DOI:
10.1039/C4RA04136D
(Paper)
RSC Adv., 2014,
4, 27955-27962
Highly efficient homogeneous and heterogenized ruthenium catalysts for transfer hydrogenation of carbonyl compounds†
Received
5th May 2014
, Accepted 16th June 2014
First published on 17th June 2014
Abstract
[Ru(acac)2(CH3CN)2] was synthesized from [Ru(acac)3] by refluxing it with zinc powder in ethanol–acetonitrile mixture. The prepared catalyst was characterized by FT-IR, 1H and 13C NMR techniques. The silica supported catalyst (‘SiO2’–NH2–RuII) was prepared by stirring [Ru(acac)2(CH3CN)2] with ‘SiO2’–NH2 in a 1
:
1 mixture of CH2Cl2–toluene for 3 days at room temperature. It was characterized by FT-IR, SEM, solid state NMR, ICP and BET surface area methods. The transfer hydrogenation reaction of carbonyl compounds was carried out separately using [Ru(acac)2(CH3CN)2] and ‘SiO2’–NH2–RuII as catalysts. The reaction conditions were optimized with different solvents, bases, catalyst amounts and temperatures using acetophenone as a model system. The scope of the reaction was extended to various substituted aryl ketones including heteroaryl ketones.
1. Introduction
Transition metal-catalyzed transfer hydrogenation of hydrogen acceptors by hydrogen donors has been recognized as a unique pathway in catalysis since it can be executed with experimental simplicity.1–4 The conventional reduction routes often require a high hydrogen pressure and cumbersome reducing reagents.5,6 Transfer hydrogenation uses economically viable and environmentally benign hydrogen sources like isopropanol and formates;7,8 more over its operational safety is better than that of traditional hydrogenation. It is a complementary protocol to the classical Meerwein–Ponndorf–Verley reduction/Oppenauer oxidation,9,10 where a stoichiometric amount of aluminium iso-propoxide is used. Generally transfer hydrogenation is catalyzed by transition metal complexes containing N-heterocyclic carbenes (NHCs),11 arenes,12 phosphines,13–15 tridentate pyridine-based framework,16 tetradentate chiral NNPP17–20 and pendant ether groups as ligands, but the essential ligand feature for catalytic activity is not definite. In recent years metal complexes stabilized by neutral, non-aqueous ligands are being recognized as active catalysts. Among them the most promising class of compounds are those incorporating easily dissociable solvent ligands.21 The coordination of labile ligands could be easily replaced by more strongly coordinating ones or by other substrates. The experimentally determined catalytic activity of the complexes correlates well with the ligand field stabilization energy as a function of the number of d electrons.22 The lower the stabilization energy of the catalyst, the higher is its catalytic activity. A number of highly active ruthenium(II) complexes has been developed and used recently23,24 for transfer hydrogenation of carbonyl compounds, but their practical applications in pharmaceutically important processes are very often hindered by their working cost as well as difficulties in removing residual metals from the desired product.25 To avoid such critical issues, the inherent approach is to heterogenize the homogeneous catalyst on to the solid support. The covalent attachment of catalyst on silica surface is the most appropriate method to prepare stable and cost effective heterogenized catalyst. The peculiar properties of silica such as ordered structures, very high surface areas, and uniform, large and tunable pore diameters make it as a cost effective solid support for grafting the catalyst.
2. Experimental
2.1. Materials
All the reagents used were of chemically pure and analar grade. Commercial grade solvents were distilled according to the standard procedures and dried over molecular sieves before use. Fumed silica (0.014 μm) and 3-aminopropyltriethoxysilane were purchased from Sigma Aldrich and used without further purification. [Ru(acac)3], [Ru(acac)2(CH3CN)2] and amine functionalized silica (‘SiO2’–NH2) were prepared according to the literature procedures.26–28
2.2. Immobilization of [Ru(acac)2(CH3CN)2] on to amine functionalized silica (‘SiO2’–NH2–RuII)
[RuII(acac)2(CH3CN)2] (100 mg) and ‘SiO2’–NH2 (1 g) were stirred at room temperature in a 1
:
1 mixture of dry dichloromethane and toluene (20 mL) for 72 h. The mixture was filtered to obtain solid which was washed several times with dichloromethane and subjected to Soxhlet extraction using acetone, followed by ethanol for about two days to ensure leaching of all unbound Ru complex. The solid was dried at 100 °C under vacuum for 6 h to afford a brown color powder (1.03 g, 0.089 wt% Ru) (Scheme 1).
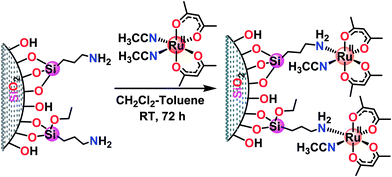 |
| Scheme 1 Preparation of ‘SiO2’–NH2–RuII. | |
2.3. Catalyst characterization
The morphology and Ru content of the catalyst were analyzed using JEOL JSM-6701F field emission scanning electron microscope (FE-SEM). FT-IR spectra were obtained on a Perkin Elmer Spectrum 100 FT-IR spectrophotometer as KBr pellet in the frequency range of 4000–400 cm−1. The BET surface area was estimated using ASAP 2020 system. The Ru content in the catalysts was measured by Perkin Elmer Optima 5300 DV inductively coupled plasma optical emission spectrometer (ICP-OES). 13C and 29Si CP-MAS solid state NMR spectra were recorded using Bruker DSX-300 solid state NMR spectrometer.
2.4. Transfer hydrogenation of carbonyl compounds
Carbonyl compound (1 equiv.), [Ru(acac)2(CH3CN)2] (2 mol%) or ‘SiO2’–NH2–RuII (0.02 mol%) and NaOH (1 equiv.) were stirred in isopropanol (10 mL) at 80 °C. After the requisite time, the reaction mixture was cooled to room temperature. The product was extracted with ethyl acetate, dried over anhydrous sodium sulphate and analyzed by GC. The extract was concentrated and chromatographed on a silica gel column with n-hexane–ethyl acetate (4
:
1) as an eluting solvent to give the corresponding alcohol.
In the case of heterogeneous catalysis, the catalyst was separated by centrifugation after completion of the reaction. The product was extracted from centrifugate using ethyl acetate. The extract was dried over anhydrous sodium sulphate, concentrated and chromatographed on a silica gel column with n-hexane–ethyl acetate (4
:
1) as the eluting solvent to afford the desired alcohol. The recovered catalyst was washed thoroughly with water, ethanol and toluene. It was dried under vacuum before reuse.
1-p-Tolylethanol. 1H NMR (400 MHz, CDCl3): δ (ppm) 1.50 (d, J = 6.40 Hz, 3H), 2.33 (s, 3H), 4.89 (q, J = 6.40 Hz, 1H), 7.18 (d, J = 8.00 Hz, 2H), 7.28 (d, J = 7.60 Hz, 2H).
1-(4-Methoxyphenyl)ethanol. 1H NMR (400 MHz, CDCl3): δ (ppm) 1.46 (d, J = 6.40 Hz, 3H), 3.79 (s, 3H), 4.82 (q, J = 6.40 Hz, 1H), 6.88 (t, J = 8.80 Hz, 2H), 7.29 (t, J = 8.40 Hz, 2H). 13C NMR (100 MHz, CDCl3): δ (ppm) 25.03, 55.26, 55.45, 72.09, 113.70, 113.80, 113.84, 126.68, 127.61, 138.12, 163.52, 90.
1-(Thiophen-3-yl)ethanol. 1H NMR (400 MHz, CDCl3): δ (ppm) 1.60 (d, J = 6.40 Hz, 3H), 5.12 (q, J = 6.40 Hz, 1H), 6.96 (d, J = 8.00 Hz, 2H), 7.22–7.24 (m, 1H). 13C NMR (100 MHz, CDCl3): δ (ppm) 25.23, 66.18, 123.15, 124.37, 126.63, 149.90.
2,3-Dihydro-1H-inden-2-ol. 1H NMR (300 MHz, CDCl3): δ (ppm) 1.81 (bs, 1H), 2.92 (dd, J = 3.18, 16.32 Hz, 2H), 3.22 (dd, J = 5.85, 16.34 Hz, 2H), 4.67–4.73 (m, 1H), 7.18–7.19 (m, 2H), 7.25–7.28 (m, 2H). 13C NMR (100 MHz, CDCl3): δ (ppm) 42.66, 73.19, 125.00, 126.67, 140.81.
Octan-2-ol. 1H NMR (400 MHz, CDCl3): δ (ppm) 0.88 (t, J = 6.80 Hz, 3H), 1.18 (d, J = 6.00 Hz, 3H), 1.30–1.45 (m, 10H), 3.74–3.82 (m, 1H). 13C NMR (100 MHz, CDCl3): δ (ppm) 14.04, 22.59, 23.43, 25.72, 29.30, 31.82, 39.36, 68.12.
Heptan-2-ol. 1H NMR (400 MHz, CDCl3): δ (ppm) 0.90 (t, J = 6.80 Hz, 3H), 1.19 (d, J = 6.40 Hz, 3H), 1.29–1.36 (m, 4H), 1.39–1.47 (m, 4H), 3.76–3.85 (m, 1H). 13C NMR (100 MHz, CDCl3): δ (ppm) 14.02, 22.63, 23.46, 25.44, 31.84, 39.33, 68.18.
2.5. Product analysis
Gas chromatograph is equipped with 5% diphenyl and 95% dimethyl siloxane, Restek capillary column (60 m length, 0.32 mm dia) and a flame ionization detector (FID). The initial column temperature was increased from 60 to 150 °C at the rate of 10 °C min−1 and then to 220 °C at the rate of 40 °C min−1. N2 was used as a carrier gas. The temperatures of the injection port and FID were kept constant at 150 and 250 °C, respectively during product analysis.
3. Results and discussion
3.1. Catalyst characterization
3.1.1. Homogeneous catalyst [Ru(acac)2(CH3CN)2]. [Ru(acac)2(CH3CN)2] was characterized by FT-IR and NMR spectral techniques. It exhibited a band at 2257 cm−1 in its FT-IR spectrum, which corresponds to the fundamental ν2 –C
N stretching frequency. The signals at 1510 and 1564 cm−1 are characteristic of coordinated acetylacetone ligands. Two bands at 2920 and 2977 cm−1 are assigned to symmetric –CH and –CH3 stretching vibrations. The 1H NMR spectrum of the complex showed a singlet around 1.7–1.8 ppm, which has been attributed to the methyl protons present in the coordinated acetylacetone ligands. In addition, the complex showed another singlet at 5.2 ppm, which has been assigned to methine proton of acetylacetonate. The resonance at 2.64 ppm is due to the methyl protons of coordinated acetonitrile ligands. The 13C NMR spectrum of the complex showed expected resonances. The signals observed in the range 27.6–27.7 ppm have been assigned to the methyl carbons of acetylacetonate ligands. The resonances due to CO carbons appeared at 183.8 and 185.4 ppm. The methyl carbon of acetonitrile and acetylacetonate γ-CH showed signals at 4.3 and 99.4 ppm respectively.
3.1.2. Heterogenized catalyst (‘SiO2’–NH2–RuII). The newly prepared heterogenized catalyst was characterized by different analytical techniques. SEM images are shown in the ESI,† which indicate the morphology change on silica surface during the synthesis of heterogenized catalyst. ICP-OES confirms that the Ru loading is approximately 0.089% per weight of the total silica mass (8.82 × 10−6 mol g−1 of Ru on silica). A BET surface area of unfunctionalized silica was 225 m2 g−1; whereas Ru anchored silica showed a surface area of 207 m2 g−1. The expected decrease in the surface area results from the attachment of Ru complex on to the surface of silica via silyloxy linkages. The 29Si CP-MAS NMR spectrum showed two peaks that indicate the presence of two different forms of silicon. The peaks at −110.19 and −66.06 ppm are characteristic of Q-type [Si(O−)4] and T-type [R1–Si–(O−)3] silicates respectively. During the grafting process of 3-aminopropyl-1-triethoxysilane, out of three ethoxy groups, only one or two underwent reaction in some cases and the unreacted ethoxy group(s) might have contributed to the split in the peak at ∼−66 ppm (Fig. 1).33 In the 13C CP-MAS NMR spectrum, the intense signals at 21.94, 33.21 and 54.04 ppm were assigned to three carbons of propyl moiety, which confirmed the attachment of amino propyl groups on to the silica. A signal at 175.4 ppm indicates the CO resonance of acetylacetonate. The coordinated acetonitrile ligands did not show any signal due to shielding effect (Fig. 2).34
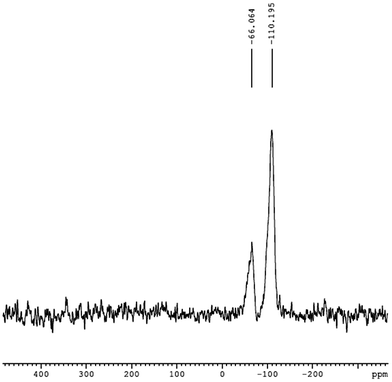 |
| Fig. 1 29Si CP-MAS solid state NMR spectrum of ‘SiO2’–NH2–RuII. | |
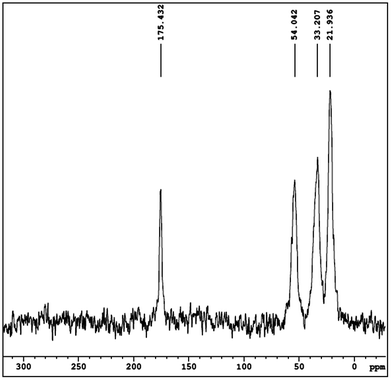 |
| Fig. 2 13C CP-MAS solid state NMR spectrum of ‘SiO2’–NH2–RuII. | |
3.2. Ruthenium-catalyzed transfer hydrogenation of carbonyl compounds
3.2.1. Optimization of reaction conditions. Initially transfer hydrogenation reaction was optimized with [Ru(acac)2(CH3CN)2] using acetophenone as a model substrate. Very narrow conversion was observed with NEt3–HCOOH or HCOONa as a hydrogen donor at 90 °C (Table 1, entries 1 and 2). The satisfactory conversion was achieved within 10 h when isopropanol was utilized as a hydrogen donor. It was found that isopropanol–water mixture was not effective (Table 1, entries 3–6), while 98% conversion was achieved using isopropanol alone as solvent and also as hydrogen donor (Table 1, entry 11). Of different bases studied, sodium hydroxide gave better conversion (Table 1, entries 7–9). The transfer hydrogenation of acetophenone at 80 °C with 2 mol% of catalyst, 1 equiv. of sodium hydroxide and isopropanol afforded an excellent conversion of 98%. The transfer hydrogenation of various substrates was studied under optimized conditions.
Table 1 Effect of solvent, base and catalyst amount on transfer hydrogenation of acetophenonea
For heterogeneous catalytic system, except catalyst quantity all other variables are unchanged. The 0.02 mol% of heterogeneous catalyst was identified as ideal quantity for productive conversion. Further reduction of catalyst amount led to extended reaction time.
3.2.2. Extension of scope. With optimal reaction conditions, transfer hydrogenation of ketones catalyzed by [Ru(acac)2(CH3CN)2] (2 mol%) was studied in refluxing isopropanol (Table 2). After 4 to 9 h, most of the ketones tested have shown greater than 87% yield. The substrates with electron withdrawing group provided the desired alcohol in good yield within 4 h (Table 2, entries 4–6). Acetophenones bearing an electron donating group required longer reaction time to reach high yield (Table 2, entries 2, 3 and 7). The electronic effect is obvious, that electron withdrawing groups favoured the transfer hydrogenation reaction. The reaction scales well, affords a high isolated yield and utilizes relatively less amount of catalyst.35,36 Interestingly 1-(furan-3-yl)ethanone achieved a maximum yield of 99% over a period of 9 h (Table 2, entry 8).
Table 2 Transfer hydrogenation of carbonyl compounds by [Ru(acac)2(CH3CN)2]a
In recent times the heterogenized catalysts attracted much attention due to several advantages such as ease of work up, isolation of the final product without contamination, recovery and reuse of expensive and toxic catalyst.29–32 The substrate scope of heterogenized catalyst (0.02 mol%) was extended to various ketones. 1-(2-Naphthyl)ethanone was converted into the corresponding alcohol in 24 h with excellent isolated yield of 98% (Table 3, entry 1). The substrates with electron withdrawing group (Table 3, entries 2 and 3) at ortho or para position showed excellent yield of 99%. These results are in agreement with the earlier reports on ruthenium catalyzed transfer hydrogenation of ketones.8,37 1-Cyclohexylethanone exhibited slow conversion (Table 3, entry 5). However an additional amount of catalyst was not used to speed up the reaction. 2-Indanone underwent an excellent transformation to give 92% of the desired product (Table 3, entry 6). Linear aliphatic ketones were smoothly reduced to secondary alcohols after extended reaction time (Table 3, entries 7 and 8).
Table 3 Transfer hydrogenation of carbonyl compounds by ‘SiO2’–NH2–RuIIa
To compare the catalytic performance of homogeneous system with that of heterogenized system, a set of aromatic ketones were subjected to transfer hydrogenation under identical conditions (Table 4). In both the systems, alcohols were obtained in excellent yield (>97%). Since the catalyst was heterogenized by exchanging one of the acetonitrile ligands by a surface-bound basic donor ligand, extended reaction time is inevitable. It was understood that the additional electron density supplied by a base (ligand) reduces the catalytic activity to certain extend.38 Heterogeneous transfer hydrogenation of 4′-aminoacetophenone gave a lower yield of 66% (Table 4, entry 3). The denounced catalytic activity may be due to the coordination of amine substrate to the Ru centre. Interestingly heteroaromatic ketones showed a better yield of 97% (Table 4, entry 6). All the above results indicate that the efficiency of heterogenized system is comparable to that of parent homogeneous catalytic system except the prolonged reaction hours. However, very less loading of Ru should be noted, which made the heterogenized catalyst superior.
Table 4 A comparison between homogeneous and heterogenized ruthenium catalysts: transfer hydrogenation of carbonyl compounds by [Ru(acac)2(CH3CN)2] (2 mol%)/‘SiO2’–NH2–RuII (0.02 mol%)a
3.2.3. Heterogeneous nature of the catalyst. The hot filtration test was performed to assure the durability of the heterogenized catalyst. A portion of reaction mixture from the reduction of acetophenone at approximately 50% conversion was filtered and the reaction was allowed to proceed in the filtrate (Fig. 3). Even after extended period, there was no further reaction occurred in the filtrate, whereas original reaction proceeded to completion. Thus it is evident that no trace of Ru metal leaches out from the supported catalyst.
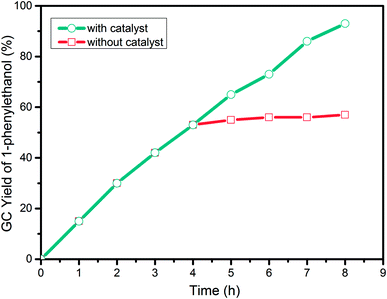 |
| Fig. 3 Hot filtration test for transfer hydrogenation of acetophenone. | |
3.2.4. Reusability. After completion of the reaction, the heterogenized catalyst was filtered and slurry was washed with water and ethanol. The recovered catalyst was dried under vacuum at 80 °C for 4 h. It was reused up to 6 times without significant loss of catalytic activity (Fig. 4). At 6th run the conversion remained at 90%, indicating that ‘SiO2’–NH2–RuII has an ability to consider as reusable catalyst. The Ru wt% (0.087) of the recovered catalyst is comparable to that of fresh catalyst. The FT-IR spectrum of the recovered catalyst showed shift in the stretching frequency values compared to the fresh catalyst, which indicates the replacement of coordinated acetonitrile by water during the workup of transfer hydrogenation reaction (Fig. 5).
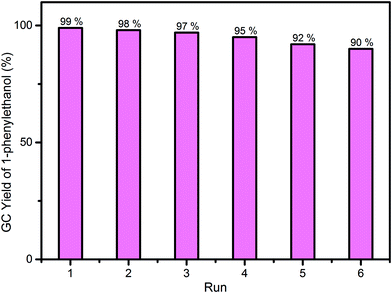 |
| Fig. 4 Reusability of ‘SiO2’–NH2–RuII for transfer hydrogenation of acetophenone. | |
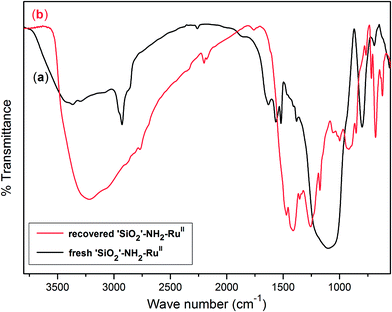 |
| Fig. 5 Comparison of IR spectra of (a) fresh and (b) recovered catalyst. | |
4. Conclusion
We have prepared and characterized homogeneous and heterogenized ruthenium catalysts consisting of acetonitrile as labile ligand. Their catalytic activity towards transfer hydrogenation has been studied and compared. Both the catalysts showed excellent activity. To the advantage, 0.02 mol% of heterogenized catalyst was sufficient for efficient conversion. This simple protocol is safe and economically viable for transfer hydrogenation of carbonyl compounds. Moreover the heterogenized catalyst was efficiently recycled and found to be a reusable catalyst.
Acknowledgements
S.G. and K.S. thank Syngene International Ltd., Biocon Park, Bangalore, India for encouragement. P.J. and R.K. thank Department of Science and Technology, Government of India for financial support.
References
- M. A. Bennett, M. I. Bruce and T. W. Matheson, in Comprehensive Organometallic Chemistry, ed. G. Wilkinson, F. G. A. Stone and E. W. Abel, Pergamon Press, Oxford, England, 1982, vol. 4, p. 945 Search PubMed.
- R. Noyori and S. Hashiguchi, Acc. Chem. Res., 1997, 30, 97 CrossRef CAS.
- T. Naota, H. Takaya and S. I. Murahashi, Chem. Rev., 1998, 98, 2599 CrossRef CAS PubMed.
- J. E. Backvall, R. L. Chowdhury, U. Karlsson and G. Wang, in Perspectives in Coordination Chemistry, ed. A. F. Williams, C. Floriani and A. E. Merbach, Wiley VCH, New York, 1992, p. 463 Search PubMed.
- B. M. Trost and I. Fleming, in Comprehensive Organic Synthesis, Pergamon Press, New York, 1991, vol. 2, p. 133 Search PubMed.
- M. Hudlicky, in Reductions in Organic Chemistry, American Chemical Society Monograph, Washington DC, 2nd edn, 1996, vol. 188, p. 19 Search PubMed.
- T. Ikariya, K. Murata and R. Noyori, Org. Biomol. Chem., 2006, 4, 393 CAS.
- I. Nieto, M. S. Livings, J. B. Sacci, L. E. Reuther, M. Zeller and E. T. Papish, Organometallics, 2011, 30, 6339 CrossRef CAS.
- J. R. Ruiz and C. J. Sanchidrian, Curr. Org. Chem., 2007, 11, 1113 CrossRef CAS.
- D. Klomp, U. Hanefeld and J. A. Peters, Hydrogenation Including the Meerwein–Ponndorf–Verley Reduction, Wiley-VCH, GmbH & Co. KGaA, Weinheim, Berlin, Germany, 2007, p. 585 Search PubMed.
- J. DePasquale, M. Kumar, M. Zeller and E. T. Papish, Organometallics, 2013, 32, 966 CrossRef CAS.
- E. Kathelyne, M. Andre and C. Jean-Francois, Adv. Synth. Catal., 2003, 345, 67 CrossRef.
- S. Cabrera, O. G. Mancheno, R. G. Arrayas, I. Alonso, P. Mauleon and J. C. Carretero, Pure Appl. Chem., 2006, 78, 257 CrossRef CAS.
- T. J. Colacot, Chem. Rev., 2003, 103, 3101 CrossRef CAS PubMed.
- C. Madrigal, A. Garcia-Fernandez, J. Gimeno and E. Lastra, J. Organomet. Chem., 2008, 693, 2535 CrossRef CAS PubMed.
- J. I. VanderVlugt and J. N. H. Reek, Angew. Chem., Int. Ed., 2009, 48, 8832 CrossRef CAS PubMed.
- A. A. Mikhailine, M. I. Maishan, A. J. Lough and R. H. Morris, J. Am. Chem. Soc., 2012, 134, 12266 CrossRef CAS PubMed.
- J. F. Sonnenberg, N. Coombs, P. A. Dube and R. H. Morris, J. Am. Chem. Soc., 2012, 134, 5893 CrossRef CAS PubMed.
- P. O. Lagaditis, A. J. Lough and R. H. Morris, J. Am. Chem. Soc., 2011, 133, 9662 CrossRef CAS PubMed.
- A. A. Mikhailine and R. H. Morris, Inorg. Chem., 2010, 49, 11039 CrossRef CAS PubMed.
- F. R. Silvana and E. K. Fritz, Chem. Rev., 2009, 109, 2061 CrossRef PubMed.
- F. E. Kühn, D. Schön, G. Zhang and O. J. Nuyken, J. Macromol. Sci., Part A: Pure Appl. Chem., 2000, 37, 971 CrossRef PubMed.
- R. Noyori, Angew. Chem., Int. Ed., 2002, 114, 2108 CrossRef.
- W. S. Knowles, Adv. Synth. Catal., 2003, 345, 3 CrossRef CAS.
- H. B. Blaser, Adv. Synth. Catal., 2002, 344, 17 CrossRef CAS.
- Y. Hoshino, Y. Yukawa, T. Maruyama, A. Endo, K. Shimizu and G. P. Sato, Inorg. Chim. Acta, 1990, 174, 41 CrossRef CAS.
- T. Kobayashi, Y. Nishina, K. Shimizu and G. P. Sato, Chem. Lett., 1988, 17, 1137 CrossRef.
- W. E. Buschmann and J. S. Miller, Chem. - Eur. J., 1998, 4, 1731 CrossRef CAS.
- Y. Arakawa, A. Chiba, N. Haraguchi and S. Itsuno, Adv. Synth. Catal., 2008, 350, 2295 CrossRef CAS.
- J. Li, Y. Zhang, D. Han, Q. Gao and C. Li, J. Mol. Catal. A: Chem., 2009, 298, 31 CrossRef CAS PubMed.
- A. M. Hayes, D. J. Morris, G. J. Clarkson and M. Wills, J. Am. Chem. Soc., 2005, 127, 7318 CrossRef CAS PubMed.
- R. Somanathan, N. A. Cortez, M. P. Hake, D. Chavez and G. Aguirre, Mini-Rev. Org. Chem., 2008, 5, 313 CrossRef CAS.
- A. R. McDonald, H. P. Dijkstra, B. M. J. M. Suijkerbuijk, G. P. M. van Klink and G. van Koten, Organometallics, 2009, 28, 4689 CrossRef CAS.
- M. A. Bennett, G. Chung, D. C. R. Hockless, H. Neumann and A. C. Willis, J. Chem. Soc., Dalton Trans., 1999, 3451 RSC.
- W. Du, P. Wu, Q. Wang and Z. Yu, Organometallics, 2013, 32, 3083 CrossRef CAS.
- F. Zeng and Z. Yu, Organometallics, 2009, 28, 1855 CrossRef CAS.
- L. P. He, T. Chen, D. X. Xue, M. Eddaoudi and K. W. Huang, J. Organomet. Chem., 2012, 700, 202 CrossRef CAS PubMed.
- S. Gago, Y. Zhang, A. M. Santos, K. Köhler, F. E. Kühn, J. A. Fernandes, M. Pillinger, A. A. Valente, T. M. Santos, P. J. A. R. Claro and I. S. Gonçalves, Microporous Mesoporous Mater., 2004, 76, 131 CrossRef CAS PubMed.
Footnote |
† Electronic supplementary information (ESI) available: Characterization details of catalysts and catalytic products, and gas chromatograms. See DOI: 10.1039/c4ra04136d |
|
This journal is © The Royal Society of Chemistry 2014 |
Click here to see how this site uses Cookies. View our privacy policy here.