DOI:
10.1039/C3RA44815K
(Paper)
RSC Adv., 2014,
4, 1212-1224
Facile preparation of uniform barium titanate (BaTiO3) multipods with high permittivity: impedance and temperature dependent dielectric behavior
Received
1st September 2013
, Accepted 14th November 2013
First published on
15th November 2013
Abstract
Perovskite barium titanate (BaTiO3) multipods were prepared via high temperature solid state reaction. The crystal structure and morphology of BaTiO3 particles were characterized by X-ray diffraction (XRD), field emission scanning electron microscopy (FESEM), high resolution transmission electron microscopy (HRTEM), and scanning probe microscopy (SPM). The XRD analysis of the crystal structure revealed that a single-phase compound was formed having tetragonal crystal structure. Calorimetric study (DSC) over room to high temperature was used to find the energy involved in different steps of synthesis especially during the initiation and the termination process for the formation of BaTiO3. These multipods have high average aspect ratio (∼10, where average diameter ∼300 nm and average length ∼3 μm) as seen from FESEM. UV-Vis spectroscopy reveals that the prepared material is UV active. The bulk and surface chemical composition of these BaTiO3 particles as investigated by Fourier transform infrared (FTIR) and X-ray photoelectron spectroscopy (XPS) spectra reveals that in the prepared BaTiO3, the titanium ions exist in two different oxidation states, namely Ti3+ and Ti4+. The BaTiO3 multipod exhibits high permittivity with relatively low dielectric loss. From impedance analysis of the material, the dual resistivity characteristics, one for grain and the other for grain-boundary can be distinguished. An equivalent circuit has been proposed through analysis of the complex impedance plot (Nyquist plot) for BaTiO3 multipods. This material has perfect capacitative nature as seen from the Bode plot, and can be used for charge storage devices and other electronic applications. From temperature dependent dielectric analysis, the Curie temperature of BaTiO3 multipods is found to be ∼85 °C.
1. Introduction
Barium titanate is an important electroactive ceramic material. Over the past few decades, the preparation of barium titanate (BaTiO3) in different nano forms such as nanoparticles, nanocubes, nanorods, nanowires, and nanotubes has attracted great attention from many researchers particularly because of their unique ferroelectric and piezoelectric properties. These properties are important and essential for the development of different nanoscale devices for transducers, piezoelectric sensors and actuators, energy-harvesting devices, memory devices including ferroelectric random access memories (FRAM), and also for optoelectronic applications.1–8 Piezoelectric oxides are of interest because of their potential applications in different fields ranging from sensors to radio frequency devices.9 Barium titanate is one of the most widely used ceramics in the electronics industry, especially for making multilayer ceramic capacitors (MLCCs).10,11 Literatures reveal that BaTiO3 can exist in different crystal structures depending on environmental temperatures, cubic (above Curie temperature), tetragonal (5 °C to Curie temperature), orthorhombic (−90 °C to 5 °C), and rhombohedral (<−90 °C) (Fig. 1).12–15
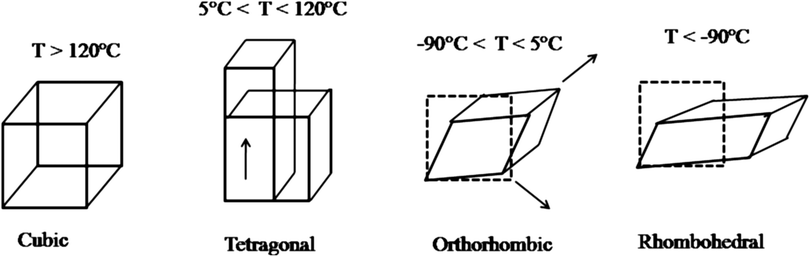 |
| Fig. 1 Crystallographic changes of BaTiO3.14,15 | |
In the cubic form, all the Ba2+ ions occupy eight corners of an elementary cubic cell, whereas single Ti4+ ion is in the centre of the cube and the O2− ions in the centre of each surface of that cube. However, below the Curie temperature BaTiO3 exists in the distorted tetragonal structure with a mutual displacement of the centers of positive and negative charges within the sub-lattice. Consequently, a dipole moment arises parallel to one of the cubic areas of the original phase. Such a generated spontaneous polarization in the tetragonal structure is the origin of its ferroelectric and piezoelectric behavior.16–18 Zhu et al. have prepared barium titanate nanoparticles through hydrothermal technique using titanium hydroxide, titanium dioxide, and barium hydroxide as starting materials where different solvents have used during the product preparation and the purification process.19 Peng et al. had taken H2TiO3 and Ba(NO3)2 as the starting materials for the preparation of BaTiO3 in aqueous medium with other solvents.20 Recently nanocrystalline BaTiO3 particles have been prepared by wet chemical methods21–24 such as sol–gel, coprecipitation, and hydrothermal methods where in all the cases solvents are used, so at the end of the process purification is necessary which is time consuming and costly process. Lee et al. have reported the preparation of barium titanate nano powder via hydrothermal and solvothermal synthesis methods and have described their structural characteristics. They have used organic solvents [diethanolamine (DEA) and triethanolamine (TEA)] to control the particle size.25 From the above literature reports, we can conclude BaTiO3 nanoparticles are usually prepared through wet chemical process. However, high cost and difficulty in process control in these routes forced to find out other ways for the preparations of BaTiO3 nano particles.26–28
The present investigation reports the preparation of BaTiO3 multipods using high temperature solid state reaction followed by sintering, using Ba(OH)2·8H2O and TiO2 as starting materials. The overall reaction for the BaTiO3 formation through heat treatment of stoichiometric amount of Ba(OH)2·8H2O and TiO2 at temperatures ranging from 700–1200 °C is given below:
|  | (1) |
The effect of process parameters like temperature on the crystal structure, morphology, optical properties, dielectric, and impedance properties of the formed barium titanate particles are discussed in detail.
2. Experimental section
2.1 Materials used
Anatase grade titanium dioxide (TiO2) and Ba(OH)2·8H2O were procured from Merck chemical Ltd., India. These two materials were used for the preparation of BaTiO3 multipods. Commercial grade BaTiO3 was purchased from Alfa Aesar, Germany and was used for comparing the results of barium titanate multipods with these supplied BaTiO3. Before the comparison study, the commercial BaTiO3 was subjected to heat treatment at 500 °C for 6 h in order to remove all the adsorbed moisture (physisorbed/chemisorbed).
2.2 Preparation and purification of BaTiO3 powder
Barium titanate multipods were prepared via high temperature solid state reaction using stoichiometric amount of Ba(OH)2·8H2O (Merck India, %) and anatase grade TiO2 (Merck India, %). Before taking the weight, both of these oxides were oven dried at 120 °C for 6 h for removing the adsorbed moisture and then these oxides were thoroughly mixed in an agate mortar and loaded in an alumina crucible. The mixture was heated in an electrical muffle furnace at 700 °C for 4 h and 1000 °C for 3 h followed by heating at 1200 °C (twice) for 4 h and 2 h respectively with three intermittent grindings. The resulting powder obtained was ground thoroughly using agate mortar and pestle. The above powder was purified using two solvents (ethanol or 1.0 N HCl solution) before doing the other characterizations. The prepared barium titanate powder was washed with ethanol/1.0 N HCl solution at three different time intervals (24 h, 48 h, and 72 h). The above product was then centrifuged and again washed with respective solvents (ethanol/DI water) for 6–7 times to maintain the neutral pH. The objective of washing the prepared powder with ethanol/1.0 N HCl solution is to remove the impurity present in the final product and to obtain purified barium titanate (BaTiO3) powder. Finally, the powder was oven dried at 120 °C for 6 h and then taken for XRD analysis. From XRD analysis, it was observed that the powder washed in 1.0 N HCl medium for 72 h (Fig. 2a) gave the best result. Finally, the purified barium titanate powder was compacted into pellets at a pressure of 12 tons for XPS, dielectric, and impedance study etc.
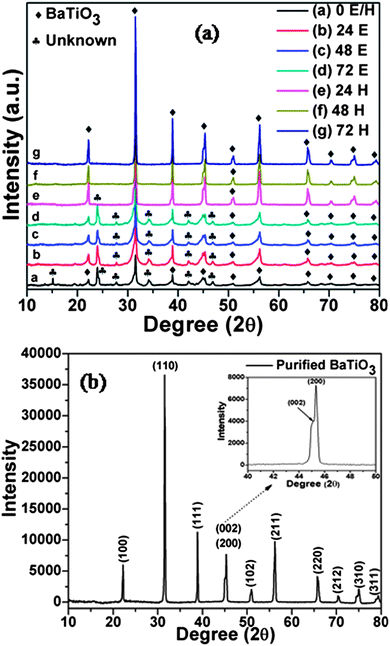 |
| Fig. 2 XRD pattern of (a) prepared BaTiO3 multipods at different purification conditions, (b) prepared BaTiO3 (pure) multipods. | |
2.3 Heat treatment of control samples [TiO2 and Ba(OH)2·8H2O] and commercial BaTiO3
Heat treatment of titanium dioxide was done at 1200 °C for 6 h in order to compare its characteristics with those of normal titania and BaTiO3 multipods. Similarly, heat treatment of Ba(OH)2·8H2O was also done but it was heat treated up to 700 °C for 6 h instead of 1200 °C as its boiling point is 780 °C.29 After heat treatment process all these samples were washed by ethanol/acid solution followed by water. Moreover, heat treatment of commercial BaTiO3 was done at 500 °C for 6 h in order to remove all the adsorbed moisture (physisorbed/chemisorbed).
3. Characterization
The crystal structure of different synthesized BaTiO3 powder samples were characterized by X-ray diffractometer (model PW 3040/60) with CuKα irradiation at λ = 1.5406 Å. The scanned diffractograms spread over the 2θ values from 10° to 90° at a scan rate of 0.13° s−1 using an X'celerator mode. The microstructure and grain size were analyzed through a field emission scanning electron microscope (FESEM, Carl Zeiss SMT AG, Germany), high resolution transmission electron microscope (HRTEM, JEM-2100), and scanning probe microscope (SPM, Multiview-1000™). FTIR spectra of different samples were recorded using IR spectrophotometer (model spectrum RX-I, PerkinElmer, Inc., MA, USA) in the range 400–4400 cm−1. The optical absorption spectra in the UV-visible range were obtained by UV-Vis spectrophotometer (Shimadzu UV-1700). Both dielectric and impedance properties of BaTiO3 powder were measured using precision LCR meter (Model. Quad Tech 7600) coupled with a homemade parallel plate sample holder. The surface composition of BaTiO3 multipods was determined through XPS using an Al-Kα excitation, an ESCA-2000 Multilab apparatus, VG microtech. Thermal analyses (TGA and DSC) of different samples were carried out using TGA/DSC 1, STARe System, METTLER TOLEDO at a heating rate of 20°C min−1 under nitrogen atmosphere over the temperature range of 45 °C to 1000 °C. The temperature dependent dielectric properties of BaTiO3 multipods were measured by Navocontrol, Alpha-A high performance frequency analyzer over the temperature range 40–250 °C at a steady increase of 5 °C up to 180 °C and at three other temperatures (200 °C, 230 °C, and 250 °C).
4. Results and discussion
4.1 X-ray diffraction analysis
X-ray diffraction analysis (XRD) was done on the prepared sample (BaTiO3) which revealed the presence of some unknown peaks along with the BaTiO3 peaks as shown in Fig. 2a. The obtained BaTiO3 powder was purified as described earlier in the Experimental section. The XRD results of both purified/impure BaTiO3 powders are given in Fig. 2a and b respectively. In Fig. 2a, “24 E” stands for washing of BaTiO3 powder for 24 h in ethanol (E) medium whereas “24 H” stands for washing of BaTiO3 powder for 24 h in HCl (H) medium. There are distinct differences in plots (Fig. 2a and b) of purified and unpurified samples of BaTiO3. Some extra peaks due to traces amount of impurity in unpurified samples (Fig. 2a) vanishes in plot of purified sample (Fig. 2b). In fact, the purified sample exhibits all well defined peaks reported for neat BaTiO3. Diffraction peaks for prepared BaTiO3 nanoparticles are observed at 2θ = 22.29°, 31.53°, 38.92°, 45.06/45.31°, 50.87°, 56.34°, 65.93°, 70.48°, 75.03°, and 79.44° and these peaks represent the Bragg reflections from the (100), (110), (111), (002)/(200), (102), (211), (220), (212), (310), and (311) planes respectively.30 The observed diffraction peaks (Fig. 2b) reveal the tetragonal crystal structure for BaTiO3 particles and the obtained XRD patterns are matching well with the standard XRD pattern of BaTiO3 particle (JCPDS card no. 79-2264). The tetragonal nature of the prepared BaTiO3 multipods is also evident from the XRD peak splitting [(002) and (200)] at 2θ ∼ 45,30 where the ratio of I002/I200 is ∼0.54 as reported by Zhu et al.30–34
Fig. 3 describes the comparison of XRD pattern of BaTiO3 multipods with normal titania, heat treated control samples [TiO2 and Ba(OH)2·8H2O], and commercial BaTiO3. It is observed that all the peaks of BaTiO3 multipods are fully matching with those of commercial BaTiO3 supplied by Alfa Aesar, Germany. Diffraction peaks for normal TiO2 particles are observed at 2θ = 25.45°, 36.90°, 37.86°, 38.64°, 48.06°, 53.85°, 54.95°, 62.27°, 62.81°, 68.96°, 70.34, 75.07, and 76.10°. But after heat treatment at 1200 °C, new peaks are observed which is due to the anatase to rutile phase transition in TiO2 at temperature above 900 °C.35 There are number of peaks observed for heat treated Ba(OH)2·8H2O, which are not present in the final product (BaTiO3 multipods).
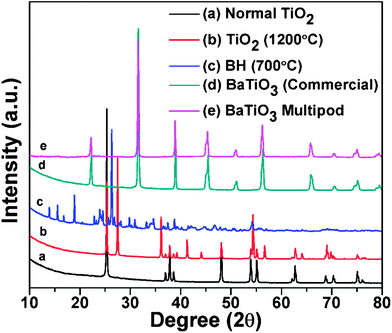 |
| Fig. 3 Comparison of XRD pattern of BaTiO3 multipods with normal titania, heat treated control samples [TiO2 and *Ba(OH)2·8H2O], and commercial BaTiO3. [*Ba(OH)2·8H2O = BH]. | |
4.2 High temperature TGA/DSC analysis
DSC analysis from room temperature to high temperature was carried out in order to find out the energy involved during barium titanate particle formation through reaction of barium hydroxide with titanium dioxide especially during the initiation and the termination process. Fig. 4A and B represent the TGA/DSC curves over the temperature range 45–1000 °C for stoichiometric mixture of Ba(OH)2·8H2O and TiO2, where Fig. 4A shows the TGA/DSC plot of the mixture during the first heating (1st run) and Fig. 4B represents the TGA/DSC plot of the mixture during the second heating (2nd run). During the first heating the weight and enthalpy changes are due to chemical reactions taking place in the system for formation of BaTiO3 whereas the changes during 2nd heating are mainly due to further modification of formed BaTiO3 during heating process. Fig. 4C shows the TGA/DSC result of impure BaTiO3 whereas Fig. 4D represents the TGA/DSC result of the purified BaTiO3. Fig. 4A shows three endothermic peaks at 81.15 °C, 135.5 °C, and 377.8 °C which are due to the three corresponding weight losses from the mixture. In case of Fig. 4B, there is only marginal weight loss but endothermic peaks at 71.6 °C, 396.6 °C, 650.2 °C, 761 °C, and 796 °C are observed which are due to the inter-diffusion (phase change) of BaTiO3 crystals and unreacted Ba(OH)2·8H2O and TiO2 crystals. Fig. 4C and D represent TGA and DSC plots for purified BaTiO3 multipods produced by solid state reaction and same BaTiO3 after chemical purification. The area under the endothermic peak (at 759.28 °C, Fig. 4D) is smaller than the area under the peak at 822.15 °C (Fig. 4C), which is due the presence of very minor quantities of impurity in case of purified BaTiO3 (Fig. 4D). In Fig. 4A–D beyond 800–850 °C, the DSC curve undergoes an exothermic phase transition (moves towards the exothermic end) which belong to the crystalline phase changes.36
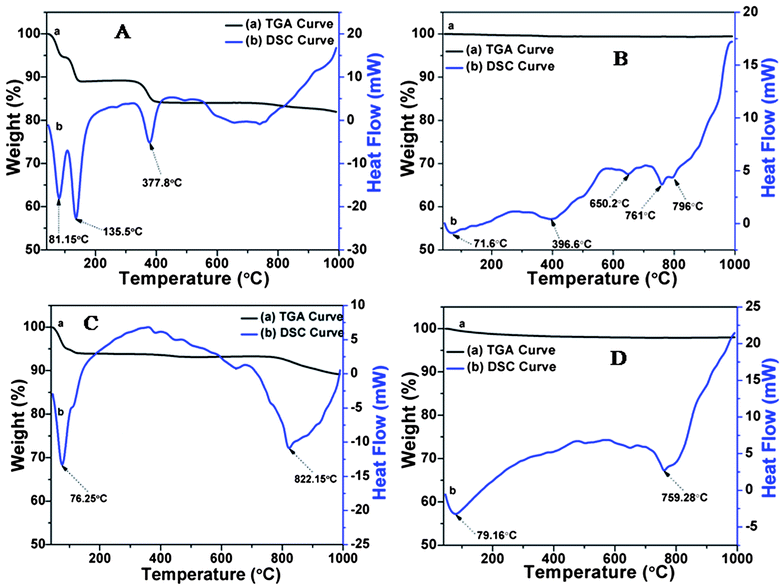 |
| Fig. 4 TGA/DSC curve for Ba(OH)2·8H2O and TiO2 mixture (A) 1st run, (B) 2nd run; TGA/DSC curve of (C) impure BaTiO3 and (D) purified BaTiO3. | |
4.3 Morphological analysis via FESEM, HRTEM, and SPM
The FESEM images of neat titania (TiO2), mixture of Ba(OH)2·8H2O and TiO2 at room temperature, and BaTiO3 prepared at different reaction conditions (temperature) are presented in Fig. 5. It is observed at ambient temperature that neat titania particles are spherical in nature where as Ba(OH)2·8H2O particles are rice grain shaped crystals (Fig. 5a and b). But solid state reaction between Ba(OH)2·8H2O and TiO2 at different temperatures lead to the formation of different types of BaTiO3 particles. In the initial stages of calcination process the inter-diffusion of Ba2+ ions to TiO2 phase and Ti4+ ions to Ba(OH)2·8H2O phase took place prior to formation of BaTiO3. When this was calcined at 700 °C (Fig. 5c), clustered mass was found to form due to inter-diffusion of counter ions. In this sample of barium titanate only one or two rod likes shape particles are observed, which may be due to the initiation of BaTiO3 particle formation. In fact, with the increase in reaction (calcinations) temperature, the extent of inter-diffusion of Ti4+ ions and Ba2+ ions increases leading to increase in concentration of BaTiO3 nanoparticles along with decrease in concentration of unreacted masses (TiO2 and Ba(OH)2·8H2O). However, the increase in calcination temperature also modifies the shape of the BaTiO3 particles. High temperature (≥1000 °C) treatment favors the anisotropic growth of barium titanate crystal in one direction. This unidirectional growth of BaTiO3 particles at 1000 °C leads to formation of grain shaped particles. This process further continues to form final star shaped BaTiO3 multipods when subjected to 1200 °C. The anisotropic growth of barium titanate crystals can be controlled by manipulating the temperature and time of reaction.37 From Fig. 5d, it is clear that some BaTiO3 particles formation is almost complete at calcination temperature 1000 °C. However, still there is small amount of unreacted clusters. When the calcination temperature is further increased to 1200 °C, BaTiO3 multipod formation becomes complete as seen from Fig. 5e and f (low and high magnification images of BaTiO3 particles). These BaTiO3 multipods are crystalline in nature as apparent from XRD analysis. Each BaTiO3 multipod consists of triangular-shaped blade like particles having higher width in the middle portion of particles with sharp ends with average particle length of ∼3 μm and average particle diameter of ∼300 nm (Fig. 5f). It is seen that each particle with high diameter in the middle with sharp ends are attached with each other at the centre and star like particle cluster is formed. These pictures reveal that as the calcinations temperature increases the formation of grain like particles increases. This is mainly because of increase in rate of diffusion process with rise in temperature. However, from XRD analysis of different BaTiO3 samples reveals that some impurities are associated with BaTiO3 particles (Fig. 2a) and this impurity can be removed by chemical purification process.
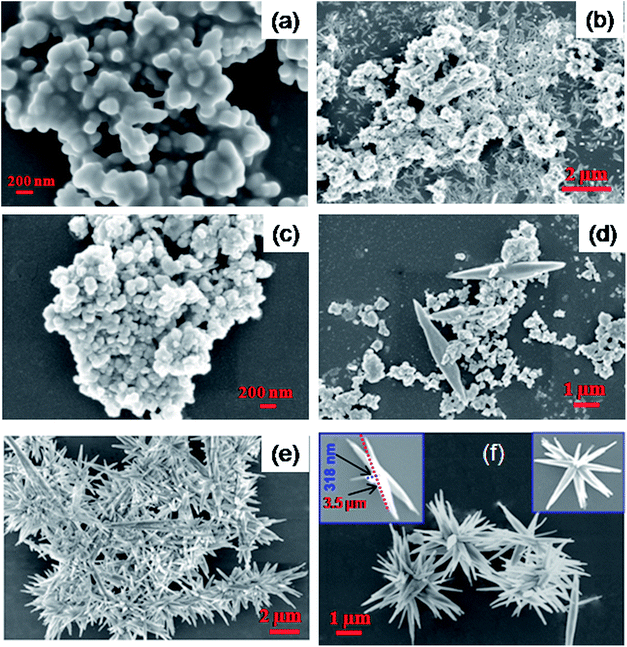 |
| Fig. 5 FESEM images of (a) neat titania powder, (b) mixture of Ba(OH)2·8H2O and TiO2 at room temperature, (c) BaTiO3 at 700 °C, (d) BaTiO3 at 1000 °C, (e) BaTiO3 multipods at 1200 °C (low magnification), and (f) star shaped BaTiO3 multipods at 1200 °C (high magnification). | |
Schematic model for different steps of formation of nano barium titanate particles through solid state reaction is proposed and shown as Scheme 1. The formation of BaTiO3 nanoparticles from Ba(OH)2·8H2O and TiO2 through solid state reaction is mainly due to inter-diffusion of Ti4+ and Ba2+ ions. As mentioned earlier the rate and extent of inter-diffusion process increase with increase in calcination temperature resulting in the formation of shell of BaTiO3 accompanied with release of water vapors during reaction process. As the process goes, there is continuous thickening of BaTiO3 shell formation. This formation of BaTiO3 particles continues till the reactants (Ba(OH)2·8H2O and TiO2) exhausts. However, taken in equimolar amount, traces of unreacted barium hydroxide and titania remain as impurity in the final BaTiO3 particles produced at highest temperature. Increase in temperature not only increase the extent of reaction but also modifies the shape of the BaTiO3 particles as mentioned earlier. At the highest temperature of calcination, the best triangular blade shaped (multipods) barium titanate particles are formed which are clustered in the form of star (Fig. 5e and f). The aspect ratio of such particles is high having average width ∼300 nm and length ∼3 μm. To understand the elemental composition of BaTiO3 multipods formed, a selected area of particle cluster is targeted for analysis (Fig. 6) and the composition of various elements present at that spot are furnished in Table 1.
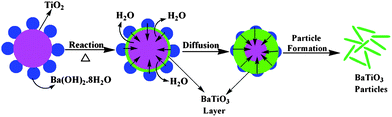 |
| Scheme 1 Proposed reaction model for the preparation of BaTiO3 multipods. | |
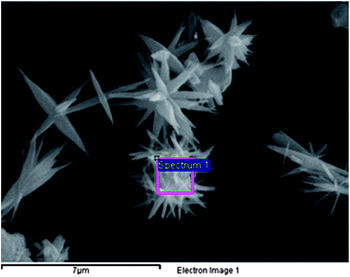 |
| Fig. 6 FESEM + EDS image of prepared BaTiO3 multipods. | |
Table 1 EDS value of BaTiO3 multipods
Element |
Weight% |
Atomic% |
O K |
49.05 |
63.01 |
Ti K |
12.45 |
18.21 |
Ba L |
38.50 |
18.77 |
Total |
100 |
|
The HRTEM image of these BaTiO3 particles is presented in Fig. 7a. From this image, it is observed that all nano particles are cylindrical grain like structure and have regular shape with high aspect ratio. The SAED pattern (Fig. 7b) exhibits distinct sharp diffraction patterns in consistent with XRD measurements. This confirms that the BaTiO3 particles are single crystalline in nature. The first four points/dots are assigned to reflection from the planes (100), (110), (111), and (200) respectively. These planes of tetragonal structure as revealed here and in good agreement with the XRD result discussed earlier.
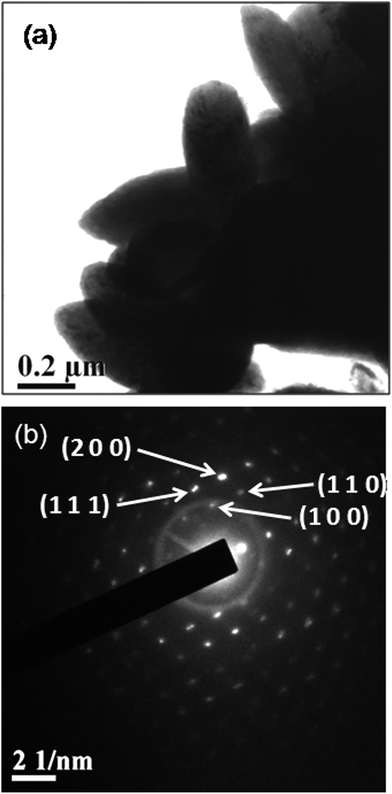 |
| Fig. 7 (a) HRTEM image and (b) SAED pattern of prepared BaTiO3 multipods. | |
SPM image and height profile of BaTiO3 particles are presented in Fig. 8a and b respectively. From the height profile (Fig. 8b), the formation of nanoparticles are confirmed through three distinct peaks (1, 2 and 3). Individual single particles of BaTiO3 can be detected in Fig. 8a at three different positions (1, 2 and 3) which was also seen from FESEM and HRTEM images. So from all these morphological analyses (FESEM, HRTEM, and SPM), the shape of BaTiO3 nanoparticles are like star shaped multipods with single/double/multi triangular blades.
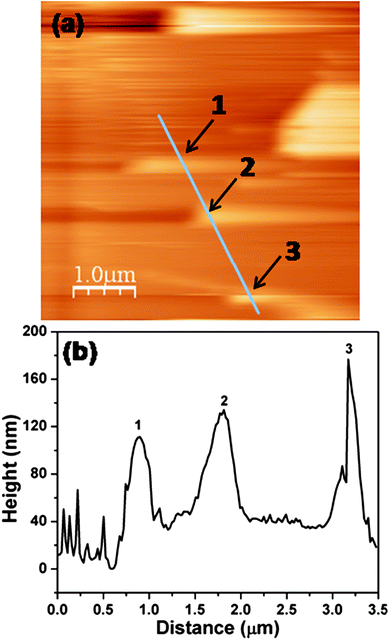 |
| Fig. 8 (a) SPM image and (b) height profiling of BaTiO3 multipods. | |
4.4 Fourier transform infrared (FTIR) spectroscopy
Fig. 9A(a)–(d) represents the FTIR spectra of neat TiO2 (dried), Ba(OH)2·8H2O (dried), and BaTiO3 (sintered at 1000 °C and 1200 °C). IR bands at 1442, 1058 and 857 cm−1 are characteristic peaks of CO2, which may be due to the areal CO2.38,39 The broad IR band centered at ∼592 cm−1 is typical of the Ti–O stretching vibrations in BaTiO3 (in TiO6 octahedra),40 and the peak at 452 cm−1 corresponds to the Ti–O bending vibrations (which is found to be at 449 cm−1 for BaTiO3 sintered at 1000 °C).40–42 The broad band observed at 3368 cm−1 corresponds to the –OH stretching vibration and the band at 1632 cm−1 is due to –OH bending vibration.41 The adsorption region spreading over ν ≈ 800–450 cm−1 is also characteristic of oscillation of M–O bonds, where M = Ba and Ti. The band at 431 cm−1 (Fig. 9B) as observed in the case of BaTiO3 sintered at 1200 °C may be attributed to the oscillation of Ba–O bonds.43 However, similar peak could not be precisely detected for TiO2 and BaTiO3 sintered at 1000 °C.
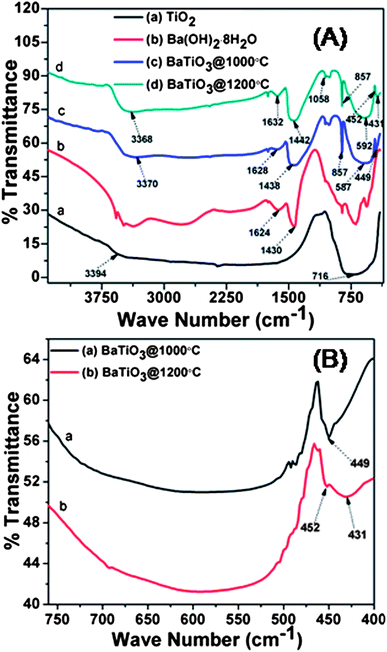 |
| Fig. 9 FTIR spectra of (A) neat titania, Ba(OH)2·8H2O, and BaTiO3 sintered at 1000 °C and 1200 °C, (B) selected portion of BaTiO3 sintered at 1000 °C and 1200 °C. | |
4.5 UV-visible spectra
The room temperature UV-visible absorption spectra of neat titania, Ba(OH)2·8H2O, and different BaTiO3 particles (prepared at three different sintering conditions) are presented in Fig. 10. The distinct UV absorption peak of BaTiO3 sintered at 1200 °C is observed at λ = 264 nm whereas for BaTiO3 sintered at 1000 °C and BaTiO3 sintered at 700 °C such distinct peaks could not be detected. For neat titania a low intensity absorption peak at λ = 229 nm is observed but Ba(OH)2·8H2O does not show any typical UV absorption peak. The observed UV absorption peak of the prepared BaTiO3 multipods can be assigned to the electronic transition in these multipods due to the presence of some Ti3+ along with Ti4+ mainly because of structural defects present in barium titanate.44 So it may be concluded that the BaTiO3 multipod as prepared in the present investigation is expected to be an useful candidate for optoelectronic applications and UV laser.16
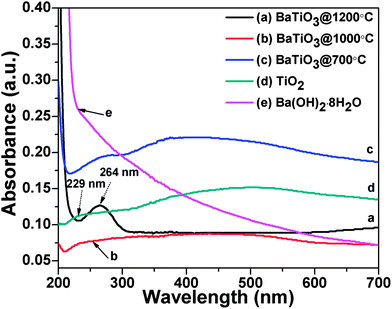 |
| Fig. 10 UV-Vis absorption spectrum of neat titania, Ba(OH)2·8H2O, and BaTiO3 multipods (at three different temperatures). | |
4.6 X-ray photoelectron spectroscopy (XPS) analysis
The XPS survey spectra of compacted BaTiO3 multipods and high resolution spectra of individual elements, Ba3d, Ti2p, and O1s are presented in Fig. 11(a)–(d). The survey spectra observed here are very similar to the reported literature.45 From the survey spectra, it is observed that the intensity of Ti2p peak is quite small as compared to Ba3d and O1s peaks, the fact was also apparent from EDS data presented in Table 1. O1s is splitted into two peaks present at around 529.73 eV and 530.71 eV which corresponds to oxygen atoms in the form of Ba–O–Ti and Ti–O–Ti respectively.46 The Ba3d peak can be resolved into two components (Ba3d5/2 and Ba3d3/2), where these peaks (Ba3d5/2 at 778.81 eV and Ba3d3/2 at 794.19 eV) correspond to barium in BaTiO3.47
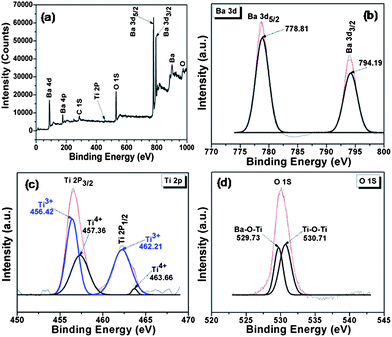 |
| Fig. 11 XPS spectra of BaTiO3 compacted powder: (a) survey spectra of BaTiO3 multipods; high resolution signals of (b) Ba3d (c) Ti2p, and (d) O1s elements. | |
The Ba4d signal is observed at 87.88 eV,47 whereas Ba4p signal is observed at 175.9 eV, which are due to different barium orbitals in BaTiO3 (as observed in survey spectrum). The Ti2p peak can be resolved into two components (Ti2p3/2 and Ti2p1/2), which can be deconvoluted into 4 peaks using Gaussian functions, two of which are located at around 457.36 eV and 463.66 eV, consistent with the Ti2p3/2 and Ti2p1/2 peaks of Ti4+ in BaTiO3 whereas other two peaks are located at around 456.42 eV and 462.21 eV, consistent with the Ti2p3/2 and Ti2p1/2 peaks of Ti3+ in BaTiO3.48 The observed binding energy (BE) of Ti2p3/2 (Ti3+) is around at 456.42 eV, which is somewhat smaller than the reported value of Ti2p3/2 (Ti4+). This downshift of the BE of Ti2p3/2 indicates that the oxidation state of Ti in BaTiO3 multipods shifts from Ti4+ to Ti3+. Some of the Ti4+ oxidation state in BaTiO3 transformed to Ti3+ state in order to balance the oxygen vacancies present in the system.49 From XPS analysis, it is apparent that there are some structural defects in the sample and these are due to local oxygen vacancies in synthesized material. The XPS analysis is a useful technique to detect the surface chemical composition and material structure.49 The C1s peak as observed in survey spectra may be due to the carbon of CO2 in the air.
4.7 Dielectric and impedance behavior of BaTiO3 multipods
The dielectric spectra in terms of semi-log plots of log
f vs. dielectric constant (ε′) and dielectric loss (ε′′) against frequency are given in Fig. 12a. From this plot, it is observed that both dielectric constant and loss factor increase with the decrease in frequency but the increase is very small over the frequency range 106 to 102 Hz, there after sudden increase in both dielectric constant (ε′) and loss (ε′′) with further decrease in frequency can be detected. It is noteworthy that the prepared BaTiO3 multipods exhibits almost frequency independent dielectric constant (ε′) and loss (ε′′) over a wide frequency range, 103 to 106 Hz. It is also observed from Fig. 12a (inset) that the magnitude of dielectric loss is less than the dielectric constant over entire frequency range of measurement, this indicates that the prepared material is a good candidate for charge storage device and can serve the purpose of useful component in electronic devices. Fig. 12b shows the AC impedance (|Z|) and phase angle of BaTiO3 multipods as a function of frequency which is also known as Bode plot. It was apparent from this figure that the impedance (|Z|) is frequency dependent and decreases with the increase in frequency. The increase in impedance (|Z|) with the decrease in frequency is an indication of the existence of space charge polarization in the material.50 The plot of real impedance (Z′) against imaginary impedance (Z′′) (Fig. 12c) is well known as Nyquist plot where, Z′ represents the bulk resistance (RB) and Z′′ represents the maximum value of angular frequency (ωmax), i.e., the top part of the semicircle, and is given by: |  | (2) |
where, RB = bulk resistance and CB = bulk capacitance.
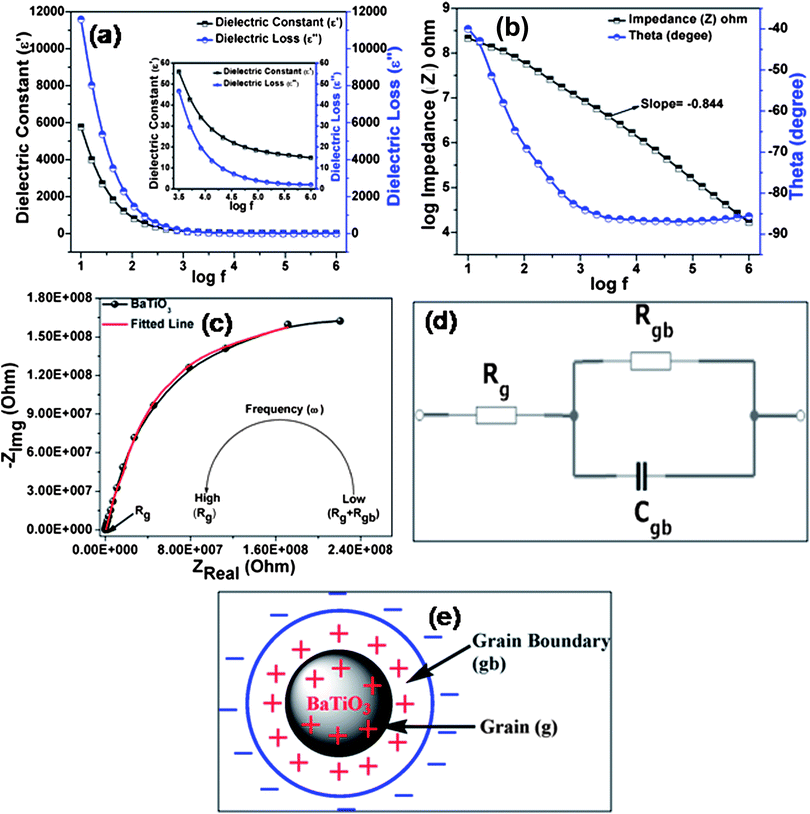 |
| Fig. 12 (a) Plot of log f vs. ε′ and ε′′, (b) Bode plot for BaTiO3 multipods, and (c) Nyquist plot for BaTiO3 multipods, (d) simplified equivalent circuit, and (e) schematic representation of BaTiO3 grain boundary and grain interior. | |
The impedance spectroscopy in terms of Nyquist plot is characterized by the appearance of the semicircular arcs. This semicircular arc for the present systems indicates the occurrence of dielectric relaxation spectra with a relatively narrow range of relaxation time. The impedance value at very high frequency is Rg whereas at very low frequency is Rg + Rgb as depicted in Fig. 12c. At both very high and very low frequencies, the phase angle is nearly zero (Fig. 12b). However, at intermediate frequencies the phase angle started to approach −90°, the phase angle of an ideal capacitor. In this region, the slope was often (but not always) close to −1 (ideal capacitor).51 Any practical dielectric having loss characteristics cannot be represented only by a loss free capacitor, rather it is a combination of capacitor and resistor, the later gives the path for loss current. Various types of combination of capacitors and resistors are possible to represent different dielectric materials effectively. For the present system also similar combination as described in Fig. 12d is proposed. From Fig. 12b, it was observed that the slope of impedance curve is −0.844 which is very close to −1, so the prepared BaTiO3 particles can act as an ideal capacitor. The obtained impedance data can be correlated with proposed equivalent circuits using electrochemical impedance spectroscopy (EIS) data analysis software (ZSimpWin) to design an equivalent circuit (Randles cell) to represent prepared BaTiO3. The equivalent circuit for semiconducting lossy BaTiO3 based material was first proposed by Heywang,52 as a common example for a simplified equivalent circuit.53 The impedance of the RC-parallel combination is given as
| 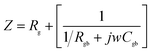 | (3) |
where,
Rg is the grain resistance,
Rgb is the grain-boundary (
Fig. 12e) resistance and
Cgb is the grain-boundary capacitance. The dc impedance equals to (
Rg +
Rgb), while the intercept of the impedance curve at high frequencies with the real axis equals to
Rg. So the BaTiO
3 may be considered as an electrically different two phase system,
i.e., one inter-grain and other inside bulk.
The dielectric constant of barium titanate multipods is compared with the control samples [heat treated TiO2 and Ba(OH)2·8H2O] and is presented in Fig. 13a. The significant increase in dielectric constant for BaTiO3 multipods at low frequency region is due to interfacial and space charge polarization. Though the difference in the dielectric constant at high frequency region is small, the value of dielectric constant of BaTiO3 multipods is more than the control samples (heat treated titania and barium hydroxide). Fig. 13b represents the comparison of permittivity (ε′) of BaTiO3 multipods with commercial BaTiO3 particles. It observed that the prepared BaTiO3 multipods have higher dielectric constant than the commercial BaTiO3 particles over the entire frequency range of measurement (10 Hz to 1 MHz). There is a significant increase in dielectric constant especially at low frequency region for the prepared sample. Fig. 13c illustrates the AC impedance (|Z|) and phase angle of BaTiO3 multipods and commercial BaTiO3 as a function of frequency which is also known as Bode plot. As we have discussed earlier the slope of impedance curve for BaTiO3 multipods is −0.844 (Fig. 13c) which is very close to −1, so the prepared BaTiO3 multipods can act as an ideal capacitor.51 Moreover, from Fig. 13c it is observed that as the impedance vs. frequency curve is not a straight line in case of commercial BaTiO3 particles, it has two slopes. At high frequency region (1 kHz to 1 MHz) its value (−0.831) is close to −1 whereas it is −0.27 at low frequency region (10 Hz to 1 kHz). This dual nature of commercial sample makes it unsuitable as capacitative material especially at low frequency range (10 Hz to 1 kHz).
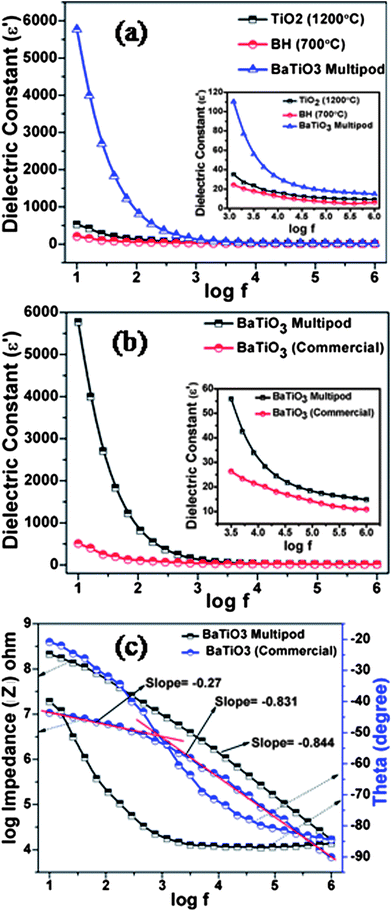 |
| Fig. 13 Comparison of permittivity (ε′) of BaTiO3 multipods (a) with control samples [heat treated TiO2 and Ba(OH)2·8H2O], (b) with commercial BaTiO3; (c) Bode plot comparison between BaTiO3 multipods and commercial BaTiO3. | |
4.8 Effect of temperature on dielectric constant/permittivity and impedance of BaTiO3 multipods
Fig. 14(a)–(c) represents the temperature dependent behavior of dielectric constant (permittivity) at three different frequencies (10, 103 and 106 Hz) for barium titanate powder prepared through high temperature solid state reaction. The value of dielectric constant is the highest at the lowest measurement frequency (10 Hz) and least at the highest frequency (1 MHz). As mentioned earlier the increased dielectric constant at low frequency is mainly due to increased contribution of space charge polarization along with dipolar polarization. It is also interesting to note that dielectric constant changes marginally with increase in temperature but suddenly shoots up to high value at the temperature 85 °C which represent its Curie point. This is found to be true for all measurement frequencies. Above ∼85 °C, the prepared sample attains the cubic structure where in the unit cell of BaTiO3 “Ti” atom exists in the equilibrium position in the center of the octahedra. However, when electric field is applied the position shifting of “Ti” with respect to oxygen atom occurs causing some induced dipoles. In fact, this crystal structure changes can be assumed to be due to distortion of edges of unit cubic cell and this distortion results in spontaneous polarization.54 In fact, this polarization arises due to movement of “Ti” atoms with respect to adjacent oxygen atoms and this gives rise to spontaneous polarization below Curie temperature where it exists in forms other than cubic structure (symmetrical structure with no bond distortion). The high dielectric constant of barium titanate is due to the permanent dipole in the structure below the Curie temperature. Due to the less stable lattice structure in vicinity of phase transitions, the Ti4+ ions have an increased mobility giving a higher dielectric constant at these transitions.
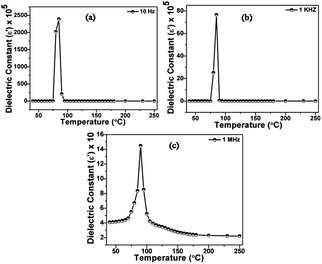 |
| Fig. 14 (a–c) Dielectric constant values of BaTiO3 multipods as a function of temperature and frequency. | |
The variation of impedance (|Z|) with frequency (log
f) at different temperatures is presented in Fig. 15. Impedance (|Z|) increases with the decrease in frequency, however at any particular frequency |Z| decreases with increase in temperature. In fact, the semilog plots of |Z| vs. frequency at three temperatures (80 °C, 85 °C, and 90 °C) are very close to each other when variations at lower temperatures (40 °C and 70 °C) and at 100 °C are shown in the same plot. However, it has been observed that the lowest impedance value at any particular frequency is observed for the measurement temperature 85 °C.
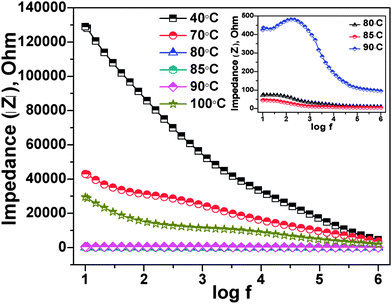 |
| Fig. 15 Variation of impedance with frequency at different temperatures. | |
This decrease in impedance indicates that the AC conductivity (σac) of BaTiO3 multipods increases with the increase in temperature and attains the highest value at ∼85 °C, which is the Curie point of the developed material. This result further corroborates the variation of permittivity against temperature as given in Fig. 14(a)–(c), where sudden increase in dielectric constant at Curie point (∼85 °C) was also observed. The reason for sudden increase in AC conductivity (σac) or permittivity (ε′) at ∼85 °C is described under the section “temperature dependent dielectric constant/permittivity”.
5. Conclusions
Solid state reaction and sintering at different temperatures forms BaTiO3 with different shapes. Star shaped BaTiO3 multipods consisting of protruding cones (average base diameter ∼300 nm and length ∼3 μm) from the centre of stars have been prepared by solid state reaction and sintering at 1200 °C. The Curie temperature of this material is found to be ∼85 °C. SAED and X-ray diffraction analyses reveal that these multipods have tetragonal structure. A dielectric study reveals that dielectric loss is less than the dielectric constant over a wide frequency range (102 to 106 Hz). The Bode plot confirms the capacitative nature of this material indicating its application as charge storage device. UV sensitivity of this material is also an interesting feature which implies that this material may be exploited for optoelectronic devices.
Acknowledgements
The authors would like to thank Indian Institute of Technology Kharagpur, India for its research facility and for providing fellowship. The authors are also thankful to Department of Physics & Meteorology, Indian Institute of Technology Kharagpur, India for XPS study.
References
- W. Chen and Q. a. Zhu, Mater. Lett., 2007, 61, 3378–3380 CrossRef CAS PubMed
.
- Z. Deng, Y. Dai, W. Chen, X. Pei and J. Liao, Nanoscale Res. Lett., 2010, 5, 1217–1221 CrossRef CAS PubMed
.
- W. Cai, C. Fu, Z. Lin and X. Deng, Ceram. Int., 2011, 37, 3643–3650 CrossRef CAS PubMed
.
- Y. Mao, T.-J. Park and S. S. Wong, Chem. Commun., 2005, 5721–5735 RSC
.
- X. Wang and Y. Li, Pure Appl. Chem., 2006, 78(1), 45–64 CrossRef CAS
.
- Y. Xia, P. Yang, Y. Sun, Y. Wu, B. Mayers, B. Gates, Y. Yin, F. Kim and H. Yan, Adv. Mater., 2003, 15, 353–389 CrossRef CAS
.
- W. S. Yun, J. J. Urban, Q. Gu and H. Park, Nano Lett., 2002, 2, 447–450 CrossRef CAS
.
- J. J. Urban, W. S. Yun, Q. Gu and H. Park, J. Am. Chem. Soc., 2002, 124, 1186–1187 CrossRef CAS PubMed
.
- Y. Yang, J. Yao, Y. U. Wang, J. Li, J. Das and D. Viehland, ACS Nano, 2009, 3, 3045–3050 CrossRef CAS PubMed
.
- X. Zhu, J. Wang, Z. Zhang, J. Zhu, S. Zhou, Z. Liu and N. Ming, J. Am. Ceram. Soc., 2008, 91, 1002–1008 CrossRef CAS
.
- E. K. Nyutu, C.-H. Chen, P. K. Dutta and S. L. Suib, J. Phys. Chem. C, 2008, 112, 9659–9667 CAS
.
-
http://www.azom.com/article.aspx?ArticleID=81
.
-
http://www.gitam.edu/eresource/Engg_Phys/semester_2/dielec/BaTiO3.htm
.
-
http://www.sjsu.edu/faculty/selvaduray/page/papers/mate115/hsiaolin.pdf, 2013.
- E. K. Al-Shakarchi, J. Korean Phys. Soc., 2010, 57(2), 245–250 CrossRef CAS
.
- R. Vijayalakshmi and V. Rajendran, Digest Journal of Nanomaterials and Biostructures, 2010, 5, 511–517 Search PubMed
.
- P. Nanni, M. Leoni, V. Buscaglia and G. Aliprandi, J. Eur. Ceram. Soc., 1994, 14, 85–90 CrossRef CAS
.
- L. K. Templeton and J. A. Pask, J. Am. Ceram. Soc., 1959, 42, 212–216 CrossRef CAS
.
- X. H. Zhu, J. M. Zhu, S. H. Zhou, Z. G. Liu, N. B. Ming and D. Hesse, Solid State Phenom., 2005, 106, 41–46 CrossRef CAS
.
- Z. Peng and Y. Chen, Microelectron. Eng., 2003, 66, 102–106 CrossRef CAS
.
- I. J. Clark, T. Takeuchi, N. Ohtori and D. C. Sinclair, J. Mater. Chem., 1999, 9, 83–91 RSC
.
- S. Kumar, G. a. L. Messing and W. B. White, J. Am. Chem. Soc., 1993, 76(3), 617–624 CAS
.
- H. S. Potdar, P. Singh, S. B. Deshpande, P. D. Godbole and S. Date, Mater. Lett., 1990, 10(3), 112–117 CrossRef CAS
.
- H. Shimooka and M. Kuwabara, J. Am. Chem. Soc., 1996, 79(11), 2983–2985 CAS
.
- H.-W. Lee, S. Moon, C.-H. Choi and D. K. Kim, J. Am. Chem. Soc., 2012, 95(8), 2429–2434 CAS
.
- U. Manzoor and D. K. Kim, J. Mater. Sci. Technol., 2007, 23, 655–658 CAS
.
- X. Wang, B. I. Lee, M. Z. Hu, E. A. Payzant and D. A. Blom, J. Mater. Sci. Lett., 2003, 22, 557–559 CrossRef CAS
.
- P. P. Phule and S. H. Risbud, J. Mater. Sci., 1990, 25, 1169–1183 CAS
.
-
http://www.chemicalland21.com/industrialchem/inorganic/BARIUM%20HYDROXIDE.htm
.
- A. C. Roy and D. Mohanta, Scr. Mater., 2009, 61, 891–894 CrossRef CAS PubMed
.
- E. J. H. Lee, F. M. Pontes, E. R. Leite, E. Longo, J. A. Varela, E. B. Araujo and J. A. Eiras, J. Mater. Sci. Lett., 2000, 19, 1457–1459 CrossRef CAS
.
- W. Zhu, S. A. Akbar, R. Asiaie and P. K. Dutta, J. Electroceram., 1998, 2(1), 21–31 CrossRef CAS
.
- S. W. Lu, B. I. Lee, Z. L. Wang and W. D. Samuels, J. Cryst. Growth, 2000, 219, 269–276 CrossRef
.
- L. Huang, Z. Chen, J. D. Wilson, S. Banerjee, R. D. Robinson, I. P. Herman, R. Laibowitz and S. O'Brien, J. Appl. Phys., 2006, 100, 034316 CrossRef
.
- D.-J. Won, C.-H. Wang, H.-K. Jang and D.-J. Choi, Appl. Phys. A: Mater. Sci. Process., 2001, 73, 595–600 CrossRef CAS
.
- G. S. Pozan and I. Boz, Can. J. Chem. Eng., 2010, 88, 76–80 CrossRef CAS
.
- F. Maxim, P. Ferreira, P. M. Vilarinho and I. Reaney, Cryst. Growth Des., 2008, 8(9), 3309–3315 CAS
.
-
http://jvarekamp.web.wesleyan.edu/CO2/FP-1.pdf
.
-
http://irina.eas.gatech.edu/EAS8803_Fall2009/Lec6.pdf
.
- M. D. C. B. Lopez, G. Fourlaris, B. Rand and F. L. Riley, J. Am. Ceram. Soc., 1999, 82, 1777–1786 CrossRef CAS
.
- A. T. Chien, X. Xu, J. H. Kim, J. Sachleben, J. S. Speck and F. F. Lange, J. Mater. Res., 2011, 14, 3330–3339 CrossRef
.
- H. Reveron, C. Aymonier, A. Loppinet-Serani, C. Elissalde, M. Maglione and F. Cansell, Nanotechnology, 2005, 16, 1137–1143 CrossRef CAS
.
- A. V. Polotai, A. V. Ragulya, T. V. Tomila and C. A. Randall, Ferroelectrics, 2004, 298, 243–251 CrossRef CAS
.
- M. R. A. Bhuiyan, M. M. Alam, M. A. Momin, M. J. Uddin and M. Islam, International Journal of Materials Engineering, 2012, 1, 21–24 CrossRef PubMed
.
-
http://tel.archives-ouvertes.fr/docs/00/71/91/96/PDF/2010CLF22040.pdf
.
- Q. Yu, D. Liu, R. Wang, Z. Feng, Z. Zuo, S. Qin, H. Liu and X. Xu, Mater. Sci. Eng., B, 2012, 177, 639–644 CrossRef CAS PubMed
.
- C. Miot, E. Husson, C. Proust, R. Erre and J. P. Coutures, J. Mater. Res., 2011, 12, 2388–2392 CrossRef
.
- J.-L. Jou, C.-M. Lei, Y.-W. Xu and W.-C. V. Yeh, Chin. J. Phys., 2012, 50(6), 926–931 CAS
.
- Y. Yang, X. Wang, C. Sun and L. Li, Nanotechnology, 2009, 20, 055709 CrossRef PubMed
.
- P. Dhak, D. Dhak, M. Das, K. Pramanik and P. Pramanik, Mater. Sci. Eng., B, 2009, 164, 165–171 CrossRef CAS PubMed
.
- D. Loveday, P. Peterson and B. Rodgers, JCT CoatingsTech, 2004, 1, 46–52 CAS
.
- W. Heywang, Solid-State Electron., 1961, 3, 51–58 CrossRef CAS
.
- Z. Tang, Z. Zhou and Z. Zhang, Sens. Actuators, B, 2003, 93, 391–395 CrossRef CAS
.
-
W. Hsiao-Lin, Structure and dielectric properties of Perovskite–Barium Titanate (BaTiO3), Submitted in Partial Fulfillment of Course Requirement for MatE 115, Fall 2002, San Jose State University.
|
This journal is © The Royal Society of Chemistry 2014 |
Click here to see how this site uses Cookies. View our privacy policy here.