DOI:
10.1039/C4RA03190C
(Paper)
RSC Adv., 2014,
4, 26309-26315
PEI@SiO2: synthesis from diatomite and application for capturing phenolic compounds from aqueous solution†
Received
9th April 2014
, Accepted 28th May 2014
First published on 28th May 2014
Abstract
A “dissolving and rebuilding” method was applied to prepare a diatomiteethyleneimine–polymer (PEI) hybrid composite, and its structure and topography were characterized by XRD, SEM, TEM, FTIR, DTG, elemental analysis and ζ-potential. The results indicated that the PEI was efficiently assembled into the SiO2 framework formed from diatomite. Attempts were made to use the composite to remove phenolic pollutants, e.g. phenol, o-chlorophenol and bisphenol A (BPA), from aqueous solution. These adsorptions were to be in accordance with lipid–water-partition law, and their Kaw values were calculated to be 79.1 L kg−1 for phenol, 37.3 L kg−1 for o-chlorophenol and 24.2 L kg−1 for BPA.
1. Introduction
Phenolic compounds are almost ubiquitous contaminants because of their widespread appearance in wastewater from discharged oil refineries, the paint, drug and pesticide industries, as the intermediates of processes.1 The potential toxicity of phenol derivatives has received increasing attention, and some have been proven to be toxic.2–5 For example, bisphenol A (BPA) can cause damage to the reproductive system and can affect cellular development.5–7 Chlorophenol may cause inflammation in the digestive system and increase blood pressure.8 Because of their toxicity, phenolic compounds incorporate two classes of compounds widely prevalent and classified by the US Environmental Protection Agency as priority pollutants.9 As per the recommendation of the World Health Organization, the threshold concentration of phenol in drinking water should fall below 1.0 μg L−1.10
During recent decades, there has been significant interest in development of efficient techniques for removal of highly toxic organic compounds such as pesticides, fertilizers, hydrocarbons, phenols and plasticizers, from wastewater.11–14 The adsorption technique was quite popular because of its simplicity, as well as the availability of a wide range of adsorbents.15,16 For adsorption of phenolic compounds from aqueous solution, various adsorbents such as granular activated carbon and fibrous activated carbon,17 mesoporous alumina-aluminum phosphates,18 synthetic polymers19 and ion exchange resins,20 have been used. In recent years, a strategy to remove organic pollutants using natural minerals was developed owing to their flexibility, general applicability and low cost.21–23 However, low adsorption capacity and poor selectivity restrict application of original natural minerals.24 Recently, further efforts in chemical modification of the pristine minerals have offered new possibilities for preparation of new materials with superior performances for a variety of applications. For instance, Bhardwaj et al. modified clinoptilolite and zeolite Y for adsorbing 2,4-dichlorophenoxyacetic acid,25 and Xie et al. demonstrated a versatile chitosan modified zeolite for removal of different pollutants from water.26 So far, impregnation, acid pickling, calcining and ionic exchange have been employed to modify natural pristine minerals. However, the conventional surface modification usually brings out some serious defects, for example unapparent improvement in adsorption capacity and easy separation of active group.10,27,28
PEI, which is composed of a large number of primary and secondary amine groups,29 exhibits outstanding adsorption ability for various pollutants,30,31 e.g. carbon dioxide,32 heavy metals29,33 and phenols.34 Diatomite is known as an adsorbent for pollution control.35–37 It can be dissolved easily to form abundant amorphous silica (SiO2·nH2O) under hydrothermal conditions. In previous papers, mesoporous materials, such as MCM-41,38–41 mordenite42 and ZSM-5 zeolites,43,44 have been obtained from natural diatomite under hydrothermal conditions. Thus it is possible to turn diatomite and PEI into a multifunctional hybrid adsorbent for phenols using a “dissolving and rebuilding” method.
In the present work, an innovative approach, i.e. dissolving and rebuilding, was used to prepare a hybrid composite PEI@SiO2 by dissolving PEI in the diatomite alkaline solution. As an excellent sorbent, it was used to adsorb phenolic compounds with a high adsorption capacity. The simple synthesis overcomes the disadvantages of traditional surface modification.
2. Experimental
2.1 Apparatus and materials
A photodiode array spectrometer (Model S4100, Scinco, Korea) was used to determine phenolic compounds in aqueous solutions. The concentrations of mixed phenolic compounds in the supernatants were measured by high-performance liquid chromatography (HPLC) with a DAD detector (Model LC 2000, Hitachi, Japan). The elemental analysis device (Model Vario EL III, Germany) was used to determine C, N and H contents of the hybrid composite. The microstructure and morphology of the material were measured by scanning electronic microscopy (SEM) (Model Quanta 200 FEG, FEI Co., USA) and transmission electron microscopy (TEM) with an energy dispersive X-ray detector (Model TECNAI G2 S-TWIN, FEI Co., USA). The FT-IR spectra of the hybrid composite were obtained, using an infrared spectrometer system (Model Equinoxss/hyperion 2000, BRUKER Co., Germany). The X-ray diffraction (XRD) (Model Bruker D8 Advance, Germany) was recorded using CuK radiation in the range of ∼10–90° 2θ at 40 kV and 40 mA. A thermal analysis system (Model Q600 SDT Simultaneous DSC/TGA, TA instruments, USA) was used for thermogravimetry analysis (TGA) of the materials. A ζ-potential instrument (Zetasizer Nano Z, Malvern, UK) was used to determine the surface potential of the PEI@SiO2 composite. An inductively coupled plasma optical emission spectrometer (ICP-OES) (Model Optima 2100 DV, PerkinElmer, USA) was used to determine metal contents in materials.
Diatomite (Aladdin Agents, China), sodium hydroxide (Aladdin Agents, China), PEI (M.W. 600, Aladdin Agents, China), sodium chloride (Aladdin Agents, China) and hydrochloric acid (Sinopharm Chemical Reagent Co., Ltd, China) were used. Three phenolic compounds, i.e. phenol, o-chlorophenol and BPA (Aladdin Agents, China), adsorbing on the PEI@SiO2 were investigated. As, Bi, Cd, Cu, Cr, Fe, Hg, Mn, Ni, Se, Pb, Zn multi-element mixed standard solutions (100 ppm, Aladdin Agents, China) were used.
2.2 Synthesis and characterization of the PEI@SiO2
Diatomite (20 g) was added to 1000 mL of 2 mol L−1 sodium hydroxide, and stirred at 500 rpm for 24 h at 363 K. The mixture was centrifuged to remove insoluble residue into the supernatant containing 17.66 g L−1 diatomite, 0.21 M PEI was added and the solution was adjusted to pH 10 with 1 M HCl under stirring. After 24 h, the PEI@SiO2 suspension was centrifuged and washed for several times with deionized water. The PEI@SiO2 product was dried and ground into powder for characterization of the structure, composition and morphology. The PEI content was calculated by determining C content with an elemental analysis device. The PEI@SiO2 powder was digested with 2.0 M sodium hydroxide and Al, Fe and Si contents in the supernatant were determined by ICP-OES. Using the same method, SiO2-only product formed from diatomite was prepared where PEI was not added.
2.3 Adsorption of phenolic compounds
The adsorption capacity of the PEI@SiO2 composite to three phenolic compounds was determined. Phenol solutions from 6 to 500 mg L−1 were treated with 0.3% of the PEI@SiO2 composite. All of the liquids were mixed for 30 min at 500 rpm by a magnetic stirrer and then centrifuged to separate adsorbent residue. The phenol concentrations remaining in the supernatants were determined by UV spectrophotometry. Using the same method, o-chlorophenol solutions from 6 to 650 mg L−1 and BPA solutions from 3 to 400 mg L−1 were treated.
The influences of pH from 3 to 11, ionic strength from 0 to 0.25 M, temperature from 298 to 328 K and the mixing time from 0 to 30 min were investigated for three phenolic compounds adsorbing to the PEI@SiO2 composite.
2.4 Treatment of phenolic wastewater and disposal of the waste
Three phenolic wastewaters containing 20 mg L−1 phenol, 42 mg L−1 o-chlorophenol and 38 mg L−1 BPA, respectively, were treated with the PEI@SiO2 from 0.1 to 1.8%. The phenolic compound remaining in each supernatant was determined by UV spectrophotometry. In addition, their mixed solution was treated with the PEI@SiO2 from 0.1 to 1.8%. The phenolic compounds in the supernatants were determined by high-performance liquid chromatography (HPLC) with a DAD detector (Model LC 2000, Hitachi, Japan), where phenol was detected at 270 nm at 5.64 min, o-chlorophenol at 275 nm at 6.56 min and BPA at 286 nm at 8.36 min. The flow phase consisted of CH3OH and H2O according to 50
:
50 (V
:
V) at 0.5 mL min−1 of the flow speed through a chromatographic column (Model Allsphere ODS-25 μm, length 250 mm). The injection volume was 20 μL.
The phenol–PEI@SiO2 waste (20 g) produced as above was calcined for 6 h at 550 °C with a Muffle furnace (Model SXL-1008, Shanghai Jinghong Lab Equipments Co., China). The residue was ground into powder approximately being 200 mesh. The phenol–PEI@SiO2 waste calcined (0.5% (w/v)) was added to the As, Bi, Cd, Cu, Cr, Fe, Mn, Ni, Se, Pb multi-element mixed standard solution (1 mg L−1) at pH 5 under stirring for 2 h. After the mixtures were centrifuged, the removal rates of pollutants in the supernatants were determined by ICP.
3. Results and discussion
3.1 Interaction of PEI with diatomite
When hybridizing PEI with diatomite to prepare the PEI@SiO2 composite, the hybridization amount of PEI increases with increase of the PEI dosage and then approaches equilibrium (Fig. 1A). Hybridization of PEI obeys the Langmuir isotherm model (Fig. 1B), i.e. ce/qe = 1/Klq∞ + ce/q∞,45 where ce is the equilibrium molarity of PEI in mol L−1, qe is the amount of PEI embedding in diatomite in mg g−1, q∞ is the saturation hybridization amount of PEI in mg g−1 and Kl is the binding constant of PEI. The maximum PEI embedding in the PEI@SiO2 composite approaches 258 mg g−1 and the Kl is calculated to be 25.4 M−1. A strong interaction, i.e. high affinity, occurs34 between PEI and diatomite. The Gibbs free energy (ΔG) is less than zero, indicative of spontaneous interaction of the PEI@SiO2. The hybridization amount of PEI increases with increase of pH from 7 to 10 and then declines very slightly (Fig. 1C). Thus, preparation of the hybrid material is carried out at pH 10. Diatomite is hydrolyzed to form dissolved diatomite. Dissolved diatomite and PEI with initial weight ratio 1
:
7 are applied to prepare the PEI@SiO2 at pH 10 (see the Experiment section).
 |
| Fig. 1 Effect of PEI on hybridization. (A) Plots qe vs. c0, (B) plots ce/qe vs. ce. (C) Effect of pH on hybridization of PEI. (D) Effect of water washing on the hybridization of PEI. | |
The basic chain structure of PEI is the alkyl chain (–[CH2–CH2–NH]–n), so there are a large number of nitrogen atoms of amino groups on the macromolecular chains of PEI. In aqueous solution, they may combine easily with H+ to form –[CH2–CH2–NH2+]–n,11,46,47 which means that the majority of amino groups on PEI chains are protonated. The chain of PEI may be positively charged, i.e. forming cationic polyelectrolyte,34 whereas diatomite particles are negatively charged, so both attract each other and PEI is adsorbed compactly to the surface of diatomite particles. The ζ-potential of diatomite-only is determined to be 34.0 mV in aqueous media, while that of the PEI@SiO2 composite changes to +12.9 mV. After hybridizing, the electric property of the surface of diatomite changes substantially; it depends on the character of macromolecule PEI, so the surface of modified diatomite has a positive charge because of the strong acceptability of N atoms of PEI chains for protons. Thus, electrostatic interaction occurs between PEI+ and diatomite.
It is well known that the main composition of diatomite is SiO2 (88%), Al2O3 and Fe2O3.48 The molar ratio of PEI to Si, Al and Fe is calculated as 1
:
248.5
:
61.8
:
2.6 in the PEI@SiO2, which is determined by element analysis and ICP. This provides evidence for formation of the PEI@SiO2 composite. Approximately 248.5 mg g−1 PEI is embedded in the composite, which is much more than reported elsewhere. In previous papers, Gao introduced an interesting study for modifying diatomite by PEI impregnation, and the maximum PEI embedding in the diatomite approached 128 mg g−1,34 and Öztekin employed bentonite clay particles to adsorb PEI with the maximum of PEI embedding approaching 145 mg g−1.49 Thus the “dissolving and rebuilding” approach increases the hybridization capacity of PEI more than the conventional surface modification approach. In addition, easy migration of active groups and secondary pollution are some serious defects of conventional surface modification,50,51 limiting its applications. PEI cannot be separated from the PEI@SiO2 composite by washing with water (Fig. 1D), which shows that the “dissolving and rebuilding” approach exhibits better resistance to migration of active groups than does conventional surface modification. Therefore, the composite is suitable for treatment of wastewater.
3.2 Structure and morphology of the PEI@SiO2
As shown in Fig. 2A, absorption peaks at 2935 (C–H stretching), 2819 (C–H stretching), 1756 (–NH2 and –NH– deformation) and 1471 (–NH2 and –NH– deformation) cm−1 indicate that PEI embedding in the PEI@SiO2 composite is confirmed from its infrared spectra (IR). The Si–O absorption peak is at 1059 cm−1. The XRD patterns for SiO2-only and PEI@SiO2 are shown in Fig. 2B. XRD patterns of SiO2-only and PEI@SiO2 all show a broad diffraction peak from 2θ = 15–30°, which indicates that SiO2 holds mainly amorphous silica structure and there is no prominent difference caused by PEI in the PEI@SiO2 composite,52–54 that is the main structure of the hybrid composite remains unchanged. If there is a nanocrystalline silica material, corresponding peaks should be observed at a definite diffraction angle.55 Similar work based on addition of ionic liquid coated sulfonic acid,54 β-cyclodextrin56 and nanosized NiO particles57 with functionalized amorphous silica composites has been reported with the prominent XRD peaks. As seen in the thermal gravimetric analysis (TGA) differential thermal gravity of PEI@SiO2 (Fig. 2C), the first step in the range of 40–200 °C is attributed to removal of the physisorbed water and interlayer water.58 Additional observed weight loss steps indicate the behavioral complexity of decomposition of the various covalently attached organic phases.59 The second step in the range of 200–400 °C is caused by removal of the branched chain group of, and the third step in the range of 400–500 °C is caused by the removal of the straight chain of PEI. Similar TGA weight losses profiling also arose from previous reports.59–61 The loss of weight between 200 °C and 500 °C indicates that approximately 25.3% PEI is embedded into the PEI@SiO2 composite, which accords with the above reaction rate of PEI. From the differential thermogravimetry analysis (DTG) curves (Fig. 2C and S1, ESI†), a new peak appears at around 272 °C for the PEI@SiO2 composite. This indicates the intermolecular interaction of PEI with SiO2. Fig. 2D illustrates the N2 sorption isotherm and the pore-size distribution with the Barrett–Joyner–Halenda method of PEI@SiO2. The isotherm is classical type IV, which refers to the mesoporous materials. Furthermore, the isotherms have two hysteresis loops, indicating a bimodal pore size distribution in the mesoporous regions. At the high relative pressure between 0.8 and 0.9, the hysteresis loops are type H1, suggesting the presence of cylindrical mesopores.62 The bimodal pore-size distribution is confirmed by the pore-size distribution in Fig. 4D. From the pore plots, no peak appeared in the pore, indicating the presence of irregular mesopores. The mesopores may be formed by the SiO2. The BET analysis of the material indicates that the specific surface area of PEI@SiO2 is determined to be 16.71 m2 g−1.
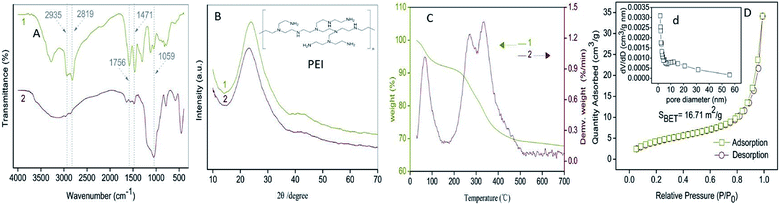 |
| Fig. 2 IR spectra (A) of PEI (A1), the PEI@SiO2 (A2) and XRD (B) of SiO2-only (B1), the PEI@SiO2 (B2), DTA of the PEI@SiO2 (C1), TGA of the PEI@SiO2 (C2) and N2 absorption–desorption isotherm and pore-size distribution (inset) for PEI@SiO2 (D, d). | |
 |
| Fig. 3 SEM images of PEI@SiO2 (A and B), diatomite (C), EDX of PEI@SiO2 (Aa) and TEM of PEI@SiO2 (D–F). | |
 |
| Fig. 4 (A) Adsorption of phenol (1), o-chlorophenol (2) and BPA (3) with PEI@SiO2. (B) The removal rate of phenol (1), o-chlorophenol (2) and BPA (3) with PEI@SiO2. Conditions-material dosage, 1.7–18 mg mL−1. (C) The removal rate of phenol (1), o-chlorophenol (2) and BPA (3) with the diatomite. Conditions-material dosage, 1.7–18 mg mL−1. (D) The removal rate of phenol (1), o-chlorophenol (2) and BPA (3) from their mixed solution with PEI@SiO2. Conditions-material dosage, 1.5–18 mg mL−1. | |
From the SEM images, diatomite consisting of the tiny aquatic organism remains fossilized (Fig. 3C). The PEI@SiO2 particles are irregular in the size of 100–500 nm and stack-up of the reticular structure (Fig. 3A and B), where all the macropores (>50 nm) disappear (Fig. 3B). The pore size distribution (see Fig. S2, ESI†) is also similar for many amorphous silica studied.63 The C, N, O, Al and Si are observed in the interior of the PEI@SiO2 composite from the EDX (Fig. 3Aa). Just as one kind of adhesive, PEI is bridging among SiO2 particles to change the morphology of the PEI@SiO2 composite (Fig. 3D). The stripes (red) of the SiO2 particles and the irregular block (blue) of PEI are found (Fig. 3E). The lattice spacing of the crystal grain is 0.20 nm (Fig. 3F). This indicates the Al2O3 crystal grains (yellow) formed (Fig. 3E).
3.3 Adsorption of solo phenolic compounds on PEI@SiO2
PEI contains lots of long hydrophobic chains so the PEI@SiO2 composite carries a large amount of hydrophobicity. lg
Kow is the logarithm of the n-octanol–water partition coefficient, which underestimates the partition of organic compounds between n-octanol and water phases. It is well known that o-chlorophenol (lg
Kow = 3.06) and BPA (lg
Kow = 3.32) are difficult to remove from water-drinking bodies by conventional methods, e.g. flocculation and disinfection.64 A few studies have suggested that phenolic compounds can be adsorbed by sorbent through intermolecular acting force (mainly hydrophobic interaction).34 Adsorption of phenol, o-chlorophenol and BPA in the PEI@SiO2 composite is to accord with the lipid–water-partition law (Fig. 4A). The partition coefficient (Kaw) of phenol is calculated to be 79.1 L kg−1, i.e. lg
Kaw = 3.90, which is more than lg
Kow. In addition, lg
Kaw = 1.38 for o-chlorophenol and 1.35 for BPA. The adsorption constant of phenol is 10−9.98. The benzene ring of the phenolic compounds may interact with the hydrophobic vinyl of PEI via a hydrophobic interaction. In addition, hydrogen bonds may form between PEI of the PEI@SiO2 composite and phenol.
The adsorption equilibrium is completed in 10 min (Fig. S3A, ESI†), which is much faster than that of activated carbon and the other polymer sorbents.65–68 It is considered that a hydrophobic interaction between adsorbent and organic compounds might be attributed to the rapid adsorption rate.69 The rapid adsorption of phenolic compounds on PEI@SiO2 ensures that sufficient time is available for adsorption equilibration to get at the usual operator condition of the adsorption. The pH of solution has not seriously affected the adsorption of those phenolic compounds (Fig. S3B, ESI†). However, in a previous paper, the adsorption capacities of diatomite with the conventional surface modification were very different under different conditions of pH values.34 The sorption of phenolic compounds on diatomite modified by the conventional surface is the mode of monomolecular layer adsorption,49,70,71 while the adsorption of phenolic compounds in PEI@SiO2 composite is to accord with the lipid–water-partition law. Diatomite modified by the conventional surface interacts with phenolic compounds via hydrogen bond interaction, and the hydrogen bond interactions between PEI on diatomite surface and phenolic compounds are affected by the change of pH values.34 However, PEI@SiO2 interacts with phenolic compounds via the hydrophobic interaction and the hydrophobic interaction stays steady at different pH values. With ionic strength increasing from 0.05 to 0.2 mol L−1, qe of phenol, o-chlorophenol and BPA increase by 31.5%, 15.1% and 6.4%, respectively (Fig. S3C, ESI†). It is considered that the hydrogen bonding between phenolic compounds and H2O becomes weak at higher ionic strength, which makes phenolic compound molecules freely available.72–74 Hence, it is attributed that ionic strength can strengthen the hydrophobic interaction between phenolic compounds and PEI@SiO2. Temperature is an important parameter for any separation process.75 With the temperature increasing from 297 to 315 K, qe of phenol decreases by 17.8%, while that of o-chlorophenol and BPA remains almost constant (Fig. S3D, ESI†). It is obvious the equilibrium adsorption capacity increases with increment of the equilibrium concentration but decreases with increasing temperature, suggesting that adsorption is favorable while an exothermic process.76 A change in adsorption capacity with temperature is possibly because the adsorbate has a tendency to escape from the solid phase to the solution when the interaction is exothermic.72
3.4 Effect of adsorbent dosage
Effects of the PEI@SiO2 composite's dosage were determined on adsorption of a mixture of three phenolic compounds (20 mg L−1 phenol, 42 mg L−1 o-chlorophenol and 38 mg L−1 BPA) and the results are shown in Fig. 4B and C. The removal rates of the three phenolic compounds increase with increasing dosage. The PEI@SiO2 composite removed 47% phenol, 68% o-chlorophenol and 89% BPA; however, diatomite removed only 16% phenol, 39% o-chlorophenol and 11% BPA (Fig. 4B). Also, being different from the PEI@SiO2 composite, diatomite adsorbing phenolic compounds obey the Freundlich model (Fig. 4C).36,45 Therefore, diatomite interacting with phenolic compounds is different from the PEI@SiO2 composite. The most possible reason is that the active group –O of diatomite interacted with phenolic compounds via hydrogen bonds. The PEI chain embedding into the PEI@SiO2 composite bound to phenolic compounds via hydrophobic interaction.
The mixture solution of 20 mg L−1 phenol, 42 mg L−1 o-chlorophenol and 38 mg L−1 BPA is treated with the PEI@SiO2 composite. From the results shown in Fig. 4D, 0.18% of the PEI@SiO2 composite removed 37% phenol, 45% o-chlorophenol and 60% BPA. Compared with Fig. 4B, the adsorption of phenol, o-chlorophenol and BPA decreased by 21%, 34% and 33%, respectively. When three solutes compete for sorption in the trisolute system, the sorption amount of each solute is less than that in a single-solute system. It indicated that competitive adsorption occurred among the three phenolic compounds. As a result of limited active sites of the PEI@SiO2, competitive hydrophobic interactions of the three phenolic compounds are expected to be the mechanism for inhibited desorption.17,77
3.5 Treatment of heavy metals with the phenol–PEI@SiO2 waste calcined
To avoid secondary pollution and increase the comprehensive use of resource, recycling of spent materials is often necessary.78 After the PEI@SiO2 sludge with phenol is calcined at 550 °C, all organic compounds (phenol and PEI) are decomposed. The material calcined consists of SiO2 and Al2O3, which is capable of adsorbing metals.79 The removal rates of Bi3+, Fe3+ and Cu2+ are more than 75% (Fig. 5).
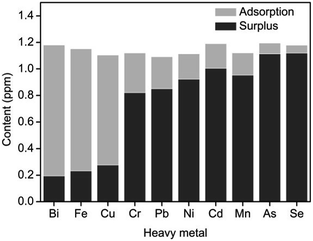 |
| Fig. 5 The adsorption of multi-metals mixed with the phenol–PEI@SiO2 waste calcined. | |
4. Conclusions
We have demonstrated an innovative method (dissolving and rebuilding) for producing hybrid adsorbent using natural mineral and organic polymer. Such a material has more hybrid amount of PEI, compared with reported materials.34 More than 22.9% PEI is embedded so that the sorbent contains a large number of active sites, which results in exceptional adsorption capacity towards phenolic compounds. It conforms to the lipid–water-partition law and the Kaw of phenol, o-chlorophenol and BPA are 79.1 L kg−1, 37.3 L kg−1 and 24.2 L kg−1. After calcinations of the used PEI@SiO2, the phenol–PEI@SiO2 waste calcined exhibits a good sorption capacity to heavy metals and also can be used to eliminate heavy metal pollutant. This work has provided a novel approach for preparation of environmentally friendly inorganic–organic hybrids.
Notes and references
- D. M. Nevskaia, E. Castillejos-Lopez, V. Munoz and A. Guerrero-Ruiz, Environ. Sci. Technol., 2004, 38, 5786–5796 CrossRef CAS.
- R. S. Juang, F. C. Wu and R. L. Tseng, J. Chem. Eng. Data, 1996, 41, 487–492 CrossRef CAS.
- B. N. Estevinho, I. Martins, N. Ratola, A. Alves and L. Santos, J. Hazard. Mater., 2007, 143, 535–540 CrossRef CAS PubMed.
- M. O. Maebana, S. B. Mishra, B. B. Mamba and A. K. Mishra, J. Appl. Polym. Sci., 2013, 128, 2073–2080 CAS.
- J. Y. Hu, T. Aizawa and Y. Magara, Water Res., 1999, 33, 417–425 CrossRef CAS.
- L. A. Jones and R. A. Hajek, Environ. Health Perspect., 1995, 103, 63–67 CrossRef.
- A. Kortenkamp and R. Altenburger, Sci. Total Environ., 1999, 233, 131–140 CrossRef CAS.
- S. H. Song and M. Kang, J. Ind. Eng. Chem., 2008, 14, 785–791 CrossRef CAS PubMed.
- M. Sarkar and P. K. Acharya, Waste Manage., 2006, 26, 559–570 CrossRef CAS PubMed.
- M. Aivalioti, P. Papoulias, A. Kousaiti and E. Gidarakos, J. Hazard. Mater., 2012, 207, 117–127 CrossRef PubMed.
- M. Amara and H. Kerdjoudj, Desalination, 2003, 155, 79–87 CrossRef CAS.
- V. Kavitha and K. Palanivelu, J. Photochem. Photobiol., A, 2005, 170, 83–95 CrossRef CAS PubMed.
- Y. X. Zhang, Z. L. Liu, B. Sun, W. H. Xu and J. H. Liu, RSC Adv., 2013, 3, 23197–23206 RSC.
- Y. X. Zhang, X. Y. Yu, Z. Jin, Y. Jia, W. H. Xu, T. Luo, B. J. Zhu, J. H. Liu and X. J. Huang, J. Mater. Chem., 2011, 21, 16550–16557 RSC.
- Y. Fukazawa, W. Pluemsab, N. Sakairi and T. Furuike, Chem. Lett., 2005, 34, 1652–1653 CrossRef CAS.
- H. El-Hamshary, S. El-Sigeny, M. F. Abou Taleb and N. A. El-Kelesh, Sep. Purif. Technol., 2007, 57, 329–337 CrossRef CAS PubMed.
- S. Kumar, M. Zafar, J. K. Prajapati, S. Kumar and S. Kannepalli, J. Hazard. Mater., 2011, 185, 287–294 CrossRef CAS PubMed.
- T. G. Danis, T. A. Albanis, D. E. Petrakis and P. J. Pomonis, Water Res., 1998, 32, 295–302 CrossRef CAS.
- D. Drechny and A. W. Trochimczuk, React. Funct. Polym., 2006, 66, 323–333 CrossRef CAS PubMed.
- S. Dutta, J. K. Basu and R. N. Ghar, Sep. Purif. Technol., 2001, 21, 227–235 CrossRef CAS.
- C. Volzone, Appl. Clay Sci., 2007, 36, 191–196 CrossRef CAS PubMed.
- V. K. Gupta, B. Gupta, A. Rastogi, S. Agarwal and A. Nayak, Water Res., 2011, 45, 4047–4055 CrossRef CAS PubMed.
- K. F. Lam, K. L. Yeung and G. McKay, Environ. Sci. Technol., 2007, 41, 3329–3334 CrossRef CAS.
- M. Rafatullah, O. Sulaiman, R. Hashim and A. Ahmad, J. Hazard. Mater., 2010, 177, 70–80 CrossRef CAS PubMed.
- D. Bhardwaj, P. Sharma, M. Sharma and R. Tomar, RSC Adv., 2014, 4, 4504–4514 RSC.
- J. Xie, C. J. Li, L. A. Chi and D. Y. Wu, Fuel, 2013, 103, 480–485 CrossRef CAS PubMed.
- A. F. D. de Namor, A. El Gamouz, S. Frangie, V. Martinez, L. Valiente and O. A. Webb, J. Hazard. Mater., 2012, 241, 14–31 CrossRef PubMed.
- K. G. Bhattacharyya and S. Sen Gupta, Adv. Colloid Interface Sci., 2008, 140, 114–131 CrossRef CAS PubMed.
- Y. L. Chen, B. C. Pan, H. Y. Li, W. M. Zhang, L. Lv and J. Wu, Environ. Sci. Technol., 2010, 44, 3508–3513 CrossRef CAS PubMed.
- M. Ghoul, M. Bacquet and M. Morcellet, Water Res., 2003, 37, 729–734 CrossRef CAS.
- Y. Kuwahara, D.-Y. Kang, J. R. Copeland, N. A. Brunelli, S. A. Didas, P. Bollini, C. Sievers, T. Kamegawa, H. Yamashita and C. W. Jones, J. Am. Chem. Soc., 2012, 134, 10757–10760 CrossRef CAS PubMed.
- R. Sanz, G. Calleja, A. Arencibia and E. S. Sanz-Pérez, J. Mater. Chem. A, 2013, 1, 1956–1962 CAS.
- P. E. Duru, S. Bektas, O. Genc, S. Patir and A. Denizli, J. Appl. Polym. Sci., 2001, 81, 197–205 CrossRef CAS.
- B. J. Gao, P. F. Jiang, F. Q. An, S. Y. Zhao and Z. Ge, Appl. Surf. Sci., 2005, 250, 273–279 CrossRef CAS PubMed.
- M. Jang, S. H. Min, J. K. Park and E. J. Tlachac, Environ. Sci. Technol., 2007, 41, 3322–3328 CrossRef CAS.
- G. D. Sheng, S. T. Yang, J. Sheng, J. Hu, X. L. Tan and X. K. Wang, Environ. Sci. Technol., 2011, 45, 7718–7726 CrossRef CAS PubMed.
- M. A. M. Khraisheh, M. A. Al-Ghouti, S. J. Allen and M. N. Ahmad, Water Res., 2005, 39, 922–932 CrossRef CAS PubMed.
- Y. A. Cao, Q. H. Yuan, X. J. Mu, Y. Q. Xu and B. L. Liu, Chin. J. Inorg. Chem., 2010, 26, 2243–2250 CAS.
- P. Yuan, D. Yang, Z. Y. Lin, H. P. He, X. Y. Wen, L. J. Wang and F. Deng, J. Non-Cryst. Solids, 2006, 352, 3762–3771 CrossRef CAS PubMed.
- D. D. Li, H. Y. Min, X. Jiang, X. Q. Ran, L. Y. Zou and J. W. Fan, J. Colloid Interface Sci., 2013, 404, 42–48 CrossRef CAS PubMed.
- J. G. Shao, W. J. Deng, Y. X. Yang, X. N. Liu and Y. R. Chen, Adsorpt. Sci. Technol., 2009, 27, 147–165 CrossRef CAS.
- V. Sanhueza, U. Kelm and R. Cid, J. Chem. Technol. Biotechnol., 2003, 78, 485–488 CrossRef CAS.
- V. Sanhueza, L. Lopez-Escobar, U. Kelm and R. Cid, J. Chem. Technol. Biotechnol., 2006, 81, 614–617 CrossRef CAS.
- V. Sanhueza, U. Kelm, R. Cid and L. Lopez-Escobar, J. Chem. Technol. Biotechnol., 2004, 79, 686–690 CrossRef CAS.
- S. K. Parida, S. Dash, S. Patel and B. K. Mishra, Adv. Colloid Interface Sci., 2006, 121, 77–110 CrossRef CAS PubMed.
- M. Amara and H. Kerdjoudj, Talanta, 2003, 60, 991–1001 CrossRef CAS.
- M. A. Andersson and R. Hatti-Kaul, J. Biotechnol., 1999, 72, 21–31 CrossRef CAS.
- S. Y. Shan, Q. M. Jia, L. H. Jiang, Q. C. Li, Y. M. Wang and J. H. Peng, Ceram. Int., 2013, 39, 5437–5441 CrossRef CAS PubMed.
- N. Öztekin, A. E. Alemdar, N. Gungor and F. B. Erim, Mater. Lett., 2002, 55, 73–76 CrossRef.
- W. X. Zhao, Q. Ma, L. S. Li, X. R. Li and Z. L. Wang, J. Adhes. Sci. Technol., 2014, 28, 499–511 CrossRef CAS.
- J. Abenojar, R. Torregrosa-Coque, M. A. Martinez and J. M. Martin-Martinez, Surf. Coat. Technol., 2009, 203, 2173–2180 CrossRef CAS PubMed.
- N. Ghaemi, S. S. Madaeni, A. Alizadeh, H. Rajabi and P. Daraei, J. Membr. Sci., 2011, 382, 135–147 CrossRef CAS PubMed.
- J. Kim, S. J. Park and S. Kim, J. Nanosci. Nanotechnol., 2012, 12, 685–689 CrossRef CAS PubMed.
- P. Gupta, M. Kour, S. Paul and J. H. Clark, RSC Adv., 2014, 4, 7461 RSC.
- H. Basri, A. F. Ismail and M. Aziz, Desalination, 2012, 287, 71–77 CrossRef CAS PubMed.
- R. Nielsen, P. Kingshott, T. Uyar, J. Hacaloglu and K. L. Larsen, Surf. Interface Anal., 2011, 43, 884–892 CrossRef CAS.
- S. A. El-Safty, Y. Kiyozumi, T. Hanaoka and F. Mizukami, Appl. Catal., A, 2008, 337, 121–129 CrossRef CAS PubMed.
- L. T. Zhuravlev, Colloids Surf., A, 2000, 173, 1–38 CrossRef CAS.
- Y. K. Buchman, E. Lellouche, S. Zigdon, M. Bechor, S. Michaeli and J.-P. Lellouche, Bioconjugate Chem., 2013, 24, 2076–2087 CrossRef CAS PubMed.
- Y. Le, D. Guo, B. Cheng and J. Yu, J. Colloid Interface Sci., 2013, 408, 173–180 CrossRef CAS PubMed.
- S. Hammache, J. S. Hoffman, M. L. Gray, D. J. Fauth, B. H. Howard and H. W. Pennline, Energy Fuels, 2013, 27, 6899–6905 CrossRef CAS.
- N. P. Wickramaratne and M. Jaroniec, J. Mater. Chem. A, 2013, 1, 112 CAS.
- G. Quercia, A. Lazaro, J. W. Geus and H. J. H. Brouwers, Cem. Concr. Compos., 2013, 44, 77–92 CrossRef CAS PubMed.
- Y. P. Wei and H. W. Gao, J. Mater. Chem., 2012, 22, 5715–5722 RSC.
- L. Sun, C. G. Tian, L. Wang, J. L. Zou, G. Mu and H. G. Fu, J. Mater. Chem., 2011, 21, 7232–7239 RSC.
- I. Y. Ipek, N. Kabay, M. Yuksel, D. Yapici and U. Yuksel, Desalination, 2012, 306, 24–28 CrossRef CAS PubMed.
- C. Pacurariu, G. Mihoc, A. Popa, S. G. Muntean and R. Ianos, Chem. Eng. J., 2013, 222, 218–227 CrossRef CAS PubMed.
- G. Xu and H. Gao, Acta Chim. Sin., 2012, 70, 2496–2500 CrossRef CAS.
- M. Khalid, G. Joly, A. Renaud and P. Magnoux, Ind. Eng. Chem. Res., 2004, 43, 5275–5280 CrossRef CAS.
- M. Aivalioti, I. Vamvasakis and E. Gidarakos, J. Hazard. Mater., 2010, 178, 136–143 CrossRef CAS PubMed.
- P. Huttenloch, K. E. Roehl and K. Czurda, Environ. Sci. Technol., 2001, 35, 4260–4264 CrossRef CAS.
- D. M. Zhang, Z. L. Chen, J. M. Shen and L. Yang, Water Sci. Technol.: Water Supply, 2012, 12, 259–269 CrossRef CAS.
- W. Wei, R. Sun, Z. Jin, J. Cui and Z. G. Wei, Appl. Surf. Sci., 2014, 292, 1020–1029 CrossRef CAS PubMed.
- L. Zhang, P. Fang, L. J. Yang, J. Zhang and X. Wang, Langmuir, 2013, 29, 3968–3975 CrossRef CAS PubMed.
- M. N. Amin, A. I. Mustafa, M. I. Khalil, M. Rahman and I. Nahid, Clean Technol. Environ., 2012, 14, 837–844 CrossRef CAS.
- C. Y. Li, M. W. Xu, X. C. Sun, S. Han, X. F. Wu, Y. N. Liu, J. H. Huang and S. G. Deng, Chem. Eng. J., 2013, 229, 20–26 CrossRef CAS PubMed.
- E. Bayram, N. Hoda and E. Ayranci, J. Hazard. Mater., 2009, 168, 1459–1466 CrossRef CAS PubMed.
- P. Wang, Q. H. Shi, Y. F. Shi, K. K. Clark, G. D. Stucky and A. A. Keller, J. Am. Chem. Soc., 2009, 131, 182–188 CrossRef CAS PubMed.
- L. Charerntanyarak, Water Sci. Technol., 1999, 39, 135–138 CrossRef CAS.
Footnote |
† Electronic supplementary information (ESI) available. See DOI: 10.1039/c4ra03190c |
|
This journal is © The Royal Society of Chemistry 2014 |
Click here to see how this site uses Cookies. View our privacy policy here.