.375 mPa s at 28 °C) is greater than that of pure ethylene glycol (∼16 mPa s at 28 °C). Under the conditions of laminar flow, the Nusselt number (hD/k) is constant.61 Therefore, as the thermal conductivities of 2 vol% MgO–propylene glycol nanofluid and ethylene glycol are comparable, their heat transfer coefficients under laminar flow conditions will also be comparable. Hence, under such conditions, the heat transfer performance of 2 vol% MgO–propylene glycol may be comparable to that of pure ethylene glycol.
Conclusions
Crystalline, magnesium oxide nanoparticles of size 30 to 40 nm were synthesized from magnesium nitrate hexahydrate and ammonium carbonate. Surfactant-free, MgO–propylene glycol nanofluids prepared through probe ultrasonication for 25 h exhibited good colloidal stability. The dispersion of MgO nanoparticles in propylene glycol caused perturbations in its hydrogen bonding network causing reduction in viscosity. This viscosity reduction was both concentration and temperature dependent, with maximum viscosity reduction of 32% observed for 2 vol% nanofluid at 28 °C. A maximum thermal conductivity enhancement of ∼20% was obtained for 2 vol% MgO–propylene glycol nanofluid, which is greater than that predicted by effective-medium approximation. The study on effect of temperature on thermal conductivity ratio suggested the role of both interfacial layering and Brownian motion in thermal conductivity enhancement.
Acknowledgements
This work was supported by (i) PG teaching grant no. SR/NM/PG-16/2007 of Nano Mission Council, Department of Science & Technology (DST), India (ii) Grant no. SR/FT/ET-061/2008, DST, India and (iii) Research & Modernization Project #1, SASTRA University, India.
Notes and references
- D. Reay, C. Ramshaw and A. Harvey, Process Intensification, Butterworth-Heinemann publishers, London, 1st edn, 2008 Search PubMed.
- I. Palabiyik, Z. Musina, S. Witharana and Y. Ding, J. Nanopart. Res., 2011, 13, 5049–5055 CrossRef CAS.
- G. Ramesh and N. K. Prabhu, Nanoscale Res. Lett., 2011, 6, 334 CrossRef PubMed.
- S. Habibzadeh, A. Kazemi-Beydokhti, A. A. Khodadadi, Y. Mortazavi, S. Omanovic and M. Shariat-Niassar, Chem. Eng. J., 2010, 156, 471–478 CrossRef CAS PubMed.
- M. B. Moghaddam, E. K. Goharshadi, M. H. Entezari and P. Nancarrow, Chem. Eng. J., 2013, 231, 365–372 CrossRef CAS PubMed.
- T. S. Sreeremya, A. Krishnan, A. Peer Mohamed, U. S. Hareesh and S. Ghosh, Chem. Eng. J., 2014, 255, 282–289 CrossRef CAS PubMed.
- L. Syam Sundar, E. Venkata Ramana, M. K. Singh and A. C. M. Sousa, Int. Commun. Heat Mass Transfer, 2014, 56, 86–95 CrossRef CAS PubMed.
- K. Rohini Priya, K. S. Suganthi and K. S. Rajan, Int. J. Heat Mass Transfer, 2012, 55, 4734–4743 CrossRef CAS PubMed.
- J. Jeong, C. Li, Y. Kwon, J. Lee, S. H. Kim and R. Yun, Int. J. Refrig., 2013, 36, 2233–2241 CrossRef CAS PubMed.
- M. Chandrasekar, S. Suresh and A. Chandra Bose, Exp. Therm. Fluid Sci., 2010, 34, 210–216 CrossRef CAS PubMed.
- A. Indhuja, K. S. Suganthi, S. Manikandan and K. S. Rajan, J. Taiwan Inst. Chem. Eng., 2013, 44, 474–479 CrossRef PubMed.
- Y. Naresh, a. Dhivya, K. S. Suganthi and K. S. Rajan, Nanosci. Nanotechnol. Lett., 2012, 4, 1209–1213 CrossRef CAS PubMed.
- S. Manikandan, N. Karthikeyan, M. Silambarasan and K. S. Rajan, Appl. Therm. Eng., 2012, 44, 1–10 CrossRef PubMed.
- S. Manikandan, N. Karthikeyan, M. Silambarasan, K. S. Suganthi and K. S. Rajan, Braz. J. Chem. Eng., 2012, 29, 699–712 CrossRef CAS PubMed.
- T. S. Sreeremya, A. Krishnan, L. N. Satapathy and S. Ghosh, RSC Adv., 2014, 4, 28020 RSC.
- B. LotfizadehDehkordi, S. N. Kazi, M. Hamdi, a. Ghadimi, E. Sadeghinezhad and H. S. C. Metselaar, Heat Mass Transfer, 2013, 49, 1109–1115 CrossRef CAS PubMed.
- P. Vishnu Vardhan, K. S. Suganthi, S. Manikandan and K. S. Rajan, Nanosci. Nanotechnol. Lett., 2014 DOI: 10.1166/nnl.2014.1884 , article in press.
- A. H. Mary, K. S. Suganthi and K. S. Rajan, Nanosci. Nanotechnol. Lett., 2013, 5, 1125–1129 CrossRef CAS PubMed.
- M. Silambarasan, S. Manikandan and K. S. Rajan, Int. J. Heat Mass Transfer, 2012, 55, 7991–8002 CrossRef CAS PubMed.
- K. S. Suganthi and K. S. Rajan, Int. J. Heat Mass Transfer, 2014, 71, 653–663 CrossRef CAS PubMed.
- B. Norton and J. E. J. Edmonds, Sol. Energy, 1991, 47, 375–382 CrossRef CAS.
- Selecting a Glycol for Solar Thermal Applications, http://www.dynalene.com/Articles.asp?ID=283, accessed on 19.08.2014.
- Solar Hot Water System Glycol High Temperature - Solar Hot Water & Heating Manufacturer|Solar Hot Water & Heating Manufacturer, http://www.sunmaxxsolar.com/shop/shop-heat-transfer-fluids/solar-hot-water-system-glycol-high-temperature/, accessed on 19.08.2014.
- Y. Xuan, Q. Li and H. Duan, RSC Adv., 2014, 4, 16206–16213 RSC.
- Y. He, S. Vasiraju and L. Que, RSC Adv., 2014, 4, 2433 RSC.
- The Engineering toolbox, http://www.engineeringtoolbox.com/ethylene-propylene-glycol-d_904.html.
- K. McMartin, Encyclopedia of Toxicology, Elsevier, 2014 Search PubMed.
- K. S. Suganthi, A. K. Radhakrishnan, N. Anusha and K. S. Rajan, J. Nanosci. Nanotechnol., 2014, 14, 4602–4607 CrossRef CAS PubMed.
- K. S. Suganthi, M. Parthasarathy and K. S. Rajan, Chem. Phys. Lett., 2013, 561–562, 120–124 CrossRef CAS PubMed.
- S. Manikandan, A. Shylaja and K. S. Rajan, Colloids Surf., A, 2014, 449, 8–18 CrossRef CAS PubMed.
- A. Shylaja, S. Manikandan, K. S. Suganthi and K. S. Rajan, J. Nanosci. Nanotechnol., 2014, 15, 1653–1659 CrossRef PubMed.
- W. Yu and H. Xie, J. Nanomater., 2012, 2012, 435873 Search PubMed.
- S. Lee, S. U. S. Choi, S. Li and J. Eastman, J. Heat Transfer, 1999, 121, 280–289 CrossRef CAS.
- P. Keblinski, S. R. Phillpot, S. U. S. Choi and J. A. Eastman, Int. J. Heat Mass Transfer, 2002, 45, 855–863 CrossRef CAS.
- W. Yu, H.-Q. Xie, Y. Li and L.-F. Chen, in ASME 2009 7th International Conference on Nanochannels, Microchannels, and Minichannels, The American Society of Mechanical Engineers, Pohang, South Korea, 2009, pp. 901–905 Search PubMed.
- M. Hemmat Esfe, S. Saedodin and M. Mahmoodi, Exp. Therm. Fluid Sci., 2014, 52, 68–78 CrossRef CAS PubMed.
- Y. Cui and Q. Zhu, in Power and Energy Engineering Conference (APPEEC), 2012, Asia-Pacific, Shanghai, 2012, pp. 1–4 Search PubMed.
- 1309-48-4 (Magnesium oxide) Product Description, http://www.chemicalbook.com/ChemicalProductProperty_US_CB8853024.aspx, accessed on 04.10.2014.
- V. Aishwarya, K. S. Suganthi and K. S. Rajan, J. Nanopart. Res., 2013, 15, 1774 CrossRef.
- K. S. Suganthi, N. Anusha and K. S. Rajan, J. Nanopart. Res., 2013, 15, 1986 CrossRef.
- H. Chen, Y. Ding and C. Tan, New J. Phys., 2007, 9, 367 CrossRef.
- G. A. Longo and C. Zilio, Exp. Therm. Fluid Sci., 2011, 35, 1313–1324 CrossRef CAS PubMed.
- L. S. Sundar, K. V. Sharma, M. T. Naik and M. K. Singh, Renewable Sustainable Energy Rev., 2013, 25, 670–686 CrossRef CAS PubMed.
- B. Aladag, S. Halelfadl, N. Doner, T. Maré, S. Duret and P. Estellé, Appl. Energy, 2012, 97, 876–880 CrossRef CAS PubMed.
- I. M. Mahbubul, R. Saidur and M. A. Amalina, Int. J. Heat Mass Transfer, 2012, 55, 874–885 CrossRef CAS PubMed.
- M. J. Pastoriza-Gallego, C. Casanova, J. L. Legido and M. M. Piñeiro, Fluid Phase Equilib., 2011, 300, 188–196 CrossRef CAS PubMed.
- J. Park, Y. Lee, K. Jun, J. Baeg and D. J. Yim, J. Ind. Eng. Chem., 2006, 12, 882–887 CAS.
- L. Chen, H. Xie, Y. Li and W. Yu, Thermochim. Acta, 2008, 477, 21–24 CrossRef CAS PubMed.
- Y. Tan, Y. Song and Q. Zheng, Nanoscale, 2012, 4, 6997–7005 RSC.
- A. Indhuja, K. S. Suganthi, N. Anusha and K. S. Rajan, Nanosci. Nanotechnol. Lett., 2013, 5, 813–817 CrossRef CAS PubMed.
- M. Chaplin, Condens. Matter, 2007, 0706.1355 Search PubMed.
- N. R. Karthikeyan, J. Philip and B. Raj, Mater. Chem. Phys., 2008, 109, 50–55 CrossRef CAS PubMed.
- J. Philip, P. D. Shima and B. Raj, Appl. Phys. Lett., 2007, 91, 203108 CrossRef PubMed.
- C. H. Li and G. P. Peterson, J. Appl. Phys., 2006, 99, 084314 CrossRef PubMed.
- S. Ozerinc, S. Kakac and A. G. Yazıcıoglu, Microfluid. Nanofluid., 2010, 8, 145–170 CrossRef.
- L. Xue, P. Keblinski, S. Phillpot, S. U.-S. Choi and J. Eastman, Int. J. Heat Mass Transfer, 2004, 47, 4277–4284 CrossRef PubMed.
- M. Myekhlai, B. Munkhbayar, T. Lee, M. R. Tanshen, H. Chung and H. Jeong, RSC Adv., 2014, 4, 2495 RSC.
- S. Harish, K. Ishikawa, E. Einarsson, S. Aikawa, T. Inoue, P. Zhao, M. Watanabe, S. Chiashi, J. Shiomi and S. Maruyama, Mater. Express, 2012, 2, 213–223 CrossRef CAS PubMed.
- S. K. Das, N. Putra, P. Thiesen and W. Roetzel, J. Heat Transfer, 2003, 125, 567–574 CrossRef CAS.
- W. L. McCabe, J. C. Smith and P. Harriott, Unit Operations of Chemical Engineering, McGraw-Hill, New York, 7th edn, 2005 Search PubMed.
- C. P. Kothandaraman and S. Subramanyan, Heat and Mass Transfer Data Book, New Age International Publishers, New Delhi, 7th edn, 2010 Search PubMed.
|
This journal is © The Royal Society of Chemistry 2014 |
Click here to see how this site uses Cookies. View our privacy policy here.