Synthesis of L10 ferromagnetic CoPt nanopowders using a single-source molecular precursor and water-soluble support†
Received
26th June 2013
, Accepted 5th August 2013
First published on 7th August 2013
Introduction
Nanoscale magnetic materials are being explored for high-density data storage applications and for achieving a better fundamental understanding of ferromagnetism on the nanoscale.1 Binary metal alloys, such as FePt, CoPt, and FePd, exhibit very large uniaxial magnetocrystalline anisotropy constants (6.6–10 × 10−7 erg cm−3 for FePt, 4.9 × 10−7 erg cm−3 for CoPt, 1.8 × 10−7 erg cm−3 for FePd) and high limiting coercivities (116 kOe for FePt, 123 kOe for CoPt, and 33 kOe for FePd) at the nanoscale, and are of particular interest for ultra-high-density data storage applications.2 Nanoparticles of these compositions are usually described as having either atomically disordered face-centered cubic (fcc) A1-type lattice structures that exhibit small coercivity and soft, superparamagnetic properties or as atomically ordered L10-type lattice structures exhibiting high coercivity, large magnetic anisotropy, and hard ferromagnetic properties. Nanoparticles formed below ca. 300 °C usually have a disordered fcc atomic structure. Phase transition to an ordered L10 unit cell for CoPt occurs upon thermal treatment between 600 and 850 °C.3 Annealing at higher temperatures leads to a decrease in observed coercivity due to phase separation.3 The search for convenient methods of preparing highly ferromagnetic CoPt nanoparticles is of continued interest, because magnetic properties of as-prepared L10 MPt alloy nanoparticles have yet to approach predicted limiting values.2 CoPt alloy nanoparticles are also known to function as chemical CO oxidation catalysts4 and as electrochemical catalysts for CO or methanol oxidation.5
CoPt nanoparticles of near 1
:
1 alloy stoichiometry have been prepared via hydrogen reduction,6,7 borohydride reduction,8–12 polyol reduction,13–18 sol–gel methods,19,20 reverse micelle methods,21,22 galvanic displacement,23 evaporation methods,24–27 ion-beam depositiom,28–30 pulse-laser-deposition/ablation/sputtering methods,31–35 or by bio-inspired or biomimetic methods.36,37 Common to these methods is use of separate sources of Co and Pt and a two-step process entailing formation of CoPt nanoparticles with subsequent thermal annealing. Ferromagnetic L10 FePt nanoparticles exhibiting high coercivity have been prepared in earlier work using single-source molecular precursors,38,39 and this general synthesis strategy is now extended to CoPt nanoparticle formation.
Ferromagnetic 1
:
1 CoPt nanoparticles are formed in a single-step process by reactive decomposition of a known 1
:
1 CoPt heterodinuclear, cluster complex that serves as a stoichiometric source of both metals. Thermal decomposition of CoPt(CO)4(dppe)Me/NaCl powder composites under a reducing atmosphere (H2/N2) at 650 °C followed by simple aqueous dissolution of the NaCl support gives free-flowing 1
:
1 CoPt nanopowders that exhibit moderate room-temperature ferromagnetism (Hc = 4.0 kOe at 300 K) and high ferromagnetism at low temperature (Hc = 26.0 kOe at 5 K).
Experimental
Reagents and general methods
All manipulations relevant to organometallic precursors were carried out under a nitrogen atmosphere using standard Schlenk techniques. Solvents used in organometallic synthesis were dried over and distilled from appropriate drying agents under N2. Reagent chemicals, dichloro(1,5-cyclooctadiene)platinum(II), dicobalt octacarbonyl, and diphenylphosphinoethane (dppe), were purchased from Strem Chemicals, Inc.; all other reagents were purchase from Aldrich. The complex, CoPt(CO)4(dppe)Me,40 was prepared as described in the literature (see ESI†).
Thermal treatments were conducted inside a quartz tube under continuous gas flow using a one-foot Linberg/Blue tube furnace. Sonication was performed in a glass container immersed in a Bransonic 2510R sonifier. Powder X-ray diffraction (XRD) scans were obtained on a Scintag X1 θ/θ automated powder X-ray diffractometer with a Cu target, a Peltier-cooled solid-state detector, and a zero-background Si(510) sample support. Characterization by TEM was performed at Vanderbilt University with a 200 kV Philips CM20T TEM and at the ORNL SHaRE User Facility with a 200 kV Philips CM200 FEG TEM. Magnetic measurements were performed at Oak Ridge National Laboratory using a SQUID magnetometer. Bulk elemental chemical microanalyses by inductively coupled plasma/optical emission spectrometry (ICP-OES) were performed by Galbraith Laboratories, Knoxville, TN.
Single-step preparation of L10 CoPt nanoparticles
In a typical preparation, 0.050 g (0.064 mmol) CoPt(CO)4(dppe)Me was dissolved in a minimum amount of CH2Cl2 (0.5 mL) under N2. To achieve a final composite of 2 wt% total metal loading, 0.815 g (13.9 mmol) of ball-milled anhydrous NaCl (see ESI†) was added to the above solution and was allowed to stir for 15 min. Solvent was removed under reduced pressure producing a free-flowing orange powder. The sample was placed in a glazed ceramic boat and was inserted in the center of a tube furnace. The tube volume was purged with N2 (20 min) and getter gas (1
:
9 H2
:
N2, 20 min), followed by a reductive decomposition at 650 °C under 1
:
9 H2
:
N2 (4 h). The resulting black powder was allowed to cool to room temperature before removal from the furnace and was very responsive to the applied magnetic field of an external magnet. CoPt nanoparticles were isolated by adding this black powder to 5 mL of water followed by mixing, mild sonication, and centrifugation to give a dark precipitate of metal powder. This procedure was repeated two times to ensure complete dissolution of the NaCl support followed by a final acetone (5 mL) wash. The wet metal powder was dried in air to give as-prepared CoPt nanoparticles as a free-flowing black, ferromagnetic powder. Bulk analysis by ICP-OES [element (wt%)]: Co (19.4); Pt (65.6) or Co1Pt1.02.
Results and discussion
Synthesis and characterization of 1
:
1 L10 CoPt nanopowder
Solvent evaporation from sodium chloride powder wetted by a solution of CoPt(CO)4(dppe)Me gives an orange precursor/NaCl composite powder. Reactive, thermal decomposition of this composite at 650 °C under a flow of getter gas (9
:
1 N2/H2) in a tube furnace forms directly CoPt/NaCl nanocomposite as a black powder. Variation of precursor/water-soluble support mass ratio determines the total metal wt% of the final nanocomposite and provides some control over mean particle size. Precursor loadings of 2 wt% total metal affords CoPt nanoparticles of ca. 11 nm average diameter. Dissolution of the NaCl support powder by aqueous trituration gives as-prepared L10-type CoPt nanoparticles as a free-flowing black powder. Bulk elemental analysis reveals a 1
:
1 Co
:
Pt atomic ratio, consistent with the metal stoichiometry of the precursor.
TEM micrographs of as-prepared CoPt powder at low and high resolution (Fig. 1) reveal single-crystal nanoparticles of irregular shape showing continuous fringe patterns. An interplanar distance of 0.380 nm, measured from a cross-fringe pattern within a single CoPt nanoparticle, corresponds well to the (001) d-spacing (0.370 nm) known for bulk L10 CoPt. A histogram of CoPt nanoparticle sizes (Fig. 1) reveals a log-normal distribution consistent with particle growth via a surface-diffusion process41 having an average CoPt particle diameter of 11 nm (σ = 7 nm).
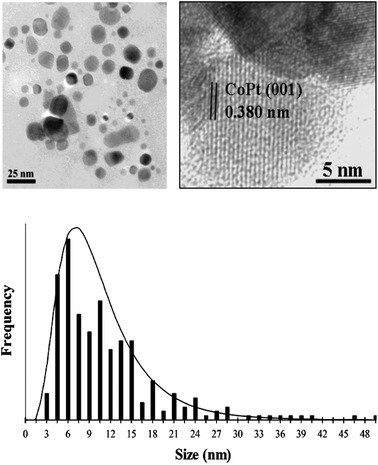 |
| Fig. 1 TEM images of as-prepared L10 CoPt nanopowder at low (left image) and high (right image) magnification showing (001) lattice fringes expected for L10 CoPt along with a corresponding particle-size histogram. | |
Successful formation of a highly ordered L10 lattice for as-prepared CoPt powder is confirmed by powder XRD (Fig. 2). Superlattice peaks expected of a L10 ordered phase are clearly observed, as evidenced by strong relative intensity of the (001) and (110) diffraction peaks and by splitting of the (200)/(002) pair of reflections. For pure, bulk L10 CoPt, unit-cell constants are a = 3.803 Å and c = 3.701 Å giving a c/a ratio of 0.9732.42 Unit-cell parameters calculated from the experimental XRD pattern (Fig. 2) gives a = 3.790 Å and c = 3.696 Å and a c/a ratio of 0.9750 confirming formation of highly pure L10 material. Scherrer's analysis of experimental L10 CoPt XRD peak widths gives a volume-weighted average crystallite size of 14 nm. This value compares well with the number-average particle size of 11 nm determined from TEM images and is consistent with only a minor number fraction of particles having diameters ≫11 nm. A diffraction peak centered at 40.50 degrees in two-theta expected for the most intense (111) reflection of a possible L12 CoPt3 impurity is not observed.
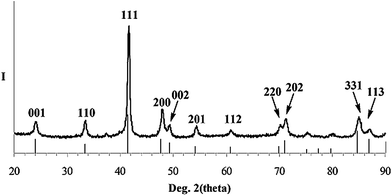 |
| Fig. 2 XRD pattern (Cu Kα radiation) of as-prepared L10 CoPt nanopowder along with the powder XRD line pattern and assigned peak indices of bulk L10 CoPt (PDF Card #43-1358). | |
Magnetic properties
Zero field cooled (ZFC) and field cooled (FC) magnetizations at 0.1 T and magnetic hysteresis loops recorded for as-prepared CoPt nanopowder at 5 K and 300 K are shown in Fig. 3. As shown in Fig. 3(a), the superparamagnetic transition is quite broad because of the size distribution of the particles, from really low temperature up to the equipment measurement limit of 380 K. From Fig. 3(b), an observed remanence of (2/π)Msat is consistent with a random uniform distribution of magnetocrystalline orientations within the powder specimen.
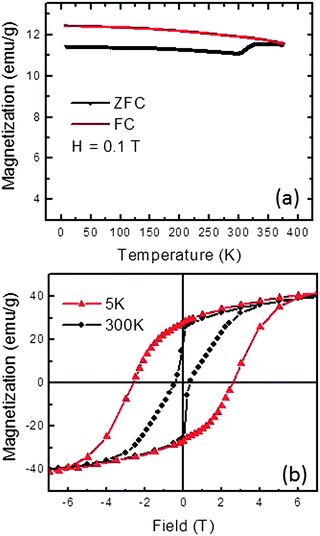 |
| Fig. 3 Temperature and field dependent magnetizations of as-prepared L10 CoPt nanopowder. (a) ZFC and FC magnetization under 0.1 T field. (b) Magnetic hysteresis loops at 5 K and 300 K. | |
However, hysteresis loop shapes and coercivity values show strong temperature dependence. At 5 K, a symmetrical ferromagnetic loop shape is observed with a coercivity value of 26.0 kOe. This coercivity is significantly greater than that reported for CoPt nanoparticles prepared by other methods (see Table 1) and is consistent with strong ferromagnetism expected of CoPt nanoparticles having high crystallinity and good control of metal alloy stoichiometry. At 300 K, a highly “pinched” hysteresis loop is observed with a coercivity of 4.0 kOe. While highly “pinched” CoPt hysteresis loops acquired near room temperature have been ascribed to the presence of a magnetically soft CoPt3 impurity phase,43 powder XRD data and the high coercivity of this powder at 5 K do not support this interpretation. A more likely explanation of the observed “pinched” hysteresis loop shape is that some number fraction of small CoPt nanoparticles are superparamagnetic near room temperature,44,45 while those particles bigger than 10 nm still show blocked behavior, giving rise to a combination of superparamagnetic and ferromagnetic effects at 300 K (see the particle-size histogram in Fig. 1). At 5 K, the sample appears wholly ferromagnetic with high coercivity, as expected when thermal energy is insufficient to randomize magnetic dipole oscillations of superparamagnetic particles.
Table 1 CoPt nanoparticulate specimen, processing temperature, nanoparticle average diameters, and measured coercivity values as reported or measured in this worka
CoPt sample |
Processing T (°C) |
CoPt size (nm) |
Coercivity, He, (Oe)/temperature |
Ref. |
PMMA = poly(methyl methacrylate); RT = room temperature.
|
CoPt powder |
650 |
11 |
4000/RT; 26 000/5 K |
Herein |
CoPt powder |
800 |
18 |
3202/RT |
19
|
CoPt powder |
700 |
13 |
3225/RT |
20
|
CoPt powder |
800 |
18 |
4442/RT |
20
|
CoPt powder |
700 |
18 |
6000/RT; 9300/5 K |
14
|
CoPt powder |
665 |
≫2 |
9000/5 K |
10
|
CoPt powder |
650 |
≫8 |
12 000/RT |
11
|
CoPt powder |
700 |
≫4 |
7570/RT |
16
|
CoPt powder |
550 |
6 |
5500/RT |
22
|
CoPt powder |
700 |
>7 |
630/RT |
18
|
CoPt/SiOx/Si |
700 |
20 |
H
‖c 8200/Rt; H⊥c 6636/RT |
26
|
CoPt/SiOx/Si |
750 |
20 |
H
⊥c 7400/RT |
46
|
CoPt/SiOx/Si |
750 |
20 |
H
‖c 7352; H⊥c 6850/RT |
44
|
CoPt/SiOx/Si |
750 |
20 |
H
‖c 5558; H⊥c 4070/RT |
47
|
CoPt/SiOx/Si |
600 |
5 |
160/RT; 1900/5 K |
15
|
CoPt/polyimide |
650 |
7 |
9800/10 K |
27, 48
|
CoPt@PMMA |
400 |
<10 |
300/300 K; 1665/5 K |
12
|
CoPt@Al2O3 |
1100/700 |
40 max. |
H
‖c 4500; H⊥c 6000/300 K |
29
|
H
‖c 9000; H⊥c 13 000/5 K |
CoPt@Al2O3 |
700 |
30 |
24 200/unspecified |
7
|
CoPt@carbon |
800 |
5.4 |
1390/RT |
6
|
CoPt@silica |
800 |
30 |
330/RT |
6
|
CoPt@Ag |
550 |
7–100 |
1000–17 000/unspecified |
49
|
Conclusions
L10 1
:
1 CoPt nanoparticles can be prepared in a one-step process by reactive thermal decomposition of CoPt(CO)4(dppe)Me supported on finely ground NaCl powder. Ferromagnetic Co1Pt1 powder is harvested by simple aqueous dissolution of the ionic support. Precursor loadings of ca. 2 wt% give polydisperse, free-flowing CoPt nanopowders having average diameter of 11 nm and high coercivity (26.0 kOe) at 5 K. This synthesis strategy provides good control of alloy stoichiometry and is both convenient and easily scalable.
Acknowledgements
Financial supported from a Vanderbilt University Discovery Grant is gratefully acknowledged by J.E.W. and C.M.L. Portions of this research were conducted at the Center for Nanophase Materials Sciences and at the SHaRE User Facility of Oak Ridge National Laboratory, both supported by the Division of Scientific User Facilities, Office of Science, U.S. Department of Energy. ORNL is managed by UT-Batelle, LLC, for the U.S. Department of Energy under contract DE-AC05-00OR22725. Work shown in this paper was supported by DOE-BES Grant DE-SC0006877.
Notes and references
-
S. Wirth and S. von Monlnar, Handbook of Advanced Magnetic Materials, Springer, New York, 2006, vol. 1, p. 294 Search PubMed.
- P. Entel and M. E. Gruner, J. Phys.: Condens. Matter, 2009, 21, 064228 CrossRef CAS.
-
T. B. Massalski and H. Okamoto, Binary alloy phase diagrams, ASM International, Materials Park, Ohio, 2nd edn, 1990 Search PubMed.
- F. Zheng, S. Alayoglu, V. V. Pushkarev, S. K. Beaumont, C. Specht, F. Aksoy, Z. Liu, J. Guo and G. A. Somorjai, Catal. Today, 2012, 182, 54–59 CrossRef CAS.
- Q.-S. Chen, S.-G. Sun, Z.-Y. Zhou, Y.-X. Chen and S.-B. Deng, Phys. Chem. Chem. Phys., 2008, 10, 3645–3654 RSC.
- E. Kockrick, F. Schmidt, K. Gedrich, M. Rose, T. A. George, R. Skomski and S. Kaskel, Chem. Mater., 2010, 22, 1624–1632 CrossRef CAS.
- Y. Sui, L. Yue, R. Skomski, X. Z. Li, J. Zhou and D. J. Sellmyer, J. Appl. Phys., 2003, 93, 7571–7573 CrossRef CAS.
- H. Wan, S. Shi, L. Bai, M. Shamsuzzoha, J. W. Harrell and S. C. Street, J. Nanosci. Nanotechnol., 2010, 10, 5089–5092 CrossRef CAS.
- C.-M. Shen, C. Hui, T.-Z. Yang, C.-W. Xiao, S.-T. Chen, H. Ding and H.-J. Gao, Chin. Phys. Lett., 2008, 25, 1479–1481 CrossRef CAS.
- H. L. Wang, Y. Zhang, Y. Huang, Q. Zeng and G. C. Hadjipanayis, J. Magn. Magn. Mater., 2004, 272–276, E1279–E1280 CrossRef CAS.
- X. Sun, Z. Y. Jia, Y. H. Huang, J. W. Harrel, D. E. Nikles, K. Sun and L. M. Wang, J. Appl. Phys., 2004, 95, 6747–6749 CrossRef CAS.
- J. Fang, L. D. Tung, K. L. Stokes, J. He, D. Caruntu, W. L. Zhou and C. J. O'Connor, J. Appl. Phys., 2002, 91, 8816–8818 CrossRef CAS.
- B. H. An, J. H. Wu, H. L. Liu, S. P. Ko, J.-S. Ju and Y. K. Kim, Colloids Surf., A, 2008, 313–314, 250–253 CrossRef.
- V. Tzitzios, D. Niarchos, G. Margariti, J. Fidler and D. Petridis, Nanotechnology, 2005, 16, 287–291 CrossRef CAS.
- M. Mizuno, Y. Sasaki, M. Inoue, C. N. Chinnasamy, B. Jeyadevan, D. Hasegawa, T. Ogawa, M. Takahashi, K. Tohji and K. Sato,
et al.
, J. Appl. Phys., 2005, 97, 10J301 CrossRef.
- C. N. Chinnasamy, B. Jeyadevan, K. Shinoda and K. Tohji, J. Appl. Phys., 2003, 93, 7583–7585 CrossRef CAS.
- C. Frommen and H. Rosner, Mater. Lett., 2004, 58, 123–127 CrossRef CAS.
- M. Chen and D. E. Nikles, J. Appl. Phys., 2002, 91, 8477–8479 CrossRef CAS.
- Y. Liu, Y. Yang, Y. Zhang, Y. Wang, X. Zhang, Y. Jiang, M. Wei, Y. Liu, X. Liu and J. Yang, Mater. Res. Bull., 2013, 48, 721–724 CrossRef CAS.
- Y. J. Zhang, Y. T. Yang, Y. Liu, Y. X. Wang, L. L. Yang, M. B. Wei, H. G. Fan, H. J. Zhai, X. Y. Liu and Y. Q. Liu,
et al.
, J. Phys. D: Appl. Phys., 2011, 44, 295003 CrossRef.
- U. Wiedwald, L. Han, J. Biskupek, U. Kaiser and P. Ziemann, Beilstein J. Nanotechnol., 2010, 1, 24–47 CrossRef CAS.
- A. C. C. Yu, M. Mizuno, Y. Sasaki, H. Kondo and K. Hiraga, Appl. Phys. Lett., 2002, 81, 3768–3770 CrossRef CAS.
- X.-W. Zhou, R.-H. Zhang, Y.-X. Jiang and S.-G. Sun, J. Nanosci. Nanotechnol., 2010, 10, 8265–8270 CrossRef CAS.
- F. Porrati, E. Begun, M. Winhold, Ch. H. Schwalb, R. Sachser, A. S. Frangakis and M. Huth, Nanotechnology, 2012, 23, 185702 CrossRef CAS.
- J. Penuelas, C. Andreazza-Vignolle, P. Andreazza, A. Ouerghi and N. Bouet, Surf. Sci., 2008, 602, 545–551 CrossRef CAS.
- L. Castaldi, K. Giannakopoulos, A. Travlos, D. Niarchos, S. Boukari and E. Beaurepaire, Nanotechnology, 2008, 19, 085701 CrossRef CAS.
- J. H. Kim, J. Kim, K. H. Baek, D. H. Im, C. K. Kim and C. S. Yoon, Colloids Surf., A, 2007, 301, 419–424 CrossRef CAS.
- J. Penuelas, A. Ouerghi, C. Andreazza-Vignolle, J. Gierak, E. Bourhis, P. Andreazza, J. Kiermaier and T. Sauvage, Nanotechnology, 2009, 20, 425304 CrossRef CAS.
- C. W. White, S. P. Withrow, J. D. Budai, D. K. Thomas, J. M. Williams, A. Meldrum, K. D. Sorge, J. R. Thompson, G. W. Ownby and J. F. Wendelken,
et al.
, J. Appl. Phys., 2005, 98, 114311 CrossRef.
- A. Hannour, L. Bardotti, B. Prevel, E. Bernstein, P. Melinon, A. Perez, J. Gierak, E. Bourhis and D. Mailly, Surf. Sci., 2005, 594, 1–11 CrossRef CAS.
- F. Tournus, N. Blanc, A. Tamion, M. Hillenkamp and V. Dupuis, J. Magn. Magn. Mater., 2011, 323, 1868–1872 CrossRef CAS.
- Z. Y. Pan, R. S. Rawat, J. J. Lin, S. Mahmood, R. V. Ramanujan, P. Lee, S. V. Springham and T. L. Tan, Appl. Phys. A: Mater. Sci. Process., 2010, 101, 609–613 CrossRef CAS.
- D. Alloyeau, C. Langlois, C. Ricolleau, Y. Le Bouar and A. Loiseau, Nanotechnology, 2007, 18, 375301 CrossRef.
- R. K. Rakshit and R. C. Budhani, J. Phys. D: Appl. Phys., 2006, 39, 1743–1748 CrossRef CAS.
- Y. Huang, Y. Zhang, G. C. Hadjipanayis, A. Simopoulos and D. Weller, IEEE Trans. Magn., 2002, 38, 2604–2606 CrossRef CAS.
- M. T. Klem, D. Willits, D. J. Solis, A. M. Belcher, M. Young and T. Douglas, Adv. Funct. Mater., 2005, 15, 1489–1494 CrossRef CAS.
-
E. L. Mayes and S. Mann, in Nanobiotechnology, ed. C. M. Niemeyer and C. A. Mirkin, 2004, pp. 278–287 Search PubMed.
- R. D. Rutledge, W. H. Morris III, M. S. Wellons, Z. Gai, J. Shen, J. Bently, J. E. Wittig and C. M. Lukehart, J. Am. Chem. Soc., 2006, 128, 14210–14211 CrossRef CAS.
- M. S. Wellons, W. H. Morris III, Z. Gai, J. Shen, J. Bentley, J. E. Wittig and C. M. Lukehart, Chem. Mater., 2007, 19, 2483–2488 CrossRef CAS.
- A. Fukuoka, S. Fukagawa, M. Hirano, N. Koga and S. Komya, Organometallics, 2001, 20, 2065–2075 CrossRef CAS.
- C. G. Granqvist and R. A. Buhrman, J. Catal., 1976, 42, 477–479 CrossRef CAS.
- Card no. 43–1358, Powder Diffraction File, International Center for Diffraction, Newton Square, PA, 1994 Search PubMed.
- V. Karanasos, I. Panagiotopoulos, D. Niarchos, H. Okumura and G. C. Hadjipanayis, J. Appl. Phys., 2000, 88, 2740–2744 CrossRef CAS.
- L. Castaldi, K. Giannakopoulos, A. Travlos, D. Narchos, S. Boukari and E. Beaurepaire, J. Magn. Magn. Mater., 2005, 290–291, 544–546 CrossRef CAS.
- V. Dupuis, N. Blanc, F. Tournus, A. Tamion, J. Tuaillon-Combes, L. Bardotti and O. Boisron, IEEE Trans. Magn., 2011, 47, 3358–3361 CrossRef CAS.
- L. Castaldi, K. Giannakopoulos, A. Travlos, D. Narchos, S. Boukari and E. Beaurepaire, J. Phys.: Conf. Ser., 2005, 10, 155–158 CrossRef CAS.
- L. Castaldi, K. Giannakopoulos, A. Travlos and D. Narchos, Appl. Phys. Lett., 2004, 85, 2854–2856 CrossRef CAS.
- J. H. Kim, J. Kim, N. Oh, Y.-H. Kim and C. K. Kim, Appl. Phys. Lett., 2007, 90, 023117 CrossRef.
- S. Stavroyiannis, I. Panagiotopoulos, D. Niarchos, J. A. Christodoulides, Y. Zhang and G. C. Hadjipanayis, Appl. Phys. Lett., 1998, 73, 3453–3455 CrossRef CAS.
Footnotes |
† Electronic supplementary information (ESI) available: See experimental procedures for molecular precursor synthesis and for NaCl ball milling. See DOI: 10.1039/c3tc31232a |
‡ Present address: Department of Physics, Fudan University, Shanghai 200433, China. |
§ Present address: Microscopy and Microanalytical Sciences, PO Box 7103, Oak Ridge, TN 37831, USA. |
|
This journal is © The Royal Society of Chemistry 2013 |
Click here to see how this site uses Cookies. View our privacy policy here.