DOI:
10.1039/C4RA00904E
(Paper)
RSC Adv., 2014,
4, 26193-26200
A novel fuel cell membrane with high efficiency†
Received
31st January 2014
, Accepted 24th April 2014
First published on 30th April 2014
Abstract
A new class of polymer electrolyte membranes containing an azo based ionic diol (30, 40 and 50 mol%) was prepared for use in a fuel cell. Its proton conductivity, hydrolytic stability, water uptake capacity, swelling behaviour and ion-exchange capacity measurement data indicated its suitability for use as a proton exchange electrolyte membrane in fuel cells. For example, the membranes containing 30, 40 and 50 mol% of azo based ionic monomers exhibit fairly good proton conductivities of 0.073 S cm−1, 0.075 S cm−1 and 0.079 S cm−1, respectively at 30 °C. Moreover, the prepared membranes show a phase separated morphology and exhibit a high thermal stability up to 460 °C which are important parameters for successful fuel cell design. Two types of azo based sulfonated poly(arylene ether sulfone) (SPAES) such as the SPAES-30 and SPAES-50 membrane electrode assembly have been successfully fabricated and yielded a good fuel cell performance in the whole range of current density.
Introduction
The majority of energy needs have been provided by the combustion of fossil fuels. Due to depleting natural resources and increasing petroleum prices, the search for alternative fuels has become intensified. Fuel cells are reliable power generation devices for vehicles, transportation and portable devices to save a significant amount of energy and reduce the emission of non-greenhouse gases.1,2 Fuel cell systems have the ability to solve the most challenging problems associated with current battery systems.3 Unlike the conventional power generation technique, fuel cells work without combustion and environmental side effects. They produce direct current and act like continuously fuelled batteries. Recent studies have been focused on non-fluorinated hydrocarbon-based polymer electrolyte membranes and composite4,5 membranes due to the loss of stability and conductivity at high temperatures in perfluorosulfonic acid membranes. The high temperature operation provides the following advantages in fuel cells.
(i) Simplification of the cooling system.
(ii) Enhanced proton conductivity.
(iii) Improved tolerance of the electrodes to carbon monoxide.
(iv) Better kinetics of methanol oxidation.
(v) Potential use of cogeneration heat.
Proton Exchange Membrane Fuel Cells (PEMFCs) are one of the best types of fuel cells for a vehicular power source to ultimately replace fuel and diesel internal combustion engines. The interest in fuel cells is basically due to their ability to continuously convert chemical energy into electrical energy with a high efficiency and low emission of pollutants.6–9 The proton exchange membrane is a key component of the PEMFC that usually acts as an electrolyte to form ionic pathways for the protons to pass from the anode to the cathode. A fuel cell membrane must have thermal, chemical and mechanical stability along with a good proton conductivity. The performance of an electrolyte membrane is controlled by various physical parameters like the ion-exchange capacity, water uptake, swelling behaviour and proton conductivity. The stability and proton conductivity of the electrolyte membranes are related to the polymer backbone and its acid moiety, respectively.
Perfluorinated ionomers have an outstanding physical and chemical stability and show an excellent performance when applied in fuel cells, especially in H2 fuel cells. Nafion® is the commercially available standard polymer electrolyte membrane used in PEMFCs due to its excellent mechanical and chemical stabilities.10,11 It is quite resistant to chemical attack and has a highly phase separated morphology that imparts excellent proton conductivity with moderate water uptakes.12–14 However, the limitations of these membranes are their high cost and production process, which may include highly toxic and environmentally-unfriendly intermediates.15 Nafion® exhibits a high methanol permeability and a low conductivity at low humidity or high operating temperatures, which restrict its commercialization.16,17 These drawbacks are the main reasons for the extensive research to develop alternative proton exchange membranes for fuel cells.18–21
Sulfonated polyimides,22–24 sulfonated polysulfones,25,26 sulfonated poly(ether ether ketone)s,27–29 sulfonated poly(arylene ether sulfone)s,30–32 sulfonated polystyrenes,33,34 and polybenzimidazoles35,36 have been studied for fuel cell membranes because of their good stability, conductivity and processability. Among these polymers, sulfonated poly(arylene ether sulfone)s have been the centre of attention of recent studies in search of a replacement for Nafion®. Although improvements have been achieved with these types of polymers, the proton conductivity at elevated temperatures is still un-satisfactory because of the lack of water retention at temperatures much above 100 °C.32
The post sulfonation process of the high performance materials such as polysulfones, poly ether ether ketones etc., has suggested that these materials are unable to form defined hydrophilic domains. The rigid polymeric backbones prevent the formation of ionic clusters. So the introduction of ionic groups in the side chain polymer via a direct copolymerization method improves the formation of the ionic cluster, the ion-exchange capacity and the proton conductivity. Another advantage of this method is that it allows for the close control of sulfonation and the polymer structure.
Several types of poly(arylene ether sulfone)s (PAES) are reported in the literature, where the anionomers are located in the main chain37–39 and the side chain40–42 of the aromatic ring. Most of the arylene polymers are functionalized by sulfonating the base polymer with sulfonating agents like conc. sulfuric acid, oleum, chlorosulfonic acid etc. The process of post sulfonation suffers some disadvantages, which may be due to its high degree of sulfonation, degradation and cross-linking by reaction sensitivity.43 If the post sulfonation takes place at the active sites of the benzene ring, it may lead to the risk of desulfonation under fuel cell conditions. Based on the above drawbacks, new monomers of novel architecture are synthesized. In this work, for the first time we report the syntheses of azo based SPAES membranes for fuel cell applications. The physical and chemical properties of these membranes are characterized using various instrumentation techniques in order to evaluate the suitability of these membranes for fuel cells.
Experimental
Materials
4,4′-Dichlorodiphenylsulfone (DCDPS), resorcinol and N,N′-dimethylacetamide (DMAc, 99.8%) were purchased from Aldrich Co., USA. Sulfanilic acid, sodium nitrite, sodium carbonate, 4,4′-bisphenol-A (BP-A), potassium carbonate, N,N-dimethylformamide, methanol and toluene were purchased from Sisco Research Laboratory Private Ltd., Mumbai, India. N-methyl-2-pyrrolidone was purchased from S. D. Fine Chem. Ltd., Mumbai, India. DCDPS and BP-A were dried at 80 °C under vacuum for 16 h before the usage. All other chemicals were used as received.
Monomer synthesis
The azo based ionic diol with a sulfonic acid group, (E)-4-((2,4-dihydroxyphenyl)diazenyl)benzene sulfonic acid, was synthesized by a diazotization reaction followed by a coupling reaction. The reaction scheme for the synthesis of the azo based diol is shown in the ESI Scheme S1.† In a 250 mL beaker, 75 g of an ice–water mixture and 10 mL of conc. HCl were added and stirred at 0–5 °C. An amount of 8.65 g of sulfanilic acid (50 mmol) in 90 mL of a 2.5% sodium carbonate solution was added to the beaker followed by the addition of 3.45 g of a saturated solution of sodium nitrite (50 mmol). A powdery white precipitate of diazonium salt was obtained within a few minutes. An amount of 4.40 g of resorcinol (40 mmol) in 60 mL of water was slowly added to the beaker through an addition funnel and stirred well for 30 min at 0–5 °C. The orange coloured precipitate was collected by filtration, washed thoroughly with ice-cold water and recrystallized from deionized water. The product was dried at 60 °C under vacuum for 12 h.
Polymerization
A typical polymerization procedure for the synthesis of SPAES-50 is as follows; 4,4′-dichlorodiphenylsulfone (14.35 g, 50 mmol), bisphenol-A (5.70 g, 25 mmol) and an azo based monomer (7.38 g, 25 mmol) were placed in a 250 mL three-necked RB flask equipped with a magnetic stirrer, a Dean–Stark trap and a nitrogen inlet. A volume of 60 mL of DMAc was added and stirred well until all the monomers were dissolved. An amount of 13.8 g of anhydrous potassium carbonate (100 mmol) and 30 mL of toluene were added and refluxed at 150 °C for 5 h. Following this step, the temperature was slowly raised to 180 °C after controlled the removal of toluene from the reaction mixture. The polymerization reaction was continued at 180 °C for 18 h. The viscous solution was cooled to 25 °C and diluted with DMF to allow easier filtering. Then, the solution was filtered using 100 μm pore size filter paper to remove most of the potassium salts. The polymer solution was slowly added to a beaker containing an excess of methanol. The precipitated azo polymer was washed several times with ethanol and then dried at 80 °C under vacuum for 24 h.
Membrane preparation
The SPAES copolymer of 10 wt% was dissolved in DMAc at 25 °C under constant stirring. After the complete dissolution of SPAES, the viscous solution was cast onto a flat glass plate. The cast membranes were dried at 60 °C for 12 h, 90 °C for 10 h and 140 °C for 6 h. Following this step, the resulting membranes were soaked in deionized water for 24 h to release the membranes from the glass plates. The obtained membranes were thoroughly washed with deionized water and finally dried at 80 °C under vacuum for 24 h.
Measurements
For the Fourier Transform Infrared Spectra (FT-IR) analysis, the samples were first dried at 100 °C under vacuum for 6 h. The spectrum was collected using an ABB MB3000 FT-IR spectrophotometer. High Performance Liquid Chromatography (HPLC) analysis was performed using a LC-10AT-VP, Shimadzu, Japan. The surface morphology was analyzed using a scanning electron microscope (SEM, Hitachi-S3400N). For the SEM analysis, the samples were cut into sufficient sizes and sputter coated with gold to make them electro conductive. Then the sample was analyzed under vacuum at an accelerating voltage of 10.0 kV. Thermogravimetric analyses of the membranes were carried out using a Thermogravimetric Analyzer (Q 50, TA Instruments, USA) at a heating rate of 20 °C min−1 in a nitrogen atmosphere. Intrinsic viscosity measurements were obtained in N-methyl-2-pyrrolidone at 25 °C using a capillary viscometer, Schott Gerate, West Germany. GPC analysis was done in DMF solvent. HR-TEM images were obtained using a FET TECHNO G2 30 (300 kV) instrument.
The concentration of the ion conducting units is generally denoted as the molar equivalents of the ion conductor per mass of dry sample and is expressed as the ion exchange capacity (IEC). The IEC of the membranes was measured using the titration method. The polymer membranes were soaked in 1.0 M HCl for 10 h to regenerate the protons from the salt form. All the membranes were thoroughly washed with deionized water several times and then soaked in a 0.1 M NaCl solution for 16 h. The protons released due to the exchange reaction with Na+ ions were titrated against a 0.01 M NaOH solution using phenolphthalein as an indicator. The IEC was determined from eqn (1).
|
IEC (meq. g−1) = (V × NNaOH)/weight of the polymer
| (1) |
where
V is the volume of NaOH consumed,
NNaOH is the normality of NaOH and meq. is milliequivalent.
For the water uptake and swelling ratio studies, the acidified membranes were dried at 120 °C until constant weights and lengths were achieved, which are recorded as Wdry and Ldry, respectively. Then, the dried membranes were immersed into deionized water. The water attached to the surface was quickly swabbed with tissue paper before measurement. The weight and length were measured several times until constant measurements were achieved, which are denoted as Wwet and Lwet, respectively. The percentage water uptake of the membrane was calculated using eqn (2).
|
% Water uptake = (Wwet − Wdry)/Wdry × 100
| (2) |
The swelling ratio was defined as eqn (3).
|
% Swelling ratio = (Lwet − Ldry)/Ldry × 100
| (3) |
The proton conductivity measurements were performed in a two-probe cell using an AC impedance spectroscopic technique. The AC impedance spectra of the membranes were recorded in the frequency range of 1.0 MHz to 10.0 Hz using an Autolab PGSTAT 30. The detailed procedure for the conductivity measurements was reported in our paper.32 The measurements were taken in the temperature range of 30–130 °C. The tensile strength and Young's modulus of the completely hydrated SPAES membranes were measured using a Universal Testing Machine (UTM), Instron, USA. Samples with a length of 50 mm and a width of 20 mm were tested using a 250 N load cell that was pulled at 50 mm min−1 within a 21 cm gauge length. Triplicate analyses were carried out and the average values for the determination of the tensile strength and Young's modulus were taken.
15 weight% of teflonized Toray-TGP-H-120 carbon paper of 0.37 mm thickness was used as the backing layer. To prepare the gas-diffusion layer (GDL), Vulcan XC-72R was suspended in cyclohexane and agitated in an ultrasonic water bath for 30 min. A 15 weight% polytetrafluroethylene (PTFE) suspension in 2 mL ammonia was added to this solution with continuous agitation to form a slurry that was coated onto the backing layer uniformly until the required loading of 1.5 mg cm−2 carbon was obtained. The obtained GDL was sintered in a muffle furnace at 350 °C for 30 min. Carbon supported platinum was used as a catalyst for both the cathode and anode. The loading of the catalyst layer on both the anode and cathode was kept at 0.5 mg cm−2. The active area for the PEMFC was 4.0 cm2. The MEA of the pristine and composite membrane was prepared by sandwiching the membrane between the two electrodes followed by hot-pressing at 130 °C for 3 min at a pressure of 20 kg cm2. The MEA was evaluated using a conventional fuel cell fixture with a parallel serpentine flow-field machined on graphite plates. The cells were tested at 60 °C under 100% humidified conditions with hydrogen at a flow rate of 100 mL min−1 at the anode and oxygen at a flow rate of 150 mL min−1 at the cathode, respectively. Measurements for the cell potentials with varying current densities were conducted galvanostatically using a Fuel Cell Test Station (Model-LCN4-25-24/LCN 50-24) procured from Bitrode Instruments (USA).
Results and discussion
The synthesis of azo based sulfonated poly(arylene ether sulfone)s
A series of SPAES copolymer membranes were synthesised by an aromatic nucleophilic polycondensation reaction. The polymer code, the mole ratio of the monomers such as bisphenol-A and azo based ionic diol used for the synthesis of the SPAES and their physical properties are given in Table 1. The reaction was carried out in the presence of potassium carbonate using N,N-dimethylacetamide (DMAc) as a solvent (Scheme 1). The resulting polymers had intrinsic viscosity in the range between 1.41 and 1.54 dL g−1. The gel permeation chromatography (GPC) experiments (ESI, Fig. S4†) indicated the weight average molecular weight (Mw) and polydispersity index (PDI) of SPAES-30 to be 10
640 Daltons and 1.41, respectively, while the Mw and PDI values for SPAES-40 were 6321 Daltons and 1.31, respectively.
Table 1 The mole ratio and physical properties of the SPAES copolymers
Polymer code |
Mole ratio of BP-A/ionic diolin copolymers |
ηinta(dL g−1) |
Tensile strength (MPa) |
Young's modulus (MPa) |
Activation energy (kJ mol−1) |
The intrinsic viscosity measured at a concentration of 1.0 g dL−1 in NMP at 25 °C. |
SPAES-30 |
1 : 0.6 |
1.41 |
43 |
513 |
7.48 |
SPAES-40 |
1 : 0.8 |
1.46 |
40 |
468 |
7.33 |
SPAES-50 |
1 : 1.0 |
1.54 |
33 |
402 |
7.01 |
 |
| Scheme 1 The synthesis of azo based SPAES. | |
Spectral analyses
The high performance liquid chromatography (HPLC) analysis confirms the absence of the starting material in the azo based ionic diol. The chromatograms of the starting material and azo based ionic diol are given in Fig. 1. The reverse-phase HPLC analysis was performed by using the mobile phase in the proportion of 70
:
30 methanol and water, pH 2.0 adjusted with formic acid. The flow rate was set to 0.75 mL min−1. The HPLC analysis was carried out by LC-10AT-VP, with a photo diode array (PDA) detector, in which we can collect the chromatogram at different wavelengths.
 |
| Fig. 1 The HPLC chromatograms of the starting material (a) and the azo based ionic diol (b). | |
A volume of 20 μL (0.10 mg mL−1 concentration) of both the starting material and the product in methanol medium was injected through a rheodine setup. The λmax of resorcinol was found to be 270 nm, whereas the λmax of product was found to be 350 nm. The chromatograms were collected at a wavelength of 350 nm for the azo compound and 270 nm for resorcinol. The retention time of resorcinol was obtained at 2.91 min and the retention time of the product was obtained at 3.96 min. In ESI Fig. S1,† the expand view of the chromatogram of the azo based ionic diol at a wavelength of 270 nm with the retention time of 2.91 min clearly shows the absence of the starting material.
The FT-IR spectrum of the azo based ionic diol is given in the ESI Fig. S2.† A broad band appeared at 3475 cm−1 which is attributed to the presence of hydroxyl groups. The aromatic C–C band appeared at 1120 cm−1. The peaks at 1166 and 1033 cm−1 are obtained because of the stretching vibration (O
S
O) of the sulfonate salt. The FT-IR spectrum of the azo based SPAES-50 copolymers is shown in Fig. 2. The peaks at 1585 cm−1 and 1488 cm−1 are attributed to the vibrations of the aromatic ring skeleton. The symmetric stretching band of the sulfone group appeared at 1153 cm−1 and 1012 cm−1. The peak at 1242 cm−1 proves the aromatic ether linkage of the SPAES. The aromatic C–N stretching vibration is observed at around 1325 cm−1.
 |
| Fig. 2 The FT-IR spectrum of the azo based SPAES-50 copolymer. | |
Proton NMR analysis was performed for the azo based ionic diol and the polymer (SPAES-50) using DMSO-d6 as the solvent. The proton NMR spectra of the azo based ionic monomer and the SPAES polymer are shown in Fig. 3. In the azo based monomer, the resonance signals that appear at 8.06 to 6.90 ppm are due to the aromatic protons and the sulfonic acid proton appears at 2.00 ppm (see Fig. 3a). The polymer (SPAES-50) shows resonance signals appearing at 8.10 to 7.00 ppm for the aromatic protons. The methyl protons in SPAES-50 appear at 1.65 ppm confirming the formation of the polymer.18,44
 |
| Fig. 3 The 1H NMR spectra of the azo monomer (a) and the SPAES-50 copolymers (b). | |
Ion exchange capacity
The ion exchange capacity (IEC) is an essential parameter for the evaluation of a polymer electrolyte membrane as it influences the water uptake and proton conductivity. The IEC of the polymer is directly dependent on the amount of sulfonic acid substituted in the polymer. Generally the proton conductivity and the water uptake of the final membrane directly depend on the amount of sulfonic acid groups and the IEC of the polymer. The sulfonic acid groups not only make the polymer proton conducting but also make it hydrophilic. The IEC values of the SPAES copolymers are given in Table 2.
Table 2 The IEC values, water uptake and swelling ratio of the SPAES copolymers
Polymer code |
IEC (meq. g−1) |
Water uptake (%) |
Swelling ratio (%) |
30 °C |
90 °C |
30 °C |
90 °C |
SPAES-30 |
1.63 |
26.2 |
33.6 |
4.75 |
6.06 |
SPAES-40 |
1.69 |
28.0 |
38.4 |
5.52 |
6.63 |
SPAES-50 |
1.86 |
35.1 |
45.6 |
6.69 |
8.07 |
As the proportion of azo monomer with an ionic group in the SPAES membrane is increased, the IEC value also increases. It can be seen that the order increased in the following manner: SPAES-30 < SPAES-40 < SPAES-50. The IEC value of the membranes clearly shows that the sulfonated monomers were well incorporated into the copolymers.
Water uptake and swelling ratio
The water uptake capacity and swelling behaviour are very important parameters in PEMFC applications because the proton conductivity and hydrolytic stability of polymer electrolyte membranes are strongly related to the presence of water. A polymer electrolyte membrane with a good water management ability would be anticipated for fuel cell applications. In this work, the water uptake capacity and swelling ratio of the membranes were analyzed at temperatures between 30 °C and 90 °C. The influence of the IEC on the water uptake of the SPAES membranes is depicted in the ESI Fig. S3.† Here, the water uptake follows the same trend as the IEC and the values are given in Table 2. At 90 °C, the SPAES copolymers showed a moderate water uptake and swelling. This may be attributed to the construction of a large and continuous ion linkage in the sulfonated polymers. The water uptake increased with the sulfonate content due to the strong hydrophilicity of the sulfonic acid group. Also the bisphenol structure had a remarkable influence on the water uptake and swelling ratio of the membranes.
Thermal and hydrolytic stability
The thermal stability of the SPAES membranes was determined using TGA measurements and the thermograms are shown in Fig. 4. All of the membranes showed a three step degradation pattern. The first step of mass loss (5%) up to 200 °C in the SPAES copolymers is due to the loss of physically and chemically bound water. The second step of degradation was found in the range of 200–460 °C which corresponds to the splitting of the aromatic sulfonyl groups as well as the degradation of the azo groups. The third weight loss which occurred at about 460 °C was due to the decomposition of the polymer backbone.45,46 SPAES-50 shows a higher stability than SPAES-30 and SPAES-40. In general the azo polymers are found to exhibit a better thermal stability, the rigidity being enhanced by the presence of azo groups. These membranes showed slight differences in the thermal stability according to their mole ratio.
 |
| Fig. 4 The TGA thermograms of the SPAES copolymers. | |
The azo based SPAES membranes had reasonably good physical properties. It is very important for a polymer electrolyte membrane to have good mechanical properties to withstand high temperatures, the high pressure fabrication process for the membrane electrode assembly and the extreme conditions of a fuel cell. The mechanical properties of the dry SPAES membranes are summarised in Table 1. All membranes exhibit tensile strength in the range from 33.6 to 43.3 MPa and modulus from 402 to 513 MPa which are flexible for the usage of polymer electrolyte membranes. An increase in the sulfonic acid content in the polymer matrix resulted in the reduction of the tensile strength. From the mechanical testing, it can be concluded that the side chain substituted SPAES membranes are flexible for fuel cell applications.
Proton conductivity
For a good proton conductivity solid electrolyte membranes should have fixed charged sites surrounded by water molecules which facilitate the transport of protons.47 The SPAES membrane has a high proton conductivity because the sulfonic acid groups have covalent bonding (S–O) and intermolecular hydrogen bonding. The principle of proton conduction is demonstrated by the Grotthuss mechanism, when the protons are transferred by forming and breaking hydrogen bonds with proton accepting media such as water or sulphonic acid.48 Several researchers have reported on different kinds of proton conducting materials as an alternative to the Nafion® membranes.49 The water uptake capacity of the sulfonated polymers have a profound effect on the proton conductivity and mechanical properties.50 For the conductivity experiments, all of the membranes were initially immersed in deionized water for 24 h at 25 °C to hydrate. The proton conductivity of the membranes based on the monomer which have more sulfonic acid content possess a higher conductivity. The conductivities of the SPAES membranes with increasing temperature from 30 °C to 130 °C were determined and the values were found to markedly increased in the order of SPAES-30 < SPAES-40 < SPAES-50. The increase in the proton conductivity of the membranes is due to more water retention and the increase in the formation of the ionic clusters.
Fig. 5 shows an Arrhenius plots of the proton conductivity as a function of temperature for the SPAES membranes and the Ea values are reported in Table 1. The activation energies of the membranes decreased in the order of SPAES-30 > SPAES-40 > SPAES-50. The increase in the percentage water uptake of the SPAES membranes lead to the lowering of their activation energy as consequence of the increase in proton conductivity. A similar trend of the increasing proton conductivity with the increase in ionic content was reported by Pei et al.51 Membranes with ionic groups in their side chain exhibit an excellent proton conductivity. Table 3 describes the compilation of some of the reported values of sulfonated polymers with side chain ionic groups.
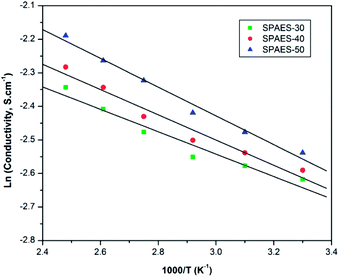 |
| Fig. 5 The Arrhenius plots of proton conductivity for the SPAES membranes. | |
Table 3 The IEC and proton conductivity values of sulfonated polymers which have ionic groups as side chains
Membrane type |
IEC (meq. g−1) |
Proton conductivity (S cm−1) |
Reference |
DHTPE – (4,4-(2,2-diphenylethenylidene)bisphenol). |
Cardo poly(aryl ether sulfone)s with pendant –OH groups |
1.41 |
0.06 (20 °C) |
52 |
SPES containing hexabenzocoronene |
1.61 |
0.11 (80 °C) |
53 |
SPES containing DHTPEa |
1.68 |
0.10 (80 °C) |
54 |
Sulfonated poly(phenylene oxide) |
1.62 |
0.07 (25 °C) |
55 |
Concentrated SPES |
1.51 |
0.06 (20 °C) |
56 |
SPAES having azo based ionic diols |
1.86 |
0.08 (30 °C) |
This work |
It can be seen from the above compilation that the IEC and proton conductivity of the azo based SPAES membranes are good and can be considered for PEMFC applications.
Electrochemical study
The SPAES-30 and SPAES-50 membranes were taken for MEA studies. Fig. 6 shows the cell polarization of MEA assembled with the synthesised SPAES membranes as the electrolyte at 60 °C and 100% RH. The best performance under these conditions was obtained for the SPAES-50 membrane, which produced a peak power density of 496 mW cm−2 at a load current density of 1500 mA cm−2 as compared to the SPAES-30 membrane with 465 mW cm−2 at 1500 mA cm−2. Recently, Lim et al. synthesized SPES containing DHTPE and achieved a maximum power density of 420 mW cm−2.57 They also compared their values with Nafion® 211, which exhibits 450 mW cm−2. Sahu et al. reported that PEMFCs with a Nafion® 1135 membrane produced a peak power density of 550 mW cm−2 at 60 °C and 100% RH.58 The cell polarization curve of the azo based SPAES membrane exhibits a good performance in PEMFC applications.
 |
| Fig. 6 The electrochemical single cell performance of the SPAES-50 membrane at 60 °C and 100% RH. | |
Conclusions
A novel azo based diol, (E)-4-((2,4-dihydroxyphenyl) diazenyl) benzene sulfonic acid, was successfully synthesised by a diazotisation reaction followed by a coupling reaction. Sulfonated poly(arylene ether sulfone)s with different mole ratios of hydrophilic groups were prepared by changing the mole ratio of the azo based ionic diol and bisphenol-A. These are the new type of proton exchange membranes having azo and sulfonic acid groups as side chains in SPAES. The obtained polymers had an intrinsic viscosity of 1.41–1.54 dL g−1. With the increase in the sulfonic acid content in the polymer matrix, the water uptake increased from 26.2 to 35.1% at 30 °C and 33.6 to 45.6% at 90 °C. All of the membranes exhibit an excellent thermal stability with a 10% weight loss observed up to 460 °C. A single cell using the SPAES-50 membrane as an electrolyte produced a maximum power density of 496 mW cm−2 in H2/O2 at 60 °C under 100% RH. The high proton conductivity and thermal stability of the azo based SPAES membranes meet the requirements of good proton exchange membranes for PEMFC applications.
Acknowledgements
The authors are thankful to Dr S. Pitchumani, CSIR-CECRI for the proton conductivity experiments and Dr Sengupta, CSIR-NCL for the GPC experiments. The authors acknowledge the funding from CSIR cross cluster project ZERIS (WP-13 and WP-21 CSC 0103).
Notes and references
- F. de Bruijn, Green Chem., 2005, 7, 132 RSC.
- Z. Song and H. Zhou, Energy Environ. Sci., 2013, 6, 2280 CAS.
- A. K. Shukla, R. K. Raman and K. Scott, Fuel Cells, 2005, 5, 436 CrossRef CAS.
- S. N. Jaisankar, S. Ramalingam, H. Subramani, R. Mohan, P. Saravanan, D. Samanta and A. B. Mandal, Ind. Eng. Chem. Res., 2012, 52, 1379 CrossRef.
- R. M. Sankar, K. M. S. Meera, D. Samanta, A. Murali, P. Jithendra, A. B. Mandal and S. N. Jaisankar, RSC Adv., 2012, 2, 12424 RSC.
- C. D. Varnado, X. Zhao, M. Ortiz, Z. Zuo, Z. Jiang, A. Manthiram and C. W. Bielawski, RSC Adv., 2014, 4, 2167 RSC.
- Y. Zhu, H. Li, J. Tang, L. Wang, L. Yang, F. Ai, C. Wang, W. Z. Yuan and Y. Zhang, RSC Adv., 2014, 4, 6369 RSC.
- R. Devanathan, Energy Environ. Sci., 2008, 1, 101 CAS.
- C. Zhang, S. Kang, X. Ma, G. Xiao and D. Yan, J. Membr. Sci., 2009, 329, 99 CrossRef CAS PubMed.
- M. A. Hickner, H. Ghassemi, Y. S. Kim, B. R. Einsla and J. E. McGrath, Chem. Rev., 2004, 104, 4587 CrossRef CAS.
- V. Neburchilov, J. Martin, H. Wang and J. Zhang, J. Power Sources, 2007, 169, 221 CrossRef CAS PubMed.
- J. J. Sumner, S. E. Creager, J. J. Ma and D. D. DesMartear, J. Electrochem. Soc., 1998, 145, 107 CrossRef CAS PubMed.
- K. A. Mauritz and R. B. Moore, Chem. Rev., 2004, 104, 4535 CrossRef CAS.
- Q. Li, R. He, J. O. Jensen and N. J. Bjerrum, Chem. Mater., 2003, 15, 4896 CrossRef CAS.
- J. Peron, Z. Shi and S. Holdcroft, Energy Environ. Sci., 2011, 4, 1575 CAS.
- M. Tanaka, M. Koike, K. Miyatake and M. Watanabe, Polym. Chem., 2011, 2, 99 RSC.
- S. H. Kim and K. Song, J. Ind. Eng. Chem., 2011, 17, 170 CrossRef CAS PubMed.
- H. K. Kim, M. Zhang, X. Yuan, S. N. Lvov and T. C. M. Chung, Macromolecules, 2012, 45, 2460 CrossRef CAS.
- L. Li and Y. Wang, J. Power Sources, 2006, 162, 541 CrossRef CAS PubMed.
- H. Zhang and P. K. Shen, Chem. Soc. Rev., 2012, 41, 2382 RSC.
- A. K. Sahu, S. D. Bhat, S. Pitchumani, P. Sridhar, V. Vimalan, C. George, N. Chandrakumar and A. K. Shukla, J. Membr. Sci., 2009, 345, 305 CrossRef CAS PubMed.
- S. Lee, W. Jang, S. Choi, K. Tharanikkarasu, Y. Shul and H. Han, J. Appl. Polym. Sci., 2007, 104, 2965 CrossRef CAS.
- N. Endo, K. Matsuda, K. Yaguchi, Z. Hu, K. Chen, M. Higa and K. Okamoto, J. Electrochem. Soc., 2009, 156, B628 CrossRef CAS PubMed.
- Z. Hu, Y. Yin, H. Kita, K. Okamoto, Y. Suto, H. Wang and H. Kawasato, Polymer, 2007, 48, 1962 CrossRef CAS PubMed.
- Y. Z. Fu and A. Manthiram, J. Power Sources, 2006, 157, 222 CrossRef CAS PubMed.
- F. Lufrano, G. Squardrito, A. Patti and E. Passalacqua, J. Appl. Polym. Sci., 2000, 77, 1250 CrossRef CAS.
- P. Deivanayagam and A. R. Ramamoorthy, J. Macromol. Sci., Part A: Pure Appl. Chem., 2012, 49, 191 CrossRef CAS.
- R. Kumar, M. Mamlouk and K. Scott, RSC Adv., 2014, 4, 617 RSC.
- V. S. Rangasamy, S. Thayumanasundaram, N. D. Greef, J. W. Seo and J. P. Locquet, Solid State Ionics, 2012, 216, 83 CrossRef CAS PubMed.
- E. P. Jutemar, S. Takamuku and P. Jannasch, Polym. Chem., 2011, 2, 181 RSC.
- H. Bi, J. Wang, S. Chen, Z. Hu, Z. Gao, L. Wang and K. Okamoto, J. Membr. Sci., 2010, 350, 109 CrossRef CAS PubMed.
- P. Deivanayagam, A. R. Ramamoorthy and S. N. Jaisankar, Polym. J., 2013, 45, 166 CrossRef CAS.
- S. Elamathi, G. Nithyakalyani, D. Sangeetha and S. Ravichandran, Ionics, 2008, 14, 377 CrossRef CAS PubMed.
- P. P. Kundu, B. T. Kim, J. E. Ahn, H. S. Han and Y. G. Shul, J. Power Sources, 2007, 171, 86 CrossRef CAS PubMed.
- A. Sannigrahi, S. Ghosh, S. Maity and T. Jana, Polymer, 2011, 52, 4319 CrossRef CAS PubMed.
- S. Yu and B. C. Benicewicz, Macromolecules, 2009, 42, 8640 CrossRef CAS.
- S. Takamuku and P. Jannasch, Polym. Chem., 2012, 3, 1202 RSC.
- H. Bi, J. Wang, S. Chen, Z. Hu, Z. Gao, L. Wang and K. Okamoto, J. Membr. Sci., 2010, 350, 109 CrossRef CAS PubMed.
- W. L. Harrison, M. A. Hickner, Y. S. Kim and J. E. McGrath, Fuel Cells, 2005, 5, 201 CrossRef CAS.
- B. Liu, G. P. Robertson, D. S. Kim, X. Sun, Z. Jiang and M. D. Guiver, Polymer, 2010, 51, 403 CrossRef CAS PubMed.
- Y. L. Liu, Polym. Chem., 2012, 3, 1373 RSC.
- S. Seesukphronrarak and A. Ohira, Chem. Commun., 2009, 4744 RSC.
- M. Gil, X. Ji, X. Li, H. Na, J. E. Hampsey and Y. Lu, J. Membr. Sci., 2004, 234, 75 CrossRef CAS PubMed.
- J. Parvole and P. Jannasch, J. Mater. Chem., 2008, 18, 5547 RSC.
- B. P. Tripathi, T. Chakrabarti and V. K. Shahi, J. Mater. Chem., 2010, 20, 8036 RSC.
- Y. L. Liu, Y. H. Su, C. M. Chang, Suryani, D. M. Wang and J. Y. Lai, J. Mater. Chem., 2010, 20, 4409 RSC.
- L. Barbora, S. Acharya, R. Singh, K. Scott and A. Verma, J. Membr. Sci., 2009, 326, 721 CrossRef CAS PubMed.
- S. Oleksandrov, J. W. Lee, J. H. Jang, S. Haam and C. H. Chung, J. Nanosci. Nanotechnol., 2009, 9, 1551 CrossRef CAS PubMed.
- T. Uma, RSC Adv., 2012, 2, 6752 RSC.
- T. A. Zawodzinski, T. E. Springer, J. Davey, R. Jestel, C. Lopez, J. Valerio and S. Gottesfeld, J. Electrochem. Soc., 1993, 140, 1981 CrossRef CAS PubMed.
- H. Pei, L. Hong and J. Y. Lee, J. Power Sources, 2006, 160, 949 CrossRef CAS PubMed.
- Q. Zhang, F. Gong, S. Zhang and S. Li, J. Membr. Sci., 2011, 367, 166 CrossRef CAS PubMed.
- Y. D. Lim, D. W. Seo, S. H. Lee, K. S. Lee, K. M. Kang and W. G. Kim, 12th IEEE International Conference on Nanotechnology (IEEE-NANO), Birmingham, United Kingdom, 2012 Search PubMed.
- Y. Lim, D. Seo, S. Lee, H. Jang, H. Lee, T. Hong, D. Kim, H. Ju and W. Kim, Solid State Ionics, 2012, 225, 277 CrossRef CAS PubMed.
- Z. Zhang, L. Wu and T. Xu, J. Membr. Sci., 2011, 373, 160 CrossRef CAS PubMed.
- S. Feng, K. Shen, Y. Wang, J. Pang and Z. Jiang, J. Power Sources, 2013, 224, 42 CrossRef CAS PubMed.
- Y. Lim, D. Seo, S. Lee, H. Jang, H. Lee, T. Hong, D. Kim, H. Ju and W. Kim, Solid State Ionics, 2012, 225, 277 CrossRef CAS PubMed.
- A. K. Sahu, G. Selvarani, S. Pitchumani, P. Sridhar and A. K. Shukla, J. Electrochem. Soc., 2007, 154(2), B123 CrossRef CAS PubMed.
Footnote |
† Electronic supplementary information (ESI) available: the synthetic scheme for azo based diol, the HPLC chromatogram of the expand region of azo based ionic diol, the FT-IR spectrum of the azo based monomer and the influence of IEC on the water uptake of the SPAES membranes. See DOI: 10.1039/c4ra00904e |
|
This journal is © The Royal Society of Chemistry 2014 |
Click here to see how this site uses Cookies. View our privacy policy here.